Error-proofing防错培训
防误防错poka yoke

防误防错poka yoke百科名片:POKA-YOKE意为“防误防错”,亦即Error & Mistake Proofing。
日本的质量管理专家、著名的丰田生产体系创建人新江滋生(Shingeo Shingo)先生根据其长期从事现场质量改进的丰富经验,首创了POKA-YOKE的概念,并将其发展成为用以获得零缺陷,最终免除质量检验的工具基本理念POKA-YOKE的基本理念主要有如下:⑴不允许哪怕一点点缺陷产品出现,要想成为世界的企业,不仅在观念上,而且必须在实际上达到“0”缺陷。
⑵⑵生产现场是一个复杂的环境,每一天的每一件事都可能出现,poka yoke书籍差错导致缺陷,缺陷导致顾客不满和资源浪费。
⑶我们不可能消除差错,但是必须及时发现和立即纠正,防止差错形成缺陷。
编辑本段基本概念剖析防误- 针对产品及过程设计出一种潜在的失效或导致失效的机理- 错误不可能发生- 前瞻性的- 预防防错- 做出改变,帮助操作人员减少或消除错误检(缺陷)- 防止错误在下游工序继续- 反应性的- 探测防误比防错更高级,更有效,例如十字路口,要避免南北向行驶的车辆与东西向行驶的车辆相撞,有两种办法,一是设置红绿灯,二是建立交桥。
但是设置了红绿灯并不能完全避免南北向行驶的车辆与东西向行驶的车辆相撞,因为有很多的司机会违规驾驶,红绿灯只能起到告警作用,这是防错。
但是如果建造了立交桥,就能完全避免相撞,这就是防误。
POKA YOKE 防错POKA YOKE防错术语过程设计防错产品设计防错零缺陷和POKA YOKE防错FMEA 和防错POKA YOKE实施POKA YOKE防错流程错误的种类人的错误的起因POKA YOKE防错级别和种类过程设计防错案例产品设计防错案例检验中的防错案例POKA YOKE防错技术的分类POKA YOKE防错探测技术的分类编辑本段基本原则消除(Elimination):将可能错误消除在过程和产品被重新设计的过程中;替代(Replacement):是进入更可靠的过程的一个变更;简单化(Facilitation):将过程运行变的更简单化,也更可靠;检测(Detection):使错误在下一步操作前被发现;缓和(Mitigation):是将错误的影响降低到最低。
约翰迪尔防差错教程_Error_Proofing_Presentation

Agenda
Morning session • How Error Proofing supports Lean • Error Proofing as Part of Visual Factory • What is Error Proofing • Hierarchy of Error Proofing Techniques • Types of Defects Afternoon Session • Error Proofing Examples • Red Flag Conditions • Defects vs. Errors • 7 Step Process Chartclass exercise • Levels of Prevention • Breakout Sessions
9
F
Prevent Abnormalities (Error-Proofing)
E Stop Abnormalities
Visual Factory Pyramid
(Prevent defects from moving on)
D
Warn about Abnormalities (Build in alarms) Build Standards into the Workplace Share Standards at the Site Share Information
Error Proofing:
