NC_SST_I分解炉锥部结皮的处理
分解炉结皮原因分析
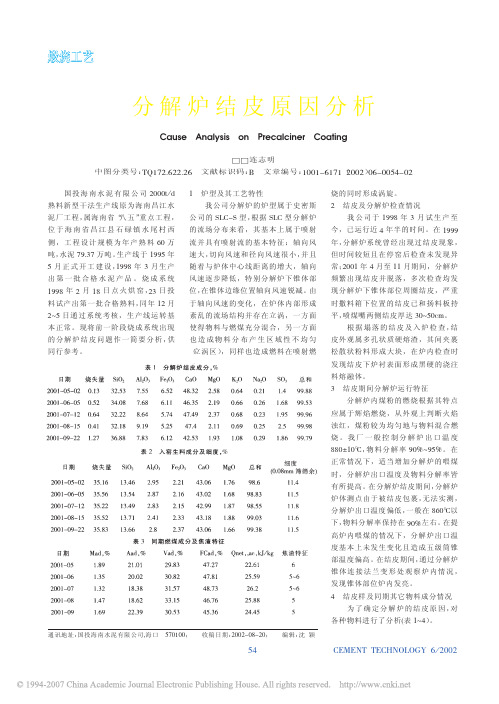
版社出版, ’33-,!
水泥技术 (++( 4 $
!!
#
炉型及其工艺特性 我公司分解炉的炉型属于史密斯
烧的同时形成涡旋。
%
结皮及分解炉检查情况 我 公 司 于 #002 年 1 月 试 生 产 至
公司的 456*4 型, 根据 456 型分 解 炉 的流场分布来看,其基本上属于喷射 流并具有喷射流的基本特征:轴向风 速大, 切向风速和径向风速很小, 并且 随着与炉体中心线距离的增大,轴向 风速逐步降低,特别分解炉下锥体部 位, 在锥体边缘位置轴向风速锐减。由 于轴向风速的变化,在炉体内部形成 紊乱的流场结构并存在立涡,一方面 使得物料与燃煤充分混合,另一方面 也造成物料分布产生区域性不均匀 ( 立涡区) ,同样也造成燃料在喷射燃
1
结皮期间分解炉运行特征 分解炉内煤粉的燃烧根据其特点
应属于辉焰燃烧,从外观上判断火焰 浊红,煤粉较为均匀地与物料混合燃 烧。我厂一般控制分解炉出口温度 物 料 分 解 率 0);30+; 。 在 22)9#): , 正常情况下,适当增加分解炉的喂煤 时,分解炉出口温度及物料分解率皆 有所提高。在分解炉结皮期间, 分解炉 炉体测点由于被结皮包裹, 无法实测, 分解炉出口温度偏低, 一般在 2’): 以 下, 物料分解率保持在 0);左右。 在提 高炉内喂煤的情况下,分解炉出口温 度基本上未发生变化且造成五级筒锥 部温度偏高。在结皮期间, 通过分解炉 锥体连接法兰变形处观察炉内情况, 发现锥体部位炉内发亮。
今,已运行近 , 年半的时间。在 #000 年, 分解炉系统曾经出现过结皮现象, 但时间较短且在停窑后检查未发现异 常; %))# 年 , 月至 ## 月期间,分解炉 频繁出现结皮并脱落,多次检查均发 现分解炉下锥体部位周圈结皮,严重 时撒料箱下位置的结皮已和扬料板持 平, 喷煤嘴两侧结皮厚达 1)3+)78。 根据塌落的结皮及入炉检查, 结 皮外观属多孔状质硬熔渣,其间夹裹 松散状粉料形成大块,在炉内检查时 发现结皮下炉衬表面形成黑硬的浇注 料熔融体。
预分解系统结皮堵塞的原因及处理对策
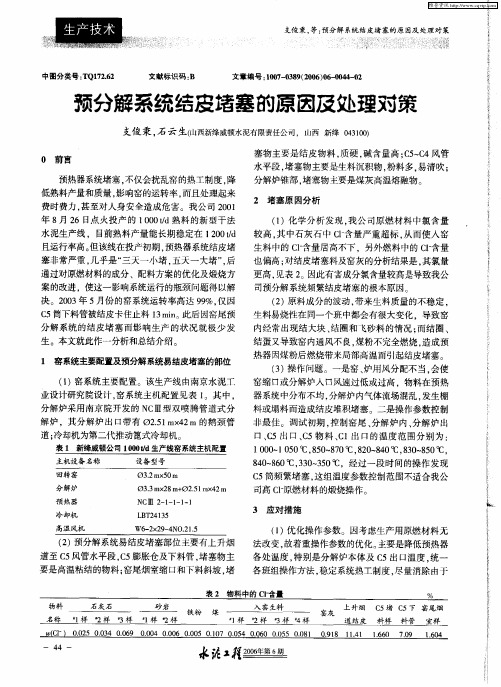
2 堵塞原 因分 析
预热器系统堵塞 , 不仅会扰乱窑的热工制度 , 降 低熟料产量和质量 , 影响窑的运转率, 而且处理起来
费时费力 , 甚至对人身安全造成危害。我公司 20 01 年 8 2 点火投产 的 l 0 t 月 61 3 0/ 0 d熟料的新型干法
法改变, 故着重操作参数的优化。 主要是降低预热器
各处温度 , 特别是分解炉本体及 C 5出 口温度 . 统一
各班组操作方法 , 稳定系统热工制度 , 尽量消除由于
一
4一 4
水滩工 程
维普资讯
支俊秉, : 等 预分解 系统结皮堵塞的原 因及处理对策
维普资讯
支俊秉 , : 等 预分解系统结皮堵塞的原 因及 处理对策
… 一
l i囊 扫 i l : |
曩 0| 跨越0 鼻 嚣 黪
中图分类号 :Q126 T 7. 2
文献标识码 : B
文章编号 :0 7 0 8 (0 6 0 - 04 0 1 0 — 3 9 2 0 )6 0 4 — 2
( )化学分析发现 。 1 我公司原燃材料 中氯含量
水泥生产线 ,目前熟料产量能长期稳定在 1 0 0/ 2 t d 且运行率高。 但该线在投产初期 , 预热器系统结皮堵
较高 , 其中石灰石 中 c一 l 含量严重超标 , 从而使人窑
生料 中的 c一 l 含量居高不下,另外燃料 中的 c一 l 含量 也偏高; 对结皮堵塞料及窑灰的分析结果是 。 其氯量
l0 0 5 0 -l 0℃ , 5 - 7 0 8 0 8 0℃ , 2 ~ 4 8 0 8 0℃ , 3 ~ 5 8 0 8 0℃ ,
【免费下载】分解炉频繁结皮原因分析及处理

分解炉频繁结皮原因分析及处理-中国水泥技术网2009-5-23 作者: 瞿学坤刘飞姚公放,义煤集团水泥公司,河南渑池472411我公司5000t/d生产线于2006年6月26日投料试生产,其中分解炉采用喷—旋结合形成复合流场的炉型。
投产后,分解炉频繁结皮严重影响生产。
1 结皮情况每次结皮均在分解炉的4根三风道燃烧器周围并向分解炉锥体延伸,向上可到分解炉直段都有结皮,严重影响窑风入炉,造成分解炉燃烧器出口堵塞,分解炉多处发生过红炉,甚至造成窑系统无法运行而停产。
由于分解炉结皮严重造成停窑清理6次,每次清理费时费力,安全性极差,最长的一次清理用了5d。
