无擦伤折弯模的结构设计
无擦伤折弯模结构设计

2侧 定 位 块 3翻动 饭 . . 6下模 饭 .
4凸模 .
5脱 料 板 .
罔 4 初 始 状 态
7支 撑 块 .
() 2 在折 弯 开 始 时 ( 图 5 , 脱 料 板 向下 运 动 , 见 )下
材 料带 动 翻动 板绕 靠 块 的 尖 角点 作 转 动 , 且 翻 动 板 并
会 在靠 块尖 角处作 相 对 滑 动 。此 时 , 要确 保 翻动 板 外
故 在制 品 的折 弯外 侧 面 会 有擦 伤 ( 越小 则 擦 伤 越严 尺 重) 。为 解决 此 问题 , 可在 此 基 础 上 改 进 , 折 弯块 也 把
的 部 改 为滚 轴 结 构 . 图 2 在 折 弯 时 滚 轴 在 制 品 如 .
的带 动下 转 动 ,网此 制 品 外侧 与 滚 轴 是 发 生 滚 动摩 擦. 成形 后擦伤 痕 迹 明显减 少 . 但不 能 完 全避 免 !
m cie bxs ( na es h eurm nst ot ufc uly aevr sit ti ahn oe c ti r) e r i et o u rsr e qai r ey tc.I s o n ,t q e e a t r
S i c l t g t n n s r p s r c u i g o d n r e d n ( e O d f u t o e o - c a e u f e sn r i ay b n i g t .Th s H e b rt g de i a i u H W e i i a n s u t r s p o i e ,a d i o mig p o e s i a ay e s w l t cu e i r v d d n t f r n r c s s n lz d a e 1 r s . Ke r s v r r i g b n i g— l c ;si i g fit n e d n i y wo d :o e t n n e d n — o k l n r i ;b n i g d e u b d c o
无擦伤折弯模具的结构概述

加強筋
反折
折邊太長
圖八 翻動板結構應用舉例
大R角
圖九 小于90度折ቤተ መጻሕፍቲ ባይዱ舉例
五,結論
此種無擦傷折彎模具的運動是滑動與轉動相 結合在以轉動為主要運動,與製品表面的相對 滑動幾乎沒有,所以能達到很好的外觀要求. 一般人們可能會認為此種結構很複雜,其實它 就是人們熟悉的擺塊結構在理論上的發展與 實踐應用的變異.
3, 當翻動板繞轉動點轉到直立插入 下脫料板與靠塊之間,此時脫料板 繼續向下,則翻動板在材料的靜摩 擦力帶動下向下運動,翻動板與靠 塊發生滑動,當翻動板下到與靠塊 下面6~8mm時成形完成,此過程的 要點是確保脫料板與靠塊的間隙 要穩定,而且翻動板的外側面與靠 塊的內側面要研磨,以便減小滑動 摩擦力,對於下脫料板的行程取 30mm較可靠.(因行程較大,一般採 用氣墊頂料)
翻倒
重力
坡度必要
圖七 脫模狀態
四,翻動板折彎模具的應用
翻動板折彎模成形過程中,材料面與翻動板的 滑動極小,所以成形後製品表面無損傷,擦痕. 常用於機殼,面板等外觀有嚴格要求的製品.也 可應用于諸如:折彎時避位多,折起直邊太長, 或折邊根部有凸起等不能用一般折彎模具的 製品(如圖八);還可用於成形在R角或小於90 度的製品,(如圖九)
二,無擦傷折彎模具的結構
如圖三所示為一”U”形製品折 彎模具結構圖, 01 1,折彎上沖頭. 02 2,翻動折彎塊(板). 03 3,翻動塊定位. 04 4,下浮動脫料板. 5,翻動板托塊(支撐塊). 05 06 6,翻動板靠塊. 07 7,下固定板
