冶金原理实验报告硫化锌精矿氧化过程动力学
锌冶金实习报告
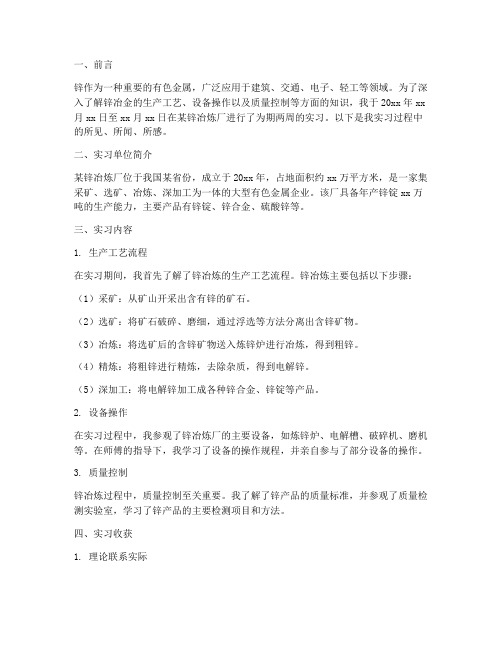
一、前言锌作为一种重要的有色金属,广泛应用于建筑、交通、电子、轻工等领域。
为了深入了解锌冶金的生产工艺、设备操作以及质量控制等方面的知识,我于20xx年xx 月xx日至xx月xx日在某锌冶炼厂进行了为期两周的实习。
以下是我实习过程中的所见、所闻、所感。
二、实习单位简介某锌冶炼厂位于我国某省份,成立于20xx年,占地面积约xx万平方米,是一家集采矿、选矿、冶炼、深加工为一体的大型有色金属企业。
该厂具备年产锌锭xx万吨的生产能力,主要产品有锌锭、锌合金、硫酸锌等。
三、实习内容1. 生产工艺流程在实习期间,我首先了解了锌冶炼的生产工艺流程。
锌冶炼主要包括以下步骤:(1)采矿:从矿山开采出含有锌的矿石。
(2)选矿:将矿石破碎、磨细,通过浮选等方法分离出含锌矿物。
(3)冶炼:将选矿后的含锌矿物送入炼锌炉进行冶炼,得到粗锌。
(4)精炼:将粗锌进行精炼,去除杂质,得到电解锌。
(5)深加工:将电解锌加工成各种锌合金、锌锭等产品。
2. 设备操作在实习过程中,我参观了锌冶炼厂的主要设备,如炼锌炉、电解槽、破碎机、磨机等。
在师傅的指导下,我学习了设备的操作规程,并亲自参与了部分设备的操作。
3. 质量控制锌冶炼过程中,质量控制至关重要。
我了解了锌产品的质量标准,并参观了质量检测实验室,学习了锌产品的主要检测项目和方法。
四、实习收获1. 理论联系实际通过实习,我将所学理论知识与实际生产相结合,加深了对锌冶金工艺流程、设备操作和质量控制等方面的理解。
2. 实践能力提升在实习过程中,我参与了部分设备的操作,提高了自己的动手能力,为今后从事相关工作打下了基础。
3. 团队协作精神实习期间,我与其他实习生共同完成各项任务,培养了团队协作精神。
4. 职业素养在实习过程中,我严格遵守厂规厂纪,认真完成各项工作,提高了自己的职业素养。
五、实习体会1. 实习使我深刻认识到理论知识的重要性。
只有掌握扎实的理论基础,才能在实际工作中游刃有余。
硫化锌精矿中氧化锌的测定
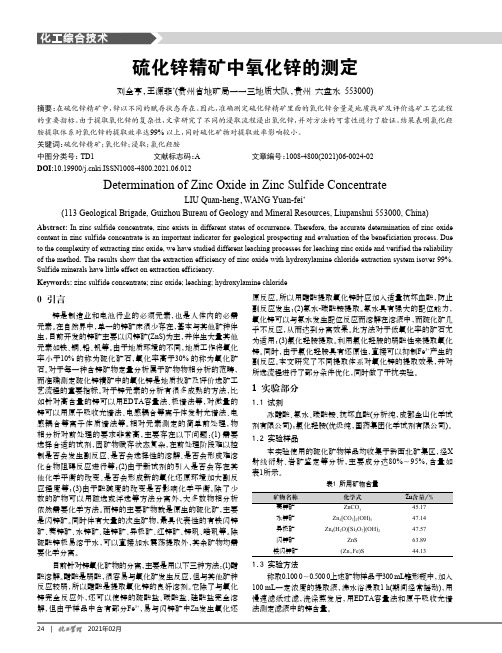
原反应。
所以用醋酸提取氧化锌时应加入适量抗坏血酸,防止副反应发生;(2)氨水-碳酸铵提取。
氨水具有强大的配位能力,氧化锌可以与氨水发生配位反应而溶解在溶液中,而硫化矿几乎不反应,从而达到分离效果。
此方法对于低氧化率的矿石尤为适用;(3)氯化羟胺提取。
利用氯化羟胺的弱酸性来提取氧化锌。
同时,由于氯化羟胺具有还原性,直接可以抑制Fe 3+产生的副反应。
本文研究了不同提取体系对氧化锌的提取效果,并对所选流程进行了部分条件优化,同时做了干扰实验。
1 实验部分1.1 试剂冰醋酸、氨水、碳酸铵、抗坏血酸(分析纯,成都金山化学试剂有限公司);氯化羟胺(优级纯,国药集团化学试剂有限公司)。
1.2 实验样品本实验使用的硫化矿物样品均收集于黔西北矿集区,经X 射线衍射、岩矿鉴定等分析,主要成分达80%~95%,含量如表1所示。
