数控火焰、等离子切割工时表
钢结构工时定额

钢结构工时定额1.下料:剪板、数控火焰切割、等离子切割、半自动小车、带锯。
下料定员:一人1.1.剪板依据剪板件重量(图纸、下料工艺),剪板数量,单件剪切次数修正GJGDE—02。
剪切次数修正系数表GJGDE—02剪切次数 1 2 3 4 5 6 7 8修正系数0.5 0.7 0.8 1 1.15 1.3 1.4 1.5剪板:下料、校形编号:表GJGDE—01剪板机下料工时定额(>0.4-13.7kg)表GJGDE—01序号重量(kg) 基准工时(分)十块内[一次剪切数量]工时表(分钟)1 2 3 4 5 6 7 8 9 101 0.4及以下 1 3.9 6 8.8 11.5 14 16.5 18.8 21 23 252 >0.4-1.0 1.5 5.1 8.8 12.7 16.4 19.9 23 26 28.8 31.4 33.83 >1.0-1.8 2 6 11.5 16.4 21 25 28.8 32.2 35.2 37.8 404 >1.8-2.6 2.5 7.4 14 19.9 25 29.7 33.8 37.2 40 42.8 455 >2.6-3.4 3 8.8 16.4 23 28.8 33.8 37.8 41.2 44.2 46.4 486 >3.4-4.2 3.5 10.1 18.8 26 32.2 37.2 41.2 44.6 47 49.1 51.17 >4.2-5.0 4 11.4 21 28.8 35.2 40 44.2 47 49.6 51.5 52.48 >5.0-5.8 4.5 12.7 23 31.4 37.8 42.8 46.4 49.1 51.5 52.2 549 >5.8-6.5 5 14 25 33.8 40 45 48 51.1 52.4 54 5511 >7.3-8.1 6 16.4 28.8 37.8 44.2 48 51.5 52.9 54.7 57.2 6012 >8.1-8.9 6.5 17.6 30.6 39.5 45.8 50 51.9 54.1 56.2 58.5 6513 >8.9-9.6 7 18.8 32.2 41.2 47 51.1 52.9 54.9 58.2 63 7014 >9.6-10.3 7.5 19.9 33.8 42.8 48 51.9 54 56.4 60 67.5 7515 >10.3-10.7 8 21 35.2 44.2 49.6 52.4 54.7 58.2 64 72 8016 >10.7-11.2 8.5 22 36.6 45.4 50.7 53.1 55.6 59.8 68 76.5 8517 >11.2-11.6 9 23 37.8 46.4 51.5 54 57.2 63 72 81 9018 >11.6-12 9.5 24 39 47.3 52.1 54.6 58.7 66.5 76 85.5 9519 >12-12.5 10 25 40 48 52.4 55 60 70 80 90 10020 >12.5-13.1 10.5 26 41.2 49.1 52.9 56.4 63 73.5 84 94.5 10521 >13.1-13.7 11 27 42.2 50.2 53.7 57.8 66 77 88 99 110剪板机下料工时定额(>51.8-117kg)序号重量(kg)基准工时(分)十块内[一次剪切数量]工时表(h)1 2 3 4 5 6 7 8 9 101 >51.8-53.5 32 0.8 1.07 1.6 2.13 2.67 3.2 3.73 4.27 4.8 5.332 >53.5-55.3 33 0.8 1.1 1.65 2.2 2.75 3.3 3.85 4.4 4.95 5.53 >55.3-57.0 34 0.8 1.13 1.7 2.27 2.83 3.4 3.97 4.53 5.1 5.674 >57.0-58.8 35 0.85 1.17 1.75 2.33 2.92 3.5 4.08 4.67 5.25 5.835 >58.8-60.5 36 0.86 1.2 1.8 2.4 3 3.6 4.2 4.8 5.4 66 >60.5-64.0 37 0.86 1.23 1.85 2.47 3.08 3.7 4.32 4.93 5.55 6.137 >64.0-68.7 38 0.87 1.27 1.9 2.53 3.17 3.8 4.4 5.07 5.7 6.248 >68.7-71.5 39 0.87 1.3 1.95 2.6 3.25 3.9 4.55 5.2 5.85 6.3410 >74.4-77.2 41 0.87 1.37 2.05 2.73 3.42 4.1 4.78 5.47 6.1 6.5511 >77.2-80.0 42 0.88 1.4 2.1 2.8 3.5 4.2 4.9 5.6 6.21 6.6512 >80.0-83.3 43 0.89 1.43 2.15 2.87 3.58 4.3 5.02 5.73 6.3 6.7513 >83.3-86.7 44 0.89 1.47 2.2 2.93 3.67 4.4 5.13 5.87 6.4 6.8514 >86.7-90.0 45 0.9 1.5 2.25 3 3.75 4.5 5.25 6 6.49 6.9415 >90.0-93.3 46 0.9 1.53 2.3 3.07 3.83 4.6 5.37 6.09 6.59 7.0416 >93.3-96.7 47 0.91 1.57 2.35 3.13 3.92 4.7 5.48 6.18 6.68 7.1317 >96.7-100 48 0.91 1.6 2.4 3.2 4 4.8 5.6 6.27 6.77 7.218 >100-104 49 0.91 1.63 2.45 3.27 4.08 4.9 5.72 6.36 6.86 7.319 >104-108 50 0.92 1.67 2.5 3.33 4.17 5 5.83 6.45 6.95 7.4120 >108-113 51 0.93 1.7 2.55 3.4 4.25 5.1 5.95 6.53 7.04 7.5221 >113-117 52 0.94 1.73 2.6 3.47 4.33 5.2 6.04 6.6 7.1 7.63剪板机下料工时定额(>117-263kg)序号重量(kg)基准工时(分)十块内[一次剪切数量]工时表(h)1 2 3 4 5 6 7 8 9 101 >117-121 53 0.95 1.77 2.65 3.53 4.42 5.3 6.12 6.69 7.19 7.742 121-126 54 0.95 1.8 2.7 3.6 4.5 5.4 6.21 6.77 7.27 7.833 126-131 55 0.96 1.83 2.75 3.67 4.58 5.5 6.28 6.85 7.37 7.944 131-137 56 0.97 1.87 2.8 3.73 4.67 5.6 6.36 6.91 7.46 8.045 137-143 57 0.98 1.9 2.85 3.8 4.75 5.7 6.44 6.99 7.56 8.126 143-149 58 0.99 1.93 2.9 3.87 4.83 5.8 6.51 7.07 7.65 8.217 149-154 59 0.99 1.97 2.95 3.93 4.92 5.9 6.58 7.14 7.74 8.318 154-160 60 1 2 3 4 5 6 6.65 7.2 7.83 8.49 160-168 61 1.02 2.03 3.05 4.07 5.08 6.07 6.71 7.28 7.92 8.4810 168-176 62 1.03 2.07 3.1 4.14 5.17 6.14 6.79 7.37 8.01 8.5711 176-183 63 1.05 2.1 3.15 4.2 5.25 6.21 6.85 7.47 8.09 8.6612 183-191 64 1.07 2.13 3.2 4.27 5.33 6.27 6.91 7.56 8.18 8.7413 191-197 65 1.08 2.17 3.25 4.33 5.42 6.34 6.97 7.64 8.26 8.8214 197-208 66 1.1 2.2 3.3 4.4 5.5 6.4 7.05 7.71 8.35 8.915 208-215 67 1.12 2.24 3.35 4.48 5.6 6.47 7.11 7.79 8.43 8.9816 215-223 68 1.13 2.27 3.4 4.54 5.65 6.53 7.17 7.87 8.51 9.0617 223-231 69 1.15 2.3 3.45 4.6 5.75 6.59 7.24 7.95 8.59 9.1418 231-239 70 1.17 2.34 3.5 4.67 5.83 6.65 7.3 8.03 8.66 9.2119 239-247 71 1.18 2.37 3.55 4.73 5.92 6.71 7.38 8.11 8.74 9.2920 247-255 72 1.2 2.4 3.6 4.8 6 6.77 7.46 8.18 8.81 9.3621 255-263 73 1.22 2.43 3.65 4.87 6.06 6.83 7.55 8.25 8.89 9.45剪板机下料工时定额(>263-428kg)序号重量(kg)基准工时(分)十块内[一次剪切数量]工时表(h)1 2 3 4 5 6 7 8 9 101 263-270 74 1.23 2.47 3.7 4.93 6.12 6.88 7.61 8.33 8.96 9.542 270-279 75 1.25 2.5 3.75 5 6.16 6.94 7.69 8.4 9.02 9.633 279-286 76 1.27 2.53 3.8 5.06 6.24 6.99 7.74 8.48 9.1 9.74 286-294 77 1.28 2.57 3.85 5.13 6.29 7.05 7.81 8.52 9.16 9.785 294-302 78 1.3 2.6 3.9 5.195 6.35 7.105 7.875 8.595 9.23 9.866 302-310 79 1.32 2.63 3.95 5.261 6.409 7.161 7.94 8.66 9.298 9.947 310-318 80 1.33 2.665 4 5.327 6.468 7.217 8.005 8.725 9.366 10.028 318-325 81 1.35 2.698 4.05 5.393 6.527 7.273 8.07 8.79 9.434 10.109 325-333 82 1.37 2.731 4.1 5.459 6.586 7.329 8.135 8.855 9.502 10.1810 333-341 83 1.385 2.764 4.15 5.525 6.645 7.385 8.2 8.92 9.57 10.26311 341-349 84 1.402 2.797 4.2 5.591 6.704 7.441 8.265 8.985 9.638 10.3412 349-357 85 1.419 2.83 4.25 5.657 6.763 7.497 8.33 9.05 9.706 10.4213 357-365 86 1.436 2.863 4.3 5.723 6.822 7.553 8.395 9.115 9.774 10.5014 365-373 87 1.453 2.896 4.35 5.789 6.881 7.609 8.46 9.18 9.842 10.5815 373-381 88 1.47 2.929 4.4 