窑运转率极低,最长的运转1个半月左右,最短的只有10d。
2原因分析该生产线最初设计使用长焰煤和贫瘦煤搭配的燃料,分解炉锥体上对称分布着4根法国皮拉德公司产的三风道燃烧器,用来强化煤粉在分解炉内的燃烧。
正式生产时考虑整个系统的适应能力,生产用原煤是陕西神木产优质烟煤,挥发分在25%~30%,与最初设计差别较大。
因燃烧器与下料点位置相距较远,煤粉燃烧放出的热能不能迅速被物料吸收,在炉锥体较小的空间形成局部高温造成结皮,甚至红炉;其次就是系统处于试生产,各种设备、电气故障多,开停窑次数较多,加上中控操作水平不熟练,导致分解炉温度波动大产生结皮。
3第一次改造及预防措施3.1 改造方案1)取消4号燃烧器(即三次风入炉口右侧第一根),改为3根燃烧器供煤;3根燃烧器位置均向上提高1m;旋转角度由原来的20°改为0°;水平夹角由原来的30°改为10°;3根燃烧器与分解炉的中心的定位角度不变;燃烧器头部伸出炉浇注料表面300mm(改造示意见图1)。
图1 分解炉改造示意2)C4下料管撒料盒位置不变,用浇注料在撒料盒板体上浇注一个斜坡,即改现有板体与水平夹角15°为30°。
3.2 预防措施1)关小三次风,加强分解炉的喷腾效应。
分解炉锥部结皮的影响及处理

分解炉锥部结皮的影响及处理摘要:近年来,新型干法生产线预热器锥部及下料管处结皮堵塞很少,但烟室和分解炉锥部结皮仍然较多。
本文从对分解炉锥部结皮的原因及特征的分析入手,进而对其结皮现象产生的影响及处理方法进行了相关论述,希望能够起到抛砖引玉的作用。
关键词:分解炉锥部结皮影响处理一、概述我公司2500/d生产线于2012年5月2日点火试生产。
采用的是喷旋结合的管道炉炉内采用的两个直筒式燃烧器。
投产后,随产量的增加,分解炉锥部结皮愈来愈严重。
造成窑内产生还原气氛,煤粉不完全燃烧。
在投产后一个半月里因分解炉解皮停窑四次每次都要耽误生产12小时以上,开始在预热器锥体开了三个200×200的门子用人工清结皮而只是能够维持不停,清理十分危险,并且漏风严重,影响到热工制度的稳定,严重影响了熟料的生产质量,针对上述情况我公司积极联系设计院于2012年6月中旬进行了一系列的调整和技改。
二、分解炉锥部结皮原因及特征分析分解炉结皮,与生料中碱含量有关,有关方面测定,结皮中K20含量占10%左右。
同时与分解炉温度控制有关,一般炉温控制在900℃左右,就很少出现熔块和结皮现象,一旦超过950℃,炉内物料粘性增加,容易造成Ⅳ级下料管堵塞。
为保证分解炉正常工作,炉温不要控制过高,CaCO3,分解率也没必要达到100%,控制在85%~90%即可。
通常情况下,分解炉锥部结皮较为严重, 一般情况下,3~4天就需停窑处理。
其结皮主要发生在分解炉三次风入口至进料口之间部位, 见图1。
根据结皮与物料成分分析情况表明,结皮主要是由煤灰渣熔结其它物料而形成大块。
一般来说,分解炉锥体部位煤灰渣结皮的形成主要是由以下两方面原因造成的:A、燃煤的焦渣特征情况,只有焦渣特征值大于一定等级时方能形成具有一定强度的煤渣结皮;B、分解炉内燃料起火预燃速度快,炉内存在偏流造成锥体部位温度场分布不均、局部高温。
但此类结皮的分布特征是在分解炉锥体内衬局部位置形成结皮。
分解炉锥部结皮原因分析及解决措施

管
通 过对 水 泥 窑 、预 热 器 系 统 的详 细 检 查 发 现 ,预 热
器旋风筒 、分解炉上部都没有结皮 ,但分解炉锥部靠
三 次风 管 沿燃 烧 器旋 流 方 向 3/4圈 结 皮 严 重 ,最 严
重处结皮厚度达到800mm左右 ,高度达到4m左右 , 分 解 炉缩 口结 皮达 到 1/3左右 。
4 效 果
(编辑 :刘翠荣 )(收稿 日期 :2012—05—25)
通过 以上改造及参数的调整 ,水泥窑开启后运
(上 接 第 3页 )
系统 烘 干 。
储存一定的物料 ,可 以延长待料时间 ;三是辊压机可
(4)缺陷情况 。辊压机功率为 3 350kW的减速 视情况关 闭气动阀止料 ,减少工作压力 ,使辊压机空
分解炉 炉锥体浇注料基本平齐(见 图 1),同时燃烧 窑头喂煤量过多 ,窑内煤粉的燃尽率较差 ,窑内出现
器位置正好处于三次风进分解炉处 (见 图2)。在运 后结圈 ,窑 内通风状况变差 ,未燃尽的煤粉与物料粘 行过程 中,窑尾煤粉经燃烧器 喷出后遇到高温富氧 附在烟室及分解炉缩 口形成结皮。
宋宏 昌:分解炉锥部 结皮原因分析及 解决措施
-一 一 臻#臻 孽≯i甍蹲秀鼙甏§毫0 誊叠曩_劳
囊棼鬣蒜磐 |薯
中图分类号 :TQ172.62 文献标识码 :B 文章 编号 :1007—0389(2013)0l一40—02
分解炉锥部结皮原 因分析及解决措施
