分离爪工艺规程和工艺装备设计
分离叉的工艺规程及铣内侧面的工装夹具设计模板
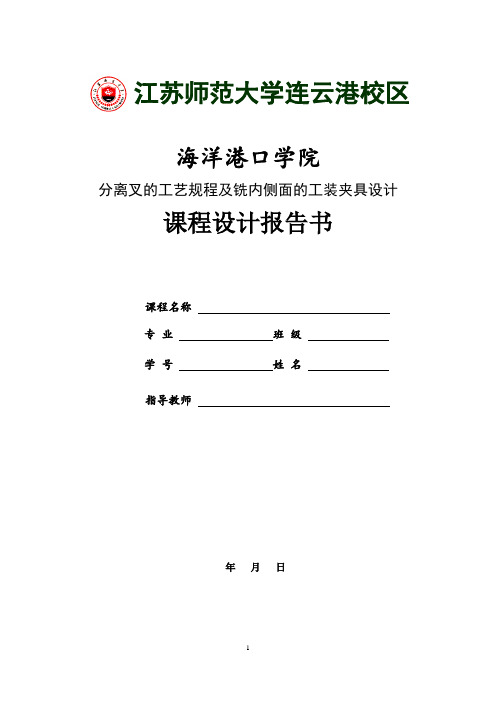
江苏师范大学连云港校区海洋港口学院分离叉的工艺规程及铣内侧面的工装夹具设计课程设计报告书课程名称专业班级学号姓名指导教师年月日摘要本次设计内容涉及了机械制造工艺及机床夹具设计、金属切削机床、公差配合与测量等多方面的知识。
分离叉加工工艺规程及其铣内侧面的夹具设计是包括零件加工的工艺设计、工序设计以及专用夹具的设计三部分。
在工艺设计中要首先对零件进行分析,了解零件的工艺再设计出毛坯的结构,并选择好零件的加工基准,设计出零件的工艺路线;接着对零件各个工步的工序进行尺寸计算,关键是决定出各个工序的工艺装备及切削用量;然后进行专用夹具的设计,选择设计出夹具的各个组成部件,如定位元件、夹紧元件、引导元件、夹具体与机床的连接部件以及其它部件;计算出夹具定位时产生的定位误差,分析夹具结构的合理性与不足之处,并在以后设计中注意改进。
关键词:工艺、工序、切削用量、夹紧、定位、误差。
ABSTRCTThe design of the content relates to the machinery manufacturing technology and machine tool fixture design, metal cutting machine tool, tolerance and measuring and other aspects of knowledge.The hollow gear shaft processing procedure and the right end keyway milling fixturedesign includes parts machining process design, process design and fixture design in three parts. In the design process should first of all parts for analysis, to understand the parts of the process to design the structure of the blank, and select good parts processing base, design parts of the process route; and then the various parts of process dimension calculation, is the key to decide all processes equipment and cutting parameters; then special fixture design, selection and design of a jig for the various components, such as positioning devices, clamping elements, the guide element, clamp and the machine tool connecting parts and other components; calculate fixture is produced when the positioning error of fixture structure, rationality and deficiency, and later in the design of improved.Keywords:The craft, the working procedure, the cutting specifications, clamp,the localization, the error目录序言 (1)一. 零件分析 (2)二. 工艺规程设计 (3)2.1确定毛坯的制造形式 (3)2.2基面的选择传 (4)2.3制定工艺路线 (4)2.4机械加工余量、工序尺寸及毛坯尺寸的确定 (5)2.5确定切削用量及基本工时 (6)三夹具设计 (7)3.1问题的提出 (7)3.2定位基准的选择 (7)3.3切削力及夹紧力计算 (8)3.4定位误差分析 (9)3.5定向键和对刀装置设计 (10)3.6夹具设计及操作简要说明 (12)总结 (14)致谢 (15)参考文献 (16)序言机械制造业是制造具有一定形状位置和尺寸的零件和产品,并把它们装备成机械装备的行业。
分离爪机械课程设计

分离爪机械课程设计一、教学目标本课程的学习目标包括知识目标、技能目标和情感态度价值观目标。
知识目标要求学生掌握分离爪机械的基本原理、结构和应用;技能目标要求学生能够运用分离爪机械解决实际问题,并进行简单的创新设计;情感态度价值观目标要求学生培养对分离爪机械的兴趣和热情,增强团队合作意识和创新能力。
通过分析课程性质、学生特点和教学要求,我们将目标分解为具体的学习成果。
学生将能够:1. 描述分离爪机械的基本原理和结构;2. 分析分离爪机械在实际应用中的优势和局限;3. 设计并实施分离爪机械的实验方案;4. 结合实际情况,提出分离爪机械的创新应用思路;5. 展现团队合作精神和创新能力。
二、教学内容根据课程目标,我们选择和了以下教学内容:1. 分离爪机械的基本原理和结构;2. 分离爪机械在不同行业中的应用案例;3. 分离爪机械的创新设计方法;4. 分离爪机械的实验操作和数据分析;5. 团队合作和创新能力的培养。
教学大纲如下:第1周:分离爪机械的基本原理和结构;第2周:分离爪机械在不同行业中的应用案例;第3周:分离爪机械的创新设计方法;第4周:分离爪机械的实验操作和数据分析;第5周:团队合作和创新能力的培养。
三、教学方法为了激发学生的学习兴趣和主动性,我们采用了多种教学方法。
包括:1. 讲授法:讲解分离爪机械的基本原理和结构;2. 讨论法:分析分离爪机械在实际应用中的优势和局限;3. 案例分析法:研究分离爪机械在不同行业中的应用案例;4. 实验法:进行分离爪机械的实验操作和数据分析;5. 小组合作法:培养团队合作精神和创新能力。
四、教学资源我们选择了以下教学资源:1. 教材:《分离爪机械基础》;2. 参考书:《分离爪机械应用案例解析》;3. 多媒体资料:分离爪机械实验操作视频;4. 实验设备:分离爪机械实验套件。
这些教学资源将支持教学内容和教学方法的实施,丰富学生的学习体验。
五、教学评估为了全面、客观、公正地评估学生的学习成果,我们设计了以下评估方式:1.平时表现评估:通过观察学生在课堂上的参与程度、提问回答等情况,了解学生的学习态度和理解程度;2. 作业评估:布置与课程内容相关的作业,要求学生在规定时间内完成,通过作业的完成质量评估学生的掌握程度;3. 考试评估:进行期中考试和期末考试,全面考察学生对课程知识的掌握和应用能力。
分离爪夹具设计说明书

一、零件的分析(一)零件的作用题目所给的零件是分离爪。
它位于车床变速机构中,主要起换档的作用,使主轴回转运动按照工作者的要求工作,工作过程:拨叉零件是在传动系统中拨动滑移齿轮,以实现系统调速,转向。
(二)零件的工艺分析C6132D车床共有两处加工表面和一个空内表面,其间有一定位置要求。
分述如下:1,零件孔Φ40mm的上加工表面这一组加工表面包括:孔Φ40mm的下加工表面,孔Φ40mm的外表面,有粗糙度要求为Ra等于5um。
加工时以Φ50mm下端面为基准面,并加紧Φ50的左右两端面。
2,孔Φ50mm下端面及孔Φ36的内表面其中Φ50mm的下端面有粗糙度要求为Ra等于5um,这需要粗车;孔Φ36mm的内表面粗糙度要求5,需要进一步精车,这都以Φ40空及端面定位,这就是先选一粗基准,然后必须要用已加工表面作为精基准根据各加工方法的经济精度及一般机床所能达到的位置精度,该零件没有很难加工的表面尺寸,上述表面的技术要求采用常规加工工艺均可以保证,对于这两组加工表面而言,可以先加工其中一组表面,然后借助于专用夹具加工另一组表面,并且保证它们的位置精度要求二、工艺规程设计(一)确定毛坯的制造形式1:零件材料为QT40-10。
考虑零件在机床运行过程中所受冲击不大,零件结构又比较简单,故选择铸件毛坯。
2:已知零件的生产为大批生产,初步确定工艺安排的基本倾向为:加工过程划分阶段,工序都要集中,加工设备主要以专用设备为主,采用专用夹具,这样生产质量高,投产快生产率较高,能适应大批量需求3:根据零件的材料确定毛坯为铸件,材料为QT40-10,毛坯的铸造方法为砂型型铸造,铸件尺寸公差等级为IT13级以下。
(二)基面的选择基面选择是工艺规程设计中的重要工作之一。
基面选择得正确与合理可以使加工质量得到保证,生产率得以提高。
(1)粗基准的选择。
对于零件而言,尽可能选择不加工表面为粗基准。
而对有若干个不加工表面的工件,则应以与加工表面要求相对位置精度较高的不加工表面作粗基准。
分离爪课程设计说明书

机械工程学院《汽车制造技术》课程设计指导书设计题目:分离爪夹具设计*名:**学号:**********班级:车辆二班指导教师:周萍刘银华日期:2015年1月目录前言 (2)1 零件的工艺分析及生产类型 (3)1.1零件的用途 (3)1.2零件的工艺分析 (3)1.3零件的生产类型 (4)2 确定毛坯种类,绘制毛坯图 (4)2.1确定毛坯种类 (4)2.2确定毛坯尺寸及机械加工总余量 (4)2.3 设计毛坯图 (4)2.4 绘制毛坯图 (5)3 选择加工方法,制定工艺路线 (5)3.1 定位基准的选择 (5)3.2 零件的表面加工方法 (6)3.3工序的集中与分散 (6)3.4工序顺序的安排 (7)3.5制定工艺路线 (7)3.6 加工设备及工艺装备选择 (8)3.7工序间加工余量的确定 (8)3.8切削用量以及基本时间定额的确定 (9)4 钻床夹具设计 (20)4.1问题的提出 (20)4.2夹具设计 (21)4.3导向元件的设计 (22)4.4夹紧装置的设 (23)4.5设置夹具体绘制夹具草图 (23)4.6绘制夹具装配图 (23)4.7绘制夹具零件图 (23)5设计心得 (24)参考文献 (25)前言本次课程设计题目是:分离爪车床夹具设计。
要求如下:材料为QT40-10,生产批量为大批大量生产,其他要求及零件参数见分离爪零件图,要求设计该分离爪的机械加工工艺规程,具体内容为:(1)根据生产类型,对零件进行工艺分析;(2)选择毛坯种类及制造方法,绘制毛坯图;(3)制订零件的机械加工工艺过程,选择工序加工设备及工艺装备,确定各工序切削用量及工序尺寸,并计算工序的工时定额;(4)填写工艺卡片;(5)撰写设计指导书。
图1 分离爪零件图1零件的工艺分析及生产类型1.1零件的用途分离爪通常用于车床变速机构中,主要起换档的作用,使主轴回转运动按照工作者的要求工作。
工作过程:拨叉零件是在传动系统中拨动滑移齿轮,以实现系统调速,转向。
主离合器分离叉工艺及指定工序夹具设计

