QT450-10铸造毛坯件检验规范
毛坯铸钢件检验规范

液体渗透检验试验方法
JB/T 6440
阀门受压铸钢件射线照相检测
ISO 15156 石油天然气工业—油气开采中含硫化氢环境中使用的材料
4 订货须知
4.1 本规范是本公司签发的采购订单、零件图相配套的文件,供方提供的零件必须同时也 满足本规范的要求;
4.2 采购订单或零件图上的要求与本规范不一致时,应优先满足采购订单及零件图的要 求;
摆锤(V 形缺口)冲击试验。
b) 一项冲击试验至少以 3 个试样为一组,应以最终热处理条件下,每批炉号材料的代
表性试棒进行试验。试样的尺寸设计和加工按 A703/A703M 图 11 规定。
注:设计标准或地方要求,允许在高于-29℃(-20ºF)的最低设计温度时做冲击试验。
c) 冲击试验应按管道设计标准在最低温度下进行。
棒取法应遵守 1/4T 的原则,试棒加工按 A703/A703M 图 4 规定。
5.3.2 拉伸和弯曲试验的力学性能应符合本规范表 1(另附)要求; 5.3.3 冲击韧性试验是在客户有需要时做,但注意下列事项:
a) 用于规定设计温度低于-29℃(-20ºF)的碳钢承压件应按 ISO148-1 或 ASTM A370 进行
5.2.化学成份应符合本规范表 1(另附)要求;其偏差应符合表 2 要求,该偏差可取得买方
同意。
表 2 铸钢件化学成份分析允许偏差
元素 C Mn Si P
范围 5%
≤0.65 ≥0.65 ≤1.00 ≥1.00 ≤0.60 ≥0.60
全部
允许偏差 %
0.03×C+0.02 0.04
0.08×Mn+0.01 0.09
检验,并满 足标准要求 8.2 铸件交货时应提供的质量文件 a)材料标准和牌号; b) 炉号; c) 化学分析结果; d) 机械性能试验和硬度测试结果; e) 热处理方法及温度记录曲线图; f) 采购合同要求的其他补充试验结果,如冲击试验、金相分析、宏观浸蚀试验、硬度和
铸件外观检验规范标准

铸件外观检验规范一、范围本规范适用于本厂产品的精铸件、砂型铸件的外观检验。
本规范规定了精铸件、砂型铸件的外观检验要求和详尽查收准则。
二、铸件外观弊端名称及分类种类序号名称特征1气孔2缩孔孔3缩松眼4渣眼5砂眼6铁豆裂7热裂8冷裂纹9温裂10粘砂表面11结疤缺12夹砂在铸件内部、表面或近于表面处有大小不等的圆滑孔眼。
形状有圆的、长的及不规则的、有单个的,也有齐聚成片的。
颜色为白色或带一层暗色,有时覆有一层氧化皮。
在铸件厚断面内部,两交界面的内部及厚断面和厚断面交接处的内部或表面,形状不规则,孔内粗糙不平,晶粒粗大。
在铸件内部细小而不连结的缩孔,齐聚在一处或多处,晶粒粗大,各晶粒间存在很小的孔眼,水压试验时渗水。
在铸件内部或表面形状不规则的孔眼。
孔眼不圆滑,里面全部或部分充塞着渣。
在铸件内部或表面有充塞着型砂的孔眼。
在铸件内部或表面有包含金属小珠的孔眼,常发生在铸铁件上。
在铸件上有穿透或不穿透的裂纹(主若是波折形的),开裂处金属表皮氧化。
在铸件上有穿透或不穿透的裂纹(主若是直的),开裂处金属表皮未氧化。
在铸件上有穿透或不穿透的裂纹。
开裂处金属表皮氧化。
由于气割、焊接或热办理不当所引起。
在铸件表面上、全部或部分覆盖着金属(或金属氧化物)与砂(或涂料)的混杂物(或化合物),或一层烧结的型砂,致使铸件表面粗糙。
在铸件表面上,有金属夹杂或包含型砂或渣的片状或瘤状物。
在铸件表面上,有一层金属瘤状或片状物。
在金属瘤片和铸件之间夹有一层型砂。
陷13冷隔形14多肉在铸件上有一种未圆满交融的缝隙或洼坑,其交接边缘是圆滑的。
铸件上有形状不规则的毛刺、披缝或凸出部分。
状15浇不足缺16变形由于金属液未圆满充满型腔而产生的铸件缺肉。
由缩短应力引起的铸件外形和尺寸与图样不符。
陷17料口毛刺由打磨料口时产生的毛刺。
三、检验要求铸件不得有明显孔眼(气孔、缩孔、缩松、渣眼、砂眼、铁豆),裂纹(热裂、冷裂、温裂),表面弊端(粘砂、结疤、夹砂、冷隔),形状弊端(多肉、浇不足、变形、料口毛刺)等严重影响产品的外观和强度弊端。
毛坯检验规范

毛坯检验规范1、目的对产品毛坯进料检验作文件化规定,使检验过程规范化和标准化,避免和减少因毛坯的不合格造成后续作业的困难和产品的不合格。
2、范围适用于本公司所有铸造毛坯、锻造毛坯和压铸毛坯的进料检验过程。
3、依据1).国家相关标准如:《逐批检查计数抽样程序及检查表》GB2828-2008《铸造铜合金技术条件》GB1176-87《阀门铸铜件外观质量要求》GB12231《锌合金、铝合金、铜合金压铸件技术条件》等;JB2702-802).产品图样、技术要求及工艺要求;3).客户要求和合同要求等。
