SMT表面组装技术对照表
SMT表面组装技术印刷机调机教材
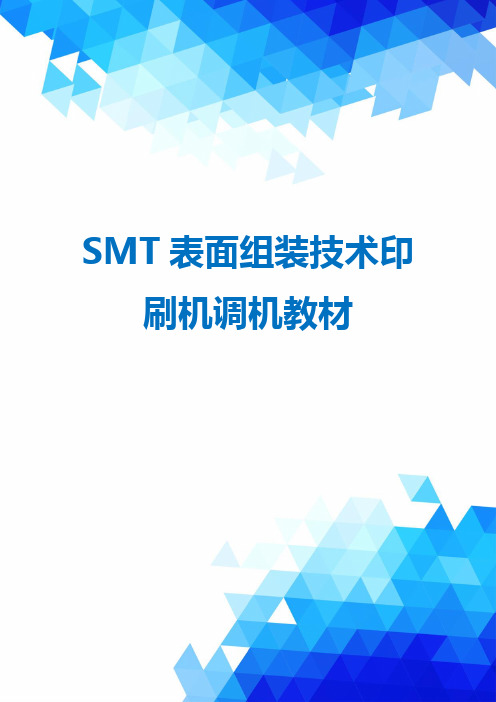
SMT表面组装技术印刷机调机教材DEK印刷机调机教材1、正确了解程序中的每一参数在生产过程中,我们在做新程序的过程中,目前的做法是在一个老的程序的基础上进行“修改”而获得我们所需要的程序,尽管如此,我们还是有必要了解在SETUP状态下EDIT菜单中各项参数的含义和使用、调整方法。
•ProductName产品名称,最多可接受不包含标点的8个字符。
•ProductID是对产品的说明性文字,没有实质性意义,最多32个字符,屏幕会显示头20个字符。
•ProductBarcode产品条形码,最长20个字符。
目前我们没有使用。
(仅265GSX可使用)•Screenbarcode对应产品的钢网的条形码,目前我们没有使用。
(265GSX)•DwellHeight刮刀停留高度(主要用于观察滚动条的情况)最小5mm 最大40mm增量1mm缺省30mm•DwellSpeed刮刀运动到Dwell高度的速度最小10mm/sec最大30mm/sec增量1mm/sec缺省24mm/sec•ScreenAdapter钢网类别,选项有NONE,255,SANYO,HERAEUS,20X20,12X12•ScreenImage钢网框架定位选择,有EDGE和CENTRE两个选项,其中EDGE只适用于SANYO和FUJI钢网框。
•CustomScreen用于对钢网位置的定义和调整,我们多数情况使用DISABLED。
•BoardWidth板宽,40--508mm,增量0.1mm•BoardLength板长,50--510mm,增量0.1mm•BoardThickness板厚,0.20--6.0mm,增量0.01mm•PrintSpeed印刷速度,2--150mm/sec,增量1mm/sec •FloodSpeed未用•PrintFrontLimit从板的前边沿到印刷起点位置的距离,0--板宽,缺省0mm•PrintRearLimit从板的后边沿到印刷起点位置的距离,0--板宽,缺省0mm•FrontPressure前刮刀压力,0--20kg,增量0.2kg •RearPressure后刮刀压力,0--20kg,增量0.2kg•FloodHeight未用•PrintGap在印刷时,PCB板和钢网之间的间隙,0-6mm,增量0.025mm•UndersideClearance定义PCB板底面和机器顶针顶端间的距离,主要是针对底面有元件的板而言。
smt表面组装技术-SMT元件介绍很不错哦,值得下载 精品
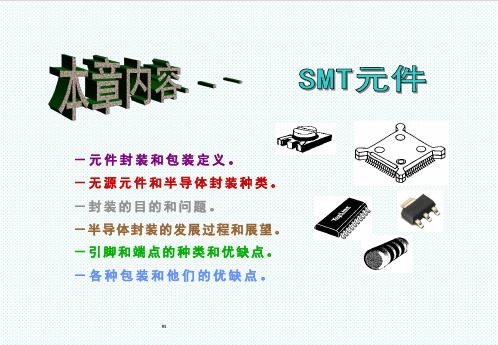
25% width 15% thickness
halved pitch more pin count
SSOP
VSOP
reduced size
20% width
QSOP 60% thickness TSSOP
reduced pitch reduced size
封装底
加入代表封装材料的字母以区别无引线芯 片载体LCC,如以PLCC代表塑膜封装等。
因封装材料的不同有:PLCC(塑膜) CLCC(陶瓷) MLCC(金属)
其中以PLCC最常用。
引脚一般采用J形设计,16至100脚。间距 采用标准1.27mm式。可使用插座。
属于成熟技术,无继续开发。
32
小外形封装 SOIC
0.04 X 0.02 0.05 X 0.04 0.06 X 0.03 0.08 X 0.05 0.10 X 0.05 0.12 X 0.06 0.12 X 0.10 0.18 X 0.12 0.22 X 0.25
1.0 X 0.5 1.2 X 1.0 1.5 X 0.8 2.0 X 1.2 2.5 X 1.2 3.2 X 1.6 3.2 X 2.5 4.5 X 3.2 5.6 X 6.4
TSOP (Thin Small Outline Package)
TSOP I 型 TSOP II 型
有I型和II型两种。厚度只有1至1.2mm。
I型由于其体薄和细间距,很受高密度组装 应用的欢迎。
II型的1.27mm间距设计是为了SOJ兼容。 引脚设计在封装的长边上有较高的可靠性。
TSOP I 型
-元件封装和包装定义。 -无源元件和半导体封装种类。 -封装的目的和问题。 -半导体封装的发展过程和展望。 -引脚和端点的种类和优缺点。 -各种包装和他们的优缺点。
SMT表面贴装技术资料

SMT知识一、 名词解释SMT:“Surface Mounted Technology” 的缩写,表面贴装技术。
SMD:“Surface Mounted Devices” 的缩写,表面组装器件。
SMC:“Surface Mounted Components”的缩写,表面组装元件。