主离合器分离叉工艺及指定工序夹具设计以主离合器分离叉工艺及指定工序夹具设计为标题,我们将从两个方面进行阐述。
一、主离合器分离叉工艺主离合器分离叉是车辆离合系统中的重要部件,其作用是将驱动盘与飞轮分离,实现离合操作。
主离合器分离叉的工艺流程对于产品质量和装配效率具有重要影响。
1. 材料准备和加工主离合器分离叉的材料通常选用高强度合金钢,首先需要对材料进行切割和成型。
切割工艺可以采用剪切或者切割机械进行,确保材料尺寸的准确性。
然后,通过冷加工或者热加工的方式将材料进行成型,保证分离叉的结构和形状符合设计要求。
2. 精加工和热处理主离合器分离叉的加工精度要求较高,需要进行精加工和热处理。
精加工包括铣削、钻孔、车削等工艺,以确保分离叉的尺寸精度和表面质量。
热处理则是通过调控材料的组织结构,提高分离叉的硬度和强度,增加其使用寿命。
3. 表面处理为了提高主离合器分离叉的耐腐蚀性和美观度,通常需要进行表面处理。
常见的表面处理方法包括镀铬、喷涂和电泳等。
这些方法可以有效地保护分离叉的表面免受外界环境的侵蚀,并增加其使用寿命。
4. 装配与调试主离合器分离叉需要进行装配和调试。
在装配过程中,需要将分离叉与其他相关部件进行组装,确保各个部件之间的配合精度和功能正常。
调试阶段主要是对分离叉的运动性能进行调整和检验,以确保其正常工作。
二、指定工序夹具设计为了提高主离合器分离叉的生产效率和产品质量,工序夹具的设计和应用是必不可少的。
下面将介绍指定工序夹具设计的基本原则和要点。
1. 夹具定位和固定夹具设计的首要任务是确保主离合器分离叉在加工过程中的位置和姿态准确稳定。
夹具的定位和固定方式应根据分离叉的结构和形状进行设计,确保夹具与分离叉之间的紧密配合,防止加工过程中产生误差。
2. 加工刀具的选择和布置夹具设计还需要考虑加工刀具的选择和布置。
根据主离合器分离叉的加工工艺要求,选择合适的刀具类型和规格,并合理布置在夹具上。
刀具的选择和布置应尽量减少加工过程中的切削力和振动,以提高加工质量和工作效率。
六自由度机械爪装配工艺流程及标准
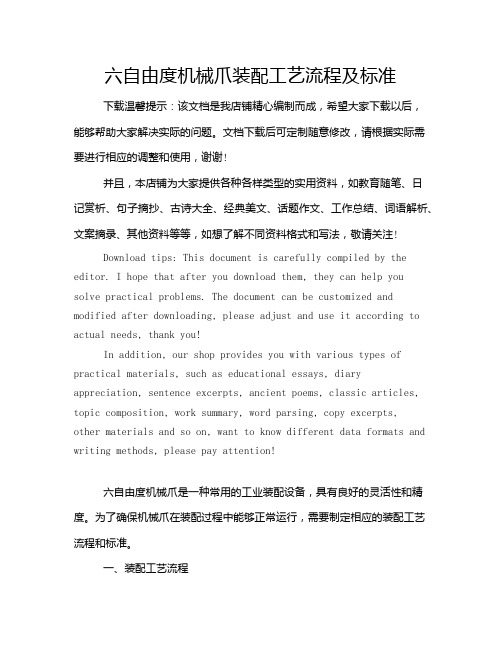
六自由度机械爪装配工艺流程及标准下载温馨提示:该文档是我店铺精心编制而成,希望大家下载以后,能够帮助大家解决实际的问题。
文档下载后可定制随意修改,请根据实际需要进行相应的调整和使用,谢谢!并且,本店铺为大家提供各种各样类型的实用资料,如教育随笔、日记赏析、句子摘抄、古诗大全、经典美文、话题作文、工作总结、词语解析、文案摘录、其他资料等等,如想了解不同资料格式和写法,敬请关注!Download tips: This document is carefully compiled by the editor. I hope that after you download them, they can help yousolve practical problems. The document can be customized and modified after downloading, please adjust and use it according to actual needs, thank you!In addition, our shop provides you with various types of practical materials, such as educational essays, diary appreciation, sentence excerpts, ancient poems, classic articles, topic composition, work summary, word parsing, copy excerpts,other materials and so on, want to know different data formats and writing methods, please pay attention!六自由度机械爪是一种常用的工业装配设备,具有良好的灵活性和精度。
分离爪 工序卡片
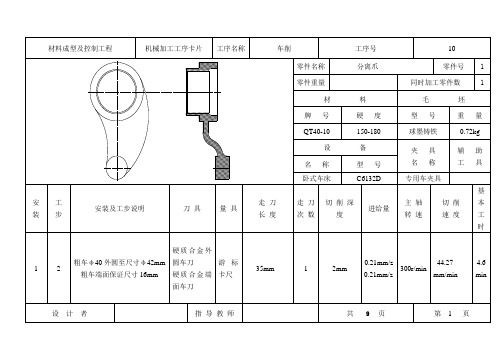
锥柄机用铰刀
内径千分尺
18mm
1
0.4mm/z
0.2mm/z
0.1m/z
400r/min
630r/min
630r/min
29.7m/min
15 m/min
29.7 m/min
25s
25s
25s
设计者
指导教师
共9页
第7页
材料成型及控制工程
机械加工工序卡片
工序名称
钻
工序号
80
零件名称
分离爪
零件号
切削
速度
基本
工时
1
2
粗车φ40外圆至尺寸φ42mm
粗车端面保证尺寸16mm
硬质合金外圆车刀
硬质合金端面车刀
游标卡尺
35mm
1
2mm
0.21mm/z
0.21mm/z
300r/min
44.27
mm/min
4.6min
设计者
指导教师
共9页
第1页
材料成型及控制工程
机械加工工序卡片
工序名称
车削
工序号
20
零件名称
切削
速度
基本
工时
1
2
精车φ40外圆至尺寸要求,倒角1×45度
硬质合金外圆车刀
游标卡尺
内径千分尺
35mm
2
0.25mm
0.10mm/z
150r/min
18.84
mm/min
2.75min
设计者
指导教师
共9页
第4页
材料成型及控制工程
机械加工工序卡片
工序名称
铣削
工序号
分离爪夹具设计说明书(邹奎阳)
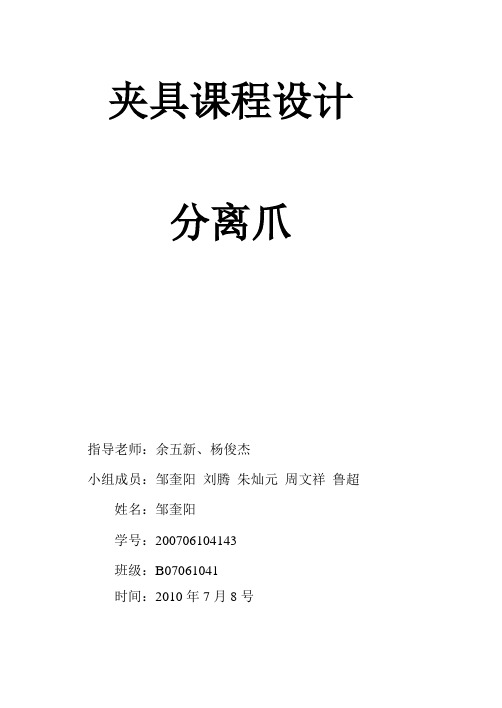
(三)平衡配重设计
平衡配重的计算通常较复杂,对于设计来说,只在夹具体上设计了配重块,配重的调整需根据实际情况进行。
(四)设计制定夹具主要技术条件
1: 首先保证孔1,孔2的尺寸和表面粗糙度不大于 。
2:其次要保证外圆的尺寸。
3:同时保证外圆端面粗糙度。
4:绘制装配图及零件图(附)。
工序三以φ36及端面为精基准,钻、铰φ8.3孔
1.选择钻头
选择直柄麻花钻钻头,粗钻时do=8mm,钻头采用双头刃磨法,后角αo=12°,二重刃长度 =2.5mm,横刀长b=1.5mm,宽l=3mm,棱带长度 ° ° °
2.选择切削用量
(1)决定进给量
查《切》 ,所以,
按钻头强度选择 按机床强度选择
最终决定选择机床已有的进给量 经校验 校验成功。
通过此次设计,是我基本掌握了零件的加工过程分析、工艺文件的编制、专用夹具设计的方法和步骤等。学会了查相关手册、选择使用工艺装备等等。本设计还存在很多不足之处。一是由于本人的画图不够纯熟,在画图遇到复杂的和难的地方时显力不从心,使图没达到预期设计出来的水平。二是对分离爪的工作原理掌握的不够熟练,在设计过程中不能全面地考虑问题,造成走许多弯路,设计速度缓慢,这些都需要进一步研究和进一步实践来解决。
(一)问题的提出
在给定的零件中,对本步加工的定位提出具体的要求是一定的公差,定位要求较高。因此,本步的重点应在保证工件的定位,来保证两孔的尺寸。
具体要求:1、保证孔1,孔2的尺寸。
2、保证图中其它的标尺寸。
(二)确定结构方案
方案一:
两小头孔外圆用一边为固定V型块,另一边用可松紧的活动V型块来夹紧工件。此结构的优点在于结构十分简单,并且易于实际应用。但其同时有致命的缺点—夹紧精度不能保证,并且竖直方向没有任何夹紧力,这使得零件加工出来的精度质量并不高,并且在进行加工时会发生翘曲形变。
主离合器分离叉工艺及指定工序夹具设计
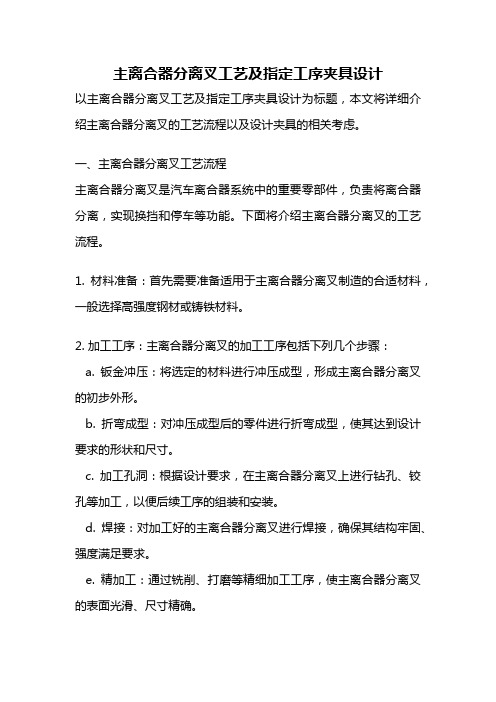
主离合器分离叉工艺及指定工序夹具设计以主离合器分离叉工艺及指定工序夹具设计为标题,本文将详细介绍主离合器分离叉的工艺流程以及设计夹具的相关考虑。
一、主离合器分离叉工艺流程主离合器分离叉是汽车离合器系统中的重要零部件,负责将离合器分离,实现换挡和停车等功能。
下面将介绍主离合器分离叉的工艺流程。
1. 材料准备:首先需要准备适用于主离合器分离叉制造的合适材料,一般选择高强度钢材或铸铁材料。
2. 加工工序:主离合器分离叉的加工工序包括下列几个步骤:a. 钣金冲压:将选定的材料进行冲压成型,形成主离合器分离叉的初步外形。
b. 折弯成型:对冲压成型后的零件进行折弯成型,使其达到设计要求的形状和尺寸。
c. 加工孔洞:根据设计要求,在主离合器分离叉上进行钻孔、铰孔等加工,以便后续工序的组装和安装。
d. 焊接:对加工好的主离合器分离叉进行焊接,确保其结构牢固、强度满足要求。
e. 精加工:通过铣削、打磨等精细加工工序,使主离合器分离叉的表面光滑、尺寸精确。
3. 表面处理:主离合器分离叉经过加工后,需要进行表面处理,以增加其耐腐蚀性和美观度。
常见的表面处理方法包括镀锌、喷涂等。
4. 检验与测试:完成主离合器分离叉的制造后,需要进行检验与测试,确保其质量符合标准要求。
常见的检验项目包括尺寸检验、外观检验、材料成分检验等。
二、指定工序夹具设计为了提高主离合器分离叉的生产效率和质量稳定性,设计合适的夹具对于工艺流程至关重要。
下面将介绍指定工序夹具的设计要点。
1. 夹具功能:根据主离合器分离叉的加工工序,设计夹具的功能应包括固定、定位、支撑和卡持等。
夹具需要能够稳定地固定主离合器分离叉,保证加工过程中的准确性和稳定性。
2. 夹具结构:夹具的结构应简洁、坚固,易于操作和维护。
考虑到主离合器分离叉的形状和尺寸特点,可以采用夹具座、夹具板和夹具夹持装置等组成,确保主离合器分离叉在加工过程中的稳定性和安全性。
3. 夹具材料:夹具材料应具有足够的强度和刚性,以承受加工过程中的力和振动。
机械工艺夹具毕业设计102分离爪工艺规程和工艺装备设计