7
Lean, Visual Factory & Error Proofing
• How does is all fit together? – Lean evolves in phases – Each phase builds upon the previous Lean Manufacturing Visual Factory Standardized Work Team Building Root Cause Analysis Quick Changeover TPM
防错法是由日本管理专家新乡重夫最早提出,该方法又名

防错法一、防错法1.防错法的概念防错法(Error Proofing或日语Poka-Yoke)是由日本管理专家新乡重夫(ShigeoShingo)最早提出的。
在日语中,Yoke是防止的意思,Poka是疏忽错误之意。
防错法意在过程差错发生之前即加以防止,是一种在生产过程中采用自动作用、报警、标识、分类等有效手段,使作业人员减少或避免产生差错的方法。
其主要目的是预防生产过程中可能出现的差错,并避免由于差错而产生的质量问题。
防错法又称愚巧法、防呆法,其义即是防止呆笨的人做错事,英文为Fool Proof,亦即连愚笨的人也不会做错事的设计方法,故又称为愚巧法。
狭义:如何设计一个东西,使错误绝不会发生。
广义:如何设计一个东西,使错误发生的机会减至最低限度。
因此,更具体地说,防呆法是:具有即使有人为疏忽也不会发生错误的构造,不需要注意力;具有外行人来做也不会错的构造,不需要经验与直觉;具有不管是谁或在何时工作都不会出差错的构造,不需要专门知识与高度的技能。
2.防错法的作用在产品和过程设计、生产制造等过程中运用防错手段,具有以下方面的作用:(1)第一次把事情做好,减少工作中的差错。
因为防错法采用一系列方法/工具以防止差错的发生,某结果即为第一次即将事情做好,防止产生差错。
(2)提升产品质量,同时减少由于检查而导致的浪费。
防错法直接结果就是产品质量的提高。
与靠检查来保证质量相比,防错法是从预防角度出发所采取的预防措施;而检查不能防止缺陷的产生,检查发现的缺陷只能去纠正。
这是一种浪费,防错法消除了这种浪费。
(3)消除返工及其引起的浪费。
防错法能提升产品质量,消除缺陷,这会导致返工次数的削减,由于返工所致的时间和资源浪费便得以消除。
3.现代防错的理念在生产和工作中出现的各种不合格,几乎都是由各种差错引起的,包括主观差错和客观差错。
主观差错是指由于操作人员失误所造成的差错,客观差错主要是人们无法控制或难以控制的随机因素所导致的过程异常或差错。
防错法培训教材
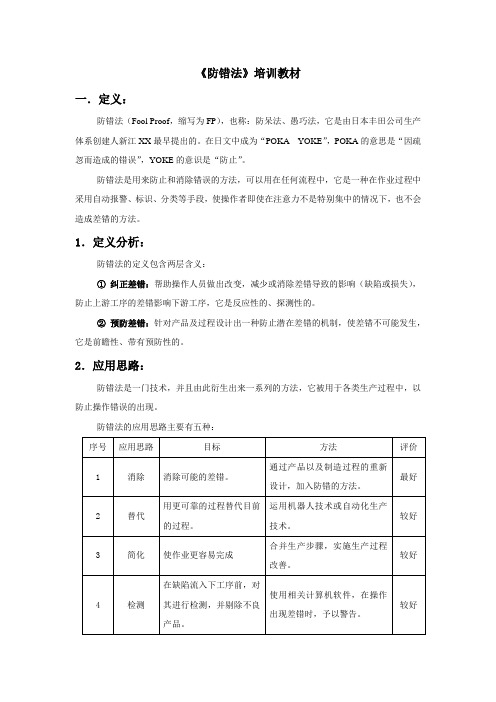
《防错法》培训教材
一.定义:
防错法(Fool Proof,缩写为FP),也称:防呆法、愚巧法,它是由日本丰田公司生产体系创建人新江XX最早提出的。
在日文中成为“POKA YOKE”,POKA的意思是“因疏忽而造成的错误”,YOKE的意识是“防止”。
防错法是用来防止和消除错误的方法,可以用在任何流程中,它是一种在作业过程中采用自动报警、标识、分类等手段,使操作者即使在注意力不是特别集中的情况下,也不会造成差错的方法。
1.定义分析:
防错法的定义包含两层含义:
①纠正差错:帮助操作人员做出改变,减少或消除差错导致的影响(缺陷或损失),防止上游工序的差错影响下游工序,它是反应性的、探测性的。
②预防差错:针对产品及过程设计出一种防止潜在差错的机制,使差错不可能发生,它是前瞻性、带有预防性的。
2.应用思路:
防错法是一门技术,并且由此衍生出来一系列的方法,它被用于各类生产过程中,以防止操作错误的出现。
防错法的应用思路主要有五种:。
防错技术(工业工程Error Proofing)

防呆的六步法
第1步:识别和描述
