催化剂装填
催化剂装填注意事项
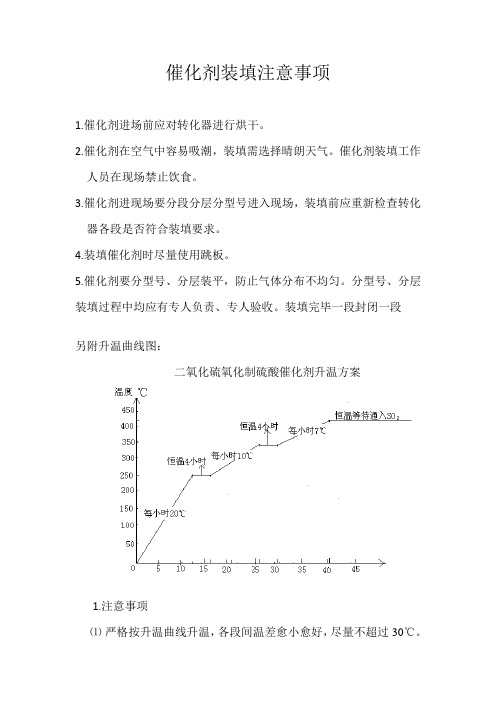
催化剂装填注意事项
1.催化剂进场前应对转化器进行烘干。
2.催化剂在空气中容易吸潮,装填需选择晴朗天气。
催化剂装填工作人员在现场禁止饮食。
3.催化剂进现场要分段分层分型号进入现场,装填前应重新检查转化器各段是否符合装填要求。
4.装填催化剂时尽量使用跳板。
5.催化剂要分型号、分层装平,防止气体分布不均匀。
分型号、分层装填过程中均应有专人负责、专人验收。
装填完毕一段封闭一段
另附升温曲线图:
二氧化硫氧化制硫酸催化剂升温方案
1.注意事项
⑴严格按升温曲线升温,各段间温差愈小愈好,尽量不超过30℃。
⑵升温过程中,要注意保持升温速度的平稳,防止超温、垮温。
⑶接气时一段温度在400~420℃之间,末段温度高于300℃。
⑷尽量开大主风机气量使温度往下推。
⑸接气时气量控制为正常气量的1/4~1/3,SO2含量为4%以下。
⑹接气时要防止超温,一段出口温度必须控制在600℃以下。
⑺当一段催化剂出口温度开始下降时,及时调整气浓及气量。
⑻当第三段出口和第五段出口温度升至320℃时为升温结束,可
通入SO2气体进行硫化饱和。
⑼在升温期间干燥循环酸浓度不得低于92.5%,注意及时换酸。
催化剂装填前注意事项

第一部分:催化剂装填前注意事项1、催化剂装填的目的:装填好坏直接对催化剂床层气流的均匀分布,以及降低床层阻力,能有效发挥催化剂的效能,对今后系统的正常生产,节能降耗乃至延长催化剂的使用寿命都会带来直接影响。
因此催化剂在装填过程中,必须严格按照催化剂装填方案进行,必须尽可能防止破损,防止架桥现象。
2、催化剂装填应具备的条件:2.1系统设备、管线吹扫工作已全部结束,并经检查验收合格。
2.2合成塔顶部封头、人孔、管线等与催化剂装填工作相关联需拆开的部位已经拆开并进行了封口保护措施2.3容器及周围现场清理打扫干净。
2.4催化剂装填所需物资、人员、工器具准备齐全,且装填人员已经过安全培训合格,振动器安装完毕。
塔内件校正并清洗热电偶套管,洗完需通过干燥空气吹干。
2.5催化剂装填的记录报表准备齐全。
2.6现场工作棚,催化剂存放棚安装完毕,防雨措施齐备。
3、催化剂的装填方法及技术要求:3.1为了防止在装填过程中,催化剂过多的吸收空气中的水分,装填催化剂时应选择晴朗、干爽的天气,不要在阴、雨天装填;催化剂不要长时间暴露在空气中,特别是潮湿的地方更需引起注意。
3.2催化剂装填前应进行过筛,以免将催化剂内粉尘带入塔内,增加催化剂床层阻力。
3.3催化剂的装填方法为撒布法,为了使催化剂装填均匀,采用分区、分段计量的方法,即横截面积沿圆周分成四个区,沿催化剂床层的高度每2m为一段,催化剂自漏斗进入塔内换热板间,每个单元装填等量的催化剂,先装填(80~90)%,然后根据测量的高度,用小勺填平补齐,力求装填均匀,使催化剂各处松紧一致。
3.4为避免催化剂在塔中发生“架桥”现象,在装填过程中,要分段多点测量装填高度,确保催化剂装填均匀一致,并间断开启振动器填实。
同时核对装填数量与高度是否相符,核对装填的规格型号是否和塔内的要求相符,并记录后再依次进行下一段的装填。
3.5认真做好装填记录,装填完毕,催化剂密度应大于或等于设计值的99%。
催化剂装填方式
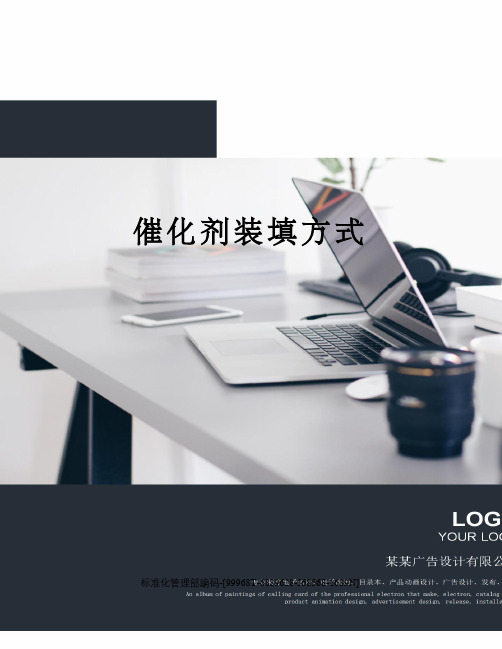
催化剂装填方式标准化管理部编码-[99968T-6889628-J68568-1689N]普通装填又叫疏相装填、布袋装填、稀相装填,和密相的其区别在于装填过程中有无外界推动力来提高催化剂的装填量和装填均匀性。
密相装填可以提高处理量,空速小,径向温差小,装填速度快,运行时间长。
催化剂的密相填装初始压降高,疏相填装压降低,随着装置的运行,密相填装的催化剂比后着要好稀相装填需要人员进行耙平;密相装填借助密相装填器进行装填,不借助人力。
密相装填比稀相装填堆积密度大,装填密实,装填量多.催化剂装填分为普通装填(疏相装填、袋式装填)和密相装填两种。
其区别在于装填过程中有无使用外界推动力来提高催化剂的装填量和装填均匀性。
普通装填方法因其多采用很长的帆布袋作为催化剂从反应器顶部向窗层料位的的输送管子而被称为布袋装填法,实际上,普通装填法中也有较多厂家不用帆布袋而改用金属舌片管来输送催化剂的。
由于普通装填法简单易行,人员上几乎不需要特别的培训,设备上不需要专利技术,因此被国内许多炼油企业所采用。
密相装填法由ARCO技术公司、法国TOTAL公司、UOP公司、Chevron公司等发明,采用密相装填法,可以将催化剂在反应器内沿半径方向呈放射性规整地排列,从而减少催化剂颗粒间的孔隙,提高催化剂的装填密度,通常,可以比普通装填法多装重量10%~25%的催化剂。
密相装填除了可以多装催化剂外,由于装填过程中催化剂颗粒在反应器横截面上规整排列,因此其沿反应器纵向、径向的装填密度也非常均匀。
密相装填与普通(稀相)装填相比,催化剂堆积密度大,反应器内装填催化剂量增大,脱硫起始温度低,脱氮相对体积活性增加7-22%。
采用密相装填时压降会相对增加,但密相装填压降升速比稀相装填要低,故在使用中期或末期压降可能比稀相装填要低。
催化剂的密相装填,可以确保物料的流量分布均匀,以最大限度地、充分地利于催化剂。
与传统的布袋装填方法相比较,催化剂的密实装填具有如下优点:①????应器可多装填催化剂,提高加工能力或延长周期、提高产品质量;②处理量相同时,密相装填的重量空速较小,可以使催化剂的运转温度降低;③处理量相同时,密相装填运转周期更长;④催化剂床层装填均匀,紧密一致,可避免床层塌陷、沟流等现象的发生,从而避免“热点”的产生;⑤催化剂床层径向温度均匀,可以提高反应的选择性。
催化剂的装填..

