需要重新设定参考点
回参考点
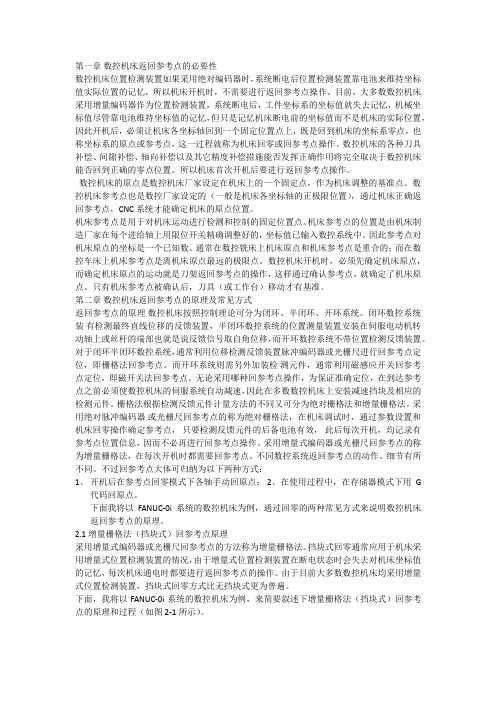
第一章数控机床返回参考点的必要性数控机床位置检测装置如果采用绝对编码器时,系统断电后位置检测装置靠电池来维持坐标值实际位置的记忆,所以机床开机时,不需要进行返回参考点操作。
目前,大多数数控机床采用增量编码器作为位置检测装置,系统断电后,工件坐标系的坐标值就失去记忆,机械坐标值尽管靠电池维持坐标值的记忆,但只是记忆机床断电前的坐标值而不是机床的实际位置,因此开机后,必须让机床各坐标轴回到一个固定位置点上,既是回到机床的坐标系零点,也称坐标系的原点或参考点,这一过程就称为机床回零或回参考点操作。
数控机床的各种刀具补偿、间隙补偿、轴向补偿以及其它精度补偿措施能否发挥正确作用将完全取决于数控机床能否回到正确的零点位置。
所以机床首次开机后要进行返回参考点操作。
数控机床的原点是数控机床厂家设定在机床上的一个固定点,作为机床调整的基准点。
数控机床参考点也是数控厂家设定的(一般是机床各坐标轴的正极限位置),通过机床正确返回参考点,CNC系统才能确定机床的原点位置。
机床参考点是用于对机床运动进行检测和控制的固定位置点。
机床参考点的位置是由机床制造厂家在每个进给轴上用限位开关精确调整好的,坐标值已输入数控系统中。
因此参考点对机床原点的坐标是一个已知数。
通常在数控铣床上机床原点和机床参考点是重合的;而在数控车床上机床参考点是离机床原点最远的极限点。
数控机床开机时,必须先确定机床原点,而确定机床原点的运动就是刀架返回参考点的操作,这样通过确认参考点,就确定了机床原点。
只有机床参考点被确认后,刀具(或工作台)移动才有基准。
第二章数控机床返回参考点的原理及常见方式返回参考点的原理数控机床按照控制理论可分为闭环、半闭环、开环系统。
闭环数控系统装有检测最终直线位移的反馈装置,半闭环数控系统的位置测量装置安装在伺服电动机转动轴上或丝杆的端部也就是说反馈信号取自角位移,而开环数控系统不带位置检测反馈装置。
对于闭环半闭环数控系统,通常利用位移检测反馈装置脉冲编码器或光栅尺进行回参考点定位,即栅格法回参考点。
数控机床原点、参考点、工作零点的区别和联系
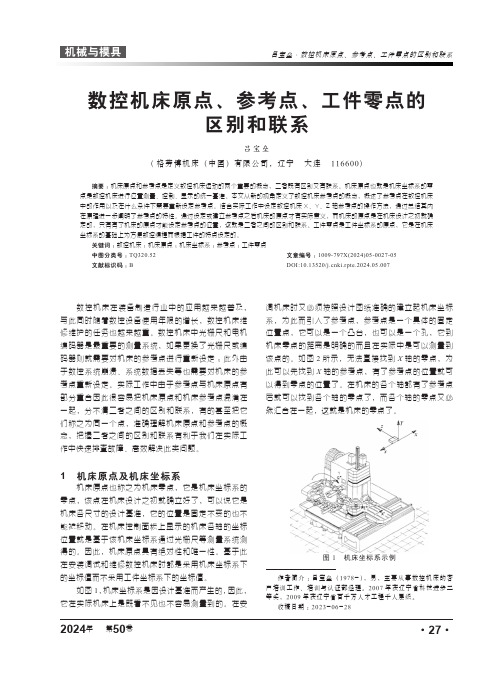
作者简介:吕宝垒(1978-),男,主要从事数控机床的客户培训工作、培训与认证部经理。
2007年获辽宁省科技进步二等奖,2009年获辽宁省百千万人才工程千人层级。
收稿日期:2023-06-28数控机床在装备制造行业中的应用越来越普及,与此同时随着数控设备使用年限的增长,数控机床维修维护的任务也越来越重。
数控机床中光栅尺和电机编码器是最重要的测量系统,如果更换了光栅尺或编码器则就需要对机床的参考点进行重新设定;此外由于数控系统崩溃、系统数据丢失等也需要对机床的参考点重新设定。
实际工作中由于参考点与机床原点有部分重合因此很容易把机床原点和机床参考点混淆在一起,分不清二者之间的区别和联系,有的甚至把它们称之为同一个点,准确理解机床原点和参考点的概念,把握二者之间的区别和联系有利于我们在实际工作中快速排查故障、高效解决此类问题。
1 机床原点及机床坐标系机床原点也称之为机床零点,它是机床坐标系的零点,该点在机床设计之初就确立好了,可以说它是机床各尺寸的设计基准,它的位置是固定不变的也不能被移动。
在机床控制面板上显示的机床各轴的坐标位置就是基于该机床坐标系通过光栅尺等测量系统测得的。
因此,机床原点具有绝对性和唯一性。
基于此在安装调试和维修数控机床时都是采用机床坐标系下的坐标值而不采用工件坐标系下的坐标值。
如图1,机床坐标系是因设计基准而产生的,因此,它在实际机床上是既看不见也不容易测量到的。
在安数控机床原点、参考点、工件零点的区别和联系吕宝垒(格劳博机床(中国)有限公司,辽宁 大连 116600)摘要:机床原点和参考点是定义数控机床运动的两个重要的概念,二者既有区别又有联系。
机床原点也就是机床坐标系的零点是数控机床进行位置测量、控制、显示的统一基准。
本文从新的视角定义了数控机床参考点的概念,概述了参考点在数控机床中的作用以及在什么条件下需要重新设定参考点。
结合实际工作中设定数控机床X、Y、Z 轴参考点的操作方法,通过总结其内在原理进一步阐明了参考点的特性。
数控机床回参考点设置方法

摘要:发那科、三菱,西门子几种常用数控系统参考点的工作原理、调整和设定方法,并举例说明参考点的故障现象,解决方法。
关键词:参考点相对位置检测系统绝对位置检测系统1 概述当数控机床更换、拆卸电机或编码器后,机床会有报警信息:编码器内的机械绝对位置数据丢失了,或者机床回参考点后发现参考点和更换前发生了偏移,这就要求我们重新设定参考点,所以我们对了解参考点的工作原理十分必要。
参考点是指当执行手动参考点回归或加工程序的G28指令时机械所定位的那一点,又名原点或零点。
每台机床有一个参考点,根据需要也可以设置多个参考点,用于自动刀具交换(ATC)、自动拖盘交换(APC)等。
通过G28指令执行快速复归的点称为第一参考点(原点),通过G30指令复归的点称为第二、第三或第四参考点,也称为返回浮动参考点。
由编码器发出的栅点信号或零标志信号所确定的点称为电气原点。
机械原点是基本机械坐标系的基准点,机械零件一旦装配好,机械参考点也就建立了。
为了使电气原点和机械原点重合,将使用一个参数进行设置,这个重合的点就是机床原点。
机床配备的位置检测系统一般有相对位置检测系统和绝对位置检测系统。
相对位置检测系统由于在关机后位置数据丢失,所以在机床每次开机后都要求先回零点才可投入加工运行,一般使用挡块式零点回归。
绝对位置检测系统即使在电源切断时也能检测机械的移动量,所以机床每次开机后不需要进行原点回归。
由于在关机后位置数据不会丢失,并且绝对位置检测功能执行各种数据的核对,如检测器的回馈量相互核对、机械固有点上的绝对位置核对,因此具有很高的可信性。
当更换绝对位置检测器或绝对位置丢失时,应设定参考点,绝对位置检测系统一般使用无挡块式零点回归。
2 使用相对位置检测系统的参考点回归方式:(1)发那科系统:1)工作原理:当手动或自动回机床参考点时,首先,回归轴以正方向快速移动,当挡块碰上参考点接近开关时,开始减速运行。
当挡块离开参考点接近开关时,继续以FL速度移动。
FANUC-3M 31号报警
