正丁烯氧化脱氢制丁二烯
恒温固定床丁烯氧化脱氢制备丁二烯的方法

恒温固定床丁烯氧化脱氢制备丁二烯的方法
恒温固定床丁烯氧化脱氢制备丁二烯是一种重要的工业化生产方法。
该方法通过将丁烯在恒温固定床反应器中进行氧化脱氢反应,得到高
纯度的丁二烯。
该方法具有反应条件温度低、反应效率高、产品纯度
高等优点,因此在工业生产中得到了广泛应用。
该方法的反应原理是将丁烯与氧气在催化剂的作用下进行氧化反应,
生成丁二烯和水。
反应中催化剂的选择对反应效率和产物纯度有着重
要的影响。
常用的催化剂有铬酸盐、钒酸盐、钨酸盐等。
其中,钒酸
盐催化剂具有反应效率高、产物纯度高等优点,因此在工业生产中得
到了广泛应用。
该方法的反应条件包括反应温度、反应压力、氧气流量等。
反应温度
一般在200-300℃之间,反应压力一般为1-3MPa,氧气流量一般为0.5-1.5L/min。
反应时间一般为数小时至数十小时不等,具体时间根
据反应器的规模和反应条件的不同而有所差异。
该方法的优点在于反应条件温和、反应效率高、产物纯度高等,因此
在工业生产中得到了广泛应用。
同时,该方法还具有反应器规模可控、操作简便等优点,使得该方法成为了丁二烯生产的主要方法之一。
总之,恒温固定床丁烯氧化脱氢制备丁二烯是一种重要的工业化生产方法。
该方法具有反应条件温和、反应效率高、产物纯度高等优点,因此在工业生产中得到了广泛应用。
同时,该方法还具有反应器规模可控、操作简便等优点,使得该方法成为了丁二烯生产的主要方法之一。
正丁烯氧化脱氢制备丁二烯的工艺流程

正丁烯氧化脱氢制备丁二烯的工艺流程下载提示:该文档是本店铺精心编制而成的,希望大家下载后,能够帮助大家解决实际问题。
文档下载后可定制修改,请根据实际需要进行调整和使用,谢谢!本店铺为大家提供各种类型的实用资料,如教育随笔、日记赏析、句子摘抄、古诗大全、经典美文、话题作文、工作总结、词语解析、文案摘录、其他资料等等,想了解不同资料格式和写法,敬请关注!Download tips: This document is carefully compiled by this editor. I hope that after you download it, it can help you solve practical problems. The document can be customized and modified after downloading, please adjust and use it according to actual needs, thank you! In addition, this shop provides you with various types of practical materials, such as educational essays, diary appreciation, sentence excerpts, ancient poems, classic articles, topic composition, work summary, word parsing, copy excerpts, other materials and so on, want to know different data formats and writing methods, please pay attention!1. 前言本篇文章主要介绍正丁烯氧化脱氢制备丁二烯的工艺流程,旨在深入研究该工艺流程的原理、优缺点以及未来的发展方向,以期帮助广大读者更好地了解和掌握这一工艺流程。
