第十章蜗杆传动分析
蜗杆传动原理

蜗杆传动原理
蜗杆传动是一种常见的传动方式,它利用蜗杆和蜗轮的啮合传递动力,广泛应用于机械设备中。
蜗杆传动具有结构简单、传动比稳定、噪音小、承载能力大等优点,因此在工业生产中得到了广泛的应用。
下面我们将详细介绍蜗杆传动的原理和工作过程。
蜗杆传动的基本原理是利用蜗杆和蜗轮的啮合来传递动力。
蜗杆是一种螺旋形的圆柱体,蜗轮则是一种与蜗杆啮合的圆盘状零件。
当蜗杆旋转时,蜗轮会随之旋转,从而实现动力传递。
蜗杆传动的传动比通常较大,可达到10:1甚至更高,因此适用于需要大传动比的场合。
蜗杆传动的工作原理非常简单,当蜗杆旋转时,由于蜗杆的螺旋形状,蜗轮会被迫转动。
蜗轮的转动带动输出轴进行工作,从而实现了动力传递。
由于蜗杆和蜗轮的啮合方式,蜗杆传动的传动比相对稳定,不易受外界因素的影响,因此在需要稳定传动比的场合得到了广泛应用。
蜗杆传动还具有承载能力大、噪音小等优点。
由于蜗杆和蜗轮的啮合方式,蜗杆传动能够承受较大的径向和轴向载荷,因此适用于承载要求较高的场合。
同时,蜗杆传动的工作过程中摩擦力较大,因此噪音较小,能够满足对噪音要求较高的场合的需求。
总的来说,蜗杆传动是一种结构简单、传动比稳定、承载能力大、噪音小的传动方式,广泛应用于机械设备中。
它的工作原理简单清晰,通过蜗杆和蜗轮的啮合来传递动力,适用于需要大传动比、稳定传动比、承载能力大、噪音小的场合。
希望本文能够对蜗杆传动的原理有所了解,对相关领域的工作者有所帮助。
蜗杆传动课件

蜗杆传动课件蜗杆传动课件蜗杆传动是一种常见的机械传动方式,它通过蜗杆和蜗轮之间的啮合来实现转动传递。
在工业领域中,蜗杆传动广泛应用于各种机械设备中,如起重机、输送机、搅拌机等。
本文将介绍蜗杆传动的原理、特点以及应用。
一、蜗杆传动的原理蜗杆传动是一种通过蜗杆和蜗轮之间的啮合来实现转动传递的机械传动方式。
蜗杆是一种螺旋形状的轴,蜗轮则是一个具有螺旋槽的圆盘。
当蜗杆旋转时,它的螺旋形状会使蜗轮产生旋转运动。
由于蜗杆的斜面角度较小,蜗轮的转速相对较低,但扭矩较大。
这使得蜗杆传动适用于需要大扭矩和较低转速的场合。
二、蜗杆传动的特点1. 大传动比:蜗杆传动的传动比可以达到较大的数值,通常在10:1至60:1之间。
这使得蜗杆传动在一些需要较大减速比的设备中非常实用。
2. 紧凑结构:由于蜗杆传动的传动比较大,所以可以通过较小的尺寸实现较大的减速比。
这使得蜗杆传动在空间有限的场合中非常适用。
3. 自锁性:蜗杆传动具有自锁性,即在没有外力作用下,蜗杆传动可以防止被传动部件的逆转。
这使得蜗杆传动在一些需要防止逆转的场合中非常有用,如起重机的升降装置。
4. 传动效率较低:由于蜗杆传动的摩擦损失较大,所以传动效率相对较低。
通常情况下,蜗杆传动的传动效率在50%至80%之间。
因此,在对传动效率要求较高的场合中,蜗杆传动可能不是最佳选择。
三、蜗杆传动的应用1. 起重机:蜗杆传动广泛应用于各种起重机中,如桥式起重机、门式起重机等。
蜗杆传动的大传动比和自锁性使得起重机的升降装置更加安全可靠。
2. 输送机:蜗杆传动也常用于输送机中,用于驱动输送带或链条的运动。
蜗杆传动的紧凑结构和大传动比使得输送机的传动装置更加节省空间且具有较大的减速比。
3. 搅拌机:蜗杆传动还广泛应用于各种搅拌机中,如混凝土搅拌机、食品搅拌机等。
蜗杆传动的大扭矩和较低转速使得搅拌机可以更好地完成搅拌工作。
总结蜗杆传动是一种常见的机械传动方式,它通过蜗杆和蜗轮之间的啮合来实现转动传递。
机械基础之蜗杆传动

机械基础之蜗杆传动1. 概述蜗杆传动是一种常见的机械传动方式,用于将大扭矩通过蜗杆传递给小扭矩的蜗轮。
它是一种精密传动装置,因其传递扭矩平稳可靠而被广泛应用于各种工业机械设备中。
2. 结构蜗杆传动由蜗杆和蜗轮组成。
蜗杆是一种带有螺旋齿的圆柱形轴,其外形类似于蜗牛的螺旋壳。
蜗轮是一种带有封闭螺旋槽的圆盘,其形状与蜗杆的齿相匹配。
蜗轮的齿数通常为1,而蜗杆的螺旋齿数通常为多个。
3. 工作原理当蜗杆转动时,其螺旋齿会将蜗轮推动转动。
由于蜗杆的斜面设计,每转动一圈,蜗轮只转动一颗齿。
这种结构使得蜗杆传动具有很大的减速比,通常可以达到20:1以上。
同时,由于蜗杆和蜗轮的齿轮接触表面较大,使得传动效率较低。
