热成型简介
热成型的温度

热成型的温度热成型是一种常用的加工方式,在制造过程中可对材料进行加热,使材料获得适应性的形状。
不同材料在进行热成型时,需要应用不同的温度和加工压力。
因此,了解每种材料的热成型温度是非常重要的。
一般情况下,热成型的温度取决于材料的种类和塑性,以及所需的成型形状。
根据材料的特性,通常热成型的温度范围在200度到700度之间,高温材料甚至可以达到1000度以上。
以下是常见材料的热成型温度:1.聚乙烯:聚乙烯是一种常见的热成型材料,其热成型温度在120度到220度之间。
聚乙烯的熔点是130度,因此加热时不能超过这个温度。
2.聚丙烯:聚丙烯也是一种常见的热成型材料,其热成型温度在160度到220度之间。
和聚乙烯类似,加热温度不能超过它的熔点148度。
3.聚苯乙烯:聚苯乙烯是一种常见的可加工塑料,其热成型温度在180度到240度之间。
由于聚苯乙烯易于膨胀,很容易地形成空气泡,所以在成型过程中需要加压。
4.PVC:PVC是一种常见的塑料材料,其热成型温度在140度到200度之间。
在成型时需要进行加压,使其保持形状。
5.尼龙:尼龙是一种高强度、高耐磨损的材料,其热成型温度在200度到250度之间。
这种材料的成型速度比较快,所以需要掌握好加工温度和压力。
6.聚酰亚胺:聚酰亚胺是一种耐高温、高强度的材料,其热成型温度在350度到400度之间。
这种材料的熔点很高,所以需要设定适当的热成型温度,然后进行高压成型。
总体来说,热成型的温度并不是固定的,需要根据各种因素去具体的调整。
这些因素包括所用材料的种类、形状和大小、生产流程、生产环境等等。
必须要掌握好热成型温度的范围,并且严格按照要求进行操作,才能顺利的进行成型生产,制作出符合要求的合格产品。
汽车热成型

汽车热成型1. 简介汽车热成型是一种用于制造汽车零部件的加工方法,通过加热和塑性变形来获得所需的形状和结构。
它广泛应用于汽车制造业,可以生产出高强度、轻量化和复杂形状的零部件,提高汽车的性能和安全性。
2. 热成型工艺2.1 热成型材料在汽车热成型过程中,常用的材料包括钢铁、铝合金和镁合金。
这些材料具有良好的塑性和强度,适合进行热成型加工。
2.2 热成型设备热成型设备包括热压机、模具和加热系统。
热压机用于施加压力,模具用于定型,加热系统用于提供所需的温度。
2.3 热成型过程(1)预处理:将原材料进行切割和清洗处理,确保表面干净,并去除可能存在的氧化层。
(2)加热:将原材料放入预热室中进行加热,使其达到适当的温度。
加热温度根据材料的特性和所需的成型形状而定。
(3)成型:将加热后的材料放入模具中,通过热压机施加压力,使其塑性变形,获得所需的形状和结构。
(4)冷却:将成型后的零部件进行冷却处理,使其固化并保持所需的形状。
(5)后处理:对成型后的零部件进行去毛刺、清洗和表面处理等工艺,以提高其表面质量和耐腐蚀性。
3. 汽车热成型应用3.1 车身结构件汽车热成型广泛应用于制造车身结构件,如车门内板、侧围、屋顶梁等。
这些零部件需要具备高强度、轻量化和优秀的抗冲击性能,以保障汽车乘员的安全。
3.2 发动机零部件汽车发动机零部件,如缸盖、曲轴箱等也常采用热成型工艺制造。
这些零部件需要具备高温下的耐久性和优秀的密封性能,以确保发动机正常运行。
3.3 悬挂系统零部件汽车悬挂系统零部件,如悬挂臂、悬挂支架等,也可以通过热成型制造。
这些零部件需要具备高强度和优秀的耐久性,以提高汽车的操控性和稳定性。
4. 汽车热成型的优势4.1 轻量化热成型可以制造出高强度的零部件,使汽车整体重量减轻。
这有助于提高燃油效率和减少尾气排放,符合现代汽车工业追求的环保和节能要求。
4.2 复杂形状热成型可以实现复杂形状的制造,满足汽车设计师对外观和空气动力学性能的要求。
热成型原理

热成型原理
热成型是一种常见的制造工艺,它利用热能将原料加热至一定温度,然后在模
具中进行成型,最终得到所需的产品。
热成型原理是基于热塑性材料在一定温度下具有可塑性和流动性的特性,通过加热和压力使其形成所需形状的工艺。
热成型原理的关键在于控制温度和压力。
首先,原料需要被加热至其玻璃转化
温度以上,这样才能使其变得柔软并具有可塑性。
