电风扇旋扭的塑料模设计
电风扇前罩注塑模具设计

目录1 前言 (1)2 总体方案设计 (3)2.1 总体方案论证 (3)2.2热塑性塑料注塑成型工艺性分析 (3)2.3设计要点 (3)2.4 塑件的测绘 (4)2.5 塑件的三维造型 (6)2。
6 塑件的工艺分析 (7)2。
6.1塑件的材料分析 (7)2.6.2塑件尺寸精度的选择 (7)2。
6.3塑件的结构工艺性分析 (8)2。
7脱模斜度的确定 (8)3总体结构设计说明 (9)3。
1注塑机的选择 (9)3.2注塑机的校验 (9)3.3型腔数目的确定 (10)3。
4塑件收缩率的计算 (10)3.5模具型腔工作尺寸计算 (10)3。
6模具型芯工作尺寸计算 (11)3.7螺纹型芯工作尺寸计算 (11)3.8分型面的设计 (11)3。
9 浇注系统设计 (12)3。
10冷却系统设计 (14)3.10。
1冷却系统的设计原则 (14)3。
10.2模具的冷却水道直径计算 (15)3.11脱模机构设计 (16)3。
12导向机构设计 (17)3.13排气系统设计 (17)3.14侧抽芯机构设计 (17)3。
15模具材料的选择 (19)3。
16模板尺寸的确定 (19)3.17绘制模具总体装配图 (19)4模具零件的工艺分析及制造 (21)4。
1零件的加工工艺分析 (21)4.2凹模的加工仿真 (22)5 结论 (25)参考文献 (26)致谢 (27)附录 (28)1 前言模具是现代工业生产的重要工艺装备。
在现代工业生产中,模具已广泛应用于电机电器产品、电子和计算机产品、仪表、家用电器、汽车、军械、通用机械等产品的生产中。
用模具生产制造所表现出来的高精度、高复杂程度、高生产率和低消耗等特点是其他加工制造方法所不能比拟的。
随着现代化工业和科学技术的发展,人们对工业产品的品种、数量、质量及款式的要求愈来愈高,模具的应用也就愈来愈广泛,其适应性也愈来愈强,已成为国家制造工艺水平的标志和独立的基础工业体系。
模具的类型很多,按照成形件的材料不同,可以分为冲压模具、塑料模具、锻造模具、压铸模具、橡胶模具、粉末冶金模具、玻璃模具和陶瓷模具等,其中应用最为广泛的是冲压模具和塑料模具。
模具毕业设计33电风扇旋钮注塑模设计说明书

届毕业设计说明书材料系、部:机械工程系学生姓名:指导教师:职称:教授专业:材料成型及控制工程班级:班学号:完成时间:5月摘要模具是利用其特定形状去成型具有一定形状和尺寸的制品的工具,按制品所采用的原料不同,成型方法不同,一般将模具分为塑料模具,金属冲压模具,金属压铸模具,橡胶模具,玻璃模具等。
因人们日常生活所用的制品和各种机械零件,在成型中多数是通过模具来制成品,所以模具制造业已成为一个大行业。
在高分子材料加工领域中,用于塑料制品成形的模具,称为塑料成形模具,简称塑料模.塑料模优化设计,是当代高分子材料加工领域中的重大课题。
本次毕业设计是电风扇旋扭,它所要达到的要求:要能耐高温,绝缘性要好,耐气候性强,刚性,韧性佳,通过对产品的各种性能分析,选用材料为ABS,该塑件的厚度为1mm,公差等级为IT5级。
它是用来调节风速和定时的,能够满足人们的热天对风力和吹风长短要求,同时也起到美观的作用。
关键词:塑料模;材料;电风扇旋钮ABSTRACTMold is used to shape the specific shape of a certain shape and size of products tools used by the products of different raw materials, different methods shaped general layout will be divided into plastic molds, metal stamping dies, metal die-casting molds, rubber molds, glass molds. It is used in the daily life of products and various mechanical parts, mostly in the shape of heads through to finishe products, it has become a major instrument manufacturing industry. In the field of macromolecular materials for plastic products shape the instrument, known as plastic molding shape. Plastic molds optimized design is contemporary in the field of macromolecular materials processing major issue.The graduation design is fanner knob and, it will reach request: to high temperature, insulation can strong sex is better, resistance to climate, rigid, toughness good, through various performance analysis ofproducts, choose materials for ABS, the thickness of plastic parts for 1mm, tolerance grade IT5 level for. It is used to regulate the speed and timing, can satisfy people's hot weather blowback for wind and length of requirements, while also play beautiful role.Key words :Plastic mould; materials; Fanner knob目录前言 (1)1 塑件的工艺性分析 (2)2 分型面位置分析和确定 (4)2.1型腔数目的确定 (4)2.2型腔的布局 (4)2.3分型面设计 (4)3 注射机的选择及工艺参数校核 (6)3.1注塑机的选择 (6)3.2工艺参数的校核 (6)4 成型零件的设计 (8)4.1型腔的结构设计 (8)4.2型腔的工作尺寸计算 (9)4.3型芯的结构设计 (9)5 模架的设计 (12)6 合模导向机构的设计 (13)6.1导柱的设计 (13)6.2导套的设计 (14)7 推出机构的设计 (15)8 浇注系统与排溢系统的设计 (19)8.1主流道的设计 (19)8.2分流道的布置 (20)8.3浇口的设计 (20)8.4浇口位置的确定 (21)8.5排溢系统的设计 (22)9 温度调节系统的设计 (24)10 模具的工作过程 (26)10.1模具的装配 (26)10.2模具的装配顺序 (26)10.3模具的动作过程 (27)结束语 (28)参考文献 (29)致谢 (30)前言光阴似箭,在校的大学四年的学习一晃而过,为具体的检验这四年来的学习效果,综合检测理论在实际应用中的能力,除了平时的考试、实验测试外,更重要的是理论联系实际,即此次设计的课题为电风扇旋钮塑料模具设计。
电风扇叶片塑料模具设计说明