4. 优点和应用蜗杆传动具有以下优点: - 减速比大:通常可以达到20:1以上的减速比。
- 扭矩传递平稳:由于每转动一圈蜗杆,蜗轮只转动一颗齿,使得扭矩传递非常平稳可靠。
- 自锁性:由于摩擦力的存在,在没有外力作用下,蜗杆传动可以固定位置,不会自动转动。
蜗杆传动广泛应用于各种工业机械设备中,如: - 起重机械:使用蜗杆传动可以实现对重物的精确起重与放下。
- 工业机械:这种传动方式可以用于带有大扭矩输出要求的设备,如搅拌机、制动器等。
- 游乐设备:蜗杆传动可以用于旋转设备的减速与传动。
5. 注意事项在使用蜗杆传动时,需要注意以下几点: - 润滑:蜗杆传动的润滑非常重要,可以使用润滑油或润滑脂对齿轮进行润滑,以确保传动效率和寿命。
- 定期维护:定期检查蜗杆传动的磨损情况,并及时更换磨损严重的零部件,以延长传动的使用寿命。
- 负载限制:应根据蜗杆传动的设计参数和工作环境确定其负载限制,以防止传动失效或损坏。
6. 总结蜗杆传动是一种重要的机械传动方式,通过蜗杆和蜗轮的组合,可以实现大扭矩到小扭矩的平稳传递。
其优点包括减速比大、扭矩传递平稳和自锁性,广泛应用于工业机械设备中。
在使用蜗杆传动时,需要注意润滑、定期维护和负载限制等细节,以保证传动的正常运行和寿命。
蜗杆蜗轮传动的受力分析

蜗杆蜗轮传动的受力分析
蜗杆传动时,齿面上作用的法向力Fn 和摩擦力Ff 可分解为三个相互垂直的分力:圆周力Ft 、径向力Fr 和轴向力Fa 。
当蜗杆轴与蜗轮轴交错角为90°且蜗杆主动时,蜗杆蜗轮所受力的大小和对应关系为:
Ft1=−Fa2=
2T1d1,Fa1=−Ft2=2T2d2, Fr1=Fr2=Ft2∗tanα 其中:T1=9549P n (T1:输入扭矩Nm ,P :输入功率Kw ,转速n :r/min)
T2=T1∗i ∗η (i :传动比,η传动效率)
T =9549P n 的来历:
T =F ∗r =1000P v ∗r =1000P rω∗r =1000P 2πn/60≈9549P n 当蜗杆主动时,各力方向判断如下:
蜗杆上的圆周力 Ft1的方向与蜗杆转向相反。
蜗杆上的轴向力 Fa1的方向可以根据蜗杆的螺旋线旋向和蜗杆转向,用(左)右手定则判断。
蜗轮上的圆周力 Ft2 的方向与蜗轮的转向相同(与蜗杆上的轴向力 Fa 1的方向相反)。
蜗轮上的轴向力 Fa2 的方向与蜗杆上的圆周力 Ft1的方向相反。
蜗杆和蜗轮上的径向力 Fr1 、Fr2的方向分别指向各自的轴心。
举例如下:。
蜗杆传动的效率
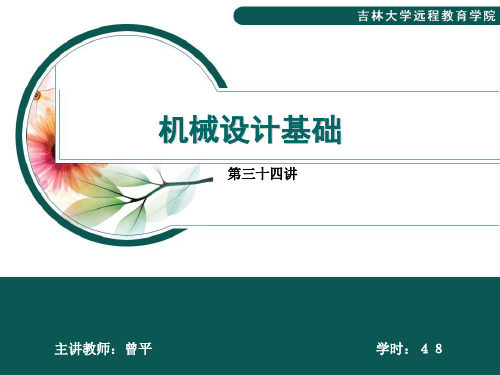
学习要求
1.了解蜗杆传动的类型、特点和应用; 2.熟悉蜗杆传动的基本参数和尺寸; 3.了解蜗杆传动的失效形式,蜗杆蜗轮 的材料选择; 4.掌握蜗杆传动的受力分析,了解强度 计算特点; 5.熟悉蜗杆传动的效率与热平衡计算; 6.了解蜗杆传动的结构。
§10-1 蜗杆传动的类型和特点
蜗杆传动常用于传 递空间两交错轴间的运 动和功率,两轴的轴交 角一般为900。通常蜗杆 为主动件。
v2
2 —轴承的效率
1 tg / tg( )
'
—— 当量摩擦角
Z1大,γ大,效率高; Z1过多,蜗杆加工困难; 减小d1 ,受蜗杆刚度限制。
vs v 1
圆柱蜗杆传动主要参数和几何尺寸
小,效率高。
1
tg tg ( )
'
当润滑条件好时,滑动速度 vs 高, 值小,效率高。反之,出现胶合。
a1
am 1
例1 解1.确定蜗杆的模数
则
m 1 5 .7 1 2
m
2 p 2 m p a m 1 1 5 .7 1 m m
2 .5 0 m m
由表10-1取标准模数 m 2 .5 m m 2.确定蜗杆分度圆直径 d 1 由表10-2知, d d 2 m 则 d d 2 m 3 2 .9 5 2 2 .5 2 7 .9 5 m m 则根据蜗杆模数 m 2 .5 m m ,
2 2
3 0 2 .5 7 5 m m
齿顶圆直径 顶圆直径 蜗轮齿宽 b 取 b 25 m m
2
d a 2 d 2 2 m 7 5 2 2 .5 8 0 m m
d e 2 d a 2 2 m 8 0 2 2 .5 8 5 m m
机械设计基础之蜗杆传动
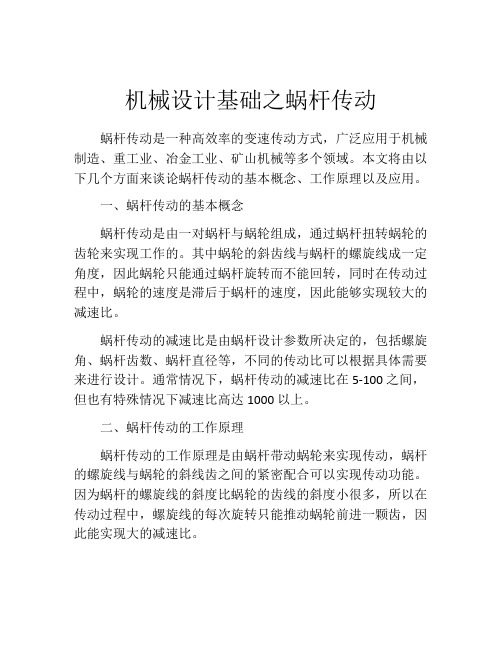