導柱
SEC M-M
圖三
M M
01 02 03 04 05 06 07
1
1.折彎塊 2.下脫料板
弯曲模模具设计

弯曲模模具设计弯曲模是模具设计领域内应用比较广泛的一种模具,它的作用是将金属或非金属等材料按照一定形状进行弯曲变形。
弯曲模的设计是一项非常重要的技术工作,需要考虑的因素非常多,包括材料的选择、模具的结构、工艺流程等多个因素,下面就从这些方面来进行介绍。
一、材料的选择弯曲模的材料应该是具有高强度、高硬度、高耐磨性能的材料。
在选择材料时要考虑模具的使用寿命和弯曲过程中所需承受的压力,同时还要考虑工艺条件、成本和其他因素等进行综合考虑。
传统上,常采用的材料是合金钢、高速钢、钴基合金等。
随着技术的不断进步,高度强化的不锈钢和硬质合金等材料已经广泛应用于弯曲模的生产制造。
二、模具的结构弯曲模的结构通常分为上下模和导向装置。
上下模是模具设备中的主要组成部分,它的设计应该具有高强度、高度一致性的特点,以保证在弯曲时模具的形状能够始终保持不变,从而满足精度要求。
导向装置的作用是保证模具定位准确,避免在弯曲过程中发生偏移而导致失误。
三、工艺流程弯曲模的设计还应考虑到整个工艺流程过程中的各个步骤,如预处理、弯曲、压力调节、折弯等。
因此,模具的设计应进行一系列的工艺分析和试验,以确定合理的工艺流程和最佳的模具设计。
在设计时应特别注意各种弯曲材料的物理特性,以及各种工艺时所需的压力、温度等参数,以确保模具能够正常运行并产生符合要求的产品。
弯曲模具是目前比较常用的模具之一,它具有结构简单、生产效率高、加工精度高等优点,在建筑、汽车、机械和电器等领域都有广泛的应用。
因此,模具设计师应该洞察客户的需求,精细研究各组件的结构、相互协作关系、材料选择等因素,打造新一代弯曲模具,适应产业的升级换代和市场的变化需求,实现产品质量的不断提升和建设经济可持续性的理念。
折弯模结构设计_图文_图文

• 3.3 上下脱料板应有内导柱导正,内导柱长度在闭合状态 下不可伸出脱料板;
• 3.4 下模做导正块,使向下折弯冲头在折弯前先被导正, 导正镶块应在自由状态时比下脱板高3~5MM为佳;
• 3.5 定位方式在一般情况下采用外定位,特殊情况采用内 孔定位。
上下成型模结构
实例
4.向下成型
•料厚T •0.6 以下 •0.6 ~1.0 •1.2~1.5 •1.6~2.0 •2.0以上
•V沟深度 •3.0 H
•俩边R值 •4.5 •请示上
级
•2.0 •2.5~3.0 •3.0~3.5 •请示上
级
• 2.3.2 当折边高度较矮时,作V曲模时一定要先 在侧视图上模拟,初始阶段料带边缘一定要过俩 边R1。0mm左右,如图B所示,相差不多时可通 过适当减少V沟深度H和俩边R值来满足此要求。 相差太多时要请示上级来确认是否按V曲模设计 ,还是按其它折弯方式。有几种方式要分别考虑 ,图C,产品中间有一小部分初始阶段料带边缘没 有过俩边R1。0mm,还是可以考虑V曲的,图D 是产品中间有很长部分初始阶段料带边缘没有过 俩边R1。0mm,图E是产品端部有一部分,此俩
•折弯模结构设计_图文_图文.ppt
一、分类
V形折弯
向下成型
折弯模的 结构分类
Z形折弯
向上成型
二、工艺分析
1.Z形折弯
• 1.1 当C<5T时,一次成形,计算参见展开系数 设计标准(如图1)为减少材料的流动性,上模 板成形部分应做压筋,宽度0.5MM≤W≤1.5MM ,深05MM≤H≤0.3MM; 为减轻材料的刮伤以及 有利于材料的成形,应在下模折弯块成形部分倒 角R≥0.3MM; 由于Z曲在折弯过程中流动性很大 ,在保证压缩量足够的情况下,弹簧压力应越大 越好。
