冲压件首件检验记录(表格模板、格式)
冲压首末件检验记录表
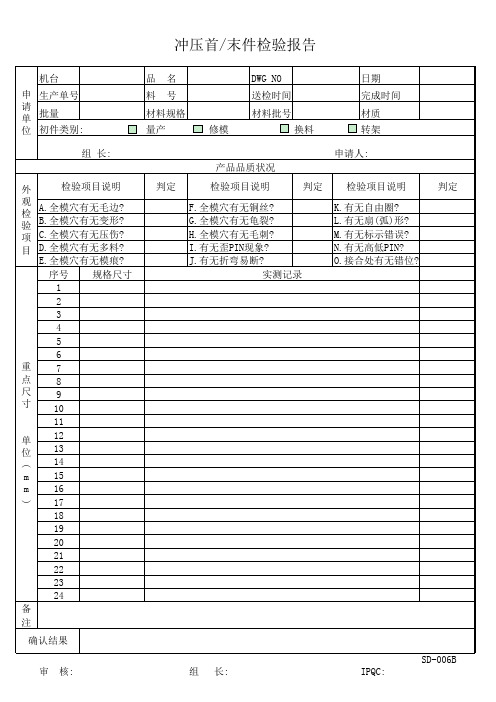
判定
组 长:
IPQC:
SD-006B
(
)
冲压首/末件检验报告
机台
申 生产单号 请 单 批量 位 初件类别:
品名 料号 材料规格 量产
修模
DWG NO 送检时间 材料批号
换料
日期 完成时间 材质 转架
组 长:
外
检验项目说明
观 检
A.全模穴有无毛边?
验 B.全模穴有无变形?
项 C.全模穴有无压伤?
目 D.全模穴有无多料?
E.全模穴有无模痕?
序号 规格尺寸
1
2
3
4
5
6
重
7
点
8
尺
9
寸 10
11
单 12 位 13
14
m
15
m 16
17
18
192021源自222324
备
注
确认结果
审 核:
产品品质状况
申请人:
判定
检验项目说明
判定 检验项目说明
F.全模穴有无铜丝? G.全模穴有无龟裂? H.全模穴有无毛刺? I.有无歪PIN现象? J.有无折弯易断?
实测记录
K.有无自由圈? L.有无扇(弧)形? M.有无标示错误? N.有无高低PIN? O.接合处有无错位?
冲压件检验记录

必须依照样件和生产作业指导书生产
生产 D:有无连续性的异常,是否已改善。 条件 E:来料是否正常(上工序)。
无异常 上工序来料合格,方可生产
F:改善措施操作人员是否了解或被执行。 改善措施操作员须了解和执行
G:产品有无异常情况,有无改善。
无异常
H:检验状态是否正确,不合格品管理是否正常 检验状态正确,不合格品管理正常
I:工具是否校验,有无过期。
工具须校验合格且在合格期内
工作时间
操作者 检查记录
尺寸
边界轮廓抽检点 孔径孔位抽检点
符合检验标准 冲压首件完序后测量,合格后方可生 或样件 产
内容
要求
工序
生产 数量
抽查 数量
首检
巡检
外观检验记录
末检
首检
巡检
版本
末检
合格 率
备注
压印点 、棱线 清晰, 曲面过 渡平滑 自然, 表面 开裂、 质量 隐裂、 符合检 变形、 验标准 起皱、 或样件 少孔、 缺边等 缺陷不 允许, 毛刺高 度≤料 厚15%
QR-8.3-01 号:0 车型
零件编号
冲压件检验记录
生产地点
A: 工作站、检验站的标准样件、生产作业 样件,检验、生产作业指导书必须备齐, 指导书、检验指导书是否备齐、正确。 方可生产
B:首件检查是否有执行,是否正确。
首件检查必须执行
C:有无依照标准样件或作业指导书的工艺参 数、条件或方法生产。
序号 1
2
检验结论
首检 巡检 末检
问题描述
生产过程质量异常问题记录
现场纠正措施和结果
当班责任人
当班检验
审核
首件检验记录表模版

外观□
焊锡/渣
目视/显微镜
孔毛刺
目视/显微镜
边毛刺
目视/显微镜
划伤
目视/显微镜
元件方向
目视/显微镜
缺料
目视/显微镜
分层
目视/显微镜
变形
目视/显微镜
表面清洁度
目视/显微镜
总装□
信号线焊接
目视
导线焊接
目视
结构件组装
目视
其它□
□作业文件
□作业人员
□设备能力
