CBN刀具在切削使用中的一些问题
数控机床刀具常见的几种故障

数控机床刀具常见的几种故障
数控机床刀具常见的几种故障包括:
1. 刀具磨损:长期使用会导致刀具磨损,影响加工质量和效率。
需要定期检查并更换磨损的刀具。
2. 刀具断裂:刀具在高速旋转和承受较大切削力时,可能会发生断裂。
这可能是由于刀具质量不好、切削参数不合适或刀具安装不正确等原因引起的。
3. 刀具卡刀:刀具在切削过程中可能会被材料卡住,无法正常工作。
这可能是由于切削参数设置不合适、材料性质异常或机床刀具夹持系统故障等原因引起的。
4. 刀具偏移:刀具在加工过程中可能出现偏移,导致加工尺寸不准确。
这可能是由于机床刚度不足、切削参数设置不合理或刀具安装不正确等原因引起的。
5. 刀具冷却不良:切削过程中,刀具需要进行冷却以降低温度和延长寿命。
如果刀具冷却不良,可能会导致刀具温度过高,影响切削效果和刀具寿命。
以上是数控机床刀具常见的几种故障。
在实际应用中,需要根据具体情况进行故障诊断和排除。
同时,定期保养和维护刀具也是预防和减少故障的重要措施。
立方氮化硼刀具(CBN刀片)资料大全
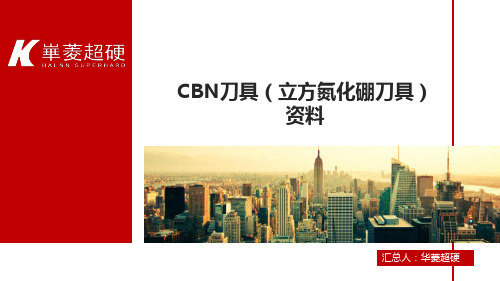
推荐刀具牌号
高硬度铸铁 (硬度:HRC3568) 硬钢 (硬度≥HRC45)
粗加工 精加工 粗加工 精加工 粗加工 精加工
BN-K1 BN-K10 BN-S10,BN-S20 BN-S200,BN-H10, BN-H11,BN-H20, BN-H21 BN-S30,BN-S300 BNK30,BN-K10
02
剥落
铣削钢和铸铁端面时,在前刀面上常出现 的贝壳状剥落。出现此类情况,可通过提 高切削速度、降低进给量,使用有负倒棱、 刃口经过钝化处理的刀片。
03
碎断
断续切削工件时常发生的破损形式,这是由 于断续切削高硬度工件时冲击载荷过大、短 时间切削后即发生的早期破损,虽然切削条 件适当,但切削较长时间后,没有及时换刀, 由于刀具材料疲劳就发生了大块的断裂。
汽 车 行 业
02
CBN刀具的应用
重载切削
高速切削
CBN刀具 的应用
以车代磨
干式切削
3
CBN刀具的切削参数
常规切削参数 华菱超硬CBN刀具切削参数 切削公式
03
CBN刀具的切削参数
常ቤተ መጻሕፍቲ ባይዱ切削参数
粗加工时,应尽量保证较高的金属切除率和必要的刀具耐用度,故一般优先选择尽可能大的切削深 度ap,其次选择较大的进给量f,最后根据刀具耐用度要求,确定合适的切削速度。精加工时,首先应 保证工件的加工精度 和表面质量要求,故一般选用较小的进给量f和切削深度ap,而尽可能选用较高 的切削速度υ c。 加工材质 硬铸铁 灰铸铁 淬火钢 耐热合金 切削速度 Vc(m/min) 70 ~ 150 400 ~ 1000 60 ~ 140 100 ~ 240 进给量 Fr(mm/r) 0.15 ~ 0.5 0.15 ~ 0.5 0.15 ~ 0.5 0.05 ~ 0.3 吃刀深度 ap(mm) 0.12 ~ 2.0 0.12 ~ 2.0 0.2 ~ 2.5 0.1 ~ 2.5
CBN刀片硬车削GCr15轴承钢表面粗糙度的切削参数优化
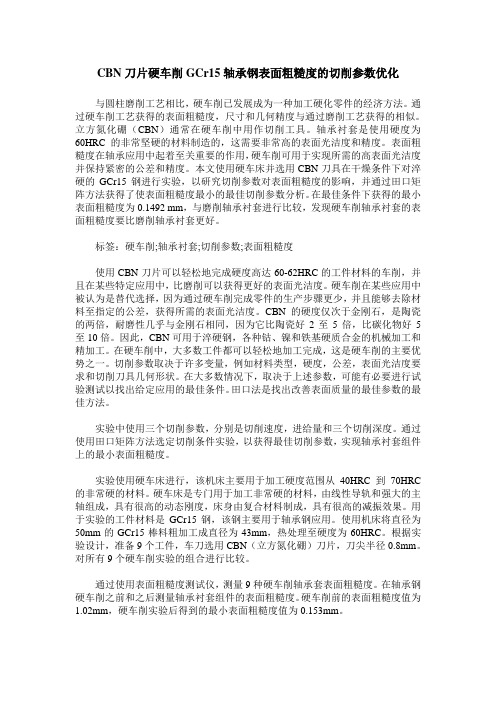
CBN刀片硬车削GCr15轴承钢表面粗糙度的切削参数优化与圆柱磨削工艺相比,硬车削已发展成为一种加工硬化零件的经济方法。
通过硬车削工艺获得的表面粗糙度,尺寸和几何精度与通过磨削工艺获得的相似。
立方氮化硼(CBN)通常在硬车削中用作切削工具。
轴承衬套是使用硬度为60HRC的非常坚硬的材料制造的,这需要非常高的表面光洁度和精度。
表面粗糙度在轴承应用中起着至关重要的作用,硬车削可用于实现所需的高表面光洁度并保持紧密的公差和精度。
本文使用硬车床并选用CBN刀具在干燥条件下对淬硬的GCr15钢进行实验,以研究切削参数对表面粗糙度的影响,并通过田口矩阵方法获得了使表面粗糙度最小的最佳切削参数分析。
在最佳条件下获得的最小表面粗糙度为0.1492 mm,与磨削轴承衬套进行比较,发现硬车削轴承衬套的表面粗糙度要比磨削轴承衬套更好。
标签:硬车削;轴承衬套;切削参数;表面粗糙度使用CBN刀片可以轻松地完成硬度高达60-62HRC的工件材料的车削,并且在某些特定应用中,比磨削可以获得更好的表面光洁度。
硬车削在某些应用中被认为是替代选择,因为通过硬车削完成零件的生产步骤更少,并且能够去除材料至指定的公差,获得所需的表面光洁度。
CBN的硬度仅次于金刚石,是陶瓷的两倍,耐磨性几乎与金刚石相同,因为它比陶瓷好2至5倍,比碳化物好5至10倍。
因此,CBN可用于淬硬钢,各种钴、镍和铁基硬质合金的机械加工和精加工。
在硬车削中,大多数工件都可以轻松地加工完成,这是硬车削的主要优势之一。
切削参数取决于许多变量,例如材料类型,硬度,公差,表面光洁度要求和切削刀具几何形状。