机械设计基础之蜗杆传动蜗杆传动是一种高效率的变速传动方式,广泛应用于机械制造、重工业、冶金工业、矿山机械等多个领域。
本文将由以下几个方面来谈论蜗杆传动的基本概念、工作原理以及应用。
一、蜗杆传动的基本概念蜗杆传动是由一对蜗杆与蜗轮组成,通过蜗杆扭转蜗轮的齿轮来实现工作的。
其中蜗轮的斜齿线与蜗杆的螺旋线成一定角度,因此蜗轮只能通过蜗杆旋转而不能回转,同时在传动过程中,蜗轮的速度是滞后于蜗杆的速度,因此能够实现较大的减速比。
蜗杆传动的减速比是由蜗杆设计参数所决定的,包括螺旋角、蜗杆齿数、蜗杆直径等,不同的传动比可以根据具体需要来进行设计。
通常情况下,蜗杆传动的减速比在5-100之间,但也有特殊情况下减速比高达1000以上。
二、蜗杆传动的工作原理蜗杆传动的工作原理是由蜗杆带动蜗轮来实现传动,蜗杆的螺旋线与蜗轮的斜线齿之间的紧密配合可以实现传动功能。
因为蜗杆的螺旋线的斜度比蜗轮的齿线的斜度小很多,所以在传动过程中,螺旋线的每次旋转只能推动蜗轮前进一颗齿,因此能实现大的减速比。
同时由于蜗杆传动的特有设计,使其具有良好的自锁性,可以起到防止倒车的作用。
这种自锁性的原理是钢制蜗杆和铜制蜗轮的制作材料不同,钢的硬度比铜高,蜗杆在向前旋转时,铜制蜗轮受力对硬度较小的钢制蜗杆产生摩擦,并将其牢固紧密地压在一起。
由于钢制蜗杆的硬度高于铜制蜗轮,所以传动的不平衡力可以被牢固地锁住,从而保证了高效稳定的传动效果。
三、蜗杆传动的应用蜗杆传动具有很多优点,如紧凑的结构、高效率、高扭矩、稳定性等。
同时也有一些缺点,如制造难度较大、制造成本高、传动效率低等。
因此,在选择使用蜗杆传动时,需要全面考虑其优缺点和应用情况。
一个常见的应用场景是纺织机械,在制造纤维纺纱机时,采用蜗杆传动来传递较大的扭矩,实现布带收卷以及其他布料加工链环中的转动。
同时,由于蜗杆传动的复杂性,目前也在工业机器人、汽车和液压泵等领域得到广泛应用,也可以用于电动自行车、自行车和其他迷你设备,因其噪声小,结构紧凑等特点。
机械设计基础蜗杆传动

类型与特点
圆柱蜗杆传动
圆柱蜗杆传动具有结构紧 凑、传动比大、工作平稳 、噪音小等优点。常用于 减速装置中。
环面蜗杆传动
环面蜗杆传动的特点是承 载能力高、传动效率高, 但制造和安装精度要求较 高。
锥蜗杆传动
锥蜗杆传动具有较大的传 动比和较紧凑的结构,但 制造和安装精度也较高。
降低摩擦系数
加强冷却和润滑
通过采用先进的表面处理技术或添加减摩 剂等措施,降低蜗杆和蜗轮之间的摩擦系 数,从而减少摩擦损失。
采用有效的冷却和润滑措施,控制传动的工 作温度,以降低热损失和摩擦损失。
05
蜗杆传动的结构设计与制造工艺
结构设计要点
选择适当的蜗杆类型
根据传动要求选择合适的蜗杆类型,如圆柱 蜗杆、环面蜗杆等。
04
蜗杆传动的效率与润滑Biblioteka 效率分析1 2 3
蜗杆传动效率的计算公式
效率 = (输出功率 / 输入功率) × 100%。由于蜗 杆传动中存在滑动摩擦和滚动摩擦,因此其效率 通常低于齿轮传动。
影响蜗杆传动效率的因素
包括蜗杆头数、导程角、摩擦系数、中心距、传 动比等。其中,蜗杆头数和导程角对效率影响较 大。
首先根据蜗杆和蜗轮的相对位置及运动关系,确定作用在蜗杆和蜗轮上的外力 ;然后分析这些外力在蜗杆和蜗轮上产生的内力,包括弯矩、扭矩和轴向力等 。
蜗杆传动的受力特点
由于蜗杆和蜗轮的螺旋角不同,使得作用在蜗杆和蜗轮上的外力产生不同的分 力,这些分力在蜗杆和蜗轮上产生的内力也不同。因此,蜗杆传动的受力分析 较为复杂。
装配顺序与方法
按照先内后外、先难后易的原则进行 装配,注意保证蜗杆和蜗轮的正确啮 合。
蜗杆传动介绍

蜗杆传动特点:
2.传动平稳、无噪声。因蜗杆与蜗轮齿的啮合是连续 的,同时啮合的齿对较多。
3.当蜗杆的螺旋升角小于啮合面的当量摩擦角时,可 以实现自锁。 4.传动效率比较低。当z1=1时,效率h=0.7~0.75; z1=2时,h=0.75~0.82;z1=3~4时,h=0.82~ 0.92。具有自锁时,h=0.4~0.45。 5.因啮合处有较大的滑动速度,会产生较严重的摩擦 磨损,引起发热,使润滑情况恶化,所以蜗轮一般常 用青铜等贵重金属制造。
效率低,传递功率不宜过大,中高速需用价贵的青铜, 制造精度要求高,刀具费用高
表3-26 几种机械传动的基本特性
基本特性