表1 所用矿物含量3水锌矿Zn 5[CO 3]2(OH)547.14异极矿Zn 4(H 2O)[Si 2O 7](OH)247.57闪锌矿ZnS 63.89铁闪锌矿(Zn ,Fe)S44.131.3 实验方法称取0.100 0~0.500 0上述矿物样品于300 mL 锥形瓶中,加入100 mL 一定浓度的提取液,沸水浴浸取1 h(期间经常摇动),用慢速滤纸过滤,洗涤蒸发后,用EDTA 容量法和原子吸收光谱法测定滤液中的锌含量。
0 引言锌是制造业和电池行业的必须元素,也是人体内的必需元素。
在自然界中,单一的锌矿床很少存在,基本与其他矿种伴生,目前开发的锌矿主要以闪锌矿(ZnS)为主,并伴生大量其他元素如铁、铜、铅、钒等。
由于地质环境的不同,地质工作将氧化率小于10%的称为硫化矿石,氧化率高于30%的称为氧化矿石。
对于每一种含锌矿物定量分析属于矿物物相分析的范畴,而准确测定硫化锌精矿中的氧化锌是地质找矿及评价选矿工艺流程的重要指标。
对于锌元素的分析有很多成熟的方法,比如针对高含量的锌可以用EDTA 容量法、极谱法等,对微量的锌可以用原子吸收光谱法、电感耦合等离子体发射光谱法、电感耦合等离子体质谱法等。
冶金学-Zn-08-7-30湿法炼锌

2.1 硫化锌精矿的焙烧:2.1.1-硫化锌精矿焙烧的热力学基础
(1)欲控制硫酸化焙烧,1是降低焙烧温度;2是提高 PO2; 3是提高 PSO2 (2)欲控制氧化焙烧,1是提高焙烧温度,2是降低氧分压 PO2 ; 3是降低二氧化硫分压PSO2
2.1 硫化锌精矿的焙烧:2.1.1-硫化锌精矿焙烧的热力学基础 (2) 硫酸化焙烧
气相边界层 ZnO
ZnS
2.1 硫化锌精矿的焙烧: 2.1.3-焙烧生产实践
硫化锌精矿的焙烧大都采用沸腾炉焙烧,有的还采
沸腾焙烧的应用是在1944年开始,首先用于硫铁矿
用多膛炉焙烧或悬浮焙烧。 的焙烧,1952年才应用到炼锌工业中。我国于1957年末建 成第一座工业沸腾焙烧炉并投入生产,且在后来新建的炼 锌厂都采用了沸腾焙烧。 沸腾炉焙烧是在焙烧过程中使空气自下而上地吹过 固体炉料层,使固体颗粒相互分离,不停地翻动,有效地 进行硫化物氧化反应的强化焙烧过程。 沸腾炉所用设备简单,易于实现自动化控制。
2.1 硫化锌精矿的焙烧:2.1.2-硫化锌精矿焙烧动力学
决定硫化锌精矿氧化焙烧速度的控 制环节: (1) 氧通过颗粒周围的气膜向其表 面扩散(外扩散); (2) 氧通过颗粒表面的氧化物层向 反应界面扩散(内扩散); (3) 在反应界面上进行化学反应; (4) 反应的产物SO2 向着与氧相反 方向的扩散。
2.1 硫化锌精矿的焙烧:2.1.1-硫化锌精矿焙烧的热力学基础 由以上分析可以看出: 1、如果湿法炼锌希望保留一部分硫酸锌存在,就意味 着降低焙烧温度、维持较高的氧浓度和二氧化硫浓度。 2、要想少生成一些铁酸锌,就需要较低的氧分压和较 高的温度(生成磁铁矿) 湿法炼锌的焙烧实际上受到上边两个矛盾的制约,很难 兼顾。因此往往采用较高的温度和适度的氧分压。越来越朝 着过程强化的方向发展。 3、较高的温度抑制了铁酸锌的生成,促进了氧化锌的 生成;而适度增加的氧分压在强化焙烧脱硫的过程中,会利 于硫酸锌的部分保留 因此焙烧产物就是氧化锌、碱式硫酸锌、硫酸锌和铁酸 锌的混合物 湿法炼锌的焙烧温度一般控制在1143~1193K,有的 达到1293K。空气过剩系数为1.20~1.30。