详细识别和描述缺陷/红牌条件。出现缺陷后,考察 缺陷的历史。为明确责任,指派一位团队队员跟踪 缺陷/红牌条件。
第2步:确定根本原因 进行因果图分析以评估根本原因。确定根本原因对 应用防错技术以消除缺陷/红旗是至关重要的。 第3步:评审现行标准程序 对发生缺陷的操作的每一步骤文件化。防错的机会 将基于对程序的仔细研究。
Error Proofing 防呆法
红牌
制造过程中通常会 引致错误的条件
*
2
防呆:红牌条件
下述的常见红牌条件能引致生产错误
1. 调整
工人必须对部件或设备作出调整以完成过程的工序
2. 工装和工装更换
易损工装在生产中的使用和/或生产过程中工装的更换
3. 尺寸/规范/关键条件
要求使用测量装置以将部件对位的操作,或要求操作 在指定的关键条件下执行(如温度、压力、速度等)
反向相似或相同物件的制造或装配操作
9. 不对称
操作所使用的部件、工具或夹具的相反方向看起来 完全相同但尺寸、形状或相对位置不同
10. 快速重复
要求重复实施相同的操作的过程
防呆:红牌条件
11. 很高/极高的数量
要求在时间的压力下快速重复的执行任务的过程。
12. 环境条件 工作地内部或周围的物理环境能影响质量或工艺。
Example : 过程中部件可能上下颠倒。滑槽 中安装的检查点可自动移开颠倒 部件。检查点有切口使颠倒部件 落入下方的转送盒中。方向正确 的部件可自由通过。结果是送到 下一位置的部件方向正确。
upside down
right side up
notch
防呆:防错装置的类型
制动器/门
防错措施Error Proofing
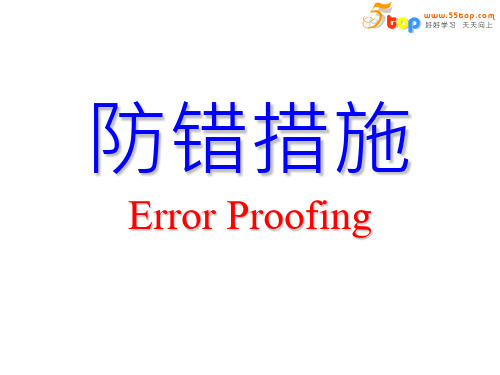
自動測試裝置
操作員
傳遞到下游 裝配操作合格的零件 不良品 料籠
合格/不合格 旋轉桌 指示燈
汽车音响检视站-改善后
從上游操作而來 未測試的電路板
旋轉桌 操作員 自動測試裝置 傳遞到下游 裝配操作合格的零件
滑槽 轉向板
不良品 料籠
防错装置案例二 输送侦测滑道
制程中导致不良的情况
2. 意义: •是一种想法,一种工具。 •必须配合实地、实物的状况,寻出最佳的 具体做法,发挥效果。
防错措施概述
?3.目的: •减少各种作业失误(负面损失),增加许多 正面的效益─提高工作质量及产品质量。 4. 防错措施的好处: •加强作业的标准程序与顺序 •当错误或不良产生时,会发出警告讯号或 停线。 •消除会导致错误动作的选择。
来自自动焊接 导槽 遗漏的轴
快速重製
正确焊接
下一制程
输送(侦测)滑道
焊接后部品
B
滑道
檢測臂
修補部 品櫃
至下一 个制程
檢測臂 滑道
未焊接 的底座
良品
防错装置范例三
制程中导致不良的情况
尺寸/規格/ 臨界條件
每个洞都是正确的 深度吗?
防错装置范例四 模板
钮扣定位治具
防错装置范例五 感应装置
防错装置范例五 感应装置
防错法制衡不良
• 您在执行防错法之前需要完全了解错误与不良 之不同之界定
• 错误之发生是因设计或制造之工程与规格之间 变异。例如错误产生是因为作业未依照制程标 准及质量系统规范作业造成,错误可能因机器
或作业人员发生在制造过程中。
• 不良的产生是任何变异的结果,不论是部品或 产品之规格变异都导致内外部顾客之不满。例 如部品不良造成不能装配之问题。 • 虽然所有的不良是错误的产生,但所有的错误 不一定都会产生不良,因此只要防止错误,不 良就不致于产生。
防错讲义

1% Defect Rate废 品率 1%
1% Defect Rate废品率1%
1% Defect Rate废 品率 1%
1% Defect Rate废品率1%
防错技术
防错态度
q 人会、并且将犯疏忽性错误! q 如果一人犯错-任何人都会 q 错误出厂,一个也多! q 错误能被消除,并且为了我们具有竞争力必须 被消除!