第1章注射模可行性分析1.1注射模设计的特点塑料注射模塑能一次性地成型形状复杂、尺寸精确或嵌件的塑料制品。
在注射模设计时。
必须充分注意以下三个特点:(1)塑料熔体大多属于假塑料液体,能剪切变稀。
它的流动性依赖于物料品种、剪切速率、温度和压力。
因此须按其流变特性来设计浇注系统,并校验型腔压力及锁模力。
(2)视注射模为承受很高型腔压力的耐压容器。
应在正确估算模具型腔压力的基础上,进行模具的结构设计。
为保证模具的闭合、成型、开模、脱模和侧抽芯的可靠进行,模具零件和塑件的刚度与强度等力学问题必须充分考虑。
1.2注射模组成凡是注射模,均可分为动模和定模两大部件。
注射充模时动模和定模闭合,构成型腔和浇注系统;开模时定模和动模分离,取出制件。
定模安装在注射机的固定板上,动模则安装在注射机的移动模板上。
根据模具上各个零件的不同功能,可由一下个系统或机构组成。
(1)成型零件指构成型腔,直接与熔体相接触并成型塑料制件的零件。
通常有凸模、型芯、成型杆、凹模、成型环、镶件等零件。
在动模和动模闭合后,成型零件确定了塑件的内部和外部轮廓尺寸。
(2)浇注系统将塑料熔体由注射机喷嘴引向型腔的流道称为浇注系统,由主流道、分流道、浇口和冷料井组成。
(3)导向与定位机构为确保动模与定模闭合时,能准确导向和定位对中,通常分别在动模和定模上设置导柱和导套。
深腔注射模还须在主分型面上设置锥面定位,有时为保证脱模机构的准确运动和复位,也设置导向零件。
(4)脱模机构是指模具开模过程的后期,将塑件从模具中脱出的机构。
(5)侧向分型抽芯机构带有侧凹或侧孔的塑件,在被脱出模具之间,必须先进行侧向分型或拔出侧向凸模或抽出侧型芯。
1.3塑料风叶设计与分析风叶是利用一定空间曲面的叶片,通过主体的高速旋转产生风能。
以前,大都是采用金属片材,经过模压制成风叶片。
然后与风叶主体固定安装成风叶。
由于模压叶片和装配等方面的原因,往往风叶的静、动平衡难以达到设计要求。
电风扇叶注塑模设计

4 电风扇叶注塑模设计4.1 注塑模设计的基本流程传统方法的注塑模设计是在二维环境下进行,从图4.1中可以看出,传统的模具制造工艺路线只是典型的串行流程,任何其中一部分没有完成都会影响下面的工作,相互之间的制约性太大,这样的结果就是生产周期的延长,人工进行的工作量非常大,而且做工粗糙、精度不高,在CAD/CAM技术高速发展的今天,传统方法终将被取而代之。
基于UG 的注塑模具的设计是在三维环境下进行的,这用方法的采用不仅提高了生成型芯和型腔零件的速度和准确度还可以进行造型设计,还能完成模具的总装配,大大缩短了模具设计周期并及时发现模具设计中的错误,有效地避免工人重复劳动[16]。
图4.1传统方式的注塑模具设计过程图4.2 基于UG的注塑模设计工程4.2 注塑模具的基本结构设计4.2.1 扇叶材料的分析风扇为人们日常生活常用品,需大批量生产,又与人们紧密接触,所以扇叶的材料必须无毒无害,同时考虑没有很高的强度要求,收缩率方面也无特殊要求,故选择ABS材料进行注塑生产。
ABS具有良好的成型加工型,制品表面光洁度高,且具有良好的涂装性和染色性,可电镀成多种光泽[17]。
塑料ABS具有以下性能:(1)冲击强度极好,耐磨性优良,尺寸的稳定性好。
(2)从热学性能上来看热变形温度为85℃左右,制品经退火处理以后还可提高10℃左右。
在-40℃时仍能表现出一定的韧性,可在-40℃到85℃的温度范围内长期使用。
(3)ABS的电绝缘性较好,并且几乎不受温度、湿度和频率的影响。
(4)ABS流动性好,易溢料,具有优良的化学稳定性、不吸水,是易成型加工的材料可用于注塑。
4.2.2 分型面的选择分型面是指上、下两模芯互相接触的表面,而分型面的设计在电风扇叶的注塑模设计中是非常重要的。
分型面一般是在确定浇注位置或被称为进料口的位置后再选择。
但在分析各种分型面方案的优缺点之后,也有可能需要重新调整浇注位置。
分型面选择原则有两个,首先要考虑到是塑件在开模时尽可能留在动模部分,同时由于塑件有曲面扇叶,所以也要尽可能留在动模部分。
电风扇上盖注塑成型模具毕业主设计

电风扇上盖注塑成型模具毕业主设计摘要:本文主要介绍了电风扇上盖注塑成型模具的主要设计。
首先,根据产品的形状和尺寸要求,确定了模具的结构类型和材料选择。
然后,通过对模具进行分解和零件设计,得到了模具的零件图。
接着,对模具进行总体结构和顶出结构设计,并给出了模具总体布置图。
最后,对模具进行了工艺路线选择和模具加工方案设计。
1.引言电风扇上盖注塑成型模具是电风扇制造中的关键工具,其设计质量直接影响到产品的质量和生产效率。
因此,对该模具的设计要求非常高。
本文将从模具的结构类型、材料选择、零件设计、总体结构设计、顶出结构设计、整体布置以及工艺路线选择等方面进行详细介绍。
2.结构类型和材料选择电风扇上盖注塑成型模具的结构类型可以根据产品的形状和尺寸要求来确定。
一般来说,采用单腔结构,由于该产品形状比较简单,不需要多腔模具。
材料选择方面,一般采用工程塑料,如ABS、PC等,具有良好的耐热性、耐磨性和强度。
3.零件设计根据模具的功能和工艺要求,对模具进行了分解和零件设计。
主要包括模具座、模芯、定位销、导向柱、顶针、顶出板等零件。
通过对零件进行尺寸和结构的合理设计,保证模具的精度和稳定性。
4.总体结构设计根据产品尺寸和形状要求,确定了模具的总体结构。
采用的总体结构是上模板、下模板和支撑板的组合结构。
上模板和下模板分别安装模芯和模具座。
通过设计模具的总体结构,使得模具在生产过程中具有良好的稳定性和刚性。
5.顶出结构设计顶出结构是电风扇上盖注塑成型模具中非常重要的一部分。
通过对产品的形状和尺寸要求的分析,设计了合理的顶出结构。
采用了顶出板和顶针的结合形式,通过弹簧将顶出板与顶针连接,保证产品的顶出效果。
6.模具布置根据模具的总体结构和顶出结构,进行了模具的整体布置。
通过分析模具的零件尺寸和工艺要求,保证模具的合理布置。
同时,还考虑到了模具在生产过程中的操作便利性和安全性。
7.工艺路线选择根据模具的结构和尺寸要求,选择了合适的注塑工艺。
旋钮设计说明书