PCB:”Printed Circuit Board”的缩写,印刷电路板。
Resistor:电阻(在PCB上用字母“R”表示,如“R1,R2,R3”等)Capacitor:电容(在PCB上用字母“C”表示,如“C1,C2,C3”等)Inductor:电感(在PCB上用字母“L”表示,如“L1,L2,L3”等)Chip bead: 磁珠(在PCB上用字母“L”表示,如“L1,L2,L3”等,我们一般也用“Inductor”来表示)IC:集成电路二、 SMT的意义1.电子产品追求小型化,以前使用的穿孔插件元件已无法缩小;2.电子产品功能更完整,所采用的集成电路(IC)已无穿孔元件,特别是大规模、高集成IC,不得不采用表面贴片元件;3.产品批量化,生产自动化,厂方要以低成本高产量出产优质产品以迎合顾客需求及加强市场竞争力;4.电子元件的发展,集成电路(IC)的开发,半导体材料的多元应用;5.电子科技革命势在必行,追逐国际潮流。
三、 现我厂SMT工艺流程印刷锡膏——手工贴片——波峰焊——目视——插件焊接——清洗——ICT测试四、 允收标准1.插件目标:焊点表层总体呈现光滑和与焊接零件有良好润湿。
部件的轮廓容易分辨。
焊接部件的焊点有顺畅连接边缘。
表层形状呈凹面状。
可接受:1)有些成份的焊锡合金、引脚或印刷板贴装和特殊焊接过程可能导致干枯粗糙、灰暗、或颗粒状外观的焊锡。
这些焊接是可接受的。
2)可接受的焊点必须是当焊锡与待焊表面,形成一个小于或等于90度的连接角时能明确表现出浸润和粘附,当焊锡的量过多导致蔓延出焊盘或阻焊层的轮廓时除外。
第一章SM表装技术介绍
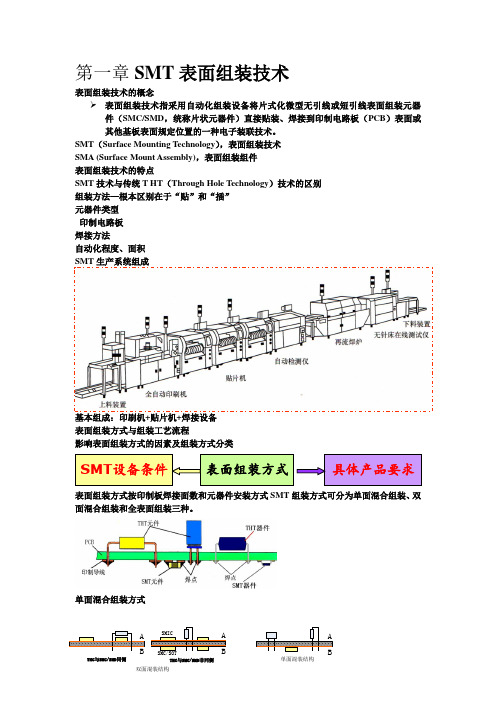
ABA B双面混装结构SMICSMC/SOTTHC 与SMC/SMD 同侧THC 与SMC/SMD 非同侧A B单面混装结构第一章SMT 表面组装技术表面组装技术的概念➢ 表面组装技术指采用自动化组装设备将片式化微型无引线或短引线表面组装元器件(SMC/SMD ,统称片状元器件)直接贴装、焊接到印制电路板(PCB )表面或其他基板表面规定位置的一种电子装联技术。
SMT (Surface Mounting Technology ),表面组装技术 SMA (Surface Mount Assembly),表面组装组件 表面组装技术的特点SMT 技术与传统T HT (Through Hole Technology )技术的区别 组装方法—根本区别在于“贴”和“插” 元器件类型 印制电路板 焊接方法自动化程度、面积 SMT 生产系统组成基本组成:印刷机+贴片机+焊接设备 表面组装方式与组装工艺流程影响表面组装方式的因素及组装方式分类表面组装方式按印制板焊接面数和元器件安装方式SMT 组装方式可分为单面混合组装、双面混合组装和全表面组装三种。
单面混合组装方式表面组装方式 SMT 设备条件 具体产品要求单面表面组装双面表面组装全表面组装结构表面组装工艺流程不同组装方式对应不同的组装工艺流程,同一组装方式也可以有不同的工艺流程:主要取决于所用元器件类型、SMA组装质量要求、组装设备、生产线实际条件等。
课后作业1、简述SMT区别于传统THT技术的特点。
2、判断电路板组装类型并给出相应的组装工艺流程。
作业答案:判断电路板组装方式并设计组装工艺流程第一步:判断组装方式:双面混合组装符合要求的组装流程有多个:举例如下组装工艺流程1:来料检测—PCB A面涂覆焊膏—贴装元器件—焊膏烘干—再流焊接—插装THC 引线折弯—翻板—B面涂覆粘结剂—贴装元器件—粘结剂固化—翻板—波峰焊接—清洗—最终检测组装工艺流程2:来料检测—PCB A面涂覆焊膏—贴装SMIC/SMC—焊膏烘干—A面再流焊接—翻板—B面涂覆粘结剂—贴装元器件—粘结剂固化—翻板—插装THC—B面波峰焊接—清洗—最终检测只翻一次板的工艺组装工艺流程3:来料检测—PCB B面涂覆粘结剂—贴装元器件—粘结剂固化—翻板—PCB A面涂覆焊膏—贴装元器件—焊膏烘干—A面再流焊接—插装THC—B面波峰焊接—清洗—最终检测工艺设计基本原则:1、依据具体电路板形式进行设计2、依据具体设备条件进行设计3、再流焊与波峰焊同时兼有时,一般先进行再流焊4、波峰焊与再流焊不能同时或无间歇连续进行5、为防止大的SMIC脱落,可增加涂覆粘结剂,但粘结剂仅起到增强元器件固定牢固度的作用第二章、表面组装元器件表面组装元器件种类表面组装元器件主要包括:【表面组装元件】【表面组装器件】【表面组装连接件】从种类来分:可分片式电阻器、片式电容、片式电感、片式机电元件。
SMT表面组装技术SMT工艺