SGM Confidential
PDF 文件使用 "pdfFactory Pro" 试用版本创建
防错技术
一次完成99.9%的事意味着…
§ § § § § § § § § 1000 PPM 每月一小时的不安全饮水 每天在上海浦东机场的两次不安全着陆 每小时16,000 件邮件丢失 每年20,000个错误的药方 每周500次不正确的外科手术 每天50个新生儿被医生掉在地上 每小时22,000个支票/付款被从错误的帐户中扣除 每年每人32,000次遗失心跳
SGM Confidential
PDF 文件使用 "pdfFactory Pro" 试用版本创建
防错技术
过去,为了防止这些差错,在作业现场一般会制定许多规 章制度并采用纪律约束,而当差错发生时,传统的做法是 批评、指责、教育直至处罚。 事实上,很多工厂的经验表明,上述措施只能防范一部分 主观的差错,而当生产节拍越来越快,作业重复性越来越 强时,工人在长时间劳动后,注意力分散、反应减缓、麻 痹疏忽等,往往不可避免。
INEVITABLE ! 人的错误是无法避免的!
n ERRORS CAN BE
ELIMINATED! 错误是可以消除的!
SGM Confidential
PDF 文件使用 "pdfFactory Pro" 试用版本创建
防错法ppt课件

行动 (20%的机会): 在线控制 持续改进
总的来说, Six Sigma 和防错法都是提高品质的有效工具
Page 15
防错法的七个步骤
步骤1: 预先评价和顺序筛选 步骤2: 定义和描述错误,过错 步骤3: 决定问题的根本原因 步骤4: 回顾当前的标准流程 步骤5: 找出和当前流程不一致的偏差 步骤6: 决定所采用的防错法工具 步骤7: 创建方法并判定他的有效性
Page 11
日常生活中的防错法
这个每天生活中的动作可能的错误是什么? 它使用了什么防错法? 怎样进一步防错?
Page 12
日常生活中的防错法
这个每天生活中的动作可能的错误是什么? 它使用了什么防错法? 怎样进一步防错?
Page 13
日常生活中的防错法
这个每天生活中的动作可能的错误是什么? 它使用了什么防错法? 怎样进一步防错?
B零件装到A零件 上时,有时会位置 不对.A上的多余 孔去掉后,去掉了 位置匹配不对的 可能.
正确
AB
多余孔
B A 把多余孔堵住,那B定位不准就不可能
Page 17
各种类型的防错法装置
2)定位销 Guide/reference/interference Rod or Pin
定位销是一个坚硬的实心小钉或小棍,能 使零件或夹具按正确的方向定位,这个小 突起能阻碍和防止零件的不正确的方向, 有时它能固定自己或工件,夹具.