保护剂的装填顺序是:按照床层容垢能力大小,脱金属能力由强 到弱。脱硫氮活性逐渐增加的顺序及优化比例的进行装填。
Add your company slogan
密箱装填几个最重要的参数
装填速度:通过调节喷嘴间隙大小 装填密度 装填器喷头到催化剂料面的距离
床层径向的均匀性(滴流床反应器) 装填质量 可以增加催化剂的装填量 轴向的紧密型和级配型
决定催化剂的床层的压降速度 和催化剂是否发生迁移
分级装填法
是指采用一种或数种不同尺寸大小、不同形状、不同孔容、 不同活性的高孔隙率活性和惰性瓷球、保护剂系列装填于主 催化剂床层上部,使床层从上到下颗粒逐渐变小、床层孔隙 率逐步减低的分级过渡装填方法。
催化剂装填方案
1 3 2 催化剂的装填技术 密相装填
3 4
装填步骤
各填充物料的作用
一、催化剂的装填技术
催化剂装填作业由两道工序组成: 第一道工序是把催化剂送
输送法 密相输送 第二道工序是用装填设备把催化剂装填到反应器的床层中。 普通装填(袋式装填/疏相装填)
密相装填
下 床 层
各填充物料的作用
卸料管:防止在此部分不流动的“死区”内发生化学反应和结焦。
瓷球
上部:
容纳杂质,防止和延缓运行刷造成催化剂料面的变化, 避免沟流发生中压降的上升,防止高物流冲。
下部:起到支撑催化剂床层,防止反应器中小颗粒的催化剂堵
塞出口收集器。
脱除原料中的结垢物,延缓压力上升
保护剂
密相装填优缺点
1、 反应器内可多装填催化剂,使装置总处理量增加。 2、 处理量相同时,密相装填的重量空速较小,可使催 化剂初期运转温度降低。 3、处理量相同时,密相装填的催化剂运转周期延长。 4、 催化剂床层装填均匀,紧密一致,可避免床层 陷、沟流等现象的发生,从而避免“热点”的产生。 5、 催化剂床层径向温度均匀,可以提高反应的选择性。 6、床层压降高
费托合成催化剂选择与处理—催化剂的装填与卸料(煤制油技术课件)

01
催化剂的装填
3 催化剂补充
对合成反应器内失活和流失催化剂的补充,这时合成反应器处 于正常操作阶段,合成反应器内的温度、压力都较高,催化剂的补充 加入量比较小。催化剂加入时需要注意保持合成反应器的操作平稳, 防止由于催化剂加入时产生液泛现象。在催化剂加入合成反应器前, 需要根据加入量提前将合成反应器的液位降低。保障在催化剂加入后 合成反应器操作液位的稳定。
还原反应器还原好的催化剂加入到合成反应器中,分合成反应 器开车加入和对合成反应器内流失、失活催化剂的补充两种方式。
01
催化剂的装填
2 开车加入
合成反应器内还没有催化剂,催化剂的加入需要时间较长,在 催化剂加入前,合成反应器的温度、压力维持在正常操作水平。在催 化剂全部加入结束前,需根据催化剂加入量控制进合成反应器的合成 气流量,注意保持合成反应器的操作平稳,催化剂加入速度可根据还 原反应器与合成反应器的压差调整。
02
催化剂的卸出
(1)紧急情况下还原反应器需要卸出催化剂时,首先还原反 应器系统降压,降至1.0MPa。
(2)确认渣蜡减压罐接收正常,调节压力调节阀开度,继续 给还原反应系统降压,待还原反应系统压力降到0.6~0.8MPa时, 关闭调节阀,还原反应器系统维持一定的压力。开启还原反应器卸 料口阀门,向渣蜡减压罐卸料。催化剂浆料卸出后,关闭催化剂卸 料阀。
煤间接液化 -催化剂的装填与卸出
目录
01 催化剂的装填 02 催化剂的卸出
01
催化剂的装填
费托合成采用浆态床反应器, 浆态床反应器的催化剂实行在线 补充加入,可以实现合成反应器 的连续操作运行。
01
催化剂的装填
1 催化剂装填
正常生产时,催化剂在还原反应器内还原后再补充到合成反应 器内。还原反应器催化剂装填采用程序控制加催化剂,还原反应器装 填重柴后,启动催化剂加料程序顺序控制。
催化剂装填方案
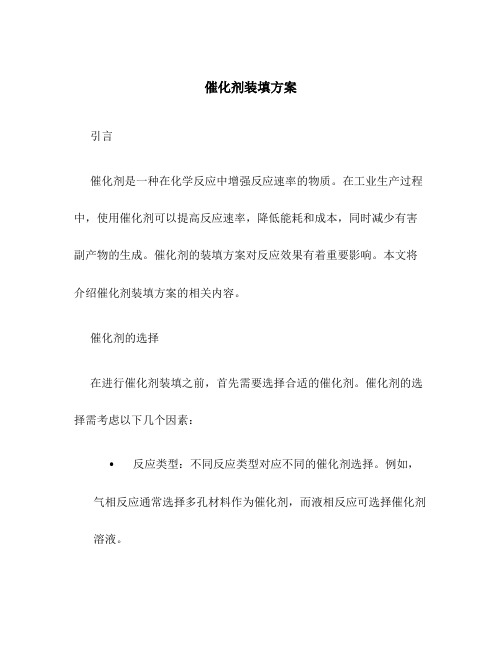
催化剂装填方案引言催化剂是一种在化学反应中增强反应速率的物质。
在工业生产过程中,使用催化剂可以提高反应速率,降低能耗和成本,同时减少有害副产物的生成。
催化剂的装填方案对反应效果有着重要影响。
本文将介绍催化剂装填方案的相关内容。
催化剂的选择在进行催化剂装填之前,首先需要选择合适的催化剂。
催化剂的选择需考虑以下几个因素:•反应类型:不同反应类型对应不同的催化剂选择。
例如,气相反应通常选择多孔材料作为催化剂,而液相反应可选择催化剂溶液。
•反应性能:催化剂对目标反应的催化活性和选择性是选择催化剂的重要指标。
一般而言,高活性和高选择性的催化剂能够提高反应效率。
•耐久性:催化剂需要具有较好的耐久性,能在长时间使用中保持相对稳定的催化性能。
•经济性:催化剂的成本也是选择催化剂的一个重要因素。
需要综合考虑催化剂的价格、使用寿命和性能等因素。
催化剂的物理形态催化剂通常以固体、液体或气体的形态存在。
下面将分别介绍这三种催化剂的装填方案。
固体催化剂的装填固体催化剂通常以颗粒、粉末或填料的形式存在。
固体催化剂的装填方式有以下几种:1.床层填料装填:将固体催化剂填充到反应器的床层中。
这种装填方式适用于颗粒或粉末状的催化剂。
填充后要保证床层的均匀性,以免发生流动不畅或堵塞等问题。
2.水平装填:将固体催化剂均匀地铺在反应器内的水平层上。
这种装填方式适用于某些对流动有一定要求的反应,如气相催化反应。
