加氢裂化装置的腐蚀与防护
重整装置氯腐蚀及防护

重整装置氯腐蚀及防护摘要:研究催化重整装置氯离子腐蚀机理,围绕催化重整装置的流程特点、操作条件、设备选材和制造等方面对重整装置的氯离子腐蚀类型和影响因素进行分析,控制催化重整氯离子腐蚀。
关键词:重整装置氯腐蚀中国石油辽阳石化分公司芳烃厂共有两套重整装置。
50万吨/年重整装置1996年建成,采用UOP的超低压重整连续反应工艺和UOP第二代再生工艺技术。
140万吨/年连续重整-歧化联合装置由中国石化工程建设公司设计,2015年建成,连续重整部分采用UOP最新一代超低压连续重整工艺技术,催化剂再生部分采用UOP CycleMax工艺技术,并采用UOP推出的Chlorsorb工艺技术。
在两套催化重整装置运行过程中,氯腐蚀给装置运行带来一定的影响,有可能出现氯化铵盐造成的换热器管程堵塞、预加氢反应器系统压降增大等故障,影响了装置的平稳运行。
一、氯的来源及影响1氯的来源原油中的氯以无机氯和有机氯的两种形式存在,无机氯一般是指原油中的无机氯盐,主要由氯化钠、氯化镁和氯化钙组成。
石油炼制过程中的电脱盐工序可以去除大部分氯化钠,但是氯化镁和氯化钙难以去除,从而水解生成氯化氢进入下道工序。
有机氯来源很多,一是原油中天然纯在的,二是采油过程中人为添加的含氯化学助剂,三是石油炼化过程中使用的化学助剂可能含有有机氯。
电脱盐工艺基本无法脱除有机氯。
另外在原油的开采输送过程中,为了提高其开采量或为降低其凝固点方便运输,会加人少量的有机氯化物如四氯化碳,这些氯化物一般存在于80~ 130℃的馏分中,随重整原料一起进人重整装置。
固定床的半再生式催化重整装置采用的是全氯型低铂铼催化剂,在重整装置的运行过程中,为了能够很好地发挥其催化剂的活性、选择性和稳定性,要求控制好催化剂的水氯平衡环境,为此需连续不断地注水、注氯,一般使用注人二氯乙烷和乙醇的方法来控制重整催化剂的水氯平衡。
二氯乙烷的注人量一般为1. 5 mg/L ,使得重整副产氢气中有少量的氯化氢进入预加氢单元。
加氢裂化装置铵盐的腐蚀及防控

加氢裂化装置铵盐的腐蚀及防控发布时间:2021-02-01T07:18:15.216Z 来源:《防护工程》2020年30期作者:刘丽喜[导读] 某石油加工厂的加氢裂化装置加工量约180万t/a,该加氢裂化装置由原料预处理、加氢精制反应器、加氢裂化反应器、进料加热炉、新氢压缩机、循氢压缩机、循环氢脱硫系统、分馏系统、循环水系统构成。
中国石化天津分公司炼油部联合三车间天津市 300270摘要:近几年来,原油中氯化物和硫化物的存在使得原料加工生产难度越来越大,通过加氢裂化的方式转化原油中的氯化物,进而脱除。
但是在加氢裂化的过程中,受到温度、设备结构、原料杂质等影响会出现铵盐腐蚀和结垢的现象。
为避免装置腐蚀堵塞,有必要对加氢裂化时产生的结垢物和结垢腐蚀的来源进行分析研究,然后制定针对性的防腐蚀方案。
关键词:加氢裂化装置;铵盐;结晶;腐蚀和结垢;防控1加氢裂化工艺某石油加工厂的加氢裂化装置加工量约180万t/a,该加氢裂化装置由原料预处理、加氢精制反应器、加氢裂化反应器、进料加热炉、新氢压缩机、循氢压缩机、循环氢脱硫系统、分馏系统、循环水系统构成。
原料油经过升压泵后和分馏塔中回流换热,再经过反冲洗过滤器进入到反应系统。
氢气则经过新氢压缩机升压后和循环氢混合,在换热器中和热高分子换热,再和原料油混合一起进入反应系统。
经过加氢裂化反应生成液态烃、轻重石脑油、柴油等产品。
2设备腐蚀堵塞情况和结垢成分分析某石油加工厂的加氢裂化装置在运行一段时间后出现了多处裂纹,且在裂化出口流控阀前和后管道内出现大量黑色固体堵塞物,之后在拆卸装置后发现壳程堵塞严重,管程腐蚀严重。
对结垢物进行焙烧处理,并使用X射线荧光光谱分析结垢物质成分发现,样品中的硫元素与铁元素含量较多,换热器内出现了腐蚀的现象。
继续对结垢物进行低温干燥处理和X射线衍射分析后发现,结构物质中含有的主要晶体成分是氯化铵,且含有一定量铁硫化物,将结垢物溶于水,对溶解的部分用离子色谱与水质测定分析可知,换热器中结垢物中含有氯元素和氮元素。
1加氢裂化高压空冷器泄漏分析与防护措施

加氢裂化装置高压空冷器泄漏分析与防护措施技术报告加氢裂化装置高压空冷器泄漏分析与防护措施摘要中石化北京燕山分公司炼油一厂加氢裂化装置由中国石化工程建设公司(SEI)设计,采用中国石油化工集团公司石油化工科学研究院(RIPP)开发的加氢精制和加氢裂化催化剂,流程属于双剂串联、一次通过的加氢裂化工艺,于2007年6月建成投产。
该装置主要加工进口含硫原油的减压蜡油和焦化蜡油,生产符合欧Ⅳ以上排放标准的清洁油品和优质乙烯裂解料。
截至2015年7月25日A-3101/E泄漏,高压空冷器A-3101/A-H使用刚满8年。
针对高压空冷泄漏问题直接影响装置长周期稳定运行,特制定相应措施,并长期严格按要求进行落实,通过对高压空冷腐蚀的分析,及时通过调整注水和监控原料油性质等方法,确保装置长周期运行提供了保障。
关键词:高压空冷器氮含量氯含量注水前言2 Mt / a 加氢裂化装置是中国石化北京燕山分公司炼油厂10 Mt 炼油改造重点工程之一 ,采用石油化工科学研究院( R IP P) 开发的提高尾油质量的加氢裂化技术及配套催化剂 ,由中国石化工程建设公司( S EI) 设计 ,于 2007 年 6 月建成投产。
该装置主要加工高硫劣质进口原油的减压蜡油和焦化蜡油 ,生产符合欧Ⅳ以上排放标准的清洁油品和优质乙烯裂解料 ,对首都北京的环境改善和燕化公司总体经济效益的提升都有重要的现实意义。
在长期加工高硫原油的情况下,设备腐蚀问题不容忽视 ,尤其是在生产过程中曾遇到高压空气冷却器(高压空冷器) 管束泄漏问题 ,给装置正常生产运行带来了隐患。
据资料分析[3 ],因高压空冷器腐蚀泄漏而导致加氢裂化装置非计划停工的不在少数 ,可见通过对其腐蚀分析与监测 ,并采取有效的防腐措施对装置长周期运转有着重要意义。
2 装置流程与设计条件2.1 工艺流程2 Mt / a 加氢裂化装置反应流出物及其注水示意流程见图 1 。
反应产物与混氢原料油换热后进入热高压分离器 ,反应产物在热高压分离器中进行油气分离 ,热高分气体分别与冷低分油循环氢换热 ,再经高压空冷器冷却至约50 ℃进入到冷高压分离器进一步进行油气分离。
加氢裂化高压空冷器的防腐现状和对策分析