丁烯氧化脱氢制丁二烯催化剂的相关分析

丁烯氧化脱氢制丁二烯催化剂的相关分析发布时间:2021-07-01T01:18:09.646Z 来源:《河南电力》2021年3期作者:孙世强[导读] 本文针对丁烯氧化脱氢制丁二烯催化剂的相关内容进行深入研究,明确丁二烯的主要性质和特点,总结丁二烯技术工艺路线。
(南京诚志清洁能源有限公司)摘要:本文针对丁烯氧化脱氢制丁二烯催化剂的相关内容进行深入研究,明确丁二烯的主要性质和特点,总结丁二烯技术工艺路线。
丁二烯作为石油化工基础原料,在现代工业中起到了至关重要的作用,也是非常重要的高分子合成材料,所以要高度重视对丁烯氧化脱氢制丁二烯技术进行全面分析,确保丁二烯生产制作工艺能够符合工业发展需求。
关键词:丁烯氧化脱氢;丁二烯;催化剂一、丁烯氧化脱氢制丁二烯的技术工艺路线丁烯氧化脱氢制取丁二烯,需要由专业人员按照专业的技术工艺路线制作,才能确保最终的品质符合要求,目前丁烯氧化脱氢制丁二烯主要对丁烯制取并制备,然后利用丁烯开展氧化脱氢反应提取出丁二烯所有的操作必须符合精度要求,整个工艺流程中的反应器需要使用流化床反应器,并通过CNN方法快速提取丁二烯原材料和相关动力装置。
在丁二烯制作工艺中要严格控制原材料和反应动力原材料,需要以乙醇、甲醇、亚硝酸钠以及水,所有材料纯度都需要达到98%以上。
甲醇需要选择工业级甲醇,吸收油则需要选择水溶性酸碱呈中性。
氧气可以直接利用空气制取,在整个配置中需要利用仪表冷冻水冷却水动力电软水等仪表风压力需要控制在0.3~0.65MPa,温度应该控制在零下7℃,压力需要控制在0.5~0.6MPa。
1,3-丁二烯(BD)是重要的石油化学基本原料,是合成橡胶和合成树脂制造中重要的单体。
丁烯氧化脱氢生产1,3-丁二烯有很好的经济效益。
铁系催化剂是丁烯氧化脱氢最有效的催化剂之一,但尖晶石ZnFe2O4和α-Fe2O3在两相催化剂中的作用还有待商榷。
最近,中国科学院兰州化学物理学研究所的含氧合成和选择性氧化国家重点实验室徐山的团队进行了关于丁烯在以铁为基础的α-Fe2O3/ZnFe2O42-上氧化脱氢的系统研究。
丁烯氧化脱氢

丁烯氧化脱氢是指将丁烯(C4H8)通过氧化反应转化为丁二烯(C4H6)的过程。
这个过程通常涉及催化剂的使用,可以通过以下反应方程式表示:
丁烯+ 氧气→丁二烯+ 水
在实际的工业生产中,丁烯氧化脱氢通常采用高温下的氧化剂进行。
其中,常用的催化剂是铜、铬、钼等金属或其氧化物。
这些催化剂可以提供活性位点,促进丁烯分子与氧气之间的反应,从而实现氧化脱氢过程。
丁烯氧化脱氢具有以下一些特点和应用:
生产丁二烯:丁二烯是一种重要的石化原料,可用于合成橡胶、塑料、纤维等化工产品。
通过丁烯氧化脱氢,可以高效地生产丁二烯,满足工业生产的需求。
催化剂的选择和优化:不同的催化剂对丁烯氧化脱氢的反应效率和选择性有影响。
因此,催化剂的选择和优化是提高丁烯氧化脱氢过程效率的关键。
温度和反应条件的控制:丁烯氧化脱氢通常需要在高温下进行,而且反应过程中需要控制氧气的供应和反应物的混合程度等因素,以实现高效的转化率和选择性。
产品分离和纯化:丁烯氧化脱氢的产物中除了目标产品丁二烯外,还可能包含其他副产物和不纯物质。