在大多数情况下,取决于上述参数,可能有必要进行试验测试以找出给定应用的最佳条件。
田口法是找出改善表面质量的最佳参数的最佳方法。
实验中使用三个切削参数,分别是切削速度,进给量和三个切削深度。
通过使用田口矩阵方法选定切削条件实验,以获得最佳切削参数,实现轴承衬套组件上的最小表面粗糙度。
立方氮化硼材料的CBN刀片与CBN砂轮知识

立方氮化硼材料的CBN刀片与CBN砂轮知识目前,CBN(立方氮化硼材料)常用语制作CBN刀具和CBN砂轮等切削工具和磨削工具用于加工黑色金属材料,实现高速切削和高速磨削,并对于难加工材料中广泛应用,不但提高加工效率而且大幅度提高了加工精度和尺寸公差。
目前CBN刀具的应用相当普遍,而CBN砂轮由于高速磨削磨床设备的经济性,普及面不广。
如何提高生产效率、降低制造成本,以具有竞争力的价格向客户提供高质量的产品,通过不断的努力,以及为了满足产品零件精度要求的CBN成形磨削工业应用,在设备投资、CBN磨轮制造成本和刀具使用寿命等方面均具有较好的经济性。
所以笔者相信,随着国内高速磨削的普及和高速磨床设备的技术发展,必将带来新的磨削技术革命,届时,CBN砂轮为基础的高速磨削将与CBN刀具一起成为高速加工的普遍性革命。
CBN(立方氮化硼)材料的知识CBN是立方氮化硼英文名称(CubicBoronNitride)的缩写,它是硬度仅次于金刚石的一种人工合成无机晶体材料,广泛地用于机械加工工业。
各工业发达国家都把CBN作为达到高效率、节约能源、超精密和操作自动化加工等目的的重要材料加以发展。
专家研究表明:当温度达到700℃左右时,金刚石的硬度会有较明显的下降趋势,而CBN材料仍能保持相当的硬度。
这说明CBN的热稳定性(红硬性)明显优于金刚石。
由于铁系金属高温时对碳元素有着很强的亲和作用,因此,由纯碳元素组成的金刚石不宜用作加工铁系金属的刀具材料。
而CBN由硼、氮两种元素组成,高温时不容易和铁系金属发生化学反应,CBN刀具的出现使得对淬火钢的切削成为了可能。
立方氮化硼刀具的知识PCBN是聚晶立方氮化硼英文名称(Polycrystalline Cubic Boron Nitride)的缩写。
由PCBN刀具坯料经过切割、焊接和刃磨制成的PCBN刀具具有良好的切削性能,主要表现在以下几个方面:高硬度和耐磨性CBN的硬度仅次于金刚石,对于可切削黑色金属的刀具材料来说,PCBN刀具的硬度最高。
立方氮化硼(CBN)刀具破损主要形态、原因的分析
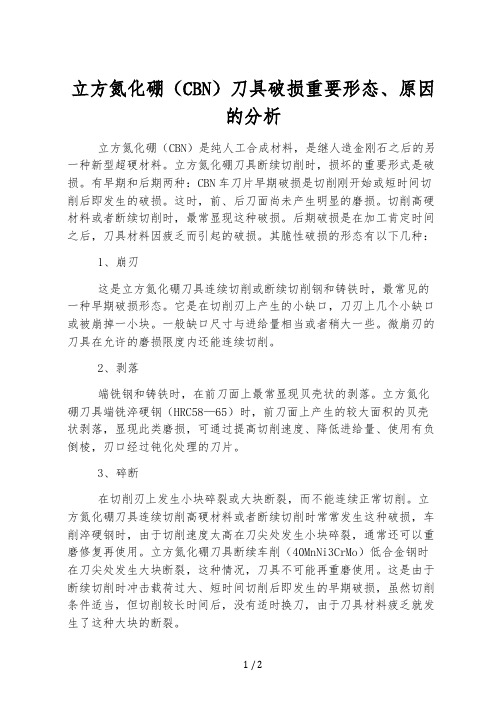
立方氮化硼(CBN)刀具破损重要形态、原因的分析立方氮化硼(CBN)是纯人工合成材料,是继人造金刚石之后的另一种新型超硬材料。
立方氮化硼刀具断续切削时,损坏的重要形式是破损。
有早期和后期两种:CBN车刀片早期破损是切削刚开始或短时间切削后即发生的破损。
这时,前、后刀面尚未产生明显的磨损。
切削高硬材料或者断续切削时,最常显现这种破损。
后期破损是在加工肯定时间之后,刀具材料因疲乏而引起的破损。
其脆性破损的形态有以下几种:1、崩刃这是立方氮化硼刀具连续切削或断续切削钢和铸铁时,最常见的一种早期破损形态。
它是在切削刃上产生的小缺口,刀刃上几个小缺口或被崩掉一小块。
一般缺口尺寸与进给量相当或者稍大一些。
微崩刃的刀具在允许的磨损限度内还能连续切削。
2、剥落端铣钢和铸铁时,在前刀面上最常显现贝壳状的剥落。
立方氮化硼刀具端铣淬硬钢(HRC58—65)时,前刀面上产生的较大面积的贝壳状剥落,显现此类磨损,可通过提高切削速度、降低进给量、使用有负倒棱,刃口经过钝化处理的刀片。
3、碎断在切削刃上发生小块碎裂或大块断裂,而不能连续正常切削。
立方氮化硼刀具连续切削高硬材料或者断续切削时常常发生这种破损,车削淬硬钢时,由于切削速度太高在刀尖处发生小块碎裂,通常还可以重磨修复再使用。
立方氮化硼刀具断续车削(40MnNi3CrMo)低合金钢时在刀尖处发生大块断裂,这种情况,刀具不可能再重磨使用。
这是由于断续切削时冲击载荷过大、短时间切削后即发生的早期破损,虽然切削条件适当,但切削较长时间后,没有适时换刀,由于刀具材料疲乏就发生了这种大块的断裂。
4、裂纹立方氮化硼刀具在较长时间的断续切削后,有因机械冲击而引起的平行于切削刃的机械疲乏裂纹,也有因热冲击而引起的垂直于或倾斜于切削刃的裂纹。
当这些裂纹不断扩展合并后,就引起刀刃碎裂或断裂。
在实际生产中,工件无论其几何形状还是材料的物理机械性能,都远不是规定和均匀的。
例如毛坯几何形状不规定、加工余量不均匀、表面硬度不均匀以及工件表面的沟、槽、孔等,全部这一切使切削加工或多或少地总带有断续切削的性质。
CBN刀具车削加工淬火钢件的切削参数范围

