库存管理讲义
管理运筹学讲义第11章库存管理

转
高
库
货 批 量
库
存
存
订货点
安全库存
订货间隔期
库存控制参数
订货提 前期
时间
管理运筹学讲义第11章库存管理
第一节 库存的相关概念
三、库存策略
1. (s,Q) 策略
(s,Q)策略是指事先设定订货点s,连续性检查库存量,在每次出库时, 均盘点剩余量。当库存量低于订货点s时,则考虑订货,订货量为Q。
这是定量订货控制策略(Perpetual Inventory Control)
管理运筹学讲义第11章库存管理
第一节 库存的相关概念
二、库存类型
独立需求与相关需求库存
• 相关需求库存是指物品的需求之间具有内在的相关性。 • 独立需求库存是指物品的需求不依赖于其它物品,而是直 接来源于企业外部的需求。
确定性库存与随机性库存
• 确定性库存是指供应过程和需求过程都是确定性的。 • 随机性库存是指供应过程的交货提前期或者需求过程 的需求数量是不确定性的,服从于一定的概率分布。
建立不同的库存模型来解决上面两个问题,如果模型中的需求 率、生产率等一些数据皆为确定的数值时,存贮模型被称为确定性 存贮模型;如果模型中含有随机变量则被称为随机性存贮模型。
管理运筹学讲义第11章库存管理
第一节 库存的相关概念
一、库存系统
库存状态
即存储物的库存数量水平,反映存储物随时间推移而发生的数 量变化,库存量随需求过程而减少,又随供应过程而增加。
最优订货量按下列不等式确定:
管理运筹学讲义第11章库存管理
第三节 随机性库存模型
二、多周期库存模型
下面讨论一个周期t后,库存数量I达到什么水平时,可以 不需订货,假设这一库存水平是s,如何找到订货点s呢? 显然,s点不需订货时的总费期望值C(S)如下:
2013自考《库存管理》讲义——供应链中的库存管理与控制
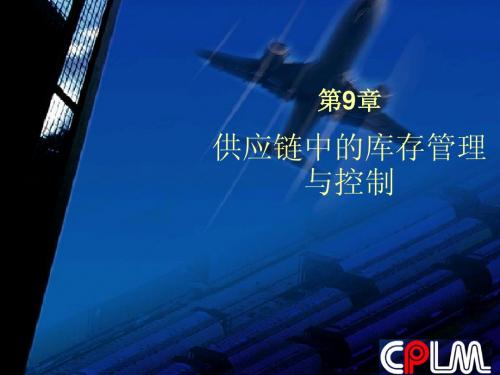
3.探索法
例3:表9-8 已知数据表 表9-9 计算过程与结果。
图9-16 计算结果的布局
三、多重配送系统中的库存 (一)配送网络
(二)水平网络
(三)垂直网络
图9-17 多重梯形配送网络系统
表9-10 水平网络中安全库存的计算公式
例4:假设由一个配送点来满足所有需求时,计算出 某产品的安全库存水平为3885个单位,并假设它们 都保持相同水平的安全库存,那么,仓库总数的增 加时安全库存的情况会如何?
③由于生产故障或递送延迟,DRP计划常易遭受系 统紧张的影响或频繁改动时间表的影响
五、均分法 图9-20 公平份额分配
第5节 展
供应链中的库存管理的发
一、供应链的全球化 (一)全球化的动力
(二)全球化与库存管理
1.全球性公司的战略组成部分 2.发展全球性业务面临的挑战 3.全球化与进货物流、出货物流 (三)全球化的挑战与限制
②产品代码服务水平的计算
③同线产品服务水平
④单位服务水平
三、供应链中的生产库存
(一)生产库存的地点
图9-4 从供应商到客户的过程
图9-5 安全库存的出现示意图
图9-6从供应商到客户的基本结构的示意图 图9-7基本结构中的单个流程示意图 图9-8基础结构以及产品结构图 (二)减少进厂物料和零部件的库存 (三)减少生产过程中的半成品库存 (四)大规模定制在降低库存中的作用
2.改善零售供应链的途径
①采用连续补货系统
②采用流动系统
③采用物流组织
2013自考《库存管理》讲义——库存控制模型

④由于每一次补充库存或货物出库都要进行记录,维持定量订货模型需要的 时间更长。
定量订货系统着重于订购数量和再订购点,每次每单位货物出库,都要进行 记录,并且立即将剩余的库存量与再订购点进行比较。如果库存已降低到再 订购点,则要进行批量为Q的订购;如果仍位于再订购点之上,则系统保持闲 置状态直到有再一次的出库需求。对于定期订购系统,只有当库存经过盘点 后才作出订购决策。是否真正订购依赖于进行盘点的那一时刻的库存水平。
普通的库存控制系统(固定订货量系统和固定间隔 期系统)不适于对一次性订购物品的库存进行控制, 其原因有如下几点:
(1) 一次性订购物品的需求量不连续;
(2)不同时期一次性订购物品的需求量可能有很大 的变化; (3)由于陈旧和易腐使一次性订购物品的市场寿命 非常短促。
典型的一次性订货问题, 不必考虑订货成本, 储存成本也不重要。
第3节 随机型库存控制系统*
一、假设条件
需求率和提前期为已知分布的随机变量,且在不同 的补充周期,这种分布不变。
补充订货在同一时间交付。
允许晚交货,即供应过程中允许缺货,但一旦到货, 所缺货的部分必须补上。
已知年平均需求量。 已知一次订货费,单位维持库存费,单位缺货损失 费。
无价格折扣。
(二)可变需求量,已知提前期;
ห้องสมุดไป่ตู้
三、一次性订货量系统的适用范围 (1)偶而发生的某种物品的需求;
(2)经常发生的某种市场寿命非常短促的物品 的不定量需求。
四、最大最小系统
每隔固定的时间就检查库存并确定库存余额,当库 存余额小于等于订货点时就发出订货,订货量等于 最高库存水平和库存余额的差。该系统由检查期T、 最高库存水谁E和订货点R三个变量所完全确定。当 经过时间间隔t时,如果库存量降到订货点及以下, 则发出订货;否则,再经过时间t时再考虑是否发 出订货。
库存管理讲义修正课件

4000/4×1.5=1500
A类品项4转 B类品项2转 C类品项1转
库存管理讲义修正
16
ABC分类法
销量
65%~75%
SKU约20个周 转率4次/月
SKU 数
10%~20% 20%~25%
SKU约40个周 转率2次/月
20%~25% 10%~15%
60%~70%
