HDR工艺--条钢直接轧制技术
钢带生产工艺

钢带生产工艺钢带生产工艺是指通过一系列工艺流程,将原材料经过熔炼、连铸、轧制等步骤,制成钢带产品的整个过程。
下面将为大家介绍一下钢带生产工艺的基本流程和设备。
首先是熔炼过程。
钢带的生产一般使用电弧炉来进行熔炼,将废钢、铁水和合金原料加入电弧炉中,通过高温,使这些原料熔化并混合。
这样得到的钢水,其成分可以根据需要进行调整,以达到生产出所需的各种钢带产品。
接下来是连铸过程。
连铸是将熔化的钢液通过一系列连续铸造过程,将其变成连铸坯,为后续的轧制过程提供原材料。
连铸设备通常包括机床、冷却水系统和连铸机等。
连铸机通过连续铸造,将钢液倒入結晶器中,经过冷却,钢液凝固并变成连铸坯。
连铸坯的大小可以根据需要进行调整。
然后是轧制过程。
轧制是将连铸坯通过轧机进行塑性变形和尺寸调整,得到符合要求的钢带产品。
轧机是生产钢带的核心设备,根据不同的钢带产品要求,可以选择不同类型的轧机。
在轧制过程中,连铸坯首先通过热轧机,进行初轧和精轧,使其厚度逐渐减薄,长度和宽度得到调整。
然后通过冷轧机进一步处理,使其表面质量更佳,并经过切割、整平等环节,得到最终的钢带产品。
最后是钢带的后续处理。
钢带生产完成后,还需要进行表面处理和切割等后续工艺。
表面处理通常包括酸洗、镀锌、涂层等过程,以保护钢带产品的表面免受氧化和腐蚀。
切割是根据用户需求,将钢带产品按照一定长度进行切割,以供后续使用。
总结一下,钢带生产工艺是一个复杂的过程,涉及到熔炼、连铸、轧制和后续处理等多个环节。
通过完善的设备和工艺流程,可以生产出各种不同类型的钢带产品,广泛应用于建筑、制造业等领域。
这些钢带产品在现代社会中发挥着重要的作用,提供了可靠的材料基础,推动了各行各业的发展。
轧钢生产线工艺流程

轧钢生产线工艺流程
轧钢是将钢坯通过轧机进行连续轧制,使其形状、尺寸和表面质量得到一定的变化和改善的工艺。
轧钢生产线是钢铁行业中一个非常重要的生产设备,它的工艺流程对于钢材的质量和性能有着至关重要的影响。
下面将详细介绍轧钢生产线的工艺流程。
1. 钢坯加热
首先,将冷的钢坯放入加热炉中进行加热处理。
加热的温度和时间是根据不同的钢种和轧制要求而定的,一般来说,加热温度在1100℃-1250℃之间。
2. 粗轧
经过加热处理的钢坯被送入粗轧机中进行粗轧。
在粗轧机上,钢坯经过多道次的轧制,逐渐变形成为所需的形状和尺寸。
3. 精轧
粗轧后的钢坯被送入精轧机中进行精轧。
精轧是在辊道上进行
的,使钢坯的尺寸更加精确,表面质量更好。
4. 冷却
经过精轧后的钢坯需要进行冷却处理,以使其温度降到适合进
行后续加工的温度。
5. 切割
冷却后的钢坯被送入切割机中进行切割,切割成所需的长度。
6. 包装
经过切割后的钢坯被送入包装区进行包装,以便于运输和储存。
以上就是轧钢生产线的工艺流程,通过这一系列的工艺处理,
钢坯最终成为我们所需的各种形状和尺寸的钢材。
轧钢生产线的工
艺流程严格控制每一个环节,以确保钢材的质量和性能达到要求。
同时,随着科技的不断发展,轧钢生产线的工艺流程也在不断地进
行创新和改进,以满足市场对于钢材的不断提高的需求。
希望通过
不断的努力和创新,轧钢生产线的工艺流程能够更加完善,为钢铁
行业的发展做出更大的贡献。
Midrex钢生产工艺
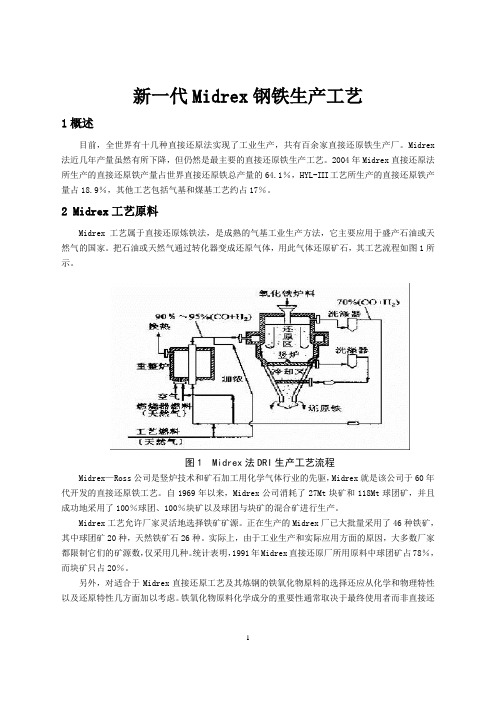
新一代Midrex钢铁生产工艺1概述目前,全世界有十几种直接还原法实现了工业生产,共有百余家直接还原铁生产厂。
Midrex 法近几年产量虽然有所下降,但仍然是最主要的直接还原铁生产工艺。
2004年Midrex直接还原法所生产的直接还原铁产量占世界直接还原铁总产量的64.1%,HYL-III工艺所生产的直接还原铁产量占18.9%,其他工艺包括气基和煤基工艺约占17%。
2 Midrex工艺原料Midrex工艺属于直接还原炼铁法,是成熟的气基工业生产方法,它主要应用于盛产石油或天然气的国家。
把石油或天然气通过转化器变成还原气体,用此气体还原矿石,其工艺流程如图1所示。
图1 Midrex法DRI生产工艺流程Midrex—Ross公司是竖炉技术和矿石加工用化学气体行业的先驱,Midrex就是该公司于60年代开发的直接还原铁工艺。
自1969年以来,Midrex公司消耗了27Mt块矿和118Mt球团矿,并且成功地采用了100%球团、100%块矿以及球团与块矿的混合矿进行生产。
Midrex工艺允许厂家灵活地选择铁矿矿源。
正在生产的Midrex厂已大批量采用了46种铁矿,其中球团矿20种,天然铁矿石26种。
实际上,由于工业生产和实际应用方面的原因,大多数厂家都限制它们的矿源数,仅采用几种。
统计表明,1991年Midrex直接还原厂所用原料中球团矿占78%,而块矿只占20%。
另外,对适合于Midrex直接还原工艺及其炼钢的铁氧化物原料的选择还应从化学和物理特性以及还原特性几方面加以考虑。
铁氧化物原料化学成分的重要性通常取决于最终使用者而非直接还原工艺。
随着三十多年来直接还原技术的进步,铁氧化物原料的化学成分对Midrex工艺来说已变得不太重要了。
然而化学成分对其后的DRI炼钢工艺却非常重要。
在直接还原工艺中,就原料而论,唯一的主要化学变化是从铁氧化物中脱氧,没有熔炼或精炼发生,基本上氧化铁原料中的所有杂质和脉石都存留在还原产品中。
能量系统优化典型技术—界面技术
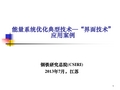
入炉铸坯温度 加热至出坯温度所需要的能量, MJ/t
1000℃ 131.06
800℃ 305.81
600℃ 480.56
400℃ 655.31
25℃ 982.97
节约温度即是节能!