CBN刀具车削加工淬火钢件的切削参数范围CBN刀具车削加工淬火钢件,已经是非常普遍的一种现象,采用CBN刀具以车代磨加工淬火钢件效率成倍提高,而且干式切削,车削加工过程中不添加切削,绿色环保,更适合制造业的绿色制造。
CBN刀具虽然广泛应用于淬火钢件的车削加工,但很多工人还不太了解CBN刀具的切削参数,经常刚上去就出现崩刀、打刀现象。
主要就是不了解CBN刀具的切削参数,用硬质合金刀具的参数测试,效果不好。
小编在机械加工行业摸爬滚打了十几年,还算是有一点小心得,今天分享给大家。
在先介绍CBN刀具车削加工淬火钢件的切削参数范围之前,先来了解一下淬火钢都有哪些难加工问题。
1、淬火钢件的粗加工:车削加工淬火过的齿轮,齿圈的生产过程中,一些齿轮、齿圈淬火或渗碳淬火后,硬度一般在HRC55以上,而且变形严重,如高铁齿轮,工程机械大齿圈,重工行业用大齿圈等,这些大型齿轮齿圈淬火后变形量非常大,这就涉及到淬火钢粗加工。
同样,在模具钢生产过程中,淬火钢的粗加工也经常看到,但很多厂家采取的措施也五花八门,有的先把大余量线切割掉,有的用硬质合金刀具慢慢啃,有的用立方氮化硼(PCBN)刀具多次走刀才能完成加工,工人感慨粗加工淬火钢是有劲使不出,干着急,没办法。
2、淬火钢件的断续加工:间断切削加工一直是个难题,何况是动辄HRC60左右的淬火钢。
特别是在高速车削淬火钢时,刀具在间断车削淬火钢时会以每分钟100次以上的冲击来完成加工,对刀具的抗冲击性能是个很大的挑战。
以汽车齿轮加工为例,淬硬齿轮以车代磨已经成为一种趋势,据了解,作为齿轮产业的三大市场之一,车辆齿轮占据了齿轮市场总额的62%,其中汽车齿轮又占据了车辆齿轮市场份额的62%。
也就是说,汽车所用齿轮占有了整个齿轮市场近40%的比重,可见齿轮对于汽车产业的重要性。
虽然淬火钢的以车代磨和硬车削已经很普及,其实汽车淬硬齿轮加工过程中仍然遇到很多问题,如一些汽车齿轮内孔有油孔,这就出现间断切削加工难题,很多CBN刀具在高速运转时期遇到油孔容易崩刀,齿轮的位置公差难以保证,等等3、淬火钢件的切槽加工:举一个简单的例子,同步器滑套啮合槽淬火后的硬车削加工,虽然立方氮化硼刀具厂家开发出了同步器滑套专用立方氮化硼切槽刀具,但PCBN刀具的寿命仍然不尽如人意。
采用CBN烧结体刀具的干式切削

0
I
自 :1 1 t 5t m l i
图1 .欧洲淬 火钢零件 加工状 况
工具材料是住硼磨料 ( 立方氮化硼磨料工具 商品名 ) N 1 、 N 2 , B X 0 B X 5 是作为能以较高速
度对淬火钢进行干式切削加工的工具材料而
\ )光 图 . 『 f苎 1 I : I J寸 _ 摩I .l 捕 防 : 变 火 刀 . 苎 竺 竺 擦 翌
.
:三 苎 竺 竺 三J
图 2 火钢干式切 嘲加 工 中的课题 .淬 开发的。本文介绍采用住硼磨料刀具进行淬 火钢的干式切削加工的概况 ,并介绍采用了 下 , 由于热量因素 ,引起工件表面组织变质
B X 0B X 5 N 1 、N 2 的高速干式切削加工实例 。
( 产生热影响层 ) 工件硬度降低, , 这种组织
切 削速度也 平均 达到 10 mi。 6 m/ n 日本 住 发 电气工 业公 司的 C N烧 结体 B
3o 。
0
() 2 加工表 面 品位 在 淬 火 钢 加 工 的 加 工 条 件 不 当 的 情 形
曩式 E ∞ H l - O
{ M
m 10 5
●
2
・
薯I ∞
维普资讯
20 年 1 1 02 月 5日出版
国外 金 属加 工
2 C N烧 结体 刀具 的 干式 切 削 B
( 若林 日)
刘 阳春 ( 南省 岳阳 市 湖
俊嘉
译
著
岳北 列检 所 )
C N 烧 绪 体 刀 具 是 能 够 实 际 应 用 于 B
() 寸精度 1尺
加 工面的尺寸精度 不仅 与工具性能有
PCBN超硬刀具的研究及进展
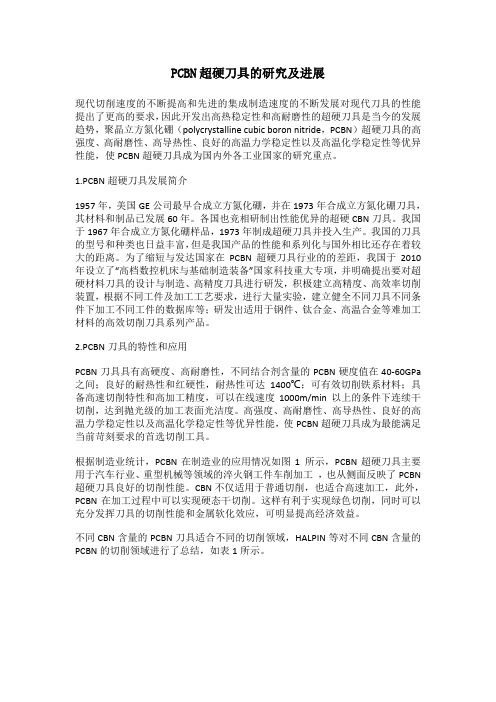
PCBN超硬刀具的研究及进展现代切削速度的不断提高和先进的集成制造速度的不断发展对现代刀具的性能提出了更高的要求,因此开发出高热稳定性和高耐磨性的超硬刀具是当今的发展趋势,聚晶立方氮化硼(polycrystalline cubic boron nitride,PCBN)超硬刀具的高强度、高耐磨性、高导热性、良好的高温力学稳定性以及高温化学稳定性等优异性能,使PCBN超硬刀具成为国内外各工业国家的研究重点。
1.PCBN超硬刀具发展简介1957年,美国GE公司最早合成立方氮化硼,并在1973年合成立方氮化硼刀具,其材料和制品已发展60年。
各国也竞相研制出性能优异的超硬CBN刀具。
我国于1967年合成立方氮化硼样品,1973年制成超硬刀具并投入生产。
我国的刀具的型号和种类也日益丰富,但是我国产品的性能和系列化与国外相比还存在着较大的距离。
