轮胎胎面胶加工
轮胎胎面胶配方

1 背 景技 术
高 的额 定 负荷 ,所 以胎面 生热 量显 著增 加 。 关 于 提高 在 高 负荷 、高滑 移 速 度和 急 转 弯 下 的耐 磨 性 ,有 专 利 文 献 ( 例 如 日 本 专 利 特 开 2 0 0 0 — 3 0 1 9 0 8和特 开 2 0 0 1 — 2 5 3 9 7 4 )提 出 了采 用 高 质 量份 的高顺 式 结构 含 量 的 聚丁 二 烯橡 胶 ,采 用
要求 防止 由于在 滑 行 中 的急 转 弯等 造 成 的大 变 形 而产 生 的崩 花 ( 花纹 端部 缺 胶) 。在着 陆 时 ,有 必 要 防止 由于激 烈 的 滑 移 、开始 着 陆 时胎 面 对 滑 行 道 的长 时 间滑 移 和 划 痕而 造成 的胎 面早 期 磨 耗 , 特 别 是 防止造 成人 字形 割 口等 。 另 外 ,在 直线 电动 机汽 车 轮 胎 中 ,会 由于直 线 电动 机汽 车 在 紧 急着 陆 时 的胎 面 大变 形 和大 负
过去, 飞 机和 直线 电动 机汽 车 ( 磁 悬浮 车)等 用 的 高速 高 负荷 轮 胎 存 在着 要 兼 顾在 严 苛 条件 下 的耐磨 性 、生 热耐 久 性 、抗 人 字 形割 口性 和抗 崩
花 性等 的 问题 。例 如 ,在航 空 轮胎 异 常 的过 载 起
飞着 陆 时 ,由于 胎面 会承 受 大 的变 形和 大 的负荷 , 所 以胎 面 生 热量 极 大 ,有 必 要 防止 在翻 新 胎 面 的 粘 合面 间产 生粘 合 剥 离 。另 外 ,在 正 常情 况 下 ,
第 2期
李汉堂 .轮胎胎面胶配方
3 7
轮胎胎 面胶配 方
李 汉堂 编 译
摘
要: 本发 明提供 一种 飞机 和直 线电动机 汽车等用的高速高负荷轮胎 , 特别 是提供适 用于飞机 的轮胎 。
轮胎翻新加工起死回生变废为宝

轮胎翻新加工起死回生变废为宝刘道春众所周知,处理和利用废旧轮胎主要有两大途径,一是旧轮胎翻新;二是废轮胎的综合利用。
所谓轮胎翻新用简单的一句话来描述,就是挑选并检测花纹磨平的轮胎(即胎体)然后附加上新的胎面的加工过程。
翻新是利用废旧轮胎的主要和最佳方式,就是将已经磨损的、废旧轮胎的外层削去,粘贴上胶料,再进行硫化,重新使用,受到了社会的广泛关注。
1.轮胎翻新就是资源的循环利用当下,轮胎翻新是一个已经比较成熟的工业,轮胎翻新效益大,好处多。
翻新是发达国家处理废旧轮胎的主要方式,目前世界翻新轮胎年产量约8000多万条,为新胎产量的7%。
自从20世纪初其诞生以来,该行业一直稳步发展。
据报道,至今在整个北美洲大约有1400个轮胎翻新厂。
这些轮胎翻新厂的规模大大小小、多种多样,小型工厂每日翻新20多条汽车轮胎,大型的工厂每天可生产2600条或更多的翻新轮胎。
此外,还有一些翻新轮胎厂只翻新一些专用轮胎如农业机械和土木工程机械的工程胎。
所有这些厂加起来每年可翻新3000多万条轮胎,消耗5亿6千万磅合成胶和天然胶,销售额超过20亿美元/年。
翻新轮胎被广泛应用于民航、美国军用飞机、学校大巴和各种急救车。
汽车运输公司已基本依靠翻新轮胎用于长途运输。
通过在实验室的模拟试验和在所有新胎可以使用的地方,同样的用翻新轮胎进行多年的实际使用,事实证明,翻新轮胎与新轮胎一样安全可靠和经久耐用。
据了解,我国每年生产3亿条、几百万吨新轮胎。
生产1吨低端轮胎需要3~4吨石油,生产1吨高端轮胎约需8吨石油。
翻新一条旧轮胎所消耗的原材料,只相当于制造同等规格新胎的30%左右,价格也仅为新胎的30%左右。
这对于我国这样一个近60%的石油和70%以上天然橡胶需要进口的国家,如果不对废旧轮胎加以高效利用,相当于每年扔掉几千万吨石油,浪费一座大庆油田的年产油量。
长途汽车运输公司是翻修轮胎的主要市场。
如果不能对轮胎进行翻新利用,他们的利益定会受到严重的影响。
抗切割型矿用轮胎胎面胶配方优化