硫化锌精矿焙烧的主要反应
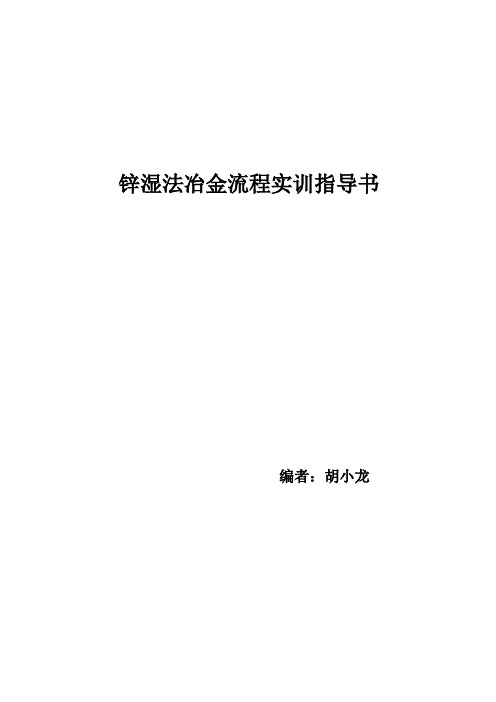
锌湿法冶金流程实训指导书编者:胡小龙目录1.锌精矿的焙烧 (1)1.1湿法炼锌对锌精矿焙烧的目的与要求 (1)1.2硫化锌精矿焙烧的主要反应 (1)1.3锌精矿焙烧 (8)2 浸出 (9)2.1浸出的目的 (9)2.2中性浸出 (9)2.3酸性浸出 (11)2.4沉矾 (12)3 净化 (14)3.1净化目的 (14)3.2一段净化 (14)3.3二段净化 (15)3.4三段净化 (15)3.5工序产品的质量要求 (16)4 综合回收 (17)4.1工艺原理 (17)4.2原料、产品要求 (17)4.3铜镉渣浸出 (18)4.4铜渣酸洗及上清压滤 (18)4.5铜镉渣浆化及过滤 (18)4.6钴渣酸洗及压滤 (19)4.7贫镉液沉钴 (19)4.8Β-奈酚除钴 (19)1.锌精矿的焙烧1.1湿法炼锌对锌精矿焙烧的目的与要求根据湿法炼锌的工艺原理,湿法炼锌焙烧硫化锌精矿的目的主要是使锌精矿中的ZnS绝大部分转变为ZnO,少量则为ZnSO4,同时尽可能完全地除去砷、锑等杂质。
具体说来其要求有五点:(1)在湿法炼锌中,出于硫化锌在一般条件下不能直接用稀硫酸进行浸出,所以焙烧时,要尽可能完全地使ZnS转型,使其绝大部分氧化成为可溶于稀硫酸的ZnO。
不过为了补偿冶金过程中H2SO4的机械损失和化学损失,仍要求焙烧矿中有适量的可溶于水的ZnSO4。
生产实践证明,一般浸出流程,只要使焙烧矿中含有2.5~4%的ZnSO4形态的硫就可以补偿冶金过程中H2SO4的损失,并不希望过多,否则会导致冶金过程中硫酸根的过剩,影响正常生产的进行和增加原材料的消耗。
(2)使砷,锑氧化成挥发性的氧化物除去,同时除去部分铅,以减轻浸出、净化工序工作量。
(3)使炉气中的SO2浓度尽可能地高,以利制造硫酸。
(4)焙烧得到细小粒子状的焙烧矿,以利下一步浸出,即不希望有烧结现象发生。
(5)在焙烧时应尽可能地少产生铁酸锌和硅酸锌。
因为铁酸锌不溶于稀硫酸,而导致锌的浸出率降低;硅酸锌虽然能溶于稀硫酸,但溶解后会产生胶体状的二氧化硅,影响浸出矿浆的澄清与过滤。
硫化锌精矿的加压酸浸(一)
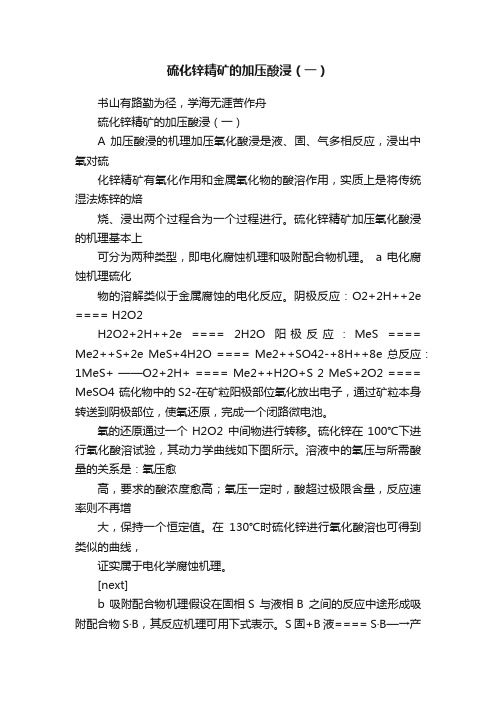
硫化锌精矿的加压酸浸(一)书山有路勤为径,学海无涯苦作舟硫化锌精矿的加压酸浸(一)A 加压酸浸的机理加压氧化酸浸是液、固、气多相反应,浸出中氧对硫化锌精矿有氧化作用和金属氧化物的酸溶作用,实质上是将传统湿法炼锌的焙烧、浸出两个过程合为一个过程进行。
硫化锌精矿加压氧化酸浸的机理基本上可分为两种类型,即电化腐蚀机理和吸附配合物机理。
a 电化腐蚀机理硫化物的溶解类似于金属腐蚀的电化反应。