3.包埋装填:将固体催化剂填充到容器的孔隙中。
这种装填方式适用于颗粒状催化剂,使催化剂能够充分接触反应物。
液体催化剂的装填液体催化剂通常以溶液的形态存在。
装填液体催化剂时,可以采用以下方式:1.注入装填:将液体催化剂通过管道或注射器注入到反应器中。
这种装填方式适用于小型反应器或实验室规模的反应。
2.循环装填:将液体催化剂通过循环泵或搅拌器循环注入到反应器中,保持催化剂与反应物的接触。
这种装填方式适用于大规模工业生产过程。
气体催化剂的装填气体催化剂通常以气体的形态存在。
催化剂装填
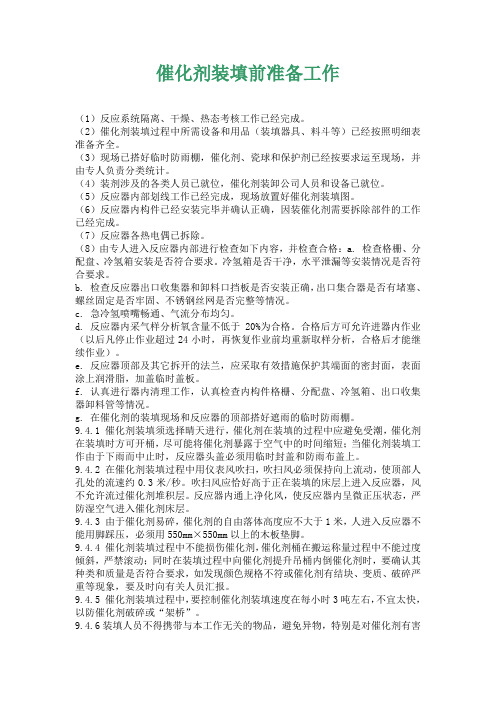
催化剂装填前准备工作(1)反应系统隔离、干燥、热态考核工作已经完成。
(2)催化剂装填过程中所需设备和用品(装填器具、料斗等)已经按照明细表准备齐全。
(3)现场已搭好临时防雨棚,催化剂、瓷球和保护剂已经按要求运至现场,并由专人负责分类统计。
(4)装剂涉及的各类人员已就位,催化剂装卸公司人员和设备已就位。
(5)反应器内部划线工作已经完成,现场放置好催化剂装填图。
(6)反应器内构件已经安装完毕并确认正确,因装催化剂需要拆除部件的工作已经完成。
(7)反应器各热电偶已拆除。
(8)由专人进入反应器内部进行检查如下内容,并检查合格:a. 检查格栅、分配盘、冷氢箱安装是否符合要求。
冷氢箱是否干净,水平泄漏等安装情况是否符合要求。
b. 检查反应器出口收集器和卸料口挡板是否安装正确,出口集合器是否有堵塞、螺丝固定是否牢固、不锈钢丝网是否完整等情况。
c. 急冷氢喷嘴畅通、气流分布均匀。
d. 反应器内采气样分析氧含量不低于20%为合格。
合格后方可允许进器内作业(以后凡停止作业超过24小时,再恢复作业前均重新取样分析,合格后才能继续作业)。
e. 反应器顶部及其它拆开的法兰,应采取有效措施保护其端面的密封面,表面涂上润滑脂,加盖临时盖板。
f. 认真进行器内清理工作,认真检查内构件格栅、分配盘、冷氢箱、出口收集器卸料管等情况。
g. 在催化剂的装填现场和反应器的顶部搭好遮雨的临时防雨棚。
9.4.1 催化剂装填须选择晴天进行,催化剂在装填的过程中应避免受潮,催化剂在装填时方可开桶,尽可能将催化剂暴露于空气中的时间缩短;当催化剂装填工作由于下雨而中止时,反应器头盖必须用临时封盖和防雨布盖上。
9.4.2 在催化剂装填过程中用仪表风吹扫,吹扫风必须保持向上流动,使顶部人孔处的流速约0.3米/秒。
吹扫风应恰好高于正在装填的床层上进入反应器,风不允许流过催化剂堆积层。
反应器内通上净化风,使反应器内呈微正压状态,严防湿空气进入催化剂床层。
9.4.3 由于催化剂易碎,催化剂的自由落体高度应不大于1米,人进入反应器不能用脚踩压,必须用550mm×550mm以上的木板垫脚。
催化剂装填

催化剂装填第一节准备工作一、催化剂装填前应具备的条件1、反应系统干燥结束,反应器降至常温(任意一点反应器温度小于60℃)。
系统压缩空气置换结束,系统中氧含量>20%(v)。
2、反应系统压力降至常压,反应系统无爆炸气(爆炸气分析合格),反应器顶部大盖具备打开条件。
3、反应器安全隔离(1)按照隔离方案,反应器所有接口加盲板或者都打开,使反应器与装置其它部分完全隔离(盲板见表一、隔离见图二)。
拆掉反应器入口大盖短节以便进人,进料线盲死。
出口短节拆除,出口管线盲死,急冷氢、冲洗氢以及压降测量引线全部盲死,以防氮气或氢气从冷氢接口或压降接口泄漏至反应器中。
对不能用盲板隔离而用阀门隔离的部位,关阀后用铁丝捆绑固定,若有放空阀,开放空阀,并在上述阀门上挂上警示牌“装剂期间,禁动此阀”。
5、反应器顶部新鲜水、氮气、仪表风、工业风线等作好明显标志,防止混用。
装置仪表风和氮气相串的部位加盲板隔离。
6、电动卷扬机、抽真空器、供风用的空压机试运正常。
7、现场安装临时照明,反应器内接24V照明电,保证夜间作业。
8、催化剂装填方案置于现场,并做好看板。
(催化剂装填方案见表六)二、催化剂装填的准备工作1、催化剂装填方案和组织实施方案提前做好审批。
协调各部门做好配合,对装剂人员做好培训。
装剂现场实行看板管理。
2、装剂专用器具、器材及作业人员劳保用品准备好,见表五。
3、专人全面负责反应器的装剂工作,做好现场指挥。
4、装剂现场设立安全监护人员,重点对进入反应器作业人员的供氧、供气及通讯照明设施进行检查确认,同时检查进反应器作业票的有效性,履行作业中的安全监护职责。
气防救护车装剂期间在现场值班。
5、进入反应器前联系化验车间,按要求进行化验分析。
化验分析项目见表二。
6、检查清扫料斗、料座内干净无杂物,插板活动灵活,联接好帆布送料筒。
7、催化剂提前运至现场,按要求摆放整齐。
催化剂搬运及摆放要求如下:(1)按装填进度要求,将催化剂准时运至现场,用叉车卸车,按种类摆好并用帆布盖好。
反应器催化剂的装填注意事项以及方法
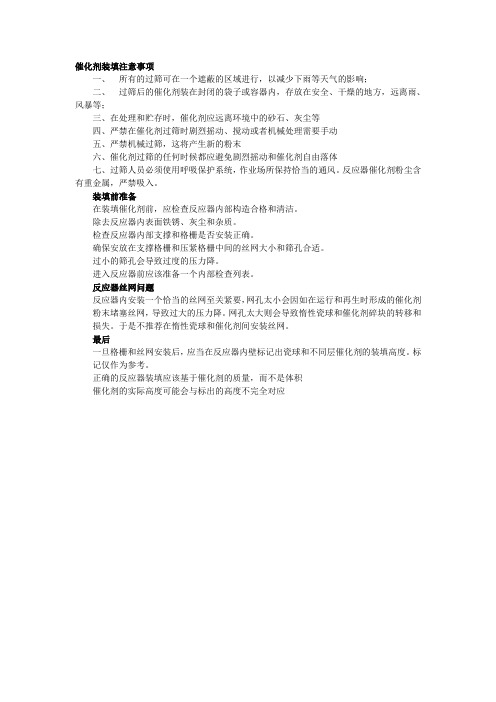
催化剂装填注意事项
一、
二、
风暴等;
三、在处理和贮存时,催化剂应远离环境中的砂石、灰尘等
四、严禁在催化剂过筛时剧烈摇动、搅动或者机械处理需要手动
五、严禁机械过筛,这将产生新的粉末
六、催化剂过筛的任何时候都应避免剧烈摇动和催化剂自由落体