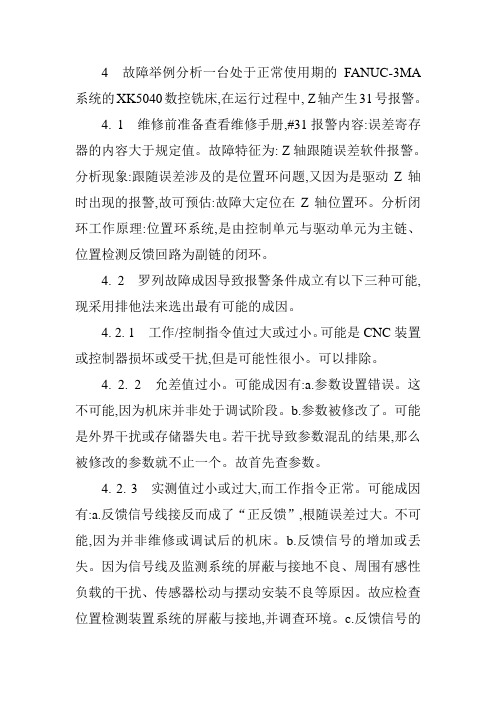
4故障举例分析一台处于正常使用期的FANUC-3MA 系统的XK5040数控铣床,在运行过程中, Z轴产生31号报警。
4. 1维修前准备查看维修手册,#31报警内容:误差寄存器的内容大于规定值。
故障特征为: Z轴跟随误差软件报警。
分析现象:跟随误差涉及的是位置环问题,又因为是驱动Z轴时出现的报警,故可预估:故障大定位在Z轴位置环。
分析闭环工作原理:位置环系统,是由控制单元与驱动单元为主链、位置检测反馈回路为副链的闭环。
4. 2罗列故障成因导致报警条件成立有以下三种可能,现采用排他法来选出最有可能的成因。
4. 2. 1工作/控制指令值过大或过小。
可能是CNC装置或控制器损坏或受干扰,但是可能性很小。
可以排除。
4. 2. 2允差值过小。
可能成因有:a.参数设置错误。
这不可能,因为机床并非处于调试阶段。
b.参数被修改了。
可能是外界干扰或存储器失电。
若干扰导致参数混乱的结果,那么被修改的参数就不止一个。
故首先查参数。
4. 2. 3实测值过小或过大,而工作指令正常。
可能成因有:a.反馈信号线接反而成了“正反馈”,根随误差过大。
不可能,因为并非维修或调试后的机床。
b.反馈信号的增加或丢失。
因为信号线及监测系统的屏蔽与接地不良、周围有感性负载的干扰、传感器松动与摆动安装不良等原因。
故应检查位置检测装置系统的屏蔽与接地,并调查环境。
c.反馈信号的滞后,在规定的监测时间内信号未到达而使实测值为0。
用久的机床上易发生:位置传感器的污染、信号线的损坏以及接触不良、位置偏移或损坏等。
故应检查位置检测装置系统及其接线系统。
d.没有反馈信号。
a)传感器未安装或连接、传感器损坏而不工作。
故应检查位置检测装置中传感器系统。
b)伺服单元故障不工作/伺服轴不动作。
分析判断得出:最可能故障类型:硬件故障。
最可能的故障成因出于位置检测装置系统(故障大定位),也不能排除环境干扰因素。
4. 3确定诊断步骤4. 3. 1现场工作步骤:环境调查→接口信号法检查位置环参数→信号追踪法检查位检系统,进行故障定位。
西门子回参考点

机床回参考点有两种情况:一种是绝对值式的,一种是增量式的。
对于增量式的来说又分为零脉冲在参考点开关之外和零脉冲在参考点开关之上。
这两种情况由机床数据MD34050 REFP_SEARCH_MARKER_REVERSE[0][编码器零脉冲在参考点开关的反向(编码器号)]来决定。
当MD34050=1时用上升沿触发,而MD34050=0用下降沿触发。
增量式的回参相对来说比较麻烦,它需要在每次开机或者传输程序后会造成参考点丢失,都要重新会参考点。
为了防止发生事故可以设置MD20700 REFP_NC_START_LOCK=1(未回参考点NC 启动禁止)来保护机床。
对于增量式来说有以下几种方式会参考点:1 手动方式回参:它是通过设置相应的参数,然后点击MCP上的Reform键触发,至于回参的方向则由MD 34010 REFP_CAM_DIR_IS_MINUS(负向逼近参考点)的值来决定。
如果按错方向键或者按键的过程中中断则程序没有反映或者回参失败。
2 触发方式回参:它是通过MD11300 JOG-INC-MODE-LEVELTRIGGRD(返回参考点触发方式)来决定的。
将该数据设置为0时,只需要点击相应的方向键,方向还是由MD34010来决定。
如果按错后程序没有反映。
它只需要点击相应的方向键一下就可以自动回参考点。
其实并不只对进给轴有效,对主轴也也可以有效,那就是与机床参数MD34200ENC_REFP_MODE[n]有关。
当该数据为1时,主轴也可以采用触发方式回参,那就意味着我们可能不是用Bero回参了。
如果有多个进给轴的话,它们可以按照顺序回参,顺序在MD34110 REFP_CYCLE_NR 中定义,也可以都定义为同一个那么所有的轴就是同时进行。
3 通道方式回参:使用接口信号“使能回参考点”(V32000001.0)启动通道专用回参考点运行。
系统使用信号“回参考点有效”(V33000001.0)响应成功启动。
浅谈数控机床回参考点及故障分析处理
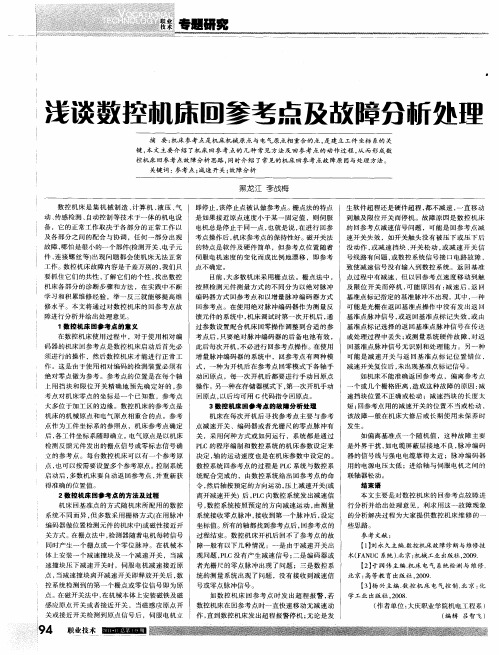
摘 要: 机床 参考点是机床机械 原点与 电气原点 相重合的 点, 是建立工件 坐标 系的关
键, 本文主要介 绍 了机床 回参 考点 的几种 常见方 法及回参 考点 的动作过 程 , 而形成数 从
控机床 回参考点故障分析 思路 , 同时介 绍 了常见的机床 回参 考点故障原 因与处理方法 。
得准 确的位置值 。
关 ,采用何种 方式或如 何运行 ,系统都 是通 过 P C的程 序编制 和数控 系统 的机 床参数 设定来 L
决 定 , 的运动速度 也是在机 床参数 中设定 的。 轴 数 控系统 回参考点 的过程是 P C系统与数控 系 L 统 配合完 成的 ,由数控 系统给 出 回参 考点 的命
速挡块 位置不 正确或松动 ;减 速挡块 的长度 太 短; 回参考点 用的减速 开关的位 置不 当或松 动 , 该 故障一般在 机床大修 后或 长期使用 未保 养 时
发生 。
检测 反馈元件 发 出的栅 点信号 或零标志 信号确
立 的参考点 。每 台数 控机床 可以有一个 参考 原 点 , 可以按需要设 置多个参考原 点。控制 系统 也 启动 后 , 多数 机床要 自动返 回参考点 , 并重新 获
关键 词 : 参考点 ; 减速 开关 ; 故障 分析
黑龙江 李 战梅
数控 机床 是集 机械 制 造 、 计算 机 、 液压 、 气
即停 止 , 该停止点被认 做参考点 。 栅点法 的特点
是 如果接近 原点速度小 于某一 固定值 ,则伺 服 电机 总是停 止于 同一点 , 也就是说 , 在进 行 回参 考 点操作后 , 机床参 考点的保持性好 。磁 开关 法 的特点是软 件及硬件 简单 ,但参 考点位 置 随着 伺 服电机速 度的变化 而成 比例地漂移 ,即参 考 点 不确定 。 目前 , 多数机床采 用栅点 法 。栅 点法 中 , 大 按 照检测元 件测量方 式 的不 同分为 以绝对 脉冲 编 码器方式 回参考点 和 以增量 脉冲 编码 器方 式 回参考点 。在使用绝 对脉 冲编码器作 为测 量反 馈 元件 的系统 中, 床调试 时第 一次 开机后 , 机 通 过参数设 置配合机床 回零操 作调整 到合适 的参 考点后 , 只要绝对 脉冲编码 器的后备 电池有 效 , 此后每次 开机 , 不必进行 回参考 点操作 。在使用
