第20章瓷粉体原料制备工艺
自蔓延法制备陶瓷粉体

八、应用自蔓延法进行生产的企业
福建施诺瑞新 材料有限公司
氮化铝粉体
纯度
化学成分 TiC纯度: ≥99%
粒度范围为 1 30m
含氮量 >33.0wt.% 氧含量在1.0wt.%以下
粉体粒度分布 曲线
五、SHS 合成超高温陶瓷
上硅所用SHS合成超高温陶瓷ZrB2-SiC-ZrC活性粉体
超高温陶瓷(UHTCS)是在1800度以上使用,具有3000度左 右熔点及高温抗氧化性和热震性的过渡金属的硼化物、碳化物 和氮化物。
发生的化学反应
(2 x)Zr (1 x)Si B4C 2ZrB2 (1 x)SiC xZrC
表 1 PZT 陶瓷的性能参数
合成温度/度 介电损耗 相对介电常数 居里温度/度
PbZr0.52Ti0.48O3
500
0.0032
332
375
七、溶胶凝胶自燃烧合成PMN-PT
Ref. 5 Ceramics International, 35 (2009), 2899–2905 Iran
七、溶胶凝胶自燃烧合成PMN-PT
自蔓延高温法制备陶瓷粉体
自蔓延高温合成 SHS
自蔓延高温合成技术(Self-propagating High-temperature Synthesis SHS)或燃烧合成(Combustion Synthesis CS),是依靠反应自身化能放 热来合成材料的新技术。
它最大的特点是除引燃外无需外部热源,效率高。
其主要特征是反应只需局部点火引发燃烧波,并使其在原料中传播以实现 系統的合成过程。
【精品文章】碳化锆(ZrC)陶瓷粉体的制备方法综述
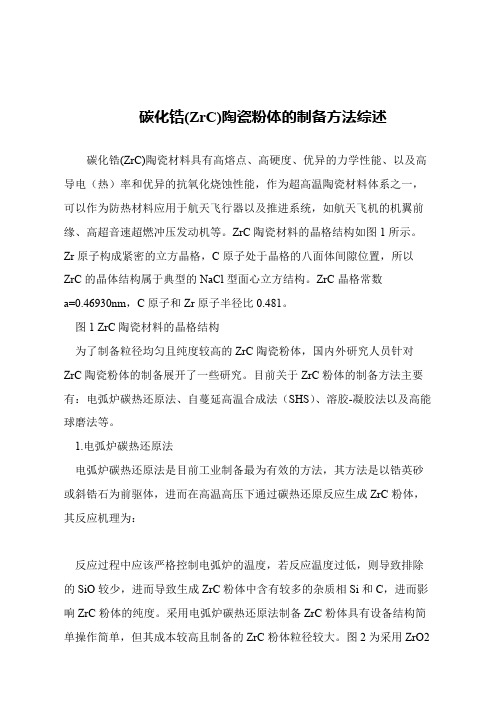
碳化锆(ZrC)陶瓷粉体的制备方法综述
碳化锆(ZrC)陶瓷材料具有高熔点、高硬度、优异的力学性能、以及高导电(热)率和优异的抗氧化烧蚀性能,作为超高温陶瓷材料体系之一,可以作为防热材料应用于航天飞行器以及推进系统,如航天飞机的机翼前缘、高超音速超燃冲压发动机等。
ZrC陶瓷材料的晶格结构如图1所示。
Zr原子构成紧密的立方晶格,C原子处于晶格的八面体间隙位置,所以ZrC的晶体结构属于典型的NaCl型面心立方结构。
ZrC晶格常数
a=0.46930nm,C原子和Zr原子半径比0.481。
图1 ZrC陶瓷材料的晶格结构
为了制备粒径均匀且纯度较高的ZrC陶瓷粉体,国内外研究人员针对ZrC陶瓷粉体的制备展开了一些研究。
目前关于ZrC粉体的制备方法主要有:电弧炉碳热还原法、自蔓延高温合成法(SHS)、溶胶-凝胶法以及高能球磨法等。
1.电弧炉碳热还原法
电弧炉碳热还原法是目前工业制备最为有效的方法,其方法是以锆英砂或斜锆石为前驱体,进而在高温高压下通过碳热还原反应生成ZrC粉体,其反应机理为:
反应过程中应该严格控制电弧炉的温度,若反应温度过低,则导致排除的SiO较少,进而导致生成ZrC粉体中含有较多的杂质相Si和C,进而影响ZrC粉体的纯度。
采用电弧炉碳热还原法制备ZrC粉体具有设备结构简单操作简单,但其成本较高且制备的ZrC粉体粒径较大。
图2为采用ZrO2。
陶瓷粉体基础表征

高温陶瓷材料在高温环境下表现出良 好的抗氧化性、抗蠕变性和高温强度, 使其成为高温环境下应用的理想材料。
高温陶瓷材料的制备通常需要经过复 杂的合成和烧结过程,以确保其具有 优良的力学性能、化学稳定性和高温 稳定性。
电子陶瓷材料
电子陶瓷材料是指具有优良电性 能的陶瓷材料,广泛应用于电子 元器件、集成电路、传感器等领
针对不同应用领域,研究具有 特定性能需求的陶瓷粉体,拓 展其在能源、环境、生物医学 等领域的应用。
加强跨学科合作,将陶瓷粉体 科学与材料科学、物理学、化 学等学科进行有机结合,推动 陶瓷粉体科学的发展。
感谢您的观看
THANKS
多孔陶瓷材料的孔径、孔隙率、比表面积等参数对其性能和应用具有重要影响,需 要根据具体应用需求进行优化设计。
06 结论与展望
研究结论
陶瓷粉体的形貌、粒径、化学 组成等基础性质对陶瓷材料的
性能具有重要影响。
通过先进的表征技术,如X射线 衍射、扫描电子显微镜、透射 电子显微镜等,可以深入了解 陶瓷粉体的结构和性质。
总结词
液相法是一种通过溶液中的化学反应来制备陶瓷粉体的方法。
详细描述