然后,通过模具施加压力,使得原料在模具中流动并形成所需的形状。
最后,冷却后,产品就可以从模具中取出。
热成型原理广泛应用于塑料加工、玻璃制品、金属加工等领域。
例如,塑料瓶、塑料包装、塑料零件等都是通过热成型原理制成的。
在玻璃制品方面,热成型原理可以制造玻璃瓶、玻璃杯等产品。
而在金属加工领域,热成型原理也被用于制造各种金属零件和工件。
热成型原理的优点在于可以制造复杂形状的产品,并且生产效率高。
此外,由
于原料在加热过程中变得柔软,因此可以减少对原料的加工压力和能耗。
然而,热成型也存在一些缺点,比如对原料的要求较高,需要严格控制温度和压力,以及成本较高。
总的来说,热成型原理是一种重要的制造工艺,它在各个领域都有着广泛的应用。
随着科技的不断进步,热成型原理也在不断改进和完善,为生产提供了更多的可能性和选择。
热成型原理
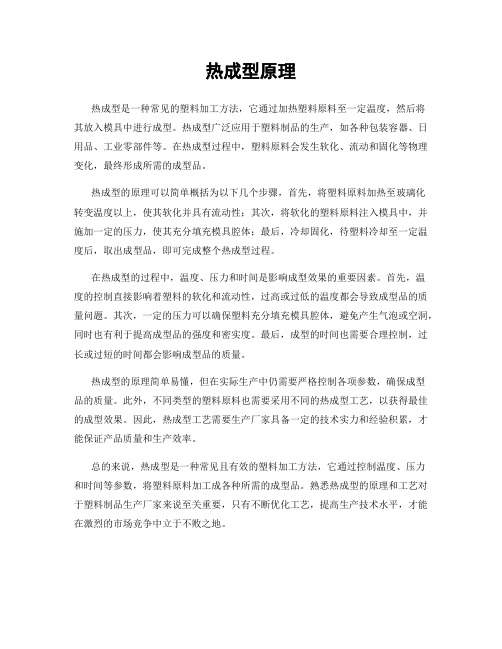
热成型原理
热成型是一种常见的塑料加工方法,它通过加热塑料原料至一定温度,然后将
其放入模具中进行成型。
热成型广泛应用于塑料制品的生产,如各种包装容器、日用品、工业零部件等。
在热成型过程中,塑料原料会发生软化、流动和固化等物理变化,最终形成所需的成型品。
热成型的原理可以简单概括为以下几个步骤,首先,将塑料原料加热至玻璃化
转变温度以上,使其软化并具有流动性;其次,将软化的塑料原料注入模具中,并施加一定的压力,使其充分填充模具腔体;最后,冷却固化,待塑料冷却至一定温度后,取出成型品,即可完成整个热成型过程。
在热成型的过程中,温度、压力和时间是影响成型效果的重要因素。
首先,温
度的控制直接影响着塑料的软化和流动性,过高或过低的温度都会导致成型品的质量问题。
其次,一定的压力可以确保塑料充分填充模具腔体,避免产生气泡或空洞,同时也有利于提高成型品的强度和密实度。
最后,成型的时间也需要合理控制,过长或过短的时间都会影响成型品的质量。
热成型的原理简单易懂,但在实际生产中仍需要严格控制各项参数,确保成型
品的质量。
此外,不同类型的塑料原料也需要采用不同的热成型工艺,以获得最佳的成型效果。
因此,热成型工艺需要生产厂家具备一定的技术实力和经验积累,才能保证产品质量和生产效率。
总的来说,热成型是一种常见且有效的塑料加工方法,它通过控制温度、压力
和时间等参数,将塑料原料加工成各种所需的成型品。
熟悉热成型的原理和工艺对于塑料制品生产厂家来说至关重要,只有不断优化工艺,提高生产技术水平,才能在激烈的市场竞争中立于不败之地。
热成型
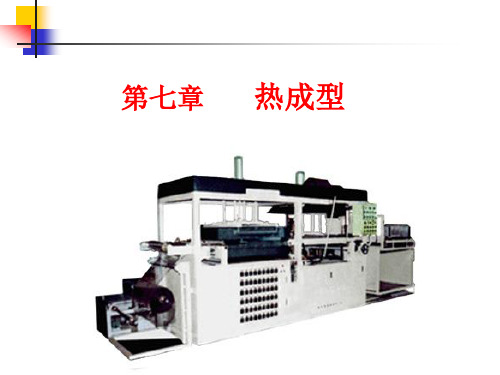
2、成型 、 厚薄不均的原因: 厚薄不均的原因: 片材各部分所受的拉伸程度不同; 片材拉伸速度的影响。 成型速度对热成型制品性能有何影响? 成型速度对热成型制品性能有何影响? 厚片材和薄片材的成型速度有何区别? 厚片材和薄片材的成型速度有何区别?
热成型的成型速度一般指最终成型时片材所受 到的拉伸速度,过大的成型速度会导致因材料流 动不足而使产品在偏凹(或凸)的位置出现厚度过 薄的现象,甚至被拉穿而成为废品。但过小的速 率又会因片材的先行冷却而出现裂纹。 薄型片材的拉伸一般都应快于厚型的,因为前 者的温度在成型时下降较快,故应适当提高成型 速度。
3、冷却脱模 、
冷却至变形温度以下P359
模具温度影响热成型制品质量 和生产效率。 和生产效率。 模温高时,制品表面光泽度 高,轮廓清晰,但成型周期延长。 适当的降温速率可减小制品的内 应力,减少制品拉伸皱痕。
注塑成型与热成型比较: 注塑成型与热成型比较: 与注塑成型相比,热成型设备投资低;由 于成型温度、压力低,对模具耐热压要求 低,所以模具费用低;易成型大制件;易 于产品更新。 但热成型只能生产结构简单的半壳型制品, 而且制品壁厚应比较均匀,不能制得壁厚 相差悬殊的塑料制品;制品后加工多,原 材料损耗大;成型温度低导致制品残余应 力大;成型形状受限,通常只有一面被模 具定型;制品精度较低。
1、加热 加热时间≈50%-80%成型工作周期 如何缩短? 双面加热
热成型的成型温度范围如何确定? 热成型的成型温度范围如何确定?