5.855 6.94 7.665 8.525 9.245 9.91 10.6616 381-388 89 1.487 2.962 4.45 5.921 6.999 7.721 8.59 9.31 9.978 10.7417 388-396 90 1.504 2.995 4.5 5.987 7.058 7.777 8.655 9.375 10.046 10.8218 396-404 91 1.521 3.028 4.55 6.053 7.117 7.833 8.72 9.44 10.114 10.9019 404-412 92 1.538 3.061 4.6 6.119 7.176 7.889 8.785 9.505 10.182 10.9820 412-420 93 1.555 3.094 4.65 6.185 7.235 7.945 8.85 9.57 10.25 11.0621 420-428 94 1.572 3.127 4.7 6.251 7.294 8.001 8.915 9.635 10.318 11.14剪板机下料工时定额(>428-593kg)序号重量(kg)基准工时(分)十块内[一次剪切数量]工时表(h)1 2 3 4 5 6 7 8 9 101 428-436 95 1.58 3.17 4.75 6.24 7.16 8.12 8.94 9.7 10.5 11.12 436-443 96 1.6 3.2 4.8 6.27 7.2 8.18 9 9.78 10.5 11.23 443-451 97 1.62 3.23 4.85 6.32 7.25 8.24 9.06 9.86 10.6 11.34 451-459 98 1.63 3.27 4.9 6.37 7.31 8.29 9.12 9.92 10.7 11.45 459-467 99 1.65 3.3 4.95 6.41 7.355 8.35 9.18 10 10.8 11.56 467-475 100 1.667 3.333 5 6.454 7.405 8.407 9.24 10.074 10.86 11.67 475-483 101 1.684 3.366 5.05 6.498 7.455 8.464 9.3 10.148 10.94 11.68 483-491 102 1.701 3.399 5.1 6.542 7.505 8.521 9.36 10.222 11.02 11.749 491-498 103 1.718 3.432 5.15 6.586 7.555 8.578 9.42 10.296 11.1 11.8310 498-506 104 1.735 3.465 5.2 6.63 7.605 8.635 9.48 10.37 11.18 11.9211 506-514 105 1.752 3.498 5.25 6.674 7.655 8.692 9.54 10.444 11.26 12.0112 514-522 106 1.769 3.531 5.3 6.718 7.705 8.749 9.6 10.518 11.34 12.113 522-530 107 1.786 3.564 5.35 6.762 7.755 8.806 9.66 10.592 11.42 12.1892857114 530-538 108 1.803 3.597 5.4 6.806 7.805 8.863 9.72 10.666 11.5 12.2715 538-546 109 1.82 3.63 5.45 6.85 7.855 8.92 9.78 10.74 11.58 12.3616 546-553 110 1.837 3.663 5.5 6.894 7.905 8.977 9.84 10.814 11.66 12.4517 553-561 111 1.854 3.696 5.55 6.938 7.955 9.034 9.9 10.888 11.74 12.5418 561-569 112 1.871 3.729 5.6 6.982 8.005 9.091 9.96 10.962 11.82 12.6319 569-577 113 1.888 3.762 5.65 7.026 8.055 9.148 10.02 11.036 11.9 12.7220 577-585 114 1.905 3.795 5.7 7.07 8.105 9.205 10.08 11.11 11.98 12.8121 585-593 115 1.922 3.828 5.75 7.114 8.155 9.262 10.14 11.184 12.06 12.901.2切割下料数控火焰切割(GJGDE—03)、空气等离子切割(GJGDE—04)、半自动切割(GJGDE—03)由下料编程人员依据图形切割件程序确定工时定额。
工时计算方法大全(各机床工时、各工序工时)

工时计算方法(各机床工时、各工序工时)生产效率:是衡量生产单位或部门管理绩效的一个指标,体现生产单位或部门的管理能力,即总标准工时与生产总工时的百分比。
为了准确快捷填写生产计划表,现将需计算之工时与相关注意事项做说明。
为了提高生产效率,结合其定义,使工时定额更加合理、准确、科学,现结合本单位实际情况,参考国家相关政策标准,制定此工时计算方法。
一.锯床工时定额计算标准1.工时计算公式:T=(k m T 机+nT 吊+T 装卸)k 2 式中:k m -材料系数n-一次装夹工件数;n=1-2;k 2—次装夹工件数修正系数,k 2=1(n=1);k 2=0。
55(n=2) 2.机动时间:T 机 2.1。
方料:式中: H — 板厚mm k B — 材料宽度系数,查下表T 机=k BH22.2.棒料:式中D-棒料外径 mm2.3。