综合判定
□合格(开始量产);
□不合格□重新调整工艺和设备□停止生产,开《产品质量异常报告处理单》
首件检验记录表
检验日期:年月日
产品图号
产品名称
数量
1
检验依据
□设计图纸□标准样件□制程检验标准□产品标准□其它
检验时机
□开机首检□批量生产之前□修模首件□转产首件□生产参数变更
检查项目
检Байду номын сангаас标准
检查方式
检查结果描述
判定
尺寸
设计图纸要求
游标卡尺
电装□
SMT贴片
目视/显微镜
手工焊接
目视/显微镜
钳装□
螺钉装配
备注:检验时发现有一项不合格则判首件确认不合格;(合格用“OK”表示,不合格用“NG”表示)
生产现场确认:签名:
冲压过程质量巡检记录表
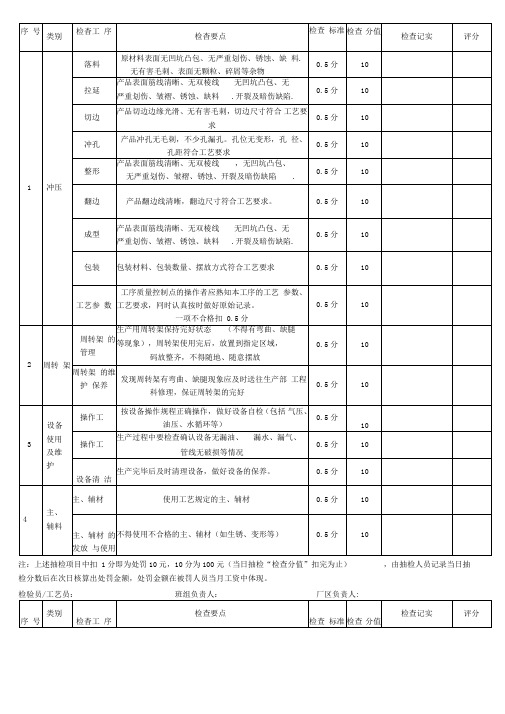
10
工艺验
证
按规定及时对工艺参数的连续监控记录,每班生
产前工艺参数需经过班长的检查验证,首件质量
需经检验员确认后才可开始后续生产
0.5分
10
检查
按照工艺要求认真填与自检卡,做好自检、互检
0.5分
10
6
生产
场地
零件码 放
零件总成要放到相应的工位器具, 并码放整齐在 焊接和搬运过程中轻拿轻放,保证零件在工位器 具中整齐摆放,不得超高以防工件磕碰、划伤。
检分数后在次日核算出处罚金额,处罚金额在被罚人员当月工资中体现。
检验员/工艺员:班组负责人:厂区负责人:
序 号
类别
检杳工 序
检查要点
检查 标准
检查 分值
检查记实
评分
5
工艺
执行
情况
工艺文
件管理
工艺文件摆放到定置规定的位置,不得随意涂改 撕毁、污染等
0.5分
10
工艺文
件执行
按照工艺文件进行生产,保证总成的质量
0.5分
10
8
信息 反馈
操作工 记录
按工乙要求认真填与生产记录单(工乙、质量、 设备工装等)
0.5分
10
设备信 息反馈
设备工装出现问题应停止生产,及时通知维修人 员,待故障排除后方可生产
0.5分
10
设备信 息反馈
设备和工装出现故障,需同时通知检验员到场确 认是否影响零件质量,若影响必须向前追溯
0.5分
管线无破损等情况
0.5分
10
设备清 洁
生产完毕后及时清理设备,做好设备的保养。
0.5分
10
4
主、
首件检验记录表模版
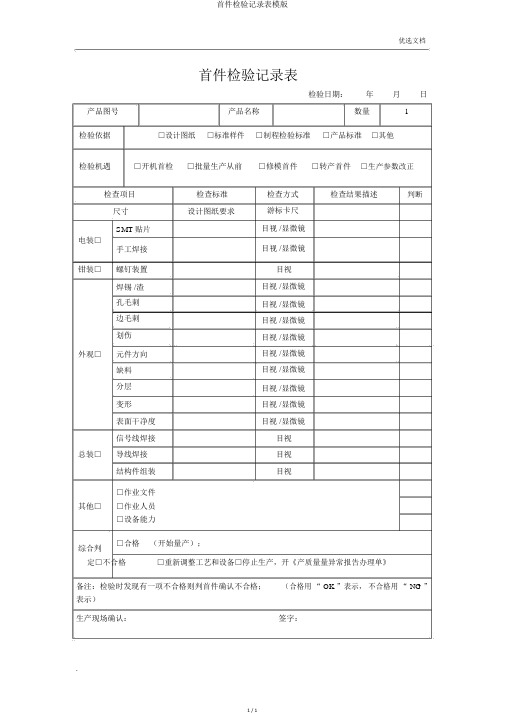
首件检验记录表模版
1 / 1 优选文档
首件检验记录表
检验日期:年月日产品图号产品名称数量 1
检验依据□设计图纸□标准样件检验机遇□开机首检□批量生产从前
检查项目检查标准
尺寸设计图纸要求
SMT 贴片
电装□
手工焊接
钳装□螺钉装置
焊锡 /渣
孔毛刺
边毛刺
划伤
外观□元件方向
缺料
分层
变形
表面干净度
信号线焊接
总装□导线焊接
结构件组装
□作业文件
其他□□作业人员
□设备能力□制程检验标准□产品标准□其他
□修模首件□转产首件□生产参数改正
检查方式检查结果描述判断游标卡尺
目视 /显微镜
目视 /显微镜
目视
目视 /显微镜
目视 /显微镜
目视 /显微镜
