半金属汽车制动衬片的摩擦性能
进口汽车用制动器衬片摩擦性能检测与产品不合格原因分析

进口汽车用制动器衬片摩擦性能检测与产品不合格原因分析作者:杨海华周崎李浩来源:《时代汽车》2024年第02期摘要:隨着国家经济的快速发展和人民对高质量、安全性的生活方向发展,而进口汽车在这一需求下逐年呈上升趋势,其中进口汽车用制动器衬片是汽车制动系统中最关键的安全零件,对制动效果起关键性作用,本文采用取样法对汽车盘式制动器衬片的摩擦性能进行测定和分析,并针对进口汽车用制动器衬片摩擦性能检测不合格原因分析。
关键词:汽车用制动器衬片摩擦性能原因分析1 前言进入21世纪,我国汽车用制动器衬片行业规模随着汽车工业的发展而稳步增长,国内市场上销售的中高档品牌汽车的制动器衬片主要从国外进口。
汽车用制动器衬片一般由钢板粘接隔热层和摩擦块组成,其中摩擦块是由摩擦材料、粘合剂组成,在查车过程中被羁押在刹车片或刹车鼓上产生摩擦,从而达到制动的目的。
一套良好有效率的制动系统必须能提供稳定、足够、可控制的制动力,并且具有良好的液压传递及散热能力,以确保驾驶人从制动踏板所施加的力能充分有效地传到制动系统的总泵以及各分泵,避免高热所导致的液压失效及刹车性能衰退。
我国现行的制动器衬片标准式GB5763-2018[1]《汽车用制动器衬片》该标准主要检测项目有:外观质量、尺寸公差、摩擦性能、剪切强度、冲击强度、热膨胀率、压缩应变和标准包装,其中,摩擦性能和剪切强度为强制性检测项目,其余为推荐性检测项目。
盘式制动器衬片的摩擦性能则是按照GB/T 34007-2017[3]中规定的方法进行检测。
对于常见的M1、M2、N1、O1、O2类车辆[2]盘式制动器衬片摩擦性能检测,在GB/T 34007-2017《道路车辆制动器衬片摩擦材料摩擦性能拖曳试验方法》中有原样法和取样法2种检测方法,因制动器衬片厂家和汽车整车厂商产品单一,均采用原样法进行摩擦性能检测,并在产品上标注设定摩擦系数,而第三方检测机构因制动器衬片产品繁多,而且每种型号必须配置和制动器衬片同型号相匹配卡钳和制动盘才能进行检测,为方便检测和节省检测成本,所以大多采用取样法进行检测,有研究表明,取样法和原样法检测结果并无显著差异,可以相互替代进行检测和评判[4]。
汽车制动摩擦片结构与基础常识

汽车制动摩擦片结构与基础常识一、结构1.摩擦材料摩擦材料是汽车制动摩擦片的关键组成部分,其质量和性能直接影响到制动效果和寿命。
常见的摩擦材料有有机摩擦材料、无机摩擦材料和半金属摩擦材料。
有机摩擦材料一般由纤维素、稳定剂、热稳定剂和润滑剂等组成,具有摩擦系数大、稳定性好和价格低廉的特点,但制动性能会随着温度的升高而下降。
无机摩擦材料主要由金属氧化物和高熔点金属等组成,具有耐高温性能好的特点,但摩擦系数较低。
半金属摩擦材料则是有机和无机摩擦材料的综合体,由一定比例的有机物和无机物组成,具有较高的摩擦效果和耐高温性能。
2.支撑座支撑座是指摩擦片与制动器活塞之间的连接件,一般由金属材料制成,用于支撑和固定摩擦材料。
3.螺栓螺栓用于固定摩擦片在制动器修处,一般由高强度合金材料制成。
螺栓需要具备一定的耐磨损性和抗蠕变性能,以确保摩擦片能够牢固地固定在制动器修处。
二、基础常识了解一些基础常识有助于我们更好地维护和管理汽车制动摩擦片。
1.使用寿命摩擦片的使用寿命受多种因素的影响,包括车辆的使用情况、行驶速度、路况等。
一般来说,摩擦片的使用寿命约为2-3万公里左右,但需要根据实际情况做出调整。
当摩擦片磨损到极限厚度时,需要及时更换,以免影响制动效果。
2.保养和维护定期对摩擦片进行保养和维护可以延长其使用寿命。
保养包括对制动系统的清洁和调整,在行驶过程中注意制动轻重,避免频繁急刹车。
另外,及时更换磨损严重的摩擦片也是保养的重要措施。
3.不良磨损不良磨损是指摩擦片由于使用不当或其他原因导致的异常磨损。
常见的不良磨损类型有脚印磨损、倒角磨损、凹槽磨损等。
不良磨损会降低制动效果,甚至导致制动失灵,因此及时发现和解决不良磨损问题是非常重要的。
4.制动效果制动效果是衡量摩擦片性能的重要指标之一、制动效果与摩擦系数、摩擦片质量和制动器状况等有关。
一般来说,摩擦系数越大,制动效果越好。
但过高的摩擦系数也会导致制动器过热和制动力过大,影响行驶的平稳性。
摩擦片摩擦系数等级