毕业设计—机械制造毕业设计说明书目录前言……………………………………………………………………………………………1机械制造技术毕业设计的目的………………………………………………………………………………2机械制造技术毕业设计的基本任务与要求…………………………………………………………………2、1、设计任务…………………………………………………………………………………………………2、2、毕业设计基本要求………………………………………………………………………………………3 毕业设计说明书的编写………………………………………………………………………………………第一章分离爪工艺规程和工艺装备设计…………………………………………………1 分离爪工艺规程和工艺装备的基本任务……………………………………………………………………2分离爪工艺规程和工艺装备的设计要求……………………………………………………………………3分离爪工艺规程和工艺装备的方法和步骤…………………………………………………………………3、1生产纲领的计算与生产类型的确定………………………………………………………………3、2零件图审查………………………………………………………………………………………3、2、1 了解零件图的功用及技术要求……………………………………………………………3、2、2 分析零件的结构工艺性…………………………………………………………………3、3毛坯的选择………………………………………………………………………………………3、3.1毛坯的种类…………………………………………………………………………………3、3.2铸件制造方法的选择………………………………………………………………………3、3.3铸件的尺寸公差与加工余量………………………………………………………………3、3.3.1铸件的尺寸公差……………………………………………………………………3、3.3.2铸件的加工余量……………………………………………………………………3、3.3.3铸件最小孔径……………………………………………………………………3、3、4毛坯—零件合图……………………………………………………………………………3、4定位基准的选择………………………………………………………………………………3、4、1 夹具设计研究原始资料……………………………………………………………………3、4、2 拟定夹具的结构方案……………………………………………………………………3、4、2、1确定夹具的类型…………………………………………………………………3、4、2、2确定工件的定位方式及定位元件的结构……………………………………………3、4、2、3确定工件的夹紧方式,计算夹紧力并设计夹紧装置……………………………………3、4、2、4确定刀具的导向方式或对刀装置…………………………………………………………3、4、2、5确定夹具体的结构类型…………………………………………………………………3、4、3 夹具总图设计……………………………………………………………………………3、4、3、1 绘制总装图的注意问题…………………………………………………………………3、4、3、2 绘制总装图的步骤………………………………………………………………………3、4、3、3 夹具总图上尺寸及精度、位置精度与技术要求的标注……………………………3、4、3、4 夹具公差与配合的选择…………………………………………………………………3、4、3、5 各类机床夹具的公差和技术要求的确定………………………………………………3、4、4夹具精度的校核…………………………………………………………………………3、4、5绘制夹具零件图样……………………………………………………………………………3、4、6夹具总体结构分析及夹具的使用说明…………………………………………………3、5拟定工艺路线……………………………………………………………………………………3、5、1 确定各表面的加工方法……………………………………………………………………3、5、2 加工顺序的安排……………………………………………………………………………3、5、3 确定加工余量……………………………………………………………………………3、5、4 计算工序尺寸及公差……………………………………………………………………3、6 确定各工序切削用量……………………………………………………………………………3、7 机床及工艺装备的选择……………………………………………………………………………3、8 工时定额的计算与确定……………………………………………………………………3、9 工艺规程卡的填写……………………………………………………………………………4、设计小结…………………………………………………………………………………………………参考文献书目…………………………………………………………………………………………分离爪工艺规程和工艺装备设计摘要:本设计的零件为分离爪,选用Q T40-10球墨铸铁。
主离合器分离叉工艺及指定工序夹具设计
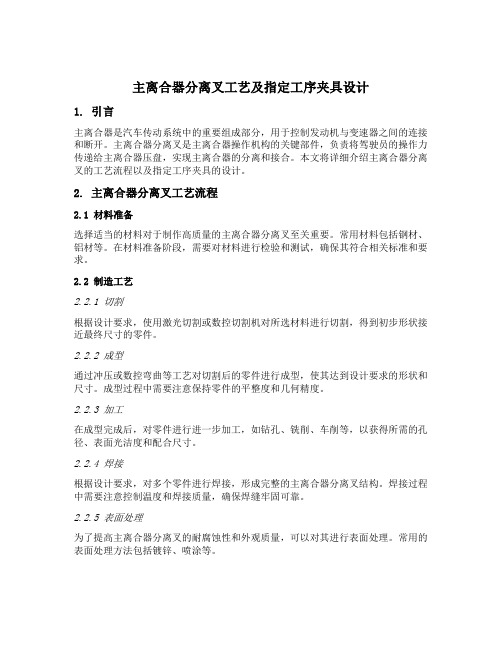
主离合器分离叉工艺及指定工序夹具设计1. 引言主离合器是汽车传动系统中的重要组成部分,用于控制发动机与变速器之间的连接和断开。
主离合器分离叉是主离合器操作机构的关键部件,负责将驾驶员的操作力传递给主离合器压盘,实现主离合器的分离和接合。
本文将详细介绍主离合器分离叉的工艺流程以及指定工序夹具的设计。
2. 主离合器分离叉工艺流程2.1 材料准备选择适当的材料对于制作高质量的主离合器分离叉至关重要。
常用材料包括钢材、铝材等。
在材料准备阶段,需要对材料进行检验和测试,确保其符合相关标准和要求。
2.2 制造工艺2.2.1 切割根据设计要求,使用激光切割或数控切割机对所选材料进行切割,得到初步形状接近最终尺寸的零件。
2.2.2 成型通过冲压或数控弯曲等工艺对切割后的零件进行成型,使其达到设计要求的形状和尺寸。
成型过程中需要注意保持零件的平整度和几何精度。
2.2.3 加工在成型完成后,对零件进行进一步加工,如钻孔、铣削、车削等,以获得所需的孔径、表面光洁度和配合尺寸。
2.2.4 焊接根据设计要求,对多个零件进行焊接,形成完整的主离合器分离叉结构。
焊接过程中需要注意控制温度和焊接质量,确保焊缝牢固可靠。
2.2.5 表面处理为了提高主离合器分离叉的耐腐蚀性和外观质量,可以对其进行表面处理。
常用的表面处理方法包括镀锌、喷涂等。
2.3 检验与测试制造完成后,需要对主离合器分离叉进行检验与测试,确保其符合相关标准和要求。
常用的检测方法包括外观检查、尺寸测量、材料测试等。
3. 指定工序夹具设计为了提高主离合器分离叉的生产效率和质量稳定性,需要设计适用的工序夹具。
以下是指定工序夹具的设计要点:3.1 夹持方式根据主离合器分离叉的形状和结构特点,选择合适的夹持方式。
常用的夹持方式包括机械夹持、气动夹持等。
3.2 夹具结构设计夹具时需要考虑主离合器分离叉的形状和尺寸,确保其能够稳固地固定在夹具上,并且方便操作人员进行装卸。
同时,还需要考虑到生产过程中可能出现的振动和变形等因素,采取相应措施以保证加工精度。
分离爪机床夹具课程设计

分离爪机床夹具课程设计一、课程目标知识目标:1. 学生能理解分离爪机床夹具的基本结构、工作原理及其在机械加工中的应用。
2. 学生能够掌握分离爪机床夹具的安装、调整和操作方法。
3. 学生能够了解并描述分离爪机床夹具的维护与故障排除方法。
技能目标:1. 学生能够运用所学的理论知识,进行分离爪机床夹具的组装和调试。
2. 学生能够通过实际操作,掌握分离爪机床夹具的安全使用技巧。
3. 学生能够分析并解决分离爪机床夹具在加工过程中出现的问题。
情感态度价值观目标:1. 培养学生对机械加工行业的热爱,增强职业责任感。
2. 培养学生团队合作精神,提高沟通与协作能力。
3. 增强学生的安全意识,养成良好的操作习惯。
课程性质:本课程为专业技能课程,以实践操作为主,理论教学为辅。
学生特点:学生已具备一定的机械加工基础,具有一定的动手能力和问题解决能力。
教学要求:结合课程性质和学生特点,注重实践与理论相结合,提高学生的操作技能和问题解决能力,培养具备实际应用能力的复合型人才。
通过本课程的学习,使学生能够达到上述课程目标,并在实际工作中得以应用。
二、教学内容1. 分离爪机床夹具的基本概念与结构- 夹具的定义、分类及功能- 分离爪机床夹具的组成及其作用2. 分离爪机床夹具的工作原理与性能- 夹紧力与加工精度的关系- 分离爪夹具的力矩计算与调整3. 分离爪机床夹具的安装与调整- 夹具在机床上的安装方法- 分离爪的调整与检验4. 分离爪机床夹具的操作与应用- 夹具操作流程及注意事项- 实际加工中的应用案例分析5. 分离爪机床夹具的维护与故障排除- 日常维护与保养方法- 常见故障现象及排除方法6. 实践操作- 分离爪机床夹具的组装与调试- 加工过程中的安全操作与问题解决教学内容安排与进度:第一周:基本概念与结构,工作原理与性能第二周:安装与调整,操作与应用第三周:维护与故障排除,实践操作教材章节关联:《金属切削机床与夹具》第四章:机床夹具概述《金属切削机床与夹具》第五章:机床夹具的结构与设计《金属切削机床与夹具》第六章:机床夹具的安装与调试《金属切削机床与夹具》第七章:机床夹具的应用实例及故障排除三、教学方法本课程采用以下多样化的教学方法,旨在激发学生的学习兴趣,提高学生的主动参与度和实践操作能力。
机电系毕业论文参考题目

机电系毕业设计论文参考题目300×400数控激光切割机XY工作台部件及单片机控制设计CA6140车床主轴箱的设计DTⅡ型固定式带式输送机的设计FXS80双出风口笼形转子选粉机;JL Y3809机立窑(加料及窑罩部件)设计JL Y3809机立窑(窑体及卸料部件)JL Y3809机立窑(总体及传动部件)设计MR141剥绒机锯筒部、工作箱部和总体设计PF455S插秧机及其侧离合器手柄的探讨和改善设计PLC在高楼供水系统中的应用Q3110滚筒式抛丸清理机的设计(总装、弹丸循环及分离装置、集尘器设计) Q3110滚筒式抛丸清理机的设计(总装、滚筒及传动机构设计)SF500100打散分级机回转部分及传动设计X700涡旋式选粉机YQP36预加水盘式成球机设计Z30130X31型钻床控制系统的PLC改造Φ3×11M水泥磨总体设计及传动部件设计Φ1200熟料圆锥式破碎机半精镗及精镗气缸盖导管孔组合机床设计(夹具设计)半精镗及精镗气缸盖导管孔组合机床设计(镗削头设计)柴油机齿轮室盖钻镗专机总体及夹具设计柴油机齿轮室盖钻镗专机总体及主轴箱设计柴油机气缸体顶底面粗铣组合机床总体及夹具设计车床变速箱中拔叉及专用夹具设计乘客电梯的PLC控制出租车计价器系统设计电动自行车调速系统的设计多用途气动机器人结构设计工艺-WH212减速机壳体加工工艺及夹具设计管套压装专机结构设计机油冷却器自动装备线压紧工位装备设计基于AT89C2051单片机的温度控制系统的设计基于普通机床的后托架及夹具设计开发金属粉末成型液压机PLC设计可调速钢筋弯曲机的设计空气压缩机V带校核和噪声处理螺旋管状面筋机总体及坯片导出装置设计模具-Φ146.6药瓶注塑模设计模具-冰箱调温按钮塑模设计模具-电机炭刷架冷冲压模具设计模具-水泥瓦模具设计与制造工艺分析膜片式离合器的设计内循环式烘干机总体及卸料装置设计全自动洗衣机控制系统的设计设计-CG2-150型仿型切割机设计-ZL15型轮式装载机设计-插秧机系统设计设计-工程钻机的设计设计机床-S195柴油机机体三面精镗组合机床总体设计及夹具设计设计机床-车床主轴箱箱体右侧10-M8螺纹底孔组合钻床设计设计-搅拌器的设计设计-精密播种机生产线上运输升降机的自动化设计实验用减速器的设计双铰接剪叉式液压升降台的设计四层楼电梯自动控制系统的设计万能外圆磨床液压传动系统设计卧式钢筋切断机的设计锡林右轴承座组件工艺及夹具设计新KS型单级单吸离心泵的设计新型组合式选粉机总体及分级部分设计压燃式发动机油管残留测量装置设计知识竞赛抢答器PLC设计自动洗衣机行星齿轮减速器的设计组合机床主轴箱及夹具设计毕业设计带式运输机用的二级圆柱齿轮减速器课程设计总泵缸体夹具设计课程设计CA6140车床后托架的夹具毕业设计拨叉C加工