3.其它加工方法
非传统加工方法简介

②激光束的功率密度很高,几乎对任何难加工的金属和非金属材料都可以加工;
③激光加工是非接触加工,工件无受力变形;
④激光打孔、切割的速度很高,加工部位周围的材料几乎不受切削热的影响,工件热变形很小。
⑤激光切割的切缝窄,切割边缘质量好。
激光加工已广泛用于金刚石拉丝模、钟表宝石轴承、发散式气冷冲片的多孔蒙皮、发动机喷油咀、航空发动机叶片等的小孔加工以及多种金属材料和非金属材料的切割加工。
超
声
波
加
工
超声波加工是利用超声频(16KHz~25KHz)振动的工具端面冲击工作液中的悬浮磨料,由磨粒对工件表面撞击抛磨来实现对工件加工的一种方法。超声发生器将工频交流电能转变为有一定功率输出的超声频电振荡,通过换能器将此超声频电振荡转变为超声机械振动,借助于振幅扩大棒把振动的位移幅值由0.005mm~0.01mm放大到0.01~0.15mm,驱动工具振动。工具端面在振动中冲击工作液中的悬浮磨粒,使其以很大的速度,不断地撞击、抛磨被加工表面,把加工区域的材料粉碎成很细的微粒后打击下来。虽然每次打击下来的材料很少,但由于打击的频率高,仍有一定的加工速度。由于工作液的循环流动,被打击下来的材料微粒被及时带走。随着工具的逐渐伸入,其形状便“复印”在工件上。
用特殊形的电极工具加工相应工件的电火花成形加工机床
①加工硬、脆、韧、软和高熔点的导电材料;
②加工半导体材料及非导电材料;
③加工各种型孔、曲线孔和微小孔;
④加工各种立体曲面型腔,如锻模、压铸模、塑料模的模膛;
⑤用来进行切断、切割以及进行表面强化、刻写、打印铭牌和标记等。
用线电极加工二维轮廓形状工件的电火花线切割机床
分类
原理
原理示意
特点及应用范围
精密加工简答题
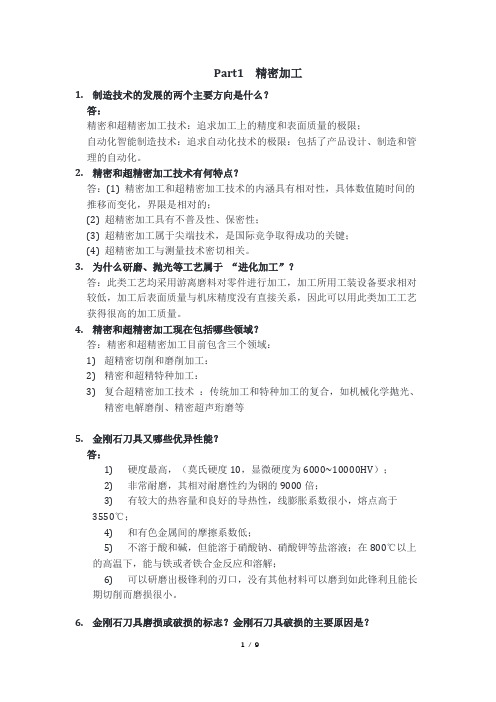
Part1 精密加工1.制造技术的发展的两个主要方向是什么?答:精密和超精密加工技术:追求加工上的精度和表面质量的极限;自动化智能制造技术:追求自动化技术的极限:包括了产品设计、制造和管理的自动化。
2.精密和超精密加工技术有何特点?答:(1) 精密加工和超精密加工技术的内涵具有相对性,具体数值随时间的推移而变化,界限是相对的;(2) 超精密加工具有不普及性、保密性;(3) 超精密加工属于尖端技术,是国际竞争取得成功的关键;(4) 超精密加工与测量技术密切相关。
3.为什么研磨、抛光等工艺属于“进化加工”?答:此类工艺均采用游离磨料对零件进行加工,加工所用工装设备要求相对较低,加工后表面质量与机床精度没有直接关系,因此可以用此类加工工艺获得很高的加工质量。
4.精密和超精密加工现在包括哪些领域?答:精密和超精密加工目前包含三个领域:1)超精密切削和磨削加工:2)精密和超精特种加工:3)复合超精密加工技术:传统加工和特种加工的复合,如机械化学抛光、精密电解磨削、精密超声珩磨等5.金刚石刀具又哪些优异性能?答:1)硬度最高,(莫氏硬度10,显微硬度为6000~10000HV);2)非常耐磨,其相对耐磨性约为钢的9000倍;3)有较大的热容量和良好的导热性,线膨胀系数很小,熔点高于3550℃;4)和有色金属间的摩擦系数低;5)不溶于酸和碱,但能溶于硝酸钠、硝酸钾等盐溶液;在800℃以上的高温下,能与铁或者铁合金反应和溶解;6)可以研磨出极锋利的刃口,没有其他材料可以磨到如此锋利且能长期切削而磨损很小。
6.金刚石刀具磨损或破损的标志?金刚石刀具破损的主要原因是?答:加工质量是否下降超差,粗糙度是否超过规定值。
微小振动引起的微观解理,造成微小崩刃7.什么是刀具锋锐度?表示锋锐度指标是什么?答:刃口锋锐度是指:刀具刃口的锋利程度指标:切削刃钝圆半径ρ的大小。
8.解释金刚石刀具设计时,通常选择100晶面做刀面,而不选择110和111晶面的理由?答:1)100:(100)耐磨性优于(110);(100)晶面的微观破损强度高于(110)晶面,(100)晶面受载荷时的破损机率比(110)晶面低很多;也更容易磨出高质量的刃口(精磨时不容易微观崩刃,反而容易减小研磨时间--尽管粗磨时费时,效率低些);(100)晶面和有色金属之间的摩擦系数要低于(110)晶面的摩擦系数。
加工虎钳总结报告范文(3篇)

第1篇一、前言虎钳是一种常见的金属加工工具,广泛应用于机械加工、制造、修理等领域。
为了提高自己的动手能力和实际操作技能,我在本次实习中选择了加工虎钳这一课题。
以下是我在实习过程中的总结报告。
二、实习目的1. 了解虎钳的结构和加工原理;2. 掌握虎钳的加工工艺和操作方法;3. 提高自己的动手能力和实际操作技能;4. 深入理解理论知识在实践中的应用。
三、实习内容1. 虎钳的结构分析虎钳主要由钳身、钳口、钳柄、钳脚等部分组成。
钳身用于夹持工件,钳口用于定位工件,钳柄用于施加压力,钳脚用于固定钳身。
2. 虎钳的加工工艺(1)钳身加工:钳身加工主要包括车削、磨削、钻孔、铣削等工序。
在加工过程中,要确保钳身尺寸准确、表面光洁。
(2)钳口加工:钳口加工主要包括钳口磨削、钳口倒角等工序。
在加工过程中,要确保钳口尺寸准确、形状规整。
(3)钳柄加工:钳柄加工主要包括车削、磨削等工序。
在加工过程中,要确保钳柄尺寸准确、表面光洁。
(4)钳脚加工:钳脚加工主要包括钻孔、铣削等工序。
在加工过程中,要确保钳脚尺寸准确、形状规整。
3. 虎钳的装配虎钳的装配主要包括钳身、钳口、钳柄、钳脚等部件的组装。
在装配过程中,要确保各部件之间配合紧密,动作灵活。