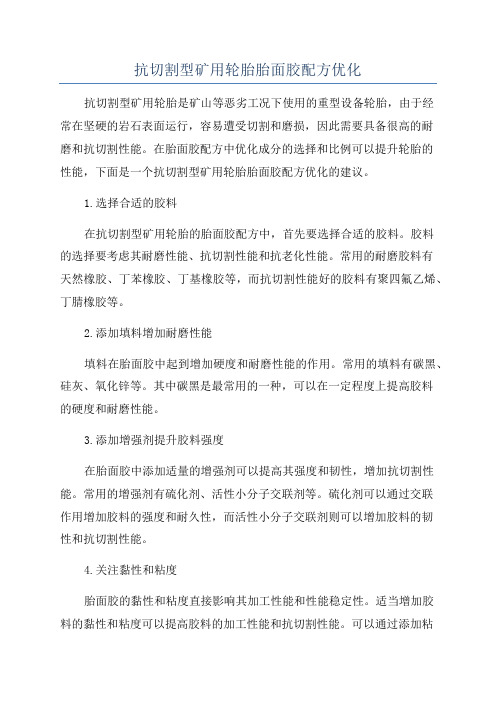
抗切割型矿用轮胎胎面胶配方优化抗切割型矿用轮胎是矿山等恶劣工况下使用的重型设备轮胎,由于经常在坚硬的岩石表面运行,容易遭受切割和磨损,因此需要具备很高的耐磨和抗切割性能。
在胎面胶配方中优化成分的选择和比例可以提升轮胎的性能,下面是一个抗切割型矿用轮胎胎面胶配方优化的建议。
1.选择合适的胶料在抗切割型矿用轮胎的胎面胶配方中,首先要选择合适的胶料。
胶料的选择要考虑其耐磨性能、抗切割性能和抗老化性能。
常用的耐磨胶料有天然橡胶、丁苯橡胶、丁基橡胶等,而抗切割性能好的胶料有聚四氟乙烯、丁腈橡胶等。
2.添加填料增加耐磨性能填料在胎面胶中起到增加硬度和耐磨性能的作用。
常用的填料有碳黑、硅灰、氧化锌等。
其中碳黑是最常用的一种,可以在一定程度上提高胶料的硬度和耐磨性能。
3.添加增强剂提升胶料强度在胎面胶中添加适量的增强剂可以提高其强度和韧性,增加抗切割性能。
常用的增强剂有硫化剂、活性小分子交联剂等。
硫化剂可以通过交联作用增加胶料的强度和耐久性,而活性小分子交联剂则可以增加胶料的韧性和抗切割性能。
4.关注黏性和粘度胎面胶的黏性和粘度直接影响其加工性能和性能稳定性。
适当增加胶料的黏性和粘度可以提高胶料的加工性能和抗切割性能。
可以通过添加粘合剂和增塑剂来调整黏性和粘度,如添加天然树脂或热塑性弹性体(TPE)。
5.改善胶料的耐老化性能长期暴露在恶劣工况下的矿用轮胎容易受到紫外线、氧气、油脂等因素的影响而老化。
通过添加抗氧化剂、紫外线吸收剂和抗裂剂等可以提高胎面胶的耐老化性能。
抗氧化剂可以防止胶料的老化以及硫化过程中的氧化反应,紫外线吸收剂可以吸收或散射紫外线,抗裂剂可以防止胶料发生裂纹。
总之,对抗切割型矿用轮胎胎面胶的配方进行优化,可以通过选择合适的胶料、添加填料、增强剂、粘合剂、增塑剂和改善耐老化性能的添加剂来提升轮胎的耐磨和抗切割性能,以满足恶劣工况下轮胎的使用要求。
彩色力车胎面胶配方

课题:彩色胎面胶配方设计班级:高分子122班组别:第一组组长:曹娟组员:张东方陈凤姣丁梓耕冯骁骁冯学帅郭倩指导老师:张小萍彩色胎面胶的使用条件分析轮胎最外层与路面接触而表面印有花纹的一层胶料。
能使轮胎具有牵引力,缓冲行驶时的冲击和摇摆,防止帘线层的割破和刺穿等。
要求具有高度的耐磨性、耐疲劳性能,良好的耐老化性能,较高的拉伸强度、弹性和强韧性,以及行驶时低的生热性。
可用天然橡胶、丁苯橡胶、顺式异戊橡胶和顺丁橡胶等生胶制造。
胶料中常加入大量炭黑,以提高其物理机械性能。
可将胶料用螺杆压出机压出或用压延机压延经冷却而成。
前法所制的胎面胶,质量较优,生产能力也较大。
一般来说,胎面配方要具有较好耐磨性能,从物理性能上应具备以下几个特点:▪①合适的定伸应力,▪②较高的拉伸强度和伸长率,▪③合适硬度,▪④较高抗撕裂性能,▪⑤较高的抗屈挠龟裂性能。
胎面胶性能指标和检测项目确定(GB/T1702-2008 力车轮胎)通过以上资料的查阅和对彩色力车胎胎面胶的综合分析,确定彩色力车胎胎面胶胶料的性能指标为:拉伸强度>8.0MPa扯断伸长率>350N/m阿克隆磨耗量≤1.2彩色力车胎胎面胶配方设计分析概述彩色力车胎胎面胶配方的设计重点应考虑胶料的耐磨性、低成本性和易加工性。
通过在胎面胶配方中采用NR与SBR 并用的生胶体系, 来满足上述性能要求, 而填充白炭黑和加工油, 既保证了胶料具有一定的物理性能, 又能拥有良好的混炼、挤出和成型等工艺性能三.彩色胎面胶胶料的配方设计及配方选材的分析与论证胶鞋大底胶料的配方分析与论证1):生胶体系的选择橡胶并用:使用天然橡胶与丁苯胶并用结合天然橡胶滞后损失小,在多次变形时生热低,丁苯橡胶的耐热性,抗湿滑性好和优良的抓着性混炼后的胶料的性能,拉伸强度很高,可以拉很长而不断裂,还具有一定回弹性。
(2):硫化体系的选择半有效硫化体系改善硫化胶的抗热氧老化和动态疲劳性能,所得到硫化胶既具有适量的多硫键,又有适量的单双硫交联键,故选用半有效硫化体系。
