5S推行实务--整理的推进重点(PPT 76)
5S推进实战要点课件
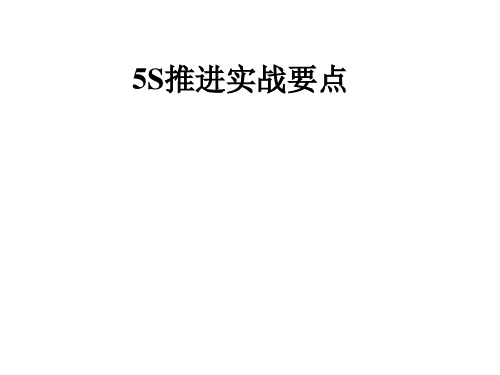
不良; 5)通过定期的点检,可以清除引发不良的因素。
5S的起源
1.5S的沿革
• 5S起源于日本,是指在生产现场中 对人员、机器、材料、方法等生产 要素进行有效的管理,这是日本企 业独特的一种管理办法。
造成; 5、形象的浪费:仪容不整;坐姿不当,机器设备保养不当
造成;
6、效率浪费:机器、物品、工具乱摆放,运料通道不当,坐 姿不当造成;
7、品质的浪费:机器设备保养不当,物品乱摆放等造成; 8、成本的浪费:机器设备保养不当,物品乱摆放等造成;
注:本节教学时宜采取提问或诱导方式,引导学员积极思考, 加深理解。
英文
典型例子
Organization 倒掉垃圾、长期不 用的东西放仓库
Neatness
30秒内就可找到要 找的东西
Cleaning
谁使用谁负责清洁 (管理)
Stangardisatio 管理的公开化、透
n
明化
Discipline and 严守标准、团队精
training
神
• 5S活动不仅能改善生活环境,还可 以提高生产效率,提升产品的品质、 服务水准,将整理、整顿、清扫进 行到底,并且给予制度化等等,这 些都是为了减少浪费,提高工作效 率,也是其它管理活动有效展开的 基础。
产效率,同时增加修理成本。
不良现象之四:物品随意摆放 例子:1)原材料随意摆放(如多种Model的材料混在一起);
2)半成品在流水线上叠放或随便放在作业台上; 3)未构成一个LOT的成品在成品区乱摆放; 4)外观投入待期品在生产线之间乱摆放; 5)不良待修品在修理处乱摆放;泡沫箱在包装工程旁边摆
5S推进实务课件

7.赞扬为零
规范化的推进者
8.出勤为零
发明快乐的岗位
第九页,共107页。
5S之间的关系(guān xì)
整理是整理的基础,反之是动摇
只需整理没有整理 只需整理没有整理 整理整理没清扫 3S之效果怎保证
一招 规范作业练素养
物品真难找的到 无法取舍乱糟糟 物品运用不牢靠 清洁(qīngjié)出来献
公司管理水平高
• 迅速快捷传递信息 • 笼统直观显现效果和糜费 • 有利于分歧看法,提高士气 • 促进企业文明(wénmíng)的构成和树立
• 向心力,凝聚力 • 5W2H WHO WHAT WHEN WHERE
WHOM HOW HOW MUCH
第四十五页,共107页。
目视管理(guǎnlǐ)的类别〔消弭黑 箱作业〕
常用(chánɡ yònɡ)的宣传谋划方 式
• 口号 • 标语 • 建议书 • 板报墙报 • 有奖竞赛 • 口号征集 • 有奖征文
环境引入企业(qǐyè)评价
第三十七页,共107页。
教育(jiàoyù)培训的步骤
• 制定教育培训(péixùn) 概要目的
方案〔PLAN〕
实施方法(fāngfǎ)
• 教育培训(péixùn)的执 评选方法(fāngfǎ)
上下班〞5分钟S〝 领班(lǐnɡ bān)值日制
竞赛-建议阶段 看板管理,目视管理