SKU约100个 周转率1次/月
库存管理讲义修正
17
四 库存管理的方法 3.2 一阶零售店安全库存量的计算
当期销售=上期库存+上期进货-本期库 以当期销售为依据计算安全库存
淡季安全库存=当期销售 x 1.5 旺季安全库存=当期销售 x 2
建议销售量=安全库存-本期库存
库存管理讲义修正
18
举例
• 上次的总存货箱数 • + 上次订货箱数 • - 本次的存货箱数 • = 零售商售出的箱数 • X 乘以1.5倍 • = 供应存货需要量的150% • - 本次的存货箱数 • = 本次需要的订货量
MA
120
CA-6
90
CA-5
75
CA-4
60
CA-3
45
CB-2
30
CB-1
15
CB-0
9
士多批发商的 库存最低SKU标 准
库存管理讲义修正
15
四 库存管理的方法 3.1 士多批发商安全库存量的计算方法
合理的库存量
安全库存(箱)=月销售箱数/ 月周转次数×1.5(库存安全系数)
例:红牛桶面前月销量4000箱,该 SKU为A类SKU
异常应对 处理方法 5
课程全貌
定义
1
2013自考《库存管理》讲义——库存管理概述

零售商
消费者
供应商 库存
原材料 库存
工厂地的 产成品库 存
区域 产成品库 存
零售 库存
消费者 库存
信息流 物流
库存
(二)库存的弊端* 1.占用大量资金
2.发生库存成本
3.带来其它一些管理上的问题
四、库存管理的基本目标 库存管理的目标就是防止超储和缺货,以最 合理的成本为用户提供所期望水平的服务, 即在达到顾客期望的服务水平下,尽量将库 存成本减少到可以接受的水平。
Hale Waihona Puke 三、库存控制系统要素* 1.仓库所在的地理位置
2.订货批次和订货数量
3.运输
4.信息
5.管理
四、库存管理的过程
(一)确定需求——需求识别与需求预测 (二)存货识别与编码* 1.存货识别与合理化 2.存货编码
(1)编码的内容
(2)编码方法 ①组码 ②条形码*。
第2节 库存分类与库存成本
一、不同企业中的库存问题
表1-1各类企业所遇到的库存问题
企业类型 零售 库存类型 消耗品 √ 原材料 在制品 产成品 √
批发
√
√
制造
√
√
√
√
三、库存的分类
1.原材料库存 2.在制品库存 3.维修库存
(一)按其在生产过程和配送过程中所处的状态分类
4.产成品库存
(三)订购批量与订购时间的确定
(四)服务水平与安全库存的确定 1.服务水平 2.安全库存
条形码是由一组规则排列的条、空以及对应的字符 组成的标记。“条”指对光线反射率较低的部分, “空” 指对光线反射率较高的部分。这些条和空 组成的数据表达一定的信息,并能够用特定的设备 识读,转换成与计算机兼容的二进制和十进制信息。 现在有很多种条码,每种条码有它自己的特征。一 个完整的条形码符号由两侧静区、起始字符、数据 字符、校验字符和终止字符组成,其排列方式如图 1-5所示: 图1-5条形码结构示意图
2013自考《库存管理》讲义——库存需求预测

二、误差精度测量
(一)平均误差
记为MD,其计算方法为:
(五)均方差 记为s2,其计算方法为
1 1 2 2 ei n (Di Fi ) n
MD= (二)平均绝对误差
记为MAD,其计算方法为:
1 n 1 n ei ( Di Fi ) n i 1 n i 1
以下的需求前景的预测。它是制订 年度计划、季度计划、库存预算、 投资等的依据。
短期预测
短期预测是指以日、周、旬、月为
分析方法、因果联系分析方 法以及模拟方法等。
单位,对一个季度以下的需求前景 的预测。它是采购、安排库存等具 体经营活动的依据
常见的预测方法
预测方法的种类 预测方法 一般预测 市场调研 小组共识 历史类比 德尔菲法 简单移动法 简单移动平均 加权平均法 加权移动平均 指数平滑 季节性预测 回归分析 经济计量模型 投入/产出 以计算机为基础的动态模 拟
(二)预测应注意的问题 1.判断在预测中的作 用 2.预测精度与成本 3.预测的时间范围和 更新频率 4.稳定性与响应性
第2节 定性预测方法
一、一般预测 二、市场调查 三、小组共识 四、历史类比 五、德尔菲法
第3节 定量预测方法
一、时间序列分析法 (一)简单平均法 利用一定时期库存数据的平均值,作为下一时期的预 测值。计算公式为: n Di Ft= (2-1)
第4节 预测监控
式中: xi ——第i时刻的实际值; xi'——第i时刻的预测值; ei——第i时刻的预测误差
一、产生误差的原因 误差可能有多种来源,一种常见的来源是将过去的趋势外推 至未来的过程,而很多预测人员却往往没有意识到这一点. 误差在预测中是不可避免的,通常将实际值与预测值之间的 差别定义为预测值的误差,表示为 ei=xi-xi' (2- 14)
管理运筹学讲义 第6讲 库存管理

演讲:王甜源
中山大学南方学院工商管理系
第6讲 库存管理
学习要点 Sub title
正确理解库存系统、库存策略和库存费用 经济订货批量和经济生产批量的适用前提 允许缺货或价格折扣的经济订货批量问题
2
OR:SM
第一节
一、库存系统
库存的相关概念
库存状态
即存储物的库存数量水平,反映存储物随时间推移而发生的 数量变化,库存量随需求过程而减少,又随供应过程而增加
单周期与多周期需求库存
• 单周期库存是指易腐品以及短寿命产品的存储。 • 多周期需求库存则指在足够长的时间里对某种物品 的重复而连续的需求,其库存需要不断地补充。
4
OR:SM
第一节
三、库存策略
库存的相关概念
订货间隔期、订货点和订货批量等参数的不同组合称为库存策略。 即确定什么时间补充库存,和每次补充的数量应该是多少?