工艺及夹具设计毕业设计拨叉A加工工艺及夹具设计毕业设计CA6140杠杆加工工艺及夹具设计毕业设计(论文)箱体顶盖零件工艺规程及工装设计课程设计“CA6140车床拨叉,型号861002”零件的机械加工工艺及工艺设备课程设计扬声器模具设计课程设计防尘盖冲压模具设计毕业论文支撑掩护式液压支架的设计课程设计“法兰盘”零件的机械加工工艺规程及工艺装备设计毕业设计机器人自动火焰切割H型钢的设计毕业设计数控龙门三枪H型钢自动火焰切割机毕业设计高速压力机设计毕业设计无摩擦球阀设计毕业设计QTZ25型塔式起重机变幅机构毕业设计卡座的冲压成形方案及模具设计——级进模设计课程设计二级展开式圆柱齿轮减速器课程设计矩形花键拉刀及矩形花键铣刀设计毕业设计CD盒注塑模设计毕业设计高层建筑外墙清洗机---升降机部分的设计课程设计设计”CA6140车床拨叉”零件的机械加工工艺规则及工艺装备课程设计设计“CA6140车床”拨叉零件的机械加工工艺规程及工艺装备(中批量生产)课程设计设计“CA6140车床”拨叉零件的机械加工工艺规程及工艺装备(中批量生产)毕业设计5号电池充电器外壳的塑件注射模毕业设计抽屉注塑模具设计毕业设计冲3孔冲压件设计毕业设计液压支架设计毕业论文塑料包装机构主传动机构设计——二级展开式圆柱圆锥齿轮减速器毕业设计多功能齿轮实验台设计与CAD毕业设计钮锁冷冲模的设计毕业设计砂带分条机设计毕业设计传动盖冲压工艺制定及冲孔模具设计毕业设计冲孔压力机毕业设计高楼外墙清洗机毕业设计交流变频调压调速乘客电梯设计毕业设计PE10自行车无级变速器设计毕业设计XK5040数控立式铣床进给系统设计毕业设计YC1040载货汽车底盘总体及制动器设计毕业设计DTⅡ型皮带运输机设计毕业设计Q3110滚筒式抛丸机总装、弹丸分离装置及除尘器设计毕业设计基于Pro/E的装载机工作装置的实体建模及运动仿真毕业设计垃圾车车厢和排出机构液压系统设计毕业设计木工用异型槽龙门铣床液压系统改进及除尘设计毕业设计经济型数控系统研究与设计毕业设计汽车大梁生产线全液压铆接机液压系统设计毕业设计BM—4010PD万达载货汽车后驱动桥的设计毕业设计隔水管横焊缝自动对中装置的设计(机械电气部分)毕业设计拖拉机拨叉铣专机(卧式)毕业设计低速载货汽车车架及悬架系统设计毕业设计YD5141SYZ后压缩式垃圾车的上装箱体设计毕业设计在高速端铣切削中切屑形成的调查毕业设计PLC控制直列式加工自动线设计毕业设计YD9160TCL轿运车箱体设计毕业设计YD9160TCL轿运车前后桥设计毕业设计大型管材相贯线切割机设计毕业设计CK-Ⅱ型车床主轴箱加工6~Ф17孔两面卧式组合钻床毕业设计硫化机卸胎装置及其微机控制系统毕业设计拖拉机拨叉铣专机(立式)毕业设计立卧三面镗床液压系统设计毕业设计双模轮胎硫化机机械手控制系统设计毕业设计钻加工CK—Ⅱ型数控车床主轴箱6-ф17孔两面卧式组合钻床毕业设计DTⅡ型皮带运输机设计毕业设计弧面蜗杆加工专用数控机床设计毕业设计车载机械自动调平机械系统设计与开发毕业设计组合机床设计毕业设计四柱万能液压机系统设计毕业设计自动弯管机装置及其电器设计毕业设计硫化机主传动微机控制系统毕业设计机械手的设计毕业设计圆柱坐标型工业机器人设计毕业设计皮带输送机设计(无角度)课程设计脱水斗式提升机设计课程设计单级圆柱齿轮减速器毕业设计高压水射流喷丸机床毕业设计刮板输送机毕业设计离心式渣浆泵结构设计毕业设计螺旋离心泵结构设计毕业设计泵轴球窝的加工毕业设计仿指按摩器按摩杆注射成型模具设计毕业设计三轴工业机器人的结构设计毕业设计落料冲孔翻边复合模具设计课程设计设计“花键传动轴”零件的机械加工工艺及夹具毕业设计柴油机连杆工艺工装设计毕业设计调节盘的数控车床编程与模拟仿真毕业设计配合零件加工工艺、程序编制及仿真毕业设计凸凹模具数控加工工艺及编程毕业设计高速枪管绞孔机毕业设计CG2-150型仿型切割机测绘说明书一级圆柱斜齿轮减速器毕业设计单筒冷却机传动装置设计毕业设计短臂冲压成形工艺分析及模具设计毕业设计汽油机连杆组合机床及工艺装备毕业设计叉杆零件工艺设计与工装设计毕业设计传动齿轮工艺设计毕业设计分离爪工艺规程和工艺装备设计毕业设计阀门零件机械加工工艺规程和工艺装备的设计毕业设计机座工艺设计与工装设计毕业设计减速箱体工艺设计与工装设计毕业设计连杆零件加工工艺及专用钻床夹具的设计毕业设计十字接头零件分析毕业设计输出轴工艺与工装设计毕业设计惰轮轴工艺设计和工装设计毕业设计斜联结管数控加工和工艺毕业设计支架零件图设计毕业设计液压升降舞台的设计毕业设计6shz-60直联式双吸离心泵的设计毕业论文液压式测力装置毕业设计自由度并联机构的平行机设计毕业设计配合零件加工工艺、程序编制及仿真毕业设计CM6132型精密车床主传动系统数控改造设计毕业设计手机充电器外壳的成形模具设计课程设计连杆弹簧复位自动调偏装置毕业设计“包装机对切部件”设计毕业设计C6163型车床的经济型数控改造设计毕业设计《喷雾咀》注塑模具设计课程设计CA10B解放牌汽车中间轴轴承支架毕业设计半自动液压专用铣床液压系统的设计毕业设计数控机床45#刀柄拉刀机构设计毕业设计车刀角度测量装置设计毕业设计雪碧瓶盖注塑模设计毕业设计带式输送机传动装置中的一级圆柱齿轮减速器毕业设计CD盒模具设计毕业设计闹钟后盖模具设计毕业设计渐开线涡轮数控工艺及加工毕业设计典型壳体的模具数控加工毕业设计人关节防脱位臼衬的模具的数控加工毕业设计大排量斜盘式轴向柱塞泵毕业设计玻璃升降器复合拉伸模的设计毕业设计TOP-HOUSING注塑模设计毕业设计把手封条注塑模的设计毕业设计掩护式液压支架设计毕业设计带式输送机传动滚筒的设计毕业设计YTP26气腿式凿岩机机体工艺、夹具设计毕业设计新型免胀套、免键联接等强度滚筒设计毕业设计电器开关网芯零件冲压工艺及模具设计毕业设计酒瓶内盖塑料模具设计毕业设计管架注塑模设计毕业设计多功能甘蔗中耕田管机改进设计毕业设计鼓形齿联轴器的设计毕业设计童心吸水杯杯盖注塑设计毕业设计DK7732数控高速走丝电火花线切割机及控制系统毕业论文拨叉机械加工工艺规程及铣断专用夹具设计毕业设计加工液压泵上体三个阶梯孔的机床专用夹具计算机辅助设计研究毕业设计垫圈落料冲孔复合模具设计毕业设计玉米脱粒机的设计课程设计设计“填料箱盖”零件的机械加工工艺及工艺设备毕业设计内充种气吸玉米免耕播种机的设计—镇压部分的设计毕业论文采煤机截割部设计毕业设计“阀体”零件的工艺设计毕业设计冲压汽车灯罩毕业设计TMJ200型水果糖糖料拉白机设计毕业设计高档化妆品瓶盖注射模具设计毕业设计螺杆压缩机系统装置设计毕业设计(旅行餐碗)注塑模设计毕业设计数控铣床的主轴箱结构设计毕业设计汽车输油管的模具设计毕业设计太阳能铝边框冲孔模设计毕业设计外壳落料拉深模具设计课程设计带式输送机说明书课程设计龙门起重机课程设计阶梯圆桶落料拉深复合模具设计课程设计MPS加工站机械设计毕业设计铰链卷圆模具设计高分子材料成型模具课程设计方便饭盒上盖注塑模具设计课程设计沐浴露瓶盖注射模设计课程设计清新剂盒盖注射模设计课程设计拖拉机用垫片的成型工艺与模具设计毕业设计轴盖复合模的设计与制造毕业设计MPS安装站机械设计课程设计托森差速器的设计课程设计双头铆接机课程设计ZL40装载机反转连杆机构工作装置的设计课程设计CD盒注塑模设计毕业设计法兰盘夹具设计设计说明书设计“CA6140车床拨叉”零件的机械加工工艺及工艺设备毕业设计移动式X光机总体及组件设计毕业设计二级齿轮减速箱设计毕业论文小型三辊卷板机设计毕业设计台灯灯座注射模具设计与制造毕业设计FDP-15非开挖导向钻机主机体设计毕业设计JZ—I型校直机毕业设计MG132/320-W型采煤机左牵引部机壳的加工工艺规程及数控编程金属切削机床课程设计CA6140型车床主运动机械变速传动系统的结构设计毕业设计X5020B立式升降台铣床拨叉壳体毕业设计XQB小型泥浆泵的结构设计毕业设计板材送进夹钳装置毕业设计塑料粉末静电喷涂生产线毕业设计拨叉80-08的加工工艺及夹具设计毕业设计攻丝组合机床设计毕业设计钻孔组合机床设计毕业设计压缩机箱体加工工艺及夹具设计毕业设计矿用液压支架的设计毕业设计CA6140车床后拖架零件加工工艺及铣底面专用夹具设计毕业设计齿轮泵泵体工艺及加工Φ14、2-M8孔夹具设计毕业设计CA6140普通车床的数控技术改造(机械部分)毕业设计CA6140普通车床床头1轴轴承座夹具设计课程设计刮板式流量计设计毕业设计WH212减速机壳体加工工艺及夹具设计毕业设计塑料水杯模具的研制毕业设计基于proe的汽车阀体零件加工工艺毕业设计智能化自寻迹程控车模外形及其控制系统设计毕业设计TGSS-50型水平刮板输送机---机头段设计毕业设计显微镜左右棱镜座压铸模设计毕业论文齿轮架零件的机械加工工艺规程及专用夹具设计毕业设计挖掘机液压系统设计毕业设计传动轴的加工工艺机床数控技术课程设计减速箱箱体的数控加工工艺与编程课程设计卧式车床主运动变速系统设计毕业设计压力机与垫板间夹紧装置的设计课程设计说明书Y A32-3150型四柱万能液压机液压系统设计课程设计说明书圆体成形车刀和圆拉刀的设计课程设计拖拉机倒档拨叉的工艺规划及夹具设计毕业设计宠物垫生产线的部件机械设计毕业设计ZXK-7532数控立式钻铣床主运动、进给系统及控制系统的设计毕业设计R175型柴油机机体加工自动线上用多功能液压机械手设计毕业论文基于PRO/E的双轴双凸轮联动轨迹再现机构机械装置的设计毕业设计台式数控龙门雕刻机TLNC-X-2030工作台及Y轴传动部件设计课程设计设计计算一台台式起重机起升机构毕业设计EX1000高效二次风选粉机(传动及壳体部件)设计毕业设计普通式双柱汽车举升机设计课程设计套筒机械加工工艺规程制订毕业设计轴向柱塞泵设计毕业设计机械手设计毕业设计带位移电反馈的二级电液比例节流阀设计毕业设计中型四柱式万能液压机及液压系统设计毕业设计送料机械手设计及Solidworks运动仿真毕业设计乳化液泵设计毕业设计小汽车维修用液压升举装置毕业设计轧钢机设计毕业设计磨粉机设计毕业设计铁水浇包倾转机构的设计毕业设计矿用液压支架的设计毕业论文对称传动剪板机毕业论文双行简易播种机毕业设计立木地板加工机床--成型机分度机构毕业设计椭圆盖板的宏程序编程与自动编程毕业设计液压传动机械手的设计课程设计说明书设计“传动轴突缘叉”零件的机械加工工艺及工艺设备毕业设计漫步者R211TⅡ低音炮外壳外型设计及其注射模设计毕业设计设计自来水管阀阀体的零件的机械加工工艺规程及6、7道工序的夹具设计毕业设计10m3机械式定量阀的研究与三维造型设计毕业设计壳形塑料件的注射模设计毕业设计鼠标上壳造型设计毕业设计塑料挂钩座注射模具设计毕业设计小电机外壳造型和注射模具设计及CAE分析毕业设计叶型加工工装设计毕业设计经济型掩护式液压支架的设计毕业设计电源插头塑料模具设计毕业设计设计“CA6140法兰盘”零件的机械加工工艺规程及工艺装备(年产量为4000件)课程设计螺旋千斤顶的设计毕业设计底座注塑模模具设计课程设计链式输送机传动装置课程设计法兰盘的机械加工工艺规程制订及选定工序专用家具的设计毕业设计JD-40型调度绞车改进设计毕