新车型工艺验证报告表
汽车申请检验报告模板

汽车申请检验报告模板
尊敬的车辆管理部门:
我谨代表申请人,要申请对以下车辆进行检验并颁发相关的检验报告。
请您安排检验人员及时间,我将配合相关工作。
1. 车辆基本信息:
- 车牌号码:
- 车辆品牌和型号:
- 发动机号码:
- 车身颜色:
- 车辆所有人姓名和联系方式:
2. 车辆检验要求:
根据车辆管理规定,申请人希望对车辆进行如下检验:
- 车辆安全性能检验:包括制动系统、轮胎、灯光、转向系统以及其他相关安全设备的检查;
- 尾气排放检验:对车辆的排放情况进行测试,确保符合国家标准;
- 车辆外观检验:对车身外观、车窗、车灯等进行检查,确保车辆外观完好并符合规定;
- 车辆内部设备检验:对车辆座椅、安全带、玻璃器皿等设备进行检查,确保正常运作并符合安全要求。
3. 申请人保证:
申请人保证该车辆符合相关法律法规和技术标准的要求,且车辆经过正常维护和保养。
申请人同意配合检验人员进行必要的
检验流程,并按照要求提供相关的车辆文件和资料。
以上车辆申请检验报告,请您安排相关工作人员进行检验,并将检验结果及报告尽快送达给申请人。
谢谢您的合作!
申请人姓名
联系方式。
新车型试制转生产厂管理程序

新车型试制转生产厂管理程序(IATF16949-2016/ISO9001-2015)1.0目的依据项目节点计划,规范新产品试制车辆转入生产线条件,明确业务工作的输入和输出,建立标准化作业框架平台,确保生产线试制车辆验证工作有序开展,特制定本管理规范。
2.0适用范围适用于公司新产品平台开发(含平台项目、车型项目、变型项目及小改项目等)项目,对于只有部分节点的新产品(如:部分项目仅有G4-G1、G8-G5-G4-G1等),则部分节点之间活动的开展应包含本流程规定的对应节点之间活动。
3.0术语及定义3.1 试制车:此处专指G5阀点通过后,在公司所辖区域的试制车辆。
3.2 生产准备:企业为了保证日常生产的正常进行,为顺利实现生产作业计划所从事的各项准备工作,本流程中特指新产品生产启动验证阶段一系列5M1E(人、机、料、法、环、测)准备工作。
3.3 PPV: 指产品及工艺验证用造车,是采用正式生产工装模具和制造工艺制造的样件,并按照生产线工艺装配而成的样车。
3.4 PP:指预试生产PP(Pre-Pilot G3),为完成产品和/或过程的最终验证和认可,使用工装零件按照工艺要求在生产线上装配产品的生产活动。
3.5 P: 指试生产P(Pilot G2)在产品正式投产(SOP)前,为验证在完全工装和工艺条件下批量提供的零部件质量,而在生产线上装配一定数量产品的生产活动。
4.0职责4.1 研究院4.1.1 负责提供产品输入(含签字版EBOM清单、签字版《车型力矩清单》、签字版装配技术说明书(含堵件PDM图-各生产厂)、签字版DTS及签字版关重件、法规件清单等)。
4.1.2 负责外购件OTS阶段认可(含外购油漆件)。
4.1.3 负责推动解决试制过程中的疑难问题(含设计、匹配及质量类)。
4.1.4 负责试制过程中安排各专业工程师技术支持。
4.1.5 参与评审试制车转大线生产条件,形成指令性文件,生产总监会签后,报项目总监签发。
汽配产品性能检测报告模板

汽配产品性能检测报告模板1. 背景介绍本报告是对某款汽配产品的性能进行检测和评估的结果总结。