防错法 (Error Proofing)
培训目标
培训结束应懂得:
区分错误(error)和过错(defect) 排序防错法的结果 执行防错法结果的评估 应用防错法解决当前区域或流程中的问题
如何进行防呆防错

4、相符原理 确保两者形状、系统等特性匹配,来避免错误的发生; •登陆微信时要求输入对应的账户和密码; •做完手术,医生会清点手术用品,必须全部完整的放进工具盒里才能结束手术 •产品设计上采用形状匹配来避免操作人员匹配错误;
防错装置
基本思路
目标
方法
排除
消除可能的错误
通过产品及制造过程的重新设 计,加入防错方法
替代
用更可靠的过程替代目前的 运用机器人技术活自动化生产
过程以降低失误
技术
容易/简 化
使作业更容易完成
合并生产步骤,实施工业工程 改善
异常检出
在缺陷流入下工序前对其进 行检测并剔除
使用计算机软件,在操作失误 时予以告警
人为错误
健误识缺随疏拖缺突蓄
忘解别乏意忽拉乏发意
错经
监事破
误验
管件坏
g. 误操作
缺陷原因
h. 调整失误 i. 设备参数不当 j. 工装夹具不当
漏掉某个作业步骤 作业失误 工件设置错误
●○○○○●○○
●
○●○●●●●●
●
●○○○
●○○
○
缺件
○○
○○●
○
●
用错零件
●●●●●●●●
●
工件加工错误
●●○○●●
五 人为错误的原因有哪些? 有人总结了错误发生的十大原因。它们分别是: 遗忘、理解错误、识别错误、新手错误、意愿错误、疏忽错误、迟钝错误、缺乏标准导致的错误 、意外错误、故意的错误。 a. 遗忘:当我们注意力不集中在某处时,会遗忘某些事情,比如王少伟昨天就丢了个手机 b. 理解错误:我们常根据以前的经验来理解新遇到的事物,比如总觉得这周六不上班(其实是 要上滴,元旦调休) c. 识别错误:看得太快、看不清楚或者没仔细看会发生错误 d. 新手错误:缺乏经验产生的错误,比如老员工一般比新员工少犯错误 e. 意愿错误:特定时候决定不采纳某些规则发生的错误,比如闯红灯 f. 疏忽错误:心不在焉发生的错误,比如无意识的穿过街道,没有留意到红灯是亮着的 g. 迟钝错误:判断或者行动迟缓发生的错误,比如刹车踩慢了 h. 缺乏标准导致的错误:没有规矩,不成方圆 i. 意外错误:没有考虑到的情况发生了,导致的错误,比如某个检验设备突然故障了 j. 故意错误:人为的故意制造错误,这个性质就恶劣啦~ 以上这些分类有些分散,之间也有很多重叠交叉的地方。但无非是技能、规则和知识导致的错误 。但总的来说可以归为人的惰性
Error Proofing
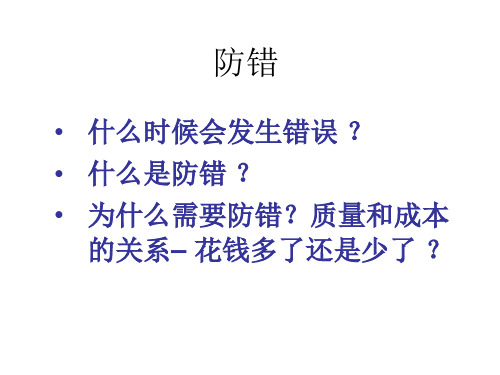
防错运用的准则
好的, 有效的防错设计,是来源于:
•对缺陷发生真正原因的把握。 了解这类缺 陷是如何发生的。 •对工艺的熟悉和操作经验。(现场操作员 的意见很重要) •广泛参与, 大家一起出主意。 •最好的办法总是要努力才能找到的,要勤 于思考, 严格要求, 不轻易放弃。(浪费的方
源头检验 自检
连续检验
控制 警告
探测点 定值
定序步骤
举例
预防差错: 限位开关 警告员工注意原胶低
限位。
流量感应器 检测原胶的 流量
很多时候你会有多种防错装置
举例
问题: 模具无法很好地合模
改进前
改进后
上模
上模
定位销子 下模
定位销子 下模
模具上的定位销子上下同一尺寸
模具上的定位销子上下不同尺寸 ,合模时只有一个方向。
✓ 源头检验 – 员工/设备在开始工作前检测运 行条件,流程直接察觉错误,使得做错成 为不可能
哪一种最好 ? 如何可以保证 ?
预防差错的方法
预防差错来源于以下两种情况:
警告 – 提供信息 控制 – 停止流程
停止最好
预防差错 – 察觉的3种方法
探测点 – 实际地测量发觉错误
测量最好
定值 – 实际点数发觉错误
式解决问题可能是容易的,但不是长久的)
我们还可以做什么来减少/消除类似的问题?