摩擦系数等级刹车片基本知识一、摩擦系数等级:1、摩擦系数:表示刹车片摩擦效能的参数叫摩擦系数,摩擦系数大概意思就是这个片有多“粘”越粘的片阻力越大制动越灵敏,但舒适性和耐热性越差,轻踩就会点头狠踩很快就烧了。
高温刹车片是指在更高温度下能保持摩擦系数,并不一定高温刹车片摩擦系数就大。
刹车片的等级用两个英文字母表示,第一个是在0~600(315.5摄氏度)华氏度间取4个点测量摩擦系数,如果都能在0.5~0.45之间,那么片的低温等级就是F。
然后在600~1112(600度)华氏度间取10个点测摩擦系数,如果也能在0.35~0.45之间高温等级也是F,那么这个片就是FF级别的片。
常说的陶瓷刹车片的摩擦系数级别就是这种FF级的。
常见的E表示摩擦系数是0.25~0.35,F上面说了,G表示在0.45~0.55之间。
1112华氏度大概合600摄氏度。
高温允许在更高温度下保持原来的摩擦系数,所以高温片并不一定就灵敏,只是很多高温片也通过增加摩擦系数来帮助达到更高温度。
我们常说的普通半金属的刹车片就是这种EF级的。
卧车刹车片大部分都能做到FF,再高的摩擦系数片的金属含量会大,踩刹车会响,舒适度下降。
轴重大的车会通过用大直径的刹车盘、用通风盘、用划线盘等方法来提高制动力和减缓热衰减。
EE级:0.25-0.35适用于欧美车系,刹车片比较大,摩擦系数比较低;FF级:0.35-0.45 国际标准摩擦系数GG级:0.45-0.55适用于欧洲车型HH级:0.55-0.65 赛车专用制动的方式是靠摩擦把车辆行驶的动能转化成热能散掉,散热越快减速就越快。
而热量的增加和散热之间也是平衡,如果热量增加太多超过制动部分能承受的极限让零件变化就会失去制动能力,这种情况主要表现在制动系统产生热衰减,热衰减主要是超过刹车片耐受温度使刹车片表面烧蚀造成。
2、热聚集和热衰减的解释:热聚集:由于摩擦产生热量,当热量不能被100%散掉就会产生累积聚集,热聚集导致温度升高。
汽车制动器衬片摩擦性能测试初探
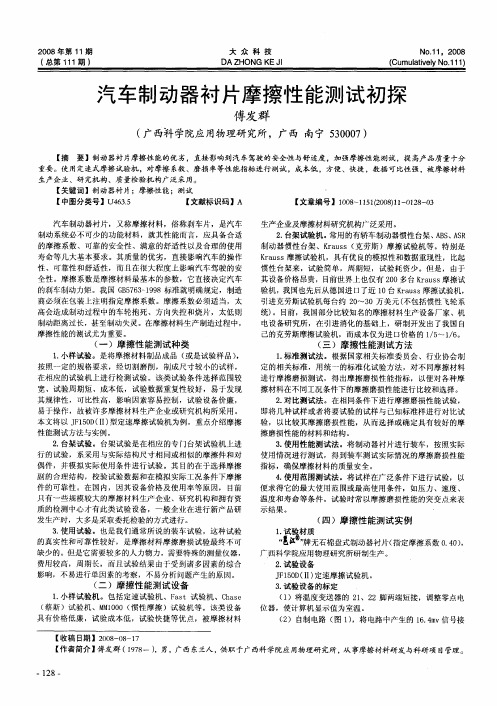
擦材料在不同工况条件下的摩擦磨损性 能进行 比较和选择 。
2 对 比测试法 。在相 同条件下进行摩擦磨损性 能试验 , .
引进克劳斯试验机每 台约 2  ̄3 0 0万美元 ( 不包括惯性飞轮系 统) 。目前,我 国部分 比较 知名 的摩擦材料生产设备厂家 、机 电设备研 究所 ,在 引进 消化 的基础上 ,研 制开发出了我国 自 己的克劳斯摩擦试验机 ,而成本仅为进 口价格 的 15 / 。 / ~l6
寿命等几大基本要求 。其质量 的优劣 ,直接影 响汽车 的操 作 性 、可靠性和舒适性 ,而且在很大程度上影 响汽车驾驶 的安
生产企业及摩擦材料研 究机构广泛采用。 2 台架试验机 。 . 常用 的有轿车制动器惯性台架 、 B 、 S AS AR 制动器惯性 台架、K a s 克劳斯 )摩擦试验机等 。特 别是 r u s( Ka s r u s摩擦试验机,具有优 良的模拟性和数据重现性, 比起 惯性 台架来 ,试验简单 ,周 期短 ,试 验耗 资少。但 是,由于 其设备价格 昂贵,目前世界上也仅有 2 0多 台 K a s 0 r u s摩擦试 验机 ,我国也先后从德国进 口了近 l 0台 K a s 摩擦试验机, rus
偶件,并模 拟实际使 用条 件进 行试验。其 目的在于选择摩擦 副的合理 结构,校验 试验 数据和 在模拟实际工况条件下摩擦
件的可 靠性 。在 国内,因其设备价 格及 使用率等原因 ,目前 只 有 一 些规 模较 大 的摩 擦 材 料 生产 企业 、 研 究机 构和 拥 有 资 质 的检测 中心才有此类试验 设备,一般 企业 在进行新产品研 发生产时 ,大多是采取委托检验的方式进行 。 3 使用试验 。也 是我们通 常所 说的装车试验,这种试验 . 的真实性和 可靠性较好 ,是摩擦材料摩擦磨损试验最 终不可 缺少 的。但是它需要较 多的人力物力 ,需要特殊的测量仪器 ,
不同温度下半金属摩擦材料的摩擦磨损性能研究

不同温度下半金属摩擦材料的摩擦磨损性能研究
近年来,半金属摩擦材料的应用越来越广泛。
针对不同温度下半金属摩擦材料的摩擦磨损性能进行研究,对于提高半金属摩擦材料的使用寿命和使用效果等方面具有重要的意义。
在常温下,半金属摩擦材料具有较好的良好的摩擦性能,摩擦系数相对较低且稳定,摩擦副的磨损量也相对较小。
而在高温下,半金属摩擦材料的磨损量明显加大,主要是因为热能的作用下摩擦副表面硬度的降低,使得材料表面更容易受到磨损。
此外,在高温下,摩擦系数也会显著增加,其原因是随着温度的升高,润滑膜形成能力会减弱,从而使得摩擦副之间产生了更多的直接接触。
在低温下,半金属摩擦材料的摩擦磨损性能也受到明显的影响。
低温下,润滑膜的形成速度受到限制,从而导致磨损增加,甚至在极端低温下会使得润滑膜的形成几乎不可能。
因此,针对不同温度下半金属摩擦材料的摩擦磨损性能进行研究是非常必要的。
研究可以通过改变材料的组成、结构和制备工艺等因素来改善材料的特性,从而达到更好的摩擦磨损性能,为广泛应用半金属摩擦材料提供更优质、更稳定的材料,并实现材料的可持续使用。
汽车用制动器衬片摩擦性能试验方法及质量控制

能的试验方法及试验 中的质量控制进行了探讨 。
2 俭 验 设 备 况 甄 述
摩擦性能试验一般是在定速摩擦试验机 上进 行的 , 目前 我 国生产该设备的企业主要有 :国家非金属矿 制品质量监督检验 中心 ( 成 阳新 益摩擦 密封设备有 限公 司 ) 、 吉林大学 机 电设 备研 究所( 吉林省 旺达机械有 限公司 ) 等单位 , 我们使用 的是成 阳新 益摩擦 密封设 备有 限公司 生产的 X D— MS M改 进型定 速摩擦 试 验机 , 该试验机主要 南三部分组 成, 即主机 、 强电控制柜 、 计 算机
验后的状态 , 将其 记录在 原始记 录中。
4 试 验 过 程 中 的 质 量 控 制
车太生硬 . 造成制动不平稳 ; 指定摩擦系数的 允许偏差这个 参数 数值 小 , 代表 了产 品在使用过 程中随着温度的变化性能稳定 , 摩 擦 系数的数值变化小 , 能始终 保持 良好的制动性能 ; 磨 损率小 则
机 的提 示 输 入 试 片 的初 始 厚 度 等 即 可 开 始 试验 , 程 序 会 按 照 输 入
往砝码托盘上加标 准砝码 , 每加一 个砝码 , 记 录一个计算 机上读
出的摩擦 力数值 , 此时 的数 值应为 ( 1 9 . 6 + 9 8 ) N左右 , 以此 类推 . 直至将 四个 标准 砝码 加 完 ,此 时计 算机 上摩 擦 力的数 值应 为 ( 1 9 . 6 + 9 8 + 9 8 + 9 8 + 9 8 ) N左 右 , 即4 1 1 . 6 N左右 , 将计 算机读 } } J 的数 值与计算值进行 比较 ,当差值不超 过 ±1 5 N时核查结果 可 以接 受, 如果结 果超 出这 个数值 , 则需 要对设 备进行调 整 , 之后 重新 对设备进行校准 。正压 力的核查方法 : ( 1 ) 抬起试验 机杠 杆 . 将正 压力测试装置 的压力传感器放在加载轴 下面 , 打 开 显示器 电源 ,
半金属与陶瓷对比报告