一般用直接观察的办法大致确定成型温度范围,最 低成型温度以保证在最大拉伸区域内不发白或不出现 明显缺陷为准,而最高成型温度则以片材不发生降解 和不会在夹持架上出现过分下垂为宜。调节成型温度 可通过改变加热距离和时间。为了获得最短的成型周 期,通常成型温度都偏于下限值。 P358
塑料成型模具设计热成型
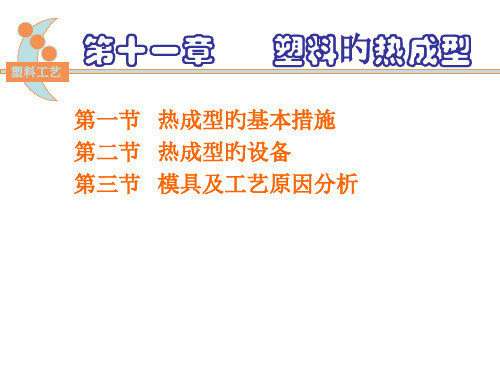
7.其他成型 板材旳弯曲,法兰旳弯制,管材旳弯制等,另外,有板材
卷成筒,容器旳口部或底部旳卷边和管材旳扩口等,都属于热 成型旳范围。
第二节 热成型旳设备
塑料工艺
热成型旳基本工序: 片材夹持、加热、成型、冷却、脱模
一.模具
1.工作压力不高时,可采用强度底旳材料制造模具。材料旳选择 要根据成型旳数量和质量要求而定,如木制模具合承受500次成型, 石膏模具可承受50次,型砂模具和树脂砂模可承受500次以上。 2.模具上旳通风孔制作也是在浇注型砂前插上表面涂有隔离剂旳 钢丝,浇注14小时后抽出钢丝。 3.外形简朴旳制品用阴模成型。因制品收缩,易取出,若构造复 杂,要施加顶出力;对用阳模成型小型拉伸制品时,阳模旳高度尤 为主要。阳模侧圆半径不应不大于板厚旳3-5倍。
品。
2) 应用范围广;日常生活中器皿,食品和药物包装, 汽车部件等。
3) 设备投资少;热成型压力不高,对设备要求不高。 4) 模具制造以便;∵压力低,除金属外,木材,塑料, 石膏等∴热成型在近十年才有较大旳发展。
塑料工艺
3.成型基本过程 1) 先将裁诚一定尺寸和固定形样旳片材夹在框架上; 2) 加热到热高弹态; 3) 成型 凭借施加压力使其贴近模具旳形面,从而得
定压强)→片材包住(模具反压力)封死→打开底模具部抽气孔抽 气→回吸而贴合→成型→冷却脱模→修整→制品 3)推气真空成型 如图 13-11
塑料工艺
塑料工艺
5.模压成型 单阳模法、 单阴模法、 对模成型
多和模压成型 使用也全部热塑性塑料
6.双片成型 这是成型中空制品旳一种措施 如图13-13 两块已加热到足够温度塑料片材,放在半合模具模框上夹
热成型方法
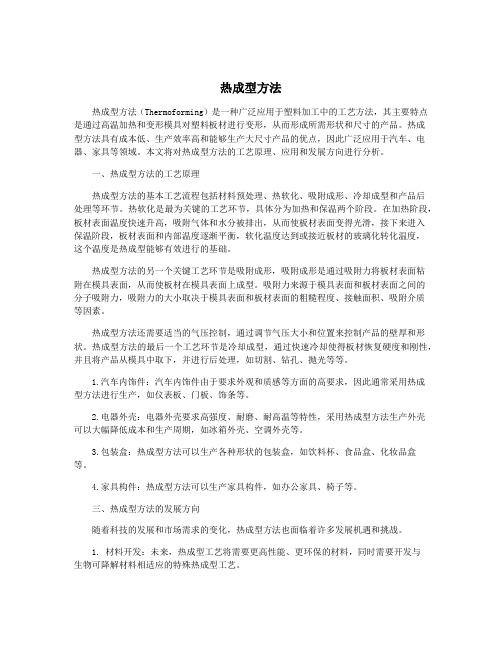
热成型方法热成型方法(Thermoforming)是一种广泛应用于塑料加工中的工艺方法,其主要特点是通过高温加热和变形模具对塑料板材进行变形,从而形成所需形状和尺寸的产品。
热成型方法具有成本低、生产效率高和能够生产大尺寸产品的优点,因此广泛应用于汽车、电器、家具等领域。
本文将对热成型方法的工艺原理、应用和发展方向进行分析。
一、热成型方法的工艺原理热成型方法的基本工艺流程包括材料预处理、热软化、吸附成形、冷却成型和产品后处理等环节。
热软化是最为关键的工艺环节,具体分为加热和保温两个阶段。
在加热阶段,板材表面温度快速升高,吸附气体和水分被排出,从而使板材表面变得光滑,接下来进入保温阶段,板材表面和内部温度逐渐平衡,软化温度达到或接近板材的玻璃化转化温度,这个温度是热成型能够有效进行的基础。
热成型方法的另一个关键工艺环节是吸附成形,吸附成形是通过吸附力将板材表面粘附在模具表面,从而使板材在模具表面上成型。
吸附力来源于模具表面和板材表面之间的分子吸附力,吸附力的大小取决于模具表面和板材表面的粗糙程度、接触面积、吸附介质等因素。
热成型方法还需要适当的气压控制,通过调节气压大小和位置来控制产品的壁厚和形状。
热成型方法的最后一个工艺环节是冷却成型,通过快速冷却使得板材恢复硬度和刚性,并且将产品从模具中取下,并进行后处理,如切割、钻孔、抛光等等。
1.汽车内饰件:汽车内饰件由于要求外观和质感等方面的高要求,因此通常采用热成型方法进行生产,如仪表板、门板、饰条等。
2.电器外壳:电器外壳要求高强度、耐磨、耐高温等特性,采用热成型方法生产外壳可以大幅降低成本和生产周期,如冰箱外壳、空调外壳等。
3.包装盒:热成型方法可以生产各种形状的包装盒,如饮料杯、食品盒、化妆品盒等。
4.家具构件:热成型方法可以生产家具构件,如办公家具、椅子等。
三、热成型方法的发展方向随着科技的发展和市场需求的变化,热成型方法也面临着许多发展机遇和挑战。
热成型
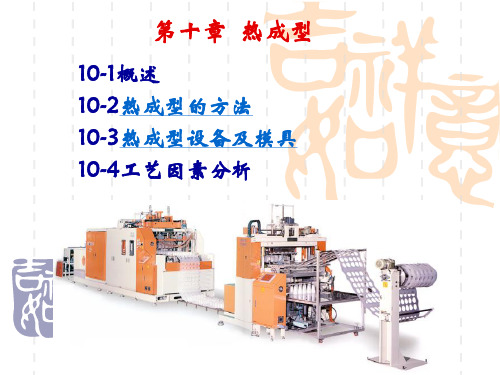
热成型汽车部件
三、热成型原料
目前用于热成型的塑料有聚苯乙烯及其改性品种、 PMMA、PVC、ABS、PE、PP、PA、PC、PET等。
热成型始终以高效、经济等优势在塑料成型方法中占有 一席之地 。