该产品是广泛应用于汽车行业的重要零部件,其性能的稳定性和可靠性直接关系到汽车的安全和性能。
通过对该产品的性能检测,可以了解其质量和可靠性,为用户提供可靠的参考。
2. 检测项目和方法2.1 检测项目本次检测主要涵盖以下几个方面的项目:1. 强度和耐久性检测2. 尺寸精度检测3. 摩擦和磨损检测4. 温度和湿度适应性检测5. 材料成分和加工工艺分析2.2 检测方法1. 强度和耐久性检测:通过负载实验和循环使用实验测试产品的承重能力和使用寿命。
2. 尺寸精度检测:采用三坐标测量和数字显微镜等方法,对产品的尺寸和形状进行精确测量。
3. 摩擦和磨损检测:利用模拟测试设备,在不同工况下测试产品的摩擦系数和磨损情况。
4. 温度和湿度适应性检测:将产品置于不同温度和湿度环境下,测试其在复杂气候条件下的性能。
5. 材料成分和加工工艺分析:采用光谱分析和显微结构观察等方法,对产品的材料成分和工艺进行分析。
3. 检测结果和分析经过以上检测项目的严格评估和分析,得出以下结论:1. 强度和耐久性:产品在负载实验中承重能力良好,且经过循环使用实验后仍保持较高的使用寿命,表现出良好的强度和耐久性。
2. 尺寸精度:产品的尺寸精度在允许范围内,与设计要求相符。
3. 摩擦和磨损:产品具有较低的摩擦系数,能够有效减小摩擦损失,并具有良好的磨损抗性。
4. 温度和湿度适应性:产品在不同温度和湿度环境下表现稳定,具有良好的适应性。
5. 材料成分和加工工艺:产品的材料成分符合标准要求,加工工艺精细,表面光滑,无明显缺陷。
4. 结论和建议根据上述检测结果,可以得出以下结论和建议:1. 该产品在强度、耐久性和尺寸精度等方面表现出良好的性能,可以满足汽车行业的使用需求。
2. 产品具有较低的摩擦系数和良好的磨损抗性,可有效降低能源损失和改善车辆性能。
3. 产品在复杂气候条件下表现稳定,适应性良好。
汽车配件检验报告模板

引言:汽车配件检验报告是在汽车生产和维修过程中非常重要的一环。
本文将为您介绍汽车配件检验报告的模板,该模板将包含引言概述、正文内容和总结三个部分。
正文内容将分为五个大点,每个大点下再细分为五到九个小点,详细介绍相关的汽车配件检验内容。
这将帮助您了解如何编写一份详细且专业的汽车配件检验报告。
正文:一、产品基本信息1. 产品名称在报告中写入被检查配件的准确名称,确保其与实际配件相符。
2. 产品型号和规格记录配件的型号和规格,这有助于以后的对比和追踪。
3. 生产商和供应商信息包括生产商和供应商的名称、联系方式和地址等信息。
4. 产品的用途和适用范围描述该配件的主要用途以及适用的车型和车辆类型。
5. 产品的生产日期和批次号记录配件的生产日期和批次号,方便追溯问题。
二、外观检验1. 外观质量检查配件的表面是否有明显的瑕疵、划痕、氧化或腐蚀等问题。
2. 尺寸和形状检查配件的尺寸和形状是否符合设计要求,是否与原配件相匹配。
3. 颜色和涂层检查配件的颜色和涂层是否均匀、无明显色差或涂层剥落等问题。
4. 图文标识和标志检查配件上的标识、标志、图案和文字是否清晰可辨。
5. 气味和味道检查配件是否有异味或有害气味,以确保其符合相关的环保标准。
三、性能测试1. 压力测试测试配件在设计压力范围内的工作性能,确保其能够承受正常工作条件下的压力。
2. 温度测试测试配件在设计温度范围内的工作性能,确保其能够适应不同的工作环境温度。
