拉丝配模的三种方法
拉丝眼镜的定配—制模板
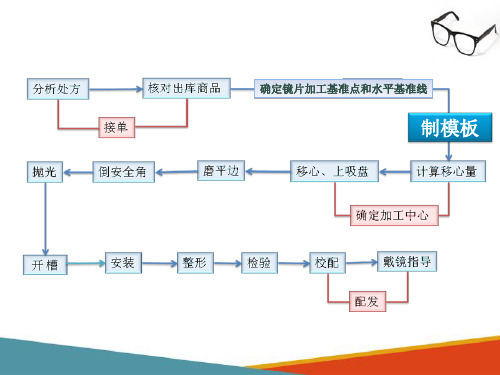
❖素质要求
1.进入天职验配中心要着装整齐,统一穿白大衣; 2.不留长指甲,女同学长发应束起; 3.掌握正确的手持眼镜架的方法,必要时应戴手套拿取。
4.耐心、细心操作;
5.规范操作使用仪器设备。
半自动磨边机定配一副拉丝眼镜的流程:
确定镜片加工基准点和水平基准线
制制模模板板
一、半框眼镜(half-frame glasses)的模板
半框眼镜半自动磨边机加工制模板
方法二 摸板坯料制模板
(详情参见学习情境一任务6)
(2)用硬纸板制作模板:适用于手工磨边机各种镜型(全框、拉丝、打 孔)的装配
(3)用塑料板(模板坯料)制作模板:适用于半自动磨边机各种镜型 (全框、拉丝、打孔)的装配
❖ 模板机(pattern maker )制模板 :适用于手工磨边机和半自动
磨边机全框眼镜的装配
扫描仪 (原厂模板/撑片/原镜片/全框镜架):适用于全自动磨
镜片台
三、拉丝眼镜半自动磨边机定配加工中制模板
ⅱ )标记水平基准线:用直尺测量撑片垂直方向最大距离的中点并标记 ,过中点画一条与三印点平行的水平线,该水平线即为水平基准线。
三、拉丝眼镜半自动磨边机定配加工中制模板
(一) 用原撑片做模板 2.操作步骤: (2)在撑片上标注左右眼及上下方向标记
磨边时为分清左右眼及镜片的上下,一定要在模板上确定鼻侧方向和近眉框方向。 (可在模板的鼻侧上方画一指向鼻侧的箭头,既指明鼻侧方向又指明近眉框方向)
边机各种镜型(全框、半框、打孔)眼镜的装配
二、制模板(model)的方法及其应用
半框眼镜定配制模板的方法: 手工制模板、扫描仪扫描
半框眼镜半自动磨边机加工制模板的方法: 手工制模板: 原撑片(衬片)制模板 塑料板(模板坯料)制模板
拉丝配模表

1.配模指南-拉丝配模四个步骤和关键数据计算方法概要:拉丝配模是金属丝拉拔时根据坯料尺寸及金属丝尺寸确定拉拔道次、拉丝模模孔尺寸及形状的工作,也叫拉拔程序或拉拔路线的制定。
可以分为单道次拉丝配模和多道次拉丝配模。
拉丝配模主要步骤包括以下四个步骤:1.选择坯料;2.确定中间退火次数;3.确定拉拔道次和分配道次延伸系数;4.配模校核.文章就圆形断面金属拉丝和异型断面金属拉丝两种情况,具体介绍拉丝配模步骤和计算方法。
2.滑动式拉丝机配模原理及配模计算实例介绍概要:拉丝配模指的是我们拉制过程中,对每道拉伸线模进行选择的方法。
合理的配模有两个要点,一是机械;滑动式拉丝机有其固定的拉线轮速比,通过实动式拉丝机配模计算实例,计算拉7.2mm铜杆至1.6mm铜线的相关数据;正文开始:写在前面:拉丝配模方法很多,很容易造成混淆,其中最根本的就是滑动系数的取值问题。
取大了有何优、缺点,取小一点又有何优、缺点,弄明白了,就会在工作中游刃有余。
死套某点,在实际中是不可能做到的。
不是简单计算,用公式一算就满足了。
如果你厂有50台机。
同是拉6种以上规格丝,如果按照某一种公式死套,想想最小要配几套模具。
所谓拉丝模具配完后,就要估计哪只模可能会引起断线。
哪个模会缩丝。
要估计断线是何原因,不要一断线就是铜杆空心,实际上,70%以上的空心铜与断线是自己拉丝造成的。
拉丝模具配模方法最常见的有以下三种:1.应用绝对滑动系数配模方法(J法),应用基础:拉丝机连续拉线,线材在每个塔轮上,单位时间体积是相等的。
2.传统理论配模方法(C法配模),以往定义符号从进线始,这里为了计算机计算方便(用Execl电子表格),刚好相反从出口模开始.3.新理论配模方法(X法配模),应用基础:即安全(不断线)顺利(能连续)拉线,又能把滑动降到最低.三种配模方法各有特点.C法,对设备,模具要求不严;X法和J法对设备精度要求高,对模具公差要求严,操作者的操作水平要求高.X法与系列套模相结合,效果更好.下面对这三种配模方法做具体介绍:一、应用绝对滑动系数配模方法(J法)应用基础:拉丝机连续拉线,线材在每个塔轮上,单位时间体积是相等的。
配模指南-拉丝配模四个步骤和关键数据计算方法

配模指南-拉丝配模四个步骤和关键数据计算方法整理:拉丝模1.什么是拉丝配模?拉丝配模是金属丝拉拔时根据坯料尺寸及金属丝尺寸确定拉拔道次、拉丝模模孔尺寸及形状的工作,也叫拉拔程序或拉拔路线的制定。
可以分为单道次拉丝配模和多道次拉丝配模。
单道次拉丝配模指在一台拉丝机上每次拉拔时金属丝只通过一个模子的拉拔配模。
多道次拉丝配模指在一台拉丝机上金属丝同时连续通过几个或十几个模子的拉拔配模。
它又分滑动式连续多道次拉丝配模和非滑动式连续多道次拉丝配模。
2.拉丝配模步骤和注意事项:拉丝配模主要步骤包括以下4个步骤:(1)选择坯料;(2)确定中间退火次数;(3)确定拉拔道次和分配道次延伸系数;(4)配模校核。
拉丝配模过程中有以下3点注意事项:(1)在保证拉丝过程稳定的条件下,充分利用金属的塑性和最少的拉拔道次达到提高拉拔生产率的目的;(2)合理分配道次延伸系数,以获得精确的尺寸、正确的断面形状及良好的表面质量;(3)配模参数与拉丝机的主要参数相适应。
下面就圆形断面金属拉丝和异型断面金属拉丝两种情况,具体介绍拉丝配模步骤和计算方法。
一、圆断面金属丝配模具体方法1.坯料选择:坯料的尺寸和断面形状应根据成品金属丝要求的状态、尺寸精度、力学性能、金属丝尺寸系列化生产及坯料的生产方式等情况选择确定。
圆丝的坯料一般为轧制、挤压及铸轧的盘条,也有采用连铸或锻造的坯料。
型丝的坯料,除了考虑尺寸大小外,还需考虑断面形状的相似性,以利于由坯料的断面形状逐步过渡到成品型丝断面形状的要求,如矩形丝选择矩形断面的坯料,双沟电车线选择圆形断面的线坯等。
2.确定中间退火次数:在拉拔过程中明显发生加工硬化的金属及合金,需要进行中间退火,恢复塑性利于继续拉拔。
对塑性好的如铜、铝等的粗线,可以不进行中间退火。
中间退火次数N用下式确定:(1)式中λΣ为由坯料至成品丝的总延伸系数;为退火问的平均总延伸系数。
3.确定拉拔道次和分配道次延伸系数拉拔道次n根据总延伸系数(无中间退火时)λΣ或两次退火间的总延伸系数λT和道次平均延伸系数确定:道次延伸系数分配分中间道次的延伸系数相等的及顺次递减的两种方案。
拉丝原理及配模

0),反之进线端甭紧则会加大反拉力,从而加大前拉力, 容易导致断线。具体计算过程参加宣天鹏有关滑动拉丝 基本条件的论文,最终得到的结果是:通过拉丝模线材 的延伸系数应
大于相邻塔轮的梯度,表示为μ/ε>1,这样线材在拉拔过 程时而紧绕在塔轮上同步前进,时而松开打滑,当然这 就会对塔轮表面产生磨损,增加功率损耗。 塔轮转动 的线
动率;累积的滑动系数是各道次滑动系数的连乘,累积 滑动率为1-1/累积滑动系数。 资料显示,滑动系数一般 在1.02-1.10之间,铜包钢与模具有着良好的润滑
作用,与塔轮的相对磨损也小,所以有学者建议滑动系 数取在1.01-1.04之内。我们倾向于1.02。 实际拉拔的过 程,因为每道次都预设了滑动,那么离成品模越
滑系数就更大。各道次伸长的分布规律一般是第一道低 一些,这是因为线坯的接头强度较低,线材弯曲不直, 表面粗糙,粗细不匀等,所以预留安全系数要大一些。 第二、三道可以取
高一些,因为经过第一道拉拔后,各种影响安全系数的 因素大大下降,同时金属的变形硬化程度也很小,这时 可以充分利用金属的塑性,而在以后的各道次中,伸长 可以逐道递减,这
