NO8五金常见不良原因对策培训教材知识讲解
五金件及烤漆常见不良现象及原因分析

不良現象
雜質 磨印 油點
烤漆常見不良缺陷原因分析
不良現象分析
1. 涂料﹑溶濟中含有雜質 2. 噴涂車間室內空氣中含塵量過大﹐及用于擦試清潔之布帶有毛線﹐這些灰塵及毛線 隨空氣流動及受噴涂時靜電的吸附于產品表面﹐導致產品表有細小之顆粒狀及線狀之 雜質 3. 通風系統過濾不徹底
因沖壓時產品有凹凸痕﹐表面進行維修打磨時﹐打磨粗糙﹐正常噴涂后不能完全 遮蓋打磨部分﹐導致烤漆后出現印痕 1. 空壓機壓縮空氣時﹐產生水份及機械油污干燥機過濾不徹底隨氣壓混入油漆中﹐ 噴涂于產品上形成﹐
4. 噴房室內溫度過高﹐油漆噴涂與產品上后﹐溶劑揮發太快﹐導至表面桔皮
1. 速度過快﹐治具晃動﹐導致噴槍噴不到位及不均勻
2. 生產時間過長﹐槍內管道堵塞﹐噴涂不均勻
1. Disc噴涂升降機上下點位置太底或高 2. DISC噴涂房內軌道上轉向器安裝位置不當﹐導致噴涂時面與面噴涂不均勻﹐少漆 。 3. 涂料濃度進高﹑噴涂靜電偏小﹐導致邊角部分少漆
1. 產品重工次數過多﹐膜厚過厚(120um以上)
2. 涂料中樹脂聚合不當﹐溶劑與油漆不相溶
3. 油漆太濃﹑噴涂壓力過大﹑距離近
不良現象 壓傷
刮傷
變形 尺寸不良
氧化 模痕 毛刺
五金常見不良缺陷原殘留于模具內﹐再次沖壓時壓于產品表面﹐導致產 品表面損傷﹐出現凹或凸出之痕跡。 2. 原材料本身凹凸痕 1. 作業員作時﹐作業動作不規范,傳送過程中碰刮模具及工作台邊角尖銳部分﹐導致 產品表面損傷。 2. 工作台面粗糙不清潔 3. 送料機送料時因調整不當引起產材料表面磨傷﹑擦傷 4. 制程中產品裸疊及包裝時產品之間相互碰刮引起表面刮傷。 1. 產品沖壓時﹐模具折邊擠壓或避位不夠導致變形 2. 操作員作業不小心,產品碰﹑摔造成 3. 產品包裝方式不正確擠壓所至 1. 產品沖壓時﹐模具定位不准及模高不正確 2. 模具設計尺寸達不到 1. 受高溫﹑高濕天氣的影響﹐車間空氣濕度過高﹐產品與空氣中的氧分子發生化學 反映。 2. 作業員作業時未確實戴好手套﹐手汗中的鹽﹑與水與產品發生氧化發映。 3. 生產排程變異,庫存時間太長 1. 模具擠壓造成 2. 材質因素 1. 模具刀口鈍化 2. 模具閉模間隙過大
五金件常用缺陷说明

1)储存、搬运过程不小心
2)货品分隔包装方式欠佳
3)模具卸料板卸料力度过大或卸料板不平行
4)材料弯曲、变形或未经过直片机校正
1)目视明显变形
2)借用工具比对才可看出的变形可视情况而定
啤坏(啤反方向)
1)工件未放正管位
2)模具避空位不够
3)模具移位
4)模具崩缺
5)模具管位欠佳,工件可正、反方向放进
2)就模具冲压常出现之问题及检查注意事项见下表(注:每工序之检查项目都必须包括外观检查):
工序名称
常见不良现象
检查注意事项
剪口(剪口或开料)
1)披锋
2)片纹方向
3)材料正、反面方向错
4)料弯曲(或扭曲)
5)材料错误(包括厚度、硬度等)
材料厚度、硬度、片纹方向、料弯曲将直接影响下工序成形效果,须重拮留意,如图纸标示不明确须即时反映(如不锈钢材料没注明其硬度要求或型号是SUS301 1/2H 3/4H或SUS304 1/2H
1)注意有否管位,工件是否能反方向放进
2)可使用投影机,相配之螺丝或夹具检测
铆接
碰焊
1)焊点披锋或焊点过深
2)虚焊(假焊)
3)锅钉松脱
4)锅钉歪斜
5)漏焊、漏铆钉(锅钉)
6)焊接移位或焊接反方向
7)锅钉螺纹被压坏或孔径变小
1)焊点深度控制在0.2mm以下
2)所有碰焊工件都必须做破坏性测试
3)用胶棒轻拿货品,可检测虚焊现象
5)模具跳屎(消屎不良,料屎跳于模面)
如产品须喷油或丝印,则表面不可有压痕不良,必要时,则以客户确认样办为准则
花痕/划伤
1)材料花(伤)