4、内容4.1毛坯尺寸规定4.1.1毛坯两端面的加工余量:1/4"--1/2"各为0.8-1.0mm;3/4"--11/4"各为1.0-1.2mm;11/2"--2"各为1.0-1.5mm;21/2"--4"各为1.2-2.0mm。
4.1.2外螺纹或外圆的半径方向加工余量:1/4"--1/2"为0.8-1.0mm;3/4"--11/4"为1.0-1.2mm;11/2"--2"为1.2-1.5mm;21/2"--4"为1.5-2.0mm。
4.1.3内孔或内螺纹半径方向加工余量:1/4"--1/2"为0.8-1.0mm;3/4"--11/4"为0.8-1.2mm;11/2"--2"为1.0-1.5mm;21/2:--4"为1.5-2.0mm。
4.1.4阀体中孔平面加工余量:0.5-1.0mm。
4.1.5内孔深度和外圆长度毛坯尺寸:与图纸加工尺寸相符。
4.1.6抛光的毛坯单向表面余量1/4"--1/2"为0.5-0.8mm;3/4"--1"为0.8-1.2mm;11/4"--2"为1.0-1.5mm。
QT450-10铸造毛坯件检验规范
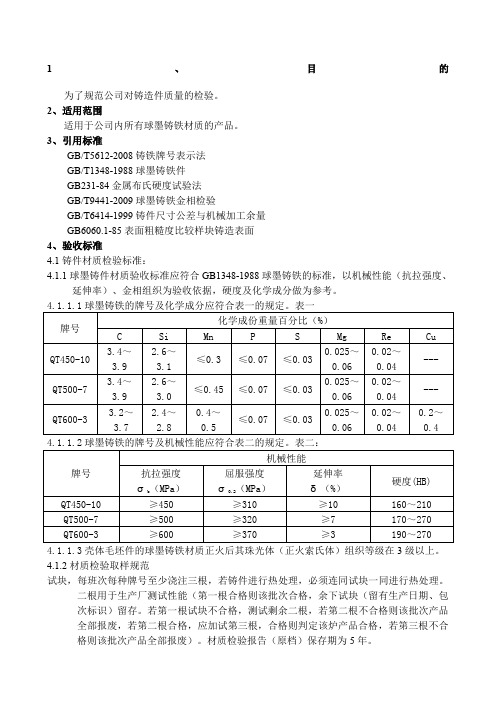
1、目的为了规范公司对铸造件质量的检验。
2、适用范围适用于公司内所有球墨铸铁材质的产品。
3、引用标准GB/T5612-2008铸铁牌号表示法GB/T1348-1988球墨铸铁件GB231-84金属布氏硬度试验法GB/T9441-2009球墨铸铁金相检验GB/T6414-1999铸件尺寸公差与机械加工余量GB6060.1-85表面粗糙度比较样块铸造表面4、验收标准4.1铸件材质检验标准:4.1.1球墨铸件材质验收标准应符合GB1348-1988球墨铸铁的标准,以机械性能(抗拉强度、延伸率)、金相组织为验收依据,硬度及化学成分做为参考。
4.1.1.3壳体毛坯件的球墨铸铁材质正火后其珠光体(正火索氏体)组织等级在3级以上。
4.1.2材质检验取样规范试块,每班次每种牌号至少浇注三根,若铸件进行热处理,必须连同试块一同进行热处理。
二根用于生产厂测试性能(第一根合格则该批次合格,余下试块(留有生产日期、包次标识)留存。
若第一根试块不合格,测试剩余二根,若第二根不合格则该批次产品全部报废,若第二根合格,应加试第三根,合格则判定该炉产品合格,若第三根不合格则该批次产品全部报废)。
材质检验报告(原档)保存期为5年。
球铁铸件从每包铁水的最后一型附铸金相试块或铸件本体进行金相检验,依次往前直到合格(或本包铁水所浇铸件检验完)为止。
附铸试块应能代表本体。
若试块不好,应对铸件本体破件进行检验。
若金相检验由问题,加倍抽查。
金相本体试块应按天分类以月为单位保存,保存期为6个月,检验报告保存期5年。
球化等级要求在3级以上,石墨大小要求为5~7级。
每炉铁水(炉前)及至少两炉铸件(炉后)的化学成分。
炉前主要化验C、Si和S,炉后所有元素全部化验。
每天第一炉溶清后必须检测C、Si、Mn、P和S,之后C、Si每炉化验检测。
化学成分记录要求齐全,记录表保存期5年。
金属布氏硬度试验法的规定进行,硬度试验可在铸件试块或铸件本体上的一个部位或几个部位上进行。
铸造毛坯件质量检验规范
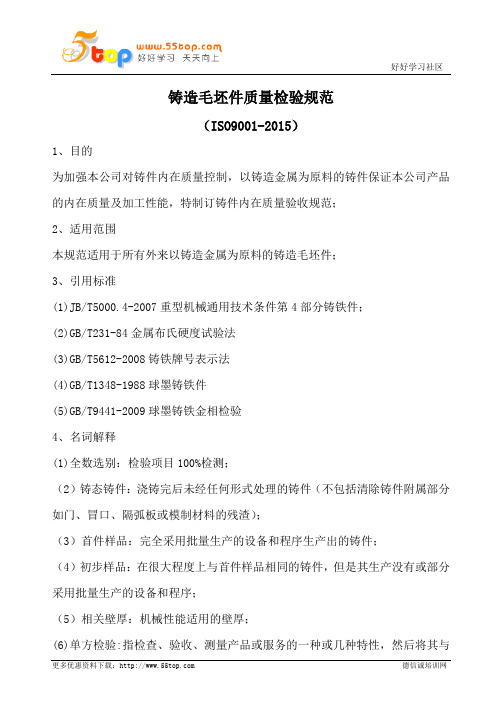
铸造毛坯件质量检验规范(ISO9001-2015)1、目的为加强本公司对铸件内在质量控制,以铸造金属为原料的铸件保证本公司产品的内在质量及加工性能,特制订铸件内在质量验收规范;2、适用范围本规范适用于所有外来以铸造金属为原料的铸造毛坯件;3、引用标准(1)JB/T5000.4-2007重型机械通用技术条件第4部分铸铁件;(2)GB/T231-84金属布氏硬度试验法(3)GB/T5612-2008铸铁牌号表示法(4)GB/T1348-1988球墨铸铁件(5)GB/T9441-2009球墨铸铁金相检验4、名词解释(1)全数选别:检验项目100%检测;(2)铸态铸件:浇铸完后未经任何形式处理的铸件(不包括清除铸件附属部分如门、冒口、隔弧板或模制材料的残渣);(3)首件样品:完全采用批量生产的设备和程序生产出的铸件;(4)初步样品:在很大程度上与首件样品相同的铸件,但是其生产没有或部分采用批量生产的设备和程序;(5)相关壁厚:机械性能适用的壁厚;(6)单方检验:指检查、验收、测量产品或服务的一种或几种特性,然后将其与指定要求相比较以确定产品是否合格的行为;(7)连续检验:指对生产一段时间后的大量相同规格的铸件的特性和/或生产参数进行定期检验;(8)跳跃检验:指对生产一段时间后的大量相同规格的铸件的特性和/或生产参数进行间断性检验;(9)试件:样品的一部分,有特定的尺寸,经过机械加工也可能没有经过机械加工,并严格遵守所要求的试验条件;5、铸件内在质量验收总则球墨铸件材质验收标准应符合