目视 /显微镜
目视 /显微镜
目视 /显微镜
目视 /显微镜
目视 /显微镜
目视 /显微镜
目视
目视
目视
综合判
□合格(开始量产);
定□不合格□重新调整工艺和设备□停止生产,开《产质量量异常报告办理单》
备注:检验时发现有一项不合格则判首件确认不合格;(合格用“ OK ”表示,不合格用“ NG ”表示)
生产现场确认:签字:
.。
首件检验记录表
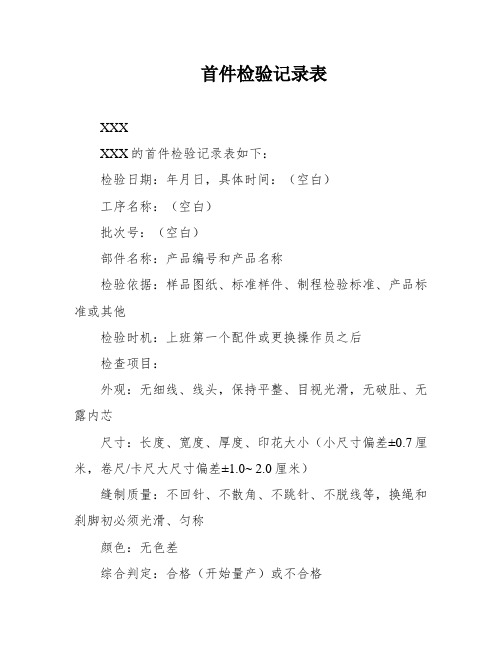
首件检验记录表
XXX
XXX的首件检验记录表如下:
检验日期:年月日,具体时间:(空白)
工序名称:(空白)
批次号:(空白)
部件名称:产品编号和产品名称
检验依据:样品图纸、标准样件、制程检验标准、产品标准或其他
检验时机:上班第一个配件或更换操作员之后
检查项目:
外观:无细线、线头,保持平整、目视光滑,无破肚、无露内芯
尺寸:长度、宽度、厚度、印花大小(小尺寸偏差±0.7厘米,卷尺/卡尺大尺寸偏差±1.0~ 2.0厘米)
缝制质量:不回针、不散角、不跳针、不脱线等,换绳和刹脚初必须光滑、匀称
颜色:无色差
综合判定:合格(开始量产)或不合格
检查标准、检查方式、检查结果描述和判定都需要填写。
如果发现不合格项,需要填写品质异常报告处理单并停止生产。
生产现场确认需要签名。
首件检验记录表和末件检验记录

检验方式
检验结果描述
判定
外观
目视
尺寸
①孔距
卷尺/卡尺
②孔深③孔径④⑤ Nhomakorabea结构
目视
颜色
■目视*
性能
治具、万用表
作业方法
作业指导书
材质
BOM
综合判定
□合格(开始蚩产);
□不合格□重新调幣工艺和设备□停止生产,开《品质异常报告处理单》。
备注:检验时发现有一件不合格项则判首件确认不合格:(合格用“0K”表示,不合格用“MG”表示)
(5)机器在生产运行期间被修理,重新工作或机器的参数从原始首件被批准后改变及新的生产工艺被实施时要进行首件检验。
日期:年 月日
编制:
审核:
批准:
XXXX有限公司
QP/FLB-XXF-0X版本:X
首件检验记录表
检验日期: 年 月 日
工序名称
产品編号
产品名称
部件名称
①、 ②. ③、 ④. ⑤、
检验依据
□SOP□标准样件□制程检验标准□其它
检验时机
□上班第i个配件□批呈生产之前□调机换模之后
□更换操作员之后□停产达24小时之后□丝印换网版之后
检验项冃
生产现场确认:签名:
审核:
品管员:
首、末件检验记录
产品代号:产品日期:
班次
早班
中班
晚班
检验规定
首件
末件
首件
末件
首件
末件
签名
说明:(1)首末件确认人员:生产工程师、质量控制人员
(2)在生产前十分钟内完成检查,按2和数据确认
(3)质量管理人员有责任在生产、班次结束时完成末件检查
(4)首件检验必须在每班开始前
首件检验纪录表

工序:日期:
客户
订单号码
品名规格
料号
批量
环保要求
检验依据:
制程检验规范、工程图纸、
图纸编号:
所用物料及规格:
品管物料确认:
判定:
环保确认:
判定:
外观检验:
判定:
尺寸检验:
判定:
工艺要求:
判定:
测试要求:
判定:
送检时间:检验结果:合格不合格
审核:
检验员:
送检人:
说明:每批初件及更换不同供应商材料均送样确认,并记录,中途异常调机无需记录,但需IPQC确认。源自首件检验记录表工序:日期:
客户
订单号码
品名规格
料号
批量
环保要求
检验依据:
制程检验规范、样版、生产单,客户资料
所用物料及规格:
品管物料确认:
判定:
外观检验:
判定:
尺寸检验:
判定:
工艺要求:
判定:
测试要求:
判定:
送检时间:检验结果:合格不合格
审核:
检验员:
送检人:
说明:每批初件及更换不同供应商材料均送样确认,并记录,中途异常调机无需记录,但需IPQC确认。
首件检验记录表

判定
项目
检查 检验标准
指令
记录
标准件电流
首检数据
问题
□虚焊 □空焊 □少锡 □多锡 偏移 □短路 □破损 □缺件 □拉尖 □起翘 □错件 □污染 □外斜 □无程序 □烧写 失败 □测试无数据
备注
总结
最终判定结果 □合格 □不合格 是否同意量产: □是 □否
检验员签名:
注意 1、所有项目均需连续检查最少5件。 事项 2、根据质量统计的不良项目进行持续跟进。
1、该工序准备好5个样件置于待检区,并通知检验员,检查判定合格后生产。
填写 2、检验员判定合格后从样品中随机挑选1个样件,进行首件标识。并连同巡检记录表一起置于产线最终检查工位。 说明 3、适用范围:生产过程所有工艺进行首件检查。
4、检查结果:合格项目打“√”,不合格项目打“×”,无此检查项目打“0”;本表单保留一年。
4、检查结果:合格项目打“√”,不合格项目打“×”,无此检查项目打“0”;本表单保留一年。
首件检验记录表
版本:A/0
名称 首件
批次
数量
生产 日期
检验时间
首检板号
信息 □直插件首检 □打磨首检 检 □掰板首检 □烧写程序首检
□打标首 □测试
检验依 据
□工程图纸
□标准样件
□制程检验标准
□产品标准
□其它
检验标准
首件检验记录表
版本:A/0
名称 首件
批次
数量
生产 日期
检验时间
首检板号
信息 □直插件首检 □打磨首检 检 □掰板首检 □烧写程序首检
□打标首 □测试
检验依 据
□工程图纸
□标准样件
□制程检验标准
首件检查记录表

(1)由调机/开机人员填写本单与样品随同送检,经IPQC人员判定合格方可生产(含调机/换料在内);
(2)填写一式两份,经IPQC人员判定OK后正本由IPQC自存,副本连同样品交申请人,并继续执行巡回检验;
送检部门填写
客户
订单号
批量
机型
品名
料号
部门
样本数
原料
班别
机台
送检时间
□每日初件□每批初件□更换材料□刚开机
□夹具修正□模具修正□颜色调整□刚调机
送检人
确认
检验部门填写
IPQC确认以上无误后进行以下检验
外
观
数量
检验项目
尺
寸
数量
规格
颜色
结构
检验结果
□A:合格,继续生产
备注:
□B:不合格,重新调机
□C:不能生产,立刻调机
首件检验记录表(模版)

外观□
焊锡/渣
目视/显微镜
孔毛刺
目视/显微镜