橡胶轮胎的配方和工艺流程-成型加工[指南]
![橡胶轮胎的配方和工艺流程-成型加工[指南]](https://img.taocdn.com/s3/m/eab2d009c4da50e2524de518964bcf84b9d52dad.png)
橡胶轮胎的原料配方和合成工艺流程一概述轮胎是供给车辆、农业机械、工程机械行驶和飞机起落等用的圆环形弹性制品。
它是车辆、农业机械、工程机械和飞机等的主要配件,能吸收因路面不平产生的震动和外来冲击力,使得乘坐舒适。
轮胎是橡胶工业中的主要制品,其消耗的橡胶量占橡胶总用量的50%-60%,是一种不可缺少的战略物资。
轮胎工业的发展可以追溯到16世纪初,在巴西发现天然橡胶后,古人用胶乳制成原始的胶球、胶鞋及各种橡胶制品。
1839年固特异发明了硫化技术,改善了橡胶的使用价值,橡胶制品得到了广泛应用。
1845年研制出硫化橡胶实心轮胎。
1890年成功试制出外胎和内胎组成的力车轮胎,胎圈内部装有金属圈,轮胎与轮辋紧密固着得以初步解决,这就是近代直角形胎圈轮胎的雏形。
1895年发明了汽车,扩大了充气轮胎的应用范围。
1904年马特发现了炭黑对橡胶具有补强作用。
1914年-1919年发明了橡胶用的有机促进剂、防老剂和帘布胶乳浸渍技术,使得轮胎的生产技术日趋成熟和完善,轮胎的质量也大为改观。
1933年法国米其林首创了用钢丝帘布制造汽车轮胎。
1948年法国米其林生产出钢丝帘布的子午线结构轮胎,并在轮胎主要设备上进行了重大的改造。
子午线结构轮胎对轮胎结构作了根本变革,是轮胎工业的一场革命。
1960年-1970年出现了聚酯纤维和芳纶纤维,并试用于轮胎。
1970年美国费尔斯通公司首先在乘用胎上试验了橡胶塑料并用的浇注轮胎,成为塑料与橡胶并用的先驱.目前我国轮胎总产量达2.1亿条左右,轮胎生产继美国,日本之后排名世界第三位,子午化率在58%.目前,米其林、固特易、普利司通、住友、韩泰、锦湖、佳通等合资企业的轮胎产量占轮胎企业总产量的50%以上。
二橡胶轮胎配方1耐高温胎面胶据资料介绍,55-75份顺式-1,4-聚异戊二烯橡胶与25-45份含量乙烯基聚丁二烯橡胶并用,课提高航空轮胎胎面的高温耐久性。
2耐割口胎面胶耐割口胎面胶配方见表1.据资料介绍,该组配方适用于航空轮胎胎面。
高分子专业生产性教学案例——胎面压出工艺
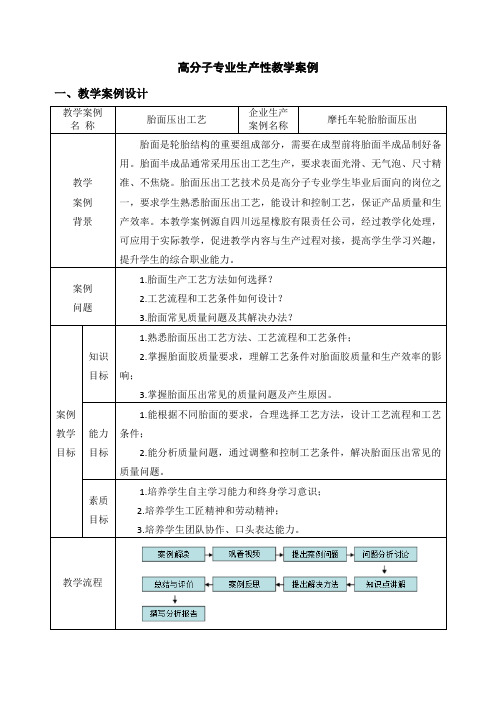
高分子专业生产性教学案例一、教学案例设计教学案例名称胎面压出工艺企业生产案例名称摩托车轮胎胎面压出教学案例背景胎面是轮胎结构的重要组成部分,需要在成型前将胎面半成品制好备用。
胎面半成品通常采用压出工艺生产,要求表面光滑、无气泡、尺寸精准、不焦烧。
胎面压出工艺技术员是高分子专业学生毕业后面向的岗位之一,要求学生熟悉胎面压出工艺,能设计和控制工艺,保证产品质量和生产效率。
本教学案例源自四川远星橡胶有限责任公司,经过教学化处理,可应用于实际教学,促进教学内容与生产过程对接,提高学生学习兴趣,提升学生的综合职业能力。
案例问题1.胎面生产工艺方法如何选择?2.工艺流程和工艺条件如何设计?3.胎面常见质量问题及其解决办法?案例教学目标知识目标1.熟悉胎面压出工艺方法、工艺流程和工艺条件;2.掌握胎面胶质量要求,理解工艺条件对胎面胶质量和生产效率的影响;3.掌握胎面压出常见的质量问题及产生原因。
能力目标1.能根据不同胎面的要求,合理选择工艺方法,设计工艺流程和工艺条件;2.能分析质量问题,通过调整和控制工艺条件,解决胎面压出常见的质量问题。
素质目标1.培养学生自主学习能力和终身学习意识;2.培养学生工匠精神和劳动精神;3.培养学生团队协作、口头表达能力。
教学流程二、教学案例相关知识(一)胎面压出对胎面胶的质量要求1.压出胎面胶断面尺寸应符合施工标准。
因为施工标准是根据成品的设计要求确定的,如果达不到要求,将影响产品质量和原料消耗定额。