GB1348-1988球墨铸铁的标准,以机械性能(抗拉强度、屈服强度、延伸率)、金相组织、硬度及化学成分为验收判定依据;5.1铸件化学成分(1)如果未在图纸或询价单或订单或者质保协议中另行规定,对于铸造材料的化学组成,应采用相关材料标准的要求;(2)如果未在图纸或询价单或订单或者质保协议中另行规定,铸造材料化学组成的有关数据应特指液体金属,即球化后浇筑前的(炉前)浇包分析;(3)如果相关材料标准和订单或询价单等都不含有铸造材料化学组成的任何有关数据,如只规定了材料的机械性能,则制造商可以自行选择适当的化学组成,但必须符合铸件使用地(毛坯或半成品或者成品的最终使用地点)的环保等法律法规要求;(5)化学组成在要求对某一铸件进行化学分析时,化学元素允许偏差要符合材料标准给出的偏差或符合采购方与制造商之间通过协议确定的偏差。
压铸件毛坯质量检验标准
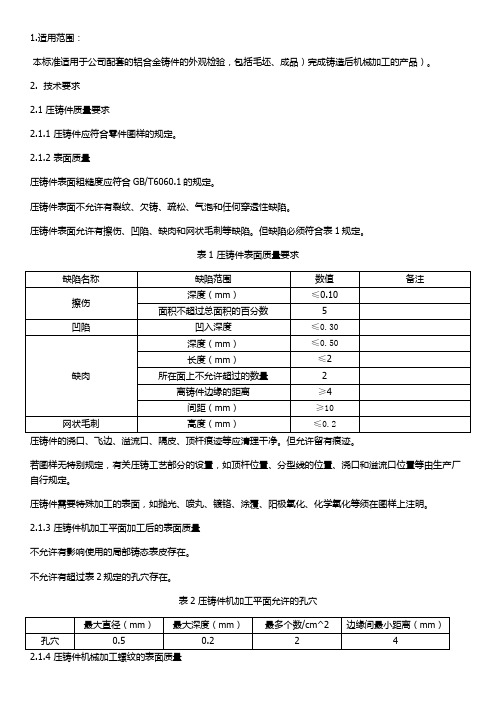
1.适用范围:本标准适用于公司配套的铝合金铸件的外观检验,包括毛坯、成品)完成铸造后机械加工的产品)。
2. 技术要求2.1 压铸件质量要求2.1.1 压铸件应符合零件图样的规定。
2.1.2 表面质量压铸件表面粗糙度应符合GB/T6060.1的规定。
压铸件表面不允许有裂纹、欠铸、疏松、气泡和任何穿透性缺陷。
压铸件表面允许有擦伤、凹陷、缺肉和网状毛刺等缺陷。
但缺陷必须符合表1规定。
表1 压铸件表面质量要求若图样无特别规定,有关压铸工艺部分的设置,如顶杆位置、分型线的位置、浇口和溢流口位置等由生产厂自行规定。
压铸件需要特殊加工的表面,如抛光、喷丸、镀铬、涂覆、阳极氧化、化学氧化等须在图样上注明。
2.1.3 压铸件机加工平面加工后的表面质量不允许有影响使用的局部铸态表皮存在。
不允许有超过表2规定的孔穴存在。
表2 压铸件机加工平面允许的孔穴2.1.4 压铸件机械加工螺纹的表面质量压铸件机械加工螺纹的头两扣不允许有任何缺陷,其余部分螺纹不允许有表3所规定的孔穴缺陷。
表3 机械加工螺纹规定的孔穴缺陷范围表4 不铸底孔加工后的螺纹表面质量2.1.5 压铸件机械加工孔加工后表面的孔穴规定范围见表5。
表5 机械加工孔表面的孔穴规定范围2.1.6 压铸件内部质量压铸件若能满足其使用性能要求,则压铸件本质缺陷不作为报废的依据。
压铸件内部不允许有冷隔缺陷。
压铸件内部允许有气孔、疏孔、夹杂等缺陷,但孔穴缺陷最大直径不超过壁厚的1/8,孔穴数量在任何剖面上不超过2个/cm2 。
重要压铸件的受力部位须进行解剖检查,符合表6中的规定。
表6 压铸件指定解剖部位内部质量规定2.1.7 其它性能要求应符合GB/T15114的规定。
3 试验方法及检验规则3.1 化学成分3.1.1 铝合金化学成分的检验方法,检验规则和复检应符合GB/T15115的规定。
3.1.2 化学成分的试样也可取自压铸件,但必须符合GB/T15115的规定。
3.2 力学性能3.2.1 力学性能的检验方法,检验频率和检验规则应符合GB/T15115的规定。
毛坯检验规范

毛坯检验规范1、目的对产品毛坯进料检验作文件化规定,使检验过程规范化和标准化,避免和减少因毛坯的不合格造成后续作业的困难和产品的不合格。
2、范围适用于本公司所有铸造毛坯、锻造毛坯和压铸毛坯的进料检验过程。
3、依据1).国家相关标准如:《逐批检查计数抽样程序及检查表》 GB2828-2008《铸造铜合金技术条件》 GB1176-87《阀门铸铜件外观质量要求》 GB12231《锌合金、铝合金、铜合金压铸件技术条件》等; JB2702-802).产品图样、技术要求及工艺要求;3).客户要求和合同要求等。
4、内容4.1 毛坯尺寸规定4.1.1 毛坯两端面的加工余量:1/4"--1/2" 各为 0.8-1.0mm;3/4"--1 1/4" 各为 1.0-1.2mm;1 1/2"--2" 各为 1.0-1.5mm;2 1/2"--4" 各为 1.2-2.0mm。
4.1.2 外螺纹或外圆的半径方向加工余量:1/4"--1/2" 为 0.8-1.0mm;3/4"--1 1/4" 为 1.0-1.2mm;1 1/2"--2" 为 1.2-1.5mm;2 1/2"--4" 为 1.5-2.0mm。
4.1.3 内孔或内螺纹半径方向加工余量:1/4"--1/2" 为 0.8-1.0mm;3/4"--1 1/4" 为 0.8-1.2mm;1 1/2"--2" 为 1.0-1.5mm;2 1/2:--4" 为 1.5-2.0mm。
4.1.4阀体中孔平面加工余量:0.5-1.0mm。
4.1.5内孔深度和外圆长度毛坯尺寸:与图纸加工尺寸相符。
4.1.6抛光的毛坯单向表面余量1/4"--1/2" 为 0.5-0.8mm;3/4"--1" 为 0.8-1.2mm;1 1/4"--2" 为 1.0-1.5mm。