液相法通常是将原料溶解在溶剂中,然后通过控制溶液的浓度、温度和pH值等参数,使原料在溶液中 发生化学反应并析出晶体,最终得到所需的陶瓷粉体。该方法制备的粉体具有较窄的粒度分布和较好 的形貌控制,但制备过程中需要去除溶剂并进行高温煅烧,成本较高且易引入杂质。
详细描述
扫描电子显微镜利用电子束扫描陶瓷 粉体表面,通过收集和分析二次电子、 背散射电子等信号,形成高分辨率的 图像,能够观察陶瓷粉体的形貌和粒 度分布。
透射电子显微镜观察
总结词
透射电子显微镜观察可以观察陶瓷粉体的内 部结构和晶体生长情况。
陶瓷粉体
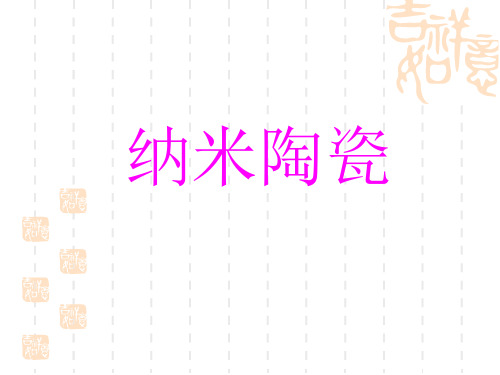
纳米陶瓷: 指显微结构中的物相(包括晶粒尺 寸、晶界宽度、第二相分布、气孔与尺 寸缺陷等)都在纳米量级的水平上的陶 瓷材料。
现有陶瓷材料的晶粒尺寸一般是在微 米级的水平。当其晶粒尺寸变小到纳米级 的范围时,晶粒的表面积和晶界的体积会 以相应的倍数增加,晶粒的表面能亦随之 剧增。 由于颗粒的线度减少而引起表面效应 和体积效应,使得材料的物理、化学性质 发生一系列变化,而且甚至出现许多特殊 的物理与化学性质。
纳米材料的制备: 纳米粉体的合成 素坯的成型 产品的烧结
粉体合成按合成条件分类: 1、气相法:气相法是直接利用气体,或 者通过各种手段将物质转变为气体,使之 在气体状态下发生物理变化或者化学反应, 最后在冷却过程中凝聚长大形成纳米粒子 的方法。 优点:制得的纳米陶瓷粉体的纯度较 高,团聚较少,烧结性能较好 缺点:产量低,设备昂贵
2、应用于提高陶瓷材料的超塑性 只有陶瓷粉体的粒度小到一定程度 才能在陶瓷材料中产生超塑性行为,其 原因是晶粒的纳米化有助于晶粒间产生 相对滑移,使材料具有塑性行为。
3、应用于制备电子(功能)陶瓷 纳米陶瓷粉体之所以广泛地用于 制备电子陶瓷,原因在于陶瓷粉体晶粒 的纳米化会造成晶界数量的大大增加, 当陶瓷中的晶粒尺寸减小一个数量级, 则晶粒的表面积及晶界的体积亦以相 应的倍数增加
3、固相法:指纳米粉体是由固相原 料制得,按其加工的工艺特点可分 为机械粉碎法和固相反应法两 类。 优点:所用设备较简单,方便操作 缺点:纯度较形状、
体积和强度的坯体的过程,素坯的相对 密 度和显微结构的均匀性对陶瓷在烧结过 程 中的致密化有极大的影响
纳米陶瓷的性能:
1、高强度: 纳米陶瓷材料在压制、烧结后,其强度比 普通陶瓷材料高出4-5倍,如在 100度下,纳米 TiO2陶瓷的显微硬度为13000KN/mm2,而普通 TiO2陶瓷的显微硬度低于2000KN/mm2。日本 的新原皓一制备了纳米陶瓷复合材料,并测定 了其相关的力学性能,研究表明纳米陶瓷复合 材料在韧性和强度上都比原来基体单相材料均 有较大程度的改善,对 Al2O3/SiC 系统来说, 纳米复合材料的强陶度比单相氧化铝的强度提 高了3-4倍。
-特种陶瓷粉体的制备(1)
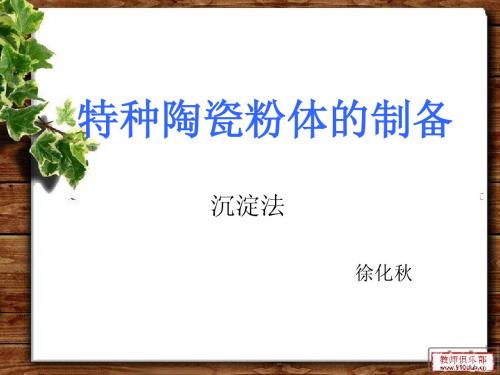
氧化锆超细粉的制备
水解沉淀法 • 此法是长时间地沸腾锆盐溶液, 使水解生成的挥发性酸HC|或 HNO 不断蒸发除去,从而使如下 水解反应平衡不断向右移动: • ZrOCI2+(3+n)H2O— Zr(OH)4· nH2O+2HCI • ZrO(NO3)2+(3+n)H2O— Zr(OH)4· nH2O+2HNO
直接沉淀法
• 沉淀操作包括加入沉淀剂或水解。 • 不同的沉淀剂可以得到不同的沉淀 产物,常见的沉淀剂为: NH3•H2O、NaOH、(NH4)2CO3、 Na2CO3、(NH4)2C2O4等。
直接沉淀法
• 优点:操作简单易行,对设备技术 要求不高,不易引入杂质,产品纯 度很高,有良好的化学计量性,成 本较低。 • 缺点:洗涤原溶液中的阴离子较难, 得到的粒子粒径分布较宽,分散性 较差。
ห้องสมุดไป่ตู้
化学共沉淀法
• 化学共沉淀法是把沉淀剂加入混 合后的金属盐溶液中,使溶液中 含有的两种或两种以上的阳离子 一起沉淀下来,生成沉淀混合物 或固溶体前驱体,过滤、洗涤、 热分解,得到复合氧化物的方法。 沉淀剂的加入可能会使局部浓度 过高,产生团聚或组成不够均匀。
化学共沉淀法
• 化学共沉淀法不仅可以使原料细 化和均匀混合,且具有工艺简单、 煅烧温度低和时间短、产品性能 良好等优点。 • 化学共沉淀法制备ATO粉体具有 制备工艺简单、成本低、制备条 件易于控制、合成周期短等优点, 已成为目前研究最多的制备方法。
均匀沉淀法