阴极反应:O2+2H++2e ==== H2O2H2O2+2H++2e ==== 2H2O 阳极反应:MeS ==== Me2++S+2e MeS+4H2O ==== Me2++SO42-+8H++8e 总反应:1MeS+ ——O2+2H+ ==== Me2++H2O+S 2 MeS+2O2 ==== MeSO4 硫化物中的S2-在矿粒阳极部位氧化放出电子,通过矿粒本身转送到阴极部位,使氧还原,完成一个闭路微电池。
氧的还原通过一个H2O2 中间物进行转移。
硫化锌在100℃下进行氧化酸溶试验,其动力学曲线如下图所示。
溶液中的氧压与所需酸量的关系是:氧压愈高,要求的酸浓度愈高;氧压一定时,酸超过极限含量,反应速率则不再增大,保持一个恒定值。
在130℃时硫化锌进行氧化酸溶也可得到类似的曲线,证实属于电化学腐蚀机理。
[next]b 吸附配合物机理假设在固相S 与液相B 之间的反应中途形成吸附配合物S·B,其反应机理可用下式表示。
S 固+B 液==== S·B—→产物吸附配合物的形成是过程的最缓慢阶段,为过程速率的控制步骤。
过程的反应动力学可以推导如下:设Q 为形成吸附配合物过程中参与反应的部分,1 - Q = 没有参与反应的游离部分设形成配合物的速率ξ1为ξ1= K1(1-Q)[B]n 设配合物分解(成组分)的速率ξ2为ξ2= K2Q 设配合物分解(成产物)的速率ξ3为ξ3= K3Q 式中,K1,K2,K3 均为速率常数。
硫化锌精矿的加压酸浸(一)

书山有路勤为径,学海无涯苦作舟硫化锌精矿的加压酸浸(一)A 加压酸浸的机理加压氧化酸浸是液、固、气多相反应,浸出中氧对硫化锌精矿有氧化作用和金属氧化物的酸溶作用,实质上是将传统湿法炼锌的焙烧、浸出两个过程合为一个过程进行。
硫化锌精矿加压氧化酸浸的机理基本上可分为两种类型,即电化腐蚀机理和吸附配合物机理。
a 电化腐蚀机理硫化物的溶解类似于金属腐蚀的电化反应。
阴极反应:O2+2H++2e ==== H2O2H2O2+2H++2e ==== 2H2O 阳极反应:MeS ==== Me2++S+2e MeS+4H2O ==== Me2++SO42-+8H++8e 总反应:1MeS+ ——O2+2H+ ==== Me2++H2O+S 2 MeS+2O2 ==== MeSO4 硫化物中的S2-在矿粒阳极部位氧化放出电子,通过矿粒本身转送到阴极部位,使氧还原,完成一个闭路微电池。
氧的还原通过一个H2O2 中间物进行转移。
硫化锌在100℃下进行氧化酸溶试验,其动力学曲线如下图所示。
溶液中的氧压与所需酸量的关系是:氧压愈高,要求的酸浓度愈高;氧压一定时,酸超过极限含量,反应速率则不再增大,保持一个恒定值。
在130℃时硫化锌进行氧化酸溶也可得到类似的曲线,证实属于电化学腐蚀机理。
[next]b 吸附配合物机理假设在固相S 与液相B 之间的反应中途形成吸附配合物S·B,其反应机理可用下式表示。
S 固+B 液==== S·B—→产物吸附配合物的形成是过程的最缓慢阶段,为过程速率的控制步骤。
过程的反应动力学可以推导如下:设Q 为形成吸附配合物过程中参与反应的部分,1 - Q = 没有参与反应的游离部分设形成配合物的速率ξ1为ξ1= K1(1-Q)[B]n 设配合物分解(成组分)的速率ξ2为ξ2= K2Q 设配合物分解(成产物)的速率ξ3为ξ3= K3Q 式中,K1,K2,K3 均为速率常数。