因此,需要进行产品的分离和纯化处理,以获得高纯度的丁二烯。
正丁烯氧化脱氢制丁二烯

六、正丁烯氧化脱氢制丁二烯丁二烯是最简单的具有共轭双键的二烯烃,易发生齐聚和聚合反应,也易与其它具有双键的不饱和化合物共聚,因此是重要的聚合物单体,主要用来生产合成橡胶,也用于合成塑料和树脂,丁二烯的主要用途见表3-2-22。
表3-2-22丁二烯的主要用途1.生产方法(1)从烃类热裂解制低级烯烃的副产C4馏分得到。
目前获取丁二烯的最经济和最主要的方法。
C4馏分产量约为乙烯的30%~50%,其中丁二烯含量可高达40%左右。
由C4馏分制取丁二烯的一种分离方案示于图3-2-37。
由于C4馏分各组分的沸点相近(正丁烯,异丁烯和丁二烯的沸点分别为-6.3,-6.9和-4.4℃),工业上通常采用萃取精馏法将它们分离,所用的萃取剂有:N-甲基吡咯烷酮,二甲基甲酰胺和乙腈等。
图3-2-37 由C4馏分制取丁二烯的工艺过程(2)由乙醇生产丁二烯乙醇合成丁二烯的总反应式为实际上反应经过一系列阶段属气-固相催化反应,在常压或减压下进行,从丁二烯中分离出的乙醛返回反应系统。
世界上采用本法生产丁二烯的不多。
(3)由正丁烷和正丁烯脱氢生产丁二烯正丁烷脱氢是连串可逆反应脱氢反应第一阶段得到三种正丁烯异构体,第二阶段三种丁烯异构体继续脱氢得到1,3-丁二烯。
两个阶段的热效应分别为-126kJ/mol和-113.7kJ/mol。
脱氢是吸热而且是摩尔数增加的反应,因而采用高温和低压(甚至负压)对脱氢反应是有利的,由于高温下副反应激烈,副产物增加,故要采用催化活性高,选择性好的催化剂。
如同乙苯脱氢一样,在反应第二阶段尚需添加水蒸气以降低丁烯的分压,提高反应平衡转化率,减少副反应(特别是丁烯热分解以及缩聚成焦反应),帮助清除催化剂表面结炭以及为脱氢反应提供热量等。
由于烯烃缩聚成焦反应比较利害,为保持催化剂活性,需频繁再生,因此脱氢周期较短,一般为几小时,甚至几分种,需专门设置再生器或设置几台(一般为2~3台)反应器切换输流使用,为此需要设置复杂的自动控制系统。
丁烯氧化脱氢制丁二烯工艺技术简介
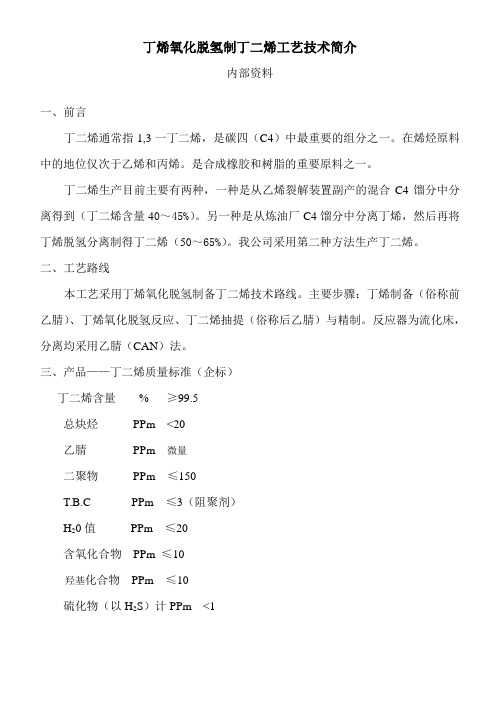
丁烯氧化脱氢制丁二烯工艺技术简介内部资料一、前言丁二烯通常指1,3一丁二烯,是碳四(C4)中最重要的组分之一。
在烯烃原料中的地位仅次于乙烯和丙烯。
是合成橡胶和树脂的重要原料之一。
丁二烯生产目前主要有两种,一种是从乙烯裂解装置副产的混合C4馏分中分离得到(丁二烯含量40~45%)。
另一种是从炼油厂C4馏分中分离丁烯,然后再将丁烯脱氢分离制得丁二烯(50~65%)。
我公司采用第二种方法生产丁二烯。
二、工艺路线本工艺采用丁烯氧化脱氢制备丁二烯技术路线。
主要步骤:丁烯制备(俗称前乙腈)、丁烯氧化脱氢反应、丁二烯抽提(俗称后乙腈)与精制。
反应器为流化床,分离均采用乙腈(CAN)法。