陶瓷摩擦片与半金属摩擦片性能对比报告半金属摩擦材料是20世纪70年代发展起来的一种新型汽车制动材料。
其配方中通常含有20%~45%左右的铁质金属组分,通过加入这些组分的材料热稳定性好、导热性好、克服了石棉摩擦材料在高温下热衰退严重、摩擦表面易开裂等缺点,目前国内应用最广泛的依然是半金属摩擦材料,但是对于国外还是国内而言,半金属摩擦材料仍然存在着很多缺点,例如,钢纤维易生锈,锈蚀后易粘着对偶并且对其有较大的损伤,使摩擦材料强度降低、磨损加剧,同时钢纤维的硬度高,与对偶的硬度差过大,易损伤对偶,加速对偶磨损。
这种种问题就像“顽疾”一般困扰着诸多厂家,一直得不到有效解决。
为解决半金属摩擦材料的诸多问题,陶瓷刹车片作为新型的配方呈现在人们眼前。
陶瓷刹车片是从金属陶瓷而非非金属陶瓷的原理出发,刹车片由于高速大力制动时,在摩擦表面产生高温。
在此高温下,制动片表面会发生金属陶瓷烧结类似反应,使刹车片在此温度下有良好的稳定性。
而半金属刹车片在此温度下不会产生烧结反应,由于表面温度急剧升高会使表面物质熔化甚至产生气垫,这就有造成连续刹车后刹车性能急剧降低或者刹车全失的情况。
因为钢纤维会锈蚀,产生噪音和粉尘,因此不能满足陶瓷型配方的要求,因此,陶瓷刹车片是由陶瓷纤维、不含铁的填料物质、胶粘剂和少量的金属组成的,包括矿物纤维、芳纶纤维和陶瓷纤维,比其他的刹车片相比,陶瓷型刹车片更清洁安静,并且在提供卓越刹车性能的同时,不磨耗对偶件。
陶瓷刹车片相比其他类型的刹车片有如下的优点:1)陶瓷刹车片与半金属刹车片最大差别是没有金属。
半金属刹车片中金属是主要产生摩擦力的材料,制动力大,但是磨损大,而且易出现噪音。
安装陶瓷刹车片后,在正常行驶中,不会产生异常尖叫。
因为陶瓷刹车片中不含金属成份,所以就避免了类似半金属刹车片与对偶件(即刹车片与刹车盘)相互磨擦的金属尖叫声。
2)稳定的摩擦系数。
摩擦系数是任何摩擦材料最重要的性能指标,关系刹车片制动能力的好坏。
制动器衬片检查方法
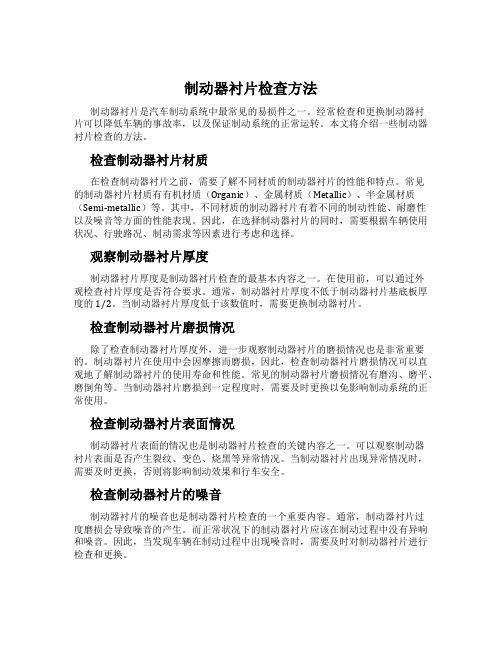
制动器衬片检查方法制动器衬片是汽车制动系统中最常见的易损件之一。
经常检查和更换制动器衬片可以降低车辆的事故率,以及保证制动系统的正常运转。
本文将介绍一些制动器衬片检查的方法。
检查制动器衬片材质在检查制动器衬片之前,需要了解不同材质的制动器衬片的性能和特点。
常见的制动器衬片材质有有机材质(Organic)、金属材质(Metallic)、半金属材质(Semi-metallic)等。
其中,不同材质的制动器衬片有着不同的制动性能、耐磨性以及噪音等方面的性能表现。
因此,在选择制动器衬片的同时,需要根据车辆使用状况、行驶路况、制动需求等因素进行考虑和选择。
观察制动器衬片厚度制动器衬片厚度是制动器衬片检查的最基本内容之一。
在使用前,可以通过外观检查衬片厚度是否符合要求。
通常,制动器衬片厚度不低于制动器衬片基底板厚度的1/2。
当制动器衬片厚度低于该数值时,需要更换制动器衬片。
检查制动器衬片磨损情况除了检查制动器衬片厚度外,进一步观察制动器衬片的磨损情况也是非常重要的。
制动器衬片在使用中会因摩擦而磨损,因此,检查制动器衬片磨损情况可以直观地了解制动器衬片的使用寿命和性能。
常见的制动器衬片磨损情况有磨沟、磨平、磨倒角等。
当制动器衬片磨损到一定程度时,需要及时更换以免影响制动系统的正常使用。
检查制动器衬片表面情况制动器衬片表面的情况也是制动器衬片检查的关键内容之一。
可以观察制动器衬片表面是否产生裂纹、变色、烧黑等异常情况。
当制动器衬片出现异常情况时,需要及时更换,否则将影响制动效果和行车安全。
检查制动器衬片的噪音制动器衬片的噪音也是制动器衬片检查的一个重要内容。
通常,制动器衬片过度磨损会导致噪音的产生。
而正常状况下的制动器衬片应该在制动过程中没有异响和噪音。
因此,当发现车辆在制动过程中出现噪音时,需要及时对制动器衬片进行检查和更换。
总结制动器衬片是车辆行驶安全的关键部件之一。
因此,定期检查和更换制动器衬片对于车辆使用来说非常重要。
汽车制动器衬片摩擦性能评价 小样台架试验方法-最新国标

