硬质仪表板材料性能技术要求
汽车仪表板的基本类型

汽车仪表板的基本类型
汽车仪表板的结构和用材多种多样,但基本上可以分为硬质和软饰仪表板两大类。
硬质仪表板一般是由塑胶材料整体注塑而成。
这种仪表板结构简单、成本低,本体部分为同一种材料构成,多用于载重汽车及客车,一般不需要表皮材料。
硬质仪表板软质仪表板由表层、缓冲层和骨架三部分构成使用多种材料构成,外表面全部或者上部经过软化处理,触感舒适。
常用材料有 PU 、 PP 、 ABS/PVC 合金等,多用于轿车。
软质仪表板此外,还有钢板冲压成型再焊接,涂装制造的钢质仪表板;钢质仪表板外层包覆人造革后制成的半软化仪表
汽车仪表板的结构和用材多种多样,但基本上可以分为硬质和软饰仪表板两大类。
硬质仪表板一般是由塑胶材料整体注塑而成。
这种仪表板结构简单、成本低,本体部分为同一种材料构成,多用于载重汽车及客车,一般不需要表皮材料。
硬质仪表板
软质仪表板由表层、缓冲层和骨架三部分构成使用多种材料构成,外表面全部或者上部经过软化处理,触感舒适。
常用材料有PU、PP、ABS/PVC合金等,多用于轿车。
软质仪表板
此外,还有钢板冲压成型再焊接,涂装制造的钢质仪表板;钢质仪表板外层包覆人造革后制成的半软化仪表板;木质仪表板等。
5项目五汽车内饰装配
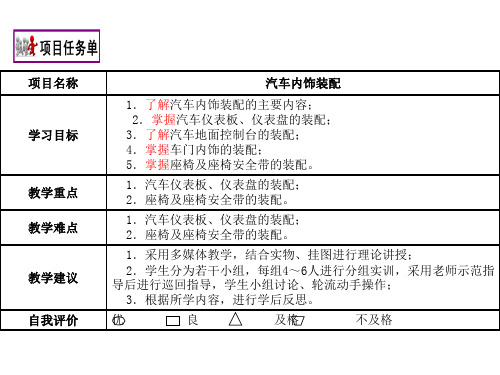
图5-2 硬质仪表板
2.软质仪表板 由表皮、骨架材料、缓冲材料等构成。一般采用钢板、 PC/ABS合金、ABS、改性PP、FRP等材料做骨架,表皮材料采用 PVC/ABS或PVC片材等。其加工工艺是先将表皮真空吸塑成形后,置 入发泡模腔内,再放上骨架,然后注入缓冲类发泡材料(如PU)成 形。由于半硬质PU泡沫有很多气孔,因此其具有良好的回弹性,并 能吸收50%~70%的冲击能量,安全性高,耐热、耐寒、坚固耐用, 且手感好。但是由这三种以上材料构成的仪表板,其材料的再生利 用极为困难。为了便于回收利用,目前正在发展热塑性聚烯烃TPO 表皮和改性聚丙烯PP骨架及聚丙烯发泡材料。软质仪表板一般常在 轿车上使用,如图5-3所示。
图5-10 安装中央支撑面板示意图
图5-11 安装仪表面板加强版
(2)安装仪表面板加强版。安装仪表面板加强版时,用自攻 螺钉1将仪表面板加强版与中央支撑面板相连,用自攻螺钉2、3将 仪表面板加强版与仪表面板相连,各螺钉的拧紧扭矩均为3~5N·m, 加图5-11所示。
(3)安装中央空气出口壳。安装中央空气出口壳时,在仪表 面板指定位置用自攻螺钉以3~ 5N·m的扭矩将中央空气出口壳拧紧, 如图5-12所示。
块上,以将手套箱门挡块安装到手套箱门上。
图5-22 安装仪表面板侧盖
图5-23 安装手套箱门总成
图 5-24 安装手套门挡块
(3)安装乘客侧气囊模块。仪表面板与乘客侧气囊模块采用 两种不同形状的卡扣连接,即上排和左右两侧采用A形卡扣,下排 用B形卡扣,安装时对准上排4个卡扣稍微压下,检查左右卡扣位置 是否正确,确认后压下即可安装完毕,如图5-25所示。
仪表用材料

仪表常用材料仪表安装材料多达上千种,常用的有近百种,可分为两大类。
一类是成品或半成品。
如仪表管材、仪表阀门、仪表使用的型钢等等,这是本章的内容。
另一类是需经机械加工的,如仪表管件(接头)、仪表安装使用的法兰、垫片、紧固件,统称为加工件,一、仪表安装常用管材仪表管道(又称管路、管线很多,可分为四类,即导压管、气动管、电气保护管和伴热管。
1、导压管导压管又称脉冲管,是直接与工艺介质相接角的一中管道,是仪表安装使用最多、要求最高、最复杂的一种管道。
由于导压管直接接触工艺介质,所以管子的选择与被测介质的物理性质、化学性质和操作条件有关。
总的要求是导压管工作在有压或常压条件下。
必须具有一定的强度和密封性。
因此这类管道应该选用无缝钢管。
在中低压介质中,常用的导压管为ф14×2无缝钢管,这是使用最多的一种管子。
有时也用ф18×3或ф18×2。
分析用的取样管路通常也用ф14×2无缝钢管,有时使用ф10×1.5、ф10×1或ф12×1无缝钢管。
在超过10Mpa的高压操作条件下,多采用ф14×4或ф15×4无缝合金钢管。
ffice ffice" />导压管的选用必须满足工艺要求和设计要求,代用必须取得设计同意。
2、气动管路气动管路也称气源管或气动信号管路。
它的通常介质是压缩空气。
压缩空气经过处理,是干燥、无油、无机械杂物的干净压缩空气(有时也用氮气),它的工用压力为0.7~0.8Mpa.气源总管通常由工艺管道专业作为外管的一种,安装到每一个装置的入口,进装置由仪表专业负责。
通常工艺外管的气源管多为DN100,即4,,管道,个别情况为DN50,即2,,管道。
一般为无缝钢管。
而进装置的仪表专业敷设的气动管路则鑫为DN25,即1,,以下的镀锌焊接钢管(旧称镀锌水煤气管)。
一般主管为DN25,即1,,,支管为DN20即3/4,,和DN15即1/2,,的镀锌焊接钢管。
汽车工艺中仪表板整体优化设计要点分析

1.2 汽 车仪 表 板 的性 能 需要
参 考 文 献
汽车仪表板安装于其内部较为特殊 的空间位置上 ,这一安装部 f11李 慧莲 ,王 文 涛 ,李 丽 等.汽 车仪 表板 材 料 氛 灯 老化 试 验 与 自然 曝
位 同时集 中了多种操作和控制功能 ,也是汽车内部操控与装饰 的核 晒试验相 关性研究fJ】.第七届 中美材料环境腐蚀与老化试验 学术研