3. 耐久性测试通过模拟实际使用条件下的频繁操作和负载条件,测试配件的耐久性和可靠性。
4. 摩擦和磨损测试检测配件在不同摩擦和磨损条件下的性能表现,确保其使用寿命和性能稳定性。
5. 其他特殊测试根据具体的配件要求,进行特殊的测试,如防水性能、防腐蚀性能等。
四、材料和成分检验1. 材料的选择和品质检查配件所使用的材料是否符合设计要求,并评估其品质和可靠性。
2. 成分分析对配件中的主要成分进行分析,确保成分的准确性和符合相关标准。
车辆白车身DFMEA分析范例

车身工程中心编制人:新严重度新频度新探测度新风险顺序数1零部件无法安装1车身数据未符合边界要求5按《白车身孔位描述书》和《零部件边界条件确认表》进行数据检查152车身无法焊装、车身运动干涉、车身异响、用户抱怨1三维数据检查未全面检查、运动校核未考虑实车精度、相关零部件未考虑到位5按《白车身自相关检查表》和《车身运动件运动校核检查表》进行数据校核6303整车外观效果差,无法满足客户需求,影响销售4设计间隙、面差不合理;装调不到位;公差分配不合理;定位方式设置不合理6参照相关车型合理设置DTS定义值,合理设置公差,合理设置定位方式6144数模校核,定位方案确定车身4增加模具费用,增加整车成本,影响利润1设计结构时未考虑后期开发车型的共用性5编制车身开发模块化说明,预先设计拓展车型结构方案6305零部件冲压起皱,翻边开裂,尖角争料,产品结构弱,易变形,尖角拉延破裂冲压负角,件拉延开裂,模具上修边刃口强度不足,影响车身性能5冲压SE分析未到位,钣金结构不合理4按《白车身SE审查报告》进行反馈及数模修改,合理设计钣金结构6120SE分析车身/制造6车身焊接操作性差,工人抱怨、生产率低,焊接效果差,影响车身性能5焊装SE分析未到位,钣金结构不合理4按《白车身SE审查报告》进行反馈及数模修改,合理设计钣金结构,合理布置焊点位置及层次2407车身电泳底漆厚度不均匀、部分区域未充分覆盖底漆、车身锈蚀、影响整车寿命5涂装SE分析未到位,钣金结构不合理4按《白车身SE审查报告》进行反馈及数模修改,合理设计钣金结构,保证涂装效果2408总装件无法安装;车身总装操作性差,工人抱怨、生产率低;零部件维修操作性差5总装SE分析未到位未分析可维修性4按《白车身SE审查报告》进行反馈及数模修改,合理设计钣金结构,合理考虑安装操作空间,进行安装虚拟验证2409影响用户乘车舒适性,影响内部载货空间,用户抱怨3未合理设计钣金结构,钣金侵占内部空间6进行CAE分析,在保证车身性能、安装结构的前提下尽量增大内部空间,可对比标杆设计7126初期确定目标值,后期按照执行,尽量加大内部空间车身/整车10影响用户乘车舒适性,影响内部装卸货方便性,用户抱怨3未合理设计钣金结构,未按人机要求设计6按人机要求设计数据,在保证车身性能、安装结构的前提下尽量改善,可对比标杆设计6108方案阶段确定各相关尺寸,保证后期数据满足要求。
产品质量检验报告表
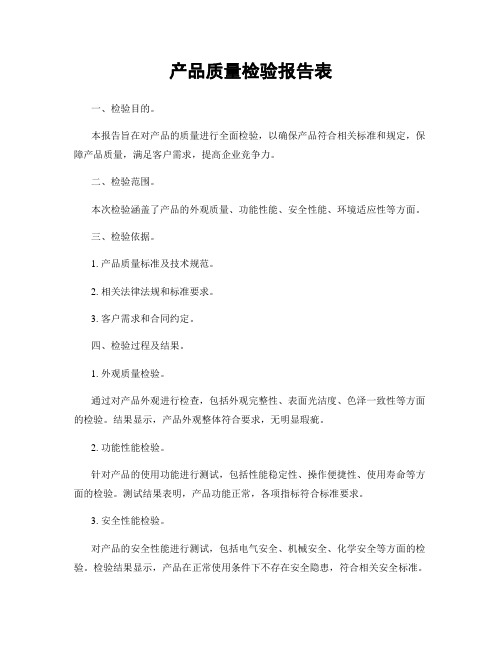
产品质量检验报告表一、检验目的。
本报告旨在对产品的质量进行全面检验,以确保产品符合相关标准和规定,保障产品质量,满足客户需求,提高企业竞争力。
二、检验范围。
本次检验涵盖了产品的外观质量、功能性能、安全性能、环境适应性等方面。
三、检验依据。
