审厂流程
审厂流程及审厂时注意事项

审厂流程及审厂时注意事项一、审厂流程1. 准备阶段审厂前,需对厂商进行评估,包括对其生产设备、质量管理体系、产品质量等进行调查和了解。
同时,需与厂商进行沟通,明确审厂的目的、要求和流程。
2. 审核计划制定根据产品类别和厂商的特点,制定审厂计划。
计划涵盖审查的内容、时间安排、审查方法和标准等。
3. 现场审查现场审查是审厂的核心环节。
审查人员应按照事先制定的审查计划,对厂商的生产设备、生产过程、质量控制措施、人员素质等进行全面检查。
同时,还应抽样检验产品,以验证其质量是否符合要求。
4. 审查结果评估审查人员根据现场审查的情况,结合相关标准和要求,对厂商的生产能力和质量管理水平进行评估。
评估结果可分为合格、不合格或待改进等。
5. 编写审查报告审查人员应将现场审查的结果整理成审查报告,详细记录审查过程、发现的问题和建议的改进措施等。
报告应准确、客观,便于厂商理解和采纳。
6. 沟通反馈审查报告应及时反馈给厂商,与其进行沟通,明确改进要求和时间安排。
同时,应就审查结果与厂商达成共识,并确保其理解和接受。
7. 监督跟进对于不合格或待改进的厂商,需进行监督跟进,确保其按照要求进行改进,并及时进行复审。
二、审厂时的注意事项1. 严格按照标准和要求进行审查,不得有偏私和歧视行为。
审查人员应保持客观公正的态度,确保审查结果真实可靠。
2. 审查人员应具备专业的知识和技能,熟悉相关标准和法规,能够准确判断产品的合格与否。
3. 在现场审查过程中,要注重细节,全面了解厂商的生产情况。
对于发现的问题,要及时记录,确保不遗漏。
4. 与厂商进行沟通时,要注意言辞的礼貌和尊重,避免引起不必要的冲突。
同时,要倾听厂商的意见和建议,尽量达成双方的共识。
5. 审查报告应准确无误,避免出现歧义或错误信息。
报告中的问题描述要具体清晰,建议的改进措施要具备可操作性。
6. 在与厂商沟通时,要注意保护商业机密和知识产权。
不得将厂商的机密信息泄露给第三方。
OEM供应商验厂审厂流程

OEM验厂流程一、目的为满足本公司对代加工厂商以及其他有意向与本公司合作的企业进行产量以及能力的可靠性评估,顺利达到合作目标,特制定此流程。
二、适用范围适用于为**********有限公司做代加工的厂商以及与本司有合作意向的其他厂商的产量及能力的可靠性评估。
三、定义无四、职责权限4.1品质部:为工厂产量及能力评估的主导部门,负责验厂全过程的跟踪、监控以及各项质量控制点、质控流程的验证并出具评估报告。
4.2技术部:负责验厂全过程的技术支持。
4.3生管物控部(采购):负责 OEM工厂的前期导入工作以及厂商基本信息的提供,必要时参与并配合品质部 OEM工厂现场审核;负责整个采购商务流程。
五、正文5.2 验厂计划的制定5.2.1生管物控部(采购)向品质部提出验厂需求,并提供相应的验厂信息。
5.2.2品质部根据厂家信息以及《OEM验厂清单》制定相应的验厂计划,并向厂家发出验厂通知,厂家确认《验厂计划》后,流程方可生效。
5.3 验厂的执行5.3.1验厂人员到厂后根据制定的验厂计划实施对该方的产量及能力评估,并进行相应的记录。
5.3.2验厂实施须进行必要的验厂前会议及验厂总结会议,并做好会议记录(参会人员需进行签到)。
5.3.3 验厂过程中填写《代工厂调查评分表》,对OEM工厂进行评估,评估范围为其品质部,技术部,生管物控部,生产部及采购部。
5.4 验厂结束5.4.1验厂结束后,根据厂商各主要部门评分表,品质部相关人员于3天内进行此次验厂报告的总结,即《验厂总结》,上报上级领导批准并反馈给公司各部门及厂商。
5.4.2 公司各部门根据验厂总结报告,决定是否与该工厂进行合作。
5.4.3 供应商不合格项目的整改措施应在3天之内完成整改并以8D形式反馈我司。
六、相关记录6.1 验厂计划6.2 验厂会议签到表6.3 验厂总结报告6.4 代工厂调查评分表6.5 8D报告附表:验厂清单验厂计划一、验厂行程:20XX/XX/XX-XX/XX工厂名称:工厂地址:启程地点:启程时间:抵达地点:抵达时间:二、验厂日期计划:编制:审核:批准:验厂会议签到表工厂名称:工厂地址:审核负责人签字:验厂总结报告审核:批准:代工厂调查评分表。
审厂核查流程图
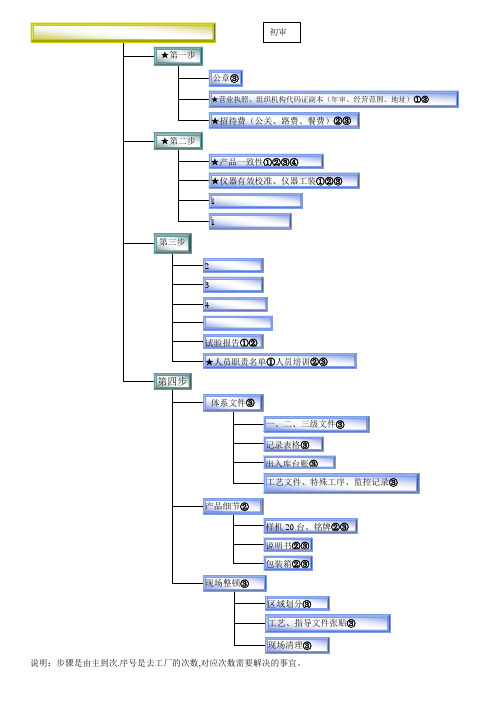
说明:步骤是由主到次.序号是去工厂的次数,对应次数需要解决的事宜。
说明:步骤是由主到次。序号是去工厂的次数,对应次数需要解决的事宜。
工厂审核流程课件
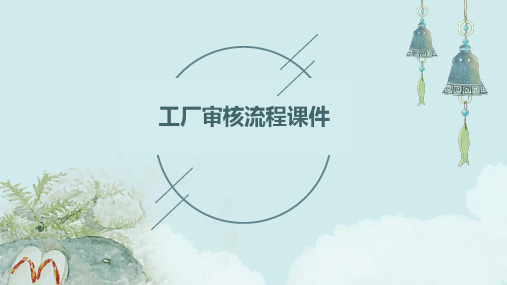
意义
帮助工厂识别存在的问题和改进 空间,促进持续改进和提升竞争
力。
工厂审核的流程和内容