10-2热成型的方法
目前生产中采用的热成型方法有数十种,最基本 的方法有6种。 一、差压成型 1、2、3 、4 二、覆盖成型 三、柱塞助压成型 四、回吸成型1、2、 五、对模成型1、2 六、双片热成型
降低温度虽然能缩短成型时间和节省能源,但是温度过低 时所得制品轮廓不清晰、尺寸稳定性差;
加热温度过高,会造成聚合物的降解,从而导致制品变色
和失去光泽。
加热坯件的原则 加热的温度下限应以片材在牵伸最大区域不发 白或不出现明显的缺陷为度; 上限温度则是片材不发生降解和不会在夹持 架上出现过分下垂的最高温度。 一般热成型过程中,加热的坯件要经过转换 工位,要有一些降温,尤其是壁薄的坯件和传热 系数比较大的坯件,散热现象比较严重,所以坯 件的加热温度要稍高于成型温度。
压缩空气系统由空气压缩机、储压罐、管路、阀门
组成。压缩空气机的额定排气量通常为0.05~0.3m3/min, 压力范围为0.6~0.7MPa,实际使用时一般不超过0.35MPa。
四、冷却系统
冷却系统有内冷和外冷, 内冷是依靠模具内设冷却盘管,通冷却水,进行冷却; 外冷则是用风冷和水雾等冷却。
通常金属模具用内冷,非金属模具用外冷。有时也采用内冷 和外冷相结合的方式,快速冷却。
方法与注塑制品的热处理方法相同。为了使热处理充分 发挥消除制品内应力和应变的作用,应在制品的修整和机械 加工后进行。
热成型思考题
1. 了解热成型的基本方法及其特点。 2. 热成型制品都有什么特点? 3. 确定热成型坯件加热温度的基本原则是什么? 4. 提高热成型制品壁厚均匀性的工艺措施都有哪些?
热成型工艺pptx
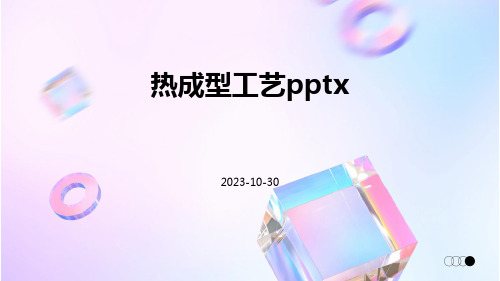
近年来,随着环保意识的不断提高,热成型工艺逐渐向绿色制造方向发展,例如采用回收塑料材料作为原料, 以及开发新的加工技术以提高生产效率和降低成本。
热成型工艺的应用范围
汽车行业
热成型工艺被广泛应用于制造汽车车身覆 盖件、仪表板、保险杠等大型塑料制品。
建筑行业
热成型工艺可制造各种类型的塑料门窗、 幕墙、扣板等建筑装饰材料。
冷却温度
冷却温度也是热成型工艺中需要严格控制的参数,冷却不当可能导致材料变形、内应力增大或者出现 气泡等缺陷。
时间控制
成型时间
成型时间太长可能导致材料变形或产生内应力,而时间太短则可能导致成型不充分或者出现缺陷。
冷却时间
冷却时间太长可能导致材料变脆或者产生内应力,而时间太短则可能导致材料未充分冷却而影响性能 。
特点
热成型工艺具有生产效率高、制造成本低、材料利用率高、 可制造大型制品等优点,但同时也存在制品精度不高、材料 性能有所损失等缺点。
热成型工艺的历史与发展
历史
热成型工艺最初起源于20世纪40年代,当时主要用于制造玻璃纤维增强塑料制品。随着材料和技术的不断发 展,热成型工艺逐渐应用于制造各种类型的塑料制品。
热成型弯曲变形
• 弯曲变形:热成型制品形状与设计不符,原因可能是材料流 动性差、模具设计不合理、冷却不均匀等。防止方法包括改 善材料流动性、优化模具设计、控制冷却速度等。
表面粗糙与橘皮状
表面粗糙
热成型制品表面不平整,原因可能是材料流 动性差、模具表面质量差等。防止方法包括 改善材料流动性、提高模具表面质量等。
热成型工艺pptx
2023-10-30
目录
• 热成型工艺简介 • 热成型工艺流程 • 热成型工艺参数控制 • 热成型工艺缺陷及防止方法 • 热成型工艺优化与发展趋势 • 热成型工艺案例展示
热成型的原理和方法

热成型的原理和方法热成型是一种超级有趣的制造工艺呢!一、热成型的原理。
热成型的原理其实就像是给材料做一个热“SPA”。
咱们先来说说材料,通常是塑料片材或者板材。
这些材料在常温的时候啊,是硬邦邦的,不太好改变形状。
但是呢,当我们给它加热的时候,情况就大不一样啦!就像冰受热会化成水一样,塑料受热后就会变得软软的,像橡皮泥一样听话。
这是因为热量让塑料分子活跃起来,它们之间的连接不再那么紧密,分子可以相对自由地移动啦。
这时候呢,我们就可以利用这个柔软的状态,通过一些模具或者外力,把它塑造成我们想要的形状。
等它冷却下来,就会保持住这个新的形状,就像记忆一样,很神奇吧?二、热成型的方法。
1. 真空成型法。
这是一种比较常见的热成型方法哦。
想象一下,我们把加热变软的塑料片材放在一个模具上面,这个模具就像是一个大模型,有我们想要的形状。
然后呢,我们在模具下面抽真空,就像用吸管把杯子里的空气吸走一样。
这时候,外界的大气压就会把软软的塑料片材紧紧地压在模具上,让它贴合模具的形状。