定序步骤 – 要求在进行到下一步骤之前必须完成易出 现差错的检测
自动检测不是预防差错……用来防止和察觉人所犯错误的工具 才是预防差错
举例
源头检验 自检
连续检验
控制 警告
探测点 定值
Error Proof教材

18
零件数目多、混合摆放 零件数目多、
Many Parts / Mixed Parts
• 容易漏装 • 容易混淆
• Easy to forget a part • Easy to mix one for another
7
何为“过失” 何为“过失”
Definition of an Error
• 与已制定的工艺有偏差
– 所有缺陷都是由过失造成 – 并不是所有过失都会造成缺陷
• Deviation from the intended process
– All defects are caused by errors – Not all errors result in defects
Common Defect Categories • 零件被损 • 零件颠倒 • 零件搭配错误 • 零件配合不重合 • 等等
• Damaged parts • Reversed parts • Mismatched parts • Misaligned parts • Etc.
12
• 检验失效 • 错误的零件 • 错误的尺寸 • 不能装配
• 大部分员工都不是 故意犯错 • 改变环境以减少人 为过失-- --把它设 为过失--把它设 计出来! 计出来!
• Most workers don’t make intentional errors • Alter the environment to reduce human error design it out!
•
Inspection – Autonomous Self Check Inspection ( Autonomation ) – 100% Inspection by Machines – Machines stop when defect is detected – Defect does not get passed to the next operation
防错(Error Proofing)
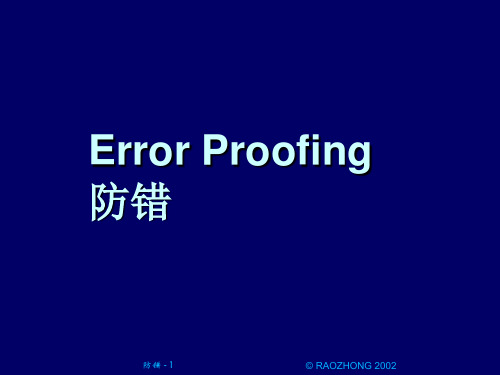
防错:错误的十种原因 防错: 4. 遗漏部件:装配、焊接或其他过程中未有全 遗漏部件:装配、焊接或其他过程中未有全 部部件 不适当的部品/部件:装配时安装了不正确的 5. 不适当的部品/部件:装配时安装了不正确的 部件 6. 处理错误的工件:对错误的部件加工 处理错误的工件:对错误的部件加工 7. 操作错误:执行操作不正确;标准过程或规 操作错误:执行操作不正确;标准过程或规 范说明的版本不正确
防错 - 25
© RAOZHONG 2002
3 自动原理
以“浮力”的方式来控制 浮力”
例如:抽水马桶之水箱内设有浮球,水升至某一高度 时,浮球推动拉杆,切断水源。
以“重量”控制的方式来完成 重量”
例:电梯超载时,门关不上,电梯不能上下,警告钟 也鸣起。
以“光线”控制的方式来完成 光线”
例:自动照相机,光线若不足时,则快门按不下去。
几乎所有的缺陷有人的错误而产生。 几乎所有的缺陷有人的错误而产生。人至少有十种错误
健忘 误解产生的错误 识别错误 新手错误 故意的错误
疏忽的错误 迟钝的错误 缺少标准的错误 意外的错误 蓄意的错误
防错 - 8
© RAOZHONG 2002
错误的类型有几种
几乎所有的缺陷都由人类的错误产生。但至少有 10种人因错误 10种人因错误 1. 遗忘:有时当我们不集中精神时我们会忘记事 遗忘:有时当我们不集中精神时我们会忘记事 情。例如,站长忘记放下交叉门。 安全措施:预先警告操作者或定期检查。 2. 误解产生的错误:有时在我们熟悉情况前得出 误解产生的错误:有时在我们熟悉情况前得出 错误结论时会出错。例如,当不熟悉自动变换器 的人踏在刹车上时会认为是离合器。 安全措施:训练,预先检查,标准化工作程序。
防错法安全教育培训

防错法安全教育培训前言近年来,越来越多的公司开始重视安全教育的重要性,以防止员工在工作中出现差错而导致的严重后果。
针对此类问题,一种有效的处理方式是通过防错法(mistake proofing)安全教育培训来对员工进行防错意识和技能的培养,以及对可能存在的隐患进行排查和改进。
防错法简介防错法又称“无误操作法(POKA-YOKE)”,是指通过针对某一过程或产品的有限变化进行的改进,以确保制造或服务等工作的高质量、高生产率和低成本,并消除由过程失误引起的人员伤害、健康问题、环境污染、财产损失和指责等问题。
防错法可以分类为三类:物理性防错法、程序性防错法和信息技术性防错法。
物理性防错法是通过改变物理方式来防范错误,如用凸起标记防止装配方向错误等;程序性防错法是通过程序或步骤来防止错误,如检查清单、工序检验等;信息技术性防错法则是通过信息技术手段来防止错误,如自动化控制、机器视觉等。
防错法教育培训的重要性防错法教育培训对企业和员工都有重要的意义。
首先,防错法教育培训可以提高员工对安全问题的重视程度和防错意识,让员工了解什么是防错法、为什么需要防错法以及如何进行防错法,从而减少人为错误的发生率。
