焊点开裂不良因素是什么?焊点失效分析
器件焊点开裂的主要原因

器件焊点开裂的主要原因
器件焊点开裂是电子产品常见的故障之一,其主要原因有以下几点:
1. 焊接工艺不当:焊接温度、时间、压力等参数不合适,会导致焊点内部应力过大,在使用过程中容易发生开裂。
2. 材料质量问题:焊点使用的焊料、基材等材料质量不良,容易发生开裂。
3. 外力冲击:在使用过程中,器件受到外力冲击,如振动、碰撞等,也容易导致焊点开裂。
4. 振动和温度变化:器件在使用过程中,由于温度变化或振动等因素,导致焊点产生微小的变形,最终导致开裂。
为避免器件焊点开裂,应注意以下几点:
1. 选择质量可靠的焊接材料和器件,确保焊接工艺规范。
2. 设计产品时应考虑到产品的使用环境和外力因素,采用合适的材料和结构设计。
3. 在使用过程中,应尽量避免器件受到外力冲击,如避免碰撞、振动等。
4. 定期对器件进行检测和维护,及时发现问题并进行修复。
- 1 -。
焊件失效分析(1)

焊件失效分析(1)焊件失效分析焊接是现代制造业中常见的连接方法,广泛应用于汽车工业、航空航天、建筑等领域。
但是,在使用过程中,焊件失效是经常发生的情况。
下面从以下几个方面来分析焊件失效原因和解决方法。
1.焊接过程控制焊接过程的控制是焊件成败的关键。
焊接过程中的一些问题如氧气和湿气的侵入、杂质的混入等都会导致焊接质量下降,甚至造成焊件的失效。
因此,在焊接过程中需要采取适当的措施,如严格控制焊接温度、控制焊接速度、选择合适的焊接材料等,以确保焊接过程的质量。
2.设计的缺陷焊件失效的另一个原因是设计缺陷。
在焊件的设计过程中,如果设计存在问题,如焊缝长、焊接点过多等,则会导致焊件在使用过程中出现疲劳断裂的问题。
因此,需要在焊件设计的过程中,结合实际使用情况,合理设计焊件结构,以降低焊件失效的风险。
3.使用环境焊件的使用环境也是焊件失效的重要原因之一。
在恶劣的使用环境下,如高温、腐蚀等,焊件的质量容易下降,导致焊件失效。
因此,需要根据实际使用环境条件选择合适的焊接材料和焊接方法,以降低焊件失效的风险。
4.焊接强度焊接强度是指焊缝的承载能力,它对焊件的稳定性和耐久性有着直接的影响。
如果焊接强度过低,焊件就容易在使用过程中出现疲劳断裂的问题。
因此,在焊接过程中要控制好焊接强度,以确保焊件长时间的稳定性。
总体来说,焊件失效是多方面因素复合的结果,需要结合实际情况进行综合分析和处理。
要做好焊件失效分析,需要在焊接前的准备过程中,对焊接材料和焊接方法进行科学而严谨的挑选和控制,并在焊件设计阶段尽可能避免缺陷。
在焊接过程中,人工操作要规范严格,监控要及时,同时根据使用环境选择合适的防护措施。
这些措施可以为焊件的长期稳定运行提供保障。
常见焊点缺陷及分析

常见焊点缺陷及分析1. 引言焊接是一种将金属零件通过熔化并在冷却过程中形成联接的技术。
在焊接过程中,焊点缺陷是不可避免的,它们可能会对焊接连接的强度、可靠性和外观造成负面影响。
理解和分析常见的焊点缺陷对于确保焊接连接的质量至关重要。
本文将介绍几种常见的焊点缺陷,包括松动焊点、气孔、夹杂物和热裂纹,并对其产生的原因和分析方法进行探讨。
2. 常见焊点缺陷及分析2.1 松动焊点松动焊点是指焊接接头中的焊点出现松动或脱落的现象。
这种缺陷可能是由焊接接头的设计不良、焊接过程中温度和压力不足、焊接材料不匹配或焊接后应力集中等因素造成的。
在分析时,可以通过检查焊接接头的外观和使用显微镜观察焊点的表面来确定是否存在松动焊点。
针对松动焊点的修复方法包括重新焊接、补焊或增加焊接材料等。
2.2 气孔气孔是指焊接接头中的小空洞或气泡。
气孔可以分为气孔性缺陷和气孔状缺陷两种类型。
气孔性缺陷是由于焊接过程中金属熔融时溶解的气体无法顺利逸出而形成的。
气孔状缺陷则是由焊接材料中的气孔聚集而成。
气孔的出现可能是由于焊接材料或焊接环境中存在杂质、气体成分不纯或焊接过程中的不良操作造成的。
分析气孔缺陷时,可以通过X射线检测、显微镜观察和金相分析等方法进行定性和定量的评估。
修复气孔缺陷的方法包括重新焊接、吹除气孔、填充焊接材料等。
2.3 夹杂物夹杂物是指焊接接头中的杂质或外来物质。
焊接过程中,杂质和外来物质可能会被夹在焊接材料中,导致焊点出现缺陷。
夹杂物的存在可能会降低焊接接头的强度和可靠性。
夹杂物的形成原因包括焊接材料的纯净度不高、焊接环境的污染、焊接操作的不当等。
