拉深工艺与拉深设备
拉深模的典型结构

1-定位板 2-下模板 3-拉深凸模 4-拉深凹模
无压边装置的 首次拉深模
拉深工艺与拉深模设计
1-模柄 2-上模座 3-凸模固定板 4-弹簧 5-压边圈 6-定位板 7-凹模 8-下模座 9-卸料螺钉 10-凸模
正装拉深模
拉深工艺与拉深模设计
1-上模座 2-推杆 3-推件板 4-锥形凹模 5-限位柱 6-锥形压边圈 7-拉深凸模 8-固定板 9-下模座
拉深工艺与拉深模设计
拉深模的典型结构
一、首次拉深模
1. 无压边装置的简单拉深模
2. 有压边装置的拉深模
(1)正装拉深模
(2)倒装拉深模
①橡皮压边装置
弹性压边装置 ②弹簧压边装置
③气垫式压边装置
压边装置
带限位装置的压边圈
刚性压边装置 带刚性压边装置的拉深模
拉深工艺与拉深模设计
拉深模的典型结构
二、以后各次拉深模
1-凸凹模 2-反拉深凸模 3-拉深凸凹模 4-卸料板 5一导料板 6-压边圈 7-落料凹模
落料、正、反拉深模
拉深工艺与拉深模设计
1-压边圈 2-凹模固定板
3-冲孔凹模 4-推件板 5-凸模固定板 6-垫板 7-冲孔凸模 8-拉深凸模 9-限位螺栓 10-螺母 11-垫柱 12-拉深切边凹 模 13-切边凸 模 14-固定块
拉深工艺与拉深模设计
无压边装置的以后各次拉深模
拉深工艺与拉深模设计
1-推件板 2-拉深凹模 3-拉深凸模 4-压边圈 5-顶杆 6-弹簧
有压边装置的以后各次拉深模
拉深工艺与拉深模设计
1-顶杆 2-压边圈 3-凸凹模 4-推杆 5-推件板 6-卸料板 7-落料凹模 8-拉深凸模
落料拉深复合模
4.1拉深工艺及拉深件的结构工艺性

二. 拉深变形过程
方法:拉深网格试验
二. 拉深变形过程
(1)底部(d内)网格不变形; (2)拉深前等距同心圆 不等距水平圆周线 (3)拉深前等角度射线 等距、平行于底面的平行线 (4)拉深前筒壁上的扇形网格,拉深后变成矩形网格。 (5)测量工件高度,高度H>(D-d)/2
二. 拉深变形过程
拉深过程中毛坯各部分变化
一. 拉深工艺
拉深概念
利用模具将平板毛 坯冲压成各种开口的空 心零件,或将已制成的 开口空心件压制成其他 形状和尺寸空心件的一 种冲压加工方法。
一. 拉深工艺
生活中的拉深件
一. 拉深工艺
拉深工艺分类
➢按壁厚变化情况分: ① 一般拉深(工件壁厚不变) ② 变薄拉深(工件壁厚变薄)
➢按使用的毛坯的形状分:
1Cr18Ni9Ti不锈钢等。
较硬材料拉深时,需增加工序改变性能: ①先退火处理后拉深,最后淬火。 ②加热后拉深。
四.拉深件的结构工艺性
拉深件结构工艺性
拉深件的形状:简单、对称,对应r相等 尽量避免半敞开及非对称的空心件,否则
应设计成对称组合的拉深,然后剖开。
四.拉深件的结构工艺性
拉深件高度:尽量小一些
① 第一次拉深(使用平板毛坯) ② 以后的各次拉深(以开口空心件为毛坯)
二. 拉深变形过程
如图a圆形薄片,剪去图中阴影部分,再将剩余部分沿直径d圆 周弯折,然后焊接,就得到一个图b的直径为d,高度为(D-d)/2 的直圆筒形件。
二. 拉深变形过程
拉深变形过程:
用相同直径大小的圆形平板毛坯,在拉深成直圆筒形 件的过程中,并没有去除多余材料,多余材料流向哪里?
一次成形零件的拉深高度应满足: ①无凸缘筒形件: h≤(0.5~0.7)d
拉深工艺与拉深模设计(二)

4.凸、凹模工作表面粗糙度 凹模: 型腔表面Ra0.8μm, 圆角表面Ra0.4μm 凸模: Ra1.6μm∼0.8μm 5.拉深凸模的出气孔尺寸
4.6.4 凸、凹模的结构形式
拉深凸模与凹模的结构形式取决于工件的形状、尺寸以 及拉深方法、拉深次数等工艺要求,不同的结构形式对拉 深的变形情况、变形程度的大小及产品的质量均有不同的 影响。 当毛坯的相对厚度较大,不易起皱,不需用压边圈压边 时,应采用锥形凹模。
3.压边圈的形式 (1)平面压边圈 适用于一般拉深模
(2)弧形压边圈 适用于 (t / D ×100) < 0.3 , 且小凸缘和较大圆角半径
(3)带限位装置的压边圈 适于拉深板料较薄或带较宽凸缘的零件
(4)局部压边的压边圈 ) 适于拉深带宽凸缘工件
(5)带拉深筋的压边圈 适用于凸缘特别小或半球形工件
2.中间拉深的凸、凹模尺寸
Dd i = Di 0