加氢裂化高压空冷器的防腐现状和对策分析加氢裂化高压空冷器是石化行业中常见的重要设备之一,其作用是冷却高温高压气体。
由于工作环境的恶劣和介质的腐蚀性,空冷器的防腐工作一直备受关注。
本文将从防腐现状和对策分析两个方面对加氢裂化高压空冷器的防腐问题进行探讨。
(一)腐蚀原因加氢裂化高压空冷器在工作中主要受到两种方式的腐蚀:化学腐蚀和电化学腐蚀。
化学腐蚀是由于介质中的酸碱物质、含氧离子、硫化物等对金属表面的腐蚀作用;电化学腐蚀则是由于电解质溶液和金属表面形成了电势差,导致金属离子被溶解的过程。
(二)腐蚀状况由于工作环境的高温高压和介质的腐蚀性,加氢裂化高压空冷器经常出现严重的腐蚀问题。
主要表现为金属表面的腐蚀、腐蚀皮膜的破损和腐蚀产物的析出,严重时还会导致设备的渗漏和破裂。
(三)防腐措施为了减少腐蚀对空冷器的影响,目前常见的防腐措施包括涂层材料的选择、阳极保护、阴极保护和材料改进等。
由于工作环境的复杂性和运行条件的限制,这些防腐措施并不能完全解决空冷器的腐蚀问题。
(一)涂层材料的选择在防腐涂层中,耐蚀性、耐热性和附着力是重要的考量因素。
目前,常用的涂层材料包括氟碳漆、环氧树脂涂层、陶瓷涂层等。
这些涂层材料具有良好的耐蚀性和耐高温性能,可以有效地延长空冷器的使用寿命。
(二)阳极保护阳极保护是利用外部电源或外部阳极材料,通过提供外部阳极电流或耐蚀性阳极材料向空冷器表面输送电子,形成保护性氧化膜,减少金属腐蚀的一种方法。
采用阳极保护技术可以有效地减少空冷器的腐蚀程度。
阴极保护是在金属表面形成一种抑制腐蚀的保护膜,以减少金属在电化学腐蚀过程中的消耗。
在加氢裂化高压空冷器中,可采用在金属表面涂覆一层阴极保护涂层,如锌涂层、镀镍层等,以减少空冷器的腐蚀速度。
(四)材料改进在制造加氢裂化高压空冷器时,可以考虑选用耐蚀性更好的材料,如铝合金、不锈钢和耐蚀合金等。
这些材料具有良好的耐蚀性和抗氧化性能,可以有效地提高空冷器的抗腐蚀能力。
加氢裂化高压空冷器腐蚀分析与防护

关 键 词 :高压 空 冷 器 结 构 冲刷 腐 蚀 防 护 加 氢 裂 化 装 置
19 9 0年 以来 , 国 的炼 油 行 业 由 于 油 品 质 我 量 和环 保 等 要求 , 陆续 建 设 了许 多 加 氢装 置 , 从
最早 引进 技术 的茂 名石 化公 司加 氢裂 化装 置 , 到
并提 出防护措 施 。
1 设 备 概 况 2 1 腐 蚀 泄 漏 .
图 1 高 压 空 冷 器 结 构 示 意
●为 十 8 5mm×o 7 1. . 5mm×6 0mm 钛 衬 管 处 0
2 设 备腐蚀 情 况
20 0 6年 4月 2 2日下 午 6点 , 操作人员发现 高
维普资讯
扬 子 石 油 化 工
Hale Waihona Puke 20 0 7年第 2 2卷 第 1期
检 发现 高压空 冷器 A一5 1 1 3 0 E入 口管 箱 与管 束 胀 接 处 出现 高压 油气 渗漏 , 置 降 压处 理 , 于 装 并 当天 1 4点 开 始 停 工 , 停 工 过 程 中, 发 现 在 又
2 中国石 化扬 子石 油化 工股 份有 限公 司炼 油厂 ) .
摘 要 : / 1Mta中压 加 氢 裂 化 装 置 高 压 空 冷 器 在 新 投 运 1 6个 月 后 连 续 2次 出 现 腐 蚀 泄 漏 事 故 , 成 装 置 非 计 划 停 工 造 2 。对 高 压 空 冷 器 的腐 蚀 原 因进 行 了分 析 , 和 进 口高 压 空 冷 器 进 行 对 比 , 为进 料 配 管 设 计 和 高 压 空 冷 器 结 构 形 式 3d 并 认 的不 合 理 , 致 进 料 分 配 不 均 匀 , 部 流 速 偏 大 , 空冷 器 管 口和 衬 管 产 生 冲 刷 腐 蚀 , H2 H2 — Hc— NH3双 相 导 局 使 在 一 s l 区加 快 了 冲 刷 腐 蚀 , 检 修 进 行 了 总 结 并 提 出 了设 备 改进 和 防护 措 施 。 对
临氢设备的腐蚀与防护以及检修期间的注意事项

临氢设备的腐蚀与防护以及检修期间的注意事项一、反应器的腐蚀与防护:1、堆焊层氢致剥离现象的特征加氢装置中,用于高温高压场合的一些设备(主要是加氢反应器),为了抵抗H2S的腐蚀,在内表面都堆焊了几毫米厚的不锈钢堆焊层(多为奥氏体不锈钢)。
主体材料2.25Cr-1Mo,堆焊层E309L、E347。
在在此类反应器上曾发现了不锈钢堆焊层剥离损伤现象。
堆焊层剥离现象有如下主要特征:1)堆焊层剥离现象也是氢致延迟开裂的一种形式。
高温高压氢环境下操作的反应器,氢会侵入扩散到器壁中。
由于制作反应器本体材料的Cr-Mo钢(如21/4Cr-lMo钢)和堆焊层用的奥氏体不锈钢(如E309和E347)的结晶结构不同,因而氢的溶解度和扩散速度都不一样,使堆焊层界面上氢浓度形成不连续状态,而且由于母材的溶解度与温度的依赖性更大,当反应器从正常运行状态下停工冷却到常温状态时,在过渡区界面上的堆焊层侧聚集大量的氢而引起脆化。
另外,由于母材和堆焊层材料的线膨胀系数差别较大,在反应器制造时会形成相当可观的残余应力。
上述这些原因就有可能使堆焊层界面发生剥离,而且经过超声检测和声发射试验的监测,发现剥离并不是从操作状态冷却到常温时就马上发生,而是要经过一段时间以后(需要一定的孕育期)才可观察到这种现象。
尽量避免非计划紧急停车;在正常停工时要采取使氢尽可能释放出去的停工条件,以减少残留氢量。
2.氢脆现象所谓氢脆,就是由于氢残留在钢中所引起的脆化现象。
产生了氢脆的钢材,其延伸率和断面收缩率显著下降。
这是由于侵人钢中的原子氢,使结晶的原子结合力变弱,或者作为分子状在晶界或夹杂物周边上析出的结果。
但是,在一定条件下,若能使氢较彻底地释放出来,钢材的力学性能仍可得到恢复。
氢脆是可逆的,也称作一次脆化现象。
对于操作在高温高压氢环境下的设备,在操作状态下,器壁中会吸收一定量的氢。
在停工的过程中,若冷却速度太快,使吸藏的氢来不及扩散出来,造成过饱和氢残留在器壁内,就可能在温度低于150℃时引起亚临界裂纹扩展,对设备的安全使用带来威胁。
加氢裂化装置的腐蚀与防护

