标准工时精益生产(韩国三星版中文)
精益生产关键词中英文对照表

精益生产关键词中英文对照表1、标准化ATT actual take time,实际单件工时。
BPP best people practices,最佳人员准则。
E.T. element time ,基本动作周期。
IOM inspection operator method,操作视察方法。
IOS inspection operator summary,操作视察要领。
JES job element sheet,工作要素单。
Kaizen改善。
NVA non-value-added,非增值。
OC operation certification,操作认可。
PPE个人防护用具。
QFD quality function deployment,质量功能展开。
SIP standardised inspection process,标准化视察程序。
SOS standardized operation sheets,标准化操作单。
Std standardiszation,标准化。
TT takt time,单件工时。
WBS工作分解表。
2、制造质量andon暗灯。
APQP advanced production quality plan,产品质量前期策划。
audit基于抽样来确定供方文件化的质量体系实施有效性的现场验证活动。
BIQ built in quality,制造质量。
CT cycle time,周期时间。
DFMEA design failure mode and effects analysis,设计失效模式和后果分析。
FMEA failure mode and effects analysis,失效模式和后果分析。
FMS flexible manufacturing systems,柔性制造系统。
FPS fixed position stop,定点停。
FTA fault tree analysis,故障树分析。
FTQ first time quality,下线合格率。
精益生产-标准作业

5
合计 14
主任
工长
工 序 能 力表
件 号
型 式
部 门
姓 名
名 称
个 数
工序能力表
年 月 日
案例链接:工序能力表填写例
LOGO
定义:确定作业分配和作业顺序的工具包括生产节拍、作业顺序、作业内容、作业时间等内容,主要用于反映人工操作和设备作业结合的关系。 另外,填入设备自动加工时间,一起考查人和设备的组合是否可能。 制定时的注意事项 - T/T(节拍时间) - C/T(循环时间)
■
■
决定标准手持的基本规则 ①从作业顺序来考虑 ②从有无设备自动加工来考虑
LOGO
案例链接:标准在制品的设置案例
成品
材料
标准手持
⑤
④
③
②
①
⑥
⑦
1工序
1工序
2工序
2工序
3工序
(A)
(B)
(A)
(B)
顺方向作业 0个 逆方向作业 1个
实现与准时生产有关的各工序间的同步化
把在制品的持有量限定在必要的最小数量
LOGO
内容
标准作业概述
1
标准作业的制定
2
标准作业改善
3
标准作业再分配
4
标准作业执行与完善
5
LOGO
海量PPT模板免费下载
标准作业的制定
在最初没有标准作业的情况下,首先要参照原有的方式把作业固定下来,使作业者能够进行反复的循环作业,然后再按照上述步骤进行。
LOGO
案例链接:作业要领书填写例
LOGO
六、山积表
①从作业顺序来考虑 (工序的流程)
②从有无设备自动加工来考虑
精益生产术语 (2)

精益生产术语为了便于读者进一步学习精益生产,并作为实践的指南,特选用与精益生产有关的术语66条,并加又以解释。
1.精益生产(Lean Production)含义:精益生产起源于日本的丰田生产方式,美国学者对这种生产方式在理论上加以概括与总结,命名为“Lean production”,中文翻译为“精益生产”。
“Lean”的意思是没有脂肪。
这种生产哲学将库存比喻为人体的脂肪,认为动作良好的企业应该是没有库存的,因此命名为2.附加价值(Value Added)含义:附加价值是企业本身创造出的价值。
附加价值愈高则获利能力愈强。
附加价值=销售额—(材料费+委外加工费+折旧费+工资)。
附加价值率的计算方式为:(附加价值/营业收入)×100%%。
比率越高则贡献越大,显示获力愈强,精益企业应达到30%以上。
3.7种浪费含义:精益生产方式将所有浪费归纳成七种——(1)等待的浪费;(2)搬运的浪费;(3)不良品的浪费;(4)动作的浪费;(5)加工的浪费;(6)库存的浪费;(7)制造过多(早)的浪费。
4.价值流图(Value Stream Mapping)含义:所谓价值流,指一个产品/服务在流程中所必须要经过的一组特定活动(包括增值活动和非增值活动),识别价值流,是在这组特定活动中识别浪费和寻找改善机会。
识别价值流的常用工具,就是价值流图。
价值流图把产品或者服务所涉及的所有物流与信息流相关内容用目视图表的方式绘制出来,作为随后即将展开的精益改造的依据。
5.丰田生产方式(Toyota Production System)含义:一般认为,丰田生产方式的支柱有两个,一是“自动化”,二是“及时生产”。
根据大野耐一的描述,丰田生产方式的现场管理,有两个特点,一是流水化制造,二是拉动式计划方法,也就是看板方式。
丰田过去是将车床、铣床分车间集中在一起,后来则改善为依照生产流程将车床、铣床、钻床一台一台流水化排列布置。
生产的产品则按照生产流程顺序流动。
精益生产 标准作业
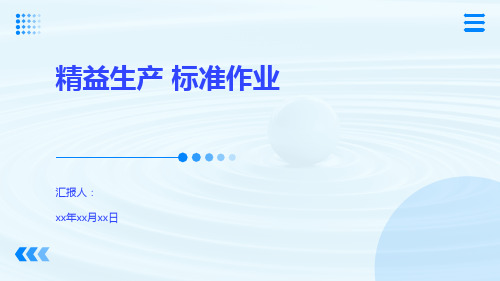
精益生产注重发挥人的作用, 鼓励员工参与和持续改进,以 实现企业长期效益的最大化。
精益生产的发展历程
精益生产的起源可以追溯到20世纪50年代,当时日本汽车制造商开始研究消除浪费、提 高生产效率的方法。