qt450-10材料金相组织标准
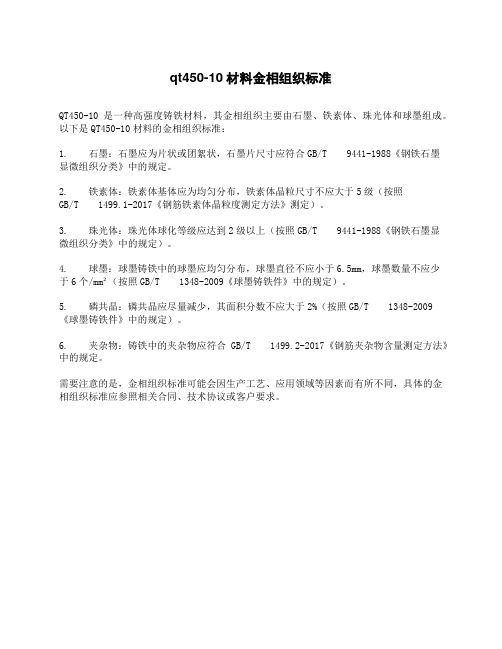
qt450-10材料金相组织标准
QT450-10是一种高强度铸铁材料,其金相组织主要由石墨、铁素体、珠光体和球墨组成。
以下是QT450-10材料的金相组织标准:
1. 石墨:石墨应为片状或团絮状,石墨片尺寸应符合GB/T 9441-1988《钢铁石墨
显微组织分类》中的规定。
2. 铁素体:铁素体基体应为均匀分布,铁素体晶粒尺寸不应大于5级(按照
GB/T 1499.1-2017《钢筋铁素体晶粒度测定方法》测定)。
3. 珠光体:珠光体球化等级应达到2级以上(按照GB/T 9441-1988《钢铁石墨显
微组织分类》中的规定)。
4. 球墨:球墨铸铁中的球墨应均匀分布,球墨直径不应小于6.5mm,球墨数量不应少
于6个/mm²(按照GB/T 1348-2009《球墨铸铁件》中的规定)。
5. 磷共晶:磷共晶应尽量减少,其面积分数不应大于2%(按照GB/T 1348-2009《球墨铸铁件》中的规定)。
6. 夹杂物:铸铁中的夹杂物应符合GB/T 1499.2-2017《钢筋夹杂物含量测定方法》中的规定。
需要注意的是,金相组织标准可能会因生产工艺、应用领域等因素而有所不同,具体的金相组织标准应参照相关合同、技术协议或客户要求。
铸态球铁QT450-10熔炼过程控制 有要点

铸态球铁QT450-10熔炼过程控制有要点铸态球墨铸铁QT450-10的熔炼过程控制1、生产条件及化学成分设计铁液采用冲天炉—感应电炉双联熔炼,其中冲天炉为3 t/h 多排小风口热风酸性炉,感应电炉为2 t中频感应电炉。
球化、孕育处理前,铁液在感应电炉中进行进一步的脱硫处理,以获得高温、低氧化、低硫的原铁液。
生产中对铸态QT450-10的化学成分提出的要求为:3.4%~3.9%C,2.5%~3.0%Si,≤0.4%Mn,<0.050%P,<0.025%S,0.04%~0.10%Mg残,0.015%~0.04%RE残。
2 、熔炼过程控制要点(1)准备和检查工作时要使用的相关物品,如:FeSi75A115—B孕育剂、FeSiMg8RE5球化剂、增碳剂、铁液搅拌工具等。
(2)新包或4 h未使用的铁液包(0.5 t)使用前必须烫包,使用地上衡称量空包和装满铁液的包,计算一包铁液的重量(用以计算合金加入量)。
(3)孕育剂、球化剂合金预热温度应大于150℃,上限越高越好,但最高不超过400℃,并且预热时不能接触明火;孕育剂粒度3~20 mm,球化剂粒度10~25 mm。
(4)计算孕育剂、球化剂的加入量,孕育剂含硅按75%计算,加入量按1.0%~1.4%计算,球化剂含硅按44%计算,加入量按1.5%~1.8%计算。
(5)放置合金,合金放在凹坑式包底的凹坑内,由下至上的放置顺序为:球化剂一孕育剂一珍珠岩砂,并尽量塞实,如必要还应加压一块小于5 kg的生铁或钢板。
其中孕育剂只能加入计算量的70%,剩余的在处理时加入。
(6)铁液出炉前应制白口化试样,送做光谱成分分析。
确定C:3.7%~3.9%,Si:1.6%~1.8%。
成分分析达不到要求,应再对铁液进行调整,并观察原铁液浇注的三角试样的断面是否正常。
(7)调整铁液的处理温度为1480~1500℃。
使用测温仪测温并记录。
(8)球化和孕育处理①铁液倒人的落点应在包内无合金的一侧,以避免球化剂过早反应:②铁液倒人1/3~1/2时再从出铁槽加入孕育剂计算量的20%;③铁液加入预定值的约2/3时进行反应,反应基本完毕进行初次搅拌,然后加足铁液进行搅拌,搅拌深度必须超过铁液深度的一半。
铸造毛坯检验规定
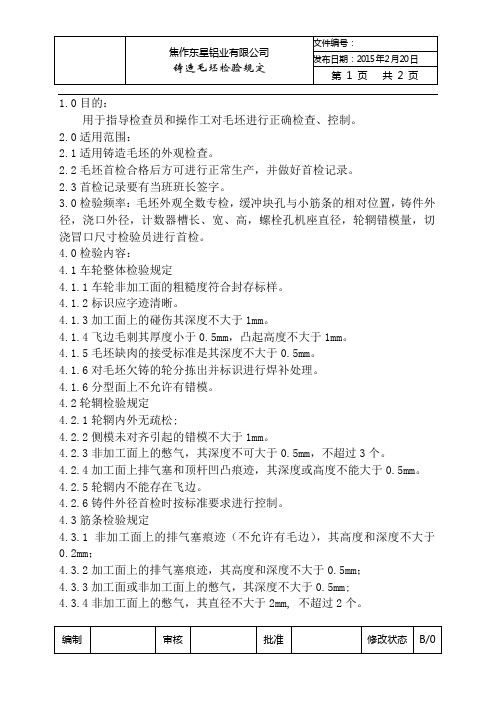
1.0目的:用于指导检查员和操作工对毛坯进行正确检查、控制。
2.0适用范围:2.1适用铸造毛坯的外观检查。
2.2毛坯首检合格后方可进行正常生产,并做好首检记录。
2.3首检记录要有当班班长签字。
3.0检验频率:毛坯外观全数专检,缓冲块孔与小筋条的相对位置,铸件外径,浇口外径,计数器槽长、宽、高,螺栓孔机座直径,轮辋错模量,切浇冒口尺寸检验员进行首检。
4.0检验内容:4.1车轮整体检验规定4.1.1车轮非加工面的粗糙度符合封存标样。
4.1.2标识应字迹清晰。
4.1.3加工面上的碰伤其深度不大于1mm。
4.1.4飞边毛刺其厚度小于0.5mm,凸起高度不大于1mm。
4.1.5毛坯缺肉的接受标准是其深度不大于0.5mm。
4.1.6对毛坯欠铸的轮分拣出并标识进行焊补处理。
4.1.6分型面上不允许有错模。
4.2轮辋检验规定4.2.1轮辋内外无疏松;4.2.2侧模未对齐引起的错模不大于1mm。