七、过筛人员必须使用呼吸保护系统,作业场所保持恰当的通风。
反应器催化剂粉尘含有重金属,严禁吸入。
装填前准备
在装填催化剂前,应检查反应器内部构造合格和清洁。
除去反应器内表面铁锈、灰尘和杂质。
检查反应器内部支撑和格栅是否安装正确。
确保安放在支撑格栅和压紧格栅中间的丝网大小和筛孔合适。
过小的筛孔会导致过度的压力降。
进入反应器前应该准备一个内部检查列表。
反应器丝网问题
反应器内安装一个恰当的丝网至关紧要,网孔太小会因如在运行和再生时形成的催化剂粉末堵塞丝网,导致过大的压力降。
网孔太大则会导致惰性瓷球和催化剂碎块的转移和损失。
于是不推荐在惰性瓷球和催化剂间安装丝网。
最后
一旦格栅和丝网安装后,应当在反应器内壁标记出瓷球和不同层催化剂的装填高度。
标记仅作为参考。
正确的反应器装填应该基于催化剂的质量,而不是体积
催化剂的实际高度可能会与标出的高度不完全对应。
催化剂装填注意事项

催化剂装填注意事项《催化剂装填注意事项》催化剂在许多化学反应中都扮演着如同魔法小精灵一般的重要角色,它们能加速反应进程,提高反应效率,就像厨师手中的秘密调料,一点点就能让菜肴风味大增。
然而,催化剂的装填可不是一件可以马虎对待的小事,这就好比给精密的钟表安装零件,任何一个小差错都可能让整个“钟表”运行不畅。
下面咱们就来唠唠催化剂装填的那些注意事项。
一、装填前的准备工作首先,装填场地得像迎接贵宾一样收拾得干干净净。
要对装填的容器(比如反应釜之类的)进行彻底的检查和清扫,就像你打扫房间准备迎接重要客人一样,不能有杂物、灰尘或者上次反应残留的“小尾巴”。
容器要是不干净,就像给催化剂安排了一个满是垃圾的“住所”,这肯定会影响它发挥魔力的。
在检查容器的时候,还要查看设备的内部结构是否完好无损。
这就好比检查房子的地基和墙壁有没有裂缝,如果有问题,那在装填过程中就可能发生催化剂泄漏之类的糟糕情况,就像水从破桶里流走一样。
另外,工具也要准备齐全并且检查好。
想象一下,你要做一顿大餐,结果发现少了关键的厨具,那可就抓瞎了。
装填催化剂的工具,像漏斗、铲子之类的,都得完好无损、干干净净的,不然可能会对催化剂造成伤害,就像用破勺子给小精灵喂食,肯定会把它们弄疼的。
二、催化剂的搬运与储存催化剂在搬运的时候得小心翼翼,就像捧着易碎的瓷器。
不能有剧烈的晃动或者碰撞,不然它可能就像受到惊吓的小动物一样,内部结构遭到破坏。
有一次我朋友搬运他心爱的手办,一个不小心摔了一下,手办就断了个胳膊,催化剂要是被摔了,那可就失去它神奇的催化能力喽。
储存方面也有讲究。
要把催化剂放在干燥、阴凉的地方,这就好比我们存放粮食,要是放在潮湿闷热的地方,粮食就会发霉变质。
催化剂要是受潮或者受热了,那它就像生病的士兵,上了战场也没什么战斗力了。
三、装填过程中的要点装填的时候,均匀分布是关键。
不能让催化剂在容器里像小山一样堆在某个角落,而其他地方空空如也。
这就好比种树,不能把所有的树苗都种在一个坑里,得均匀地分布在整个林地里。
催化剂装填安全注意事项

.催化剂装填安全注意事项1、详细的装填资料一.准备工作1. 合成塔壳程和汽包水试压及蒸煮合格后,降至常温。
2. 已清除合成塔的堵塞物,用钢刷将部除锈并清扫干净。
3. 合成循环回路吹扫完毕。
4. 打开合成塔上下人孔盖,进入塔仔细检查是否清理干净,催化剂支承框上的钢丝网是否完好。
5. 准备好装填氧化铝球和催化剂所需工具:孔径3×4筛子 2台吊车 1台低压安全灯 3台磅称 2台防雨蓬布数扒具探绳数条(7000 mm)防尘口罩五节电简数支防尘镜10~15L的小袋若干皮卷尺特别防尘连体工作服扫把6.要求物资供应部门将Φ25和Φ8~10两种氧化铝球送至现场,搬运到合成塔筐架二层平台上,在平台上放一块蓬布,其上放一块塑料布。
将氧化铝球开桶倒出检查,把破碎的捡出来。
二.装填惰性球1.低压安全照明灯应接到塔,以便入塔人员工作。
2.操作人员必须将身上携带的小刀、硬币、钢笔等易脱落物品取下,并穿戴特别防尘连体式工作服、手套、安全帽后方能进入合成塔工作。
3.按预计装填高度在合成塔下封头划好大、小瓷球从下部人孔的装填高度线。
4.由一至二名操作员从合成塔下人孔进入下封头,在合成塔底部装填Φ25瓷球至大瓷球装填高度线,并用扒具扒平。
5.继续从下人孔装入一层Φ8瓷球至无法再装填为止,并用扒具扒平。
测量出剩余空间的高度,计算好剩余空间的体积及所需Φ8的瓷球量。
6. 清理出所有工具和物品后,封好下部人孔。
7. 从上人孔进入合成塔上管板,按计算量补装Φ8瓷球。
补装时应按反应管排布规律分六部分依次循迴逐层往上装填,装填时要缓慢、均匀防止瓷球在列管架桥。
8.从上管板补装瓷球的过程中,应不断用探绳测量各个部位瓷球装填高度,使各部位瓷球装填高度尽可能相等(尽量控制装填高度差在10mm以)。
9.瓷球最终装填与下管板齐平。
三.催化剂装填1.在干净的地上放置两蓬布,在蓬布上用孔径3×4筛子将催化剂开桶过筛,除去其中的触媒灰和碎粒。
催化剂装填方案

附B催化剂装填及开工方案使用固定床反应器,催化剂的装填是非常重要的,它不仅仅影响催化剂的装填量和装置的处理能力,更为主要的是在装填过程中,如果催化剂床层疏密不均,容易造成物料走“短路”或偏流,使反应器内物料的温度分布不均,从而影响产品的质量和催化剂的寿命。