FANUC 0系统如何保护你的参数和程序不被修改
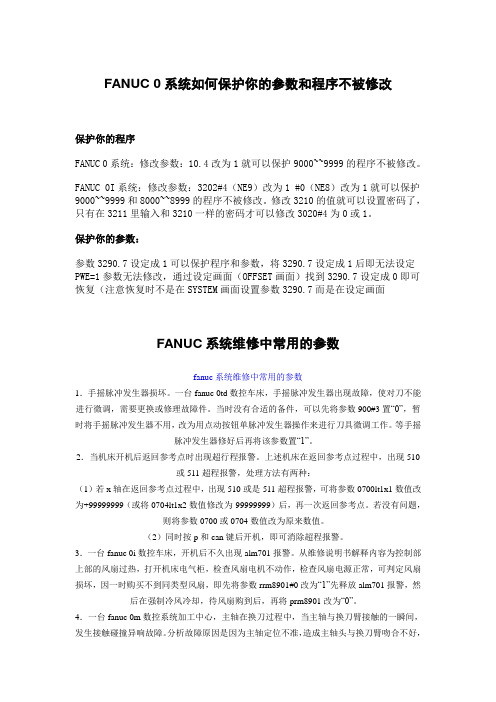
FANUC 0系统如何保护你的参数和程序不被修改保护你的程序FANUC 0系统:修改参数:10.4改为1就可以保护9000~~9999的程序不被修改。
FANUC 0I系统:修改参数:3202#4(NE9)改为1 #0(NE8)改为1就可以保护9000~~9999和8000~~8999的程序不被修改。
修改3210的值就可以设置密码了,只有在3211里输入和3210一样的密码才可以修改3020#4为0或1。
保护你的参数:参数3290.7设定成1可以保护程序和参数,将3290.7设定成1后即无法设定PWE=1参数无法修改,通过设定画面(OFFSET画面)找到3290.7设定成0即可恢复(注意恢复时不是在SYSTEM画面设置参数3290.7而是在设定画面FANUC系统维修中常用的参数fanuc系统维修中常用的参数1.手摇脉冲发生器损坏。
一台fanuc 0td数控车床,手摇脉冲发生器出现故障,使对刀不能进行微调,需要更换或修理故障件。
当时没有合适的备件,可以先将参数900#3置“0”,暂时将手摇脉冲发生器不用,改为用点动按钮单脉冲发生器操作来进行刀具微调工作。
等手摇脉冲发生器修好后再将该参数置“1”。
2.当机床开机后返回参考点时出现超行程报警。
上述机床在返回参考点过程中,出现510或511超程报警,处理方法有两种:(1)若x轴在返回参考点过程中,出现510或是511超程报警,可将参数0700lt1x1数值改为+99999999(或将0704lt1x2数值修改为-99999999)后,再一次返回参考点。
若没有问题,则将参数0700或0704数值改为原来数值。
(2)同时按p和can键后开机,即可消除超程报警。
3.一台fanuc 0i数控车床,开机后不久出现alm701报警。
从维修说明书解释内容为控制部上部的风扇过热,打开机床电气柜,检查风扇电机不动作,检查风扇电源正常,可判定风扇损坏,因一时购买不到同类型风扇,即先将参数rrm8901#0改为“1”先释放alm701报警,然后在强制冷风冷却,待风扇购到后,再将prm8901改为“0”。
FANUC系统四种返回参考点方法

四种返回参考点方法综述返回参考点的方法有4种:1) 栅格法;2)手动输入法;3)双MARK法;4) 扭矩法。
4.1栅格法:栅格法适用围最广;即适用于半闭环系统,也适用于全闭环系统;即适用于增量型位置反应元件,也适用于绝对型位置反应元件。
栅格法分两种情况:1〕有回零减速开关;2〕无回零减速开关。
4.1.1 有回零减速开关:1) 有关的参数:P1002(1)=0,且P1005(1)=0:有减速开关。
P1006(5):确定回零方向。
0:正向;1:负向。
注:回零方向和回零时的运动方向是两个概念。
P3003(5):减速开关有效状态。
0:“0〞有效;1:“1〞有效。
P1424:回零快速速度。
压减速开关前的速度。
注:假设P1424=0,以P1420*快速倍率的速度运行。
P1425:回零低速速度。
压上减速开关后降至到此速度。
P1850:栅格偏移量。
脱开减速开关找到第一个MARK点后,伺服轴偏移的距离。
P1240:第一参考点的坐标值。
返回参考点完成后,机床坐标系变为P1240设定的值。
2) 有关的PMC状态:方式:G43(0,1,2,7)=(1,0,1,1);返回参考点〔REF〕方式。
运动方向:G100(0-7);分别控制8个轴返回参考点时的正向运动;G102(0-7);分别控制8个轴返回参考点时的负向运动。
注:运动方向与P1006(5)的回零方向是两个概念。
减速开关:*9(0-7) 分别代表8个轴的减速开关;注:减速开关是“0〞有效还是“1〞有效,取决于P3003(5)。
回零完成:F120(0-7) =1 分别表示8个轴的参考点已经建立;注:使用增量型反应元件的轴,在不断电的时,保持为“1〞,断电后为“0〞;使用绝对型反应元件的轴,断电后也保持为“1〞。
F94(0-7)=1 分别表示返回参考点完成,且在参考点上。
注:当轴移动后,便为“0〞。
3)回零过程(以*轴回零为例):将操作方式置成回零方式,G43(0,1,2,7)=(1,0,1,1)。
数控机床回参考点的探索

数控机床回参考点的探索作者:史晓龙洪超来源:《智能制造》2020年第09期摘要:本文阐述了什么是参考点,参考点与机床原点(零点)之间的关系,回参考点的作用与意义,参考点与位置编码器的之间的关系,针对使用FANUC系统,不同位置编码器的数控机床而采用的有挡块、无挡块和标记点三种设置参考点的方式,给出了具体的设置参数、设置方法和操作步骤,为数控机床操作和调试提供一定的帮助。
关键词:参考点;机床原点;位置编码器;有挡块无挡块标记点1 参考点与机床原点参考点是指数控机床上某一固定位置的特定点。
通常数控系统启动后,首先要做的工作就是回参考点操作,也称回机床原点或回零操作。
回参考点是数控机床的重要功能,也是机床操作人员操作数控机床时最常见的操作。
数控机床在加工零件时,数控系统通过发出各种程序指令来控制刀具和机床的运动。
为了准确地控制运动的方向和移动的距离,就有必要在机床上建立一坐标系作为加工的基准,这个加工基准就是机床坐标系。
因为机床各轴的正方向是统一规定好的,所以只要确定了机床坐标系原点(零点)的位置,也就确定了机床坐标系的位置。
机床坐标系是机床固有的坐标系,是制造和调整机床的基础,坐标系的原点是机床生产厂家在设计机床时就已经确定好的,用户不能随意更改,且机床原点只是一个设计定义的点,不方便被直接测量定位。
那怎样才能找到机床原点的准确位置呢?方法是通过回参考点。
机床参考点是数控机床上人为设置的一个固定位置的点,通常是设在各个轴正方向行程的极限位置处。
这样,只要通过指定机床参考点到机床原点之间的距离,并始终保持二者之间的固定位置关系,就可以通过直接定位参考点位置的同时间接确定机床原点的位置。
确定了机床原点(零点),也就确定了机床坐标系和加工的基准。
机床参考点与机床原点可以是同一点,也可以不是。