现场检查阶段
对工厂的各个部门、生产线、 设备等进行实地查看,验证工 厂的实际操作是否符合要求。
沟通反馈阶段
与工厂管理层进行沟通,反馈 审核结果,提出改进建议和要 求。
准备阶段
明确审核目的、范围和标准, 制定审核计划,准备审核工具 和资料。
收集和整理相关信息和资料
收集与审核相关的信息和资料,例如工厂的规章制度、操作 规程、质量记录等。
对收集到的信息和资料进行整理和分析,以便在审核过程中 进行参考和使用。
03
现场审核阶段
首次会议
会议目的
首次会议是审核流程的开场,目的是 介绍审核目的、范围、方法和时间安 排,以及澄清任何疑问。
01
02
编写审核报告
报告内容
根据审核数据和信息的分析结果,编写详细的审核报告, 包括工厂概况、审核目的、审核过程、发现的问题、改进 建议等内容。
报告格式
按照规定的格式编写报告,确保报告清晰、准确、易于理 解。
报告审核
对报告进行审核,确保报告内容准确无误,符合审核要求 。
反馈审核结果和建议
结果反馈
将审核结果及时反馈给工厂管理层及相关部门,让他们了解审核 发现的问题和改进建议。
设备检查
检查工厂使用的设备是否 符合安全和性能要求,是 否进行了适当的维护和保 养。
操作流程评估
评估工厂的生产操作流程 是否符合相关法规和标准 ,是否存在潜在的安全风 险和环境影响。
与员工和管理层访谈
目的
通过访谈了解工厂的实际 运作情况,包括员工的工 作状况、管理层的管理方 式和效果等。
审厂的规则和流程

审厂的规则和流程
审厂是指对工厂生产过程、产品质量、环境保护等进行全面检查、评估的一种行为,旨在确保生产企业遵守相关法律法规和标准,保障消费者权益,维护公共安全和环境。
为了保证审厂的公正、客观和科学性,需要遵守一定的规则和流程。
一、审厂的规则
1.法律法规:审厂必须严格遵守国家和地方的法律法规,特别是相关质量、环保、安全、劳动等方面的规定。
2.客观公正:审厂必须客观、公正、科学,不得偏袒或歧视任何一方。
3.保密原则:审厂过程中涉及到的企业商业机密、技术秘密,应当严格保密,不得泄露。
4.安全意识:审厂人员应当具备安全意识,遵守现场安全规定,确保审厂过程安全。
二、审厂的流程
1.准备阶段:审厂前应当确定检查范围和内容,编制检查计划和方案,并组织人员和设备准备。
2.现场检查:审厂人员到达现场后,应当进行工厂内、外环境的检查,包括设备设施、生产过程、产品质量、员工安全等方面。
3.资料核查:审厂人员应当查阅企业的各类资料,包括财务报表、生产记录、工艺流程、产品检测报告、环保审批等方面的资料,以评估企业的管理水平和产品质量。
4.问题反馈:审厂人员应当及时将发现的问题反馈给企业负责人,并做出建议和整改要求。
5.报告编制:审厂结束后,应当编制审厂报告,对企业的生产过程、产品质量、环保情况等进行评估和分析,并提出建议和整改要求。
6.跟踪评估:审厂报告完成后,应当对企业整改情况进行跟踪评估,确保问题得到解决。
如有必要,应当进行再次审厂。
验厂的方法与流程
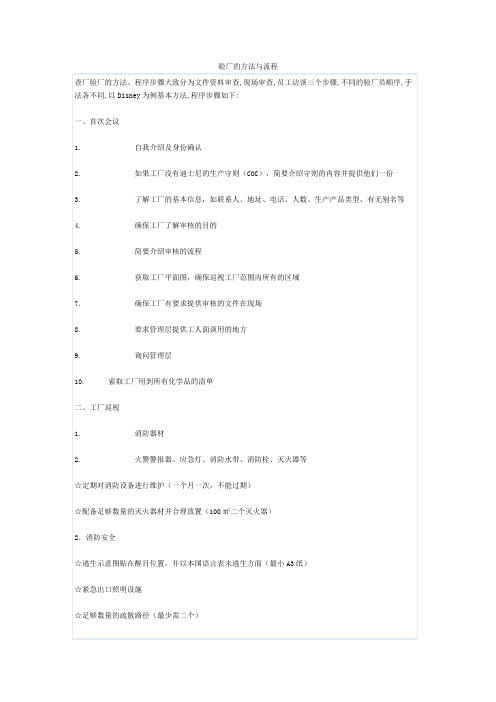
验厂的方法与流程查厂验厂的方法、程序步骤大致分为文件资料审查,现场审查,员工访谈三个步骤,不同的验厂员顺序,手法各不同,以Disney为例基本方法,程序步骤如下:一、首次会议1. 自我介绍及身份确认2. 如果工厂没有迪士尼的生产守则(COC),简要介绍守则的内容并提供他们一份3. 了解工厂的基本信息,如联系人、地址、电话、人数、生产产品类型、有无别名等4. 确保工厂了解审核的目的5. 简要介绍审核的流程6. 获取工厂平面图,确保巡视工厂范围内所有的区域7. 确保工厂有要求提供审核的文件在现场8. 要求管理层提供工人面谈用的地方9. 询问管理层10. 索取工厂用到所有化学品的清单二、工厂巡视1. 消防器材2. 火警警报器、应急灯、消防水带、消防栓、灭火器等☆定期对消防设备进行维护(一个月一次,不能过期)☆配备足够数量的灭火器材并合理放置(100㎡二个灭火器)2.消防安全☆逃生示意图贴在醒目位置,并以本国语言表未逃生方面(最小A3纸)☆紧急出口照明设施☆足够数量的疏散路径(最少需二个)☆清楚的标识出口并保持畅通(不得锁死、堵塞)☆组织疏散演习及消防安全方面的培训让员工清楚如何逃生,最近的消防警铃及灭火器的位置(半年一次,照片,记录,总结报告等)3.机器安全☆定期检查和维护☆装配防护装置(切割点、转动部位、传动部位)☆机械设备可以安全运行☆员工应接受机械安全操作的培训4.急救☆部门需配备有急救箱☆且药箱内必备药品齐全☆药品在有效期内☆车间需配急救人员(100人中需二人)5.个人防护用品(PPE)☆眼罩碎片、刨屑或危险化学品(烟雾)、焊工☆手套化学品☆耳塞每天持续8小时以上工和在85分贝的环境中工作6.