闭式 h 开式 0.90~0.96 ≤25~30 <10000 ≤1000 ≤75 ≤15 2~4 小 短 良 大 100 0.93~0.96 ≤20 (40) <5000 ≤4000 ≤100 齿形链15 滚子链10 ≤5~8 大 中等 差 大 140 0.94~0.96 ≤15~25(斜齿) (200) <10000 ≤50000 ≤3000 ≤10 3~5 大 长 差 小 165
式中 d1--螺杆分度圆直径,mm。 蜗杆导程角与传动效率有关, 导程角大,效率高;导程角小, 可能导致自锁。蜗轮的螺旋角b 与蜗杆的导程角g应数值相等、 旋向相同(图3-55)。
3.螺杆分度圆直径 d1与螺杆直径系数 q 由于切制蜗轮的滚刀必须与蜗杆的形状相 当,为此,对于相同模数的蜗杆,每一种分 度圆直径都必须用一把切制蜗轮的滚刀,这 样,刀具的数量可能太多。为了减少刀具品 种并便于标准化,对于每一个模数其蜗杆分 度圆直径d1只规定少数,见表3-21。螺杆 直径系数用q表示,即q=d1/m。
2.螺杆导程角 g和蜗轮螺旋角 b
蜗杆传动工作原理

蜗杆传动工作原理蜗杆传动是一种常用的传动方式,它由蜗杆和蜗轮组成。
蜗杆是一种螺旋线形状的齿轮,蜗轮则是一种圆盘状的齿轮。
蜗杆传动主要通过蜗杆的螺旋线与蜗轮的齿轮咬合来传递动力。
蜗杆传动具有传动比大、传动平稳、噪音小等优点,因此广泛应用于各个领域。
蜗杆传动的工作原理如下:1.螺旋线齿形:蜗杆的齿形是螺旋线形状的。
螺旋线的角度越大,齿数越少,蜗杆传动的传动比就越大;反之,传动比较小。
螺旋线的螺距越大,传动效率就越高。
2.齿轮齿形:蜗轮的齿形是圆柱面的。
蜗轮的齿数越多,传动效率就越高。
蜗轮的齿数与蜗杆的螺旋线角度呈正比,与蜗杆的螺距呈反比。
3.咬合过程:当蜗杆转动时,蜗轮受到蜗杆螺旋线作用力的影响,开始进行旋转。
蜗轮的旋转产生的力会使蜗杆进行推动,从而实现动力传递。
4.传动比:传动比是指蜗轮转一圈,蜗杆转动的圈数。
传动比等于蜗轮的齿数除以蜗杆的齿数。
蜗杆传动具有以下几个特点:1.传动比大:蜗杆传动的传动比一般较大,通常为1:20至1:300之间。
这使得蜗杆传动适用于需要减速的场合。
2.传动平稳:由于螺杆的齿数较少,蜗杆传动的传动平稳,减小了机械设备的振动和冲击。
因此,蜗杆传动常被用于需要平稳传动的场合。
3.传动效率低:蜗杆传动的咬合面积较小,齿面摩擦力大,因此传动效率低。
一般情况下,蜗杆传动的传动效率约为30%至80%之间。
4.可逆性:蜗杆传动具有较好的不可逆性。
在停机状态下,蜗杆无法迅速被蜗轮带动,相反,蜗轮却可以被蜗杆带动。
5.噪音小:由于蜗杆传动的咬合面积小,齿面摩擦力小,因此产生的噪音也较小。
总结起来,蜗杆传动是一种通过螺旋线齿形的蜗杆和圆齿轮的蜗轮进行咬合来传递动力的传动方式。
它具有传动比大、传动平稳、噪音小等优点,因此被广泛应用于各个领域。
然而,由于传动效率较低,蜗杆传动常常需要与其他传动方式进行组合使用,以提高效率。
第十章 蜗杆传动

b.凑传动比
' ' ' 1 a' 1 ( d d ) [( d 2 xm ) mz 1 2 1 2] 2 2
1 a1 ( d d ) 1 2 2) 2 2 (d1 mz
5.蜗杆传动的几何尺寸计算
见表10-3
互动:在蜗杆传动中,模数不变,选择较大直径系数产生什么后果?(蜗杆刚度和强度提高)
2.2 KT2YF 2.2 KT2YF F 2 [ F ] md1d 2 m d1 z 2
b2
360 cos
d1
Y 0.667
mn m cos
Y 1
2.2 KT2YF 2 m d1 z2 [ F ]
140
(表10-2)定m、d1
YFa2 —— 蜗轮齿形系数,按当量齿数从表10-5查
应用于冶金、矿山、石油等领域中空间两交错 轴间运动与动力传递。
vs v1
§10-2、普通圆柱蜗杆传动的主要参数及几何尺寸计算 1、中间平面:通过蜗杆轴线并垂直于蜗轮轴线的平面 2、在中间平面内,蜗杆 传动相当于齿轮齿条传 动,取该平面的参数为 基准值。 3、主要参数及其选择 1)模数、压力角 正确啮合条件:
2 d2
v2
P
1
d1
v2 vs v1
1 2 3
1 tg / tg ( V )
--啮合摩擦损耗所决定的效率
V
tg 1 2 3 (0.95 ~ 0.97) tg ( v )
互动:为什么蜗杆 传动一般布置在高 速级?