4.2.3非加工面上的憋气,其深度不可大于0.5mm,不超过3个。
4.2.4加工面上排气塞和顶杆凹凸痕迹,其深度或高度不能大于0.5mm。
4.2.5轮辋内不能存在飞边。
4.2.6铸件外径首检时按标准要求进行控制。
4.3筋条检验规定4.3.1非加工面上的排气塞痕迹(不允许有毛边),其高度和深度不大于0.2mm;4.3.2加工面上的排气塞痕迹,其高度和深度不大于0.5mm;4.3.3加工面或非加工面上的憋气,其深度不大于0.5mm;4.3.4非加工面上的憋气,其直径不大于2mm, 不超过2个。
4.3.5筋条上不能有疏松;4.3.6飞边、毛刺其厚度小于0.5mm,凸起高度不大于1mm。
4.3.7与轮辋交接处不允许有裂纹、缩松。
4.3.8筋条非加工面不允许有涂料脱落、凹凸不平等缺陷。
4.4轮鼓部位检验规定4.4.1轮鼓内各交接处无裂纹;4.4.2排气塞痕迹其深度不大于0.5mm,高度不大于0.3mm。
4.4.3轮鼓内的顶杆痕迹其高度和深度不大于1mm。
QT450-10铸造毛坯件检验规范

1、目的为了规范公司对铸造件质量的检验。
2、适用范围适用于公司内所有球墨铸铁材质的产品。
3、引用标准GB /T5612-2008 铸铁牌号表示法GB/T1348-1988 球墨铸铁件GB 231-84 金属布氏硬度试验法GB/T9441-2009 球墨铸铁金相检验GB/T6414-1999 铸件尺寸公差与机械加工余量GB 6060.1-85 表面粗糙度比较样块铸造表面4、验收标准4.1 铸件材质检验标准:4.1.1 球墨铸件材质验收标准应符合GB1348-1988 球墨铸铁的标准,以机械性能(抗拉强度、延伸率)、金相组织为验收依据,硬度及化学成分做为参考。
4.1.1.3 壳体毛坯件的球墨铸铁材质正火后其珠光体(正火索氏体)组织等级在3级以上。
4.1.2 材质检验取样规范4.1.2.1机械性能检查:机械性能测试的试块,每班次每种牌号至少浇注三根,若铸件进行热处理,必须连同试块一同进行热处理。
二根用于生产厂测试性能(第一根合格则该批次合格,余下试块(留有生产日期、包次标识)留存。
若第一根试块不合格,测试剩余二根,若第二根不合格则该批次产品全部报废,若第二根合格,应加试第三根,合格则判定该炉产品合格,若第三根不合格则该批次产品全部报废)。
材质检验报告(原档)保存期为5年。
4.1.2.2金相组织检查:球铁铸件从每包铁水的最后一型附铸金相试块或铸件本体进行金相检验,依次往前直到合格(或本包铁水所浇铸件检验完)为止。
附铸试块应能代表本体。
若试块不好,应对铸件本体破件进行检验。
若金相检验由问题,加倍抽查。
金相本体试块应按天分类以月为单位保存,保存期为6个月,检验报告保存期5年。
球化等级要求在3级以上,石墨大小要求为5~7级。
4.1.2.3化学成分检查:每天必须分析每炉铁水(炉前)及至少两炉铸件(炉后)的化学成分。
炉前主要化验C、Si和S,炉后所有元素全部化验。
每天第一炉溶清后必须检测C、Si、Mn、P和S,之后C、Si每炉化验检测。
铸件质量检验标准

铸件质量检验标准一、目的:为了确保外协毛坯铸件、采购毛坯铸件、标准铸件、成品铸件质量符合工艺、技术要求,为了满足产品特性,结合相关文件特制定本标准。
二、适用范围:本标准适用于我公司产品外协、采购、生产、装配过程中,全部铸件质量检验标准。
三、检验标准:3.1 铸件结构要符合设计要求或加工工艺要求。
无特殊要求时按铸件通用标准执行。
通用标准等级分为:交货验收技术条件标准;铸件质量分等通则(合格品、一等品、优等品)材质、检验方法;工艺和材料规格等一般性规则。
3.2 铸件成品检验。
铸件成品检验包括:铸件的内部质量检验和外观质量检验。
铸件内部质量检验包括:化学成分、机械性能等。
铸件外观质量检验包括:表面质量、粗糙度、铸件尺寸、重量等。
3.2.1 铸件内部质量检验①化学成分:表1②机械性能表23.2.2 铸件外观质量检验①表面质量检验。
机械加工生产一线人员在工艺过程中对铸造毛坯的检验主要是对其外观铸造缺陷(如有无砂眼、砂孔、疏松、浇不足、铸造裂纹等)的检验;以及毛坯加工余量是否满足加工要求的检验。
表3 铸件外观质量检验项目(GB6060.1-1997)②粗糙度检验。
表4 铸件表面粗糙度(Ra值μm)(GB6060.1-1997)③铸件尺寸检验。
主要一种是采用划线法检查毛坯的加工余量是否足够。
另一种方法是:用毛坯的参考基准面(也称工艺基准面)作为毛坯的检验基准面的相对测量法(需要测量相对基准面的尺寸及进行简单换算)。
表5 铸件尺寸公差数值(mm)(GBT 6414-1997)1)在等级CT1~CT15中对壁厚采用粗一级公差。
2)对于不超过16mm的尺寸,不采用CT13~CT16的一般公差,对于这些尺寸应标注个别公差。