宋 宏 昌(青海祁连山水泥有限公司,青海 西宁810021)
2 原 因分 析
图2 燃烧器、三次风管位置
式 计 算 ,当地 大 气 压 力 72.633 kPa,是 海 平 面 的 71.68% ;大 气 密 度 1.031 kg/m’,是 海 平 面 的
浅析分解炉结皮原因及处理措施

浅析分解炉结皮原因及处理措施
白银涛
【期刊名称】《河南建材》
【年(卷),期】2012(000)003
【摘要】综合分析了我公司分解炉锥体结皮的原因,提出处理措施,认为生产中加强操作,加强工艺管理,合理配料,有效控制原燃料有害成分,避免结皮。
【总页数】2页(P159-160)
【作者】白银涛
【作者单位】邓州中联水泥有限公司,474150
【正文语种】中文
【中图分类】TQ172.622
【相关文献】
1.水泥预分解系统的结皮、积料和堵塞的原因及处理措施浅析 [J], 邓德新
2.1000t/d预分解窑预热器结皮原因及处理措施 [J], 张淑广
3.分解炉锥部结皮原因分析及解决措施 [J], 宋宏昌
4.TSD分解炉预燃炉结皮原因及预防 [J], 史高勇
5.分解炉锥部结皮的原因与处理 [J], 楼美善;王广杰
因版权原因,仅展示原文概要,查看原文内容请购买。
一起分解炉耐火砖烧蚀的原因及处理方法
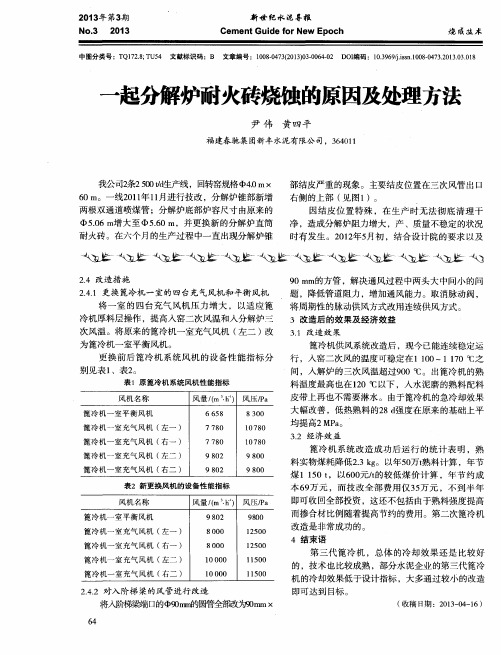
风 机 名 称 风量 / ( m . h - 1 风压/ P a
料温 度最 高也 在 1 2 0 o C 以下 ,入水 泥磨 的熟 料 配料 皮带 上再也 不需要 淋水 。由于篦冷机 的急冷却 效果 大 幅改善 ,低 热熟 料 的2 8 d 强度 在原 来 的基 础 上平 均提 高2 MP a 。
一
起分解炉耐火砖烧蚀的原因及处理方法
尹伟 黄 四平
福建春驰 集团新丰水泥有限公 司 ,3 6 4 0 1 1
我公司2 条2 5 0 0 生产线 ,回转窑规格 4 1 0 m× 6 0 m。一线 2 0 1 1 年1 l Y ] 进行技 改 ,分解炉 锥部新 增 两根双 通道 喷煤 管 ;分 解炉底 部炉 容尺 寸 由原来 的
2 0 1 3 年 第3 期
No . 3 2 0 1 3
新 世 纪水 泥导报
C e me n t Gu i d e f o r N e w E p o c h 鹰 威键术
中图分类号 : T Q 1 7 2 . 8 ; T U 5 4 文献标识码 :B 文章编号:1 0 0 8 — 0 4 7 3 ( 2 0 1 3 ) 0 3 — 0 0 6 4 — 0 2 D 0 I 编码 :i 0 . 3 9 6 9 / j . i s s n . 1 0 0 8 — 0 4 7 3 . 2 0 1 3 . 0 3 0 1 8
9 8 0 0
篦冷 机 系 统 改 造成 功 后 运 行 的统计 表 明 ,熟 料 实物煤 耗 降低2 . 3 k g 。以年5 0 万t 熟 料计算 ,年节 煤1 1 5 0 t ,以6 0 0 元/ t 的较 低 煤 价计 算 ,年 节 约成
分解炉的不良安装对熟料烧成的影响及改进措施

为①5 m×33.73 m的NC SST-I型分解炉 。受建设 时技
术水平所限,在生产中暴露出一些 问题,如:入窑
生料 分解 率偏 低, 窑产 、质量 一直 不理 想 ;分 解炉
结 皮厚重 , 影响窑 内通 风, 甚至停 窑 处理 等 。经过
一 段时问的摸索和持续改进,取得了较好效果。
1 NC.ssT_I型分解炉简 介
滑履轴承罩壳是 由分片罩壳通过法兰把合而成, 下部 固定在 滑 履轴 承底 板上 。罩 壳 与筒 体问 的密封 结构常见的有:橡胶加毛毡密封 、带弹簧的橡胶唇
型密封 (类似于唇型密封 圈 )。 橡 胶 密封 圈 (图 1)由于 其截 面厚 实 ,弹性 较 差 ,
图1橡胶密封 圈
分解炉 内未燃尽 的煤粉 ,通过C 旋风筒收集 ,进入 窑 内继续燃烧 ,造成烟室温度 高达 1 100-1 200℃ 。调 节 窑前煤 也无 法控 制尾 温 ,大 量低熔 点 液相提 前 出 现 ,在G筒膨胀仓 、窑尾 下料斜坡及分解炉锥部 结皮 严重,并在窑尾末端形成厚窑皮 (实际上是结皮), 同样影响窑内通风,严 重时窑尾密封圈漏料。我们 在 操作 中总 结 出这样 的配煤 经验 : 当煤 粉灰分 <28% 时,炉 、窑用煤 比例控制为60:40; 当煤粉灰分 >28%时,炉 、窑用煤 比例控制为55:45,以保证煤 粉 在分 解炉 内充分 燃 烧和 生料 的足 够分 解率 ,情 况 稍有好转 。 4改进措 施
(1) 由于 两 喷煤 嘴喷 出角 及风 速 不当, 使煤 粉