2.胎面胶胶料致密性好、无气泡、表面平整、无疤痕、无裂缝、无水渍、无杂质、无焦烧和喷霜现象。
否则硫化过程中,影响胶料的流动性,产生外观缺陷,降低胎面胶与胎体的附着力。
3.胎肩两侧对称,不得有凹凸不平,不得有短边等缺陷。
4.存放时间不小于4h,不大于60h,先压出先用。
(二)压出工艺方法1.单层整体压出特点:采用一种配方的胶料,通过一台挤出机压出。
管理方便,但不能充分发挥胎面各部位胶料的作用,仅适用于小规格轮胎胎面生产。
轮胎成型工艺

第二章 轮胎的成型工艺
(一)轮胎制造工艺流程和准备工艺 1、胎面压出 (3)胎面压出工艺条件
冷却 半成品胎面的冷却程度影响压出质 量。胎面胶压出离开口型时,胶温高达 120℃以上,极易产生热变形,加速其收缩 定型;影响规格尺寸的稳定性,同时在存 放过程中容易焦烧,因此,必须将胶温降至 40℃以下,才能获得充分冷却。
帘线跳线、弯曲 产生原因由于胶料热炼不足,胶料软硬程度不均匀;帘线受潮 后伸张不一致,造成纬线松紧不等;中辊积胶过多,局都受力过大;卷取时布卷 过松等因素造成。
帘布打折 产生原因由于压延速度和冷却辊速度不一致,两边续布操作不一致; 帘布伸张不均匀或垫布卷取过松所致。
压延帘布厚薄不均匀 产生原因是出于辊距调节不当,两边不等;辊温不稳定; 压延速度与冷却速度配合不一是致;胶料可塑度不均所致。
当,夹入空气;压出温度过高;压出速度过快,供胶不足。 胎面断面尺寸、重量不符合要求 产生原因为:压出口型板安装不正;
口型板变形;热炼温度和压出温度掌握不正;压出速度不均匀或联 动装置配合不当;压出后冷却不足;热炼不充分。 焦烧 产生原因为:胶料配方设计不当,焦烧性能差;热炼和压出温度 过高;机头中有积胶、死角或冷却水不通;供胶中断;空车滞料。 断边烂边 产生原因为:热炼不足,胶料可塑性小;胶料焦烧;胎面口型 边部流胶口小或堵塞;机头、口型板温度低。
↓
内胎硫化
欧洲市场Premium HP夏季轿车子午线轮胎胎面胶配方的开发

欧洲市场Premium HP夏季轿车子午线轮胎胎面胶配方的开发王建功,黄义钢,张锡熙,赵晓东(青岛双星轮胎工业有限公司,山东青岛 266400)摘要:介绍欧洲市场Premium HP夏季轿车子午线轮胎胎面胶配方的开发情况。
试验结果表明:采用高相对分子质量、高苯乙烯含量的溶聚丁苯橡胶(SSBR)并用低相对分子质量、低苯乙烯含量SSBR,同时高填充高分散性白炭黑,胶料的加工性能良好,硫化胶的各项性能满足轿车子午线轮胎基本性能要求;成品轮胎的抗湿滑性能提高,滚动阻力降低,其中抗湿滑等级和滚动阻力等级可分别达到欧盟轮胎标签法的A级和C级。
关键词:轿车子午线轮胎;胎面胶;溶聚丁苯橡胶;高分散性白炭黑;抗湿滑性能;滚动阻力;轮胎标签法中图分类号:TQ333.1;U463.341+.4/.6 文章编号:1006-8171(2021)05-0315-05文献标志码:A DOI:10.12135/j.issn.1006-8171.2021.05.0315自2012年欧盟强制实施轮胎标签法以来,全球各大轮胎制造企业致力于提高自有品牌轮胎性能,以达到更高轮胎标签等级,从而提升品牌竞争力[1]。
2018年5月17日,欧盟委员会发布了修订版No.1222/2009法规提案,即新版轮胎标签法。
新版轮胎标签等级在现有基础上对轮胎的抗湿滑性能和滚动阻力等提出了更为严苛的要求[2]。
本工作将开发针对欧洲市场Premium HP夏季轿车子午线轮胎胎面胶的新配方,考虑其应用条件及新版轮胎标签法的要求,着重提高轮胎的抗湿滑性能,同时兼顾降低滚动阻力。
1 设计思路和技术目标1.1 设计思路明确欧洲市场Premium HP夏季轿车子午线轮胎产品定位,以高抗湿滑性能为主,兼顾低滚动阻力及其他性能。
由于溶聚丁苯橡胶(SSBR)对胎面胶配方设计“魔三角”(抗湿滑性能、滚动阻力和耐磨性能)有较好的平衡作用,因此广泛应用于轿车子午线轮胎胎面胶中。