3)等级CT16仅适用于一般公差规定为CT15的壁厚。
表6 单件、小批量生产的铸件公差等级(GBT 6414-1997)注:1)表中所列出的公差等级是小批量的或单件生产的砂型铸件通常能够达到的公差等级。
铸件检验标准
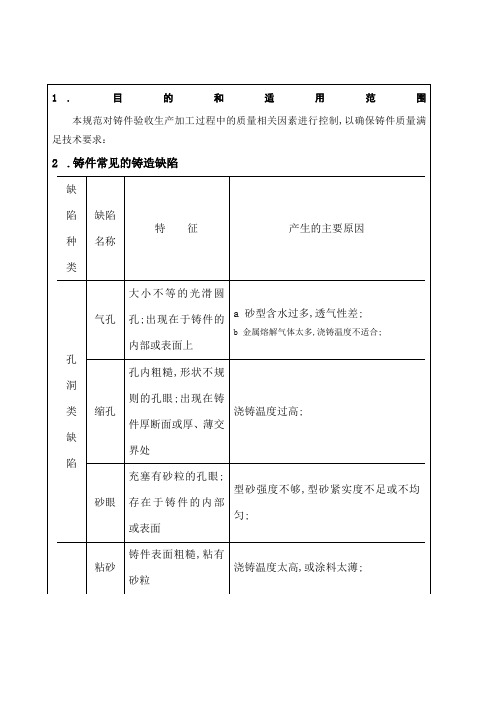
3.
铸件出现铸造缺陷后,并非都是废品,应根据铸件的具体技术要求判断,判断原则如下:
a铸件出现铸造缺陷后,其质量达不到技术要求,而又不能修补时,应列为废品;
b 不重要的铸件或铸件的某些部位即使存在铸造缺陷,如不影响使用或者修补后不影响使用时,可以不列为废品;
c 当铸件出现铸造缺陷,即使技术上可以修补,并且修补后不影响使用,但由于经济上不合算,或因此会给企业造成不良影响时,仍应不修补而列为废品;
浇铸温度过高;
砂眼
充塞有砂粒的孔眼;存在于铸件的内部或表面
型砂强度不够,型砂紧实度不足或不均匀;
粘砂
铸件表面粗糙,粘有砂粒
浇铸温度太高,或涂料太薄;裂纹开裂Fra bibliotek开裂处金属表面氧化
合金化学成分不当,铸件厚薄相差大,结构不合理,金属浇铸温度过高,型砂或泥芯容让性差或落砂过早;
冷隔
未完全融合的缝隙或洼坑,交接处是圆滑的
a为铸件生产和管理部门提供质量信息;保证产品质量;
b铸件的检验主要包括铸件表面质量检验、铸件内在质量检验以及铸件质量的综合鉴定;其中,铸件的表面质量包括铸件的表面缺陷、尺寸精度、质量偏差、表面粗糙度等;
4:铸件外观质量的检验
检验的依据是铸件的有关标准、技术条件和图样;铸件的表面质量主要包括铸件的表面缺陷、尺寸精度、质量偏差、形状偏差、表面粗糙度和铸件表面清理质量等多方面内容;
5、铸件
为保证铸件的表面质量,检验要求一般规定如下;
在铸件上不允许有裂纹、通孔、穿透性的冷隔和穿透性的缩松、夹渣缺陷;
铸件非加工表面的毛刺、披锋、粘砂应清理至与铸件面同样平整;
铸件待加工表面,允许有不超过加工余量范围内的任何缺陷存在,但裂纹缺陷应予清除;
铸铁件通用检验标准

铸铁件通用检验标准1目的:规范公司对铸铁件的检查验收。
2适用范围:适用于铸铁件。
※本标准就是铸件的通用型标准,铸件存有特殊要求时,参看有关铸件分类环评标准。
3环评标准:3.1铸铁件材质检验标准:3.1.1球墨铸铁件材质检验标准:球墨铸件材质环评标准应当合乎gb1348或en1563:1997球墨铸铁的标准,以机械性能(抗拉强度、延伸率)、球化率和渗碳体含量为环评依据,硬度、其它金二者非政府及化学成份作为参照。
3.1.1.1球墨铸铁牌号及机械性能(单铸试块)见下表:机械性能球铁牌号抗拉强度,σqt400-18qt400-15qt450-10qt450-12qt500-7qt600-3qt700-2qt550-6b屈服强度,σ0.2延伸率,硬度(hb)δ(%)≥18≥15≥10≥12≥7≥3≥2≥6130-180130-180160-210160-210170-270190-270225-305187-255(mpa)(mpa)≥400≥400≥450≥450≥500≥600≥700≥550≥250≥250≥310≥310≥320≥370≥420≥3793.1.1.2球墨铸铁常规金二者非政府球铁牌号qt400-18qt400-15qt450-10球化率≥80%≥80%≥80%基体组织铁素体f≥80%铁素体f≥75%铁素体f≥75%渗碳体≤3%≤3%≤3%qt450-12qt500-7qt600-3qt700-2qt550-6≥80%≥80%≥80%≥80%≥80%铁素体f≥75%铁素体f+珠光体p珠光体p+铁素体f珠光体p珠光体p+铁素体f≤3%≤3%≤3%≤3%≤3%3.1.1.3球墨铸铁化学成份球铁牌号qt400-18qt400-15qt450-10qt450-12qt500-7qt600-3qt700-2qt550-6化学成份c,%3.4-3.93.4-3.93.4-3.93.4-3.93.4-3.93.2-3.73.2-3.73.4-3.9si,%mn,%p,%2.6-3.12.6-3.12.6-3.12.6-3.12.6-3.02.4-2.82.3-2.62.6-3.0≤0.2≤0.2≤0.3≤0.3≤0.450.4-0.50.5-0.70.1-0.4s,%mg,%re,%cu,%0.2-0.40.2-0.4≤0.07≤0.030.025-0.060.02-0.04≤0.07≤0.030.025-0.060.02-0.04≤0.07≤0.030.025-0.060.02-0.04≤0.07≤0.030.025-0.060.02-0.04≤0.07≤0.030.025-0.060.02-0.04≤0.07≤0.030.025-0.060.02-0.04≤0.07≤0.030.025-0.060.02-0.04≤0.06≤0.030.025-0.060.02-0.043.1.2灰铸铁件材质检验标准:灰铸件材质环评标准应当合乎gb9439或en1561:1997灰铸铁件的标准,以机械性能(抗拉强度)和硬度为环评依据,金二者非政府及化学成份作为参照。