环保(排污许可证)☆职业安全与健康☆空气质量☆化学品暴露限制☆危险品废物☆其他潜在危险(空气质量、废水处理、污染、回收)7.现场记录☆各类报表、签收要统一核对,且勿放罢于生产现场(切勿有星期天) ☆保持现场环境整洁☆勿张贴切加班表、处罚单☆检查各类机械保养记录8.洗手间:纸巾、洗手液配置,卫生情况工厂巡视目的:选择参与面谈的工人辨别有无可疑的童工对可疑的情况提出问题1) 工人不工作或加快工作速度2) 进出工厂的车辆检查生产流程:是否有分包三、文件审核目的:确保工厂运作的合法性;确保工厂符合当地法律及守则的要求 文件清单工卡或考勤记录(过去十二个月)工资表(过去十二个月)人事花名册及员工个人档案劳动合同社会保险收据、花名册及合格证明文件等工商营业执照消防检查报告或合格证明文件消防演习记录、紧急疏散计划及工伤记录等环保证明文件厂规或员工手册ZF有关当地最低工资规定文件设备安全许可证(如电梯使用许可证,、厨房卫生许可证等)特种工人上岗证(如电梯工、电工、厨工卫生许可证等)当地劳动局关于延长加班之批文未成年工体检及劳动局登记记录厂房平面图童工求证1) 在工厂巡视过程中挑选看起来很小的员工2) 在人事档案里抽查3) 挑选25名工人访谈4) 在面谈过程中,根据人事档案交*检查存有不一致的信息5) 当发现童工时(现时或历史性)必须登记工人的工号、姓名、出生年月、入厂日期四、工人面谈面谈的目的1) 从工人层面了解工厂的实际运作2) 获取其他过程无法得到的信息以及考察文件的一致性3) 对异常的区域进行更深入的了解面谈问卷(EIQ)面谈工人人数=工厂总人数的25%,但不超过25名工人扩大访谈人数1) 发现的违规情况需要更深入的了解,如家庭工作、虚假账本等2) 工人的身份证明文件和工人实际回答有出入时挑选程序1.50%的工人在工厂巡视过程中挑选1) 年轻工人2) 从所有部门挑选3) 如果条件允许,应该性别比例等同,种族等同4) 危险岗位工人2.50%的工人从工资表、工卡和文件审核中挑选1) 加班超时的工人2) 低工资的工人3) 青少年工人4) 老工人3.不公开1) 面谈必须在管理人员不在场的情况下进行2) 一对一面谈,不能分组面谈4.保密性1) 参与面谈的工人必须被告知所有的访谈内容均为保密2) 反映问题的工人名字不能在报告上出现5.面谈技巧1) 友善――这使得工人放松和敞开胸怀2) EIQ作为指引,但不局限面谈的问题3) 不同的国家对工人的问题不同,如洪都拉斯重点是童工、墨西哥重点是怀孕测试、中国是加班时间、土耳其是有无供祈祷的地方五、末次会议1. 告知管理层审核已经完成2. 归还借用供审核的文件3. 感谢他们对审核工资的支持和合作4. 解释所发现的问题、解答工厂的疑问以及书写改善计划确认报告(CAPAR)5. 教育并提供改善的最佳运作指引,帮助工厂达到守则的要求现场:消防安全与卫生1).消防演习①.要保留工厂消防演习记录,宿舍消防演习记录,最少每半年一次,记录应包括文字,照片,特别是总结报告(一般验厂员都要)②.要保留消防培训记录,记录包括培训时间,地点,培训内容,参加人员等2).消防设施①消防器材应有标识,如在灭火器或消防栓上喷”灭火器”等红色标识②灭火和消防栓应有消防部门或具有同等资格的部门签签发的年审合格证,通常有合格证或出厂合格证就可以,但要注意其有效期是维修日期或出厂日期开始一年当地消防门每年检查的合格证明文件.③消防栓要加封条,封条写上日期加盖工厂公章④灭火器和消防栓应定期检查,并做记录.⑤灭火器类型应选用ABC型,不要选用单纯的一种⑥手提式灭火器不能直接放在地上,应设置在挂钩,拖架或灭火器箱内,其顶部不超过1.5米,其底部离地面高度不宜小于0.15米.⑦消防栓或挂灭火器的地方,应用红色画出一个隔离区,隔离区内严禁堆放物.3).疏散通道,安全出口标志,应急灯①厂房,宿舍每层安全出口的数目不应少于2个,每个安全出口要保持畅通,应装应急灯.②每层楼梯间应安装应急灯③厂房,宿舍每层楼应有清晰的疏散路线图,图上应清楚标明安全出口,逃生方向,和看图所在位置.④生产车间,仓库应以黄色通道线把生产区域与通道分画出来,通道上还应标示逃生方向箭头.4).防爆灯仓库照明应使用防爆灯。
工厂审核流程 PPT课件
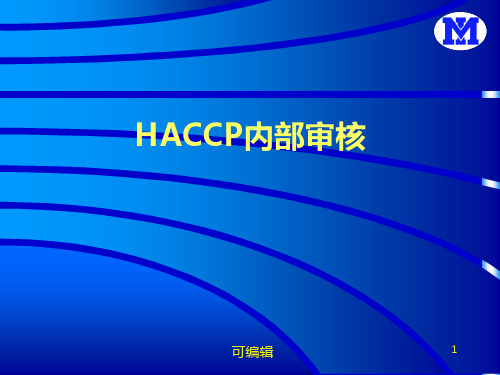
可编辑
34
不符合项报告
xxxxxx厂
日期:2002/4/21
报告编号:01
参考标准:MI H-01 <<可操作性HACCP体系规范>>
1. 不符合项描述 (包括不符合项对最终产品/服务的潜在影响) 在杀菌工序现场审核时,发现用于测量水温的温度计没有校准,并且在“常压杀菌操作 记录”中只记录了开始或结束恒温时的水温,不符合MI H-01中4.7的规定.