连铸-热区段界面技术应用案例—热送热装 唐山钢铁公司第二炼钢 - 轧钢厂在 1996 年、 2003 年分别建立了 第1棒材轧钢车间和第2棒材轧钢车间。第1轧钢车间全部采用切分 轧制技术生产 ∅ 12mm~∅18mm 螺纹钢(一座加热炉 +18 架棒材轧 机机组);第二棒材轧钢车间全部生产∅20mm以上的螺纹钢。 在技术改造过程中,高度重视炼钢车间与第 1 、第 2 轧钢厂之 间的平面布置关系(流程网络),特别是 6# 连铸机和第 1 棒材车 间之间紧凑-顺畅的铸坯输送路线,走行距离为241.1m;5#连铸机 和第2棒材车间之间的更为紧凑-顺畅的铸坯输送路线,铸坯的走 行距离为 81.5m 。现在两个棒材车间分别与 5# 、 6# 连铸机固定供 坯生产,实际钢材产量已达220万吨/年。其中铸机-加热炉之间铸 坯的高温直接入炉技术、铸机定重供坯技术以及与此相关的切分 轧制等生产工艺改进,有着重要的作用。
20.79% 11639 31.00% 18.42% 8.16% 0.00% 0.00% 2433 1509 0 0 6.48% 4.02% 0.00% 0.00%
33.87% 21283 52.63% 21963 58.50%
5. 总结
界面技术优化可以加速物质流运转速度和过程运输时间 节奏,因此可以减少物质流运输过程的能量损失,如铁水 温度损失和铸坯温度损失。 面这些技术仅需要少量的硬件 投资,而且仅是操作过程的优化即可取显著的节能效果、 经济效益和社会效益。
科技成果——板带轧机板形控制技术

科技成果——板带轧机板形控制技术成果简介提高板带轧机板形质量的一个重要途径是采用新的板形控制技术。
目前普遍采用的诸如加大弯辊力、采用可移动中间辊等手段在提高了轧机板形控制能力的同时,也带来了轧辊剥落、辊耗增加等负面结果。
目前国内已经投产的板带轧机在板形控制方面均存在一些不足。
本成果在板形控制和辊形设计思想上实现了突破和创新,通过与宝钢和武钢等大型钢铁企业的合作,获得了板形质量明显提高的实际效果,年经济效益超亿元。
获得了包括国家科技进步一等奖、原冶金部科技进步一等奖在内的多项奖励。
技术主要内容1、板带轧机变接触轧制技术板带轧机变接触轧制简称VCR(Varying Contact Rolling),由与轧机形式相适应的辊形设计(“VCR变接触支持辊”、“均压型PPT中间辊”、“轴向移位变凸度工作辊”和“ASR非对称自补偿工作辊”)及配套的工艺制度、控制模型和带钢平坦度检测装置等多项技术所组成。
具有增强轧机对板形的调控能力、提高消化来料板形和规格波动能力、使机架间负荷分配趋于合理、保证轧制过程顺行、提高板形质量和生产率、实现超平材超薄材等极限难轧品种的轧制、降低轧辊及轴承消耗等效果。
武钢和宝钢等企业的冷热连轧机已采用了这项技术。
2、板带轧机板形控制模型板形控制模型与控制系统是现代化板带轧机的重要标志,是实现板形自动控制的关键。
通本单位自主开发了热连轧机板形自动控制模型、板形板厚解耦模型、冷连轧机的弯辊自动设定模型和板形控制目标生成模型,并成功应用于大型工业轧机,属于国内首创。
该技术的开发和应用,不仅提高了轧机板形自动控制的水平,改善了产品质量,提高了生产效率,同时也显示在板形控制这个国际前沿领域,我国的理论研究和技术开发已经达到了国际先进水平。
应用范围及效益本项技术不需要对设备进行大的改造,因此适合国内的各类四辊、六辊轧机,如常规四辊、HC、CVC、WRS、PC等薄带轧机以及中厚板轧机等。
我国已经投产和正在建设的宽带钢轧机和中厚板轧机有几十套,以年产200万吨的连轧机为例,通过提高板形质量,年经济效益可达千万元。
棒材直接轧制

棒材直接轧制1. 引言棒材直接轧制是一种常见的金属加工方法,用于将金属坯料通过轧制工艺加工成具有特定形状和尺寸的棒材产品。
这种加工方法广泛应用于钢铁、铝合金、铜合金等金属材料的生产中,具有高效、经济、灵活等优点。
本文将对棒材直接轧制的工艺流程、设备和应用领域进行详细介绍。
2. 工艺流程棒材直接轧制的工艺流程通常包括原料准备、预轧制、精轧制、冷却和整形等步骤。
2.1 原料准备原料准备是棒材直接轧制的第一步,主要包括选择合适的金属材料、切割成适当的坯料尺寸和加热处理等操作。
金属材料的选择应根据产品的要求和生产成本进行综合考虑,常见的金属材料有碳钢、不锈钢、铝合金等。
切割成适当尺寸的坯料可以提高轧制效率和产品质量。
加热处理可以改善金属的塑性和可加工性。
2.2 预轧制预轧制是棒材直接轧制的第二步,主要目的是通过辊道的压力和摩擦力将坯料逐渐塑性变形成较小的截面尺寸。
预轧制可以提高轧制效率、减少轧制力和改善产品表面质量。
预轧制通常采用多道次的轧制,每道次的辊道间隙逐渐减小,使坯料逐渐变形。
2.3 精轧制精轧制是棒材直接轧制的第三步,主要目的是进一步减小截面尺寸、提高产品的表面质量和机械性能。
精轧制通常采用单道次的轧制,辊道间隙较小,轧制力较大。
精轧制过程中需要控制轧制温度、轧制速度和轧制力等参数,以保证产品的质量和尺寸精度。
2.4 冷却和整形冷却和整形是棒材直接轧制的最后一步,主要目的是通过冷却和整形工艺使产品获得所需的形状和尺寸。
冷却可以改善产品的力学性能和表面质量,通常采用水冷或空冷方式。