二、经济生产批量模型——不允许缺货,且分批到货
与前一个模型的最优库存策略公式相比,此模型的式多了一个 因子, P
P 1 当供给率很快,即P→+∞时, P R PR
此时经济生产批量模型拓变回经济订货批量模型,两组公式完全相同。
因此本模型是前模型当 P→+∞(即生产速度无限快,或一次到货)时
R=30000只/年; c3 =50元/次;k=0.5元/只; c1=0.2c=0.1元/只.年。
(2) 明年仪表产量提高一倍,则R=60000只/年,其它已知条件不变,
得 Q = 2 50 60000 =7746 (只),比今年增加7746-5477=2269(只) 0
R 60000 N * 7.75 (次) 全年订购次数 Q 7746
2013自考《库存管理》讲义——库存绩效与标杆管理

库存绩效与标杆管理
第一节
库存绩效
一、绩效指标及其评价原则 (一)现行企业绩效评价指标的特点
(二)供应链绩效评价应遵循的原则
① 突出重点,对关键绩效指标进行重点分析; ② 采用能反映供应链业务流程的绩效指标体系; ③ 指标要能反映整条供应链的运营情况,而不仅仅 是反映单个节点企业的运营情况;
⑥ 特定时间内没有移动库存的比率。
⑦ 库存满足需求的比率。
⑧ 库存与目标库存的比较。
⑨ 多余库存的数量。 ⑩ 用户报怨的次数。
(三)出入库服务(管理)水平 1.出库率(reat of delivery)
2.供给率( rate of supply)
3.及时发放率(rate of prompt delivery) 4.综合发放率(rate of perfect delivery) 5.收发差错率 6.帐卡物相符率
二、标杆管理流程 第一阶段:什么过程需要标杆管理。
第二阶段:选定标杆学习伙伴。
第三阶段:搜集及分析资讯。 第四阶段:评价与提高。
(一)什么过程需要标杆管理 1.决定向标杆学习什么
2.组成标杆管理小组(学习团队)
图10-1 业务流程图
(二)选定标杆学习伙伴 1.内部标杆学习伙伴 2.外部标杆学习伙伴 3.寻找标杆学习伙伴的优先次序:
(四)标杆管理收益
1.实施标杆管理对一个组织内部规范和操作进行细致观察和研究,可 以更深入了解公司的运作情况。 2.通过标杆管理实施中与最佳者的对比分析,可以确定关键成功因素 和关键绩效指数 (KPIs)。 3.通过比较相似问题的不同解决方法,从他人的经历中进行学习。 4.通过挑战有关绩效、效能、效率及改进潜力等方面的传统观念,标 杆管理能促进组织改革。 5.可以确认并采用最佳流程,而且避免了“复别人探索过程”的不确 定性及时间、金钱的花费。 6.它可以作为一种激发组织中各层次人员创造力的一种方法。 7.标杆管理可增加员工在改进过程中的主人翁意识,因为他们大量参 与了标杆管理体系的引入。 8.由于标杆管理不仅仅关注公司内部,它可引起或增加顾客的注意。
自考《库存管理》讲义__库存控制决策的定量分析

二、基本经济订货间隔期
年总成本=年购入成本+年订货成本+年储存成本
TC=DP+mC+DPH/2m=DP+C/T+DPHT/2
令年总成本对订货间隔期T的一阶导数等于零,得出经济订货间
隔期为:T0 = 2C
DPH
最优年检查次数为:M0=1/T0=
DPH 2C
Q0 =DT0 =D
年总成本=年购入成本+年订货成本+年存储成本
即:TC=C*D/Q+P*H*Q/2+P*D
(4-1)
利用微分法进行求解,对决策变量Q求一阶导数,并令其
为零:
( TC ) Q
DC Q2
PH
2
0
EOQ = 2DC
(4-2)
PH
例4: 某企业每年需要耗用1000件的某种物资,现已知 该物资的单价为20元,同时已知每次的订货成本为5元, 每件物资的年存储费率为20%,试求经济订货批量、年 订货总成本以及年存储总成本。
例2:某公司要用1.2万种物料,其中各种物料的有 关资料如表4-6所示,请对这些物料进行ABC分类
表4-6 各种物料的有关数据资料
解:① 将物品按需求价值从大到小进行排序;
② 计算各种物品占用金额的百分比并进行累计(或 进行品种百分比累计)
③ 按照分类标准,即选择断点进行分类,确定A、 B、C三类物品
=
50(件)
最低总库存成本为:
TC
=
PH
Q
2
C
D Q
PD
=200.250/2+10005/50+201000=20200元
库存管理的讲义InventoryManagement
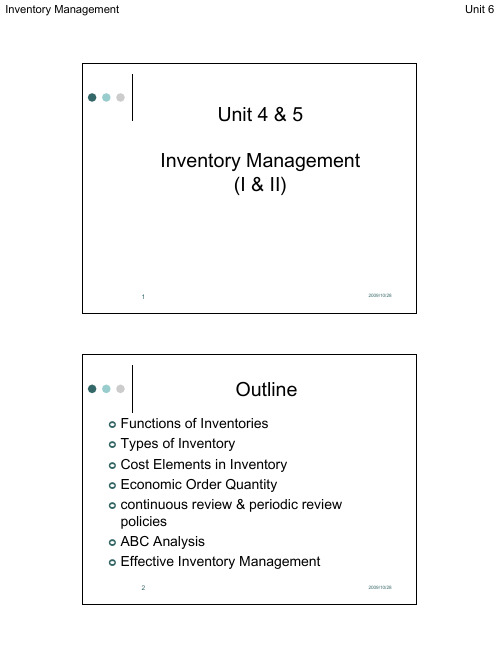
2009/10/281Unit 4 & 5Inventory Management(I & II)2009/10/282Outline|Functions of Inventories|Types of Inventory|Cost Elements in Inventory|Economic Order Quantity|continuous review & periodic reviewpolicies|ABC Analysis|Effective Inventory Management2009/10/283Inventory is an important performancemeasure for a supply chain|In 1998, Dell had 10 days of inventoryand Compaq had 100 days.|When the prices of PC dropped,Compaq was hurt the most ………2009/10/284What is Inventory|Inventory are materials and supplies thata business or institution carries either forsales or to provide inputs or supplies tothe production process. All business andinstitutions require inventories.|they are a substantial part of total assets.2009/10/285Inventory Management|Inventory Management is responsible for planning and controlling inventory from raw material stage to the customer. Since inventory either results from production or supports it, the two cannot be managed separately and, therefore, must be coordinated |Inventory must be considered at each of theplanning levels and is thus part of productionplanning, master production scheduling, andmaterial requirement planning.2009/10/286Role of inventory in the supplychain|Stabilizes the production andworkforce|Supply/Demand uncertainty|Material delivery lead time uncertainty|Speculation (value of item expected toincrease in the future)|Economies of scale in purchasing andtransportation2009/10/287Why Inventory ExistsRate of supply from input processInventoryRate of demandfrom output process 2009/10/288Functions of Inventories|Inventory serves as buffer between:z Supply and demandz Customer demand and finished goodsz Finished goods and componentavailabilityz Requirements for an operation and theoutput from the preceding operationz Parts and materials to begin productionand the suppliers of materials2009/10/289Factors affecting inventorylevel|There are many factors affecting theinventory level and hence the inventory costin a Supply Chain, the following are some ofthe most important ones:zService level zDemand and supply variability zLead time and lead time variability zInformation (demand information)z Supply chain cost2009/10/2810Type of Inventory|Anticipation Inventory|Buffer Inventory|Cycle Inventory|Pipeline Inventory2009/10/2811Anticipation Inventory|Anticipation inventories are built up inanticipation of future demand.