模具零部件制程排配作业规范
制程作业流程图
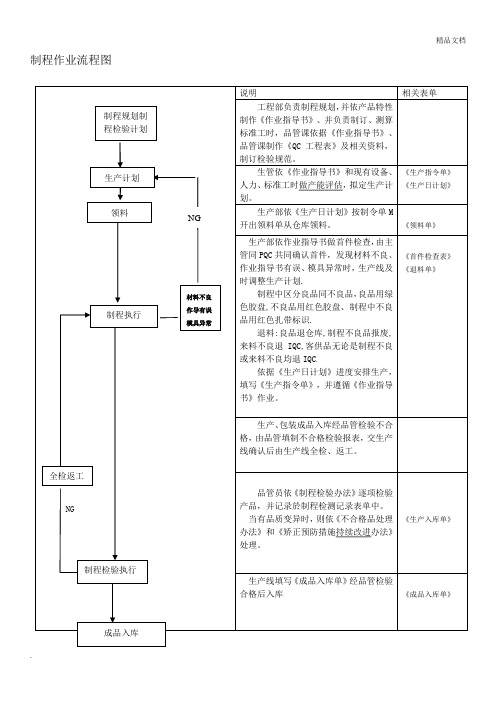
品管员依《制程检验办法》逐项检验 产品,并记录於制程检测记录表单中。
当有品质变异时,则依《不合格品处理 《生产入库单》 办法》和《矫正预防措施持续改进办法》 处理。
生产线填写《成品入库单》经品管检验
合格后入库
《成品入库单》
生管依《作业指导书》和现有设备、 《生产指令单》
人力、标准工时做产能评估,拟定生产计 《生产日计划》
划。
生产部依《生产日计划》按制令单 M
开出领料单从仓库领料。
《领料单》
生产部依作业指导书做首件检查,由主 管同 PQC 共同确认首件,发现材料不良、 《首件检查表》 作业指导书有误、模具异常时,生产线及 《退料单》 时调整生产计划.
制程中区分良品同不良品,良品用绿 色胶盘,不良品用红色胶盘、制程中不良 品用红色扎带标识.
退料:良品退仓库,制程不良品报废, 来料不良退 IQC,客供品无论是制程不良 或来料不良均退 IQC.
依据《生产日计划》进度安排生产, 填写《生产指令单》,并遵循《作业指导 书》作业。
生产、包装成品入库经品管检验不合 格,由品管填制不合格检验报表,交生产 线确认后由生产线全检、返工。
制程作业流程图制程规划制 程检验计划 源自产计划领料制程执行
全检返工 NG 制程检验执行 成品入库
.
精品文档
NG
材料不良 作导有误 模具异常
说明
相关表单
工程部负责制程规划,并依产品特性
制作《作业指导书》、并负责制订、测算
标准工时,品管课依据《作业指导书》、
品管课制作《QC 工程表》及相关资料,
制订检验规范。
如何做好来料、制程、成品检验质量管理

和试验是质量控制的重点,也是实行质量管理活动的必需过程。
最终检验项目
待装或入库产品的验证,包括外观、尺寸、结构、功能等 纸箱的验证
包装效果的验证 成品的装箱数量
出货检验规程
一、目的 确保明确FQC/OQC工作程序,以保证成品合格出入库。
抽样检验:适用于数量较多,质量较稳定,经常性使用的 物料。
全数检验:适用于数量少,价值高,不允许有不合格品的 物料。
免检试用:车间按工艺要求试做,并试做检验报告,判该 批是否合格。
免检:1.购进材料具备合格证明文件2.但汽配厂进料就要 求供方提供材料(零件)检验报告,以进行复验。3同一 供方材料经连续多次检验皆合格后,可经调整型抽检列为
5.制程质量控制能力分析及质量改进
七、品质部各岗位的职 能与功能
质量检验(QC)
1.质检计划的制定与执行
2.IQC、IPQC、FQC过程检验控制
3.保存工序检验的检查及测试报告
4.分析工序检验的每日、每周、每月报告
5.现场不合格品的控制
6.检验仪器的管理
八、什么叫来料检验 (IQC)
1.IQC 的工作手法:
3.返工的成品要巡检人员全程跟进,返工结束后再次抽检,合格后放行并开具出货报 告。
九、制程检验(IPQC)
制程控制:一般是指对物料进入物料仓到成品入库前各阶段的生产活动的品质控制。 主要要包括:原材料加工控制、半成品、在制品控制、和产品装配与包装控制。
制程检验范围:从物料上线开始至成品全部完成、合格入库为止。
IPQC检验方式
A、首件检验 a.首件检验是在生产开始时(上班或换班)或工序因素调整后(换人、换料、换工、调
模具制程检验作业指引

模具制程检验作业指引模具制程检验可太重要啦!这就好比我们做饭的时候,得时不时看看菜炒得怎么样,调料放得对不对,别等到出锅了才发现不对劲,那就晚喽!咱先来说说为啥要有模具制程检验这个事儿。
我给您讲个我亲身经历的事儿。
有一回啊,我们厂接了一个大单子,做一批精密模具。
大家一开始都干劲十足,想着赶紧完成任务。
结果呢,在制程中少了检验这一环,等到模具都快完工了,才发现尺寸有偏差,而且表面还有不少瑕疵。
这可把大家急坏了,重新修改费时费力不说,还差点耽误了交货时间,客户那边也很不满意。
从那以后,我们就知道了,模具制程检验那是万万不能少的!那模具制程检验到底要检些啥呢?首先得看看模具的原材料对不对,是不是符合要求的那种材质和规格。
这就好比盖房子,要是砖头质量不行,这房子能结实吗?然后呢,加工过程中得盯着那些工艺参数,像切削速度、进给量啥的,可不能乱来。
比如说有一次,一个师傅为了赶进度,把切削速度调得太快,结果模具表面都被刮花了,这可不行!还有啊,模具的各个零部件也得仔细瞅瞅。
尺寸精度那得用精密量具量一量,差一点儿都不行。
就像上次一个小零件,尺寸就差了那么一丢丢,装到模具里就不匹配,整个模具的性能都受影响啦。
在检验的时候,咱们得有一套标准的流程和方法。
比如说,先检什么后检什么,得安排得明明白白的。
不能东一榔头西一棒子,那样容易有疏漏。
而且啊,检验的工具也得选对,该用卡尺的时候用卡尺,该用千分尺的时候用千分尺,可不能瞎用。
检验人员也得有一双“火眼金睛”。
得经过专门的培训,知道怎么看,怎么判断。
不能模棱两可,差不多就行。
这可关系到模具的质量,一点儿都不能马虎。
说到这儿,您可能会问了,那检验出来有问题咋办?这就得赶紧采取措施啊。
小问题能当场解决的就当场解决,大问题就得停下生产线,好好研究研究,找出根源,彻底解决,可不能让问题留到后面。