分析夹杂物缺陷时,可以通过显微镜观察、化学分析和金相测试等方法进行定性和定量的评估。
修复夹杂物缺陷的方法包括重新焊接、清除夹杂物、更换焊接材料等。
2.4 热裂纹热裂纹是指焊接接头中的裂纹缺陷。
焊接过程中,焊接材料经历了热收缩和冷却的过程,可能会导致焊接接头出现残余应力和裂纹。
CQFP器件焊点开裂失效分析_张伟
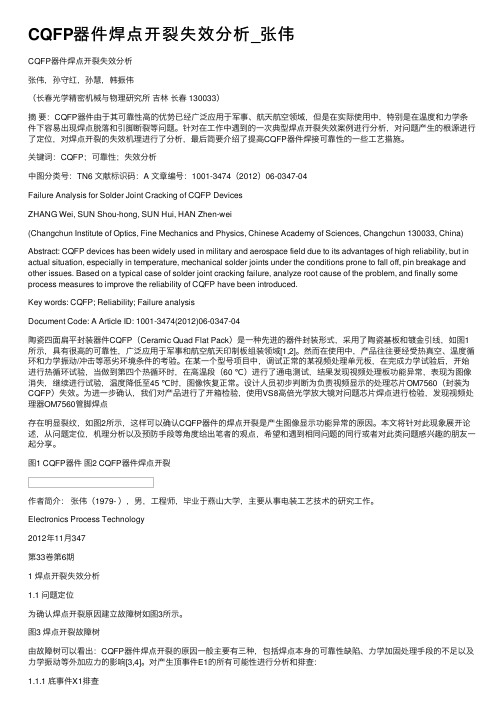
CQFP器件焊点开裂失效分析_张伟CQFP器件焊点开裂失效分析张伟,孙守红,孙慧,韩振伟(长春光学精密机械与物理研究所吉林长春 130033)摘要:CQFP器件由于其可靠性⾼的优势已经⼴泛应⽤于军事、航天航空领域,但是在实际使⽤中,特别是在温度和⼒学条件下容易出现焊点脱落和引脚断裂等问题。
针对在⼯作中遇到的⼀次典型焊点开裂失效案例进⾏分析,对问题产⽣的根源进⾏了定位,对焊点开裂的失效机理进⾏了分析,最后简要介绍了提⾼CQFP器件焊接可靠性的⼀些⼯艺措施。
关键词:CQFP;可靠性;失效分析中图分类号:TN6 ⽂献标识码:A ⽂章编号:1001-3474(2012)06-0347-04Failure Analysis for Solder Joint Cracking of CQFP DevicesZHANG Wei, SUN Shou-hong, SUN Hui, HAN Zhen-wei(Changchun Institute of Optics, Fine Mechanics and Physics, Chinese Academy of Sciences, Changchun 130033, China) Abstract: CQFP devices has been widely used in military and aerospace field due to its advantages of high reliability, but in actual situation, especially in temperature, mechanical solder joints under the conditions prone to fall off, pin breakage and other issues. Based on a typical case of solder joint cracking failure, analyze root cause of the problem, and finally some process measures to improve the reliability of CQFP have been introduced.Key words: CQFP; Reliability; Failure analysisDocument Code: A Article ID: 1001-3474(2012)06-0347-04陶瓷四⾯扁平封装器件CQFP(Ceramic Quad Flat Pack)是⼀种先进的器件封装形式,采⽤了陶瓷基板和镀⾦引线,如图1所⽰,具有很⾼的可靠性,⼴泛应⽤于军事和航空航天印制板组装领域[1,2]。
电阻焊常见缺陷及产生原因
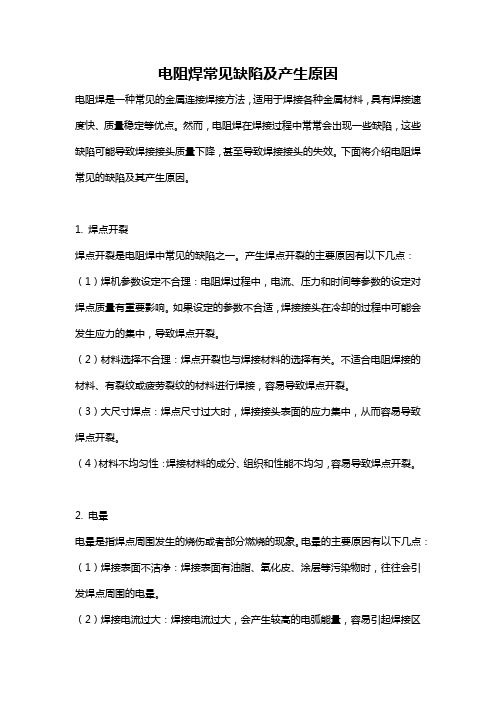
电阻焊常见缺陷及产生原因电阻焊是一种常见的金属连接焊接方法,适用于焊接各种金属材料,具有焊接速度快、质量稳定等优点。
然而,电阻焊在焊接过程中常常会出现一些缺陷,这些缺陷可能导致焊接接头质量下降,甚至导致焊接接头的失效。
下面将介绍电阻焊常见的缺陷及其产生原因。
1. 焊点开裂焊点开裂是电阻焊中常见的缺陷之一。
产生焊点开裂的主要原因有以下几点:(1)焊机参数设定不合理:电阻焊过程中,电流、压力和时间等参数的设定对焊点质量有重要影响。
如果设定的参数不合适,焊接接头在冷却的过程中可能会发生应力的集中,导致焊点开裂。
(2)材料选择不合理:焊点开裂也与焊接材料的选择有关。
不适合电阻焊接的材料、有裂纹或疲劳裂纹的材料进行焊接,容易导致焊点开裂。
(3)大尺寸焊点:焊点尺寸过大时,焊接接头表面的应力集中,从而容易导致焊点开裂。
(4)材料不均匀性:焊接材料的成分、组织和性能不均匀,容易导致焊点开裂。
2. 电晕电晕是指焊点周围发生的烧伤或者部分燃烧的现象。