• 应该指出,用均匀沉淀法仍不能避 免后沉淀和混晶共沉淀现象。
均匀沉淀法
• 均匀沉淀法中的沉淀剂,如 (C2O4)2-、 (PO4)3- 、S2等,可用相应的有机酯类化合物或 其他化合物水解而获得。 • 也可以利用络合物分解反应和氧化 还原反应进行均匀沉淀。
陶瓷粉体制备ppt课件
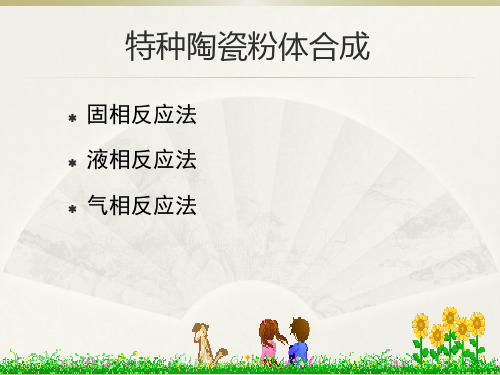
解速度有利于溶胶凝胶形成。 湿度。一般<50% 温度。提高温度促进水解、缩聚反应,缩短
凝胶时间
20
醇盐分解法
采用金属醇盐M(OR)n为先驱体,以无水乙醇为溶 剂,遇水后很容易水解形成氧化物或其水合物。
控制水解条件可以获得粒径几纳米到几十纳米的超 细粉。
2. 在适当的高温下煅烧合成 3. 将合成的熟料块体粉碎研磨至所需细度
主要用于合成复合氧化物(如BaTiO3等)
BaCO3 TiO2 BaTiO3 CO2
3Al2O3 2SiO2 3Al2O3 2SiO2
3
碳热还原反应法
非氧化物的合成
碳化物
TiO2 C ArTiC CO2 SiO2 3C Ar SiC 2CO
R O
R O
Si
H2O
O R
O R
H O
OH
Si
HO
O H
21
水热法
在密闭反应釜(高压釜)内,采用水溶液为反应介质,对 反应釜加热,溶剂蒸发形成高温高压,使通常条件下难溶 或不溶的物质发生溶解析出传质,得到晶体颗粒。
优点:
晶粒发育完整、细小、均匀; 无(或少)团聚; 无煅烧及粉碎等加工过程。
这两种力的合力状态决定了颗粒的团聚 与分散(DLVO理论)。 影响分散的因素:
pH、电解质溶液中离子强度 分散剂
25
干燥过程
干燥过程中的团聚主要是由颗粒间液体 的表面张力产生的。
P 2 LV cos
R
• 乙醇的表面张力比水小,因此,通过乙 醇清洗后再干燥,可减少干燥中的团聚 程度。
陶瓷粉体的制备通常采用传统的烧结粉碎法

陶瓷粉体的制备通常采用传统的烧结粉碎法,但这种方法耗时长、能耗高、污染大。
此外,还有化学沉淀法、溶胶凝胶法、熔剂蒸发法、水热法、乳化液法、喷雾热分解法、蒸发一凝聚法、气相化学反应法等,这些方法各有特点。
但近年来,自蔓延燃烧技术作为陶瓷粉料的一种新的制备方法愈来愈显示出其优越性。
自蔓延燃烧技术是利用反应物之间高化学反应热的自加热和自传导作用来合成材料的一种技术。
该技术由前苏联科学院化学物理所的燃烧问题专家Merzhanov等人在研究火箭固体推进剂燃烧问题时首先发现,并于1967年提出的。
美国和日本也先后引进并发展了SHS技术。
我国开展SHS 技术的研究起步较晚,但发展极为迅速,己经取得了一系列令人瞩目的成就,并发表了大量的高水平学术论文。
“八五”期间,国家高技术“863"计划,设立了金属-非金属材料复合的自蔓延高温还原合成技术项目。
在1998年国家高技术新材料领域专家委员会发表的“新材料领域战略系统”报告中,把SHS技术列入当前研究的热点项目[l]。
利用自蔓延燃烧技术合成陶瓷粉体具有反应时间短、污染小,通过化学反应自身放热维持反应进行等特点。
因此,采用自蔓延燃烧技术合成陶瓷粉体是对传统制备工艺的挑战,它将为粉体合成开辟了新的途径。
2 自蔓延燃烧技术简介2.1自蔓延燃烧技术的原理SHS技术是基于放热化学反应的基本原理,利用外部能量诱发局部化学反应(点燃),形成化学反应前沿(燃烧波),此后,化学反应在自身放热的支持下继续进行,表现为燃烧波蔓延至整个体系,最后合成所需的材料。
这是一种高放热反应,参与反应的物质一般在固—固,固—气介质中进行,但最终产物一般是固态。
其主要特征是反应只需局部点火引发燃烧波,并使其在原料中传播以实现系统的合成过程。
反应过程如图1所示[1]:自蔓延反应形式主要有两种:直接合成法和Mg热、A1热合成法。
直接合成法是两种或两种以上反应物发生反应直接合成产物,而无需中间反应。
陶瓷粉体制备
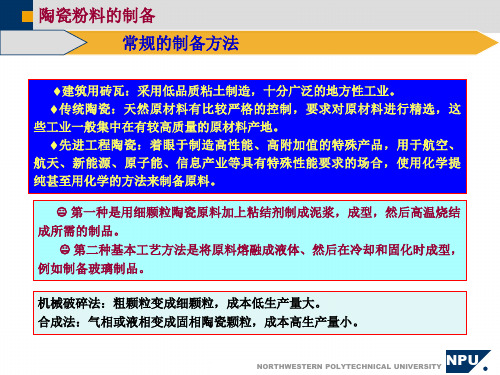
SiC制备基本反应: SiO2+3C → SiC+2CO
分步反应: SiO2+C → SiO(气)+CO SiO+2C → SiC+CO SiO+C → Si(气)+CO Si+C → SiC
用于碳化硅生产的阿奇逊电炉 (a)炉役开始前;(b)炉役结束后