与塔轮的相对磨损也小,所以有学者建议滑动系数取在 1.01-1.04之内。我们倾向于1.02。 实际拉拔的过程,因 为每道次都预设了滑动,那么离成品模越远的道
次,塔轮与铜包钢线之间的滑动就越大,塔轮表面磨损 也就越严重,这种滑动的不均匀性会缩短塔轮的使用寿 命,因此要考虑一个累积滑动效应,它是从成品模开始 向进线方向以连乘
口处,依次逐渐降低滑动率,最后降到1.01,箭头图表示 为: 1.01—1.01—1.01模时,与伸长相对应的有一个减面率的概念,也就 是面积减少的比例。比如从1.1拉到1.02,面积比例是 1.1*1.1:1.02*1.02=1.163,进线是1
拉丝工艺操作规程
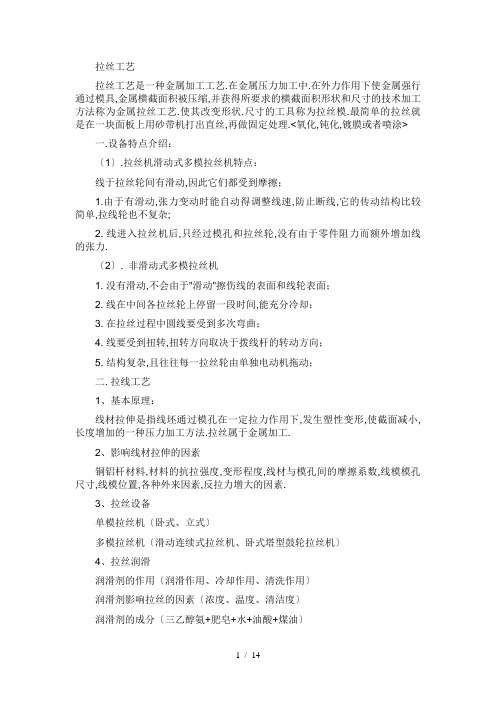
拉丝工艺是一种金属加工工艺.在金属压力加工中.在外力作用下使金属强行通过模具,金属横截面积被压缩,并获得所要求的横截面积形状和尺寸的技术加工方法称为金属拉丝工艺.使其改变形状.尺寸的工具称为拉丝模.最简单的拉丝就是在一块面板上用砂带机打出直丝,再做固定处理.<氧化,钝化,镀膜或者喷涂>一.设备特点介绍:〔1〕.拉丝机滑动式多模拉丝机特点:线于拉丝轮间有滑动,因此它们都受到摩擦;1.由于有滑动,张力变动时能自动得调整线速,防止断线,它的传动结构比较简单,拉线轮也不复杂;2. 线进入拉丝机后,只经过模孔和拉丝轮,没有由于零件阻力而额外增加线的张力.〔2〕. 非滑动式多模拉丝机1. 没有滑动,不会由于"滑动"擦伤线的表面和线轮表面;2. 线在中间各拉丝轮上停留一段时间,能充分冷却;3. 在拉丝过程中圆线要受到多次弯曲;4. 线要受到扭转,扭转方向取决于拨线杆的转动方向;5. 结构复杂,且往往每一拉丝轮由单独电动机拖动;二. 拉线工艺1、基本原理:线材拉伸是指线坯通过模孔在一定拉力作用下,发生塑性变形,使截面减小,长度增加的一种压力加工方法.拉丝属于金属加工.2、影响线材拉伸的因素铜铝杆材料,材料的抗拉强度,变形程度,线材与模孔间的摩擦系数,线模模孔尺寸,线模位置,各种外来因素,反拉力增大的因素.3、拉丝设备单模拉丝机〔卧式、立式〕多模拉丝机〔滑动连续式拉丝机、卧式塔型鼓轮拉丝机〕4、拉丝润滑润滑剂的作用〔润滑作用、冷却作用、清洗作用〕润滑剂影响拉丝的因素〔浓度、温度、清洁度〕润滑剂的成分〔三乙醇氨+肥皂+水+油酸+煤油〕按材质分〔硬质合金模、钻石模、聚金模、钢模〕︳︳︳︳大量生产生产细线中小拉机中间模大截面6、拉丝配模道次延伸系数的选择线径㎜铜铝≧1.01.30~1.551.20~1.500.1~1.01.20~1.351.10~1.200.01~0.11.10~1.25——各道次延伸系数范围延伸系数的定义:拉制后线材的长度与拉制前线材长度的比值.7、废品的分析和处理断线的原因〔接头不牢、有杂物、配模不合理、模孔性状不正确或不光滑、反拉力过大、绞轮上压线、酸洗不净〕常见的表面不合格{〔擦伤、碰伤、刮伤、〕〔起皮、麻坑、三角口、毛刺〕〔波形、蛇行〕〔氧化、水渍、油污〕}三.常见的不合格品问题分析与解决办法:〔1〕产品的外径偏差的精确控制由于铜线拉丝设备的不间断生产,拉丝的速度也会逐渐地与退火不同步,这就会使拉丝时由于牵引速度的时快时慢而使线径出现间断的、不规则的变化.该现象产生的原因有以下几点:1. 储线轮上的张力的不稳定.生产车间使用气压的地方可能较多,这会造成拉丝机气泵的气压时大时小,这也就使储线器的张力不是恒定的,而由于收线的速度是不变的,这就使拉丝所受的拉力也非恒值,由此可造成单丝外径偏差无法精确控制.2. 铜线在退火轮上的颤动.这使得铜线在时松时紧的状态下进行退火,退火的电流密度时大时小,而铜线在较高速度下的强度是比较低的,因此容易造成铜线在退火轮上打火,使铜线的表面由于火花的作用而线径不均匀.3. 由于主电机齿轮箱的长期使用而造成的磨损.这能使拉丝的定速轮速度与牵引速度以与收线速度不相匹配,从而形成单丝的拉细.解决方法:对储线器进行很好的润滑,避免其在高速运转时对线造成反向的磨擦力进而使线拉细;调整好线的张力,使拉丝的行程始终紧贴于退火轮;保证退火轮钢圈的完好,避免因钢圈的表面缺陷而使退火电流不稳定.根据拉丝机的实际情况重新对拉丝机进行配模:根据拉丝原理来调整退火轮传动轴上的可调节的三角带轮的直径,使退火轮转速/定速轮转速=前滑系数×定速轮直径/退火轮直径,其中定速轮和退火轮的直径是已知的,定速轮和退火轮的转速也可以测出,由此可得到前滑系数,由滑差系数即可对本拉丝机进行重新配模,这样配出的模具才能满足要求.〔2〕.拉丝机拉出的单丝表面时有不同程度的氧化.该问题的产生可能有以下原因:1. 密封室中冷却水的温度过高,超过了40℃,这样密封室对单丝就起不到所要求的冷却效果,造成单丝在退火后温度仍然很高,高温下遇到空气中的氧气而氧化.2. 密封室中的冷却液的皂化液含量不够,这就会使单丝与各导轮的磨擦力增加,进而使单丝温度再度上升,造成单丝表面氧化.3. 密封室中冷却水的水压与水量不够,使单丝不能够达到满意的冷却效果.解决方法:经常检查冷却循环水的设备是否运转正常,冷却效果是否正常;在密封室中隔一定的时间就加入能够提高皂化液浓度的物质,这样可以改变冷却水中皂化液的含量,保证单丝能够在导轮上正常运转;定期检查循环水的水压是否正常,在生产时不断根据水压的变化来改变进入密封室中的冷却水的压力与水量.〔3〕. 拉丝生产中经常会出现频繁的断丝现象.出现此种情况主要有以下几个因素造成:1. 拉丝模在不间断的生产中会由于正常磨损而使拉丝模的定径区变大.2. 由于各种杆材的质量问题.在生产过程中,杆材不规则地出现质量缺陷,这就使单丝在拉丝变形中被各种无法预测的张力拉断.此情况在杆材好时较少出现.3. 由于生产中退火电流的不恒定,电流忽然偏高,单丝在退火过程中被拉断或是被突变的强电流熔断.解决方法:根据不同的杆材选取不同的配模方案,在生产中不断摸索.例如在生产上引法生产的铜杆时,拉2.53mm的单丝需要8道拉丝模,而生产同样外径的单丝,若用轧杆时,则要根据要求在配模时多加一块过桥模;在生产前,要对欲生产的铜杆做充分的自检,与时发现铜杆的质量缺陷,根据不同情况与时找到相应对策,或降低拉丝速度,或将此段有缺陷的剔除.生产中不断地观察拉丝的退火电流是否正常,尤其在刚刚启动的时候,特别要注意退火电流的变化,要根据线速的变化来调节退火电流的大小,进而使退火电流慢慢地随着线速的增加而变大,保证设备的正常运行.相信只要在实际生产中着重对以上几点进行控制,铜拉丝产品的质量和生产效率都会有不同程度的提高,才能更好、更快的为下道工序生产提供强有力的生产保障拉丝配模方法大致有一下三种:一、传统理论配模方法〔C法配模〕★符号定义与有关公式以往定义符号从进线始,这里为了计算机计算方便〔用Execl电子表格〕.刚好相反.1. 各道模子孔径:〔出口模〕d1,d2,d3…dn….2. 各道延伸系数:〔定速辊始〕μ1,μ2,μ3…μn…3. 各塔轮增速比:〔定速辊始〕ν1ν2ν3…νn…4. 各道滑动系数:τ1τ2τ3….τn…5. 第n个塔轮绝对〔累计〕滑动系数:Τn=Vn/Un6. 第n个塔轮的线速度:Vn7. 第n个塔轮上铜线的速度:Un8. μn=νn*τn9. dn=dn-1*√μn下面以LH-280/17拉丝机为例,说明配模计算方法:A.确定拉丝机机械参数:每种拉丝机说明书都有设备参数,机械延伸率〔或不同叫法〕,也就是拉丝机相邻塔轮增速比,有的说明书有说明计算.LH-280/17拉丝机的增速比是:1.20:1,〔最后一道:1.15:1〕,即:νn=1.2B.