电晕的主要原因有以下几点:(1)焊接表面不洁净:焊接表面有油脂、氧化皮、涂层等污染物时,往往会引发焊点周围的电晕。
(2)焊接电流过大:焊接电流过大,会产生较高的电弧能量,容易引起焊接区域局部温度过高,从而导致电晕的发生。
(3)焊接参数设定不合理:焊接过程中,电流、压力和时间等参数的设定不合理,也会导致电晕的发生。
3. 气孔气孔是指焊接接头中产生的孔洞状缺陷。
气孔的产生原因主要有以下几点:(1)焊接区域含有气体:焊接区域杂质、氧化物或者其他含气体的物质,会在焊接过程中释放出气体,进而产生气孔。
(2)焊接材料含水量高:焊接材料含有过多的水分,焊接过程中蒸发的水分会形成气泡,从而形成气孔。
(3)焊接区域氧气过量:焊接区域的氧气含量过高,氧气和金属之间的反应会产生气体,并形成气孔。
4. 金属飞溅金属飞溅是指焊接过程中,熔融金属在电极与焊件之间产生的喷溅现象。
金属飞溅的产生原因主要有以下几点:(1)电流过大:焊接电流过大,熔融金属的喷溅量会增加,从而导致金属飞溅的产生。
常见的点焊质量缺陷及原因
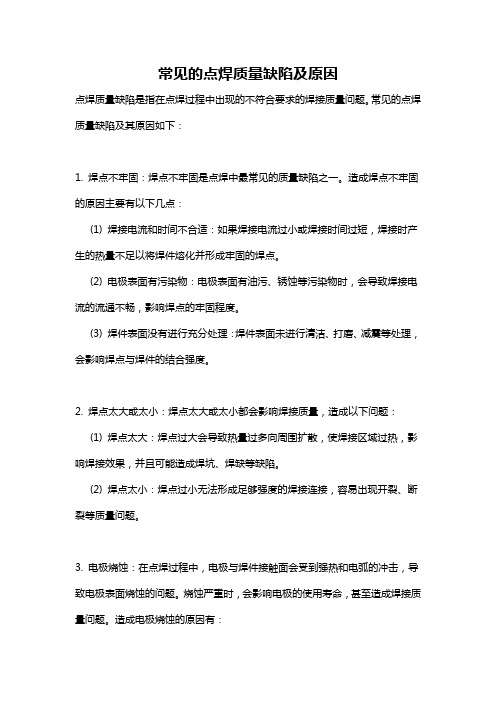
常见的点焊质量缺陷及原因点焊质量缺陷是指在点焊过程中出现的不符合要求的焊接质量问题。
常见的点焊质量缺陷及其原因如下:1. 焊点不牢固:焊点不牢固是点焊中最常见的质量缺陷之一。
造成焊点不牢固的原因主要有以下几点:(1) 焊接电流和时间不合适:如果焊接电流过小或焊接时间过短,焊接时产生的热量不足以将焊件熔化并形成牢固的焊点。
(2) 电极表面有污染物:电极表面有油污、锈蚀等污染物时,会导致焊接电流的流通不畅,影响焊点的牢固程度。
(3) 焊件表面没有进行充分处理:焊件表面未进行清洁、打磨、减震等处理,会影响焊点与焊件的结合强度。
2. 焊点太大或太小:焊点太大或太小都会影响焊接质量,造成以下问题:(1) 焊点太大:焊点过大会导致热量过多向周围扩散,使焊接区域过热,影响焊接效果,并且可能造成焊坑、焊缺等缺陷。
(2) 焊点太小:焊点过小无法形成足够强度的焊接连接,容易出现开裂、断裂等质量问题。
3. 电极烧蚀:在点焊过程中,电极与焊件接触面会受到强热和电弧的冲击,导致电极表面烧蚀的问题。
烧蚀严重时,会影响电极的使用寿命,甚至造成焊接质量问题。
造成电极烧蚀的原因有:(1) 电极材质选择不当:电极材质应根据焊件材质和焊接工艺参数选择合适的材料,否则容易导致电极烧蚀。
(2) 焊接电流过大:过大的焊接电流会使电极与焊件间产生较大的热量,电极表面无法承受,容易导致烧蚀。
4. 焊接过热:过热是指焊接过程中焊件局部温度过高,超过了焊接工艺要求。
过热会导致焊缝过深、焊缺、焊缝太宽等缺陷。
造成焊接过热的原因主要有:(1) 焊接电流过大:过大的焊接电流会使焊件受到较大的热量和电弧冲击,容易导致过热现象。
(2) 焊接时间过长:焊接时间过长,焊件得到的热量过多,容易造成过热。
5. 焊缺、错位、飞溅:焊缺、错位和飞溅等问题都会影响焊接质量,导致焊点无法完成预期的功能。
造成这些问题的原因主要有:(1) 材料不匹配:焊接的两个焊件材料不匹配,例如金属种类、厚度等差异较大,会导致焊缺和错位等问题。
最常见焊接缺陷并分析原因
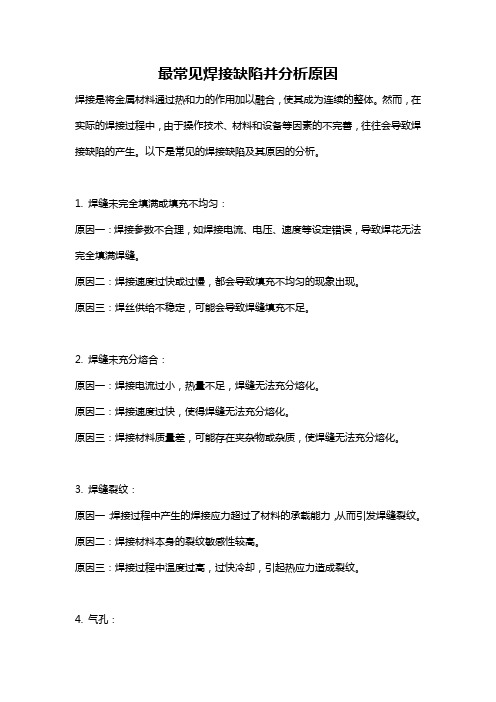
最常见焊接缺陷并分析原因焊接是将金属材料通过热和力的作用加以融合,使其成为连续的整体。
然而,在实际的焊接过程中,由于操作技术、材料和设备等因素的不完善,往往会导致焊接缺陷的产生。
以下是常见的焊接缺陷及其原因的分析。
1. 焊缝未完全填满或填充不均匀:原因一:焊接参数不合理,如焊接电流、电压、速度等设定错误,导致焊花无法完全填满焊缝。
原因二:焊接速度过快或过慢,都会导致填充不均匀的现象出现。
原因三:焊丝供给不稳定,可能会导致焊缝填充不足。
2. 焊缝未充分熔合:原因一:焊接电流过小,热量不足,焊缝无法充分熔化。
原因二:焊接速度过快,使得焊缝无法充分熔化。
原因三:焊接材料质量差,可能存在夹杂物或杂质,使焊缝无法充分熔化。
3. 焊缝裂纹:原因一:焊接过程中产生的焊接应力超过了材料的承载能力,从而引发焊缝裂纹。
原因二:焊接材料本身的裂纹敏感性较高。
原因三:焊接过程中温度过高,过快冷却,引起热应力造成裂纹。
4. 气孔:原因一:焊工操作不当,引入大量空气进入焊接区域。
原因二:焊接环境湿度过高,焊材含水量较高,蒸汽在焊接时形成气孔。