加氢裂化装置的腐蚀与防护加氢裂化是炼油厂重要的二次加工手段,可以获得高质量的轻质燃料油。
其特点是对原料适应性强,可加工直镭重柴油、催化裂化循环油、焦化镭出油,甚至可以用脱沥青重残油生产汽油、航煤、和低凝点柴油。
其次,生产方案灵活,可根据不同的季节改变生产方案,并且产品质量好,产品收率高。
加氢裂化操作条件:温度380-450°C,操作压力8-20Mpa,采用的催化剂含有Pt、Pd、W、Mo、Ni、Co等金属氧化物作为加氢组分,以硅酸铝、氟化氧化铝或结晶硅铝酸盐为载体。
原料油经加氢、裂化、异构化等反应转化为轻油产品,收率一般可达100%(体积),可以获得优质重整原料、高辛烷值汽油、航煤、和低凝点柴油,同时产品含硫、氮、烯坯低,安定性好。
加工含酸、高酸原油主要对原料油进料系统有严重影响,加氢反应器也应选择防护措施。
6.1腐蚀形态6.1.1氢损伤高温高压条件下扩散在钢中的氢与钢中不稳定的碳反应生成甲烷,可引起钢的内部脱碳,甲烷不能从钢中逸出,聚集在晶界及其附近的空隙、夹杂物等不连续处,压力不断升高,形成微小裂纹和鼓泡,钢材的延展性、韧性等显著降低,随之变成较大的裂纹,致使钢最终破坏。
因为路铝钢具有良好的高温力学性能和抗氢损伤性能,近年来加氢反应器大多选用2.25CrlMo 钢制造。
6.1.2堆焊层氢致开裂在高温高压的氢气氛中,氢气扩散侵入钢材,当反应器停工冷却过程中,温度降至150°C以下时,由于氢气来不及向外释放,钢中吸藏了一定量的氢,这样在一定条件下就有可能发生开裂。
裂纹的产生和钢中的氢气含量有很大关系,曾经有实验证明,停工7个月后的加氢反应器,堆焊层仍有29ppm的氢含量,在堆焊层上取样进行弯曲实验,弯曲角度在19-750范围内试样就发生了开裂,取试样进行脱氢处理后,试样中氢含量降到1.2ppm,试样弯曲到1800也没有发生开裂。
实验证明了氢脆的危害性,同时也证明了氢脆是可逆的。
加氢装置腐蚀类型及选材要点

加氢装置腐蚀类型及选材要点加氢裂化装置存在的主要腐蚀类型主要有:氢损伤(包括高温氢腐蚀、氢脆、氢致剥离)、高温H2+H2S腐蚀、连多硫酸腐蚀、Cr-Mo钢的回火脆性、高温S腐蚀、低温部位的H2S+H2O腐蚀、H2S+NH3 +H2O腐蚀。
1.氢损伤【定义】由于氢原子扩散进入金属本体或与金属反应引起金属材料性能的破坏称为氢损伤。
【部位】氢损伤发生的主要部位在:高温、高压氢气环境下的反应系统设备和管线。
【分类】氢损伤主要可以分为:氢脆、高温氢腐蚀和氢致剥离。
(1)氢脆【定义】钢在临氢条件下使用,氢以原子状态扩散浸入晶格内、又以分子状态聚集于晶界或非金属夹渣物周围。
【特征】物理过程,可逆的,称为一次脆化现象。
材料的抗拉强度或硬度没有特别大的变化,但是在常温条件下材料的缺口强度或韧性降低,有时还产生裂纹。
受到氢脆的材料经过脱氢处理后,如果没有产生裂纹,其延性和韧性都能得到恢复。
(2)高温氢腐蚀【定义】氢在高温(T>220℃)高压下与合金中的夹杂物(碳合物F3C或固溶碳C)或合金添加物(如Si)发生化学反应,生成高压气体。
从而导致钢材产生脱碳和结晶界裂纹。
受到高温氢腐蚀的材料的抗拉强度和延性、韧性显著降低。
【特征】高温氢腐蚀与氢脆性质完全不同,它是化学反应过程,具有不可逆性,称为永久脆化现象。
高温氢腐蚀主要有2种形式:一是表面脱碳;一是内部脱碳。
钢材与氢接触后可产生表面脱碳。
表面脱碳不会产生裂纹,但材料的强度和硬度稍有下降,而延伸率增加。
发生的主要反应有:Fe3C+2H2→CH4+3Fe。
这一反应一般从钢的表面开始,逐渐向内部推进,生成的甲烷气体不易逸出,他们聚集在晶界或杂质周围,形成的局部压力可高达几千大气压以上,因此,不仅钢的表面和里层脱碳脆化,而且还发展为严重的鼓泡开裂。
钢中的固溶的碳也会与钢中溶解的氢反应:C+4H→CH4;Si+4H→SiH4。
高温氢腐蚀的特点是要经过一个潜伏期,根据材料和环境条件的不同,潜伏期短可几个小时,长则数年。
加氢裂化分馏系统的腐蚀防护思路

加氢裂化分馏系统的腐蚀防护思路张 培1,袁耀如2(1.石油化工管理干部学院,北京100101;2.金陵石化公司一联合车间,江苏南京210033)摘要:结合金陵石化公司炼油厂加氢裂化装置技术改造过程,分析了含硫原油加工对加氢裂化装置系统腐蚀情况,并提出相应的腐蚀防护措施。
本套装置自投产以来,经历了2次炼制高含硫原油的扩能技术改造,加工原油处理量由800kt/a 增加到112M t/a ;原油硫质量分数由013%~015%逐渐上升到平均硫质量分数115%左右,最高达215%,使本套装置加工原油的能力大大提高,同时对处理劣质原油特别是高含硫原油的设备腐蚀问题找到了一些解决办法。
提出相应的应对方法和腐蚀防护思路。
关键词:加氢裂化;含硫原油;腐蚀与防护中图分类号:TE98 文献标识码:A 文章编号:0253-4320(2008)S1-0063-04Thought on corrosion protection for distillation unit in hydrocracking plantZH ANG Pei 1,YUAN Yao 2ru2(1.S inopec Management Institute ,Beijing 100012,China ;2.C ombined Plant #1of Jingling Petrochemical C omplex ,Nanjing 210033,China )Abstract :In this article ,in combination with the hydrocracking unit retrofit in the refinery of Jinling Petrochemical C ompany ,the corrosions problems in the hydrocracking unit for processing the crudes with high sulfer content is studied and its s olutions are brought forward.The unit were retrofitted twice since operation in order to enlarge the throughput and process the crude with higher content sulfer (the crude processing throughput from 800kt/a to 112Mt/a ,the sulfer content increasing from 013%-015%to 115%as an average even max.to 215%),which enhanced the capacity of the unit for crude oil treatment greatly ,as well as providing s ome measures to overcome the equipment corrosion by low quality oil ,especially crude oil with high content of sulfur.K ey w ords :hydrocracking ;crude with sulfer ;corrsion and Protction 收稿日期:2008-03-25 作者简介:张培(1956-),女,副教授,主要从事石化技术培训工作,zhangpeiwang @ 。
催化重整装置氯腐蚀及防护