滑动系数τn:中拉机一般取:1.02-1.04,取τn=1.03C.计算线材的延伸系数:μn=νn*τn=1.2*1.03=1.236D.确定进出线规格:进线:2.80;出线:1.00E.配模计算二、新理论配模方法〔X法配模〕★新理论配模基础:低滑动拉线基础是:即安全〔不断线〕顺利〔能连续〕拉线,又能把滑动降到最低.因此滑动系数最低规范要求:1.τ3-τn要求1.0-1.01,在配模计算中平均取:1.0052.安全滑动系数τ2这里介绍确定安全滑动系数τ2的方法,LH-280/17拉丝机,具备满足了低滑动拉线的性能的结构,安全滑动系数是通过降低最后一道塔轮增速比来实现的.因此,安全滑动系数τ2=〔1.2/1.15〕*1.005=1.049.如:LH-200/17拉丝机安全滑动系数τ2=〔1.2/1.15〕*1.005=1.049;B22拉丝机,设计的安全滑动系数τ2=〔1.175/1.15〕*1.005=1.027;B32拉丝机安全滑动系数τ2=〔1.15/1.12〕*1.005=1.032;S20拉丝机安全滑动系数τ2=〔1.12/1.08〕*1.005=1.042;S24拉丝机安全滑动系数τ2=〔1.1/1.08〕*1.005=1.024.☆☆☆☆☆☆☆☆☆☆☆☆☆☆☆☆☆☆☆☆☆☆☆☆☆☆A.确定拉丝机机械参数:每种拉丝机说明书都有设备参数,机械延伸率〔或不同叫法〕,也就是拉丝机相邻塔轮增速比,有的说明书有说明计算.LH-280/17拉丝机的增速比是:1.20:1,〔最后一道:1.15:1〕,即:νn=1.2B.滑动系数:1.τ3-τn取1.0052.安全滑动系数τ2=〔1.2/1.15〕*1.005=1.049C.计算线材的延伸系数:μ1=ν1*τ2=1.15*1.049=1.206μn=1.2*1.005=1.206D.确定进出线规格:进线:2.80;出线:1.00E.配模计算:dn=dn-1*√μn 〔1.00-1.098-1.206-1.325-1.455-1.597-1.754-1.927-2.116-2.323-2.552-2.800〕三、利用绝对滑动系数配模方法★利用绝对滑动系数配模基础:拉丝机连续拉线,线材在每个塔轮上,单位时间体积是相等的.即U1*S1=Un*Sn 〔U1:线材在定速轮上速度,S1:定速轮上线材的截面积〕那么Τn=Vn/UnUn=Vn/Tn,U1=V1设:绝对速比Kn=V1/Vn安全滑动系数Τ2=τ2;其余的Τ3=Τ2+0.001....Τn=Τn-1+0.001☆☆☆☆☆☆☆☆☆☆☆☆☆☆☆☆☆☆☆☆☆☆☆☆☆☆☆☆☆☆☆☆☆A.确定拉丝机机械参数:每种拉丝机说明书都有设备参数,机械延伸率〔或不同叫法〕,也就是拉丝机相邻塔轮增速比,有的说明书有说明计算.LH-280/17拉丝机的增速比是:1.20:1,〔最后一道:1.15:1〕.B.滑动系数:1.安全滑动系数Τ2=τ2=〔1.2/1.15〕*1.005=1.049.2.Τ3-Τn取:Τ3=Τ2+0.001....Τn=Τn-1+0.001〔穿模时,留相对滑动量〕C.确定进出线规格:进线:2.80;出线:1.00D.配模计算:1.先假定定速轮的V1=1000,利用机相邻塔轮增速比,计算出Vn2.通过绝对速比Kn=V1/Vn,再计算Kn3.通过dn=d1×√Kn*Τn,计算出各个模具的规格.〔实际利用EXCEL很方便〕〔1.00-1.098-1.204-1.319-1.446-1.585-1.737-1.903-2.086-2.286-2.506-2 .746-2.800〕四、结束语:通过以上三种配模方法比较,低滑动拉线从节能方面占有很大优势.并且拉丝油损耗降低,塔轮寿命延长,综合效益明显.三种配模方法因地制宜,根据技术水平、管理水平,合理选用.三种配模方法各有特点〔不能说那种不好〕.C法,对设备、模具要求不严;X法和J法对设备精度要求高,对模具公差要求严,操作者的操作水平要求高.X法与系列套模〔见《中拉丝机使用系列套模提高模具利用率》〕相结合,效果更好.欲低滑动拉线节能取得好效果,使用模具和润滑系统也很重要.多方面的提升,才能提高生产水平、技术水平,公司才能整体上一台阶,才能最终达到节能目的.产生环沟的原因:那是由于进入模孔的金属线横截面变化时所受的抗力,和拉伸过程中金属线的振动而产生的周期性压力,导致线模的疲劳破坏.拉线模环沟的出现,加剧模孔的磨损.因为拉线模的模孔出现环沟后,环沟上因松动而剥落的模芯材料小颗粒,象磨料一样地研磨着工作区和定径区.而进入模孔的金属线,则象模棒一样加剧模孔的磨损.此时模孔和金属线之间的摩擦力增加,产生高温,加剧了磨损的过程.一般来说,拉线模在拉伸过程中的磨损,可分为三个阶段.第一是模孔表面尖点磨损阶段,第二是一个低而稳定速率的磨损阶段,三是随着模孔表面磨损沟纹的出现,达到一个高速磨损阶段.拉伸条件对拉线模使用寿命的影响一方面取决于本身的质量,另一方面还取决于拉伸条件〔一〕减缩率的影响在拉伸过程中,;拉线模对金属线产生压力,而金属线在变形时对拉线模壁也产生了一个反压力.拉伸时所用的减缩率愈大,孔壁对金属线产生的压力也就愈强,而金属线对孔壁所产生的反作用力也随之增强,此力如大于模子本身的抗张能力,则拉线模就会崩裂.〔二〕润滑剂的影响在拉伸过程中,润滑剂的质量与润滑剂供给是否充分都影响拉线模的使用寿命.润滑剂在拉线过程中具有润滑作用、冷却作用、清洗作用和防锈作用.〔三〕金属坯料表面质量的影响金属坯料表面如有氧化层、砂土或者其他杂质,对拉线模的使用寿命带来不利影响.因为金属表面的氧化层硬而脆,当金属坯料通过模孔时,它会象磨料一样造成拉线模模孔很快磨损与擦伤表面.所以在拉伸前,必须把它酸洗掉;在坯料堆放时,要注意堆放场地的整洁,避免与砂土与其他杂质接触.滑动式拉线机的特点:〔1〕线材与绞轮之间有滑动,因此都要受到磨损,所以主要用于具有中等强度的铜线拉伸.〔2〕张力控制敏感,传动系统简单,电气控制要求不十分严格.〔3〕总的加工率大,适合塑性好的金属线材拉伸.〔4〕拉伸速度高.〔5〕易于实现机械化、自动化.拉线模模孔各区域的名称和作用入口区和润滑区入口区一般带有圆弧,便于拉伸金属进入工作区,而不致被模孔边缘擦伤.润滑区是导入润滑剂,使拉伸材料得到润滑.工作区工作区是金属拉伸塑性变形的基本部分,一般来说,其高度不小于孔径.如过小,被拉伸的金属对线模工作区将产生过大的压力,使拉伸应力显著增加,导致拉线模磨损过快.工作区高度,随着拉伸材料的性质,与其直径和润滑情况而有所不同,其选择的原则是:1. 拉伸软金属线时,应较硬金属线短.2. 拉伸小直径线材时,应较大直径线材短.3. 湿式润滑拉伸时,应较干式润滑短.工作锥角的选择原则:1. 压缩率愈小,工作锥角应愈小.2. 拉伸线材愈硬,工作锥角应愈小.3. 拉伸小直径材料较大直径材料小.定径区高度的选择原则:1. 拉伸软金属材料较硬金属材料短.2. 拉伸大直径材料较小直径材料短.3. 湿式润滑拉伸较干式润滑拉制短.模孔的拉伸半角与拉伸间的关系拉伸力是随着拉伸半角的增大而减小,到一定数值后,又随着拉伸半角的继续增大逐渐增大.模孔形状与拉伸间的关系在圆锥形的模孔中,线材在拉伸时的变形程度是平均的.由于复合力逐渐增大,因此愈近模孔出口处,复合力也就愈大.所以在接近出口处的模孔容易崩裂,致使拉线模使用寿命缩短.在圆弧形模孔中,金属在拉伸时,开始时变形程度较大,以后逐渐下降.变形抗力不集中在出口处,而在压缩区.圆弧形模孔在拉伸的过程中,是先把圆弧形磨成直线后,再继续向外移,因而增加了拉线模的使用寿命.