四、实习过程1. 钳身加工首先,对钳身进行车削,确保钳身尺寸准确。
然后,对车削后的钳身进行磨削,提高表面光洁度。
接着,在钳身上钻孔,用于固定钳口。
最后,对钻孔进行铣削,确保孔的形状规整。
2. 钳口加工首先,对钳口进行磨削,确保钳口尺寸准确。
然后,对磨削后的钳口进行倒角,提高钳口的使用寿命。
3. 钳柄加工首先,对钳柄进行车削,确保钳柄尺寸准确。
然后,对车削后的钳柄进行磨削,提高表面光洁度。
4. 钳脚加工首先,在钳脚上钻孔,用于固定钳身。
然后,对钻孔进行铣削,确保孔的形状规整。
5. 虎钳装配将钳身、钳口、钳柄、钳脚等部件组装在一起,确保各部件之间配合紧密,动作灵活。
五、实习收获1. 通过本次实习,我深入了解了虎钳的结构和加工原理,掌握了虎钳的加工工艺和操作方法。
机械零件的加工工艺

机械零件的加工工艺机械零件的加工工艺是指将原材料通过一系列的工艺过程,进行切削、成形、联接等操作,最终得到符合设计要求的零件。
机械零件的加工工艺涉及到材料选择、工艺规程、加工工艺参数的确定等方面。
下面将从机械零件加工的基本步骤、常用加工方法和工艺参数的选择等方面进行详细介绍。
1. 机械零件加工的基本步骤:机械零件加工的基本步骤包括工艺准备、加工操作和工艺检验三个方面。
(1)工艺准备:包括依据设计图纸和工艺要求,选择合适的材料、设备和工具,制定加工工艺规程,并依据工艺规程制作工艺文件,如加工工序卡和工艺路线。
(2)加工操作:按照工艺文件的要求,进行机械零件的加工操作。
具体包括切削加工、成形加工、联接加工等过程。
在加工操作过程中,需要根据工艺文件和现场实际情况,灵活控制机床和工艺参数,保证加工质量和工艺效率。
(3)工艺检验:通过对加工过程和加工结果的检验,验证加工质量是否符合要求。
主要包括工艺过程中的工件检测、工艺参数记录、加工精度检验等。
通过工艺检验,及时发现问题和改进不足,提高加工质量。
2. 常用加工方法(1)切削加工:包括车削、铣削、钻削、磨削等。
切削加工是利用刀具对工件进行材料的切削,达到工件形状和精度要求的加工方法。
(2)成形加工:包括冲压、锻造、拉伸等。
成形加工是通过对工件施加压力,使其发生塑性变形,从而得到所需形状的加工方法。
(3)联接加工:包括焊接、铆接、螺纹连接等。
联接加工是将多个零件通过一定的方式连接在一起,形成一个整体的加工方法。
3. 工艺参数的选择在机械零件加工中,选取合适的工艺参数对于加工质量和效率有着重要影响。
影响工艺参数的因素包括材料的物理性质、切削刃具的材料和形状、机床类型和切削速度等。
(1)刀具材料选择:合理选择刀具材料能够提高切削刃具的硬度、耐磨性和耐冲击性。
常用的刀具材料有高速钢、硬质合金和陶瓷等。
(2)刀具形状选择:合理选择刀具的形状和刃角能够适应不同加工工艺的要求。
芹菜的加工方法

芹菜的加工方法(一)腌芹菜1.原料:青芹菜50千克,盐12.5千克,18度盐水5千克。
2.制作过程:选9月份的青嫩芹菜,去叶除根,捆好后入缸腌制,放一层芹菜撒一层盐,并撒入少量盐水。
每天倒缸1次,扬汤散热,促使盐粒溶化。
腌制15天后出缸,切成3厘米长的段,入缸密封贮存。
(二)咸芹菜1.原料:鲜芹菜20千克,食盐3千克。
2.制作过程:将芹菜去叶去根,用水把茎洗净,控干水分。
将盐、红糖等调料放入坛中拌匀,放入芹菜,泡1天即为成品。
(三)泡芹菜1.原料:芹菜10千克,红糖25克,食盐200克,咸卤水10千克,干辣椒250克。
2.制作过程:将芹菜去叶去根,用水把茎洗净,控干水分。
将盐、红糖等调料放入坛中拌匀,放入芹菜,泡1天即为成品。
(四)糖醋芹菜1.原料:芹菜5千克,醋350克,糖350克,食盐400克,凉开水2千克。
2.制作过程:将芹菜去叶去根,洗净晾干,切成3厘米长的段,把各种调料混在一起拌匀,将芹菜放入浸泡,密封,2周后即为成品。
(五)桂花芹菜1.原料:芹菜叶5千克,桂花500克,食盐250克,糖50克,花椒5克。
2:制作过程:将菜叶洗净,加盐腌去水分,再加入桂花、盐、糖等调料,拌匀,一同装入容器,7天后即为成品。
(六)虾油芹菜1.原料:芹菜10千克,食盐2.5千克,虾油5千克。
2.制作过程:将芹菜去叶除根,把茎切成3厘米长的段,放入开水中焯一下,捞出用凉水冷却,控干水,装缸,撒入食盐,拌匀。
腌制16小时,捞出芹菜,控干盐水,投入虾油中浸泡, 1周后即为成品。
(七)芹菜脯1.原料选择:选用质地脆嫩、大小全都的芹菜,剔除有腐烂和病虫害的芹菜。
2.处理:将芹菜去掉叶、根,用清水洗净,再切成4厘米长的段。
3.浸泡:将处理好的芹菜放进沸水中浸泡1分钟,捞出冷却。
4.浸石灰:将芹菜段放进配制的0.5%~1%石灰水内浸泡8~10小时。
浸泡后漂洗两遍,捞出沥干。
5.浸糖:在夹层锅内配制45%糖液,煮沸5分钟,倒入浸渍机,再把芹菜倒入,真空浸渍1小时。
机械制造加工工艺(3篇)

第1篇摘要:机械制造加工工艺是机械制造行业中的重要组成部分,它直接关系到产品的质量和性能。
本文从机械制造加工工艺的基本概念、加工方法、加工设备、加工精度等方面进行了详细阐述,旨在为机械制造行业提供有益的参考。
一、引言机械制造加工工艺是指将原材料通过各种加工方法,加工成具有预定形状、尺寸和性能的零件或产品的过程。
在机械制造行业中,加工工艺的合理选择和优化对于提高产品质量、降低生产成本、提高生产效率具有重要意义。
本文将详细探讨机械制造加工工艺的相关内容。
二、机械制造加工工艺的基本概念1. 加工方法:机械制造加工工艺主要包括切削加工、磨削加工、锻造加工、铸造加工、焊接加工、热处理加工等方法。