原因三:焊接电流过大,使得电解液膨胀并形成气孔。
5. 偏心焊缝:原因一:焊工操作不准确,在焊接过程中无法保持合适的焊接位置,导致焊缝偏移。
原因二:焊接设备的不准确性或不稳定性,可能导致焊缝位置不正确。
6. 焊接变形:原因一:在多道焊接中,没有采取适当的换向焊接方法,导致焊接变形。
原因二:焊接时温度过高,快速冷却会导致焊接变形。
原因三:焊接残余应力超过了材料的承载能力,导致焊接变形。
以上是焊接过程中常见的缺陷及其原因的分析,通过了解这些缺陷和原因,焊工可以采取相应的措施来减少和避免焊接缺陷的发生,从而提高焊接质量。
波峰焊锡裂的原因及对策

波峰焊锡裂的原因及对策
波峰焊锡裂是指在波峰焊接过程中,焊锡出现裂纹的现象。
这种问题可能会导致焊接质量下降,甚至影响产品的可靠性。
波峰焊锡裂的原因有很多,主要包括以下几个方面:
1. 温度过高,波峰焊过程中,如果焊接温度过高,会导致焊锡的熔点降低,容易造成焊锡裂纹。
这可能是由于焊接参数设置不当或者焊接时间过长导致的。
2. 焊接速度过快,焊接速度过快会导致焊接过程中焊锡的流动性不好,容易造成焊锡裂纹。
这可能是由于设备调整不当或者操作不规范导致的。
3. 金属表面处理不当,如果焊接前的基材表面存在氧化物、油污等杂质,会影响焊锡与基材的结合,容易造成焊锡裂纹。
4. 焊接材料问题,选用质量不合格的焊锡材料或者焊剂也可能导致焊锡裂纹的问题。
针对波峰焊锡裂的问题,可以采取一些对策来解决:
1. 合理设置焊接参数,根据实际情况合理设置焊接温度、速度等参数,确保焊接过程中温度和速度的控制在合适的范围内。
2. 加强表面处理,在焊接前对基材进行充分的清洁和处理,确保基材表面没有杂质,以提高焊锡与基材的结合性。
3. 选用优质材料,选择质量可靠的焊锡材料和焊剂,确保焊接材料的质量符合要求。
4. 定期维护设备,定期对波峰焊设备进行维护和保养,确保设备的正常运行和焊接质量。
5. 加强操作培训,对操作人员进行培训,提高其对波峰焊操作的规范性和技能水平,减少人为因素对焊接质量的影响。
综上所述,波峰焊锡裂的原因可能涉及多个方面,需要从焊接参数设置、基材处理、材料选用等多个方面综合考虑,并采取相应的对策来解决问题,以确保波峰焊接的质量和可靠性。
焊接件断裂的原因及预防措施

开展焊接件断裂的实验研究和 案例分析,积累更多的实际经 验和数据,为预防措施的制定 和实施提供更加可靠的支撑。
加强焊接结构的安全性和可靠 性研究,推动焊接技术的不断 创新和发展,为工业生产和工 程建设提供更加可靠和高效的 技术支持。
THANKS
谢谢您的观看
止裂纹的产生。
结构设计改进
01
02
03
优化焊缝设计
合理布置焊缝位置、数量 和尺寸,避免焊缝集中、 受力不均等问题。
加强薄弱部位
对结构中的薄弱部位进行 加强设计,提高焊接件的 承载能力。
考虑焊接变形
在结构设计时充分考虑焊 接变形的影响,采取相应 的补偿措施。
03
工程实例分析
工程实例一:某大型桥梁的焊接断裂问题
总结词
材料缺陷、结构设计不合理
详细描述
该大型桥梁在焊接过程中,由于材料存在缺陷或焊接工艺不当,导致焊接部位出 现微裂纹。在长期承受载荷的作用下,裂纹逐渐扩展,最终导致桥梁断裂。
工程实例二:某压力容器的焊接开裂问题
总结词
焊接工艺不当、使用环境恶劣
详细描述
该压力容器在焊接过程中,由于焊接工艺参数设置不当或焊接后热处理不足,导致焊接部位存在残余应力。在长 期承受压力和腐蚀介质的作用下,焊接部位出现开裂。
焊接件断裂的原因及预防措 施
汇报人: 20 • 焊接件断裂的预防措施 • 工程实例分析 • 结论与展望
01
焊接件断裂的原因
材料因素
母材缺陷
母材中存在的夹渣、气孔、裂纹 等缺陷会导致焊接接头强度下降 ,增加断裂的风险。
焊缝金属组织不均
焊缝金属组织中存在大量脆性相 或夹杂物,导致焊缝金属的韧性 下降,容易发生脆性断裂。
焊接裂纹产生原因
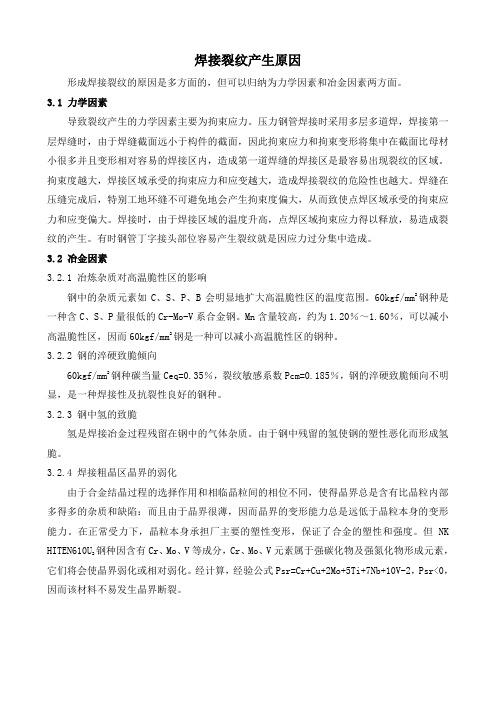
焊接裂纹产生原因形成焊接裂纹的原因是多方面的,但可以归纳为力学因素和冶金因素两方面。
3.1 力学因素导致裂纹产生的力学因素主要为拘束应力。
压力钢管焊接时采用多层多道焊,焊接第一层焊缝时,由于焊缝截面远小于构件的截面,因此拘束应力和拘束变形将集中在截面比母材小很多并且变形相对容易的焊接区内,造成第一道焊缝的焊接区是最容易出现裂纹的区域。