整形包括切割、修直、打标等操作,以满足产品的需求。
3. 设备棒材直接轧制需要使用一系列专用设备,包括轧机、辊道、传动系统、冷却系统和控制系统等。
3.1 轧机轧机是棒材直接轧制的核心设备,用于通过辊道的压力和摩擦力将金属坯料塑性变形成棒材产品。
轧机通常由上辊和下辊组成,辊道间隙可以调节,以适应不同的轧制需求。
轧机的类型和规格根据产品的要求和生产能力确定。
《连续铸造及其与轧制的衔接工艺》课件

1)连铸坯内部绝热技术和烧嘴加热技术相结合。 2)火焰切割机附近采用板坯边部加热装置。可采用电磁感应 加热或煤气烧嘴加热。
连续铸造及其与轧制的衔接工艺
1.3 连铸生产工艺 注意防止各种缺陷的产生,严格控制浇注温度,化学成分要求严格。控制
Mn/Si和Mn/S。 拉坯速度-重要的工艺参数。 根据钢种不同,控制二次冷却区的冷却强度,控制各种缺陷的产生。
连续铸造及其与轧制的衔接工艺
2连铸与轧制的衔接工艺 2.1钢坯断面规格及产量的匹配衔接
连续铸造及其与轧制的衔接工艺
1.1连续机类型 按铸坯断面形状分:厚板坯、薄板坯、大方坯、小方坯、
圆坯、异型坯、椭圆坯连铸机。 按铸坯运行轨迹分:立式、立弯式、垂直-多点弯曲式、
垂直-弧形、多半径弧形(椭圆形)、水平式、旋转式连 铸机。 1.2连铸机组成 钢水运转装置(钢水包、回转台)、中间包及更换装置、 结晶器及其振动装置、二冷区夹持辊及冷却水系统、拉引 矫直机、切断设备、引锭装置。
《连续铸造及其与轧制的衔 接工艺》
连续铸造及其与轧制的衔接工艺
1连续铸钢技术 将钢水连续注入结晶器,待钢水凝成硬壳后从结晶器出口
连续拉出或送出,经喷水冷却,全部凝固后切成坯料或直送 轧制工序。
(1)钢水在结晶器内得到迅速而均匀的冷却凝固,细晶 区较厚,柱状晶不发达。
冶金轧钢生产新技术解析

冶金轧钢生产新技术解析随着中国钢铁行业的发展,轧钢生产技术不断创新,为提高轧钢产品质量、效率和经济性,国内外钢铁企业纷纷推出新的轧钢技术。
本文对几种新的轧钢技术进行了解析。
1. 带钢直接冷却淬火技术带钢直接冷却淬火技术是目前国内外钢铁企业普遍采用的一种全新的带钢生产技术。
该技术的主要特点是,采用了连续冷却淬火设备,直接将加热好的带钢通过冷却淬火设备进行淬火,并且冷却速度非常快,让热带钢迅速冷却,以达到制造高强度、高塑性带钢产品的目的。
带钢直接冷却淬火技术相比传统的制造工艺,不仅提高了带钢产品的强度和塑性,而且还能有效降低生产成本。
同时,该技术所生产出来的带钢产品具有更高的耐磨性、耐蚀性和密度均匀性,广泛应用于汽车制造、工程机械、航空航天等领域。
2. 无缝钢管连铸轧管技术无缝钢管连铸轧管技术是一种全新的无缝钢管生产技术。
该技术主要是通过铸造工艺,将钢液直接倒入连铸坯机的结晶器中进行连铸,将连铸坯经过加热、穿孔、酸洗等工艺制成无缝钢管,而无需进行中间的轧制处理。
该技术的主要特点是使用连铸工艺代替传统的轧制工艺,能够大大提高无缝钢管的生产效率、降低生产成本。
同时,该技术所生产出来的无缝钢管具有高强度、高韧性、密度均匀、表面质量好等特点,广泛应用于石油、天然气、化工、航空航天等行业。
3. 背板轧辊技术背板轧辊技术是近年来国内外钢铁企业引进的一种全新的轧钢生产技术。
该技术主要是通过背板轧辊的方式进行轧制,将辊芯变大,轧制出更大直径的钢管和钢板产品。
背板轧辊技术的主要特点是轧制的辊芯变大,不仅可以生产更大直径的钢管和钢板产品,而且还能提高轧制的生产效率和产品质量,同时也可以减少设备的投资和占地面积,对于改善钢铁企业的生产环境和生产效益具有重要意义。
板带生产工艺

板带生产工艺1 概论1.1 板带产品特点、分类及技术要求1.1.1 板带产品的外形特点:扁平,宽厚比大,单位体积的表面积也很大;1.1.2 板带材的使用特点:(1)表面积大,故包容覆盖能力强,在化工、容器、建筑、金属制品、金属结构等方面都得到广泛应用;(2)、可任意剪裁、弯曲、冲压、焊接、制成各种制品构件,使用灵活方便,在汽车、航空、造船及拖拉机制造等部门占有极其重要的地位;(3)、可弯曲、焊接成各类复杂断面的型钢、钢管、大型工字钢等结构件,故称为“万能钢材”。
1.1.3 板带材的生产特点:(1)板带材是用平辊轧出,故改变产品规格较简单容易,调整操作方便,易于实现全面计算机控制的自动化生产;(2)带钢的形状简单,可成卷生产,且在国民经济中用量最大,故必须而能够实现高速度的连轧生产;(3)由于宽厚比和表面积都很大,故生产中轧制压力很大,可达数百万至数千万牛顿,不仅使轧机设备复杂庞大,而且使产品厚、宽尺寸精度和板形控制技术及表面质量控制技术变得十分困难和复杂。
1.2 板带材的分类及技术要求1.2.1 板带材产品分类板带:一般将单张供应的板材和成卷供应的带材总称。