1. 产品质量标准及技术规范。
2. 相关法律法规和标准要求。
3. 客户需求和合同约定。
四、检验过程及结果。
1. 外观质量检验。
通过对产品外观进行检查,包括外观完整性、表面光洁度、色泽一致性等方面的检验。
结果显示,产品外观整体符合要求,无明显瑕疵。
2. 功能性能检验。
针对产品的使用功能进行测试,包括性能稳定性、操作便捷性、使用寿命等方面的检验。
测试结果表明,产品功能正常,各项指标符合标准要求。
3. 安全性能检验。
对产品的安全性能进行测试,包括电气安全、机械安全、化学安全等方面的检验。
检验结果显示,产品在正常使用条件下不存在安全隐患,符合相关安全标准。
4. 环境适应性检验。
通过对产品在不同环境条件下的适应性进行测试,包括温度适应性、湿度适应性、耐腐蚀性等方面的检验。
测试结果显示,产品在各种环境条件下均能正常使用,适应性良好。
五、检验结论。
根据以上检验结果,本次产品质量检验合格。
产品外观完好,功能正常,安全可靠,环境适应性良好。
符合相关标准和规定,可放心投放市场销售。
六、检验人员。
本次检验由公司专业技术人员进行,保证了检验过程的严谨性和可靠性。
七、检验日期。
本次产品质量检验于XX年XX月XX日完成。
八、备注。
如有任何问题或建议,请及时与我们联系,我们将尽快处理并改进产品质量。
以上为产品质量检验报告表,如有疑问或需要进一步了解,请随时与我们联系。
感谢您对我们产品的关注与支持。
新车型工艺验证报告表

新车型工艺验证报告第一轮□第二轮□第三轮□工位:设备名称:供应商:应用车型:最近一次改动的日期:交付工厂日期:验证机构:冲压车间□焊装车间□涂装车间□总装车间□生管物流部□参加人员:根据以下所列项目评估:工艺文件完整性:符合□不符合□不符合原因:说明:1、是否有工艺文件;2、控制计划、作业指导书是否完整工艺参数合理性:符合□不符合□无要求□不符合原因:说明:是否满足实物质量要求等工艺合理性:符合□不符合□无要求□不符合原因:说明:工艺参数、工艺布局等是否满足工艺要求人机工程合理性:符合□不符合□无要求□不符合原因:说明:IE工程工艺节拍:符合□不符合□无要求□不符合原因:说明:节拍调整的范围能够适应生产线的节拍工具符合性:符合□不符合□无要求□不符合原因:说明:操作空间、精度等是否符合要求辅具符合性:符合□不符合□无要求□不符合原因:说明:辅具的必要性,合理性工艺防错:符合□不符合□无要求□不符合原因:说明:工艺防错是否涵盖关键力矩、关键尺寸,自检、互检工作是否完善过程能力:符合□不符合□无要求□不符合原因:说明:过程能力指数满足要求检测/检验:符合□不符合□无要求□不符合原因:说明:必要的检测检验项目是否齐全,检验标准是否符合产品要求安全性:符合□不符合□无要求□不符合原因:说明:符合工装安全标准,符合工装技术协议要求。
结论:符合□不符合□要求整改日期:编制:日期:审核:日期:批准:日期:。
汽车-车身开发工艺工程-8-工艺验证
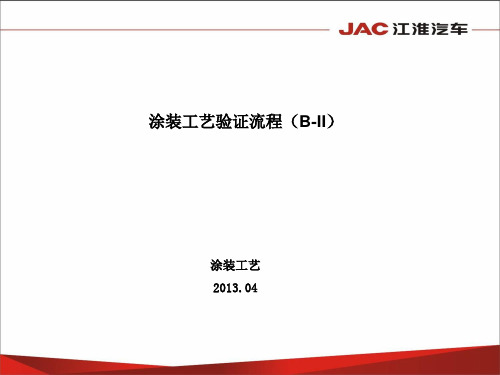
4、热水洗 工件自动进入热水洗工位,喷淋清洗。温度:55-65℃,喷淋压力:0.1-0.2MPa ,时间 30S。符合工艺要求。