2 反应系统中水含量的平衡控制根据上图中的水氯平衡反应式,如果重整反应部分的水含量增多,那么引起重整催化剂上的氯流失。
为了控制氯的流失,就需要严格控制水含量,达到水氯平衡状态,尽可能的减少氯的产生,防止氯腐蚀。
因此,我们必须降低循环氢中的水含量。
第一种是降低重整进料的水,第二种是优化催化剂再生系统的运行。
2.1 重整进料水的优化本装置通过优化预加氢分馏部分运行,降低预加氢精制油的水含量。
直馏石脑油经加氢处理和分馏汽提,预加氢精制石脑油水含量较低。
加氢裂化重石脑油自罐区的水含量未经过汽提,此股物料水含量一直偏高。
重整进料的水含量高,催化剂的比表面积严重下降,催化剂的持氯能力下降;为了保持催化剂的氯含量,导致注入系统更多的氯,导致进入下游物料的氯含量高。
重整进料的水含量偏高是困扰装置运行的难题。
2.2 优化催化剂再生系统的运行装置对仪表风的水含量进行严格的监控,其水含量处于正常范围。
再生烧焦使用的仪表风,通过干燥器降低仪表风的水含量。
除此之外在干燥器的出口安装水分析仪,监控干燥器出口的水含量。
再生器氧化区,焦碳与O 2燃烧,生成二氧化碳和水并放热,因此再生烧焦烟气的水含量高。
焦炭+O 2→H 2O + CO 2 +热量催化剂再生部分采用UOP 公司Chlorsorb 工艺技术回收再生放空气体中的氯。
氯吸附系统通过低温催化剂比高温催化剂持有更多的氯这样的特点获得经济效益。
所以在燃烧区的高温催化剂上损失的氯可以在氯吸附系统中的吸附区重新吸附到催化剂上。
再生烧焦烟气经过氯吸附系统、放空气脱氯罐后放大气或进入加热炉。
高水的再生烧焦烟气导致重整催化剂的比表面积下降。
目前部分催化重整装置将Chlorsorb 氯吸附系统切除,催化剂比表面积下降速率减缓。
0 引言辽阳石化油化厂催化重整装置原料为常减压装置来的直馏石脑油经加氢处理和拔头,与加氢裂化重石脑油混合,作为重整进料。
催化剂再生部分采用美国UOP 公司最新的CycleMax Ⅲ工艺技术,并采用Chlorsorb 工艺技术回收再生放空气体中的氯,在Chlorsorb 氯吸附后增加气相脱氯设施。
加氢装置常见腐蚀

加氢装置常见的腐蚀1. 氢腐蚀氢腐蚀是在高温高压条件下,分子氢发生部分分解而变成原子氢或离子氢,并通过金属晶格和晶界向钢中扩散,扩散侵入钢中的氢与不稳定的碳化物发生化学反应,生成甲烷气泡(它包含甲烷的成核过程和成长),即Fe3C+2H2→CH4+Fe,并在晶间空穴和非金属夹杂部位聚集,而甲烷在钢中的扩散能力很小,聚积在晶界原有的微观孔隙(或亚微观孔隙)内,形成局部高压,造成应力集中,使晶界变宽,并发展成为裂纹,开始时是很微小的,但到后期,无数裂纹相连,引起钢的强度、延性和韧性下降与同时发生晶间断裂。
由于这种脆化现象是发生化学反应的结果,所以他具有不可逆的性质,也称永久脆化现象。
在高温高压氢气中操作的设备所发生的氢腐蚀有两种形式:一是表面脱碳,二是内部脱碳。
表面脱碳不产生裂纹,这点与钢材暴露在空气、氧气或二氧化碳等一些气体所产生的脱碳相似,表面脱碳的影响一般很清,其钢材的强度和硬度局部有所下降而延性有所提高。
内部脱碳是由于氢扩散侵入到钢中发生反应生成甲烷,而甲烷又不能扩散到钢外,就聚集于晶界或夹杂物附近。
形成了很高的局部应力,使钢产生龟裂、裂纹或鼓包,其力学性能发生了显化。
造成氢腐蚀的因素:1 操作温度、氢的分压和接触时间。
温度越高或者压力越大发生高温氢腐蚀的起始时间越早。
氢分压8.0MPa是个分界线,低于此值影响比较缓和,高于此值影响比较明显,操作温度200℃是个临界点,高于此温度钢材氢腐蚀程度随介质的温度升高而逐渐加重。
氢在钢中的话浓度可以用下面公式表示:C=134.9P1/2exp(-3280/T)式中:C-氢浓度P——氢分压,MPaT-温度,K从式中可看出,温度对钢中氢浓度的影响比系统氢分压更显著。
2 钢材中合金元素的添加情况。
在钢中不能形成稳定碳化物的元素(如镍、铜)对改善钢的抗氢腐蚀的性能毫无作用;而在钢中添加形成很稳定碳化物的元素(入铬、钼、钒、钛、钨等),就可以使碳的活性降低,从而提高钢材抗氢腐蚀的能力。
渣油加氢装置湿硫化氢腐蚀及防护

一
属设备造成腐蚀 。原料油 中基本上不含水 , 即使 夹带 有少 量 的水 , 由于 油膜 的屏 蔽 作 用 而 构不 成
明显 的湿 硫化 氢腐 蚀环境 。 虽然 原料 油 系统 中硫 含 量 较 高 , 由于处 于低 温环 境 条 件 ( 0 ≤20℃ ) 但 该 系 统基 本 上 不考 虑 , 湿硫 化氢 的腐蚀 。当介质 温度 换热 到 20c 以上 6 = I
样, 也存 在 突 出 的硫 化氢 腐 蚀 环 境 。硫 化 氢 的
来 源 有两 个 : 原料 油 中带 来 的含 硫 化物 加 氢 转 化
生成 ; 为保 持 催化 剂 活 性 而 添 加 的硫 化 剂在 加 氢
条 件 下与 氢气 生成 的 。 由于装置 处 于高温 、 压 、 高
临氢工况 , 如果加氢装置 中硫化氢含量维持在一 个 较 高 的水平 , 旦发 生承 压金 属部 件失 效 , 果 一 后
腐 蚀环 境 。
温 度大 于 20c 5 C的部 分 , 于 高 温硫 腐 蚀环 属
境 , H. .M C n m 选材 即可 。 按 F c oo y
温 度小 于 20℃ 的部 分 , 有硫 化氢 的存在 , 5 虽 且有水 结露 的温 度 条 件 , 因为 含 水量 几 乎 可 以 但
部位都 未 经抗 湿硫 化 氢 腐 蚀设 防 , 也没 有 出现 过 与湿硫 化 氢有关 的金 属构 件失 效 的事情发 生 。
2 2 反应流 出物 系统 .
对于 温 度 大 于 20℃ 的部 分 , 于 典 型 的 0 属 “ 温 H +H s 腐蚀 环境 , A I4 的 N L O 高 2 2” 按 P9 1 ESN 曲线 和 C P E 曲线选 材 即可 。 OPR
加氢裂化装置高压空冷器的腐蚀及防护