第三十页,共107页。
5S推进(tuījìn)八大要诀
• 1全员参与(cānyù) 其乐无量 • 2培育5S大气候 • 3指点挂帅 • 4彻底了解5S肉体 • 5立竿见影的方法 • 6指点巡视现场 • 7上下一心 彻底推进 • 以5S为改善的桥梁
第十四页,共107页。
5S活动推行实务PPT课件(43页)
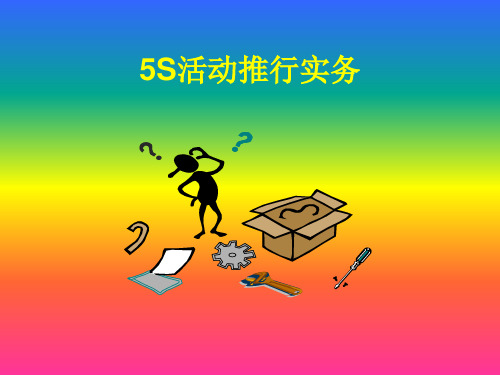
清扫。
素养
实施内容 :
➢ 日常工作有计划和时间观念; ➢ 礼仪习惯。
❖ 人人养成好习惯,依规定行事,培养积极进 取的精神。
❖ 目的: ❖ 培养具有好习惯、遵守规则的员工 ❖ 营造团队精神
四、如何推行5S
❖ 1、整理 实施要领
❖ 1.1自己的工作场所(范围)全面检查,包括 看得见和看不见的地方(如设备内部、踏板底 等);
普通 1~2个月使用1次或以上 置于车间内 各摆放区
1周使用数次 常用 1日使用数次
每小时都使用
工作区内 随手可得
如机台旁 流水线旁 个人工具箱
清扫
实施内容 :
➢ 办公室、办公桌、文件的清扫。
❖ 清除工作场所内的脏污,并防止脏污的发生, 保持工作场所干净亮丽。
❖ 目的: ❖ 保持令人心情舒畅干净亮丽的环境 ❖ 减少脏污对品质的影响 ❖ 减少工业伤害事故
送工务维修或报废
归档存放,整月累积后交资 料室 交还资料室处理
作为垃圾丢弃
2、整顿 实施要领
❖ 2.1落实整理的工作; ❖ 2.2明确“3要素”—场所、方法、标示; ❖ 2.3明确“3定”原则---定点、定容、定量; ❖ 2.4大量使用“目视管理”; ❖ 进行整顿的方法: ❖ 分析情况——规划 ❖ 明确场所——定位 ❖ 明确方法——要求 ❖ 明确标示——识别
❖ 1.2制订“要”和“不要”的判别基准;
❖ 1.3按基准清除不要的物品。
❖ 1.4重要的是物品的“现使用价值”,而不是 “原购买价值”;
❖ 1.5制订废弃物处理方法;
❖ 1.6每日自我检查。
(部门)要与不要的物品判别基准及处置方法
5S现场管理推行实务课件(PPT65页)
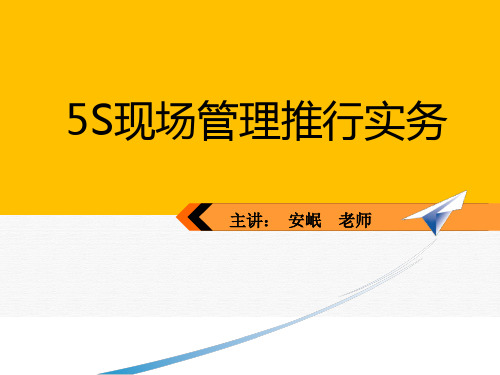
1 5S推进重点
办公桌清扫标准
责任人:
监督人:
清扫部位
清扫要求
清扫周期
台面
桌腿 桌左右侧面 桌子背面
抽屉 抽屉底板
把台上物品移开,用湿抹布将台面擦干 净,再用干抹布擦净,做到用手摸没有 灰尘。 用湿抹布擦净,再用干抹布擦干净,做 到用手摸没有灰尘。 同上,如与其他桌子并联的一面则移开 擦净,
移开墙壁或其他桌子,方法同上。
1 5S推进重点
要与不要物料判定三法则
•产品功能是否丧失
1 5S推进重点
不要什么
A、地板上的:
C、墙壁上的:
1.纸箱、灰尘、杂物、烟蒂
1.蜘蛛网
2.油污
2.过期海报、看板
3.不再使用的设备治、工、模具 3.无用的提案箱、卡片箱、挂架
4.不再使用的办公用品、垃圾筒 5.破垫板、纸箱、抹布、破篮框 6.呆料或过期样品 7.呆人
涂墨
加 工
抛
成品仓库 光
备注:1、虚线表示物流路线 2、原材料至粗加工车间的距离有600米