边毛刺
目视/显微镜
划伤
目视/显微镜
元件方向
目视/显微镜
缺料
目视/显微镜
分层
目视/显微镜
变形
目视/显微镜
表面清洁度
目视/显微镜
总装□
信号线焊接
目视
导线焊接
目视
结构件组装
目视
其它□
□作业文件
□作业人员
□设备能力
综合判定
□合格(开始量产);
□不合格□重新调整工艺和设备□停止生产,开《产品质量异常报告处理单》
首件检验记录表
检验日期:年月日
产品图号
产品名称
数量
1
检验依据
□设计图纸□标准样件□制程检验标准□产品标准□其它
检验时机
□开机首检□批量生产之前□修模首件准
检查方式
检查结果描述
判定
尺寸
设计图纸要求
游标卡尺
电装□
SMT贴片
目视/显微镜
手工焊接
目视/显微镜
钳装□
螺钉装配
备注:检验时发现有一项不合格则判首件确认不合格;(合格用“OK”表示,不合格用“NG”表示)
生产现场确认:签名:
首件检验记录表模版.doc
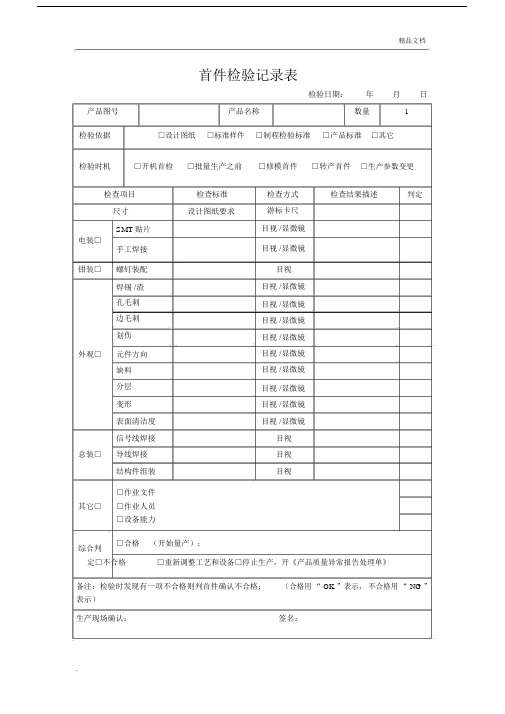
精品文档
首件检验记录表
检验日期:年月日产品图号产品名称数量 1
检验依据□设计图纸□标准样件检验时机□开机首检□批量生产之前
检查项目检查标准
尺寸设计图纸要求
SMT 贴片
电装□
手工焊接
钳装□螺钉装配
焊锡 /渣
孔毛刺
边毛刺
划伤
外观□元件方向
缺料
分层
变形
表面清洁度
信号线焊接
总装□导线焊接
结构件组装
□作业文件
其它□□作业人员
□设备能力□制程检验标准□产品标准□其它
□修模首件□转产首件□生产参数变更
检查方式检查结果描述判定游标卡尺
目视 /显微镜
目视 /显微镜
目视
目视 /显微镜
目视 /显微镜
目视 /显微镜
目视 /显微镜
目视 /显微镜
目视 /显微镜
目视 /显微镜
目视 /显微镜
目视 /显微镜
目视
目视
目视
综合判
□合格(开始量产);
定□不合格□重新调整工艺和设备□停止生产,开《产品质量异常报告处理单》
备注:检验时发现有一项不合格则判首件确认不合格;(合格用“ OK ”表示,不合格用“ NG ”表示)
生产现场确认:签名:
.。
冲压质量测试记录表
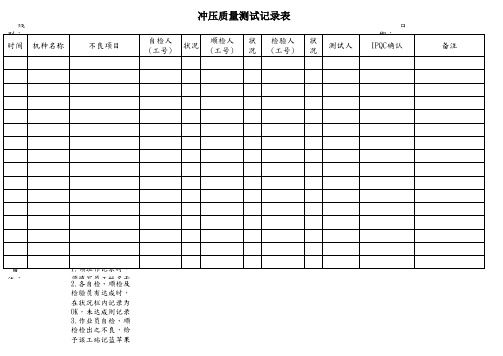
线别: 时间 机种名称 不良项目 自检人 (工号) 状况 顺检人 (工号) 状况 检验人 (工号) 状况 测试人 日期: IPQC确认 备注
备注:
1.领班作记录时,须填写员工姓名于相应之自检、顺检及检验员字段。 2.各自检、顺检及检验员有达成时,在状况栏内记录为OK,未达成则记录NG. 3.作业员自检、顺检检出之不良,给予该工站记蓝苹果一个。 4.作业员自检、顺检未检出之不良,给予该工站记红苹果一个并作书面检讨一份。 5.检验员未检出,在质量广告牌做相应记录,一周内每出现两次作书面检讨一份。 6.记录公平、公正,且记录须真实可靠。
核
首件检查记录表(专业版)

机台:
首 件 信 息
组别:
工艺: □注塑、 □喷油、 □丝印、 □电镀
产品名称
生产日期 制令单号 检验时间 产品限度说明 时 分