三、产品——丁二烯质量标准(企标)丁二烯含量% ≥99.5总炔烃PPm <20乙腈PPm 微量二聚物PPm ≤150T.B.C PPm ≤3(阻聚剂)H20值PPm ≤20含氧化合物PPm ≤10羟基化合物PPm ≤10硫化物(以H2S)计PPm <1四、原材料规格及动力配置名称规格原料;混合碳四分析项目碳二总量丙烷丙烯异丁烷正丁烷反-2-丁烯1-丁烯异丁烯顺-2-丁烯异戊烷正戊烷1,3-丁二烯甲醇含量二甲醚含量其他合计鲁深发0.052.60.8632.7412.7814.2713.88138.740.590.160.150.060.030.12100其他单位0.042.540.2622.2920.620.6716.83114.290.690.10.150.080.090.37100氧化脱氢反应用丁烯原料丁烯(重量):% ≤98% 异丁烯(重量):% ≤0.5 总碳三(重量):% ≤0.1 总碳五(重量):% ≤0.1 总硫(重量):PPm ≤3乙腈纯度(重量):% ≥98氢氰酸:PPm <50丙烯腈:PPm ≤500酸度(以醋酸计):PPm <50 水:(重量)% ≤0.5丙腈:% ≤1.0甲醇工业级亚销酸钠纯度:(重量)% ≥98水不溶物:% <0.01 NaNO3含量:(重量)% <1.5对叔丁基苯邻二酚(T.B.C)纯度(重量)%:≥99 熔点:℃≥52外观:白色或微黄晶体吸收油(正己烷)馏程:℃碘值:I2g/100g <0.1 水溶性酸碱中性脱氢催化剂铁系催化剂D-006催化剂外观:灰色不透明球状颗粒,水质量分数≤%氧气用空气生压机润滑油Iso-vg46动力规格:动力电:供生产装置用380伏。
丁烯氧化脱氢制丁二烯技术研究
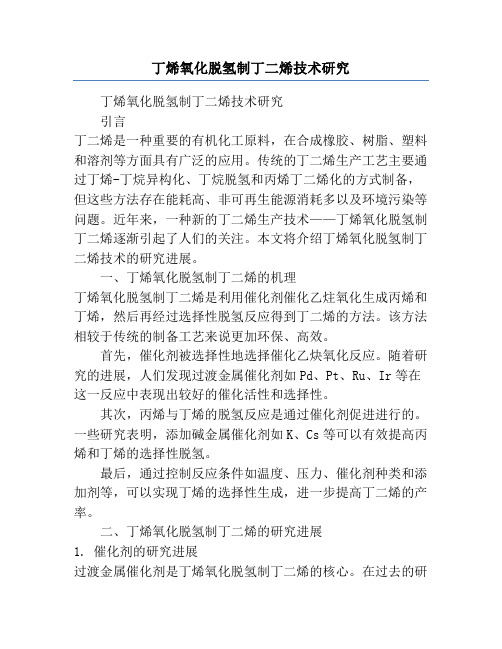
丁烯氧化脱氢制丁二烯技术研究丁烯氧化脱氢制丁二烯技术研究引言丁二烯是一种重要的有机化工原料,在合成橡胶、树脂、塑料和溶剂等方面具有广泛的应用。
传统的丁二烯生产工艺主要通过丁烯-丁烷异构化、丁烷脱氢和丙烯丁二烯化的方式制备,但这些方法存在能耗高、非可再生能源消耗多以及环境污染等问题。
近年来,一种新的丁二烯生产技术——丁烯氧化脱氢制丁二烯逐渐引起了人们的关注。
本文将介绍丁烯氧化脱氢制丁二烯技术的研究进展。
一、丁烯氧化脱氢制丁二烯的机理丁烯氧化脱氢制丁二烯是利用催化剂催化乙炷氧化生成丙烯和丁烯,然后再经过选择性脱氢反应得到丁二烯的方法。
该方法相较于传统的制备工艺来说更加环保、高效。
首先,催化剂被选择性地选择催化乙炔氧化反应。
随着研究的进展,人们发现过渡金属催化剂如Pd、Pt、Ru、Ir等在这一反应中表现出较好的催化活性和选择性。
其次,丙烯与丁烯的脱氢反应是通过催化剂促进进行的。
一些研究表明,添加碱金属催化剂如K、Cs等可以有效提高丙烯和丁烯的选择性脱氢。
最后,通过控制反应条件如温度、压力、催化剂种类和添加剂等,可以实现丁烯的选择性生成,进一步提高丁二烯的产率。
二、丁烯氧化脱氢制丁二烯的研究进展1. 催化剂的研究进展过渡金属催化剂是丁烯氧化脱氢制丁二烯的核心。
在过去的研究中,人们广泛探索了不同催化剂对该反应的催化活性和选择性的影响。
研究发现,Pd基催化剂表现出较好的活性和选择性,因此被认为是最有潜力的催化剂之一。
此外,制备高分散度催化剂也成为了研究的重点,以提高反应的效率和选择性。
2. 添加剂的研究进展在丁烯氧化脱氢制丁二烯的过程中,添加剂的引入对催化剂的活性和选择性起到了重要的作用。
研究表明,碱金属催化剂的引入可以提高丙烯和丁烯的选择性脱氢。
此外,添加一些促进剂如硫、氯等也能够改善催化剂的性能。
3. 反应条件的研究进展反应条件对丁烯氧化脱氢制丁二烯的反应效果具有重要影响。
温度、压力、反应物比例和催化剂用量等参数的优化可以提高反应的选择性和产率。
丁二烯生产技术现状及发展方向