随着SiC生成电阻越来越大,炉芯区域温度达 2700~2800℃,SiC分解, SiC=Si+C SiC+2SiO2=3SiO+CO SiC+SiO=2Si+CO 分解生成的Si及SiO蒸气向低温区扩散与C反应生成 SiC 将SiC结晶块挑选出来,经过复杂的粉碎过程获得各种粒度的SiC粉料
TaC Ta2O5+炭黑 Mo2C Mo+炭黑,MoO3+炭黑
炉内气氛 H2,CO, CnHm 真空 H2,CO, CnHm 真空 H2,CO, CnHm H2,CO, CnHm H2,CO, CnHm 真空 H2,CO, CnHm 真空 H2,CO, CnHm 真空 H2,CO, CnHm 真空
温度范围 2200-2300℃ 1600-1800℃ 1800-2300℃ 1700-1900℃ 1900-2300℃ 1100-1200℃ 1400-1500℃ 1200-1300℃ 1900-2000℃ 1600-1700℃ 1400-1600℃ 1200-300℃ 2000-2100℃ 1600-1700℃ 1200-1400℃
Mo+炭黑 WC
W+炭黑,WO3+炭黑 W+炭黑 Si+C SiC SiO2+C
H2,CO, CnHmH2,CO, ຫໍສະໝຸດ nHm1100-1300℃
1400-1600℃ 1200-1400℃
1500-1700℃
微波陶瓷粉体生产工艺流程

微波陶瓷粉体生产工艺流程下载温馨提示:该文档是我店铺精心编制而成,希望大家下载以后,能够帮助大家解决实际的问题。
文档下载后可定制随意修改,请根据实际需要进行相应的调整和使用,谢谢!并且,本店铺为大家提供各种各样类型的实用资料,如教育随笔、日记赏析、句子摘抄、古诗大全、经典美文、话题作文、工作总结、词语解析、文案摘录、其他资料等等,如想了解不同资料格式和写法,敬请关注!Download tips: This document is carefully compiled by theeditor. I hope that after you download them,they can help yousolve practical problems. The document can be customized andmodified after downloading,please adjust and use it according toactual needs, thank you!In addition, our shop provides you with various types ofpractical materials,such as educational essays, diaryappreciation,sentence excerpts,ancient poems,classic articles,topic composition,work summary,word parsing,copy excerpts,other materials and so on,want to know different data formats andwriting methods,please pay attention!微波陶瓷粉体是一种新型的陶瓷材料,具有高热稳定性、高电导率、高机械强度等优良性能,广泛应用于微波器件、高频元件、陶瓷基片等领域。
粉体陶瓷成形技术
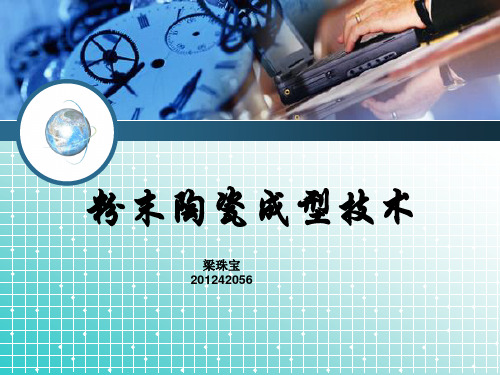
2.粉体的成形方法及设备
2.2粉体的制备 液体金属雾化法
许多雾化法部是采用双液流:一为液态金属流,—为 液体或气体流。后者冲击液态金属流,将之破碎成金属 液滴,随后凝固成粉末颗粒。对于制取铁、钢粉末,一 般用水或油作为冲击流体;对于某些特殊金属,则采用 空气、水蒸气或惰件气体作为冲击流体;对于其他金属, 用惰性气体氮、氩或氮作为雾化介质;在某些场合.采 用水蒸气。
2.粉体的成形方法及设备
2.4 粉体的成形
通过一定的方法,将粉体原料制成具有一 定形状、尺寸、密度和强度坯体的过程称 为成形 (1)压制成形 (2)塑性成形 (3)浇注成形
2.粉体的成形方法及设备
2.4 粉体的成形
压制成形——是粉 末陶瓷成形的常用 方法之一。将松散 的粉状原料放入模 具中,并施加一定 的压力后便获得块 状坯体。
粉末陶瓷成型技术
梁珠宝 201242056
粉末陶瓷成型技术 1 粉末陶瓷成型的基本原理 2 粉体的成形方法及设备
3 粉末陶瓷成形新技术
粉末陶瓷成型技术
1 粉末陶瓷成型的基本原理