1985年,詹姆斯·P·沃麦克(James P. Womack)和丹尼尔·T·琼斯(Daniel T. Jones)发 表了《精益思想》(Lean Thinking)一书,将精益生产总结为五项基本原则。
03
实施效果
通过标准化作业的实施,该企业的生 产效率和质量水平得到了显著提升, 员工的工作效率和操作规范性也得到 了提高,减少了操作失误和质量问题 的发生。
06
前瞻性思考
精益生产标准作业未来的发展趋势
精益生产标准作业的普及和应用 范围将进一步扩大。
技术和智能化将推动精益生产标 准作业的进一步发展。
这些原则被广泛接受和应用,精益生产逐渐成为一种全球性的管理趋势。
精益生产的意义
1
精益生产是一种先进的管理模式,有助于提高 企业生产效率和质量,降低成本和库存,提高 客户满意度。
2
精益生产可以帮助企业实现可持续发展,提高 企业竞争力,实现长期盈利。
3
精益生产可以促进企业创新和改进,不断追求 卓越,保持竞争优势。
背景介绍
要点二
实施过程
该企业为了持续改进生产效率和质量 ,建立了精益生产标准作业制度,并 明确了各个岗位的职责和要求。
在实施过程中,该企业采用了PDCA 循环和5W1H分析法等工具,针对生 产现场的各个环节进行了持续改进, 并定期对员工进行培训和考核。
要点三
实施效果
通过持续改进,该企业的生产效率和 质量水平得到了持续提升,产品交货 期缩短了10%,客户满意度提高了 15%,员工的工作积极性和主动性也 得到了提高。
三星精益生产(lean_)

PRO-GB Training
-.资材效率结构图
效率
结构图
LOSS种类
材料效率
材 料 工程效率 综 合 效 率 设计效率
投入数量
作业数量
材料
LOSS
由制造现场的失败、失误 发生的LOSS (资材 Handling时作业失误)
日 报 上 记
良品数量
工程
LOSS
不良LOSS
录 管 理
标准量
设计
LOSS
非效率性 附加值动
作
属浪 动 作
费
· 等待作业 · 聊天 · 闲逛(流动)
※人 · 寻找 · 搬运 · 移动 ·SW on/off 操作
※ 设备 · 感应(加工) · Loading(装载) ·Un Loading
“ SDI Six Sigma = 成長 Engine ”
IE -8
PRO-GB Training
安排,标准作业
LAY OUT,载积方法
Claim,再作业,品位低下,信用低下(检查员) 前后工程UNBALANCE,资材品质(人\设备\材料) 引发PROCESS浪费的主体是人, 要因是他性,老婆心,平安事,理致主义,权威意识
IE -10
生产性
PRO-GB Training
“ SDI Six Sigma = 成長 Engine ”
IE -18
PRO-GB Training
◇ 制造能力分析图
▶Tact Time: 实动时间(工作时间)/生产要求量 Cycle Time : 反复性工程中,完成1次单位作业所需的时间
Tact time
稼动
LOSS
Neck time
遗失的能力 (失去的能力)
精益生产-标准工时的设定方法

保证生产质量
统一工作标准
标准工时可以作为员工工作的统一标准,确保每个员工按 照相同的标准进行操作,提高产品质量的稳定性。
01
发现并改进问题
通过设定标准工时,企业可以发现生产 过程中的瓶颈和问题,进而改进工艺、 提高产品质量。
02
03
提高员工技能水平
标准工时要求员工具备相应的技能水 平,促使员工不断学习和提高自身技 能。
直接时间研究
总结词
直接时间研究是一种通过实地观察和测量,直接获取作业时间的方法。
详细描述
直接时间研究需要观察员对作业过程进行实地观察,记录每个作业步骤的时间消 耗,包括正常时间、宽放时间等,并考虑作业的准备和结束时间。这种方法能够 提供较为准确的标准工时数据,但需要耗费大量时间和人力。
预定时间标准法
将调整后的标准工时反馈给 员工,并进行培训和指导, 确保员工能够按照新的标准 工时进行操作,同时持续关 注生产过程中的问题和改进 点,不断优化和改进标准工 时。
06
标准工时设定方法的案例 分析
案例一:某汽车制造企业的标准工时设定
总结词
科学分析与实践结合
VS
详细描述
该汽车制造企业采用时间研究方法,结合 生产现场实际情况,对每个作业岗位的工 作流程进行详细分析,通过观测、记录和 计算,确定标准工时。同时,引入作业改 善建议机制,鼓励员工提出改进意见,持 续优化标准工时。
精益生产的核心思想
01
02
03
04
价值导向
关注客户价值,以客户需求来 确定产品的价值,并以此为基
础进行生产和改进。
流动与平衡
通过优化流程,实现生产过程 中的物流平衡和顺畅,减少等
待和搬运浪费。
精益生产术语中英文版
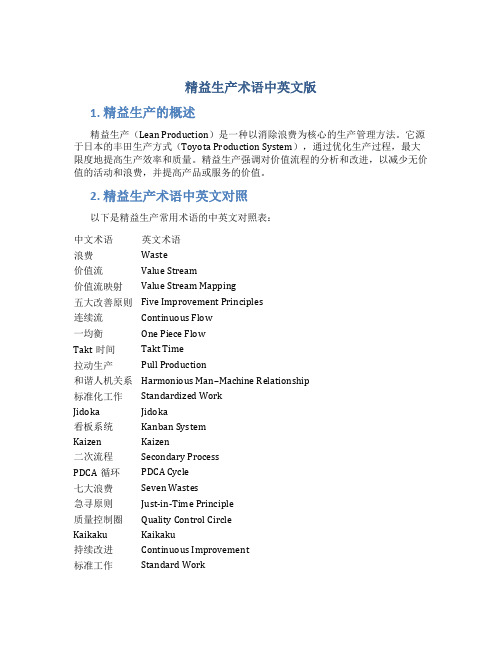
精益生产术语中英文版1. 精益生产的概述精益生产(Lean Production)是一种以消除浪费为核心的生产管理方法。
它源于日本的丰田生产方式(Toyota Production System),通过优化生产过程,最大限度地提高生产效率和质量。
精益生产强调对价值流程的分析和改进,以减少无价值的活动和浪费,并提高产品或服务的价值。
2. 精益生产术语中英文对照以下是精益生产常用术语的中英文对照表:中文术语英文术语浪费Waste价值流Value Stream价值流映射Value Stream Mapping五大改善原则Five Improvement Principles连续流Continuous Flow一均衡One Piece FlowTakt时间Takt Time拉动生产Pull Production和谐人机关系Harmonious Man–Machine Relationship标准化工作Standardized WorkJidoka Jidoka看板系统Kanban SystemKaizen Kaizen二次流程Secondary ProcessPDCA循环PDCA Cycle七大浪费Seven Wastes急寻原则Just-in-Time Principle质量控制圈Quality Control CircleKaikaku Kaikaku持续改进Continuous Improvement标准工作Standard Work3. 精益生产术语解释3.1 浪费(Waste)在精益生产中,浪费指的是任何不增加价值但增加成本和时间的活动。