其微观结构对胶料性能会产生不同影响,分子链苯乙烯含量越大,相对分子质量越大,玻璃化温度(T g)越高,对抗湿滑性能的贡献越大,但滚动阻力相应增大,反之则相反[3-5]。
一种轮胎胎面胶及其制备方法
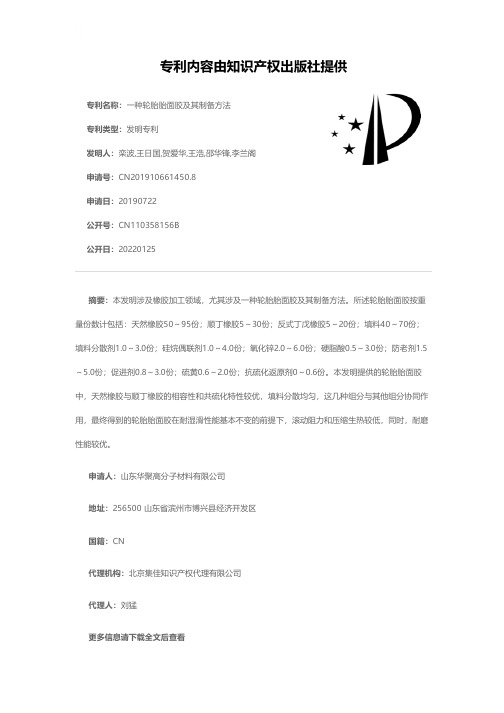
专利名称:一种轮胎胎面胶及其制备方法
专利类型:发明专利
发明人:栾波,王日国,贺爱华,王浩,邵华锋,李兰阁申请号:CN201910661450.8
申请日:20190722
公开号:CN110358156B
公开日:
20220125
专利内容由知识产权出版社提供
摘要:本发明涉及橡胶加工领域,尤其涉及一种轮胎胎面胶及其制备方法。
所述轮胎胎面胶按重量份数计包括:天然橡胶50~95份;顺丁橡胶5~30份;反式丁戊橡胶5~20份;填料40~70份;填料分散剂1.0~3.0份;硅烷偶联剂1.0~4.0份;氧化锌2.0~6.0份;硬脂酸0.5~3.0份;防老剂1.5~5.0份;促进剂0.8~3.0份;硫黄0.6~2.0份;抗硫化返原剂0~0.6份。
本发明提供的轮胎胎面胶中,天然橡胶与顺丁橡胶的相容性和共硫化特性较优,填料分散均匀,这几种组分与其他组分协同作用,最终得到的轮胎胎面胶在耐湿滑性能基本不变的前提下,滚动阻力和压缩生热较低,同时,耐磨性能较优。
申请人:山东华聚高分子材料有限公司
地址:256500 山东省滨州市博兴县经济开发区
国籍:CN
代理机构:北京集佳知识产权代理有限公司
代理人:刘猛
更多信息请下载全文后查看。
出工序胎面胶焦烧原因分析及解决措施

万方数据
挤出工序胎面胶焦烧原因分析及解决措施
作者: 作者单位: 刊名: 英文刊名: 年,卷(期): 李凌峰, LI Ling-feng 山东泰山轮胎有限公司,山东,肥城,271600 橡胶科技市场 CHINA RUBBER SCIENCE AND TECHNOLOGY MARKET 2010,8(5)
000
第2种形式胶料焦烧的解决措施:(1)调整胶 料混炼工艺,严格控制密炼排胶温度为145~ 165℃;(2)挤出过程中产生的返回胶、机头胶要 经切割、薄挤并确认安全后,按不超过10%的比 例掺入挤出胶料中。 第3种和第4种形式胶料焦烧的解决措施: (1)严格控制烟片胶烘胶温度为30,-一60℃,烘胶 时间为24---,48 h,标准胶烘胶温度为30一..60℃, 烘胶时间为2~24 h,确保生胶门尼粘度稳定; (2)延长胶料密炼时间5~30 s,使胶料中配合剂 分散均匀,提高胶料的加工安全性;(3)适当增大 防焦剂用量;(4)严格检验和控制原材料性能指 标,原材料性能指标变化较大时要及时调整胶料 配方和生产工艺;(5)优化胶料配方,适当调整 硫化体系;(6)热炼时捣胶次数控制为3~4次; (7)保证挤出工序操作衔接顺畅、紧凑;(8)控制供 胶开炼机温度不高于85℃,胎面胶挤出温度不高
kg的焦烧胶
料,同时保证了轮胎生产的顺利进行,促进了轮胎 产品质量的提高,具有较国家自然科学基金委有机高分子材料学科于 2009年年底提出:未来5~10年,橡胶领域可望 在13个方面取得重大进展和突破。“十二五”期 间橡胶领域的11个研究方向和6个交叉领域的 研究将获优先支持。 据介绍,未来有望获得突破的13个橡胶领域 包括:基于大量的基础研究,可以从计算机上直接 设计出新型的橡胶材料,较为准确地呈现出可能 的链结构、聚集态结构、动力学特征和热力学特 征;新来源的天然橡胶以及高性能的生物基橡胶 的研制;更加节能、耐磨和抗湿滑的轮胎用新集成 橡胶材料的设计与制备;更宽温度范围使用的密 封用橡胶新材料的设计与制备;填充和交联的橡 胶复杂网络结构的科学描述;橡胶材料复杂结构 与其粘弹性能间的新本构关系的建立;橡胶磨耗 以及摩擦的新原理和新表征方法;更加节能环保 的橡胶分散和加工成型新方法;新型橡胶纳米增 强剂和交联剂的设计与制备;液体浇注高性能充 气轮胎的研制;新一代热塑性弹性体材料的研制;