圆弧拉线模模孔的缺点;由于线材与模孔孔壁的接触面增大,因此拉伸阻力也相应增大,即在拉伸过程中,拉伸力消耗较大.定径区长短与拉伸间的关系定径区的长短,与消耗在克服此区的拉伸阻力的大小有直接的关系.定径区愈高,拉伸阻力也就愈大,必须增加拉伸力,以达到将线材拉出模孔的目的.因此,定径区过高,金属线材拉出模孔后,就容易引起缩径.定径区高度过短,容易产生金属线材弯曲和表面不平的情况,同时有降低了模具寿命.模孔的光洁程度与拉伸间的关系拉伸模孔的光洁程度,是决定模孔孔径和线材之间的摩擦力大小的重要因素.模孔光洁程度愈差,孔壁和线材之间的摩擦阻力就愈大,克服阻力所消耗的拉伸力就愈大.在同样的拉伸半角的条件下,高度抛光的模孔所需的拉伸力,一般抛光的模孔所需的拉伸力小.模孔的光洁程度不仅影响拉伸力的增减,而且还会影响被拉伸金属线材表面的质量.拉线模模孔光洁度高,被拉伸的金属线材表面也就光滑;反之,模孔光洁度不高,所拉的金属线材表面就比较粗糙.拉线模的模孔光洁度愈差,模子的使用寿命就愈短.KWS—1006超声波清洗机KWS—1006清洗机是由超声波发生器、换能器、自动温控加热系统、清洗槽、机架与整机外罩组成.超声波发生器:产生超音频信号,以供给换能器.换能器:将超声波发生器产生的超音频电能转换成高音频机械振荡而传入清洗液中,从而达到超声清洗的目的.超声清洗槽:盛载清洗液,待洗工件在此槽进行超声波清洗,可将工件表面与缝隙中的脏物振落.自动温控系统:自动控制清洗槽中的清洗液温度与加热与否.超声波清洗的基本工作原理利用超音频电能,通过换能器转换成高频机械震荡而传入到清洗液中.超声波在清洗液中疏密相间地向前辐射,使液体流动,并产生数以万计的微笑气泡,这些气泡在超声波纵向传播的负压区形成与生长,而在正压区迅速闭和〔熄灭〕.这种小气泡的形成、生长、迅速闭和称为空化现象.在空化现象中气泡闭和时形成超过1000个大气压的瞬间高压,连续不断产生的瞬间高压就像一连串小爆炸不断地轰击物体表面,使物体表面与缝隙中的污垢迅速剥落,这种空化侵蚀作用就是超声波清洗原理.使用注意事项:1. 清洗槽内无清洗液时,绝对不能启动超声,否则会导致损坏换能器的严重后果.2. 不得将物体直接放入清洗槽底,如有异物落入槽底应与时取出,否则会损坏超声波发生器.3. 不可将液体溅湿换能器与超声波发生器.4. 起切不可使用可燃性液体作清洗液.5. 清洗槽内积物过多时,应与时放液冲洗清除.6. 槽内无清洗液或清洗液面未超过2/3深度时,绝对禁止加热,否则会损坏发热板.7. 旧液换新液时,应在温度控制器置于0℃的位置,超声开关置于关的位置,与液体温度在常温下进行.8. 环境湿度过大时,应经常将换能器上附着的潮气、水珠吹干.9. 在清洗槽内注满清洗液的情况下应尽量避免推动或搬移机体.滑动式连续拉伸的特点第一个特点是除K道外,其余各道都存在滑动.保证正常滑动的办法是在相邻两绞轮间,如果让拉线后的长度与拉线前的长度之比大与后面与前面的绞轮线速度之比,就会在前面绞轮上产生需要的滑动.当τn=1时,n-1道没有滑动.由于模具的磨损决不会按同一规律发展.再由于其它因素影响,这种情况几乎维持不住,就会很快断线.当τn<1时,一开车就断线,不能拉.当τn>1时,在n-1道绞轮上有滑动,能自动调节张力,保持长时间不断线.τn=1.015~104有时τn可达1.10.一般线径越细,τ值应较小,成品处的τ值也应小些.第二个特点是除第一道外,其余各道均存在反拉力.影响拉伸力的因素:1. 铜、铝杆〔线〕材料.在其它条件相同时,拉铜线比拉铝线的拉伸力大,拉铝线容易断,所以拉铝线应取较大的安全系数.2. 材料的抗拉强度.材料的抗拉强度因素很多,如材料的化学成分、压延工艺等,抗拉强度高则拉伸力大.3. 变形程度.变形程度越大,在模孔中变形长度越长,因而增加了模孔对线的正压力,摩擦力也随之增加,所以拉伸力也增加.4. 线材与模孔间的摩擦系数.摩擦系数越大,拉伸力也越大.摩擦系数由线材的材料和模芯材料的光洁度、润滑剂的成分与数量决定.铜杆表面酸洗不彻底,表面有残存的氧化亚铜细粉,也使拉伸力增大.5. 线模模孔工作区和定径区的尺寸和形状.在线模工作区圆锥角增加,有两个因素影响着拉制力,一方面摩擦表面减少,摩擦力相应减少;另一方面金属在变形区的变形,抗力随圆锥角的增大而增大,使拉伸力变大.6. 线模位置.线模安放不正或模座歪斜也会增加拉伸力,使线径与表面质量达不到标准要求.7. 各种外来因素.如进线不直,放线时打结,拉线过程中线的抖动,都会使拉伸力增大,严重时引起断线.8. 反拉力增大的因素.反拉力增大则拉伸力增加.如放线架制动力过大,前一道离开绞轮线材的张力等会增加后一道的反拉力.铜的物理、机械和工艺性能熔点:1083℃沸点:约2500℃电阻率:0.017241Ω·mm2/m密度:8.89〔20℃〕抗拉强度:216~235N/mm2<软>363~412 N/mm2<硬>伸长率:40%~45%〔软〕;4%~6%〔硬〕铸造温度:1150~1200℃最低再结晶温度:200~270℃再结晶退火温度:500~700℃铜中所含杂质与微量元素将影响导电等各方面的性能,其中以磷、硅、铁、砷影响最大,银、镉、铬、锌影响较小,对铜的加工性能影响不大,但可不同程度提高铜的强度和硬度.氧含量的增加将显著降低铜的工艺性能和耐腐蚀性,使焊接、镀锡等过程不易进行,拉伸后的线材表面易发毛.含氧铜在还原性气体中加热,还会产生"氢气病",造成表面裂开.配模注意事项:1. 配模结果如果出现第一道的µ大于计算值或小于γ值时,均无害.只要增大的µ是在被拉金属能够承受的限度之内,因为在这里不存在γ,故µ增大不会导致滑动增加,µ较小时也不会拉细拉断.2. 如因生产需要或为了保证产品性能而必须加大进线直径d0,即需要进行所谓"超规格"拉伸时,应核算有关各道的拉伸力和电机功率.对滑动式拉线机应尽量避免超规格拉伸,以免导致滑动损耗大;其次,在超规格拉伸中必然要加大某些道次的µ值,这些道次应尽量放在前几道〔即进线端上〕,以减轻滑动的累积程度.3. 实践证明,适当提高线径d的取值精度对减少滑动损耗、保持各道延伸系数或积线系数的均匀性,减少拉细拉断现象和顺利拉伸,尤其对高速拉伸是非常必要的,也是能够做到的.当d以mm为单位时,在配模中通常应取三位有效数字,即:d>10mm时,小数点后保留一位数字;d<10mm和>1mm时,小数点后保留两位数字;d<10mm时,小数点后保留三位数字.4. 拉伸道次和配模尺寸的计算,往往需要重复计算和进行必要的调整.例如计算所得道次带有小数点,或由d起推算各道d值至d0时同预定的进线直径有出入等情况时均需重新计算.前者应选择就近的整数〔道次〕,然后重新安排各道次延伸系数;后者应适当修改前〔进线端〕几道的d值和延伸系数,以便使d0同实际进线直径相符.而所作的调整和修改,均应使各该道次的滑动系数τ保持在合理的范围以内.加工出口区最应注意的是出口区和模孔的同心度.拉线模的倒喇叭作用是保护线材消除拉线模变形区定径区连接处尖角的目的是减小拉伸阻力拉丝与绞线工艺学拉丝机滑动式多模拉丝机特点线于拉丝轮间有滑动,因此它们都受到摩擦;1.由于有滑动,张力变动时能自动得调整线速,防止断线,它的传动结构比较简单,拉线轮也不复杂;2.线进入拉丝机后,只经过模孔和拉丝轮,没有由于零件阻力而额外增加线的张力.二、非滑动式多模拉丝机1.没有滑动,不会由于"滑动"擦伤线的表面和线轮表面;2.线在中间各拉丝轮上停留一段时间,能充分冷却;3.在拉丝过程中圆线要受到多次弯曲;4.线要受到扭转,扭转方向取决于拨线杆的转动方向;5.结构复杂,且往往每一拉丝轮由单独电动机拖动;中间某一道如断线拉线工艺学1、基本原理:线材拉伸是指线坯通过模孔在一定拉力作用下,发生塑性变形,使截面减小,长度增加的一种压力加工方法.拉丝属于金属加工.2、影响线材拉伸的因素铜铝杆材料,材料的抗拉强度,变形程度,线材与模孔间的摩擦系数,线模模孔尺寸,线模位置,各种外来因素,反拉力增大的因素.3、拉丝设备单模拉丝机〔卧式、立式〕多模拉丝机〔滑动连续式拉丝机、卧式塔型鼓轮拉丝机〕4、拉丝润滑润滑剂的作用〔润滑作用、冷却作用、清洗作用〕润滑剂影响拉丝的因素〔浓度、温度、清洁度〕润滑剂的成分〔三乙醇氨+肥皂+水+油酸+煤油〕5、模具按材质分〔硬质合金模、钻石模、聚金模、钢模〕︳︳︳︳大量生产生产细线中小拉机中间模大截面6、拉丝配模道次延伸系数的选择。