分类:(1)、按材料种类分:钢板钢带、铜板铜带和铝板铝带等;(2)、按产品尺寸规格一般可分为厚板(包括中板和特厚板)、薄板和极薄带材(箔材)三类;厚板:中板: 4~20mm厚板: 20~60mm特厚板: >60mm以上,最后可达500mm 薄板:4.0~0.2mm(热轧薄至1.2mm)极薄带材(箔材):<0.2mm,目前箔材最薄可达0.001mm日本:规定3~6mm为中板,6mm以上为厚板(3)、板带钢按用途又可分为造船板、锅炉板、桥梁板、压力容器板、汽车板、镀层板(镀锡、镀锌板等)、电工钢板、屋面板、深冲板、焊管坯、复合板及不锈、耐酸耐热等特殊用途钢板等有关品种规格可参看国家标准1.2.2板带材产品的技术要求对板带材的技术要求具体体现为产品的标准,板带材的产品标准一般包括有品种(规格)标准、技术条件、试验标准及交货标准等。
冷轧带钢生产技术

冷轧带钢生产技术冷轧带钢生产线技术解析1、了解带钢:带钢是相对于钢卷,由中小型生产线冷轧工艺轧制而成的带钢产品。
冷轧带钢的用途可谓广泛,根据后期的加工方式,可以分为如下类型:(1) 带式:如打包带、铠装电缆用带等;(2) 管式:如薄壁管(含家具用管)、复合管、缠绕管等;(3) 冷弯型材:如滑轨、龙骨、塑钢内衬、电缆桥架;(4) 压型钢板:如卷帘门板、钢结构建筑围护用墙板、屋面板等;(5) 冲压用板:如电池壳体、汽车用板、家电用板等。
冷轧的关键工序:一为酸洗、二为冷轧、三为热处理、四为平整。
酸洗是为了去除对冷轧有害的原料钢卷表面上的氧化铁皮;冷轧是生产冷轧板带钢的关键工序;热处理在冷轧工序中有二个作用,一是消除冷轧带钢的加工硬化和残余应力,软化金属,改善塑性,以便于进一步进行冷轧或其它加工;二是改善组织结构,产生所需要的晶粒大小和取向;平整是精整工序中十分重要的工序,它可以改善带钢的性能,提高钢板的成形性能,提高钢带的平直度及改善钢板的表面状态。
冷轧工艺的定义:轧制是将金属坯料通过一对旋转轧辊的间隙(各种形状),因受轧辊的压缩使材料截面减小,长度增加的压力加工方法,这是生产钢材最常用的生产方式,冷轧即是在常温下完成的轧制过程,其所使用的原料为热轧加工成的板带(卷)。
2、酸洗工艺带钢冷轧前必须酸洗,清洗其表面氧化铁皮,因为氧化铁皮在冷轧时会损坏轧辊表面,而导致带钢表面产生缺陷。
通常热轧带钢表面氧化铁皮通常是3层结构:外层为Fe2O3(三氧化二铁),中层为Fe304(四氧化三铁),内层为Fe0(氧化铁)。
先进的冷轧厂多采用高速运行的连续酸洗机组或推拉式酸洗。
以连续酸洗为例,是将带钢连续地通过几个酸洗槽进行酸洗。
为使作业线上过程连续,将前一个热轧带钢卷的尾部和后一个钢卷头部焊接起来,酸洗后带钢按需要的卷重、卷径切断带钢并收卷。
连续酸洗机组除完成清除带钢表面氧化铁皮的任务外,还有几个作用:(1) 用圆盘剪将带钢侧边剪齐。
轧制工艺2
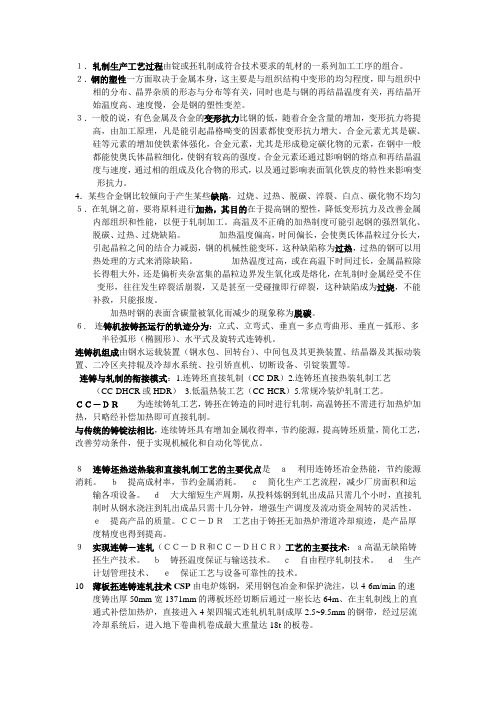
1.轧制生产工艺过程由锭或抷轧制成符合技术要求的轧材的一系列加工工序的组合。
2.钢的塑性一方面取决于金属本身,这主要是与组织结构中变形的均匀程度,即与组织中相的分布、晶界杂质的形态与分布等有关,同时也是与钢的再结晶温度有关,再结晶开始温度高、速度慢,会是钢的塑性变差。
3.一般的说,有色金属及合金的变形抗力比钢的低,随着合金含量的增加,变形抗力将提高,由加工原理,凡是能引起晶格畸变的因素都使变形抗力增大。
合金元素尤其是碳、硅等元素的增加使铁素体强化,合金元素,尤其是形成稳定碳化物的元素,在钢中一般都能使奥氏体晶粒细化,使钢有较高的强度。
合金元素还通过影响钢的熔点和再结晶温度与速度,通过相的组成及化合物的形式,以及通过影响表面氧化铁皮的特性来影响变形抗力。
4.某些合金钢比较倾向于产生某些缺陷,过烧、过热、脱碳、淬裂、白点、碳化物不均匀5.在轧钢之前,要将原料进行加热,其目的在于提高钢的塑性,降低变形抗力及改善金属内部组织和性能,以便于轧制加工。
高温及不正确的加热制度可能引起钢的强烈氧化、脱碳、过热、过烧缺陷。
加热温度偏高,时间偏长,会使奥氏体晶粒过分长大,引起晶粒之间的结合力减弱,钢的机械性能变坏,这种缺陷称为过热,过热的钢可以用热处理的方式来消除缺陷。
加热温度过高,或在高温下时间过长,金属晶粒除长得粗大外,还是偏析夹杂富集的晶粒边界发生氧化或是熔化,在轧制时金属经受不住变形,往往发生碎裂活崩裂,又是甚至一受碰撞即行碎裂,这种缺陷成为过烧,不能补救,只能报废。
加热时钢的表面含碳量被氧化而减少的现象称为脱碳。
6.连铸机按铸抷运行的轨迹分为:立式、立弯式、垂直-多点弯曲形、垂直-弧形、多半径弧形(椭圆形)、水平式及旋转式连铸机。
连铸机组成由钢水运载装置(钢水包、回转台)、中间包及其更换装置、结晶器及其振动装置、二冷区夹持辊及冷却水系统、拉引矫直机、切断设备、引锭装置等。
连铸与轧制的衔接模式:1.连铸坯直接轧制(CC-DR)2.连铸坯直接热装轧制工艺(CC-DHCR或HDR)3.低温热装工艺(CC-HCR)5.常规冷装炉轧制工艺。
常用冶金技术词汇缩写英汉对照六
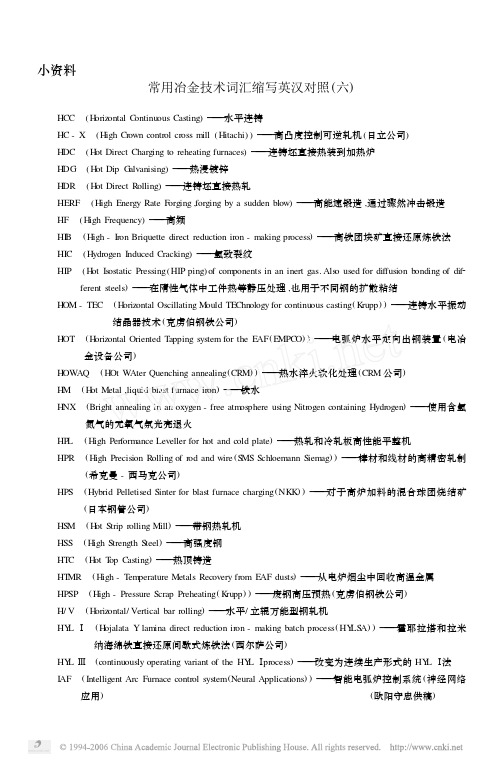