检验人员/部 门
客户 □开机首检
检验项目 材 质
颜色 □材料变更 明 或 要 求 □其他:
□修模首件 检验确认
□生产人员变更 检 验 说
品质和工程要确认
结 构 试 装 颜 色
外观 (含喷油 检 、丝印工 艺) 查
项 目
尺 寸 丝 印 喷 油
功能测试
破Hale Waihona Puke 测试其它注意事项相 关 □熟悉产品品质要求 人 员 □不熟悉产品品质要求 确 认
员工: FQC: 领 班: 技 术 员:
最终判定结果: □合格 □不合格 □可试产 □可生产
确认签名: 品质主管: 生产主管: 总经理助理:
注意事项:所有在生产前必须做首样,合格后方可试产、再投产。
首件检验记录表(模版)

产品图号
产品名称
数量
1
检验依据
□设计图纸□标准样件□制程检验标准□产品标准□其它
检验时机
□开机首检□批量生产之前□修模首件□转产首件□生产参数变更
检查项目
检查标准
检查方式
检查结果描述
判定
尺寸
设计图纸要求
游标卡尺
电装□
SMT贴片
目视/显微镜
手工焊接
目视/显微镜
钳装□
螺钉装配
目视
外观□
焊锡/渣
目视/显微镜
孔毛刺
目视/显微镜
边毛刺
目视/显微镜Байду номын сангаас
划伤
目视/显微镜
元件方向
目视/显微镜
缺料
目视/显微镜
分层
目视/显微镜
变形
目视/显微镜
表面清洁度
目视/显微镜
总装□
信号线焊接
目视
导线焊接
目视
结构件组装
目视
其它□
□作业文件
□作业人员
□设备能力
综合判定
□合格(开始量产);
□不合格□重新调整工艺和设备□停止生产,开《产品质量异常报告处理单》
备注:检验时发现有一项不合格则判首件确认不合格;(合格用“OK”表示,不合格用“NG”表示)
生产现场确认:签名:
- 1、下载文档前请自行甄别文档内容的完整性,平台不提供额外的编辑、内容补充、找答案等附加服务。
- 2、"仅部分预览"的文档,不可在线预览部分如存在完整性等问题,可反馈申请退款(可完整预览的文档不适用该条件!)。
- 3、如文档侵犯您的权益,请联系客服反馈,我们会尽快为您处理(人工客服工作时间:9:00-18:30)。
冲压件首件检验记录
生产车间
产品名称型号规格
合同/储备编号
生产批号
图号模具号操作者每盘数抽检数生产日期
外观主要尺寸
检验标准检验结果检验标准检验结果检验标准检验结果判定
插拔力标准测试具
检验标准插入力第一次:第六次:拔出力第一次:第六次:
检验结果插入力第一次:第六次:拔出力第一次:第六次:
判定判定
质检员意见质检员签字时间
注:仅作3只记录。
JCH-QR8.2.3-02
冲压件首件检验记录
生产车间产品名称型号规格合同/储备编号生产批号
图号模具号操作者每盘数抽检数生产日期
外观主要尺寸
检验标准检验结果检验标准检验结果检验标准检验结果判
插拔力标准测试具检验标准插入力第一次:第六次:拔出力第一次:第六次:
检验结果插入力第一次:第六次:拔出力第一次:第六次:
判定判定
质检员意见质检员签字时间注:仅作3只记录。