2. 加工设备:加工设备是完成加工工艺的必要条件,如车床、铣床、磨床、数控机床等。
3. 加工精度:加工精度是指零件尺寸、形状、位置等几何参数的精确程度,是衡量加工工艺质量的重要指标。
4. 加工表面质量:加工表面质量是指零件加工表面粗糙度、波纹度、裂纹等缺陷的程度,影响零件的使用性能。
三、机械制造加工方法1. 切削加工:切削加工是机械制造中最常用的加工方法,主要包括车削、铣削、刨削、磨削等。
(1)车削:车削是利用车刀在工件上切除多余材料,使工件达到预定尺寸和形状的过程。
车削适用于内外圆柱面、圆锥面、螺纹等加工。
(2)铣削:铣削是利用铣刀在工件上切除多余材料,使工件达到预定尺寸和形状的过程。
铣削适用于平面、斜面、曲面、键槽等加工。
(3)刨削:刨削是利用刨刀在工件上切除多余材料,使工件达到预定尺寸和形状的过程。
刨削适用于平面、斜面、曲面等加工。
(4)磨削:磨削是利用磨具对工件表面进行研磨,使工件达到预定尺寸和形状的过程。
磨削适用于内外圆柱面、圆锥面、平面、曲面等加工。
2. 磨削加工:磨削加工是利用磨具对工件表面进行研磨,提高工件表面质量和精度的一种加工方法。
3. 锻造加工:锻造加工是将金属加热至一定温度,使其具有一定的塑性,然后在模具中施加压力,使金属产生塑性变形,从而获得预定形状和尺寸的零件。
第3章金属切削加工方法与设备外园表面加工

—主轴Ⅵ
② 车削螺纹传动链
CA6140卧式车床能够车削米制、英制、模数制和径节制4种标准螺纹, 还能够车削大导程、非标准和较精密的螺纹,这些螺纹可以是左旋的也可以 是右旋的。
表3-3
各种标准螺纹的螺距参数及其与螺距、导程的换算关系
螺纹种类
螺距参数
螺距/mm
导程式/mm
米制
螺距P/mm
P=P
L=KP
26
Ⅴ
80 20
正常螺蚊导程
50
Ⅳ
50
80
Ⅲ
20
44 44Ⅷຫໍສະໝຸດ Ⅸ2658
(右螺蚊)
33
Ⅹ
25
25
33
(左螺蚊)
(扩大螺蚊导程)
((116600米模4300 英数 11制径97007500螺节蚊螺)蚊)
25 36
(M3
开)
Ⅻ
基
XIV
25 36
Ⅻ
(米制及模数螺蚊)
中心钻类型
① 不带护锥中心钻(A型) ② 带护锥中心钻(B型)
③ 弧形中心钻(R型)
带螺纹中心孔(C型)加工
3.3外圆表面的磨削加工及设备
3.3.1磨床 1.磨床的主要类型及应用范围 应用范围:
磨床可以加工各种表面。凡是车床、钻床、镗床、铣床、 齿轮和螺纹加工机床等加工的零件表面,都能够在相应的 磨床上进行磨削精加工。此外,还可以刃磨刀具和进行切 断等,
模数制 英制
径节制
模数m/mm
Pm=m
Lm=KPm=Km
La=KPa=25.4K/ La=KPa=25.4K/
a
a
La=KPa=25.4K/a
径节DP(牙/in)
实用动物皮毛加工方法
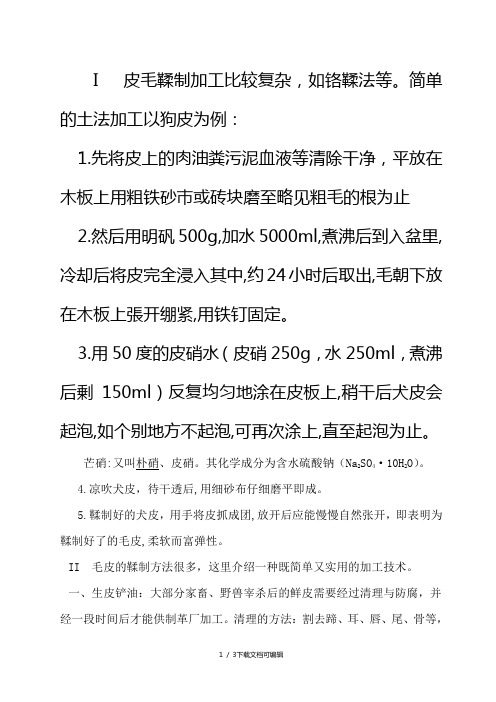
I 皮毛鞣制加工比较复杂,如铬鞣法等。
简单的土法加工以狗皮为例:1.先将皮上的肉油粪污泥血液等清除干净,平放在木板上用粗铁砂巿或砖块磨至略见粗毛的根为止2.然后用明矾500g,加水5000ml,煮沸后到入盆里,冷却后将皮完全浸入其中,约24小时后取出,毛朝下放在木板上張开绷紧,用铁钉固定。
3.用50度的皮硝水(皮硝250g,水250ml,煮沸后剰150ml)反复均匀地涂在皮板上,稍干后犬皮会起泡,如个别地方不起泡,可再次涂上,直至起泡为止。
芒硝:又叫朴硝、皮硝。
其化学成分为含水硫酸钠(Na2SO4·10H2O)。
4.凉吹犬皮,待干透后,用细砂布仔细磨平即成。
5.鞣制好的犬皮,用手将皮抓成团,放开后应能慢慢自然张开,即表明为鞣制好了的毛皮,柔软而富弹性。
II 毛皮的鞣制方法很多,这里介绍一种既简单又实用的加工技术。
一、生皮铲油:大部分家畜、野兽宰杀后的鲜皮需要经过清理与防腐,并经一段时间后才能供制革厂加工。
清理的方法:割去蹄、耳、唇、尾、骨等,再用削刀除去皮下的残肉和脂肪,洗去沾在皮上的泥、粪、淤血等,然后把鲜皮肉面向外,挂在通风处晾干,防止强光曝晒。
也可以采用盐酸腌法,即将皮张肉面撒盐,用盐量约为皮重的25%,盐腌6天左右,即要堆集。
二、浸水洗皮:将经过处理的鲜皮,置于缸内用清水浸泡,水温以15—18℃为宜,时间需6—10小时。
浸泡的目的是使原料皮吸水软化。
每百张羊皮用纯碱3—4斤或肥皂5—6连;每百张狗皮用纯碱2.5—3斤或肥皂2—3连。
然后将浸过的皮张放入稀碱液内搓洗,除去油污,再放入清水漂洗后,拧干。
碱水洗皮约需4—6分钟,洗皮的时间不宜过长,否则容易造成绒毛脱落,影响裘皮外观。
三、下缸鞣制:按明矾4—5份,食盐3—5份、清水100份的比例配制鞣制液。
先用温水妥明矾,再加入食盐和清水,混合均匀。
温度15℃时,应少加些食盐,超过20℃时则多加些食盐,水温以30℃左右为宜。
把毛皮投入浸泡7—10天后取出,将毛皮用清水漂洗,肉面不必举不胜举,最后用蓖麻油10份、肥皂10份、水100份的比例配成溶液,涂于半干状态的毛皮肉面,并适当喷此水使其回潮,再用塑料薄膜包扎好,用石块压平。
常用机械加工方法
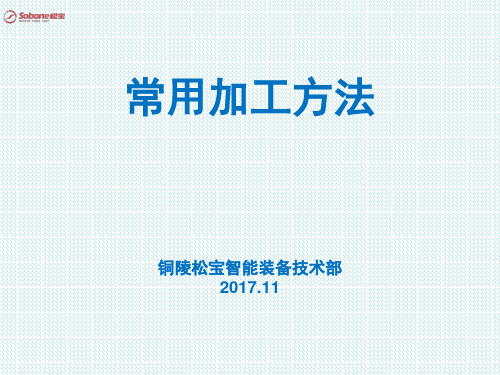
磨削的应用:
1.外圆的磨削:一般在普通外圆磨床或万能外圆磨床上进行,外圆磨削 有纵、横、综合、深磨法等 。
2.孔的磨削:可以在内圆 磨床上进行,也可以在 万能外圆磨床上进行, 它可以加工圆柱孔、圆 锥孔和成形内圆面等。