这些活动是没有必要的,可以被消除或减少。
根据精益生产的理念,浪费被分为七类,即运输、库存、运动、等待、超生产、缺陷和过度加工。
3.2 价值流(Value Stream)价值流是指从原材料到最终产品或服务交付前的所有步骤和活动。
通过分析价值流,可以发现哪些步骤是无价值的或无必要的,并进行优化,以提高整体效率和质量。
精益生产知识工时节拍
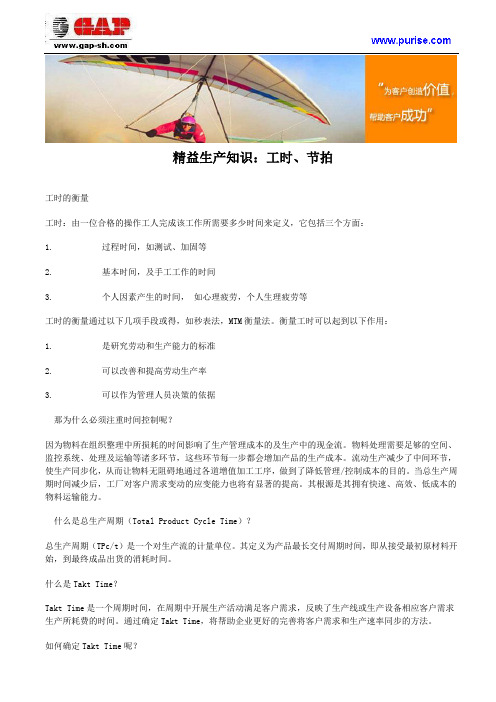
精益生产知识:工时、节拍工时的衡量工时:由一位合格的操作工人完成该工作所需要多少时间来定义,它包括三个方面:1. 过程时间,如测试、加固等2. 基本时间,及手工工作的时间3. 个人因素产生的时间,如心理疲劳,个人生理疲劳等工时的衡量通过以下几项手段或得,如秒表法,MTM衡量法。
衡量工时可以起到以下作用:1. 是研究劳动和生产能力的标准2. 可以改善和提高劳动生产率3. 可以作为管理人员决策的依据那为什么必须注重时间控制呢?因为物料在组织整理中所损耗的时间影响了生产管理成本的及生产中的现金流。
物料处理需要足够的空间、监控系统、处理及运输等诸多环节,这些环节每一步都会增加产品的生产成本。
流动生产减少了中间环节,使生产同步化,从而让物料无阻碍地通过各道增值加工工序,做到了降低管理/控制成本的目的。
当总生产周期时间减少后,工厂对客户需求变动的应变能力也将有显著的提高。
其根源是其拥有快速、高效、低成本的物料运输能力。
什么是总生产周期(Total Product Cycle Time)?总生产周期(TPc/t)是一个对生产流的计量单位。
其定义为产品最长交付周期时间,即从接受最初原材料开始,到最终成品出货的消耗时间。
什么是Takt Time?Takt Time是一个周期时间,在周期中开展生产活动满足客户需求,反映了生产线或生产设备相应客户需求生产所耗费的时间。
通过确定Takt Time,将帮助企业更好的完善将客户需求和生产速率同步的方法。
如何确定Takt Time呢?1. 确定满足客户总需求所涉及到的工艺流程。
仔细认证准确的需求信息,同时考虑批量的增减情况。
如在同一设备上生产进行多样化生产,则这种复合需求也应计算在Takt Time之内。
生产能力计划需于需求量的层次相适应,将生产层次于设备设计产能挂钩。
产能水平以精细产能率(Lean Capacity Rate),最大产能(Max Capacity)和弹性产能率(Flex Capacity Rate)表示。
(精益生产)精益生产方式简介(中英文翻译)
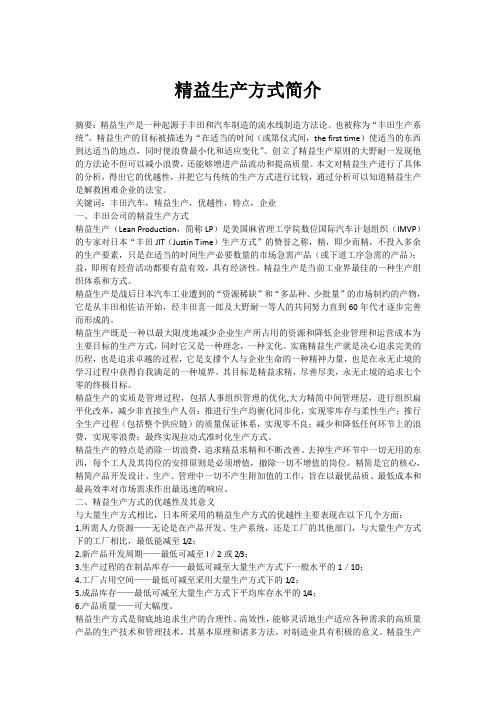
精益生产方式简介摘要:精益生产是一种起源于丰田和汽车制造的流水线制造方法论。
也被称为“丰田生产系统”。
精益生产的目标被描述为“在适当的时间(或第仪式间,the first time)使适当的东西到达适当的地点,同时使浪费最小化和适应变化”。
创立了精益生产原则的大野耐一发现他的方法论不但可以减小浪费,还能够增进产品流动和提高质量。
本文对精益生产进行了具体的分析,得出它的优越性,并把它与传统的生产方式进行比较,通过分析可以知道精益生产是解救困难企业的法宝。
关键词:丰田汽车,精益生产,优越性,特点,企业一、丰田公司的精益生产方式精益生产(Lean Production,简称LP)是美国麻省理工学院数位国际汽车计划组织(IMVP)的专家对日本“丰田JIT(Justin Time)生产方式”的赞誉之称,精,即少而精,不投入多余的生产要素,只是在适当的时间生产必要数量的市场急需产品(或下道工序急需的产品);益,即所有经营活动都要有益有效,具有经济性。
精益生产是当前工业界最佳的一种生产组织体系和方式。
精益生产是战后日本汽车工业遭到的“资源稀缺”和“多品种、少批量”的市场制约的产物,它是从丰田相佐诘开始,经丰田喜一郎及大野耐一等人的共同努力直到60年代才逐步完善而形成的。
精益生产既是一种以最大限度地减少企业生产所占用的资源和降低企业管理和运营成本为主要目标的生产方式,同时它又是一种理念,一种文化。
实施精益生产就是决心追求完美的历程,也是追求卓越的过程,它是支撑个人与企业生命的一种精神力量,也是在永无止境的学习过程中获得自我满足的一种境界。
其目标是精益求精,尽善尽美,永无止境的追求七个零的终极目标。
精益生产的实质是管理过程,包括人事组织管理的优化,大力精简中间管理层,进行组织扁平化改革,减少非直接生产人员;推进行生产均衡化同步化,实现零库存与柔性生产;推行全生产过程(包括整个供应链)的质量保证体系,实现零不良;减少和降低任何环节上的浪费,实现零浪费;最终实现拉动式准时化生产方式。
精益生产-LineBalanceModels中英文版

控制过程变革和控制制定控制计划计算最终财务过程指标项目过渡给未来项目管理者项目鉴 别转化机会
测量
定义
项目编号工具项目定义表净现值分析内部回报率分析折算现金流分析 ?(按现值计算的现金流量分析)PIP管理过程RACIQuad 表
过程图价值分析脑力风暴投票归类法柏拉图因果图/鱼骨图FMEA查检表运行图控制图量具 R&R
Line Balance Model
学习目标
如何设计和实施由“线平衡模型”支持的一个流程以确保优化配置:人 地方固定资产材料知道如何使生产率最大化
Line Balance Model
What’s in It for Me?