管料:式中d 0—管料内径;mm2.4..方管:式中:H—方管外形高mm ;H 0—方管内腔高mm ; B 0—方管内腔宽mm ;3.吊料时间:4.装卸料时间及其它时间:T机=D24T 机=D —d 02 2410000T 机=H—H 0*B 0208000T吊=L 1000T 装卸=0。
LD综上所述:方料:T=(0。
12+n0.0519H+0.001L)k 2-0.00013 H 0*B 0 (min ) 圆料:T=(0.12+n0.0429D+0。
001L )k 2—0。
0001 d 02 (min ) n —一次装夹工件数;n=1—2;k 2—次装夹工件数修正系数,k 2=1(n=1);k 2=0。
55(n=2)二.剪板冲压折弯工时定额计算标准1..剪板工时定额计算方法剪板单件工时定额:a —每块工时系数、见表b —剪角次数剪板工时系数表12+1800840T =k *a+b a3注:准备工时按100件基数计算,每件0.2,共计200分剪板毛刺工时:T=0。
3 + 处理长度/400剪板校正T校=k*T材料系数K=1~1.52.冲压每冲一次工时3.。
各种机加工工时计算表

1200.00 0.833333333
0.2-0.3 0.15 26.0 1379
>>>>>>>往复式平面粗磨理论工时计算<<<<<<<
零件参数
砂轮、机床参数
工件材料
淬火钢 砂轮直径 mm
400
磨削形式
零件装置在夹具中或用千 分表校准
**当加工孔径较大 时,ap取大值;加 工孔径较小,且加 工精度要求较高 时,ap取小值
钢、铸钢 刀具材料 精镗 刀具类型 5 刀具直径 mm 20 推荐切削参数范围 0.6-1.2 1.00 8 509 请输入实际切削参数 3.00 0.60 1.00 600.00 0.3
刀具参数
硬质合金 镗刀块 5.00
4.00 20 1273
>>>>>>>高速钢铰刀铰孔理论工时计算<<<<<<<
零件参数
材料种类
材料性能
孔直径 mm
铰
刀具直径 mm 待加工孔深度 mm
切削深度 mm 铰削余量 mm 实际每转进给量 实际主轴转速 理论工时 min
推荐切削参数 中硬铸铁 铰削余量 mm
175HBS 每转进给量 f mm 6.00 切削速度 m/min 6.0 主轴转速 10.0
材料种类 孔直径 mm
深度 mm
钻
零件参数
不锈钢 刀具直径 mm
12.50 每转进给量 mm
20.00
切削速度 主轴转速
m/min
请输入实际切削参数
推荐切削参数范围 8 ~ 20
火焰切割工时计算
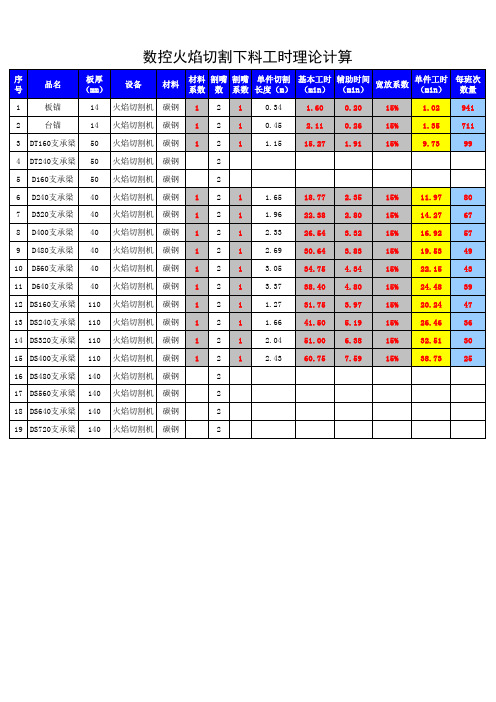
60.75 7.59
15%
38.73
25
16 DS480支承梁 140 火焰切割机 碳钢
2
17 DS560支承梁 140 火焰切割机 碳钢
2
18 DS640支承梁 140 火焰切割机 碳钢
2
19 DS720支承梁 140 火焰切割机 碳钢
2
15%
19.53
49
10 D560支承梁 40 火焰切割机 碳钢 1 2 1
3.05
34.75 4.34
15%
22.15
43
11 D640支承梁 40 火焰切割机 碳钢 1 2 1
3.37
38.40 4.80
15%
24.48
39
12 DS160支承梁 110 火焰切割机 碳钢 1 2 1
1.27
31.75 3.97
0.45
2.11
0.26
15%
1.35
711
3 DT160支承梁 50 火焰切割机 碳钢 1 2 1
1.15
15.27 1.91
15%
9.73
99
4 DT240支承梁 50 火焰切割机 碳钢
2
5 D160支承梁 50 火焰切割机 碳钢
2
6 D240支承梁 40 火焰切割机 碳钢 1 2 1
1.65
18.77 2.35
数控火焰切割下料工时理论计算
序 号
品名
板厚 (mm)
设备
材料
材料 系数
割嘴 数
割嘴 系数
单件切割 长度(m)
基本工时 (min)
辅助时间 (min)
宽放系数
单件工时 (min)
每班次 数量
工时计算方法
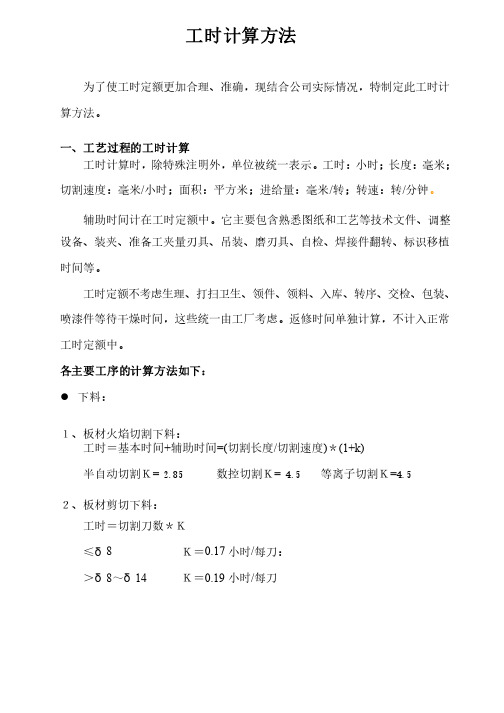
工时计算方法为了使工时定额更加合理、准确,现结合公司实际情况,特制定此工时计算方法。
一、工艺过程的工时计算工时计算时,工时计算时,除特殊注明外,除特殊注明外,除特殊注明外,单位被统一表示。
单位被统一表示。
单位被统一表示。
工时:工时:工时:小时;小时;小时;长度:长度:长度:毫米;毫米;切割速度:毫米/小时;面积:平方米;进给量:毫米/转;转速:转/分钟分钟。
辅助时间计在工时定额中。
它主要包含熟悉图纸和工艺等技术文件、辅助时间计在工时定额中。
它主要包含熟悉图纸和工艺等技术文件、调整调整设备、装夹、准备工夹量刃具、吊装、磨刃具、自检、焊接件翻转、标识移植时间等。
工时定额不考虑生理、打扫卫生、领件、领料、入库、转序、交检、包装、喷漆件等待干燥时间,这些统一由工厂考虑。
返修时间单独计算,不计入正常工时定额中。
各主要工序的计算方法如下:l 下料:1、板材火焰切割下料:工时=基本时间+辅助时间=(切割长度/切割速度)*(1+k) 半自动切割K=2.85数控切割K= 4.5 等离子切割K=4.52、板材剪切下料:工时=切割刀数*K≤δ8K=0.17小时/每刀:>δ8~δ14 K=0.19小时/每刀>δ14~δ20 K=0.20小时/每刀每刀3、型材下料:3、型材下料:工时按实际考核数据。
参见附件一:型材下料工时工时按实际考核数据。
参见附件一:型材下料工时l成型:成型:基本时间+辅助时间工时=基本时间+辅助时间l焊接:焊接:1、焊前准备:包括划线、焊前焊缝处表面清理、二级库焊材烘干。
、焊前准备:包括划线、焊前焊缝处表面清理、二级库焊材烘干。
易打磨大件:焊前焊缝表面清理时间:0.08小时/米不易打磨件或小件:焊前焊缝表面清理时间:0.15小时/米2、定位焊接:、定位焊接:3、焊接成型:、焊接成型:工时=基本时间+辅助时间。
工时=基本时间+辅助时间。
焊接(气刨)基本时间=焊缝长度*层数/焊接(气刨)速度焊接(气刨)速度 4、焊后整理:包括校正、清理焊渣时间。