拉丝配模的三种方法

1.配模指南-拉丝配模四个步骤和关键数据计算方法概要:拉丝配模是金属丝拉拔时根据坯料尺寸及金属丝尺寸确定拉拔道次、拉丝模模孔尺寸及形状的工作,也叫拉拔程序或拉拔路线的制定。
可以分为单道次拉丝配模和多道次拉丝配模。
拉丝配模主要步骤包括以下四个步骤:1.选择坯料;2.确定中间退火次数;3.确定拉拔道次和分配道次延伸系数;4.配模校核.文章就圆形断面金属拉丝和异型断面金属拉丝两种情况,具体介绍拉丝配模步骤和计算方法。
2.滑动式拉丝机配模原理及配模计算实例介绍概要:拉丝配模指的是我们拉制过程中,对每道拉伸线模进行选择的方法。
合理的配模有两个要点,一是机械;滑动式拉丝机有其固定的拉线轮速比,通过实动式拉丝机配模计算实例,计算拉7.2mm铜杆至1.6mm铜线的相关数据;正文开始:写在前面:拉丝配模方法很多,很容易造成混淆,其中最根本的就是滑动系数的取值问题。
取大了有何优、缺点,取小一点又有何优、缺点,弄明白了,就会在工作中游刃有余。
死套某点,在实际中是不可能做到的。
不是简单计算,用公式一算就满足了。
如果你厂有50台机。
同是拉6种以上规格丝,如果按照某一种公式死套,想想最小要配几套模具。
所谓拉丝模具配完后,就要估计哪只模可能会引起断线。
哪个模会缩丝。
要估计断线是何原因,不要一断线就是铜杆空心,实际上,70%以上的空心铜与断线是自己拉丝造成的。
拉丝模具配模方法最常见的有以下三种:1.应用绝对滑动系数配模方法(J法),应用基础:拉丝机连续拉线,线材在每个塔轮上,单位时间体积是相等的。
2.传统理论配模方法(C法配模),以往定义符号从进线始,这里为了计算机计算方便(用Execl电子表格),刚好相反从出口模开始.3.新理论配模方法(X法配模),应用基础:即安全(不断线)顺利(能连续)拉线,又能把滑动降到最低.三种配模方法各有特点.C 法,对设备,模具要求不严;X法和J法对设备精度要求高,对模具公差要求严,操作者的操作水平要求高.X法与系列套模相结合,效果更好.下面对这三种配模方法做具体介绍:一、应用绝对滑动系数配模方法(J法)应用基础:拉丝机连续拉线,线材在每个塔轮上,单位时间体积是相等的。
拉丝原理及配模解析

2%之间,加上滑动率,一般将配比定为13-15%之间,依 据相邻模具的出线口径大小,我们可以直接算出减面率 或者伸长率,或者反过来,已知道某道模具的大小,已 知需要的
与塔轮的相对磨损也小,所以有学者建议滑动系数取在 1.01-1.04之内。我们倾向于1.02。 实际拉拔的过程,因 为每道次都预设了滑动,那么离成品模越远的道
次,塔轮与铜包钢线之间的滑动就越大,塔轮表面磨损 也就越严重,这种滑动的不均匀性会缩短塔轮的使用寿 命,因此要考虑一个累积滑动效应,它是从成品模开始 向进线方向以连乘
伸长率,可以推算上一道次模具的大小。值得一提的是, 在拉拔软线时,一定要注册出线模的局部压缩不能太大, 否则定速轮张力过大会将软线拉伤,导致线径缩小,延 伸下降。
在拉丝领域,人们普遍使用滑动式水箱拉丝机,也就是 卷筒与钢丝线速度存在差距,这样钢丝才能在与卷筒的 接触面打滑,从而产生滑动摩擦力,这个
0),反之进线端甭紧则会加大反拉力,从而加大前拉力, 容易导致断线。具体计算过程参加宣天鹏有关滑动拉丝 基本条件的论文,最终得到的结果是:通过拉丝模线材 的延伸系数应
大于相邻塔轮的梯度,表示为μ/ε>1,这样线材在拉拔过 程时而紧绕在塔轮上同步前进,时而松开打滑,当然这 就会对塔轮表面产生磨损,增加功率损耗。 塔轮转动 的线
力量带动钢丝在每个模具前后实现拉拔。 首先是拉丝
生产的效率问题,参照钢丝生产效率的计算,最关键的 是机器的利用率,出线的大小,以及最快收线速度。如 果按每小时
是有直接关系的,在我公司常规生产中,通过分析统计 发现,铜层变化几乎可以忽略。 再次是模具的工作问
拉丝配模计算

拉丝配模计算信息来源:金属制品日期:2013-12-30 点击:33 文字大小:[大][中][小]拉丝的方式有单拉和连拉两种,单次拉丝机每次通过一个模具拉拔,当一盘丝拉完后,将丝材从卷筒上取下,重新穿头,进行下道次的拉拔。
为提高拉拔速度和减少辅助操作时间,提高生产效率,常将数台单拉机串联起来,组成连续拉丝机,这样一次可连续穿几个模子,实现连续拉拔。
显而易见,在连续拉拔中,丝材直径变细,长度增加,要保证连拉正常运行,丝材与各卷筒(塔轮)之间有一定的配合关系的。
根据通过模具后丝材与卷筒(塔轮)有无相对运动,连续拉丝机可分为非滑动式和滑动式两种。
老式积线式滑轮拉丝机和现代直线式拉丝机拉拔过程中丝材与卷筒之间没有相对滑动,称为非滑动式拉丝机。
水箱式拉丝机拉拔过程中,丝材和塔轮之间存在相对滑动,称为滑动式拉丝机。
9.1. 非滑动拉丝机配模计算9.1.1. 拉拔道次估算减面率是实际生产中最常使用的变形参数,用同一道次减面率连续拉拔数道次后的总减面率,并不等于各道次减面率之和,为便于根据总减面率确定拉拔道次,提供道次减面率与总减面率计算表,如表12。
拉拔时,总减面率的选择和各道次之间减面率分配方法可参考本文6.6节提供的原则确定。
此外线材直径和强度与摩擦力也有一定的关系。
摩擦力过小,牵引力不足,易引起断丝。
摩擦力过大,在滑动时,丝材不易松开,将引起该级阶梯伸出端丝材松弛,塔轮表面压线,甚至断头。
丝材在塔轮表面缠绕圈数过多和塔轮表面出现粗糙或出现沟槽都是造成摩擦力过大的主要原因。
因此,实际操作中一般前几个模子出线端绕2~3圈,接近成品时绕1~2圈。
拉拔较细丝时,所绕圈数应更少,甚至只绕半圈。
十四模拉丝机一般只绕半圈。
9.2.2. 滑动式拉丝机配模计算在滑动式拉丝机上,除最后一道次(K道次)线速等于轮速(B K=V K),因而没有滑动外,其余各道次的轮速均大于线速(V n>B n)。
表示滑动程度大小的概念有:绝对滑动量,相对滑动率(简称滑动率),相对前滑系数(简称滑动系数),累计滑动率,累计滑动系数。
常见的机械拉丝的方式有哪些
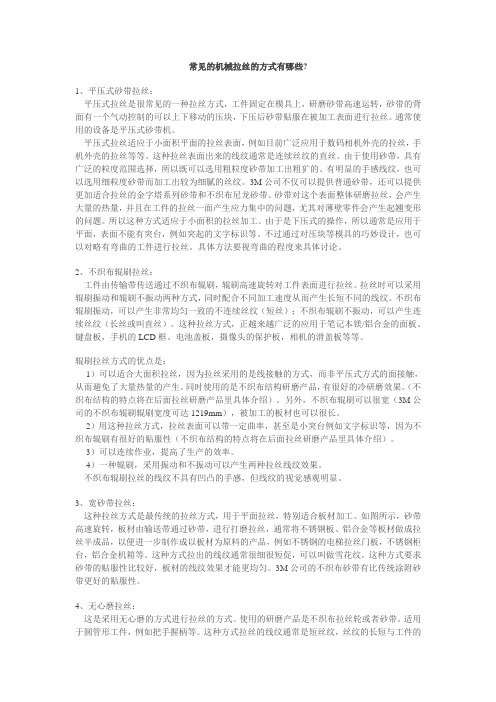
常见的机械拉丝的方式有哪些?1、平压式砂带拉丝:平压式拉丝是很常见的一种拉丝方式,工件固定在模具上,研磨砂带高速运转,砂带的背面有一个气动控制的可以上下移动的压块,下压后砂带贴服在被加工表面进行拉丝。
通常使用的设备是平压式砂带机。
平压式拉丝适应于小面积平面的拉丝表面,例如目前广泛应用于数码相机外壳的拉丝,手机外壳的拉丝等等。
这种拉丝表面出来的线纹通常是连续丝纹的直丝。