根据汽车仪表板制造材料的不同对其种类进行划分 ,主要包括软饰 在对汽车仪表板进行优化设计时 ,可根据默雷尔研究所指定的仪表
仪表板和硬质仪表板两种类型 ,其 中,软饰仪表板主要包括骨架 、缓 板 目视距 离 公 式 以及 Henry Dreyfns标 准 对其 其 目视 距 离 进行 合 理
冲层和表层 等几个构成部分 ,而且 ,不同构成 部分所选用 的材料 也 确定 。按照 中国人身材的基本特征 ,结合汽车仪表板 的优化设计经
随着 近 年来 我 国 社会 经 济 的快 速 发展 ,我 国居 民 的汽 车 购买 能 表板潜在的盲 区等问题进行适 当安排 ,并在操作者看得准确且最容
力 和 汽 车保 有 量也 呈 现 出 了快 速 增 长 的趋 势 ,各 个 汽 车 生 产企 业 所 易看到的部位 安装仪表板 。在对 汽车仪表板的盲区进行 合理安排
存 在一定 的差异 ,ABS/PVC合金 、PP 聚丙烯塑料 、PU 聚氨 酯等 均 验 ,本 文对 汽 车仪 表 板 的 目视距 离 设 定 为 460r am至 710r am 之 间 ,
为其 常 用 的制 造 材 料 ,且 主要 应 用 于轿 车 等 家 庭 用 车 的设 计 和 制造 其 中 ,最 佳仪 表 板 目视 距 离 为 550r am。
仪表台成型工艺简介
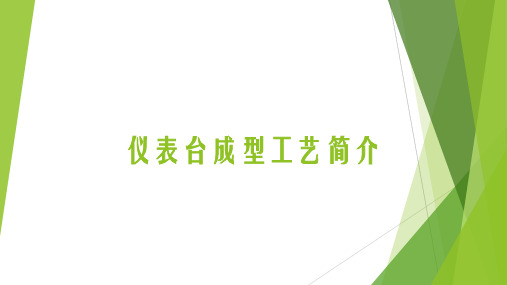
1.06 80~85 6 350 42
(TPU)
四、仪表板表皮的阴模吸塑成型
阴模吸塑成型技术是阳模真空吸塑与搪塑技术的有机结合,它是一种热模成型技术, 即将不带皮纹的热片材(0.8mm TPO表皮+2.0mm泡沬)放置在发泡层与阴模的型腔之间, 通过真空吸附使片材与模具型腔(模具型腔已做出了皮纹)接触成型。冷却时片材收缩, 并与发泡层吸附贴合成型。与传统的成型和复合工艺相比,该工艺不会出现皮纹拉伸现象, 而且可以在一个零件上实现不同的皮纹形式,皮纹均匀、清晰且手感好,与搪塑效果相当。
搪塑表皮一般具有如下优点:由于搪塑表皮的表面花纹是在表皮成型过程中形成的, 因此花纹表面的一致性好;在产品设计上,只要照顾到模具的局部加热性,即可将模具做 成较深的凹陷,甚至做成一定的负角,以加大产品造型设计的裕度;材料成本相对较低。 其缺点是:模具投资大,寿命短(一般模具的质量保证只有20000次表皮寿命);设备投 资大;需要不断地清理模具,导致辅助工时较长。
聚氨酯喷涂仪表板的工艺流程为:注塑成型仪表板骨架→PU喷涂→发泡层 发泡→切割孔和边→焊接主要零件(如需要)→组装相关零件。(高端车型采 用)
一、仪表板的注塑成型
对于全塑的硬质仪表板和发泡仪表板而言,其骨架的注塑成型一般需要使用锁模 力为2000~3000T的注塑机,骨架材料可以采用PC/ABS、SMA或PP+GF,下表对这3 种材料的成型性、成本和使用性能做了比较。片材切割阳模吸塑源自型三、仪表板表皮的搪塑成型
搪塑表皮的制造过程是:首先将带有表面花纹的搪塑模具加热到搪塑表皮的成 型温度,然后将粉箱与搪塑模扣合,使之按设定的程序旋转。当粉料熔化并粘附 于模具表面达到一定厚度后,脱开粉箱。接着,继续加热模具外表面,以使模具 内表面的搪塑表皮得到塑化烧结。最后,快速冷却模具外表面(不喷淋),使表 皮冷却成型。
汽车仪表板结构设计
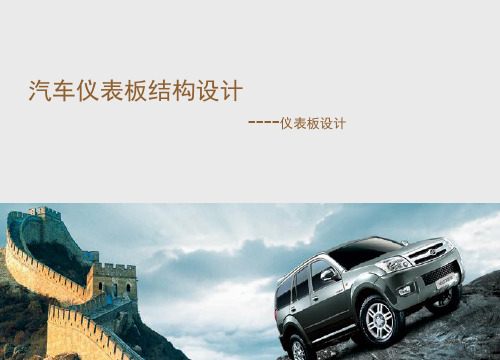
(1)硬塑仪表板 由树脂材料一次注塑成型,具有成本低,质量轻的特点,常用材料有:改性PP、ABS 等,仪表板材料要求耐热、耐湿且刚性好、不易变形。 (2)软化仪表板
是由表皮,软化层、骨架构成 ★ 表皮材料多为为PVC或ABS材料 ★ 软化层材料多为PUR或PE发泡材料 ★ 骨架为硬纸板、木纤维构成
行协调之后确定
表一
15
(5)仪表罩上端界线的确定
• 仪表罩上端界线的确定原则 • 汽车标准对各类汽车的前视野都有规定如:在设计中对汽车下视角不小于
12° • 国标规定:(长头车盲区应小于6米、平头车盲区应小于4米),因此在仪表板
整体布置中,首先在确定仪表位置及仪表罩高度时,要保证其不得越过下视角 的边界线,(驾驶员的视线处于最佳下视角30°)范围内。见(图4)
驾驶员的视线处于最佳下视角30°范围内。见(图3)
图3
14
(4)仪表板的目视距离
• 仪表板的目视距离确定见(表一) • 参考美国Hen-ry Dreyfus的推荐值即最大视距为711mm,最佳视距 • 550mm • 另外还可参考英国默雷尔推荐的视距计算公式:2D±1.2-1.5L • 式中;D=最佳读取距离 L=仪表板外廓长度 • 在实际的设计中上述参数的确定不是孤立的,是需要通过综合平衡,进
6
• 4.工程设计 • 1)零件图、总成图、装置图设计、明细表编写 • 1)二次设计图的承认(厂家图) • 5.试制样件 • (RP)试制试装验证 • 6.零部件试验 • 1)可开启件及翻转件的寿命试验 • 2)塑料件的耐冲击、抗老化、高低温耐久试验 • 3)模拟实车震动噪声试验 • 4)红外光照试验 • 5)气候变化试验(冷热交变) • 7.整车道路试验 • 主观感觉评价及震动指标(2万公里可靠性试验)
浅谈汽车硬质仪表板乘员侧气囊框设计