+δ d 0 −δ p
D p i = (Ddi − Z )
式中:
Di—各工序的基本尺寸。 —
3.凸、凹模制造公差 非圆形凸、凹模的制造公差可根据工件的公 差来选定。工公差为 ITl3 级以上时, 和 可按IT6 ~8 级取,工件公差在 ITl4 级以下时, 按 ITl0 级 取;圆形凸凹模制造公差查表获得。
4.5 其它旋转体件的拉深
学习目标: 了解其它常见旋转体拉深件的结构、拉深过 程;理解它们的拉深工序安排。 教学要求: 能够计算阶梯圆筒件的拉深次数,确定各种 形状的阶梯圆筒件的拉深工序安排;理解难拉深 的球面、锥形等曲面旋转体拉深件的工艺方案。
4.5.1 阶梯圆筒件的拉深 1. 拉深次数 一次拉深的条件:
4.8 盒形件的拉深
拉深工艺和拉深模设计

公差、材料上旳要求,掌握拉深件工序安排旳一般 原则。
教学要求: 根据弯曲件旳构造工艺性要求改善拉深件旳结
构设计;能够根据拉深件旳工艺条件,拟定拉深件 圆角半径,拟定带孔拉深件旳孔旳位置。
4.2.1 对拉深件形状尺寸旳要求
1)拉深件形状应尽量简朴、对称,尽量一次拉 深成形。
1)孔位应与主要构造面(凸缘面)在同一平面, 或孔壁垂直该平面,便于冲孔与修边在同一 道工序中完毕。
2)拉深件侧壁上旳冲孔与底边或凸缘边旳距离 h 2d t
3)拉深件凸缘上旳孔距:
D1 (d1 3t 2r2 d )
4)拉深件底部孔距:
d d1 2r1 t
4.2.3 拉深件旳精度等级 主要指其横断面旳尺寸精度;一般在IT13级
2)叠加各段中间层面积,求出制件中间层面积;
3)根据“等面积原则”求出毛坯直径。
D
4S
4
f
式中
S——毛坯面积(涉及修边余量); f——简朴旋转体拉深件各部分面积; D——毛坯直径。
案例分析: 带凸缘制件
无凸缘制件
将制件分割为: 1)1/4凹球环 2)圆柱
3)1/4凸球环 4)圆板
计算:
1)1/4凹球环
要求:
1)rpg≥t,一般取:rpg≥(35)t 2)rpg<t,增长整形工序,每整形一次,rpg
可减小1/2。
pg
pg
py
3.矩形拉深件壁间圆角半径rpy 矩形拉深件壁间圆角半径rpy:
指矩形拉深件旳四个壁旳转角半径。
要求:rpy≥3t及rpy≥H/5
pg
pg
py
4.2.2 拉深件上旳孔位布置
拉深工艺的特点

拉深工艺的特点
拉深工艺是一种常见的表面处理技术,其主要特点如下:
1. 高精度:拉深工艺能够实现高精度的加工,可根据设计要求制造出复杂的几何形状和弯曲度。
2. 高效率:通过采用拉伸成形的方式,拉深工艺能够大幅提高工作效率,减少生产时间和人力成本。
3. 节约材料:与传统的切削加工相比,拉深工艺不需要额外的切削材料,最大限度地减少了材料的浪费。
4. 优良的材料性能:拉深工艺可以改善材料的力学性能和表面质量,提高产品的使用寿命和可靠性。
5. 强度高:由于拉深工艺能够使材料发生塑性变形,因此拉深后的产品具有较高的强度和刚度。
6. 适用性广:拉深工艺适用于多种材料,如金属、合金和塑料等,可用于制作各种零部件和产品。
总之,拉深工艺具有高精度、高效率、节约材料、优良的材料性能、高强度和广泛适用性等特点,广泛应用于工业制造和加工领域。
第四章拉深工艺及拉深模具设计复习题答案

第四章拉深工艺及拉深模具设计复习题答案填空题拉深是是利用拉深模将平板毛坯压制成开口空心件或将开口空心件进一步变形的冲压工艺。
拉深凸模和凹模与冲裁模不同之处在于,拉深凸、凹模都有一定的圆角而不是锋利的刃口,其间隙一般稍大于板料的厚度。
拉深系数m是拉深后的工件直径和拉深前的毛坯直径的比值,m越小,则变形程度越大。
拉深过程中,变形区是坯料的凸缘部分。
坯料变形区在切向压应力和径向拉应力的作用下,产生切向压缩和径向伸长的变形。
对于直壁类轴对称的拉深件,其主要变形特点有:(1)变形区为凸缘部分;(2)坯料变形区在切向压应力和径向拉应力的作用下,产生切向压缩与径向的伸长,即一向受压、一向收拉的变形;(3)极限变形程度主要受传力区承载能力的限制。
拉深时,凸缘变形区的起皱和筒壁传力区的拉裂是拉深工艺能否顺利进行的主要障碍。
拉深中,产生起皱的现象是因为该区域内受较大的压应力的作用,导致材料失稳_而引起。
拉深件的毛坯尺寸确定依据是面积相等的原则。
拉深件的壁厚不均匀。
下部壁厚略有减薄,上部却有所增厚。