➢ 小结会:
在审核组对审核结果汇总分析后,应与被审核方负责人 沟通,并征求他们的意见,形成审核报告。
可编辑
23
4、末次会议(总结会)
◆审核组长主持会议,请参加会议人员签到; ◆感谢各部门对此次内审的支持和合作; ◆重申此次审核的目的、依据、范围和方法; ◆此次审核的简要说明,并肯定各部门工作的
优点和成绩; ◆陈述审核中发现的不符合项,请被审核部门
可编辑
20
2、现场审核
(1)现场审核是审核员寻找客观证据的过程,是 内审中是重要的环节,审核中应注意以下几点:
a) 审核组长要控制审核过程; b) 审核采用抽样进行; c) 选择的样本要有代表性; d) 依据核查表进行现场审核,偏离时应小心谨慎; e) 从问题的各种表述形式寻找客观证据; f) 发现影响食品安全的不符合项时,必要时可进行彻
确定不符合项,商定纠正措施和跟踪计划; ◆声明是随机抽样活动,没有发现问题的部门
并不等于没有问题; ◆宣布内审报告; ◆征求各部门的意见; ◆请到会的高层领导讲话。
可编辑
24
三、审核总结
1. 内审报告
2. 不符合项报告
3. 纠正措施及跟踪验证
4. 内审记录保存
可编辑
审厂稽核流程

审厂稽核流程下载温馨提示:该文档是我店铺精心编制而成,希望大家下载以后,能够帮助大家解决实际的问题。
文档下载后可定制随意修改,请根据实际需要进行相应的调整和使用,谢谢!并且,本店铺为大家提供各种各样类型的实用资料,如教育随笔、日记赏析、句子摘抄、古诗大全、经典美文、话题作文、工作总结、词语解析、文案摘录、其他资料等等,如想了解不同资料格式和写法,敬请关注!Download tips: This document is carefully compiled by theeditor. I hope that after you download them,they can help yousolve practical problems. The document can be customized andmodified after downloading,please adjust and use it according toactual needs, thank you!In addition, our shop provides you with various types ofpractical materials,such as educational essays, diaryappreciation,sentence excerpts,ancient poems,classic articles,topic composition,work summary,word parsing,copy excerpts,other materials and so on,want to know different data formats andwriting methods,please pay attention!《审厂稽核流程》一、准备工作阶段。
在正式开展审厂稽核之前,需做好充分准备。
客户审厂流程

负责与外协厂做好审厂前的新产品样品、展示、产品介绍等准备工作,并做好工艺装备、产品性能指标、执行的标准等资料准备和接待。
6
6.1
6.2
7.
7.1营销部接收到经审批生效的审厂通知时同各相关部门确认落实情况。
7.2生产计划部接收到经审批生效的审厂通知时,依据客户等级及时同工厂进行协调,安排驻厂工程人员和工厂相关部门提前做好接待陪同工作。
3
适用于公司接待客户审厂工作的策划、准备和实施。
4
4.1参观类型:有业务往来或有潜在合作意向的客户。
a)一般客户:提供工厂详细地址及联系人,生产计划部门安排驻厂人员接待,安排主管引导整个参观工厂过程。
b)重点客户:营销安排接送专车全程陪护,生产计划部门协调工厂安排横幅迎接,安排厂长引导整个参观工厂过程。
4.2考察方试:现场察看
5
5.1
负责审批客户审厂需求
5.2
负责与客户协调审厂的相关事项及具体日程安排,并向公司提出申请,将客户审厂相关事项通知公司相关部门。
5.3
品质部负责与外协厂做好审厂所涉及的与产品标准化和质量管理方面的接待并做好有关质量管理体系文件、资料准备和接待。
5.4
负责与外协厂做好审厂前的厂容厂貌整理工作,搞好现场5S管理,并做好设备、作业规范、过程控制等资料准备和接待。
7.3品质部接收到经审批生效的审厂通知时,及时同工厂品质部进行协调,安排驻厂品质人员做好接待陪同工作。
8.
8.1客户达到工厂后,驻厂人员引领客户到工厂接待室或会议室同客户介绍工厂陪同审厂的相关人员。根据客户提的要求进行顺序参观。由工厂人员进行引导及做详细介绍直到对方不再有任何疑问为止。
9.