2)模具边角锋利,货品取放时划花
3)员工操作不良
五金常见生产异常处理培训资料
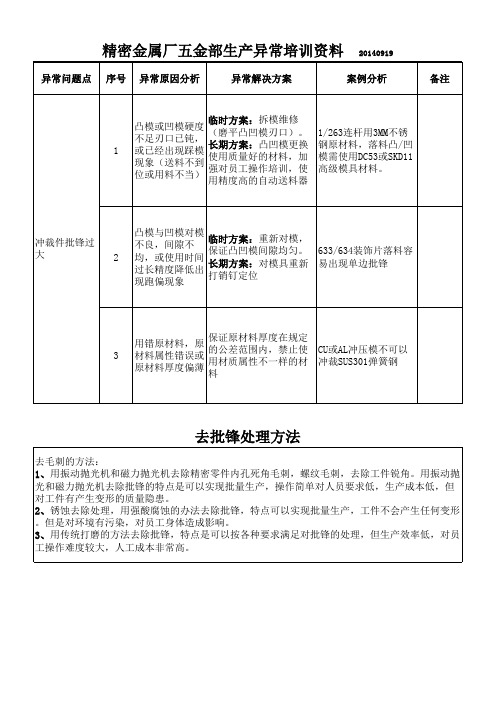
3
保证原材料厚度在规定 用错原材料,原 的公差范围内,禁止使 材料属性错误或 用材质属性不一样压模不可以 冲裁SUS301弹簧钢
去批锋处理方法
去毛刺的方法: 1、用振动抛光机和磁力抛光机去除精密零件内孔死角毛刺,螺纹毛刺,去除工件锐角。用振动抛 光和磁力抛光机去除批锋的特点是可以实现批量生产,操作简单对人员要求低,生产成本低,但 对工件有产生变形的质量隐患。 2、锈蚀去除处理,用强酸腐蚀的办法去除批锋,特点可以实现批量生产,工件不会产生任何变形 。但是对环境有污染,对员工身体造成影响。 3、用传统打磨的方法去除批锋,特点是可以按各种要求满足对批锋的处理,但生产效率低,对员 工操作难度较大,人工成本非常高。
精密金属厂五金部生产异常培训资料
异常问题点 序号 异常原因分析 异常解决方案
20140919
案例分析
备注
1
凸模或凹模硬度 不足刃口已钝, 或已经出现踩模 现象(送料不到 位或用料不当)
临时方案:拆模维修 (磨平凸凹模刃口)。 长期方案:凸凹模更换 使用质量好的材料,加 强对员工操作培训,使 用精度高的自动送料器
1/263连杆用3MM不锈 钢原材料,落料凸/凹 模需使用DC53或SKD11 高级模具材料。
冲裁件批锋过 大
2
凸模与凹模对模 不良,间隙不 均,或使用时间 过长精度降低出 现跑偏现象
临时方案:重新对模, 保证凸凹模间隙均匀。 633/634装饰片落料容 长期方案:对模具重新 易出现单边批锋 打销钉定位
正确认识品质常见五金不良
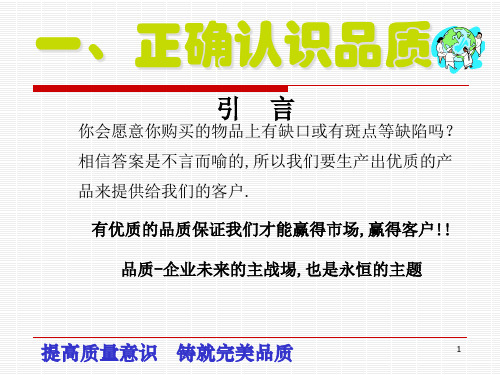
6LA39704 断面及面
生锈
提高质量意识 铸就完美品质
26
常见五金不良
生锈
一般产生原因: 1、空气的湿度较大,水分含量比重大,随着时间推移氧化
严重度加大.
2、空气的腐蚀有害物质含量较多,对部品腐蚀氧化生锈.
3、原材料成份中含有杂质,在进行表面处理时杂质被氧化 生锈.
其不良影响:
1、严重影响部品外观美观.
其不良影响:
1、刮花影响组装后的整体美观。 2、表面受到破坏易生锈、氧化。
提高质量意识 铸就完美品质
17
常见五金不良
刮花
预防措施:
1、产品摆放时做到 披锋面与披锋面,轧形面与轧形面相对 并入箱内,部品间要采用纸皮隔开,对表面要求严格部
品要用刀卡单个摆放入箱内. 2、在流水线上,不可堆积重叠,特别是人工滑拉时要特别
和決心 .計劃 .系統面
提高质量意识 铸就完美品质
12
三个金人
曾经有个小国到中国来,进贡了三个一模一样的金人,金碧辉煌, 把皇帝高兴坏了。可是这小国不厚道,同时出一道题目:这三个金人 哪个最有价值?
皇帝想了许多的办法,请来珠宝匠检查,称重量,看做工,都是 一模一样的。怎么办?使者还等着回去汇报呢。泱泱大国,不会连这 个小事都不懂吧?
部品一定要放入到管位。
易发生尺寸超差的工序:扎形工序、冲孔工序
提高质量意识 铸就完美品质
25
常见五金不良
2.7.生锈
定 义: 又称氧化,是指物体在高温高湿环境下,或受盐、碱
等腐蚀物质的影响,腐蚀物体外表面保护层,表层被
破坏,生成点状、块状、变色等不良现象.
图 片: 6LA39704断面 LM4292 及面生锈
不良原因分析及改善对策培训教材
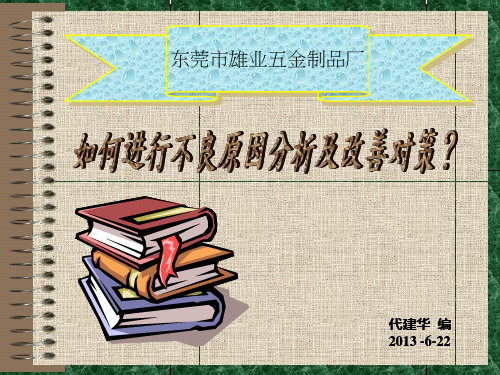
• 矫正措施:对异常现象,不符合现象及客 户投诉,为及时消除异常或不符合现象 的所采取措施; • 预防措施:提出有效的改善对策防止异常 点再度发生及潜在问题发生,并对防范 措施持续管控; • 品质异常:产品质量不符合产品规格或不 符合制程条件等现象 .