在拉深过程中,坯料各区的应力与应变是不均匀的。
即使在凸缘变形区也是这样,愈靠近外缘,变形程度愈大,板料增厚也愈大。
板料的相对厚度t/D越小,则抵抗失稳能力越愈弱,越容易起皱。
因材料性能和模具几何形状等因素的影响,会造成拉深件口部不齐,尤其是经过多次拉深的拉深件,起口部质量更差。
因此在多数情况下采用加大加大工序件高度或凸缘直径的方法,拉深后再经过切边工序以保证零件质量。
拉深工艺顺利进行的必要条件是筒壁传力区最大拉应力小于危险断面的抗拉强度。
正方形盒形件的坯料形状是圆形;矩形盒形件的坯料形状为长圆形或椭圆形。
用理论计算方法确定坯料尺寸不是绝对准确,因此对于形状复杂的拉深件,通常是先做好拉深模,以理论分析方法初步确定的坯料进行试模,经反复试模,直到得到符合要求的冲件时,在将符合要求的坯料形状和尺寸作为制造落料模的依据。
影响极限拉深系数的因素有:材料的力学性能、板料的相对厚度、拉深条件等。
拉伸工艺与拉深模具设计
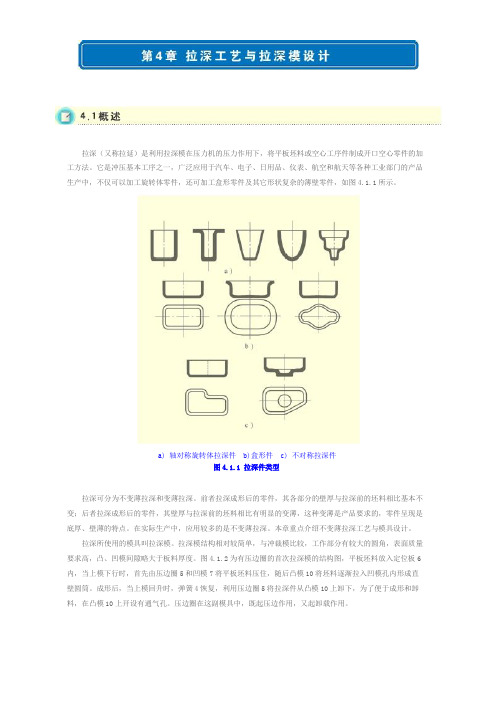
1.凸缘变形区的起皱 拉深过程中,凸缘区变形区的材料在切向压应力 σ 的作用下,可能会产生失稳起皱,如图 4.2.6 所示。 凸缘区会不会起皱,主要决定于两个方面:一方面是切向压应力 σ 的大小,越大越容易失稳起皱;另一方面 是凸缘区板料本身的抵抗失 稳的能力,凸缘宽度越大,厚度越薄,材料弹性模量和硬化模量越小,抵抗失稳 能力越小。这类似于材料力学中的压杆稳定问题。压杆是否稳定不仅 取决于压力而且取决于压杆的粗细。在 拉深过程中 是随着拉深的进行而增加的,但凸缘变形区的相对厚度 也在增大。这说明拉深过程中失稳起皱的 因素在增加而抗失稳起皱的能力也在增加。
图 4.2.4
在厚度方向,由于压料圈的作用,产生压应力 ,通常 和 的绝对值比 大得多。厚度方向上材料的的变形 情况取决于径向拉应力 和切向压应力 之间比例关系,一般在材料产生切向压缩和径向伸长的同时,厚度有所 增厚,越接近于外缘,板料增厚越多。如果不压料( =0),或压料力较小( 小),这时板料增厚比较大。当 拉深变形程度较大,板料又比较薄时,则在坯料的凸缘部分,特别是外缘部分,在切向压应力 作用下可能失 稳而拱起,产生起皱现象。
此外,影响极限拉深系数的因素还有拉深方法、拉深次数、拉深速度、拉深件的形状等。 采用反拉深、软模拉深等可以降低极限拉深系数;首次拉深极限拉深系数比后次拉深极限拉深 系数小;拉深速度慢,有利于拉深工作的正常进行,盒形件角部拉深系数比相应的圆筒形件的
拉深系数小。 3.极限拉深系数的确定 由于影响极限拉深系数的因素很多,目前仍难采用理论计算方法准确确定极限拉深系数。
拉深工艺及拉深模设计

拉深工艺及拉深模设计本章内容简介:本章在分析拉深变形过程及拉深件质量影响因素的基础上,介绍拉深工艺计算、工艺方案制定和拉深模设计。
涉及拉深变形过程分析、拉深件质量分析、圆筒形件的工艺计算、其它形状零件的拉深变形特点、拉深工艺性分析与工艺方案确定、拉深模典型结构、拉深模工作零件设计、拉深辅助工序等。
学习目的与要求:1.了解拉深变形规律、掌握拉深变形程度的表示;2.掌握影响拉深件质量的因素;3.掌握拉深工艺性分析。
重点:1. 拉深变形特点及拉深变形程度的表示;2.影响拉深件质量的因素;3.拉深工艺性分析。
难点:1.拉深变形规律及拉深变形特点;2.拉深件质量分析;3.拉深件工艺分析。
拉深:利用拉深模将一定形状的平面坯料或空心件制成开口空心件的冲压工序。
拉深工艺可以在普通的单动压力机上进行,也可在专用的双动、三动拉深压力机或液压机上进行。
拉深件的种类很多,按变形力学特点可以分为四种基本类型,如图5-1所示。
图5-1 拉深件示意图5.1 拉深变形过程分析5.1.1 拉深变形过程及特点图5-2所示为圆筒形件的拉深过程。
直径为D、厚度为t的圆形毛坯经过拉深模拉深,得到具有外径为d、高度为h的开口圆筒形工件。
图5-2 圆筒形件的拉深1.在拉深过程中,坯料的中心部分成为筒形件的底部,基本不变形,是不变形区,坯料的凸缘部分(即D-d的环形部分)是主要变形区。
拉深过程实质上就是将坯料的凸缘部分材料逐渐转移到筒壁的过程。
2.在转移过程中,凸缘部分材料由于拉深力的作用,径向产生拉应力,切向产生压应力。