小资料常用冶金技术词汇缩写英汉对照(六)HCC (H orizontal C ontinuous Casting)———水平连铸HC-X (High Crown control cross mill(Hitachi))———高凸度控制可逆轧机(日立公司)H DC (H ot Direct Charging to reheating furnaces)———连铸坯直接热装到加热炉H DG (H ot Dip G alvanising)———热浸镀锌H DR (H ot Direct R olling)———连铸坯直接热轧HERF (High Energy Rate F orging,forging by a sudden blow)———高能速锻造,通过骤然冲击锻造HF (High Frequency)———高频HI B (High-Iron Briquette direct reduction iron-making process)———高铁团块矿直接还原炼铁法HIC (Hydrogen Induced Cracking)———氢致裂纹HIP (H ot Is ostatic Pressing(HIP ping)of com ponents in an inert gas.Als o used for diffusion bonding of dif2 ferent steels)———在隋性气体中工件热等静压处理,也用于不同钢的扩散粘结H OM-TEC (H orizontal Oscillating M ould TEChnology for continuous casting(K rupp))———连铸水平振动结晶器技术(克虏伯钢铁公司)H OT (H orizontal Oriented T apping system for the E AF(E MPC O))———电弧炉水平定向出钢装置(电冶金设备公司)H OW AQ (H Ot W Ater Quenching annealing(CRM))———热水淬火软化处理(CRM公司)H M (H ot Metal,liquid blast furnace iron)———铁水H NX (Bright annealing in an oxygen-free atm osphere using Nitrogen containing Hydrogen)———使用含氢氮气的无氧气氛光亮退火HP L (High Performance Leveller for hot and cold plate)———热轧和冷轧板高性能平整机HPR (High Precision R olling of rod and wire(S MS Schloemann Siemag))———棒材和线材的高精密轧制(希克曼-西马克公司)HPS (Hybrid Pelletised Sinter for blast furnace charging(NKK))———对于高炉加料的混合球团烧结矿(日本钢管公司)HS M (H ot Strip rolling Mill)———带钢热轧机HSS (High Strength Steel)———高强度钢HTC (H ot T op Casting)———热顶铸造HT MR (High-T em perature Metals Recovery from E AF dusts)———从电炉烟尘中回收高温金属HPSP (High-Pressure Scrap Preheating(K rupp))———废钢高压预热(克虏伯钢铁公司)H/V (H orizontal/Vertical bar rolling)———水平/立辊万能型钢轧机HY LⅠ (H ojalata Y lamina direct reduction iron-making batch process(HY LS A))———霍耶拉塔和拉米纳海绵铁直接还原间歇式炼铁法(西尔萨公司)HY LⅢ (continuously operating variant of the HY LⅠprocess)———改变为连续生产形式的HY LⅠ法I AF (Intelligent Arc Furnace control system(Neural Applications))———智能电弧炉控制系统(神经网络应用)(欧阳守忠供稿)。
马钢冷轧介绍
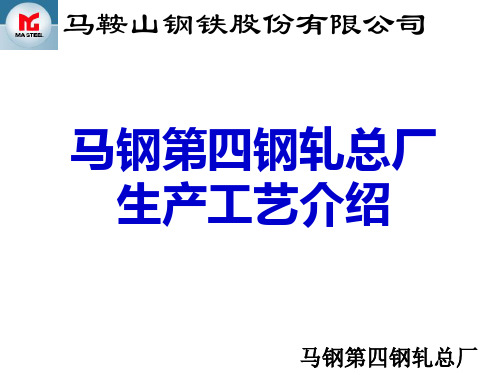
80℃
热轧精整线-平整分卷线
生产规模和产品特点: 平整分卷机组年产量为80 万吨,平整分切成5~45t的成品卷,产品 特点如下:
产品规格:
其中: 平整卷: 分切卷:
1.2~12.7mm×800~2130mm
1.2~6.35mm×800~2130mm 1.2~12.7mm×800~2130mm
钢卷单重:
炼钢工程-粗炼工序
2、采用过程控制模型
主要包括:冶炼炉次跟踪;物料平衡模型;加料
控制模型;底吹控制模型;氧枪控制模型,氧平
衡、热平衡、渣平衡模型;两步法脱磷模型;脱
碳模型、脱氧及合金化模型、出钢模型、溅渣护
炉模型、转炉熔池高度和几何形状计算模型、动
态吹炼修正计算模型等。
炼钢工程-精炼工序
• 马钢新区炼钢项目一期工程的精炼工序由 一套300t钢包精炼装置(LF) 和一套300t 真空循环脱气装置(RH)构成。 • 炼钢项目二期工程计划再分别增建LF和RH 各一套。
炼钢工程