1. 人员 (Man) 他参照作业标准工作吗? 他的工作效率达到要求吗?
二.作法:
机
人 特 性
材料
方法
环境
1. 以4M1E法找出大原因: (Man,Machine,Material,Method,Environment) 2. 以5W1H之思维模式找出中小原因: (What,Where,When,Who,Why,How) 3. 创造性思考法:希望点例举法、缺点列举法、特性列案法. 4. 脑力激荡法:“Brain Storming”严禁批评、自由奔放.
东莞市雄业五金制品厂
代建华 编 2013 -6-22
目錄
一.实例:不合格改善对策图示 二.异常术定义 三.4M1E分析法 四.5W1H分析法 五.特性要因圖(鱼骨图)分析法 六.实例分析
何谓异常?
• • • • • 应该做到而没有做到; 不应该发生而发生; 维持活动中发生问题,出现不符合; 实绩与管制基准不符合。 等等…发生异常时,应立刻进行异常分 析
自主检查未落实 品管管理方法不当
标准不完善 材料不良 现场管理不严
作业方法不当
其他
方法
謝謝大家!!!
数量对吗?
有杂质吗? 有浪费吗?
4.方法 (Method) 作业标准适当吗? 标准有修订吗? 安全吗? 工作程序适当吗? 温度、湿度、灯光亮度适当吗? 前后工序衔接良好吗? 能确保品质吗?
• 环境(Environment)
精密五金冲压件不良品常见问题及解决办法

精密五金冲压件不良品常见问题及解决办法
精密五金冲压件不良品常见问题及解决办法
答:精密五金冲压件在生产过程中会遇到许多问题,不良品的产生是常有的事情,冲压加工件常见的品质问题有毛刺、凸米、缺料等,方法总比问题多,诚瑞丰冲压厂的工程师经验丰富,熟悉各种冲压五金产品的解决办法,下面就来一起探讨一下。
1.毛刺问题。
毛刺的定义是金属片边缘产生金属丝残留,未能彻底处理干净,
阻碍与其他物件的组装,或者影响外部美观。
首先分析工序,金属片与模具刃口的接触最频繁,假如刃口不够锋利,就不能将产品彻底裁切,例如刃口有缺损,毛刺就会在同一位置反复出现,而磨损较严重时,接触面积增大,还会产生弹料的现象。
所以要将模具拆卸下来,多两边的刃口进行打磨。
2.凸米问题。
属于五金件表面凹凸的现象,具体表现是各种小坑、凸包等症状,
属于不良品的棘手问题,经过丰富的生产案例积累,你会发现这种原因来自于模具间隙,只有把间隙调节合理之后才能解决,拆模重组是一个较好的解决办法。
3.缺料问题。
五金件的部位缺失,不同于上述两个问题,这种情况会直接使产
品报废,无法修复。
所以应该立即停机,待问题处理完之后才能继续量产。
从缺料的角度,不难发现是冲床或者模具错位,使冲切的位置偏移,造成此现象,要及时纠正冲床的位置。
以上就是诚瑞丰冲压厂为您分析的3个问题,精密五金冲压件的应用领域非常广泛,包含大部分金属外壳、内部结构件等,如有冲压五金的产品需求,欢迎咨询合作。
正确认识品质常见五金不良.pptx

2
正确认识品质
众所周知,产品质量是影响企业生存和发展的重要因 素之一,然而影响产品质量的重要因素就是员工的质量意 识。人的意识决定行为,人的行为决定工作质量,也就决 定了产品质量。质量决定品牌,品牌决定企业的发展前景, 而员工的质量意识又决定了产品的质量。
提高质量意识 铸就完美品质
3
正确认识品质
1.1.了解品质
品质概括:
人的品質
生活的品質
工作品質
環境品質
產品品質
服服務務品品質質
提高质量意识 铸就完美品质
4
正确认识品质
1.2.品质相关概念
什么是品质? 是反映实体满足明确或隐含需要的能力特性总和. 一.品质管理的观念发展过程是由品质是检验出来的到品 质是制造出來的,品质是”习惯”出來的. 二.不接受不良品,不制造不良品及不流出不良品是我们应 有的品质概念. 第一次就把工作做好,是我们与生产追求的目标
最后,有一位退位的老大臣说他有办法。 皇帝将使者请到大殿,老臣胸有成竹地拿着三根稻草,插入第一 个金人的耳朵里,这稻草从另一边耳朵出来了。第二个金人的稻草从 嘴巴里直接掉出来,而第三个金人,稻草进去后掉进了肚子,什么响 动也没有。老臣说:第三个金人最有价值!使者默默无语,答案正确。 这个故事告诉我们,最有价值的人,不一定是最能说的人。老天 给我们两只耳朵一个嘴巴,本来就是让我们多听少说的。善于倾听, 才是成熟的人最基本的素质。
但是:品质是制造出来的,而不是检查出来的。
提高质量意识 铸就完美品质
9
正确认识品质
1.7.品质的重要性
优良的品质有利于:
减少产品的返工过程,降低报废、 节省人力、物力,提高效益,降低成本
提高价格与市场竞争力,赢得更多的客户与市场 提高员工的自身利益 提升企业形象
五金不良培训

(八)起 皱
定 义:
指产品的边缘表面有皱纹现象 。
图 片:
起皱
起皱 图 7
一般产生原因: 1. 压边力太小、压边力不均匀; 2. 凸凹模间隙过大; 3. 凹模圆角半径太大; 4. 材料表面有颗粒状杂物等都将导致工件起皱。
起皱不良影响: 严重影响产品的外观或增加抛光成本,严重时产品报废。
(九)R位偏大或偏小或不均匀
严重影响产品的外观或增加抛光成本,严重时产品报废。
(十)牙位偏深或偏浅
定 义:
指产品的牙位的凹凸痕迹过浅、过深。
牙位偏浅 图 片:
一般产生原因:
1、弹力胶胆力造成材料受力不均牙位深浅不均;
2.冲压机台调试参数大小冲压行程过浅(材料受力不均)造成。
3. 上下模不同心造成模具间隙不均导致材料受力不均造成。 4. 一次拉伸弧度不够或深度程度不够,造成二次成型时有裂痕。
3.在生产过程中,模具/夹具弹簧弹力不均匀。脱料弹力小。
(六)裂 痕/拉伤
定 义:
指产品的表面有破裂的痕迹或迹象 。
图 片: 裂痕 裂痕
一般产生原因:
1、上模R位处R角小(凸凹模圆角半径太小)的模具的崩裂造成的 2.模具/夹具模具间隙偏小(间隙太小,摩擦阻力太大)造成;
3. 上下模不同心、不平行。
一般产生原因:
1. 模具/夹具设计不完善、模具/夹具磨损/老化, 2. 产品在模具/夹具可能发生管位/定位松、断公或爆模的不良, 3. 作业员未按作业指导书的正确方法操作,会发生不良 4. 在前工序的来料(半成品)尺寸即以起差,受其影响,致本工 序尺寸不良. 5. 铝/冲压、加工---减料过程 ---抛光/研磨---减料过程 ---氧化的影响
(五)变 形
五金常见不良分析-讲义

三,攻牙加工不良异常处理说明
1.滑牙的预防 1.1攻牙时注意不可将丝攻攻得太深; 1.2检查牙孔是否冲制过大,超出标准; 1.3经常用牙刷或风枪将丝攻上的销屑等杂物处理干净; 1.4检查丝攻是否有磨损; 1.5检查丝攻是否有缺口 断丝之不良; 1.6检查攻牙机旋转速度是否过快;
2.牙紧的预防 2.1攻牙时不可攻得太浅,否则导致牙紧; 2.2丝攻检查是否有磨损,残缺; 2.3注意攻牙机转速不可过快;
NO .3-48UNC -56UNC
NO .4-40UNC -48UNC
NO .5-40UNC -44UNC
NO .6-32UNC -40UNC
NO .8-32UNC -36UNC
RH4 3
RH4 4
RH5 4
RH5 4
RH5 5
RH6 5
1.96~2.02(100-65) 1.98~2.04(100-65) 2.25~2.32(100-65) 2.29~2.32(100-65) 2.52~2.60(100-70) 2.57~2.64(100-70) 2.86~2.93(100-70) 2.88~2.95(100-70) 3.09~3.17(100-75) 3.19~3.26(100-70) 3.76~3.84(100-75) 3.80~3.88(100-75)
1.5 缩短工时,节省劳力,操作简单.
1.6 同一模具制造出来的产品,具有相同的尺寸与形状,有良好的互换性.
一.冲压加工不良异常处理说明
冲床加工的种类:
生使 塑材 性料 變產 形
沖床加工法
斷使 分材 离料
剪
壓 縮 加 工
端擠壓壓其 壓制印花他
成 形 加 工
圓凸孔捲頸其 緣張凸緣縮他
五金连续冲模常见不良及其改善措施
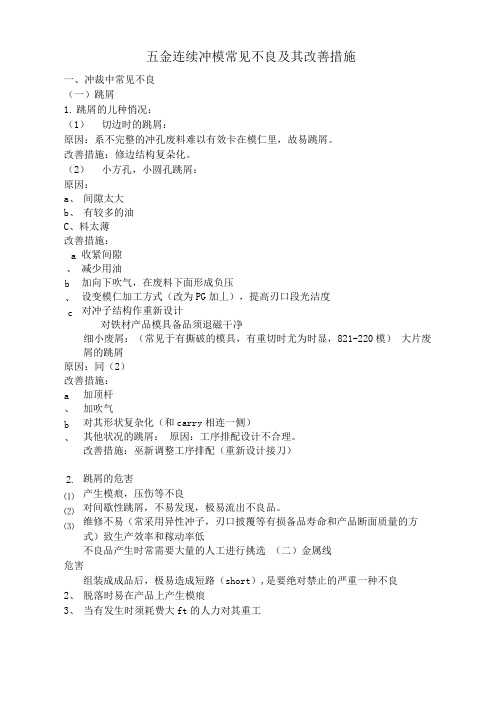
五金连续冲模常见不良及其改善措施一、冲裁中常见不良(一)跳屑1. 跳屑的儿种悄况:(1) 切边时的跳屑:原因:系不完整的冲孔废料难以有效卡在模仁里,故易跳屑。
改善措施:修边结构复朵化。
(2) 小方孔,小圆孔跳屑:原因:a 、 间隙太大b 、 有较多的油C 、料太薄改善措施:收紧间隙减少用油加向下吹气,在废料下面形成负压设变模仁加工方式(改为PG 加丄),提高刃口段光洁度对冲子结构作重新设计对铁材产品模具备品须退磁干净细小废屑:(常见于有撕破的模具,有重切时尤为时显,821-220模) 大片废屑的跳屑原因:同(2)改善措施:加顶杆加吹气对其形状复杂化(和carry 相连一侧)其他状况的跳屑: 原因:工序排配设计不合理。
改善措施:巫新调整工序排配(重新设计接刀)跳屑的危害产生模痕,压伤等不良对间歇性跳屑,不易发现,极易流出不良品。