Able to design and implement a balanced process lineUnderstand the issues in a typical process environment and how to impact those issues
Revised 1-12-02
Line Balance Model
精益6
过程改善流程
分析
控制
改进
定义选定题目列出客户从顾客之声中列出关建需求定出项目焦点和重要指标完成 PDF
测量绘制业务流程图绘制价值流程图制定数据收集计划测量系统分析收集数据过程能力分析
分析提出关键因子区分关键因子验证关键因子评枯每个关键因子对结果的影响量化机会根本原因排序寻找根本原因针对关键因子
Process MappingValue AnalysisBrainstormingMulti-Voting TechniquesPareto ChartsC&E/Fishbone DiagramsFMEACheck SheetsRun ChartsControl ChartsGage R&R
标准工时精益生产(韩国三星版中文)

○
○
M 动作分析
Line 便性 ORDLIX SHA,SLP 5S
I
E
E
TPM 直接观测,Rating
W PTS(MODAPTS)
M Work sampling PAC V E Q C 技能分析 7种 道具
4
IE 分析技法
产品(PRODUCT)
技能(FUNCTION)
工程(PROCESS)
单位作业(OPERATION) 作业要素(ELEMENT) 动作(MOTION)
MTM (Method Time Measurement)
分解为作业上需要 的基本动作 赋予对应 性质和条件的时间值
MTM1:1948年 MTM2:1965年 MTM3:1971年
Rule : 简单 分析 : 稍微 困难
1 TMU(Time Measurement Normal Pace 充分并
Unit)
17
MODAPTS发 动作记号解说
区分 编号 1 移 动 距 离 2 3 4 5 6 7 8 结 尾 动 作 9 10 11 12 13 14 动作 手指 手 下胳膊 上胳膊 肩膀 握 握 握 握 握 放 放 放 放 记号 M1 M2 M3 M4 M5 G0 G1 G2 G3 G 11 P0 P2 P3 P5 MOD 1 2 3 4 5 0 1 2 3 11 0 2 3 5 使用手指动作 从手腕开始使用手面和手指 使用 下胳膊和手面,手指 使用上胳膊和下胳膊,手面,手指 伸开的胳膊和肩膀受刺激时 简单的碰东西的动作 抓的单纯状态的动作 利用轴拾起的动作 用 眼睛和注意力 及2 回以上动作夹的时候 利用手指末端关节的动作 (高度注意) 放下不必要的注意力 通过手的 1回以上的修正 放下物品的动作 (注意) (注意) (注意) (注意) (注意) 记号说明 备注 2.5 ㎝ 5㎝ 15 ㎝ 30 ㎝ 40 ㎝
标准工时是在正常操作条件下,以标准的作业方法及合理的劳动强度和速度完成符合质量要求的所需的作业时间

标准工时是在正常操作条件下,以标准的作业方法及合理的劳动强度和速度完成符合质量要求的所需的作业时间标准工时是指操作者在中等劳动强度和熟练程度下连续完成一件产品所需要的时间。
标准工时=正常时间+宽放时间正常时间=观测时间X评定系数观测时间采用秒表测时法获得,或者直接用MTM、WF、MOD等方法计算标准时间,也可以用标准资料法来预测标准工时。
标准工时主要用于人员编制(人事)、工时成本计算(财务)、工厂的先期规划(规划)、以及计划排产(生产管理及计划)等,标准工时是一个企业的基础性数据,属于企业机密。
什么是标准工时制,哪些工种实行标准工时制?问:什么是标准工时制,哪些工种实行标准工时制?答:标准工时制是指职工实行每日工作8小时,平均每周工资40小时,星期六、星期日为周休息日的工作制度。
实行这一制度,应保证完成生产和工作任务,不增加人员编制和财政支出,不减少职工的收入。
我市各级国家机关、社会团体、企业事业单位以及其他组织的职工,一律实行没日工作8小时,平均每周工作40小时的标准工时制度。
什么是标准工时制度、综合计算工时工作制、不定时工作制和非全日什么是标准工时制度、综合计算工时工作制、不定时工作制和非全日制工作制?答:(1)我国现在实行的是每日工作不超过8小时、每周工作不超过40小时的工时制度,这是标准工作时间。
(2)综合计算工时工作制是针对因工作性质特殊,需连续作业或受季节及自然条件限制的企业部分职工,采用的以周、月、季、年等为周期的综合计算工作时间的一种工时制度。
在综合计算工作时间的周期内,具体某一天、某一周的工作时间可以超过8小时或40小时。
(3)不定时工作制是指每一工作日没有固定的上下班时间限制的工作时间制度。
经批准实行不定时工作制的职工,不受日延长工作时间标准和月延长工作时间标准的限制,但用人单位应采用弹性工作时间等适当的工作和休息方式,确保职工的休息休假权利和生产、工作任务的完成。