当n=1 反应。
冶金原理实验报告

冶金原理实验报告专业班级学号姓名同组成员电极过程动力学一、实验目的通过对铜电极的阳极极化曲线和阴极极化曲线的测定,绘制出极化曲线图,从而进一步加深对电极极化原理以及有关极化曲线理论知识的理解。
通过本实验,熟悉用恒电流法测定极化曲线。
二、实验原理当电池中由某金属和其金属离子组成的电极处于平衡状态时,金属原子失去电子变成离子获得电子变成原子的速度是相等的,在这种情况下的电极称为平衡电极电位。
电解时,由于外电源的作用,电极上有电流通过,电极电位偏高了平衡位,反应以一定的速度进行,以铜电极Cu|Cu2+为例,它的标准平衡电极电位是+0.337V,若电位比这个数值更负一些,就会使Cu2+获得电子的速度速度增加,Cu失去电子的速度减小,平衡被破坏,电极上总的反应是Cu2+析出;反之,若电位比这个数值更正一些,就会使Cu失去电子的速度增加,Cu2+获得电子的速度减小,电极上总的反应是Cu溶解。
这种由于电极上有电流通过而导致电极离开其平衡状态,电极电位偏离其平衡的现象称为极化,如果电位比平衡值更负,因而电极进行还原反应,这种极化称为阴极极化,反之,若电位比平衡值更正,因而电极进行氧化反应,这种极化称为阳极极化。
对于电极过程,常用电流密度来表示反应速度,电流密度愈大,反应速度愈快。
电流密度的单位常用安培/厘米2,安培/米2。
由于电极电位是影响影响电流密度的主要因素,故通常用测定极化曲线的方法来研究电极的极化与电流密度的关系。
一、实验方法及装置本实验电解液为CuSO4溶液(溶液中CuSO4.5H2O浓度为165g/l,H2SO4 180g/l);电极用φ=0.5mm铜丝作为工作电极,铂片电极作为辅助电极。
为了测得不同电流密度下的电极电位,以一个甘汞电极与被测电极组成电池,甘汞电极通过盐桥与被测电极相通,用CHI660B电化学工作站测得不同电流密度下对应的阴极或阳极极化曲线。
装置如图所示3 1——铜丝(工作电极Ф1.0mm);2——铂片(辅助电极);3——甘汞电极;4——盐桥;二、实验步骤1、将铜电极的工作表面用0号金相砂纸磨光,用蒸馏水洗净,用滤纸擦干,然后放入装有CuSO溶液的电解槽中。
硫化锌精矿直接浸出动力学及其半经验模型

硫化锌精矿直接浸出动力学及其半经验模型1 绪论硫化锌精矿的直接浸出是以硫酸铜为萃取剂浸出提取硫化锌精矿中的锌离子的一种常用方法,该反应机理复杂,许多参数及水解反应率常数等影响因素影响着该反应进程及效果,因此在理论上进行分析是必要却非常困难的。
本文试图探索硫化锌精矿直接浸出反应的动力学行为及其半经验模型。
2 材料与方法实验材料:硫化锌精矿实验设备:反应釜、PH计、氢氧化钠溶液、硫酸铜实验方法:在制定的实验条件(pH值以及硫酸铜浓度)下反复浸出硫化锌精矿,观测其反应进程以及反应效果,收集实验数据,分析反应动力学以及半经验模型。
3 反应动力学硫化锌精矿的直接浸出具有一个综合的复杂的反应过程,从传统的动力学角度看,它涉及:单步、两步、微生物活性和不确定步骤。