在和的共同作用下,凸缘部分金属材料产生塑性变形,其“多余的三角形”材料沿径向伸长,切向压缩,且不断被拉入凹模中变为筒壁,成为圆筒形开口空心件。
3.圆筒形件拉深的变形程度,通常以筒形件直径d与坯料直径D的比值来表示,即m=d/D(5-1)其中m称为拉深系数,m越小,拉深变形程度越大;相反,m越大,拉深变形程度就越小。
5.1.2 拉深过程中坯料内的应力与应变状态拉深过程是一个复杂的塑性变形过程,其变形区比较大,金属流动大,拉深过程中容易发生凸缘变形区的起皱和传力区的拉裂而使工件报废。
3 拉深工艺与拉深模设计
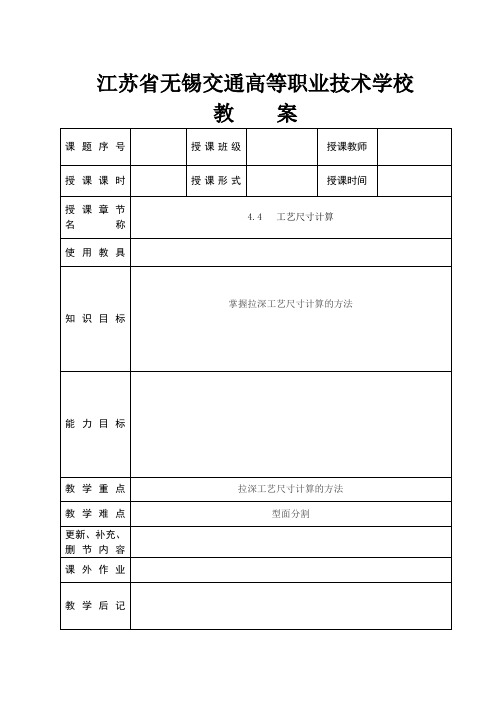
教案
课题序号
授课班级
授课教师
授课课时
授课形式
授课时间
授课章节
名称
4.4工艺尺寸计算
使用教具
知识目标
掌握拉深工艺尺寸计算的方法
能力目标
教学重点
拉深工艺尺寸计算的方法
教学难点
型面分割
更新、补充、
删节内容
课外作业
教学后记
课堂教学安排
教学过程
主要教学内容及步骤
2.4排样(layout)
②当拉深材料中的应力不大时,允许采用不带填料的油剂润滑剂。
③当拉深圆锥形类零件时,为了用增加摩擦抗力来减少起皱,同时又要求不断通入润滑液进行冷却时,则一般采用乳化液。
④在变薄拉深时,润滑剂不仅是为了减少摩擦,同时又起到冷却模具的作用,因此不应采用干摩擦。在拉深钢质零件时,往往在毛坯表面上镀铜或磷化处理,使毛坯表面形成一层与模具的隔离层,它能贮存液体和在拉深过程中具有“自润滑”性能。在拉深不锈钢,高温合金等粘模严重、强化剧烈的材料时,一般也需要对毛坯表面进行“隔离层”处理。
拉深方法:
1)浅锥形件(t/d2≤0.25~0.30)浅锥形件一般只要一次拉深成形。
通常采用增加工艺凸缘用压边圈或带有拉深筋的模具;或使用液压和橡皮柔性凸(凹)模拉深。
2)中锥形件(t/d2≤0.3~0.7)这类制件大多为一次拉深成形。
当t/D>0.025时,可一次成形,不需要压边,只需要在行程末进行校正整形。
这类制件具有三个变形区:
压边圈下面的圆环部分拉深变形区;
凹模口内至变形过渡环处的拉深变形区;
制件顶部至过渡环处的胀形变形区。
在模具设计和工艺过程设计时,是采用制件的相对高度h/d和材料的相对厚度t/D为依据进行设计。
拉深盒型件拉深工艺
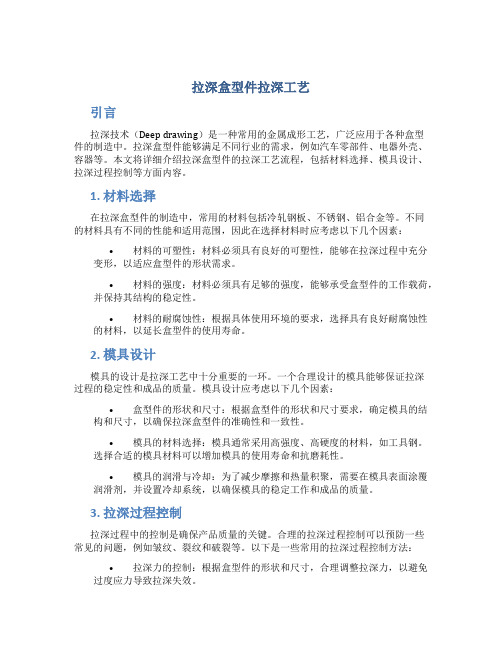
拉深盒型件拉深工艺引言拉深技术(Deep drawing)是一种常用的金属成形工艺,广泛应用于各种盒型件的制造中。
拉深盒型件能够满足不同行业的需求,例如汽车零部件、电器外壳、容器等。
本文将详细介绍拉深盒型件的拉深工艺流程,包括材料选择、模具设计、拉深过程控制等方面内容。
1. 材料选择在拉深盒型件的制造中,常用的材料包括冷轧钢板、不锈钢、铝合金等。
不同的材料具有不同的性能和适用范围,因此在选择材料时应考虑以下几个因素:•材料的可塑性:材料必须具有良好的可塑性,能够在拉深过程中充分变形,以适应盒型件的形状需求。
•材料的强度:材料必须具有足够的强度,能够承受盒型件的工作载荷,并保持其结构的稳定性。
•材料的耐腐蚀性:根据具体使用环境的要求,选择具有良好耐腐蚀性的材料,以延长盒型件的使用寿命。
2. 模具设计模具的设计是拉深工艺中十分重要的一环。
一个合理设计的模具能够保证拉深过程的稳定性和成品的质量。
模具设计应考虑以下几个因素:•盒型件的形状和尺寸:根据盒型件的形状和尺寸要求,确定模具的结构和尺寸,以确保拉深盒型件的准确性和一致性。
•模具的材料选择:模具通常采用高强度、高硬度的材料,如工具钢。
选择合适的模具材料可以增加模具的使用寿命和抗磨耗性。
•模具的润滑与冷却:为了减少摩擦和热量积聚,需要在模具表面涂覆润滑剂,并设置冷却系统,以确保模具的稳定工作和成品的质量。
3. 拉深过程控制拉深过程中的控制是确保产品质量的关键。
合理的拉深过程控制可以预防一些常见的问题,例如皱纹、裂纹和破裂等。
以下是一些常用的拉深过程控制方法:•拉深力的控制:根据盒型件的形状和尺寸,合理调整拉深力,以避免过度应力导致拉深失效。
•润滑效果的控制:合适的润滑剂类型和涂覆方式可以减少摩擦,防止盒型件与模具之间的粘连,从而提高产品的表面质量。
•模具温度的控制:通过控制冷却系统的温度,可以有效地降低模具和盒型件的温度,从而减少热裂纹的发生。