业设计3L-10/8空气压缩机曲轴零件的机械加工工艺及夹具设计毕业设计拨叉(12-07-05)加工工艺及夹具设计毕业设计后钢板弹簧吊耳加工工艺及夹具设计毕业设计300X400数控激光切割机设计毕业设计闭风器的设计课程设计设计“CA6140车床法兰盘”零件的机械加工工艺及工艺设备课程设计单级斜齿圆柱齿轮传动设计+绞车传动毕业设计CA6140型铝活塞的机械加工工艺设计及夹具设计毕业设计CA6140填料箱盖加工工艺及数控编程毕业论文搅拌摩擦焊焊接工装设计毕业论文1.0t普通座式焊接变位机工装设计毕业论文自动高压排液阀毕业论文基于Pro/E的蒸汽电熨斗的建模设计毕业设计200米液压钻机变速箱的设计毕业设计100米钻机变速箱设计毕业设计75米钻机的总体设计毕业设计万能渐开线检查仪数据处理毕业设计液压钻机本体组合机床设计毕业论文杠杆零件机械加工工艺规程制订及第25工序工艺装备设计毕业论文低位放顶煤液压支架(支撑掩护式液压支架)的设计课程设计带式运输机用展开式二级圆柱齿轮减速器设计毕业论文数控机床自动夹持搬运装置的液压系统设计毕业论文小型钢坯步进式加热炉液压传动系统课程设计GBW92外圆滚压装置设计课程设计GBW92外圆滚压装置设计课程设计MG132320-W型采煤左牵引部机壳的加工工艺规程及数控编程课程设计MG250591-WD型采煤机右摇臂壳体的加工工艺规程及数控编程毕业设计法兰盘工艺规程设计课程设计基于单片机的电子密码锁的设计毕业论文输出轴零件机械加工工艺规程制订及第工序工艺装备设计毕业论文XTK7140数控立式铣镗床及控制系统设计毕业论文CLK6140轻型数控车床主运动及进给系统设计毕业设计大油壶盖注塑模具设计毕业设计天然气汽车供气系统减压装置设计毕业论文连杆钻孔φ10H9专用夹具毕业论文某机型铰链座制造与工艺毕业论文端面齿盘的设计与加工毕业设计DX型钢丝绳芯带式输送机课程设计制定CA6140车床法兰盘的加工工艺,设计钻φ6mm孔的钻床夹具毕业设计CA6140主轴加工工艺及夹具设计毕业论文冲压废料自动输送装置毕业论文C618型卧式车床经济型数控纵向改造毕业论文C6136型卧式车床经济型数控改造机械自造工艺及夹具课程设计制定CA6140C车床拨叉的加工工艺,设计钻22mm孔的钻床夹具毕业论文移动手柄设计毕业设计数控电火花线切割机床坐标工作台进给系统设计毕业论文半轴机械加工工艺及工装设计毕业论文液压控制阀的理论研究与设计课程设计普通CA6140车床的经济型数控改造毕业论文设计轴承座车Φ30mm孔的车床夹具毕业论文套筒加工工艺及夹具设计毕业设计轴套零件加工工艺规程设计与编程毕业设计座体的工艺分析及数控加工毕业设计雷达控制箱盒体的数控加工毕业论文SPT120-12A?5?1 推料装置毕业论文SSCK20A数控车床主轴和箱体加工编程毕业论文T611镗床主轴箱传动设计及尾柱设计课程设计蜗轮蜗杆传动减速器毕业论文设计加工客车上“车门垫板”零件的冲裁模毕业论文络筒机槽筒专用加工机床及夹具设计课程设计点钞盒底座注射模具设计毕业设计曲轴润滑油孔加工机床的设计研究毕业设计锁壳冲裁模具设计毕业论文WHX112减速机壳加工工艺及夹具设计毕业设计微电机转子冲片模具设计毕业设计CA6140车床后托架的加工工艺及夹具设计毕业论文CA6150车床主轴箱设计金属切削原理与刀具课程设计说明书圆孔拉刀设计机械制造工艺课程设计说明书法兰零件夹具设计毕业论文CA6140车床后托架加工工艺及夹具设计毕业设计物流液压升降台的设计毕业论文落料,拉深,冲孔复合模毕业设计DTⅡ型固定式带式输送机毕业设计打印机压轮设计毕业设计快速模具集成系统精度保证体系研究毕业设计滤油器支架模具设计毕业设计梳棉机箱体设计毕业论文LMXC-Ⅰ型露天选采机液压系统设计毕业设计可伸缩带式输送机结构设计毕业设计AWC机架现场扩孔机设计毕业论文复合化肥混合比例装置及PLC控制系统设计毕业论文膜片弹簧的冲压工艺及模具设计机械设计课程设计带式输送机说明书和总装图课程设计X-Y数控工作台毕业设计ZFS1600/12/26型液压支架掩护梁设计毕业设计运送铝活塞铸造毛坯机械手设计毕业设计上料机液压系统设计毕业设计接线端子板冲孔、落料、压弯复合模设计毕业设计冲压废料自动输送装置毕业论文设计脚手架冲孔模具毕业设计手机塑料外壳注塑模(不够完整)课程设计设计一卧式单面多轴钻孔组合机床液压系统设计说明书铣断夹具毕业论文WY型滚动轴承压装机设计毕业设计论文经济型数控车床纵向进给运动设计及润滑机构设计毕业设计论文J45-6.3型双动拉伸压力机的设计毕业设计冲裁垫片模具的设计毕业设计气动通用上下料机械手的设计——机械结构设计毕业设计水电站水轮机进水阀门液压系统的设计毕业设计63CY14-1B轴向柱塞泵改进设计课程设计设计低速级斜齿轮零件的机械加工工艺规程毕业设计普通CA6140车床的经济型数控改造毕业论文钩尾框夹具设计(镗φ92孔的两道工序的专用夹具)机械制造工艺学课程设计设计“拨叉”零件的机械加工工艺规程及工艺装备(年产量5000件)课程设计带式输送机传动装置毕业论文桥式起重机副起升机构设计毕业论文桥式起重机小车运行机构设计课程设计四工位专用机床传动机构设计无模压力成形机设计普通车床主传动系统小型三辊卷卷板轴向柱塞泵设计三辊卷板机椭圆盖板的宏程序编程与自动编程。
六自由度机械爪装配工艺流程及标准

六自由度机械爪装配工艺流程及标准英文回答:The assembly process of a six-degree-of-freedom mechanical gripper involves several steps to ensure the proper functioning of the gripper. The standard assembly process includes the following steps:1. Inspection of Components: Before starting the assembly, all the components of the mechanical gripper are thoroughly inspected to ensure that they are free from any defects or damages.2. Sub-assembly of Components: The components of the gripper are then sub-assembled according to the design specifications. This may include assembling the fingers, joints, actuators, and sensors.3. Integration of Sub-assemblies: Once the sub-assemblies are completed, they are integrated to form thecomplete gripper assembly. Care is taken to ensure that all the components are aligned properly and securely fastened.4. Functional Testing: After the assembly is completed, the gripper undergoes functional testing to ensure that all the degrees of freedom are functioning as expected. This may involve testing the gripping force, range of motion, and response to control signals.5. Quality Inspection: A final quality inspection is carried out to check for any defects or malfunctions. This may include visual inspection, dimensional measurements, and performance testing.6. Packaging and Shipment: Once the gripper assembly passes all the quality checks, it is packaged according to the standard packaging requirements and shipped to the customer.The standard for the assembly process of a six-degree-of-freedom mechanical gripper ensures that the final product meets the required specifications and functions asintended.中文回答:六自由度机械爪的装配工艺流程包括以下几个步骤,以确保机械爪的正常运行:1. 零部件检查,在开始装配之前,对所有零部件进行彻底检查,以确保它们没有任何缺陷或损坏。
毕业设计参考题目

毕业设计参考题目81 传动齿轮工艺设计82 带式运输机用的二级圆柱齿轮减速器设计83 低速级斜齿轮零件的机械加工工艺规程84 端面齿盘的设计与加工85 惰轮轴工艺设计和工装设计86 二级直齿轮减速器设87 法兰零件夹具设计188 分离爪工艺规程和工艺装备设计89 杠杆90 杠杆工艺和工装设计91 过桥齿轮轴机械加工工艺规程92 后钢板弹簧吊耳的工艺和工装设计93 活塞的机械加工工艺,典型夹具及其CAD设计94 机械手的设计95 机座工艺设计与工装设计96 减速箱体工艺设计与工装设计97 渐开线涡轮数控工艺及加工98 金属切削加工车间设备布局与管理99 连杆零件加工工艺及100 滤油器支架模具设计101 螺旋千斤顶设计102 平面关节型机械手设计103 汽车半轴104 青饲料切割机105 三辊卷板机106 设计“推动架”零件的机械加工工艺及工艺设备(毕设)107 设计“CA6140法兰盘”零件的机械加工工艺规程及工艺装备108 设计“推动架”零件的机械加工工艺及工艺设备(课设)109 设计一用于带式运输机上的传动及减速装置110 十字接头零件分析111 输出轴工艺与工装设计112 数控车削中心主轴箱及自驱动刀架的设计113 数控机床自动夹持搬运装置的液压系统设计114 套筒机械加工工艺规程制订115 椭圆盖板的宏程序编程与自动编程116 斜齿圆柱齿轮减速器装配图及其零件图117 型星齿轮的注塑模设计118 轴向柱塞泵设计119 总泵缸体加工120 组合件数控车工艺与编程121 组合铣床的总体设计和主轴箱设计122 FXS80双出风口笼形转子选粉机123 JLY3809机立窑(加料及窑罩部件)设计124 