丁二烯生产技术现状及发展方向1.丁烯氧化脱氢制丁二烯技术1.1反应原理在进行丁烯氧化脱氢生产丁二烯过程中,会释放出大量的热量,此时可以借助系统的提纯处理来获取丁二烯,丁烯完全氧化后可以得到一氧化碳、二氧化碳和水。
但是在实际反应过程中受多方面因素影响,从而导致氧化反应发生一系列的变化,最终得到多种含氧化合物。
氧化降解后会生成丙酮、甲醛等氧化合物,氧化生成四个碳原子的含氧化合物,如丁烯醛、丁酮等。
在进行深度氧化反应过程中,脱氢后可以得到乙烯基乙炔等产物,然后通过一系列的氧化后可以得到二氧化碳、一氧化碳和水等產物,该阶段所生成的产物与副产物又能够通过凝结聚合形成新的产物。
1.2工艺流程丁烯氧化脱氢制丁二烯的工艺生产流程主要包括油吸收和氧化脱氢反应两个单元。
其中氧化脱氢反应单元又能够细分为反应、水冷以及洗醛三个主要环节。
图一所示为氧化脱氢反应单元的主要流程示意图。
在反应器内,丁烯与空气在催化剂的作用下发生反应,从而生成丁二烯以及醛酸等一系列副产物。
由于整个反应为放热反应,为了避免放热温度过高对反应温度造成影响,需要在反应器内注入大量蒸汽,从而有效控制反应温度,以此来有效延长催化剂的操作周期。
之后对反应器生成的产物借助水冷塔进行冷却处理,将复合产物中的酸成分分离,再通过生成器压缩机对水冷后生成气进行加压,在洗醛塔中加压水洗清除产物中的醛和酮成分,最后将生成气引入油吸收系统进行下一个生成环节。
图二所示为油吸收单元的基本操作流程,通过油吸收单元可以有效分离和剔除生成气中的C4烃。
通常情况下,油吸收单元需要先进行吸收油吸收,随后开展重吸收油吸收,这样可以有效地减少C4以及吸收油的损耗。
在吸收塔中洗醛塔顶产生的C4物料与吸收油进行逆流接触,而C4相关物料能够溶于吸收油,从而在解析塔中被吸收油分解提取。
塔顶的C4物料能够直接参与到丁二烯抽提单元,该过程中塔釜的吸收油能够循环使用,并且还可以与尾气混合在一起进入重油吸收系统并进行二次抽取和循环利用,进一步对尾气中的C4物料进行收集和提取,并回收,从而有效提高吸收油的再利用效率。
正丁烯氧化脱氢成丁二烯的方法[发明专利]
![正丁烯氧化脱氢成丁二烯的方法[发明专利]](https://img.taocdn.com/s3/m/be9009f0866fb84ae55c8dc8.png)
专利名称:正丁烯氧化脱氢成丁二烯的方法
专利类型:发明专利
发明人:P·格鲁尼,W·鲁廷格尔,C·施密特,C·瓦尔斯多夫申请号:CN201480038902.2
申请日:20140707
公开号:CN105377796A
公开日:
20160302
专利内容由知识产权出版社提供
摘要:本发明涉及正丁烯氧化脱氢成丁二烯的方法,所述方法包括两个或更多个生产步骤(i)和至少一个再生步骤(ii)。
在所述方法中:(i)在生产步骤中将包含正丁烯的起始气体混合物与含氧气体混合,并使混合气体在固定床反应器中在220-490℃的温度下与包含至少钼和其它金属的多金属氧化物催化剂接触。
在固定床反应器的出口处得到至少包含丁二烯、氧气和蒸汽的产物气体混合物,和(ii)在再生步骤中通过使含氧再生气体混合物在200-450℃的温度下通过催化剂固定床并烧掉沉积在催化剂上的碳而使多金属氧化物催化剂再生。
再生步骤(ii)在两个生产步骤(i)之间进行,其中固定床反应器出口处的产物气体混合物中的氧含量为至少5体积%且生产步骤(i)的持续时间不多于1000小时。