( 阳大 洋 化 学 有 限 公 司 , 阳 1 0 1 ) 沈 沈 10 6
摘 要 考 察 了 加 氢 裂 化 装 置 高 压 空 冷 器 加 工 高 硫 原 油 后 出 现 的 腐 蚀 问 题 , 进 行 了加 注 并 S Y 1 1 氢 裂 化 阻 垢 缓 蚀 剂 的工 业 试 验 。结 果 表 明 ,YD 一0 加 氢 裂 化 阻 垢 缓 蚀 剂 能 有 效 地 YD -0 加 S Y 11 阻止和延缓空冷设备及管线因硫含量过高而引起的腐蚀。
蚀 体 系[ 。 5 ]
加氢裂 化装置 的显 著 特点 是 高温 、 高压 、 临氢 、 易燃 、 易爆 , 且在有毒介 质环境 下操作u 。工艺 目的 j 是精炼 目标 产 品 的同 时 除去 烃类 中的 s N, 等非 , 0
理想组分 , 因此会 有大 量 的 H S Ha, 。 H N等 , NH , C
随着油 田 的 长期 大 量 开 采 , 油 性 质 逐 渐 劣 原 化 , 油组 分 中的硫 含量增 长 以及生 产工 艺装置 的 原 扩 建改造 , 导致 炼油 生 产过程 中不 断暴露 出设备 安 全 运行 、 腐蚀 防护 、 品质 量 保证 以及 安 全 环保 等 产 诸 多方 面 的问题 。尤 其 是 在 炼 油加 氢 裂 化 工艺 过 程中, 高压 空冷 器 的腐 蚀 防护 问题 已经成 为保证 工 艺装 置正 常生产 运行 的基 本条 件 。
有 所增加 , 是造 成腐 蚀 的又一 个 原 因。例 如某炼 也 油厂重油加氢装 置两 台高压 空冷器在 8 5 月 内 ~1 个 相继发生 3 腐蚀 泄露 事故 , 造 成装 置 单 系列非 次 共 计划停 工 4 天 。造 成腐 蚀 的直 接原 因是改 造后 两 5 台空冷器 出入 口温 度 降 低 以及 介 质 中硫 化 氢 含 量 增 加 。在注 水 条 件 下 , NH 、 HS NH 1 合 物 及 C混 H s等物 质 , 成凝 液 而 发生 电化 学 腐蚀 , 形 凝液 的 不 断浓 缩进 一步 加 剧 了腐 蚀 , 终 造 成 穿孔 泄 漏 , 最 给安 全生 产 带来 隐 患[ 。 因此 研 究加 氢 裂化 装 2 ] 置高压 空 冷器腐 蚀及 防护 问题具 有重 要意义 。
加氢裂化操作规程
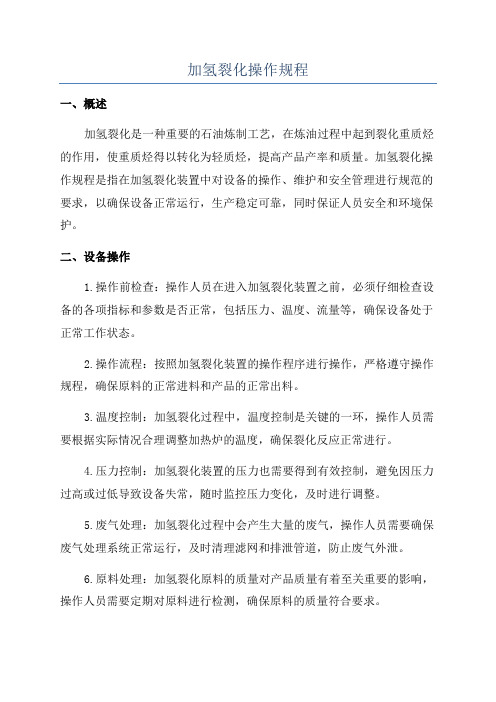
加氢裂化操作规程一、概述加氢裂化是一种重要的石油炼制工艺,在炼油过程中起到裂化重质烃的作用,使重质烃得以转化为轻质烃,提高产品产率和质量。
加氢裂化操作规程是指在加氢裂化装置中对设备的操作、维护和安全管理进行规范的要求,以确保设备正常运行,生产稳定可靠,同时保证人员安全和环境保护。
二、设备操作1.操作前检查:操作人员在进入加氢裂化装置之前,必须仔细检查设备的各项指标和参数是否正常,包括压力、温度、流量等,确保设备处于正常工作状态。
2.操作流程:按照加氢裂化装置的操作程序进行操作,严格遵守操作规程,确保原料的正常进料和产品的正常出料。
3.温度控制:加氢裂化过程中,温度控制是关键的一环,操作人员需要根据实际情况合理调整加热炉的温度,确保裂化反应正常进行。
4.压力控制:加氢裂化装置的压力也需要得到有效控制,避免因压力过高或过低导致设备失常,随时监控压力变化,及时进行调整。
5.废气处理:加氢裂化过程中会产生大量的废气,操作人员需要确保废气处理系统正常运行,及时清理滤网和排泄管道,防止废气外泄。
6.原料处理:加氢裂化原料的质量对产品质量有着至关重要的影响,操作人员需要定期对原料进行检测,确保原料的质量符合要求。
7.填料更换:加氢裂化装置的填料是一项重要的维护工作,操作人员需要定期对填料进行更换和清理,保证填料的良好状态。
8.安全操作:加氢裂化过程中,操作人员需要严格遵守安全操作规程,佩戴个人防护用具,防止意外伤害发生。
三、设备维护1.定期检查:加氢裂化装置需要定期进行检查和维护,包括设备的各个部位和连接点,确保设备的正常运行。
2.润滑保养:加氢裂化装置中的各种设备和部件需要定期进行润滑保养,确保设备的正常运转和延长设备的使用寿命。
3.设备清洁:加氢裂化装置需要定期进行清洁,除去积灰和杂物,保持设备表面清洁,避免设备堵塞和腐蚀。
4.防腐处理:加氢裂化装置的设备容易受到腐蚀,需要进行防腐处理,定期检查设备表面和内部是否出现腐蚀迹象,及时进行处理。
加氢裂化装置腐蚀问题及应对策略研究