SMT表面组装技术SMT工艺一.概述.1.S MT:表面装贴工艺.指将无引脚的片式元件(SMD)装贴于线路板上的组装技术SMT技术在电子产品制造业中,已被越来越多的工厂采用.是电子制造业的发展趋势.SMT:Surfacemountingtechnology表面装贴工艺SMD:Surfacemountingdevice表面装贴元件2.特点A.由于采用SMT机器,自动化程度高,减少了人力。
B.元件尺寸小,且无引脚,可使电子产品轻,薄,小型化。
C.装配密度高,速度快。
二.OKMCOSMT生产工艺流程,如下::使用机器将锡浆印刷在线路板上。
(DEK-265 印刷锡浆机):使用机器将规则元件贴在线路板上。
(NITTO 多元件高速贴片机):使用机器将不规则元件贴在线路板上。
(TENRYU中速贴片机)热风回流,将锡浆熔解,形成焊点.(HELLER回流炉),如短路,少锡,元件移位等。
(使用检查模板检查)三.工艺简介。
1. 锡浆印刷。
采用的机器:DEK-265锡浆印刷机(英国DEK 公司)。
1.1基本原理。
以一定的压力及速度,用金属或橡胶刮刀将装在钢网上的锡浆通过钢网漏印在线路板上。
锡浆成份为:锡63%,铅37%,松香含量:9-10%,熔点为183O C. 步骤为:图示:刮刀锡浆钢网(厚0.15MM)顶针 线路板(PCB)1.2DEK265印刷锡浆机印刷锡浆的品质直接影响点焊回流炉的品质,所以需要检查锡浆的印刷品质.一般地,主要检查以下的项目:少锡 短路 无锡浆 偏位印刷轮廓不良:拉尖,锡浆下垂。
如果钢网无损坏,印刷参数设置合适,通常印刷后,无以上不良。
主要的控制方法为过程技术员监控锡浆的厚度,如太厚,易产生QFPIC短路或锡珠。
如太薄,易产生假焊或少锡。
1.3要达到好的印刷品质,必须具备以下几点:(OKMCO选用原则)A.好的印刷钢网: 钢网厚度,钢网的开口尺寸等参数合适,孔壁垂直,无损坏。
如果钢网太厚,或开口尺寸太大,印刷在线路板上的锡浆份量就会太多,容易引起锡珠问题.同时,在元件较密集或IC脚距较小的地方,容易引起短路。
SMT表面组装技术 (3)

2.环氧玻璃纤维布覆铜板 环氧树脂或改性环氧树脂为粘合剂制作的玻璃纤维布覆铜板是当前 覆铜板中产量最大,使用最多的一类。环氧玻璃纤维布覆铜板特点: (1)可以冲孔和采用高速钻孔技术,通孔孔壁光滑,金属化效果 好; (2)低吸水性、工作温度较高,本身性能受环境影响小; (3)电气性能优良;机械性能好、尺寸稳定性,抗冲击性比酚醛 纸基覆铜板要高; (4)适合制作单面板、双面板、多层板; (5)适合制作中、高档民用电子产品。
(5)焊盘内不允许印有字符和图形标志,标志符号离焊盘边缘距离应 大于0.5mm。凡无外引脚的器件的焊盘,其焊盘之间不允许有通孔,以 保证清洗质量。
(6)两个元件之间不应使用单个大焊盘,避免锡量过多,熔融后拉力 大,将元件拉到一侧
(7)对于引脚中心距为0.65mm及其以下的细间距元件,应在焊盘图 形的对角线方向上,增设两个对称的裸铜基准标志,用于光学定位。
3.1.2 评估基板质量相关参数 (一)PCB相关参数 1.铜箔种类和厚度 2.玻璃化转变温度Tg 3.热膨胀系数CTE 4.可焊性 5.热应力 6.吸湿性 7.导线电阻 8.绝缘电阻 9.耐电压 10.孔电阻 11.互连电阻 12.电路短路和电路完善性
(二)表面贴装(SMT)对PCB的要求 1.外观要求:基板外观应光滑平整,不可有翘曲或高低不平,基板 表面不能出现裂纹,伤痕,锈斑,氧化等不良。2.热膨胀系数的关 系:表面贴装元件的组装状态会由于几基板受热后的胀缩应力对元件 产生影响。
纸基覆铜板特点:
(1)纸基疏松,只能冲孔,不能钻孔;吸水性高、相对密度小; (2)介电性能及机械性能不如环氧板; (3)耐热性、力学性能与环氧-玻纤布基覆铜板相比较低; (4)成本低、价格便宜,一般在民用产品中被广泛使用; (5)一般只适合制作单面板;在焊接过程中应注意温度调节,并注 意PCB的干燥处理,防止温度过高使PCB出现起泡现象。
SMT实用表面组装技术

SMT实用表面组装技术SMT复习内容和范围1.表面贴装技术的优点?(P4)1.组装密度高;2.可靠性高;3.高频特性好;4.降低成本;5.便于自动化生产;2.SMT有两类基本的工艺流程,分别是什么?画出其流程图,并说明其优缺点?(P6)(1)锡膏一再流焊工艺,如图1.3所示。
印刷焊膏——贴装元件——再流焊——清洗特点:简单、快捷,有利于产品体积的减小,该工艺流程在无铅工艺中更显示出优越性。
(2)贴片一波峰焊工艺,如图1.4所示。
涂敷黏结剂——表面贴装元器件——加热固化——翻转——插通孔元器件——波峰焊——清洗特点:利用双面板空间,电子产品的体积可以进一步做小,并部分使用通孔元件,价格低廉。
但设备要求增多,波峰焊过程中缺陷较多,难以实现高密度组装。
3.表面贴装技术SMT的组成包含哪三个方面的内容?(P7)(1)电子元器件,它既是SMT的基础,又是SMT发展的动力,它推动着SMT专用设备和装联工艺不断更新和深化。