总之啊,模具制程检验就像是模具生产的“守护神”,只有把这个工作做好了,才能做出高质量的模具,让客户满意,让咱们的工厂有好口碑。
模具结构变更及模具维修作业程序
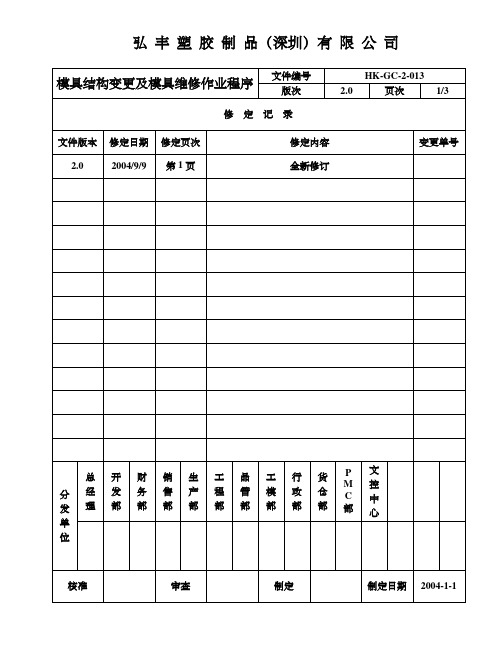
射胶时间
注塑周期
□
不可以进行小批量生产
□
秒/啤
可以进行大批量生产
□
不可以进行大批量生产
□
模具存在问题:
前后模及柱位光洁度未达标 □
生产效率未达标
□
重大设计、制作缺陷
□
样板顶白拉白锲模
□ 加工部位多处免收(不含水口) □
10 啤内打脱模剂超过 1 次
□
备注:
工程 业务 品管 生产 工程
工程
工模部分派人员领取模具,制定生产计划, 执行改/修模,确保按时将改/修好之模具移 交原交接单位。
工程部负责跟进工模部改/修模的进度,确保 生产顺利进行。
工模 工程
注塑部制订试模计划,执行试模任务:品管 与工程到生产现场作技术与品质方面的指 导。
注塑 品管 工程
品管对注塑部所送的试模样板进行品质确 认: A. 试模产品品质不符合标准/要求:若不合
顶出机构 顶针 □ 丝 筒 针 □ 斜 顶 □ 推 板 □
复位机构 回针 □ 弹 簧 □ 橡 胶 □ 铲 机 □
进料机构 大水口 □ 细水口 □ 潜水口 □
特殊加工 光 面 □ 蚀 纹 □ 淬 火 □ 氮 化 □ 电 镀 □ 烧焊 □
互换性 藏 模具生产状况:
顶白 □ 粘水口 □ 拉花 □ 粘模 □ 变形 □ 顶爆 □ 拉爆 □ 行位不顺
5.2 工程部确认需改/修模后,由工程部签发“修改模通知单”(表 8.1)给工模部, 同时通知模仓管理员预备发模具,由工程部签发“试模通知及试模报告单”(表 8.2)给生产部注塑课。
5.3 工模部负责改/修模: 5.3.1 工模部在接到修/改模通知单后,及时分派人员至工模仓领取模具------仓管 员必须在接到工程部通知后,知会工模部人员一同至工模仓领/发模具; 5.3.2 工模部制定生产计划,并在“修改模通知单”上回复工程部修/改模的进度,; 5.3.3 工模部负责修/改模的生产实施、生产进度跟踪、制程品质状况控制,并按 时将改好之模具移交给原交接单位(仓库或注塑课)。
模具制程检验作业指导书【完整版】

模具制程检验作业指导书【完整版】(文档可以直接使用,也可根据实际需要修订后使用,可编辑放心下载)1、目的为确保公司内部加工零件质量,符合公司品质要求,防止因加工过程中的不合格零件流入下道工序而影响模具的制作周期与品质。
2、适用范围适用模具厂内部各工序加工的零件与装配中的模具。
3、定义:无4、职责4.1 各工序操作员对本工序的加工零件自检并填写?自检单?以及报检,加工组长复查后并签名。
4.2 制模组长负责加工后以及装配过程中工件的复检。
4.3 品质部制程检验员负责零件加工完成的检验制程巡检和关键零件终检, 监督纠正预防措施的实施。
4.4品质部文员负责将?质量异常联络单?及时交相关人员签批并将签批完成后的?质量异常联络单?复印给相关部门。
4.5品质工程师负责?模具厂纠正预防措施?的发出与跟踪,品质工程师负责?质量异常联络单?与?模具厂纠正预防措施单?的审核以及每月制程异常数据的统计与分析。
5.程序内容:5.1 操作员报检、制程检验员巡检5.1.1 各工序操作员在该工序加工完成后,严格按照加工要求以及零件图对外观、重点尺寸进行自检并填写好?自检单?,自检确认合格将?自检单?交加工组长审核后放置于机台指定位置报检。
制程检验员不停对机台巡检,收到机台操作员的报检信息或发现待检验区有已加工完成的零件,取下机台上的?自检单?,根据加工要求和零件图,结合电脑3D图对其外观、尺寸进行详细的检测。
如零件较复杂需要超过一小时的检测时间,需提前与制模组长沟通,以防止模具因非加工、装配停留的时间过长而延误交期,检验完成后,?自检单?由品质部制程检验组保存。
5.2 检验标准与测量方法深孔钻、钻床、铣床检验标准与测量经过检验假设零件外观、尺寸、性能等有一项或多项不符合加工要求那么判定该零件此加工工序的品质状态为不合格。
5.4 品质标识检验完成后,根据其零件的品质状态在物料上做好相应的品质状态标识〔物料质量合格贴绿色“QC.PASS〞标签,不合格贴红色“QC.REJ〞标签〕,必要时在物料上用油性笔标识好模号、零件号等信息。
(整理)模具尺寸配合公差标注作业标准

加工一般公差
>0~6 ±0.1
>120~350 ±0.5
>6~30 ±0.2
>350~1000 ±0.8
>30~120 ±0.3
>1000 ±1.2
2.12.2.1 在现有图框中新增孔与孔中心距公差及加工一般公差的字段
2.12.2.2 此一公差适用对象:模座加工的逃孔,如RP弹簧、S.P、小拉
杆…等,以及螺丝逃孔。
2.8.1
滑块配合面单边
0 -0.01
mm
2.8.3
镶件沉头厚度
0 -0.02
mm
2.8.5
中子沉头厚度
0 -0.02
mm
2.8.2 镶件配合面单边
0 -0.01
mm
2.8.4 中子直径采g6级配合公差
2.8.6
中子固定方向尺寸
0 -0.02
mm
精品文档
精品文档
2.9 斜顶 2.9.1斜顶 配合公差为 2.9.2斜顶 孔之公差为
mm . mm .