9.1带领客户回到接待室或会议室并就客户对工厂感兴趣的地方进行进一步交流,并就工厂现行情况逐步同客户进行讲解,包括工厂质量管体系运行和质量管理控制及以往的成功案例。
审厂流程及审厂时注意事项

审厂流程及审厂时注意事项一、审厂流程审厂是指对供应商的生产工艺、产品质量、设备设施等进行检查和评估的过程,以确保供应商能够满足客户的要求和标准。
下面是一般的审厂流程:1.确定审厂标准和要求:在进行审厂之前,首先要明确审厂的标准和要求,包括产品质量、环境管理、安全管理、设备设施等方面的要求。
2.选择供应商并预约审厂时间:根据客户的需求和要求,选择合适的供应商,并与供应商协商确定审厂时间。
3.准备审厂资料:在审厂之前,需要准备相关的资料,包括供应商的企业资质、产品质量控制文件、员工培训记录等。
4.现场检查和评估:审厂过程中,需要进行现场检查和评估,包括对供应商的生产车间、设备设施、原材料储存、生产工艺等方面进行检查和评估。
5.记录和整理审厂结果:在审厂过程中,需要对检查和评估结果进行记录和整理,包括存在的问题、改进措施等。
6.编写审厂报告:根据审厂结果,编写审厂报告,对供应商的能力和条件进行评价。
7.反馈和跟进:将审厂报告反馈给供应商,并跟进改进措施的执行情况,确保问题得到解决。
二、审厂时注意事项在进行审厂时,需要注意以下事项,以确保审厂的顺利进行和结果的准确可靠:1.准备充分:在进行审厂之前,需要对审厂标准和要求进行充分了解,并准备好相关的资料和工具。
2.专业人员参与:审厂过程中,需要有专业人员参与,包括质量工程师、生产专家等,以确保对供应商的检查和评估能够准确有效。
3.注意细节:在进行现场检查和评估时,需要注意细节,包括生产车间的整洁度、设备的运行状态、员工的操作规范等,以发现潜在的问题。
4.与供应商合作:在进行审厂时,需要与供应商进行合作,相互沟通,解决问题,确保审厂的顺利进行。
5.客观公正:在进行审厂过程中,需要客观公正,不偏不倚,避免主观臆断和偏见的影响。
6.及时反馈和跟进:在审厂结束后,需要及时将审厂结果反馈给供应商,并跟进改进措施的执行情况,确保问题得到解决。
7.保密原则:在进行审厂时,需要遵守保密原则,确保供应商的商业机密和敏感信息不被泄露。
pcba审厂注意事项

PCBA审厂注意事项一、前言在进行P CB A(Pr int e dC ir cu it Bo ar dAs s em bl y,印刷电路板组装)中,为了保证产品质量和生产效率,进行审厂是非常重要的一环。
本文将介绍PC BA审厂的注意事项和流程,帮助您顺利完成审厂任务。
二、审厂前准备工作在进行P CB A审厂前,需要进行以下准备工作:准备资料1.:收集与P CB A相关的文档、设计文件和规范要求,包括P C B图纸、元器件清单、工艺文件等。
选择供应商2.:选择具备良好信誉和经验的PC BA供应商进行审厂,确保供应商能够满足您的需求。
明确要求3.:明确产品质量、交付时间和售后服务等要求,并将其与供应商沟通和确认。
三、P C B A审厂中的注意事项在进行P CB A审厂过程中,需要注意以下事项:1.引导供应商与供应商沟通时,需要引导供应商理解您的需求并按照要求进行操作。
确保供应商能够对PC B布局、焊接工艺、元器件选型等进行合理的技术决策。
2.技术问询在审厂过程中,可以向供应商提问,了解其在PC BA生产过程中使用的技术和工艺。
例如,焊接方式、元器件安装方式、表面处理工艺等。
通过技术问询,可以更好地了解供应商的生产能力和技术实力。
3.现场考察在审厂前后,可以进行现场考察,了解供应商的生产环境、设备状况和员工素质。
尤其需要关注生产车间的整洁程度、设备的运行状况和操作人员的操作规范性。
4.抽样检验对于PC BA产品,通过抽样检验可以有效评估生产批次的质量。
可以根据样品数量的计算公式,确定抽样数量,进行外观检查和性能测试。
确保产品达到设计要求和规范要求。
5.文件审查在审厂过程中,还需要进行文件审查,核对供应商提供的文件和资料是否与实际生产一致。
包括P CB图纸、元器件清单、工艺文件等。
如果发现差异或错误,及时与供应商沟通并进行修改。
6.售后服务在选择供应商时,需要了解其售后服务政策和承诺。
确保供应商能够及时处理产品质量问题和技术支持,并与供应商签署书面协议以确保售后服务的权益。
工厂验厂流程的五个步骤
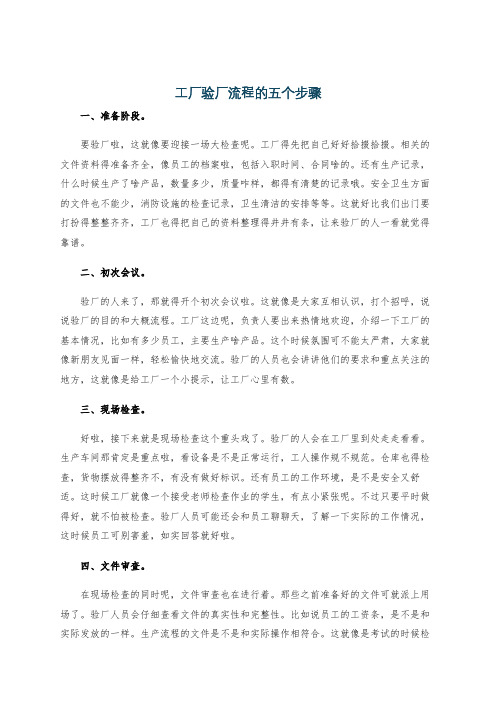
工厂验厂流程的五个步骤一、准备阶段。
要验厂啦,这就像要迎接一场大检查呢。
工厂得先把自己好好拾掇拾掇。
相关的文件资料得准备齐全,像员工的档案啦,包括入职时间、合同啥的。
还有生产记录,什么时候生产了啥产品,数量多少,质量咋样,都得有清楚的记录哦。
安全卫生方面的文件也不能少,消防设施的检查记录,卫生清洁的安排等等。
这就好比我们出门要打扮得整整齐齐,工厂也得把自己的资料整理得井井有条,让来验厂的人一看就觉得靠谱。
二、初次会议。
验厂的人来了,那就得开个初次会议啦。
这就像是大家互相认识,打个招呼,说说验厂的目的和大概流程。
工厂这边呢,负责人要出来热情地欢迎,介绍一下工厂的基本情况,比如有多少员工,主要生产啥产品。
这个时候氛围可不能太严肃,大家就像新朋友见面一样,轻松愉快地交流。
验厂的人员也会讲讲他们的要求和重点关注的地方,这就像是给工厂一个小提示,让工厂心里有数。
三、现场检查。
好啦,接下来就是现场检查这个重头戏了。
验厂的人会在工厂里到处走走看看。
生产车间那肯定是重点啦,看设备是不是正常运行,工人操作规不规范。
仓库也得检查,货物摆放得整齐不,有没有做好标识。
还有员工的工作环境,是不是安全又舒适。