通过实验,得到直接浸出过程涉及多道反应,反应网络有多步反应及多道反应,它可以概括为两步反应:尾矿中存在的硫脲酸根铜离子(Cu2 2+)与金属离子(Zn2 +)反应形成硫酸铜锌,然后硫酸铜离子与尾矿中存在的铜离子反应,形成硫酸铜和金属离子的萃取复合物,经过单步的水解反应,形成硫酸铜和金属离子。
4 半经验模型将反应动力学表达式拟合到实验结果,形成半经验模型,半经验模型包括两个部分,一是根据反应动力学建立的实验数学模型,另一个是利用蒙特卡洛法确定的参数集合。
研究过程中,实验发现的硫化锌精矿浸出反应的半经验模型为:动力学表达式:k1=dC/dt=-K1[Cu2+][Zn2+]k2=d(CuZn)/dt=-K2[Cu2+]参数集合:K1=0.02243;K2=1.552其中K1、K2为水解反应速率常数,[Cu2+]、[Zn2+]为Cu2+和Zn2+的质量分数。
5 结论本文通过实验研究对硫化锌精矿直接浸出动力学进行了研究,形成了一套半经验模型。
该模型给出了两个水解反应速率常数,反应过程及结果具有良好的交叉验证性和可重复性,有助于深入研究硫化锌精矿直接浸出动力学模型及过程研究。
- 1、下载文档前请自行甄别文档内容的完整性,平台不提供额外的编辑、内容补充、找答案等附加服务。
- 2、"仅部分预览"的文档,不可在线预览部分如存在完整性等问题,可反馈申请退款(可完整预览的文档不适用该条件!)。
- 3、如文档侵犯您的权益,请联系客服反馈,我们会尽快为您处理(人工客服工作时间:9:00-18:30)。
冶 金 原 理 实 验 报 告
专业班级: 冶金0905 学号: 0503090629 姓名:吴海艳 实验日期: 2011 年 11 月 日 室温: 20C ︒ 大气压:Pa 1001.15⨯
实验名称:硫化锌精矿氧化过程动力学
一.实验目的
(1) 采用固定床进行硫化锌精矿氧化焙烧,分析各段时间硫的产出率,来测定氧
化速度与时间曲线。
(2) 学会氧化动力学的研究方法。
(3) 了解硫化锌精矿氧化过程机理。
(4) 学会硫的分析方法。
二.实验原理
在冶炼过程中,为了得到所要求的化学组分,硫化锌精矿必须进行焙烧,硫化锌的氧化是焙烧过程最主要的反应:ZnS+3/2O 2=ZnO+SO 2 反应过程的机理:
ZnS+1/2O 2(气)——ZnS …[O]吸附——ZnO+[S]吸附 ZnO+[S]吸附+O 2——ZnO+SO 2解吸
这个反应是有气相与固相反应物和生成的多相反应,包括向反应界面和从反应界面的传热与传质过程。
可以认为反应按如下步骤进行 (1) 氧通过颗粒周围的气体膜向其表面扩散; (2) 氧通过颗粒表面氧化生成物向反应界面扩散; (3) 在反应界面上进行化学反应;
(4) 反应生成的气体SO 2向着氧相反的方向扩散,即反应从颗粒表面向其中心部
位逐层进行,硫化物颗粒及其附近气体成分的浓度可用未反应核模型表示。
提高硫化物氧化速度,可以通过以下方式:
提高氧分压,加速SO 2吸收,减小矿石粒度,降低氧化层厚度,提高温度 本实验采用固定床焙烧,来测定硫化锌氧化速度。
分析氧化过程某一时刻产生的SO 2
的量,来计算硫化锌硫的脱出率;即单位时间硫的脱出率。
为了便于比较不同硫化物和不同条件下硫化物的氧化速度,引入以下公式:总
S S S i R =