0引言随着汽车技术的不断发展以及消费者安全意识的不断提升,消费者对汽车的要求逐渐从汽车的性能与美观方面转移至汽车乘驾安全方面。
汽车发生正面碰撞事故时,乘员侧安全气囊可防止乘客与仪表板发生撞击而受伤。
乘员侧气囊框作为乘员侧安全气囊的安装载体,其布置和设计对安全气囊的正常起爆至关重要。
本文就气囊框的人机工程、结构设计及定位设计进行了分析与介绍。
1气囊框简介1.1乘员侧气囊区域结构乘员侧气囊区域结构由仪表板本体、气囊框、气囊构成,工艺流程如下:①仪表板骨架弱化;②仪表板骨架与气囊框焊接;③仪表板总成、仪表板横梁总成与气囊总装装配。
1.2气囊框分类按气囊框的开启方式可将气囊框分为“H ”型气囊框和“U 型”气囊框,见表1。
2人机工程乘员侧气囊区域基本参考尺寸见图1、图2和表2。
3结构设计3.1弱化线设计3.1.1弱化线位置仪表板弱化工艺主要有激光弱化和铣刀弱化两种,其中弱化线位置非常重要,对起爆结果有很大影响,综合各项目的试验结果,弱化线应选择在气囊框内壁外延1mm 的位置,如图3所示。
3.1.2弱化线圆角弱化线圆角过小会导致气囊起爆时不按预设位置展开,所以圆角设计应适当加大。
激光弱化时圆角R ≥8mm ,铣刀弱化时圆角R=18mm ,弱化线圆角见图4。
浅谈汽车硬质仪表板乘员侧气囊框设计陈文彬(江西昌河汽车有限责任公司,景德镇333002)摘要:本文通过对汽车硬质仪表板乘员侧气囊框的分类、人机工程、结构设计、定位设计等方面进行探讨,为后续新开发车型硬质仪表板乘员侧气囊框的设计开发及结构分析优化提供参考。
关键词:气囊框;人机工程;结构设计序号类型示意图优点缺点1H 型气囊框与前风挡距离要求低,易于布置气囊框向人侧展开,安全系数低2U 型气囊框气囊框向车前方向展开,安全系数高与前风挡距离近,布置要求高表1气囊框分类图1气囊区域布置示意图一图2气囊区域布置示意图二Internal Combustion Engine &Parts表2气囊区域的基本参考尺寸序号校核项尺寸A B C D E F G H I JPAB 盖板爆破后与前挡玻璃的安全间隙PAB 盖板沿爆破角度方向上的顶端点至挡风玻璃内侧的间隙PAB 盖板的撕裂线点在Z 向上于挡风玻璃的内侧间隙PAB 爆破方向与挡风玻璃的夹角PAB 的布置角度沿爆破角度方向上的顶端点至PAB 的爆破面的安全距离PAB 中心与转向支撑中心的偏移量PAB 的爆破中心点与转向支撑的中心点之间的距离PAB 与转向支撑的安全间隙PAB 的爆破方向与仪表板的夹角>10mm >300mm >150mm <37°20°~30°>20mm <20mm 50mm ~70mm >20mm 80°~100°3.1.3弱化线深度弱化线深度设计原则为:按照气囊展开顺序,从“人侧-两侧-铰链侧”,弱化线深度逐渐减小,形成梯度,便于气囊从薄弱处展开;弱化深度不宜过深,过深会导致外观会有印痕,残余厚度应大于0.12mm 。
汽车仪表板包覆工艺应用分析

汽车仪表板包覆工艺应用分析摘要:随着近年来我国社会经济的快速发展,我国居民的汽车购买能力和汽车保有量也呈现出了快速增长的趋势,各个汽车生产企业所面临的市场竞争也日趋激烈,因此,为了进一步提高其自身的市场竞争能力,汽车生产和销售企业不仅要在配套服务、售后和营销策略等方面改进服务质量,提升品牌价值,汽车的设计和制造工艺也逐步成为了产品差异化研究的主要方向,并主要表现为汽车的品牌形象和个性化设计两个方面。
仪表板是汽车设计和生产工艺中的重要环节,也是一个集装饰性、舒适性、功能性和安全性等功能于一身的核心部件,本文简单的介绍了汽车仪表板的分类和性能要求及包覆工艺。
关键词:汽车;仪表板;包覆工艺前言:随着我国居民生活水平和质量的逐步提高,人们对于汽车的需求量也在进一步增加,且其对于汽车仪表板的认识也由传统的基础性作用和功能逐步扩展到了对于舒适性、可靠性、安全性等方面的需求,在仪表板的设计方面也需要满足人们举目必望、伸手可及的需要,同时,还应注重仪表板色调、色泽、手感、操控便捷性、观察视野等方面的改善。
1、汽车仪表板的分类和性能要求1.1 汽车仪表板类型的划分根据汽车仪表板结构功能的不同,可将其划分为不同的种类,根据汽车仪表板制造材料的不同对其种类进行划分,主要包括软饰仪表板和硬质仪表板两种类型,其中,软饰仪表板主要包括骨架、缓冲层和表层等几个构成部分,而且,不同构成部分所选用的材料也存在一定的差异,ABS/PVC 合金、PP 聚丙烯塑料、PU 聚氨酯等均为其常用的制造材料,且主要应用于轿车等家庭用车的设计和制造中。
而硬质仪表板通常为同类材料造成,且相对结构较为简单,一般情况下无需使用表皮材料,能够直接利用注塑成型等工艺进行制造,并主要应用于客车和载货汽车等的生产制造中。
同时,汽车仪表板还可利用钢板直接冲压成型焊接和涂装技术制成钢质仪表板,再将一层人造革包裹在钢质仪表板的外层,并组装为木质仪表板或是软包仪表板等。
仪表板设计规范

汽车仪表板设计方法仪表板是汽车内饰中结构最为复杂, 零部件数量最多的总成零件。
仪表板的外观质量和风格决定了客户对整车内饰的评价,它包括了许多功能性的零件, 如组合仪表、音响娱乐系统、各种电器开关、空调控制器等等零件,同时在仪表板设计上还涉及到许多安全法规的要求,如驾驶员可视区域的要求、头部撞击的要求、膝部撞击的要求等。
所以仪表板的设计有着较高的设计难度。