精品文档
精品文档 斜顶 配合公差标示
2.10 EJECTOR BLOCK (顶出块) 2.10.1 顶出块部份为 mm ◦ 2.10.2 镶件部分为 mm ◦
精品文档
精品文档
2.11 靠破
2.11.1
凡靠破面尺寸公差是
+0.01 0
mm
精品文档
精品文档
EJECTOR BLOCK 配合公差标示
精品文档 1 用途 1.1 提升制程,缩短工时 1.2 精确控制尺寸 1.3 便于装配 2 作业内容 2.1 组立图 2.1.1 型腔型芯部分±0.01mm 2.1.2 滑块压条±0.01mm
模具开发作业指导书

模具开发作业指导书1. 目的:1.1 为确保新开发之模具能够满足客户之产品质量、成本、交期之要求。
1.2 在设计时间,按已有系统进行制作及检验,以顺利达成设计质量要求。
2. 范围:新产品模具开发需求至客户验收为止之阶段均属之。
3. 权责:3.1模具厂协理:负责整个模具厂所有人员的管理及制度的订定与执行,工程部及厂务部的事项统筹协调,协助业务部提供技术的指导,与客户交期的确立。
3.2工程部:负责模具开发设计及设计变更、试模产品承认及开模模具指令发行、文件控制。
3.3工程部课长:工程部人员的管理、任务的分配,协助模具厂协理及业务部进行工程设计数据的提供及进度的彚报,提供工程部技术的指导,负责工程部设计组及工程部产品组工作的协调与试模检讨。
3.4工程部产品组:负责模具产品开发前协助业务部进行客户端样品及图档的确认、客户端图面的检讨、合理性的判定、客户端设计变更的检讨、报价系统数据的整理提供并参与试模检讨。
3.5工程部设计组:负责模具开发设计及设计变更、2D/3D产品图面设计、3D建模、设计模具的组立图、3D拆模与拆电极、绘制零件图并参与试模检讨。
3.6工程部品管组:负责进料检验、加工零件检测、试模产品检测、量具检测等质量管理相关工作,同时负责文件管控。
3.7工程部生管组:负责模具设计、加工、组立、试模,从开模需求至客户验收为止之各段工作进度追踪。
3.8 业务部:负责模具产品开发前之调研及开发申请、客户端样品及图档的确认、报价、模具的移转。
3.9 厂务部经理:负责督导模具加工、组立、试模,从开模需求至客户验收为止之各段加工进度追踪,厂务人员的安排及管理,车间作业指导书的建立,车间作业技术的指导,转发厂外加工的申请,及校对设计图面是否完善。
3.10 厂务部仓库:负责模具零件、刀具之仓库点收及发放、储存。
3.11 采购部:负责模具零件、刀具及各种生产用具及物料之采购。
3.12 现场加工各组:负责模具零件的加工。
塑胶模具设计规范-1
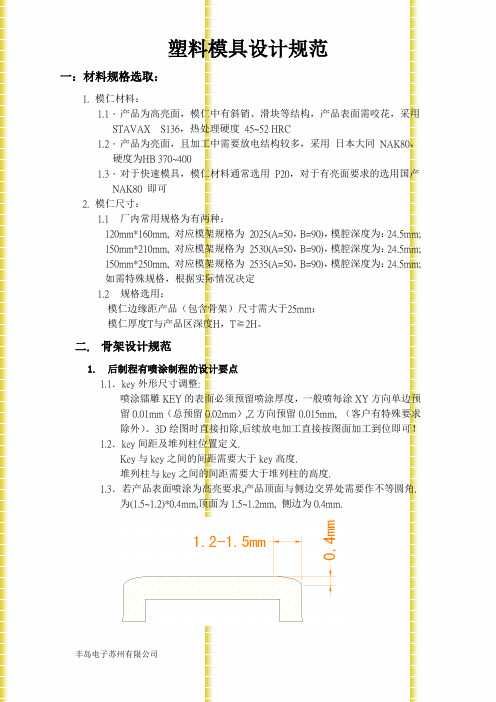
一:材料规格选取:1.模仁材料:1.1.产品为高亮面,模仁中有斜销、滑块等结构,产品表面需咬花,采用STAVAX S136,热处理硬度45~52 HRC1.2.产品为亮面,且加工中需要放电结构较多,采用日本大同NAK80,硬度为HB 370~4001.3.对于快速模具,模仁材料通常选用P20,对于有亮面要求的选用国产NAK80 即可2.模仁尺寸:1.1厂内常用规格为有两种:120mm*160mm, 对应模架规格为2025(A=50,B=90),模腔深度为:24.5mm;150mm*210mm, 对应模架规格为2530(A=50,B=90),模腔深度为:24.5mm;150mm*250mm, 对应模架规格为2535(A=50,B=90),模腔深度为:24.5mm;如需特殊规格,根据实际情况决定1.2规格选用:模仁边缘距产品(包含骨架)尺寸需大于25mm;模仁厚度T与产品区深度H,T≧2H。
二. 骨架设计规范1. 后制程有喷涂制程的设计要点1.1.key外形尺寸调整:喷涂镭雕KEY的表面必须预留喷涂厚度,一般喷每涂XY方向单边预留0.01mm(总预留0.02mm),Z方向预留0.015mm, (客户有特殊要求除外)。
3D绘图时直接扣除,后续放电加工直接按图面加工到位即可!1.2.key间距及堆列柱位置定义.Key与key之间的间距需要大于key高度.堆列柱与key之间的间距需要大于堆列柱的高度.1.3.若产品表面喷涂为高亮要求,产品顶面与侧边交界处需要作不等圆角.为(1.5~1.2)*0.4mm,顶面为1.5~1.2mm, 侧边为0.4mm.2. 后制程有印刷制程的设计要点2.1.不可有任何凸出物高于印刷面,防止凸出物刮伤网板,3.确定进(出)胶方式:按键类产品须有进胶口和出胶口,其方式主要有直接进(出)胶和搭接进(出)胶两种,进胶方式决定于产品结构:①, 产品侧边允许有毛边,或者产品周边有裙边,通常采用直接进胶.②, 产品侧边不允许有毛边,且无裙边的产品通常采用搭接进胶.C.进(出)胶位置及数量:①按键类产品如果进(出)胶选择在长边,长边尺寸小于14mm,尽量做1个进胶1个出胶的方式;(进出胶需错位) 长边尺寸大于14mm,可采用1个进胶2个出胶的方式;②按键类产品如果进(出)胶选择在短边, 采用1个进胶1个出胶的方式即可.(进出胶无需错位)③对于圆环型产品需要做1进3出,分别均匀分布在产品四周.D. 进(出)胶口尺寸:㈠对于直接进出胶:进(出)胶口宽度尺寸设计,视KEY的形状而定,通常进胶比出胶口大0.5~1.0mm。
FMEA作业规范

FMEA作业规范(IATF16949-2016)1.0 目的旨在确定模具设计或产品制造过程中所有的失效模式,及早发现模具设计或产品制造过程中所有的致命性与关键性的失效发生的可能性,以便及早的消除或降低失效发生的机率。
2.0 适用范围适用于本公司所有产品在量产前之模具设计及制程质量之规划时。
3.0 职责和权限3.1 技术部:负责制程质量之PFMEA之制作,组织并主导编写制程质量之PFMEA。
3.2 设计课:负责模具开发和制造PFMEA之制作,组织并主导编写模具开发和制造之PFMEA。
3.3 相关部门:金型部、技管课、生管课、品保部、成型部、营业部、资材课、维修组等单位配合成立跨部门功能小组,参与执行及推动。
3.4 跨部门功能小组:负责PFMEA基本数据之建立、审查、检讨及追踪。
4.0 定义4.1 FMEA:失效模式及效应分析,旨在发现和评价模具设计和制造、产品制造过程中潜在的失效及其失效后果,找到能够避免或减少这些潜在失效发生的措施,并将整个过程文件化的一组系统化的活动。
4.2 潜在的失效模式:指产品可能无法达到设计意图、后续要求或客户预期的可能产品缺失,潜在失效模式的假设为有可能发生却非一定发生。