炉 内的分散和均布 。
沿炉壁 喷 出, 影 响燃料点 火 速度 及预 燃环境 , 造成
炉 内温 度 场分布 不 均,偏 流 严重 ,局 部高 温 。分 解
分解炉锥体部分烧穿问题的分析与处理

致分 解炉 锥部 烧穿 ( 缩
口膨 胀节 至撒 料 台锥 体
部 分 的 结 皮 , 是 与 燃 烧 烟 煤 且 采 用 分 料 装 置 有 也
4 1 元 /, 0 0 生 产 4 .水 泥 4 . 万 t 约 成 本 .2 t 2 1 年 25 88 节
4 .万 t41 元/ 2 1 5 万 元 ; 88 x .2 t 0 . 6 = 0
2 1 全 年 产 生 经 济效 益达 到 了 成本 为 349 5 00 3. 7
万元
( ) 00 共 生 产矿 粉 48 万 t其 中煤 渣 用 量 1 21年 .6 , 09 万 t两 种 物 料 的 不 含 税 价 格 分 别 为 煤 渣 6 .9 .7 , 46 元 /矿渣 157  ̄/合计节约生产成本7 . 7 t , 4 .9 _, t 86 万元。 6 ( ) 干 煤 耗 降低 35 gt无 烟 煤 不 含 税 价格 2 烘 .k/,
为 l。两 侧 喷煤 口炉 内偏 角 一 致 、 称 布 置 ; 是 5, 对 三 缩 口尺寸 缩 小 至 210 nx lO 0 mi 2 O mm, 以解 决 塌 料 问
部分经 常结皮 , 最厚 曾达 1n 二是人分解炉下部下 题 ; ; i 四是 炉 容偏 大 , 窑分 解 率 较 高 , 人 系统 产 量会 偏 料管分料 阀位置在 6 %~ 0 %范 围内调整多次 , 0 10 效 大 , 时要控 制 好分 解炉 出 口温 度 在 80 此 8 ℃以下 。 果不 明显 , 当分 料超过 7%时 , 口出现塌料 现 且 0 缩 经过 以上几点改进 , 分解 炉局部烧穿现象及结 且 象; 三是三次风 阀开度约 3%, 5 多次调整 , 效果甚微。 皮得 到 较好 解决 , 回转 窑 系统 产 质量 较 为稳 定 。
分解炉频繁结皮原因分析及处理-推荐下载

分解炉频繁结皮原因分析及处理-中国水泥技术网2009-5-23 作者: 瞿学坤刘飞姚公放,义煤集团水泥公司,河南渑池472411我公司5000t/d生产线于2006年6月26日投料试生产,其中分解炉采用喷—旋结合形成复合流场的炉型。
投产后,分解炉频繁结皮严重影响生产。
1 结皮情况每次结皮均在分解炉的4根三风道燃烧器周围并向分解炉锥体延伸,向上可到分解炉直段都有结皮,严重影响窑风入炉,造成分解炉燃烧器出口堵塞,分解炉多处发生过红炉,甚至造成窑系统无法运行而停产。
由于分解炉结皮严重造成停窑清理6次,每次清理费时费力,安全性极差,最长的一次清理用了5d。
窑运转率极低,最长的运转1个半月左右,最短的只有10d。
2原因分析该生产线最初设计使用长焰煤和贫瘦煤搭配的燃料,分解炉锥体上对称分布着4根法国皮拉德公司产的三风道燃烧器,用来强化煤粉在分解炉内的燃烧。
正式生产时考虑整个系统的适应能力,生产用原煤是陕西神木产优质烟煤,挥发分在25%~30%,与最初设计差别较大。
因燃烧器与下料点位置相距较远,煤粉燃烧放出的热能不能迅速被物料吸收,在炉锥体较小的空间形成局部高温造成结皮,甚至红炉;其次就是系统处于试生产,各种设备、电气故障多,开停窑次数较多,加上中控操作水平不熟练,导致分解炉温度波动大产生结皮。
3第一次改造及预防措施3.1 改造方案1)取消4号燃烧器(即三次风入炉口右侧第一根),改为3根燃烧器供煤;3根燃烧器位置均向上提高1m;旋转角度由原来的20°改为0°;水平夹角由原来的30°改为10°;3根燃烧器与分解炉的中心的定位角度不变;燃烧器头部伸出炉浇注料表面300mm(改造示意见图1)。
图1 分解炉改造示意2)C4下料管撒料盒位置不变,用浇注料在撒料盒板体上浇注一个斜坡,即改现有板体与水平夹角15°为30°。
3.2 预防措施1)关小三次风,加强分解炉的喷腾效应。
分解炉缩口结皮的原因分析及解决措施

分解炉缩口结皮的原因分析解决措施0 前言河南新乡平原同力水泥有限责任公司(以下简称“我公司”)第一条5000t/d水泥熟料生产线于2005年4月上旬建成投产运行。
2006年4月该生产线分解炉缩口结皮严重,使系统通风量减小,造成窑内产生还原气氛和煤粉不完全。
采用加大拉风后,则增大了高温风机的电耗,且把烧成带向窑尾移动,导致熟料提前成球而结粒偏大,黄心料、欠烧料较多。
据统计,此时熟料叫w(f-CaO)值平均在2.0%左右,28 d强度约降低5 MPa,严重影响了熟料产质量。
采取相应措施后,分解炉缩口结皮很少,熟料产量大幅度提高、质量明显好转。