炼钢工程主要由铁水预处理工序、粗 炼工序、精炼工序、连铸工序及石灰焙烧、 渣处理等部分组成。一期工程设计年产 567万吨,生产高档汽车板钢、家电用钢、 弹簧钢、管线钢及各类结构钢等品种的合 格铸坯。它的建成投产将对马钢产能的扩 大、产品档次的提升,以及未来的可持续 发展起到极为重要的作用。
炼钢工程
氧 氮气 废钢 废钢斗 高炉 鱼雷罐 CaO 辅料 合金 复合渣料 活性石灰 碳粉 铁水预处理
300t顶底复合吹转炉
钢包 活动烟罩 脱硫渣罐 转炉渣罐 固定烟罩及汽化冷却烟罩 铸 余 渣 渣处理系统 2机2流板坯连铸机 煤气柜 放散烟囱 炉尘 其它用户 回收废钢铁 轧机 LF-RH 或LF或RH 蒸汽
直接炼钢技术
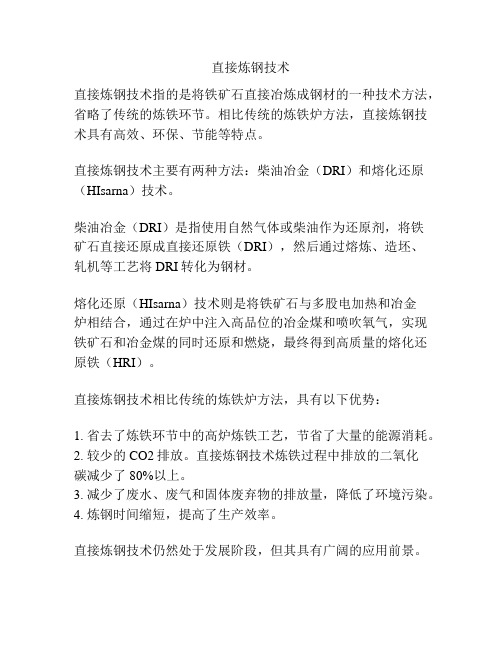
直接炼钢技术
直接炼钢技术指的是将铁矿石直接冶炼成钢材的一种技术方法,省略了传统的炼铁环节。
相比传统的炼铁炉方法,直接炼钢技术具有高效、环保、节能等特点。
直接炼钢技术主要有两种方法:柴油冶金(DRI)和熔化还原(HIsarna)技术。
柴油冶金(DRI)是指使用自然气体或柴油作为还原剂,将铁
矿石直接还原成直接还原铁(DRI),然后通过熔炼、造坯、
轧机等工艺将DRI转化为钢材。
熔化还原(HIsarna)技术则是将铁矿石与多股电加热和冶金
炉相结合,通过在炉中注入高品位的冶金煤和喷吹氧气,实现铁矿石和冶金煤的同时还原和燃烧,最终得到高质量的熔化还原铁(HRI)。
直接炼钢技术相比传统的炼铁炉方法,具有以下优势:
1. 省去了炼铁环节中的高炉炼铁工艺,节省了大量的能源消耗。
2. 较少的CO2排放。
直接炼钢技术炼铁过程中排放的二氧化
碳减少了80%以上。
3. 减少了废水、废气和固体废弃物的排放量,降低了环境污染。
4. 炼钢时间缩短,提高了生产效率。
直接炼钢技术仍然处于发展阶段,但其具有广阔的应用前景。
随着环保和节能要求的提高,直接炼钢技术在钢铁行业中的应用将逐渐增多。
(五)连铸坯热装与直接轧制
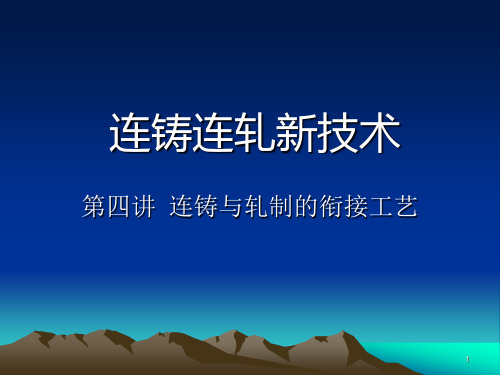
5、炼钢-连铸-热轧生产管理一体化 连铸坯热送热装工艺特别是直装工艺对各工 序的时间要求很严格,如果生产组织不当, 将 达不到热送热装应有的效果。因此,需要有一 个能够合理连接炼钢-连铸-热轧三大工序生产计 划管理一体化的系统,以实现三大工序时间上 的衔接及生产批量的协调。
17
三. 铸坯温度保证技术
• 提高铸坯温度主要靠充分利用其内部冶金 热能,其次靠外部加热。后者虽属常用手 段,但因时间短,其效果不太大,故一般 只用做铸坯边角部补偿加热的措施。 • 保证板坯温度的技术主要是在连铸机上争 取铸坯有更高更均匀的温度(保留更多的 冶金热源和凝固潜热)、在输送途中绝热 保温及补偿加热等,
18
谢谢!
6
二. 连铸与轧制衔接模式
• 从温度与热能利用着眼,钢材生产中连铸与轧制 两个工序的衔接模式一般有如下图所示的五种类 型
7
• 方式1为连续铸轧工艺,铸坯在铸造的同 时进行轧制。方式1称为连铸坯直接轧制工 艺(CC-DR),高温铸坯不需进加热炉加 热,只略经补偿加热即可直接轧制。 • 方式2称为连铸坯直接热装轧制工艺(CCDHCR或HDR),也可称为高温热装炉轧 制工艺,铸坯温度仍保持在A3线以上奥氏 体状态装入加热炉,加热到轧制温度后进 行轧制。
铸机的生产能力应与炼钢及轧钢的能力相匹配铸坯的断面和规格应与轧机所需原料及产品规格相匹配见表21及表22并保证一定的压缩比见表2aa55aa66为实现连铸与轧制过程的连续化生产应使连铸机生产能力略大于炼钢能力而轧钢能力又要略大于连铸能力例如约大10才能保证产量的匹配关系
连铸连轧新技术
第四讲 连铸与轧制的衔接工艺
13
2、连铸坯热送热装过程中的热技术 连铸坯热送热装全部热过程的数学模型是由四 个子模型组成:连铸坯凝固过程数学模型、连铸 坯辊道输送过程数学模型、连铸坯在保温坑内保 温过程数学模型和连铸坯在加热炉内加热过程数 学模型。这四个模型基本上包括了生产实际过程 中的各种情况。结果最大相对误差不超过5%。这 些模型除了用于生产控制外,还可用于分析、完 善设备和工艺过程。
轧钢工艺技术要点
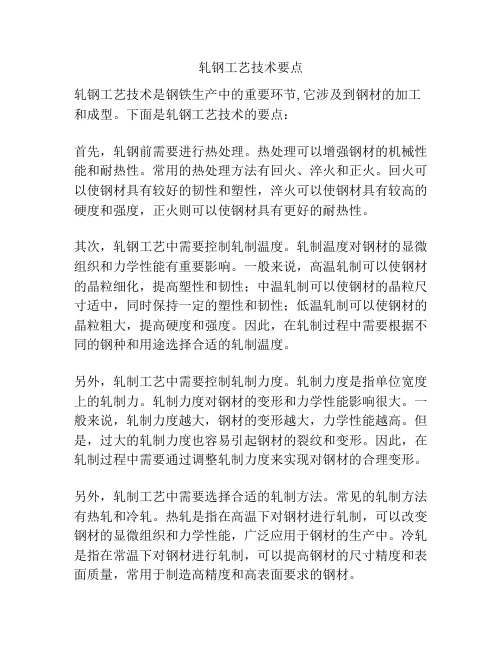
轧钢工艺技术要点轧钢工艺技术是钢铁生产中的重要环节, 它涉及到钢材的加工和成型。
下面是轧钢工艺技术的要点:首先,轧钢前需要进行热处理。
热处理可以增强钢材的机械性能和耐热性。
常用的热处理方法有回火、淬火和正火。
回火可以使钢材具有较好的韧性和塑性,淬火可以使钢材具有较高的硬度和强度,正火则可以使钢材具有更好的耐热性。
其次,轧钢工艺中需要控制轧制温度。
轧制温度对钢材的显微组织和力学性能有重要影响。
一般来说,高温轧制可以使钢材的晶粒细化,提高塑性和韧性;中温轧制可以使钢材的晶粒尺寸适中,同时保持一定的塑性和韧性;低温轧制可以使钢材的晶粒粗大,提高硬度和强度。
因此,在轧制过程中需要根据不同的钢种和用途选择合适的轧制温度。
另外,轧制工艺中需要控制轧制力度。
轧制力度是指单位宽度上的轧制力。
轧制力度对钢材的变形和力学性能影响很大。
一般来说,轧制力度越大,钢材的变形越大,力学性能越高。
但是,过大的轧制力度也容易引起钢材的裂纹和变形。