3.平面的磨削: 周磨——利用砂轮的外圆面进行磨削。端磨——利用砂轮的端面进行磨削。
常用加工方法
铜陵松宝智能装备技术部 2017.11
零件加工方法多种多样,根据被加工零 件的具体情况和要求,在选择加工方法是也 不尽相同。按是否去除材料分为无切削加工 与切削加工,按是否自动化分数控自动加工 与非自动加工,按是否放电分为放电加工与 机械加工。 其中常用的普通切削加工有:车、钻、 镗、刨、拉、铣和磨等,包含数控机械加工, 数控加工是运用CAM计算机控制程序进行自动 化加工。 无切削加工有冲压、钣金、铸造、锻造 等。放电加工有:线切割(分快丝、中丝、 慢丝)、穿孔机、电火花(电脉冲)等。
单刃镗刀在镗铣床上镗孔的方法
粗镗 半精镗 精镗
IT12-IT11 IT10-IT9 IT8-IT7
Ra 25-12.5μm Ra 6.3-3.2μm Ra 1.6-0.8μm
车床上镗孔:工件旋转、镗刀进给,如图下图所示:
在镗床上镗孔:镗刀刀杆随主轴一起旋转,完成主运动;进给运动可由 工作台带动工件纵向移动,也可由主轴带动镗刀杆轴向移动完成, 如下 图。
分析讨论各种成型加工方法的特点和共性

分析讨论各种成型加工方法的特点和共性1.铸造工艺由于铸造采用液态下一次成形,所以对材料种类及零件形状、尺寸大小和生产批量的适应性非常广,特别适合复杂形状铸件的生产,且生产成本较低,在机械制造中具有重要的地位。
铸造可直接利用成本低廉的废机件和切屑,设备费用较低。
同时铸件加工余量小,节省金属,减少机械加工余量,从而降低制造成本。
但液态成形的特点也使铸造工序多、铸件质量控制难度大、铸件力学性能差。
铸造车间一般工作环境差,容易对工人的健康有危害,而且对环境污染较严重。
铸造的应用范围:生产毛坯。
如机床床身、内燃机等2.锻造工艺由于金属材料经过锻造后,其内部组织更加致密、均匀,使同一种金属的锻件比铸件有更好的力学性能。
因此,各种承受重载荷及冲击载荷的重要零件,多以锻件作为毛坯,但由于锻造固态塑性成形的特点,无法获得形状(特别是内腔)复杂的锻件。
3.焊接工艺焊接是通过加热加压或加压或两者并用的方法,使金属达到原子结合的一种加工方法。
与其它方法相比,焊接具有节省材料、接头密封性好、经济性好、生产周期短等优。
但对工人的技术要求比较高。
焊接的应用范围在造船、电力设备生产、航天工业中广泛应用。
4.车削工艺车削加工是指在车床上应用刀具与工件作相对切削运动,用以改变毛坯的尺寸和形状等,使之成为零件的加工过程。
车工在切削加工中是最常用的一种加工方法。
车床占机床总数的一半左右,故在机械加工中具有重要的地位和作用。
车床应用范围:用来加工各种回转表面,如:内、外圆柱面;内、外圆锥面;端面;内、外沟槽;内、外螺纹;内、外成形表面;丝杆、钻孔、扩孔、铰孔、镗孔、攻丝、套丝、滚花等。
5.铣削工艺由于铣削的主运动是铣刀的旋转,铣刀又是多齿刀具,故铣削的生产效率高,刀具的耐用度高铣床及其附件的通用性广,铣刀的种类很多,铣削的工艺灵活。
铣削的加工范围较广,铣削两样适用小批与大批量的生产。
6.刨削工艺在刨车上用刨刀加工工件的方法叫刨削。
常见的刨床有牛头刨、龙门刨。
不锈钢的加工方法
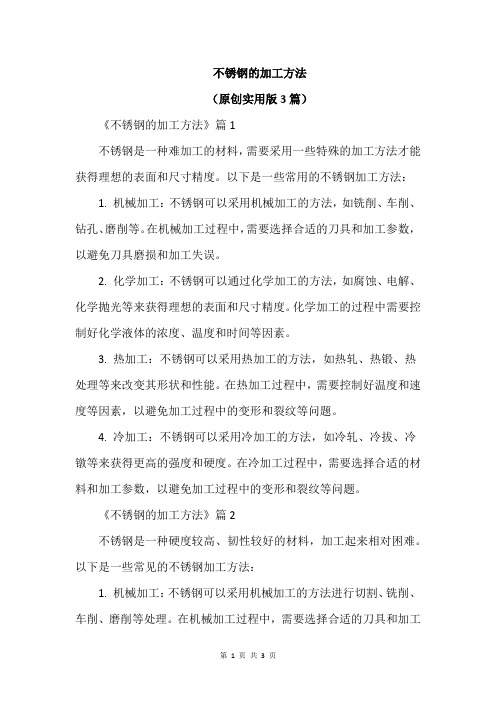
不锈钢的加工方法(原创实用版3篇)《不锈钢的加工方法》篇1不锈钢是一种难加工的材料,需要采用一些特殊的加工方法才能获得理想的表面和尺寸精度。
以下是一些常用的不锈钢加工方法:1. 机械加工:不锈钢可以采用机械加工的方法,如铣削、车削、钻孔、磨削等。
在机械加工过程中,需要选择合适的刀具和加工参数,以避免刀具磨损和加工失误。
2. 化学加工:不锈钢可以通过化学加工的方法,如腐蚀、电解、化学抛光等来获得理想的表面和尺寸精度。
化学加工的过程中需要控制好化学液体的浓度、温度和时间等因素。
3. 热加工:不锈钢可以采用热加工的方法,如热轧、热锻、热处理等来改变其形状和性能。
在热加工过程中,需要控制好温度和速度等因素,以避免加工过程中的变形和裂纹等问题。
4. 冷加工:不锈钢可以采用冷加工的方法,如冷轧、冷拔、冷镦等来获得更高的强度和硬度。
在冷加工过程中,需要选择合适的材料和加工参数,以避免加工过程中的变形和裂纹等问题。
《不锈钢的加工方法》篇2不锈钢是一种硬度较高、韧性较好的材料,加工起来相对困难。
以下是一些常见的不锈钢加工方法:1. 机械加工:不锈钢可以采用机械加工的方法进行切割、铣削、车削、磨削等处理。
在机械加工过程中,需要选择合适的刀具和加工参数,以避免刀具磨损和不锈钢材料的变形和损坏。
2. 化学加工:不锈钢可以通过化学加工的方法进行腐蚀、抛光、钝化等处理。
这些处理可以提高不锈钢的表面质量,增强其抗腐蚀性和美观度。
3. 热加工:不锈钢可以采用热加工的方法进行锻造、轧制、挤压等处理。
在热加工过程中,需要控制温度和变形量,以避免不锈钢材料的变形和损坏。
4. 冷加工:不锈钢可以采用冷加工的方法进行冲压、拉伸、折弯等处理。
在冷加工过程中,需要选择合适的材料和加工参数,以避免不锈钢材料的变形和损坏。
5. 激光加工:不锈钢可以采用激光加工的方法进行切割、打孔、焊接等处理。
激光加工具有高精度、高效率和自动化程度高等优点,适用于大批量生产的不锈钢零部件。
加工方法的实验报告(3篇)

第1篇实验名称:加工方法实验一、实验目的1. 了解不同加工方法对材料性能的影响;2. 掌握常见加工方法的基本原理和操作步骤;3. 分析加工过程中的影响因素,提高加工质量。