如果瓷球的规格与催化剂的粒度搭配不当,可能造成催化剂的迁移。
因此,应高度重视催化剂的装填,严格按照装填设计要求进行。
一、催化剂装填前的准备工作1、打开人孔,在具备人身安全的条件下,操作人员下到反应器内,将筒体内壁清扫干净,并检查不锈钢丝网是否安装完好,严防物料走夹层短路。
2、在反应器底部出口卸料孔上安装好覆盖的金属网,螺栓等部件必须固定好,卸料孔的出口盲板也必须安装完备。
3、催化剂装填前,操作人员进入反应器,按设计装填高度标(画)出各层瓷球和催化剂装填的标记线,要求标记线四个方向等高。
4、清理好催化剂装填现场,保持现场和反应器平台的清洁。
5、按照装填图,画好记录装填数据的表格。
6、催化剂装填前,现场取样分析,并取出桶内产品合格证和杂物,如果发现催化剂中有细粉,装填时必须过筛。
7、联系吊车、起重工、铆工和化验工等配合人员。
8、参加装剂人员要分工明确,专职专责,避免造成混乱及发生事故。
建议专人负责指挥催化剂的装填,并专人负责催化剂的搬运、检查、装填床层的耙平、催化剂的过秤以及装填记录等。
二、催化剂装填过程中的注意事项1、催化剂的装填工作应选在干燥的晴天进行。
2、催化剂在搬运过程中,要轻放、轻卸、避免破碎。
3、散落在地或玷污的催化剂,不得装入反应器内。
4、装填过程中,催化剂的自由落体高度要小于50cm。
5、接触催化剂的工作人员必须穿好洁净的工作服,进入反应器的人员要扎紧袖口、裤口、清除衣袋中的杂物,以防掉入反应器内。
6、装填速度要均匀,每装完一层后要耙平,四个方向达到标高后用水平尺测量达到水平,然后进行下一步装填,这一点必须严格执行。
7、装填过程中,要控制催化剂的下放速度,不宜太快,以防催化剂破碎,或“架桥”。
催化剂装填分析

山东恒源石油化工股份有限公司15000NM3/h制氢装置催化剂装填量及装填方案一、催化剂装填:L Y T—701/LYT-702 加氢催化剂:催化剂装填前的准备:工作场地干燥、清洁、无杂物;检查反应器内构件是否完好,内部热电偶管和衬里有无破损;认真清扫,抹净反应器内壁、出口筛板与过滤网上的赃物;准备号筛子、加料漏斗、帆布袋和软梯等。
在反应器内壁标记号瓷球和催化剂的装填高度。
将所需瓷球洗净晾干。
在催化剂床层的下部,由向往上分别装入Φ10和Φ3毫米的普通瓷球,在催化剂床层的上部由下往上分别装入Φ3、Φ5毫米的活性瓷球,即与催化剂床层接触的都是Φ3毫米的小瓷球。
瓷球高度不小于100毫米,装瓷球的目的是防止运转过程中催化剂床层位移和下陷。
催化剂装填:催化剂是一种强吸水剂,为了避免吸潮,应选在晴天装催化剂,并连续工作装完为止。
装催化剂时用料斗和帆布袋将催化剂送入反应器,催化剂出袋后的自由自由落体高度小于1米,催化剂装填人员应使布袋口沿反应器圆周方向移动,使床层均匀上升。
每升高半米至一米,耙平一次,然后再装。
使其使床层径向温差增大。
装填催化剂时应有专人负责指挥,并认真做好现场装填记录。
精心搬运,认真记录编号及计量。
催化剂装填完毕后,要及时将反应器封好,以备装置试密。
三、LYT-701/LYT-702加氢催化剂硫化催化剂装填完毕后,将硫化流程以外的系统加盲板彻底隔离。
硫化流程采用闭路循环流程或加氢反应气出口放火炬流程。
反应系统气密合格,建立氢气-氮气循环后,进行催化剂硫化。
硫化条件:氢压,MPa 常压-5.0 MPa循环介质,% N2-H2混合气氢气含量,%(v/v) 30-50空速,h-1 200-500第一个恒温硫化阶段床层温度和时间 260℃恒温6小时第二个恒温硫化阶段床层温度和时间 300℃恒温8小时硫化剂二硫化碳或二甲基二硫理论需硫量,m%(对催化剂)约8.0实际需二硫化碳、二甲基二硫量,m%(对催化剂) 15/18硫化步骤:(1)以15~20℃/h将反应器入口温度升温至175℃恒温,启动二硫化碳泵或二甲基二硫开始注入二硫化碳或二甲基二硫,开始注入量控制反应器入口硫含量在0.5-1.5%(v/v)。
催化剂装填及还原方案

催化剂装填方案一、概述二、原料液240方/小时三、脱盐水:脱去氯化钠,氯离子可以使铜中毒,氯离子<3ppm本装置催化剂装填的质量直接关系到产品的质量,故必须细心、认真作好该项工作。
二、转化器的清洗和准备1、转化器在装填催化剂前,必须确保导热油温度(240-270不能超过280度催化剂就失效了)通入转化器,在高温状态下转化器列管内不发生漏油,方可装填。
2、将转化器上、下封头拆下,先检查转化器器内上下封头、列管内、板管和花板上的铁锈杂物全部清除干净,必要时可进行酸洗、水洗,再擦净、吹干备用,要求无铁锈、无杂物。
3、下封头花板上按要求规格放2层12目丝网,往花板上堆满已经洗净吹干的Φ5~8mm的氧化铝瓷球,将瓷球上表面推平,要求瓷球上表面与转化器下花板面保持有一定高的空间10-15cm,仔细装好下封头,垫片必须用新的,保证一次安装成功。
三、催化剂的装填过程1、准备1)检查检修工具及防护用品是否齐全完好。
2)准备好装催化剂量杯、漏斗、标尺、称等专用工具。
3)对催化剂开桶进行质量检查,用6~10目的钢网筛将催化剂中的碎粉筛除备用。
在运输或存库中不当受到污染或被水浸泡变质的催化剂一般不能使用。
只有确认催化剂质量符合要求时,才能装入转化器内。
4)装填人员检查自己衣服口袋,不要携带手机、打火机、香烟、钥匙等物品上转化器。