4.3 潜在的失效效应:指如果失效模式一旦发生,失效模式对客户可能造成的影响或效应。
4.4 严重度(S):对失效模式所造成的失效效应严重程度的评估,如某项缺点一旦发生,则可能对客户产生影响之严重程度。
4.5 发生率(O):指对某一特定失效原因发生导致失效模式产生的发生频率。
4.6 检出率(D):指某项缺点在零件生产或组装中,乃至于在离开制造场所或装配场所之前,能以现行管制方法检测出该缺点的比率。
4.7 风险顺序数(RPN):为严重度、发生率及检出率等三项数字之乘积,亦即为一项纠正缺失的优先排行指数,其数字本身不具有意义。
5.0 参考文件和资料5.1 《FMEA手册》(最新版)6.0 内容7.0 附表7.1 PFMEA表PFM EA表格.d oc。
模具品质检验作业规范
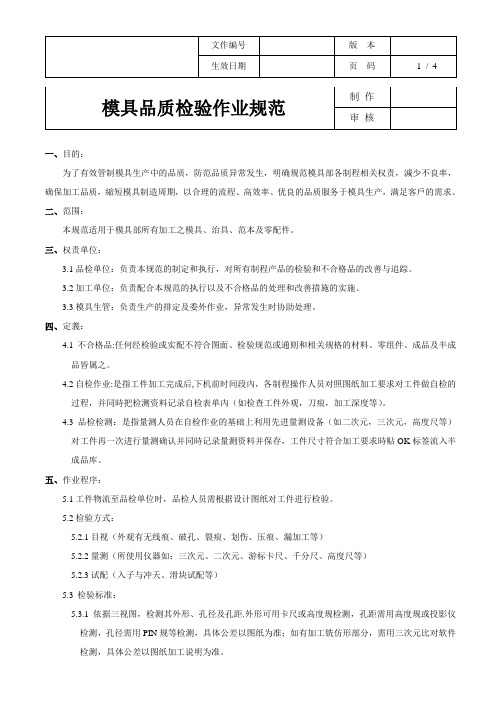
一、目的:为了有效管制模具生产中的品质,防范品质异常发生,明确规范模具部各制程相关权责,減少不良率,确保加工品质,縮短模具制造周期,以合理的流程、高效率、优良的品质服务于模具生产,满足客戶的需求。
二、范围:本规范适用于模具部所有加工之模具、治具、范本及零配件。
三、权责单位:3.1品检单位:负责本规范的制定和执行,对所有制程产品的检验和不合格品的改善与追踪。
3.2加工单位:负责配合本规范的执行以及不合格品的处理和改善措施的实施。
3.3模具生管:负责生产的排定及委外作业,异常发生时协助处理。
四、定義:4.1不合格品:任何经检验或实配不符合图面、检验规范或通则和相关规格的材料、零组件、成品及半成品皆属之。
4.2自检作业:是指工件加工完成后,下机前时间段內,各制程操作人员对照图纸加工要求对工件做自检的过程,并同時把检测资料记录自检表单內(如检查工件外观,刀痕,加工深度等)。
4.3品检检测:是指量测人员在自检作业的基础上利用先进量测设备(如二次元,三次元,高度尺等)对工件再一次进行量测确认并同時记录量测资料并保存,工件尺寸符合加工要求時贴OK标签流入半成品库。
五、作业程序:5.1工件物流至品检单位时,品检人员需根据设计图纸对工件进行检验。
5.2检验方式:5.2.1目视(外观有无线痕、破孔、裂痕、划伤、压痕、漏加工等)5.2.2量测(所使用仪器如:三次元、二次元、游标卡尺、千分尺、高度尺等)5.2.3试配(入子与冲天、滑块试配等)5.3检验标准:5.3.1依据三视图,检测其外形、孔径及孔距.外形可用卡尺或高度规检测,孔距需用高度规或投影仪检测,孔径需用PIN规等检测,具体公差以图纸为准;如有加工铣仿形部分,需用三次元比对软件检测,具体公差以图纸加工说明为准。
5.4模具在运送过程中,应注意保护工件及自我防护,以免发生工件碰伤及工伤事件。
5.5各制程工件进站需确认工件外观是否有碰伤现象,图纸是否完整无误,版次是否为最新。
汽车塑胶配件制程管制作业办法
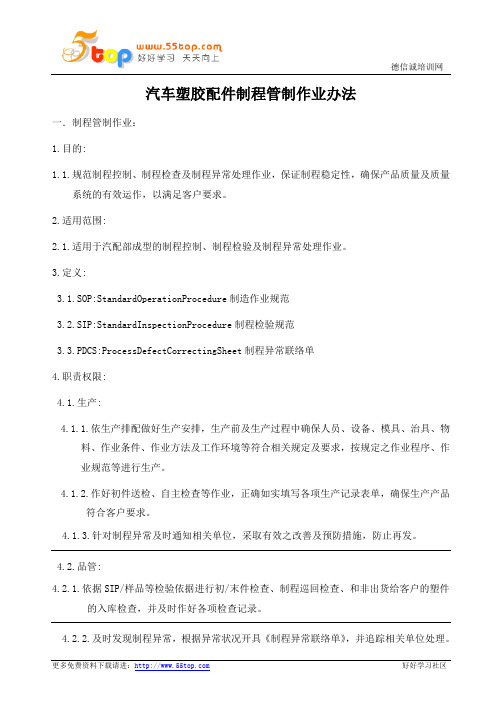
汽车塑胶配件制程管制作业办法一.制程管制作业:1.目的:1.1.规范制程控制、制程检查及制程异常处理作业,保证制程稳定性,确保产品质量及质量系统的有效运作,以满足客户要求。
2.适用范围:2.1.适用于汽配部成型的制程控制、制程检验及制程异常处理作业。
3.定义:3.1.SOP:StandardOperationProcedure制造作业规范3.2.SIP:StandardInspectionProcedure制程检验规范3.3.PDCS:ProcessDefectCorrectingSheet制程异常联络单4.职责权限:4.1.生产:4.1.1.依生产排配做好生产安排,生产前及生产过程中确保人员、设备、模具、治具、物料、作业条件、作业方法及工作环境等符合相关规定及要求,按规定之作业程序、作业规范等进行生产。
4.1.2.作好初件送检、自主检查等作业,正确如实填写各项生产记录表单,确保生产产品符合客户要求。
4.1.3.针对制程异常及时通知相关单位,采取有效之改善及预防措施,防止再发。
4.2.品管:4.2.1.依据SIP/样品等检验依据进行初/末件检查、制程巡回检查、和非出货给客户的塑件的入库检查,并及时作好各项检查记录。
4.2.2.及时发现制程异常,根据异常状况开具《制程异常联络单》,并追踪相关单位处理。
4.2.3对工程之意见(原因分析/不良品处理意见/临时对策/长期对策/责任单位等)进行复核。
4.2.4.负责最终质量之判定。
4.3.FQC:4.3.1.依据SIP/样品等检验依据进行出货给客户的塑件的入库检查,并及时作好各项检查记录。
4.3.2.及时发现制程异常,根据异常状况开具《制程异常联络单》,并追踪相关单位处理。
4.4.工程:4.4.1.制程异常之确认与初步原因分析。
4.4.2.临时对策的拟定,并提出建议的不良品处理意见及长期对策。
4.4.3.提出责任单位与会签单位。
4.5.责任单位及会办单位:4.5.1.责任单位针对制程异常拟定长期改善对策及依需求提出会办单位,准时回复并按期落实执行;4.5.2.会办单位针对制程异常及责任单位需求回复相应改善对策,准时回复并按期落实执行。
IPQC(制程控制)工作流程与方法

IPQC(制程控制)工作流程与方法IPQC(InPut Process Quality Control)中文意思为制程控制,是指产品从物料投入生产到产品最终包装过程的品质控制。
由于IPQC采用的检验方式是在生产过程中的各工序之间巡回检查,所以又称为巡检。
IPQC一般采用的方式为抽检,检查内容一般分为对各工序的产品质量进行抽检、对各工序的操作人员的作业方式和方法进行检查、对控制计划中的内容进行点检。
1IPQC目的产品实现的过程是一个复杂的人机交互的系统,由不同的工序构成, 在这个过程中,既有物流,又有信息流,要想使输出满足客户要求,就必须做到如下几个方面:1.保证输入质量2.机器设备稳定,有充分的能力,人员严格按标准作业3.与产品质量密切相关的各关键参数(CTQ)处于稳定受控状态4.信息准确,完整,及时,能发挥指导作用5.有效的工序监控机制,能及时发现过程的异常6.向前反馈机制使过程能及时对异常进行修正7.向后反馈机制能有效防止不良流失8.产品初末件审核,提供班次质量保证9.工序接口顺畅,防止资源浪费以上各方面的执行有赖于IPQC的持续努力,而正是有了以上的支持,过程才是真正意义上的,保证输出质量的过程,所以IPQC的工作,实现了流程向过程的过渡,使输出不再是输入的简单相加,而是数量和质量上增值。