申请人:巴斯夫欧洲公司
地址:德国路德维希港
国籍:DE
代理机构:北京市中咨律师事务所
更多信息请下载全文后查看。
- 1、下载文档前请自行甄别文档内容的完整性,平台不提供额外的编辑、内容补充、找答案等附加服务。
- 2、"仅部分预览"的文档,不可在线预览部分如存在完整性等问题,可反馈申请退款(可完整预览的文档不适用该条件!)。
- 3、如文档侵犯您的权益,请联系客服反馈,我们会尽快为您处理(人工客服工作时间:9:00-18:30)。
六、正丁烯氧化脱氢制丁二烯丁二烯是最简单的具有共轭双键的二烯烃,易发生齐聚和聚合反应,也易与其它具有双键的不饱和化合物共聚,因此是重要的聚合物单体,主要用来生产合成橡胶,也用于合成塑料和树脂,丁二烯的主要用途见表3-2-22。
表3-2-22丁二烯的主要用途1.生产方法(1)从烃类热裂解制低级烯烃的副产C4馏分得到。
目前获取丁二烯的最经济和最主要的方法。
C4馏分产量约为乙烯的30%~50%,其中丁二烯含量可高达40%左右。
由C4馏分制取丁二烯的一种分离方案示于图3-2-37。
由于C4馏分各组分的沸点相近(正丁烯,异丁烯和丁二烯的沸点分别为-6.3,-6.9和-4.4℃),工业上通常采用萃取精馏法将它们分离,所用的萃取剂有:N-甲基吡咯烷酮,二甲基甲酰胺和乙腈等。
图3-2-37 由C4馏分制取丁二烯的工艺过程(2)由乙醇生产丁二烯乙醇合成丁二烯的总反应式为实际上反应经过一系列阶段属气-固相催化反应,在常压或减压下进行,从丁二烯中分离出的乙醛返回反应系统。
世界上采用本法生产丁二烯的不多。
(3)由正丁烷和正丁烯脱氢生产丁二烯正丁烷脱氢是连串可逆反应脱氢反应第一阶段得到三种正丁烯异构体,第二阶段三种丁烯异构体继续脱氢得到1,3-丁二烯。
两个阶段的热效应分别为-126kJ/mol和-113.7kJ/mol。
脱氢是吸热而且是摩尔数增加的反应,因而采用高温和低压(甚至负压)对脱氢反应是有利的,由于高温下副反应激烈,副产物增加,故要采用催化活性高,选择性好的催化剂。
如同乙苯脱氢一样,在反应第二阶段尚需添加水蒸气以降低丁烯的分压,提高反应平衡转化率,减少副反应(特别是丁烯热分解以及缩聚成焦反应),帮助清除催化剂表面结炭以及为脱氢反应提供热量等。
由于烯烃缩聚成焦反应比较利害,为保持催化剂活性,需频繁再生,因此脱氢周期较短,一般为几小时,甚至几分种,需专门设置再生器或设置几台(一般为2~3台)反应器切换输流使用,为此需要设置复杂的自动控制系统。
将正丁烷脱氢制丁二烯分二步进行的方法称为二步脱氢法。
由正丁烷脱氢制混合丁烯为第一步,在540~550℃,0.12MPa下进行,采用负载在氧化铝上的氧化铬催化剂(氧化铬含量为10%~20%,甚至高达40%),助催化剂是氧化钾、氧化铈、氧化铍、氧化锆、氧化铯和氧化铷等。
这种铝铬催化剂对水很敏感,要求原料必须严格脱水。
脱氢反应器和再生器均为沸腾床反应器,丁烷单程转化率41%~45%,选择性71%~74%,丁烯和丁二烯单程收率30%~32%(其中含2.5%的丁二烯)。
未转化的原料丁烷经回收后循环使用。
经与原料丁烷分离后的混合丁烯,进入正丁烯脱氢制丁二烯系统(即第二步),采用铁系催化剂(例如Shell 205)和磷酸铬钙镍催化剂,反应温度650℃左右,水蒸气-正丁烯(重量)为8~20∶1。
单程转化率20%~30%,选择性75%~85%,丁二烯单程收率25%左右。