维修不易(常采用异性冲子,刃口披覆等有损备品寿命和产品断面质量的方式)致生产效率和稼动率低不良品产生时常需要大量的人工进行挑选 (二)金属线危害组装成成品后,极易造成短路(short ),是要绝对禁止的严重一种不良2、 脱落时易在产品上产生模痕3、 当有发生时须耗费大ft 的人力对其重工a 、b 、c a 、 b 、 2. ⑴ ⑵ ⑶产生原因常见于有撕破的模具,比如2、先向下撕破,后乂被向上拍平,撕破切口处产生二次挤压,形成金属线2、 先向一个方向撕破后乂向相反方向折弯成形3、 一次撕破折弯不到位时,让设计不合理改善措施撕破处后面工站闪开(放电)避免撕破和被反复拍打。
(抽引毛坯的准备)2、 对抽引,有撕破准备毛坯的后面各工站,均应闪开撕破缝隙处,或是重新对carry 进行设计,以改善其变形,防止接缝段太长。
3、 撕破方向应和后续"进行的成形方向一致,能采用一次撕破折弯成形方案的 要尽可能采用。
4、 在撕破处须进行二次forming,要合理设计•穿过缝隙的冲子和模仁与撕破口间的间隙>0.02 (三)冲子蹦根源:结构设计不合理2、直刀面太长为(大于10mm )2、 该用PG 加工(光学研磨)的未用,III 于压板槽的影响,使用强度大大削弱C820-380N1)3、 采用PG 加工时结构设计不合理,PG 槽对其削弱很多,822-173U 形冲子4、 弧量的部分太过细长5、 太过细小冲子的导向段送样不合理(入子加工方式不好) 改善措施: PG 加工的冲子直刀面应小于10mm长^*宽<3^*3者应采用PG 加工方式来设计和加工对大多数改U 形结构冲子来讲,尽量釆用PG 加工,也应采用分体式结构, 以尽量减小对其强度的削弱。
经典五金常见不良分析汇总

品擦产品,易发生碎渍附在料面产生压印)。并及时上报品管
及部门组长;
3、对模具/夹具(上模)的废料及时清理,每0.5小时用风枪、折 白色碎布清洁干净后,再自检生产的产品有无问题。
品管部培训教材
19
金正江大五金塑胶制品有限公司
4、生产中,发现模具/夹具易沾铁屑或易跳废料时,应停机反馈给 上司,作出处理。
组长、技工;
●从预防问题再次发生的角度:生产
操作员;
●从管理问题的有效性的角度:直属
上司人员。
品管部培训教材
12
金正江大五金塑胶制品有限公司
造成不良原因的主要因素:4 M+1E
所謂4M+1E即是
1) MAN 2) MACHINE 3) MATERIAL 4) METHOD + 1) ENVIRONMENT
金正江大五金塑胶制品有限公司
常见五金不良现象如下:
一:压印
二:鼓包
三、披锋
四:刮花/碰伤/刮伤
五:变形
六:裂痕/拉伤Байду номын сангаас
七:翘边
八:起皱
九:R位偏大/偏小/不均匀
十、牙位偏深或偏浅
十一:字唛偏深、偏浅、崩裂、移位
十二:漏工序 十三、尺寸超差 十四:麻点
十五:线纹等
品管部培训教材
15
金正江大五金塑胶制品有限公司
●无追踪出责任对象不放过;
●无追踪至落实有效改善措施不放过; ●无责任人和操作人未受教育不放过。
品管部培训教材
8
金正江大五金塑胶制品有限公司
现场作业员检查方式:
● 产品互检;
● 产品自检;
● 产品全检。
一控:指控制自检正确率,努力使自检正确率达到100%
五金常见不良汇总1

常见五金不良
(五)漏工序
定 义:
指部品加工流向过程中,因人为或管理的失误造成整批或个 别部品缺少某项或几项工程的加工,而流向下工程或客户。 图 片: 人为失误造
成漏折弯 OK样品形 状
常见五金不良
(五)漏工序
一般产生原因: 1.作业员生产时,因无人指导及标准作业书的参照,不清楚 自己的部品流向(如应攻牙后再扎形的部品,却未送攻牙, 直接就扎形了), 2.作业员生产时因现场摆放零乱、标识不清等,造成以加工 与未加工部品混淆 漏工序不良影响: 严重影响客户组装功能。 预防措施: 1.在部品开啤时,现场应标挂样品/检查指导书指引现场人 员作业,并由现场管理员对其作业者进行岗前培训。让 作业员明确自己所加工的部品上、下工序的工程流向。
常见五金不良
(五)漏工序
2.部品在加工时,一定要把加工前与加工后的部品明显分
开放在机台上,一个卡板上不要同时放已加工与未加工部 品的盛装箱。人离机后,要把机台的部品清理干净方可(如 上洗手间、修模等)
3、试模品要在开啤前及时清理,交由QC处理,不可与现制品 混乱 易发生漏工序的工序: 各工序间都可能会发生(多数为冲孔模、压平批锋、中间两次 加工的工序等).