山西机电职业技术学院(注塑模具设计说明)题目: 家用洗衣机旋钮注塑模具设计说明姓名: 刘晓婧专业: 模具设计与制造系别: 数控工程系学号: 29160216指导教师:王毅、申锐2010-12-24山西机电职业技术学院(注塑模具设计说明)诚信声明本人郑重声明:所呈交的注塑模具设计说明,题目《家用洗衣机旋钮注塑模具说明》是本人在指导教师的指导下,独立进行研究工作所取得的成果。
对本文的研究做出重要贡献的个人和集体,均已在文中以明确方式注明。
除此之外,本论文不包含任何其他个人或集体已经发表或撰写过的作品成果。
本人完全意识到本声明的法律结果。
注塑模具设计说明作者签名:刘晓婧日期:2010-12-24目录摘要 (1)第一章前言 (2)一、模具行业及产品发展现状 (2)二、选题意义 (3)三、设计任务 (3)第二章塑件设计分析 (5)一、塑件模型建立 (5)二、塑件参数设计 (6)三、塑件模流分析 (9)第三章注塑设备和模架选择 (19)一、注塑设备选择 (19)二、注塑机重要参数校核 (21)三、模架选择 (24)第四章浇注系统设计 (24)一、主流道设计 (25)二、分流道设计 (26)三、浇口设计 (27)四、冷料穴和钩料脱模装置 (28)第五章成型零件设计加工工艺方案制订 (29)一、型腔的设计 (29)二、型芯设计 (30)三、镶件设计 (31)四、加工工艺方案制订........................... 错误!未定义书签。
第六章顶出机构设计 (33)一、顶杆顶出机构 (33)二、顶管顶出机构............................... 错误!未定义书签。
第七章冷却系统设计 (34)一、冷却管道的工艺计算 (34)二、冷却水道的结构设计 (36)第八章模具装配图和零件图 (36)-、模具3D图形绘制 (36)二、模具及其零件2D图形绘制 (40)第九章模具设计的创新与特色总结 (42)第十章设计存在的问题与解决设想 (43)参考文献 (44)致谢 (45)附录模具装配图成型零件图塑件产品图家用洗衣机旋钮注塑模具设计说明【摘要】通过对家用洗衣机旋钮塑件的设计分析,设计出该塑件的模具。
旋钮注塑模具说明书 一模8腔

5
6
内形尺寸
7
8
9
10 11
19.5 R1.34 R20.3 0.75
36 2.1 0.6 表 3-4 塑件尺寸
19.5+0.41 ������1.34+0.23 ������20.3+0.41 0.75+0.23
36+0.5 2.1+0.23 0.6+0.23
4. 成型设备的选择
4.1 计算塑件的体积 根据制件的三维模型,利用三维软件直接求得塑件的体积为: V=4500.2194mm3,取 V=4.5cm3。
S=310mm,因此符合开模行程的要求。 6.6 模厚校核
模具闭合高度为 352mm,符合注射机 150 ~ 360mm 的模厚要求。
综上所述:选取 HTF120J/TJ 型螺杆式注射成型机完全符合本模具的使用要求。 锁模力 CAE 分析图
7 浇注系统的设计
7.1 设计原则 浇注系统设计原则:
(1)浇注系统与塑件一起在分型面上,应有压降,流量和温度的分布的均衡布 置;
材料名称
型腔
型芯
聚丙烯(PP)
25′~45′
20′~45′
考虑零件形状的复杂性,型腔采用 45′脱模斜度,型芯采用 20′脱模斜度。
3.2.4 壁厚:
-5-
上海工程技术大学材料工程学院
旋钮注塑模课程设计说明书
设计合理,壁厚相对均匀,且符合最小壁厚的要求。查 P434 表 2-2-7[1],聚 丙烯最小壁厚为 0.85 mm。 3.2.5 圆角: 要从分型面位置、型芯、型腔结构来分析过渡圆角的设置。工件转角处加圆角, 最小圆角尺寸为 0.5 mm。 3.3 塑件表面质量分析
电风扇叶片注塑模具设计中期报告
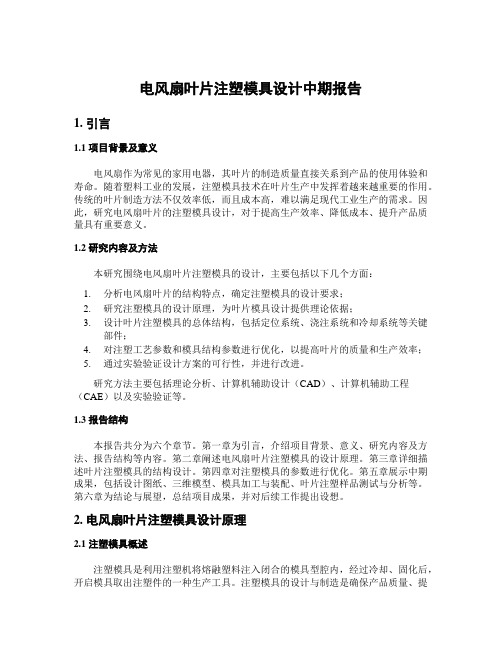
电风扇叶片注塑模具设计中期报告1. 引言1.1 项目背景及意义电风扇作为常见的家用电器,其叶片的制造质量直接关系到产品的使用体验和寿命。
随着塑料工业的发展,注塑模具技术在叶片生产中发挥着越来越重要的作用。
传统的叶片制造方法不仅效率低,而且成本高,难以满足现代工业生产的需求。
因此,研究电风扇叶片的注塑模具设计,对于提高生产效率、降低成本、提升产品质量具有重要意义。
1.2 研究内容及方法本研究围绕电风扇叶片注塑模具的设计,主要包括以下几个方面:1.分析电风扇叶片的结构特点,确定注塑模具的设计要求;2.研究注塑模具的设计原理,为叶片模具设计提供理论依据;3.设计叶片注塑模具的总体结构,包括定位系统、浇注系统和冷却系统等关键部件;4.对注塑工艺参数和模具结构参数进行优化,以提高叶片的质量和生产效率;5.通过实验验证设计方案的可行性,并进行改进。
研究方法主要包括理论分析、计算机辅助设计(CAD)、计算机辅助工程(CAE)以及实验验证等。
1.3 报告结构本报告共分为六个章节。
第一章为引言,介绍项目背景、意义、研究内容及方法、报告结构等内容。
第二章阐述电风扇叶片注塑模具的设计原理。
第三章详细描述叶片注塑模具的结构设计。
第四章对注塑模具的参数进行优化。
第五章展示中期成果,包括设计图纸、三维模型、模具加工与装配、叶片注塑样品测试与分析等。
第六章为结论与展望,总结项目成果,并对后续工作提出设想。
2. 电风扇叶片注塑模具设计原理2.1 注塑模具概述注塑模具是利用注塑机将熔融塑料注入闭合的模具型腔内,经过冷却、固化后,开启模具取出注塑件的一种生产工具。
注塑模具的设计与制造是确保产品质量、提高生产效率、降低成本的关键环节。
电风扇叶片作为常见的塑料制品,其注塑模具设计需满足以下要求:一致性高、尺寸精度高、表面光洁度好、生产效率高、使用寿命长。
注塑模具主要由动模、定模、导向系统、浇注系统、冷却系统、顶出系统等组成。
其中,动模和定模是模具的核心部分,它们的结构设计直接影响到叶片的尺寸精度和表面质量。
电风扇叶片塑料模具设计说明