弯曲模模具设计

弯曲模模具设计弯曲模模具设计是一种常用于金属加工行业的模具设计方式,其主要功能是用于弯曲金属材料工件的加工,从而形成各种形状的工业制品。
与传统的模具设计方式相比,弯曲模具设计具有设计精度高、生产效率高等优势,受到了越来越多厂商和企业的青睐。
1. 弯曲模模具的概述弯曲模模具主要由上、下模两部分组成,上模和下模均分别设置了凹槽和凸轮,并且凸轮与凹槽紧密配合。
在金属材料弯曲加工时,将金属材料放在两个模具之间,通过模具上凸轮与凹槽的剪切作用,将金属材料弯曲成需要的形状。
弯曲模模具具有结构简单、加工方便、成本低等特点,因此被广泛应用于金属加工行业。
2. 弯曲模模具的设计要点弯曲模模具的设计需要考虑以下几个方面:(1)磨具选用。
弯曲模模具的磨具应选择硬度高、耐磨性好的材料制作,以确保使用寿命长。
(2)弯曲半径的控制。
弯曲半径是弯曲模模具最为核心的设计要素之一,在设计时需要针对不同的金属材料弯曲半径进行精确控制,以确保弯曲加工后符合生产要求。
(3)凸轮和凹槽的设计。
凸轮和凹槽是弯曲模模具最为重要的组成部分之一,需要设计成互相匹配的形状。
同时,凸轮和凹槽的大小也需要根据弯曲的材料厚度和弯曲半径进行定制。
(4)模具的材料和硬度。
弯曲模模具需要具有高强度、高硬度和高韧性,以便在弯曲加工中经受住复杂的机械力和磨损。
3. 弯曲模模具的制造工艺弯曲模模具的制造主要分为以下几个步骤:(1)设计制图。
在制造弯曲模模具前需要对其进行精确的设计和绘制,建立出完整的工程文件。
(2)材料采购。
制造弯曲模模具需要使用高强度、高硬度和高韧性的材料,材料的选用需要根据需要弯曲的金属材料,弯曲半径和弯曲角度等进行合理选择。
(3)零件加工。
根据设计图纸进行部件的加工,材料切割、粗加工、精加工、电火花加工、刻度等工序的执行。
(4)零件组装。
完成部件的加工后,进行总体组装,同时进行工装和夹具的制作。
(5)调试命令。
进行弯曲模模具的调试、调整和试运行,以确保最终产品的质量和稳定性。
弯曲模结构设计_图文_图文

弯曲模设计
凸模 凹模 弹簧 凸模活动镶块
凹模活动镶块
定位销 转轴 顶板
U形件弯曲模
凹模活动镶块
弯曲模设计
弯曲角小于90°的U形弯曲模 1-凸模 2-转动凹模 3-弹簧
第三章 弯曲工艺与弯曲模设计
弯曲模两次成形弯曲模 a)首次弯曲 b)二次弯曲 1-凸模 2-定位板 3-凹模 4-顶板 5-下模形
弯曲模设计
弯曲模设计
1-凸模 2-压板 3-芯棒 4-坯料 5-凹模 6-滑块 7-楔模 8-活动凹模
小圆弯曲模
弯曲模设计
小圆一次压弯
弯曲模设计
三道工序弯曲大圆
弯曲模设计
两道工序弯曲大圆
弯曲模设计
带摆动凹模的一次弯曲成形模 1-支撑 2-凸模 3-摆动凹模 4-顶板 5-上模座 6-芯棒 7-反侧压块 8-下模座
弯曲模结构设计_图文_图文.ppt
弯曲模设计
一、单工序弯曲模
1.V形件弯曲模
V形弯曲模的一般结构形式 1-凸模2-定位板3-凹模4-定位尖5-顶杆 6-V形顶板7-顶板8-定料销9-反侧压块
弯曲模设计
一、单工序弯曲模(续)
V形精弯模
1-凸模
2-支架
3-定位板(或定位销)
4-活动凹模 5-转轴
6-支承板 7-顶杆
弯曲模设计
摆动凸模 压料装置 凹模
带摆动凸模弯曲模
弯曲模设计
弯曲模设计
弯曲工艺与弯曲模设计
多次V形弯曲制造复杂零件举例
弯曲工艺与弯曲模设计
折弯机用弯曲模的端面形状 a)通用凹模 b)直臂式凸模 c)曲臂式凸模
弯曲工艺与弯曲模设计
通用V形弯曲模
弯曲模设计