就好像大气在说:“小塑料片,你就按照这个模具的样子变吧!”这样就完成了一次简单的真空热成型啦。
2. 压力成型法。
这个方法和真空成型有点像,但不是抽真空,而是施加压力。
我们把加热好的塑料放在模具之间,然后通过机械装置给它施加压力,就像用力把两块东西压在一起一样。
这个压力会让塑料乖乖地填充到模具的每一个角落,形成我们想要的形状。
这就好比是强迫小塑料按照我们的想法变形,不过效果可是很棒的呢!3. 吹塑成型法。
吹塑就更有趣啦。
我们先把塑料加热变软,然后把空气吹进这个软软的塑料里面,就像吹气球一样。
不过这个“气球”是按照我们预先设计好的模具形状来膨胀的。
空气的力量会让塑料不断地扩张,直到它贴紧模具的内壁,这样就得到了我们想要的形状。
是不是感觉像在玩魔法一样呢?热成型在我们的生活中可是无处不在的哦。
像我们用的一些塑料包装盒、汽车内饰的一些塑料部件,很多都是通过热成型制作出来的。
汽车热成型技术

汽车热成型技术
汽车热成型技术是一种重要的汽车零部件加工技术。
其基本原理是将金属材料在一定温度下进行加热,然后施加外力使其变形,最终使其成为所需的形状。
热成型技术具有成形精度高、生产效率高、加工成本低等优点,被广泛应用于汽车制造中。
目前,汽车热成型技术主要包括热挤压成型、热冲压成型、热锻造成型等。
其中,热挤压成型适用于生产大量的汽车零部件,如车身结构件、发动机罩等;热冲压成型则适用于生产中小型汽车零部件,如车门、车窗等;热锻造成型适用于生产高强度、高硬度的汽车零部件,如汽车曲轴、销轴等。
在汽车热成型技术中,温度和压力是两个关键因素。
合理的温度和压力控制可以使得汽车零部件的形状和性能达到最佳状态。
此外,材料的选择也是影响成型效果的重要因素。
一般来说,汽车热成型技术采用的材料主要有铝合金、钢、钛合金等。
总之,汽车热成型技术是一种非常重要的汽车零部件加工技术。
随着汽车工业的不断发展,热成型技术也在不断创新和改进,为汽车制造业带来了更高效、更优质的零部件加工解决方案。
- 1 -。
工程材料及热成型工艺

工程材料及热成型工艺
工程材料是指在工程领域中用于制造构件或构造物的材料,包括金属、非金属、合金和复合材料等。
这些材料必须具有足够的强度、硬度和耐磨性等特性,以满足工程制造的要求。
热成型工艺是指通过加热材料到一定温度,利用材料的可塑性使其变形成所需形状的工艺。
主要有以下几种热成型工艺:
1. 热轧成型:将金属坯料加热到高温后,通过辊轧使其变形成薄板、薄壁管等形状。
2. 热挤压:将金属坯料加热到高温后,通过挤压机将其挤压成所需形状的材料。
3. 热冲压:将金属板材加热到一定温度后,利用模具进行冲压,使其承受大变形,形成复杂的形状。
4. 热拉伸:将金属坯料加热到高温后,通过拉伸使其变形成细丝或丝状材料。
5. 热淬火:将金属件加热到高温后迅速冷却,使其获得高硬度和高强度。
这些热成型工艺在工程制造中广泛应用,能够使材料获得良好的力学性能和形状。
同时,不同的工程材料和工艺可以相互配合,以满足不同工程的要求。
第十一章 热成型
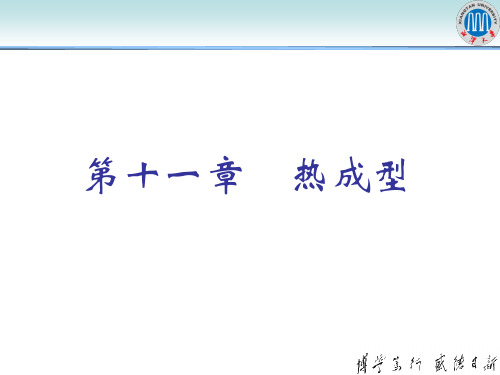
图11-8 挤出-真空成型
6、其它热成型
弯曲
卷筒 卷边和翻边 扩口 成波
热收缩管
异型管件的成型
(1)板材的弯曲 大 批 量 生 产 几 何 尺 寸 严格的制品常采用阴模 阳模弯曲成型方法。 阳 模 预 热 后 加 热 型 坯 , 逐渐下压弯曲型坯。 类似于模压成型
1-型坯 2-阳模 3-模板
2、成型机种类及结构 (1)单片供料热成型机
(2)片卷供料热成型机
(3)连接在生产线中的专用热成型机
(1)单片供料热成型机
适于不易成卷的厚片及板材的热成型,特别是大 型制件的生产。
1)单工位热成型机
片材进入成型机之后,在同一位置先后进行加热、 成型、冷却,取件等操作,所以,所设置的加热装置、 模具台、柱塞、冷却装置等,均以片材夹持框为中心。 2) 多工位热成型机
1、滑动成型(slip-forming)
型坯可在成型过程中滑动
适合于厚壁,大深度制品
2、弹性隔膜成型(a)
隔膜成型是一种复合材料成型方法,即将预浸的 复合材料层压后放置于模具上,通过一种特制隔膜的 辅助作用经过抽真空和加热等方法,将层压件压向模 具,形成所需形状。
弹性隔膜成型(b)弹性隔膜液压成型
工位热成型机,主要是双工位和三工位,以三工 位热成型机为例:第一工位是取件和片材夹持,第二 工位加热,第三工位成型,周而复始
单工位热成型机