|For example, they are created ahead of apeak selling season, a promotion program,vacation shutdown, or possibly the threat ofa strike.|They are built up to help level productionand to reduce the costs of changing production rates 2009/10/2812Buffer Inventory (Safety Stock)|Inventory is held to cover randomunpredictable fluctuations in supply anddemand or lead time.|If demand or lead time is greater thanforecast, a stockout will occur.|Safety stock is carried to protect againstthis possibility. Its purpose is to preventdisruptions in manufacturing or deliveries tocustomers.|Safety stock is also called reserve stock.2009/10/2813Cycle Inventory|Cycle inventory occurs becauseone or more stages in the operationcannot supply all the items itproduces simultaneously.2009/10/2814Pipeline Inventory|Pipeline inventory exist because of the timeneeded to move goods from one location toanother such as from a plant to a distributioncentre of a customer.|They are sometimes called TransportationInventory or Movement Inventory.2009/10/2815Objectives of Inventory Management|A firm wishing to maximize profit willhave at least the following objectives:•Maximum customer service•Low-cost plant operation•Minimum inventory investment 2009/10/2816Possible InventoryLocationSuppliers CustomerTotal company InventoryManufacturingDistributionCustomer Delivery Raw Materials Inventory Work-in-process Inventory Finished Product Inventory2009/10/2817Cost Elements in Inventory1.Item cost 2.Carrying costs 3.Ordering costs 4.Stockout costs 5.Capacity-associated costs 2009/10/2818Item Cost|Item cost is the price paid for a purchase item, which consists of the cost of the item and any other direct costs associated in getting the item into the plant. |These could include such things as transportation, custom duties, and insurance. The inclusive cost is often called the landed price .|For an item manufactured in-house, the cost includes direct material, direct labor, and factory overhead . |These costs can usually be obtained from eitherpurchasing or accounting.2009/10/2819Carrying Costs|Carrying Costs include all expenses incurred by the firm because of the volume of inventory carried. |As inventory increase, so do thesecosts. They can be broken downinto three categories:1.Capital costs2.Storage costs3.Risk costs 2009/10/2820Ordering Costs|Every time an order is placed to replenish stock a number of transactions are needed which incur costs to the company. |These include the clerical tasks ofpreparing the order and all thedocumentation associated with it,arranging for the delivery to be made,arranging to pay the supplier for thedelivery, and the general costs ofkeeping all the information whichallows us to do this.2009/10/2821Stockout Costs|If demand during the lead time exceeds forecast, we can expect a stockout. |A stockout can potentially be expensive because of back-order costs, lost sales, and possibly lost customers.|Stockout can be reduced by carrying extra inventory to protect against those times when the demand during lead time is greater than forecast.2009/10/2822Capacity -Associated Costs|When output levels must be changed, there may be costs for overtime, hiring, training, extra shift, and layoffs.|These capacity-associated costs can be avoided by leveling production,that is, by producing items in slack periods for sale in peak periods.