因此,在轧制过程中需要通过调整轧制力度来实现对钢材的合理变形。
另外,轧制工艺中需要选择合适的轧制方法。
常见的轧制方法有热轧和冷轧。
热轧是指在高温下对钢材进行轧制,可以改变钢材的显微组织和力学性能,广泛应用于钢材的生产中。
冷轧是指在常温下对钢材进行轧制,可以提高钢材的尺寸精度和表面质量,常用于制造高精度和高表面要求的钢材。
最后,轧制工艺中需要控制轧制速度。
轧制速度是指轧制辊与钢材之间的相对速度。
轧制速度对钢材的变形控制和表面质量有重要影响。
一般来说,较大的轧制速度可以增加钢材的变形量,提高生产效率;较小的轧制速度可以提高钢材的表面质量和尺寸精度。
因此,在轧制过程中需要根据不同的要求和钢种选择合适的轧制速度。
总之,轧钢工艺技术要点包括热处理、轧制温度的控制、轧制力度的调整、轧制方法的选择和轧制速度的控制。
这些要点对于提高钢材的机械性能和表面质量,实现钢铁生产的可持续发展非常重要。
轧制工艺技术要求

轧制工艺技术要求轧制是一种重要的金属加工方法,通过不同类型的轧机对金属材料进行压制和变形,从而得到所需形状和尺寸的产品。
然而,轧制过程中存在着一些技术要求,以确保产品的质量和工艺的稳定性。
以下是对轧制工艺技术要求的一些主要内容。
首先,轧制过程中需要控制适当的轧制温度。
温度是影响金属材料的塑性和形变行为的重要因素,过高或过低的温度都会对轧制过程产生不良影响。
因此,在轧制过程中,需通过预热或冷却等方式控制金属材料的温度,以保证其塑性适中,便于变形和成形。
其次,轧制过程中需要控制适当的轧制压力。
压力是实现金属材料变形和破碎的驱动力,过大或过小的轧制压力都会影响成形质量和工艺稳定性。
因此,在轧制过程中,需要根据金属材料的特性和产品的要求,选择合适的轧制压力,以保证金属材料的连续变形和均匀分布。
第三,轧制过程中需要控制合理的轧制速度。
轧制速度与轧制压力、金属材料的塑性等因素密切相关,过大或过小的轧制速度都会导致变形不均匀和产品品质问题。
因此,在轧制过程中,需要根据具体情况调整轧制速度,以保证金属材料的连续变形和均匀分布。
最后,轧制过程中需要保证良好的润滑条件。
润滑是减少金属材料与轧机滚轮间摩擦和磨损的重要手段,同时也有助于金属材料的变形和成形。
因此,在轧制过程中,需要提供充分的润滑剂,以保证轧制工艺的稳定性和产品质量的一致性。
总结起来,轧制工艺技术要求主要包括控制适当的轧制温度、轧制压力、轧制速度和良好的润滑条件。
通过合理地控制这些要求,可以提高轧制工艺的稳定性和产品质量的稳定性。
同时,也可以大大减少因轧制过程中的不良控制而导致的废品率和能源浪费。
因此,轧制工艺技术要求的落实是提高轧制生产效率和产品质量的重要保障。
地条钢生产工艺
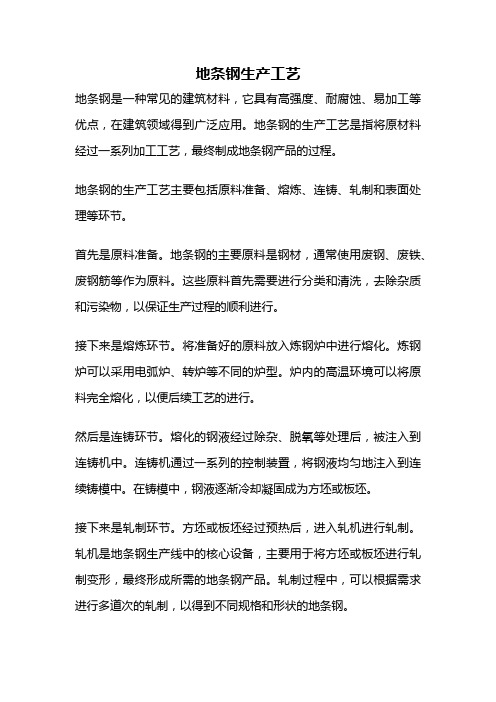
地条钢生产工艺地条钢是一种常见的建筑材料,它具有高强度、耐腐蚀、易加工等优点,在建筑领域得到广泛应用。
地条钢的生产工艺是指将原材料经过一系列加工工艺,最终制成地条钢产品的过程。
地条钢的生产工艺主要包括原料准备、熔炼、连铸、轧制和表面处理等环节。
首先是原料准备。
地条钢的主要原料是钢材,通常使用废钢、废铁、废钢筋等作为原料。
这些原料首先需要进行分类和清洗,去除杂质和污染物,以保证生产过程的顺利进行。
接下来是熔炼环节。
将准备好的原料放入炼钢炉中进行熔化。
炼钢炉可以采用电弧炉、转炉等不同的炉型。
炉内的高温环境可以将原料完全熔化,以便后续工艺的进行。
然后是连铸环节。
熔化的钢液经过除杂、脱氧等处理后,被注入到连铸机中。
连铸机通过一系列的控制装置,将钢液均匀地注入到连续铸模中。
在铸模中,钢液逐渐冷却凝固成为方坯或板坯。
接下来是轧制环节。
方坯或板坯经过预热后,进入轧机进行轧制。
轧机是地条钢生产线中的核心设备,主要用于将方坯或板坯进行轧制变形,最终形成所需的地条钢产品。
轧制过程中,可以根据需求进行多道次的轧制,以得到不同规格和形状的地条钢。
最后是表面处理环节。
轧制后的地条钢需要进行表面处理,以提高其耐腐蚀性能和美观度。
常见的表面处理方法包括酸洗、磷化、镀锌等。
这些方法可以去除地条钢表面的氧化皮和杂质,形成一层保护层,同时可以使地条钢表面具有一定的光泽度。
地条钢生产工艺是一个复杂的过程,需要多个环节的协同作业。
每个环节都需要严格控制工艺参数,以保证地条钢产品的质量和性能。
此外,随着技术的不断发展,地条钢生产工艺也在不断改进和创新,以适应市场的需求和环保要求。
地条钢的生产工艺虽然复杂,但是通过合理的工艺设计和优化,可以实现高效、低耗的生产。
地条钢作为一种重要的建筑材料,将继续在建筑领域发挥重要作用。
随着工艺的不断改进和创新,相信地条钢的质量和性能将会更加优化,为建筑行业提供更好的材料选择。
- 1、下载文档前请自行甄别文档内容的完整性,平台不提供额外的编辑、内容补充、找答案等附加服务。
- 2、"仅部分预览"的文档,不可在线预览部分如存在完整性等问题,可反馈申请退款(可完整预览的文档不适用该条件!)。
- 3、如文档侵犯您的权益,请联系客服反馈,我们会尽快为您处理(人工客服工作时间:9:00-18:30)。
HDR工艺--条钢直接轧制技术
1 生产工艺