—— 当量摩擦角,查表10-9
节圆改变,蜗轮节圆永远与分度 圆重合。只对蜗轮变位。
3)变位系数计算 a.凑中心距
蜗杆传动原理详解,机械人不可不知

蜗杆传动原理详解,机械人不可不知蜗杆传动:蜗杆传动是在空间交错的两轴间传递运动和动力的一种传动,两轴线间的夹角可为任意值,常用的为90°。
蜗杆传动用于在交错轴间传递运动和动力。
先来一段精彩视频介绍,让您秒懂机械蜗杆传动原理。
2分7秒视频建议WiFi学习哦1.简介蜗杆传动由蜗杆和蜗轮组成,一般蜗杆为主动件。
蜗杆和螺纹一样有右旋和左旋之分蜗杆传动,分别称为右旋蜗杆和左旋蜗杆。
蜗杆上只有一条螺旋线的称为单头蜗杆,即蜗杆转一周,涡轮转过一齿,若蜗杆上有两条螺旋线,就称为双头蜗杆,即蜗杆转一周,涡轮转过两齿。
2.特点(1)传动比大,结构紧凑。
蜗杆头数用Z1表示(一般Z1=1~4),蜗轮齿数用Z2表示。
从传动比公式I=Z2/Z1可以看出,当Z1=1,即蜗杆为单头,蜗杆须转Z2转蜗轮才转一转,因而可得到很大传动比,一般在动力传动中,取传动比I=10-80;在分度机构中,I可达1000。
这样大的传动比如用齿轮传动,则需要采取多级传动才行,所以蜗杆传动结构紧凑,体积小、重量轻。
(2)传动平稳,无噪音。
因为蜗杆齿是连续不间断的螺旋齿,它与蜗轮齿啮合时是连续不断的,蜗杆齿没有进入和退出啮合的过程,因此工作平稳,冲击、震动、噪音都比较小。
(3)具有自锁性。
蜗杆的螺旋升角很小时,蜗杆只能带动蜗轮传动,而蜗轮不能带动蜗杆转动。
(4)蜗杆传动效率低,一般认为蜗杆传动效率比齿轮传动低。
尤其是具有自锁性的蜗杆传动,其效率在0.5以下,一般效率只有0.7~0.9。
(5)发热量大,齿面容易磨损,成本高。
3.圆柱蜗杆圆柱蜗杆传动是蜗杆分度曲面为圆柱面的蜗杆传动。
蜗杆传动其中常用的有阿基米德圆柱蜗杆传动和圆弧齿圆柱蜗杆传动。
①阿基米德蜗杆的端面齿廓为阿基米德螺旋线,其轴面齿廓为直线。
阿基米德蜗杆可以在车床上用梯形车刀加工,所以制造简单,但难以磨削,故精度不高。
在阿基米德圆柱蜗杆传动中,蜗杆与蜗轮齿面的接触线与相对滑动速度之间的夹角很小,不易形成润滑油膜,故承载能力较低。
机械设计蜗杆传动

机械设计蜗杆传动蜗杆传动是一种常用于机械设计中的传动方式,主要是通过蜗杆和蜗轮的相互作用来实现转动的传递。
相较于其他传动方式,蜗杆传动具有传递大扭矩、传动平稳、结构简单等优点,被广泛应用于工程中。
蜗杆传动的基本原理是蜗杆通过蜗轮的直动螺旋轴向推入来产生运动,由于蜗杆的斜度较小,因此受力与传动效率较高。
通常情况下,蜗杆是由高耐磨材料制成,如钢、镍硬铁等。
蜗轮则是由高强度材料制成,如铸铁、淬火钢等。
蜗轮的形状一般为圆柱形,外部有直纹螺旋齿。
在运动过程中,蜗轮齿与蜗杆螺纹齿相互咬合,使蜗轮绕蜗杆转动,并将转动运动传递给其他零部件。
蜗杆传动的优点之一是传递大扭矩。
由于蜗杆的斜度小,因此在相同的尺寸下,可以传递较大的扭矩。
这使得蜗杆传动在一些需要承受大扭矩的设备中得到广泛应用,如起重机械、矿山机械等。
蜗杆传动的另一个优点是传动平稳。
由于蜗轮齿与蜗杆螺纹齿咬合面积大,传动过程中噪音小、振动小,能保证整个机械系统的稳定运行。
这使得蜗杆传动在一些要求稳定性的设备中得到广泛应用,如精密机械、仪器设备等。
蜗杆传动的结构相对简单,易于制造和安装。
传动比可以通过改变蜗杆的斜度来调整,使其适用于不同的工作条件。
此外,蜗杆传动具有自锁功能,可以保持装置的位置不变。
然而,蜗杆传动也存在一些不足之处。
首先,由于蜗轮齿与蜗杆螺纹齿的接触线速度高、接触点压力大,因此在高负荷情况下容易受到磨损和热量的影响。
同时,蜗杆传动的效率较低,一般在30%到90%之间,这意味着有一部分能量在传动过程中会消耗掉。
为了提高蜗杆传动的效率和使用寿命,可以采用以下方法:选择合适的蜗杆和蜗轮材料,如使用高硬度、高韧性的材料制造;改进蜗轮齿形,如使用渐开线螺线齿形代替直纹螺旋齿形;润滑蜗杆传动,如采用有润滑剂的润滑方式;进行散热和冷却,如增加散热片、采用冷却设备等。
总之,蜗杆传动是一种常用的机械传动方式,具有传递大扭矩、传动平稳、结构简单等优点。
在机械设计中,应根据实际工作条件和需求选择合适的蜗杆传动方案,并采取相应的措施提高传动效率和使用寿命。
[教学]蜗轮蜗杆传动总结
![[教学]蜗轮蜗杆传动总结](https://img.taocdn.com/s3/m/d1581dc2e43a580216fc700abb68a98271feacd8.png)