双工位热成型机
旋转式三工位热成型机
旋转式四工位热成型机
(2)片卷供料热成型机
(9)冷成型
用热塑性塑料板材在玻璃态和结晶状态拉伸成型容 器类制品,在工业上称冷成型。该办法是借助于金属加 工中板材冷冲压法发展起来的新方法,其主要特点是型 坯在低于玻璃化温度(非结晶型塑料)或低于熔融温度 (结晶型塑料)下成型。型坯在室温下或加热到 20~40℃,低于玻璃化温度或熔融温度,将其周边固定 在夹紧装置上,用阳模施以成型压力,进行成型。减少 或完全取消了型坯的加热工序,也没有冷却阶段。用冷 成型法制得的产品厚度精度和壁厚均匀性都优于热成型 法。
塑料成型工艺学热成型
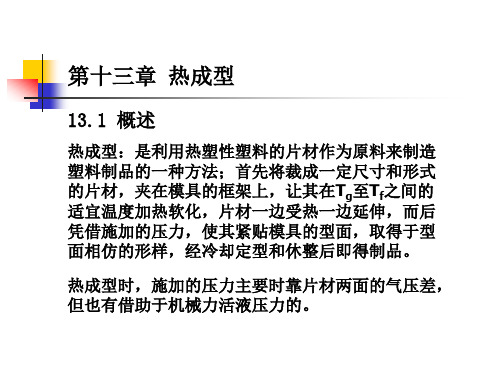
13.2.2 覆盖成型
与真空成型基本相同,不同者只是所用模具只有阳模; 成型时系借助于液压系统的推力,将阳模顶入由框架 夹持且已加热的片材中,也可用机械力移动框架将片 材合扣复在模具上,然后在抽真空使片材包复于模具 上而成型。
覆盖成型特点:
1.与模面贴合的一面质量较高,结构上也较鲜明、细致;
2.壁厚的最大部位在模具的顶部,而最薄的部位则在模具侧面与 底面的交界处;
根据片材两面产生压差的方法,可分为真空成型和 加压成型两种。
13.2.1 差压成型
差压成型特点:
1.制品结构上比较鲜明和精细部位是与模面贴合的一 面,而且光洁度也较高; 2.成型时,凡片材与模面在贴合时间上愈后的部位, 其厚度愈小; 3.模具结构简单,通常只有阴模;
4.制品表面光泽好,并不带任何瑕疵,材料原来的 透明性成型后不发生变化。
目前工业上用于热成型的塑料有:聚甲基丙烯酸 甲酯、聚氯乙烯、聚乙烯、ABS等多种热塑性共 聚物等。用浇铸、压延、挤出等方法制造的片材 为原料。
13.1 概述
与注射成型相比热成型具有: 优点:生产效率高、方法简单、设备投资 少、能够制造表பைடு நூலகம்较大的制品。 缺点:原料成本高,制品厚加工工序多。
13.2 热成型方法
13.2.1 差压成型
先用夹持框将片材夹紧,并置于模具上,然后用加 热器进行加热,当片材已被热至足够温度时移开加 热器,并立即抽真空或通入压缩空气加压,这时由 于在受热软化的片材两面形成压差,片材被迫向压 力较低的一边延伸和弯曲,最后紧贴于模具型腔表 面,取得所需形状,经冷却定型后,即自模具底部 气孔通入压缩空气将制品吹出,经修饰后即为制品。
3.制品侧面常会出现牵伸合冷却条纹;通常在接近模面顶部的侧 面处最多。
热成型工艺技术

热成型工艺技术热成型工艺技术是一种常用的工艺方法,用于将塑料材料加热至可塑状态,然后通过模具进行成型。
热成型工艺技术具有成本低、生产效率高、制品精度高等优点,被广泛应用于塑料制品的生产过程中。
热成型工艺技术可以分为热冲压、热挤压和热吹塑等几种形式。
其中,热冲压是通过将塑料材料加热至可塑状态,然后放入冲压机内进行冲压,通过模具将塑料板材冲压成所需的形状。
热挤压是通过将塑料材料加热到可塑状态,然后通过挤出机将塑料挤压到模具中,形成所需的形状。
热吹塑则是先将塑料加热至可塑状态,然后通过吹塑机将塑料膨胀成空心制品。
热成型工艺技术具有一定的工艺参数,例如加热温度、加热时间、冷却时间等。
这些工艺参数的选择会直接影响最终产品的质量和性能。
一般来说,加热温度要控制在塑料的熔融温度到热分解温度之间,以保证塑料能够达到可塑状态而不发生分解。
加热时间要根据塑料的类型和厚度来确定,一般来说,厚度较大的制品需要较长的加热时间。
冷却时间要充分保证制品的硬化,以避免在取模过程中变形。
热成型工艺技术在塑料制品生产中具有广泛应用。
例如,手机壳、电视外壳、汽车零部件等塑料制品的生产过程中,都离不开热成型工艺技术的应用。
热成型工艺技术具有快速高效的特点,能够大大提高生产效率,降低生产成本。
此外,热成型工艺技术还可以制作出各种形状复杂的制品,提供了更多设计的可能性。
热成型工艺技术制作的制品具有一定的强度和韧性,可以满足不同应用领域的需求。
但是,热成型工艺技术也存在一定的局限性。
首先,塑料材料的选择和质量会直接影响制品的质量和性能。
不同的塑料材料对加热温度和时间有不同的要求,需要根据具体的材料选择合适的工艺参数。
其次,热成型工艺技术在成型过程中会产生一定的废料,对资源有一定的浪费。
因此,在使用热成型工艺技术时,需要合理选择工艺参数,尽量减少废料的产生,提高生产效率和质量。
综上所述,热成型工艺技术是一种常用的工艺方法,具有成本低、生产效率高、制品精度高等优点。
铝合金热成型