二、实验原理加工方法是指将原材料或半成品经过各种物理、化学或机械手段,使其达到所需形状、尺寸和性能的过程。
常见的加工方法有切削加工、热加工、电加工、化学加工等。
切削加工是利用刀具与工件之间的相对运动,通过切削力、切削热和切削液的作用,将工件上的材料去除,实现加工的目的。
切削加工包括车削、铣削、磨削、刨削等。
热加工是利用加热、冷却、变形等手段,改变材料的组织结构和性能,实现加工的目的。
热加工包括锻造、轧制、热处理等。
电加工是利用电流、电弧、电火花等作用,对材料进行加工的方法。
电加工包括电火花加工、电化学加工等。
化学加工是利用化学反应,改变材料的组织结构和性能,实现加工的目的。
化学加工包括电镀、阳极氧化、化学腐蚀等。
三、实验内容1. 切削加工实验(1)实验材料:45号钢、车刀、砂轮、切削液;(2)实验步骤:①将45号钢加工成所需形状和尺寸;②根据加工要求选择合适的刀具和切削参数;③进行切削加工,观察加工效果;④分析加工过程中的影响因素,提高加工质量。
2. 热加工实验(1)实验材料:Q235钢、加热炉、模具;(2)实验步骤:①将Q235钢加热至一定温度;②将加热后的钢坯放入模具中进行锻造;③观察锻造效果,分析锻造过程中的影响因素。
3. 电加工实验(1)实验材料:45号钢、电极、电解液;(2)实验步骤:①将45号钢加工成所需形状和尺寸;②根据加工要求选择合适的电极和电解液;③进行电火花加工,观察加工效果;④分析加工过程中的影响因素,提高加工质量。
4. 化学加工实验(1)实验材料:45号钢、电镀液、阳极氧化液;(2)实验步骤:①将45号钢加工成所需形状和尺寸;②根据加工要求选择合适的电镀液或阳极氧化液;③进行电镀或阳极氧化处理,观察加工效果;④分析加工过程中的影响因素,提高加工质量。
铜件加工工艺(3篇)

第1篇一、引言铜作为一种重要的金属材料,广泛应用于电子、机械、建筑、装饰等领域。
铜件加工是将铜材料通过各种加工方法,制成所需形状、尺寸和性能的零件。
铜件加工工艺包括铸造、锻造、冲压、切削、焊接等多种方法。
本文将详细介绍铜件加工工艺,包括加工原理、加工方法、加工设备、质量控制等方面。
二、铜件加工原理铜件加工原理主要基于金属材料的物理和力学性能。
铜具有优良的导电性、导热性、耐腐蚀性、易加工性等特点,使得铜件加工具有广泛的应用。
铜件加工原理主要包括以下几个方面:1. 塑性变形原理:铜在受力后,可以发生塑性变形,从而改变其形状、尺寸和性能。
塑性变形是铜件加工的主要原理。
2. 切削原理:切削是利用切削工具对铜材料进行去除,使其形成所需形状和尺寸的过程。
切削原理主要包括切削力、切削温度、切削速度等方面。
3. 焊接原理:焊接是将两个或多个铜材料通过加热、熔化、冷却等方式连接在一起的过程。
焊接原理主要包括焊接方法、焊接材料、焊接工艺等方面。
三、铜件加工方法1. 铸造铸造是将熔融的铜液倒入模具中,冷却凝固后得到所需形状和尺寸的铜件。
铸造方法包括砂型铸造、金属型铸造、压力铸造等。
(1)砂型铸造:将熔融铜液倒入砂型模具中,冷却凝固后取出铜件。
砂型铸造适用于形状复杂、尺寸较大的铜件。
(2)金属型铸造:将熔融铜液倒入金属模具中,冷却凝固后取出铜件。
金属型铸造适用于形状简单、尺寸较小的铜件。
(3)压力铸造:将熔融铜液在高压下注入金属模具中,冷却凝固后取出铜件。
压力铸造适用于形状复杂、尺寸精度要求较高的铜件。
2. 锻造锻造是将铜材料加热至一定温度,通过锤击、挤压等方式使其变形,从而得到所需形状和尺寸的铜件。
锻造方法包括自由锻造、模锻、挤压等。
(1)自由锻造:将铜材料加热至一定温度,通过锤击使其变形。
自由锻造适用于形状简单、尺寸较大的铜件。
(2)模锻:将铜材料加热至一定温度,通过模具使其变形。
模锻适用于形状复杂、尺寸精度要求较高的铜件。
167;3-5 其它常规加工方法

三、钳工及其附件
1、钳工——以手工操作为主的方法进行加工、产品装配及 零件修理的一个工种。
2、钳工内容
完成加工前的准备工作(举例说明) 某些精密零件的加工(举例说明)
产品的组装、调试、试车及设备的维修 零件在装配前进行的钻孔、铰孔、攻套螺纹及装备时对零件的修整
一些不能或不适合机械加工的零件的加工(举例)
主运动——拉刀的直线移动
运动
进给运动——由拉刀结构完成,拉刀上刀齿齿升量形成进给
1、拉削加工及其特点
与其它加工方法相比,拉削加工特点: ①拉削加工范围广(介绍其工艺范围) ②生产率高(介绍提高生产率的因素) ③加工质量好(介绍拉削加工的精度、表面质量及影响因素) ④拉刀耐用度高、使用寿命长(说明原因) ⑤拉刀容屑、排屑及散热困难(介绍拉削加工中的不利因素) ⑥拉刀制造复杂、成本高
1、刨削加工及其装备
(3)刨削常用附件 平口钳、压板、螺栓、挡铁、角铁……
(4)宽刃刨削
使用宽刃精刨刀 较低切削速度(2~5m/min) 较小余量——预刨0.08~0.12mm,终刨0.03~0.05mm 获较高精度(直线度0.02/1000),小表面粗糙度(Ra0.2~0.8um) 生产率高
2、插削加工
辅助运动——回程的抬刀运动
1、刨削加工及其装备
(2)刨床 ①牛头刨床 A、牛头刨的组成与布局
B、牛头刨床的种类及其特点
(按主运动传动方式分类介绍)
机械传动
液压传动
C、牛头刨床应用——加工中小 型零件
1、刨削加工及其装备
(2)刨床 ②龙门刨床 A、龙门刨床的组成与布局 B、龙门刨床的应用——大型零件或多件同时加工