|However, this builds inventory in the slack periods.2009/10/2823Cost trade-offs to Be Considered by the Purchasing Executive* The savings associated with volume buying include:Lower per-unit purchasing prices Lower transportation costsLower warehouse handling costs Lower order-processing costsLower production lot quantity costs Lower stockout costsThe costs of carrying inventory include:Capital costs associated with the inventory investment Inventory service costs (insurance and taxes)Storage space costs Inventory risk costs Cost savings associated with volume buying *Inventory carrying costs ±Source: Douglas M. Lambert and Jay U. Sterling, “Measuring Purchasing Performance,”Production and InventoryManagement Review 4, no.6 (June 1984), p. 52. Reprinted with permission from P&IM Review, June 1984. Copyright 1984 by T.D.A. Publications, Inc., Hollywood, FL.2009/10/2824Methods of Accounting for Inventory|First-in, First-out (FIFO)zStock acquired earliest is assumed to be sold first, leaving stock acquired more recently in inventory |Last-in, First-out (LIFO)zSales are made from the most recently acquired stock, leaving items acquired in the earliest time period in inventory|Average CostzEach new purchase is averaged with the remaining inventory to obtain a new average price2009/10/2825Class Exercise2009/10/2826Inventory Cycle ChartPeriods of Time (days)Q u a n t i t y o f I t e m i n S t o c kSafety LevelZero StockOperating LevelPeak inventoryOrder Lead TimeRe-Order CycleReceipt of supplyOrder PointConsumption ReplenishmentAverage Inventory2009/10/2827Economic Order Quantity Method|The EOQ method is an attempt to estimate the best order quantity by balancing the conflicting cost of holding stock and of placing replenishment orders|The large order quantity gives a much higher average stock level , and the small order quantity gives a lower average stock level |The small order quantity must bereplenished by placing many more orders than the large order quantity2009/10/2828Economic Order Quantity MethodAssumptions1.Demand is relatively constant and is known.2.The item is produced in lots or batches and not continuously3.Order preparation and inventory-carrying costs are constant and known.4.Replacement occurs all at once.2009/10/2829The Economic Order QuantityI n v e n t o r y L e v e lTimeDemand (D) = 1000 items per yearPlan A Q = 400Plan B Q = 100Average Inventory for Plan A = 200Average Inventory For Plan B = 500.1 Year0.4 Year2009/10/2830The Economic Order Quantity (2)|Average Inventory = Order Quantity/2zPlan A = 200z Plan B = 50|Number of Orders per year = Annual Demand/Order QuantityzPlan A = 1000/400 = 2.5z Plan B = 1000/100 = 10|Annual Cost of Placing Orders |Annual Cost of Carrying Inventory2009/10/2831The Economic Order Quantity (3)D =Annual Usage in Units (1000)S =Ordering Cost in Dollars Per Order ($20)i =Annual Carrying Cost rate as a % (50%)c =Unit Cost in Dollars ($2)Q=Order Quantity in Units (400, 100)|Annual Cost of Placing Ordersz Plan A (2.5 x 20 = $50)zPlan B (10 x 20 = $200)|Annual Cost of Carrying Inventoryz Plan A (400/2 x $2 x 50% = $200)zPlan B (100/2 x $2 x 50% = $50)2009/10/2832Cost & Ordered Quantity Trade-offTotal CostsCarrying CostsProcurement (ordering cost) & Out-of-stock CostsEOQQuantity OrderedT o t a l R e l e v a n t C o s t s2009/10/2833|The optimum quantity for inventory procurement when procurement cost equals to carry costEconomic Order Quantity2DS ICEOQ =D = Annual Usage in UnitsS = Ordering Cost in Dollars Per OrderI = Annual Carrying Cost rate as a % C = Unit Cost in Dollars Q = Order Quantity in Units2009/10/2834Example of EOQAnnual Demand (D): 1000 units Ordering Cost (S):$20Carrying Cost Rate (i):50%Unit Cost in $ (c):$2Q = 2(1000)(20)$2 x 0.5= 400001EOQ = 200 units2009/10/2835Example Problem|An item has an annual demand of 5000 units, Ordering costs are $20 per order, and the cost of carrying inventory is 20%. The cost per unit is $5.|What is:z D = z S = z c = zi = |Then :zEOQ =2009/10/2836Example Problem|An item has an annual demand of 5000 units, Ordering costs are $20 per order, and the cost of carrying inventory is 20%. The cost per unit is $5.