加氢裂化装置腐蚀问题及应对策略研究引言加氢裂化装置是石油炼制过程中常用的一种工艺,用于生产高质量汽油和液化石油气。
然而,加氢裂化装置在运行过程中常常会遇到腐蚀问题,导致设备的损坏和生产效率的下降。
本文将对加氢裂化装置腐蚀问题及应对策略进行研究。
加氢裂化装置腐蚀问题分析加氢裂化装置腐蚀主要包括以下几个方面:1. 原料腐蚀在加氢裂化装置的过程中,原料中的硫化物和氯化物等化合物会导致设备腐蚀。
特别是硫化物会在高温和催化剂的存在下形成硫酸,加剧腐蚀现象。
2. 液相腐蚀在高温和高压下,裂化油会产生酸性物质,如酚和酮类物质。
这些物质具有强腐蚀性,容易导致设备的腐蚀。
3. 气相腐蚀加氢裂化装置中的气相组分,特别是硫化氢和氯化氢等酸性气体,会与金属设备表面发生反应,导致设备的气相腐蚀。
4. 温度和压力对腐蚀的影响高温和高压是加氢裂化装置的工艺条件,但也是腐蚀问题的重要因素。
在高温和高压下,设备中的腐蚀现象更加严重。
加氢裂化装置腐蚀问题的应对策略针对加氢裂化装置的腐蚀问题,可以采取以下措施:1. 原料预处理在加氢裂化装置进料前,对原料进行预处理,去除其中的硫化物和氯化物等有害物质。
可以通过物理吸附、吸收、化学反应等方式进行预处理。
2. 催化剂选择选择抗硫、抗氯的催化剂,减少催化剂对设备的腐蚀作用。
催化剂的选择要根据原料成分和工艺条件进行合理的优化。
3. 材料选择在设备的设计和建设中,选择优质的耐腐蚀材料,如不锈钢、镍基合金等,以提高设备的抗腐蚀性能。
此外,还可以采用涂层技术对设备表面进行保护。
4. 温度和压力控制合理控制加氢裂化装置的温度和压力,避免超过材料的耐腐蚀极限。
可以通过优化工艺参数和加强监控管理等方式实现温度和压力的控制。
5. 清洁和维护加氢裂化装置需要定期进行清洗和维护,及时清除设备表面的积垢和腐蚀物质,并进行润滑和防护处理。
结论加氢裂化装置的腐蚀问题是一个需要重视和解决的技术难题。
通过原料预处理、催化剂选择、材料选择、温度和压力控制以及清洁和维护等措施,可以有效降低加氢裂化装置的腐蚀现象,提高装置的安全性和可靠性。
中压加氢裂化装置部分设备的腐蚀与防护

9 1 2 3 41 4 5 6 73 7 5 3 9 7 5 8l 8 9 9 7
分 析 次 数
验、 汲取教训 , 为今后的防腐工作提供参考和依据。
1 高 压换热 器管 束大 面积腐蚀 穿孔 1 1 腐蚀 简 介 .
图 l 加氢 原料 中氯 的质 量分数
E54管束材质为 l 号钢 , - 0 0 对硫 、 氯腐蚀非常
敏感 。从 2 0 0 8年 1 到 2 0 月 0 9年 1 , 氢 装置 滤 月 加
后原料中硫含量不断增加 , 氯质量分数也大大超过
了 lt / g g的工 艺 指 标 。特 别 是 从 20  ̄ 0 9年 3月 采 用重 质 氯分析 仪进行 分 析后 , 析结 果 大 幅度升 高 分
力 正常 。通过 分析 , 定是 E54内漏 导 致脱 丁烷 工机械专业 , 认 .0 工程师 , 现任 中 国石 油化工股 份有 限公 司炼油 塔压 力超 高 , 系调 度 和 瓦斯 班 后 , 应 系 统 向火 事业部综合处处长 。Ema : ex @s oe. o 联 反 - i m nq i pc石ro i 化o e to n 蚀he 防u ty Cr so P 工 ni er c mia n 护 油 r t ci P to 与 l d sr 腐 o n& c I
2 1 1 , 2 0 8 ( 6 ) ・ 1 8 ・
中压 加 氢 裂化 装 置 部分 设 备 的腐 蚀 与 防护
孟 宪 强 , 漾 易
( 中国石油化工股份有 限公 司炼油事业部 , 北京 10 2 ) 0 7 8
摘要 : 自加工 高含硫原 油后 , 中压加氢裂化装置 的腐蚀 问题 日趋严 重, 先后 出现 高压换 热 器管束
腐 蚀穿孔、 分馏塔加热炉进 料线大小头腐蚀减 薄、 石脑油塔 顶空冷器 管柬腐蚀 穿孔和脱硫后 干 气 H s
加氢反应流出物腐蚀案例分析(可编辑)