铝合金热成型是一种利用高温和压力将铝合金板材或薄壁管材加工成所需形状的工艺。
该工艺具有高效、精确、可重复性好等优点,广泛应用于航空航天、汽车制造、建筑等领域。
铝合金热成型的过程通常包括以下几个步骤:首先,将铝合金材料加热至一定温度,使其变得柔软易变形;然后,将加热后的铝合金放置在模具中,施加一定的压力,使其按照模具的形状进行变形;最后,冷却后取出成型件并进行后续处理。
铝合金热成型的优点在于其可以制造出复杂形状的零件,而且成型件具有较高的强度和刚性。
此外,由于铝合金材料的密度较低,因此热成型后的零件重量较轻,有利于降低整个产品的重量和能耗。
然而,铝合金热成型也存在一些挑战和限制。
例如,由于铝合金材料的熔点较高,因此需要使用特殊的加热设备和技术来确保材料能够均匀地加热到所需的温度。
此外,由于铝合金材料的热传导性能较差,因此在成型过程中需要控制好温度和压力等因素,以避免产生缺陷和变形等问题。
综上所述,铝合金热成型是一种重要的金属加工工艺,具有广泛的应用前景。
随着技术的不断进步和发展,相信这种工艺将会在未来得到更广泛的应用和发展。
热成型工艺

热成型工艺热成型工艺是指在熔融或固态条件下,加热某种金属或合金,然后以模具、压力等形式,使材料塑性变形后,得到特定形状的产品的工艺。
热成型工艺通常包括铸造、浇铸、注射成型、挤出成型、热压成型和复合成型等。
铸造是将液体金属或金属合金用模具,经过加热或高压冷却,使材料凝固而成型的过程。
它可以制造出任意复杂的模具,此外,它还可以节约材料,提高加工精度。
但是铸造的过程也比较费时费力,而且材料的熔点必须足够低,这就要求在生产中管理工艺的要求相对较高。
浇铸是将液态金属或金属合金,由一些孔口投入模具,通过液体压力表面活性剂,使液体熔融金属合金均匀的灌入模具内的一种工艺。
浇铸能够得到产品体积大、表面平滑,结构紧密的零件。
浇铸步骤比较简单,在生产中受到工厂们的极大欢迎。
同时,它也可以制造复杂模具,它可以节约材料,提高产品质量、加工精度和温度控制精度。
注射成型是将熔融金属或合金放入模具内,再通过压力和模具的作用,将模具的内壁塑形而成的工艺。
注射成型的优点在于能够得到产品表面光洁、复杂性结构,可以节约材料,提高加工精度,减少生产费用。
此外,它同样可以制造复杂模具,它的整体成型速度快,可以有效避免因模具变形而产生的损失。
挤出成型是将金属及合金放入模具中,给模具推动,使其发生塑性变形,获得所需形状和尺寸,以及相应的表面品质技术。
挤出成型的优点在于节约材料,提高产品精度,可以制造出复杂的模具,而且成本比较低。
热压成型是将表面加工过的金属、合金放入模具中,给模具施加温度和压力,使之发生塑性变形,获得所需形状和尺寸,以及相应的表面品质技术。
热压成型的优点是表面光洁,加工精度高,产品复杂程度高,能够生产出大量产品,而且可以节省成本。
复合成型技术是将不同金属或金属合金混合在一起,并通过烘烤和压力变形实现复合的一种技术。
复合成型的优势在于可以综合利用不同材料的特性,增加产品耐腐蚀性,抗磨损性和抗拉伸性,而且成本低,可以提高产品的质量和性能。
热成型方法

热成型方法
热成型方法是一种广泛应用于工业生产中的加工技术。
它通过将热塑性材料加热至一定温度后,使其软化并塑形成所需的形状。
这种方法具有成本低、效率高、生产速度快等优点,因此被广泛应用于塑料、橡胶、铝合金、钢铁等材料的加工中。
热成型方法主要分为热压成型和热吹塑成型两种。
热压成型是指将加热后的材料置于模具中进行加压成型的方法,适用于高精度、高强度的产品制造。
热吹塑成型则是将加热后的材料通过管道吹入模具中,然后加压成型的方法,适用于生产大批量、低成本的产品。
在热成型方法中,温度是一个非常关键的因素。
温度过高会导致材料烧焦或分解,而温度过低则会导致材料难以软化和成型。
因此,在热成型过程中,需要对温度进行精确控制,以确保产品质量和生产效率。
除了温度控制外,热成型方法中还需要注意模具的设计和制造。
模具的形状和尺寸直接影响产品的成型效果和精度,因此需要根据不同的产品要求进行设计和制造。
同时,模具材料的选择也非常重要,不同的材料具有不同的热导率和耐热性能,需要根据实际情况进行选择。
在实际生产中,热成型方法还可以与其他加工方法相结合,以达到更好的加工效果。
例如,可以将热成型与冷冲压、冷冻淬火等方法
相结合,以实现更高的生产效率和产品质量。
热成型方法是一种非常重要的加工技术,具有广泛的应用前景。
只要掌握了正确的操作方法和技巧,就可以在生产中实现高效、低成本的加工过程,为工业生产提供有力支持。