(2)SMT专用设备,人们称它为SMT的硬件;(3)装联工艺,人们称它为SMT的软件;4.混装形式的两面表面贴装工艺顺序(P6)混合安装工艺流程如图1.5所示。
先做A面:印刷焊膏——贴装元件——再流焊——翻转再做B面:点贴片胶——表面贴装元器件——加热固化——翻转——插通孔元器件——波峰焊——清洗先做A面:锡膏-再流焊再做B面:点胶,贴片固化翻转补插文件后波峰焊特点:充分利用PCB双面空间,是实现安装面积最小化的方法之一,仍保留通孔元器件价廉的特点,多见于消费类电子产品的组装。
5.从引脚的形状来分,SMD主要有哪三种?(P56)1.翼形引脚(Gull-Wing)常见的器件品种有SOP和QFP。
具有翼形引脚的器件具有吸引应力的特点,因此与PCB匹配性好,这类器件引脚共面性差,特别是多引脚细间距的QFP,引脚易损坏,贴装过程中应小心对待。
2.J形引脚(J-Lead)常见的器件品种有SOJ和PLCC。
50条SMT工艺技术
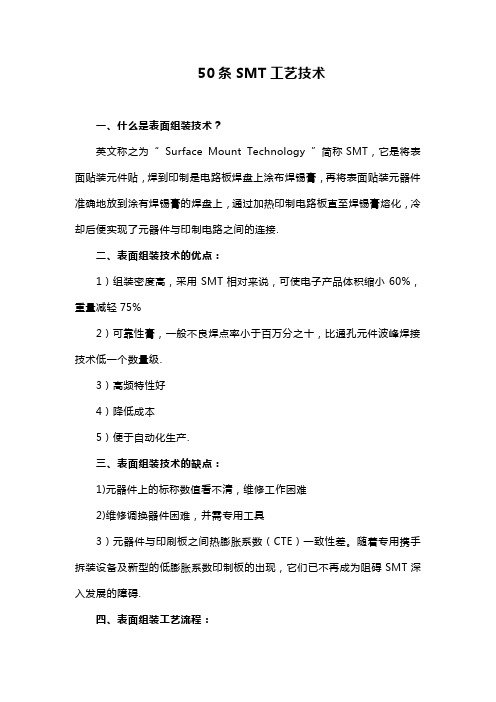
50条SMT工艺技术一、什么是表面组装技术?英文称之为“Surface Mount Technology ”简称SMT,它是将表面贴装元件贴,焊到印制是电路板焊盘上涂布焊锡膏,再将表面贴装元器件准确地放到涂有焊锡膏的焊盘上,通过加热印制电路板直至焊锡膏熔化,冷却后便实现了元器件与印制电路之间的连接.二、表面组装技术的优点:1)组装密度高,采用SMT相对来说,可使电子产品体积缩小60%,重量减轻75%2)可靠性膏,一般不良焊点率小于百万分之十,比通孔元件波峰焊接技术低一个数量级.3)高频特性好4)降低成本5)便于自动化生产.三、表面组装技术的缺点:1)元器件上的标称数值看不清,维修工作困难2)维修调换器件困难,并需专用工具3)元器件与印刷板之间热膨胀系数(CTE)一致性差。
随着专用携手拆装设备及新型的低膨胀系数印制板的出现,它们已不再成为阻碍SMT深入发展的障碍.四、表面组装工艺流程:SMT工艺有两类最基本的工艺流程,一类为锡膏回流焊工艺,另一类是贴片—波峰焊工艺.在实际生产中,应根据所用元器件和生产装备的类型以及产品的需求选择不同的工艺流程,现将基本的工艺流程图示如下:1)锡膏—回流焊工艺,该工艺流程的特点是简单,快捷,有利于产品体积的减小.2)贴片-波峰焊工艺,该工艺流程的特点是利用双面板空间,电子产品的体积可以进一步减小,且仍使用通孔元件,价格低廉,但设备要求增多,波峰焊过程中缺陷较多,难以实现高密度组装。
3)混合安装,该工艺流程特点是充分利用PCB板双面空间,是实现安装面积最小化的方法之一,并仍保留通孔元件价低的特点.4)双面均采用锡膏—回流焊工艺,该工艺流程的特点能充分利用PCB 空间,并实现安装面积最小化,工艺控制复杂,要求严格,常用于密集型或超小型电产品,移动电话是典型产品之一。
我们知道,在新型材料方面,焊膏和胶水都是触变性质流体,它们引起的缺陷占SMT总缺陷的60%,训练掌握这些材料知识才能保证SMT质量.SMT还涉及多种装联工艺,如印刷工艺,点胶工艺,贴放工艺,固化工艺,只要其中任一环节工艺参数漂移,就会导致不良品产生,SMT工艺人员必须具有丰富的工艺知识,随时监视工艺状况,预测发展动向。
第五章 表面组装技术(SMT)与表面组装元器件(SMC、SMD)

3.凸点载带自动键合(BTAB) 结构特点: 将连接用的凸点制作在载带引线上,与TAB相反. 载带结构:
与载带配合的芯片电极结构类型:
与TAB相比的特点: 操作工艺比TAB有所提高和简化 实用化遇到的两个问题:
I. 引出线端部凸点的形成工艺较为复杂;
II. 载带连接引线端部的凸点成形,与芯片 电极连接的面在平面度上有一定的差别;
三引脚,最大芯片尺寸:0.760.76mm; SOT89(EIA TO223):
三引脚,从管子的同一侧引出, 最大芯片尺寸:1.5 1.5mm; SOT143(EIA TO253): 四引脚,最大芯片尺寸:0.64 0.64 焊接方法:波峰焊和再流焊
B.小外型塑封集成电路(SOP) 外形结构(三种引线结构):
特点:实现了高密度的芯片组装,突破了细 微电极间距集成电路芯片组装的难关。
§5.3 其他片式元件举例 一.表面波滤波器
表面波滤波器的工作原理
二.表面组装电磁继电器(机电元件) 1. EB2型的工作原理
2. EB2型继电器的结构
§5.4 表面组装件的设计 §5.4.1 设计工作概述
一. 步骤:
将LSI等装在具有特殊结构的载体上,制成合格 的微电子器件;
具有两种引出结构: 引线式-特殊结构的短引线 无引线式-引出端为焊料凸点结构
多层布线电路板: 陶瓷多层布线板:
❖ 特点:热膨胀系数相近,导热性好,不老化;但 介电常数大,增加信号的延迟,耐冲击性差,工 艺比较复杂
❖ 工艺:多层共烧 厚膜多层布线板:
加盖封装.