1、仪表板零件简介仪表板总成是汽车座舱系统(COCKPIT)的重要组成部分,它包含的零部件种类和数量要看座舱系统的具体结构和对它如何划分, 一般而言,仪表板总成由以下几部分组成:1.仪表板本体,它是座舱系统的载体和框架. 从触感上可分为硬塑仪表板和软化仪表板. 硬塑仪表板一般用于低价的家庭用车,如CORSA 仪表板和秦川仪表板。
为了提高仪表板的外观质量(大型注塑件上易产生注塑缺陷)和触感,常常在仪表板的表面喷涂软触漆。
另一类是软化的仪表板,可以通过发泡材料在表皮和骨架之间发泡,或是将带有泡沫背基的表皮复合到仪表板骨架上来达到软化的效果。
第一种方式可以制造形状复杂的仪表板,外观和触感较好,但模具、设备的投入较大;第二种方式只适应于较平坦的仪表板, 泡沫的背基一般为3-4 毫米, 但工艺简单,投入较少.2.各种电器仪表、开关及音响娱乐系统。
这些都是一些功能性的零件,如组合仪表、车灯开关、收音机、保险盒、继电器盒等3.通风系统,主要由空调机、空调控制器、各种风道和出风口组成,提供汽车除霜除雾功能及车内环境温度控制。
4.副驾驶侧安全气囊, 它是现代汽车必备的安全设备,通常气囊系统由气体发生器、气袋、安装金属框架、气囊导向框架和气囊盖板组成。
现流行没有气囊盖板的气囊,它是用激光切割仪表板的背面,POLO 和AUDI A6 的仪表板就是无缝气囊.5.手套箱和各种储物盒6.各种各样的装饰面板7.金属加强粱, 加强粱承受了座舱系统各个零件的载荷,包括气囊发射的动载荷及转向管柱、方向盘、收音机、组合仪表、手套箱等的静载荷. 所以COCKPIT 都有强大的加强粱。
现代汽车仪表板成型与加工工艺技术综述_1

现代汽车仪表板成型与加工工艺技术综述发布时间:2022-12-02T05:36:45.169Z 来源:《科学与技术》2022年8月第15期作者:王少杰[导读] 仪表板作为汽车内部装饰系统里面最重要的系统之一王少杰长城汽车股份有限公司河北省汽车技术创新中心河北保定 071000摘要:仪表板作为汽车内部装饰系统里面最重要的系统之一,它非常复杂、零件非常多的内部结构以及人们对于汽车内部装饰的舒适、美观、功能、安全等的要求推动着汽车工程师们加深对于汽车仪表板的成型工艺、加工工艺等的研究和开发,从而生产不同级别不同配置不同功能的车型以满足人们的不同需求。
本文通过对仪表板的成型工艺、加工工艺、表面装饰工艺这三个方面技术进行阐述分析,以期望为进一步推动现代汽车的仪表板内部装饰添砖加瓦。
关键词:汽车仪表板成型加工工艺技术一、引言在汽车行业快速发展的大趋势下,汽车购买者对汽车内部装饰的要求也越来也多,渐渐不满足于最开始简单的内部装饰,而是期望更美观舒适、功能多样化的内部装饰环境。
而在汽车里面仪表板是位于驾驶员的正前方,其主要配件有行驶、车速里程表、发动机转速表等等,是汽车内部装饰的重要组成部分,因此仪表板的成型、加工、表面装饰等也随着汽车行业的发展以及不同群体的汽车购买者的不同购买需求而日渐发展成熟,一起推动着工艺技术的不断前进。
二、仪表板成型生产工艺汽车仪表板根据触感不同,分为硬质仪表板、软质仪表板以及半硬质仪表板三种。
硬质仪表板是指仪表板上体直接注射成型的单层结构仪表板,表面触感较硬,常采用改性聚丙烯材料作为基材。
采用注塑成型的工艺既简单又成熟,因此普遍应用于经济型车型。
软质仪表板除仪表板骨架之外,还带有表皮和泡沫填充层结构,外观触感较软富有弹性、表面光泽度较低、很好地提升整个仪表板的质感和品位,软质仪表板成型过程涉及搪塑、发泡、焊接等多个复杂工艺技术,成本较高,多用于中高档车型;同时随着购车者对品质的日渐提升,经济型车辆也开始陆续采用软质仪表板。
内饰常用材料介绍

内饰常用材料介绍内饰是指车辆内部装饰的各种材料,包括座椅、仪表盘、门板、中控台等。
车辆内饰材料的选择有着重要的安全性、舒适性和美观性的考虑。
一、座椅材料1.真皮:真皮是目前高端汽车内饰座椅常用的材料。
它具有质地柔软、透气性好、舒适性高的特点,同时也很耐磨损。
真皮的颜色和纹理多样,可以提供丰富的选择。
2.人造革:人造革是一种以合成纤维为原料制成的仿真皮革材料,它的外观和手感与真皮相似。
人造革相对便宜,易于维护和清洁,但持久性和透气性较真皮差一些。
3.织物:织物座椅是许多经济型车辆常用的材料。
它具有多样的颜色和图案选择,透气性好,对皮肤较友好。
但是,织物座椅相对容易染色和清洁困难。
二、仪表盘材料1.汽车级塑料:汽车仪表盘主要由汽车级塑料制成。
这种材料具有较好的耐候性和抗老化能力。
同时,汽车级塑料可以根据设计者的需要进行颜色和纹理的调整,从而提供多样化的选择。
2.仿木纹饰板:仿木纹饰板可以给车载仪表盘带来高级和豪华的感觉。
它的使用大大提升了车内的档次感。
现代仿木纹饰板采用了高分子材料,不仅外观逼真,而且具有较好的耐磨性和耐污性。
三、门板材料1.软质材料:车门中部通常使用软质材料进行装饰,它可以有效地降低碰撞时的冲击力。
同时,软质材料可以有效减少噪音和振动,提升乘坐舒适性。
2.硬质材料:门板的外部通常使用硬质材料进行装饰,比如塑料、铝合金等。
这些材料具有足够的强度和刚性,能够提供一定的保护,还具有较好的耐磨性和耐腐蚀性。
四、中控台材料1.高级塑料:中控台主要使用高级塑料进行装饰,这种塑料不仅具有良好的耐用性和耐高温性,而且外观质感较好,可以呈现出金属的质感和光泽。
2.金属材料:中控台还常常使用金属材料进行装饰,如铝合金、不锈钢等。