[教学]蜗轮蜗杆传动总结蜗杆的头数选择蜗杆头数z1时,主要考虑传动比、效率和制造三个方面从制造方面,头数越多,蜗杆制造精度要求也越高从提高效率看,头数越多,效率越高;若要求自锁,应选择单头从提高传动比方面,应选择较少的头数;在动力传动中,在考虑结构紧凑的前提下,应很好地考虑提高效率。
当i传动比较小时,宜采用多头蜗杆。
而在传递运动要求自锁时,常选用单头蜗杆。
蜗杆蜗轮传动中应注意事项蜗杆导程角()是蜗杆分度圆柱上螺旋线的切线与蜗杆端面之间的夹角,与螺杆螺旋角的关系为,蜗轮的螺旋角,大则传动效率高,当小于啮合齿间当量摩擦角时,机构自锁。
引入蜗杆直径系数q是为了限制蜗轮滚刀的数目,使蜗杆分度圆直径进行了标准化m一定时,q大则大,蜗杆轴的刚度及强度相应增大;一定时,q小则导程角增大,传动效率相应提高。
蜗杆头数推荐值为1、2、4、6,当取小值时,其传动比大,且具有自锁性;当取大值时,传动效率高。
与圆柱齿轮传动不同,蜗杆蜗轮机构传动比不等于,而是,蜗杆蜗轮机构的中心距不等于,而是。
蜗杆蜗轮传动中蜗轮转向的判定方法,可根据啮合点K处方向、方向(平行于螺旋线的切线)及应垂直于蜗轮轴线画速度矢量三角形来判定;也可用“右旋蜗杆左手握,左旋蜗杆右手握,四指拇指”来判定。
蜗轮蜗杆正确啮合的条件1 中间平面内蜗杆与蜗轮的模数和压力角分别相等,即蜗轮的端面模数等于蜗杆的轴面模数且为标准值;蜗轮的端面压力角应等于蜗杆的轴面压力角且为标准值,即==m ,==2 当蜗轮蜗杆的交错角为时,还需保证,而且蜗轮与蜗杆螺旋线旋向必须相同。
蜗轮及蜗杆机构的特点可以得到很大的传动比,比交错轴斜齿轮机构紧凑两轮啮合齿面间为线接触,其承载能力大大高于交错轴斜齿轮机构蜗杆传动相当于螺旋传动,为多齿啮合传动,故传动平稳、噪音很小具有自锁性。
当蜗杆的导程角小于啮合轮齿间的当量摩擦角时,机构具有自锁性,可实现反向自锁,即只能由蜗杆带动蜗轮,而不能由蜗轮带动蜗杆。
- 1、下载文档前请自行甄别文档内容的完整性,平台不提供额外的编辑、内容补充、找答案等附加服务。
- 2、"仅部分预览"的文档,不可在线预览部分如存在完整性等问题,可反馈申请退款(可完整预览的文档不适用该条件!)。
- 3、如文档侵犯您的权益,请联系客服反馈,我们会尽快为您处理(人工客服工作时间:9:00-18:30)。
第十章蜗杆传动阿讨论题10-1解:如改变蜗杆的回转方向,作用于蜗杆,蜗杆上的径向力F r1、F r2方向不变,而圆周力F t,轴向力F a的方向均与图中相反。
10-2 解:1、3—蜗杆2、4—蜗轮(1)根据蜗杆与蜗轮的正确啮合条件,可知蜗轮2与蜗杆1同旋向——右旋。
为使II轴上所受轴向力能抵消一部分,蜗杆3须与蜗轮2同旋向——右旋,故与之啮合的蜗轮4也为右旋。
(2)II轴和III轴的转向见上图。
(3)10-3 解:闭式蜗杆传动的效率一般包括三部分:啮合效率、轴承效率和溅油损耗的效率。
其中啮合效率为主要部分,它与蜗杆导程角γ和当量磨擦角ρv有关,ρv主要与蜗轮齿圈材料、蜗杆啮面硬度及蜗杆传动的滑动速度v s有关;而起主要作用的为导程角γ。
轴承效率与轴承类型有关。
溅油损耗与回转体浸油深度及宽度、圆周速度和油的粘度等因素有关。
啮合效率η1随γ角的增大而提高,当γ=45°-时,达到最大值η1max,故若γ继续增大则η1将下降,过大的γ使制造较为困难,且在γ>30°后,η1的增长已不明显,故在设计中一般γ角不超过30°。
思考题及习题10-1 解:按蜗杆的形状不同,蜗杆传动可分为:圆柱蜗杆传动、环面蜗杆传动及锥蜗杆传动。
而圆柱蜗杆传动按加工蜗杆时刀刃形状的不同可分为:普通圆柱蜗杆传动和圆弧齿圆柱蜗杆传动。
普通圆柱蜗杆传动由于刀具及加工方法不同、蜗杆齿形不同又分为:阿基米德圆柱蜗杆传动(ZA型),法向直廓圆柱蜗杆传动(ZN型),渐开线圆柱蜗杆传动(ZJ型),锥面包络圆柱蜗杆传动(ZK型)。
阿基米德蜗杆在端面上齿廓为阿基米德螺旋线,在轴面内为直线齿廓,其齿形角为20°,它可在车床上用直线刀刃车削加工,切削刃须通过蜗杆的轴线。
它加工及测量比较方便,但难以磨削,故精度不高,升角大时,车削困难。
法向直廓蜗杆的端面齿廓为延伸渐开线,法面齿廓为直线,它亦不易磨削,特别是较难获得高精度的蜗轮滚刀。
渐开线蜗杆的端面齿廓为渐开线,在切于基圆柱的截面上为直线齿廓,刀具的齿形角应等于蜗杆的基圆柱螺旋角,它可在专用机床上,用平面砂轮磨削,获得较高精度,适于用范成法加工,是圆柱蜗杆中较理想的传动。
锥面包络圆柱蜗杆不能在车床上加工,只能在铣床上铣制并在磨床上磨削,铣刀(或砂轮),回转曲面的包络面即为蜗杆的螺旋齿面,它便于磨削,以得到较高精度,应用日益广泛。