为了缩短与发达国家在PCBN超硬刀具行业的的差距,我国于2010年设立了“高档数控机床与基础制造装备”国家科技重大专项,并明确提出要对超硬材料刀具的设计与制造、高精度刀具进行研发,积极建立高精度、高效率切削装置,根据不同工件及加工工艺要求,进行大量实验,建立健全不同刀具不同条件下加工不同工件的数据库等;研发出适用于钢件、钛合金、高温合金等难加工材料的高效切削刀具系列产品。
2.PCBN刀具的特性和应用PCBN刀具具有高硬度、高耐磨性,不同结合剂含量的PCBN硬度值在40-60GPa 之间;良好的耐热性和红硬性,耐热性可达1400℃;可有效切削铁系材料;具备高速切削特性和高加工精度,可以在线速度1000m/min以上的条件下连续干切削,达到抛光级的加工表面光洁度。
高强度、高耐磨性、高导热性、良好的高温力学稳定性以及高温化学稳定性等优异性能,使PCBN超硬刀具成为最能满足当前苛刻要求的首选切削工具。
根据制造业统计,PCBN在制造业的应用情况如图1 所示,PCBN超硬刀具主要用于汽车行业、重型机械等领域的淬火钢工件车削加工,也从侧面反映了PCBN 超硬刀具良好的切削性能。
CBN砂轮在磨削加工中的应用
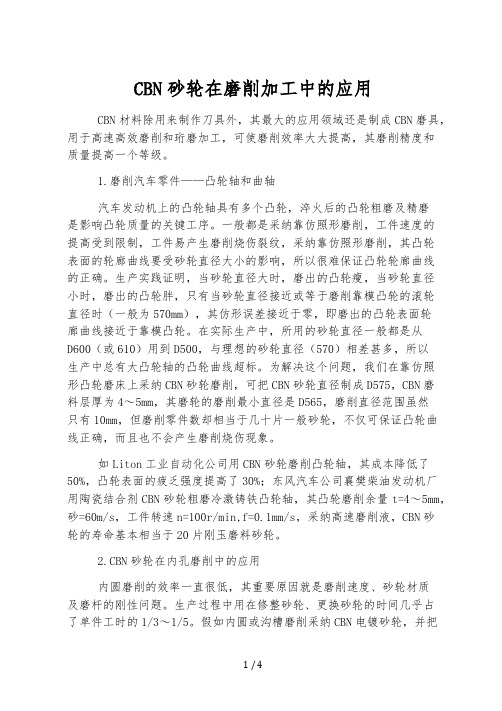
CBN砂轮在磨削加工中的应用CBN材料除用来制作刀具外,其最大的应用领域还是制成CBN磨具,用于高速高效磨削和珩磨加工,可使磨削效率大大提高,其磨削精度和质量提高一个等级。
1.磨削汽车零件——凸轮轴和曲轴汽车发动机上的凸轮轴具有多个凸轮,淬火后的凸轮粗磨及精磨是影响凸轮质量的关键工序。
一般都是采纳靠仿照形磨削,工件速度的提高受到限制,工件易产生磨削烧伤裂纹,采纳靠仿照形磨削,其凸轮表面的轮廊曲线要受砂轮直径大小的影响,所以很难保证凸轮轮廊曲线的正确。
生产实践证明,当砂轮直径大时,磨出的凸轮瘦,当砂轮直径小时,磨出的凸轮胖,只有当砂轮直径接近或等于磨削靠模凸轮的滚轮直径时(一般为570mm),其仿形误差接近于零,即磨出的凸轮表面轮廊曲线接近于靠模凸轮。
在实际生产中,所用的砂轮直径一般都是从D600(或610)用到D500,与理想的砂轮直径(570)相差甚多,所以生产中总有大凸轮轴的凸轮曲线超标。
为解决这个问题,我们在靠仿照形凸轮磨床上采纳CBN砂轮磨削,可把CBN砂轮直径制成D575,CBN磨料层厚为4~5mm,其磨轮的磨削最小直径是D565,磨削直径范围虽然只有10mm,但磨削零件数却相当于几十片一般砂轮,不仅可保证凸轮曲线正确,而且也不会产生磨削烧伤现象。
如Liton工业自动化公司用CBN砂轮磨削凸轮轴,其成本降低了50%,凸轮表面的疲乏强度提高了30%;东风汽车公司襄樊柴油发动机厂用陶瓷结合剂CBN砂轮粗磨冷激铸铁凸轮轴,其凸轮磨削余量t=4~5mm,砂=60m/s,工件转速n=100r/min,f=0.1mm/s,采纳高速磨削液,CBN砂轮的寿命基本相当于20片刚玉磨料砂轮。
2.CBN砂轮在内孔磨削中的应用内圆磨削的效率一直很低,其重要原因就是磨削速度、砂轮材质及磨杆的刚性问题。
生产过程中用在修整砂轮、更换砂轮的时间几乎占了单件工时的1/3~1/5。
假如内圆或沟槽磨削采纳CBN电镀砂轮,并把砂轮速度提高,增大磨杆直径,便可适当提高工件转速与进给速度,不仅可保证孔(弧)径、槽宽尺寸与形位精度,表面粗糙度和避开烧伤,而且还可以成倍地提高加工效率,降低加工成本。
分析造成CBN刀具断裂的原因

●切削深度与刀片断裂,应用 CBN 刀片,选择切削深度,应尽量控制切削深度
不在切削刃二分之一处,这个点是刀片断裂最易发生的危险点。
富耐克研发生产的新型 CBN 刀具应用实践证明: � 不仅适合于精加工( 切深在 0.05~2mm) ,也适合于粗加工切深在(3~30mm) 。
ห้องสมุดไป่ตู้
�
不 仅 适 合 于 高 速 切 削 (200~2000m/min) , 也 适 合 于 中 低 速 切 削 (5~60m/min) 。
刀具断裂现象的原因 分析造成 分析造成刀具断裂现象的原因
在生产加工实际操作中,常常都会出现刀具断裂的现象。具体产生断裂现象 原因有很多,富耐克在客户实际运用中总结出以下原因: ●此现象的发生主要原因是切削条件不当,刀具自身的原因:刀片底不平, 刀垫不平, 刃口崩豁、刀片在制造中的裂纹等。 ●切削过程的原因:在加工高铬、高镍、高钒等合金铸铁材料,工作层含 有大量的高硬度碳化物,切削过程对刀刃有划伤作用,就出现了刃口的豁口。 在 长时间切削的不断冲 击,最终导致刀片难以承受,导致刀片断裂。 ●使用问题:刀具在切削过程中撞刀、撞车、刀刃出现豁口、严重磨损不 换刀刃、切削参数选择不当,不合理使用,属非正常现象。
�
不仅适合于难加工材料,也适合硬度较低的加工材料。
� �
不仅适合于轻载稳定切削,也适合重载断续切削 同时具有卓越抗断裂性和良好的耐磨性
资料来源:
浅析CBN刀片崩刃的问题