防老剂BLE-W 在半钢胎胎面胶中的应用

防老剂BLE-W在半钢胎胎面胶中的应用李海艳 徐 岩 曹进忠山东丰源轮胎制造股份有限公司51中国橡胶应用技术APPLIED TECHNOLOGY(2)硫化胶的制备采用XLB-400-400型四立柱平板硫化机进行硫化,得到硫化胶。
硫化温度150℃,硫化时间42min 。
5.测试与表征按照相应国家标准,测试胶料各项性能。
二、结果与讨论1.防老剂属性检测结果本文检测中,胎面配方所用防老剂的基本性能见表2。
其中,防老剂BLE-W 中有的效成分含量为65%,因此其灰分较大,加热减量也较大。
2.小配合试验(1)胶料的硫化特性轮胎胎面胶小配合试验胶料的硫化特性见表3。
从表3可以看出,轮胎胎面配方优化后的门尼粘度略有升高,同时焦烧时间略有降低,但差别较小,差值为0.1min ,说明胎面胶料的加工性能基本无差别;优化后的配方,M L 、M H 略高,差值分别为3.2%、3.4%,且随着防老剂BLE-W 份数的增加有正向趋势,优化后配方的正硫化时间t 90略有延长,约为0.1min (1.5份防老剂BLE-W );交联程度也随着BLE-W 用量的增加呈略提高趋势。
(2)胶料的物理性能轮胎胎面胶小配合试验胶料的物理特性见表4。
从表4老化前数据可以看出,轮胎胎面胶料优化前后硬度,1份防老剂BLE-W 无差异,1.5份防老剂BLE-W 差别为1。
定伸应力方面,10%基本无差别,1份防老剂后进行开炼机加硫加工终炼。
二段开炼机混炼加料及操作顺序为:一段母炼胶→硫黄、促进剂CZ 、防焦剂CTP 等小料→打三角包翻辊4~6遍后,胎面终炼胶下片。
大料车间试验,采用SSM 低温一步法炼胶工艺。
天然橡胶等生胶料与硬脂酸、促进剂等小料在XM370型密炼机中进行预混合混炼,然后排胶到XM305型开炼机(双驱全自动)上,初步塑炼并压制成片,然后分流给4组全自动混炼开炼机进行后续混炼。
胎面胶料在每组混炼开炼机上进行自动混炼,过程包含补充混炼、胶料冷却、胶料收取等步骤。
轮胎-胶料生产基础知识

胶料生产基础知识一、轮胎简介按结构分:斜交胎和子午线轮胎(分半钢和全钢)。
简介斜交胎与子午胎,全钢子午胎,一般由三层钢丝带束层、一层钢丝胎体及肩部各两层零度带束层组成。
二、轮胎制造工艺流程炼胶工序:生产混炼胶→压延压出工序:生产半成品部件→裁断成型工序:半成品加工与组装成胎胚→硫化工序:将胎胚硫化成成品胎→成品检验:外观和X光检验三、炼胶工序工艺流程1、母胶:原材料加工、称量(小药加工、称量;炭黑油料加工输送称量;生胶烘胶加工称量)→密炼机内混炼→双螺杆挤出压片→浸隔离剂→上冷却线挂片冷却→摆片2、终炼胶:母胶称量、小药称量→密炼机内混炼→开炼机补充混炼压片→浸隔离剂→上冷却线挂片冷却→摆片四、胶料生产工艺的几个基本概念1、塑炼①塑炼是指通过机械力、热、氧或化学塑解剂作用,使生胶的分子链断裂,使其由强韧的弹性状态转变为柔软的塑性状态的工艺过程。
②生胶塑炼的目的是为了获得工艺要求的可塑性,使混炼过程中橡胶与配合剂易于混合而且分散均匀,在压延时易于渗入纤维,在挤出和成型时容易操作,胶料溶解性和粘着性得以提高,并且获得适当的流动性,使模型制品有清晰的花纹轮廓。
子午胎胶料一般不单独进行塑炼。
2、混炼①混炼是指通过炼胶机将各种配合剂均匀加入具有一定塑性的生胶中的工艺过程。
②混炼的目的是在生胶中加入各种配合剂,以提高橡胶制品的使用性能,改善加工工艺性能,节约生胶及降低成本。
③混炼胶质量要求:一是能保证成品具有良好的物理机械性能,二是应具有良好的加工工艺性能。
④混炼,目前生产中一般分为母炼和终炼,相应的胶料称为母炼胶和终炼胶。
因为胶料配方体系有些配合剂对温度敏感,高温易起反应,一般要求在较低的混炼温度。
这些配合剂如硫化剂、促进剂、防焦剂及子午胎用的部分粘合剂等。