通常数控铣削类机床的参考点与机床原点是重合的,分别在 X轴、Y轴和Z轴的正向行程最大极限处。
而数控车床上的参考点与机床原点就不在同一点.机床原点位于卡盘回转中心与端面相交的中心。
840D的轴原点重新设置

关于840D的轴原点重新设置如果是增量的测量系统你可以有两种方法来重新定义零点:第一,在MD34100中设定数值,并用此数值来表示当前的坐标值。
第二,在MD34080中设定数值使测量系统找到零脉冲后继续运动此数值停止,停止的位置为坐标零点。
绝对测量系统可以采用第一种方法,这其中你得掌握绝对测量系统重设坐标的步骤。
MD34200及MD34210设为零后重启系统,系统启动后MD34100设定你要的数值,34210设为1后按复位键,接着在回参考点方式下按轴移动方向键,搞定。
通过参数设置已经能够达到原点重新定位的功能。
中间加了个M 指令来执行原点重新定位。
后来又将用操作面板按钮将DB2*.DBX1.0激活,增加了不在原点启动NC的功能。
22 旋转轴是可以在任意位置设为零点的。
4.BERO回参:对于主轴而言还有一种常用回参方法就是利用外部BERO来回参考点。
它的基本原理就是在执行SPOS??命令时,主轴由静止启动,主轴加速到MD34040??定义的速度,与接近开关同步,并且以MD35300??定义的速度定位。
主轴旋转方向由机床数据MD35350 确定。
常用的基本参数设置如下:34200??ENC_REFP_MODE=??7 接近开关作为主轴定向信号34040??REFP_VELO_SEARCH_MARKER??实际值??主轴定向速度(单位:转/分)34060??REFP_MAX_MARKER_DIST??=720??搜索接近开关的距离(单位:度)35300??SPOS_POSCTRL_VELO??实际值??主轴位控速度35350??SPOS_POSITIONING_DIR??3/4??主轴定向方向(3-正/4-负)另外还需要更改驱动参数:修改驱动数据:进入系统画面[SHIFT]+[ALARM],进入[机床数据]→[驱动器数据] 选相应的主轴参数SERVO?? 选择[显示参数]:如果主轴BERO信号接到x20的端子设定参数P495[0]=2;如果接到x21的端子上则设定参数P495[0]=5,然后设定P971=1,等待P971??由1??变0或者点击数据存储软件保存数据。
几种机床系统的原点回归方式
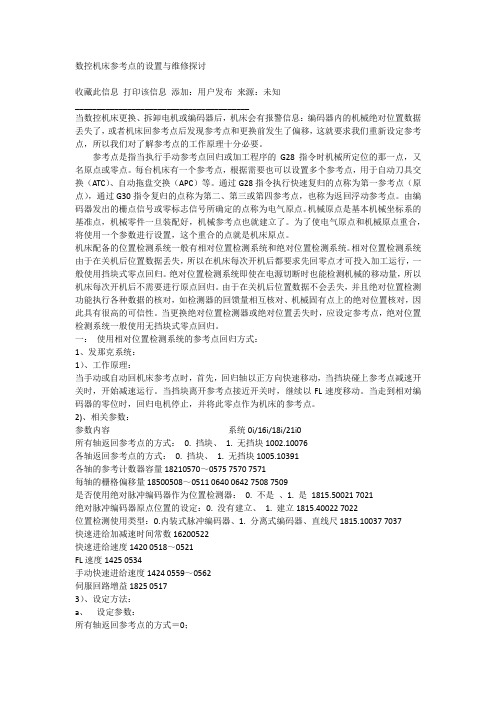
数控机床参考点的设置与维修探讨收藏此信息打印该信息添加:用户发布来源:未知________________________________________当数控机床更换、拆卸电机或编码器后,机床会有报警信息:编码器内的机械绝对位置数据丢失了,或者机床回参考点后发现参考点和更换前发生了偏移,这就要求我们重新设定参考点,所以我们对了解参考点的工作原理十分必要。
参考点是指当执行手动参考点回归或加工程序的G28指令时机械所定位的那一点,又名原点或零点。
每台机床有一个参考点,根据需要也可以设置多个参考点,用于自动刀具交换(ATC)、自动拖盘交换(APC)等。
通过G28指令执行快速复归的点称为第一参考点(原点),通过G30指令复归的点称为第二、第三或第四参考点,也称为返回浮动参考点。
由编码器发出的栅点信号或零标志信号所确定的点称为电气原点。
机械原点是基本机械坐标系的基准点,机械零件一旦装配好,机械参考点也就建立了。
为了使电气原点和机械原点重合,将使用一个参数进行设置,这个重合的点就是机床原点。
机床配备的位置检测系统一般有相对位置检测系统和绝对位置检测系统。
相对位置检测系统由于在关机后位置数据丢失,所以在机床每次开机后都要求先回零点才可投入加工运行,一般使用挡块式零点回归。
绝对位置检测系统即使在电源切断时也能检测机械的移动量,所以机床每次开机后不需要进行原点回归。
由于在关机后位置数据不会丢失,并且绝对位置检测功能执行各种数据的核对,如检测器的回馈量相互核对、机械固有点上的绝对位置核对,因此具有很高的可信性。
当更换绝对位置检测器或绝对位置丢失时,应设定参考点,绝对位置检测系统一般使用无挡块式零点回归。
一:使用相对位置检测系统的参考点回归方式:1、发那克系统:1)、工作原理:当手动或自动回机床参考点时,首先,回归轴以正方向快速移动,当挡块碰上参考点减速开关时,开始减速运行。
当挡块离开参考点接近开关时,继续以FL速度移动。
编码器报警
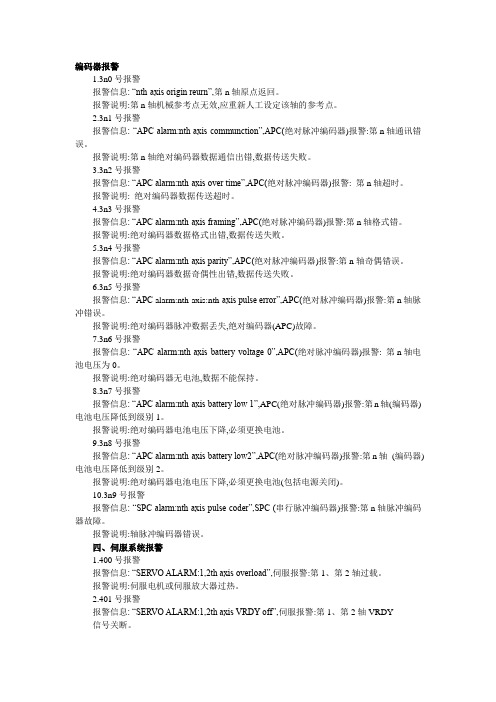
编码器报警1.3n0号报警报警信息: “nth-axis origin reurn”,第n轴原点返回。
报警说明:第n轴机械参考点无效,应重新人工设定该轴的参考点。
2.3n1号报警报警信息: “APC alarm:nth-axis communction”,APC(绝对脉冲编码器)报警:第n轴通讯错误。
报警说明:第n轴绝对编码器数据通信出错,数据传送失败。
3.3n2号报警报警信息: “APC alarm:nth-axis over time”,APC(绝对脉冲编码器)报警: 第n轴超时。
报警说明: 绝对编码器数据传送超时。
4.3n3号报警报警信息: “APC alarm:nth-axis framing”,APC(绝对脉冲编码器)报警:第n轴格式错。
报警说明:绝对编码器数据格式出错,数据传送失败。
5.3n4号报警报警信息: “APC alarm:nth-axis parity”,APC(绝对脉冲编码器)报警:第n轴奇偶错误。
报警说明:绝对编码器数据奇偶性出错,数据传送失败。
6.3n5号报警报警信息: “APC alarm:nth-axis:nth-axis pulse error”,APC(绝对脉冲编码器)报警:第n轴脉冲错误。
报警说明:绝对编码器脉冲数据丢失,绝对编码器(APC)故障。
7.3n6号报警报警信息: “APC alarm:nth-axis battery voltage 0”,APC(绝对脉冲编码器)报警: 第n轴电池电压为0。
报警说明:绝对编码器无电池,数据不能保持。
8.3n7号报警报警信息: “APC alarm:nth-axis battery low 1”,APC(绝对脉冲编码器)报警:第n轴(编码器)电池电压降低到级别1。
报警说明:绝对编码器电池电压下降,必须更换电池。