各类加工工时费参考
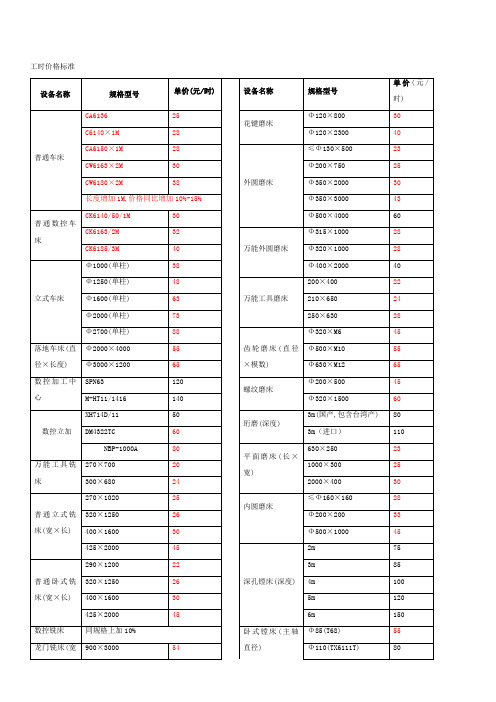
60×2500
150
等离子切割机(适用于批量下料)
4mm(元/米)
冲床(公称压力)
250KN
22
5mm(元/米)
630KN
32
6mm(元/米)
弯管机(直径)
Ф25
20
8mm(元/米)
Ф38
25
10-12mm(元/米)
Ф60
35
14-16mm(元/米)
Ф108
40
18-20mm(元/米)
6
折边机
2×800
300×680
24
2000×400
30
普通立式铣床(宽×长)
270×1020
25
内圆磨床
≤Ф160×160
28
320×1250
26
Ф200×200
33
400×1600
30
Ф500×1000
45
425×2000
45
深孔镗床(深度)
2m
75
普通卧式铣床(宽×长)
290×1200
22
3m
85
320×1250
26
4m
100
400×1600
30
5m
120
425×2000
45
6m
150
数控铣床
同规格上加10%
卧式镗床(主轴直径)
Ф85(T68)
55
龙门铣床(宽×长)
900×3000
54
Ф110(TX6111T)
80
1250×4000
65
Ф130(TX6113C)
100
1600×4000
78
座标镗床(工作台面积)
数控工时定额

数控工时定额规范
1、规范说明:
(1)本规范工时定额包括:作业时间、休息与生理需要时间、准备与结束时间及宽放时间。
(2)本规范中的工时定额是以加工般碳钢为基准,数控等离子切割不锈钢材料时乘以系数K-1.2。
(3)生理休息时间25分钟,准备终了时间45分钟。
2、作业时间
(1)数控等离子切割下料
(2)数控火焰切割下料
注1: 16mm以下(包含16mm)钢板下料下料时采用等离子切割注2:18mm以上(包含18mm)钢板下料下料时采用火焰切割
数控切割机般两只割嘴同步作业,当工艺或特殊需求单件切割时,乘以系数2。
3、宽放时间:宽放系数按25%计算。
钢结构工时定额
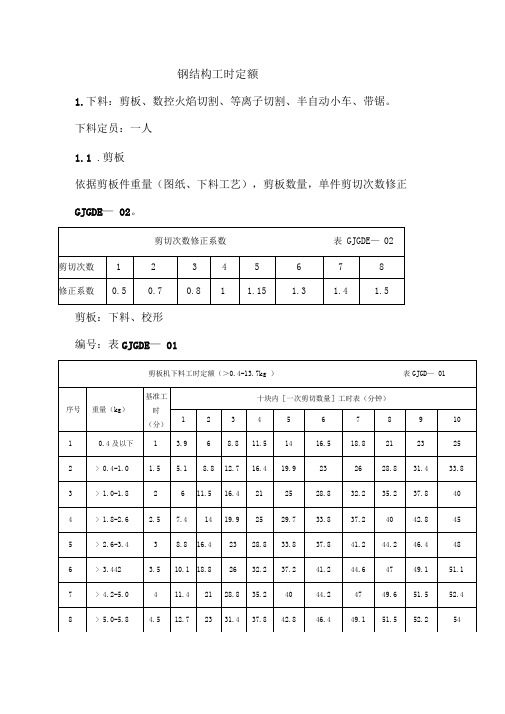
26
32.2
37.2
41.2
44.6
47
49.1
51.1
7
> 4.2-5.0
4
11.4
21
28.8
35.2
40
44.2
47
49.6
51.5
52.4
8
> 5.0-5.8
4.5
12.7
23
31.4
37.8
42.8
46.4
49.1
51.5
52.2
54
9
> 5.8-6.5
5
14
25
33.8
40
45
48
33.8
3
> 1.0-1.8
2
6
11.5
16.4
21
25
28.8
32.2
35.2
37.8
40
4
> 1.8-2.6
2.5
7.4
14
19.9
25
29.7
33.8
37.2
40
42.8
45
5
> 2.6-3.4
3
8.8
16.4
23
28.8
33.8
37.8
41.2
44.2
46.4
48
6
>3.442
3.5
10.1
钢结构工时定额
1.下料:剪板、数控火焰切割、等离子切割、半自动小车、带锯。
下料定员:一人
1.1
依据剪板件重量(图纸、下料工艺),剪板数量,单件剪切次数修正
GJGDE
剪切次数修正系数
机加工工时计算表

平面--铣削范围(长 X 宽)mm
<50X50
<50X100
<100X100
<100X150
<100X200
TR
TC
TR
TC
TR
TC
TR
TC
TR
TC
0.3
0.5
0.7
0.9
1.2
1.7
1.9
2.5
2.5
3.3
0.2
0.3
0.5
0.7
0.8
1.2
1.2
1.7
1.6
2.3
0.2
0.3
0.3
0.5
0.5
0.9
内腔轮廓--铣削范围(长X宽)mm
时间 刀具直徑(mm)
SAE PART ID
<50X50
粗
精
1.0
SC7-702-00071S
8.3
8.3
1.5
SC7-702-00072S
3.7
3.7
2.0
SC7-702-00073S
2.1
2.2
2.5
SC7-702-00074S
1.3
1.4
3.0
SC7-702-00075S
4002銑刀--普通CNC铣削加工标准时间(min)
<50X100
TR
TC
1.1
1.5
0.7
1.0
0.5
0.8
0.3
0.7
TR:粗加 工时间/次
塑胶类(ESD225、ESD420、Derlin等)
平面--铣削范围(长 X 宽)mm
<100X100
工时标准

准备工时
序号
单件重量 W (kg)
准备时间 T (Min)
1
W≤2
0.2
2
2<W≤5
0.4
3
5<W≤10
0.8
4
10<W≤20
1.2
5
20<W≤50
1.5
7
50<W≤100
2
8
100<W≤200
3
9
200<W
4
激光切割下料工时
准备时间包括 换激光头 巡边及调换程式,上下料板的时间
单件下料工时 = 单件切割时间+准备工时 T
50<W≤100
2
8
100<W≤200
3
9
200<W
4
单件下料工时 = 单件切割时间/割嘴数+准备工时 T
坡口工时 = 1.2*坡口长度 L(MM)/坡口切割速度 B
打磨工时 = 零件周边长度(M)/0.3
工时计算说明: 1、割嘴数由编程时根据实际情况确定; 2、坡口切割工时计算时,板厚规格应取坡口斜边实际切割厚度。
0.2
3
3<W≤5
0.3
4
5<W≤10
0.5
5
PL≤3
10<W≤15
1
6
15<W≤20
1.5
7
20<W≤30
2
8
30<W≤50
3
9
50<W≤70
4
10
1<W≤3
0.5
11
3<W≤5
0.5
12
5<W≤10
1
13
10<W≤15
1.2
14 15
PL>3
15<W≤20 20<W≤30
超级详细的机加工工时计算表格,值得收藏!