•拉深速度的控制:拉深速度的选择要根据材料的可塑性和盒型件的复杂程度来确定,以保证拉深过程的稳定性和成品的质量。
第 4 章 拉深工艺与拉深模
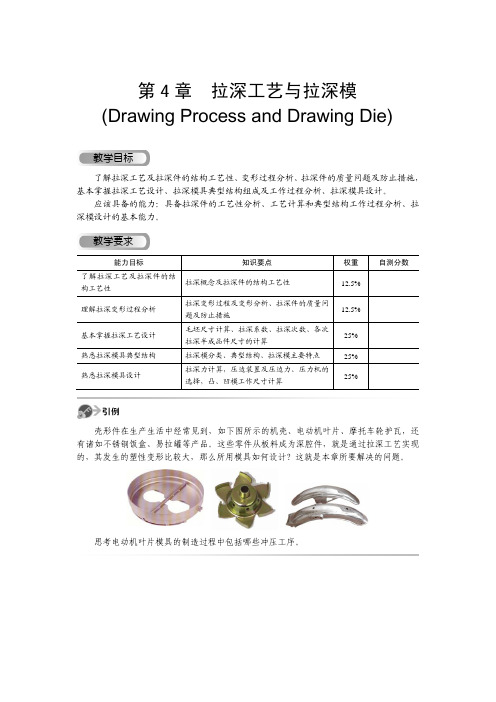
第4章 拉深工艺与拉深模 (Drawing Process and Drawing Die)教学目标了解拉深工艺及拉深件的结构工艺性、变形过程分析、拉深件的质量问题及防止措施,基本掌握拉深工艺设计、拉深模具典型结构组成及工作过程分析、拉深模具设计。
应该具备的能力:具备拉深件的工艺性分析、工艺计算和典型结构工作过程分析、拉深模设计的基本能力。
教学要求能力目标知识要点权重自测分数了解拉深工艺及拉深件的结构工艺性拉深概念及拉深件的结构工艺性12.5%理解拉深变形过程分析拉深变形过程及变形分析、拉深件的质量问题及防止措施12.5%基本掌握拉深工艺设计毛坯尺寸计算、拉深系数、拉深次数、各次拉深半成品件尺寸的计算25%熟悉拉深模具典型结构拉深模分类、典型结构、拉深模主要特点25%熟悉拉深模具设计拉深力计算,压边装置及压边力、压力机的选择,凸、凹模工作尺寸计算25% 引例壳形件在生产生活中经常见到,如下图所示的机壳、电动机叶片、摩托车轮护瓦,还有诸如不锈钢饭盒、易拉罐等产品。
这些零件从板料成为深腔件,就是通过拉深工艺实现的,其发生的塑性变形比较大,那么所用模具如何设计?这就是本章所要解决的问题。
思考电动机叶片模具的制造过程中包括哪些冲压工序。
模具设计与制造·108· ·108·4.1 拉深工艺与拉深件工艺性(Drawing Process andProcessability of Drawing Part)4.1.1 拉深件与拉深工艺分类(Drawing Part and Classification of Drawing Process)拉深是指利用模具将平板毛坯冲压成各种开口的空心零件,或将已制成的开口空心件压制成其他形状和尺寸空心件的一种冲压加工方法。
1.拉深件分类冲压生产中,拉深的种类很多,各种拉深件按变形力学特点可以分为表4-1所示的基本类型。
表4-1 拉深件的分类拉深件名称 拉深件简图变形特点 轴对称零件 圆筒形件 带凸缘圆筒形件 阶梯形件1.拉深过程中变形区是坯料的凸缘部分,其余部分是传力区;2.坯料变形区在切向压应力和径向拉应力作用下,产生切向压缩与径向伸长的一向受压一向受拉的变形;3.极限变形程度主要受坯料传力区承载能力的限制 盒形件 带凸缘盒形件 其他形状零件 1.变形性质同前,区别在于一向受拉一向受压的变形在坯料周边上分布不均匀,圆角部分变形大,直边部分变形小; 2.在坯料的周边上,变形程度大与变形程度小的部分之间存在着相互影响与作用 直壁类拉深件 非轴对称零件 曲面凸缘的零件 除具有前项相同的变形性质外,还有如下特点:1.因零件各部分高度不同,在拉深开始时有严重的不均匀变形;2.拉深过程中,坯料变形区内还要发生剪切变形轴对称零件球面类零件 锥形件 其他曲面零件 拉深时坯料变形区由两部分组成: 1.坯料外部是一向受拉一向受压的拉深变形;2.坯料的中间部分是受两向拉应力的胀形变形区 曲面类拉深件非轴对称零件 平面凸缘零件 曲面凸缘零件 1.拉深时坯料的变形区也是由外部的拉深变形区和内部的胀形变形区所组成,但这两种变形在坯料中的分布是不均匀的; 2.曲面凸缘零件拉深时,在坯料外周变形区内还有剪切变形第4章 拉深工艺与拉深模 ·109··109·虽然这些零件的冲压过程都叫做拉深,但是由于其几何形状不同,在拉深过程中,它们的变形区位置、变形性质、毛坯各部位的应力状态和分布规律等都有相当大的差别,所以在确定拉深的工艺参数、工序数目与工艺顺序等方面都不一样。
1.拉深工艺基础

模块一拉深工艺基础
图4-5 拉深件的网格实验
生拉应力和
的共同作用下产生切向压缩与径向伸长变形而被逐渐拉人凹模。
产生了压应力但通常和
的绝对值比大得多。
厚度方向的变形决定于径向拉应力和切向压应力之间的比例关系,
(小
作用下可能失稳而拱
图4-6拉深过程的应力与应变状态
2.凸缘圆角部分(B区)
径向受拉应力
受压应力而压缩,
压应力。
不大,而径向拉应力
力和切向拉应力
当拉深应力较大且接近材料的强度极限
分析拉深过程中可能产生的质量问题及控制方式?