概述
粉末陶瓷材料以粉体(粉末)为原材料, 经过成形和烧结工艺制备而成。
1.粉末陶瓷成型的基本原理
陶瓷材料的成形过程与粉末冶金相似,所不同的是两者采 用不同的原材料。 一般情况下,陶瓷材料的组织结构包括晶相、玻璃相和气 相三个部分,其中的晶相是陶瓷材料的主要组成相。
2.粉体的成形方法及设备
2.6后处理
粉末陶瓷制品在烧结中通常产生收缩、变形 以及一些表面缺陷,烧结后的表面粗糙度差, 一般情况下,不能作为最终产品直接使用。 浸渍:用油、石蜡、树脂填充烧结制品的空 隙。 精整:烧结后再模具中再压一次以获得所需 的尺寸精度和表面粗糙度。 精压:获得特定的表面形状和适当改善密度 的工艺。 复压:提高制品密度、提高强度的工艺。
陶瓷材料及其制备烧结工艺培训课件:粉体的制备、烧结后处理与加工
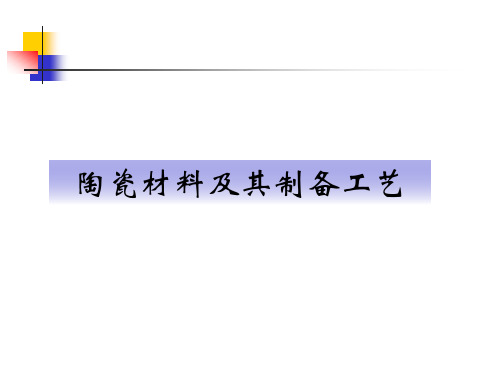
a.水晶
b.脉石英
c.砂岩
d.石英岩
e.石英砂
石英
水晶
3.长石类原料 长石是陶瓷生产中的主要熔剂性原料,一般用作坯料、釉
料、色料熔剂等的基本成分,用量较大,是日用陶瓷的三大原 料之一。自然界中长石的种类很多,归纳起来都是由以下四种 长石组合而成:
3)放电等离子体烧结
4)微波烧结 5)反应烧结 6)爆炸烧结
帮助理解
常压烧结:常压 热压烧结:加压 热等静压烧结:高温恒压 气氛烧结:防氧化、加气 反应烧结:加入气相或者液相以 获得一 定强度和精度
热压烧结
2.热压烧结 包括
热压烧 (在10~ 重排与致密 设备与模具 的烧制。
热等 复杂制品生 轴承、反射 亦可采用此
五、烧结原理与工艺
(一) 概念
烧结是指多孔状陶瓷坯体在高温条件下,表面积减 小、孔隙率降低、机械性能提高的致密化过程。
陶瓷烧结示意图
(a)颗粒间的松散接触;(b)颗粒间形成颈部; (c)晶界向小晶粒方向移动并逐渐消失,晶粒逐渐长大; (d)颗粒互相堆积形成多晶聚合体
(一) 概念
陶瓷的烧结类型可以分 固相烧结、液相烧结。
2. 陶瓷的分类 (1) 按陶瓷概念和用途来分类:
陶瓷
普通陶瓷
特种陶瓷
日用陶瓷
(包括艺术 陈列陶瓷)
建筑卫 生陶瓷
化工陶瓷
电瓷 化学瓷 及其它 结构陶瓷 功能陶瓷
工业用陶瓷
结构陶瓷主要是用于耐磨损、高强度、耐热、耐热 冲击、硬质、高刚性、低热膨胀性和隔热等结构陶瓷 材料;
粉末冶金工艺陶瓷制品制备的流程

粉末冶金工艺陶瓷制品制备的流程下载温馨提示:该文档是我店铺精心编制而成,希望大家下载以后,能够帮助大家解决实际的问题。
文档下载后可定制随意修改,请根据实际需要进行相应的调整和使用,谢谢!并且,本店铺为大家提供各种各样类型的实用资料,如教育随笔、日记赏析、句子摘抄、古诗大全、经典美文、话题作文、工作总结、词语解析、文案摘录、其他资料等等,如想了解不同资料格式和写法,敬请关注!Download tips: This document is carefully compiled by theeditor. I hope that after you download them,they can help yousolve practical problems. The document can be customized andmodified after downloading,please adjust and use it according toactual needs, thank you!In addition, our shop provides you with various types ofpractical materials,such as educational essays, diaryappreciation,sentence excerpts,ancient poems,classic articles,topic composition,work summary,word parsing,copy excerpts,other materials and so on,want to know different data formats andwriting methods,please pay attention!粉末冶金工艺是一种通过将金属粉末或陶瓷粉末进行成型和烧结来制造零件或制品的工艺方法。
第20章 陶瓷粉体原料制备工艺