其次,防错法教育培训可以强化员工的品质意识,提高生产、服务的质量水平和生产效率,并减少因产品和服务质量问题而带来的财产和信誉损失。
再者,防错法教育培训可以为员工提供更多实用的技术和方法,让员工在工作中更加得心应手、自信满满,提高工作效率和质量。
最后,防错法教育培训可以为公司防止因安全隐患而带来的责任和损失提供保障,减少企业安全事故的发生率和风险程度。
综合来看,防错法教育培训对企业和员工都具有非常重要的意义,是企业精益生产、安全生产和可持续发展的重要保障。
防错法教育培训的内容防错法教育培训的内容可以按照以下几个方面进行:1. 安全标准和操作规程防错法教育培训应该包含对安全标准和操作规程的讲解,以确保员工正确、规范地操作。
- 1、下载文档前请自行甄别文档内容的完整性,平台不提供额外的编辑、内容补充、找答案等附加服务。
- 2、"仅部分预览"的文档,不可在线预览部分如存在完整性等问题,可反馈申请退款(可完整预览的文档不适用该条件!)。
- 3、如文档侵犯您的权益,请联系客服反馈,我们会尽快为您处理(人工客服工作时间:9:00-18:30)。
The human factor accounts for the vast majority
人的因素占了绝大比例
The consequences of mistakes错误造成的后果
Missed Operation漏掉某个作业步骤 Processing Error作业失误 Errors in Part Set-up工件设置措施 Missing Parts缺件 Wrong Parts用错零件 Processing Wrong Workplace工件加工错误 Mis-operation误操作 Adjustment Error调整失误 Improper Equipment Set-up设备参数设置不当
Training, error proofing 培训、防错
Purchase equipment with good accuracy 购置精度更好的设备TPM、SPC Warehouse inspection , SPC, and Supply control入库检验,SPC,供应链管理 QFD,DOE,FMEA Robust,DOE MSA,GR&R
Error Proofing 什么是防错
Man, machine, material, method, environment, measurement and other factors lead to issues 人、机、料、法、环、测等因素导致异常;
Problems from 问题来源 Problems 常见问题 Solutions 解决方法
Object
目标
Eliminate potential errors消除可能的错 误
Method
方法
Add error proofing method by re-designing product and process通过产品及制造过程 的重新设计, 加入防错方法 Use robotics or automation technology运用 机器人技术或自动化生产技术
Three dimensions of error proofing防错的三个维度:
Causes 原因
Generate 产生
Results 结果
Lead to 导致
Consequences 后果 Rework/Return/Claim /Damage/Disaster 返工/救火 退货/索赔 耗損/灾害
Cause of error 错误发生的原因
Ten causes of error导致错误的十大直接原因:
序号 NO. 1 2 3 4 5 6 7 8 9 10 Reasons 原因 Forgethfulness健忘(或不知道) Misunderstanding误解(沟通问题) Misidentification辨认(不正确的观察…距离太远) Inexperience新手(未经训练的人员) Willfulness藐视规定(不理会规定) Inadvertent疏忽大意(分心、疲劳) Slowliness迟钝(判定的延迟) No Standard欠缺标准(书面或视觉的) Superise意外的错误(机器性能或故障) Intentional destruction蓄意的破坏
Change design 设计修改
Design
设计防错 PFMEA 过程 FMEA
Output
防错输出
Requirements 顾客需求
DFMEA 设计
CP 控制计划
WI 作业SOP
FMEA
Change Process
过程修改
Process
过程防错
Implementation
防错运行
Three ways of error proofing 防错的三个途径
Improper Tools and Jigs工装夹具准备不当
The consequences of mistakes错误造成的后果
Matrix of causes and consequences原因和结果矩阵图:
Management Flow of error proofing防错管理流程
•
The Process 重新设计过程控制
-
Change or add tools and fixture 改变或增添工具、工装 Change the process 改变加工步骤 Add usage of lists, templates, or gauges 增加使用清单、模板或测量仪 Use control chart 执行控制图表