第1章注塑模具的可行性分析1.1 注塑模具设计特点注塑成型可以一次成型复杂形状、精确尺寸或插入塑料制品。
在注塑模具设计中。
必须充分注意以下三个特点:(1)大部分塑料熔体属于假塑料液体,可以剪切和稀释。
其流动性取决于材料类型、剪切速率、温度和压力。
因此,必须根据其流变特性设计浇注系统,并检查型腔压力和锁模力。
(2)注塑模具被视为具有高型腔压力的耐压容器。
模具的结构设计应在正确估计模腔压力的基础上进行。
为保证合模、成型、开模、脱模和侧抽芯的可靠性能,必须充分考虑模具零件和塑料零件的刚度和强度等力学问题。
1.2 注塑模具的组成所有的注塑模具都可以分为动模和定模两部分。
当注模时,动模和定模闭合,形成型腔和浇注系统;开模时,定模和动模分离,取出零件。
定模安装在注塑机的固定板上,动模安装在注塑机的动模板上。
根据模具上各部分功能的不同,可组成一个系统或机构。
(1) 成型零件指形成型腔的零件,与熔体直接接触并形成塑料零件。
通常有冲头、型芯、成型棒、凹模、成型环、镶件等零件。
动模和动模合模后,成型件决定了塑件的外轮廓尺寸和外轮廓尺寸。
(2)浇注系统将塑料熔体从注塑机的喷嘴引向型腔的流道称为浇注系统,它由主流道、分流道、浇口和冷井组成。
(3) 导向定位机构为保证动模和定模合模时能准确导向和对准,通常在动模和定模上分别设置导柱和导套。
深型腔注塑模具还必须在主分型面上设置锥面定位,有时还要设置导向件,以保证脱模机构的准确移动和复位。
(4) 释放机制它是指在开模过程的后期将塑料件从模具中取出的机构。
(5) 横向剖分抽芯机构对于有侧凹或侧孔的塑件,在从模具中顶出之前,必须先进行侧分型,或者必须将侧冲头或侧芯拉出。
1.3 塑料风扇叶片的设计与分析风叶是利用一定空间曲面通过主体高速旋转产生风能的叶片。
过去,它们大多是由金属片制成,并模制成风叶。
然后,与扇叶主体固定安装,形成扇叶。
由于叶片成型和组装等原因,往往使风机叶片的静、动平衡难以满足设计要求。
塑料旋钮结构毕业设计正文

* * * * * * * * * * 装* * * * * * * * * * * * 订* * * * * * * * * * * * 线* * * * * * * * * * * *1塑件的工艺性分析1.1 制件的产品图插座产品三维结构如图1-1所示,其二维图如图1-2所示。
图1-1 插座三维示意图图1-2 插座二维图塑料旋钮结构如图1-3所示。
图1-3 旋钮三维图* * * * * * * * * * 装* * * * * * * * * * * * 订* * * * * * * * * * * * 线* * * * * * * * * * * * 1.2 尺寸及精度塑料制件的尺寸精度是指所获得的塑件与产品图中尺寸的符合程度。
影响塑件尺寸的精度很多,首先是模具的的制造精度,和模具的磨损程度,其次是塑料收缩率的波动以及成型时工艺条件的变化,塑件成型后的时效变化和模具的形状结构等。
因此,塑件的尺寸精度往往不高,应该在保证使用的前提下尽可能选用低精度等级。
根据定义图纸的要求公差为自由公差,结合塑料制件公差数值标准SJ137278,确定公差等级为4级,即一般精度标准。
1.3表面粗糙度塑件的外观要求越高,表面粗糙度应越低。
这除了在成型时从工艺上尽可能避免冷疤,云纹等疵点来保证外,主要是取决于模具型腔表面粗糙度。
一般模具表面粗糙度要比塑件的要求低1~2级。
由于此产品的外观要求不高,塑件的表面粗糙度定为Ra0.4μm。
1.4脱模斜度塑件冷却时的收缩会使它包紧住模具型芯或型腔中凸起的部分,因此为方便制件从型芯后从型腔中取出,必须设计一定的脱模斜度。
根据常用的塑件脱模斜度表查询得,型腔的脱模斜度为1°,型芯的脱模斜度为30'。
1.5塑件壁厚塑料制品应该有一定的厚度,这不仅是为了塑料制品本身在使用中有足够的强度和刚度,而且也是为了塑料在成型时有良好的流动状态。
塑件壁厚受使用要求、塑料材料性能、塑件几何尺寸以及成型工艺等众多因素的制约。
模具毕业设计10电风扇开关上盖