(4)非全日制工作制是指以小时计酬,劳动者在同一用人单位平均每日工作时间不超过4小时,同时为一个以上用人单位提供非全日制工作的,每周累计工作时间不得超过40小时的用工形式。
精益生产 标准工时及其测量方法
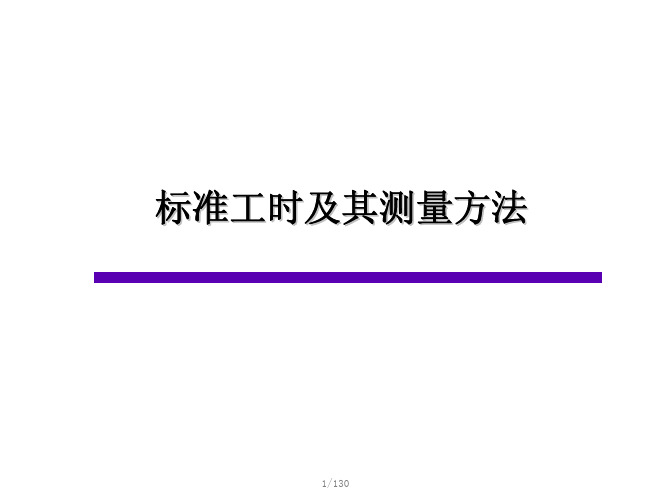
等
汇总并整理过去求得的标准时间 值,用于类似或同类作业
对于每个要素动作使用预先规定的 适用的时间值,如MTM和WF等
作业内容不确定等 不适合时间研究的 作业
经验估计法
具有渊博知识和经验的人凭经验进 行估计的方法,精度不很高,用于 单件生产等情况
每个作业单位的标准时间表制作
标准时间的承认
标准时间内容的直接说明及工厂干部说明 标准时间的承认
标准时间的维持系统的设计
20/130
标准时间的实施(使用)
◇ 正常时间的设定
● 根据连续时间研究法的分析(例)
(单位DM : 1/100分)
要素作业
1
2
3
4
5
6
7
8
9
10
个别时间 要素作 评价 系 正常
合计
9/130
1.6 标准工时的组成
准备
正规作业 主作业
收尾
宽放时间 作业上的 管理上的
人的
休息
其他
正常作业时间
最小限度的设定
标准时间 = 正常时间 + 宽放时间 = 正常时间 × (1+宽放率)
宽放时间
工厂宽放 作业宽放 生理性宽放 疲劳宽放
特殊宽放
10/130
1.7 标准工时的计算
◇ 各种时间的计算
标准作业速度
4/130
1.3 标准工时的目的
●● 某某个个计计划划所所需需『『时时间间』』的的『『预预测测值值』』基基础础资资料料 ------------ 树树立立计计划划
●● 当当完完成成对对应应的的标标准准作作业业时时,, 进进行行『『实实绩绩确确认认』』 ------------ 确确认认实实绩绩所所需需的的指指标标的的基基本本资资料料
精益生产工具及术语汇编
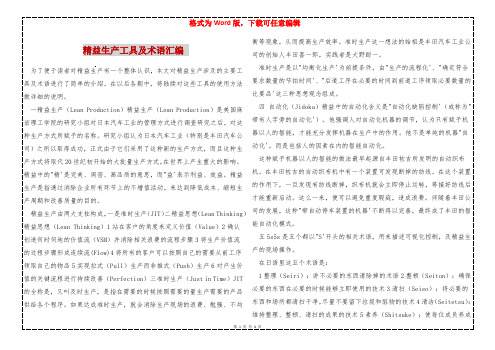
良好的习惯,遵守规则的技术六浪费精益生产中对浪费的定义是凡是超过生产产品所绝对必要的最少量的设备、材料、零件、和工作时间的部分,都是浪费。
生产现场的浪费归纳为以下七种:1等待的浪费2搬运的浪费3不良品的浪费4动作的浪费5加工本身的浪费6库存的浪费7制造过多(早)的浪费七价值流图(VSM)所谓价值流,是当前产品通过其基本生产过程所要求的全部活动。
这些活动包括给产品增加价值和不增加价值两部分,包括了从产品最基本的原材料阶段一直到产品交付客户的全部过程。
价值流图(Value Stream Mapping)是帮助你分析整个价值流的一个强有力的工具,他可以使整个价值流--通常是纷乱复杂的,变为可视的一张价值流现状图,使得价值流中的问题显现出来,这样就可以应用各种精益技术将不增值的活动--即浪费消除。
这种改进不仅能够消除浪费,而且能够消除浪费之源,使之不至于卷土重来,从而提高企业的竞争力。
八工业工程(IE)工业工程(Industrial Engineering,简称IE)是对人员、物料、设备、能源和信息所组成的集成系统进行设计、改善和设置的一门学科。
它综合运用数学、物理学和社会科学方面的专门知识和技术,以及工程分析和设计的原理与方法,对该系统所取得的成果进行确定、预测和评价。
体系包括四方面的内容:1作业改善(作业本身)2流程改善(作业流程)3现场改革(原料投入到成品产出、生产线)4企业系统改革、精益生产体系(包括信息流、物流、采购、制造、销售等的改革)九生产性生产性是投入生产要素和产出生产要素的比率,是评价生产效率高低的指标。
生产性的种类包括以下四种:1物质生产性:以物量表示产出量,适当把握效率或技术水平2价值生产性:以货币单位表示产出量,跟不同行业(公司)比较时有效3劳动生产性:产出/劳动,直接关系到工资问题4资本生产性:产出/资本,能左右企业的维持和发展十标准时间(Standard Time)标准时间是在正常的操作条件下,以标准的作业方法及合理的劳动强度和速度完成符合质量要求所需的作业时间。
精益生产(准时化生产jit)精益质量管理模型概述

精益质量管理模型概述围绕生产与质量主题,目前国内外已形成了多种理论和方法。
最引人注目的当属ISO9000质量管理体系、精益生产管理(Lean Production)、六西格玛管理(Six Sigma)。
ISO9000质量管理体系十多年来在国内受到企业热捧,证书需要是重要原因,但不可否认ISO9000质量管理体系自身的科学性和应用价值。
精益生产管理与六西格玛管理近年来在国内受到追捧,精英企业理论实践一体的明星示范效应功居至伟,其理论方法的实用价值功不可没。
上面所提到的三种理论方法尽管在我国应用过程中存在一些不足和偏差,但各自均是值得深入研究和应用的管理模式。
我们应看到,这三种理论方法均是舶来品,是西方先进企业管理精华的提炼,虽然科学的理论方法不应有国界之分,但管理学科本身所具有的软性和弹性特征,使我们在借鉴应用这些理论方法时有必要结合国情。