改进后布局图
粗加工 检验
原材料 仓库
精加工抛光
定
镀
芯
膜
镀膜
涂墨
成品仓库
1 5S推进重点
仓库四号定位实战案例#
A仓库
工厂
C仓库 2号 ABCD 货货货货 架架架架
A仓库
1号 3号 A层 B层 C层 D层 A货架
拉手、抽屉版用湿抹布擦净,再用干抹 布擦净。
把物品拿出来擦净,再把物品放回原处。
一次/天
一次/天 一次/天 一次/三天 一次/天 一次/一星期
1 5S推进重点
清扫作业规范案例
OA机器清扫基准 一、目的
5S推进法 ppt课件
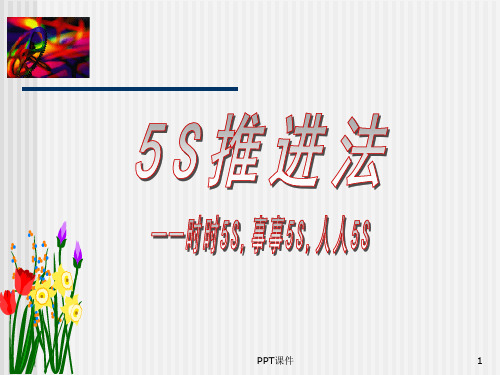
彻底消除。
PPT课件
9
二、为什么清扫是必要的?
1.地板上全是油渍、垃圾、粉尘——人会滑倒而受伤
2.产品或零部件沾满灰尘或垃圾——就这样进入市场销售肯定会 被顾客投诉
3.作业人员吸入灰尘或垃圾——危害健康而导致生病
4.生产设备因进入灰尘或垃圾而产生故障——生产停滞
5.生产工具变脏,变得不易操纵——生产效率降低
3.行动,即动手去做。5S不是“说”的学问,而是“做” 的学问,借活动来改变人的思考方式和行动品质,从而 改变公司的管理水准。5S强调人人动手,全员参与,大 家一起动手提升企业品质。
4.教育,即优质的教育始于5S。通过指导员工重复做这
些简单的小事来达到“习惯成自然”,最终提高素养的
教育目的。
PPT课件
PPT课件
8
第3步 清扫
一、清扫的含义
1.清扫是指将附着在基准面上的污垢进行分离,并将其集中在一 起。
2.清扫的标准是时常保持基准面的清洁,或者保持如新的状态。
3.基准面:桌子、地板、墙壁、设备、置物架、零部件等凡是能 够看得见的地方都可以认为是基准面。
4.污渍:灰尘、垃圾、粉尘、油渍、斑痕、污垢等这些崭新物品 上不会有的一切。
6.给来参观的客户留下不良印象——有可能还会被取消订单
另外,如果不进行清扫,安全就不能得到保障;作业环境恶化, 卫生状况也得不到保障;产品质量下降,投诉也不可避免;设备 故障或作业速度降低,会导致生产效率降低,成本提高;给客户 留下不良印象而导致订单被取消,销售额就会降低。脏乱的餐厅 是不会有客人愿意光顾的。餐桌上满是灰尘、虫子乱爬的饭店是 生存不下去的。
胶带或透明胶带时间久了就不容易撕掉了,这是因为粘合力 变强了。清扫的要点就在于趁着污渍容易剥离的时候将其去除掉。
5S推行实务(1)(精品PPT)
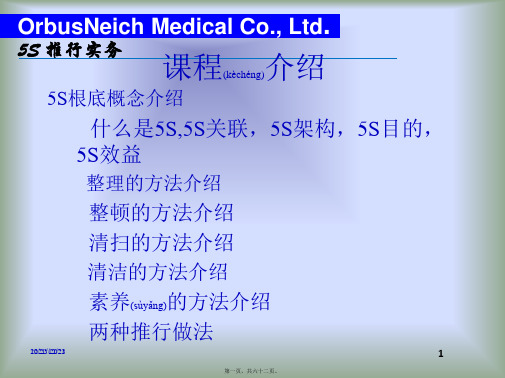
时时保持美观、干净
人
2120/2213//1220/213
第5个S
修身
使员工(yuángōng)养成好习惯遵守规那 么
第三页,共六十二页。
OrbusNeich
5S 推行实务
Medical
C5So的.三, L大t(dsān.dà)架构
三大 创造有规律的工厂 创造干净的工厂
架构
创造目视管理的工厂
目标 (提高管理水准) (提升工厂设备干净度) (提增错误防止力)
OrbusNeich Medical Co., Ltd.