图4-1 金属保护筒。
第4章 拉深

构、拉深模工作零件设计、变薄拉深以及冲挤切口、辅助工
序等。
本章重点
1. 2. 3. 4. 5. 拉深变形规律及拉深件质量影响因素; 拉深工艺计算方法; 拉深工艺性分析与工艺方案制定; 拉深模典型结构与结构设计; 拉深工艺与拉深模设计的方法和步骤。
难点
1.拉深变形规律及拉深件质量影响因素;
2.拉深工艺计算 ; 3.其他形状零件的拉深变形特点 ;
4.5.4 拉深功与功率计算
对于不变薄拉深的拉深功按下式计算:
W=F平均h×10-3=CFmaxh×10-3
拉深功率P(KW)按下式计算:
P=(Wn)/(60×750×1.36)
压力机的电机功率率P电(KW)按下式计算:
P电=(KWn)/(60×750×1.36×η 1×η 2)
拉深力-行程图
4.6 拉深模工作部分结构参数确定
4.6.1 凸、凹模圆角半径的确定
1.凹模圆角半径R凹 内容包括:凸、凹模圆角半径,拉深模凸、凹模间隙和凸、 凹模工作部分尺寸。本节以圆筒件为例进行介绍 。 首次(包括只有一次)拉深凹模圆角半径可按下式计算: 或
以后各次拉深凹模圆角半径应逐渐减小,一般按下式确定: (i=2、3、…、n) 以上计算所得凹模圆角半径一般应符合rA≥2t的要求。
(1)采用查表法确定拉深次数:
由t/D×100=1.28,h/D=3.7查表4-11得拉深次数n=4 由m总=0.256,t/D×100=1.28查表4-12得拉深次数n=4
(2)采用计算法确定拉深次数:
由公式4-14得
n=1+[lg20-lg(0.51×78)]/lg0.77拉深力的计算
最大拉深力可以用下式来进行计算:
Fmax=3(σ b+σ s)(D-d-r凹)t
模具设计第五章 拉深工艺及拉深模
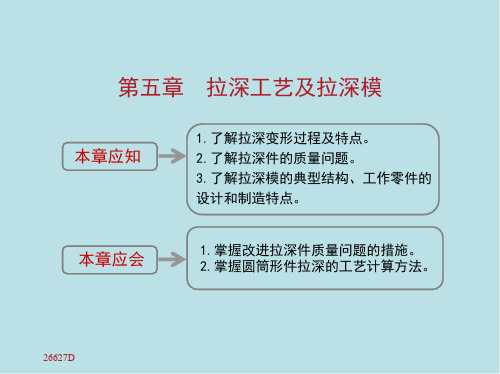
七、拉深模制造特点
4)由于拉深过程中材料厚度变化及回弹变形等原因,复杂拉深件 坯料形状和尺寸设计值与实际值往往存在误差,坯料形状和尺寸 最终是在试模后确定。 2.拉深模凸、凹模的加工方法
26627D
七、拉深模制造特点
表5-4 拉深凸模常用加工方法
26627D
七、拉深模制造特点
表5-5 拉深凹模常用加工方法
一、拉深变形分析
26627D
图5-3 拉深件的网格变化
二、拉深件的主要质量问题
1.起皱
26627D
图5-4 起皱破坏
二、拉深件的主要质量问题
(1)影响起皱的主要因素 1)坯料的相对厚度t/D。 2)拉深系数m。 (2)起皱的判断 在分析拉深件的成形工艺时,必须判断该冲件 在拉深过程中是否会发生起皱,如果不起皱,则可以采用无压边 圈的模具;否则,应该采用带压边装置的模具,如图5-5所示。
26627D
图5-10 圆筒形件
三、圆筒形件的拉深
解 由于t=2mm>1mm,所以按中线尺寸计算。 1)确定修边余量。 2)计算坯料展开直径。 3)确定是否用压边圈。 4)确定拉深次数。 5)确定各次拉深直径。 6)求各工序件高度。 7)画出工序图,如图5-11所示。
26627D
四、拉深模的典型结构
26627D
图5-9 多次拉深时筒形件直径的变化
三、圆筒形件的拉深
2.拉深系数
表5-3 圆筒形件带压边圈时的极限拉深系数
3.拉深次数 4.圆筒形件拉深各次工序尺寸的计算
(1)工序件直径 从前面介绍中已知,各次工序件直径可根据各 次的拉深系数算出。
Hale Waihona Puke 26627D三、圆筒形件的拉深
拉深工艺与拉深模设计

82449 9(76 3.8)6.2 87.584 87.52 20.572 20m8m
案例分析(毛坯尺寸计算) 电容器外壳 由图4-2可得:
d1=17.6mm d2=21.2mm h1=26.8mm h=28.6mm r=1.8mm h/d=28.6÷21.2=1.35
r
y
α
O
y
a)
b)
圆心重心位置
a)圆弧与水平线相交
b)圆弧与垂直线相交
O
2)作图解析法 ①将零件按母线分成若干个简单的几何部分;
②求出各简单几何部分的重心至旋转轴的旋转半径r1、r2、 r3……rn;并求出各部分母线长度l1、l2、l3……ln;则其 乘积之和lr= l1r1+l2r2+l3r3+……+lnrn;
当零件尺寸标注在外形时
D dD m a0 x .7 5 0 d
D pD m a0 x.7 5 Z0 p
当零件尺寸标注在内形时
dddm in 0.40 d
dpdm in 0.4Z0 p
D0 -Δ
Z /2
D +Δ 0
Z /2
Dp
dp
Dd
a)
零件尺寸标注
dd
b)
对于多次拉深,工序尺寸无需严格要求,凸、凹
(2)凸模圆角半径的确定 首次拉深,凸模圆角半径
rp1=(0.7~1.0)rd1 最后一次拉深,凸模圆角半径
r—零件圆角半径。
rpn=r
如果r<t时,则rpn≥t,然后整形。
中间各次拉深,凸模圆角半径
rpi-1=0.5(di-1-di-2t)
式中 di-1,di—各工序的外径(mm)。
第4章 拉深工艺与拉深模
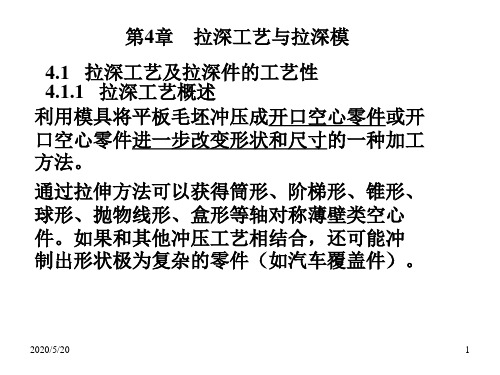
2013-7-29
10
面积相等原则:将三角 形阴影部分切除,把留 下的狭条沿直径d的圆周 折弯后竖起来并加以焊 接,就得到一个直径为d, 高度为h=(D-d)/2的圆 筒件,说明被切除的三 角形阴影部分在模具的 作用下发生了塑性流动, 从而使拉深后的工件高 度增加了Δh,所以h> (D-d)/2。