金属材料可以提供豪华感和稳重感,同时还具有耐磨性和耐腐蚀性。
总体来说,车辆内饰材料的选择需要考虑安全性、舒适性和美观性。
车辆制造商通常会根据车型定位、价格定位和消费者需求来选择不同的内饰材料。
仪器仪表包装通用技术条件

仪器仪表包装通用技术要求一、一般要求1、产品包装应根据产品的性质、外形和尺寸、储存装卸条件和用户的要求进行设计,达到包装紧凑、防护周密、结构合理、安全可靠、美观试销的要求。
2、在正常的储运装卸条件下,应保证产品自制造厂发货之日起至少一年,不致因包装不善而引起产品损坏、散失、锈蚀、长霉和降低性能等。
3、重量大于200㎏的包装件应作起吊试验。
4、运输中允许堆码的包装件应作堆码试验。
5、包装件外形尺寸和重量应符合国外运输方面有关超限、超重的规定,其中硬质直方体运输包装件的尺寸应符合GB4892的规定二、包装材料要求选用的包装材料不应引起产品的表面色泽改变或腐蚀,亦不应由于包装材料变形二引起产品损坏,1、木材包装用木材质量应符合GB153及GB4817的规定,其中滑木、枕木、框架木及内包装板选用一等材,外包装板选用二等材。
2、瓦楞纸板包装用瓦楞纸板应符合GB6544的规定。
出口产品包装用瓦楞纸板应符合GB5034的规定。
3、胶合板包装用胶合板应符合GB1349和GB738的规定。
4、纤维板包装用的纤维板应符合GB1923的规定5、刨花板包装用的刨花板应符合GB4897的规定6、纸板包装用纸板含水率为8%-14%7、菱镁硅包装用菱镁硅应符合GB13041的规定。
8、钙塑瓦楞板包装用钙塑瓦楞板应符合GB6980的规定。
9、发泡塑料制作内包装用发泡塑料,其含水率不应大于4%10、竹编胶合板竹编胶合板应符合GB1 3123的规定。
11、其它材料在能满足储运、装卸要求的情况下允许采用其他包装材料,例如铝塑复合薄膜PP复合低泡塑料薄膜等。
三、制箱要求(一)木箱1、普通木箱普通木箱应符合GB 12464的规定。
2、框架木箱框架木箱应符合GB 7284的规定。
3、滑木箱滑木箱应符合GB/T 13384的有关规定。
(二)瓦楞纸箱瓦楞纸箱应符合GB 6543的规定。
出口产品包装用瓦楞纸箱应符合GB 5033的规定。
(三)胶合板、纤维板箱胶合板、纤维板箱应符合GB/T 13384的规定。
WSS-M15P4-F_产品试验大纲 中文版解析

硬质彩色成型内饰总成性能WSS-M15P4-F1、范围该规范对硬质彩色成型内饰板、嵌条、顶臵及落地控制台以及由各种材料组合而成、有装饰和/或功能特性的装饰总成,如硬质仪表板的最低耐用性及性能要求作了明确规定。
2、应用该规范原发放适用对象为塑料内饰件如门板、中央及顶臵控制台、四分之一面板、A-、B-、C-、D-柱嵌条、硬质仪表板、仪表板零部件和装饰条。
除非福特工程部另有规定,否则应按照表1中的详细规定进行测试。
除非零件几何形状不允许,否则测试应在零件上进行。
在这种情况下,可使用带有产品皮纹和颜色的合适的饰板。
试样量和所需测试见表1。
2.1 适用范围软仪表板、内饰软板及包层件(WSS-M15P45-B)、后臵物板(WSS-M15P6-D)、方向盘(WSS-98P12-A)、车顶内衬(WSS-M15P27-F)、铺有地毯的本体(WSS-M8P16-A)、模压肘靠和头枕(WSS-M15P39-A)、贴花(WSS-M15P34-C1/C2)、遮阳板(WSS-M98P3-B)、内饰涂装零部件(WSS-M2P188-A1)、镀铬零部件(WSS-M1P83-C1/D2/D3)和内饰弹性体(WSS-M9P8-B)的性能另有规定,未含在该规范中。
3、要求3.1 生产用材料标准要求材料供应商及零件制造商必须符合福特公司生产用材料标准要求(WSS-M99P1111-A)。
该规范以原始材料为基础,但只要技术可行且符合福特材料工程部规定的所有材料及PV测试要求,就应使用WSS-M99P42-A中规定的含有回收成分的材料(消费后和/或工业后回收物以及再聚合回收材料)。
出于经济/环境因素考虑,如符合WSS-M99P1111-A中的规定,允许使用再研磨料。
3.2 外观3.2.1 用人工照明配色(FLTM BI 109-01,目测)颜色、图案与表面处理应与已批准的设计中心标准样板一致或按照工程文件上的规定。
3.2.2 光泽度(FLTM BI 110-01)按照工程文件上的规定。
仪表板设计规范

XXXXX有限公司仪表板板设计规范编制:日期:校对:日期:审核:日期:批准:日期:发布实施XXXXX有限公司发布目录1 简要说明1.1仪表板知识简要说明1.2仪表板的分类1.3仪表板的加工工艺简介1.4仪表板零件构成图1.5仪表板的开发流程介绍2 设计构想(思想、理念)2.1设计思路2.2拔模方向确定2.3目标市场特殊要求2.4仪表板总成安装方式的选择2.5售后服务便利性的分析2.6间隙面差的初步定义2.7其他标识的设计要求3 仪表板的典型截面分析3.1典型截面简介3.2固定点的分布3.3仪表的视野校核及仪表罩边界条件的确认3.4仪表板和前风挡的配合截面3.5前除霜风口的布置3.6前除霜风管的布置3.7侧除霜风口的布置3.8侧除霜风管的布置3.9空调出风口的布置3.10空调出风管的布置3.11扬声器面罩的布置3.12仪表板和A柱护板的布置3.13 烟灰缸的布置3.14 手套箱的布置3.15 无缝气囊(PAB)的布置3.16 杯托的布置3.17 驾驶员腿部空间的布置3.18 