B.有引线陶瓷芯片载体: 目的:防止热胀冷缩引起的焊点开裂 类型: ❖ 预引线陶瓷芯片载体:
采用铜合金引线和可伐引线,由厂家将 其钎焊在顶上或附在城堡上 ❖ 后引线陶瓷芯片载体:
smt表面组装技术-SMT、DIP生产流程介绍 精品

氮气回流焊
在回流焊工艺中使用惰性气体(通常是氮气)已经有一段时间了,但对于成本效益的 评估还有很多争论。在回流焊工艺中,惰性气体环境能减少氧化,而且可以降低 焊膏内助焊剂的活性,这一点对一些低残留物或免洗焊膏的有效性能来讲,或者 在回流焊工艺中需要经过多次的时候(比如双面板),可能是必需的。如果涉及到多 个加热过程,带OSP的板子也会受益,因为在氮气里底层铜线的可焊性会得到比 较好的保护。氮气工艺其它好处还包括较高表面张力,可以扩宽工艺窗口(尤其对 超细间距器件)、改善焊点形状以及降低覆层材料变色的可能性。
2 温度曲线分析与设计
温度曲线是指SMA 通过回流炉,SMA 上某一点的温度随时间变化的曲线;其本 质是SMA在某一位置的热容状态。温度 曲线提供了一种直观的方法,来分析某个 元件在整个回流焊过程中的温度变化情 况。这对于获得最佳的可焊性,避免由于 超温而对元件造成损坏以及保证焊接质 量都非常重要。
1.1表面安装的工艺流程
1.1.1表面安装组件的类型: 表面安装组件(Surface Mounting Assembly) (简称:SMA)
类型: 全表面安装(Ⅰ型) 双面混装 (Ⅱ型) 单面混装(Ⅲ型)
a.全表面安装(Ⅰ型): 全部采用表面安装元器件,安装的印制电
路板是单面或双面板.
表面安装示意图
a.单面全表面安装
单面安装流程
b.双面全表面安装 双面安装流程
c.单面混合安装 单面混合安装流程
d、双面混合安装 双面混合安装流程
1.1.3 锡膏印刷
锡膏印刷工艺环节是整个SMT流程的重 要工序,这一关的质量不过关,就会造 成后面工序的大量不良。因此,抓好印 刷质量管理是做好SMT加工、保证品质 的关键。
b.双面混装(Ⅱ型): 表面安装元器件和有引线元器件混合
SMT表面组装技术SMT工艺技术
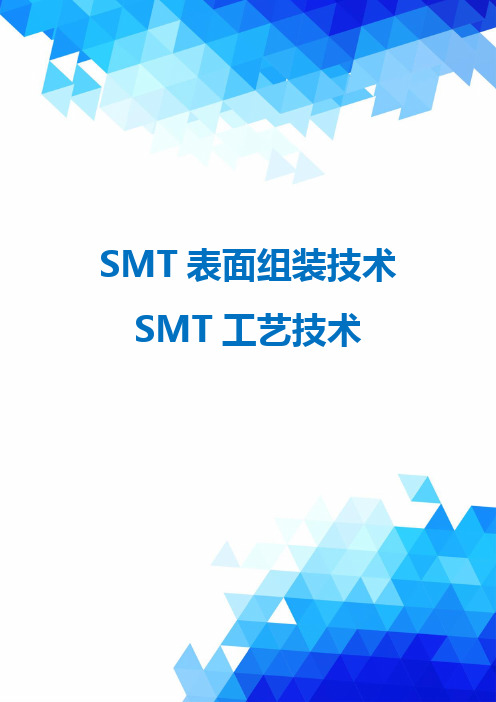
SMT表面组装技术SMT工艺技术SMT工艺技术(一)SMT——表面贴装技术(SurfaceMountTechnology)SMC——表面安装元件(SurfaceMountponet)SMD——表面安装器件(SurfaceMountDevice)SMB——表面安装印刷电路板(SurfaceMountPrintedCircuitBoard)THT——通孔插装技术MSI——中规模集成电路LSI——大规模集成电路SMT的优点:1.元器件安装密度高,电子产品体积小,重量轻。
2.可靠性高,抗振能力强。
3.高频特性好。
4.易于实现自动化,提高生产效率。
5.可以降低成本。
SMT的八大技术问题:管理工程,测试,材料,设备,工艺方法,图形设计,基板,元器件。
一.锡膏要具备的条件焊膏是由合金焊料粉、糊状焊剂和一些添加剂混合成而成的具有一定粘性和良好触变性特性的膏状体。
它是一种均相的、稳定的混合物。
在常温下焊膏可将电子元器件初粘在既定位置,当焊膏被加热到一定温度时,随着溶剂和部分添加剂的挥发、合金粉的熔化,焊膏再流使被焊元器件与焊盘互联在一起经冷却形成永久连接的焊点。
对焊膏要求能采用多种方式涂布,特别要具有良好的印刷性能和再流焊特性,并且在贮存时要具有稳定性。
1.焊膏应用前需具备以下特性:1)。
具有较长的贮存寿命,在2~5度下保存3~6个月,贮存时不会发生化学变化,也不会出现焊料粉和焊剂分离的现象,并保持其粘度和粘接性不变。
2)。
吸湿性小、低毒、无臭、无腐蚀性。
2.涂布时以及再流焊预热过程中具有的特性。
1)。
要具有良好的印刷性和滴涂性,脱膜性良好,能连续顺利的进行涂布,不会堵塞丝网或漏板的孔眼及注射用的管嘴,也不会溢出不必要锡膏。
2)。
有较长的工作寿命运,在印刷或滴涂后通常要求在常温下能放置12-24小时,其性能保持不变。
3)。
在再流焊预热过程中,焊膏应保持原来的形状和大小,不产生塌落。
塌落是指一定体积的焊膏印刷或滴涂于PCB后,由于重力和表面张力的作用及温度升高或停放时间过长而引起的高度降低,底面积超出规定边界的现象,塌落的程度称为塌落度。
SMT表面装贴技术-3[1]
![SMT表面装贴技术-3[1]](https://img.taocdn.com/s3/m/59fd1be64b35eefdc8d333ea.png)
燈
符號 R C L SOT Q
D
Led
SOP
PLCC
QFP
BGA
十七. SMT常用零件及規格
常用電阻規格(外形尺寸)
英吋 0402 0603 0805 1206 1210 2010 2512 毫米 1005 1608 2012 3216 3225 5025 6332
常用電容規格(外形尺寸)