1 分解炉缩口结皮原因分析1.1煤质的影响我公司原煤采用低挥发分无烟煤(煤的工业分析见表1)。
原煤的供应商较多(少时有3家,最多时有7~8家)。
为了降低成本,允许供应商在满足我公司原煤各项质量指标要求的前提条件下对原煤进行搭配调整。
但在经济利益的驱动下,有的供应商会掺加一些价格低廉的高硫煤。
虽然进厂混合煤全硫含量(质量分数)控制都小于1.5%,但混合煤可能是由含硫量差别不大的三种煤组成,也可能是由低含硫量煤 [w(Sbad)=0.3%~0.5%]与高含硫量煤[w(Sbad) =3.5%~4.0%]与其他煤按比例混合而成,这在煤的工业分析中是难以分析清楚的。
若是后者且均化措施又不到位,那高硫煤时,在无旁路放风的情况下,在硫和碱反应达到平衡后还有过剩,过剩的硫会在分解炉缩口形成致密的结皮。
表1 煤粉工业分析Mad/% Vad/% Aad/% Sbad/% Qnet,ad/(kJ�6�1kg-1)1.38 10.57 30.71 1.91 23452.68另外,煤粉细度偏粗也是造成分解炉缩口结皮的原因之一。
因对正常运行中的回转窑来说,在温度和系统通风量基本稳定的情况下,煤粉的速度与煤粉的挥发分、灰分、水分含量和细度有关。
在选定矿点原煤后,煤粉的挥发分、灰分和水分含量基本固定,则煤粉细度成为满足特定工艺的关键参数。
分解炉缩口结皮的原因分析及解决措施

分解炉缩口结皮的原因分析及解决措施(作者:江超,郝延辰,朱建妨本信息发布于2009年05月21日,共有2143人浏览) [字体:大中小]2 采取的措施2.1 稳定煤质首先,根据原煤的煤质、价格及供应商的信誉等因素确定2~3家作为长期稳定的供应商;其次,加强原煤的进厂质量检验,避免或减少使用高硫煤(如必须使用高硫煤,则应加强原煤预均化和均化工作);第三,降低煤粉筛余控制指标,由5.0%降低到3.0%,并在生产中严格控制,以提高煤粉的燃尽率。
2.2 合理用风在喂料量不变的情况下,三次风闸板开度加大,能增加分解炉燃烧空气量,降低了系统阻力;同时相应增加分解炉用煤量,有利于尾煤的充分燃烧,提高了入窑生料CaCO3分解率。
正常生产情况下,我公司三次风闸板开度一般控制在55%~65%。
当三次风闸板烧坏后,运转期内,为了完成当月的生产任务,可以采用向三次风管内扔耐火砖的办法,以改变窑炉的风量分配;系统检修时,则应及时对烧坏的三次风闸板进行更换处理。
2.3 保持合适的窑、炉用煤比例窑头用煤量的大小主要是依据入窑生料的喂料量和CaCO3分解率、生料易烧性、熟料f-CaO和升重、窑速及窑皮等因素来确定的。
分解炉用煤量主要是根据入窑生料分解率、生料易烧性、分解炉出口气体温度来调节的。
如果风量分配合理、入炉煤粉燃烧充分,但分解炉出口气体温度偏低,入窑生料分解率低,C5出口气体温度低,这说明分解炉用煤量过少,应增加。
如果预分解系统温度偏高,热耗增加,甚至出现分解炉内煤粉燃尽率低,煤粉到C5内继续燃烧,导致预分解系统产生结皮或堵塞,这说明分解炉用煤量过多,应降煤。
操作中,窑炉用煤比例取决于入窑生料分解率、生料易烧性、窑速及燃料的特性等。
一般情况下,窑头用煤控制在40%~45%、分解炉用煤控制在60%~55%时比较合适。
杜绝出现窑炉用煤比例倒置现象,应注意。
2.4 扩大分解炉主炉下缩口预分解窑窑尾气体成分表征了窑内燃料的燃烧状况及窑内的通风情况。
防止SLC-S型预热器系统结皮堵塞的措施

度降低后 , 以硫 酸盐或氯化 物的形 态冷凝在
原 料 上 , 而 这 蝗 物 质 的熔 点较 低 通 , 过 多 次
挥发
,循环
富集
, 加 剧 了在 高温 时挥发
低温
。
时 凝聚 的过程 这 , 些 凝 聚下 来的 物料 粘附在
预热器 、
分解
炉
及连接管道
内形 成结 皮
处
、
1 . 气 体温 度 急剧 卜升 。 堵 塞 时生 料量 大 幅度减少 ,生料和热气体不能交换 ,整个系 } 统 温 度 会 上二升 , 尤 其 是 它 下 面 一 级 的 旋 风 i 简 ,温度将会急剧 上 升 。
1 .物料烧融造成 的结皮堵塞
一 般发 生 在 C 5 , 物料在 预 热器 内过 早 出现 熔 融状 态 粘 , 附在旋风 筒锥 部 或下 料 管 壁 ,更容易吸附高温 物料 ,而 造成下 料管旋 风筒堵塞 。
( 1 )物料太 软 。 由于 配 料 K H 、S M 偏 低 ,
R 2 0 、Mg O 含量偏高 ,生料成分波动大 ,造成 物料熔点低 。
同程度 的造成分解 炉 塌 料 ,分解炉本 身 由于 抽风不足也会造成塌料。 主要 原 因有 :
( 1 )上 升烟道 高温 阀开 度过 大 , 使窑和 炉 的风量 分配 不 合理 窑 , 内通 风 过 大 , 而 炉