中间面板的布置3.19 换挡手柄的布置3.20 手刹手柄的布置3.21 副仪表板扶手的布置3.22 搪塑仪表板特殊的布置要求3.23组合开关护罩的布置4 仪表板三维数据的设计4.1 材料的详细说明4.2 加强筋的分布4.3 圆角半径的分析4.4 整体强度的分析4.5 装配的注意事项4.6 模具周期的分析5 造型与工程的关系5.1 工程对造型的要求5.2 造型配合工程的设计分析6法规6.1头部碰撞与内部突出物校核6.2 内部突出物的分析6.3 膝盖碰撞的分析7 成本7.1 减少成本的一般措施8一般注意事项8.1 重要特征描述8.2 其他要求(比如生产程序的要求等)9 图纸模式9.1 尺寸公差9.2 技术要求10 仪表板常用的标准简介10.1 仪表板采用的材料标准代号10.2 仪表板产品标准代号10.3 仪表板系统所涉及到的国标代号1 简要说明1.1仪表板知识简要说明仪表板是汽车中非常独特的部件,集安全性、功能性、舒适性与装饰性于一身。
仪表板设计规范标准[详]
![仪表板设计规范标准[详]](https://img.taocdn.com/s3/m/dfc0025b81c758f5f61f67c3.png)
汽车仪表板设计方法仪表板是汽车饰中结构最为复杂 , 零部件数量最多的总成零件。
仪表板的外观质量和风格决定了客户对整车饰的评价,它包括了许多功能性的零件,如组合仪表、音响娱乐系统、各种电器开关、空调控制器等等零件,同时在仪表板设计上还涉及到许多安全法规的要求,如驾驶员可视区域的要求、头部撞击的要求、膝部撞击的要求等。
所以仪表板的设计有着较高的设计难度。
1、仪表板零件简介仪表板总成是汽车座舱系统(COCKPIT) 的重要组成部分,它包含的零部件种类和数量要看座舱系统的具体结构和对它如何划分,一般而言,仪表板总成由以下几部分组成:1.仪表板本体,它是座舱系统的载体和框架。
从触感上可分为硬塑仪表板和软化仪表板。
硬塑仪表板一般用于低价的家庭用车,如CORSA 仪表板和川仪表板。
为了提高仪表板的外观质量(大型注塑件上易产生注塑缺陷)和触感,常常在仪表板的表面喷涂软触漆。
另一类是软化的仪表板,可以通过发泡材料在表皮和骨架之间发泡,或是将带有泡沫背基的表皮复合到仪表板骨架上来达到软化的效果。
第一种方式可以制造形状复杂的仪表板,外观和触感较好,但模具、设备的投入较大;第二种方式只适应于较平坦的仪表板,泡沫的背基一般为3-4 毫米,但工艺简单,投入较少。
2.各种电器仪表、开关及音响娱乐系统。
这些都是一些功能性的零件,如组合仪表、车灯开关、收音机、保险盒、继电器盒等3.通风系统,主要由空调机、空调控制器、各种风道和出风口组成,提供汽车除霜除雾功能及车环境温度控制。
4.副驾驶侧安全气囊,它是现代汽车必备的安全设备,通常气囊系统由气体发生器、气袋、安装金属框架、气囊导向框架和气囊盖板组成。
现流行没有气囊盖板的气囊,它是用激光切割仪表板的背面,POLO 和AUDI A6 的仪表板就是无缝气囊。
5.手套箱和各种储物盒6.各种各样的装饰面板7.金属加强粱,加强粱承受了座舱系统各个零件的载荷,包括气囊发射的动载荷及转向管柱、方向盘、收音机、组合仪表、手套箱等的静载荷。
基于硬质仪表板无缝PAB的布置及设计蒋明良

基于硬质仪表板无缝PAB的布置及设计蒋明良发布时间:2021-09-09T08:34:31.030Z 来源:《中国科技人才》2021年第17期作者:蒋明良[导读] 随着人们对汽车安全性、美观性和舒适性要求的提高,无缝PAB仪表板(又称整体式安全气囊仪表板,气囊盖为隐藏式)已成为越来越多中高级车型的首选。
本文介绍硬质仪表板上无缝PAB的布置及设计的要求,给布置、设计无缝PAB提供技术参考,在仪表板设计中应加以充分注意。
柳州市翼墨汽车技术服务有限公司广西柳州 545006摘要:随着人们对汽车安全性、美观性和舒适性要求的提高,无缝PAB仪表板(又称整体式安全气囊仪表板,气囊盖为隐藏式)已成为越来越多中高级车型的首选。
本文介绍硬质仪表板上无缝PAB的布置及设计的要求,给布置、设计无缝PAB提供技术参考,在仪表板设计中应加以充分注意。
关键词:仪表板;PAB;设计Abstract: As people on car safety, aesthetics and comfort requirements, seamless PAB dashboard (also known as monolithic airbag dashboard, airbag cover for hidden) has become more and more advanced models of choice. In this paper, the hard plastic on the dashboard of seamless PAB decorate and design requirements, to provide technical reference to the layout, design of seamless PAB, in the dashboard design should be sufficient attention.Key words: IP; PAB; Design0 引言传统的PAB(乘员安全气囊)一般设计为有缝气囊(如图1所示),有缝气囊盖虽然成本低、工艺结构简单、拆装方便,但其缺点为气囊盖板与仪表板匹配处存在目视可见的装接线。