由于使用砂带,具有广泛的粒度范围选择,所以既可以选用粗粒度砂带加工出粗犷的、有明显的手感线纹,也可以选用细粒度砂带而加工出较为细腻的丝纹。
3M公司不仅可以提供普通砂带,还可以提供更加适合拉丝的金字塔系列砂带和不织布尼龙砂带。
砂带对这个表面整体研磨拉丝,会产生大量的热量,并且在工件的拉丝一面产生应力集中的问题,尤其对薄壁零件会产生起翘变形的问题。
所以这种方式适应于小面积的拉丝加工。
由于是下压式的操作,所以通常是应用于平面,表面不能有突台,例如突起的文字标识等。
不过通过对压块等模具的巧妙设计,也可以对略有弯曲的工件进行拉丝。
具体方法要视弯曲的程度来具体讨论。
2、不织布辊刷拉丝:工件由传输带传送通过不织布辊刷,辊刷高速旋转对工件表面进行拉丝。
拉丝时可以采用辊刷振动和辊刷不振动两种方式,同时配合不同加工速度从而产生长短不同的线纹。
不织布辊刷振动,可以产生非常均匀一致的不连续丝纹(短丝);不织布辊刷不振动,可以产生连续丝纹(长丝或叫直丝)。
这种拉丝方式,正越来越广泛的应用于笔记本镁/铝合金的面板、键盘板,手机的LCD框、电池盖板,摄像头的保护板,相机的滑盖板等等。
辊刷拉丝方式的优点是:1)可以适合大面积拉丝,因为拉丝采用的是线接触的方式,而非平压式方式的面接触,从而避免了大量热量的产生。
同时使用的是不织布结构研磨产品,有很好的冷研磨效果。
(不织布结构的特点将在后面拉丝研磨产品里具体介绍)。
另外,不织布辊刷可以很宽(3M公司的不织布辊刷辊刷宽度可达1219mm),被加工的板材也可以很长。
拉丝工艺设计操作规程

拉丝工艺拉丝工艺是一种金属加工工艺。
在金属压力加工中.在外力作用下使金属强行通过模具,金属横截面积被压缩,并获得所要求的横截面积形状和尺寸的技术加工方法称为金属拉丝工艺。
使其改变形状.尺寸的工具称为拉丝模。
最简单的拉丝就是在一块面板上用砂带机打出直丝,再做固定处理。
(氧化,钝化,镀膜或者喷涂)一.设备特点介绍:〔1〕.拉丝机滑动式多模拉丝机特点:线于拉丝轮间有滑动,因此它们都受到摩擦;1.由于有滑动,*力变动时能自动得调整线速,防止断线,它的传动构造比拟简单,拉线轮也不复杂;2.线进入拉丝机后,只经过模孔和拉丝轮,没有由于零件阻力而额外增加线的*力。
〔2〕. 非滑动式多模拉丝机1.没有滑动,不会由于"滑动〞擦伤线的外表和线轮外表;2.线在中间各拉丝轮上停留一段时间,能充分冷却;3.在拉丝过程中圆线要受到屡次弯曲;4.线要受到扭转,扭转方向取决于拨线杆的转动方向;5.构造复杂,且往往每一拉丝轮由单独电动机拖动;二.拉线工艺1、根本原理:线材拉伸是指线坯通过模孔在一定拉力作用下,发生塑性变形,使截面减小,长度增加的一种压力加工方法。
拉丝属于金属加工。
2、影响线材拉伸的因素铜铝杆材料,材料的抗拉强度,变形程度,线材与模孔间的摩擦系数,线模模孔尺寸,线模位置,各种外来因素,反拉力增大的因素。
3、拉丝设备单模拉丝机〔卧式、立式〕多模拉丝机〔滑动连续式拉丝机、卧式塔型鼓轮拉丝机〕4、拉丝润滑润滑剂的作用〔润滑作用、冷却作用、清洗作用〕润滑剂影响拉丝的因素〔浓度、温度、清洁度〕润滑剂的成分〔三乙醇氨+肥皂+水+油酸+煤油〕5、模具按材质分〔硬质合金模、钻石模、聚金模、钢模〕︳︳︳︳大量生产生产细线中小拉机中间模大截面6、拉丝配模道次延伸系数的选择线径㎜铜铝≧1.01.30~1.551.20~1.500.1~1.01.20~1.351.10~1.200.01~0.11.10~1.25——各道次延伸系数*围延伸系数的定义:拉制后线材的长度与拉制前线材长度的比值。
拉丝模具加工工艺

拉丝模具加工工艺ﻫ直纹拉丝模具是指在铝板表面用机械磨擦的方法加工出直线纹路。
它具有刷除铝板表面划痕和装饰铝板表面的双重作用。
直纹拉丝有连续丝纹和断续丝纹两种。
连续丝纹可用百洁布或不锈钢刷通过对铝板表面进行连续水平直线磨擦(如在有靠现装置的条件下手工技磨或用刨床夹住钢丝刷在铝板上磨刷)获取。
改变不锈钢刷的钢丝直径,可获得不同粗细的纹路。
断续丝纹一般在刷光机或擦纹机上加工制得。
制取原理:采用两组同向旋转的差动轮,上组为快速旋转的磨辊,下组为慢速转动的胶辊,铝或铝合金板从两组辊轮中经过,被刷出细腻的断续直纹。
ﻫ乱纹拉丝是在高速运转的铜丝刷下,使铝板前后左右移动磨擦所获得的一种无规则、无明显纹路的亚光丝纹。
这种加工,对铝或铝合金板的表面要求较高。
波纹一般在刷光机或擦纹机上制取。
利用上组磨辊的轴向运动,在铝或铝合金板表面磨刷,得出波浪式纹路。
旋纹也称旋光,是采用圆柱状毛毡或研石尼龙轮装在钻床上,用煤油调和抛光油膏,对铝或铝合金板表面进行旋转抛磨所获取的一种丝纹。
它多用于圆形标牌和小型装饰性表盘的装饰性加工。
螺纹是用一台在轴上装有圆形毛毡的小电机,将其固定在桌面上,与桌子边沿成60度左右的角度,另外做一个装有固定铝板压茶的拖板,在拖板上贴一条边沿齐直的聚酯薄膜用来限制螺纹竞度。
利用毛毡的旋转与拖板的直线移动,在铝板表面旋擦出宽度一致的螺纹纹路。
喷砂处理是为了获得膜光装饰或细微反射面的表面,以符合光泽柔和等特殊设计需要。
均匀适度的喷砂处理,基本上也可以克服铝材表面的常见缺陷。
对外观零件,不管是用拉丝还是喷砂,通常都是需要再做表面氧化处理的。
至于是选择哪种加工工艺,应该是与造型相关要考虑的一个问题,两种工艺可获得的表面质感还是有差别的。
另外有一种工艺和喷砂接近,但是用的是一种化学腐蚀的方法进行,俗称化学烂砂处理或者化学砂面腐蚀,尤适用于铝材表面处理,其砂面的均匀性远优于喷砂处理。
化学砂面腐蚀分酸性腐蚀和碱性腐蚀。
讲义-拉丝

拉丝重点:滑动式连续多次拉伸原理及配模1、线材拉伸基本原理1、线材拉伸概念线材拉伸是指线坯通过模孔,在一定拉力作用下发生塑性变形,使其截面减小而长度增加的压力加工方法。
这种方法称为拉伸。
2、拉伸特点:1 可以得到形状尺寸精确,表面光洁以及断面形状复杂的制品。
2 能提高制品的机械强度。
3 能拉伸大长度和各种直径的线材。
4 拉伸工艺、工模具、设备简单,生产效率高。
5 拉伸耗能较大,变形体受一定限制,故往往需多次拉伸才能达到目的。
3、实现拉伸过程的条件为实现拉伸过程,拉伸应力大于变形区金属的变形抗力,同时小于模孔出口端金属的屈服极限,即:σk<σl<σs式中:σk——变形区金属的变形抗力σl——拉伸应力σs——被拉金属出口端的屈服强度由于金属拉伸后的屈服极限σs很难精确得到,实际上与金属的抗拉强度极限接近,故实现拉伸过程的条件可写为:σk<σl<σb4、拉伸原理拉伸过程中遵循“体积不变”定律。
Vo=V1 ∵ Vo=SoLo V1=S1L1∴ SoLo= S1L1则So/S1=L1/Lo =(do/d1)2 =μ式中:Vo——拉伸前线材体积V1——拉伸后线材体积So——拉伸前线材断面积S1——拉伸后线材断面积Lo——拉伸前线材长度L1——拉伸后线材长度μ——延伸系数2、多次拉伸过程多次拉伸按被拉金属在鼓轮上有无滑动而分为滑动式和非滑动式两种。
1、非滑动式连续拉伸过程Vn-1=Bn-1 Vn=Bn 则Vn/ Vn-1= Bn/ Bn-1=γn(速比)实际生产中,由于模孔尺寸本身存在上下偏差以及鼓轮的不断磨损,因此延伸系数经常变更,要求各级鼓轮速比随同延伸系数而自动调整跟踪。
2、非滑动式不连续多次拉伸如我公司一车间的十模铝拉机和八模铝拉机,则为积线式拉丝机。
拉丝过程:思考:拨线杆分别在什么情况下随鼓轮正转或反转?3、滑动式连续多次拉伸特点:①线材在拉伸中除最后一个鼓轮外,其余鼓轮上都存在滑动。