从我国企业普遍管理状况和管理方法需求出发,对有关理论方法进行创新探索应该是有必要的。
从生产系统综合改善的角度,精益生产管理、六西格玛管理理论方法可以有效结合,ISO9000质量管理体系有关思想也可借鉴其中。
此种结合就是华安盛道研究倡导的精益质量管理模式(Lean Quality)。
如下图所示:精益质量管理由五大子系统组成,分别为员工职业化、生产系统化、工序标准化、度量精细化、改进持续化,这五方面是企业推行精益质量管理的五大法宝。
这五大法宝各自又由相关要素组成,从而使精益质量管理形成体系。
精益质量管理模式是围绕生产作业系统质量、效率、成本综合改善这个目标,吸收借鉴精益生产、六西格玛、ISO9000体系的优秀成果,并结合我国企业的实际情况而形成的。
精益质量管理模型五大法宝1、员工职业化精益质量管理五大法宝之一是员工职业化。
精益质量管理将员工职业化放在一个非常突出的位置,这是与精益生产、六西格玛、ISO9000体系的一个显著区别。
精益质量管理借鉴有关管理革新项目成败经验教训,将员工职业化作为推行精益质量管理革新的首要关键要素。
三星公司质量管理讲解之精益生产1.doc
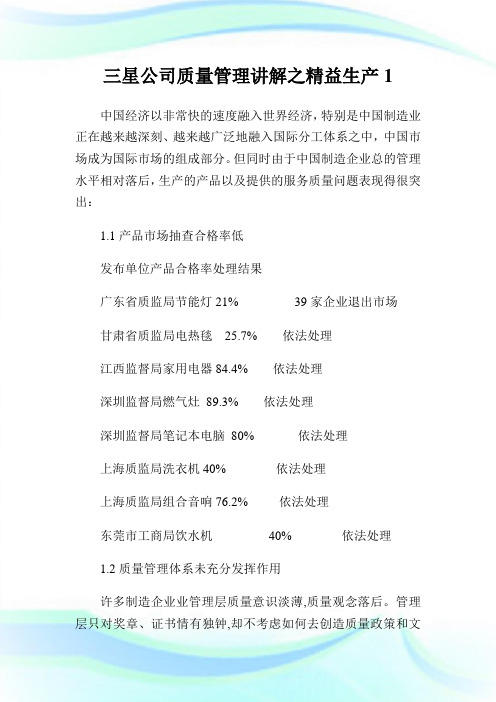
三星公司质量管理讲解之精益生产1中国经济以非常快的速度融入世界经济,特别是中国制造业正在越来越深刻、越来越广泛地融入国际分工体系之中,中国市场成为国际市场的组成部分。
但同时由于中国制造企业总的管理水平相对落后,生产的产品以及提供的服务质量问题表现得很突出:1.1产品市场抽查合格率低发布单位产品合格率处理结果广东省质监局节能灯21% 39家企业退出市场甘肃省质监局电热毯25.7% 依法处理江西监督局家用电器84.4% 依法处理深圳监督局燃气灶89.3% 依法处理深圳监督局笔记本电脑80% 依法处理上海质监局洗衣机40% 依法处理上海质监局组合音响76.2% 依法处理东莞市工商局饮水机40% 依法处理1.2质量管理体系未充分发挥作用许多制造企业业管理层质量意识淡薄,质量观念落后。
管理层只对奖章、证书情有独钟,却不考虑如何去创造质量政策和文化。
虽然现IS09000,IS014000等管理体系在国际上运行已经比较成熟,但是目前在我国许多制造企业并没有真正地在企业内部进行很好地运作。
即使有许多企业通过了质量管理体系的认证,但其中大多数也是在走形式,只是认为这些体系是进入市场的敲门砖,没有多少实际作用,对其认识不够透彻,更没有按照体系标准的要求认真实施。
大多数企业的管理层都将生产、销售放到了第一位。
他们关心的仅仅是企业的盈利、现金收支等指标。
至于产品质量他们认为那只是质量职能部门的事,将产品质量与生产截然分割开来。
当“产品质量”与“产量”、“交货期”等发生冲突和矛盾的时候,首先考虑的是确保“产量”和“交货期”,其次才是产品质量。
特别是,有些企业的最高管理层一提到加强质量管理就会想到要加大投入、耗费资金。
1.3过程质量控制缺乏,过程损失严重在产品生产过程中,由于多种因素的影响,产品质量必然存在着波动。
许多企业管理人员只注重结果、注重检验,而忽视过程管理。
在我国制造企业广泛使用SPC且效果良好的只有4.8%,有9.5%的企业广泛使用SPC,但效果一般;有23.8%的企业部分使用SPC且效果良好,有47.6%的企业部分使用且效果一般。
精益生产概念与标准时间

项目 1)所需人力
大批量 精益生产
1
1/2
2)新产品开发周期
1
1/2-2/3
3)生产过程的在制品库存
1
1/10
4)工厂占用空间
1
1/2
5)成品库存
1
1/4
6)产品质量
1
3
工程分析
工程分析目的
检讨单一工程或工程系列的合理性,推动总体生产活动的改善
生产要素 Input 生产线 Output 5M
成品
加工 搬运 检查 存放 停滞
区分 生产业务 工 程 单位作业 要素作业 动 作
展
开 单位 技法
箱体拼装
蒸发器组装 内胆组装 侧帮组装
左侧帮 右侧帮
拿侧帮 放在夹具上 固定镙丝
将手伸开 回转 抓住 抬起 移动
日/小时
小时/分
工程分析
分/秒 作业分析
时间分析
秒以下 动作分析
工程分析
工程分析体系
根据分析的对象的不同而使用不同的分析方法
方法时间 衡量MTM
模特法 MOD
英文
发明 时间
Motion Time 1924 Analysis
Work Factor 1934 System
Methods Time 1948 Measurement
Model Arrangement
of Predetermined 1966
Time Standard
平均活性指数的评价和改善着眼点
活性指数 评价
<0.5
0.5-1.3
因放在地面上 的时间多而使 浪费增加的现 场
地面已整理 现场
1.3-2.3
>2.3
精益流程管理三星工厂内教PPT课件

第28页/共41页
三星内教精益管理培训-精益流程管理
五、流程优化或再造目标选择工具:标杆瞄准法.