弯曲模设计
折弯模具设计
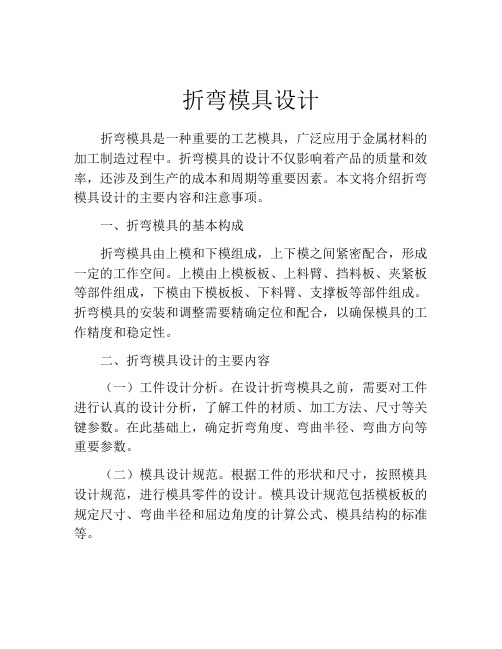
折弯模具设计折弯模具是一种重要的工艺模具,广泛应用于金属材料的加工制造过程中。
折弯模具的设计不仅影响着产品的质量和效率,还涉及到生产的成本和周期等重要因素。
本文将介绍折弯模具设计的主要内容和注意事项。
一、折弯模具的基本构成折弯模具由上模和下模组成,上下模之间紧密配合,形成一定的工作空间。
上模由上模板板、上料臂、挡料板、夹紧板等部件组成,下模由下模板板、下料臂、支撑板等部件组成。
折弯模具的安装和调整需要精确定位和配合,以确保模具的工作精度和稳定性。
二、折弯模具设计的主要内容(一)工件设计分析。
在设计折弯模具之前,需要对工件进行认真的设计分析,了解工件的材质、加工方法、尺寸等关键参数。
在此基础上,确定折弯角度、弯曲半径、弯曲方向等重要参数。
(二)模具设计规范。
根据工件的形状和尺寸,按照模具设计规范,进行模具零件的设计。
模具设计规范包括模板板的规定尺寸、弯曲半径和屈边角度的计算公式、模具结构的标准等。
(三)设备选型和调试。
在确定模具设计方案后,需要选择适合的设备,进行模具安装和调试。
设备选型需要考虑设备的承载能力、调节范围、加工速度和精度等因素。
模具调试需要根据工件的要求,调整上下模的配合精度和模板板的位置。
(四)制造、热处理和表面处理。
完成折弯模具设计后,需要进行模具制造、热处理和表面处理。
模具制造需要选择优质的原材料,并采用精密加工工艺,确保模板板和各零件的精度和平整度。
热处理需要根据模具材料的特性,选择合适的处理方式和温度,以改善模具的硬度和强度。
表面处理需要采用防锈、耐磨和美化等处理方式,以保证模具的使用寿命和外观质量。
三、折弯模具设计的注意事项(一)优化模具结构。
针对不同的工件和加工方式,需要经常优化折弯模具结构。
比如,在大尺寸、薄壁厚的工件加工中,需要设置加强板或支撑板,以增强模具结构的刚性和稳定性。
(二)设备调试精度。
设备调试是折弯模具必不可少的环节,需要特别注意调节精度。
如果调节不精细,会导致加工尺寸误差和工件质量不合格。
无擦伤折弯模具结构的设计

无擦伤折弯模具的结构设计摘要: 越来越多的机箱(机柜)面板或上盖等板金制品中,对其外观表面要求很严格.在这些制折弯成形时,用一般的折弯模具很难达到此种表面质量要求,对此,提出一种新的折弯模具结构的设计.关键词: 翻转块折弯块, 滑动摩擦, 静摩擦. 转动轴点. 翻倒.一,一般折弯模具结构分析最常见的板金制品折弯模具结构如图一所示,此种模具结构折弯时,因制品与折弯块是相对滑动摩擦,故在制品的折弯外侧面会有擦伤(R 越小则擦伤越严重).为解决此问题,也可在此基础上改进,把折弯块的R 部改为滚轴结构,如图二,在折弯时滚轴在制品的带动下转动,因此制品外侧与滚轴是发生滚动摩擦,成形后擦伤痕迹明显减少,但不能完全避免!1.折弯块,2.下脱料板 1,滚轴 2.折弯块,3.下脱料板 图一 一般折弯模具二,无擦伤折弯模具的结构设计如右图三所示为一”U”形制品折弯模具结构图, 1,折弯上冲头 2,翻动折弯块(板) 3,翻动块定位 4,下浮动脱料板5,翻动板托块(支撑块) 6,翻动板靠块 7,下固定板制品示意图三,翻动板折弯成形过程分析及设计要点:1. 模具在折弯初始状态时,翻动折弯块水平置于下脱料板与翻动板定位块之间,脱料板比翻动折弯块高出1~2mm.如图四所示,设计时要确保b=a+0.05,方便翻动块能立起,并且要使翻板左下部修成大R角, 同时使转动半径c=d-0.1,防止翻动板绕转动轴点翻转时与定位块干涉.2,在折弯开始时,下脱料板向下运动,材料带动翻动板绕靠块的尖角点作转动,并且翻动板会在靠块尖角处作相对滑动.