塑料成形工艺与模具设计课程设计设计课题电风扇开关上盖注射模具设计说明书系部机电系班级具(2)班姓名指导教师设计时间:年10 月11日目录目录 (2)一.设计任务书 (3)二.塑件的结构工艺分析 (4)2-1. 塑件原材料的成型特性分析 (4)2-2. 塑件的结构工艺性分析 (5)2-2-1.塑件的尺寸精度分析 (5)2-2-2.塑件的表面质量要求 (5)2-2-3.塑件的结构工艺性分析 (5)2-2-4.塑件的生产批量 (6)2-3.初选注射机 (6)2-3-1.制定成型工艺卡 (6)2-3-2.确定成型设备 (6)2-3-3.确定模具温度和冷却方式 (6)2-3-4.确定注射成型的工艺参数 (6)2-3-5.根据塑件本身的几何形状及生产批量确定型腔数目 (7)2-3-6.计算塑件体积和重量 (7)三. 分型面及浇注系统的设计 (8)3-1. 分型面的选择 (8)3-2.浇注系统的设计 (9)3-2-1.主流道和定位圈的设计 (10)3-2-2.分流道的设计 (11)3-2-3.浇口的设计 (11)3-2-4.冷料穴的设计 (11)四.模具设计方案论证 (12)4-1.型腔布置 (12)4-2.成形零件的结构确定 (12)4-2-1.型腔的设计 (12)4-2-2.型芯设计 (12)4-3.导向定位机构设计 (12)4-4.推出机构设计 (12)4-5.冷却系统设计 (13)4-6.抽芯机构的确定 (13)五.主要成型零部件的设计计算 (13)5-1.成型零件的成型尺寸 (13)5-2.模具型腔壁厚的确定 (13)5-2-1.型腔侧壁厚度S的计算 (14)5-2-2.型腔底板厚度T的计算 (14)5-3.抽芯机构的设计计算 (15)5-3-1.抽芯距S的计算 (15)5-3-2.抽芯力的计算 (15)5-3-3.确定滑块上的弹簧 (15)5-3-4.确定楔紧块的 ′ (15)5-4. 推出机构的设计 (15)5-5. 标准模架的确定 (15)六.成型设备的校核计算 (15)6-1.注射机注射压力的校核 (15)6-2.最大注射量的校核 (15)6-3.锁模力的校核 (16)6-4.安装尺寸的校核 (16)6-5.推出机构的校核 (16)6-6.开模行程的校核 (16)七.心得体会 (17)【参考文献】 (18)附图(Moldflow对塑件的分析) (19)模具报价 (21)模具三维爆炸图 (22)一、设计任务书1.塑料制品名称:电风扇开关上盖2.成型方法与设备:在XS-ZY-125型注射机上成型3.塑料原料:ABS4.收缩率:0.3%-0.8%5.生产批量:30万件6.塑件图:图1所示为该制品的二维图样,图2所示为该制品的三维图样。
风扇叶注塑模具设计

风扇叶注塑模具设计机械设计制造及其自动化200703536 孙桂兰指导老师刘晓琴(讲师)摘要:本文以日用电风扇叶片缩型为例,提出了对风扇叶的注塑模具设计。
根据注塑模具的工艺分析、生产规模等要素,选定了注塑机系列,确定了注塑模具的结构。
全文对模架机构进行了详尽的设计与定义,采用特殊分型面进行分模,实现塑件的顺利顶出。
根据塑件特性,详尽设计了注塑模具的浇注系统、冷却系统和顶出系统。
关键词:风扇叶,注塑模,注塑机,Solidworks,AS塑料工业是当今世界上增长最快的工业门类之一,而注塑模具是其中发展较快的种类,因此,研究注塑模具对了解塑料产品的生产过程和提高质量有很大意义。
1注射模可行性分析及注塑设备的选择1.1注射性能分析1.1.1注射成型工艺的可行性分析风扇叶形状复杂,壁厚不均,尺寸精度要求较高,而且有较高的表面质量和尺寸稳定性要求,因此对模具和设备的要求也较高。
而注射成型方法具有如下优点:几乎没有复杂性限制,容许模具内有不同塑料的成型型腔;塑件可小到不足1克,大到几十千克,没有限制;在一定温度范围内具有适宜流动性的热塑性塑料;可注射高精度的塑件,有较好的表面质量和尺寸稳定性;生产率中等,循环时间主要由塑件壁厚决定,最短可在十几秒内,可增加每模的型腔数来提高生产率。
由以上塑件的特点和注射成型工艺的优点分析可知:该塑件适合于采用注射成型方法。
1.1.2注射成型工艺要求风扇叶外表面要求较高,因此其表面粗糙度取Ra0.4mm,而其内表面由于是风扇基座的内部,为顾客视线所不及,故不影响其外观视觉质量。
从简化加工工艺和节约加工成本的角度考虑,其内表面选用的表面粗糙度为Ra0.8mm。
按SJ1372—1978标准,塑料件尺寸精度分为8级。
本塑件所用材料为AS塑料,由此查资料[5]可知,本塑件宜选用5级精度。
塑件尺寸精度与模具的制造精度密切相关,根据塑件零件图确定模具精度等级为IT8。
AS的成型收缩率较小(0.2-0.6%),而且塑件对型芯的包紧面积也较大,所以应取较大的脱模斜度。
家用电风扇叶片注塑模具设计文献综述

杭州电子科技大学毕业设计(论文)文献综述毕业设计(论文)题目家用电风扇叶片注塑模具设计文献综述题目注塑模具的发展学院机械工程学院专业机械设计制造及自动化姓名XXX班级XXX学号XXXXX指导教师XX模具是用来成型物品的工具,这种工具由各种零件构成,不同的模具由不同的零件构成。
它主要通过所成型材料物理状态的改变来实现物品外形的加工。
按所成型的材料的不同,模具可分为金属模具和非金属模具。
金属模具又分为:铸造模具(有色金属压铸,钢铁铸造)、和锻造模具等;非金属模具也分为:塑料模具和无机非金属模具。
而按照模具本身材料的不同,模具可分为:砂型模具,金属模具,真空模具,石蜡模具等等。
其中,随着高分子塑料的快速发展,塑料模具与人们的生活密切相关。
塑料模具一般可分为:注射成型模具,挤塑成型模具,气辅成型模具等等[1]。
注塑模具是生产各种工业产品的重要工艺装备,随着塑胶模具设计工业的迅速发展以及塑胶制品在航空、航太、电子、机械、船舶和汽车等工业部门的推广应用,产品对模具的要求越来越高,传统的塑胶模具设计方法已无法适应产品更新换代和提高质量的要求[2]。
电脑辅助工程(CAE)技术已成为塑胶产品开发、模具设计及产品加工中这些薄弱环节的最有效的途经。
1943年,位于葡马立尼亚.格兰特市(marinhagrande)一家小型玻璃模具厂股东阿尼巴尔(aníbalh.abrantes)萌发了生产注塑模具的构想。
由于未能获得其他股东的支持,阿尼巴尔不得不出售自己拥有的公司股份以筹集资金,并开始专注于注塑模具的研发和制造。
2年后,他成功地制造了第一只注塑模具。
此后,在马立尼亚.格兰特市和奥利维拉.德.阿泽麦伊斯市(oliveiradeazeméis)(葡萄牙另一传统玻璃工业区)逐步出现其它注塑模具企业[3]。
所谓注塑成型(Injection Molding)是指,受热融化的材料由高压射入模腔,经冷却固化后,得到成形品的方法。
风扇后盖注塑模具设计说明书-毕业设计