2、装催化剂1)卸下转化器上盖,再次检查转化器内是否干净,若不符合要求,要重新清扫干净。
逐根检查反应管,看有无堵塞等异常现象。
2)逐根定体积(或重量)装填催化剂,并做记号,以免漏装或重装。
(氧化铝瓷球)催化剂,氧化铜3)装填时不能急于求成,以防出现架桥现象,当出现架桥时应作好标记,及时处理。
4)定量装填完后,再逐根检查有无漏装,当确认无漏装并已处理了架桥现象。
如需要,再补充加装一遍,保证每根管内催化剂量基本相等。
5)当全部装填完毕后,用仪表空气吹净上管板,装好转化器上封头及管线。
6)装填完毕后,应对系统进行试压试漏。
催化剂装填.

山东恒源石油化工股份有限公司 15000NM 3/h 制氢装置催化剂装填量及装填方案 一、催化剂装填:LY T —701/LYT-702 加氢催化剂:催化剂装填前的准备:工作场地干燥、清洁、无杂物;检查反应器内构件是否完好,内部热电偶管和衬里有无破损;认真清扫,抹净反应器内壁、出口筛板与过滤网上的赃物; 准备号筛子、加料漏斗、帆布袋和软梯等。
在反应器内壁标记号瓷球和催化剂的装填高度。
将所需瓷球洗净晾干。
在催化剂床层的下部,由向往上分别装入Φ 10 和Φ 3 毫米的普通瓷球,在催化剂床层的上部由下往上分别装入Φ 3、Φ 5 毫米的活性瓷球,即与催化剂床 层接触的都是Φ 3 毫米的小瓷球。
瓷球高度不小于 100 毫米,装瓷球的目的是防止运转过程 中催化剂床层位移和下陷。
催化剂装填:催化剂是一种强吸水剂,为了避免吸潮,应选在晴天装催化剂,并连续工作装完为止。
装催化剂时用料斗和帆布袋将催化剂送入反应器,催化剂出袋后的自由自由 落体高度小于 1 米,催化剂装填人员应使布袋口沿反应器圆周方向移动,使床层均匀上升。
每升高半米至一米,耙平一次,然后再装。
使其使床层径向温差增大。
装填催化剂时应有专 人负责指挥,并认真做好现场装填记录。
精心搬运,认真记录编号及计量。
催化剂装填完毕 后,要及时将反应器封好,以备装置试密。
三、LYT-701/LYT-702 加氢催化剂硫化催化剂装填完毕后,将硫化流程以外的系统加盲板彻底隔离。
硫化流程采用闭路循环流程或加氢反应气出口放火炬流程。
反应系统气密合格,建立氢气-氮气循环后,进行催化剂硫化。
硫化条件: 氢压,MPa 常压-5.0 MPa 循环介质,% N 2-H 2 混合气 氢气含量,%(v/v ) 30-50空速,h -1200-500第一个恒温硫化阶段床层温度和时间 260℃恒温 6 小时 第二个恒温硫化阶段床层温度和时间 300℃恒温 8 小时硫化剂二硫化碳或二甲基二硫 理论需硫量,m%(对催化剂)约 8.0实际需二硫化碳、二甲基二硫量,m%(对催化剂)15/18硫化步骤:(1)以 15~20℃/h 将反应器入口温度升温至 175℃恒温,启动二硫化碳泵或二甲基二硫开始注入二硫化碳或二甲基二硫,开始注入量控制反应器入口硫含量在 0.5-1.5%(v/v )。
催化剂装填服务合同

催化剂装填服务合同《催化剂装填服务合同》甲方(委托方):____________乙方(受托方):____________根据《中华人民共和国合同法》及相关法律法规的规定,甲乙双方在平等、自愿、公平、诚实信用的原则基础上,就甲方委托乙方进行催化剂装填服务的事宜,达成如下协议:一、服务内容1.1 乙方负责为甲方提供催化剂装填服务,包括催化剂的搬运、装填、调试等工作。
1.2 乙方向甲方提供的催化剂应符合甲方的技术要求和相关标准。
二、服务期限2.1 本合同的服务期限为____个月,自甲方委托书发出之日起计算。
2.2 乙方应在合同约定的服务期限内完成催化剂装填工作。
三、服务费用3.1 乙方向甲方提供的催化剂装填服务费用为人民币(大写):____元整(小写):¥_____。
3.2 甲方应按照合同约定的付款方式及时支付服务费用。
四、付款方式及时间4.1 甲方支付服务费用的方式为____(现金、转账等)。
4.2 甲方应在催化剂装填工作完成后____个工作日内支付服务费用。
五、违约责任5.1 乙方未按照合同约定完成催化剂装填工作的,应向甲方支付违约金,违约金为服务费用的____%。
5.2 甲方未按照合同约定支付服务费用的,应向乙方支付滞纳金,滞纳金为应付款项的____%。
六、争议解决6.1 双方在履行合同过程中发生的争议,应首先通过友好协商解决;协商不成的,可以向有管辖权的人民法院起诉。
七、其他约定7.1 本合同一式两份,甲乙双方各执一份。
7.2 本合同自双方签字(或盖章)之日起生效,有效期至服务期限届满之日止。
甲方(盖章):____________ 乙方(盖章):____________代表(签名):____________ 代表(签名):____________签订日期:____________ 签订日期:____________请注意,以上合同仅供参考,具体条款需根据实际情况调整,并在签订前征求法律人士的意见。
- 1、下载文档前请自行甄别文档内容的完整性,平台不提供额外的编辑、内容补充、找答案等附加服务。
- 2、"仅部分预览"的文档,不可在线预览部分如存在完整性等问题,可反馈申请退款(可完整预览的文档不适用该条件!)。
- 3、如文档侵犯您的权益,请联系客服反馈,我们会尽快为您处理(人工客服工作时间:9:00-18:30)。