9.3n8号报警报警信息: “APC alarm:nth-axis battery low2”,APC(绝对脉冲编码器)报警:第n轴(编码器) 电池电压降低到级别2。
加工中心设置零点两种方法
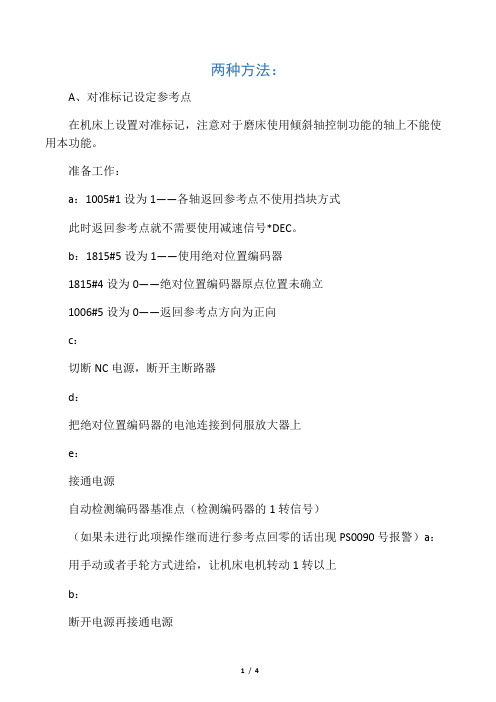
两种方法:A、对准标记设定参考点在机床上设置对准标记,注意对于磨床使用倾斜轴控制功能的轴上不能使用本功能。
准备工作:a:1005#1设为1——各轴返回参考点不使用挡块方式此时返回参考点就不需要使用减速信号*DEC。
b:1815#5设为1——使用绝对位置编码器1815#4设为0——绝对位置编码器原点位置未确立1006#5设为0——返回参考点方向为正向c:切断NC电源,断开主断路器d:把绝对位置编码器的电池连接到伺服放大器上e:接通电源自动检测编码器基准点(检测编码器的1转信号)(如果未进行此项操作继而进行参考点回零的话出现PS0090号报警)a:用手动或者手轮方式进给,让机床电机转动1转以上b:断开电源再接通电源设定参考点a:JOG方式下对各轴手动移动,将机床移动到1006#5设定的反方向处,例如上面设的1006#5为0即返回参考点方向为正向,则将机床移至负向,如下图:b:按1006#5设定的返回参考点的方向移动机床,直至机床对准标记与参考点位置重合,当位置快要重合时使用手轮进给进行微调。
c:将1815#4设为1——绝对位置编码器原点位置已确立。
B、无挡块返回参考点不需要安装限位开关和挡块准备工作:a:1005#1设为1——各轴返回参考点不使用挡块方式此时返回参考点就不需要使用减速信号*DEC。
b:1815#5设为1——使用绝对位置编码器1815#4设为0——绝对位置编码器原点位置未确立1006#5设为0——返回参考点方向为正向c:切断NC电源,断开主断路器d:把绝对位置编码器的电池连接到伺服放大器上e:接通电源自动检测编码器基准点(检测编码器的1转信号)(如果未进行此项操作继而进行参考点回零的话出现PS0090号报警)a:用手动或者手轮方式进给,让机床电机转动1转以上b:断开电源再接通电源设定参考点a:JOG方式下对各轴手动移动至参考点返回方向的反方向,然后以1006#5设置的方向向参考点移动。
FANUC数控机床参考点丢失后建立方法

() 5 调节阀门特性 曲线与调节系统静态特性曲线不相符 。 机 组正常状态下 , 动机活塞行程相当于调节汽 门开度 , 油 随着调节
汽门开度增 大,即油动机活塞行程增大 ,汽轮机功率也随之增
大。调节阀门特性 曲线即是油动机行程和汽轮机 功率之问 的关 系曲线 。 在某一功率下 , 根据调节阀门特性曲线可得到对应 的油 动机活塞行 程和调节汽 门开度 ,再根据调速汽门开度得到相对
栅点法 回机床原点根据采用 的编码器不 同有 :挡块 式回参
考 点 、 块 式 回参考 点 及 无 挡 块 或撞 块 时 回参 考 点 。 照 检 测 元 撞 按
测反馈元件所发 出的栅点信号或零标志信号确立的参考点 。为
了使电气原点与机械原点重合 ,必须将 电气原点到机械原点 的
件测量方式的不 同分为绝对脉冲编码器和增量脉冲编码器方式
应的汽轮机转速 。汽轮机功率和汽轮机转速之间的关 系曲线即
是 调节 系统静态特性 曲线 。 机 组负荷在 2 MW 以下运行时 , 组加减 负荷时均平稳正 2 机
圈 设 管 与 修 22 5 置 理 维 0 № 1
运行正常 。
() 2 汽轮机调节系统故障。进行调节系统静态试验 , 输入模
拟信号调节油动机行程 , 对应汽轮 机调速汽 门开度符合要求 。
() 3 电液 转 换 器 故 障 或 控 制油 压 力 问题 。 换 1台新 电 液 转 更
换器 , 调整 电控供油系统 中的溢 流阀 , 保持 系统 油压 , 机组甩 负 荷现象没有改善 。 () 4 调节阀故 障。测量调节阀操纵座连杆滚轮与凸轮 间隙 ,
在 2 MW 以上 运 行 时 , 节 阀 门特 性 曲线 与 调 节 系统 静 态 特 性 2 调 曲线 不 相符 是 造 成 发 电机 组 甩 负 荷 的 主 要 原 因 。
FANUC系统四种返回参考点方法

四种返回参考点方法综述返回参考点的方法有4种:1)栅格法;2)手动输入法;3)双MARK 法;4)扭矩法。
4.1栅格法:栅格法适用范围最广;即适用于半闭环系统,也适用于全闭环系统; 即适用于增量型位置反馈元件,也适用于绝对型位置反馈元件。
栅格法分两种情况:1)有回零减速开关;2)无回零减速开关。
4.1.1有回零减速开关:1)有关的参数:P1002(1)=0,且 P1005(1)=0:有减速开关。
P1006(5):确定回零方向。
0:正向;1:负向。
注:回零方向和回零时的运动方向是两个概念。
P3003(5):减速开关有效状态。
0:“0”有效;1:“1”有效。
P1424:回零快速速度。
压减速开关前的速度。
注:若P1424=0,以P1420*快速倍率的速度运行。
P1425:回零低速速度。
压上减速开关后降至到此速度。
P1850:栅格偏移量。
脱开减速开关找到第一个MARK点后,伺服轴偏移的距离。
P1240:第一参考点的坐标值。
返回参考点完成后,机床坐标系变为P1240设定的值。
2)有关的PMC状态:方式:G43(0,1,2,7) = (1,0,1,1);返回参考点(REF)方式。
运动方向:G100(0-7);分别控制8个轴返回参考点时的正向运动;G102(0-7);分别控制8个轴返回参考点时的负向运动。
注:运动方向与P1006(5)的回零方向是两个概念。
减速开关:X9(0-7)分别代表8个轴的减速开关;注:减速开关是“0”有效还是“1”有效,取决于P3003(5)。
回零完成:F120(0-7) =1分别表示8个轴的参考点已经建立;注:使用增量型反馈元件的轴,在不断电的时,保持为“1”,断电后为“0”;使用绝对型反馈元件的轴,断电后也保持为“1”。
F94(0-7)=1分别表示返回参考点完成,且在参考点上。
注:当轴移动后,便为“0”。
3)回零过程(以X轴回零为例):将操作方式置成回零方式,G43(0,1,2, 7) = (1,0,1,1)。
参考点的设置(Fanuc

1、发那克系统:
1)、工作原理:
当手动或自动回机床参考点时,首先,回归轴以正方向快速移动,当挡块碰上参考点接近开关时,开始减速运行。当挡块离开参考点接近开关时,继续以FL速度移动。当走到相对编码器的零位时,回归电机停止,并将此零点作为机床的参考点。
b、选择“手动”模式,将控制轴移动到参考点附近;
c、输入参数:MD34100,机床坐标位置;
d、激活绝对编码器的调整功能:MD34210=1.绝对编码器调整状态;
e、按机床复位键,使机床参数生效;
f、机床回归参考点;
g、机床不移动,系统自动设置参数:34090. 参考点偏移量;34210. 绝对编码器设定完毕状态,屏幕上显示位置是MD34100设定位置。
b、重启电源,回参考点。
C、在|报警/诊断|→|伺服|→|伺服监视(2)|,计下栅间隔和栅格量的值。
d、计算栅罩量:
当栅间隔/2<栅格量时,栅罩量=栅格量-栅间隔/2
当栅间隔/2>栅格量时,栅罩量=栅格量+栅间隔/2
e、把计算值设定到栅罩量参数中。
f、重启电源,再次回参考点。
g、重启电源。
2)、无挡块参考点方式调整:
a、设定参数: #2049 = 2 无挡块参考点调整方式;
#2050 = 0 正方向、 = 1 负方向;
b、选择“绝对位置设定”画面,选择手轮或寸动模式;
c、在“绝对位置设定”画面,选择“无碰压”方式;
d、#0绝对位置设定=1 , #2原点设定:以基本机械坐标为准,设定参考点的坐标值;
是否使用绝对脉冲编码器作为位置检测器: 0. 不是 、1. 是 1815. 50021 7021
阿玛达数控冲床报警代码300
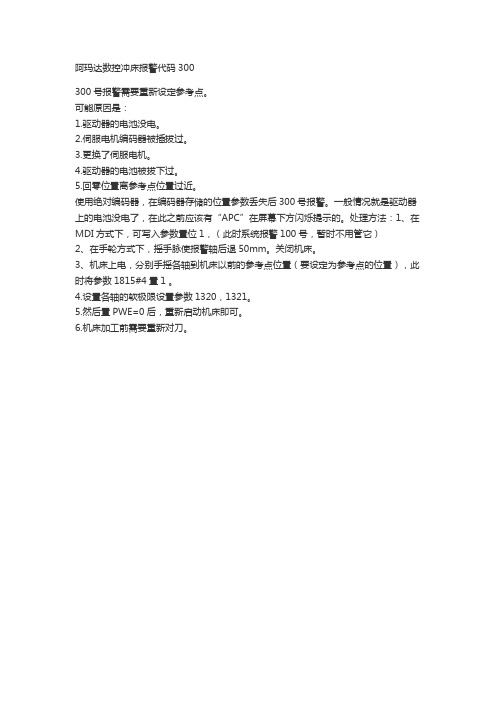
阿玛达数控冲床报警代码300
300号报警需要重新设定参考点。
可能原因是:
1.驱动器的电池没电。
2.伺服电机编码器被插拔过。
3.更换了伺服电机。
4.驱动器的电池被拔下过。
5.回零位置离参考点位置过近。
使用绝对编码器,在编码器存储的位置参数丢失后300号报警。
一般情况就是驱动器上的电池没电了,在此之前应该有“APC”在屏幕下方闪烁提示的。
处理方法:1、在MDI方式下,可写入参数置位1,(此时系统报警100号,暂时不用管它)
2、在手轮方式下,摇手脉使报警轴后退50mm。
关闭机床。
3、机床上电,分别手摇各轴到机床以前的参考点位置(要设定为参考点的位置),此时将参数1815#4置1 。
4.设置各轴的软极限设置参数1320,1321。
5.然后置PWE=0后,重新启动机床即可。
6.机床加工前需要重新对刀。
参考点返回方法
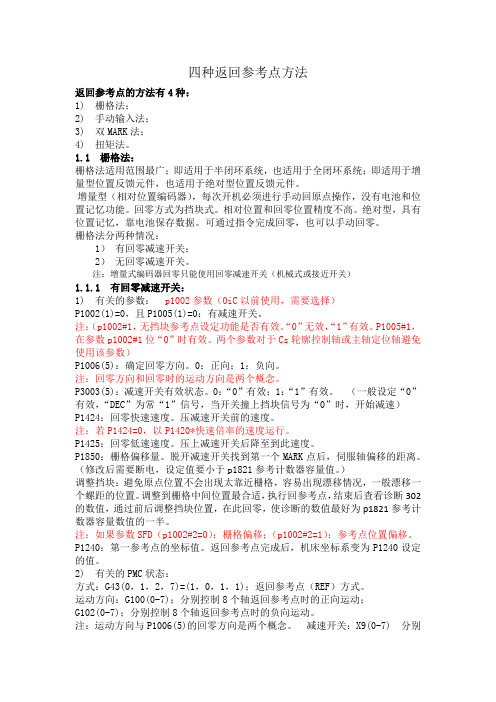
四种返回参考点方法返回参考点的方法有4种:1) 栅格法;2) 手动输入法;3) 双MARK法;4) 扭矩法。
1.1 栅格法:栅格法适用范围最广;即适用于半闭环系统,也适用于全闭环系统;即适用于增量型位置反馈元件,也适用于绝对型位置反馈元件。
增量型(相对位置编码器),每次开机必须进行手动回原点操作,没有电池和位置记忆功能。
回零方式为挡块式。
相对位置和回零位置精度不高。
绝对型,具有位置记忆,靠电池保存数据。
可通过指令完成回零,也可以手动回零。
栅格法分两种情况:1)有回零减速开关;2)无回零减速开关。
注:增量式编码器回零只能使用回零减速开关(机械式或接近开关)1.1.1 有回零减速开关:1) 有关的参数:p1002参数(0iC以前使用,需要选择)P1002(1)=0,且P1005(1)=0:有减速开关。
注:(p1002#1,无挡块参考点设定功能是否有效。
“0”无效,“1”有效。
P1005#1,在参数p1002#1位“0”时有效。
两个参数对于Cs轮廓控制轴或主轴定位轴避免使用该参数)P1006(5):确定回零方向。
0:正向;1:负向。
注:回零方向和回零时的运动方向是两个概念。
P3003(5):减速开关有效状态。
0:“0”有效;1:“1”有效。
(一般设定“0”有效,“DEC”为常“1”信号,当开关撞上挡块信号为“0”时,开始减速)P1424:回零快速速度。
压减速开关前的速度。
注:若P1424=0,以P1420*快速倍率的速度运行。
P1425:回零低速速度。
压上减速开关后降至到此速度。
P1850:栅格偏移量。
脱开减速开关找到第一个MARK点后,伺服轴偏移的距离。
(修改后需要断电,设定值要小于p1821参考计数器容量值。
)调整挡块:避免原点位置不会出现太靠近栅格,容易出现漂移情况,一般漂移一个螺距的位置。
调整到栅格中间位置最合适,执行回参考点,结束后查看诊断302的数值,通过前后调整挡块位置,在此回零,使诊断的数值最好为p1821参考计数器容量数值的一半。
840D回参考点步骤

840D回参考点步骤⼀、⼀般的机床数据10循环时间10取样实际值分配系数10速度设定输出的超前时间10位置控制器输出保持时间的偏置10中断程序段监控时间(失效-激活)10重新启动延迟10缺少总线时脉冲抑制的等待时间10监控周期的系数10检查周期时间的显⽰10安全数据再确认循环时间显⽰10⽂件存取号10安全报警禁⽤级10安全⽅式屏蔽10安全诊断功能10对于 SPL-差额停⽌反应10通讯的系数10安全通讯循环时间10最⼤PLC周期10确认的平均时间10启动的监控时间10与MMC通讯的时间限制10过载时屏幕更新处理10在零件程序中监控时间MMC命令10同时发⽣的MMC节点数量10位置的显⽰⽅式10与驱动通讯的时间限制10与驱动通讯的系数10与MMC通讯的系数10预留:10任务的启动时间限制10任务到准备任务的系数10运⾏时间分量10模拟的换⼑时间10齿轮换挡时间10线性位置的计算精度10⾓度位置的计算精度10激活⽐例系数10机床数据⽐例系数10基本公制长度单位10的转换系数10有效转换的基本设定10位置表的⽐例系统10对rel.6.3的⽐较>和<兼容10不同的显⽰变量⽅式10⼑具数据的物理单位10⼑具数据的单位10⼑沿数据的物理单位10⼑沿数据的单位10的模拟输⼊数10的模拟输出数10模拟输⼊的⽐例10模拟输出的⽐例10预留:10数字输⼊字节的数量10数字输出字节的数量10开关量输⼊输出短路10模拟输⼊的配置10模拟输出的配置10数字输⼊配置10数字输出的配置10更新NCK I/O 设备10外设的引导时间10的处理10安全-地址主控-设备10安全-地址输⼊-设备10安全-地址输出-设备10输⼊分配 $A_INSE 到 PROFIsafe-de 10输出分配 $A_OUTSE 