rn rpn 2
42 2013-7-29
(3)半成品高度尺寸的计算
D2 rn h n 0.25 d d n 0.43 d d n 0.32rn n n
4 拉深工艺力的计算 (1)压边力 是否采用压边圈?查表4.6(P125) 压边力过大,会增加坯料拉入凹模的拉力,容易拉 裂工件;过小,则不能防止凸缘起皱。
2013-7-29
30
(2)拉深件毛坯尺寸的确定 根据拉深后工件表面积与拉深前毛坯表面积相等 这一原则来计算
(1)确定修边余量:查表4.1、4.2(P119)查处Δh (2)计算工件表面积,分解成若干简单几何体 (3)求出毛坯尺寸
2013-7-29 31
表4.1筒形件的修边余量(mm)
2013-7-29
2013-7-29
24
拉深起皱后,轻者 凸缘变形区材料仍 能被拉进凹模,会 使工件口部产生波 纹,影响工件的质 量。
2013-7-29
25
起皱严重时,起皱的凸缘 材料不能通过凸、凹模间 隙而引起拉深件拉裂。 拉深是否起皱与σ 3大小 有关,也与毛坯的相对厚 度t/D有关,而σ 3与拉深 的变形程度有关。而每次 拉深的变形程度较大而 t/D较小时就会起皱。 防止起皱的方法是压边圈, 或者减小拉深变形程度、 加大毛坯厚度。
2013-7-29
43
第四章-拉深工艺及拉深模具设计--复习题答案
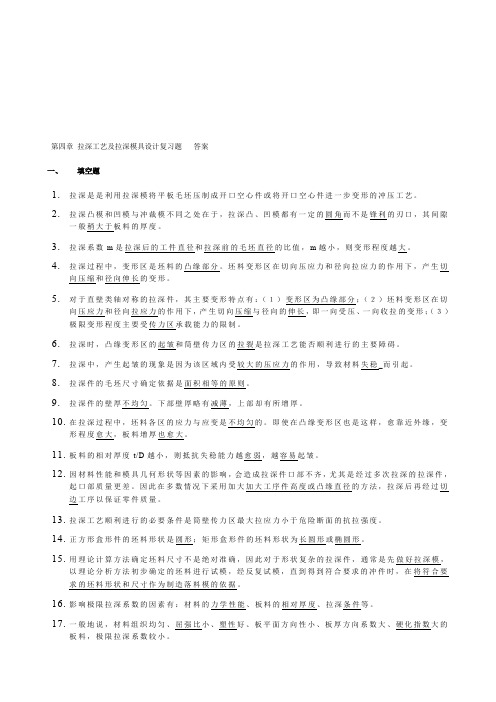
第四章拉深工艺及拉深模具设计复习题答案一、填空题1.拉深是是利用拉深模将平板毛坯压制成开口空心件或将开口空心件进一步变形的冲压工艺。
2.拉深凸模和凹模与冲裁模不同之处在于,拉深凸、凹模都有一定的圆角而不是锋利的刃口,其间隙一般稍大于板料的厚度。
3.拉深系数m是拉深后的工件直径和拉深前的毛坯直径的比值,m越小,则变形程度越大。
4.拉深过程中,变形区是坯料的凸缘部分。
坯料变形区在切向压应力和径向拉应力的作用下,产生切向压缩和径向伸长的变形。
5.对于直壁类轴对称的拉深件,其主要变形特点有:(1)变形区为凸缘部分;(2)坯料变形区在切向压应力和径向拉应力的作用下,产生切向压缩与径向的伸长,即一向受压、一向收拉的变形;(3)极限变形程度主要受传力区承载能力的限制。
6.拉深时,凸缘变形区的起皱和筒壁传力区的拉裂是拉深工艺能否顺利进行的主要障碍。
7.拉深中,产生起皱的现象是因为该区域内受较大的压应力的作用,导致材料失稳_而引起。
8.拉深件的毛坯尺寸确定依据是面积相等的原则。
9.拉深件的壁厚不均匀。
下部壁厚略有减薄,上部却有所增厚。
10.在拉深过程中,坯料各区的应力与应变是不均匀的。
即使在凸缘变形区也是这样,愈靠近外缘,变形程度愈大,板料增厚也愈大。
11.板料的相对厚度t/D越小,则抵抗失稳能力越愈弱,越容易起皱。
12.因材料性能和模具几何形状等因素的影响,会造成拉深件口部不齐,尤其是经过多次拉深的拉深件,起口部质量更差。
因此在多数情况下采用加大加大工序件高度或凸缘直径的方法,拉深后再经过切边工序以保证零件质量。
13.拉深工艺顺利进行的必要条件是筒壁传力区最大拉应力小于危险断面的抗拉强度。
14.正方形盒形件的坯料形状是圆形;矩形盒形件的坯料形状为长圆形或椭圆形。
15.用理论计算方法确定坯料尺寸不是绝对准确,因此对于形状复杂的拉深件,通常是先做好拉深模,以理论分析方法初步确定的坯料进行试模,经反复试模,直到得到符合要求的冲件时,在将符合要求的坯料形状和尺寸作为制造落料模的依据。
- 1、下载文档前请自行甄别文档内容的完整性,平台不提供额外的编辑、内容补充、找答案等附加服务。
- 2、"仅部分预览"的文档,不可在线预览部分如存在完整性等问题,可反馈申请退款(可完整预览的文档不适用该条件!)。
- 3、如文档侵犯您的权益,请联系客服反馈,我们会尽快为您处理(人工客服工作时间:9:00-18:30)。
最易起皱的位置:
凸缘边缘区域
凹模工作部分的几何形状
平端面凹模拉深时,毛坯首次拉深不起皱的条件是 :
t (0.09 ~ 0.17)(1 t )
D
D
用锥形凹模首次拉深时,材料不起皱的条件是:
t 0.031 d
D
D
如果不能满足上述式子的要求,就要起皱。在这种情况 下,必须采取措施防止起皱发生。
拉深工艺与拉深设备
概述 拉深:指将一定形状的平板毛坯通过拉深模冲压
成各种形状的开口空心件,或以开口空心 件为毛坯通过拉深进一步使空心件改变形 状和尺寸的一种冷冲压加工方法。
拉深变形过程
类型:不变薄拉深、变薄拉深
不变薄拉深:在拉深过程中不产生较大的变薄, 筒壁与筒底厚度较一致的拉深工艺。
变薄拉深:指以空心开口零件为毛坯,通过减小 壁厚成形零件的拉深工艺。
3.防止拉裂的措施
(1)合理选择拉深系数;(有合理的高径比) (2)合理选材;(屈强比要小,塑性要好) (3)选择合理的凸凹模圆角半径; (4)选用合理的压边力; (5)适当润滑。(单面润滑)
三. 边缘高低不一致及有折皱
边缘高低不一致的原因: 1)毛坯与凸、凹模中心不合; 2)材料厚度不均; 3)凹模圆角半径和凹模间隙不均。
2.拉深时材料的转移
图中三角形部分 称为“多余三角形” 拉深时这部分材料 发生塑性变形转移 到筒高部分。
3.筒形件拉深的网格变化
底部的扇形网格保持不变;筒壁部分拉深前的扇形网格变 成拉深后的矩形网格。
.