1 前言我国的塑料工业近几十年来得到了迅猛发展,尤其是二十多年的改革开放,塑料工业取得了举世瞩目的成就。
随着塑料工业的飞速发展和通用塑料与工程塑料在强度和精度等方面的不断提高,塑料制品已广泛用于电子电器、医疗器材、包装材料、农业、家用电器、仪器仪表、建筑器材、汽车工业、日用五金等众多领域,塑料制品所占的比例正迅猛增加。
目前,塑料工业已形成设计、生产、检测、标准以及教学等一套完整的工业体系。
由于在工业产品中,一个设计合理的塑件往往能代替多个传统金属结构件,加上利用工程材料特有的性质,可以一次成型非常复杂的形状,并且还能设计成卡装结构,成倍地减少整个产品中的各种紧固件,大大地降低金属材料消耗量和加工及装配工时,所以,今年来工业产品塑料化的趋势不断上升。
因此,国内外专家极为关注。
我国塑料工业的高速发展对模具工业提出了越来越高的要求,塑料模具在整个模具行业中所占比例已经相当高,在未来几年中还将保持较高速度发展。
国内塑料模具市场以注塑模具需求量最大,其中发展重点为工程塑料模具。
注塑模具制造的特点a.型腔及型芯呈立体型面。
塑件的外部和内部形状是由型腔和型芯直接成型的,这些复杂的立体型面加工难度比较大,特别是型腔的盲孔型内成型表面加工,如果采用传统的加工方法,不仅要求工人技术水平高、辅助工夹具多、刀具多,而且加工的周期长。
b.精度和表面质量要求高,使用寿命要求长。
目前一般塑件的尺寸精度要求为IT6~7,表面粗糙度Ra0.2~0.1μm,相应的注塑模具零件的尺寸精度要求达到IT5~6,表面粗糙度Ra0.1μm以下。
长寿命注塑模具对于提高高效率和降低成本是很必要的,目前注塑模具的使用寿命一般要求100万次以上。
精密注塑模要用刚度大的模架,增加模板的厚度,增加支承柱或锥形定位元件以防止模具受压力后产生变形,有时内压可以达到100MPa。
顶出装置是影响制品变形和尺寸精度的重要因素,因此应该选择最佳的顶出点,以使各处脱模均匀。
28 电风扇旋扭的塑料模具设计

导向机构是保证动模或上下模合模时,正确定位和导向的零件。本副模具是采用 导柱、导套导向。导向机构它起到的作用有:定位作用、导向作用、承载作用、保持 运动平稳的作用。
导柱导向通常是由导柱和导套的间隙配合而组成的。 导柱分带头导柱和有肩导柱。因为该产品是成批量的生产,导柱经常运动,容易 磨损,所以采用导套,这样导套坏了,可以随时更换。小型模具采用带头导柱。 导柱的技术要求包括:导柱的长度、形状、材料、数量及布置。此副模具把导柱 设在动模一侧,这样有利于推杆的运动。导柱固定端与模板之间采用 H7/m6,而导柱 与导套采用 H7/f7 的间隙配合。导套也分直导套和芾头导套。其用法与导柱的用法一 样。导套的技术要求的技术要求包括:导套的形状、导套的材料、及固定形式及配合 精度。导套采用 H7/r6 配合镶入模板。 导柱结构和尺寸如下图所示:
直径 d=φ(L2Q/nE)1/4 =1.5(1202105/4x2.2x105)<10
取直径为 10mm,已经足够了。 进行强度校核:
取导柱的长度为 100mm,导柱的材料选 T8A,淬火处理到 55~60HRC,导柱的前端做成锥 台形,这样是为了导柱顺利进入导套,导柱固定端粗糙度 Ra 为 0.8,导向部分 Ra 为 0.4 该导柱的布置采用等直径导柱对称分布,但是为了在合模时要注意。
导套采用直导套,这样简单易制作,而且也适用。其结构和形状如图所示:
设计要求: 根据工件的实际形状与尺寸,设计一副注塑模把它生产出来,要求它的外表面比
较光滑即表面粗糙度要求高。
通过对塑件外部造型、工艺结构的设计、对塑件进行计算仿真和生产验证,也通 过对分模线、塑件的壁厚、圆角、塑件的尺寸精度、脱模斜度进行了综合的考虑,工
风扇叶片注塑模具设计毕业论文