②除第一道外,其余各道均存在反拉力。
拉丝设备的配模计算

拉丝设备的配模计算要正确配模,首先要知道所购设备的机械减面率。
这在设备规范里都有注明的。
目前国内拉丝机的机械减面率如下:20D(普通双变频微拉机) 11% i=1.173 定速轮减面率4% i=1.06324VX(立式单变频微拉机) 8% i=1.086 定速轮减面率6% i=1.08622D(立式双变频细拉机) 15% i=1.176 定速轮减面率8% i=1.08624D(立式双变频细拉机) 13% i=1.149 定速轮减面率8% i=1.08624DW(卧式单变频细拉机)13% i=1.149 定速轮减面率8% i=1.08614D(中线伸线机) 15% i=1.176 定速轮减面率8% i=1.08617MD (链条中拉机) 15 % i=1.176 定速轮减面率13% i=1.14917DS (铸造箱体齿轮中拉) 20% i=1.176 定速轮减面率15.5 % i=1.183知道这些设备的减面率,配模就有理论根据了。
一般情况下,考虑到塔轮上的滑差系数,模具的配比要大于设备减面率2---6%之间。
具体选多少,主要看铜线材料好坏,铜材质量好,塔轮上滑动系数取小一点,铜材不好,为了方便把机器开起来,可以把塔轮滑动系数放的大一点。
也就是说,塔轮的滑动系数放小了,对铜材要求高,同时因塔轮上滑动小,塔轮寿命长。
相反,塔轮滑动系数放大,会比较好开,但是塔轮寿命会缩短。
所以要根据自己实际的铜杆质量配模比较理想。
配模公式:1-【(下模)×(下模)÷(上模)×(上模)】=机械减面率+2—6%例如24D的拉丝机,如果知道上模尺寸,推算下模规格,如下:进线0.8MM 24D的机械减面率是13%,按照一般的铜材质量,取塔轮滑动系数在2.5%,这样推导出下模规格是:1-【(下模×下模)÷(0.8×0.8)】=0.155。
手把手教您拉丝机配模具
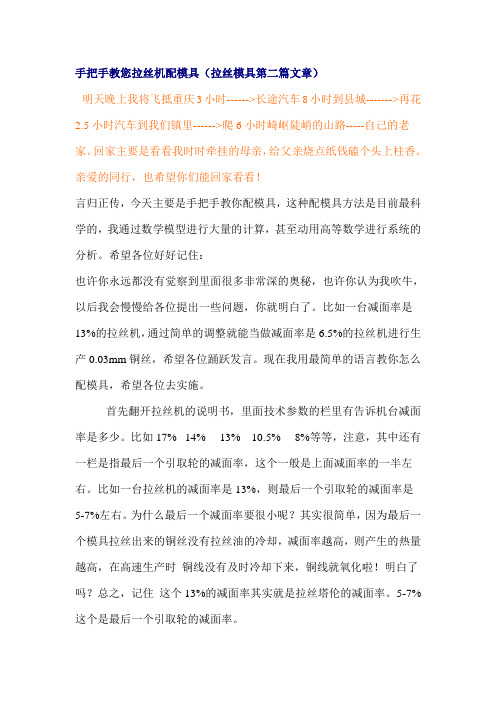
手把手教您拉丝机配模具(拉丝模具第二篇文章)明天晚上我将飞抵重庆3小时------>长途汽车8小时到县城------->再花2.5小时汽车到我们镇里------>爬6小时崎岖陡峭的山路-----自己的老家。
回家主要是看看我时时牵挂的母亲,给父亲烧点纸钱磕个头上柱香。
亲爱的同行,也希望你们能回家看看!言归正传,今天主要是手把手教你配模具,这种配模具方法是目前最科学的,我通过数学模型进行大量的计算,甚至动用高等数学进行系统的分析。
希望各位好好记住:也许你永远都没有觉察到里面很多非常深的奥秘,也许你认为我吹牛,以后我会慢慢给各位提出一些问题,你就明白了。
比如一台减面率是13%的拉丝机,通过简单的调整就能当做减面率是6.5%的拉丝机进行生产0.03mm铜丝,希望各位踊跃发言。
现在我用最简单的语言教你怎么配模具,希望各位去实施。
首先翻开拉丝机的说明书,里面技术参数的栏里有告诉机台减面率是多少。
比如17% 14% 13% 10.5% 8%等等,注意,其中还有一栏是指最后一个引取轮的减面率,这个一般是上面减面率的一半左右。
比如一台拉丝机的减面率是13%,则最后一个引取轮的减面率是5-7%左右。
为什么最后一个减面率要很小呢?其实很简单,因为最后一个模具拉丝出来的铜丝没有拉丝油的冷却,减面率越高,则产生的热量越高,在高速生产时铜线没有及时冷却下来,铜线就氧化啦!明白了吗?总之,记住这个13%的减面率其实就是拉丝塔伦的减面率。
5-7%这个是最后一个引取轮的减面率。
模具减面率的定义:以相邻两个模具为例:模具减面率=大孔径x大孔径-小孔径x小孔径大孔径x大孔径配模具的核心就是:模具的减面率大于机台相应位置的减面率第四:模具的减面率从母线开始逐渐递减,最后接近机台的减面率,目前许多公司设计的减面率却是相距机台减面率一样,其实这种设计方法是绝对错误的!!!!!!!这个我会以后建立数学模型进行论述,比较复杂,可能有些人听不懂。
常见的机械拉丝的方式有哪些
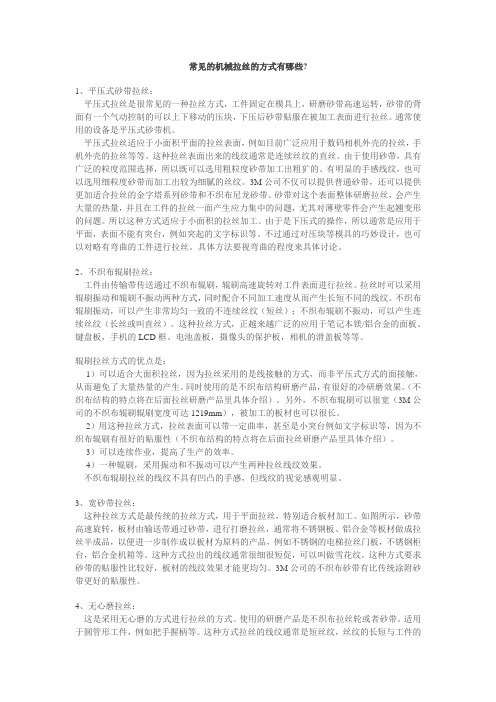
常见的机械拉丝的方式有哪些?1、平压式砂带拉丝:平压式拉丝是很常见的一种拉丝方式,工件固定在模具上,研磨砂带高速运转,砂带的背面有一个气动控制的可以上下移动的压块,下压后砂带贴服在被加工表面进行拉丝。
通常使用的设备是平压式砂带机。
平压式拉丝适应于小面积平面的拉丝表面,例如目前广泛应用于数码相机外壳的拉丝,手机外壳的拉丝等等。
这种拉丝表面出来的线纹通常是连续丝纹的直丝。
由于使用砂带,具有广泛的粒度范围选择,所以既可以选用粗粒度砂带加工出粗犷的、有明显的手感线纹,也可以选用细粒度砂带而加工出较为细腻的丝纹。
3M公司不仅可以提供普通砂带,还可以提供更加适合拉丝的金字塔系列砂带和不织布尼龙砂带。
砂带对这个表面整体研磨拉丝,会产生大量的热量,并且在工件的拉丝一面产生应力集中的问题,尤其对薄壁零件会产生起翘变形的问题。
所以这种方式适应于小面积的拉丝加工。
由于是下压式的操作,所以通常是应用于平面,表面不能有突台,例如突起的文字标识等。
不过通过对压块等模具的巧妙设计,也可以对略有弯曲的工件进行拉丝。
具体方法要视弯曲的程度来具体讨论。
2、不织布辊刷拉丝:工件由传输带传送通过不织布辊刷,辊刷高速旋转对工件表面进行拉丝。
拉丝时可以采用辊刷振动和辊刷不振动两种方式,同时配合不同加工速度从而产生长短不同的线纹。
不织布辊刷振动,可以产生非常均匀一致的不连续丝纹(短丝);不织布辊刷不振动,可以产生连续丝纹(长丝或叫直丝)。
这种拉丝方式,正越来越广泛的应用于笔记本镁/铝合金的面板、键盘板,手机的LCD框、电池盖板,摄像头的保护板,相机的滑盖板等等。
辊刷拉丝方式的优点是:1)可以适合大面积拉丝,因为拉丝采用的是线接触的方式,而非平压式方式的面接触,从而避免了大量热量的产生。
同时使用的是不织布结构研磨产品,有很好的冷研磨效果。
(不织布结构的特点将在后面拉丝研磨产品里具体介绍)。
另外,不织布辊刷可以很宽(3M公司的不织布辊刷辊刷宽度可达1219mm),被加工的板材也可以很长。
拉丝模具加工工艺
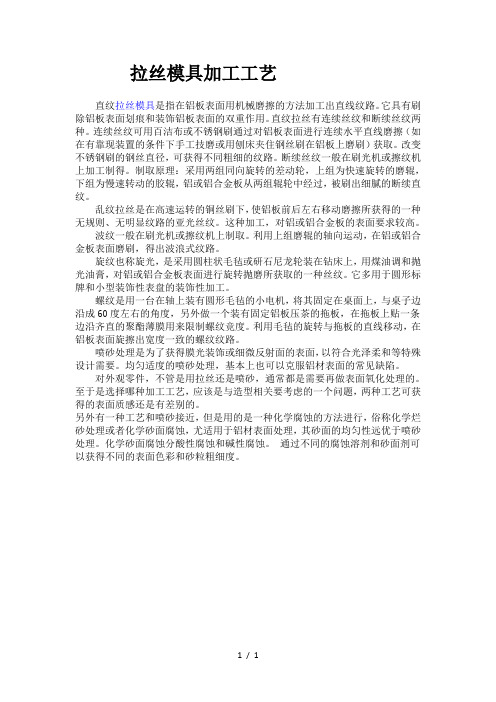
拉丝模具加工工艺直纹拉丝模具是指在铝板表面用机械磨擦的方法加工出直线纹路。
它具有刷除铝板表面划痕和装饰铝板表面的双重作用。
直纹拉丝有连续丝纹和断续丝纹两种。
连续丝纹可用百洁布或不锈钢刷通过对铝板表面进行连续水平直线磨擦(如在有靠现装置的条件下手工技磨或用刨床夹住钢丝刷在铝板上磨刷)获取。
改变不锈钢刷的钢丝直径,可获得不同粗细的纹路。
断续丝纹一般在刷光机或擦纹机上加工制得。
制取原理:采用两组同向旋转的差动轮,上组为快速旋转的磨辊,下组为慢速转动的胶辊,铝或铝合金板从两组辊轮中经过,被刷出细腻的断续直纹。
乱纹拉丝是在高速运转的铜丝刷下,使铝板前后左右移动磨擦所获得的一种无规则、无明显纹路的亚光丝纹。
这种加工,对铝或铝合金板的表面要求较高。
波纹一般在刷光机或擦纹机上制取。
利用上组磨辊的轴向运动,在铝或铝合金板表面磨刷,得出波浪式纹路。
旋纹也称旋光,是采用圆柱状毛毡或研石尼龙轮装在钻床上,用煤油调和抛光油膏,对铝或铝合金板表面进行旋转抛磨所获取的一种丝纹。
它多用于圆形标牌和小型装饰性表盘的装饰性加工。
螺纹是用一台在轴上装有圆形毛毡的小电机,将其固定在桌面上,与桌子边沿成60度左右的角度,另外做一个装有固定铝板压茶的拖板,在拖板上贴一条边沿齐直的聚酯薄膜用来限制螺纹竞度。