毛坯铸件检验规程

毛坯铸件检验规程一、检验目的:严格控制毛坯质量,杜绝不合格毛坯进入生产。
二、适用范围:适用于本公司进厂的毛坯质量检验。
三、检验内容:铸件内外表面质量、铸件材质、尺寸等。
四、检验方法:全检。
目测、测量。
五、检验依据:合同、生产指导书、材质化验单。
六、检验要求:1、铸件的内、外部表面质量检验。
表面粗糙度按“ GB6060. 1-85"标准验收,各种铸造件的内、外表面粗糙度不低于Ra25要求。
铸件内外表面上的飞边、粘砂、毛刺必须清理干净,铸件错箱部位要打磨平整、光洁。
铸件要求表面不允许有明显的气孔、砂眼、夹渣、凹凸、铸肉、重皮、平面变形等现象,错箱度不得超过1.5mm2、清理状态:铸件内、外表面上的粘砂和铸刺必须清理干净,铸件错箱部位要打磨平整、光洁。
3、尺寸检测:各部位尺寸、壁厚必须按我公司给定的图纸数据制作。
铸造孔径椭圆度不得超过1. 5mm若出现加工不起来的现象则视为废品。
4、重量检验:根据我公司模型推算出的铸件重量,经双方确认之后,按件数计算重量。
5、铸件材质检验:铸件的材质必须按合同给定的材质牌号生产,批量送检时必须持铸造单位《铸件材质报告单》和合同,并对上述报告的真实性负责。
公司不定期或按批量对铸造厂家做材质抽检化验,若化验材质不合格。
一切损失由铸造厂家承担。
6、铸件不允许用捶击、堵塞、浸渍等方法消除渗漏缺陷,更不允许用焊接的方法对铸件的缺陷进行焊补。
7、铸件的硬度适中,易于切削加工,铸件的铸字必须按照合同规定铸造。
如果铸件的铸字出现错误、不清晰等现象则视为不合格品处理。
&铸件在加工过程中出现气孔、夹渣、材料硬度过大等不良缺陷、加工尺寸不足导致加工不起来的情况,作为废品处理。
七、检验步骤:1、供应商登记进厂后,通知有关外协人员。
并提供以下资料:《生产指导书》号;釆购合同;材质单。
有关外协人员填写到货检验报告交至质检科进行入厂检验,相关外协人员必须在场。
2、质检人员进行入库检验时,必须按照检验要求进行检验。
QT450-10铸造毛坯件检验规范

1、目的为了规范公司对铸造件质量的检验。
2、适用范围适用于公司内所有球墨铸铁材质的产品。
3、引用标准GB /T5612-2008 铸铁牌号表示法GB/T1348-1988 球墨铸铁件GB 231-84 金属布氏硬度试验法GB/T9441-2009 球墨铸铁金相检验GB/T6414-1999 铸件尺寸公差与机械加工余量GB 6060.1-85 表面粗糙度比较样块铸造表面4、验收标准4.1 铸件材质检验标准:4.1.1 球墨铸件材质验收标准应符合GB1348-1988 球墨铸铁的标准,以机械性能(抗拉强度、延伸率)、金相组织为验收依据,硬度及化学成分做为参考。
4.1.1.3 壳体毛坯件的球墨铸铁材质正火后其珠光体(正火索氏体)组织等级在3级以上。
4.1.2 材质检验取样规范4.1.2.1机械性能检查:机械性能测试的试块,每班次每种牌号至少浇注三根,若铸件进行热处理,必须连同试块一同进行热处理。
二根用于生产厂测试性能(第一根合格则该批次合格,余下试块(留有生产日期、包次标识)留存。
若第一根试块不合格,测试剩余二根,若第二根不合格则该批次产品全部报废,若第二根合格,应加试第三根,合格则判定该炉产品合格,若第三根不合格则该批次产品全部报废)。
材质检验报告(原档)保存期为5年。
4.1.2.2金相组织检查:球铁铸件从每包铁水的最后一型附铸金相试块或铸件本体进行金相检验,依次往前直到合格(或本包铁水所浇铸件检验完)为止。
附铸试块应能代表本体。
若试块不好,应对铸件本体破件进行检验。
若金相检验由问题,加倍抽查。
金相本体试块应按天分类以月为单位保存,保存期为6个月,检验报告保存期5年。
球化等级要求在3级以上,石墨大小要求为5~7级。
4.1.2.3化学成分检查:每天必须分析每炉铁水(炉前)及至少两炉铸件(炉后)的化学成分。
炉前主要化验C、Si和S,炉后所有元素全部化验。
每天第一炉溶清后必须检测C、Si、Mn、P和S,之后C、Si每炉化验检测。
铸造毛坯检验标准
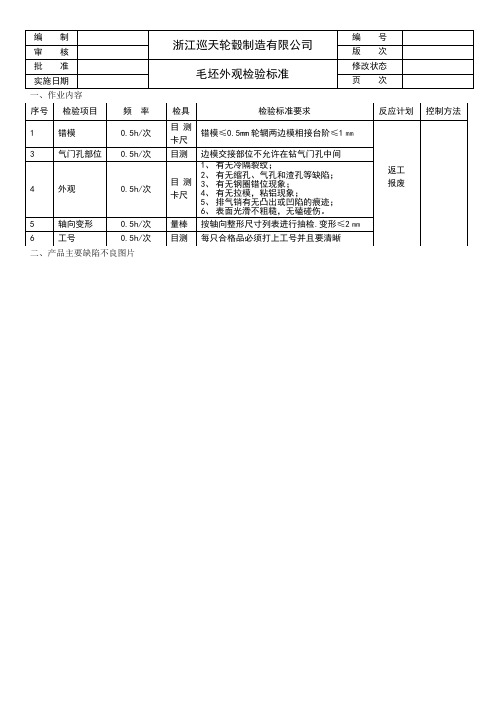
浙江巡天轮毂制造有限公司
编号
审核
版次
批准
毛坯外观检验标准
修改状态
实施日期
页次
序号
检验项目
频率
检具
检验标准要求
反应计划
控制方法
1
错模
0.5h/次
目测卡尺