5S 推行实务 〔4〕划线(huáxiàn)定位
色带宽度的参考标准:
主通道:10㎝
次通道或区域线:5-7㎝。
通道宽度的参考标准:
纯粹人行道:约80㎝以上。
单向车通道,约W车+60㎝以上〔W车为车身最大宽度〕 双向车通道:约W车1+W车2+90㎝以上。
)较 走道
亮丽 畅通
设备
提高(tí gāo)
稼动率
地板
干净
减少品质 不良
异常立判
心情较愉快 节省寻找时间
工作气氛好
降低 故障率
5S 的 效 益
减少
公伤、公害
降低报废 料品
降低仓库呆料
感到较有制度 较认同
公司 外宾参观有面子
其他
人员
〔从干部的角度来看5S的效益〕
2120/2213//1220/213
7
划线定位方式: 油漆论 ○定位胶带 ○磁砖 ○栅栏 颜色表示区分: 黄色:一般通道、区域线
白色:工作区域
绿色:料区、成品区 红色:不良(bùliáng)品区警告、平安管制等
具体用何种颜色视原先的底色而定。
5S之整理整顿方法PPT课件
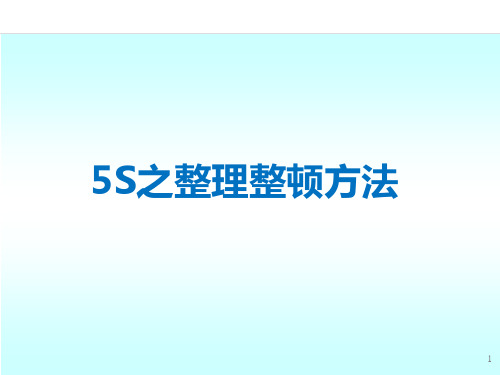
A、地板上
1、杂物、灰尘、纸屑、油污等; 2、不再使用的工装、模 具、夹具等; 3、不再使用的办公用品; 4、破烂的垃圾筒、 纸箱等; 5、呆滞物料等。
不要 B、工作台
1、过时的报表、资料; 2、损坏的工具、样品等; 3、多 余的材料等; 4、私人用品。
C、墙上
1、蜘蛛网; 2、老旧无用的标准书; 3、老旧的海报标语;
B. 明黄色与黑色组成的斜纹斑马线:危险提示、 突起物警示防止碰头、防止跌倒等
C. 红色实线:不良品、危险品摆放区的划分线
D. 绿色实线:独立品检站合格品摆放区的划分 线
65
66
车间内主\辅通道线
主
主通道
通
道
辅通道
说明:主通道(黄色、线宽度10CM) 辅通道(黄色、线宽度5CM)
67
68
69
39
40
41
42
43
44
45
46
柜内物品定位参考
47
柜内物品定位参考
48
安全帽定位方法参考
参考图片
49
不要物—设备上的
• 设备周围的无用工具 • 个人物品 • 设备上的污染物、油迹 • 废弃的管线 • ……
50
51
52
53
54
55
工具定位参考
56
工具定位参考
57
问题:“小”事值得那么重视吗?
好处是,一眼就可以判断物品的数量、 质量、形状、类别或状态。
例:红灯停, 绿灯行等等……
96
技巧三:形迹管理
利用物品形状进行定位的方法
97
除了自己手头的工作, 我们还要些做什么……?