英吋 0402 0504 0603 0805 1206 1210 1812 1825 毫米 1005 1310 1608 2012 3216 3225 4532 4564
D
T1 <1/4T D1>50%D
九.零件方向(M6)
理想
1.無極性之垂直或水平安裝的零件,編號 可由同一方向讀出.
2.有極性零件需與PCB 標注相同.
3.多腳零件的安 裝要根據其方向.
九.零件方向(M6)
可接受 非極性零件方位不一致.例如: R2
九.零件方向(M6)
不接受 1. 零件方向錯(C1),引至極性零件的極性和PCB
十一. 平直帶狀“L”及羽翼腳貼裝
拒收 1. 元件腳偏位超出腳寬50%. 2. 焊盤錫量少,不充足,錫流不明顯
D
D > 50% W
十二. “J”腳貼裝
標準狀態: 零件腳在焊接片中央
十二. “J”腳貼裝
允收: 接觸面多於零件腳闊或腳厚的50%.
十二. “J”腳貼裝
拒收 1. 零件腳偏位A>1/2W. 2. 零件腳離開焊接銅片.
可靠性測試設備
振動、跌落、高低溫通電等Check List 要點.
另:功能測試需按測試程序,正確操作機架,OK PASS,
SMT表面组装技术SMT技术组成

SMT 技术组成SMT表面组装技术SMT技术组成报告名字:指导老师:班级:时间:目录第一章SMT生产设备11.1 涂敷设备11.1.1 印刷设备11.1.2 点涂设备11.2贴片设备21.2.1贴片机的基本结构21.3焊接设备41.3.1 回流炉41.3.2 波峰焊接机41.4检测设备41.4.1 检测用治具51.5 返修设备51.5.1 手工返修设备——电烙铁51.6 清洗设备51.6.1 水清洗机51.6.2 气相清洗机51.6.3 超声清洗机6第二章SMT生产工艺62.1 涂敷工艺62.1.1 焊膏涂敷62.1.2 贴片胶涂敷62.2 贴装工艺72.2.2 保证贴装质量的三要素72.2.3 贴片机编程72.3 焊接工艺72.3.1 回流焊工艺82.3.2 波峰焊工艺8第三章SMT管理83.1 5S管理83.1.1 5S的作用83.2 SMT质量管理93.2.1 ISO900093.2.2 统计过程控制(SPC)103.2.3 6σ103.2.4 质量管理的常用工具103.3 SMT生产过程中的静电防护103.3.1静电的产生113.3.2 静电的危害113.3.3 SMT生产中的静电防护11第一章SMT生产设备1.1涂敷设备涂敷主要目的是将胶水活焊膏准确地涂敷与PCB上,使贴片工序贴装的元器件能够粘在PCB焊盘上。
主要涂敷设备有印刷设备和点涂设备。
1.1.1印刷设备用于焊膏印刷的印刷机品种很多,以自动化程度来分,可分为手动印刷机、半自动印刷机、全自动印刷机。
1.印刷机的基本结构无论哪种印刷机,其基本结构都是由机架、印刷工作台、模板固定机构、印刷头系统以及其他保证印刷精度而配备的其他选件CCD、定位系统、擦板系统、2D及3D测量系统等。
1.1.2点涂设备点涂可简单地定义为通过压力作用使液体发生移位。
点胶机是用途广泛的点涂设备,可注滴包括瞬间胶(快干胶)、红胶、黄胶、环氧树脂、硅胶、厌氧胶(螺丝胶)、防焊剂、锡浆、润滑油、焊膏等。
SMT表面组装技术参数SMT全套

SMT表面组装技术参数SMT全套1.视觉全自动印刷机(G3)主要特点:1.马达驱动刮刀升降,悬浮式印刷头;2.标准型不锈钢刮刀,刮刀角度固定为60°,长度330mm,可选:橡胶刮刀;3.双照视觉对准系统,可选择单照;4.全新网板清洗系统,喷淋式清洗纸润湿系统,干式/湿式/真空可编程网板清洗系统;5.无缝式钢导轨,导轨数控自动调宽系统;6.X、Y、θ方向自动调整工作台组件;7.印刷精度:±0.025mm,可印刷0603(0201英制)片状元件,0.4mmPITCH的QFP;8.精密滚珠丝杆定位,重复印刷精度:±0.01mm;9.标准网板夹持组件;10.多层软件结构设计,内建式软件诊断系统;11.WindowsXP系统,默认中文操作界面,可方便的切换成英文操作界面;12.标准SMEMA接口;13.三色灯塔,声光报警;14.传送方向:左至右(标准);右至左,左至左,右至右可设置15.17“液晶显示器16.三段脱模,脱模速度、距离软件可调17.G3设备通过CE认证18.双层平台面积400(X)*360(Y)mm19.工作台调节范围X=±5mmY=±5mmθ=±2°20.网框尺寸520(X)*420(Y)mm—737(X)×737(Y)mm21.PCB尺寸50(X)*50(Y)mm—400(X)*350(Y)mm22.PCB厚度0.2mm~6mm23.印刷速度0~200mm/s24.PCB夹持装置方式侧向夹紧,非拉片Z向夹紧,磁性顶针/真空吸盘;25.标准刮刀长度330mm26.刮刀压力0~20kgf27.传送高度900±20mm28.气源压力0.45~0.6MPa29.电源220VAC50~60HZ30.耗气量0.5L/Min31.额定功率3.0KW32.