汽车制动器衬片摩擦性能评价小样台架试验方法1范围本标准规定了汽车制动器衬片(以下简称“衬片”)摩擦磨损性能的小样台架试验程序及摩擦系数的级别和标记。
本文件适用于汽车用盘式制动器衬片和汽车用鼓式制动器衬片。
本文件不适用于驻车制动器制动衬片。
2规范性引用文件下列文件中的内容通过文中的规范性引用而构成本文件必不可少的条款。
其中,注日期的引用文件,仅该日期对应的版本适用于本文件;不注日期的引用文件,其最新版本(包括所有的修改单)适用于本文件。
GB/T5620道路车辆汽车和挂车制动名词术语及其定义GB5763汽车用制动器衬片3术语和定义GB/T5620和GB5763界定的术语和定义适用于本文件。
4试验设备4.1试验设备功能试验设备为如图1和图2所示的摩擦材料小样台架试验机。
试验机应具备以下功能:a)测量制动鼓的温度;b)加热制动鼓;c)控制制动鼓加热速率;d)仅从制动鼓的背面冷却制动鼓;e)控制制动鼓降温速率;f)测量摩擦力;g)测量制动鼓的转速。
4.2温度测量4.2.1温度测量装置应由焊接的热电偶、合金金属环、银石墨碳刷、具有高输入阻抗的记录仪组成。
4.2.2温度测量系统的精度为满量程的±2%。
4.3摩擦力测量摩擦力测量系统的精度为满量程的±2%,试验载荷的偏差为±2%。
4.4制动鼓4.4.1制动鼓速度测量系统的精度为满量程的±2%。
4.4.2制动鼓升温应按如下方式进行调节,并在试验过程中保持此状态:制动鼓转速417r/min,用冷却空气将制动鼓从149℃冷却至93℃,然后关闭冷却空气,自然冷却至82℃时,打开加热器并开始计时,加热10min。
制动鼓温度应在10min升到221℃±14℃。
4.4.3制动鼓降温应按如下方式进行调节,并在试验过程中保持此状态:制动鼓转速417r/min,用加热器将制动鼓加热至371℃,然后关闭加热器,开启冷却空气,降温至343℃时开始计时,冷却10 min。
不同温度下半金属摩擦材料的摩擦磨损性能研究
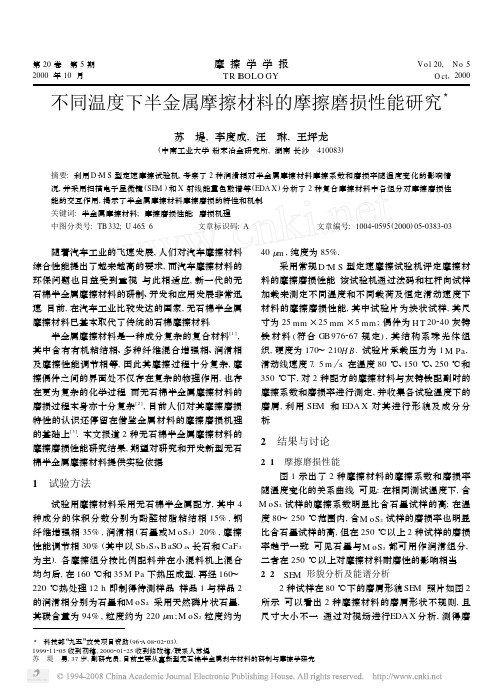
第20卷 第5期摩擦学学报V o l20, N o5 2000年10月TR I BOLO GY O ct,2000不同温度下半金属摩擦材料的摩擦磨损性能研究3苏 堤,李度成,汪 琳,王坪龙(中南工业大学粉末冶金研究所,湖南长沙 410083)摘要:利用D2M S型定速摩擦试验机,考察了2种润滑相对半金属摩擦材料摩擦系数和磨损率随温度变化的影响情况,并采用扫描电子显微镜(SE M)和X射线能量色散谱等(EDA X)分析了2种复合摩擦材料中各组分对摩擦磨损性能的交互作用,揭示了半金属摩擦材料摩擦磨损的特性和机制.关键词:半金属摩擦材料;摩擦磨损性能;磨损机理中图分类号:TB332;U465.6文章标识码:A文章编号:100420595(2000)0520383203 随着汽车工业的飞速发展,人们对汽车摩擦材料综合性能提出了越来越高的要求,而汽车摩擦材料的环保问题也日益受到重视.与此相适应,新一代的无石棉半金属摩擦材料的研制、开发和应用发展非常迅速.目前,在汽车工业比较发达的国家,无石棉半金属摩擦材料已基本取代了传统的石棉摩擦材料.半金属摩擦材料是一种成分复杂的复合材料[1],其中含有有机粘结相、多种纤维混合增强相、润滑相及摩擦性能调节相等,因此其摩擦过程十分复杂,摩擦偶件之间的界面处不仅存在复杂的物理作用,也存在更为复杂的化学过程.而无石棉半金属摩擦材料的磨损过程本身亦十分复杂[2],目前人们对其摩擦磨损特性的认识还停留在借鉴金属材料的摩擦磨损机理的基础上[3].本文报道2种无石棉半金属摩擦材料的摩擦磨损性能研究结果,期望对研究和开发新型无石棉半金属摩擦材料提供实验依据.1 试验方法试验用摩擦材料采用无石棉半金属配方,其中4种成分的体积分数分别为酚醛树脂粘结相15%,钢纤维增强相35%,润滑相(石墨或M oS2)20%,摩擦性能调节相30%(其中以Sb2S3、B aSO4、长石和CaF2为主).各摩擦组分按比例配料并在小混料机上混合均匀后,在160℃和35M Pa下热压成型,再经160~220℃热处理12h即制得待测样品.样品1与样品2的润滑相分别为石墨和M oS2.采用天然磷片状石墨,其碳含量为94%,粒度约为220Λm;M oS2粒度约为40Λm,纯度为85%.采用常规D2M S型定速摩擦试验机评定摩擦材料的摩擦磨损性能.该试验机通过法码和杠杆向试样加载来测定不同温度和不同载荷及恒定滑动速度下材料的摩擦磨损性能,其中试验片为块状试样,其尺寸为25mm×25mm×5mm;偶件为H T20240灰铸铁材料(符合GB976267规定),其结构系珠光体组织,硬度为170~210H B.试验片承载压力为1M Pa,滑动线速度7.5m s.在温度80℃、150℃、250℃和350℃下,对2种配方的摩擦材料与灰铸铁配副时的摩擦系数和磨损率进行测定,并收集各试验温度下的磨屑,利用SE M和EDA X对其进行形貌及成分分析.2 结果与讨论2.1 摩擦磨损性能图1示出了2种摩擦材料的摩擦系数和磨损率随温度变化的关系曲线.可见:在相同测试温度下,含M oS2试样的摩擦系数明显比含石墨试样的高;在温度80~250℃范围内,含M oS2试样的磨损率也明显比含石墨试样的高,但在250℃以上2种试样的磨损率趋于一致.可见石墨与M oS2都可用作润滑组分,二者在250℃以上对摩擦材料耐磨性的影响相当. 2.2 SE M形貌分析及能谱分析2种试样在80℃下的磨屑形貌SE M照片如图2所示.可以看出2种摩擦材料的磨屑形状不规则,且尺寸大小不一.通过对视场进行EDA X分析,测得磨3科技部“九五”攻关项目资助(962A08202203).1999211205收到初稿,2000201225收到修改稿 联系人苏堤.苏 堤 男,37岁,副研究员,目前主要从事新型无石棉半金属刹车材料的研制与摩擦学研究.(a )F ricti on coefficient (b )W ear rateF ig 1 V ariati on s inthe fricti on coefficien t and w ear rate w ith temperatu re图1 摩擦系数和磨损率随温度变化的关系曲线屑中3种主要元素的原子浓度比随温度变化的情况 (a )Graphite(b )M oS 2F ig 2 SE M mo rpho logy of the w ear deb ris of tw o samp les at 80℃图2 两种试样在80℃下的磨屑形貌SE M 照片如图3所示.一般认为,采用EDA X 测得的磨屑中的主要元素的原子浓度可间接地反映该元素对应的化合物材料在磨屑中的含量,即相应的复合相组分从摩擦材料中磨损脱落的数量.试验中B a 元素基本检测不到,因此可以认为摩擦材料中的B aSO 4组分的磨损质量损失很小.从图3(a )可见,含M oS 2的试样在各温度下的磨屑中的Ca 含量,即CaF 2组分的磨损质量基本相同;含石墨样品在80℃和350℃下的磨(a )Ca elem ent(b )Sb elem ent(c )Fe elem en tF ig 3 V ariati on s in the atom ic concen trati on of Ca ,Sb ,and Fe in w ear deb ris w ith temperatu re图3 摩擦材料磨屑中典型元素的原子浓度随温度变化的关系曲线屑中的Ca 含量较高,而在250℃下Ca 含量最低.总体而言,2种试样的磨屑中的Ca 含量相差不大.从图3(b )可以看出,含M oS 2的试样的磨屑中Sb 的原子浓度随着温度升高略有降低;含石墨试样的磨屑在483摩 擦 学 学 报第20卷低温下的Sb 含量较低,而在高温下Sb 含量明显增加.我们推测,在低温摩擦过程中,含石墨试样中的Sb 2S 3组分与石墨组分发生了相互作用,从而使得摩擦材料中的Sb 2S 3组分的磨损损失较小;而M oS 2与Sb 2S 3之间的这种相互作用较弱,因而含M oS 2的摩擦材料中的Sb 2S 3组分的磨损损失较为显著.由于摩擦材料中的润滑组分与Sb 2S 3组分的相互作用随温度升高而减弱,因而2种试样经高温摩擦磨损试验后磨屑中Sb 2S 3组分含量趋于一致.从图3(c )可以看出,含石墨的试样在较低试验温度下的磨屑中的Fe 含量较高,随着试验温度的升高,磨屑中的Fe 含量逐渐降低;在本文的各个试验温度下,含石墨试样的磨屑中的Fe 含量比含M oS 2试样的高.这说明含石墨试样中的钢纤维在各个试验温度下的磨损比含M oS 2试样中的严重.以上试验结果之间的差异,表面看来归因于摩擦材料中石墨与M oS 2组分之间的差异.但从深层次来看,我们推测这种差异归因于摩擦材料中2种润滑组分与其他组分之间相互影响的差异.如图3(c )所示,含M oS 2试样在各个试验温度下的磨屑中的Fe 含量都比含石墨试样的低,且随温度的变化不大.与金属轴承材料中的M oS 2具有减摩抗磨作用相似,在摩擦材料中的M oS 2同样能够有效地防止金属材料表面之间的咬合,减轻金属偶件的磨损[4].而由于摩擦表面的瞬时高温,摩擦材料中的石墨极易对低碳钢纤维表面产生较强的渗碳作用,使钢纤维表面碳含量剧增,表面硬度增加和脆性增大,在摩擦过程中摩擦表面的钢纤维易破碎脱落并进而划伤偶件表面、或在正压力和剪切力作用下拔脱,从而使磨损加剧.而M oS 2对钢纤维不会产生渗碳作用,因而整体而言含M oS 2摩擦材料试样中的钢纤维的磨损比含石墨试样中的轻微.3 结论a . 摩擦材料中的润滑组分M oS 2和石墨与其他组分之间的相互作用存在差异,这使得含M oS 2和石墨润滑组分的2种摩擦材料的摩擦磨损行为明显不同.b . 在其它组分相同的条件下,含M oS 2润滑相的摩擦材料的耐磨性优于含石墨润滑相的摩擦材料,这是由于M oS 2对摩擦材料中的钢纤维无渗碳作用,因而不加剧钢纤维的脱落及其对偶件表面的损伤作用所致.c . 两种摩擦材料的磨屑元素组成主要为Fe 、Sb 和Ca 等.参考文献:[1] 徐仁泉,胡庆.冷压盘式刹车片摩擦磨损性能的研究[J ].摩擦学学报,1998,18(3):259~262.[2] 贾贤,周本濂,陈永潭,等.半金属摩擦材料与灰铸铁滑动摩擦表面层特性的分析研究[J ].摩擦学学报,1995,15(2):171~176.[3] K 2H 哈比希.材料的磨损与硬度[M ].严立译.北京:机械工业出版社,1987.[4] 王汝霖.润滑剂摩擦化学[M ].北京:中国石化出版社,1994.Fr iction and W ear Behav ior of Two Sem i -m etallic Fr iction M ater i alsSU D i ,L I D u 2cheng ,W AN G L in ,W AN G P ing 2long(P o w d er M eta llu rgy R esea rch Institu te ,Cen tra l S ou th U n iversity of T echnology ,Chang sha 410083,Ch ina )Abstract :T he fricti on and w ear behavi o r of tw o sem i 2m etallic fricti on m aterials con tain ing M oS 2o r grap h ite as the lub ricating p hase has been investigated on a D 2M S fricti on and w ear tester .T he m o rp ho logy and ele 2m en tal com po siti on s of the w ear deb ris have been exam ined by m ean s of scann ing electron m icro scop y and en 2ergy disp ersive sp ectrom etry ,resp ectively .T he w ear m echan is m of the fricti on m aterials is discu ssed by tak 2ing in to accoun t the in teracti on am ong the lub ricating p hase and the o ther com ponen ts.A s the resu lts ,M oS 2and grap h ite show difference in term s of the in teracti on w ith the o ther com ponen ts in the fricti on m aterials .T he fricti on m aterial con tain ing M oS 2show better w ear 2resistance than that con tain ing grap h ite .T h is is be 2cau se M oS 2as the lub ricating com ponen t does no t enhance p u lling ou t and w ear of the steel fiber in the fric 2ti on m aterial by w ay of carbu rizati on .T he w ear deb ris is m ain ly com po sed of Fe ,Ca ,and Sb .Key words :sem i 2m etallic fricti on m aterial ;fricti on and w ear behavi o r ;w ear m echan is m583第4期苏堤等: 不同温度下半金属摩擦材料的摩擦磨损性能研究。
道路车辆—制动衬片摩擦材料—摩擦性能缩比试验方法(编制说明)