内通 风过 小 。 (2 )分解炉燃烧不稳定 。 分解炉煤量波
动大 或 , c 4 来料量 波动大 ,造 成分解 炉 内温
(2 )温 度控制过 高 。 操作 中加煤量 过大 ,
或生料喂料量波动过大 , 造成物料温度过
高 , 液相 提前 出现 。 ( 3 )不 完全燃烧 。 由于 煤灰份过高 ,煤粉
分解炉锥部结皮的影响及处理

…
墨 3 年月 2
C h 甲 i n a 圉 C 化 h e m 上 i c a 员 l T 易 r a d e
分解炉锥部结皮的影响及处理
王 毅
( 扎兰 屯水 泥有 限公司 . 内蒙 古呼伦 贝尔 1 6 2 6 5 0 )
墨 篓 强 备
摘
要 :近年来 ,新 型干法生产线预热 器锥部 及下料管处 结皮堵 塞很 少, 但烟 室和 分解炉锥部结皮仍 然较 多。本文从对分解炉锥部结皮 的原 因及
三、分解 炉锥 部结皮 的影 响
通 常情 况 下 ,分解 炉锥 部 结皮 严重 ,会 使 系统通 风 量减 小 ,造成 窑 内产生还 原气 氛 和煤 粉不 完全燃 烧 。采用 加大 拉风 后 ,则 增大 了高 温风机 的 电耗 ,且把 烧 成带 向窑尾 移动 ,导 致熟 料提 前 成球 而结 粒偏 大 ,黄 心料 、欠烧 料较 多。据 统计 ,此 时熟料 值平 均在 2 . 0 %左右 ,2 8
一
部位 , 见图 l 。
l § 懿 番
筛筛 余 6 %以下也不 形成 结皮 ; 6 . 当燃 煤 的焦 渣 特征 值 在 4  ̄ 6时 ,若 煤 粉 的细 度 控制 在 O . 0 8 a r m 筛筛余 8 %以上 ,分解 炉锥 体部位 也不 产生结 皮 。 根据 以上特 征及 分解 炉 运行 的现 象 ,可 以充 分说 明我 厂分 解 炉锥 体 部 位 结 皮 的 原 因是 :我 厂 采 用 的燃 煤 挥 发分 普 遍 偏 高 ,基本 都 在 3 0 %以上 ,而 且原 煤热 值较 高 ,由于 煤粉 制备 时为 满足 窑头 要 求 ,煤 粉 的细度 一直控 制在 0 . 0 8 am 筛筛 余小于 8 r %,因此 ,在 煤粉 喷入 分解 炉 后 ,迅 速起 火 燃烧 且燃 烬速 度快 ,甚至 形成 明焰 燃烧 ,造 成 分解 炉 内燃 料燃 烧集 中在分解 炉 上游 部 位 ,从而 在分解 炉 下锥 体 部位 形成 区 域性 温度 偏高 ,一方 面造 成分 解 炉下 锥体 部位 内衬 烧 损 ,另一 方面 在 燃煤 焦渣特 征值 大于 4时 ,煤 灰易 熔结其 它物料 在此部 位形 成结皮 。 另外 ,结 合我 厂分 解 炉椎体 部 位结 皮 的具体 现 象 ,其结 皮 的主要 原因 是分解 炉燃 烧 器布 置位 置 不 当 ,原 燃烧 器三 个对 称 喷嘴 考虑 煤质 优 劣 布置 ,而 燃 烧器 位 置 过于 靠 下 ,距离 C 4下料 口太 远 ,并 且 其布 置 角度 偏 向侧壁 燃烧 产 生 的高温 气体 不 能迅 速 与物料 混合 ,产生 局部 高温 ,导致 结皮 。另外 三次 风与 分解 炉 圆周 成度 夹 角入 炉 ,扰乱 了分 解 炉 内的流场 分布 ,物料 与气流不 能迅 速混 匀 ,导 致局部 高温结 皮 。 通过 对 分解 炉下 锥体 结 皮原 因 的分析 ,可 以得 到 以下 的 启示 :在 分解 炉 的优化 操 作 中 ,应 以充足 的炉 容及 良好的 流场 结构 来 确保 炉 内 物料 适宜 的料 气 滞 留时 间以 及物 料 的均匀 分 布 ,从 而 实现 出炉 物料 的 分解 率 。在实 际 控制 中应 尽可 能 确保 分解 炉 内温 度 场 的稳 定 、合 理 , 避免 因偏 流或 原 燃材 料 理化 性 能波 动 等造 成 炉 内温 度场 的 局 部偏 差 , 从而 保证分 解炉 系统 的良好 、稳定 运行 。严重影 响了熟 料产质 量 。
分解炉锥部结皮的原因与处理

分解炉锥部结皮的原因与处理1 存在的问题我公司2 500 t/d熟料生产线,自xxxx年投产以来,分解炉锥部一直因结皮严重影响烧成系统的正常运转,大块结皮经常垮塌堵住分解炉缩口,严重时窑根本无法运行需停窑开孔清理。
据生产报表的统计,平均每年因结皮而造成的短时间止料养火处理多达21次,需停窑较长时间处理的达2次。
2 原因分析(1)我公司锥部结皮最严重的部位主要集中体现在三次风进口与C4筒下料管这一区域(见图1),因该区域恰好是三次风进入的位置,此处的气流中氧含量较高,是富氧区,分解炉的一只喷煤管喷嘴刚好位于富氧区,使得该区域煤粉燃烧速度过快,形成局部高温致使物料粘料结皮。