2IPQC工作流程简单的说:工作内容包括首件检查、各类变更文件的跟踪。
4M1E的巡查。
发现异常的提出、跟踪与验证。
详细的说:过程检验(IPQC,in process quality contrl)目的是为了防止出现大批不合格品,避免不合格品流入下道工序去继续进行加工。
因此,过程检验不仅要检验产品,还要检定影响产品质量的主要工序要素(如 4MIE)。
实际上,在正常生产成熟产品的过程中,任何质量问题都可以归结为4M1E中的一个或多个要素出现变异导致,因此,过程检验可起到两种作用:1. 根据检测结果对产品做出判走,即产品质量是否符合规格和标准的要求;2. 根据检测结果对工序做出判定,即过程各个要素是否处于正常的稳定状态,从而决定工序是否应该继续进行生产。
制程检验规范(含记录)
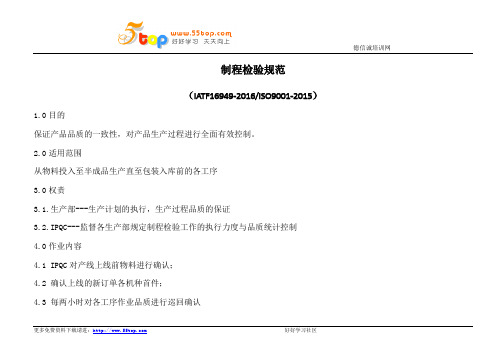
德信诚培训网制程检验规范(IATF16949-2016/ISO9001-2015)1.0目的保证产品品质的一致性,对产品生产过程进行全面有效控制。
2.0适用范围从物料投入至半成品生产直至包装入库前的各工序3.0权责3.1.生产部---生产计划的执行,生产过程品质的保证3.2.IPQC---监督各生产部规定制程检验工作的执行力度与品质统计控制4.0作业内容4.1 IPQC对产线上线前物料进行确认;4.2 确认上线的新订单各机种首件;4.3 每两小时对各工序作业品质进行巡回确认德信诚培训网4.4 单项外观不良率超过3%,电性不良率超过1%须立即开立品质异常联络单进行反馈4.5 对于由现场执行的改善措施进行跟踪并及时反馈上司。
工序项目允收标准检验方法检验工具及附件判定基准类别内容MAJ MIN裁线外观印字清晰无油污,字体一致.印字内容与要求相同.目视工程图/样品△线材外被光滑无明显夹痕,无损伤,无色差. 目视样品/色板△印字方向每把线材印字头尾方向一致目视目视△裁线结构尺寸线材规格与工程图中线材规格标准一致量测千分尺△色序/排线与图面相符目视工程图/样品△分线分线长度与图面要求相符且无压伤量测/目视钢尺/工程图△总长度与图面要求相符量测尺/工程图△剥皮长度与工程图面相符量测钢尺/工程图△线芯无切伤/切断芯线及导体目视/ △端子压著外观端子型号/规格无变形、料带过长、损伤,端子型号规格均与图面相符.目视工程图/样品△线材无压伤、破损,规格、颜色符合图面要求. 目视工程图/样品△压着结构拉力依线材规格及端子型号确定拉力大小,须符合<<标准拉力表>>中要求量测拉力计△到位端子前脚两端均可见芯线且端子后脚间能看见绝缘皮目视/ △芯线不能有外露、压断铜丝、飞铜丝现象目视/ △全检端子外观除拉力外同端子压著工序目视放大镜△组装胶芯插端子规格Housing型号规格与工程图相符.颜色和塞孔正确.线材规格裁线长度正确,与工程图相符.量测尺/工程图△印字Housing和线材印字清晰,内容与颜色正确,不易脱落.目视工程图/样品△外观Housing无损伤,缺料,杂色等,线材无压伤,无端子变形,无单根受力,色序排列正确,无掉PIN,端子未插到位,漏插胶壳,飞丝,芯线掐伤,组合线无长短不一,套管到位烘紧无破损.目视工程图/样品△测试电气性能无开路,短路,错位,绝缘,耐压,接触不良测试测试机△焊接分线外观无分伤线,撕破外被,露铜,分线尺寸符合工程图要求.目视/量测钢尺/工程图△剥线尺寸剥头尺寸符合工程图面/SOP要求量测钢尺/工程图△外观无飞丝,剥断铜丝或伤芯线目视/ △焊接材料连接器规格型号与图纸一致,无用错规格目视工程图/样品△外观 焊点圆滑,饱满,无假焊,脱焊,漏焊,错位,烫伤零件及线材.目视 工程图/样品 △ 焊接接点焊点排位 焊点排位与图纸要求一致,无焊错位目视 工程图/样品 △ 温度铬铁温度 焊接温度是否符合作业要求,有无偏高或偏低.量测 温度计 △ 成型成型材料使用胶料材质颜色硬度等与图纸一致目视 工程图/样品△ 外观无缩水,流纹,毛边,冲胶,杂色,错模,变形,模印,气泡,缺料.目视 / △ 无压伤线材及零件目视 / △ 模具编号、LOGO 方向及图样与工程图相符目视 工程图/样品 △ 尺寸头部外露、SR 卡口等尺寸与工程图面相符量测 卡尺/工程图△ 吹 套 管外观 外观 套管缩紧,无烫伤,无破损.目视 / △ 尺寸规格 套管规格颜色正确,长度及烘烤位置符合工程图要求.量测 钢尺/工程图△ 脱 皮脱外皮外观脱皮口平齐,无刮伤芯线外被及铜丝,头尾方向正确目视 / △ 尺寸脱皮长度与工程图面相符.量测 钢尺/工程图△ 剥芯线外观无脱断/脱伤芯线及铜丝,铜丝保持整齐,无散乱.目视 / △ 尺寸脱皮尺寸符合工程图要求.量测钢尺/工程图△扭线扭铜丝外观无飞丝,打结,无漏扭及过松现象目视/ △尺寸各尺寸与工程图面相符. 量测钢尺/工程图△焊接温度铬铁温度焊接温度是否符合作业要求,有无偏高或偏低.量测温度计△材料锡丝规格锡丝是否为无铅环保锡丝,锡丝型号规格是否与工程图面要求符合目视/量测卡尺△产品外观焊点圆滑,饱满,无假焊,漏焊,错位,烫伤零件及线材.目视/量测测试机/工程图△沾锡参数锡炉温度锡炉温度是否符合作业要求,有无偏高或偏低.量测温度计△材料锡丝锡条规格锡条是否为无铅环保锡条,焊接头型号规格是否与工程图面要求符合,锡炉是否为环保专用锡炉目视/量测XRF环保测试仪△产品外观沾锡部分光亮,无连锡、大头、OD不符;沾锡不到位、烫伤线皮、线身沾锡渣、氧化发黑等目视工程图△绕扎线材料扎带规格扎带规格材质颜色等符合图纸要求目视工程图△尺寸扎线及头尾尺寸扎线中间主体尺寸及头尾留长尺寸与图纸一致量测钢尺△绕扎线外观外观扎带无破损、露铁芯;扎带扭转圈数正确,无松散;PET扎带有筋面是否朝上;线材是否刮伤;头/尾是否夹伤撞伤目视目视△功能测试治具测试治具测试治具使用是否正确,治具是否正常. 量测点检样品/工程图△参数设定测试参数测试机各项参数设定是否与工程图要求一致. 目视工程图△电气性能电性测试无开路,短路,错位,绝缘,耐压,打火,瞬间不良等.测试测试机△外观全检外观头部端子规格与图纸一致;无冲胶缺胶、缩水流纹料花、压伤线材五金头、五金头脏污氧化;外模鼓包变形;外模错模、合模线过大、外模开口凹坑、露内模锡点、LOGO方向正确;网尾裂缝等目视图纸/样品△线身线材印字内容与图纸一致,整把线材印字内容头尾方向须一致;线身无刮伤脏污颗粒,印字清晰可识别;目视图纸△尾部SR无变形,压线露铜,进料嘴过大手感明细目视目视△尺寸尺寸成品各尺寸符合图纸要求(端子外露、SR卡口、SR留长及锡尾留长等尺寸)量测卡尺/钢尺/卷尺△电测性能电性无短断路绝缘耐压不良等测量导通测试机△信耐性可靠性可靠性线材摇摆及头尾吊重及阻燃等级等可靠性符合图纸要求测量摇摆机/吊重仪/阻燃测试仪△包装外观包装方式包装方式符合图纸/SOP要求;外箱标签内容正确;标签内容与实物一致,无混料错料目视图纸/SOP △数量数量装箱数量符合要求,无短装多装量测电子磅△5.0参考文件制程检验程序6.0相关记录IPQC巡检记录IPQC巡检日报表(2).xls成品抽检台帐成品检验报告.docIQC进料检验报告德信诚培训网IQC进料检验报告.xls铬铁/锡炉温度点检表烙铁温度点检表.xls外观、电性全检日报表FAI检验报告记录表.xls。