T/XXX 10XX-201X《道路车辆—制动衬片摩擦材料—摩擦性能缩比试验方法》团体标准编制说明《缩比试验方法》标准起草组二0一八年十月道路车辆—制动衬片摩擦材料—摩擦性能缩比试验方法Road vehicles — Brake lining friction materials—Friction behavior scale test procedure标准编制说明1项目背景1.1 项目的来源:在标准的“引言”中,对缩比试验标准产生的背景做了说明。
1.1.1在摩擦材料产品开发和生产过程中,如何评价材料的摩擦性能,始终是一个探讨和争论的议题。
A.目前广泛采用总成试验的方法,但它存在诸多的影响因素,而且试验周期长,成本高。
本标准旨在提供一种只针对摩擦材料,又能模拟汽车行驶的实际工况的试验方法。
B.本标准将缩比原理应用于摩擦材料性能测试。
其中最为关键的是,将总成试验的工况条件,按照缩比原则进行缩小,以相同的减速制动方式,进行性能测试和评价;实现与总成试验的可比性。
C.现行的恒速拖磨试验方法(和质量标准),存在诸多弊端。
由于与实际驾驶工况、制动系统特性或汽车动力学特性没有相互关系;所拖磨方式测出的摩擦系数的含义不同于模拟实验(减速制动);事实证明,用恒速拖磨的方式对摩擦性能进行评价是不准确的。
D.推出摩擦材料缩比试验方法的目的,是要提出一种缩比惯性测功机的试验程序,它能够在较大变化范围的行驶速度、制动温度、制动压力或制动减速度等条件下,模拟汽车的制动过程,对材料的摩擦性能进行评价。
1.1.2本标准推出的缩比试验方法具有以下特点:A.等同采用国内外广泛应用的制动器总成试验程序,便于与全尺寸总成试验台的数据进行比较;B.由于采用相同的缩比制动器和对偶,缩比试验的测试结果可用于摩擦材料之间的相互比较;C.本试验方法用于测试材料的摩擦性能,应用于原料筛选,产品早期开发,过程质量控制和样件测试;D.与全尺寸总成试验相比,缩比试验有更高的效率,较低的测试成本;1.1.3这个标准所推出的试验方法具有创新性,也有针对现行摩擦材料质量标准中存在的弊端的意图。
半金属汽车制动衬片的摩擦性能
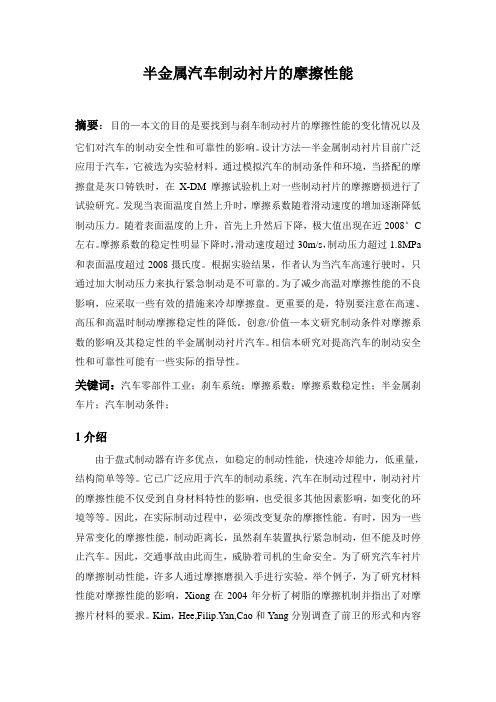
半金属汽车制动衬片的摩擦性能摘要:目的—本文的目的是要找到与刹车制动衬片的摩擦性能的变化情况以及它们对汽车的制动安全性和可靠性的影响。
设计方法—半金属制动衬片目前广泛应用于汽车,它被选为实验材料。
通过模拟汽车的制动条件和环境,当搭配的摩擦盘是灰口铸铁时,在X-DM摩擦试验机上对一些制动衬片的摩擦磨损进行了试验研究。
发现当表面温度自然上升时,摩擦系数随着滑动速度的增加逐渐降低制动压力。
随着表面温度的上升,首先上升然后下降,极大值出现在近2008°C 左右。
摩擦系数的稳定性明显下降时,滑动速度超过30m/s,制动压力超过1.8MPa 和表面温度超过2008摄氏度。
根据实验结果,作者认为当汽车高速行驶时,只通过加大制动压力来执行紧急制动是不可靠的。
为了减少高温对摩擦性能的不良影响,应采取一些有效的措施来冷却摩擦盘。
更重要的是,特别要注意在高速、高压和高温时制动摩擦稳定性的降低。
创意/价值—本文研究制动条件对摩擦系数的影响及其稳定性的半金属制动衬片汽车。
相信本研究对提高汽车的制动安全性和可靠性可能有一些实际的指导性。
关键词:汽车零部件工业;刹车系统;摩擦系数;摩擦系数稳定性;半金属刹车片;汽车制动条件;1介绍由于盘式制动器有许多优点,如稳定的制动性能,快速冷却能力,低重量,结构简单等等。
它已广泛应用于汽车的制动系统。
汽车在制动过程中,制动衬片的摩擦性能不仅受到自身材料特性的影响,也受很多其他因素影响,如变化的环境等等。
因此,在实际制动过程中,必须改变复杂的摩擦性能。
有时,因为一些异常变化的摩擦性能,制动距离长,虽然刹车装置执行紧急制动,但不能及时停止汽车。
因此,交通事故由此而生,威胁着司机的生命安全。
为了研究汽车衬片的摩擦制动性能,许多人通过摩擦磨损入手进行实验。
举个例子,为了研究材料性能对摩擦性能的影响,Xiong在2004年分析了树脂的摩擦机制并指出了对摩擦片材料的要求。
Kim,Hee,Filip.Yan,Cao和Yang分别调查了前卫的形式和内容在刹车片的摩擦性能上的影响。
汽车半金属刹车材料的热能转换功能及其磨损问题分析