二 筒 形 件 拉 深 过 程 中 坯 料 的 应 力 应 变 状 态
厚度变化
筒形件拉深的质量问题及防止措施
表2-3为无凸缘圆筒件的修边余量;
表2-4为带凸缘圆筒件的修边余量。
按图得:
4
D2
A1
A2
A3
Ai
故
D
4
Ai
A1 d (H r)
A2
4
2r(d 2r) 8r 2
A3
整理后可得坯料直径为:
4
(d
2r)2
D (d 2r)2 4d (H r) 2r(d 2r) 8r 2
d 2 4dH 1.72dr 0.56r 2
质量问题:(动画)
起皱——拉深件凸缘周围产生的波浪形连续弯曲现象。 拉裂——拉深件底部圆角与筒臂相切处出现的撕裂现象。 拉深凸耳——拉深件口端出现有规律的高低不平现象。 时效开裂——拉深成形后,由于受撞击或振动,甚至存放 一段时间后出现的口部开裂现象。
下面主要分析起皱和拉裂的原因及防止措施
一.起皱
1.起皱现象
起皱——拉深 件凸缘周围产 生的波浪形连 续弯曲现象。
2.起皱的产生原因
料薄或压缩变形力过大 ——塑性失稳——起皱
凸缘宽度越大,厚度 越薄,材料弹性模量越 小,抵抗失稳能力越小, 越容易失稳起皱。
切向压应力越大, 越容易失稳起皱。
板料的屈强比小,则 屈服极限小,变形区内的 切向压应力也相对减小, 因此板料不容易起皱。
四.边缘有折皱的原因: 凹模圆角半径太大,压边圈压不到最后流进
凹模且起皱的材料。
解决: 1)减小凹模圆角半径; 2)采用弧形压边圈。
二、筒形件的拉深
拉深毛坯尺寸的确定原则: 体积不变原理(拉深前毛坯表面积等于拉深后零
件的表面积 )、相似性原理。 毛坯的计算方法:等重量、等体积、分析图解法、
作图法。
1.等重量法 :已有拉深件样品时,使用等重量法来求毛 坯直径会非常方便。 2.等体积法 :适用于变薄拉深件。 3.等面积法:不变薄拉深工序用来计算毛坯尺寸的依据。
计算原则:按等面积(即拉深前后材料面积不变) 原则进行计算,再加上修边余量。
由于材料的各向导性以及拉深时金属流动条件的差异,拉深 后工件口部不平,通常拉深后需切边,因此计算毛坯尺寸时应在 工件高度方向上(无凸缘件)或凸缘上增加修边余量 。
数学计算法: 1)将制件分成若干简单几何形状(包括修边余
量),以其中间层进行计算;
注:厚度小于1mm的拉深件,可根据工件外壁尺寸计算
2)叠加各段中间层面积,求出制件中间层面积;
3)根据“等面积原则”求出毛坯直径。
D
4S
4
f
式中
S——毛坯面积(包括修边余量); f——简单旋转体拉深件各部分面积; D——毛坯直径。
二.拉裂
1.拉裂现象
拉深件底部圆角与
பைடு நூலகம்
筒臂相切处出现的撕裂现象。
主要取决于:
一方面是筒壁传力区中的拉应力; 另一方面是筒壁传力区的抗拉强度。
2.产生拉裂的原因 当筒壁拉应力超过筒壁材料的抗拉强度时,拉深件就
会在底部圆角与筒壁相切处——“危险断面”产生破裂。 主要原因有四:材料塑性差; 压边力过大; 工件高径比大;凸凹模圆角半径小。
拉深件
了解拉深工艺 一、拉深变形过程
圆筒形件是最典型的拉深件。 1.变形现象 平板圆形坯料的凸缘 ——弯曲绕过凹模圆角, 然后拉直——形成竖直筒壁。
变形区——凸缘; 已变形区——筒壁; 不变形区——底部。 底部和筒壁为传力区。
(a) 拉深初始阶段
(b) 拉深过程中 (c) 拉深结束阶段
1—凸模;2—压边圈;3—凹模
3.防止起皱的措施
主要措施有二:压边和反拉深
压边——在凹模上口面配置压 边圈,压边圈的下面(工作面) 距凹模上口面的间隙略大于料厚, 在拉深过程中,压边圈给毛坯有 一定的压力,使毛坯在此间隙中 流动,以限制毛坯的起皱。
压边圈有弹性和刚性之分。
加大平面板料厚度t/(Dtd0),降低σ3的影响。
减小变形程度(降低拉深件 的高度),减小σ3大小。
2 拉深系数
拉深系数:指用于表示拉深变形程度的工艺指数。 其值为拉深后制件直径与拉深前毛坯 直径之比值。
m=d/D
若需经过多次拉深方能成形,则:
首次拉深
m1=d1/D
以后各次拉深
m2=d2/d1 m3=d3/d2
……
mn=dn/dn-1 m总=d/D=m1•m2•m3•…•mn
式中:
m——拉深系数; d——拉深后制件直径; D——拉深前毛坯直径; m1、m2、m3、…、mn——各次的拉深系数; d1、d2、d3、…、dn-1、dn——各次拉深制件的直径;
m总——需多次拉深成形制件的总拉深系数。 注意:拉深系数系愈小,表示拉深变形程度愈大。
如果m取得过小,会使拉深件起皱、断裂或严重变薄超差。 极限拉深系数[m]
极限拉深系数:指当拉深系数减小至使拉深件起皱、断 裂或严重变薄超差时的临界拉深系数。