98
参考图片
5S工作推进方案ppt课件
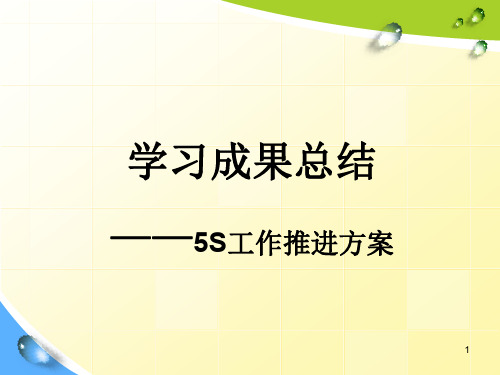
现场5S管理未 与员工、班组 长的绩效挂钩, 单充靠检查考 核不能形成长 效机制。
4
3 5S推进方案目标
认识不足
培训不够
培训不够 未将 5S当 成 一 项 长期工作来做
未能将成果标准化
工作不体系
能力欠缺
培训不到位
5S推进
部门领导未高 度重视
绩效考评 不健全
5
4 5S推进方案目标
5S推进
完善5S推 进组织建 设、培训 体系构建
培训目的
选定样板线 的线长、班 长、部门推
进者
5S管理的重要性及意义
5S管理知识
整理、整顿的着眼点、定 置管理、可视化改善的技
法 5S管理办法、评价基准
让线长、班长从 思想上充分认识 5S知识的进一步 强化
提高班组长的技 能水平
掌握一定标准
培训 组织 时间 者
10月 总经
份
办
10
5 5S推进方案实施—制定部门标准
点检日期
点检项目
是否符合 标准
存在问题
责任者
整改完成时 间
14
5 5S推进方案实施—推广
整理、整顿结束后,现场检查小组按检查基 准对线体进行评价,对发现问题再进一步进 行改进,当评价得分达到90分以上时,在推 广部门其他线体进行推广。
15
16
健全5S管 理标准
制定5S检 查、评价
基准
推进部门5S 平均得分下 半年保持在 90分以上
5S推进
6
5 5S推进方案计划
实施对策
9月份
实施进度 10月份 11月份 12月份 1月份
备注
完善5S管理制度、推进 组织、评价基准
选定样板线对班组长进 行培训。进行整理、整 顿
推行实务整理的推进重点

推行实务整理的推进重点1. 背景介绍推行实务整理是指对某一领域或者某一实践进行综合整理和归纳,以便于在实践中更好地应用和推广。
实务整理可以帮助组织和团队更好地总结经验、提高工作效率、保证质量,并能够为未来的实践工作提供指导和参考。
2. 推行实务整理的意义推行实务整理具有以下重要意义: - 总结经验教训:通过实务整理可以对过去的工作进行回顾和总结,找出成功的经验和失败的教训,从而为未来的实践提供借鉴和启示。
- 提高工作效率:实务整理可以帮助团队对工作进行规范化和流程化,提供标准操作流程和工作文档,从而提高工作效率和质量。
- 保证工作质量:实务整理可以帮助团队发现和解决工作中的问题和风险,提高工作质量和客户满意度。
- 提升专业能力:通过实务整理,团队成员可以不断学习和积累经验,提升专业能力和技术水平。
3. 推进实务整理的关键要点要推进实务整理工作,需要注意以下关键要点:3.1 明确目标和范围在开始实务整理之前,需要明确整理的目标和范围。
目标可以是总结某一项目的实践经验,也可以是整理某一领域的最佳实践。
范围可以包括项目组内部的工作经验,也可以包括行业内其他组织的经验。
3.2 收集和整理资料收集和整理资料是实务整理的重要步骤。
可以通过查阅文献、采访专家、收集团队成员的经验等方式,获取相关资料。
在整理资料时,应该按照一定的分类和顺序进行组织,方便后续的分析和总结。
3.3 分析和总结经验在收集和整理好资料后,需要进行经验的分析和总结。
可以采用SWOT分析、鱼骨图、归因分析等方法,找出工作中的优点、不足和需要改进之处,并从中提炼出通用的经验和规律。
同时,还要注意挖掘出隐含的知识和技巧,方便将来在实践中应用。
3.4 形成标准操作流程和工作文档在经验总结的基础上,要形成标准的操作流程和工作文档。