标杆瞄准法可用在设立改革的目标和远景、确定 流程再造的基准等方面。 在许多行业都有一些成功的企业,这些企业的做法可 以为行业中的其他企业所效仿,因此,也可以将这些 企业的一些具体的指标作为其他企业的标杆。
第25页/共41页
三星内教精益管理培训-精益流程管理
三、流程选择工具:绩效表现—重要性矩阵
流程或流程的结果在矩阵上的位置代表其重要程 度以及组织对它们运行的好坏程度,重要性程度与运 行绩效程度分别从低到高,结合比较一下客户反馈数 据和企业内部数据常常会得到意想不到的结果。如果 两方面都按照1分~5分评价,就可将项目分成四个类 型,其中重要程度高、绩效程度低的就是最需要改进 的领域。
第4页/共41页
三星内教精益管理培训-精益流程管理
企业实施精益流程管理所必备的条件: (1)管理者和员工素质必须提高。 管理要勇于革新,有强烈的市场竞争意识,能与公
司内外进行有效沟通,深入领悟精益流程管理的内涵。 在实施精益流程管理后,员工都将拥有更多决策机 会,必须有相应的高素质以及全流程的视角。
在处理符号的前后都应是数据符号.数据流程图以数 据符号开始和结束.(特殊符号外)
第19页/共41页
三星内教精益管理培训-精益流程管理
程序流程图: 程序流程图表示程序中的操作顺序. 程序流程图包括: a.指明实际处理操作的处理符号,它包括根据逻
生产性 (三星 LG等韩国企业)
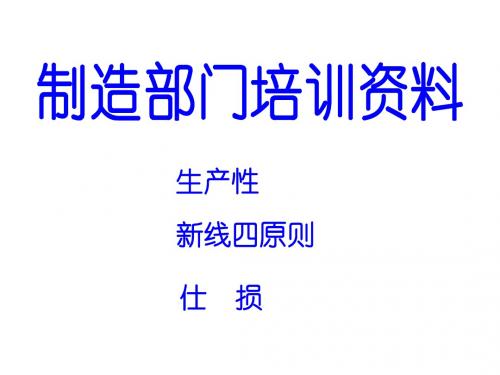
一、生产性计算方法
完成台数×标准时间 生产性= 作业时间×人数×0.95 标准时间是指一个熟练的操作员重复作业一万次所测试出的时间。 例如:某工程 标准时间:0.155627分,生产台数为:13682 台,实际作业时间为12H,人数:3.6人 生产性= 13682 × 0.155627 ×100% = 86.4% ×100%
品 投入数是指在某个时间段投入部品或组件的数量
某工程共投入了37.63公斤材料生产了96600个物镜, 例如: 其中小黑点不良有35PCS共报废0.013公斤,为对应黑 点不良又报废了2公斤材料 仕损率= 0.013+2 37.63
×100% = 5.34%
O/L 3天内工程不良3%以下;
O/L 一周内工程不良1%以下;
14682×0.97× 0.155627
工程不良下降2%,
生产性上升1.8% 减少加班后生产性=
14682×0.99× 0.155627
(12H× 3人+9×0.6) × 60分×0.95
× 100%=91.8%
一、仕损计算方法
仕损 = 仕损金额
完成台数*单价+仕损金额
×100%
定义:报废品是指不良的产品或部品通过修理不能再利用到生产中去的产
作 业 员 作 业 员 组 长 修 理 员 物 料 员
一、增加产量来提高生产性
例如:LEP-304A工程:完成台数由13682台→14682台,生产人 数为3.6人,作业时间为12H
增加前生产性=
13682× 0.155627
12H× 3.6人× 60分× 0.95
× 100%=86.4%
产量增加1000台, 生产性上升6.3% 增加后生产性=
- 1、下载文档前请自行甄别文档内容的完整性,平台不提供额外的编辑、内容补充、找答案等附加服务。
- 2、"仅部分预览"的文档,不可在线预览部分如存在完整性等问题,可反馈申请退款(可完整预览的文档不适用该条件!)。
- 3、如文档侵犯您的权益,请联系客服反馈,我们会尽快为您处理(人工客服工作时间:9:00-18:30)。
17
MODAPTS发 动作记号解说
区分 编号 1 移 动 距 离 2 3 4 5 6 7 8 结 尾 动 作 9 10 11 12 13 14 动作 手指 手 下胳膊 上胳膊 肩膀 握 握 握 握 握 放 放 放 放 记号 M1 M2 M3 M4 M5 G0 G1 G2 G3 G 11 P0 P2 P3 P5 MOD 1 2 3 4 5 0 1 2 3 11 0 2 3 5 使用手指动作 从手腕开始使用手面和手指 使用 下胳膊和手面,手指 使用上胳膊和下胳膊,手面,手指 伸开的胳膊和肩膀受刺激时 简单的碰东西的动作 抓的单纯状态的动作 利用轴拾起的动作 用 眼睛和注意力 及2 回以上动作夹的时候 利用手指末端关节的动作 (高度注意) 放下不必要的注意力 通过手的 1回以上的修正 放下物品的动作 (注意) (注意) (注意) (注意) (注意) 记号说明 备注 2.5 ㎝ 5㎝ 15 ㎝ 30 ㎝ 40 ㎝
• Motion Study
• Material Handling • Production Schedule • Standardization
66 %
53 % 45 % 60 %
Work Measurement 工厂设备 及 设计
• Time Study
•PTS法 • Plant Layout • 设备购入和更新 • Incentive • 职务评价
时间观测
现象作业 MODEL化
预备分析
• 产品,工程,作业, 设备,治工具 调查
비 标准作业的改善
改善作业的MODEL化
精 密 时 间 决 定 方 法
类似性分析 作成 标准资料 决定 项目 分析 变动要因
• 所有变动要因 • 主 变动要因 14
有余时间的决定
设定 标准时间
3. 标准时间教育的 必要性和适用实态
85 %
65 % 85 % 52 % 60 % 52 % 37 % 60 % 3
支付薪水
统
计
• Process Control • Cost Control
管理技术和生产 LOSS的 Matrix
生产 LOSS 工 程 损 耗 ○ 便 性 损 耗 ○ ○ ○ ○ ○ ○ ○ ○ ○ ○ ○ ○ ○ ○ ○ ○ ○ ○ ○ ○ ○ ○ ○ ○ ○ ○ ○ ○ ○ ○ ○ ○ ○ ○ ○ ○ ○ ○ ○ ○ ○ ○ ○ ○ ○ ○ ○ ○ ○ ○ ○ ○ ○ ○ 搬运 及 物流分析 5S 设备效率 高水准化 设定 标准时间 1,2 MODAPTS 稼动分析 作业分析 1,2 VE 品质管理 1,2 制造作业 System的 LOSS 作 业 损 耗 动 作 损 耗 版 设 备 损 耗
(独立) (独立)
○
○
M 动作分析
Line 便性 ORDLIX SHA,SLP 5S
I
E
E
TPM 直接观测,Rating
W PTS(MODAPTS)