风扇叶片注塑模具设计1. 引言随着人们生活水平的提高和环境意识的增强,风扇作为主要的空调设备之一,被广泛应用于家庭、办公室和工业领域。
风扇的性能和效果主要取决于风扇叶片的设计和制造质量。
本文将重点研究风扇叶片注塑模具的设计,以提高风扇叶片生产过程的效率和质量。
2. 风扇叶片注塑模具的作用风扇叶片注塑模具是风扇叶片生产的关键设备,它决定了风扇叶片的形状、尺寸和材料质量。
风扇叶片注塑模具的设计和制造质量直接影响到最终产品的性能和质量。
因此,合理设计和优化风扇叶片注塑模具对提高风扇叶片生产效率和产品质量至关重要。
3. 风扇叶片注塑模具设计的基本原理3.1. 风扇叶片注塑模具的结构风扇叶片注塑模具主要包括模具底板、模具芯、模具腔、导向机构和注塑系统。
其中,模具底板用于固定模具的整体结构,模具芯和模具腔则用于成型风扇叶片的内部和外部形状。
导向机构用于保证模具芯和模具腔之间的位置和运动精度,注塑系统则用于向模具中注入熔融塑料。
3.2. 风扇叶片注塑模具的工艺参数风扇叶片注塑模具的工艺参数主要包括注塑温度、注塑压力、注塑速度和冷却时间等。
这些参数的选择和控制对于保证风扇叶片的尺寸精度、表面质量和物理性能非常重要。
3.3. 风扇叶片注塑模具的设计要点风扇叶片注塑模具的设计要点包括模具结构的合理性、模具材料的选择、模具加工工艺的确定、模具的组装和调试等。
其中,模具结构的合理性是设计的关键,它要求模具尺寸的精准度、模具的开合速度和行程、模具的冷却系统和模具的排气系统等都要能够满足风扇叶片生产的要求。
4. 风扇叶片注塑模具设计的优化方法4.1. 模具流动分析模具流动分析是风扇叶片注塑模具设计优化的重要方法之一。
通过数值模拟软件对模具流动状态进行分析,可以得到模具填充过程中的温度、压力分布等关键参数,从而优化模具结构和工艺参数。
4.2. 模具材料的选择模具材料的选择在风扇叶片注塑模具设计中起到至关重要的作用。
优质的模具材料应具备高强度、高硬度、良好的耐磨性和耐腐蚀性,以保证模具的使用寿命和加工质量。
- 1、下载文档前请自行甄别文档内容的完整性,平台不提供额外的编辑、内容补充、找答案等附加服务。
- 2、"仅部分预览"的文档,不可在线预览部分如存在完整性等问题,可反馈申请退款(可完整预览的文档不适用该条件!)。
- 3、如文档侵犯您的权益,请联系客服反馈,我们会尽快为您处理(人工客服工作时间:9:00-18:30)。
毕业设计(论文)课题名称电风扇旋扭的塑料模具设计学生姓名学号院(系),专业指导教师年月日目录前言 (3)第1章设计任务书 (4)第2章塑件的工艺分析 (5)第3章注塑模的设计要点 (6)第4章注塑模的设计 (7)第4.1节成型零件的设计 (7)第4.2节合模导向机构的设计 (10)第4.3节推出机构的设计 (12)第4.4节浇注系统与排溢系统的设计 (15)第4.5节分型面的设计 (19)第4.6节温度调节系统的设计 (20)第4.7节模架的设计 (21)第4.8节注射模与注射机的关系 (22)第5章设计总结 (25)致谢 (26)参考文献 (27)前言近年来,由于模具技术的迅速发展。
模具设计与制造已成为一个行业越来越引起人们的关注。
成为生产各种工业产品不可缺少的工艺装备。
作为二十一世纪的大学生,综合方面的素质越来越显得重要,特别要从事模具专业,毕业设计是培养综合运用所学理论知识和技能解决实际问题的一个重要环节,这是对我们大学阶段智力的一次总检验。
更是我们受到集中培养和综合设计能力,科研能力,创新能力的一次难得的机会。
毕业设计的主要目的有两个:一,让学生撑握查阅资料与手册的能力,能够熟练运用C A D进行模具设计;二,掌握模具设计方法和步骤,了解模具的工艺过程。
此次本人设计的课题是:注塑模的设计。
此注塑件是电风扇开关旋纽,体积小,形状复杂,在设计过程中,本人通过了参考实际产品,了解塑件的特点。
在设计过程中查了很多资料。
在设计过程中得到了何晓明等老师的精心指导和广大同学的帮助,在此表示感谢。
第1章设计任务书此次毕业设计是电风扇旋扭,它所要达到的要求:要能耐高温,绝缘性要好,耐气候性强,刚性,韧性佳,通过对产品的各种性能分析,选用材料为ABS,该塑件的厚度为1mm,公差等级为IT5级。
它是用来调节风速和定时的,能够满足人们的热天对风力和吹风长短要求,同时也起到美观的作用。
设计要求:根据工件的实际形状与尺寸,设计一副注塑模把它生产出来,要求它的外表面比较光滑即表面粗糙度要求高。
通过对塑件外部造型、工艺结构的设计、对塑件进行计算仿真和生产验证,也通过对分模线、塑件的壁厚、圆角、塑件的尺寸精度、脱模斜度进行了综合的考虑,工件的尺寸和形状如下图:第2章塑件的工艺分析ABS塑料是由丙烯、丁二烯、苯乙共聚而成。
ABS具有良好的综合力学性能,ABS成型塑件时有较好的光泽。
其密度为1.02~1.05g/cm3 . ABS还有很好的冲击强度。
ABS在升温时粘度增高。
所以成型时压力增高。
塑件的脱模角度宜稍大。
ABS还易吸水,所以为了得到较好的塑件,在加工之前,还必须把它进行干燥处600 C左右,热水器的盖要求它的理。
要求塑件精度较高时,可以控制模温在50~800C左右。
外表面光泽,应控制模温在60~0.8%,塑料的收缩率对塑件的质量和形状是一个很ABS塑料的收缩率为0.3%~重要的参数。
取其制品精度IT5级,要得到良好的塑件,不但要控制好塑料的收缩率,而且还要对模具质量也很重要,一副较好的模具,模具加工容易,寿命较高,而且对产品的质量得到很好的保证。
该工件是属于薄壁塑件,且过渡角也不是很大,所以模具的型腔和型芯加工是比较难的。
此塑件算是小型塑件,所以模架也不算大,并且精度也不是要求特别的高,所以采用一模多腔,这样对提高生产效率是很有利的。
第3章注塑模的设计要点ABS塑料它是属于热塑性塑料,该产品是通过注塑成型的。
它的原理是将颗粒或粉状塑料从注塑机的料中送进加热器中,经加热熔化,在受压的情况下,把它注到成型的型腔中,再冷却成型。
注塑成型它的周期短,能成型复杂的、尺寸精确的制件。
它的成型工艺过程包括如下:成型前的准备,注塑过程,塑件后处理。
由于ABS料它是属于易湿的塑料,所以在加工前要把它进行充分的干燥。
注塑过程它是一个比较关键的进程,各个步骤都要控制好,这对塑件的质量和形状起着至关重要的作用。
注塑成型的核心问题是:就是采用措施得到良好的塑料熔体,并把它注塑到型腔中去,在控温下,使塑件达到所求的质量。
温度、注塑压力、时间是其关键的工艺参数。
注塑模按结构分为单分型、双分型和多分型面,此塑件是采用侧浇口工件较简单,因此采用单分型面的模具,又因为该工件属于薄壁塑件,当采用推杆,会把塑件容易顶坏。