山东恒源石油化工股份有限公司15000NM3/h制氢装置催化剂装填量及装填方案一、催化剂装填:L Y T—701/LYT-702 加氢催化剂:催化剂装填前的准备:工作场地干燥、清洁、无杂物;检查反应器内构件是否完好,内部热电偶管和衬里有无破损;认真清扫,抹净反应器内壁、出口筛板与过滤网上的赃物;准备号筛子、加料漏斗、帆布袋和软梯等。
在反应器内壁标记号瓷球和催化剂的装填高度。
将所需瓷球洗净晾干。
在催化剂床层的下部,由向往上分别装入Φ10和Φ3毫米的普通瓷球,在催化剂床层的上部由下往上分别装入Φ3、Φ5毫米的活性瓷球,即与催化剂床层接触的都是Φ3毫米的小瓷球。
瓷球高度不小于100毫米,装瓷球的目的是防止运转过程中催化剂床层位移和下陷。
催化剂装填:催化剂是一种强吸水剂,为了避免吸潮,应选在晴天装催化剂,并连续工作装完为止。
装催化剂时用料斗和帆布袋将催化剂送入反应器,催化剂出袋后的自由自由落体高度小于1米,催化剂装填人员应使布袋口沿反应器圆周方向移动,使床层均匀上升。
每升高半米至一米,耙平一次,然后再装。
使其使床层径向温差增大。
装填催化剂时应有专人负责指挥,并认真做好现场装填记录。
精心搬运,认真记录编号及计量。
催化剂装填完毕后,要及时将反应器封好,以备装置试密。
三、LYT-701/LYT-702加氢催化剂硫化催化剂装填完毕后,将硫化流程以外的系统加盲板彻底隔离。
硫化流程采用闭路循环流程或加氢反应气出口放火炬流程。
反应系统气密合格,建立氢气-氮气循环后,进行催化剂硫化。
硫化条件:氢压,MPa 常压-5.0 MPa循环介质,% N2-H2混合气氢气含量,%(v/v) 30-50空速,h-1 200-500第一个恒温硫化阶段床层温度和时间 260℃恒温6小时第二个恒温硫化阶段床层温度和时间 300℃恒温8小时硫化剂二硫化碳或二甲基二硫理论需硫量,m%(对催化剂)约8.0实际需二硫化碳、二甲基二硫量,m%(对催化剂) 15/18硫化步骤:(1)以15~20℃/h将反应器入口温度升温至175℃恒温,启动二硫化碳泵或二甲基二硫开始注入二硫化碳或二甲基二硫,开始注入量控制反应器入口硫含量在0.5-1.5%(v/v)。
(2)在反应系统压力下,循环氢全量循环。
(3)各系统平稳后,以10~15℃/h升温至230℃,开始预硫化。
(4)每半小时分析一次循环氢中硫化氢的含量,每四小时分析一次循环氢的组成,记录高分中水的生成量。
(5)当温波穿过反应床层后,230℃恒温结束,以5℃/h升温至300℃,并恒温8小时。
每小时取一次循环氢气样,测定H2S含量。
(6)预硫化过程中水生成,硫化开始后对水进行计量,定时排水做好记录,每次排水前,取样分析生成水中硫化氢的含量。
(7)在硫化过程中原则上按预先计算好的二硫化碳或二甲基二硫量注入及升温要求,如出现下列现象,按下列方法调整操作:a. 注入CS2或二甲基二硫后,反应器中催化剂因吸附硫化物,将出现一个温波,在此温波通过反应器前,不要升温。
b. 升温阶段,任何反应器床层温升超过20℃时停止升温,必要时适当减少CS2或二甲基二硫注入量,直至停止注入。
c. 循环氢中H2S含量未被测出或浓度小于0.3(v/v)%之前,反应器内床层温度不能超过230℃。
d. 反应器内床层温度低于230℃时循环氢中H2S含量控制在0.1~0.5(v/v)%,大于230℃时,循环氢中H2S含量控制在0.5~1.0(v/v)%,300℃恒温阶段结束前,循环氢H2S含量控制在大于1.0(v/v)%,并由此控制CS2或二甲基二硫注入量。
e. 温度在200℃后上硫较多,升温速度一定要缓慢。
(8)温度达到300℃后,恒温8小时,期间保持循环氢中H2S含量控制在1.0~2.0(v/v)%,确认高分液面不再上升,无水生成则硫化结束。
(9)硫化结束后,用氮气置换,直至加氢反应器及硫化流程中的硫含量降至30ppm以下,将反应器入口温度调至开工设计温度,等待进料。
正常操作待反应器床层温度平稳后,换进原料气。
在加氢过程中,影响产品质量的因素除原料气的性质和催化剂活性外,还有反应温度、压力、空速和氢油比等操作参数。
固定操作压力、空速、氢油比后,可根据情况调整反应速度,如需提高反应温度,每次提温的幅度不要太大,约5℃。
停工时催化剂处理停工时,以每小时20~30℃速度,将催化剂床层温度降至200℃,停进料氢气继续吹扫2小时,然后加热炉熄火自然降温。
反应器卸压后用氮气置换,在氮气存在条件下,封存催化剂,并保持氮压0.5MPa。
淄博鲁源工业催化剂有限公司技术部 2010年4月16日恒源石化制氢装置应用Z417/Z418烃类转化催化剂开工要点Z417/Z418烃类转化制氢催化剂开工使用说明Z417/Z417催化剂是中石化齐鲁分公司研究院开发成功的高活性烃类蒸汽转化制氢催化剂,适用于以干气不大于180℃的轻石脑油及其他液态烃、气态烃为原料制取氢气、氨合成及甲醇合成气的造气过程。
上段Z417与下段Z418按一定比例组合装填于转化炉管内。
Z417/Z418催化剂具有较高的比表面和优良的活性、抗积碳性和机械强度,并有较低的钾流失速率,而且能够耐较高的空速,操作弹性大,对炉型适应性较强,可用于顶烧和侧烧两种转化炉型。
一、催化剂的物理性质和化学性质(1)催化剂的物理性质催化剂的物理性质见表1*催化剂的尺寸可根据用户需要进行调整。