浅析CBN刀片崩刃的问题刀片的不正常崩刃、打刀是刀具用户最头疼的问题,会带来加工成本增加,工件报废或返工,加工效率低下等一系列问题。
尤其是价格高昂的CBN刀片,崩刀/崩刃会造成很大的浪费,所以选对、用好CBN刀片至关重要。
华菱超硬总结以下刀片崩刃原因,抛砖引玉,与大家共同探讨。
1,CBN刀片本身的性能因素,较大的CBN颗粒和适合的结合剂整体烧结会有很高的抗拉轻度,这也是粗加工中常用整体CBN刀片的优势之所在。
CBN刀片生产过程中除了需要高纯净度的原材料,还需要CBN微粉经过脱氧等很多程序处理,并检其测堆积密度,这也是市场上CBN刀片质量参差不齐的最大原因。
另外就是合成工艺,它直接决定CBN刀片在合成时聚晶晶粒的形状和尺寸。
华菱超硬研制的整体CBN刀片完全可胜任强断续重载粗加工(点此进入案例)。
2,CBN刀片的选择因素,焊接复合式CBN刀片一般吃刀深度控制在0.3mm以内甚至跟小才能保证使用安全性,如有强断续切削,世界任何焊接复合CBN刀片都不能保证不崩刀,这时候只能选择整体CBN刀片。
(详见:夹砂白口铸铁加工-华菱超硬整体式和焊接式CBN刀具的应用区别)3,刀具型号选择因素,同样性能牌号的CBN刀片,抗冲击性能依次为圆形刀片,常用的25度,45度,75度,83度,90度(装卡后的刀具主偏角);除了主偏角外CBN刀片本身的负倒棱宽度、角度以及刃口处理都影响刀片的强度。
4,切削参数的影响:从切削力上来讲,减少走刀量是最可行的办法;如是间断车削或细长轴加工需要降低转速。
5,机床本身原因,首先机床的整体系统刚性必须要好,避免引起加工震动;粗加工时注意避免“闷车”。
6,刀杆的伸出长度:刀杆伸出过长有震动崩刃风险,伸出长度为刀方尺寸以内最佳。
7,刀杆质量因素:质量好的刀杆具有导热性能优异,刚性好抗震性能好的特点;虽然价格高一点,但对加工总成本影响并不大,且会明显降低刀片不必要的浪费。
8,切削液的使用:在灰铸铁等材质粗加工时CBN刀片是可以使用冷却液的,但存在热应力造成CBN刀片裂纹导致崩刃的风险。
CBN刀具可以加工硬度范围

CBN刀具可以加工硬度范围引言:目前,CBN刀具在黑色金属加工领域,是耐磨性能最好的刀具材料,经过论证,立方氮化硼刀片的寿命一般是硬质合金刀片和陶瓷刀片的几倍到几十倍。
立方氮化硼刀具(CBN刀具)作为脆性超硬刀具材料,硬度是其最明显的特点,而韧性是其最基本的保证,本文通过使用CBN刀具车削不同硬度的铬钻(Cr-Mo)合金钢的试验,阐述了工件材料硬度对CBN刀具寿命的影响,并对其原因作了分析;来进一步明确CBN刀具适宜加工硬度范围,进一步指导CBN刀具的使用。
并浅谈了华菱超硬除了除了对CBN刀具硬度之外的研究—--抗冲击韧性。
CBN刀具的性能与能加工硬度范围一、CBN刀具的性能立方氮化硼(CB N)是人工合成的一种高硬度材料,它的硬度(HV7300~9000)仅次于金刚石,但它的耐热性和化学稳定性都大大高于金刚石,它能耐 1300~1500℃的高温,与铁族金属直至 1 200~1300℃时也不易起化学作用。
因此,CBN刀具既适用于非铁族难加工材料的加工,也适用于淬硬钢、冷硬铸铁及高温合金等铁族难加工金属的切削。
用CBN刀具进行半精加工和精加工,加工精度可达IT5,表面粗糙度可小至Ral.25~0.2μm。
着刀具具有较优的几何形状,无论是在刀具寿命还是加工表面粗糙度方面,CBN刀具切削都完全可以代替磨削加工。
二、CBN刀具的耐用度,由于CBN对铁族金属呈化学惰性并具有高硬、耐磨、耐高温、强度好等特点,故其加工对象多为淬火钢类难加工零件,使用CBN刀具切削软质材料的资料较少,CB ND具切削软质材料时的磨损情况资料不多。
为了明确CBN刀具的适用范围,通过车削不同硬度的Cr一伽合金钢来测定CBN刀具的耐用度,发现了一些值得注意的现象。
实验是在以下条件下进行的。
切削时不使用切削液。
这是因为使用水溶性切削波在高温下CBN会和水发生化学反应,损害CBN的性能。
同时CBN刀具的切削速度一般选得较高,以便使切削区加热到促使材料软化的温度而有利于切削,这时使用切削液可能引起对具冷热不匀,产生很大的热应力而导致热龟裂,使 CBN刀具崩刃。
如何使用CBN刀片加工铸铁件

如何使用CBN刀片加工铸铁件(华菱超硬刀具研发部)铸铁件上的硬质点、气孔、表皮激冷层、夹砂等确实给加工过程带来一些问题,加快了数控刀片的磨损或造成刀具破损,特别在流水线上大批量加工铸铁件时,刀片的破损或快速磨损会打乱流水线的工作节拍,降低生产效率;大型铸铁件表面精加工时,中途换刀会影响加工质量。
由于铸铁件的使用量极大,加工成本的降低或效率的提高,均能带来相当可观的经济效益。
因而人们便企盼用更好的刀具材料来加工铸铁件,以降低加工成本或提高加工效率。