成形法——以刀具齿形保证齿轮齿形 切削加工
各种加工方法的加工精度

各种加工方法的加工精度一:车削车削中工件旋转,形成主切削运动。
刀具沿平行旋转轴线运动时,就形成内、外园柱面。
刀具沿与轴线相交的斜线运动,就形成锥面。
仿形车床或数控车床上,可以控制刀具沿着一条曲线进给,则形成一特定的旋转曲面。
采用成型车刀,横向进给时,也可加工出旋转曲面来。
车削还可以加工螺纹面、端平面及偏心轴等。
车削加工精度一般为IT8—IT7,表面粗糙度为6.3—1.6μm。
精车时,可达IT6—IT5,粗糙度可达0.4—0.1μm。
车削的生产率较高,切削过程比较平稳,刀具较简单。
二:铣削主切削运动是刀具的旋转。
卧铣时,平面的形成是由铣刀的外园面上的刃形成的。
立铣时,平面是由铣刀的端面刃形成的。
提高铣刀的转速可以获得较高的切削速度,因此生产率较高。
但由于铣刀刀齿的切入、切出,形成冲击,切削过程容易产生振动,因而限制了表面质量的提高。
这种冲击,也加剧了刀具的磨损和破损,往往导致硬质合金刀片的碎裂。
在切离工件的一般时间内,可以得到一定冷却,因此散热条件较好。
按照铣削时主运动速度方向与工件进给方向的相同或相反,又分为顺铣和逆铣。
顺铣铣削力的水平分力与工件的进给方向相同,工件台进给丝杠与固定螺母之间一般有间隙存在,因此切削力容易引起工件和工作台一起向前窜动,使进给量突然增大,引起打刀。
在铣削铸件或锻件等表面有硬度的工件时,顺铣刀齿首先接触工件硬皮,加剧了铣刀的磨损。
逆铣可以避免顺铣时发生的窜动现象。
逆铣时,切削厚度从零开始逐渐增大,因而刀刃开始经历了一段在切削硬化的已加工表面上挤压滑行的阶段,加速了刀具的磨损。
同时,逆铣时,铣削力将工件上抬,易引起振动,这是逆铣的不利之处。
铣削的加工精度一般可达IT8—IT7,表面粗糙度为6.3—1.6μm。
普通铣削一般只能加工平面,用成形铣刀也可以加工出固定的曲面。
数控铣床可以用软件通过数控系统控制几个轴按一定关系联动,铣出复杂曲面来,这时一般采用球头铣刀。
数控铣床对加工叶轮机械的叶片、模具的模芯和型腔等形状复杂的工件,具有特别重要的意义。
紫河车加工方法
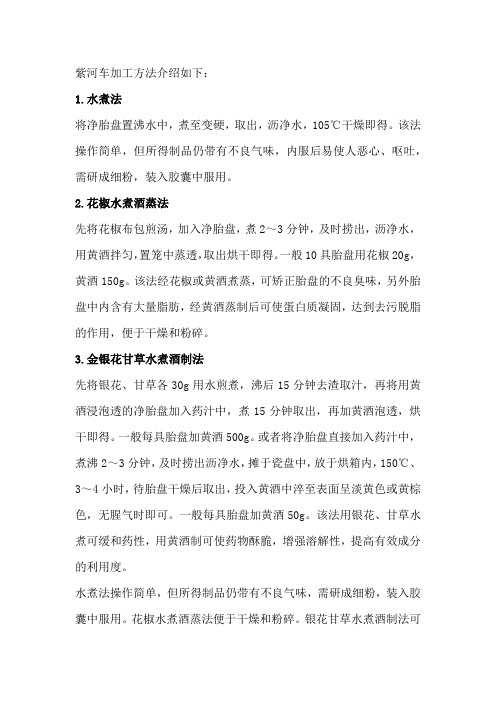
紫河车加工方法介绍如下:
1.水煮法
将净胎盘置沸水中,煮至变硬,取出,沥净水,105℃干燥即得。
该法操作简单,但所得制品仍带有不良气味,内服后易使人恶心、呕吐,需研成细粉,装入胶囊中服用。
2.花椒水煮酒蒸法
先将花椒布包煎汤,加入净胎盘,煮2~3分钟,及时捞出,沥净水,用黄酒拌匀,置笼中蒸透,取出烘干即得。
一般10具胎盘用花椒20g,黄酒150g。
该法经花椒或黄酒煮蒸,可矫正胎盘的不良臭味,另外胎盘中内含有大量脂肪,经黄酒蒸制后可使蛋白质凝固,达到去污脱脂的作用,便于干燥和粉碎。
3.金银花甘草水煮酒制法
先将银花、甘草各30g用水煎煮,沸后15分钟去渣取汁,再将用黄酒浸泡透的净胎盘加入药汁中,煮15分钟取出,再加黄酒泡透,烘干即得。
一般每具胎盘加黄酒500g。
或者将净胎盘直接加入药汁中,煮沸2~3分钟,及时捞出沥净水,摊于瓷盘中,放于烘箱内,150℃、3~4小时,待胎盘干燥后取出,投入黄酒中淬至表面呈淡黄色或黄棕色,无腥气时即可。
一般每具胎盘加黄酒50g。
该法用银花、甘草水煮可缓和药性,用黄酒制可使药物酥脆,增强溶解性,提高有效成分的利用度。
水煮法操作简单,但所得制品仍带有不良气味,需研成细粉,装入胶囊中服用。
花椒水煮酒蒸法便于干燥和粉碎。
银花甘草水煮酒制法可
提高有效成分的利用度。
其中,以银花、甘草水煮酒制法为最优,且药用方便。
饲料常用加工方法

饲料常用加工方法饲料加工的目的是为了饲料进一步提高饲料利用率,增加适口性,提高饲料消化率。
一般饲料经过合理可提高饲料利用率5~15%或者更高一些。
也许还能提高增重5~10%。
情况是提高饲料利用率比较明显,对提高增重率无效或无明显效果。
见表1。
表1饲料加工的作用及重要程度作用重要程度(%)改变饲料物理形式(主要是粒度)40方便贮藏25分离饲料中的特定成分22增加适口性8提高消化率4脱毒>1淡化营养物质结构1.常用加工方法将惯用加工方法总结于表2。
表2常用加工方法干加工湿加工冷加工粉碎浸提滚压打浆预配合化学处理(酸,碱等)质地改造(发芽)热加工热爆裂膨化蒸气滚压微波膨化蒸气压片烘炒爆裂热压榨制粒膨化以下就我国饲料工业和动物简要生产中均常见的加工方法作简要介绍。
1).粉碎饲料工业粉碎饲料原料常用3-6mm筛片控制粒度。
机械粉碎受饲料种类、水分、筛孔大小等多种因素影响。
大部份谷类中等程度大多数粉碎为宜。
一些籽粒较硬的谷类如高梁、带壳大麦,则以细粉碎为好。
但过细有如下坏处:粉尘或风带走的损失大;在动物消化道易成团状;影响适口性,特别是反刍动物不喜爱吃粉状饲料;自动化饲养中,饲料漏不出自动饲料肠痉挛,影响动物采食;粉状料通过消化道棕黄色的速度快,致使消化率降低;较长时间使用,容易引起消化道紊乱,如猪可能产生胃炎。
粉碎制品也包括压碎、压扁、切碎等将饲料物理适当改变等加工方法。
2).制粒是一种比较理想的饲料分析方法加工方法。
常结合蒸汽制粒。
制粒温度60-100℃。
制粒过程饲料含水17-18%。
最终产品DM90%左右。
随着饲料工业的经济发展,制粒加工有取代或部分取代粉料加工加工的趋势明显。
饲料制粒的好处是:饲料损失减小。
适口性增加。
限制动物选食猪饲料,减少饲料浪费,制粒后提高了纤维素和一些被束搏磷的营养素的利用率,如尼克酸,植酸磷等的利用率。