|What is:z D = 5000 units z S = $20z c = $5zi = 0.2|Then :zEOQ = 2 x 5000 x 205 x 0.2= 447.21 or 448 units2009/10/2837Class exercise2009/10/2838Fixed order quantity system|Perpetual inventory system|Event triggered: Initiates order when stock depleted to a specific level.zReorder point|Inventory replaced in fixed amountszEconomic order quantities|Issues: visual signals, IT applications2009/10/2839Fixed Order Quantity Systemlead time (L)ROPcycle stockINVENTORYTIMEROP = Lead time demand2009/10/2840Safety Stock|Safety stock is held because of uncertainty in supply and/or demand|The trade-off is the cost of stocking out versus the cost of holding inventory|Safety stock levels can be calculated using statistical techniques.z e.g., Take into account standard deviation of demand2009/10/2841Fixed Order Quantity System:Cycle Stock, Safety Stock and Lead Timelead timeROPcycle stock (Q)INVENTORYTIMESafety Stock2009/10/2842Fixed time period systems|Inventory on-hand counted at specific time intervals and replenished to a desired level|Only the passage of time triggers the model2009/10/2843Fixed Time Period System :Cycle Stock, Safety Stock and Lead TimeINVENTORYTIMESafety Stockreview periodlead timeQ2009/10/2844Replenishment Policies|When to reorder?|How much to reorder?|Continuous Review : order fixed quantity when total inventory drops below reorder point (ROP)|Periodic review : order at fixed time intervals to raise total inventory to order up to level (OUL)2009/10/2845Inventory systems|Continuous Review system:zsystem that keeps track of removals from inventory continuously, thusmonitoring current levels of each item. z When stock level reaches a certain level (ROP), an order of fixed quantity (EOQ) is placed2009/10/2846Inventory systems|Periodic review system:zOrders are placed at fixed review period (RP) intervals.z The order quantity varies and is calculated to meet somepredetermined target inventory level (TIL)2009/10/2847Comparing continuous review & periodic review policies|Factors driving safety inventory in periodic review policyz Demand uncertaintyz Replenishment lead time z Service level zReorder interval|Periodic review policy is easier and cheaper to implement|Periodic review policy requires more safety inventory than continuous review policy for the same lead time and service level2009/10/2848Inventory Priorities –ABC SystemPercentage Percentage value of itemsof annual usage Class A items About 20%About 80%Class B items About 30%About 15%Class C itemsAbout 50%About 5%2009/10/2849Classifying Inventory|ABC Analysis based on Pareto ’s Law –the “80 –20 Rule ”.|Decision steps in applying ABC Analysis:zSelect criterion appropriate for inventory under consideration eg sales revenue z Rank items in descending order of importancez Calculate actual and cumulative total sales revenuez Assign items into ABC groups 2009/10/2850Product Classification Analysis (ABC)Product Number Sales (000)Percent of Sales CumulatoveSales PercentCumulatirveProducts PercentCategory145,00030.030.05A 235,00023.353.310A 325,00016.770.015A 415,00010.080.020A 58,000 5.385.325B 65,000 3.388.730B 74,000 2.791.335B 83,000 2.093.340B 92,000 1.394.745B 101,0000.795.350B 111,0000.796.055C 121,0000.796.760C 202500.2100.00100C2009/10/2851A Typical Pareto Curve with ABC AnalysisS a l e s V a l u eNumber of Products20%50%100%80%95%100%Class CClass BClass A2009/10/2852Steps in Making an ABC Analysis1.Establish the item characteristics that influence the results of inventory management. This is usually annual dollar usage but may be other criteria, such as scarcity of material.2.Classify items into groups based on the established criteria.3.Apply a degree of control in proportion to the importance of the group.2009/10/2853Control Based on ABC Classification|Different controls used with different classifications might be the following:z A items: high priority.•Tight control including complete accurate records, regular and frequent review by management, frequent review of demand forecasts, and close follow-up and expediting to reduce lead timezB items: medium priority.