目前,加工铸铁件的数控刀片多为硬质合金数控刀片,陶瓷刀片,CBN刀片;CBN是硬度仅次于金刚石的超硬刀具材料,我国河南超硬材料研究所曾最先针对加工高铬合金铸铁、白口铸铁件等硬铸铁材料研制出CBN刀具材质BN-H10及BN-K10;并于2007年推出可粗加工硬铸铁和淬火钢的CBN刀具材质BN-K1和BN-S20,自此,CBN刀具在高硬度铸铁件的粗加工方面取得了的跨时代的意义。
而对于非难加工类铸铁工件(如灰口铸铁,球墨铸铁、耐磨合金铸铁工件),华菱超硬刀具尝试用CBN刀具加工易切削铸铁件,在粗、精加工方面均取得了很好的效果。
以BN-S30材质CBN刀片为例,其CBN含量(VoL%):92-96 ;CBN粒度(μm):2-8;采用5%含量非金属粘合剂高温高压烧结而成;其硬度HRC98;能实现对HT250,HT200等材质灰口铸铁、高强度球墨铸铁,硼合金铸铁,高硅钼球墨铸铁等铸铁材料进行高速切削。
BN-S30材质CBN刀片相比涂层硬质合金刀片,更能实现高速切削,其适合的线速度范围为:粗加工200—500m/min,精加工500—1500m/min;而且适合加工中心中以1500m /线速度以上进行高速切削。
所以,其加工效率是硬质合金数控刀片效率的2倍以上(硬质合金涂层数控刀片的精加工线速度上限为350m/min)。
从刀具耐用度(刀具寿命)来讲,BN-S30材质CBN数控刀片的寿命是涂层硬质合金寿命的15倍左右,以日本某进口硬质合金数控刀片为例,粗车铸铁工件时,BN-S30材质寿命是UC5115的6倍以上,精车时寿命是UC5115的20倍。
CBN砂轮加工高速钢刀具磨削性能实验研究
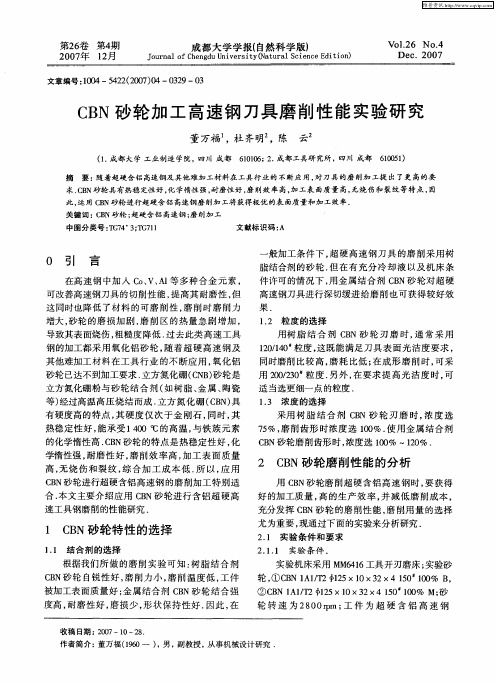
实验机床采用 M 6 1 工具 开刃磨床 ; M 46 实验砂
轮 , C N 1 1T 15×1 3 ① B A /2+2 0× 2×4 10 0 % B。 5 10
② C N 1 1T 15×1 B A / 2+ 2 0×3 ×410 0 % M; 2 5 10 砂
度高 , 耐磨性好 , 磨损少 , 形状保持性好 . 因此 , 在
要: 随着超硬含铝高速钢及其他难h_ 材料在工具行 业的不 断应 用, 刀具的磨 削加 工提 出了更 高的要 r - . 对
求 .B C N砂轮 具有热稳 定性好 , 学惰性强 , 化 耐磨性好 , 削效率高 , _ 表 面质量 高, 磨 hr - . 无烧伤 和裂 纹等特点 , 因 此, 运用 C N砂轮 进行超硬含 铝高速钢磨削加工将获得极优的表 面质量和加 工效率 . B
合 . 文主要 介 绍 应用 C N砂 轮 进 行 含 铝 超 硬 高 本 B 速 工具 钢磨 削 的性 能研 究 .
2 C N砂 轮磨 削 性 能 的 分 析 B
用 C N砂 轮磨 削超 硬 含 铝 高 速 钢 时 , 获 得 B 要 好 的加 工质 量 , 的 生 产 效 率 , 减 低 磨 削成 本 , 高 并 充分 发挥 C N砂 轮 的 磨 削性 能 , 削 用 量 的选 择 B 磨 尤 为重要 , 通过 下面 的实验 来分 析研 究 . 现
收 稿 日期 : 07— 0— 8 20 1 2 .
轮 转 速 为 2 0 m; 件 为 超 硬 含 铝 高 速 钢 0p 工 8 r
作者简介 : 董万福(90一 ) 男 , 16 , 副教授 , 事机械设计 研究 从
维普资讯
维普资讯
第2 卷 第4 6 期 2 0 年 l 月 07 2
氮化硼刀片切削参数,氮化硼刀片吃刀量

氮化硼刀片切削参数,氮化硼刀片吃刀量氮化硼刀具与金刚石刀具同称为超硬刀具,其性质与金刚石类似,可用于高速精密切削多种材料。
氮化硼刀具的发展,大幅度地提高了劳动生产率,改善了产品质量,降低了生产成本,现如今在市场上已占有很大的份额。
今天为大家说一下氮化硼刀片切削参数,氮化硼刀片吃刀量,一起来看看吧。
氮化硼是什么?氮化硼是由氮原子和硼原子所构成的晶体。
化学组成为43.6%的硼和56.4%的氮,具有四种不同的变体:六方氮化硼(HBN)、菱方氮化硼(RBN)、立方氮化硼(CBN)和纤锌矿氮化硼(WBN)。
通常氮化硼刀片是指立方氮化硼刀片。
什么是立方氮化硼刀片?立方氮化硼(CBN)刀片是利用人工方法在高温高压条件下用立方氮化硼微粉和少量的结合剂合成的,其硬度仅次于金刚石而远远高于其它材料,因此它与金刚石刀具统称为超硬刀具。
立方氮化硼刀具的特点立方氮化硼(CBN)刀具包括立方氮化硼成型刀具和立方氮化硼刀片两类。
立方氮化硼成型刀具是把立方氮化硼复合层直接焊接到成型刀具上,它具有如下特点:(1)高强度和耐磨性。
CBN微观硬度大约为8000~9000HRC,仅次于金刚石9000~10000HRC。
此外,CBN刀具的耐磨性比硬度合金、陶瓷和金刚石刀具都高得多,可用于加工强硬的铸铁以及强度大、硬度高及热敏性高的钢件或其他合金材料。
(2)热稳定性好。
CBN耐热性可达1400~1500℃,在1200℃下可保持硬度不变,比金刚石几乎高出1倍。