颗粒饲料方便机械化养畜。
单胃两栖类可提高增重率5%左右,提高饲料利用率5~10%左右。
- 1、下载文档前请自行甄别文档内容的完整性,平台不提供额外的编辑、内容补充、找答案等附加服务。
- 2、"仅部分预览"的文档,不可在线预览部分如存在完整性等问题,可反馈申请退款(可完整预览的文档不适用该条件!)。
- 3、如文档侵犯您的权益,请联系客服反馈,我们会尽快为您处理(人工客服工作时间:9:00-18:30)。
3.其它加工方法3.1 改进曲面分层粗加工1)增加过滤刀具加工盲区功能;此功能可过滤掉如镶片牛鼻刀等粗加工时在一些小区域内的走刀路径,可有效的保护刀具;参数设定及示意图如图3-25所示:图3-25 过滤刀具加工盲区2)最大盲区半径是指当前刀具在没有使用过滤刀具盲区功能前在某一小区域内生成路径的最大半径或者是路径的最大水平向长度,而不是图形区域上的尺寸大小。
最大盲区半径一般设置为当前刀具加工盲区的半径。
如图3-26所示圆孔直径为16mm,当前刀具为牛鼻刀12.00-2.0,则加工路径对比:(a) 未过滤刀具加工盲区 (b) 过滤刀具加工盲区图3-26 过滤刀具加工盲区前后的路径对比需要注意的是:1.支持过滤刀具盲区功能的下刀方式有:折线下刀和螺旋下刀两种方式,其它下刀方式但不支持。
2.过滤刀具盲区半径的计算公式:最大刀具盲区半径=刀具半径- 圆角半径系统默认关系式为:bldr=0.5*tldi其中:bldr 表示刀具盲区半径,tldi表示刀具直径,0.5为关系式系数,“*”为乘法运算符。
3.2 改进曲面残料补加工1)增加残料模型功能:系统首先根据已加工过的路径来自动计算出毛胚当前剩余的残料模型,然后在此基础上生成当前小刀具的残料补加工路径。
由于参照了实际的毛胚当前剩余残料模型,残补路径仅仅在残料的位置生成路径,路径的安全性、可靠性更高,还可以过滤大量的空刀路径,提高残料补加工的效率。
这种方式可以作为大刀具开粗后进行残料补加工的首选加工方法。
图3-1 当前残料模型设定残料定义方式2)指定上把刀具时,计算残料区域更准确,如图3-2所示;(a)5.20版本生成的路径长度为9.253米 b)5.50版本生成的路径长度为8.076米图3-2 两个JDP版本生成的曲面残料补加工路径对比需注意的是:1.系统用来计算剩余毛胚的路径为路径管理器中当前残料补加工路径之前的所有已生成的路径,应用此方法时应确保这些已生成的路径与在机床上实际加工过的路径一致性;2.如果前面的开粗路径使用的是有盲区的刀具,并且计算开粗路径时选择了“过滤刀具盲区”选项,或者粗加工路径做过手工删除等操作,则强烈建议使用“当前残料模型”这种残料定义方式,来计算曲面残料补加工路径,这样才能保证加工的安全可靠。
3.平面加工路径、投影加工路径、输入的NC路径均可以用做毛坯剩余残料模型的计算,这样不仅优化了加工工艺,还保证了小刀具清根清角的安全高效。
4.“设定刀具直径”:此种残料定义方式只使用于上把刀具和本次刀具为同类型的场合,否则计算的残料模型不准确,会导致残料补加工路径的刀具吃刀量过深;5.一般为了提高路径质量,可以设定当前残料补加工路径的表面余量稍大于粗加工时设定的表面余量值。
3.3 旋转雕刻功能改进旋转雕刻直接根据几何模型计算加工路径, 计算准确,这一点不同于将旋转模型展平成平面模型再计算路径的方法。
JDPaint 5.50的旋转雕刻功能的特点包括:1)新增保护面限定加工范围,用户可以通过保护面余量及保护面抬高参数调整路径修剪的范围;如图3-3所示:图3-3 保护面限定加工范围2)新增空间边界限定加工范围;如图3-4所示:图3-4 空间边界限定加工范围需要注意的是:a.空间边界线必须是空间封闭,而且展开也是封闭的;b.若遇到空间封闭而展开不封闭的图形,可以使用增加线段方式使其变成展开封闭的轮廓;如下图3-5所示:(a) 空间边界线展开图不闭合 (b) 空间边界线展开图闭合(c) 修正后的空间边界图3-5 空间边界线的修正3)新增曲线旋转投影加工,实现在旋转模型上的单线雕刻;如图3-6所示:(a) 参数设定 (b)曲线旋转投影路径 (c) 曲线旋转投影加工效果图3-6 曲线旋转投影加工需要注意的是:a.曲线应当落在旋转模型上,以便提高计算的准确性;b.作投影的曲线可以是封闭的,也可以是不封闭的;4)新增Y向偏移量,提高侧刃加工时间,增长刀具耐用度;如图3-7所示:(a) 偏移参数设定 (b) Y向偏移路径(c) 旋转雕刻Y向偏移路径对比图3-7 Y向偏移参数及偏移前后路径比较需要注意的是:a.实际加工中,确保移动量与机床的移动量相同;b.如果加工机床是3轴设备, 旋转轴替代了Y轴,强烈建议用户不要设置偏移量,避免造成加工误差 ;JDPaint5.50软件的旋转雕刻路径仍然只提供了类似于平行截线走刀方式,加工残留量可以通过路径角度进行优化。
需要注意的是旋转雕刻路径0度方向计算速度最快, 加工速度也最快, 所以除了一些特殊场合, 建议用户采用0度走刀。
3.4 新增导动加工功能导动加工是一种基于导动线而生成路径的方法, 包括以下四种加工方法:曲线投影,单轨扫描,双轨扫描,曲线吸附;这些加工方法常用于加工模具上的小槽和流线型曲面组,也可以用于单线体字的雕刻加工。
该加工方法全部支持保护面修剪路径和轮廓修剪路径,封闭路径支持螺旋连刀,开口路径支持圆弧进退刀以及进退刀直线延伸功能。
加工域选择时,必须选择导动线来引导生成导动加工路径,轮廓线只是用来限定路径生成的范围,二者不能混淆。