此时,要确保翻动板外侧有在R,以免下侧定位块干涉,而翻不起来,在靠块尖角处不可以倒角,否则翻动板可能会滑出.3,当翻动板绕转动点转到直立插入下脱料板与靠块之间,此时脱料板继续向下,动,翻动板与靠块发生滑动,当翻动板下到与靠块下面6~8mm时成形完成,要点是确保脱料板与靠块的间隙要稳定,磨,以便减小滑动摩擦力,对于下脱料板的行程取30mm较可靠.(因行程较大,用气垫顶料)4,脱模时,下脱料板被顶起,翻动板在反撑块的作用下向上推出,完全脱出后,翻动板在自身重力的作用下绕着支撑块的支撑点向外翻动与材料脱离,翻倒后在侧定位块的大圆角作用下自找正,回复到原始状态.此过程的要点是一定要把支撑块的上面以及翻动板下支撑部分做成斜坡(支撑点越小越好),以便于靠自重力翻转.(注意:斜坡只能是局部而不是整条,否则折弯开始时翻动块可能会滑出.)四,翻动板折弯模具的应用:翻动板折弯模成形过程中,材料面与翻动板的滑动极小,所以成形后制品表面无损伤,擦痕.常用于机壳,面板等外观有严格要求的制品.也可应用于诸如:折弯时避位多,折起直边太长,或折边根部有凸起等不能用一般折弯模具的制品(如图八:);还可用于成形在R角或小于90度的制品,(如图九:)五,结束语此种无擦伤折弯模具的运动是滑动与转动相结合在以转动为主要运动,与制品表面的相对滑动几乎没有,所以能达到很好的外观要求.一般人们可能会认为此种结构很复杂,其实它就是人们熟知的摆块结构在理论上的发展与实践应用的变异.参考文献:1,<<泠压冲模设计>>,第四机械工业部标准化研究所,1979.北京.2,<<冲模设计手册>>,冲模设计手册编写组,1999,机械工业出版社。
无痕折弯模具结构

无痕折弯模具结构模具壳体是无痕折弯模具最基本的构件,它一般由高强度的合金材料制成。
模具壳体的内部设计是整个模具结构中最关键的部分,它的形状和尺寸需要根据所要加工的金属板材的要求来确定。
模具壳体的内部一般包括多个辊轮槽,用于安装辊轮。
辊轮是无痕折弯模具中起主要作用的部分,它可以分为上下辊轮和后辊轮。
上下辊轮常被称为工作辊,后辊轮常被称为辅助辊。
工作辊一般由高硬度、耐磨的材料制成,以保证其在折弯过程中对金属板材的压力和磨损性能。
工作辊的直径和宽度需要根据所要加工的金属板材的要求来确定。
辅助辊一般由弹性材料制成,以起到支撑和协助工作辊的作用。
传动装置是无痕折弯模具中用于传输能量的部分,它主要由电机、减速器和传动轴等组成。
电机提供动力,减速器进行速度调节和转矩输出,传动轴将转动能量传输到辊轮上。
传动装置的设计需要考虑到加工的金属板材的大小和厚度等参数,以确保加工过程中的稳定性和准确性。
1.确定所要加工的金属板材的尺寸和厚度等参数。
2.根据金属板材参数设计模具壳体的形状和尺寸,并制造模具壳体。
3.在模具壳体的辊轮槽中安装上下辊轮和后辊轮,调整工作辊的位置和间距,确保辊轮的平行度和垂直度。
4.安装传动装置,将电机、减速器和传动轴与辊轮相连。
5.调试模具,根据金属板材参数和需求,调整工作辊的高度和压力,以确保加工的准确性和无痕性。
6.根据加工要求和金属板材参数,确定折弯工艺和折弯角度。
7.将金属板材放入模具中,并通过启动电机,使辊轮运转,完成折弯加工。
8.取出已加工的金属板材,并进行质量检查和尺寸测量。
无痕折弯模具的结构和使用步骤对于保证加工的准确性和无痕性至关重要。
通过合理的设计和操作,无痕折弯模具可以高效地完成金属板材的折弯加工任务,提高生产效率和产品质量。
同时,无痕折弯模具还可以减少材料的浪费和成本,为企业的发展带来更大的经济效益。