M Work sampling PAC V E Q C 技能分析 7种 道具
4
IE 分析技法
产品(PRODUCT)
技能(FUNCTION)
工程(PROCESS)
单位作业(OPERATION) 作业要素(ELEMENT) 动作(MOTION)
=1/100000H
(100% Rate)
使用于中工业
MODAPTS法 (Modular Arrangement of PTS) 据身体 各部位动作 的距离赋予时间值
Basic M:1966年
Offixe M:1969年 Trmnit M:1973年
1 MOD Rule : 非常 简单 分析 : 简单 (Modular) 0.129秒/0.1秒 0.143秒/0.12秒 可以任意 采用4种PACE 充分并适用于 精密机械业体
21 22
23 24 25 26 27 28
重新拿起 重新拿起
脚 旋转 弯 弯 坐站 注意
R2 R4
F3 C4 B 17 B8 S 30 N3
2 4
3 4 17 8 30 3
重新拿起小东西时 重新拿起大东西时
脚后跟踩地或者放松时 做圆型运动的目的 将身体弯曲伸直的动作 顺次性 B17 动作 在椅子上坐下站起的反复动作 注意 及 危险动作
复杂的加工 复杂 & 注意
相当~ ” ~ 低 10.单 调 感 中等 高 多少烦 11. 烦 烦 很烦
1 4
8 0 1 4 0 2 5
1 4
8 0 1 4 0 1 2
4
2 0 2 7 0 1 2 3 4 5 7 9 11 13 17 22
4
4 1 3 7 1 2 3 4 6 8 10 13 16 20 *** *** 8. 消 音 7.注意力 calorie / ㎠ / 秒) 6.等待条件 (温度 启示度 :M
生产一枚产品 需要的时间
7
– 适用的问题 Q1. Tailor 选定了 体格健壮的 熟练工 但是不能说现场的作业者们都是熟练工. 对于 这点 您有何想法?
Q2. 为了促进工厂经营效率性 测定作业 和 标准时间 有着重要的作用。但是 为何对此想为是 抵抗呢?
Q3. 消除在现场感觉到的 抵抗或者过敏现象
感觉可能与工作需要注意的操作
眼睛看正确的位置把东西放到正确位置的动作
1 MOD = 0.1秒(High) = 0.129秒(Normal) = 0.143秒(包括疲劳10.75% )
18
MODAPTS发 动作记号解说
区分 编号 15 16 17 18 19 其 它 动 作 20 动 作 两 (重量) 看 (眼睛) 判 按 按 步行 断 记号 L1 E2 D3 A2 A4 W5 MOD 1 2 3 2 4 5 记号说明 搬运重量物的动作(用补正系数 计算加权值) 眼睛移动时和焦点相对时的动作 瞬间判断的动作 2㎏ 以下的压力动作 (手动作) 2㎏ 以上的压力动作 (全身) 走一步或者旋转时 (独立) (独立) (独立) (独立) 备 注
16
5. PTS (Pre-Determined Time Standard) 分析方法
1) MODAPTS法
据身体部位, 应用21个基本动作和8个基本时间值, 用定标准时间的方法修改或者设定的时候, 比其它方法对应迅速及程度高。 对于动作的判断 RULE 非常简单。 PACE的 基准 : 可以任意设定3种 PACE 身体各部位的动作距离附有时间 所以分析难易度较为简单. 训练期间短. (2~3日) 对精密机械工业 是 适当的技法.
MTM (Method Time Measurement)
分解为作业上需要 的基本动作 赋予对应 性质和条件的时间值
MTM1:1948年 MTM2:1965年 MTM3:1971年
Rule : 简单 分析 : 稍微 困难
1 TMU(Time Measurement Normal Pace 充分并
Unit)
RWF (Ready Work-Factor)
根据身体各部位的 作难易度赋予 Work Factor DWF:1945年
Rule : 复杂 分析 : 简单
1RU(Ready Time Unit) =0.001分
充分,适用于 Incentive Pace (125% Rate) 电子 及 机械组装 业体
W/H 运输
标
就 准 业
空 Box 处理
作业有余
放下扳手 与组长一起确 认不良 WC/水
时
时 间 间
剩余时间 生理有余 疲劳有余
解决生理性需要
职长有余
目的性管理所需时间
恢复疲劳需要的时间
适用手腕
损失时间
非作业时间/管理损失时间
11
– 有余率
区 1.个人有余 2.基础有余 站的姿势 3.姿势别 不自然姿势 不便的姿势 相当 ~ ” ~ 2.3 Kg 4.5 Kg 6.8 Kg 9.0 Kg 11.3 Kg 4.取极重量 (印章, 拉, 压力) 13.6 Kg 15.9 Kg 18.1 Kg 20.4 Kg 22.6 Kg 27.2 Kg 37.8 Kg 分 有余率 男 5 女 7 5.照明不良 区 分 多少低 低 男 0 2 女 0 2 9.精神性 疲劳
加 工 材 料 损 耗 加 工 时 间 损 耗
Performance LOSS
成 本 计 算
管理技术 工程分析 作业 分析 单独 联合
面 ○ ○ ○
机 器 故 障
材 料 短 缺
等
未 熟 练
待 ○ ○
暂 时 等 待
作 业 不 良
作 业 速 度
不 良 品
产 品 设 计 向 损 耗
比
较
工程, 生产 Variety 分析 ○ ○ ○ ○ 单独作业分析和改善 联合作业分析和改善 动作分析和改善 Line 作业便性
相当低
16 14 12 10 8 6 5 4 3 2 详细的作业 精密 或者 正确 相当 ~ ” ~ 连续音 偶尔的高音 相当大的声音
5
0 0 0 3 10 21 31 45 64 100 0 2 5 0 2 5
5
0 0 0 3 10 21 31 45 64 10 0 0 2 5 0 2 5
12
– PTS的 时间决定 要素
2) 适用 实态
- 精密度 3种 技法 ( MTM, RWF, MODAPTS ) 全部一样 - 越是最近开发的技法,越容易开发分析 (MODAPTS是 最新的)
15
4. PTS (Pre-Determined Time Standard) 比较表
区 分 定 义 开发背景 复杂性/难易度 时间单位 Pace 精密度/适用
动作种类
移 动 结 合 拿 …..
正常考虑要素
身体 部位