(2)三次风进入分解炉后形成切向气流,并在进分解炉接口部位又形成一个涡流,造成部分煤粉贴近浇注料燃烧。
(3)燃烧器的位置在C4筒撒料台与三次风口的中下部位,由于旋流与上升气流的影响致使物料和煤粉在上升过程中有部分被粘挡在撒料台的突出部位。
(4) C5筒下料管与烟室斜坡存在700 mm高的落差(见图2),从C5筒进入窑内的生料粉极易被窑内进入窑尾烟室的上升高温气流扬起,增加了气流中的粉尘浓度,加上硫、碱等有害成分的作用,导致缩口与锥部的结皮加剧。
3 改进措施(1)为了避开煤粉在三次风富氧区域和切向气流影响的部位燃烧,变动喷煤管的位置,把原先两根呈180°摆放的喷煤管,改为呈90°摆放(见图1),向撒料台喷煤。
(2)降低C5筒下料管使下料点与烟室斜坡保持在同一平面,从而减少物料与气流反向运动而带起的二次扬尘,降低入分解炉气体的粉尘浓度(见图2)。
4 改造效果从、技术改造后运行至今,锥部未出现结皮现象,停窑后检查也未发现有结皮。
改造后运行一年,也未发生一起因分解炉结皮而导致的工艺事故。
窑运行稳定,工人的劳动强度、工作环境也得到了较大幅度的改善。
预分解系统结皮的原因及预防措施

预分解系统结皮的原因及预防措施预分解系统结皮是指高温生料与窑气中有害组分经过化学反应后形成粘附在内壁上的层状物。
在窑尾、烟室缩口、最下一级旋风筒及其下料溜子、分解炉等部位最容易产生结皮,结皮可导致通风面积减小,阻力增大,而迫使主排风机负荷增大。
结皮脱落时又极容易造成系统堵塞,影响正常的生产。
一般认为:结皮的产生与所用原料、燃料的成分,系统温度的变化,系统通风的情况,设备运转的情况以及工艺操作因素有关。
下面结合一些的具体情况,通过对预热器各级旋风筒中原、燃料中有害元素的分析,以及设备状况,工艺操作等有关因素,对结皮形成的原因进行分析以及相应的处理方法。
1.有害元素的影响有害元素主要包括硫、碱、氯等,它们是形成结皮的一个很重要的因素,煤炭作为目前水泥窑的主要燃料,是有害元素硫的一个重要来源,煤燃烧的大部分硫进入烟气中,烟气中带有大量的CaO生料粉,它在煅烧过程中与K2O、Na2O和SO3发生反应,生成各种硫酸盐物质,主要是K2SO4、2 CaSO4·K2SO4、K2SO4·H2O,,这些硫酸盐属于低熔点化合物,它们会粘附在器壁表面,使粘度增加,流动性减小,久而久之形成结皮。
消除有害元素的影响主要是控制硫、碱的摩尔比,硫碱的摩尔比过高或过低都易形成结皮。
即使硫、碱含量均较高,只要硫碱比在控制范围之内,对结皮也产生不了太大影响,因为原燃料中的大部分硫、碱可以中和在熟料中被带出。
经过分解后的物料进入回转窑后,在烧成带温度极高的情况下,使K2SO4 分解成气态的K2O 和SO3,挥发进入循环气流。
这些物质通过三次风管和窑返回到预热器中,在遇到低温时又生成成固相或液相化合物,附着在物料上被带回窑中,只有少部分热量和粉尘被排出,如此反复形成了预热器与回转窑中的碱循环。
在新型干法水泥生产线中,由于原、燃料中的氯化物在窑内烧成挥发,并随窑内气体进入预分解系统,在此遇到较低温度而凝结于器壁表面,从而使回旋中的物料发粘,流动性变差,附着于壁,累积而形成结皮,附着在物料上的部分氯又进入窑内煅烧,一部分挥发形成气态进入循环气流,这样就形成了氯化物的循环。
分解炉结皮塌料原因的确定方法
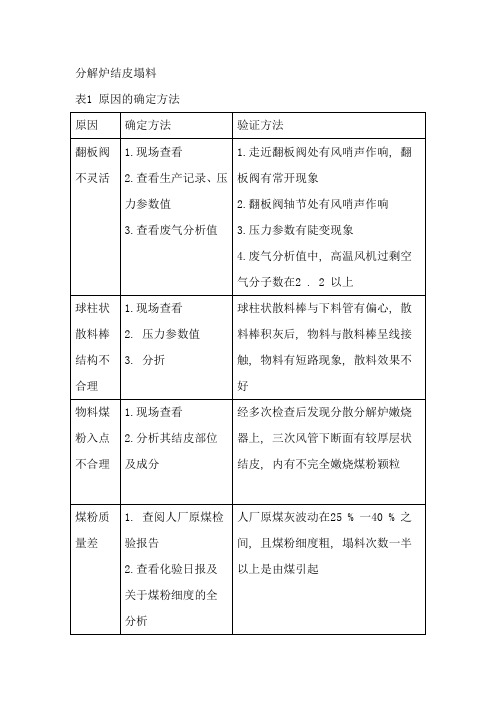
3.分折
球柱状散料棒与下料管有偏心,散料棒积灰后,物料与散料棒呈线接触,物料有短路现象,散料效果不好
物料煤粉入点不合理
1.现场查看
2.分析其结皮部位及成分
经多次检查后发现分散分解炉嫩烧器上,三次风管下断面有较厚层状结皮,内有不完全嫩烧煤粉颖粒
煤粉质量差
1.查阅人厂原煤检验报告
2.查看化验日报及关于煤粉细度的全分析
分解炉结皮塌料
表1原因的确定方法
原因
确定方法
验证方法
翻板阀不灵活
1.现场查看
2.查看生产记录、压力参数值
3.查看废气分析值
1.走近翻板阀处有风哨声作响,翻板阀有常开现象
2.翻板阀轴节处有风哨声作响
3.压力参数有陡变现象
4.废气分析值中,高温风机过剩空气分子数在2 . 2以上
球柱状散料棒结构不合理
1.现场查看
人厂原煤灰波动在25 %一40 %之间,且煤粉细度粗,塌料次数一半以上是由煤引起
表2原因的查找与对策
原因
产生原因
对策
目标
翻板阀不灵活
1.翻板阀轴变形
2 .翻板阀轴进灰
1.对翻板阀的轴进行吹扫
2.严重的翻板阀进行更换
减低漏风系数,待之降低至40 %
散料棒结构不合理
球柱状散料棒与下料管有偏心
散料棒更挨成箱式散料口.改进散料方式
达到预期效果
物料煤粉人点不合结构不合理.