Man 人
Machine 机 Material 料 Method 法 Environment 环 Measurement 测
Making mistake 犯错误
Equipment has accuracy trouble, abrasion and drifting 设备精度故障、磨损、漂移 Lot quality is un-stable 批次不稳定 Not the best method 非最优 Disturb by vibration 变量干扰 Stability 测量稳定性
Detect and remove defects before entering the next process在缺陷流入下 工序前对其进行检测并剔除 Minimize the impact of errors将错误影 响降至最低
Better 较好
Good 好
Ten principles of error proofing 防错的十大原理
Why is there a missing corner on the phone card ? 手机卡上为什么缺了一个 角
Error Proofing 什么是防错
Error proofing: POKA-YOKE in Japanese and Error Proof or Fool Proof in English. Error Proofing is a
Socket 插座
Connector of projector 投影仪接口
Ten principles of error proofing--Insurance 防错的十大原理--保险原理
2. Insurance: More than two actions must be performed together or in sequence to complete the task. 2. 保险原理:借用两个以上的动作必需共同或依序执行才能完成工作。
-
Enlarge the dissimilarity of parts 夸大零件的不相似处
Enlarge the asymmetry of parts 夸大零件的不对称性 Design clear error proofing identifications 设计明显防错标识
Ideas of error proofing防错的基本思路
systematic approach for anticipating and detecting potential defects and preventing them from reaching the customer(Internal or External).
防错,日文称POKA-YOKE,英文又称Error Proof或Fool Proof(防呆),是一种预测及探测潜在 缺陷以及阻止缺陷影响客户的体系方法(内部防错和外部防错)。
1. 2. 3. 4. 5. 6. 7.
Completely cured 断根原理 Insurance 保险原理 Automation 自动原理 Corresponding 相符原理
Order 顺序原理
Isolation 隔离原理 Duplication 复制原理
8.
9.
Stratification 层别原理
Cause of error 错误发生的原因
Error percentage caused by man人为错误比例:
Causes 失误原因 Forgethfulness忘记 Not familiar with process and operation对过程/作业不熟悉 Inexperience缺乏工作经验 Intentional destruction故意失误 Inadvertent疏忽 Slowliness行动迟缓 No WIs缺乏适当的作业指导 Superise突发事件 Classification 原因归类 Man人 Man人 Man人 Man人 Man人 Man人 Method方法 Equipment设备 11.1% 11.1% 77.8% Percentage 所占比例
Warning 警告原理 缓和原理
10. Cushion
Ten principles of error proofing--Completely cured 防错的十大原--断根原理
1. Completely cured: The cause of the error will be eliminated from the root, so that no error will occur. 1. 断根原理:将会造成错误的原因从根本上排除掉,使绝不发生错误。
•
The Design 重新设计产品
-
Eliminate the conditions for error 消除犯错误的条件 Redesign symmetrical or asymmetrical designs 重新进行对称或不对称设计
-
Change the material 改变材料
Change the type and character of parts 改变组件的类型、特征
Errors 错误