不同温度下半金属摩擦材料的摩擦磨损性能研究

不同温度下半金属摩擦材料的摩擦磨损性能研究摩擦磨损是半金属摩擦材料性能的重要指标之一,影响着摩擦副的工作性能与寿命。
本文通过对不同温度下半金属摩擦材料的摩擦磨损性能进行实验研究,分析了其磨损规律与磨损机制,为材料的应用提供了参考依据。
实验以球盘式摩擦试验机为基础,选取Fe-Cr-C系材料作为半金属摩擦材料,球形试样为硬质钢球,盘形试样为不锈钢盘,试样尺寸均为Φ10 mm*6 mm,在不同温度下进行磨损实验。
实验温度分别为室温、200℃、400℃、600℃和800℃,磨损载荷为20 N,滑动速度为1 m/s,磨损时间为20 min。
实验后对磨损试样进行形貌观察和成分分析,得到摩擦磨损率、磨损系数等参数,进一步分析磨损规律与机制。
实验结果表明,随着温度的升高,半金属摩擦材料的摩擦磨损率呈现先升高后降低的趋势。
在室温和200℃时,磨损率较小,摩擦磨损主要为表面疲劳和氧化磨损;随温度升高,磨损率逐渐提高,摩擦磨损机制转变为热疲劳和微结构变化磨损,磨损表面出现较大的裂纹和疏松区域;在800℃时,磨损率开始下降,摩擦磨损主要为氧化磨损和表面液化,试样表面出现涂层和玻璃化区域,且疲劳破坏显著减少。
综上所述,不同温度下半金属摩擦材料的磨损规律和机制主要受到温度、表面氧化等因素的影响。
在实际应用中,需要根据工作条件和材料特性选择适当的温度和材料,以达到最佳的摩擦磨损性能。
进一步分析发现,半金属摩擦材料在室温和200℃时,磨损率较小的原因是,相对较低的温度使得摩擦副处于相对稳定的摩擦状态,磨损机制主要为表面疲劳和氧化磨损。
而随着温度升高,动态摩擦使得试样表面的微观结构发生变化,形成一些较大的裂纹和疏松区域,此时的磨损机制转变为热疲劳和微结构变化磨损,磨损率不断上升。
当温度达到800℃时,半金属摩擦材料的磨损率开始下降,这是因为高温下氧化反应强烈,产生了一层具有较高硬度的涂层和玻璃化区域,摩擦表面的液化减少了磨损,试样表面疲劳破坏显著减少。
石棉和半金属、NAO刹车片优缺点

有着汽车保护神之称的刹车片,不仅是刹车系统中重要零部件之一,更是汽车易损件中的一种。
刹车片的好坏直接决定着汽车刹车效果,所以它的选择也就尤为重要,可面对市场上不同材质的刹车片,到底要选择哪一种的刹车片呢?日产汽配网小编为您整理了不同材质的刹车片,让您轻松选择。
石棉型汽车刹车片从最初开始石棉就已经被用作刹车片的加固材料,由于石棉纤维具有高强度和耐高温的特性,因此可以满足刹车片及离合器盘和衬垫的要求。
这种纤维具有较强的抗张能力,甚至可以同高级钢材相匹配,并且可以承受316℃的高温。
更重要的是石棉相对廉价,它是从闪石矿石中提炼出来的,而此种矿石在很多国家已被大量发现。
在石棉型刹车片的成分比例中,石棉占到40-60%,这种材料也被采用于早先尼桑刹车片,后来人们现在发现多数石棉具有潜在的危害,石棉已被医学界证实是致癌物质,其针状的纤维很容易进入肺部并停留,造成剌激,最终可导致肺癌的发生,但这种病症潜伏期可长达15-30年,所以人们往往认识不到由石棉引发的危害。
只要石棉纤维被摩擦材料自身固定后将不会对工作人员的健康造成危害,但是当石棉纤维伴随着制动摩擦形成制动尘埃而排放时,就可能成为一系列影响健康的根源。
由于石棉是绝热的,其导热能力特别差,通常反复使用制动器会使热量在刹车片中堆积起来,刹车片变热后,它的制动性能就要发生改变,要产生同样的摩擦和制动力会需要更多的踩刹车次数,这种现象被称为“制动萎缩”,如果刹车片达到一定的热度,将导致制动失灵。
渐渐地这种材质的刹车片也就淘汰了。
当车辆制造商和制动材料供应商决定发展新的更安全的石棉替代品时,新的摩擦材料几乎同时应运而生。
这就是下面要谈到的“半金属”混合物型和无石棉有机物型(NAO)刹车片。
“半金属”混合物型汽车刹车片“半金属”混合物型刹车片(Semi-met)主要是采用粗糙的钢丝绒作为加固纤维和重要的混合物。
从外观上(细的纤维和微粒)可以很方便地将石棉型和无石棉有机物型刹车片(NAO)区分开来,另外它们还具有一定的磁性。
汽车用Lapinus纤维LFC301半金属材料制动摩擦片的研制毕业答辩解析