圆弧齿圆柱蜗杆传动、环面蜗杆传动及锥蜗杆传动克服了普通圆柱蜗杆传动承载能力低、效率低、不易磨削、不能粹火、精度等级难于提高等缺点,为提昌应用的蜗杆传动类型。
10-2 解:在中间平面内,阿基米德蜗杆传动就相当于齿条与齿轮的啮合传动,故在设计蜗杆传动时,均取中间平面上的参数(如模数、压力角等)和尺寸(如齿顶圆、分度圆度等)为基准,并沿用齿轮传动的计算关系,而中间平面对于蜗杆来说是其轴面,所以轴向模数和压力角为标准值。
阿基米德蜗杆传动的正确啮合条件是:m x1=m t2=m(标准模数)αx1=αt2=20°γ(导程角)=β(蜗轮螺旋角)且同旋向式中:m x1、αx1——蜗杆的轴向模数,轴向压力角;m t2、αt2——蜗轮的端面模数、端面压力角。
10-3 解:(1)i=w1/w2=n1/n2=z2/z1≠d2/d1;因为蜗杆分度圆直径d1=z1m/tanγ,而不是d1=z1m。
(2)同理:a=(d1+d2)/2≠m(z1+z2)/2;(3)F t2=2000T2/d2≠2000T1i/d2;因为蜗杆传动效率较低,在计算中,不能忽略不计,T2=iηT1。
10-4 解:蜗杆分度圆直径d1=z1m/tanγ,令z1/tanγ=q则d1=mq。
q=d1/m称为蜗杆直径系数。
q与蜗杆头数z1及导程角γ有关。
在蜗杆传动中,为保证蜗杆与配对蜗轮的正确啮合,常用与蜗杆具有同样尺寸的蜗轮滚刀来加工与其配对的蜗轮。
这样,只要有一种尺寸的蜗杆,就得有一种对应的蜗轮滚刀,而d 1=z 1m /tan γ,即同一模数下,当γ、z 1不同时,就有不同直径的蜗杆,因而对每一模数就要配备很多蜗轮滚刀,这是很不经济的,为使刀具数量减少,同时便于滚刀的标准化,则规定每一标准模数相应只有1~4个蜗杆分度圆直径。
10-5 解: 与齿轮传动一样,蜗杆传动的失效形式有齿面点蚀、磨损、胶合和轮齿折断等,但由于蜗杆传动工作齿面间相对滑动速度较大,当润滑不良时,温升过高,胶合和磨损更容易发生。
对材料的选择,要求有一定的强度且具有良好的减摩性、耐磨性及抗胶合性,且易跑合。
蜗杆一般用碳钢或合金钢制成,一般用途的蜗杆,用40、45、50钢进行调质处理,其硬度为220~300HBS ;重要用途(高速重载)的蜗杆,可用20Cr 、20CrMnTi 等进行渗碳淬火,使表面淬硬至58~63HRC ,或用40、45、40Cr 等表面淬火到40~55HRC 。
常用的蜗轮材料为锡青铜、无锡青铜及铸铁等,可按滑动速度v s 选用。
当v s >6m/s 时选用铸造锡青铜,ZCuSn10P1、ZCuSn10Zn2、ZCuSn5Pb5Zn5;当v s <6m/s 时选用无锡青铜如ZCuAl9Fe4Ni4、ZCuAl8Mn13Fe3Ni2、ZCuAl19Fe3、ZCuZn38Mn2Pb2等;一般低速v s ≤2m/s ,对效率要求不高时,可采用铸铁HT150、HT200等。
10-6解: 当蜗轮材料选得不同时,其失效形式不同,故其许用接触应力也不同。
当蜗轮材料为锡青铜时,其承载能力按不产生疲劳点蚀来确定,因为锡青铜抗胶合能力强,但强度低,失效形式为齿面点蚀,其许用接触应力按不产生疲劳点蚀来确定。
当蜗轮材料为铸铁或无锡青铜时,其承载能力主要取决于齿面胶合强度,因这类材料抗胶合能力差,失效形式为齿面胶合,通过限制齿面接触应力来防止齿面胶合,许用接触应力按不产生胶合来确定。
10-7解: 对于连续工作的闭式蜗杆传动进行热平衡计算其目的是为了限制温升、防止胶合。
蜗杆传动由于效率低,工作时发热量大,在闭式传动中,如果散热不良温升过高,会使润滑油粘度降低,减小润滑作用,导致齿面磨损加剧,以至引起齿面胶合,为使油温保持在允许范围内,对连续工作的闭式蜗杆传动要进行热平衡计算,如热平衡不能满足时可采用以下措施:①增大散热面积A :加散热片,合理设计箱体结构。
②增大散热系数K s :在蜗杆轴端加风扇以加速空气的流通;在箱体内装循环冷却管道,采用压力喷油循环润滑。
10-8 解:由热平衡验算式(10-13)C t A K P t s ︒=+⨯⨯-⨯=+-=5.132202.1105.7)82.01(1000)1(1000011η t 1>[t 1]=70~90°C 该减速器不能连续工作。
10-9 解:(1)、(2)、(3)见上图(4)如蜗杆回转方向改变,各力之间的大小不变,径向力F r 方向也不变,F t1、F t2、F a1、F a2的方向与上图中的方向相反。