JLY3809机立窑(窑体及卸料部件)125 JLY3809机立窑(总体及传动部件)设计125 MR141剥绒机锯筒部、工作箱部和总体设计126 PF455S插秧机及其侧离合器手柄的探讨和改善设计127 化工塔图与说明书128 环面蜗轮蜗杆减速器129 多用途气动机器人结构设计130 三通管的塑料模设计131 高速数字多功能土槽试验台车的设计132 高层建筑外墙清洗机---升降机部分的设计133 0-卧式钢筋切断机的设计134 颗粒状糖果包装机设计135 矩形花键拉刀及矩形花键铣刀设计136 活动钳137 杠杆Zl159-a138 0-卧式钢筋切断机的设计139 04双齿减速器设计140 03CG2-150型仿型切割机141 普通钻床改造为多轴钻床142 (设计)5XZ-3.0型重力式清选机下体设计143 毕业设计齿轮144 单拐曲轴机械加工工艺145 带式输送机传动装置设计146 传动盖冲压工艺制定及冲孔模具设计147 ML280螺旋钻采煤机推进机构的设计148 PE10自行车无级变速器设计149 QTZ25型塔式起重机变幅机构150 CM6132型精密车床主传动系统数控改造设计151 CA6140杠杆加工工艺及夹具设计152 可伸缩带式输送机卷带装置设计(半成品)153 05多功能自动跑步机(机械部分设计)154 单级圆柱齿轮减速器155 3L-108空气压缩机曲轴零件156 拨叉(12-07-05)加工157 后钢板弹簧吊耳加工工艺及夹具设计158 铣套筒四槽铣床与夹具图纸及说明书159 设计气门摇杆轴支座零件的机械加工工艺规程及专用夹具160 柴油机曲轴工艺设计及夹具设计161 钻泵体盖6-φ7机床与夹具图纸说明书162 钻泵体盖6-φ2孔机床与夹具图纸说明书163 CA6140车床手柄座钻法兰四孔夹具及加工工艺和说明书164 钻阀门φ16机床与夹具图纸说明书165 设计机床-CJK6132数控车床及其控制系统设计168 组合机床主轴箱及夹具设计169 钻箱体6-@17孔夹具170 一级圆柱齿轮减速器171 摇臂磨床钻机设计图纸172 压燃式发动机油管残留测量装置设计173 铣箱体平面夹具174 设计-机械手-数控机床上下料机械手设计(高速切削的数控加工工艺) 175 X62W铣床主轴机械加工工艺规程与钻床夹具设计176 X5020B立式升降台铣床拔叉壳体工艺规程制订177 Z90型电动阀门装置及数控加工工艺的设计178 回转盘工艺规程设计及镗孔工序夹具设计179 MG132320-W型采煤左牵引部机壳的加工工艺规程及数控编程180 MG250591-WD型采煤机右摇臂壳体的加工工艺规程及数控编程181 CA6140床头I轴轴承座及专用夹具设计182 “填料箱盖”零件的工艺规程及钻孔夹具设计183 CA6140型铝活塞的机械加工工艺设计及夹具设计184 8英寸钢管热浸镀锌自动生产线设计185 102机体齿飞面孔双卧多轴组合机床及CAD设计186 200米液压钻机变速箱的设计187 “包装机对切部件”设计188 C618数控车床的主传动系统设计189 地下自卸汽车工作、转向液压系统190 DTⅡ型皮带机设计191 GBW92外圆滚压装置设计192 NK型凝汽式汽轮机调节系统的设计192 PLC控制机械手设计193 SPT120推料装置194 T611镗床主轴箱传动设计及尾柱设计195 XQB小型泥浆泵的结构设计196 YZJ压装机整机液压系统设计197 巷道堆垛类自动化立体车库198 巷道式自动化立体车库升降部分199 小型轧钢机设计200 校直机设计201 液压绞车设计202 液压式双头套皮辊机203 玉米脱粒机设计204 自动跳绳机205 柴油机燃油系统毕业论文206 自动冲床设计207 0.6L摩托车用四气门电喷汽油机气缸盖的设计208 星轮加工工艺及夹具设计209 万能外圆磨床液压传动系统设计210 实验用减速器的设计211 单转子可逆式锤式破碎机212 反击锤式破碎机.rar213 设计“支架”零件的机械加工工艺规程及此零件“铣77两端面”.ra r 214 白炽灯自动生产线动力传递主系统优化设计.rar 215 往复杠杆的工艺夹具设计.rar216 CA6140车床拨叉831003.rar218 X62w主轴工艺规程及钻4-M12夹具设计.rar219 分离爪的工艺分析及工装夹具设计.rar220 汽车变速器体的工艺及夹具设计.rar221 活塞机械加工工艺规程及粗镗销孔夹具设计.rar222 打印机墨加工工艺223 传动箱体工艺与夹具设计.rar224 拖拉机倒挡拨叉两套夹具设计及说明书225 数控加工工艺分析及程序设计226 壳体加工艺及量检具设计227 二级展开式圆柱齿轮减速器228 摇柄浇注模模型建模及数控加工工艺设计与仿真加工229 拨叉的上数控加工数控工艺230 组合件的数控工艺分析及加工231 复合轴的数控工艺分析及加工232 连杆合件工艺夹具设计233 油压泵盖工艺夹具设计234 转速器盘工艺夹具设计235 分度盘零件的机械加工工艺规程及工艺装备设计236 十字头的机械加工工艺规程及五套夹具设计237 连杆螺钉及其夹具238 盘类零件工艺规程编制及钻床夹具设计239 CA6140“法兰盘”零件的机械加工240 CA6140“法兰盘”零件的机械加工241 拨叉80-08的加工工艺规程及夹具设计(CA6140车床)242 柴油机P型喷油器的设计243 单级圆柱齿轮减速器244 普通机床的数控改造(横向进给机构的设计)245 吊葫芦246 端盖夹具设计247 柴油机气缸体两端面粗铣组合机床总体及夹具设计248 蜗轮——蜗杆减速器的设计249 铣床杠杆零件工艺设计与工装设计250 阀体零件工艺及夹具设计251 传动轴凸缘叉(A10B解放牌汽车)252 卧式蜗轮蜗杆减速器253 结合件工艺分析254 玩具汽车的建模与仿真加工255 液压阀芯加工工艺及翻转铰链式钻孔夹具设计256 十字接头零件工艺及钻孔夹具设计257 倒档拨叉”零件机械加工工艺规程及工艺装备(钻削)设计258 端盖加工艺及专用夹具设计259 后缸盖加工工艺及夹具设计260 汽缸加工工艺及夹具设计261 拨叉D的加工工艺规程及夹具设计262 轴加工工艺规程及铣方块163 LS-150型注塑机注射座数控加工工艺设计及专用夹具设计264 检具的数控加工工艺与编程265 汽车连杆加工工艺及夹具设计(打印)266 C6132车床尾座体的机械加工工艺规程及夹具设计267 摆架铣槽夹具268 机床主轴箱加工工艺及夹具设计269 压缩机后支承座钻孔组合机床设计270 差速器壳盘部多轴钻床设计271 仪表壳体类零件的数控加工工艺设计272 设计机床-车床主轴箱箱体右侧10-M8螺纹底孔组合钻床设计273 X5032A-6270216工作台加工工艺及夹具设计274 中心架盖加工工艺规程及工装夹具设计275 CA6140车床主轴箱体的设计与工艺分析及镗模276 叉形凸缘加工工艺及双面铣床夹具设计277 XZ25-50变速箱278 江淮12变速箱体机械加工工艺及钻两侧面孔工序的夹具279 凸缘机械加工工艺及工装设计280 “CA6140车床手柄座”零件的工艺工装设计281 TY495柴油机机体工艺工装设计282 变速箱体加工工艺及夹具设计283 箱盖的加工工艺及夹具设计(Φ17,Φ22轴孔加工)284 传动箱体工艺与夹具设计(2)285 皮带盘加工工艺规程及工装夹具设计286 TY495柴油机机体工艺工装设计287 支架加工工艺规程及工装夹具设计288 连接座零件钻6-φ7孔组合机床设计及其说明书289 连接座加工艺及钻床夹具设计说明书290 车床转盘零件的机械加工工艺规程及工艺装备设计291 阀盖加工工艺规程及工装夹具设计292 蜗轮箱I的工艺规程和夹具设计293 钻夹具与精磨夹具设计294 浮动夹头工艺及夹具设计295 钻夹具与精磨夹具设计296 刀库支座数控加工工艺及夹具设计297 主轴承盖的工艺方案分析及工装设计298 液压系统中截止阀的钻孔夹具设计299 铣削组合机床及其主轴组件设计300 “万向节滑动叉”φ39孔端面铣削组合机床设计301 XK5032A托架的加工工艺及Φ55H7镗孔夹具设计302 +设计-200米钻机回转器设计303 B6030牛头刨床设计304 FX280-2201梳葙墙板305 解放牌汽车第四及第五速变速叉工艺及夹具设计306 XT-4032-F41-11箱体零件的机械制造工艺与夹具设计307 AVC1200电机座的工艺308 计算机辅助W型往复式活塞压缩机设计309 数控机床的进给传动装置设计310 智能巡线机器人设计311 装载机智能称重仪设计312 步进电机指数规律升降速的单片机控制系统设计313 基于LabVIEW的监控系统设计314 基于LabVIEW远程监控系统设计315 基于PLC立体车库控制系统设计316 基于声卡的数据采集317 计算机辅助V型往复式活塞压缩机设计318 132汽车差速器壳加工工艺及夹具设计319 AutoCAD Lisp二次开发带轮的参数化绘制320 AutoCAD二次开发钣金展开CAD系统开发B321 AutoCAD—油浸式变压器的参数化绘图设计322 AVC1200螺母座的机械加工工艺及镗孔夹具设计323 CG6125主轴加工工艺及夹具设计324 X62W主传动设计325 X6232C齿轮加工工艺及其齿轮夹具和刀具设计326 典型零件(连杆)的工艺及工装设计327 内冷式砂轮的机床附件机构设计及工艺设计328 轴向柱塞泵体加工生产线专机及主要辅助设备生产线布置及粗镗机液压系统设计329 轴向柱塞泵体加工生产线专机及主要辅助设备多头钻床及攻丝机床液压系统设计330 轴向柱塞泵泵体加工生产线专机及主辅助设备(车基准机床及双头镗床液压系统设计)331 铣床工作台机械加工工艺及铣削T形槽夹具设计332 推动架的数控工艺及钻孔夹具的设计333 输出轴的数控工艺及主要工装设计334 十字头零件的工艺规程335 气缸盖多轴钻孔组合机床设计336 连接座的数控工艺337 进给箱体加工工艺及夹具设计338 减速箱体及夹具设计339 加工箱体零件的组合机床设计340 后托架零件工艺及加工Φ40、Φ30.2、Φ25.5孔夹具设计341 锻钢固定球阀加工工艺及中体螺孔8-M20的钻孔夹具设计342 铣床升降台加工工艺及夹具设计343 柴油机气门摇臂轴支座加工艺及夹具设计345 柴油机机体加工工艺及组合机床铣两端面夹具设计346 柴油机机体机械加工工艺及其Φ66镗孔夹具设计347 900150旋回破碎机设计348 BJ-130汽车变速箱二轴一二档齿轮工艺、刀具及夹具设计349 箱体零件上六孔的组合机床设计350 尾座体工艺及夹具设计351 套筒加工工艺及夹具设计352 双面铣组合机床设计353 平切口连杆的工艺工装设计354 内冷式砂轮的理论研究355 连杆加工工艺及夹具设计356 将旧车床改造成拉削齿轮内花键的拉床及主体部分设计357 将旧车床改造成拉削齿轮内花键的拉床及浮动部分设计358 机床主传动设计359 