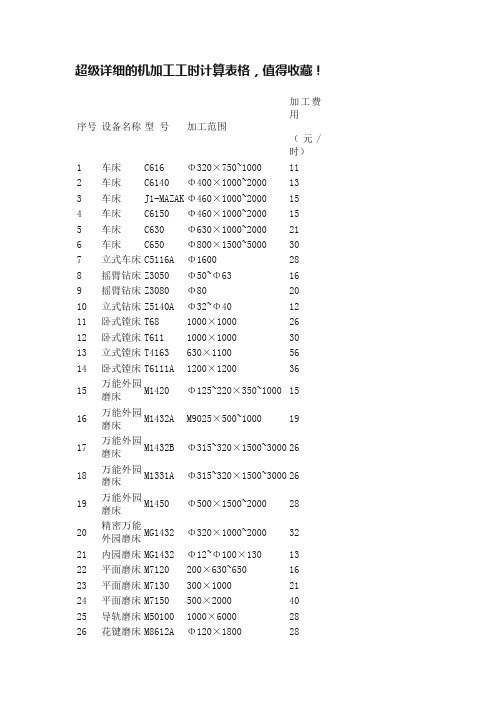
超级详细的机加工工时计算表格,值得收藏!序号设备名称型号加工范围加工费用(元/时)1 车床C616 Φ320×750~1000112 车床C6140 Φ400×1000~2000133 车床J1-MAZAK Φ460×1000~2000154 车床C6150 Φ460×1000~2000155 车床C630 Φ630×1000~2000216 车床C650 Φ800×1500~5000307 立式车床C5116A Φ1600288 摇臂钻床Z3050 Φ50~Φ63169 摇臂钻床Z3080 Φ802010 立式钻床Z5140A Φ32~Φ401211 卧式镗床T68 1000×10002612 卧式镗床T611 1000×10003013 立式镗床T4163 630×11005614 卧式镗床T6111A 1200×12003615 万能外园磨床M1420 Φ125~220×350~10001516 万能外园磨床M1432A M9025×500~10001917 万能外园磨床M1432B Φ315~320×1500~30002618 万能外园磨床M1331A Φ315~320×1500~30002619 万能外园磨床M1450 Φ500×1500~20002820 精密万能外园磨床MG1432 Φ320×1000~20003221 内园磨床MG1432 Φ12~Φ100×1301322 平面磨床M7120 200×630~6501623 平面磨床M7130 300×10002124 平面磨床M7150 500×20004025 导轨磨床M50100 1000×60002826 花键磨床M8612A Φ120×18002827 螺纹磨床Y7520W Φ200×5002028 齿轮磨床Y4632A Φ320×6M3029 万能工具磨床M5MC Φ200×5001330 万能工具磨床MW6020 Φ200×5001331 万能工具磨床M9025 Φ200×6501632 万能工具磨床M6025H Φ250×6501633 万能工具磨床M6425 Φ250×6501634 拉刀磨床M6110D Φ100×1500~17001635 滚齿机YM3150E Φ500×8M2236 杆齿轨YM5150B Φ500×8M1837 立式铣床X5030A Φ300×11201638 立式铣床X52K Φ320×12501839 立式铣床XA5032 Φ320×12501840 卧式铣床X63W Φ400×16002441 滑枕铣床XS5646/1 Φ425×20002842 牛头刨床B665 650×8001443 牛头刨床B650 650×8001144 液压牛头刨床BY60100 900~1000 1645 液压牛头刨床B690 900~1000 1646 龙门刨床B2016A 900~1000 2847 龙门刨床B2020A 2000~6000 5048 杆床B5032 200~320 1249 拉床L6140 40T 1550 划线钳工Φ200×6501551 装配钳工Φ200×6503052 模具钳工Φ200×6503053 加工中心Φ200×6508054 线切割Φ200×650955 焊刀Φ200×6507机加工方法报价表格(范例)一般件、小批量时的单个计价方法加工方法小类和基本参数参数1 参数2和单位价格钻孔单个孔L/d≤2.5d≤25 X*d元'L=孔深,d=孔径' 25≤d<>元L/d>2.5 d≤25 X*d元(*L/d/2.5)25≤d<>元(*L/d/2.5)孔径公差<>对应基价的倍数 X倍孔距公差<>对应基价的倍数 X倍单个孔加工的最低价格 X元附带攻丝钢件 X*d元d=螺纹直径铸铁件 X*d元L=螺纹长度铝件加不锈钢丝套费用 X*d元不加丝套费用 X*d元铜件 X*d元批量优惠批量>200个孔且<>个孔对应基价的倍数 X倍批量>10000个孔对应基价的倍数 X倍车类加工光轴加工'L=轴长,d=轴径,D=毛坯轴径' 一般精度L/d≤10 X*D*L元L/d>10 X*D*L元(*L/d/10)精度<0.05 l>0.05 l>元L/d>10 X*D*L元(*L/d/10)带锥度轴L/d≤10 X*D*L元L/d>10 X*D*L元(*L/d/10)阶梯轴对应光轴基价的倍数 X倍一般精度的丝杠对应光轴基价的倍数 X倍法兰盘类零件d≤430 X*D元d=法兰外径,D=毛坯直径 d>430 X*D元圆螺母零件 X*D元d=圆螺母外径,D=毛坯直径六角螺母零件 X*D元d=六角螺母外径,D=毛坯直径轴套类零件(直径小于100径长比小于2) 