一、研究意义
我国有关标准及汽车制造厂根据摩擦片的使用工况条 件,对摩擦片提出了相应的机械强度要求。如:冲击强度、 抗弯强度、抗压强度、剪切强度等。为了满足这些强的性 能要求,需要选用合适的纤维品种增加、满足强度性能。 目前摩擦材料存在的问题集中在两方面:高温状态下存在 热衰退,高温状态下的物理性能下降。
汽车用Lapinus纤维LFC301半金属材料制动摩擦 片的研制
Development of Lapinus fiber LFC301 half metallic materials brake for automobile
学 生: 学 号: 专 业:
指导老师 : 答辩日期 :
报告内容
➢ 研究意义 ➢ 研究内容 ➢ 实验部分 ➢ 结果与讨论 ➢ 结果 ➢ 致谢
因此加快研制开发新型的价格低廉、性能稳定、耐热 耐磨性能良好的摩擦材料已成为摩擦材料业的当务之急。
二、研究内容
本实验采用摩擦片的干法生产工艺,通过改变纤维 LFC301在基础配方里的含量,制备五组摩擦片。为了 获得最优的Lapinus纤维LFC301半金属材料制动摩擦片 并确定LFC301的最适用量,通过实验测定其各项性能 从而获得最佳的配方。
100℃ 0.39 0.37 0.36 0.36 0.32
不同温度下的摩擦材料的磨损率
100℃ 150℃
1 0.38
0.34
2 0.42
0.40
3 0.39
0.31
4 0.36
0.38
5 0.44
0.49
200℃ 0.40 0.37 0.34 0.37 0.50
250℃ 0.52 0.44 0.43 0.37 0.53
第五组配方中摩擦因数在0.32-0.39之间变化,摩擦因 数随温度的升高先增大后减小又增大,降温过程中摩擦因 数随温度的降低先减小后增大又减小,不稳定。第五组的 磨损率比较大,随温度的升高先减小后增大再减小。
小宋杂谈-半金属摩擦材料

小宋杂谈-半金属摩擦材料Semi-metallic formula1.配方定义:包含钢纤维,多孔性铁粉,增摩填料,石墨,焦炭润滑剂等。
钢纤维与铁粉含量大概在40%以上。
(日本资料40%以上,SAE资料50%,中国资料30-45%)2.主要特性:•较低的成本•高的导热性•优良的耐磨性•适用于重负荷制动工况3.存在的主要问题 :•Noise, Vibration and Harshness (NVH) 噪音振动粗糙度,容易引发低频噪音,同时伴随车体的剧烈振动。
•粉尘较多(高温衰退不好)。
•高金属含量使得低温低速制动力不足,易使脚踏力疲劳。
•高的热导率和升温速率使热量被传递到制动钳及其组件上,这种热量会加快制动钳,活塞密封圈及回位弹簧等组件的老化。
高的热导率易使摩擦材料产生热分解和高温衰退,会使制动衬片出现剥离或开裂现象。
•粘附性和易生锈,锈蚀后粘附对偶或者损伤对偶,磨损加剧。
4.配方实例:No Raw Material Vol%1 Phenolic Resin 19.52 Bariu Sulfate 9.53 Steel Wool 13.54 Iron Sponge 19.55 Mineral fibers 4.06 Graphite 8.27 Coke 2.78 Cashew Particles 7.49 Rubber 11.510 Vermiculite 4.2简单唠叨下:Nicholson 在《Facts About Friction》中提出过Asserts that volume percent is the correct unit of measure for friction material composition. 体积百分比是衡量摩擦材料最正确的单位。
再次感谢美国的lily小姐,提供我部分《Facts About Friction》资料,一个优秀的配方工程师应该自觉的掌握了解各种原材料的基本性质(密度、粒度、硬度、水分、化学成分、弹性模量and so on...)原谅我卖弄一下很简单的英语!同时应该清楚的知道各种摩擦材料对摩擦材料制品的微观和宏观性能的影响。
摩擦衬片(衬块)的磨损特性计算

摩擦衬片(衬块)的磨损特性计算摩擦衬片(衬块)的磨损与摩擦副的材质、表面加工情况、温度、压力以及相对滑磨速度等多种因素有关,因此在理论上要精确计算磨损性能是困难的。
但试验表明,摩擦表面的温度、压力、摩擦系数和表面状态等是影响磨损的重要因素。
汽车的制动过程,是将其机械能(动能、势能)的一部分转变为热量而耗散的过程。
在制动强度很大的紧急制动过程中,制动器几乎承担了耗散汽车全部动力的任务。
此时由于在短时间内制动摩擦产生的热量来不及逸散到大气中,致使制动器温度升高。
此即所谓制动器的能量负荷。
能量负荷愈大,则摩擦衬片(衬块)的磨损亦愈严重。
制动器的能量负荷常以其比能量耗散率作为评价指标。
比能量耗散率又称为单位功负荷或能量负荷,它表示单位摩擦面积在单位时间内耗散的能量,其单位为W/mm2双轴汽车的单个前轮制动器和单个后轮制动器的比能量耗散率分别为式中:δ——汽车回转质量换算系数;ma——汽车总质量v1 v2——汽车制动初速度与终速度,m/s;计算时轿车取v1= 100km/h(27.8m/s);总质量 3.5吨以下的货车取vl=80km/h(22.2m/s);总质量3.5 t以上的货车取v1=65 km/h(18m/s);t一制动时间,s;按下式计算j一制动减速度,m/ s2计算时取j=0.6g;A1,A2一前、后制动器材特(衬块)的摩擦面积;β一制动力分配系数,见式(3-12)在紧急制动到v2=0时,并可近似地认为δ=1,则有鼓式制动器的比能量耗散率以不大于1.8 W/mm2为宜,但当制动初速度油vl低于式(4-25)下面所规定的v1时,则允许略大于 1.8 W/mm2。
轿车盘式制动器的比能量D 耗散率应不大于6.0 W/mm2发比能量耗散率过高,不仅会加快制动摩擦衬片(衬块)的磨损,而且可能引起制动鼓或盘的龟裂。
磨损特性指标也可用衬片(衬块)的比摩擦力即单位摩擦面积的摩擦力来衡量。
单个车轮制动器的比摩擦力为式(4-27)Tf中:Tf一单个制动器的制动力矩;R一制动鼓半径(或制动盘有效半径)A一单个制动器的衬片(衬块)摩擦面积。
石棉和半金属、NAO刹车片优缺点