第20章陶瓷粉体原料制备工艺§20.1 粉体制备工艺传统的粉体制备工艺就是机械破碎法,生产量大,成本低,但杂质混入不可避免。
随着先进陶瓷的发展,各种反应合成法得以应用,优点是纯度高、粒度小、成分均匀,但成本高。
20.1.1 传统粉体制备工艺以机械力使原材料变细的方法在陶瓷工业中应用极为广泛。
陶瓷原料进行破碎有利于提高成型坯体质量,提高致密程度并有利于烧结过程中各种物理化学反应的顺利进行,降低烧成温度。
一、颚式破碎机颚式破碎机是陶瓷工业化生产所经常采用的一种粗碎设备,主要用于块状料的前级处理。
设备结构简单,操作方便,产量高。
但颚式破碎机的粉碎比不大(约4),进料块度一般很大,因此出料粒度一般都较粗,而且粒度的调节范围也不大。
二、轧辊破碎机轧辊破碎机的优点在于粉碎效率高,粉碎比大(>60),粒度较细(通常可达到44 m)。
但当细磨硬质原料时,由于轧辊转速高,磨损大,使得粉料中混入较多的铁,影响原料纯度,要求后续去铁。
同时由于设备的特点,其粉料粒度分布比较窄,只宜用于处理有粒度分布要求的原料。
三、轮碾机轮碾机是陶瓷工业化生产所常采用的一种破碎设备,也可用于混合物料。
在轮碾机中,原料在碾盘与碾轮之间的相对滑动及碾轮的重力作用下被研磨、压碎。
碾轮越重、尺寸越大,粉碎力越强。
为了防止铁污染,经常采用石质碾轮和碾盘。
轮碾机的粉碎比大(约10),轮碾机处理的原料有一定的颗粒组成,要求的粒度越细,生产能力越低。
轮碾机也可采用湿轮碾的方法。
四、球磨机球磨机是工业生产普遍使用的细碎设备,也可用于混料。
为了保证原材料的纯度,经常采用陶瓷作为衬里,也可采用高分子聚合物材料作为衬里,并以各种陶瓷球作为研磨球。
湿球磨所采用的介质对原料表面的裂缝有劈裂作用,间歇式湿球磨的粉碎效率比干球磨高,湿球磨所得到的粉料粒度可达几个微米。
球磨机转速对球磨机效率的影响。
球磨机转速直接影响磨球在磨筒内的运动状态,转速过快,磨球附看在磨筒内壁,失去粉碎作用;转速太慢,低于临界转速太多,磨球在磨筒内上升不高就落下来,粉碎作用很小;当转速适当时,磨球紧贴在筒壁上,经过—段距离,磨球离开筒壁下落,给粉料以最大的冲击与研磨作用,具有最高的粉碎效率。
- 1、下载文档前请自行甄别文档内容的完整性,平台不提供额外的编辑、内容补充、找答案等附加服务。
- 2、"仅部分预览"的文档,不可在线预览部分如存在完整性等问题,可反馈申请退款(可完整预览的文档不适用该条件!)。
- 3、如文档侵犯您的权益,请联系客服反馈,我们会尽快为您处理(人工客服工作时间:9:00-18:30)。
第20章陶瓷粉体原料制备工艺§20.1 粉体制备工艺传统的粉体制备工艺就是机械破碎法,生产量大,成本低,但杂质混入不可避免。
随着先进陶瓷的发展,各种反应合成法得以应用,优点是纯度高、粒度小、成分均匀,但成本高。
20.1.1 传统粉体制备工艺以机械力使原材料变细的方法在陶瓷工业中应用极为广泛。
陶瓷原料进行破碎有利于提高成型坯体质量,提高致密程度并有利于烧结过程中各种物理化学反应的顺利进行,降低烧成温度。
一、颚式破碎机颚式破碎机是陶瓷工业化生产所经常采用的一种粗碎设备,主要用于块状料的前级处理。
设备结构简单,操作方便,产量高。
但颚式破碎机的粉碎比不大(约4),进料块度一般很大,因此出料粒度一般都较粗,而且粒度的调节范围也不大。
二、轧辊破碎机轧辊破碎机的优点在于粉碎效率高,粉碎比大(>60),粒度较细(通常可达到44 m)。
但当细磨硬质原料时,由于轧辊转速高,磨损大,使得粉料中混入较多的铁,影响原料纯度,要求后续去铁。
同时由于设备的特点,其粉料粒度分布比较窄,只宜用于处理有粒度分布要求的原料。
三、轮碾机轮碾机是陶瓷工业化生产所常采用的一种破碎设备,也可用于混合物料。
在轮碾机中,原料在碾盘与碾轮之间的相对滑动及碾轮的重力作用下被研磨、压碎。
碾轮越重、尺寸越大,粉碎力越强。
为了防止铁污染,经常采用石质碾轮和碾盘。
轮碾机的粉碎比大(约10),轮碾机处理的原料有一定的颗粒组成,要求的粒度越细,生产能力越低。
轮碾机也可采用湿轮碾的方法。
四、球磨机球磨机是工业生产普遍使用的细碎设备,也可用于混料。
为了保证原材料的纯度,经常采用陶瓷作为衬里,也可采用高分子聚合物材料作为衬里,并以各种陶瓷球作为研磨球。
湿球磨所采用的介质对原料表面的裂缝有劈裂作用,间歇式湿球磨的粉碎效率比干球磨高,湿球磨所得到的粉料粒度可达几个微米。