'd<100,d>100,d>元d=轴套外径,L=轴套长度'd<100,d>2' X*D元(*d/L/2)100,d>修补轴承座(台)类零件 't<><><>元't=磨损量,d=轴承外径,B=轴承座宽度''t<2,d>40或B>25' X元(*d/40*B/25)2,d>需要上中心架的对应上述基价的倍数 X倍铣床加工一般键槽L=键槽长度,B=键槽宽度位置度公差7级以下的L/B≤10 X*B 元L/B>10 X*B元(*L/B/10)最低价 X元位置度公差7级和以上的对应上述基价的倍数 X倍硬度>HRC40的材料加工对应上述基价的倍数 X倍一般花键L/d≤5 X*d元L=键槽长度,d=轴径 L/d>5 X*d元(*L/d/5)最低价 X元一般齿轮类Z=齿数,m=模数一般圆柱直齿轮 X*Z*m元斜齿轮,伞齿轮,变位齿轮对应上述基价的倍数 X倍铣一般平面每mm2 X元铣沉孔每个 X*d元d=孔径最低价 X元刨床加工平面每mm2 X元t=刨削深度磨削加工一般精度内、外圆 t=磨削深度每mm2 X元一般精度平面 t=磨削深度每mm2 X元一般精度成形磨 t=磨削深度每mm2 X元高精度、小粗糙度对应上述基价的倍数 X倍线切割一般零件S=切断面积每mm2 X元慢走丝每mm2 X元要穿丝每个穿丝孔 X元电火花一般零件S=切断面积每mm2 X元每处最低价 X元电焊 L=焊接长度焊条成本(各种焊条不同:碳钢、不锈钢、铸铁、有色金属等用)每条 X元焊缝长度每mm价格(与材料和焊缝种类有关) X*L元气割一般板件S=切割面积每mm2 X元等离子切割一般碳钢每mm2 X元不锈钢每mm2 X元剪板机一般板件S=剪切面积一般碳钢t≤8每mm2 X元一般碳钢8<><>每mm2 X元t=板厚铝板t≤12每mm2 X元铜板t<>每mm2 X元特别加急件与加班件特别加急件定义为:第一时间安排为某特定客户维修或制造紧急零件。
工时计算方法大全(各机床工时、各工序工时)
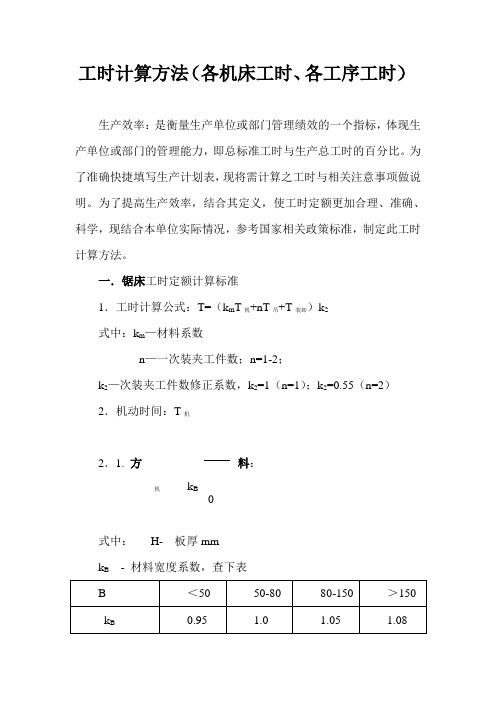
工时计算方法(各机床工时、各工序工时)生产效率:是衡量生产单位或部门管理绩效的一个指标,体现生产单位或部门的管理能力,即总标准工时与生产总工时的百分比。
为了准确快捷填写生产计划表,现将需计算之工时与相关注意事项做说明。
为了提高生产效率,结合其定义,使工时定额更加合理、准确、科学,现结合本单位实际情况,参考国家相关政策标准,制定此工时计算方法。
一.锯床工时定额计算标准1.工时计算公式:T=(k m T 机+nT 吊+T 装卸)k 2 式中:k m —材料系数n —一次装夹工件数;n=1-2;k 2—次装夹工件数修正系数,k 2=1(n=1);k 2=0.55(n=2) 2.机动时间:T 机 2.1. 方料:式中: H- 板厚mm k B - 材料宽度系数,查下表T 机=k BH22.2.棒料:式中D —棒料外径 mm2.3. 管料:式中d 0—管料内径;mm2.4..方管:式中:H—方管外形高mm ;H 0—方管内腔高mm ; B 0—方管内腔宽mm ;3.吊料时间:4.装卸料时间及其它时间:T机=D24T 机=D —d 02 2410000T 机=H—H 0*B 0208000T吊=L 1000 T装卸LD综上所述:方料:T=(0.12+n0.0519H+0.001L )k 2-0.00013 H 0*B 0 (min ) 圆料:T=(0.12+n0.0429D+0.001L )k 2-0.0001 d 02 (min ) n —一次装夹工件数;n=1-2;k 2—次装夹工件数修正系数,k 2=1(n=1);k 2=0.55(n=2)二.剪板冲压折弯工时定额计算标准1..剪板工时定额计算方法剪板单件工时定额:a —每块工时系数、见表b —剪角次数剪板工时系数表=0.12+1800840T =k *a+b a3注:准备工时按100件基数计算,每件0.2,共计200分剪板毛刺工时:T=0.3 + 处理长度/400剪板校正T校=k*T材料系数K=1~1.52.冲压每冲一次工时3..折弯工时定额计算方法折弯工时定额:t2=Σa i折弯工时定额系数表注:规格栏中,为折弯长度,a为每折一刀的工时(理论计算:每刀0.15分×折1.5=0.225+0.2=0.425→0.5)↓准备工时三.风割焊接工时定额计算标准1.风割工时公式:修磨工时含补焊工时: T 修磨 = T 风割 /22.焊接单件工时: T 焊接=T 工件装卸+T 点焊+ T 全焊 2.1 装卸工件工时:T 工件装卸=(T 01+0.2n )B式中:T 01—装卸基本工时;(取T 01=0.2); n-- 工件数 B-- 重量系数(见表)2.2. 点焊单件工时:T 点焊= T 02+0.1J+0.1N式中:T 02—点焊基本工时;J —点焊数;N —点焊时工件翻转次数;2.3. 