拘束度越大,焊接区域承受的拘束应力和应变越大,造成焊接裂纹的危险性也越大。
焊缝在压缝完成后,特别工地环缝不可避免地会产生拘束度偏大,从而致使点焊区域承受的拘束应力和应变偏大。
焊接时,由于焊接区域的温度升高,点焊区域拘束应力得以释放,易造成裂纹的产生。
有时钢管丁字接头部位容易产生裂纹就是因应力过分集中造成。
3.2 冶金因素3.2.1 冶炼杂质对高温脆性区的影响钢中的杂质元素如C、S、P、B会明显地扩大高温脆性区的温度范围。
60kgf/mm2钢种是一种含C、S、P量很低的Cr-Mo-V系合金钢。
Mn含量较高,约为1.20%~1.60%,可以减小高温脆性区,因而60kgf/mm2钢是一种可以减小高温脆性区的钢种。
3.2.2 钢的淬硬致脆倾向60kgf/mm2钢种碳当量Ceq=0.35%,裂纹敏感系数Pcm=0.185%,钢的淬硬致脆倾向不明显,是一种焊接性及抗裂性良好的钢种。
3.2.3 钢中氢的致脆氢是焊接冶金过程残留在钢中的气体杂质。
由于钢中残留的氢使钢的塑性恶化而形成氢脆。
3.2.4 焊接粗晶区晶界的弱化由于合金结晶过程的选择作用和相临晶粒间的相位不同,使得晶界总是含有比晶粒内部多得多的杂质和缺陷:而且由于晶界很薄,因而晶界的变形能力总是远低于晶粒本身的变形能力。
在正常受力下,晶粒本身承担厂主要的塑性变形,保证了合金的塑性和强度。
但NK 钢种因含有Cr、Mo、V等成分,Cr、Mo、V元素属于强碳化物及强氮化物形成元素,HITEN610U2它们将会使晶界弱化或相对弱化。
焊接裂纹产生原因及防治措施

焊接裂纹产生原因及防治措施焊接裂纹是焊接过程中常见的缺陷之一,它会降低焊接接头的强度和密封性,严重影响焊接质量。
本文将从焊接裂纹产生的原因和防治措施两个方面进行探讨。
一、焊接裂纹产生的原因1. 焊接应力过大:焊接过程中,由于材料的热膨胀和收缩,会产生焊接应力。
如果应力过大,就容易引起焊接裂纹的产生。
2. 材料的选择不当:焊接材料的选择不当,例如选择了冷脆性较大的材料,容易在焊接过程中产生裂纹。
3. 焊接参数设置不合理:焊接参数的设置是影响焊接质量的关键因素之一。
如果焊接电流过大或过小,焊接速度过快或过慢,都会导致焊接裂纹的产生。
4. 焊接时的工艺操作不当:焊接操作不规范也是焊接裂纹产生的原因之一。
例如焊接时没有进行预热、焊接过程中没有使用适当的焊接顺序等。
5. 焊接材料的质量问题:如果焊接材料本身存在缺陷,例如含有太多的杂质或气孔,也容易导致焊接裂纹的产生。
二、焊接裂纹的防治措施1. 合理控制焊接应力:通过合理的焊接参数设置和焊接顺序安排,可以减小焊接应力的产生。
此外,还可以采用局部预热、焊后热处理等方法来降低焊接应力。
2. 选择合适的焊接材料:在进行焊接工艺设计时,应根据具体情况选择合适的焊接材料,避免选择冷脆性较大的材料。
此外,还要确保焊接材料的质量,避免使用存在缺陷的材料。
3. 合理设置焊接参数:在进行焊接操作时,要根据具体情况合理设置焊接参数,如焊接电流、焊接速度等。
可以通过试验和经验总结来确定最佳的焊接参数。
4. 规范焊接操作:进行焊接操作时,要严格按照焊接工艺要求进行操作,如预热、焊接顺序等。
同时,要保证焊接设备的正常运行和维护,避免因设备故障导致焊接裂纹的产生。
5. 加强焊后检测和质量控制:焊接完成后,要进行全面的焊后检测,发现裂纹及时进行修复。
同时,要加强质量控制,确保焊接质量符合要求。
焊接裂纹的产生原因较为复杂,涉及材料、焊接参数、工艺操作等多个方面。
为了防止焊接裂纹的产生,需要从多个方面进行控制和改进,提高焊接质量。
焊接裂纹产生原因及防治

焊接裂纹产生原因及防治焊接裂纹是在焊接过程中或焊接完成后在焊缝或母材中产生的开裂缺陷。
焊接裂纹的产生原因多种多样,主要包括以下几个方面:1.焊接过程中的温度应力:焊接时,因为焊接区域发生了局部加热和冷却,导致焊接接头中的温度差异,从而造成了焊接区域的应力。
如果这种应力超过了焊接材料的强度极限,就会产生裂纹。
2.冶金因素:焊接过程中,由于温度升高,焊接材料和母材之间发生相互作用,形成了互溶区。
如果溶液比较富含低熔点的物质,就会导致物质从高温区流向低温区,从而增大了焊接接头的收缩量,引起裂纹。
3.废气、含氧量过高:当焊接环境中的氧气含量过高时,焊接时会发生氧化反应,在焊接接头中产生大量的氧化物,增大了焊接接头的收缩量,从而导致了裂纹的产生。