CBN刀具具有抵抗周期性高温作用的能力,当用来高速加工高温合金时,CBN刀具的切削速度可以为硬质合金的4~6倍。
(3)良好的导热性。
CBN的导热性大大高于高速钢、陶瓷和硬质合金,且CBN刀具的导热系数随温度的提高而增大。
(4)化学稳定性极强。
CBN化学惰性大,在中性和还原性介质中对酸碱都是稳定的。
在2000℃高温情况下才与碳元素起反应,因此非常适合用于加工黑色金属。
立方氮化硼刀具的应用磨辊是磨煤机磨辊总成的重要耐磨件,其材料为BTMCr20,含有Cr、Ni、Mn及Cu等成分。
常见切削刀具材料的磨损现象及原因分析

常见切削刀具材料的磨损现象及原因分析1引言从20世纪80年代开始,由于数控机床的主轴、进给系统等功能部件设计制造技术的突破,数控机床的主轴转速和进给速度均大幅度提高,在现代制造技术全面进步的推动下,切削加工技术开始进入高速切削的新阶段。
目前,高速切削已在模具、航空、汽车等制造业领域得到了大量应用,产生了显著的经济效益,并正向其它应用领域拓展。
高速切削加工对刀具提出了一系列新的要求。
研究表明,高速切削时,造成刀具损坏的主要原因是在切削力和切削温度作用下因机械摩擦、粘结、化学磨损、崩刃、破碎以及塑性变形等的引起的磨损和破损。
因此,对高速切削刀具材料最主要的性能要求是耐热性、耐磨性、化学稳定性、抗热震性以及抗涂层破裂性能等。
陶瓷、CBN、PCD、金属陶瓷等刀具材料具有良好的耐热性和耐磨性,当其韧性得到改善后,非常适合用于高速切削。
先进涂层技术的发展进一步改善了刀具材料的性能。
目前,新型涂层材料和涂层工艺的开发方兴未艾,预示着涂层刀具在高速切削领域将有巨大发展潜力和广阔应用前景。
本文对高速切削加工时陶瓷刀具、立方氮化硼刀具、金刚石刀具、金属陶瓷刀具和涂层刀具的磨损机理进行了综合评述,对刀具的磨损形态和磨损寿命进行了分析,这些研究将有益于实际生产加工中对高速切削刀具的合理选用与磨损控制。
2高速切削刀具的磨损形态高速切削时,刀具的主要磨损形态为后刀面磨损、微崩刃、边界磨损、片状剥落、前刀面月牙洼磨损、塑性变形等。
后刀面磨损是高速切削刀具最经常发生的磨损形式,可看作是刀具的正常磨损。
后刀面磨损带宽度的加大会使刀具丧失切削性能,在高速切削时常采用后刀面上均匀磨损区宽度VB值作为刀具的磨损极限。
微崩刃是在刀具切削刃上产生的微小缺口,常发生在断续高速切削时,通过选用韧性好的刀具材料、减小进给量、改变刀具主偏角以增加稳定性等措施,均可减小微崩刃的发生概率。
通常只要将刀具微崩刃的大小控制在磨损限度以内,刀具仍可继续切削。
立方氮化硼刀具(CBN刀具)车削加工硬质合金材料
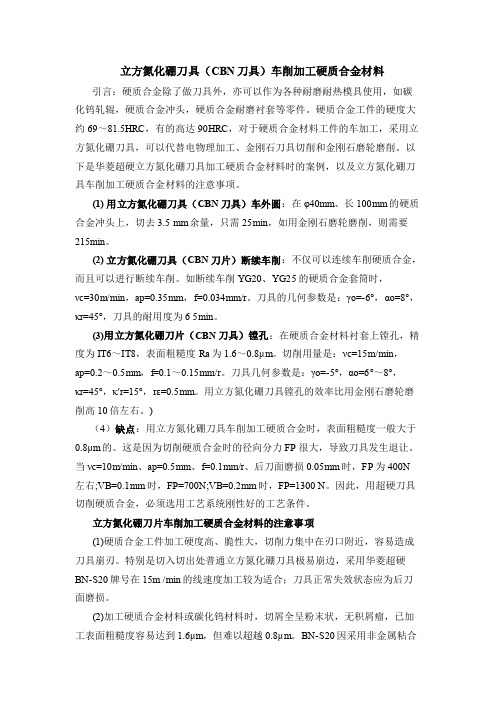
立方氮化硼刀具(CBN刀具)车削加工硬质合金材料引言:硬质合金除了做刀具外,亦可以作为各种耐磨耐热模具使用,如碳化钨轧辊,硬质合金冲头,硬质合金耐磨衬套等零件。
硬质合金工件的硬度大约69~81.5HRC,有的高达90HRC,对于硬质合金材料工件的车加工,采用立方氮化硼刀具,可以代替电物理加工、金刚石刀具切削和金刚石磨轮磨削。
以下是华菱超硬立方氮化硼刀具加工硬质合金材料时的案例,以及立方氮化硼刀具车削加工硬质合金材料的注意事项。
(1) 用立方氮化硼刀具(CBN刀具)车外圆:在φ40mm、长100mm的硬质合金冲头上,切去3.5 mm余量,只需25min,如用金刚石磨轮磨削,则需要215min。
(2) 立方氮化硼刀具(CBN刀片)断续车削:不仅可以连续车削硬质合金,而且可以进行断续车削。
如断续车削YG20、YG25的硬质合金套筒时,νc=30m/min,ap=0.35mm,f=0.034mm/r。
刀具的几何参数是:γo=-6°,αo=8°,κr=45°,刀具的耐用度为6 5min。
(3)用立方氮化硼刀片(CBN刀具)镗孔:在硬质合金材料衬套上镗孔,精度为IT6~IT8,表面粗糙度Ra为1.6~0.8μm。
切削用量是:νc=15m/min,ap=0.2~0.5mm,f=0.1~0.15mm/r。
刀具几何参数是:γo=-5°,αo=6°~8°,κr=45°,κ′r=15°,rε=0.5mm。
用立方氮化硼刀具镗孔的效率比用金刚石磨轮磨削高10倍左右。
)(4)缺点:用立方氮化硼刀具车削加工硬质合金时,表面粗糙度一般大于0.8μm的。
这是因为切削硬质合金时的径向分力FP 很大,导致刀具发生退让。
当νc=10m/min、ap=0.5mm、f=0.1mm/r、后刀面磨损0.05mm时,FP为400N左右;VB=0.1mm时,FP=700N;VB=0.2mm时,FP=1300 N。
CBN刀具高速车削加工钛合金的磨损特性研究
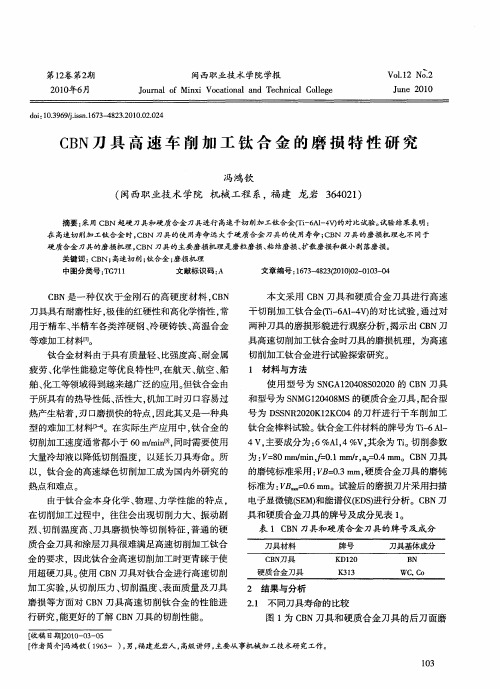
21 不同刀具寿命的 比较 .