常见五金不良
(三)刮 花
一般产生原因: 1、产品摆放不当造成(如披 锋面与正表面重叠摆放入箱时, 产品间无间隔物、杂乱摆放等)。 2、产品周转不当造成(如产品在流水拉生产时,产品堆积滑 拉,部品装箱过松、过紧等)。 3、因顶位针尖过长,从模具内放、取产品不当,造成顶针擦 花部品。 其不良影响: 1、刮花影响组装后的整体美观。 2、表面受到破坏易生锈、氧化。
常见五金不良
(一)压 印
一般产生原因:
1、来料在未加工前就因来料表面不良。 2、原材料待加工部品表面附有脏物,在冲压时产生。
NO8五金常见不良原因对策培训教材
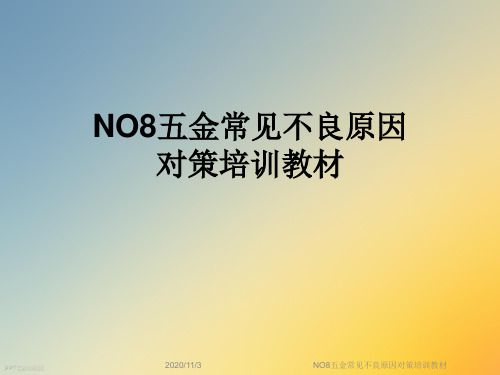
PPT文档演模板
NO8五金常见不良原因对策培训教材
•(一)压 印
•定 义:•又称料屑,零件表面被模具内的附着的异物(如
模具内的料屑)在重压下产生的痕迹. 一般压印在
非正表面,且无明显凹凸可以接收
•图 片:
•模具内有铁屑 未清除致压印
•OK品
PPT文档演模板
NO8五金常见不良原因对策培训教材
•一般产生原因:
PPT文档演模板
NO8五金常见不良原因对策培训教材
•其不良影响:
1、影响组装后的整体美观。
2、影响组装的性能。
•预防措施:
•
1、在加工本工序前,即应对来料外观加以确认,且对
散装料的上 层料用风枪清洁后再加工。模具方面应确保有防
带料装置。
PPT文档演模板
NO8五金常见不良原因对策培训教材
•2、生产中,发现模具顶针易沾铁屑时,应停机反馈给上司及 • QC,作出处理、并由各区担当组织检讨对策。
NO8五金常见不良原因 对策培训教材
PPT文档演模板
2020/11/3
NO8五金常见不良原因对策培训教材
目录
A:背 景 B:现状说明 C:原因分析 D:改善对策
PPT文档演模板
NO8五金常见不良原因对策培训教材
常见五金不良现象如下:
v 一:压印 v 三:刮花 v 五:漏工序 v 七:生锈
二:披锋 四:变形 六:尺寸超差 八:缺料
•3、在模具内放、取产品要轻拿轻放,避免部品在模内乱摆放, • 或取部品时,从模内倾斜拖出(要求平行取出)有异常时 • 对模具定位针作出修改。
•易发生刮花的工序:
•冲压每个工序间的操作、摆放都会因操作不当发生。
PPT文档演模板
经典五金常见不良分析汇总

品管部培训教材 29
金正江大五金塑胶制品有限公司 预防措施: 1、产品摆放时做到披锋面与披锋面,轧形面与轧形面相 对并入箱内,对表面要求严格产品要用吸塑单个摆放 入胶盘内,用胶盆每层用纸或纸板隔离产品周转。 2、在流水带上,不可堆积重叠,特别是使用人工滑拉时要特 别留意,前后工序的操作员须配合,须要相互提示。 3、在模具/夹具内放、取产品要轻拿轻放,避免产品在模内乱 摆放,或取产品时,从模内倾斜拖出(要求平行或向上取出) 必要时对模具定位针作出修改。 4、在自动冲压和滚骨等工序在出料口需要增加辅助工具防止产 品与产品相互碰撞,必要时增加人员负责摆放装箱。 易发生刮花的工序:
每个工序间的操作、摆放、包装都会因工艺/操作不当发生
品管部培训教材 30
金正江大五金塑胶制品有限公司
(五)变 形
定 义: 产品在冲压、加工、抛光、组装或摆放包装过程中,因受模具 的变异或碰撞造成外观整体或局部发生不规则的形态变化. 图 片:
变形样品形 状
OK产品
品管部培训教材
31
金正江大五金塑胶制品有限公司 一般产生原因: 1.作业员在抛光产品时力度大或时间过长。 2.作业员将产品放入模具/夹具管位不到位; 3.在生产过程中,模具/夹具弹簧弹力不均匀。脱料弹力小。 4.模具/夹具模具间隙偏大或偏小造成产品成形变形。 5.模具/夹具模具避位不良造成产品变形。 6.包装方式不正确:过松、过紧、过高。 7.来料材料材质硬度小(太软)。 8.…….。 不良影响: 1.严重影响客户组装功能及美观。严重时产品报废。
五金件及烤漆常见不良现象及原因分析

不良現象 壓傷
刮傷
變形 尺寸不良
氧化 模痕 毛刺
五金常見不良缺陷原因分析
不良現象分析 1. 沖壓時﹐模具切除之廢料反彈殘留于模具內﹐再次沖壓時壓于產品表面﹐導致產 品表面損傷﹐出現凹或凸出之痕跡。 2. 原材料本身凹凸痕 1. 作業員作時﹐作業動作不規范,傳送過程中碰刮模具及工作台邊角尖銳部分﹐導致 產品表面損傷。 2. 工作台面粗糙不清潔 3. 送料機送料時因調整不當引起產材料表面磨傷﹑擦傷 4. 制程中產品裸疊及包裝時產品之間相互碰刮引起表面刮傷。 1. 產品沖壓時﹐模具折邊擠壓或避位不夠導致變形 2. 操作員作業不小心,產品碰﹑摔造成 3. 產品包裝方式不正確擠壓所至 1. 產品沖壓時﹐模具定位不准及模高不正確 2. 模具設計尺寸達不到 1. 受高溫﹑高濕天氣的影響﹐車間空氣濕度過高﹐產品與空氣中的氧分子發生化學 反映。 2. 作業員作業時未確實戴好手套﹐手汗中的鹽﹑與水與產品發生氧化發映。 3. 生產排程變異,庫存時間太長 1. 模具擠壓造成 2. 材質因素 1. 模具刀口鈍化 2. 模具閉模間隙過大
油點 噴漆不均
異色 溢漆 少漆 桔皮 咬花不良
2. 噴漆池循環水濺于產品一
3. 素材表面油污未清洗干淨
1. 烤漆線上懸挂產品之吊盤轉動不靈活
2. DISC自動噴涂上下定位不佳
3. 噴漆技朮員作修補噴涂時﹐手補動作不均勻﹐導致表面噴漆不均 1. 涂料中顏料密度不同﹐密度大的下沉﹐輕的上浮于表面﹐噴涂后產品表面形成異 色。 2. 換機種生產是﹐噴涂設備清洗不干淨﹐不同顏色的油漆混合在一起噴涂于產品表 面上形成 1. 作業員將產品挂于治具上時﹐產品未有與治具完全密合 2. 治具因搬運﹑積漆過厚除漆時不正當的作業使治具變形﹐當產品挂在治具上時﹐ 導致產品與治具無法密合 3. 產品噴涂時﹐靜電過大﹐導致不需要噴涂的區域因受靜電的吸附溢漆
- 1、下载文档前请自行甄别文档内容的完整性,平台不提供额外的编辑、内容补充、找答案等附加服务。
- 2、"仅部分预览"的文档,不可在线预览部分如存在完整性等问题,可反馈申请退款(可完整预览的文档不适用该条件!)。
- 3、如文档侵犯您的权益,请联系客服反馈,我们会尽快为您处理(人工客服工作时间:9:00-18:30)。
冲孔工序,扎形工序。
(二)披 锋
定 义:
又称毛刺,零件受模具冲切后,边缘部位或孔边缘有突出表面 的毛边,用手触摸有刮手感觉,一般标准允许披峰高度不能超 过料厚1/10或板厚的正公差。
图 片:
冲孔时漏加油 或堵屎造成批
锋
OK品形状
一般产生原因:
1、模具间隙偏大或偏小。 2、材质较软或料过厚。 3、作业员操作时,冲压油加入模具频次过少.