到 PROFIsafe-de 10外部接⼝的输⼊分配10外部接⼝的输出分配10可直接在 NC 读取的 PLC 输⼊字节数量10直接读PLC输⼊位起始地址10可直接在 NC 写⼊的 PLC 输⼊字节数量10直接写PLC输出位起始地址10输⼊循环升级时间10⽤于PLCIO左最⾼位/右最⾼位10编辑循环输⼊字节数量10编译循环输出字节数10编译循环的NCK输出10编辑循环的硬件调试屏蔽10分配软件凸轮到机床轴10负凸轮1 - 16(32)的时间响应10正凸轮1 - 16(32)的时间响应10设备上1 - 8凸轮的配置10设备上9 -16凸轮的配置10设备上17 - 24凸轮的配置10设备上25 - 32凸轮的配置10凸轮信号输出的屏蔽10凸轮特性10测量的软挡块10⽐较器字节1的模拟量输出10⽐较器字节2的模拟量输出10⽐较器字节1的参数化10⽐较器字节2的参数化10框架)旋转的输⼊类型10⼏何轴转换的FRAME10改变⼏何轴的⼯作区限制10镜象参考轴10镜象改变10全局基础FRAME复位后激活10上电后复位全局基础FRAME10在⼦程序存储时FRAME⾏为10轴变化的保护范围10欧拉⾓的名称10普通⽮量的名称10⽅向⽮量的名称10旋转⽮量的名称10临时⽮量的名称10第⼆路径⽅向编程名称10底⾓的名称10插补参数的名称10定义轮廓⾓度名称10定义轮廓半径名称10定义轮廓斜⾯名称10中间坐标点的名称10位置信息名称10轴位置信息名称10多项式编程不带 G 功能 POLY 编程10程序预处理阶段10块信号停⽌预防10空运⾏激活10跳越有效10编程测试模式10程序段搜索模式10更新的设定数据10未配置的NC代码列表10带预处理停⽌的 M 代码10复位后 M 代码 f.主轴激活10 代码由⼦程序代替10代码替换的⼦程序名称10代码替换的⼦程序名称10带参数的 M 代码替代10功能替换的参数化10上电操作⽅式10参数更改10⼿动(JOG)键的功能10⼿动(JOG)键的功能10,G153,SUPA的说明10删除TP编辑启动禁⽌10第⼀ M 功能通道同步10通道同步的最后M功能10功能激活 ASUP10功能没激活 ASUP10中断程序激活(ASUP)10测量信号结构10带G68双⼑架10调⽤的M功能10功能macro调⽤的⼦程序名称10调⽤的G功能10功能macro调⽤的⼦程序名称10启动(M96)的中断数10快速返回的中断数(G10.6)10代码的最⼤号码10合适的 CNC 系统定义10模式:G代码系统10外部NC语⾔的⽤户G代码表10带或不带数值运算命令10增量系统10⼑具的位置号10外部语⾔的⼑具编程模式10插补10分度轴表1位置数10分隔位置表110分度轴表2的位置数10分隔位置表211辅助功能组的辅助功能数量11辅助功能组说明11程序全局⽤户数据(PUD)系数有效11除GUD模块以外的地址11上电时装载标准数据11仅保存修改过的机床数据11初始化⽂件出错时的系统反应11⽂件备份的结构11号11停机处理11语⾔元素的默认值激活11在⼯件⽬录处理 INI ⽂件11在DRAM选择⽬录11中选择⽬录11记录⽂件的存储类型11⽅式中的INC和REF11⽅向改变⼿轮的阀值11每个间隔位置的⼿轮脉冲数11每个凸轮⽖位置的轮廓⼿轮脉冲11⼿轮号码在 VDI 接⼝中描述11⼿轮的增量⼤⼩11第三⼿轮:驱动类型11第三⼿轮:驱动号/测量电路号11第三⼿轮:输⼊模块/测量电路11⼿轮:11信号影响⽅式组11安全集成测试机床数据11地址单元的INTEGER整数显⽰11地址单元的REAL显⽰11地址单元的INTEGER整数输⼊11地址单元的REAL输⼊11地址单元的内容重写11轴变量服务器出错11激活内部轨迹功能11报警输出的屏蔽11报警激活11报警响应 CHAN_NOREADY 有效11报警参数作为⽂本输出11记录⽂件⼤⼩(KB)11数字化时的通道定义11选择 3 轴或 3+2 轴数字化11参数化搜索11异步往复的模式表单11重新配置的属性11中PLC轨迹数据的缓存深度11中PLC轨迹数据的缓存深度11中PLC轨迹数据的缓存深度11受保护的同步动作11最⼤允许的IPO负载11固定的BAG响应11运⾏时不考虑停⽌的原因11优先级有效11⽤户定义 ASUP 程序激活11⽤户定义ASUP编程的保护级11的程序名称11使能间隔在MD $MC_AXCONF_MACHAX_USED 11打开在#MC_AXCONF_MACHAX_USED中的保护11可能的电⼦齿轮箱数量11卡代码12轴进给倍率开关编码12轴进给倍率系数12灰度 - 编码轨迹进给率开关12路径进给倍率的系数12灰度码快速运⾏倍率开关12快速进给的倍率系数12灰度码主轴倍率开关12主轴倍率的系数12回参考点速度的倍率12进给倍率12⼆进制编码的倍率限定12在倍率0时运⾏12直线轴的固定进给率12旋转轴的固定进给率12主轴固定转速12在NCU组中的NCU代码12号,总线终⽌阻抗有效12联接总线波特率12信息存储区重复的最⼤量12在轴系列1中的轴清单12在轴系列2中的轴清单12在轴系列3中的轴清单12在轴系列4中的轴清单12在轴系列5中的轴清单12在轴系列6中的轴清单12在轴系列7中的轴清单12在轴系列8中的轴清单12在轴系列9中的轴清单12在轴系列10中的轴清单12在轴系列11中的轴清单12在轴系列12中的轴清单12在轴系列13中的轴清单12在轴系列14中的轴清单12在轴系列15中的轴清单12在轴系列16中的轴清单12轴系列名称12数字PLC输⼊地址的起始地址12数字输⼊地址号12数字PLC输出地址的起始地址12数字输出地址号12模拟PLC输⼊地址的起始地址12模拟输⼊地址号12模拟PLC输出地址的起始地址12模拟输出地址号13驱动在运⾏13逻辑驱动号13驱动模块的功率部分代码13模块识别13驱动类型13逻辑驱动地址13标准通讯类型13使⽤DP功能13驱动类型 Profibus13诊断驱动母线13探头极性改变13带数字输出的测量脉冲模拟13带Profibus驱动的测头操作类型13探头延迟时间14绝对值编码器的波特率14启动延迟14延时14输⼊字节的个数(从PLC)14输出字节的个数(到PLC)14⽤户数据的号(INT)14⽤户数据的号(HEX)14⽤户数据的号(FLOAT)14⽤户数据(INT)14⽤户数据(HEX)14⽤户数据(FLOAT)14⽤户数据(HEX)17全局MMC信息(没有物理单元17全局MMC状态信息(没有物理单元) 17替换⼑具的最⼤号17卸载后⼑具 - 数据的运⾏状态17产⽣新⼑具:默认设置17对于 HMI 标记的⼑具-数据-变化17中log存储最优化深度18更新PLC接⼝18卡的版本和⽇期18⾃由⽆缓冲内存[bytes]18⾃由缓冲内存[bytes]。