4.焊接过程中的振动:焊接过程中的振动会使焊接接头中的晶粒发生变化,从而影响了焊接材料的性能,使其发生了裂纹。
针对焊接裂纹的防治措施主要包括以下几个方面:1.提高焊接工艺:合理选择焊接工艺参数,如焊接电流、焊接电压和焊接速度等,以控制焊接过程中的温度和应力。
2.控制焊接过程中的温度升降速度:控制焊接过程中的升温速度和冷却速度,以避免焊接接头产生过大的应力。
3.控制焊接环境:减少焊接环境中的含氧量,避免产生氧化反应和氧化物。
4.优化焊接材料:合理选择焊接材料,根据焊接接头的要求选择合适的材料,以提高焊接接头的性能。
5.加强材料的前处理:在焊接前进行必要的预处理工作,如去污、除锈、磷化等,以提高焊接接头的质量。
综上所述,焊接裂纹的产生原因多种多样,需要综合考虑多个方面的因素来进行防治。
通过合理选择焊接工艺参数、控制焊接过程中的温度和应力、控制焊接环境、优化焊接材料以及加强材料的前处理等措施,可以有效预防和防治焊接裂纹的产生,提高焊接接头的质量。
焊接不良现象分析

一、标准焊点的要求: 1可靠的电气连接2、足够的机械强度3、光洁整齐的外观-股岸料量均不趕岀3 0^3!界曲遅媳的捍点巻閒疑洁用如秦月理甥的埠点表面光清昭如弯月电子元件标准焊点(1)不良术语短路:不在同一条线路的两个或以上的点相连并处于导通状态。
起皮:线路铜箔因过分受热或外力作用而脱离线路底板。
少锡:焊盘不完全,或焊点不呈波峰状饱满。
假焊:焊锡表面看是波峰状饱满,显光泽,但实质上并未与线路铜箔相熔化或未完全熔化在焊接不良现象分析R好的期豪这里也構竜月閒奩月閒夫*C 1 5* 和旺龙祕厦理啰的輝点衰窗比洁带剜曜月建想的理点老閒光洁形效葺月线路铜箔上。
脱焊:元件脚脱离焊点。
虚焊:焊锡在引线部与元件脱离。
角焊:因过分加热使助焊剂丢失多引起焊锡拉尖现象。
拉尖:因助焊剂丢失而使焊点不圆滑,显得无光泽。
元件脚长:元件脚露出板底的长度超过 1.5-2.0mm 。
盲点:元件脚未插出板面。
(2)不良现象形成原因,显现和改善措施1、加热时间问题(1)加热时间不足:会使焊料不能充分浸润焊件而形成松香夹渣而虚焊。
(2)加热时间过长(过量加热),除有可能造成元器件损坏以外,还有如下危害和外部特征。
A、焊点外观变差。
如果焊锡已经浸润焊件以后还继续进行过量的加热,将使助焊剂全部挥发完,造成熔态焊锡过热。
当烙铁离开时容易拉出锡尖,同时焊点表面发白,出现粗糙颗粒,失去光泽。
B、高温造成所加松香助焊剂的分解碳化。
松香一般在210度开始分解,不仅失去助焊剂的作用,而且造成焊点夹渣而形成缺陷。
如果在焊接中发现松香发黑,肯定是加热时间过长所致。
C、过量的受热会破坏印制板上铜箔的粘合层,导致铜箔焊盘的剥落。
因此,在适当的加热时间里,准确掌握加热火候是优质焊接的关键。
(3)不良焊点成因及隐患1、松香残留:形成助焊剂的薄膜。
隐患:造成电气上的接触不良。
原因分析:烙铁功率不足焊接时间短引线或端子不干净。
2、虚焊:表面粗糙,没有光泽。
隐患:减少了焊点的机械强度,降低产品寿命。
焊点开裂不良失效分析–电镀在线
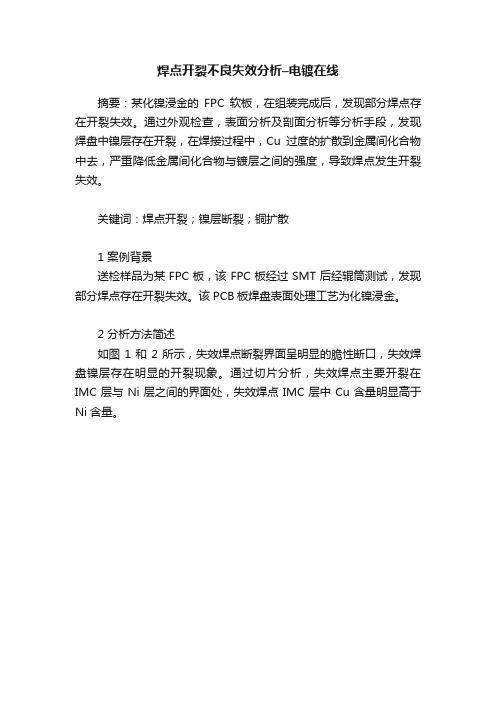
焊点开裂不良失效分析–电镀在线
摘要:某化镍浸金的FPC软板,在组装完成后,发现部分焊点存在开裂失效。
通过外观检查,表面分析及剖面分析等分析手段,发现焊盘中镍层存在开裂,在焊接过程中,Cu过度的扩散到金属间化合物中去,严重降低金属间化合物与镀层之间的强度,导致焊点发生开裂失效。
关键词:焊点开裂;镍层断裂;铜扩散
1 案例背景
送检样品为某FPC板,该FPC板经过SMT后经辊筒测试,发现部分焊点存在开裂失效。
该PCB板焊盘表面处理工艺为化镍浸金。
2 分析方法简述
如图1和2所示,失效焊点断裂界面呈明显的脆性断口,失效焊盘镍层存在明显的开裂现象。
通过切片分析,失效焊点主要开裂在IMC层与Ni层之间的界面处,失效焊点IMC层中Cu含量明显高于Ni含量。
3 分析与讨论 该焊点失效界面为典型的铜扩散现象,正常的ENIG 焊盘与焊料之间形成Ni3Sn4的IMC 层,Ni 层作为阻挡层,阻挡Cu 向焊料扩散,亦或形成少量的(Cu ,Ni )6Sn5的三元合金,当Ni 层发生开裂时,
Cu会沿裂缝向焊料急剧扩散,当Cu大量异常的向锡镍合金扩散时,必然改变IMC的结构和物理性能,其机械性能弱化,脆性增加而与Ni 层的结合力减弱,在受到外力作用下,易发生开裂失效现象。