模具各阶段作业说明

模具各阶段作业说明1.0 目的:了解模具各階段之任務及職能分工,增強配合協調性。
保障模具順利投入生産。
2.0 範圍:涉及模具各環節之單位3.0 相關文件:751-230-05 塑膠部模具科作業規範751-230-01 塑膠產品試產規範730-380-07 模具開發作業辦法730-220-01 模具設計控制程序741-316-01 零件承認規範751-220-01 模具製作控制規範4.0 名詞進度CTF:Critical to FunctionAIR:Article Inspction ReportRQT:Reliability Quality TestFC:Function CheckTA:Test AEP:TRR:5.0 作業流程及步驟1 2 3 4 5 6 7評鋻——〉合約——〉開模——〉制模——〉確認——〉試模——〉驗收5.1开模资格确认模具厂是否具备开模能力的要求,需先经过RD、QC、採購單位三方评鉴。
R D:负责评估模具厂设计技术能力及设备能力。
Q C:负责评估模具厂品质管控系统是否完善及远作状况。
採購:负责评估模具厂信用、资金、交期、配合度、价格等状况。
5.2合约签订(业务联系会)当确认模具厂具备符合要求后,需求方将下P/O签订合约,形成书面的约定,明定開模要求及供需双方责任。
5.3开模检讨模具厂与客人就开模设计检讨达成共识后,模具厂设计单位出图,(由产品3D转模具3D,2D)並展开BOM,进行备料。
5.4制模/组模模具厂依BOM及设计图面进行加工制模/組模,如有ECM导入,由生技發動,設計出圖,制程执行,QC追踪。
5.5确认模具经钳工组立后,必须经过初步静态验证,QC确认OK后,方可进行试模动作。
5.6试模( 分为3个阶段,T0,T1…TN,V0 )5.6.1 阶段:T0定義:模具廠商自檢確認參與單位:PT、RD職能分工:PT----模具自身檢討RD----設計問題達成目標:發現所有模具自身及設計問題達成要求:1. 必須經PT QC同意方可進行試模2. 原則上T0要能有正常成型之產品以供確認3. 進行重要關鍵尺寸測量(以需求/產品狀況進行)5.6.2. 階段:T1-----Tn (經PT QC確認同意方可進入)定義:客戶確認參與單位:PT、RD、成型廠商職能分工:PT ----- 模具問題確認成型廠商-----成型機台調整確認RD ----- 產品外觀/設計結構確認達成目標:通過初步確認,可用於EP / TA生産達成要求:1. 用於EP/TA階段要求①原則上無影響結構之缺陷---- RD確認②外觀可允許有輕微瑕疵----- RD確認,如QC有異議由PM確認簽樣確認③噴漆可靠性必須通過正常生産測試------成型廠(PIM/QC)④責任單位簽樣后,可放行。
冲压模具设计与制造规范

冲压模具设计与制造规范一.目的:统一公司模具设计规范,更好地配合加工单位,适应快速作业的需要。
二.范围:适用于本公司所有部门之作业。
三.权责:由各个部门编写文件之人员负责执行此规范。
四.内容:1.开模前相关作业程序:1-1 程序说明:新项目提出开模时,模具工程师必须先向业务或此项目负责人确认此项目预估的量能会有多少,之后再依照此量能特性加以分析,以最快速、经济、合理之要求达成最佳化冲压模具状态,以确保后续之量产能力。
模具开发前期制作冲压模具工程设计制作分析,此分析用意在于预见模具开发可能产生之问题点,将其整理以及早发现及早修正的形态为目的,其次安排各工程图面的合理性(包含单工程模具工程图面以及连续模料带图面)、考虑模具结构设计的安全以及正确性……等,另外依照评估后模具形式决定模具材质以及热处理特性,再规范定义各配件的使用时机,明确规划出最佳化模具的形式。
在模具制作期间,模具开发进度的掌控往往是造成一个新的项目是否有办法如期成行的一个重要症结点。
试模时实际的状况记录于试模检讨记录中,藉由实际的问题记录以及改善确认方式此套新开发的模具运行无误有量产能力,最后确认每个单件皆符合RD所设计的规范要求后,签认模具移交单以做模具验收的标准,而针对以上叙述以下用流程图加以说明:冲压模具级数及作业分类原则Design For Manufacture Report工程图以带图面确定工程模:各工程工序图连续模:料带图模具确定各工程模具结构图模具开发进度掌控模具开发进度表试模检讨改善记录FAI Report & Cpk Report模具确认模具验收办法2. 冲压模具级数、寿命定义及模具组织架构:2-1 冲压模具级数定义:各类冲压模具依照不同程度产能之要求,定义出三种级数冲压模具结构尺寸以及相关规定之设计形态,分别为每个月产能在50K以下少量产能型态的模具(定义为一般产能模具)50K~100K之间中产能型态之模具(定义为中产能模具)以及每个月100K以上产量之模具(定义为高产能模具),定义各级数产能模具如下表所示:由于模具在冲压过程中有一定的磨损、变形,为了保证产品的质量,冲压一定次数后就必须有一次模具保养,根据本厂内多年的现场统计,总结模具保养规律如下:2-3 冲压模具结构分类:冲压类模具可分为下料形式、冲孔形式、折弯形式、连续模具等,其模具结构、板材尺寸、模具材质规范如以下所示。
模具管理制度
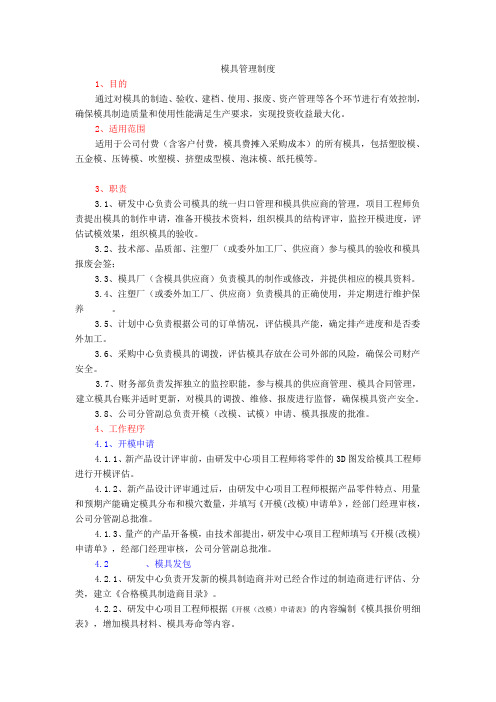
模具管理制度1、目的通过对模具的制造、验收、建档、使用、报废、资产管理等各个环节进行有效控制,确保模具制造质量和使用性能满足生产要求,实现投资收益最大化。
2、适用范围适用于公司付费(含客户付费,模具费摊入采购成本)的所有模具,包括塑胶模、五金模、压铸模、吹塑模、挤塑成型模、泡沫模、纸托模等。
3、职责3.1、研发中心负责公司模具的统一归口管理和模具供应商的管理,项目工程师负责提出模具的制作申请,准备开模技术资料,组织模具的结构评审,监控开模进度,评估试模效果,组织模具的验收。