WSS-M15P4-F_产品试验大纲 中文版解析

硬质彩色成型内饰总成性能WSS-M15P4-F1、范围该规范对硬质彩色成型内饰板、嵌条、顶臵及落地控制台以及由各种材料组合而成、有装饰和/或功能特性的装饰总成,如硬质仪表板的最低耐用性及性能要求作了明确规定。
2、应用该规范原发放适用对象为塑料内饰件如门板、中央及顶臵控制台、四分之一面板、A-、B-、C-、D-柱嵌条、硬质仪表板、仪表板零部件和装饰条。
除非福特工程部另有规定,否则应按照表1中的详细规定进行测试。
除非零件几何形状不允许,否则测试应在零件上进行。
在这种情况下,可使用带有产品皮纹和颜色的合适的饰板。
试样量和所需测试见表1。
2.1 适用范围软仪表板、内饰软板及包层件(WSS-M15P45-B)、后臵物板(WSS-M15P6-D)、方向盘(WSS-98P12-A)、车顶内衬(WSS-M15P27-F)、铺有地毯的本体(WSS-M8P16-A)、模压肘靠和头枕(WSS-M15P39-A)、贴花(WSS-M15P34-C1/C2)、遮阳板(WSS-M98P3-B)、内饰涂装零部件(WSS-M2P188-A1)、镀铬零部件(WSS-M1P83-C1/D2/D3)和内饰弹性体(WSS-M9P8-B)的性能另有规定,未含在该规范中。
3、要求3.1 生产用材料标准要求材料供应商及零件制造商必须符合福特公司生产用材料标准要求(WSS-M99P1111-A)。
该规范以原始材料为基础,但只要技术可行且符合福特材料工程部规定的所有材料及PV测试要求,就应使用WSS-M99P42-A中规定的含有回收成分的材料(消费后和/或工业后回收物以及再聚合回收材料)。
出于经济/环境因素考虑,如符合WSS-M99P1111-A中的规定,允许使用再研磨料。
3.2 外观3.2.1 用人工照明配色(FLTM BI 109-01,目测)颜色、图案与表面处理应与已批准的设计中心标准样板一致或按照工程文件上的规定。
3.2.2 光泽度(FLTM BI 110-01)按照工程文件上的规定。
- 1、下载文档前请自行甄别文档内容的完整性,平台不提供额外的编辑、内容补充、找答案等附加服务。
- 2、"仅部分预览"的文档,不可在线预览部分如存在完整性等问题,可反馈申请退款(可完整预览的文档不适用该条件!)。
- 3、如文档侵犯您的权益,请联系客服反馈,我们会尽快为您处理(人工客服工作时间:9:00-18:30)。
ELV
铅:<0.1%
汞:<0.1%
六价铬:<0.1%
多溴联苯<:0.1%
多溴二苯醚:<0.1%
镉:<0.01%
Q/JQ 110112-2011
100mm×100mm数量3
5零件总成性能
仪表板总成:包括仪表板总成(本体骨架、仪表板上体总成、仪表板下体总成、左/右除霜面板总成、中央下护板总成、副驾驶侧下面板总成、驾驶侧下面板总成、左/右端盖)等等。
1A型原始标距50mm 5件
3
断裂延伸率
≥500%
GB/T 1040.2-2006,试验速度50mm/min
ISO527-21A样条5件
4
弯曲强度
≥23MPa
GB/T 9341-2008,试验速度2mm/min
80mm×10mm×4mm5件
5
弯曲模量
≥950MPa
GB/T 9341-2008,试验速度2mm/min
80mm×10mm×4mm5件
7
耐热性
零件不得出现脆变,也不得在形状、颜色和表面上出现明显的变化
110℃24h
产品1件
8
高温老化试验
表面没有结构变化,即聚丙烯没有典型的分解
150℃200h
产品1件
9
耐晒色牢度
与供货状态相比,被照射过的表面不得出现色变、裂纹和粉化等变化
照光要求:黑色标准温度(100±3)0C;试样室温度(65±3)0C;试样室相对空气湿度(20±10)%;照射强度(300~400nm)60W/m2,一般达到以下照射量,视为照光周期的结束点,α型氙光仪=10MJ/m2(300~400nm)一次照光周期
10
耐寒性能
在低温下成品件必须仍保持功能,不允许出现裂纹或类似的破坏
存放温度:(-40±2)℃存放时间;(22+2)小时
成品1件
11
落球试验
没有断裂,无裂纹
—400C/24h后按PV3905落球高度(40±0.5)cm
成品2件
12
阻燃性D
≤100mm/min
GB8410-2006
356×70×厚度5件
将零件置于(105±2)℃/500h恒温箱中,安装状态。完成后目测判定
总成1套
4
气候交变试验
外观要求同上
1个周期12小时,从室温用2小时升至80℃×80%RH,保持4小时,用2小时降至-40℃,保持4小时,再用2小时升至80℃×80%RH,共进行12个周期,安装状态。
总成1套
5
低温存放
不允许出现相对于供货状态的可见变化,比如,裂缝,变形,开裂,轮廓和弧度的挠曲,变色,光泽度改变等现象。
ISO 868,5秒钟,邵氏A
产品取样
4
抗拉强度
≥ 7N/mm2
ASTM D638 Ⅰ型样条,拉伸速度100mm/min。
产品取样
5
抗拉延伸率
≥200%
同上
产品取样
6
撕破力
≥35N/mm
DIN53515,速度500mm/min。
产品取样
7
耐热性
在进行110oC温度下存放500小时后在环境温度下存放2小时.然后进行以下试验
在室温中暖和后也不能出现裂纹或其它损害.