不良影响: 1.严重影响客户组装功能。 2.影响外观。
预防措施:
1、作业员现场操作时产品摆放及装箱,不要用力碰撞、 或部品间滑动。
2.放入模具要放到位、模具接触产品部位确保光滑。
3.遵守自检指引,发现异常即时停止作业向上反馈。
易发生变形的工序:扎边各个工序。
(五)漏工序
定 义: 指部品加工流向过程中,因人为或管理的失误造成整批或个 别部品缺少某项或几项工程的加工,而流向下工程或客户。
(三)刮 花
定 义:
指产品的表面被尖锐性物品划成条纹线状或部品间摩擦造成 的部件表面掉镀层、磨花的现象,如正表面刮花明显,手指 尖触摸有手感即不可接受。
图 片:
摆放不良造成 刮花
表面OK
一般产生原因: 1、产品摆放不当造成(如披 锋面与正表面重叠摆放入箱时, 产品间无间隔物、杂乱摆放等)。 2、产品周转不当造成(如产品在流水拉生产时,产品堆积滑 拉,部品装箱过松、过紧等)。 3、因管位尖部过长呀峰利,产品放入模具内或取产品不当 时,造成管 位擦花部品。
其不良影响:
毛刺对客户组装操作有机能与安全的影响。
预防措施:
1、保证模具设计,模具间隙装配均衡.有异常时及时作出改善对策。 2、购买合适的原材料. 3、作业员在开料时,对每张料涂上合适的冲压油,在冲孔工序,
对每生产5-10PCS对模具内涂上冲压油(日本工作油G6231).
易发生披锋的工序:
第一工序开料或冲孔或成形工序时;有时因模具间隙过小,在轧形时模 具挤料使部品边部产生披锋。
图 片:
人为失误造成 漏折弯
OK样品形 状
一般产生原因:
1、作业员生产时,因无人指导及标准作业书的参照,不清楚
自己的部品流向(如应攻牙后再扎形的部品,却未送攻牙, 直接就扎形了), 2.作业员生产时因现场摆放零乱、标识不清等,造成以加工 与未加工部品混淆 漏工序不良影响:
严重影响客户组装功能。 预防措施:
其不良影响: 1、严重影响部品外观美观. 2、生锈后的锈迹掉入机器中,造成机器故障.
预防措施: 1、缩短物体裸露在空气中的时间、使用包材一定不能有水。 2、防止及杜绝部品与腐蚀性物质接触(如:手汗水、HCL…) 3、仓库部品采用先进先出的原则来安排出货,对每季度进行
稽查部品的外观表面的变化. 4、对一切接触部品的人员必须戴手套或手指套防止直接与部
目录
A:背 景 B:现状说明 C:原因分析 D:改善对策
常见五金不良现象如下:
❖一:压印 ❖三:刮花 ❖五:漏工序 ❖七:生锈
二:披锋 四:变形 六:尺寸超差 八:缺料
一般产生原因:
1、来料在未加工前就因来料表面不良。 2、原材料待加工部品表面附有脏物,在冲压时产生。 3、模具内的顶针有磁性或顶针弹簧不够,易带铁屑在模具
2、管位松动,管位设计不合理,使啤出的部品易产生缺料。 其不良影响:
1、因缺少一部份,对部品装配及功能都有严重影响。 2、严重影响部品外观、有可能会引致客户整机开捆的可能。
预防措施:
1、对操作员工现场指导、教育、现场领班管理人员意识同时 要提高。
2、对模具管位、导柱、配件、维护一定要有决心、调模人员 一经发现有异常时必须有马上对应意识。
3.作业员放入部品在模具内时,未靠紧管位,或未按上司指导的 正确方法操作,会发生不良.
4.在前工序的来料(半成品)尺寸己超差,受其影响,致本工 序尺寸不良.