采用两台并联的绝热式反应器,脱氢和再生轮流切换使用。
由于使用大量水蒸气,第二步能耗大约是第一步的5倍,从而使整个脱氢过程生产成本大大提高。
由正丁烷在同一台反应器内经二次脱氢直接制取丁二烯的方法称为一步脱氢法。
采用铝铬催化剂,反应温度590~630℃,压力0.017MPa,正丁烷单程转化率约20%,选择性约60%,丁二烯单程收率约11.1%,并联5~8台绝热式反应器,脱氢和再生轮流切换使用。
由于不配入水蒸气,催化剂极易因表面结炭而失活,操作周期仅为13~22.5分种,其中接触脱氢5~9分钟,水蒸气吹扫1.5~1.8分钟,再生5~9分钟,再生气排空1.5~2.7分钟,因而阀门切换频繁,自控要求高。
一步脱氢法省去了回收丁烷的工序和设备,原料丁烷消耗比二步脱氢法低得多(一步法为1.9t/t丁二烯,二步法为2.2~2.4t/t丁二烯),能量消耗也低,因此生产成本低,经济性比二步法好。
在工业上有较强的竞争力。
二步脱氢法或一步脱氢法得到的脱氢接触气,首先利用沸点差,采用蒸馏方法脱除甲烷、氢、C3馏分和C5及C5以上馏分,得到的丁烷-丁烯-丁二烯馏分因沸点接近,常用萃取蒸馏法分离。
(4)正丁烯氧化脱氢法制丁二烯在脱氢反应气中加入适量的氧来迅速除去脱氢反应中产生的氢,这就是氧化脱氢法。
它有利于化学平衡和反应速度的提高。
氧化脱氢法有如下优点:①反应温度较低正丁烯制丁二烯只需400~500℃,比通常的脱氢反应低100~200℃;②通常脱氢是吸热反应(约126kJ/mol),需补给热量,而氧化脱氢却是放热的,可省去原先的供热设备;③由于催化剂在较低温度和氧气氛下工作,结炭极少,所以催化剂没有必要再生就可以长期运转;④在通常脱氢反应中,压力对平衡转化率有很大影响,但在氧化脱氢时,压力影响甚微,所以减压或用水蒸气稀释并非一定必要;⑤由于使用温度较低,有可能让转化率及选择性都获得提高。
在通常的脱氢法中,升高温度转化率可以提高,但选择性因副反应激烈往往是下降的。
因此,烃类的氧化脱氢工艺有着光明的前景。
氧化脱氢法虽具有上述优点,但已实现工业化的仅为正丁烯氧化脱氢制丁二烯,甲醇氧化脱氢制甲醛等少数几个化工工艺。
其中最关键的问题是控制氧化深度。
如果氧化过剧,不仅把脱下的氢氧化掉,而且可把原料烃和脱氢产物也氧化,生成CO2和CO,并放出大量热,使反应温度难于控制,酿成”飞温"和爆炸事故。
所以要求催化剂不仅具有相当的脱氢能力,并且供氧活性只足够和表面上吸附氢作用而不足以氧化产物,脱氢中间体抑或原料烃类。
现在,随着清洁燃料需求量的增加,生产烷基化汽油和MTBE(甲基叔丁基醚)所需的异丁烷和异丁烯的量猛增,将由石油烃热裂解获得的C4馏分或丁烷脱氢馏分进行切割以获取纯度较高的异丁烷和异丁烯势在必行,由此得到的纯度较高的正丁烯用来进行氧化脱氢,不仅工艺技术上是可行的,而且在资源的利用上也是合理的。
表3-2-23示出了催化脱氢法和氧化脱氢法的比较表3-2-23 催化脱氢法和氧化脱氢法的比较由表3-2-23可见,氧化脱氢法原料单耗小,蒸气单耗低,技术经济指标比催化脱氢法优越。
2.正丁烯氧化脱氢工艺原理(1)化学反应正丁烯氧化脱氢生成丁二烯的主反应是一个放热反应。
其氧化脱氢反应的平衡常数与温度的关系式为由上式可知,该反应在任何温度下平衡常数均很大,实际上可视为一个不可逆反应,因此反应的进行不受热力学条件的限制。