式中R S ——精矿中硫的氧化分数;S i ——硫化锌精矿氧化过程中某一时间内失去的硫量;S 总——精矿中所有的含硫量。
利用氧化分数和时间关系作出,可以得出不同温度、不同粒度、不同气相组成对硫化锌焙烧过程的影响。
实验利用卧式管状炉,通空气在温度低于硫化锌的熔点下进行。
通过秒表计时,控制吸收液的吸收时间,利用滴定来分析SO 2得到S 的脱出率。
三.主要仪器、试剂及装置图
仪器等:
电子天平、管状电炉、智能温度控制器、气体吸收装置、无油空气压缩机、锥型瓶、碱式滴定管、秒表、滴定台。
试剂:
硫化锌精矿(其中S 30.27%)、双氧水、指示剂(甲基红、亚甲基蓝)、氢氧化钠溶液(0.21mol/L)
四.实验步骤和实验现象
1、开启温度控制器,对卧式管状炉进行;
2、检查气体管路,并熟悉气体走向和三通阀门的转向;
3、按35mlH2O2+0.2%甲基红15ml+0.2%亚甲基蓝2ml+水定容为500ml,分装入12支试管,并连接好管道,检查连接是否正确;
4、利用电子天平准确称量硫化锌1~2g,并装入舟皿;
5、待炉子升到所需温度,将已装好硫化锌的舟皿用铁丝推入炉管中最亮的地方,并迅速塞好塞子,接通管道,开启无油空气压缩机,保持气流稳定,吸收液一有气泡就开始计时;
6、每5分钟旋转一次阀门,进入下一组试管进行吸收;
7、将已吸收过二氧化硫的溶液用NaOH溶液滴定,颜色由紫色变为亮绿色为终点,记下相应的组数和体积;
8、实验完毕,整理实验场地;
9、根据所得数据计算脱硫率,作出脱硫率Rs-t时间关系曲线图,根据相应化学反应的速度公式判断为何种控制环节。
五.实验结果及数据处理(张贴原始记录卡)NaOH的浓度C=0.21mol/l; n理=0.01056mol
组数体积
(ml)
时间
(min)
硫的物质的
量(mol)
脱硫率(%)
1 49.6 5 0.005208 49.318
2 15.
3 10 0.0068145 64.531
3 4.7 15 0.0070308 66.580
4 0.4 20 0.0073
5 69.602
5 0.05 25 0.00735525 69.651
6 0.05 30 0.0073605 69.702
六.实验讨论
1、在炉子升到所需温度,将以装好的硫化锌的舟皿用铁丝推入炉管中最亮的地方,并迅速塞号塞子,接通管道,开启无油空气压缩机,保持气流稳定,当吸收液一有气泡就开始记时间。
2、试验注意事项:本实验是在高温条件下操作,所以试验过程中要注意安全,取放舟皿时佩戴手套,试验完成后取出舟皿时切勿直接放在试验台面上要放在专门的地方,以免损坏试验台;气密性是试验成功的关键性因素,试验前务必检查装置的气密性;旋转活塞时注意观察好方向确保一次成功;双氧水现配现用;
3、可以通过一下方式提硫化锌的氧化速度:提高加热温度、磨碎矿石尽量减小矿石的粒度、加速二氧化硫的吸收、提高氧分压、选用大一些的舟皿平铺氧化锌精矿来降低氧化层的厚度;
4、试验区误差的原因:本实验通过秒表计时控制吸收缩液的吸收时间,因此时间记录的准确性是后期分析处理数据的前提;滴定过程中没有注意观察颜色变化,氢氧化钠过滴或少滴;称硫化锌时天平不准确;双氧水过期;吸收液太少二氧化硫没有吸收完全。