SMT的高温和长时间回流焊及焊盘的Ni层开裂均有助于Cu扩散现象的发生。
本案焊点失效的主要原因为在SMT前,焊盘的Ni镀层存在开裂,致使在焊接过程中Cu向IMC层大量扩散,改变了IMC层的结构和物料特性,致使界面机械性能严重下降。
内容来源:美信检测作者:邓胜良。
PCBA上BGA焊点失效失效分析
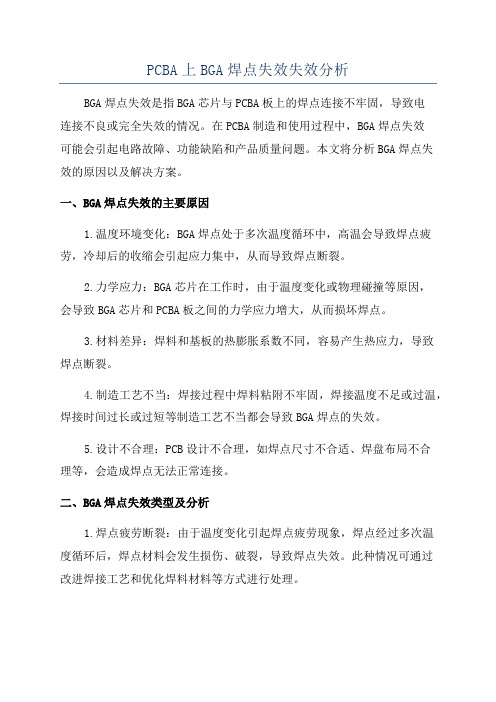
PCBA上BGA焊点失效失效分析BGA焊点失效是指BGA芯片与PCBA板上的焊点连接不牢固,导致电连接不良或完全失效的情况。
在PCBA制造和使用过程中,BGA焊点失效可能会引起电路故障、功能缺陷和产品质量问题。
本文将分析BGA焊点失效的原因以及解决方案。
一、BGA焊点失效的主要原因1.温度环境变化:BGA焊点处于多次温度循环中,高温会导致焊点疲劳,冷却后的收缩会引起应力集中,从而导致焊点断裂。
2.力学应力:BGA芯片在工作时,由于温度变化或物理碰撞等原因,会导致BGA芯片和PCBA板之间的力学应力增大,从而损坏焊点。
3.材料差异:焊料和基板的热膨胀系数不同,容易产生热应力,导致焊点断裂。
4.制造工艺不当:焊接过程中焊料粘附不牢固,焊接温度不足或过温,焊接时间过长或过短等制造工艺不当都会导致BGA焊点的失效。
5.设计不合理:PCB设计不合理,如焊点尺寸不合适、焊盘布局不合理等,会造成焊点无法正常连接。
二、BGA焊点失效类型及分析1.焊点疲劳断裂:由于温度变化引起焊点疲劳现象,焊点经过多次温度循环后,焊点材料会发生损伤、破裂,导致焊点失效。
此种情况可通过改进焊接工艺和优化焊料材料等方式进行处理。
2.焊点裂纹:焊点的高温冷却过程中,未能得到充分的冷却时间,导致焊点出现裂纹,影响焊接质量。
此种情况可通过控制焊接温度和冷却速度等方式进行处理。
3.焊点剥离:焊点粘附不牢固,焊盘与焊点之间会出现空隙,从而导致焊点剥离。
此种情况可通过改进焊接工艺和优化焊料粘附性能等方式进行处理。
4.焊点内部孔隙:焊点内部可能存在孔隙或气泡,导致焊点的结构不均匀,容易破裂。
此种情况可通过改进焊接工艺和优化焊料材料等方式进行处理。
5.焊点受污染:焊接过程中可能会受到污染物的侵入,导致焊点质量下降。
此种情况可通过增强焊接工艺的洁净度和环境控制等方式进行处理。
三、BGA焊点失效的解决方案1.优化焊接工艺:通过调整焊接温度、时间和压力等参数,保证焊接的稳定性和可靠性。
烧结银焊点常见失效模式
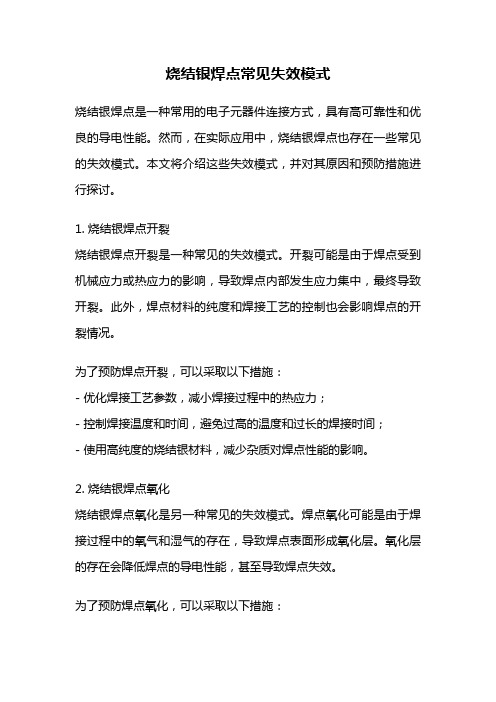
烧结银焊点常见失效模式烧结银焊点是一种常用的电子元器件连接方式,具有高可靠性和优良的导电性能。
然而,在实际应用中,烧结银焊点也存在一些常见的失效模式。
本文将介绍这些失效模式,并对其原因和预防措施进行探讨。
1. 烧结银焊点开裂烧结银焊点开裂是一种常见的失效模式。
开裂可能是由于焊点受到机械应力或热应力的影响,导致焊点内部发生应力集中,最终导致开裂。
此外,焊点材料的纯度和焊接工艺的控制也会影响焊点的开裂情况。
为了预防焊点开裂,可以采取以下措施:- 优化焊接工艺参数,减小焊接过程中的热应力;- 控制焊接温度和时间,避免过高的温度和过长的焊接时间;- 使用高纯度的烧结银材料,减少杂质对焊点性能的影响。
2. 烧结银焊点氧化烧结银焊点氧化是另一种常见的失效模式。
焊点氧化可能是由于焊接过程中的氧气和湿气的存在,导致焊点表面形成氧化层。
氧化层的存在会降低焊点的导电性能,甚至导致焊点失效。
为了预防焊点氧化,可以采取以下措施:- 在焊接过程中,控制焊接环境的氧气和湿气含量;- 使用氮气等惰性气体进行保护焊接,减少氧气的接触;- 使用防氧化剂或涂覆保护层,防止焊点表面氧化。
3. 烧结银焊点脱落烧结银焊点脱落是焊点失效的严重情况之一。
焊点脱落可能是由于焊接工艺不当,焊点与基材之间的粘结力不足,或者焊点材料的质量问题所致。
为了预防焊点脱落,可以采取以下措施:- 优化焊接工艺参数,确保焊点与基材之间的粘结力达到要求;- 使用适当的焊接材料,确保焊点材料的质量;- 进行焊点可靠性测试,及时发现并修复焊点脱落的问题。
总结起来,烧结银焊点常见的失效模式包括焊点开裂、焊点氧化和焊点脱落。
这些失效模式的发生可能与焊接工艺参数、焊接材料的质量以及焊接环境等因素有关。
为了提高焊点的可靠性,我们应该优化焊接工艺,选择高质量的焊接材料,并控制焊接环境的氧气和湿气含量。