标准操作流程可以用流程图的方式呈现,包括各个环节的操作步骤、责任人和时间节点。
工作文档可以包括模板、样例、注意事项等内容,方便团队成员在实践中参考和应用。
5S推行实务PPT课件
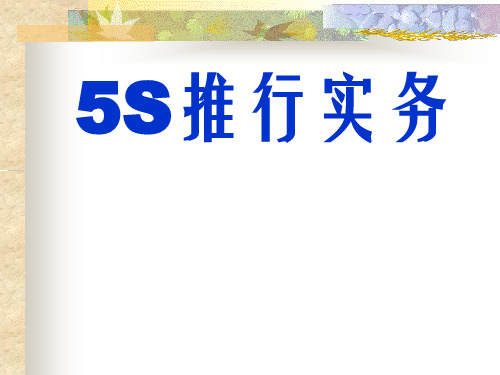
第16页
十二、5S应用之工具
(1)目视管理:感官之效能比率,视觉85% 、听觉11% ,考虑人容易看的位置(眼线触及之处),人容易取 得的位置(腰部以上肩部以下),目视管理应透明化( 检查窗)及状态化(透明水管加上浮标看水流) 。
(2) 目视管理: (a)管理卷标(将物品标示名称、状态、用途、管理界 限) (b)管理界限标志(仪表、对齐、定位、定点相片、 划线定位) 。 (c)人员动态标示。
(4)整顿之目的乃是节省寻找所须之时间,以提升工 作效率。
(5)整顿之最高境界新进人员、作业规范化透过颜色 管理,标示管理,做好目视管理。
第8页
六、清 扫 (Seiso)
(1)清扫:扫除垃圾、扫除污染。 (2)清扫并非单指把工具、机械或厂房清扫擦拭
干净而是应在清扫过程中,去早日发觉问题, 即清扫即点检。
(b)生产线旁也加以编组
(c)序列供应为混流生产的关键点
(d)工具按机械别摆置
(e)工具亦需生产线化摆置
第30页
Step3:使清扫点检成为习惯化[清扫]
(1)清扫时将点检业务纳入 (2)实践清扫点检 (3)决定清扫点检的对象 (4)决定清扫点检担当者 (5)决定清扫点检的方法
(a)现象面的点检点 (b)机构面的点检点 (c)制作清扫点检查检表 (6)实施清扫点检
第31页
Step4:使整洁的职场成为习惯化[清洁]
(1)不要的物品是否有丢弃的基准 (2)物品稍有零乱是否立即加以复原 (3)一有脏乱是否马上将其清理整洁 (4)检讨一3S的程度
性及其效益,并且说明公司之目标及实施办法。 (5)推动:应将计划彻底的实施,否则,无济于事。 (6)诊断与稽核,为使计划落实,必须定期实施稽核
5S推动技巧实务课件

第一章5S绪论一﹑何谓5S﹖整理( Seiri )---区分要与不要的东西﹐把不需要的东西丢弃或整理﹐把需要的东西保管。
整顿(Seiton)---把需要的东西以最简便的方式放好﹐并将之标示﹑定位﹑归位。
清扫(Seiso)---经常打扫﹑保持清洁﹑消除脏乱﹐发现污染源﹑故障源。
清洁(Seiketsu)---维持整理﹑整顿﹑清扫的成果﹐根绝污染源﹑故障源。
修养(Shitsuke)---养成遵守既定事项的规定与标准的习惯﹐进而发挥自动自发的精神。
◎取日文发音的第一个S﹐故谓5S。
5 S之定义二﹑5S的基本概念1.要使效率提高﹐先从整理开始。
◎整理并不是把物品排好或堆好﹐那叫做整列。
◎整理的应用例子如「人员整理」﹑「委外整理」等。
虽然觉得可异﹐该丢的还是要丢2.免除「寻找」的浪费﹐由整顿开始。
◎整顿不是把眼所能见的东西整齐的排好﹐那叫列。
◎整顿是把需要的东西放在自己周围﹐其次使大家对这些需要的东西能一目了然也是很重要。
把不明白的东西贴条子3.清扫是提高品质的基础。
◎先用扫把扫一遍﹐然后再用抹布擦一次是最基本的﹐当然﹐窗缝与墙角也不可疏忽。
4.安全的第一步﹐就是清洁。
◎常保无垃圾﹑无污秽的现场是安全的第一步。
5.5S是以教养为始终。
◎保持自身之美﹐就是教养。
这是十分重要的。
「道早安」是教养的第一步三﹑实施5S的目的1.从原点再出发﹐养成良好的习惯﹐变成一个有教养的工厂与作业人员。