这时候工厂就像一个接受老师检查作业的学生,有点小紧张呢。
不过只要平时做得好,就不怕被检查。
验厂人员可能还会和员工聊聊天,了解一下实际的工作情况,这时候员工可别害羞,如实回答就好啦。
四、文件审查。
在现场检查的同时呢,文件审查也在进行着。
那些之前准备好的文件可就派上用场了。
验厂人员会仔细查看文件的真实性和完整性。
比如说员工的工资条,是不是和实际发放的一样。
生产流程的文件是不是和实际操作相符合。
这就像是考试的时候检查答案有没有写错一样,可不能有漏洞哦。
如果发现文件有问题,工厂可得好好解释解释,要是真的是自己的失误,那就赶紧改正。
五、末次会议。
最后就是末次会议啦。
这就像是一场总结大会。
验厂人员会把在验厂过程中发现的问题和优点都讲一讲。
客户审厂流程

5
5.1
负责审批客户审厂需求
5.2
负责与客户协调审厂的相关事项及具体日程安排,并向公司提出申请,将客户审厂相关事项通知公司相关部门。
5.3
品质部负责与外协厂做好审厂所涉及的与产品标准化和质量管理方面的接待并做好有关质量管理体系文件、资料准备和接待。
5.4
负责与外协厂做好审厂前的厂容厂貌整理工作,搞好现场5S管理,并做好设备、作业规范、过程控制等资料准备和接待。
7.3品质部接收到经审批生效的审厂通知时,及时同工厂品质部进行协调,安排驻厂品质人员做好接待陪同工作。
8.
8.1客户达到工厂后,驻厂人员引领客户到工厂接待室或会议室同客户介绍工厂陪同审厂的相关人员。根据客户提的要求进行顺序参观。由工厂人员进行引导及做详细介绍直到对方不再有任何疑问为止。
9.1带领客户回到接待室或会议室并就客户对工厂感兴趣的地方进行进一步交流,并就工厂现行情况逐步同客户进行讲解,包括工厂质量管体系运行和质量管理控制及以往的成功案例。
3
适用于公司接待客户审厂工作的策划、准备和实施。
4
4.1参观类型:有业务往来或有潜在合作意向的客户。
a)一般客户:提供工厂详细地址及联系人,生产计划部门安排驻厂人员接待,安排主管引导整个参观工厂过程。
b)重点客户:营销安排接送专车全程陪护,生产计划部门协调工厂安排横幅迎接,安排厂长引导整个参观工厂过程。
客户审厂管理程序
文件修订履历
版本
修订条款及内容
修订人
日期
区分
职位
签名
日期
拟定
生产计划部
徐正新
标准化
文控中心
审核
会签
批准
工厂年审流程

工厂年审流程温馨提示:该文档是小主精心编写而成的,如果您对该文档有需求,可以对它进行下载,希望它能够帮助您解决您的实际问题。
文档下载后可以对它进行修改,根据您的实际需要进行调整即可。
另外,本小店还为大家提供各种类型的实用资料,比如工作总结、文案摘抄、教育随笔、日记赏析、经典美文、话题作文等等。
如果您想了解更多不同的资料格式和写法,敬请关注后续更新。
Tips: This document is carefully written by the small master,if you have the requirements for the document, you can download it, I hope it can help you solve your practical problems. After downloading the document, it can be modified and adjustedaccording to your actual needs.In addition, the store also provides you with a variety of types of practical information, such as work summary, copy excerpts, education essays, diary appreciation, classic articles, topic composition and so on. If you want to know more about the different data formats and writing methods, please pay attentionto the following updates.随着经济的不断发展,工厂年审流程逐渐成为了一项重要的管理措施。
吸尘器制造审厂流程

吸尘器制造审厂流程As a manufacturer of vacuum cleaners, the production process goes through several steps before the final product is ready for sale. It is crucial to follow a thorough manufacturing audit process to ensure that the products meet quality standards and specifications. This not only guarantees customer satisfaction but also helps maintain a good reputation in the market.作为吸尘器制造商,生产过程经历几个步骤,最终产品才能准备好销售。
遵循严格的制造审查流程至关重要,以确保产品符合质量标准和规格。
这不仅能确保客户满意,还有助于在市场上保持良好的声誉。