重量950kg33.设备尺寸L1141mm*W1410mm*H1460mm可选配:1.导轨只有侧夹,没有Z向夹紧;2.刮刀升降可选用气缸控制;3.刮刀长度可选范围140~420mm;4.2D检测模块2.G0半自动锡膏印刷机1.1主要配置及性能特点--印刷刮刀采用直线导轨及马达驱动,印刷速度可变频控制,参数设定方便,确保印刷的稳定;--翻转式刮刀头设计,清洁刮刀无需拆卸,省时方便;刮刀压力、刮刀角度可手动调节;--印刷头可根据印刷范围前后调节,网框臂可分别左右调整,适应不同尺寸钢网的需要;--组合式万用工作台,调节方便、稳定可靠,可依PCB基板大小设定安置顶针和真空吸盘,使装夹更加快速、容易;--网框升降采用气缸及导柱传动,具有较高的刚性且升降稳定可靠;--具有PCB板与丝网间隙的微调装置,保证PCB板与钢网帖合稳定;--整机采用PLC控制,可智能化管理生产过程;1.2整机规格参数指标--工作台面积:500mm×320mm--工作台调节范围:X=±5mmY=±5mmθ=±2°--框架尺寸:340mm×470mm~650mm×550mm--PCB尺寸:50mm×50mm~330mm×250mm--PCB厚度:0.4mm~6mm--印刷速度:0~100mm/s--定位方式:定位销、顶针、真空吸盘--标准刮刀长度:250mm(140mm~420mm可选)--刮刀压力:0~20kgf--工作台高度:820±20mm--气源压力:0.4~0.6MPa--电源:220VAC50~60HZ--额定功率:0.2KW--重量:300kg--设备尺寸:860mm(L)×865mm(W)×1550mm(H)3.半自动印刷机(SEM-300)主要特点:1.采用精密滚珠直线导轨,配合调速马达传动,确保印刷之稳定性和精密度,印刷精度:+/-0.05mm;2.刮刀压力和印刷速度可调,精密可调压力表;3.悬浮式刮刀系统;4.组合式工作台,可依PCB基板大小设定安置顶针和真空吸咀,对于多品种基板的转换较为方便;5.无论单双面PCB基板均可作业;6.精密电路控制,实现半自动印刷流程;7.可印刷0.5mm间距的焊盘;8.刮刀行程:Max:380mm;刮刀可调高度:0~12mm;网框可调高度:0~11mm;9.定位方式:销针定位+真空定位;(6个真空吸盘,4*4=16个支撑顶针)其它:--平台面积:400(X)*400(Y)mm--工作台调节范围:X=±5mmY=±5mmθ=±2°--网框尺寸:420(X)*370(Y)mm—650(X)*550(Y)mm--PCB尺寸:50(X)*50(Y)mm—330(X)*250(Y)mm--PCB厚度:0.4mm~3mm--印刷速度:0~76mm/s--标准刮刀长度:280mm(其它:140~420mm可选;如果选标准280mm,注意小网框420(X)*370(Y)等能否印刷);--刮刀压力:0~15kgf--气源压力:0.45~0.6MPa--电源:220VAC50~60HZ--额定功率:0.2KW--耗气量:0.3L/Min--重量:250kg--设备尺寸:L820*W850*H1465mm4.全自动PCB上料装置(LD-300)规格:-基板尺寸:MinW50*L50-MaxW250*L330mm-传送高度:900±20mm-步距选择:10,20,30,40,50mm-料架尺寸:W320*L350*H570mm-料架搭载总数:3个-电源:AC220V200W-气源:5-6bar-机身尺寸:L1250*W860*H1220mm-方向:左至右5.全自动PCB下料装置(UL-300)规格:-基板尺寸:MinW50*L50-MaxW250*L330mm -传送高度:900±20mm-步距选择:10,20,30,40,50mm-料架尺寸:W320*L350*H570mm-料架搭载总数:3个-电源:AC220V240W-气源:5-6bar-机身尺寸:L1820*W860*H1220mm-方向:左至右6.先进泛用贴片机(SM421S)包括:6个吸嘴及6套相机元件识别系统35MMFOV固定相机Y轴双马达伺服驱动系统IT智能喂料器接口单边喂料器基座可安排60支8mm带式喂料器基准点识别相机36孔位自动吸嘴更换装置15"彩色液晶显示屏3段传送系统自动转导宽度调整PCB边夹紧装置喂料器过程跟踪检测感应器WindowsXP操作系统顺序及喂料排序自动优化程序标准吸嘴一套SMEMA工具包电源:AC200/208/220/240/380/415V50/60Hz,3相, RMS3kVA(Max.4.7kVA)气源:0.5~0.7MPa(5.1~7.1kgf/㎠),260Nℓ/min重量:1,800Kg设备尺寸:1,650(L)×1,690(D)×1,535(H)7.