- 1、下载文档前请自行甄别文档内容的完整性,平台不提供额外的编辑、内容补充、找答案等附加服务。
- 2、"仅部分预览"的文档,不可在线预览部分如存在完整性等问题,可反馈申请退款(可完整预览的文档不适用该条件!)。
- 3、如文档侵犯您的权益,请联系客服反馈,我们会尽快为您处理(人工客服工作时间:9:00-18:30)。
热成型
1.概述
热成型采用热和压力或真空迫使热的热塑性材料作用于模具表面,从而达到加工目的。
热成型是热塑性材料最常用的一种加工方法,该方法是用于金属片和部分纸片加工方法的延伸。
尽管各种不同的加工方法存在着许多不同的特点,但实际上都是:采用片材和模具,通过热和负压或真空,将片材承压成所需形状。
虽然金属和金属合金的种类很多,但是他们还是无法与热塑性塑料片材种类相比。
下面主要就塑料热成型的工艺以及热成型制品结构工艺性要求两方面进行简单的介绍。
2.热成型工艺简介
2.1.热成型工艺原理和特点
热成型是一类以热塑性塑料片材为原料生产敞口容器形薄壳类制品的成型工艺。
具体方法是:将加热到软化温度的塑料片材与模具边缘夹持固定;给软化的片材单向施压,使其紧贴在模具型面上而成型;充分冷却后脱模取件;经修饰即得成品。
热成型可以使用各种工艺制成的塑料片材。
成型力可以是真空吸力、空气压力、机械压力、弹性材料变形恢复力等。
与其它成型方法相比,热成型具有以下特点:
①制品规格多样,可成型特厚、特薄、特大、特小各类制件,产品应用遍及各行各业范围极广。
②原料适应性强,几乎所有的热塑性塑料都可用此法成型。
③设备投资少,模具精度及材质要求低,成型效率高。
④制品与模具贴合面结构形状鲜明,光洁度较高。
⑤制品厚度均匀性差,与模具贴合晚的部位厚度较小。
⑥不能成型结构太复杂的塑件,制品使用需要的孔洞需后加工。
⑦需要回收使用的,边角废料较多。
2.2.热成型工艺类型
热成型工艺类型很多,施力方法、模具等各有特点,产品种类、规格、性能等也有所不同。
简介如下:
①凹模真空成型
又叫阴模真空成型,简便易行,使用广泛,塑件外表面形状尺寸由模具限定,用于成型深度不大的塑件,深形塑件壁厚偏差大。
(图见下页)
②凸模真空成型
又叫阳模真空成型,塑件内表面形状尺寸由模具限定,塑件壁厚偏差较小,收缩率低。
(图见下页)
③气压成型
制品特点与凹模真空成型类似,成型压力较真空成型高,速度快,可成型厚片或较复杂制品。
制品与模具贴合面光洁度高,形状清晰,尺寸准确。
(图见下页)
④柱塞辅助真空成型
制品厚度均匀性较好,可成型深度较大的制品。
但塑件上可能残留柱塞压痕。
⑤气压预拉伸凹模真空成型
俗称鼓泡成型,与直接凹模真空成型相比制品厚度均匀性大幅改善,且塑件上没有柱塞压痕。
⑥气压预拉伸凸模真空成型
鼓泡成型的又一种方式。
除此之外,还可采用其它方法进行片材预拉伸,其目的及效果类似。
⑦凸凹模对压成型
机械力施压,塑件内外表面均由模具限定,形状清晰、尺寸精确,壁厚偏差较小,但需两半刚性模。
⑧钢模与硅橡胶模对压成型
弹性恢复力施压,塑件外表面由钢模具限定,形状清晰精确,壁厚偏差较小,制品性能接近凸凹模对压成型,模具费用较低。
3.热成型制品结构工艺性要求
与其它模塑制品一样,热成型制品设计除考虑使用功能、强度要求及艺术造型等设计条件之外,也必须满足其成型工艺性要求。
3.1几何形状
开口宽阔、深度浅、流线型外轮廓、形状简单,壁薄,避免大平面,避免侧孔、侧凹。
3.2脱模斜度和转角
和其它型腔模一样,需要脱模斜度。
选取范围:0.5 ~4 °
阴模:1/120~1/60;
阳模:1/30~1/20。
斜度大,壁厚均匀。
塑件角隅部分不允许有锐角,圆弧R要尽可能大一些,圆角半径不小于壁厚的3~5倍。
3.3引伸比和展开倍率
引伸比即深度和直径之比H/D。
用于表示片材的变形程度。
引伸比在很大程度上反映了塑件成型的难易程度。
引伸比大难成型,制品壁厚小、均匀性差。
引伸比取值视片材变形能力而定,一般不大于1.5,韧性好易成型材料可大于4。
展开倍率(x)是指塑件表面积与夹持圈内片材面积之比。
也与片材的延展性有关,不同塑料有不同最佳值:硬PVC=3,ABS =5~7,PC=3~5。
同种片材,成型压力较大时可获得较大的展开倍率。
制品厚度、展开倍率、片材厚度三者之间有以下关系,可以互相演算。
3.4产品精度及形位公差
热成型时片材温度低于塑料粘流温度,制品形状靠成型压力强迫材料拉伸变形获得,成型收缩率很大。
因此,热成型制品尺寸及形状精度都不能要求太高。