3.2、技术部、品质部、注塑厂(或委外加工厂、供应商)参与模具的验收和模具报废会签;3.3、模具厂(含模具供应商)负责模具的制作或修改,并提供相应的模具资料。
3.4、注塑厂(或委外加工厂、供应商)负责模具的正确使用,并定期进行维护保养。
3.5、计划中心负责根据公司的订单情况,评估模具产能,确定排产进度和是否委外加工。
3.6、采购中心负责模具的调拨,评估模具存放在公司外部的风险,确保公司财产安全。
3.7、财务部负责发挥独立的监控职能,参与模具的供应商管理、模具合同管理,建立模具台账并适时更新,对模具的调拨、维修、报废进行监督,确保模具资产安全。
3.8、公司分管副总负责开模(改模、试模)申请、模具报废的批准。
4、工作程序4.1、开模申请4.1.1、新产品设计评审前,由研发中心项目工程师将零件的3D图发给模具工程师进行开模评估。
4.1.2、新产品设计评审通过后,由研发中心项目工程师根据产品零件特点、用量和预期产能确定模具分布和模穴数量,并填写《开模(改模)申请单》,经部门经理审核,公司分管副总批准。
4.1.3、量产的产品开备模,由技术部提出,研发中心项目工程师填写《开模(改模)申请单》,经部门经理审核,公司分管副总批准。
4.2 、模具发包4.2.1、研发中心负责开发新的模具制造商并对已经合作过的制造商进行评估、分类,建立《合格模具制造商目录》。
IML工艺及模具设计技术要点-20160119

二. IML產品設計要點
2.2.IML Part Design guideline
2.2.3.Depth and Outer Radii design
Recommended
Min/ Max
H PC_7.0mm; PMMA_3.0mm; PET_6.0mm
R t PC_0.6mm; PMMA_0.8mm; PET_0.6mm
二. IML產品設計要點
2.3.產品設計案例介紹
2.3.3.Titan產品介紹
1.產品3D圖示 2.材料:PC film + PC/ABS塑膠原料
PET:DE1-1 T=0.125mm PC/ABS: S a b I c PC/ABS C1200HF WH8B229 3.產品規格: 長:93.12mm;寬:52.01mm;肉 厚:1.35mm. 4.產品制程: PET-印刷-CCD打孔-熱壓-裁切注塑 5.產品顏色種類
Notes: Changes in thickness should be gradual or sink marks will be created.
二. IML產品設計要點
2.2.IML Part Design guideline
2.2.6 .Internal Mechanical Features design
R c 建議 ≧ 3.0 mm ≧ 4.0 mm ≧ 5.0 mm
頂部R角R t最小建議為薄膜印刷后厚度的 2.5倍以上。
側面轉角R c越大越好,否則Forming薄膜易皺 褶,PC/PET膜轉角易拉白,PMMA膜轉角易拉裂。 依不同材料建議R c值最小:PC膜__ 6倍膜厚以上, PMMA/PET膜__ 10倍膜厚以上。
二. IML產品設計要點
- 1、下载文档前请自行甄别文档内容的完整性,平台不提供额外的编辑、内容补充、找答案等附加服务。
- 2、"仅部分预览"的文档,不可在线预览部分如存在完整性等问题,可反馈申请退款(可完整预览的文档不适用该条件!)。
- 3、如文档侵犯您的权益,请联系客服反馈,我们会尽快为您处理(人工客服工作时间:9:00-18:30)。
模具零组件制程排配作业规范1. 目的依照本公司加工设备条件及零组件加工要求制订本标准,使制造流程标准化,以确保产品质量合乎要求,以达到客户中意之目的.2. 适用范围各种周密模治具零组件加工, 其制造流程均依此标准设定。
3. 引用文件《模具零组件订单变更管制作业规范》 STB01024.作业细则4.1 指导原则:4.1.1 制程排配要求:4.1.1.1 制程排配须考虑各工段工时负载, 以确保交期及质量。
4.1.1.2制程排配依工件的交期先后进行选择。
4.1.1.3.制程必须首先考虑加工设备能够达到的加工范围及精度。
4.1.1.4 制程按硬度要求、材质、零件形状、尺寸、公差及客户要求等事项进行选择。
4.1.1.5.制程按客户指定的方法选择。
4.1.2 制程排配性质:4.1.2.1.限制性:4.1.2.1.1 受设备条件之限制。
4.1.2.1.2 受零件形状、尺寸及公差、硬度等条件之限制。
4.1.2.1.3 受材料、治工具之限制。
4.1.2.1.4 受客户使用要求之限制。
4.1.2.1.5 受订单交期及本厂各工段订单量之限制。
4.1.2.2.灵活性: 一零件可能有多种制造流程, 都能达到图面要求。
4.1.2.3.机动性: 加工中可对制程作有限度的变更, 具体作业请参照《模具零组件订单变更管制作业规范》。
变更后的制程必须在以下情况之内:4.1.2.3.1 变更后的制程更能保证交货日期。
4.1.2.3.2 变更后的制程更能保证加工质量。
4.1.2.3.3 变更后的制程更能满足客户使用要求。
4.1.2.3.4 变更后的制程更能降低成本。
4.1.2.3.5 应客户要求作变更。
4.1.3 制程排配原则:4.1.3.1内容:4.1.3.1.1 第一原则: “快"──制程必须首先保证客户需求日期。
4.1.3.1.2 第二原则: “稳"──选择能够确保质量完美无缺、不出异常的制程.4.1.3.1.3 第三原则: “廉"──采纳最省时省力, 最少消耗的加工方法及工具材料等,制造让客户中意的产品。
4.1.3.2.选择顺序:首先按第一原则、第二原则选择, 在二者都能保证的情况下选择第三原则。
4.2 制程排配标准:4.2.1 下料方式选择: 依相关加工设备条件及零件加工要求,分为三种下料方式,即成型铣床下料、成型研磨下料和线切割下料,分不适用于不同情况:4.2.1.1 成型铣床下料:4.2.1.1.1 工件有螺丝孔、让位孔、槽。
4.2.1.1.2 工件有大切削量;有后工段,为防止变形或方便加工而进行的去余量工作。
4.2.1.1.3 不须经后工段, 用铣床加工就能达到要求。
4.2.1.2 成型研磨下料:4.2.1.2.1 急件若备料仓有合适材料,一般采纳研磨下料,以缩短交期.4.2.1.2.2 如工件切削量不大, 不易产生变形, 且没有螺丝孔, 则采纳研磨下料。