全焊单件工时:T 全焊= T 03+0.1M+0.1N+L Σ/200+0.2NC 式中:T 03—全焊基本工时;M —焊缝段数;N —全焊时工件翻转次数;L Σ--焊缝长 NC---焊接参数调节次数注:小件装卸与点焊工时合并,统称点焊工时; 重量系数(B )T风割=风割长度×3+1.5V1、飞溅按焊接工时的二分之一计算+0.12、校正按焊接工时的二分之一计算+0.13、有辅助工帮助表卸模,从焊接工时中分取三分之一4、焊接有准备工时按每项20分钟5、点焊螺母按0.5分钟一个四.钻床工时定额1、T=kT机+ T装卸其中k—难度系数有工差要求k=1.5 有深度要求k=1.1 扩孔及攻丝k=0.82、机动时间:T机注:L/D≥8时,须另增排屑时间60%。
Laser标准工时

激光下料标准工时参照表
工 序 上/下料 人 数 2 规 格 1220*2440 ≤300mm ≤500mm >500mm T≤1.0 标准时间 180秒 取料 卸料 2 15秒 20秒 35秒 8mm/1秒 计算方法 作业内容
折弯标准工时参照表
人 数 1 1 1 2 2 1 1 2 2 2 1 1 2 2 2 人 数 1 2 1 1 2 2 规 格 ≤200mm ≤350mm ≤500mm ≤650mm >650mm ≤200mm ≤350mm ≤500mm ≤650mm >650mm ≤200mm ≤350mm ≤500mm ≤650mm >650mm 规 格 标准时间 9秒 12秒 15秒 20秒 30秒 15秒 18秒 25秒 32秒 46秒 15秒 20秒 20秒 20秒 20秒 标准时间 8秒 13秒 8秒/PCS 10秒/PCS 15秒/PCS 6秒/PCS 10秒/PCS 12秒/PCS 备 注
压铆标准工时参照表
备 注
倒角
攻牙
摆放
≤300mm ≤500mm >500mm ≤300mm ≤500mm >500mm ≤300mm ≤500mm >500mm
压铆
摆放
≤300mm ≤500mm >500mm ≤300mm ≤50:
核准:
切割 工 序 Laser下料 上料 作业 卸料
L/8 *T 折弯机加工 备 注 NCT冲切标准:3 秒/次。 同激光卸料时间
NCT下料标准工时参照表
人 数 2 2 2 规 格 1220*2440 一次成型孔 线型冲切 标准时间 180秒 1PCS/3秒 12mm/秒
摆放
沉孔攻牙标准工时参照表
作业内容 取件 人 数 1 2 1 1 1 1 1 1 1 规 格(外型) 标准时间 8秒 13秒 8秒/PCS 12秒/PCS 15秒/PCS 6秒/PCS 12秒/PCS 15秒/PCS 15秒/PCS 18秒/PCS 20秒/PCS 审核: 备 注 作业内容 取件
数控火焰等离子切割机使用说明书

xxxxxxxx xxxxxxxxxxxxxxxxxxxxxx x xxxxxxx SKX 、SKL 序列数控火焰、等离子两用切割机使 用 说 明 书 科技有限公司 电话:- 传真: 网址:邮编: 地址:有限公司生产的本手册为前 言SxX-1型便携式 数控切割机使用说明书。
本手册所记载内容可能有因产品升级、改良生产而与产品相异 的情况,另外,本手册所记载的内容可能在未经预先通知的情 况下更改。
本手册的单位为国际单位,有时与产品的标识不同。
本手册所记载的图片、插图均为打印图片,故有可能与实物有 所出入。
本手册敬请您妥善保存,以备随时查用。
本手册所记载的内容如有不明之处,请与经销商或直接联系厂 家,也可以登陆我们的网站,本公司将竭诚为您服务,及时解 决您的问题。
xxxxx设备维修保养说明及安全操作规程1、防止触电● 当通电或机器正在运转时,请不要接触电器柜和操作台内的任何电气元件。
否则会发生触电。
● 请不要湿手操作任何开关旋钮,以防止触电。
● 请不要带电进行查线或更换电气元件,否则会触电或受伤。
● 具备相应技术资格的维修人员,并应严格按照电气维修技术要求才可维修该设备,以防发生意外。
2、防止火灾● 切割机使用的工作原料为易燃性气体如乙炔、丙烷、液化气等气体,因此需定期检查整个气路是否密封完好。
● 切割机的气源部分应远离明火,并在其附近放置性能正常的二氧化碳或其他相应的灭火装置。
● 操作人员在调火时应对其进行及时控制,以免发生火灾。
3、防止损伤● 当切割机运行时应注意前方是否有人或其他物体,以免撞伤。
● 在每次切割完毕后,应提升割炬到最高处,以免碰到钢板,撞坏割炬。
● 机械维修人员在维修保养时应确保机器处于停止工作状态,并挂上警示牌,以免机器突然运行而发生人为事故。
● 在机器运行较长时间时,不得用手直接触摸模块上的散热片和其它的发热器件,以免烫伤。
4、操作注意事项(1) 开机前检查机器管路是否有漏气现象,有漏气现象决不开机。