0.07-0.08MPa ,温度室温,时间1min,沥水时间自控。符合工艺要求。 23、转挂:解除摆杆链,将车身及滑橇转载到滚床上,符合工艺要求。 24、电泳烘干:车身进入电泳烘房进行电泳漆烘干,烘干设定温度180℃,总时间30min,符
合工艺要求。 25、强冷:对电泳车身进行强冷,自热风强冷,时间5min,符合工艺要求。
➢P2工艺验证……………………………………验证问题整改
试制准备……………………………工艺参数、白车身精度、工装设备确认 P1问题整改验证……………………对P1问题点验证 车身质量改进验证…………………对车身质量改进进行验证 问题总结及改进措施………………存在问题进行总结
3 工作开展过程
P1工艺验证-BII
金属漆:40-70S(F-4杯),素色漆:50-70S(F-4杯);温度:23-26℃,相对湿度: 65±5%,物化压力0.6-0.8MPa,风速:0.3-0.5m/s。满足工艺需求 3、色漆闪干 车身经2个气封的升温段后进入保温段,最后经强冷转到罩光漆喷涂工位,车身在此工位将 面漆中大量水分脱去,闪干段要求脱水率达85%以上。面漆闪干分为三段:一段:气封并 升温,温度为室温至70℃,时间3.2min;2段:升温,温度为90℃,时间3.2min。三段: 强冷,温度<35℃,时间1.6min。符合工艺要求。 4、喷罩光漆 喷罩光漆分为人工喷罩光漆和机器人喷罩光漆两道工序。工艺要求如下:施工粘度:27-39S (F-4杯),温度:23-26℃,相对湿度:65±5%,物化压力0.6-0.8MPa,风速:0.30.5m/s,满足工艺要求。 5、面漆烘干 流平后的车身随滑橇经升降机升至面漆烘干室,对面漆及罩光漆进行烘干,时间为2025min。其中升温一段温度为130℃,升温二段温度为135℃,保温段温度为150℃。对烘 干后的车身经升降机降至强冷工位,强行降低车身表面温度,时间为5min。符合工艺要 求。
- 1、下载文档前请自行甄别文档内容的完整性,平台不提供额外的编辑、内容补充、找答案等附加服务。
- 2、"仅部分预览"的文档,不可在线预览部分如存在完整性等问题,可反馈申请退款(可完整预览的文档不适用该条件!)。
- 3、如文档侵犯您的权益,请联系客服反馈,我们会尽快为您处理(人工客服工作时间:9:00-18:30)。
好好学习社区
更多优惠资料下载: 德信诚培训网 新车型工艺验证报告
第一轮 □ 第二轮 □ 第三轮 □ 工位:
设备名称: 供应商:
应用车型: 最近一次改动的日期: 交付工厂日期:
验证机构: 冲压车间□ 焊装车间□ 涂装车间□ 总装车间□ 生管物流部□ 参加人员:
根据以下所列项目评估:
工艺文件完整性:
符合 □
不符合 □ 不符合原因: 说明:1、是否有工艺文件;2、控制计划、作业指导书
是否完整 工艺参数合理性: 符合 □ 不符合 □ 无要求 □
不符合原因: 说明:是否满足实物质量要求等 工艺合理性: 符合 □
不符合 □
无要求 □
不符合原因: 说明:工艺参数、工艺布局等是否满足工艺要求 人机工程合理性: 符合 □
不符合 □
无要求 □
不符合原因: 说明:IE 工程 工艺节拍: 符合 □
不符合 □
无要求 □
不符合原因: 说明:节拍调整的范围能够适应生产线的节拍 工具符合性: 符合 □
不符合 □
无要求 □
不符合原因: 说明:操作空间、精度等是否符合要求 辅具符合性: 符合 □
不符合 □ 无要求 □
不符合原因: 说明:辅具的必要性,合理性。