球磨机转速对球磨机效率的影响。
球磨机转速直接影响磨球在磨筒内的运动状态,转速过快,磨球附看在磨筒内壁,失去粉碎作用;转速太慢,低于临界转速太多,磨球在磨筒内上升不高就落下来,粉碎作用很小;当转速适当时,磨球紧贴在筒壁上,经过—段距离,磨球离开筒壁下落,给粉料以最大的冲击与研磨作用,具有最高的粉碎效率。
球磨机的临界转速与球磨筒直径有关,直径越大,临界转速越小。
它们之间的关系可用下列关系表示:D>1.25m,N=35/D1/2,D<1.25m,N=40/D1/2,其中N为接近临界转速的工作转速(r/min),D 为球磨筒有效内径(m)。
磨球对球磨机效率的影响。
球磨时加入磨球越多、破碎效率越高,但过多的磨球将占据有效空间,导致整体效率降低。
磨球的大小以及级配与球磨筒直径有关,可用公式:D(磨筒直径)/24>d(磨球最大直径)>90d0(原料粒度)来计算。
磨球的比表面积越大,研磨效能越高,但也不能太小,必须兼顾磨球对原料的冲击作用。
此外磨球的密度越大球磨效果越好。
水与电解质的加入量对球磨机效率的影响。
湿磨时水的加入对球磨效率也有影响,根据经验,当料/水=1/(1.16~1.2)时球磨效率最高;为了提高效率,还可加入电解质使原料颗粒表面形成胶粘吸附层,对颗粒表面的微裂缝发生劈裂作用、提高破碎效率。
例如加入0.5~1%亚硫酸纸浆废液或AlCl 3可提高效率30%。
装载量对球磨机效率的影响。
通常装料总量占磨筒空间的4/5,原料、磨球、水的重量比为1:(1.2~1.5):(1.0~1.2)。
原料原始颗粒度以及加料的先后顺序对球磨机效率也有影响。
五、气流磨气流磨或气流粉碎机可得到0.1~0.5μm 的微粉,工作原理是:压缩空气通过喷嘴在空间形成高速气流,使粉体在高速气流中相互碰撞达到粉碎的目的。
气流粉碎机破碎的粉料粒度分布均匀,粉碎效率高,能保证纯度,可在保护气体中粉碎。
六、振动磨振动磨具有很高的破碎效率。
振动磨是利用磨球在磨机中作高频振动将原料破碎,磨球除了有激烈的循环运动,还有激烈的自转运动。
对原料有很大的研磨作用,湿磨时粉料粒度可达到1μm 。
同时振动也能使原料本身存在的缺陷遭到破坏,达到粉碎的目的;振动磨的振动频率一股在50~100Hz ,装载系数为0.8~0.9体积(干磨),湿磨时为0.7,磨球与粉料的重量比为8:10。
a bcd e图20-1 机械破碎法,a 颚式破碎机,b 轧辊破碎机,c 轮碾机,d 球磨机,e 气流磨20.1.2 固相法制备陶瓷粉体固相法利用固态物质间所发生的各种固态反应来制取粉末。
在制备陶瓷粉体原料中常用 的固态反应包括化合反应、热分解反应和氧化物还原反应,但这几种反应在实际工艺过程中经常同时发生,使用固态法制备的粉末有时不能直接作为原料使用,需进一步加以粉碎。
● 化合反应:钛酸钡:BaCO 3+TiO 2=BaTiO 3+CO 2尖晶石:Al 2O 3+MgO=MgAl 2O 4莫来石:3Al 2O 3+2SiO 2=3Al 2O 3-2SiO 2● 热分解反应许多高纯氧化物粉末可以采用加热相应金属的硫酸盐、硝酸盐的方法,通过热分解制得性能优异的粉末,例如铝的硫酸铵盐在空气中加热,可以得到性能优异的氧化铝粉末。
● 氧化物还原反应高压空气碎料碳化硅和氮化硅是十分重要的先进工程陶瓷材料。
对于这两种陶瓷材料原料粉末的制备,在工业上经常采用氧化物还原法。
碳化硅:SiO2+3C=SiC+2CO硅:SiO2+2C=Si+2CO氮化硅:3SiO2+6C +4N2=2Si3N4+6CO●元素反应碳化硅:Si+C=SiC碳化硼:4B+C=B4C20.1.3 液相法制备陶瓷粉体使用液相法生产的超微粉已在先进陶瓷材料的制造中得到了广泛的应用。
液相法制备陶瓷粉末的主要优点在于能更好地控制粉末化学成分,在更高的(离子)水平上获得混合均匀的多成分复合粉末,并有利于微量成份的添加。
●沉淀法沉淀法的基本工艺路线是在金属盐溶液中施加或生成沉淀剂,并使溶液挥发,对所得到的盐和氢氧化物通过加热分解得到所需的陶瓷粉末。
这种方法能很好地控制组成,合成多元复合氧化物粉末,很方便地添加微量成分,得到很好的均匀混合。
但必须严格控制操作条件。
沉淀法分为直接沉淀法、均匀沉淀法和共沉淀法。
钛酸钡微粉可以来用直接沉淀法合成。