错模≤0.5mm轮辋两边模相接台阶≤1㎜
返工
报废
3
气门孔部位
0.5h/次
目测
边模交接部位不允许在钻气门孔中间
4
外观
0.5h/次
目测卡尺
1、有无冷隔裂纹;
2、有无缩孔、气孔和渣孔等缺陷;
3、有无钢圈错位现象;
4、有无拉模,粘铝现象;
5、排气销有无凸出或凹陷的痕迹;
6、表面光滑不粗糙,无磕碰伤。
5
轴向变形
0.5h/次
量棒
按轴向整形尺寸列表进行抽检.变形≤2㎜
6
工号
0.5h/次
目测
每只合格品必须打上工号并且要清晰
一Hale Waihona Puke 作业内容二、产品主要缺陷不良图片
- 1、下载文档前请自行甄别文档内容的完整性,平台不提供额外的编辑、内容补充、找答案等附加服务。
- 2、"仅部分预览"的文档,不可在线预览部分如存在完整性等问题,可反馈申请退款(可完整预览的文档不适用该条件!)。
- 3、如文档侵犯您的权益,请联系客服反馈,我们会尽快为您处理(人工客服工作时间:9:00-18:30)。
1、目的
为了规范公司对铸造件质量的检验。
2、适用范围
适用于公司内所有球墨铸铁材质的产品
3、引用标准
GB /T5612-2008
GB/T1348-1988 铸铁牌号表示法球墨铸铁件
GB 231-84
GB/T9441-2009 GB/T6414-1999 金属布氏硬度试验法
球墨铸铁金相检验
铸件尺寸公差与机械加工余量
GB 表面粗糙度比较样块铸造表面
4、验收标准
铸件材质检验标准:
球墨铸件材质验收标准应符合GB1348-1988球墨铸铁的标准,以机械性能(抗拉强度、延伸率)、金相组织为验收依据,硬度及化学成分做为参考。
壳体毛坯件的球墨铸铁材质正火后其珠光体(正火索氏体)组织等级在3级以上。
材质检验取样规范
机械性能检查:机械性能测试的试块,每班次每种牌号至少浇注三根,若铸件进行热处理, 必须连同试块一同进行热处理。
二根用于生产厂测试性能(第一根合格则该批次合格, 余下试块(留有生产日期、包次标识)留存。
若第一根试块不合格,测试剩余二根,
若第二根不合格则该批次产品全部报废,若第二根合格,应加试第三根,合格则判定该炉产品合
格,若第三根不合格则该批次产品全部报废)。
材质检验报告(原档)保存期为5年。
金相组织检查:球铁铸件从每包铁水的最后一型附铸金相试块或铸件本体进行金相检验,依次往前直到合格(或本包铁水所浇铸件检验完)为止。
附铸试块应能代表本体。
若试块不好,应对铸件本体破件进行检验。
若金相检验由问题,加倍抽查。
金相本体试块应按天分类以月为单位保存,保存期为6个月,检验报告保存期5年。
球化等级要求在3级以上,石墨大小要求为5〜7级。
化学成分检查:每天必须分析每炉铁水(炉前)及至少两炉铸件(炉后)的化学成分。
炉前主要化验C、Si和S,炉后所有元素全部化验。
每天第一炉溶清后必须检测C、Si、Mn P和S,之后C、Si每炉化验检测。
化学成分记录要求齐全,记录表保存期5年。
硬度试验检查:布氏硬度试验应按GB231-84金属布氏硬度试验法的规定进行,硬度试验可在铸件试块或铸件本体上的一个部位或几个部位上进行。
铸件尺寸检验标准:
铸件外形及尺寸应符合我公司提供的图纸、合同/订单的要求。
铸件尺寸的未注公差采用GB/T 6414-1999标准的9级公差检验,公差值为土1/2 CT9级。
如表三所示。
表三:
铸件外观质量
铸字、标识:铸件上所要求的铸字、标识必须完整、清晰、正确,符合图纸要求。
错箱值:铸件最大错箱值不超过。
浇冒口、飞边残留高度:铸件上浇冒口、披缝等要清理干净,最大残留高度不超过。
表面粗糙度:铸件表面应光滑、平整,表面有粘砂、氧化皮、锈蚀等应清理干净,表面粗糙
度应按GB 《表面粗糙度比较样块铸造表面》的规定,表面粗糙度不超过Ra 50。
铸件表面缺陷生产交货的铸件表面质量应进行100%目测检验。
铸件上不允许存在影响性能的缺陷(裂纹、冷隔、缩孔、夹渣、浇不足、缩孔等)存在。
铸件的非加工表面不允许有直径超过1mm深度超过的单孔洞存在,但每平方厘米面积范围内允许直径小于1mm深度小于的孔不多于三处,相邻缺陷间隔在10mm以上。
但不允许在铸件壁厚的相应面上出现,不允许成片的孔眼类缺陷:
铸件加工面允许存在加工时可以去除的缺陷,一般控制在不超过加工余量的2/3 尺寸。
铸件非加工表面每棱边上的磕碰砸伤不得多于2处,并且每处面积不得大于Immxlmm 铸件柄部在折弯的R角处不允许有孔眼类缺陷。
5、铸件表面防护处理
铸件表面的锈蚀、粘砂、氧化皮等应通过抛丸处理干净。
对铸件有特殊防腐处理要求的,应按指定的要求(喷涂、防锈油或防锈漆)进行表面处理,表面处理后颜色应一致且符合要求。
涂层均匀表面光滑,没有磕碰、划伤、堆集和气泡等明显缺陷。
表面洁净,无污物粘连。
编制:审核:批准:。