路径向导中导动加工方式的选择如图3-8所示:图3-8 路径向导中几种导动方式的选择JDPaint5.50软件提供的导动加工功能由以下几个部分组成:3.3.1 曲线投影加工曲线投影是沿着导动曲线在曲面上的投影线生成刀具路径的一种加工方法,它是由加工曲面和导动线来限制的。
改进后的曲面投影加工可以将曲线直接投影到曲面上生成路径,避免了在早期版本中必须先生成单线雕刻路径然后投影变换路径的繁琐过程。
图3-9 曲线投影示意图图3-10 曲面法向偏移设置界面1.曲线投影加工支持路径分层,按照分层方式得不同分为沿Z向偏移和沿曲面法向偏移两种。
通过参数“曲面法向偏移”来控制,默认是Z向投影加工,该参数为未选中状态;参数设置如上图3-10所示:2.曲线投影分层加工特点:Z向投影加工,按照Z向进行分层,生成的刀具路径是沿Z轴向上或向下平移复制产生的,每一层的切削路径在XY面的投影是一样的,可能得到的工件会在曲面的凸出或下凹的深度不一致;沿曲面法线偏移,按照曲面法向偏移分层,就保证了刀具在曲面上的加工深度一致;两种方式分层加工示意图如图3-11所示:(a) Z向投影分层 (b) 曲面法线偏移分层图3-11 曲线投影分层加工原理示意图需要注意的是:1.曲线投影的分层加工是通过路径层数和吃刀深度来控制实际加工功深度的,而划槽深度决定在曲面下所要加工的深度;由于路经分层从下向上进行的,当实际加工深度和划槽深度有出入时分为以下二种情况:a)吃刀深度*路径层数<=划槽深度此时路径生成在曲面及曲面下方,此时存在一定的风险,可能第一层路径的下刀在曲面下方,这样第一层的切削量会比较大,对刀具磨损比较大。
b)吃刀深度*路径层数>划槽深度此时生成的路径均匀分布在曲面的上下方,加工过程中不会出现突然切削量增大的现象,有利于更好的保护刀具。
2.当投影面为平面时,沿曲面法向偏移和沿Z向偏移的路径是一样的;当投影面为曲面时,建议用户采用沿曲面法向偏移方式加工,从而避免沿Z 向投影产生的在不同区域的加工深度不一致的问题。
3.曲面下分层加工是过切加工方式,路径分析检查的结果为过切状态。
3.3.2 曲线吸附加工曲线吸附加工主要是曲线上线按照曲面所在法线方向来计算刀具路径的,它可以沿着曲面上的曲线加工出等宽的槽。
与曲线投影加工中的沿曲面法向偏移不同的是刀具的接触点落在曲面上的曲线上,同时曲线吸附加工也支持分层加工;加工示意图 3-12所示:图3-12 曲线吸附选项及原理示意图需要注意的是:1.划槽深度不能大于加工使用刀具的半径,否则生成的路径有变形,不能使用。
2.选用曲线吸附加工时,为提高加工精度,建议选择的导动线为曲面上线。
3.曲线吸附的分层加工同曲线投影的分层加工相同,注意事项参照曲线投影中的分层加工即可。
3.3.3 单轨扫描加工单轨扫描加工, 就是根据曲线的走向,在加工曲面上生成刀具路径的加工方法。
主要有以下特点:1.单轨扫描提供垂线扫描和沿轨迹线扫描两种加工方式,如图3-13所示;两种加工方式的选择,通过参数来控制,默认为沿轨迹线走刀,该参数为选中状态;图3-13 单轨扫描导动加工2.根据曲线方向提供:向左,向右,两边三种偏移方向选择,参数设置如图3-14所示:图 3-14单轨扫描偏移方向设置需要注意的是:a.单轨扫描使用偏移距离参数控制扫描宽度;b.轨迹扫描的条数使用偏移距离和路径间距估算获得;估算方法是:轨迹条数 = 偏移距离 / 路径间距;c.偏移距离为投影到XY平面上的曲线单边偏移量,路径间距为空间间距;有时偏移距离不好精确计算,我们可以将该值设的稍大些,然后可以通过设置保护面,就可以生成较为理想的单轨扫描路径了。
d.偏移的方向是根据曲线的方向来确定,方向偏移示意图如下。
图3-15 单轨偏移方向示意图e.单轨扫描关键是要提取出来要加工曲面的脊线(即加工曲面边界线的中线,详情见6.2)3.3.4 双轨扫描加工双轨扫描加工, 同单轨扫描原理一样,同样支持垂线扫描和沿轨迹线扫描两种方式;两种扫描方式通过参数来控制,默认为沿轨迹走刀,该参数为选中状态;两种方式生成的路径如图3-16(a)、(b)所示:(a) 双轨扫描(垂直轨迹线走刀) (b) 双轨扫描(沿轨迹线走刀)图3-16 双轨扫描导动加工需要注意的是:a.轨迹扫描的条数是由轨迹线之间的最大路径长度和路径间距计算获得;b.用于导动的曲线应当尽量光滑,对于质量不好的曲线可采用“曲线光顺”功能,以便提高路径的质量;c.封闭的曲线之间导动时,应当合理设置曲线起点和方向,否则可能导致路径扭曲;如图3-17所示为比较两轨迹线的方向一致性对生成的导动加工路径的影响:(a) 两轨迹线方向一致 (b) 两轨迹方向相反图3-17两轨迹线的方向一致性对生成的导动加工路径的影响d.双轨导动也常用于流线型的曲面组的加工;图56中的模型是由多张曲面组成,由于每张曲面的流线方向不完全一致,生成的曲面流线精加工路径如图3-18(a)所示,采用双轨扫描导动加工的路径如图3-18(b)所示;(a) 曲面流线精加工路径(b) 双轨扫描导动加工图3-18 曲面流线与双轨扫描导动加工比较e.双轨扫描加工路径只能在选中的两条导动线之间来生成,所以在加工凸模具时,一般应将提取的两条轨迹线往外偏移一定的距离,否则会出现导动加工路径不能加工到位的情况。
如图3-19所示(图中红线为轨迹线):(a)原始轨迹线(b)轨迹线偏移后图3-19 导动加工路径3.5 新增插铣加工功能插铣加工是一种固定轴操作类型,通过刀具轴向运动高效率地进行大切削量的加工,由于是利用刀具的上下运动,所以类似于使用连续钻孔方式加工。