所以一般母炼胶是指在生胶中加入除硫化剂、促进剂、防焦剂及子午胎用的部分粘合剂等所有配合剂的胶料,母炼段一般是在高温快速下进行混炼的,现一般采用大型密炼机(如GK400N)进行生产。
不同炼胶工艺对半钢轮胎磨耗性能的影响

作者简介:龙飞飞(1985-),女,研究生,工程师,主要从事半钢轮胎配方开发与研究。
收稿日期:2020-09-02伴随着一带一路战略的推进,中国经济正在不断腾飞,如翱翔在天际的巨龙,中国的汽车行业正经历着翻天覆地的变化,轮胎在欧美等发达国家都是作为重要的安全部件,并进行PPAP/APQP/DFMEA 等程序和过程控制。
轮胎是乘用车最重要的安全配件、关键零部件,轮胎的各项性能也越来越多的被关注、重视,中央电视台等主流媒体也多次对国内外轮胎进行对比采样分析。
在评价成品轮胎性能优劣的众多性能中,胎面的耐磨程度是一项重要指标,胎面的耐磨性的好坏,从机理上分析,可分析到轮胎表层的机械性能、分子结构等,涉及到物理及深层的化学变化,但其中影响最关键的因素还是由生产胎面的胶料的混炼工艺和胎面胶料所使用的配方体系构成。
轮胎胎面胶料的耐磨耗性能,是表征胎面胶料硫化后在抵抗摩擦力的作用下因胎面表面破坏而导致胶料损耗的能力。
磨耗性能属于力学性能范畴,表现为以下三种形式:(1)轮胎胎面产生的疲劳磨耗,是指行驶中的轮胎胎面在路面上反复运动的过程中受周期性的剪切、压缩、拉伸等变形作用,轮胎的表面产生疲劳,轮胎的胎面逐渐产生微裂纹进而造成胎面表面的剥落(微观)。
随着胎面胶料拉伸强度的降低,疲劳磨耗随之增大,因此轮胎胎面需要提升胶料的拉伸强度进而降低疲劳磨耗。
(2)轮胎胎面产生的磨损磨耗,是指行驶中的轮胎胎面与路面上的尖锐的粗糙物在不断地发生切割、不同炼胶工艺对半钢轮胎磨耗性能的影响龙飞飞,刘鹏,郭志钢,张聪,李海艳(山东丰源轮胎制造股份有限公司,山东 枣庄 277300)摘要:分析对比不同生产工艺条件下轮胎胎面胶的各项性能,可以看出SSM 混炼工艺生产的胎面胶白炭黑和炭黑分散度提升,胶料流动性向好,成品轮胎外观缺陷(花纹圆角、胎冠缺胶等)出现的几率降低;轮胎胎面的疲劳磨耗、胎面的磨损磨耗降低;胎面胶的磨耗体积量,SSM 混炼工艺较传统法工艺整体有大幅度降低,相比传统法提升量大于50%。
轮胎胶料配方设计
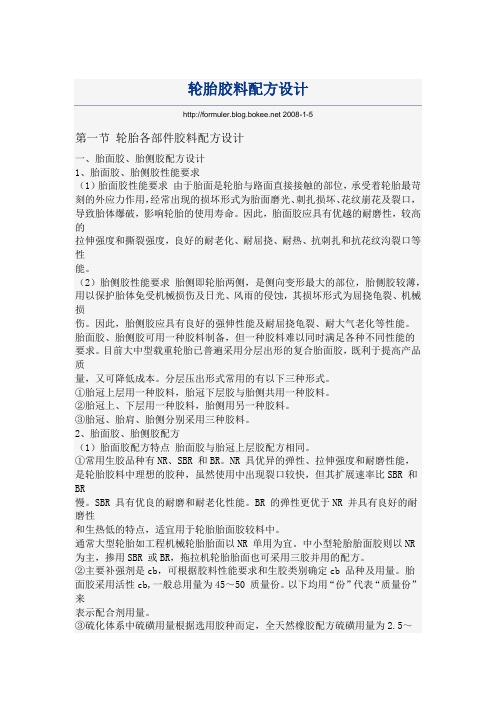
轮胎胶料配方设计 2008-1-5第一节轮胎各部件胶料配方设计一、胎面胶、胎侧胶配方设计1、胎面胶、胎侧胶性能要求(1)胎面胶性能要求由于胎面是轮胎与路面直接接触的部位,承受着轮胎最苛刻的外应力作用,经常出现的损坏形式为胎面磨光、刺扎损坏、花纹崩花及裂口,导致胎体爆破,影响轮胎的使用寿命。
因此,胎面胶应具有优越的耐磨性,较高的拉伸强度和撕裂强度,良好的耐老化、耐屈挠、耐热、抗刺扎和抗花纹沟裂口等性能。
(2)胎侧胶性能要求胎侧即轮胎两侧,是侧向变形最大的部位,胎侧胶较薄,用以保护胎体免受机械损伤及日光、风雨的侵蚀,其损坏形式为屈挠龟裂、机械损伤。
因此,胎侧胶应具有良好的强伸性能及耐屈挠龟裂、耐大气老化等性能。
胎面胶、胎侧胶可用一种胶料制备,但一种胶料难以同时满足各种不同性能的要求。
目前大中型载重轮胎已普遍采用分层出形的复合胎面胶,既利于提高产品质量,又可降低成本。
分层压出形式常用的有以下三种形式。
①胎冠上层用一种胶料,胎冠下层胶与胎侧共用一种胶料。
②胎冠上、下层用一种胶料,胎侧用另一种胶料。
③胎冠、胎肩、胎侧分别采用三种胶料。
2、胎面胶、胎侧胶配方(1)胎面胶配方特点胎面胶与胎冠上层胶配方相同。
①常用生胶品种有NR、SBR 和BR。
NR 具优异的弹性、拉伸强度和耐磨性能,是轮胎胶料中理想的胶种,虽然使用中出现裂口较快,但其扩展速率比SBR 和BR慢。
SBR 具有优良的耐磨和耐老化性能。
BR 的弹性更优于NR 并具有良好的耐磨性和生热低的特点,适宜用于轮胎胎面胶较料中。
通常大型轮胎如工程机械轮胎胎面以NR 单用为宜。
中小型轮胎胎面胶则以NR 为主,掺用SBR 或BR,拖拉机轮胎胎面也可采用三胶并用的配方。