2.自主管理﹐对自己工作场所和工厂﹐付出爱心。
3.保持清洁干净的愉快的现场﹐提高品质﹑效率和员工向心力。
4.从5S展开现场改善﹐达到经营革新的目标。
5.造成一流的工作环境﹐彻底消除死角﹐提高经营绩效。
四﹑5S的目标目标 1. 多品种生产时要做到换线时间为“0”(Products)◎你可以立刻取出模具吗﹖◎有没有遇到过到处寻找治具﹑工具或刀具的情形﹖目标 2. 为了提高品质要达无不良品(Quality)闪闪发亮。
在清洁美观的工厂中﹐不良品是十分碍眼的﹐因此﹐在清洁美观的工厂里有不良品的话﹐大家都会觉得不好意思。
- 1、下载文档前请自行甄别文档内容的完整性,平台不提供额外的编辑、内容补充、找答案等附加服务。
- 2、"仅部分预览"的文档,不可在线预览部分如存在完整性等问题,可反馈申请退款(可完整预览的文档不适用该条件!)。
- 3、如文档侵犯您的权益,请联系客服反馈,我们会尽快为您处理(人工客服工作时间:9:00-18:30)。
23
(5)不能使用的工装夹具; (6)破烂的垃圾桶、包装箱; (7)过时的报表、资料; (8)枯死的花卉; (9)停止使用的标准书; (10)无法修理好的器具设备等; (11)过期、变质的物品
24
不使用的物品
(1)目前已不生产的产品的零件或半成品; (2)已无保留价值的试验品或样品; (3)多余的办公桌椅; (4)已切换机种的生产设备; (5)已停产产品的原材料; (6)安装中央空调后的落地扇、吊扇;
9
如图示:
那么,必需物品的使用频率可能是每小时或每天都要用,也 可能每一周都要用,凡是它的使用频率为每小时或每天及每 周都要用到的,就称为必需用品
10
它的处理方法就是放在工作台上,或是随 身携带。如笔就是我们经常要用的必需用品。 如图示:
11
【自检】
请检查一下你的办公室或者家里, 哪些是必需物品,哪些是非必需 品?对非必需品,你是如何进行 妥善处理?你又如何摆放它的顺 序?
第4讲 整理的推进重点
【本讲重点】
整理的含义 整理的作用 整理的推行要领 推行整理的步骤 具体实例
1
整理的含义
将必需与非必需品区分开,在岗位上只放必需物。
图4-1 整理含义图
2
特别说明
如果您的工作岗位堆满了非必需物品 ,就会导致您的必需物品反而无处 摆放;您可能希望增加一张工作台 来堆放必需品,这样一来必然造成 不必要的浪费,二来更形成了后果 严重的恶性循环。
7
(2)对目前的生产或工作无任何作用的, 需要报废的物品。它又包括以下两 种:
①非必需用品:如钉钉子的铁锤,可能不是每天要用, 也不可能是每周都要用,但它可能每隔一段时间 或每个月会用到一两次,也许半年或一年才会用 到几次,就叫做非必需用品;
8
②不能用的物品:如过期的图纸、样品,处 理方法只有一种,就是放在仓库。有一 种东西,是必须要封存的,一年或两年 才会用到的,像这一类的东西应放在仓 库里封存。同时把非必需用品摆在库里 后,要建立一个档案,并定期地检查。
12
推行整理的步骤
在推行整理的过程中,要增加场地的空间, 把东西整理好,把必需品和非必需品区分开, 将工作的场所整理干净了。如果还把不必要 的物品也整齐地与必需品摆在一起,那就会 很容易弄不清所需要的物品应是哪一个,而 且还会因放置了不必要的物品而放不下必需 的物品。
13
推行整理的步骤
第一步:现场检查 第二步:区分必需和非必需品 第三步:清理非必需品 第四步:非必需品的处理 第五步:每天循环整理