4.2.1.3 线切割下料:4.2.1.3.1 工件厚度太薄, 无法用前二种下料方式。
4.2.1.3.2 材料价格昂贵、如采纳前二种下料方式将造成白费。
4.2.1.3.3 虽可用前二种下料方式, 但易发生变形而达不到图面公差要求。
4.2.1.3.4 工件交期较短,通过前两种下料延误时刻过长。
4.2.1.3.5 能够内外一体切割直接成型。
4.2.2 铣削加工4.2.2.1 平面铣(刨)削加工(PM):4.2.2.1.1 加工精度:尺寸公差: 0.10mm 以上、面粗度:▽或▽▽。
形位公差: 平面度、平行度、垂直度要求每100㎜均在0.05㎜以上。
4.2.2.1.2 加工范围:外表面形状:平行面、垂直面。
需热处理前的材料如SKD11以及无须热处理的材料如S45C,S55C,P20等。
模板尺寸大于100x200m㎡或90x300 m㎡以上请购光板﹐在此范围之外由铣削自行加工;4.2.2.2 成型铣削工段的安排(M):4.2.2.2.1 加工精度:尺寸公差: 0.05 以上、面粗度: ▽或▽▽。
形位公差: 平面度、平行度、垂直度、对称度要求每100㎜均在0.05㎜以上。
4.2.2.2.2 加工范围:外表面形状:平行面、垂直面、斜面、台阶、圆柱面、圆锥面、圆弧、外螺纹。
表面形状:圆孔(槽)、圆锥孔(槽)、多边形孔(槽)(圆角)、螺纹孔、键槽、圆弧槽。
各类小模板加工。
4.2.2.3 切削中心工段安排(MC):4.2.2.3.1 加工精度尺寸公差: 0.02㎜以上、面粗度: ▽或▽▽形位公差: 平面度.平行度.垂直度.对称度.同心度.同轴度及柱要求每1OO㎜均在0.05㎜以上.4.2.2.3.2 加工范围:外表面形状﹕平面度.垂直度.斜面.台阶、圆柱面.圆锥面.圆弧面.复杂型面.内表面形状: 圆孔.锥孔.多边形孔.螺纹孔.各种槽及复杂异形孔.4.2.2.3.3 模板类不:上垫板销孔线切割加工其余切削中心加工,(无热处理时全由切削中心加工)上夹板冲子孔.导柱.或衬套孔.销孔.异形孔由线切割加工,其余切削中心加工脱背板异形孔.销孔.线切割加工,其余切削中心加工脱料板冲子孔.导柱或衬套孔.销孔抽牙孔.异形孔由线切割加工,其余切削中心加工下模板冲子孔.导柱或衬套孔.销孔.抽牙孔.异形孔由线切割加工,其余切削中心加工下垫板销孔.异形孔.抽牙(形)冲子孔(有的反抽)线切割加工其余切削中心加工(无热处理和无异形孔时全由切削中心加工)上下模座、上下承板切削中心加工.4.2.2.4 切削中心工段安排3D加工(CNC):4.2.2.4.1 加工精度尺寸公差: 0.01mm以上、面粗度: ▽或▽▽形位公差: 平面度.平行度.垂直度.对称度.同心度.同轴度及柱要求每1OOmm均在0.05mm以上.4.2.2.4.2 加工范围:外表面形状平面.垂直面.斜面.台阶、圆柱面.圆锥面.圆弧面.及三D曲面.内表面形状: 圆孔.锥孔.多边形孔.螺纹孔.各种槽及三D曲面.4.2.2.5 车床工段安排(L):4.2.2.5.1 加工精度尺寸公差: 0.02㎜以上、面粗度: ▽或▽▽。
形位公差: 平面度、平行度、垂直面、对称度、同心度、同轴度及柱要求每100㎜均在0.05㎜以上。
4.2.2.5.2 加工范围外表面形状:轴平行台阶面、垂直面、斜面、倒角、圆弧面、圆柱面、圆锥面、外螺纹、轴套类。
内表面形状: 圆孔、锥孔、螺纹孔台阶孔、中心孔。
.4.2.3 热处理工段的安排(H)(外包鸿准加工):热处理包括一般热处理和真空热处理两种一般依照客户要求进行选择.4.2.3.1 工件有硬度要求且采纳铣床下料则安排热处理工段.4.2.3.2 工件有硬度要求但可直接使用热处理料板下料则无需安排热处理工段.4.2.3.3工件无硬度要求不安排热处理工段.4.2.4研磨制程排配标准:4.2.4.1 平面研削加工4.2.4.1.1 加工精度:尺寸公差: 0.01以上、面粗度:▽▽或▽▽▽4.2.4.1.2 加工范围:(小水磨GP):工件研削平面面积在60*70~1000*500以内的模具零组件(大水磨SG): 工件研削平面面积在250*200~1500*600以内的模具零组件外表面形状:平行面要求每100mm均在0.01mm以上4.2.4.2 成型研磨工段的安排(G):4.2.4.2.1 加工精度:尺寸公差:0.001以上、面粗度:▽▽或▽▽▽。
形位公差:平面度、平行度、垂直度、同心度、同轴度及圆柱度、对称度要求每100mm均在0.02mm以上4.2.4.2.2 加工范围:外表面形状: 平行面、垂直面、斜面、台阶、通槽、V 型槽、圆弧面内表面形状: 不能加工内表面光学研磨工件需粗磨逃料时。
4.2.4.2.3 研磨次数之确定:第二次研磨之目的: 精磨外表面、抓尺寸、抓位置度、成型外表面、精修变形以下情况采纳两次研磨: 薄片零件多件加工, 先研磨长、宽方向尺寸, 经线切割切片后, 再研厚度尺寸,线切割或放电不能保证的尺寸公差或形位公差, 在第二次研磨时保证。
第二次研磨时磨滑块之靠肩,压线,线切割线头等。
4.2.5 线切割工段的安排:4.2.5.1 水割(WE)4.2.5.1.1 加工精度:尺寸公差: 0.003以上、面粗度: ▽▽或▽▽▽。
形位公差: 平面度、平行度、垂直度、对称度、同心度、同轴度及圆柱度要求每100mm均在0.01 mm以上。
4.2.5.1.2 加工范围:外表面形状:平行面、垂直面、斜面、台阶、圆柱面、圆锥面、圆弧面、各种复杂的外表面。
上下异形工件加工。
4.2.5.1.3 内表面形状: 除螺纹、非贯穿面外的各种形状孔、槽。
4.2.5.1.4模板类不:上垫板销孔线切割加工,其余切削中心加工。
(无热处理时全由切削中心加工)上夹板冲子孔、导柱孔或榇套孔、销孔、异形孔由线切割加工,其余切削中心加工。
脱背板异形孔、销孔线切割加工。
脱料板冲子孔、导柱或榇套孔、销孔、抽牙孔、异形孔由线切割加工,其余切削心加工。
下模板冲子孔、导柱或衬套孔、销孔、抽牙孔、异形孔由线切割加工,其余切削中心加工。
下垫板销孔、异形孔、抽牙(形)冲子孔(有的反抽)线切割加工,其余切削中心加工。
(无热处理和异形孔时全由切削中心加工)4.2.5.2 油割(WO) (外包鸿准加工)4.2.5.2.1 加工精度:尺寸公差: 0.002以上、面粗度: ▽▽▽或▽▽▽▽。
形位公差: 平面度、平行度、垂直度、对称度、同心度、同轴度及圆柱度要求每100mm均在0.004 mm以上。
4.2.5.2.2 加工范围:外表面形状:平行面、垂直面、斜面、台阶、圆柱面、圆锥面、圆弧面、各种复杂的外表面。