②主要补强剂是cb,可根据胶料性能要求和生胶类别确定cb 品种及用量。
胎面胶采用活性cb,一般总用量为45~50 质量份。
以下均用“份”代表“质量份”来表示配合剂用量。
③硫化体系中硫磺用量根据选用胶种而定,全天然橡胶配方硫磺用量为2.5~2.8 份,掺用SBR 或BR 的配方,以采用低硫高促体系。
- 1、下载文档前请自行甄别文档内容的完整性,平台不提供额外的编辑、内容补充、找答案等附加服务。
- 2、"仅部分预览"的文档,不可在线预览部分如存在完整性等问题,可反馈申请退款(可完整预览的文档不适用该条件!)。
- 3、如文档侵犯您的权益,请联系客服反馈,我们会尽快为您处理(人工客服工作时间:9:00-18:30)。
轮胎胎面胶加工
轮胎是人们生活和工作中不可或缺的重要交通工具之一。
而作
为轮胎最关键的部分之一,“胎面胶”更是它的灵魂所在。
胎面胶
的质量不仅关乎轮胎的性能和寿命,而且对行车安全也有着直接
的影响。
本文将从轮胎胎面胶的加工工艺、技术与质量等方面进
行探讨。
一、胎面胶的制作工艺
轮胎胎面胶的制作工艺可以分为以下几个步骤:
1、原料准备:主要原料有橡胶、碳黑、灰石等。
其中,橡胶
是胎面胶的主要成分,碳黑是用来增加胎面胶的耐磨性和抗老化性,灰石则是用于调整胎面胶的硬度和强度。
2、混炼:将各种原料按一定比例放入混炼机中,经过高速搅
拌和切割,将所有的原料充分混合均匀,形成混合胶料。
3、压延:将混合胶料放入压延机中,通过多次的压延和拉伸,将胶料压成一定厚度的大型胶片。
4、成型:将压延好的胶片裁切成一定尺寸,再分别加工成不
同形状的轮胎胎面。
5、硫化:将成型好的轮胎胎面放入硫化炉中,经过高温高压,使轮胎胎面与钢丝帘子牢固地结合在一起,形成完整的轮胎胎面胶。
二、胎面胶的技术要求
轮胎胎面胶是轮胎最为重要的组成部分之一,对汽车的行驶性
能和安全性有着极大的影响。
因此,胎面胶的技术要求也非常高,包括以下几个方面:
1、耐磨性:轮胎胎面是汽车与地面接触的唯一部分,因此必
须具有足够的耐磨性,才能保证车辆的长期使用寿命。
2、抗老化性:轮胎在长时间使用后,会受到日晒、雨淋、温
度变化等多种因素的影响,因此必须具有一定的抗老化性,避免
出现龟裂和渗漏等问题。
3、抗冲击性:轮胎胎面要具有足够的抗冲击性,避免在行驶中因路面凹凸不平而产生鼓起或破损等现象,确保行车安全。
4、耐高温:轮胎胎面在行车过程中,会产生大量的热量,因此必须具有一定的耐高温性能,避免胎面过热导致爆胎等危险。
以上要求需要胎面胶材料具备的特定物理和化学特性,如分子链结构、化学反应性、硫化条件等要素是非常的重要的。
三、胎面胶加工的现状与趋势
目前轮胎胎面胶加工工艺主要采用混炼、压延等传统的手工工艺,但这种加工方式存在着一些制约因素,例如生产效率低、人工费用高等问题。
针对这些问题,在现代化的轮胎生产工艺中,越来越多的高科技加工技术被应用到轮胎的生产中。
例如,在轮胎胶料的配方设计方面,采用计算机模拟等先进技术,能够快速优化配方,提高胎面胶的耐磨性、抗老化性等性能。
在实际生产中,近年来越来越多的轮胎企业开始采用流延技术生产轮胎胎面胶,进行轮胎整体生产工厂智能化建设,尝试着将人工工艺转换为高科技设备的智能化生产。
同时,轮胎胎面胶加工中的误差控制也成为一个比较迫切的问题。
因而,基于机器视觉和人工智能技术,许多轮胎企业开始采用自动化的视觉系统进行误差控制,以提高轮胎胎面加工的精度和效率。
在未来,轮胎胎面胶加工也将会朝着微型化、智能化、精密化的方向发展,更加注重轮胎的“个性化定制”,根据不同车型和行驶路线的需求,生产更适合的胎面胶,以满足不同客户的需求。
总之,轮胎胎面胶加工的质量和技术水平直接关系到汽车行驶的安全性能和寿命,必须高度重视和持续改进。
在未来,随着技术和市场的不断变化,轮胎胎面胶加工也将不断发展创新,为汽车行业带来更加先进的轮胎技术和更高品质的轮胎产品。