东方红拖拉机变速箱箱体工艺及夹具设计360 典型零件(EM170A-01001)工艺过程及工装设计361 磁阀体中心孔组合机床、机床总体工位布置和钻、扩、铰工位液压系统设计362 车床小刀架机械加工工艺及镗孔的夹具设计363 CA6140车床床身加工工艺及夹具设计364 c615车床进给箱加工工艺及其镗孔夹具设计365 弹簧吊耳零件工艺及加工Φ30 两孔夹具设计366 四缸柴油机曲轴工艺工装设计367 减速箱体零件工艺规程及铣尺寸159两侧面铣床夹具设计368 泵体工艺规程及钻6M8孔夹具设计369 X6132主轴加工工艺及夹具设计370 箱体零件工艺规程及加工φ42 孔夹具设计371 铣削组合机床及其传动装置设计372 减速箱体零件工艺规程及加工φ52H8孔夹具设计373 减速器箱体零件工艺及加工Φ120外圆的夹具设计374 电磁阀体平面加工组合机床液压系统设计375 蛙式打夯机设计376 镗削动力头及主轴组件设计378 电磁阀体进出油口孔加工组合机床液压系统设计379 CA6140主轴加工工艺及夹具设计380 钻模体工艺规程及钻2-ф16H7孔夹具设计381 单转子可逆式锤式破碎机设计382 铣削组合机床及其主轴组件设计383 AVC1200电机座的工艺及其镗孔夹具设计384 铣床升降台机械加工工艺及刨燕尾夹具设计385 铣削组合机床及其工作台设计386 减速箱箱体加工工艺及夹具设计387 减速器箱体零件的工艺设计及其加工72H7孔的夹具设计388 齿轮泵泵体工艺及加工Φ14、2-M8 孔夹具设计389 X6132-28主传动设计及主轴组件设计390 压缩机箱体加工工艺及夹具设计391 CQM6132主轴前轴承加工工艺及夹具设计392 CA6140车床后拖架零件加工工艺及铣底面专用夹具设计393 柴油机机体机械加工工艺及其组合机床钻孔夹具设计394 泵体工艺规程及镗Φ48H8孔夹具设计395 XK5032A螺母座加工工艺及其4-M8深20钻孔夹具设计396 VF67空气压缩机曲轴加工工艺及夹具设计397 LH9900拉丝机卷筒机构设计398 EQ140变速箱二轴三档齿轮工艺、刀具及夹具设计399 D85推土机齿轮工艺及刀具设计400 BJ-130汽车变速箱壳体工艺及其夹具设计401 盘类轴向多孔成组钻模设计402 副翼摇臂零件的机械加工工艺规程和机床夹具设计403 带轮工艺及夹具设计404 铣刀405 复合材料数控加工及刀具设计研究406 CA6140拨叉831005408 盘型体三套工装夹具设计409 毕业设计“CA6140法兰盘”零件的机械加工工艺规程及工艺装备410 设计175F柴油机曲轴零件的机械加工工艺规程及加工20孔的夹具411 左支座零件数控加工412 尾座体工艺及夹具设计413 齿轮泵前盖加工艺及铣8mm流油槽夹具414 左支座工艺及夹具设计415 带式输送机的圆柱斜齿轮二级减速器416 蜗轮箱工艺及夹具设计(课程)417 支架零件的机械加工工艺规程编制及钻削φ4孔工序专用夹具设计418 定位支座铣槽夹具设计419 茶叶修剪机420 CA6140滤油器体421 钻床夹具零件钻孔设计422 单拐曲轴工艺规程与装备设计423 磨床砂轮夹具主体加工工艺424 S195柴油机机体工艺及夹具设计425 数控轴类零件加工设计说明书426 数控X-Y工作台设计457 数控加工458 “175F柴油机凸轮轴”零件的机械加工工艺规程及铣键槽的铣床夹具459 带式输送机的圆柱直齿轮二级减速器460 CA6140滤油器体工艺及夹具设计461 浅论轴类零件的数控加工工艺分析与夹具设计462 活塞加工艺463 钻孔组合机床设计464 杠杠加工工艺分析设计465 轴承座加工工艺设计466 CA6140车床拨叉83008加工艺及夹具设计468 彩印机偏心套工艺规程及专用夹具设计469 基于数控机床的典型零件的编程及加工工艺470 车床长丝杠零件机械加工工艺规程制订工艺装备设计471 摇臂零件机械加工工艺规程制订及工艺装备设计472 密封件定位套473 密封件定位套工艺及夹具设计478 底座工艺规程及专用夹具设计479 杠杆机械加工工艺规程设计480 钳身钻孔夹具481 油泵阀芯工艺规程及专用夹具设计482 设计蜗轮零件的数控加工工艺规程483 砂轮外圆整修器零件机械加工工艺规程制订及工序工艺装备设计484 拨叉加工工艺分析485 数控加工工艺与编程综合设计486 阀门装置及数控加工工艺的设计487 杠杆831009488 换档叉铣端面夹具489 高压转子联轴器工艺过程设计490 转向器壳体加工工艺及专用夹具设计491 连杆零件机械加工工艺过程及钻铰Φ14H9孔和倒角夹具设计492 1阀体工艺规程及专用夹具设计493 拨叉861002工艺及夹具设计(CA6140车床)494 拨叉加工工艺规程及专用夹具设计495 车夹具设计496 传动轴凸缘叉(A10B解放牌汽车)497 对开螺母下部工装及夹具设计498 飞锤支架夹具装配图499 设计“轴承座”零件机械加工工艺规程及工艺装备500 输出轴工艺与工装设计501 数控零件加工设计说明书502 轴承座加工工艺说明书及夹具设计503 轴出轴夹具设计504 “填料箱盖”零件的工艺规程及钻孔夹具设计505 变速器换档叉506 传动轴凸缘叉(A10B解放牌汽车)507 底板坐架零件的机械加工工艺规程及工艺装备300--50508 对开螺母下部工装及夹具设计509 套筒加工艺及专用夹具设计510 设计“CA6140车床拨叉”831007零件的机械加工及夹具设计511 拨叉工艺及专用夹具设计512 放泄块接头工艺及其夹具设计513 端盖加工艺及专用夹具设计(大批量)514 端盖加工艺及专用夹具设计(小批量)515 “法兰盘”零件的机械加工(小批量)516 设计“CA6140法兰盘”零件的机械加工517 拨叉夹具工艺及夹具设计518 1拨叉夹具工艺及夹具设计519 踏脚座夹具加工艺及专用夹具设计520 右端盖加工艺及专用夹具设计521 1轴承座工艺及夹具设计522 蜗杆轴工艺工装夹具设计523 摇臂轴座工艺及夹具设计524 支架工艺规程及夹具设计525 微电机壳加工工艺规程及钻孔夹具设计526 设计油封盖零件图零件的机械加工工艺规程及工艺装备527 C6140车床齿轮零件的机械加工工艺规程528 杠杆加工工艺规程及端部宽22mm的槽铣削加工夹具设计529 4100QB柴油机箱体钻孔三面立卧式组合机床后多轴箱设计(立式)530 左右摆动杠杆加工工艺531 右支架工艺及夹具设计532 底座的工艺及其夹具设计533 轮芯工艺夹具设计534 典型零件的造型与数控加工工艺设计535 CA6140数控化改造536 加工脱粒机箱体后面a组孔系的专用机床及工装设计537 减速器箱体镗模夹具设计538 杠杆加工工艺规程及端部宽22mm的槽铣削加工夹具设计539 杠杆6加工工艺及钻孔夹具设计540 深孔夹具设计说明书及图纸541 变速器齿轮轴机械加工工艺过程分析542 轴加工工艺规程分析543 泵座加工工艺规程分析544 机壳机械加工工艺过程分析545 车用空调双孔法兰加工工艺规程及夹具设计(大批量生产)546 角型轴承箱547 车用空调高压充注法兰加工工艺规程及夹具设计(大批量生产)548 自行车花盘复合膜凸模549 减速器箱体镗模夹具设计550 中央泵房自动控制设计551 注塑模-圆珠笔笔盖的模具设计552 冲大小垫圈复合模553 斗式提升机全套毕业设计(水泥谷物)554 模具-电机炭刷架冷冲压模具设计555 安全气囊556 杯子模具557 带式输送机的PLC控制558 毕业设计-花生去壳机559 茶叶修剪机560 柴油机喷油泵的专用夹具设计561 车床改进毕业设计562 齿辊破碎机详细设计563 齿轮箱工艺及钻2-φ20孔、工装及专机设计564 冲压汽车灯罩565 带式二级圆锥圆柱齿轮减速器设计566 电子钟后盖注射模具设计567 冲压汽车灯罩568 盖子零件注射模设计569 谷物运输机传动装置设计570 活塞结构设计与工艺设计571 纳米粉体的实验装置毕业设计572 起重机设计573 清车机毕业设计(打印)574 双螺杆压缩机的设计575 水峪矿300万吨新井设计576 提升机制动系统577 洗衣机机盖的注塑模具设计578 铣床的数控x-y工作台设计579 移动式x光机总体及移转组件设计580 中央泵房自动控制设计581 减速箱体零件工艺规程及两套夹具设计582 车用空调视镜体加工工艺规程及夹具设计(大批量生产)583 底座零件数控加工工艺及夹具设计584 车用空调压缩机充注三通加工工艺规程及夹具设计585 车用空调用压缩机充注体加工工艺规程及夹具设计(大批量生产)586 复合轴的数控工艺分析及加工587 钻体零件的工艺及夹具设计588 车用空调高压管进气锁紧件加工工艺规程及夹具设计(大批量生产)589 箱体加工工艺与夹具设计590 车用空调双孔法兰加工工艺规程及夹具设计(大批量生产)591 滤油器壳体工艺工装设计592 齿轮箱箱箱体制造工艺设计593 汽车变速箱箱体零件的数控加工工艺设计594 “CA6140车床拨叉设计”零件的机械加工工艺规程设计595 离合器从动盘花键套机械加工工艺及夹具设计596 支架的加工工艺与夹具设计597 曲轴箱箱盖零件机械加工工艺规程制订及铣端面工序工艺装备设计598 便携式研磨机锥体座的加工工艺设计及工装准备599 联接轴零件工艺加工及分析600 手柄座夹具设计601 床头箱盖定位器(ZL06-C)零件机械加工工艺规程制订及第钻孔工序工艺装备设计602 泵体零件机械加工工艺规程制订及钻孔工序工艺装备设计603 数控加工工艺卡及夹具设计604 江淮12变速箱体精镗两侧面孔组合机设计及夹具设计605 减速器箱体专用组合机床及工艺装备设计606 对开螺母夹具设计及箱体零件数控加工工艺设计607 CBF-E32-41齿轮泵泵体8-M10底孔钻削专用机床及夹具设计608 泵体零件及夹具设计609 双轴承支撑座钻铰组合机床610 汽车轮毂加工工艺的编制及钻床夹具611 C620车床轴承座的机械加工工艺与夹具设计612 杯轴零件的数控加工工艺设计613 CA6140车床法兰盘的设计及工艺分析614 端盖加工工艺设计615 C6140后托架加工工艺及钻孔夹具设计616 轴承壳体加工艺及专用夹具设计612 上刀连杆槽铣用夹具设计613 机床丝杠的加工工艺及夹具设计614 泵体零件及钻床夹具设计615 设计“连杆盖”零件的机械加工工艺规程(大批量生产)616 轴类零件材料与成形方法的设计及案例分析607 轴承座的材料与加工工艺设计608 安装框架的夹具设计609 变速箱体机械加工工艺规程及铣顶斜面夹具设计610 缸盖两夹具设计611 汽车轴承盖工艺工装设计612 减速箱箱座的夹具设计613 A2J-PK921卧式双面差速器壳钻孔锪端面组合机床的总体设计614 空气压缩机曲轴零件的机械加工工艺及夹具设计615 冲模数控加工工艺文件的拟订616 薄壁套的机械加工工艺规程及专用夹具设计617 轴零件机械加工工艺规程制订及第4刀具9夹具13-14量具工序工艺装备设计。