所以该工件采用推件板推出,容易保证塑件的质量。
注塑模包括:成型零部件、合模导向机构、浇注系统、侧向分型与抽芯机构、推出机构、加热和冷却系统、排气系统、支承零部件。
只有处理好各个环节的制约关系,才能设计出一副较好的模具出来,一副模具设计出来,把它装在注塑机上,还要通过校核,才能投入生产。
因此注塑模与注塑机的关系也是至关重要。
第4章注塑模的设计第4.1节成型零件的设计成型零件是决定塑件的几何尺寸和形状的关键。
成型零件它直接与高温、高压的塑料流接触,因此成型零件要求具有较高的强度、刚度和耐磨性能。
成型零部件,它包括:型腔、型芯、成型杆、和成型环等。
该产品是IT5级精度制造的,产品外表面要求比较光滑,因此要求成型零件的抛光性能要好,表面应该光滑美观。
表面粗糙度要求Ra0.4以下。
型腔的材料选45钢。
淬火处理,使其达到硬度40HRC以上。
(1) 型腔的结构设计:由于该塑件结构比较简单,但要求其精度也要较高,要求其塑件不充许产生拼接线痕迹,经过仔细的参考,该型腔采用整体式较为合理。
其结构和尺寸如下图所示:查阅资料可得塑件的理想的外壁圆角半径为塑件的壁厚的1.5倍。
即R=1.5Xt,即R=1.5mm,该型腔的加工,先下料一块为400X400X50mm的45钢,然后在磨床上进行磨削,使其达到应有的光洁度,然后热处理,使其达到硬度达到40HRC 以上。
成型的型腔可以在电火花机上加工得到所要的尺寸和精度,最后通过精磨和抛光,得到所要的型腔。
(2)型腔的工作尺寸计算:所谓工作尺寸就是指成型零件上直接用以成形塑件部位的尺寸。
它主要包括型腔的径向尺寸、型腔的深度、中心距等尺寸。
它受到塑件的尺寸精度的影响。
型腔的计算公式如下:型腔的径向尺寸计算 (LM )δz=[(1+Scp)Ls-3/4△]δz=[(1+0.55/100)x52-3/4x0.013]δz=[52.286-0.00975]δz=[52.2765]δz。
(L)0δz=[(1+Scp)Ls-3/4△]δz=[(1+0.55/100)x15-0.75x0.008]δz=[15.0765]δz其中LM 是型腔的径向尺寸,Scp是塑料的平均收缩率,△是塑件的公差值。
查表得ABS塑料的最小收缩率为0.3%,最大的收缩率为0.8%,由公式得S cp =(0.3%+0.8%)/2得Scp为0.55,至于塑件的精度,在此到△的系数为0.75,当塑件的精度不同时会有变化。
型腔的深度尺寸计算:(HM )δz=[(1+Scp)Hs-2/3△]δz=[(1+0.55/100)x26-0.009x2/3]δz=[26.143-0.006]δz= [26.136]δz其中HM为型腔的深度尺寸,△的系数取2/3。
塑件的字体是通过在型腔上做相反的字,它的深度为0.3mm,它是通过金雕工艺,把它雕到上的,因此在这里不详细说明是怎么样生产出来的。
(3)型芯的结构设计:型芯是成型塑件的内表面的的零件。
此塑件它有两个小孔,它是用小型芯来成型,主型是用来成型塑件的内壁,塑件的内表面精度要求要稍微低一些,因此型芯的加工可以稍稍粗糙点。
该芯采用整体式,它结构牢固,它固定在动模固定板上。
其形状和尺寸如下图:所示:其工件角度都是通过核算而得到的。
型芯选45钢,淬火处理,使其硬度达到40HRC 以上,以保证其硬度,不使它在加工时,变弯、变软。
它的加工过程是,先取一段φ60x40的一块圆棒料,开始在车床上车削,然后进行热处理,再进行电火花加工,使其达到所要求的形状和尺寸,最后进行磨和抛光。
型芯的尺寸计算:型芯的径向尺寸:(L M)-δz0=[(1+Scp)Ls+3/4△]-δz0=[(1+0.55)x50+0.75x0.011]-δz=[50.2835]-δz(LM )-δz0=[(1+Scp)Ls+3/4△]-δz=[(1+0.55/100)x13+0.75x0.008)]-δz=[13.0775]-δz0其上面字母所表示的意义和型芯的字母是一样的。
型芯的高度尺寸计算如下:(HM )=[(1+Scp)Hs+2/3△]-δz=[(1+0.55/100)25+2/3x0.006]-δz=[25.1425]-δz塑件中心距的尺寸计算:(LM )-δz0=(1+Scp)Ls±δ/2=(1+0.55/100)x26±δ/2塑件理想的内角圆半径应为塑件壁厚的1/3以上。
所以取内角圆半径为0.5mm.型腔由于受到熔体的高压作用,应具有足够的强度和刚度。
如果型腔侧壁和厚度过下,则会引起溢料和出现飞边,这样就降低了塑件的精度,严重时还会影响脱模。
因此还要计算侧壁和底板的厚度。
模具型腔的壁厚的计算,应以最大的压力为准。
此塑件是属于小尺寸塑件,强度计算。
这个零件可以近似看作圆形件。
型腔侧壁的计算如下:S=r{{([σ]/([σ]-2P))}1/2}S是侧壁厚度。
P是型腔压力,[σ]模具材料的许用应力。
r型腔半径。
经算得,图中型腔的壁厚已经足够。
型腔的厚度计算公式如下:h=1.1rx(p/[σ])1/2其中:h型腔的高度,r型腔的半径。
经算得15mm已经满足要求了。
型腔动模支承板的厚度的计算。
因为该型腔是采用整体式型腔,动模垫块厚度的选择显得较为自由。
S=3.14xR2=3.14x26x26=21.22cm225mm.本副模具选厚度为25mm.由教材上的书161页的表5-18查得垫块为20~第4.2节合模导向机构的设计导向机构是保证动模或上下模合模时,正确定位和导向的零件。
本副模具是采用导柱、导套导向。
导向机构它起到的作用有:定位作用、导向作用、承载作用、保持运动平稳的作用。
导柱导向通常是由导柱和导套的间隙配合而组成的。
导柱分带头导柱和有肩导柱。
因为该产品是成批量的生产,导柱经常运动,容易磨损,所以采用导套,这样导套坏了,可以随时更换。
小型模具采用带头导柱。
导柱的技术要求包括:导柱的长度、形状、材料、数量及布置。
此副模具把导柱设在动模一侧,这样有利于推杆的运动。
导柱固定端与模板之间采用H7/m6,而导柱与导套采用H7/f7的间隙配合。
导套也分直导套和芾头导套。
其用法与导柱的用法一样。
导套的技术要求的技术要求包括:导套的形状、导套的材料、及固定形式及配合精度。
导套采用H7/r6配合镶入模板。
导柱结构和尺寸如下图所示:取导柱的长度为100mm,导柱的材料选T8A,淬火处理到5560HRC,导柱的前端做成~锥台形,这样是为了导柱顺利进入导套,导柱固定端粗糙度Ra为0.8,导向部分Ra为0.4该导柱的布置采用等直径导柱对称分布,但是为了在合模时要注意。