不符合料粉,煤粉在分解对下料点和燃烧器位置进行改理炉内流态化分布机理
对下料点和燃烧器位.煤灰份高,波动大
2.原煤粉品质杂,堆放无序
3.煤粉细度粗
1.加强采购的质量控制
2.降低煤粉细度
人厂煤灰份二27 %±
预热器捅堵、结皮清理应急预案 Microsoft Word 文档

预热器捅堵、结皮清理应急预案(试行)一.堵塞的判断:①中控室判断:预热器堵塞时其锥部负压为零,该旋风筒出口温度明显上升,下料管温度不变或下降(如堵塞点在热电偶以下,热电偶被料埋住下料管温度变化不大;如堵塞点在热电偶以上,没有物料通过下料管温度会有下降趋势)。
通过摄像头观察翻板阀无抖动现象。
C4及C3、C2、C1堵塞则分解炉出口温度异常升高(速度很快),C5堵塞则无该现象。
②现场判断:因没有物料通过翻板阀无抖动现象,打空气炮无贯通声音。
如堵塞部位在翻板阀以下,翻板阀翘起且扳不下去(也适用于中控摄像头判断),如堵塞在翻板阀以上则无此现象。
通过以上所有条件综合判断,确定预热器是否堵塞。
二、堵塞解决方法:中控发现锥部负压为零时,及时打空气炮并开环吹通知岗位工根据堵塞判断第②款进行现场判断是否堵塞(此时严禁打开观察孔观察,更不能进行捅料防止突然喷料伤人),此时岗位人员只能开环吹打空气炮并活动翻板阀严禁进行其他操作如打开捅料孔进行捅料,如确定堵塞按以下规程处理:1、中控室方面:堵塞后迅速止料,止尾煤减头煤,迅速扣风但要兼顾窑头及预热器使其处在负压状态,其余按正常停窑处理。
2、现场方面:①、在中控操作员停窑过程中迅速准备工器具其包括:足够长度的气管、捅料钢钎、打水炮用水,水炮用钢管、风镐、手电、境界绳、调派维修人员及电气焊、根据堵塞部位是否需要搭建钢平台等。
②、捅料过程中指定专人负责指挥并负责现场一切事宜,其他任何人不得随意发号指令,如有需要必须汇报给负责人,由负责人统一进行,参与捅料人员不得听从非负责人指令以免事故发生。
负责人有事,需向接班负责人交待清楚后离开。
③、具体堵塞位置判断:如翻板阀翘起则说明堵塞点在翻板阀以下,堵塞点多在下料管拐弯处,如需割孔应在此部位进行;如翻板阀活动灵活则堵塞部位在翻板阀以上,割孔需在其上拐弯处进行。
④、堵塞后应优先使用用空气炮、环吹进行吹堵;其次用水炮及压缩空气吹堵。
如果上述处理措施实施两次后无效果,需割孔进行清堵。
- 1、下载文档前请自行甄别文档内容的完整性,平台不提供额外的编辑、内容补充、找答案等附加服务。
- 2、"仅部分预览"的文档,不可在线预览部分如存在完整性等问题,可反馈申请退款(可完整预览的文档不适用该条件!)。
- 3、如文档侵犯您的权益,请联系客服反馈,我们会尽快为您处理(人工客服工作时间:9:00-18:30)。
2006.No.1我公司2号熟料生产线采用NC-SST-I管道式分解炉,规格为Φ3.9m×24m,设计生产能力为
1300t/d,2004年10月投产。
进入2005年后,分解
炉锥部结皮十分严重,每次点火投料三四天后,分解炉出口压力就从-0.60kPa上升到-1.8kPa以上,系统风量和窑炉用风比例无法稳定,熟料产质量波动较大,窑内结球、结圈等工艺事故较多。
为了维持生产,在分解炉锥部增设捅灰孔,班班清理,仍多次出现大块结皮垮落,堵住分解炉下缩口,被迫停窑处理的事故。
该分解炉两煤粉喷嘴对称布置在锥部两侧,C4
下料管布置在三次风入炉口一侧煤粉喷嘴的偏上方。
现场观察,三次风管入炉口一侧存在明火,另一侧煤粉喷嘴入口忽明忽暗。
因煤粉喷嘴入口位置在三次风管入炉口的中部,入炉煤粉与含有大量新鲜氧气的高温三次风直接接触,迅速燃烧,放出大量的热量,而受入炉三次风和下料点的影响,在此一侧形成料的稀相区,放出的热量无物料来吸收,同时部分正在燃烧的煤粉在切向入炉三次风的作用下,被抛向炉壁,黏附到炉壁上,继续燃烧,在锥部形成局部高温,黏附未燃尽的煤粉及生料粉,使结皮逐渐增厚。
基于以上的分析,2005年5月6日,利用停窑的机会,将三次风管入炉口一侧的煤粉喷嘴向上抬高500mm左右,高于三次风管入炉口位置(见图1),一方面,使煤粉着火点靠近下料点,使燃烧能受到物料的抑制,减缓了煤粉的燃烧速度;另一方,避免高速切向入炉的三次风中携带过多未燃尽的煤粉,增加锥部结皮的几率。
改造后,虽三次风入炉口一侧仍存在明火,但温度明显下降,分解炉锥部结皮的情况大为改观,再未发生因锥部结皮严重停窑的事故。
NC-SST-I型分解炉具有炉容大、煤粉及物料
在炉内停留时间长的特点,火嘴位置的上移,并未造成入窑物料分解率的下降,而分解炉锥部结皮的减少,保证了系统风量的稳定,为窑系统实现稳产、高产创造良好的条件。
图1分解炉喷煤嘴改造前后位置
(编辑顾志玲)
中图分类号:TQ172.622.26
文献标识码:B
文章编号:1002-9877(2006)01-0053-01
NC-SST-I分解炉锥部结皮的处理
赵来山,倪宏山,尚国辉
(中宁赛马水泥有限公司,宁夏中宁
755100)
动。
改进后的上壳体衬板连接如图3。
图3
壳体加固
锤头断裂
,
造成细碎腔壳体衬板断裂。
因无备件,采用厚30mm的低碳合金结构钢16Mn制作壳体衬
板。
DCFP破碎机改进后3年多的运转情况表明,锤
头外型及材质的改进,有效防止了锤头的断裂,延长了锤头的使用寿命;销轴及锤盘的改进,防止了销轴的轴向及径向窜动,保障了破碎机的安全运行;上壳体经特殊处理,增强了壳体的刚性,衬板螺栓一次紧固不再松动;利用16Mn钢板制作的上壳体衬板,使用至今,仅正常磨损,未发现其他异常,预计使用寿命
至少为5年。
(编辑
王艳丽)
!!!!!!!!!!!!!!!!!!!!!!!!!!!!!!!!!!!!!!!!!!!!!!!
53--。