加氢反应流出物腐蚀案例分析炼油与化工第卷加氢反应流出物腐蚀案例分析杨秀娜,齐慧敏,高景山,李欣抚顺石油化工研究院,辽宁抚顺摘要:介绍了加氢反应流出物系统存在的主要腐蚀形式和系统的腐蚀原因。
通过分析加氢装置的实际腐蚀案例,提出了相应的防腐控制对策及腐蚀控制原则。
关键词:加氢装置;铵盐腐蚀;防护措施中图分类号: 文献标识码: 文章编号:随着进口高硫原油量的逐年增加和环保法规浓缩沉积造成垢下腐蚀,形成蚀坑,最终导致穿的日益严格,加氢技术作为一种油品清洁方法在孔。
由于垢下腐蚀发生了强烈的金属溶解,产生炼油行业的作用越来越重要。
由于进口原油中硫大量的金属阳离子“,使溶液中的正电荷过剩,吸引外部的和一,借电泳作用移动到发生腐蚀含量较高,已经大大超出了原有加氢装置所能处的部位,造成了和一的富集,使该部位溶液的理的范围,因此加氢装置的腐蚀问题日益严重,腐值下降。
同时金属表面的保护膜由于蚀泄漏事件也不断发生,同时由于加氢装置属于和的存在被破坏,使腐蚀进一步加剧,高温高压临氢操作,物料易燃易爆,装置一旦发生生成更多的阳离子,吸引更多的阴离子进来。
如腐蚀泄漏,其危害性非常严重。
此循环往复,形成自催化过程,并随时间推移而加加氢装置的腐蚀主要是加氢反应器、反应流速进行下去。
因此,如果系统内一旦形成出物换热器、高温高压管线的 :、 : 腐蚀、高压空和的结垢物,在少量水存在的情况下,便会冷器的、腐蚀以及连多硫酸应力腐蚀发生十分严重的局部腐蚀口。
开裂?。
其中高压换热器和高压空冷器为加氢装的垢下腐蚀机理置最容易发生腐蚀泄漏的设备,这是由于高压换的垢下腐蚀反应方程式见 , 式。
热器或空冷器前需注水溶解铵盐,使得加氢产物?到达换热器或空冷器时形成了水和硫化氢的较强?腐蚀环境,而且由于水的注入使物流温度降低而当摩尔分数低于 %不会发生明显腐发生部分相变,更加加剧了换热器或空冷器的腐蚀,随着摩尔分数上升,腐蚀加剧。
当蚀。
因此了解换热器或空冷器的腐蚀机理及相应的浓度增加到较大时,会形成氨离子络合的腐蚀案例对于换热器和空冷器的设计、减少腐物,剥离金属表面的保护层,急剧增加垢下腐蚀事故的发生具有重要意义。
加氢装置脱硫化氢汽提塔系统腐蚀调查——腐蚀控制对策
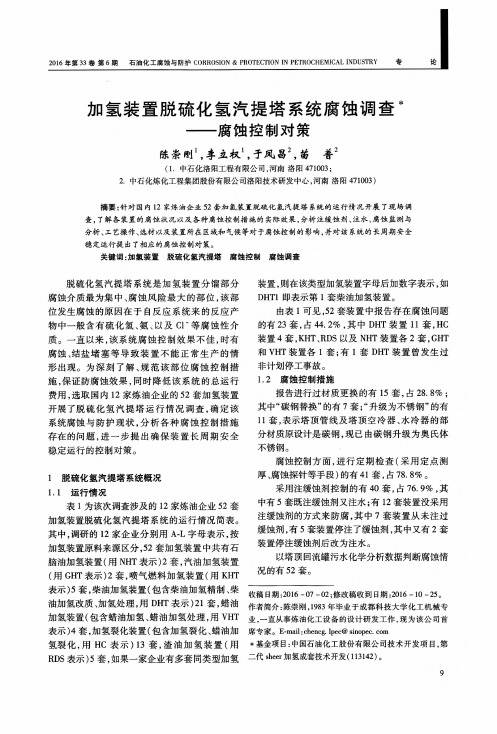
蚀监测,并且部分企业在定期腐蚀监测中发现了 潜在的腐蚀问题,并按计划进行了处理。
调查发现,如果原料中硫质量分数低于
用要求。但考虑到操作的变化以及实际分段的困 难,脱硫化氢汽提塔材质全塔使用碳钢+0Crl3 (0crl3A1)或碳钢+奥氏体不锈钢更为合理。 对于采用重沸炉(器)汽提的脱硫化氢汽提 塔,在操作上能避免塔内铵盐结晶的情况下,使用
10
空冷器入口加合金保护套管,在空冷器入口注水, 腐蚀控制良好;
企业E装置KHT塔顶系统停注缓蚀剂后,塔
顶管线增加保温,注水改为除盐水,使用5 a时 间,管线未见明显腐蚀减薄。 2.3腐蚀监测与分析 腐蚀调查结果表明,所有企业都进行定期腐
上部碳钢+0Crl3(0Crl3A1)或碳钢+奥氏体不锈
钢(304L,316L和321)、下部为碳钢材料的方案,
加氢装置脱硫化氢汽提塔系统腐蚀调查术
——腐蚀控制对策
陈崇刚1,李立权1,于凤昌2,苗
普2
(1.中石化洛阳工程有限公司,河南洛阳471003; 2.中石化炼化工程集团股份有限公司洛阳技术研发中心,河南洛阳47l003)
摘要:针对国内12家炼油企业52套加氢装置脱硫化氢汽提塔系统的运行情况开展了现场调 查,了解各装置的腐蚀状况以及各种腐蚀控制措施的实际效果,分析注缓蚀剂、注水、腐蚀监测与 分析、工艺操作、选材以及装置所在区域和气候等对于腐蚀控制的影响,并对该系统的长周期安全 稳定运行提出了相应的腐蚀控制对策。 关键词:加氢装置脱硫化氢汽提塔腐蚀控制 腐蚀调查
决定停注的。目前这12套装置塔顶冷凝冷却系 2存在的问题
2.1
统腐蚀控制均良好,因此在该系统是否加注缓蚀 剂,与系统是否能有效防止腐蚀没有必然联系。 2.2注水
- 1、下载文档前请自行甄别文档内容的完整性,平台不提供额外的编辑、内容补充、找答案等附加服务。
- 2、"仅部分预览"的文档,不可在线预览部分如存在完整性等问题,可反馈申请退款(可完整预览的文档不适用该条件!)。
- 3、如文档侵犯您的权益,请联系客服反馈,我们会尽快为您处理(人工客服工作时间:9:00-18:30)。
加氢裂化是炼油厂重要的二次加工手段,可以获得高质量的轻质燃料油。其特点是对原料适应性强,可加工直馏重柴油、催化裂化循环油、焦化馏出油,甚至可以用脱沥青重残油生产汽油、航煤、和低凝点柴油。其次,生产方案灵活,可根据不同的季节改变生产方案,并且产品质量好,产品收率高。
加氢裂化操作条件:温度380-450℃,操作压力8-20Mpa,采用的催化剂含有Pt、Pd、W、Mo、Ni、Co等金属氧化物作为加氢组分,以硅酸铝、氟化氧化铝或结晶硅铝酸盐为载体。原料油经加氢、裂化、异构化等反应转化为轻油产品,收率一般可达100%(体积),可以获得优质重整原料、高辛烷值汽油、航煤、和低凝点柴油,同时产品含硫、氮、烯烃低,安定性好。
基材、焊缝
微裂纹
磁粉探伤检查裂纹,打硬度
打磨修补,严重时考虑更换
应力集中
裂纹
裙座与封头连接部位,外构件连接部位
焊缝裂纹
磁粉探伤检查裂纹,超声波检查大小和部位
打磨修补
蠕变裂纹
反应器开口锻件与壳体连接部位焊缝热影响区
延展率下降,收缩率下降,蠕变断裂
磁粉探伤检查裂纹,超声波检查大小和部位
修补
堆焊层氢脆裂纹
6.1.5 高压空冷器的垢下腐蚀
由于重油加氢原料中含有硫化物、氮化物和氯化物,在加氢反应中会生成H2S、NH3和HCl,经过冷却后,会在高压空冷器部位生成腐蚀性很强的NH4HS和NH4Cl环境。如果设计工艺条件合理,操作条件基本与设计条件一致,腐蚀将会比较缓和。但是,如果设计条件不合理,或者操作条件严重偏离设计条件,该部位将会出现严重的局部腐蚀。
反应器基材与堆焊层界面剥离现象是氢致裂纹长大的一种形式。由于反应器在高温高压条件下操作,金属内部吸藏有大量的氢,在高温状况和低温状况下,氢气在基材和堆焊层中的饱和溶解度变化不一致,一旦停工,氢气不能完全释放,在界面层聚集,导致界面层脆化造成的。另外,熔合层上的应力和不锈钢堆焊层的化学成分也是重要的影响因素。所以装置停工应采用氢较为彻底释放的方案,即停工时冷却速度尽量放缓,在较高的温度多停留一段时间,严格遵循操作规程,避免异常升温和紧急停工。
2.25Cr-1Mo钢基材、焊缝金属
氢腐蚀裂纹
长期在200℃以上含氢介质中使用,钢表面和内部产生脱碳
2.25Cr-1Mo钢基材、焊缝金属
氢致裂纹
高温操作后急冷
2.25Cr-1Mo钢基材、焊缝热影响区
奥氏体不锈钢焊接部位的氢脆裂纹
高温操作氢扩散入钢内部,停工后冷却速度过快
反应器内部堆焊层、内构件连接焊缝,垫片密封槽
材料性能
劣化
所有部位
超声波检查裂纹和内部缺陷;磁粉探伤检查裂纹;检查硬度和金相组织变化
6.4 防腐蚀系统设计