普钢的生产工艺可分类如下:
1)从连铸机拉出的铸坯一旦停留,就需在加热炉加热升温后再送到轧制设备进行轧制(下简称送轧),这就是加热炉轧制工艺;
2)将铸坯在较高温度下装入加热炉,待达到所需温度后再送轧,即热装轧制(简称HCR);
3)将从铸机拉出的高温铸坯直接送轧,这是直接轧制(简称HDR)。
由于HDR工艺在连铸和轧制工序之间实现了没有升温的设备和工序,故可以降低操作成本并减少设备投资和维护费用。
从热装轧制和直接轧制(HDR)的铸坯温度变化历程比较可知:实施HCR的普钢电炉生产厂家需将铸坯温度提高150℃后再送轧。
以城市煤气作为燃料而实施HCR的日本电炉生产厂家的操作为例,试算实施HDR时的节能效果。
试算设定了如下的条件和参数:铸坯在加热炉中升温ΔT=150℃、城市煤气发热值J=46046kJ/m3、加热炉热效率η=30%、铁的比热C=0.461kJ/m3。
计算其煤气耗量为(ΔT×C×1000)/η/J=(150×0.461)/0.3/46046=5m3(加热1t铸坯的煤气耗量)。
以上计算结果表明,较之HCR,实施HDR时每吨铸坯可以节省煤气消耗5.0m3,这相当于普钢总能耗的3.3%。
另外,若与一般将冷至常温的铸坯再重新升温的加热炉轧制工艺比较,HDR的每吨铸坯则可减少煤气消耗30m3。
2 HDR设备与技术
直接轧制设备上,必须连续供应高温铸坯。
即使因细小事故而使设备停止运转,也会造成高温铸坯的供应中断而影响整体生产,故要求设备具有高的可靠性。
为了进行铸坯的直接轧制,必须提高连铸机供给铸坯的温度,故首先应考虑在铸机的二冷带,将铸坯的冷却控制最小限度。
对在铸速2.5m/min下改变比水量,将通过二冷带的铸坯温度控制为1050℃时和按铸坯质量要求将其设定允许温度提高至1100℃时,进行铸坯温度变化模拟实验,其结果表明,若比较2种铸坯按预定长度切断开始运送时的温度仅相差15°,且铸坯到预定长度切断间的温降大。
在高速铸造的条件下,可以缩短铸坯按预定长度切断的周期时间,故能将保持高温状态铸坯供给下流工序设备。
另一方面,在结晶器内的凝固坯壳厚度变薄的高速连铸中,因结晶器内坯壳的不均匀凝固,使坯壳易破裂而产生向外飞散的拉漏。
为了实现稳定的高速铸造,结晶器内对铸坯的均匀冷却技术特别重要。
因此采用了即使高速铸造也能发挥均匀冷却效果的(具有特殊锥度)管式结晶器
V60-MOULD,从而保证了铸速的高速化。
为了查明上述V60-MOULD管式结晶器的实际使用效果,对加金铸坯进行辐射线处理,利用金和钢的辐射化率之差对比测定了结晶器内铸坯凝固壳厚度。
结果表明:无论是在结晶器的中部或是下端位置,原来结晶器的四边凝固壳形状不够规则、厚度不够均匀,特别是四个转角部厚度更不均匀、形状更不规则。
反之,使用了新型结晶器的坯壳形状规则,厚度均匀,且四个转角部的坯壳规则且厚度均匀。
这就表明,后者的铜板内壁与铸坯壳接触良好,即使在高速铸造时,也难以产生热应力,从而可以稳定操作(生产实践也证实了此效果)。
对铸坯温度分别进行了模拟和实测,并将二者进行了比较。
结果表明:在连铸设备的夹送辊机架处和剪切机处的铸坯实测温度与模拟值基本一致。
在轧制设备入口处的铸坯实测温度平均值与模拟值虽然一致,可是实测值有一定波动,推定这是由于切断后的铸坯到达轧制设备的时间存在波动造成。
从直接轧制时轧制力矩的验证结果可知,当轧制温度为950℃时,可以容纳设计值70%左右的力矩负荷率。
神户制钢的直接轧制设备,因引进了上述的多项技术而达到了95%的作业率。
同时,实机验证中也表明如何实现送轧铸坯温度的稳定化是今后的课题。
为了解决上述问题,有必要将原来按操作经验手动选择的连铸二冷特性曲线的方式,转变为完全自动化系统,为轧制提供稳定温度铸坯。
3 二次冷却动态控制
对铸机注入结晶器的每流钢液连续测温,若能将温度反映到二冷水量的计算中,即可提高铸坯温度控制精度。
用辐射温度计虽可测温,但其可靠性尚未达到实用化程度。
神户制钢不采用上述方法,而是决定开发实测铸坯表面温度,动态地改变二冷水量,从而任意控制铸坯温度的系统。
并且,为了缩短控制周期,还在二冷带铸坯出口附近设置了辐射温度计,并将之纳入冷却水套中以提高使用寿命。
为了提高实际生产设备的可靠性,特别有必要充实检测温度异常时的无差错功能。
在此并行了动态控制和原来的铸速串级控制,当判定无法进行动态控制时,可在瞬间切换为铸速的串级控制。
从串级控制和动态控制的铸坯温度的比较可知,在已设的串级控制中,每次更换大包时,铸坯温度都有变化的倾向,因换包前后铸速无大的变化,故可以认为这是受到钢液温度影响之故。
另一方面,动态控制开始后,较之设定温度,铸坯温度有±10℃的变化。
由于各流铸速的波动,铸坯的切断顺序随时间而变化,每块铸坯在轧机侧的待轧时间也就不同。
故担心铸坯温度不能收敛为设定值。
为了防止起因于待轧过程温降的轧制温度波动,将铸造高速化而减少流数的方法是有效的。
4 结语
神户制钢公司利用直接轧制工艺实现了不用加热炉的无加热轧制作业。
此工艺中重要的是铸坯温度的稳定。
为了提高连铸设备上二冷动态控制,重复进行了
实机试验。
今后,为了开发连铸-轧制完全直接连接的设备,必须加强对高速连铸系列技术的研发。
(中国冶金报)。