•Normal controls with good records, regular attention, and normal processing.zC items: lowest priority.•Simplest possible controls –make sure there are plenty.•Simple or no records; perhaps use a two-bin system or periodic review system.•Order large quantities and carry safety stock .2009/10/2854ABC AnalysisA Items|Very tight control|Order only calculated or know requirement |Accurate recording of receipts and issues |Schedules constantly reviewed |Continuous progressing|Minimal buffer stocks (probably less than 2 weeks)2009/10/2855B Items|Moderate level of control|Order against forecast from historical data |Recording of all receipts and issues |Moderate level of review of schedules |Progress items in short supply or late |Larger buffer stocks (6 –8 weeks)ABC Analysis (Cont)2009/10/2856ABC Analysis ( Cont )C Items|Lower level of control|Minimal recording of receipts/issues |Low level of schedule review |No progressing|Large safety stocks (12 weeks)2009/10/2857Class Exercise2009/10/2858Symptoms of Poor Inventory|Increasing numbers of back orders|Increasing dollar investment in inventory with back orders remaining constant.|High customer turnover rate.|Increasing number of orders being cancelled.|Periodic lack of sufficient storage space.|Wide variance in inventory turnover among distribution centers and major inventory items.Effective Inventory Management|Traditional method –adequate safetystock of inventory|Contemporary method –adoption of VMI & ECR|EIM depends highly on IT communicationnetwork require information sharingbetween suppliers and customers shiftingresponsibility for managing andreplenishing inventory to vendor2009/10/28 59。
库存管理讲义

第12章库存管理库存管理是生产管理体系中最为悠久的分支之一,库存管理的内容包含仓库管理和库存控制两个部分。
仓库管理的内容是指库存物料的科学保管,以减少损耗,方便存取;库存控制则是要求控制合理的库存水平,即用最少的投资和最少的库存管理费用,维持合理的库存,以满足使用部门的需求和减少缺货损失。
本章主要讨论库存控制。
库存管理概述库存(Inventory )的定义国民经济的各个行业,尤其是制造业和服务业都会遇到库存问题。
狭义的理解,库存即放在仓库中,暂时未被利用的物资。
从广义上理解,凡是处于暂时闲置状态,尚未被利用的各类社会资源都可被视为库存。
与这种资源是否存放在仓库中,是否处于运动状态没有关系。
放在仓库里是闲置,准备被利用,铁路运输中的货物,是为了未来需要而闲置在途中,是一种在途库存。
库存的作用库存是闲置的资源,不能立即为企业产生效益,但库存又是必须的,因为库存有以下重要的作用。
1•满足预期顾客的需求一定的成品库存可以使顾客很快采购到他们所需要的物品。
这样,可以缩短顾客的订货提前期,也有利于供应厂商争取预期顾客。
2.平滑生产的均衡性外部的需求总是波动的,而企业的生产要求具有均衡性。
要满足需方的波动的需求,又要使供方的生产均衡,就必须维持一定量的库存。
3.分摊订货费用订货需要费用,需要一件订购一件,将订货费用摊在一件物品上,是不经济的。
一次采购一批,虽然会造成库存,但可以将订货费用分摊到各件物品上,是经济的。
在生产过程中,采用批量生产加工,可以分摊生产准备费用和结束整理费用。
4.防止缺货维持一定量的库存,可以防止缺货的产生。
商店没有一定量的货物库存,顾客就买不到东西;酒店没有一定的床位库存,游客就不能入住;在生产过程中维持一定量的在制品,可以防止生产因缺货而中断。
5. 避免价格上涨企业对有涨价可能性的物资会加大库存量,也会通过加大订货量以获取数量折扣。
库存具有重要的作用,但也有其不利的一面。
库存要占用资金,物资的库存要修建仓库;要维持库存物品不损耗、不老化,都需要大量支出。
精选库存管理培训讲义

按量折扣模型
权重:
按量折扣模型
一致折扣模式下的最优订货策略: 针对各个折扣价格计算对应的EOQ值
按量折扣模型
一致折扣模式下的最优订货策略:
按量折扣模型
一致折扣模式下的最优订货策略:
按量折扣模型
一致折扣模式下的最优订货策略: 有三个值可以作为最优解的候选者:400, 500 和 1000。 单位时间的成本函数如下
按量折扣模型
分段折扣模型:
按量折扣模型
分段折扣模型:
按量折扣模型
分段折扣模型:
按量折扣模型
分段折扣模型:
按量折扣模型
分段折扣模型: 和 均为有效值;因为 ,所以 为无效值。 最优解可通过比较 和 的大小而获得。
按量折扣模型
分段折扣模型:小结对于每个价格区间,确定其对应的成本代数表达式将 的表达式代入 表达式中 从上一步中确定最小的有效值(即落在正确的区间中)
经济订货批量(EOQ)模型
基本模型:经济订货批量 (EOQ)
经济订货批量(EOQ)模型
基本模型: 从上述图中可见,最小总成本恰巧是两个分项成本的交叉点。 注意在经济订货批量Q* 的计算公式中,没有进货价格 c。
经济订货批量(EOQ)模型
例1: 单位时间的需求率 保管费用 换产成本 经济订货批量 EOQ
资源受限时多品种库存系统
解: 我们只需将各EOQ值乘以比率 30000 / 35835 = 0.8372 即可。
资源受限时多品种库存系统
一般地,假定 n 类品目其单位成本为 c1, …, cn, 总的可利用投入为C。
资源受限时多品种库存系统
两种可能性:1)所得的EOQ解有效;2)所得的EOQ解违反约束条件。 如果所得的EOQ解有效,则 如果所得的EOQ解违反约束条件,则
- 1、下载文档前请自行甄别文档内容的完整性,平台不提供额外的编辑、内容补充、找答案等附加服务。
- 2、"仅部分预览"的文档,不可在线预览部分如存在完整性等问题,可反馈申请退款(可完整预览的文档不适用该条件!)。
- 3、如文档侵犯您的权益,请联系客服反馈,我们会尽快为您处理(人工客服工作时间:9:00-18:30)。
第12章库存管理库存管理是生产管理体系中最为悠久的分支之一,库存管理的内容包含仓库管理和库存控制两个部分。
仓库管理的内容是指库存物料的科学保管,以减少损耗,方便存取;库存控制则是要求控制合理的库存水平,即用最少的投资和最少的库存管理费用,维持合理的库存,以满足使用部门的需求和减少缺货损失。
本章主要讨论库存控制。
库存管理概述库存(Inventory)的定义国民经济的各个行业,尤其是制造业和服务业都会遇到库存问题。
狭义的理解,库存即放在仓库中,暂时未被利用的物资。
从广义上理解,凡是处于暂时闲置状态,尚未被利用的各类社会资源都可被视为库存。
与这种资源是否存放在仓库中,是否处于运动状态没有关系。
放在仓库里是闲置,准备被利用,铁路运输中的货物,是为了未来需要而闲置在途中,是一种在途库存。
库存的作用库存是闲置的资源,不能立即为企业产生效益,但库存又是必须的,因为库存有以下重要的作用。
1. 满足预期顾客的需求一定的成品库存可以使顾客很快采购到他们所需要的物品。
这样,可以缩短顾客的订货提前期,也有利于供应厂商争取预期顾客。
2. 平滑生产的均衡性外部的需求总是波动的,而企业的生产要求具有均衡性。