将零件置于温度(-40±1)℃、存放时间(22±2)h
总成1套
6
落球试验
表皮或泡沫无破裂或裂缝
试样在温度(-20±1)℃下存放(22±2)h后,牢固地安放在指定的位置上,用直径为φ50.0±0.5 mm重量为(500±5)g不锈钢球,从230 mm高度垂直落下冲击零件表面,目测判定。
Q/JQ 110112-2011
100mm×100mm数量3
PVC:一般为仪表板上体表皮的材料,具体性能如下:
序号
试验项目
标准
试验标准/方法
样品数量
1
密度
1.1+0.2/-0.1 g/cm3
DIN EN ISO1183-1
产品取样
2
灼烧残余
重量最大4%
DIN EN ISO1172
产品取样
3
硬度
75±10(Shore A)
前 言
本标准是公司产品企业标准之一。
本标准为公司统一执行的企业标准。
为了保证仪表板的性能,根据产品设计开发控制程序的要求,结合试验室编制的XCH-BZ-SY-001《汽车硬质仪表板技术标准》技术标准。本标准修改采用了部分相关国标和行业标准的内容。
本标准由试验中心提出,由试验中心主任批准。
本标准由试验中心技术主管负责标准化审核及归口管理。本标准起草部门:试验中心。
本标准主要起草人:
本标准的参与起草人:。
本标准于 2014年1月30日首次批准发布,2014 年 03月 01 日实施。
1
为了保证汽车仪表板的性能,本标准规定了硬质仪表板系统性能评价规范。
本规范适用于公司各硬质仪表板系统。
2规范性引用文件
下列文件中的条款通过本标准的引用而成为本标准的条款。凡是注日期的引用文件,其随后所有的修改单(不包括勘误的内容)或修订版均不适用于本标准,然而,鼓励根据本标准达成协议的各方研究是否可使用这些文件的最新版本。凡是不注日期的引用文件,其最新版本适用于本标准。
产品取样
9.1
颜色的变化
灰色标度等级4级以上
5个周期后,样品按EN 20105-A02鉴定灰色标度等级,
10
耐磨性
100此行程,按DIN EN ISO 105-A03评价表面沾色。
产品取样
10.1
干态
≥4级
10.2
湿态
≥4级Leabharlann 11气味性C1≤3.0级;
C2≤3.5级;
C3≤4.0级
C11L容器内放置50ml蒸馏水,存放(23±2)℃,存放时间(24±1)h;
GB/T8410-2006《内饰阻燃性能》
QC/T15-92《汽车塑料制品通用试验方法》
3
仪表板
本规范中所述的仪表板
4 材料性能
PC+ABS:一般应用在仪表板上体骨架以及各种需要喷漆或电镀的饰条上,具体的性能要求如下:
序号
试验项目
标准
试验标准/方法
样品数量
1
密度
1.12±0.01g/cm³
DIN EN ISO 1183-1
13
热变形温度℃
≥105
GB/T 1634.2-2004,侧放
120mm×10mm×4mm2件
14
VOC有害物质散发
符合本标准条款6.1
按本标准条款6.2进行
100mm×100mm数量3
15
ELV
铅:<0.1%
汞:<0.1%
六价铬:<0.1%
多溴联苯<:0.1%
多溴二苯醚:<0.1%
镉:<0.01%
10mm×10mm5件
2
弯曲强度
≥65MPa
GB/T 9341-2008,试验速度2mm/min
80mm×10mm×4mm5件
3
缺口冲击强度
≥20KJ/m2
GB/T 1843-2008,冲击能量5.5J
80×10×4mm1/3厚度缺口5件
4
热变形温度
≥120℃
GB/T 1634.2-2004,侧放
120mm×10mm×4mm2件
产品取样
8
耐热性存放后的延伸率
≥180%
ASTM D638 Ⅰ型样条,拉伸速度100mm/min。
8.2
颜色的变化
灰色标度等级4级以上
按DIN EN 20105-A02评价。
8.3
其他的变化
没有光泽改变,裂纹等现象.
目测
9
耐光照性
没有渗出,变暗,颜色改变,光泽改变或其他变化
照光要求:黑色标准温度(100±3)0C;试样室温度(65±3)0C;试样室相对空气湿度(20±10)%;照射强度(300~400nm)60W/m2,一般达到以下照射量,视为照光周期的结束点,α型氙光仪=10MJ/m2 (300~400nm) 一次照光周期
356×70×厚度5件
10
VOC有害物质散发
符合本标准条款6.1
按本标准条款6.2进行
100mm×100mm数量3
11
ELV
铅:<0.1%
汞:<0.1%
六价铬:<0.1%
多溴联苯<:0.1%
多溴二苯醚:<0.1%
镉:<0.01%
Q/JQ 110112-2011
100mm×100mm数量3
PP+EPDM-T25:应用在下体骨架、中央下护板、副驾驶侧下面板、手套箱灯盖板、手套箱内斗、手套箱盖板、驾驶侧下面板等仪表板的大部分区域,具体的性能见下表:
总成1套
8
饰件的耐摩擦色牢度
表面质量与批准样品相比,容许有微小的光泽变化(指用沾湿的抹布也不能清除的痕迹)。允许摩擦织物上稍许沾色。灰色标度≥(3-4)级,按GB 251-1995标准评价
按AATCC 8标准的试验方法用摩擦织物通过沾色试验仪对试样表面摩擦100次,目测判定
数量: 样品尺寸150×50mm各2件 (材料、色调相同的任选其一)
100×100mm取自产品平整部位(至少三件)
7
相对光照的色牢度
照光要求:黑色标准温度(100±3)0C;试样室温度(65±3)0C;试样室相对空气湿度(20±10)%;照射强度(300~400nm)60W/m2,一般达到以下照射量,视为照光周期的结束点,α型氙光仪=10MJ/m2(300~400nm)一次照光周期
80mm×10mm×4mm5件
6
悬臂梁缺口冲击
≥6KJ/m2
GB/T 1843-2008,冲击能量5.5J