利用毛毡的旋转与拖板的直线移动,在铝板表面旋擦出宽度一致的螺纹纹路。
喷砂处理是为了获得膜光装饰或细微反射面的表面,以符合光泽柔和等特殊设计需要。
均匀适度的喷砂处理,基本上也可以克服铝材表面的常见缺陷。
对外观零件,不管是用拉丝还是喷砂,通常都是需要再做表面氧化处理的。
至于是选择哪种加工工艺,应该是与造型相关要考虑的一个问题,两种工艺可获得的表面质感还是有差别的。
另外有一种工艺和喷砂接近,但是用的是一种化学腐蚀的方法进行,俗称化学烂砂处理或者化学砂面腐蚀,尤适用于铝材表面处理,其砂面的均匀性远优于喷砂处理。
化学砂面腐蚀分酸性腐蚀和碱性腐蚀。
通过不同的腐蚀溶剂和砂面剂可以获得不同的表面色彩和砂粒粗细度。
- 1、下载文档前请自行甄别文档内容的完整性,平台不提供额外的编辑、内容补充、找答案等附加服务。
- 2、"仅部分预览"的文档,不可在线预览部分如存在完整性等问题,可反馈申请退款(可完整预览的文档不适用该条件!)。
- 3、如文档侵犯您的权益,请联系客服反馈,我们会尽快为您处理(人工客服工作时间:9:00-18:30)。
1.配模指南-拉丝配模四个步骤和关键数据计算方法
概要:拉丝配模是金属丝拉拔时根据坯料尺寸及金属丝尺寸确定拉拔道次、拉丝模模孔尺寸及形状的工作,也叫拉拔程序或拉拔路线的制定。
可以分为单道次拉丝配模和多道次拉丝配模。
拉丝配模主要步骤包括以下四个步骤:1.选择坯料;2.确定中间退火次数;3.确定拉拔道次和分配道次延伸系数;4.配模校核.文章就圆形断面金属拉丝和异型断面金属拉丝两种情况,具体介绍拉丝配模步骤和计算方法。
2.滑动式拉丝机配模原理及配模计算实例介绍
概要:拉丝配模指的是我们拉制过程中,对每道拉伸线模进行选择的方法。
合理的配模有两个要点,一是机械;滑动式拉丝机有其固定的拉线轮速比,通过实动式拉丝机配模计算实例,计算拉7.2mm铜杆至1.6mm铜线的相关数据;
正文开始:
写在前面:拉丝配模方法很多,很容易造成混淆,其中最根本的就是滑动系数的取值问题。
取大了有何优、缺点,取小一点又有何优、缺点,弄明白了,就会在工作中游刃有余。
死套某点,在实际中是不可能做到的。
不是简单计算,用公式一算就满足了。
如果你厂有50台机。
同是拉6种以上规格丝,如果按照某一种公式死套,想想最小要配几套模具。
所谓拉丝模具配完后,就要估计哪只模可能会引起断线。
哪个模会缩丝。
要估计断线是何原因,不要一断线就是铜杆空心,实际上,70%以上的空心铜与断线是自己拉丝造成的。
拉丝模具配模方法最常见的有以下三种:
1.应用绝对滑动系数配模方法(J法),应用基础:拉丝机连续拉线,线材在每个塔轮上,单位时间体积是相等的。
2.传统理论配模方法(C法配模),以往定义符号从进线始,这里为了计算机计算方便(用Execl电子表格),刚好相反从出口模开始.
3.新理论配模方法(X法配模),应用基础:即安全(不断线)顺利(能连续)拉线,又能把滑动降到最低.三种配模方法各有特点.C法,对设备,模具要求不严;X法和J法对设备精度要求高,对模具公差要求严,操作者的操作水平要求高.X法与系列套模相结合,效果更好.
下面对这三种配模方法做具体介绍:
一、应用绝对滑动系数配模方法(J法)
应用基础:拉丝机连续拉线,线材在每个塔轮上,单位时间体积是相等的。
即U1*S1=Un*Sn (U1:线材在定速轮上速度,S1:定速轮上线材的截面积)
那么
Τn=Vn/Un
Un=Vn/Tn,U1=V1
设:绝对速比Kn=V1/Vn
安全滑动系数Τ2=τ2;其余的Τ3=Τ2+0.001....Τn=Τn -1+0.001
A.确定拉丝机机械参数:
每种拉丝机说明书都有设备参数,机械延伸率(或不同叫法),也就是拉丝机相邻塔轮增速比,有的说明书有说明计算。
LH-280/17拉丝机的增速比是:
1.20:1,(最后一道:1.15:1)。
B.滑动系数:
1.安全滑动系数Τ2=τ2=(1.2/1.15)*1.005=1.049.
2.Τ3-Τn 取:Τ3=Τ2+0.001....Τn=Τn -1+0.001(穿模时,留相对滑动量)
C.确定进出线规格:进线:2.80;出线:1.00
D.配模计算:
1.先假定定速轮的V1=1000,利用机相邻塔轮增速比,计算出Vn
2.通过绝对速比Kn=V1/Vn ,再计算Kn
3.通过 dn=d 1×Tn *Kn ,计算出各个模具的规格。
(实际利用EXCEL 很方便)
(1.00-1.098-1.204-1.319-1.446-1.585-1.737-1.903-2.086-2.286-2.506-2.746-2.800)
二、传统理论配模方法(C 法配模)
符号定义及有关公式
以往定义符号从进线始,这里为了计算机计算方便(用Execl 电子表格),刚好相反从出口模开始。
1. 各道模子孔径:(出口模)d1,d2,d3…dn….
2. 各道延伸系数:(定速辊始)μ1,μ2,μ3…μn…
3. 各塔轮增速比:(定速辊始)ν1ν2ν3…νn…
4. 各道滑动系数:τ1τ2τ3….τn…
5. 第n 个塔轮绝对(累计)滑动系数:Τn=Vn/Un
6. 第n 个塔轮的线速度:Vn
7. 第n 个塔轮上铜线的速度:Un
8. μn=νn*τn 9. dn=dn-1*n
下面以LH-280/17拉丝机为例,说明配模计算方法:
A.确定拉丝机机械参数:
每种拉丝机说明书都有设备参数,机械延伸率(或不同叫法),也就是拉丝机相邻塔轮增速比,
有的说明书有说明计算。
LH-280/17拉丝机的增速比是:
1.20:1,(最后一道:1.15:1),即:νn=1.2
B.滑动系数τn:
中拉机一般取:1.02-1.04,取τn=1.03
C.计算线材的延伸系数:μn=νn*τn=1.2*1.03=1.236
D.确定进出线规格:进线:2.80;出线:1.00
E.配模计算
1.0-1.112-1.236-1.374-1.528-1.698-1.888-
2.099-2.334-2.595-2.800
三、新理论配模方法(X法配模)
低滑动拉线基础是:即安全(不断线)顺利(能连续)拉线,又能把滑动降到最低。
因此滑动系数最低规范要求:
1.τ3-τn要求1.0-1.01,在配模计算中平均取:1.005
2.安全滑动系数τ2
这里介绍确定安全滑动系数τ2的方法,LH-280/17拉丝机,具备满足了低滑动拉线的性能的结构,安全滑动系数是通过降低最后一道塔轮增速比来实现的。
因此,安全滑动系数τ2=(1.2/1.15)*1.005=1.049.
如:LH-200/17拉丝机安全滑动系数τ2=(1.2/1.15)*1.005=1.049;
B22拉丝机,设计的安全滑动系数τ2=(1.175/1.15)*1.005=1.027;
B32拉丝机安全滑动系数τ2=(1.15/1.12)*1.005=1.032;
S20拉丝机安全滑动系数τ2=(1.12/1.08)*1.005=1.042;
S24拉丝机安全滑动系数τ2=(1.1/1.08)*1.005=1.024。
A.确定拉丝机机械参数:
每种拉丝机说明书都有设备参数,机械延伸率(或不同叫法),也就是拉丝机相邻塔轮增速比,有的说明书有说明计算。
LH-280/17拉丝机的增速比是:
1.20:1,(最后一道:1.15:1),即:νn=1.2
B.滑动系数:
1.τ3-τn取1.005
2.安全滑动系数τ2=(1.2/1.15)*1.005=1.049。