将Ba(OC3H7)和Ti(OC5H11)4溶解在异丙醇或苯中,加水水解,得到颗粒直径5~10nm的结晶良好的化学计量BaTiO3微粉,通过水解过程消除杂质,可显著提高粉料的化学纯度(纯度>99.98%),采用这种粉比用一般原料制得制品的介电常数要高得多。
钛酸钡微粉也可以采用共沉淀法合成,得到混合均匀的高纯粉料。
将氯化钡BaCl2和四氯化钛TiCl4均匀混合,得到原子尺度上的混合,一边搅拌,一边逐滴加入草酸溶液,得到BaTiO(C2H2)2·4H2O,经低温加热分解,得到具有化学计量组成且烧结性能良好的超微粒子。
●醇盐水解法采用这种方法能制得高纯度的粉料,粉料颗粒直径从几纳米到几十纳米,化学组成均匀。
钛酸钡微粉微粉可用这种方法制取。
增韧氧化锆(四方氧化锆)中稳定剂(Y2O3,CeO2等)的加入具有决定性的作用,为得到均匀弥散的分布,一般采用醇盐加水分解法制备粉料。
把锆或锆盐与乙醇—起反应合成锆的醇盐Zr(OR)4,同样的方法合成钇的醇盐Y(OR)3,把两者混合于有机溶剂中,加水使其分解,将水解生成的溶胶洗净,干燥,并在850℃燃烧得到粉料。
根据不同水解条件可得到从几纳米到几十纳米均匀化学组成的复合氧化锆粉料,由于金属醇盐水解不需添加其它离子,所以能获得高纯度成分。
●溶胶-凝胶法(Sol-Gel)将金属氧化物或氢氧化物的溶胶加以适当调整,在90~100℃加热形成凝胶物质,经过滤、脱水、干燥,再在适当的温度燃烧,就可制得高纯度超细氧化物粉末。
用这种方法制得的ThO2烧结性能良好,可在1150℃的较低温度下进行烧结,所得制品致密程度可达理论密度的99%。
溶胶-凝胶法也经常直接用于许多表面膜和复合材料的制备。
●水热法把锆盐等的水溶液放入高压釜中加热,通过与高压水的反应进行水解,可直接析晶得到纳米级ZrO2的超细粉。
●喷雾法采用液相法制取陶瓷细粉或超细粉工艺过程中所得到的粉料沉淀物或胶体经常需要水洗、过滤、干燥、煅烧。
这些工艺过程经常直接影响粉料成分的均匀性、颗粒大小以及形状。
采用喷雾的方法将溶液分散成小滴,使组分偏析程度达到最小,并使溶剂迅速蒸发,得到具有均匀尺寸与形状的粉料。
根据干燥方法的不同,可分为冷冻干燥法、喷雾干燥法,以及喷雾热分解法。
将金属盐的水溶液喷到低温有机液体中使液滴瞬间冰冻,然后在低温降压条件下升华、脱水,再通过热分解制得粉料,采用这种方法能制得组成均匀,反应性和烧结性良好的微粉。
在使用这种方法时,干燥过程不会造成冰凉液体的收缩,生成粉料的比表面积大,表面活性高。
将金属盐的水溶液分散成小液滴喷入热风中并使之迅速干燥得到β-Al2O3和铁氧体粉料,制备烧结体后具有较细的晶粒,这种方法也是一种广泛使用的造粒方法,经常被称为喷雾干燥法。
将金属盐的溶液喷入高温气氛中,引起溶剂蒸发和金属盐的热分解,从而直接合成氧化物粉料的方法称为喷雾热分解法(也经常称作雾热焙烧法、火焰雾化法、溶液蒸发分解法(EDS)。
喷雾热分解法可以把溶液喷到加热的反应器中,也可直接喷到高温火焰中。
金属盐的溶剂则经常采用可燃性的,如乙醇,以利用其燃烧热。
喷雾热分解法不仅具备冰冻干燥法和喷雾干燥法的优点,还可以用于在后续热分解过程中产生熔融金属盐的情况。
20.1.4 气相法制备陶瓷粉体气相法制备陶瓷粉料的方法有两种:蒸发-凝聚法(PVD)和气相沉积法(CVD)。
将原料用电弧或等离子体加热至气化,然后在加热源和环境之间很大的温度梯度条件下急冷,凝聚成粉状颗粒。
颗粒尺寸可达5~100nm。
适用于制备单相氧化物、复合氧化物、碳化物和金属微粉。
化学气相反应法是采用挥发性金属化合物蒸气通过化学反应合成所需物质的方法。
气相化学反应可分为两类:一类为单一化合物的热分解;另一类为两种以上化学物质之间的反应。
气相化学反应法制备陶瓷粉料的特点是:①纯度高,生成粉料无需粉碎;②生成粉料的分散性良好;③颗粒直径分布窄;④容易控制气氛;⑤适用于制备多种不同的陶瓷粉料。
TiCl4+O2=TiO2+2Cl2SiCl4+O2=SiO2+2Cl23SiCl4+4NH3=Si3N4+12HCl3SiH4+4NH3=Si3N4+12H2SiCl4、SiH4与CH4、C3H8 等反应生成β-SiC。
SiCH3Cl3、Si(CH3)2Cl2、Si(CH3)4 热解生成SiC。
§20.2 粉体的表征与测量20.2.1 粉体的表征一、颗粒大小与形状如果给出一个球形颗粒,要确定其颗粒大小,很自然要测量其直径。
如果摆放着一些其它形状的颗粒,合理的办法是根据一些特性把颗粒等效为一个球形颗粒,以解决这一难题。