不良影响:
尺寸不良会严重影响客户组装功能,甚至完全不能装配。
预防措施: 1.调模员在作业时,发现模具的管位发生变动,或可左、右、
前后松动时,应及时修理或重配管位(特别是胶水沾的管 位或夹纸管位,贴胶布状态严禁送检. 2.员工冲压部品双啤后,要马上停止作业,知会QC及上司,要 求QC重 新测数及模具处理后,才能决定是否可继续生产。
1.在部,并由现场管理员对其作业者进行岗前培训。让 作业员明确自己所加工的部品上、下工序的工程流向。
2.部品在加工时,一定要把加工前与加工后的部品明显分
开放在机台上,一个卡板上不要同时放已加工与未加工部 品的盛装箱。人离机后,要把机台的部品清理干净方可(如 上洗手间、修模等)
适当的测量仪器,才能发现.
图 片:
模具管位松动, 部品放入管位
内有间隙
OK管 位
一般产生原因:
1、模具管位因做模时未用螺丝固定死或贴胶布、沾胶水定位跑 动 、极易在生产时,发生变异造成尺寸不良。
2.部品在模具内双啤后,模具内极有可能发生管位松、断公或爆 模的不良,作业员未及时反馈,仍作业时,尺寸不良就会发生.
其不良影响:
1、刮花影响组装后的整体美观。
2、表面受到破坏易生锈、氧化。
预防措施:
1、产品摆放时做到 披锋面与披锋面,轧形面与轧形面相对 并入箱内,部品间要采用纸皮隔开,对表面要求严格部 品要用刀卡单个摆放入箱内.
2、在流水带上,不可堆积重叠,特别是人工滑拉时要特别 留意。
3、在模具内放、取产品要轻拿轻放,避免部品在模内乱摆放, 或取部品时,从模内倾斜拖出(要求平行取出)有异常时 对模具定位针作出修改。
表面受压下一个部品时产生。 4、模具间隙过大或过小,长时间的生产、产生料屑堆积模
具内产生不良。
5、加工周围环境空气含有尘粒,流入模具产生不良。
其不良影响:
1、影响组装后的整体美观。
2、影响组装的性能。
预防措施:
1、在加工本工序前,即应对来料外观加以确认,且对 散装料的上 层料用风枪清洁后再加工。模具方面应确保有防 带料装置。
品质是企业的根本、改善是 每个员工的天职!没有做不
到、只是你是否用心去做
3、调模品要在开啤前及时清理,可使用的部品修理后交由QC 确认处理、不可使用直接报废、同时最好是能把产品做到 有防漏管位。
易发生漏工序的工序:
各工序间都可能会发生(多数为冲孔模、压平批锋、中间两次
加工的工序等).
(六)尺寸超差
定 义:
即零件加工的规格超出图纸所要求的极限公差外,一般凭目视
难以发现缺陷(如超差太大可以目视到形态发生变异),需借以
物质的影响,腐蚀物体外表面保护层,表层被 破坏,生成点
状、块状、变色等不良现象.
图 片:
表面保护 层破坏造
成生锈
OK部品
一般产生原因: 1、空气的湿度较大,水分含量比重大,随着时间推移氧化严 重度加大. 2、空气的腐蚀有害物质含量较多,对部品腐蚀氧化生锈. 3、原材料成份中含有杂质,在进行表面处理时杂质被氧化生锈.
品接触.东洋钢板产品调模时一定要带手套。
易发生工序:部品在高温高湿的环境下,在每工序都易发生.
(八)缺 料
定 义: 是指部品在制程之中,因受人为及定位不良等原因使部品在某 个部位缺少一部份,形成缺口、缺折弯等部品残缺不全.
图 片:
作业员放料 不正确,偏 斜造成不良.
OK部品
一般产生原因:
1、部品在落料,切边人为没有把部品靠到管位,使部品产生 缺口、缺料、大部原因都是定位不好操作产生。
易发生刮花的工序:
冲压每个工序间的操作、摆放都会因操作不当发生。
定 义:
(四)变 形
产品在冲压或摆放流向过程中,因受模具的变异或碰撞造成 外观整体或局部发生不规则的形态变化.
图 片:
OK样品形 状
部品受外 力碰撞引 起变形
一般产生原因: 1.作业员在产品摆放及装箱时,杂乱堆压。 2.作业员把产品放入模具时未放到管位引起管不到。 3.模具在生产过程中,结构发生变异。送料不到位。
易发生工序:
1、在部品落料工序易发生. 2、在剪边切边时易发生.
现场作业员品质控制“三不”原 则
●不接受不良品 ●不制造不良品 ●不流出不良品
现场作业员检查方式
产品互检:即对所有上工序流入本工序的部品在每箱 开始生产时进行外观上的品质抽检。发现不良品及时 报告QC、上工序操作员及上司作出处理。 产品自检:对本工序生产的部品,要每生产5~20PCS即 要自行检查以制品的外观。发现不良品及时隔离,并 告知QC及其上司作出处理。 产品全检:当本工序发生不良品时,要对前面最近时 间段生产的部品作出全检,如全检时发现有不良,要 追溯到本批部品的全检。 调模员:严格控制绝不能以假乱真因小失大。
3.作业员按标准作业方式操作、避免只求数量,一味蛮干; 部品一定要放入到管位、发现有异常时一定要提出。
4、当所有机器都在生产时必须有模具保养意识把异常模 具记录并在生完成后送修。
易发生尺寸超差的工序:扎形工序、冲孔工序、V曲模。
(七)生 锈
定 义:
又称氧化,是指物体在高温高湿环境下,或受盐、碱等腐蚀
2、生产中,发现模具顶针易沾铁屑时,应停机反馈给上司及 QC,作出处理、并由各区担当组织检讨对策。
3、生产过程中,要保持模具的清洁,每30分钟清洁一次模具, 单冲每5PCS自检一次;连续每20PCS自检一次。
4、机器周围有严重灰尘污染时(如未洒水扫地,上方工程时等) 应停止生产,向上司报告作出处理;