25
销售不出去的产品
(1)目前没登记在产品目录上的产品; (2)已经过时、不合潮流的产品; (3)预测失误而造成生产过剩的产品; (4)因生锈等原因不能销售的产品; (5)有使用缺陷的产品; (6)积压的不能流通的特制产品。
26
多余的装配零件
19
非必需品的处理
图4-2 非必需品的处理方法
20
养成每天循环整理的习惯
21
整理贵在日日做,时时做,如果仅 是偶尔突击一下,做做样子,就完 全失去了整理的意义。
整理,是一个循环的工作,根据需 要而随时进行,需要的留下,不需 要的马上放在另外一边。
22
具体实例
无使用价值的物品
(1)不能使用的旧手套、破布、砂纸; (2)损坏了的钻头、丝锥、磨石; (3)已损坏而无法使用了的锤、套筒、刃具等
15
区分必需品与非必需品
管理必需品和清除非必需品同样重要。 首先要判断这个东西的重要性是什么? 然后根据此物的使用频率来决定它的管 理方法。如果是一支笔,它的使用频率 是每天、每周或者每个小时都在用,它 就是必需品,要用恰当的方法来保管必 需品,以便于寻找和使用。
16
对于必需品,许多人往往混淆了客观上的需 要与主观想要的概念,他们在保存物品方面 总是采取一种保守的态度,也就是那种以防 万一的心态,最后把工作场所几乎变成了杂
将必需品的适量降到最低的程度; 对可有可无的物品,不管是谁买的,无论
有多昂贵,都呢?
所谓必需物品,是指经常必须使用的物品, 如果没有它,就必须购入替代品,否则就 会影响工作。非必需品则可分为两种:
(1)使用周期较长的物品,即一个月,三个月, 甚至半年才使用一次的物品;如样品、图 纸、零配件等;
资金浪费; ●因场所狭窄,物品时常不断地移动,造成
了工时浪费; ●管理非必需品的场地和人力浪费,花时间
去管那些没有必要的东西,就会造成场地 和人力资源的浪费; ●库存管理以及盘点,造成时间浪费。
5
整理的推行要领
马上要用的,暂时不用的,先把它区别开。 一时用不着的,甚至长期不用的要区分对 待。即便是必需品也要适量;
3
整理的作用
1.整理的作用
●能使现场无杂物,过道通畅,增大作 业空间,提高工作效率;
●减少碰撞,保障生产安全,提高产品 质量;
●消除混杂材料的差错; ●有利于减少库存,节约资金; ●使员工心情舒畅,工作热情高涨。
4
2.因缺乏整理会造成的各种浪费
●空间造成浪费; ●零件或产品因为过期而不能使用,造成了
物馆,所以对管理者能而言,准确地区 分需要还是想要,是非常关键的问题。
17
清理非必需品
清理非必需品时必须把握好的是 看物品现在有没有使用价值,很 重要的一句话是,应注意使用价 值,而不是原来的购买价值,也 就是使用价值大于购买价值。
18
要重点清理以下物品:货架、工具箱、抽屉、 橱柜中的杂物,过期的报刊、杂志,空的罐 子,已损坏的工具或器皿,仓库墙角、窗台、 货架上,甚至货柜顶上摆放的样品,长时间 不用或已不能使用的设备、工具、原材料、 半成品、成品,在你的办公场所、桌椅下面、 还有显示写字板上报废的文具、过期的文件、 表格、速记记录等。
14
现场检查
对工作场所要进行全面性的检查,包括眼睛看到的 和看不到的地方。例如,设备的内部,文件柜的顶 部,桌子的底部位置。特别是设备,一个大机械设 备,它的内部是看不见的,文件柜的底部,桌子的 底部,这些都是现场检查时应特别需要注意的地方。 归纳起来就是两点:看得见的要整理,看不到的更 要进行整理。