先进泛用贴片机(SM421)包括:6个吸嘴及6套相机元件识别系统35MMFOV固定相机Y轴双马达伺服驱动系统IT智能喂料器接口双边喂料器基座可安排120支8mm带式喂料器基准点识别相机36孔位自动吸嘴更换装置15"彩色液晶显示屏3段传送系统自动转导宽度调整PCB边夹紧装置喂料器过程跟踪检测感应器WindowsXP操作系统顺序及喂料排序自动优化程序标准吸嘴一套SMEMA工具包电源:AC200/208/220/240/380/415V50/60Hz,3相, RMS3kVA(Max.4.7kVA)气源:0.5~0.7MPa(5.1~7.1kgf/㎠),260Nℓ/min重量:1,800Kg设备尺寸:1,650(L)×1,690(D)×1,535(H)8.三星高速贴片机(SM431)包括:方向:左至右1)速度52,000CPH(最佳条件)2)双臂Y轴双伺服驱动系统3)双臂共16个贴装头高速飞行图像识别系统-元件适应范围:0402mmChipto□12mm -贴装精度:±50µm@3σ4)适用新SM喂料系统-适用不停机喂料器-适用滑轨方式的喂料器-LED显示喂料器状况5)双传送系统-双传送模式:330x250(2PCB)-单传送模式:460x460(1PCB)6)可放84支8mm喂料器7)具有以供前后操作的LCD显示器8)自动换嘴装置9)WindowsXP操作系统10)安全盖11)工具包9.三星高速贴片机(SM411)包括:方向:左至右1)速度42,000CPH(IPC9850标准)2)双臂Y轴双伺服驱动系统3)双臂共12个贴装头高速飞行图像识别系统-元件适应范围:0603mmChipto□14mm -贴装精度:±50µm@3σ4)适用新SM喂料系统-适用不停机喂料器-适用滑轨方式的喂料器-LED显示喂料器状况5)双传送系统-双传送模式:510x250(2PCB)-单传送模式:510x460(1PCB)6)可放120支8mm喂料器7)具有以供前后操作的LCD显示器8)自动换嘴装置9)WindowsXP操作系统10)安全盖11)工具包10.接驳检查装置(NC-300E) -具有上下位机通信-电眼控制,PCB板检查位置可调-机身尺寸:L1000*H900mm-PCB板宽度:50-350mm-方向:左至右(可以订右到左)*带灯架、PLC程序控制为非标配置,需在合同/订单上注明11.接驳检查装置(NC-300B)-电眼控制,PCB检查位置可调-机身尺寸:L1000*W750*H900mm-PCB宽度:max.30-300mm-方向:左至右12.无铅热风回流炉(Genesis608E)规格:1)加热部分—增压式强制热风系统,直联高温马达驱动,焊接区变频调整风速—8个加温区,16个加热模块(上8个/下8个),独立温控及开关—温度控制范围:室温-320℃—温度控制精度:±1℃(静态)—基板横向温度偏差:±2℃2)冷却部分—增压式强制冷却—冷却长度1000MM—冷却区温度显示3)控制部分—PC+PLC控制系统,Windows操作界面,中英文繁简体在线自由切换,LCD显示器—分段式加热功能,—热风马达异常警报—温度曲线分析,存储,调用功能,—热冲击度可控4)传动部分—链条及W560mm网带同步传输(标准)—传送速度:0.35M-1.5M/Min,精度±2mm/min—传送高度及方向:900±20mm,左至右(标准)—PCB宽度:min50mm~max440mm—基板元件高度:上层Max30mm,下层Max20mm—手动导轨调宽—两段式导轨5)保护系统—温度超差、传送速度超差、掉板警报—内置电脑及传输UPS—链条自动润滑功能—电脑自我诊断—操作员密码管理,操作记录—延时关机功能6)助焊剂直排装置7)机器规格—机身尺寸:L5040*W1430*H1535mm—电源:AC3Ф5W380V50/60HZ—额定功率:46KW13.无铅热风回流炉(WINPLUS-8)包括:—增压式强制热风系统,直联高温马达驱动—8个加温区,16个加热模块(上8个/下8个),独立温控及开关—对流风机强制冷却—PC+PLC控制,Windows操作界面,中英文繁简体在线自由切换,LCD显示器—温度曲线分析,存储,调用功能—电动自锁式炉体开闭—不锈钢炉膛—链条及网带同步传输—内置电脑及传输UPS—链条自动润滑装置规格:—基板尺寸:L50*W50~L400*W440mm—基板零件高度:以链条加长轴为基准:+30mm,-20mm—传送速度:0.35-1.5M/Min无级调速—网带传送高度:900±20mm—温度控制范围:室温-320℃—温度控制精度:±1℃(静态)—基板横向温度偏差:±2℃—升温时间:约20分钟—系统自我诊断及警报,延时关机功能—温度超差警报—传送方向:左至右(标准)—机身尺寸:L4675*W1200*H1610mm—电源:AC3Ф5W380V50/60HZ—额定功率:50KW14.SMT接驳台(BC-300E)-具有上下位机通信-电眼控制,机器尾部检测位-机身尺寸:L800*H900mm-PCB板宽度:50-350mm-方向:左至右(可以订右到左)*带灯架、PLC程序控制为非标配置,需在合同/订单上注明。