只有这样,才能确保烧结银焊点在电子元器件连接中发挥出最佳的性能。
插装元器件引脚焊点开裂失效分析与控制

插装元器件引脚焊点开裂失效分析与控制随着我国航天工业的发展,宇航用元器件的电子装联密度不断增大,同时对装联可靠性的要求也不断提高。
在电子装联产品中,部分封装元器件通过引脚与焊盘或导线焊接,通过焊点实现电气与机械连接,因而焊接质量直接决定了电子产品的可靠性。
对于焊点存在缺陷的产品,装联后初测时焊点可维持连接状态,产品功能正常,但在后续使用中可能会发生缺陷劣化甚至焊点失效的风险,因而需要对焊点进行质量检查,必要时需要根据使用需求进行考核试验。
航天产品在生产与使用过程中,会经历温度交变、外力振动、应力冲击等多种力热环境,元器件引脚焊点会随产品经受应力,带有裂纹缺陷的焊点作为应力集中区与结构薄弱点,经常发生失效。
当元器件引脚焊点存在引脚焊接性差或界面金脆等问题时,虽电气性能正常,但焊点内可能已萌生裂纹源,在后续的宇航环境下使用时,存在焊点裂纹扩展甚至断裂的安全隐患。
针对存在部分产品初测性能合格,但经历宇航级环境考核试验后发生了焊点失效的情况,本文选取了JW117稳压器器件引脚通孔插装焊点失效案例进行分析。
通过对未进行考核试验的同批次初装产品的引脚焊点进行形貌观察、金相与成分检验,对元器件引脚焊点失效的原因进行了分析,并结合失效机理,为提升元器件引脚的焊接可靠性提出了针对性的改进建议。
1. 故障描述某型号元器件选用了某公司生产的JW117三端稳压器,采用通孔插装焊接方式将三只引脚焊于PCB板上。
产品经历力学振动和温度循环试验后,器件的一只引脚发生信号时断时续的失效情况,检查发现失效焊点的焊料与引脚交界处存在贯穿整个焊点的裂纹。
上述的失效产品在初装后测试时信号通信正常,但经历宇航级环境考核试验后,发生了器件引脚焊点失效现象。
为查明上述元器件引脚焊点开裂原因,对未进行考核试验的同批次产品的元器件引脚焊点进行了复查。
检查表明,部分元器件的引脚焊点存在焊接不良缺陷,此类焊点在力热试验过程中存在缺陷扩展并导致焊点开裂失效的风险。
- 1、下载文档前请自行甄别文档内容的完整性,平台不提供额外的编辑、内容补充、找答案等附加服务。
- 2、"仅部分预览"的文档,不可在线预览部分如存在完整性等问题,可反馈申请退款(可完整预览的文档不适用该条件!)。
- 3、如文档侵犯您的权益,请联系客服反馈,我们会尽快为您处理(人工客服工作时间:9:00-18:30)。
一站式的材料检测、分析与技术咨询服务焊点开裂不良因素是什么?焊点失效分析
邓胜良
(深圳市美信检测技术股份有限公司,深圳宝安,518108)
摘要:某化镍浸金的FPC软板,在组装完成后,发现部分焊点存在开裂失效。
通过外观检查,表面分析及剖面分析等分析手段,发现焊盘中镍层存在开裂,在焊接过程中,Cu过度的扩散到金属间化合物中去,严重降低金属间化合物与镀层之间的强度,导致焊点发生开裂失效。
关键词:焊点开裂;镍层断裂;铜扩散
1 案例背景
送检样品为某FPC板,该FPC板经过SMT后经辊筒测试,发现部分焊点存在开裂失效。
该PCB板焊盘表面处理工艺为化镍浸金。
2 分析方法简述
如图1和2所示,失效焊点断裂界面呈明显的脆性断口,失效焊盘镍层存在明显的开裂现象。
通过切片分析,失效焊点主要开裂在IMC层与Ni层之间的界面处,失效焊点IMC层中Cu含量明显高于Ni含量。
一站式的材料检测、分析与技术咨询服务
图1 失效样品外观图片
图2 失效样品SEM图片
图3 失效焊点的切片图
一站式的材料检测、分析与技术咨询服务
表1. NG-3焊点切片EDS测试结果(Wt%)
3 分析与讨论
该焊点失效界面为典型的铜扩散现象,正常的ENIG焊盘与焊料之间形成Ni3Sn4的IMC 层,Ni层作为阻挡层,阻挡Cu向焊料扩散,亦或形成少量的(Cu,Ni)6Sn5的三元合金,当Ni层发生开裂时,Cu会沿裂缝向焊料急剧扩散,当Cu大量异常的向锡镍合金扩散时,必然改变IMC的结构和物理性能,其机械性能弱化,脆性增加而与Ni层的结合力减弱,在受到外力作用下,易发生开裂失效现象。
SMT的高温和长时间回流焊及焊盘的Ni层开裂均有助于Cu扩散现象的发生。
本案焊点失效的主要原因为在SMT前,焊盘的Ni镀层存在开裂,致使在焊接过程中Cu 向IMC层大量扩散,改变了IMC层的结构和物料特性,致使界面机械性能严重下降。