氯化铵和硫氢化铵的沉淀物可造成换热器和管线的堵塞和垢下腐蚀,对操作物料进行断续的水洗,以冲洗这些沉淀物。水冲洗仅在为了减少操作压力降的时候才可以进行,避免长期连续注水,防止材料长期和酸性溶液接触。
加氢反应器的开停工要求:开工时反应器入口温度达到170℃,其它部位的温度大于135℃时开始升压;停工时反应器任何部位的温度降到135℃时装置的操作压力要降到不超过铬钼钢回火脆变后确定的最大允许压力。
6.2.2 其它措施
停工期间应严格按照NACE推荐执行标准PR01-75(《炼油厂停工期间使用中和溶液防止奥氏体不锈钢产生应力腐蚀开裂》)进行操作。
汽体塔顶及其冷凝系统在此部位由于存在低温H2S-HCl-H2O型腐蚀,所以在生产操作过程中应考虑注水、注中和剂和缓蚀剂,必要时材料升级为双相钢。关于注水、注中和剂和缓蚀剂的情况参考常减压塔顶系统工艺防腐规范。
由于连多硫酸应力腐蚀开裂在装置停工期间发生,因此装置停工期间应参照NACE推荐执行标准PR-170-97(《奥氏体不锈钢和其它奥氏体合金炼油设备装置在停工期间产生连多硫酸应力腐蚀开裂的防护》)进行操作。
6.1.4铬钼钢的回火脆性
铬钼钢具有回火脆性,所谓回火脆性指铬钼钢长期在371-593℃使用,由于钢中微量不纯元素和合金元素向奥氏体晶界偏析,使晶界凝聚力下降,致使材料脆化转变温度向高温迁移,导致产生晶间破坏的韧性劣化现象。在加氢裂化装置中使用的铬钼钢系列中以2.25Cr-1Mo和3Cr-1Mo钢的回火脆性敏感性最为显著。如果所存在的缺陷尺寸、作用应力、回火脆化后的断裂韧性值符合断裂力学的断裂条件,在低温升压时,就有可能引起脆性破坏。
为防止热壁加氢反应器高温氢+硫化氢腐蚀,通常在反应器基体内壁再堆焊超低碳不锈钢防护层。为防止高温裂纹,堆焊层表面3mm以下范围内的金相组织应为均匀的奥氏体+铁素体双相组织,焊后状态铁素体含量为3-10%。这是因为铁素体含量过低,容易产生热裂纹,铁素体含量过高,在设备焊后热处理时,一部分铁素体转化为σ相,造成不锈钢堆焊层的脆化,这对于加氢反应器,特别是内部支持件附近非常重要。堆焊层铁素体含量可以采用Schaeffler Diagram(谢菲尔图)进行检查,也可以使用铁素体测量仪直接在堆焊层上测量。
反应器发生的主要缺陷类型、部位、检查处理方法见表9。
表9反应器发生的主要缺陷类型、部位、检查处理方法
缺陷类型
缺陷部位
缺陷形态
检查方法
处理方法
回火脆化
基材、焊缝
韧性下降
反应器内挂片试验或定期取样检查
提高升压时温度(开工),缩短检修周期,监视韧性下降程度
氢腐蚀
基材、焊缝
裂纹、脱碳
超声波检查腐蚀程度
修补
氢致裂纹
6.1.2堆焊层氢致开裂
在高温高压的氢气氛中,氢气扩散侵入钢材,当反应器停工冷却过程中,温度降至150℃以下时,由于氢气来不及向外释放,钢中吸藏了一定量的氢,这样在一定条件下就有可能发生开裂。裂纹的产生和钢中的氢气含量有很大关系,曾经有实验证明,停工7个月后的加氢反应器,堆焊层仍有29ppm的氢含量,在堆焊层上取样进行弯曲实验,弯曲角度在19-750范围内试样就发生了开裂,取试样进行脱氢处理后,试样中氢含量降到1.2ppm,试样弯曲到1800也没有发生开裂。实验证明了氢脆的危害性,同时也证明了氢脆是可逆的。另外,一旦有σ相的叠加作用,将会导致堆焊层的延展性能进一步损失。
加工含酸、高酸原油主要对原料油进料系统有严重影响,加氢反应器也应选择防护措施。
6.1 腐蚀形态
6.1.1氢损伤
高温高压条件下扩散在钢中的氢与钢中不稳定的碳反应生成甲烷,可引起钢的内部脱碳,甲烷不能从钢中逸出,聚集在晶界及其附近的空隙、夹杂物等不连续处,压力不断升高,形成微小裂纹和鼓泡,钢材的延展性、韧性等显著降低,随之变成较大的裂纹,致使钢最终破坏。因为铬钼钢具有良好的高温力学性能和抗氢损伤性能,近年来加氢反应器大多选用2.25Cr1Mo钢制造。
反应器内构件和内部堆焊层
6.2工艺防腐措施
6.2.1 加氢高压空冷器
设备进料中含硫化氢和氨越多,腐蚀性越强。硫化氢和氨反应生成硫氢化铵,硫氢化铵的浓度越大腐蚀性越强,一般引用硫化氢和氨的百分子摩尔数的乘积,Kp:
Kp = [H2S]*[NH3]
Kp值越大,硫氢化铵浓度越高,相应的腐蚀越严重。对于加氢高压空冷器,选用碳钢设备时,控制Kp在0.5%以下,流速控制在4.6-6.09m/s,介质中无氰化物和氧存在;如果Kp大于0.5%,流速低于3.5m/s或高于7.62m/s时,选用3RE60、Monel、Incoloy800等,不允许选用Cr17钢(SA430)。
高压空冷器还应采用如下措施:使用碳钢管束增加管子壁厚,管子进口端增加耐蚀套管,套管长度不小于200mm;空冷器管束进口管线应对称分布,管束结构采用管箱式,不允许采用回弯头式结构;为防止管束内铵盐沉积堵塞管线,可采用定期或不定期注水方式,控制注水的pH值9-9.5(可使用含硫污水);根据情况选择合适缓蚀剂进行注入;每片空冷器均设阀门,为预防万一,可切断。
6.3 设备防腐设计
为减少产生晶间腐蚀的可能,焊接结构中使用稳定性不锈钢(0Cr18Ni10Ti、0Cr18Ni10Nb),不使用0Cr18Ni9钢。
有可能发生湿硫化氢应力腐蚀的环境中,所使用的设备应选用镇静钢(最好选用抗HIC钢),不得选用含Ni钢,基材和焊缝的硬度不得大于HB200,基材和焊缝应进行100%超声波探伤。检验结果应符合JB4730-1994《压力容器用钢无损检测》中 级要求。
对加氢生成物空冷器,最好不使用U形管束,采用两侧管箱式。因为如果使用U形管束,在弯头外侧上部900范围内,由于涡流的影响,冲蚀十分严重。
在湿硫化氢环境下,为防止产生应力腐蚀开裂,设备制造时应满足下列要求:设备制造完毕后,应进行焊后消除应力热处理,控制焊缝及其热影响区的硬度小于等于HB200。当采用埋弧自动焊时,不得用陶瓷型焊剂,必须使用熔融型焊剂。
铬钼钢回火脆性的特征:脆性断面呈现晶界破坏形态;回火脆性对材料抗拉强度和延展率影响不大,主要反映在冲击韧性上;材料一旦脆化,则脆性转变温度向高温迁移;回火脆性是可逆的,将脆化的材料加热到600℃以上后急冷,材料可以恢复到原来的韧性。
回火脆性的影响因素主要有化学成分和热处理条件的影响。
化学成分影响:微量不纯元素磷、锡、砷、锑四种元素对脆化影响最大,称为脆化元素,含量多时,回火脆化特别显著。锡、砷、锑三种元素可以通过严格控制炼钢原料使它们降到适当的程度,关键是对磷的控制。硅和锰是促进脆化元素,含量过大可以显著提高材料回火脆性敏感性。Cr添加后也显著提高材料回火脆性敏感性,特别Cr在2-3%时影响最大。Ni含量影响不大,但如果磷、锡存在时有影响,含少量的钼、钨影响较低,它们含量较高时钢的回火脆性敏感性也会增加。铜不是脆化元素,但具有脆化催化剂的作用。
热处理的影响:在热处理过程中,奥氏体化温度和从奥氏体转化温度冷却的速度都对钢的回火脆性敏感性产生很大的影响。提高奥氏体转化温度,就会使奥氏体晶粒粗大,容易脆化。从奥氏体转化温度以不同的冷却速度冷却时,因冷却速度不同将会产生不同的显微组织,当钢的化学成分相同时,钢的回火脆性敏感性按马氏体、贝氏体、珠光体顺序递减。