The first step in the manufacturing audit process is to assess the materials used in the production of the vacuum cleaners. It is essential to check the quality of raw materials to ensure that they meet the required standards. This includes inspecting components such as motors, filters, brushes, and dust bags. Any substandard materials should be rejected to prevent compromising the quality of the final product.制造审查流程中的第一步是评估用于生产吸尘器的材料。
工厂审核流程课件
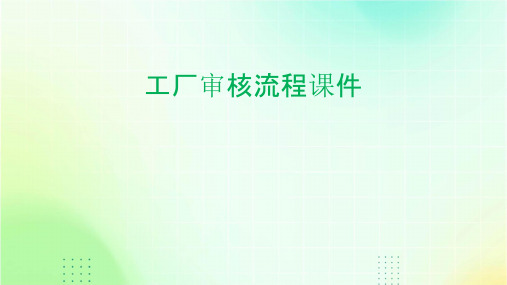
04
工厂审核方法与工具
审计表格法
审计表格法是一种常用的工厂审核工具,通过设计针对不同审核需求的表格,收集 和分析数据,以评估工厂的运营状况。
审计表格通常包括生产效率、质量、成本、交货期、员工福利等方面的指标,以及 针对环境、安全等方面的评估项目。
通过定期填写审计表格,工厂管理层可以了解工厂运营的全面情况,及时发现和解 决问题,持续改进工厂管理。
总结词
评估工厂安全生产设施和操作规程的有效性。
详细描述
通过检查工厂安全生产设施、操作规程、应急预案和演练记录等方式,评估工 厂安全生产设施和操作规程的有效性。
社会责任审核
总结词
评估工厂对社会责任的履行情况。
详细描述
通过检查工厂员工福利、劳工权益保护、企业社会责任报告等方式,评估工厂对 社会责任的履行情况。
增强客户信任度
通过审核,客户可以更全面地了解工 厂的生产和管理情况,从而增强对工 厂的信任度。
提升企业竞争力
通过审核,提高工厂生产效率和管理 水平,降低成本,增强企业竞争力。
工厂审核的范围
01
质量管理体系
审核工厂的质量管理体系是否健 全,是否符合客户工厂的健康安全管理体系是 否健全,是否符合职业健康安全
案例三:某机械制造厂审核案例分析
总结词
规范、专业、高效
详细描述
该机械制造厂在审核过程中,严格按照行业规范和标准进行。 从生产设备的维护和保养,到产品的加工精度和质量,都达 到了专业水平。同时,该厂还注重提高生产效率,通过优化 流程和技术升级来提高产能。
案例四:某玩具厂审核案例分析
总结词
安全、环保、创新
根据审核计划,对工厂的设施、设备、工艺流程、工作环境等 进行实地检查和评估。
- 1、下载文档前请自行甄别文档内容的完整性,平台不提供额外的编辑、内容补充、找答案等附加服务。
- 2、"仅部分预览"的文档,不可在线预览部分如存在完整性等问题,可反馈申请退款(可完整预览的文档不适用该条件!)。
- 3、如文档侵犯您的权益,请联系客服反馈,我们会尽快为您处理(人工客服工作时间:9:00-18:30)。
11.14 符合绿色的产品包装或本体是否有相应的标识与报告数据
11.15 是否有环境管理相关教育训练的规定,标准和计划
7商
供 应
7.4
对于来料检验不良的结果是否有要求供应商采取相应的纠正和预防措施
7
商 7.5 采购要求是否充分传达到供应商
管 7.6 供应商的审核计划是否建立,并且按照计划进行实施
理 7.7 审核表是否有固定格式
0.5
0.5
0.5
0.5
0.5
0.5
0.5
0.5
总分
4.5
4.5
平均分
100.00%
8.1 是否有程序来控制和管理变更并规定如何提出, 审批, 发放和执行变更 (例如, 0.5
10.3 是否有必要的标准颁布来预防客诉发生
10.4 每个客诉档案是否相对独立,并且集中管理所有客诉
10.5 是否有机制评估客户满意度
10.6 如客户满意度低于指标时,是否有既定程序改善以确保提高客户满意度
客 10.7 对于客户投诉,是否定立相关反应时间标准
10
户 满 意
10.8 是否具备标准程序监测能否有效解决客户投诉 10.9 是否有能力分析或验证零件等级不良之真因
0.5
0.5
9.3 为了提高检验能力和加强部品信赖性是否会改善检验条件
0.5
0.5
信 赖
9.4 9.5
在研发和量产过程中是否执行信赖性实验 每年的信赖性报告是否与品质目标(设计目标)做比较
及 9.6 信赖性实验的条件和实际的是否一致
9
可 9.7 变更过的部品/材料是否有执行信赖性分析 靠 9.8 当信赖实验不合格时是否有分析和对策
有无跟踪审查改善措施的实施情况,有无改善效果 有无跟踪改善措施的进展/实施的体系
所有的改善措施及结果是否都被文件化
总分
是否有原材料仓库的物品放置平面图 原材料仓库的5S情况是否好,是否定点摆放、整齐、规范 仓库是否避光、防尘 是否有程序规定仓库的温度、湿度
平均分
当温度或湿度超出规定界线时有无采取措施
0.5 0.5 0.5
N/A 0.5 N/A
11.11 是否有建立对供货商评估之绿色环保环境管理体系查检表
0.5
0.5
11.12 11.13
不良品是否被隔离处理,是否有记录,且否追查原因并采取防止再次发生的措施 检测出有毒物质超过标准时,是否有24小时内报告EBEN,已交货到EBEN后,是否向 EBEN报告
是否有程序规定控制产品的先进先出,是如何运作的
是否定期对仓库进行盘点,记录 原料的堆放高度是否符合规定
残余的原料是否保持密封,有无包装敞开
原料的保质期是否有规定管理
特殊材料,敏感材料是否特别保存
长期库存是否放置在指定的长期库存仓库
是否有原料收入检验的标准和准备的样本
配分 1.0 1.0 1.0 1.0 1.0 1.0 1.0 1.0 1.0 1.0 1.0 1.0 1.0 1.0 14.0 92.86% 0.5 1.0 1.0 1.0 0.5