要满足需方的波动的需求,又要使供方的生产均衡,就必须维持一定量的库存。
3. 分摊订货费用订货需要费用,需要一件订购一件,将订货费用摊在一件物品上,是不经济的。
一次采购一批,虽然会造成库存,但可以将订货费用分摊到各件物品上,是经济的。
在生产过程中,采用批量生产加工,可以分摊生产准备费用和结束整理费用。
4. 防止缺货维持一定量的库存,可以防止缺货的产生。
商店没有一定量的货物库存,顾客就买不到东西;酒店没有一定的床位库存,游客就不能入住;在生产过程中维持一定量的在制品,可以防止生产因缺货而中断。
5. 避免价格上涨企业对有涨价可能性的物资会加大库存量,也会通过加大订货量以获取数量折扣。
库存具有重要的作用,但也有其不利的一面。
库存要占用资金,物资的库存要修建仓库;要维持库存物品不损耗、不老化,都需要大量支出。
不仅如此,大量的库存还可能掩盖某些管理中的问题。
库存控制的目标1. “零库存”的境界“零库存”的观念在20世纪80年代成为一个流行的术语。
如果供应部门能够紧随需求的变化,在数量上和品种上都可以及时供应所需物资,即实现供需同步。
那幺,库存就可以取消,即达到“零库存”。
有一项统计反映,美国拥有的存货价值超过6500亿美元,这些存货由于这种或那种原因存放在仓库里,如果能将其中的一半解放出来用于投资,按比较保守的10%的收益率计算,将有325亿美元的年收入。
因此,企业经营者将减少库存作为一种潜在的资本来源,将“零库存”作为一种追求,就不足为怪了。
但由于需求的变化往往随机发生,难以预测,完全实现供需同步是不易做到的,而且由于供应部门、运输部门的工作也会不时出现某些故障,使完全的“零库存”只能是一种理想的境界。
2. 库存控制的目标现代管理要求在充分发挥库存功能的同时,尽可能地降低库存成本。
这是库存控制的基本目标。
库存控制应实现:(1)保障生产供应库存的基本功能是保证生产活动的正常进行,保证企业经常维持适度的库存,避免因供应不足而出现非计划性的生产间断。
这是传统库存控制的主要目标之一。
现代的库存控制理论虽然对此提出了一些不同的看法,但保障生产供应仍然是库存控制的主要任务。
(2)控制生产系统的工作状态一个精心设计的生产系统,均存在一个正常的工作状态,此时,生产按部就班地有序进行。
生产系统中的库存情况,特别是在制品的数量,与该系统所设定的在制品定额相近。
反之,如果一个生产系统的库存失控,该生产系统也很难处于正常的工作状态。
因此,现代库存管理理论将库存控制与生产控制结合为一体,通过对库存情况的监控,达到生产系统整体控制的目的。
(3)降低生产成本控制生产成本是生产管理的重要工作之一。
无论是生产过程中的物资消耗,还是生产过程中的流动资金占用,均与生产系统的库存控制有关。
在工业生产中,库存资金常占企业流动资金的60%-80%,物资的消耗常占产品总成本的50%-70%。
因此,必须通过有效的库存控制方法,使企业在保障生产的同时,减少库存量,提高库存物资的周转率。
库存ABC管理企业的库存物资种类繁多,对企业的全部库存物资进行管理是一项复杂而繁重的工作。
如果管理者对所有的库存物资均匀地使用精力,必然会使其有限的精力过于分散,只能进行粗放式的库存管理,使管理的效率低下。
因此,在库存控制工作中,应强调重点管理的原则,把管理的重心放在重点物资上,以提高管理的效率。
ABC分析法便是库存控制中常用的一种重点控制法。
ABC分析法的基本思想意大利经济学家帕累托(Vilpredo Pareto_)在调查19世纪意大利城市米兰的社会财富分配状况时发现,米兰市社会财富的80%被占人口20%的少数人占有,而占人口80%的多数人,仅占有社会财富的20%。
帕累托把其统计结果,按从富有到贫穷的顺序排列,绘制成管理界所熟知的帕累托图(如下图)。
后来,发现类似于帕累托图所显示的分布不均匀的统计现象,不仅存在于社会财富的分布上,而且普遍存在于社会经济生活的许多方面。
即所谓的20-80律,也有简称为2-8律的。
ABC分析法基于20-80律,即20%左右的因素占有(带来)80%左右的成果。
如,在超市中,占品种数20%左右的商品为企业带来了80%左右的销售额,20%左右的员工为企业作出了80%左右的贡献等。
图帕累托图库存管理的ABC分析法还在20-80律的指导下,分析企业的库存,以找出占有大量资金的少数物资,并加强对它们的控制。
这样,可以只用20%左右的精力就控制了80%左右的库存资金的管理。
而对那些只占少量资金的多数物资,则施以较轻松的控制和管理。
ABC分析法把企业占用65%-80%价值,而品种数仅为15%-20%的物资划为A类;把占用了15%―20%价值,品种数为30%-40%的物资划为B类;把占用了5%-15%价值,品种数为40%-55%的物资划为C类。
对ABC各类物资采用不同的管理方式,增强管理的针对性。
达到简化管理程序,提高管理效率的目的。
ABC分析法的实施实施ABC分析法的具体步骤:1. 根据企业的库存物资信息,计算各库存物资占用资金情况。
具体做法是把每一种物资的年使用量乘上单价。
年使用量可以根据历史资料或本年预测数据来确定。
为更好地反映现状,一般使用预测数据。
2. 把各库存物资按资金占用情况,从多到少的顺序排列,并计算出各库存物资占用资金的比例。
(见表)表浦光机器厂2004年库存物资资金占用统计表物资代码年使用量单价(元)年资金占用量(万元)资金占用比例(%)K-8400件20000800 S-12500件10000500 S-82000件6001203. 分析各库存物资占用资金情况,将各物资归入相应的类别,完成分类。
表是对表的数据进行分类处理后的结果。
表浦光机器厂2004年库存物资ABC分类汇总表ABC分析法的运用对库存物资进行ABC 分类后,企业可以对不同类别的物资采用不同的控制策略。
1. A类物资是控制的重点。
,应该严格控制其库存储备量、订货数量、订货时间。
在保证需求的前提下,尽可能减少库存,节约流动资金。
2. B类物资可以适当控制,在力所能及的范围内,适度地减少B类库存。
3. C类物资可以简单控制,增加订货量,加大两次订货期间的时间间隔,在不影响库存控制整体效果的同时,减少库存管理工作的工作量。
需要注意的是,在实际的库存物资分类工作中,在考虑到资金占用情况的同时,要兼顾供货和物资重要程度等因素。
一些特别关键或供应较难保障的物资,虽然占用资金不多,但需要按A类物资对待。
沃尔玛为师。
沃尔玛花4-6周的时间进行库存的准备工作,公司的内部审计部门提前45天给每个分店下达库存指南,内容包括库存管理的各项具体要求以及13项业务流程。
沃尔玛的库存管理小组有18-40名成员,由盘点员和公司运行部门、损失预防部门和内部审计部门的代表组成。
沃尔玛的各分店一般在上午8点到下午6点之间做好库存记录,库存记录填写完毕之后,盘点小组立即盘点,并将盘点结果与库存记录进行比较,根据盘点结果来修正库存记录,最后由公司内部审计部门复审所有物资每11-13个月彻底盘点1次,大部分盘点在3-9月份进行。
彻底盘点一般不在11月份和12月份进行,因为这时盘点会干扰大家过圣诞节;也不在1月份的第1周进行,因为这时员工还没完全进入工作状态,他们正忙于互致问候与互赠礼品。
沃尔玛的库存年周转次(同行竞争者的年平均周转次数为次),所有分店销售的产品的品种在6万-9万种之间。
从这些数字可以看出,沃尔玛的库存管理工作做起来不是那幺容易。
沃尔玛在两次盘点之间采用一个专门的连续系统来记录商品售出时间、售出商品的成本和数量。
这样,每个盘点期之后所售商品的成本与数量都能准确地统计,同时也能知道任何时候手中现货的成本和数量。
资料来源:. “Inventory on a Grand Scale,” Supermarket Business, February 1997 . Reproduced with permission from Supermarket Business.库存控制模型物资储存模型和经济订购批量的制定1. 无保险储备的定量储存模型图是无保险储备的库存变化模型,从中可看出当时间为零时,储存量为Q,随着生产进行,物资陆续领出,库存成线性递减。
当库存量降到R时,采购人员就得以批量Q的数量去订购,并要求在时间T L内送到,以保证生产的进行。
现在的问题是如何来确定订购批量Q,使总费用最省图无保险储备的定量储存模型。
设A 为该物资全年需要量,M 为物资单价,C 为单位物资全年持有费用,P 为每次订购费用。
因库存量在Q 与零之间均匀变动,则其理论上的库存量平均值为2Q。
于是,全年持有费用为2QC 。
全年订购费用应为每年订购次数Q A 与P 的乘积。
全年物资费用为AM ,则全年总费用T 为T=AM QAP 2CQ ++ 式中:AM 为全年固定的物资费用QAP2CQ +为全年可变费用 可变费用的大小随着Q 的变化而变化。
式中C 、P 、A 、M 都是常量,故T 实际上只是Q的函数。
现要知Q 为多少才能使T 最小,这可用求极小值的方法求得。
即令:0Q AP2C dQ dT 2=-= 得Q=C2AP再求二次导数:0Q2APdQ T d 322>= 因而求得经济批量(简称EOQ )Q 0为:Q 0=Q2AP因此,只要知道A 、P 、C 三个数值,即可算出Q 0。
[例1] 某厂每年需某种零件4,000件,该零件单价10元,每只零件每年的持有费用为5元,每次订购费用为100元,求经济批量Q 0。