行研究 , 能更好的了解 C N刀具的切削性能。 B
[ 收稿 日期 ]O O 0 — 5 2 L一 3 0
图 1 C N刀具和硬质合金刀具的后刀面磨 为 B
【 作者简介] 冯鸿钦 ( 93 ) 男, 16 - , 福建龙岩人 , 高级讲 师, 主要从 事机械加 工技术研 究工作 。
13 0
损 量随 切削路 程的变 化 。 图 1 以看 出 。 高速切 从 可 在 削加工 T一 14V时 , 质合金 刀具 的整个磨 损过 i6A— 硬
程都是急剧磨损 ,没有 明显的初期磨损和正常磨损
阶段 。当后刀 面磨损量 达 到 03m 时 , 削路 程仅 . m 切 70r左 右 ; 0 n 当切 削 路程 达到 9 0m左 右时 。 0 后刀 面 磨 损量 就 达 到 06mm。而 C N刀具 的整 个 切 削过 . B
质合金刀具和涂层刀具很难满足高速切削加工钛合
金 的要求 .因此钛合 金 高速 切削 加工 时更 青 睐 于使
用超硬刀具 。 使用 C N刀具对钛合金进行高速切削 B
加 工 实验 , 切 削 压力 、 削 温度 、 面质 量 及 刀具 从 切 表 磨损 等 方 面对 C N 刀具 高 速 切 削 钛 合 金 的性 能进 B
切削加工速度通常都小于 6 / i ̄ 同时需要使用 0 mn , m t 大量冷却液 以降低切削温度 .以延 长刀具寿命 。所
以 .钛 合金 的高 速绿 色切 削加 工成 为 国内外 研 究 的
热 点和难 点 。
4 , 主要成分为 : %A , V, V 6 I 4% 其余为 T。 i切削参数
第 l 卷第 2 2 期
CBN刀具的韧性

CBN刀具的韧性导读:毋庸置疑,目前,CBN刀具在黑色金属加工领域,是耐磨性能最好的刀具材料。
而且随着研究的进步,CBN刀具适应各种高硬度复杂材料的加工,华菱HLCBN新研制的CBN刀具牌号,可以加工HRC70以上硬度的碳化钨,在国内尚属首例。
但同时,CBN刀具相比硬质合金材料刀具,其脆性大是不争的事实。
那么如何加强CBN刀具的韧性,怎么用可靠的韧性来保证使用的经济型呢?这也刀具用户最关心的问题之一。
一,影响CBN刀具韧性的因素1,原材料的纯度及合理的粒度配置是CBN刀具的韧性最基本保证,在此不再赘述。
(详见立方氮化硼刀具生产及制造方法)2,刀具负倒棱以及刃口微观处理:实测当CBN刀具的倒棱角度从-5°变化到-20°时,切削力出现先减小后又稍有增大的趋势,而切削力直接考验了刀具的韧性。
华菱超硬认为,虽然随着倒棱宽度和角度增大,有利于增加CBN刀具的韧性,但并不能一概而论;具体到加工材质不同(铁屑形状与切削力的形成不同),加工余量、走刀量等都影响负倒棱之于刀具韧性的微观变化。
华菱超硬一般会根据用户的具体加工情况“量体裁衣”选择,这是国外超硬刀具厂家所不能做到的。
当然,如何改进CBN刀具的韧性也是从以上两点反复验证,其中第一条直接决定了CBN刀具的韧性梯度。
二,CBN刀具的韧性在使用中的案例体现1,以华菱超硬BN-S10牌号为例,它不仅可以断续切削淬硬钢,也可以大余量切除工件的淬硬层,但前提是并没有牺牲刀具的耐磨性,这是与市场上的CBN 刀具最大的不同,“耐磨性与抗冲击性的完美平衡”是HLCBN品牌屹立于世界超硬刀具行业的原因之一。
2,刀具的韧性与耐磨性的辩证在机械加工过程中,刀片碎裂、崩刀造成的刀具成本增加是不容忽视的问题,但是刀片碎裂并不一定是刀片的韧性差,也可能是刀具的耐磨性能不足引起,(原因见“立方氮化硼刀片的寿命与耐磨性”)综述:CBN刀具作为脆性超硬刀具材料,韧性是其最基本的保证,但我们不能因为一味的追求其韧性,而丧失了它的超硬材料特性--耐磨性,作为超硬材料的研究者,我们应该反思总结,避免使超硬刀具研究走向另外一个极端。
CBN刀具的切削参数

C B N刀具的切削参数作者单位:郑州华菱超硬材料有限公司一,CBN刀具切削参数的制定方法:?粗加工时,应尽量保证较高的金属切除率和必要的刀具耐用度,故一般优先选择尽可能大的切削深度ap,其次选择较大的进给量f,最后根据刀具耐用度要求,确定合适的切削速度。
精加工时,首先应保证工件的加工精度和表面质量要求,故一般选用较小的进给量f和切削深度ap,而尽可能选用较高的切削速度υc。
1,切削深度ap的选择1)切削深度应根据工件的加工余量来确定。
粗加工时,除留下精加工余量外,一次走刀应尽可能切除全部余量。
当加工余量过大,工艺系统刚度较低,机床功率不足,刀具强度不够或断续切削的冲击振动较大时,可分多次走刀。
切削表面层有硬皮的铸锻件时,应尽量使ap大于硬皮层的厚度,以保护刀尖。
2)半精加工和精加工的加工余量一般较小时,可一次切除,但有时为了保证工件的加工精度和表面质量,也可采用二次走刀。
3)多次走刀时,应尽量将第一次走刀的切削深度取大些,一般为总加工余量的2/3~3/4。
4)在中等功率的机床上、粗加工时的切削深度可达8~10mm,半精加工(表面粗糙度为~μm)时,切削深度取为~2mm,精加工(表面粗糙度为~μm)时,切削深度取为~。
2,进给量f的选择切削深度选定后,接着就应尽可能选用较大的进给量f。
粗加工时,由于作用在工艺系统上的切削力较大,进给量的选取受到下列因素限制;机床—刀具—工件系统的刚度,机床进给机构的强度,机床有效功率与转矩,以及断续切削时刀片的强度。
半精加工和精加工时,最大进给量主要受工件加工表面粗糙度的限制。
工厂中,进给量一般多根据经验按一定表格选取(详见车、钻、铣等各章有关表格),在有条件的情况下,可通过对切削数据库进行检索和优化。
3,切削速度υc的选择在切削深度ap选定以后,可在保证刀具合理耐用度的条件下,用计算的方法或用查表法确定切削速度υc的值。
在具体确定υc值时,一般应遵循下述原则:1)粗车时,切削深度和进给量均较大,故选择较低的切削速度;精车时,则选择较高的切削速度。