尺寸不同,其堆密度及床层阻力也有所不同(2)化学性质两种催化剂均以金属镍为活性组份。
Z417以高铝水泥做粘结剂,以钾碱为抗积碳助剂。
Z418以预烧铝酸钙为载体,浸渍法加入活性组份,主要化学成分见表表2、催化剂的主要化学组成下段Z418对上段Z417催化剂缓慢驰放出来的钾有一定的补集能力。
Z417中的硅与其他组份呈结合状态,难以挥发流失,不会因钾、硅迁移对过程和设备产生危害。
二、开工使用要点Z417/Z418催化剂必须按填装方案的具体要求完成装填。
装填质量达到规定的要求由于Z417/Z418催化剂是以氧化态供货的,因此开工过程必须对其进行还原,使之达到正常应用条件。
整个制氢装置的开工过程就是一个对各种催化剂进行活化处理的过程。
只有各种催化剂都进行了正确合理的活化处理,才能保证装置的顺利开产成功。
1、装置升温,进行催化剂干燥脱水和还原首先对系统进行气密试验合格后,再进行氮气置换合格对于以氧化态供货的催化剂,一般采用氧化气氛升温的方法。
所谓氧化气氛升温,就是从常温升至转化床层入口约200℃的阶段,用氮气循环升温(其中进行催化剂干燥脱水,建议160℃恒温8-12小时,升温速度小于50℃/小时),当催化剂床层各点温度均在水蒸气露点温度(约200℃)以上时,可引入水蒸气以30-40℃/小时的速度继续升温。
使床层温度分布均匀,整个升温过程都应防止系统中漏入烃类。
升至还原温度时(入口480-520℃,出口800±20℃),切入还原介质,控制水氢比小于7.0。
开始进行催化剂还原。
2、催化剂还原镍催化剂还原是轻微的吸热反应:NiO+H2≒H2O+Ni 吸热反应过程无体积变化,提高温度和氢分压有利于还原。
还原介质可用氢气、氨合成气、重整氢、富氢天然气等,也可用转化炉投氨自产氨裂解气,不管使用哪种还原介质,建立循环必须使干气氢浓度大于60%,湿气水氢比小于7.0温度是还原过程的关键因素。
从氧化镍还原的平衡及反应速度考虑,提高温度都是有利的,在整个还原期间的催化剂床从入口要尽可能提高,维持在490-510℃(如果上段入口处装预还原态催化剂,入口温度可以低些),出口温度800±10℃,以利于催化剂成分还原。
还原过程中要确保各炉管均达到还原温度;还原过程中最好点齐全部烧嘴,以保证温度均匀,因超温不能点齐时,也应在还原过程中交换点燃。
还原压力可根据还原系统的阻力而定,一般为0.6-1.0MPa。
工业装置一般在还原气中配入水蒸气,在湿氢条件下还原。
还原过程中氢空速必须控制在300h-1以上,水氢比为3.0-7.0,使保证催化剂处于还原气氛中,水氢比越低越有利于还原,还原期间,严防原料烃进入转化,以防造成积碳表3 恒源石化制氢转化炉升温、还原升温控制程序转化催化剂具体还原条件为:转化炉入口温度 480-520℃转化炉出口温度800±20℃循环气氢气浓度>60%水氢比<7.0氢空速>300h-1还原时间8-12h3、投料、提量Z417/Z418催化剂一般可用于转化干点不大于180℃的轻石脑油、LPG及炼厂气等轻质烃类原料。
液态原料中芳烃含量小于12% v/v 。
对所有的烃类原料,氯含量小于0.5ppm,铅含量不大于20ppb,砷含量不大于 5.0ppb;经过加氢净化进转化炉的原料中,硫含量小于0.5ppm,氯含量小于0.5ppm还原结束,保持一定的返氢量或循环量,并将蒸汽量调到满负荷生产的50%左右,逐步引入烃类原料,其量逐步提到满负荷的30-40%,压力随之逐渐提高。
提压速度约为0.2-0.5MPa。
当系统压力达到装置正常操作压力后,调整运行参数,使装置稳定运行,然后根据生产要求,分数次提高蒸汽量和烃类进料量,每次提负荷5-10%,水碳比由7.0左右分数次将至规定值。
进料的同时,烧嘴的燃烧量作相应调整,维持出口温度在750℃以上,提量过程中,原料应稳步提高,严防脉冲进料及负荷分布不均,每次提量应先提蒸汽量,稳定后再提原料量,并尽快标定水碳比。
至此,转化系统开车成功,调整装置后续部分操作,至装置生产出合格产品,整套装置开车成功。
制氢转化催化剂使用说明书反应原理及使用条件(一)转化反应原理一般认为,烃类水蒸气转化的主要反应有:CnHm+nH2O→nCO+(m/2+n)H2(1)吸热CO+H2O→CO2+H2 (2)放热CO+3H2→CH4+H2O (3)放热此外,还存在高级烃类裂解成低分子烃类的反应等,最终产品气组成由反应2和3平衡决定。
烃类转化反应是体积增大的强吸热反应,压力低、温度高及水碳比高均有利于化学平衡向产品气生成方向移动,但由于高压能够显著降低动力消耗,因此仍为工业上采用。
在制氨合成气和制氢为目的的一段炉中使用,经济合理的水碳比在此3.2-6.0之间为宜,视具体工艺条件而定。
温度高有利于反应进行,但受到管材的限制。
反应温度过低会引起残余甲烷升高,而且还可能因上段转化不完全引起高级烃向下穿透,导致下段催化剂积碳。
一般在出口温度760-815℃下操作,催化剂床层入口温度尽可能提高到480-500℃左右为宜。
如用轻油作原料则需要配入一定量的氢,转化要求控制氢/油为0.25以上,较高的氢油比可降低轻油的分压,使温度保持在露点以上。
有利于脱硫系统的稳定操作,这对高干点的轻油尤为重要。
另外还有助于缓和转化管顶部催化剂的积碳,防止顶部催化剂的钝化。