VMC850E设置参考点方法-斗笠刀库
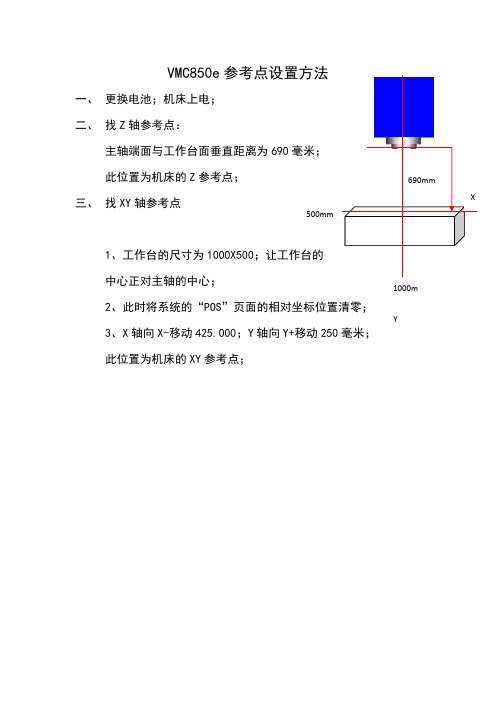
一、二、三、、 更换电、 找Z 轴主轴端此位置、 找XY1、工中心正2、此3、X 轴此位置VM 电池;机床轴参考点:端面与工作置为机床的轴参考点作台的尺正对主轴的时将系统轴向X-移置为机床的MC850e 床上电;作台面垂直的Z 参考点点尺寸为100的中心;统的“POS”移动425.0的XY 参考参考点直距离为点; 00X500;让”页面的000;Y 轴考点;690向Y+移动动250毫米米; 690mm四、 设置参数:在 “MDI”方式下,按“SYSTEM”键,找到显示器上的参数“参数”, 输入1815;搜索;将1815参数的APZ=1; N01815 #7 #6 #5 #4 #3 #2 #1 #0 X1Y 1 Z1备注:机床的参数不允许随意改动,出厂已经锁住,需要修改参数务必左手按在急停开关旁边的“reset”键。
五、 机床下电再重新上电!机床参考点设置完成! 六、 设置斗笠刀库第二参考点:1、 在“MDI”方式下执行“M19”;2、 在“JOG”模式下,将钥匙开关拨到右边;有提示报警“2003 MAGAZINE ADJUST”。
3、 按“刀盘前进”按钮; 4、 装一把刀在刀夹上;5、主轴必须“松刀”;6、在“MPG”手脉方式下,Z轴慢慢向下移动;7、临近刀具的时候,试着松卡刀几次,观察主轴是否能卡住刀,能卡住,刀盘也不被上抬,此时的位置为Z轴的第二参考点;按动“刀库后退”按钮;8、将在Z轴机械坐标值写入参数“1241”的Z值中,带负号;9、设置参数6930=6931=1241+0.1;6950=6951=1241-0.1;例如:Z坐标值是-123.456;1241参数号 参数及设定值1241 XYZ -123.456;6930 -123.456+0.1 -123.3566931 -123.456+0.1 -123.3566950 -123.456-0.1 -123.5566951 -123.456-0.1 -123.556七、在“JOG”方式下,按动“刀盘正转”;转动到“1号刀”的位置;八、在“MDI”方式下执行“M68”刀库初始化完成!把钥匙开关拨到左边。
- 1、下载文档前请自行甄别文档内容的完整性,平台不提供额外的编辑、内容补充、找答案等附加服务。
- 2、"仅部分预览"的文档,不可在线预览部分如存在完整性等问题,可反馈申请退款(可完整预览的文档不适用该条件!)。
- 3、如文档侵犯您的权益,请联系客服反馈,我们会尽快为您处理(人工客服工作时间:9:00-18:30)。
需要重新设定参考点。
可能:
1.驱动器的电池没电。
2.伺服电机编码器被插拔过。
3.更换了伺服电机。
4.驱动器的电池被拔下过。
5.回零位置离参考点位置过近.
两种方法:
A、对准标记设定参考点
在机床上设置对准标记,注意对于机床使用倾斜轴控制功能的轴上不能使用本功能。
准备工作:
a:1005#1设为1——各轴返回参考点不使用挡块方式
此时返回参考点就不需要使用减速信号*DEC。
b:1815#5设为1——使用绝对位置编码器
1815#4设为0——绝对位置编码器原点位置未确立
1006#5设为0——返回参考点方向为正向(根据实际情况)
c:切断NC电源,断开主断路器
d:把绝对位置编码器的电池连接到伺服放大器上
e:接通电源
自动检测编码器基准点(检测编码器的1转信号)
(如果未进行此项操作继而进行参考点回零的话出现PS0090号报警)
a:用手动或者手轮方式进给,让机床电机转动1转以上
b:断开电源再接通电源
设定参考点
a:JOG方式下对各轴手动移动,将机床移动到1006#5设定的反方向处,例如上面设的1006#5为0即返回参考点方向为正向,则将机床移至负向。
b:按1006#5设定的返回参考点的方向移动机床,直至机床对准标记与参考点位置重合,当位置快要重合时使用手轮进给进行微调。
c:将1815#4设为1——绝对位置编码器原点位置已确立。
B、无挡块返回参考点
不需要安装限位开关和挡块
准备工作:
a:1005#1设为1——各轴返回参考点不使用挡块方式
此时返回参考点就不需要使用减速信号*DEC。
b:1815#5设为1——使用绝对位置编码器
1815#4设为0——绝对位置编码器原点位置未确立
1006#5设为0——返回参考点方向为正向(根据实际情况)
c:切断NC电源,断开主断路器
d:把绝对位置编码器的电池连接到伺服放大器上
e:接通电源
自动检测编码器基准点(检测编码器的1转信号)
(如果未进行此项操作继而进行参考点回零的话出现PS0090号报警)
a:用手动或者手轮方式进给,让机床电机转动1转以上
b:断开电源再接通电源
设定参考点
a:JOG方式下对各轴手动移动至参考点返回方向的反方向,然后以1006#5设置的方向向参考点移动。
对移动过程如果不满足以下条件则会发出PS0090报警。
进给速度F=【(伺服位置偏差*60)/1000】*伺服环增益*检测单位
其中伺服位置偏差为参数1836设定值
伺服环增益为参数1825设定值乘以0.01
检测单位是以um为单位
参考点返回的栅格间隔就是电机旋转一周参考计数器容量,1821参数的设定值。
b:把轴移动到想要设为参考点的位置之前,大约1/2栅格的距离
c:选择返回参考点方式对各轴进行返回参考点操作,当机床到达参考点时返回参考点完成信号ZPx为1,1815#4自动变成1。
对参考点位置的调整
使用栅格偏移功能,可以对参考点在1个栅格范围内进行微调。
通常一个栅格和电机旋转一周机床的移动量相等。
使参考点错开一个栅格以上位置时须改变挡块的安装位置(有挡块时),或者修改参考点设定(无挡块时)的方法。
a:执行手动返回参考点
b:在位置画面将所有轴的相对位置归零
c:手轮进给将机床移动到所想设的参考点位置,读取相对位置值
d:将读取的值写入参数1850——各轴栅格偏移量中。
e:断电开机再次返回参考点检查参考点位置是否正确。
仅供参考,具体看FANUC的说明书。