10-10 解:采用阿基米德蜗杆传动1、选择材料及热处理方式蜗杆选用45钢,表面淬火处理,齿面硬度>45HRC 。
蜗轮材料选用ZCuSn10Pb1,砂型铸造。
2、确定蜗杆头数z 1和蜗轮齿数z 2由表10-2,取z 1=2,则z 2=iz 1=20×2=40蜗轮转速n 2=n 1/i =1460/20=73r/min3、按齿面接触强度确定主要参数由式10-11m 2d 1≥222][9000⎪⎪⎭⎫ ⎝⎛H E z Z KT σ(1)T 2=800N·m(2)确定载荷系数K ,由表10-5查得K A =1.1(连续工作),假设v 2<3m/s ,取K v =1;因工作载荷稳定,蜗轮齿圈材料软,易磨合,取K β=1。
则 K =K A K v K β=1.1×1×1=1.1(3)确定许用接触应力[σH ][σH ]=Z N ×[σH0]由表10-6查得[σH0]=200MPaN 2=60an 2t =60×1×73×15000=6.57×107N 2在取值范围(2.6×105≤N 2≤25×107)内,则79.01057.61010877827=⨯==N Z N 故[σH ]=0.79×200=158MPa (4)确定弹性系数Z E =160MPa(5)确定蜗杆模数m 和分度圆直径d 1m 2d 1≥1.5076158401608001.19000][90002222=⎪⎭⎫ ⎝⎛⨯⨯⨯⨯=⎪⎪⎭⎫ ⎝⎛H E z Z KT σmm 3 查表10-1得m =8mm ,d 1=80mm4、验算蜗轮圆周速度v 2,相对滑动速度v s蜗轮分度圆直径d 2=mz 2=8×40=320mm则 v 2=1000607332010006022⨯⨯⨯=⨯ππn d =1.22m/s<3m/s与原假设相符,取K v =1合适。
由tan γ=mz 1/d 1=8×2/80=0.2,得γ=11.31°v s =︒⨯⨯⨯⨯=⨯⨯31.11cos 100060146080cos 10006011πγπn d =6.23m/s 5、验算蜗轮齿根弯曲强度 由式(10-12) m d d Y KT Fa F 2122cos 1530γσ=≤[σF ](1)上式中 K 、T 2、d 1、d 2、m 和γ同前(2)确定Y Fa2由z v2=z 2/cos 3γ=40/cos 311.31°=42.42,查表10-8得Y Fa2=1.51(3)确定许用弯曲应力[σF ][σF ]=Y N ·[σF0]由表10-9查得[σF0]=51MPa由前计算可知N 2=6.57×107,因N 2的取值范围为105≤N 2≤25×107,故628.01057.61010976926=⨯==N Y N 因此[σF ]=0.628×51=32.03MPa83208051.131.11cos 8001.11530cos 15302122⨯⨯⨯︒⨯⨯⨯==m d d Y KT Fa F γσ =9.73MPa<[σF ]=32.03MPa蜗轮轮齿弯曲强度足够。
6、热平衡计算由热平衡验算式(10-14)011)1(1000t AK P t s +-=η≤[t 1] (1)上式中 87.0~86.0)18.131.11tan(31.11tan )96.0~95.0()tan(tan )96.0~95.0(=︒+︒︒=+=v ργγη (查表10-4得:ρv =1.18°)取η=0.865(2)确定蜗杆传递的功率P 1P 1=T 1n 1/9550=T 2n 1/(9550i η)=800×1460/(9550×20×0.865)=7.07kW(3)确定K s ,自然通风,取K s =12W/m 2·°C(4)设环境温度t 0=20°C ,取[t 1]=80°C将以上数据代入式(10-14)估算散热面积A =32.112)2080(07.7)865.01(1000)]([)1(1000011=--=--s K t t P ηm 2 7、主要几何参数m =8mm ,z 1=2,z 2=40,γ=11.31°=11°18’36’’d 1=80mm ,d 2=320mm ,a =21(d 1+d 2)=21(80+320)=200mm 蜗轮喉圆直径 d a2=d 2+2h a2=320+2×1×8=336mm齿顶圆直径 d a1=d 1+2h a1=80+2h a1=80+2×1×8=96mmd e2=d a2+1.5m =336+1.5×8=348mm齿根圆直径 d f1=d 1-2h f1=80-2×1.2×8=60.8mmd f2=d 2-2h f2=320-2×1.2×8=300.8mm8、结构设计从略。