主要的副反应有:①正丁烯氧化降解生成饱和及不饱和的小分子醛、酮、酸等含氧化合物,如甲醛、乙醛、丙烯醛、丙酮、饱和及不饱和低级有机酸等;②正丁烯氧化生成呋喃,丁烯醛和丁酮等;③完全氧化生成一氧化碳,二氧化碳和水;④正丁烯氧化脱氢环化生成芳烃;⑤深度氧化脱氢生成乙烯基乙炔,甲基乙炔等;⑥产物和副产物的聚合结焦。
上述副反应的发生,与所采用的催化剂有关。
使用钼酸铋系催化剂,含氧副产物较多,尤其是有机酸的生成量较多(2%~3%),使用铁酸盐尖晶石催化剂时,含氧副产物总生成率小于1%。
但在该催化剂上会发生深度氧化脱氢生成炔烃,它们给丁二烯的精制带来困难。
(2)催化剂和催化机理工业应用的正丁烯氧化脱氢催化剂主要有两大系列。
A.钼酸铋系列催化剂是以Mo-Bi 氧化物为基础的二组分或多组分催化剂,初期用的是Mo-Bi-O二组分和Mo-Bi-P-O三组分催化剂,但活性和选择性都较低,后经改进,发展为六组分,七组分或更多组分的混合氧化物催化剂,例如Mo-Bi-P-Fe-Ni-K-O,Mo-Bi-P-Fe-Co-Ni-Ti-O等,催化活性和选择性均有明显的提高.在适宜的操作条件下,采用六组分混合氧化物催化剂,正丁烯转化率可达66%,丁二烯选择性为80%,这类催化剂中Mo或Mo-Bi氧化物是主要活性组分,其余氧化物为助催化剂,用以提高催化剂活性,选择性和稳定性(寿命)。
常用的载体是硅胶。
如上所述,这类催化剂的主要不足之处是副产较多的含氧化合物(尤其是有机酸),经分离它们成为三废,会污染环境。
B.铁酸盐尖晶石系列催化剂ZnFe2O4,MnFe2O4,MgFe2O4,ZnCrFeO和Mg0.1Zn0.9Fe2O4(原子比)等铁酸盐4具有尖晶石型(A2+Be3+O4)结构的氧化物是60年代后期开发的一类正丁烯氧化脱氢催化剂。
据研究,在该类催化剂中α-Fe2O3的存在是必要的,不然催化剂的活性就会很快下降。
铁酸盐尖晶石系列催化剂具有较高的催化活性和选择性。
含氧副产物少,转化率可达70%,选择性达90%或更高。
C.其他主要有以Sb或Sn氧化物为基础的混合氧化物催化剂。
例如Sb2O3-SnO2等。
中国兰州化物所研制的Sn-P-Li(原子比为2∶1∶0.6~1.0)催化剂,正丁烯转化率达95%左右。
丁二烯选择性为89%~94%,丁二烯收率85%~90%,但含氧化合物较高,占正丁烯总量的3%~5%。
在不同催化剂上进行的反应历程(机理)是不同的。
现以铁酸盐尖晶石催化剂为例说明正丁烯的氧化脱氢机理.反应步骤如下图所示:正丁烯分子吸附在催化剂表面Fe3+附近的阴离子缺位上(以表示),氧则解离为O-形式吸附在毗邻的另一缺位上。
吸附的丁烯在O-的作用下,先以均裂方式去掉一个α-H,并与O-结合,再以异裂方式脱掉第二个α-H而形成C4H6-,脱去的第二个氢则与晶格氧相结合。
所形成的C4H-6与Fe3+发生电子转移而转化为产物丁二烯并从催化剂表面解吸出来,而Fe3+则被还原为Fe2+。
所形成的两个OH基则结合生成H2O,同时产生一个缺位。
气相氧吸附在此缺位上发生解离吸附形成O-,同时使Fe2+氧化成Fe3+,因而形成氧化-还原催化循环。
Fe3+对氧化脱氢有活性,如还原为Fe2+活性就迅速衰退。
Fe2+对氧化脱氢没有活性,正丁烯吸附在Fe2+上,只能被完全氧化为CO2,因此在氧化脱氢反应中,必须避免Fe3+的过度还原。
在铁酸盐尖晶石催化剂中锌离子和铬离子的存在有利于促进氧化-还原的循环,避免Fe2+的生成。