分离爪课程设计说明书2教材

机械工程学院机械制造技术课程设计说明书设计题目:分离爪钻床夹具设计姓名:南宫飞狐学号:1314419999班级:机械某班指导教师:周老师日期:2016年9月9日目录概述 (2)题目及其要求 (3)一、零件的要求加工工序分析 (4)二、零件结构的定位分析与夹具设计2.1定位分析 (5)2.2 导向方案及导向元件的选择和设计 (6)2.3夹紧装置的设计 (7)2.4 设计夹具体、绘制夹具草图 (7)2.5 夹具结构设计 (8)2.6 绘制夹具装配图 (8)三、主要零件的技术条件分析 (10)四、绘制夹具体零件图及工艺编排4.1芯轴 (10)4.2.夹具基体 (11)五、设计心得 (14)参考文献 (15)概述机床夹具是机械加工工艺系统的重要组成部分,是机械制造中的一项重要工艺装备。
工件在机床上进行加工时,为保证加工精度和提高生产效率,必须使工件在机床上相对刀具占有正确的位置,完成这一功能的辅助装置称为机床夹具。
机床夹具在机械加工中起着重要的作用,它直接影响机械加工的质量、生产率和生产成本以及工人的劳动强度等。
因此机床夹具设计是机械加工工艺准备中的一项重要工作。
在机床上进行加工时,必须先把工件安装在准确的加工位置上,并将其可靠固定,以确保工件在加工过程中不发生位置变化,才能保证加工出的表面达到规定的加工要求(尺寸、形状和位置精度),这个过程叫做装夹。
简言之,确定工件在机床上或夹具中占有准确加工位置的过程叫定位;在工件定位后用外力将其固定,使其在加工过程中保持定位位置不变的操作叫夹紧。
装夹就是定位和夹紧的总和。
夹具工作原理的要点包括以下几点:1)使工件在夹具中占有正确的加工位置。
这是通过工件各定位面与夹具的相对定位元件的定位工作面(定位元件上起定位作用的表面)接触、配合或对准来实现的;2)夹具对于机床应先保证有准确的相对位置,而夹具结构又保证定位元件的定位工作面对夹具与机床相连接的表面之间的相对准确位置,这就保证了夹具定位工作面相对机床切削运动形成表面的准确几何位置,也就达到了工件加工面对定位基准的相互位置精度要求;3)使刀具相对有关的定位元件的定位工作面调整到准确位置,这就保证了刀具在工件上加工出的表面对工件定位基准的位置尺寸。
- 1、下载文档前请自行甄别文档内容的完整性,平台不提供额外的编辑、内容补充、找答案等附加服务。
- 2、"仅部分预览"的文档,不可在线预览部分如存在完整性等问题,可反馈申请退款(可完整预览的文档不适用该条件!)。
- 3、如文档侵犯您的权益,请联系客服反馈,我们会尽快为您处理(人工客服工作时间:9:00-18:30)。
分离爪工艺规程和工艺装备设计
本设计的零件为分离爪,选用Q T40-10球墨铸铁。
根据零件的形状、尺寸精度、生产的经济效益等各方面的详细分析其加工工艺,多采用专用机床加工。
通过对零件的分析,此轴要求精度高,工序适当集中,要求光滑,所以选用工具和尺寸要准。
最后对零件进行校核。
以便达到零件精度的要求。
1分离爪工艺规程和工艺装备设计
机械制造技术课程设计是培养机械工程类专业学生应职应岗能力的重要实践性教学环节,它要求学生能全面综合地运用所学的理论和实践知识,进行零件机械加工工艺规程和工艺装备的设计。
其基本目的是:
(1)培养工程意识。
(2)训练基本技能。
(3)培养质量意识。
(4)培养规范意识。
2机械制造技术课程设计的基本任务与要求
2、1、设计任务
(1)设计一个中等复杂的零件的加工工艺规程;
(2)设计一个专用夹具;
(3)编写设计说明书。
2、2、课程设计基本要求
(1)内容完整,步骤齐全。
(2)设计内容与说明书的数据和结论应一致,内容表达清楚,图纸准确规范,简图应简洁明了,正确易懂。
(3)正确处理继承与创新的关系。
(4)正确使用标准和规范。
(5)尽量采用先进设计手段。
3课程设计说明书的编写
说明书要求系统性好、条理清楚、语言简练、文字通顺、字迹工整、图例清晰、图文并茂,充分表达自己的见解,力求避免抄书。
4分离爪工艺规程和工艺装备设计
(1)设计分离爪中车左侧端面,位置尺寸16;粗车外圆至Φ41.5车床夹具
(2)加工工件零件图如图4-1所示。
(3)生产类型:大批量生产。
(4)毛胚:模铸件。
(5)工艺内容:工件材料为Q T40-10。
车削大头做侧端面。
粗车外圆至Φ41.5。
使用设备为C A6140车床。
刀具为标
准普通刀具。
其工序简图如4-2所示
(6)工序的加工要求:Φ36外圆中心距为(36±0.212)m m;
平行度允差0.05m m;。
第一章分离爪工艺
图4-1
规程和工艺装备设计
1.基本任务:
(1)绘制零件工件图一张;
(2)绘制毛坯—零件合图一张;
(3)编制机械加工工艺规程卡片一套;
(4)编写设计说明书一份;
(5)收集和研究原始资料,为夹具结构设计做好技术准备。
(6)初步拟定夹具结构方案,绘制夹具结构草图,进行必要的理论计算和分析。
选择最佳的夹具结构方案,确定夹具精度和夹具总图尺寸、
公差配合与技术要求。
(7)绘制夹具总图和主要非标准件零件图,编写设计说明书。
(8)编制夹具特殊使用维护、操作、制造方面的说明或技术要求。
2.设计要求:
(1)应保证零件的加工质量,达到设计图纸的技术要求;
(2)在保证加工质量的前提下,尽可能提高生产效率;
(3)要尽量减轻工人劳强度,必须考虑生产安全、工业卫生等措施;
(4)在立足本企业的生产条件基础上,尽可能采用国内外新技术、新工艺、新装备;
(5)工艺规程应正确、完整、简洁、清晰;
(6)工艺规程应满足规范化、标准化要求;
(7)夹具设计保证工件的加工精度;
(8)提高生产效率;
(9)工艺性好;
(10)使用性好;
(11)经济性好。
3.方法和步骤:
3.2零件图审查
3.2.1了解零件的功用及技术要求
熟悉用途、性能及工作条件,明确被加工零件在产品
中的位置和功用,审查图样的完整性和正确性。
分离爪的主要目
的就是分离事物。
3.2.2分析零件的结构工艺性
零件的结构工艺分析主要应考虑以下几个方面:
(1)零件的尺寸公差、形位公差和表面粗糙度的要求应经
济合理;
(2)各加工表面的几何形状应尽量简单;
(3)有相互位置要求的表面应尽量在一次装夹中加工;
3.3毛坯选择
3.3.1毛坯的种类—铸件Q T40-10。
Q T40-10是球墨铸铁,
它的热处理与钢相似,但因其含碳、硅、锰量较多,所以热处理
需要较高的加热温度和较长的保温时间,其淬透性比碳钢好。
毛
坯的铸造后采用低温退火。
3.3.2铸件制造方法的选择
毛坯制造方法应与材料的工艺性、零件的结构形状及
(IT)
砂型铸造 13级以下小Q T40-10各种尺寸简单
3.3.3铸件的尺寸公差与加工余量
3.3.4铸件加工余量表1-6用于成批和大量生产与铸件尺寸公差配套使用的铸件机械加工余量等级和表1-7铸件尺寸公差配套使用的铸件机械加工余量(机械制造技术课程设计3.3.5铸件最小孔径
表面类型成批生产
车削15~30MM
3.3.4毛坯—零件合图
用查表法确定各表面的加工总余量和余量公差。
表1-5铸件尺寸公差数值(机械制造技术课程设计)
表1-6用于成批和大量生产与铸件尺寸公差配套使用的铸件机械加工余量等级
表1-7铸件尺寸公差配套使用的铸件机械加工余量(机械制造技术课程设计)
3.4定位基准的选择
正确地选择定位基准是设计工艺过程的一项重要内容,也是保证
加工精度的关键。
定位基准分为粗基准和精基准。
对于无合适定位面的零件可在毛坯上另外专门设计或加工出定位表面,称为辅助基准。
定位基准的选择原则(机械制造基础P254)
粗基准的选择原则
(1)应选择不加工表面为粗基准。
(2)对于具有较多加工表面的工件,粗基准的选择,应合理分配各加工表面的加工余量,以保证:
1)各加工表面都有足够的加工余量;
2)对某些重要的表面,尽量使其加工余量均匀;
3)使工件上各加工表面总的金属切除量最小;
(3)作为粗基准的表面,应尽量平整,没有浇口,冒口或飞边等其它表面缺陷,以便定位准确;
(4)同一尺寸方向上的粗基准表面只能使用一次;
精基准的选择原则:
(1)基准重合原则
(2)基准统一原则
(3)互为基准原则
(4)自为基准原则
3.4.1夹具设计研究原始资料
1、研究加工工件图样
了解该工件的结构形状.尺寸.材料.热处理要求,主要是表面的加工精度.表面粗糙度及其他技术要求
2、熟悉工艺文件,明确以下内容
(1)毛坯的种类.形状.加工余量及其精度。
(2)工件的加工工艺过程,工序图,本工序所处的地位,本工序前已加工表面的精度及表面粗糙度,基准面的状
况。
(3)本工序所使用的机床.刀具及其他辅助工具的规格。
(4)本工序所采用的切削用量。
3.4.2拟定夹具的结构方案
1.确定夹具的类型
2.确定工件的定位方式及定位元件的结构
工件的定位方式主要取决于工件的加工要求和定位基准
的形状.尺寸。
分析加工工序的技术条件和定位基准选择
的合理性,遵循六点定位原则,按定位可靠.结构简单的
原则,确定定位方式。
常见的定位方式有平面定位.内孔
定位.外圆定位和组合表面(一面两销)定位等。
在确定
了工件的定位方式后,即可根据定位基面的形状,选取相
应的定位元件及结构。
(1)平面定位
在夹具设计中常用的平面定位元件有固定支承.可调支
承.自位支承及辅助支承,其中固定支承又可分为支承钉
和支承板。
3.工件的夹紧方式,计算夹紧力并设计夹紧装置
夹紧机构应保证工件夹紧可靠.安全.不破坏工件的定位及夹压表面的精度和粗糙度。
在设计夹紧装置时必须合
理选择夹紧力的方向和作用点,必要时还应进行夹紧力的
估算。
(1)夹紧力的计算
在确定夹紧力的大小时,为简化计算,通常将夹具和工件
看成一个刚性系统。
根据工件所受切削力.夹紧力(大型
工件还应考虑重力.惯性力等)的作用情况,找出加工过
程中对夹紧最不利的状态,按静力平衡原理计算出理论夹
紧力,最后再乘以安全系数。
(机械制造技术课程设计)
(2)夹紧装置的设计
夹紧装置的设计实际上是一个综合性的问题,确定夹紧力
的大小.方向和作用点时,必须全面考虑工件的结构.工
艺方法.定位元件的结构与布置等因素。
要求夹紧装置动
作迅速,操作安全省力,结构简单.易于制造并且体积
小.刚度好,有足够的夹紧行程和装卸工件的间隙。
常见
的夹紧机构有斜锲机构.螺旋机构.偏心机构等。
也可采
用机动夹紧如液压.气动夹紧等。
4.确定刀具的导向方式或对刀装置表3-49~表3-62为常用的对刀元件和导向元件(机械制造技术课程设计),
供设计时选用
5.确定夹具体的结构类型
夹具上的各种装置和元件通过夹具体连接成一个整
体,因此夹具体的形状及尺寸取决于夹具各种装置的
布置及夹具与机床的连接。
(1)对夹具体的要求
1.有适当的精度和尺寸稳定性
2.有足够的强度和刚度
3.结构工艺性好
4.排屑方便
5.在机床上安装稳定可靠
6. 夹具体毛坯的类型
7. 型材夹具体
8. 铸造夹具体
3、4、3 夹具总图设计
1绘制总装图的注意问题
(1)尽可能采用1:1的比例,以求直观不会产生错觉。