对于零组件外包, 是否建立了不使用环境关联物质的管理体系 材料确认时,是否有成分表,不使用证明书和国家认可检测中心之测定数据及原材料 厂 是商 否之 要G求P部证品明,原材料供货商提供ICP数据和成分表等文件,且有声明未使用禁止物 质
0.5 0.5 0.5
N/A 0.5 0.5
11.6 材料规格书/图纸/承认书中是否明确标注不使用有关环境禁用物质
0.5
0.5
11.7 进料检验程序是否有明确定义有关环境禁用物质的检验程序与标准
0.5
0.5
11
ROHS & 11.8 REACH 11.9 11.10
是否有程序管制RoHS与非RoHS材料
对交货材料是否按照保管的ICP数据和成分表,确认实物和数据的一致性,有效期限 使用二次材料时,有无完善的管理体制,使用有材料证明的材料?是否有进行禁止物质 的确认
1.0
4
开 4.5 在产品量产之前有无检验产品是否达到设计水准的业务规则 发
管 4.6 设计检讨的文件及记录是否文件化
1.0
1.0
0.5
0.5
理
4.7
有无程序掌控新产品的导入及量产转移(例如,制成作业指导书,文件明细 表,设备明细表,指导作业,试生产,试生产报告检讨等)
0.5
0.5
总分
5.0
5.0
平均分
0.5 0.5 1.0 0.5 1.0
0.5 0.5 1.0 0.5 1.0
理 5.16 出货检查是否有不合格品控制程序
1.0
1.0
5.17 出货检查是否有程序来管理,并有受控
1.0
1.0
5.18 出货检查的标准和样本是否具备
1.0
1.0
5.19 出货检查水平是否多于顾客的入货检查
1.0
1.0
5.20 出货检查的结果是否收集并且定期分析汇总(周、月报)
0.5
0.5
0.5
0.5
理 8.7 物料变更标记是否附在产品上面
1.0
1.0
8.8 是否通过变更点台帐对变更点、回复等信息都进行管理并集中管理
0.5
0.5
总分
5.0
5.0
平均分
100.00%
9.1 可靠性测试有否按规定执行,即在极端温度/湿度老化以及机械可靠性测试 1.0
1.0
9.2 可靠性失效有否立即加以分析以找出故障原因
1.0
1.0
每批检查完成后是否有承认、否决的标记
0.5
0.5
2.16 不合格批次的特别选用是否符合相关的程序
0.5
0.5
佐证资料
2.17 进料检查的结果是否收集并且定期分析汇总(周、月报)
0.5
0.5
2.18 是否有程序来监控来自物料供货商的任何改动
0.5
0.5
2.19 原料、半成品、及成品的不良品仓库是否分开管理 2.20 是否有不良品处理的清单
1.0
1.0
0.5
0.5
0.5
0.5
0.5
0.5
0.5
0.5
性 9.9 当信赖实验不合格时是否考虑到研发的部分,变更点的部分 管
0.5
0.5
理 9.10 当信赖实验不合格时是否对已发出的产品进行处理来满足客户
0.5
0.5
9.11 可靠性测试可否接受
总分
平均分
10.1 是否会与客户定下协议并签字作实
10.2 客户投诉的信息是否在收到的第2天内通知到相关部门
0.5
0.5
5.10 是否对前几大不良有系统的改善计划
0.5
0.5
5
制 程 / 过 程 管
5.11 5.12 5.13 5.14 5.15
改善活动的有效性是否被追踪确认 确认可修理品是否投入到前期工序进行检查确认 确认投入的可修理品是否有标记[不合格品是否被正确地标识, 记录和隔离] 可修理品的储存情况是否良好 出货检查是否规定了抽样计划和接收标准
0.5
0.5
5.21 对执行的所有检查是否有全面的检查报告
0.5
0.5
5.22 报告中是否记录有测试和检验测量的数据
0.5
0.5
5.23 顾客的承认标准、检查标准、出货检查记录是否吻合
1.0
1.0
5.24 顾客投诉的事宜是否被记录在案
1.0
1.0
5.25 是否有顾客需要的检查表或能反映检查结果的表单
制 2.15
供应商Check List评鉴表
详细内容
有无品质手册、品质方针并且规定了品质关联管理和执行人员的责任和权限
有无规定品质目标 品质目标是否传达及宣导 有无建立部门达成品质目标的品质计划文件
有无内部品质审查规则 有无建立内部品质审查计划 内部品质审查是否检验品质目标达成,客户/工程的要求和 ISO 规定项目 有无规定内部品质审查判定基准 有无完好地保管审查结果及记录 审查中的问题点有无公布相关责任部门和责任人 审查中不足事项是否进行改善
器 6.5 确认设备及周围环境是否干净
与 6.6 确认计测器是否都有相应的证明书
6
设 备 6.7 是否有计测器台帐并且它们都在受控状态
管 6.8 每个计测器是否有自己的历史记录(卡片)
理 6.9 计测器证明书是否保存良好,商标是否存在
0.5
0.5
0.5
0.5
0.5
0.5
0.5
0.5
0.5
0.5
0.5
0.5
6.10 计测器的自检是否在做自检方法是否合理,是否有点检记录
0.5
0.5
总分
5.0
5.0
平均分
100.00%
7.1 是否有供应商选择、评价和重新评价的准则及选择步骤,并按规定实施
1.0
1.0
7.2 是否有合格供应商名录
1.0
1.0
供 7.3 供应商来料,检验规程是否文件化并执行
0.5
0.5
应
总分 平均分
1.0
1.0
0.5
0.5
0.5
0.5
0.5
0.5
0.5
0.5
1.0
1.0
1.0
1.0
8.5
8.5
100.00%
1.0
1.0
4.2 产品开发阶段有否考虑人力及设备资源状况
0.5
0.5
4.3 是否具备设计验证所需的资源 产 品 4.4 所有开发量产的产品文件、图纸是否都保存完好
0.5
0.6.5
100.00%
1.0