有着汽车保护神之称的刹车片,不仅是刹车系统中重要零部件之一,更是汽车易损件中的一种。
刹车片的好坏直接决定着汽车刹车效果,所以它的选择也就尤为重要,可面对市场上不同材质的刹车片,到底要选择哪一种的刹车片呢?日产汽配网小编为您整理了不同材质的刹车片,让您轻松选择。
石棉型汽车刹车片从最初开始石棉就已经被用作刹车片的加固材料,由于石棉纤维具有高强度和耐高温的特性,因此可以满足刹车片及离合器盘和衬垫的要求。
这种纤维具有较强的抗张能力,甚至可以同高级钢材相匹配,并且可以承受316℃的高温。
更重要的是石棉相对廉价,它是从闪石矿石中提炼出来的,而此种矿石在很多国家已被大量发现。
在石棉型刹车片的成分比例中,石棉占到40-60%,这种材料也被采用于早先尼桑刹车片,后来人们现在发现多数石棉具有潜在的危害,石棉已被医学界证实是致癌物质,其针状的纤维很容易进入肺部并停留,造成剌激,最终可导致肺癌的发生,但这种病症潜伏期可长达15-30年,所以人们往往认识不到由石棉引发的危害。
只要石棉纤维被摩擦材料自身固定后将不会对工作人员的健康造成危害,但是当石棉纤维伴随着制动摩擦形成制动尘埃而排放时,就可能成为一系列影响健康的根源。
由于石棉是绝热的,其导热能力特别差,通常反复使用制动器会使热量在刹车片中堆积起来,刹车片变热后,它的制动性能就要发生改变,要产生同样的摩擦和制动力会需要更多的踩刹车次数,这种现象被称为“制动萎缩”,如果刹车片达到一定的热度,将导致制动失灵。
渐渐地这种材质的刹车片也就淘汰了。
当车辆制造商和制动材料供应商决定发展新的更安全的石棉替代品时,新的摩擦材料几乎同时应运而生。
这就是下面要谈到的“半金属”混合物型和无石棉有机物型(NAO)刹车片。
“半金属”混合物型汽车刹车片“半金属”混合物型刹车片(Semi-met)主要是采用粗糙的钢丝绒作为加固纤维和重要的混合物。
从外观上(细的纤维和微粒)可以很方便地将石棉型和无石棉有机物型刹车片(NAO)区分开来,另外它们还具有一定的磁性。
- 1、下载文档前请自行甄别文档内容的完整性,平台不提供额外的编辑、内容补充、找答案等附加服务。
- 2、"仅部分预览"的文档,不可在线预览部分如存在完整性等问题,可反馈申请退款(可完整预览的文档不适用该条件!)。
- 3、如文档侵犯您的权益,请联系客服反馈,我们会尽快为您处理(人工客服工作时间:9:00-18:30)。
半金属汽车制动衬片的摩擦性能摘要:目的—本文的目的是要找到与刹车制动衬片的摩擦性能的变化情况以及它们对汽车的制动安全性和可靠性的影响。
设计方法—半金属制动衬片目前广泛应用于汽车,它被选为实验材料。
通过模拟汽车的制动条件和环境,当搭配的摩擦盘是灰口铸铁时,在X-DM摩擦试验机上对一些制动衬片的摩擦磨损进行了试验研究。
发现当表面温度自然上升时,摩擦系数随着滑动速度的增加逐渐降低制动压力。
随着表面温度的上升,首先上升然后下降,极大值出现在近2008°C 左右。
摩擦系数的稳定性明显下降时,滑动速度超过30m/s,制动压力超过1.8MPa 和表面温度超过2008摄氏度。
根据实验结果,作者认为当汽车高速行驶时,只通过加大制动压力来执行紧急制动是不可靠的。
为了减少高温对摩擦性能的不良影响,应采取一些有效的措施来冷却摩擦盘。
更重要的是,特别要注意在高速、高压和高温时制动摩擦稳定性的降低。
创意/价值—本文研究制动条件对摩擦系数的影响及其稳定性的半金属制动衬片汽车。
相信本研究对提高汽车的制动安全性和可靠性可能有一些实际的指导性。
关键词:汽车零部件工业;刹车系统;摩擦系数;摩擦系数稳定性;半金属刹车片;汽车制动条件;1介绍由于盘式制动器有许多优点,如稳定的制动性能,快速冷却能力,低重量,结构简单等等。
它已广泛应用于汽车的制动系统。
汽车在制动过程中,制动衬片的摩擦性能不仅受到自身材料特性的影响,也受很多其他因素影响,如变化的环境等等。
因此,在实际制动过程中,必须改变复杂的摩擦性能。
有时,因为一些异常变化的摩擦性能,制动距离长,虽然刹车装置执行紧急制动,但不能及时停止汽车。
因此,交通事故由此而生,威胁着司机的生命安全。
为了研究汽车衬片的摩擦制动性能,许多人通过摩擦磨损入手进行实验。
举个例子,为了研究材料性能对摩擦性能的影响,Xiong在2004年分析了树脂的摩擦机制并指出了对摩擦片材料的要求。
Kim,Hee,Filip.Yan,Cao和Yang分别调查了前卫的形式和内容在刹车片的摩擦性能上的影响。
其次,为了研究制动条件对摩擦性能的影响,Han,San,Zhang,Ma,Sviridenok,Meshkov,Straffelini和Bao分别对速度,压力和温度对摩擦学的影响进行了实验。
第三,为了研究环境的影响,Mutlu于2006年研究了酚醛复合制动片在不同接触条件下(如纯净水、盐、水和油)的摩擦性能。
基于目前的研究,发现实验模拟的主要是低速下的制动条件,这是完全不同于实际汽车制动条件。
因此,实验结论对指导实际的刹车不是很有用。
更重要的是,摩擦性能不是综合得分。
一般说来,只有摩擦系数大小被考虑,而很少考虑到摩擦系数的稳定性。
为了更全面的调查制动衬片的摩擦性能,在本文中,已广泛应用于中国汽车的半金属制动衬片被选为材料。
通过模拟其在高速、高压和高温的工作条件下,摩擦系数的变化及其稳定性和对滑动速度影响系数、制动压力、表面温度进行了许多实验。
基于实验结果,摩擦性能对汽车的制动安全性和可靠性被深刻探讨。
相信本研究对提高汽车的制动安全性和可靠性可能有一些实际的指导。
2实验2.1实验材料自从半金属制动衬片已广泛应用于中国制造的桑塔纳和捷达汽车,然后被选为实验材料。
如图1所示,因金属纤维的含量和粉末已经超过了50%,所以被称为半金属。
半金属的粘合材料制动片perbunan-modified phenolaldehy 树脂和加强材料是铜纤维。
一些铜,氧化铝和长石粉添加摩擦学的的监管机构,配对的摩擦盘HT250铸铁,这是一般用于制造汽车的制动盘。
图1半金属刹车片2.2实验设备及其测试方法众所周知,衬里和阀瓣的汽车盘式制动气装置块和阀瓣的表面接触之间的运动是刹车之间的联系方式,它们是绝对的滑动。
X-DM摩擦试验机,最好是模拟盘式制动器的操作条件进行摩擦磨损实验。
X-DM摩擦试验机的测试原理与tribologia性能的测试类似,遵循国家标准GB5763-1998“汽车刹车片”(中华人民共和国国家标准,中国,1998)。
械的原理图机构和摩擦接触如图2所示。
X-DM摩擦测试仪的测试原理表述如下:调速电动机的驱动引起摩擦盘向顺时针方向旋转。
汽车的速度可以通过电动机附近叫做计数传感器的轴测得。
正向的压力加载到两块制动衬片样品上。
摩擦力由固定在摩擦台上的扭转传感器测量。
周围的温度可以被加热管,鼓风机和水阀控制。
制动衬片的表面温度被放置在摩擦盘表面,制动衬片和阀瓣的接触区域的热电偶测得。
实验参数的设置,收集和处理大多数由电脑控制的测试系统完成。
一般说来,摩擦系数作为影响材料摩擦性能的主要指标。
为了研究摩擦性能的稳定性,摩擦系数大小和摩擦系数稳定性都需要考虑。
测试这两个指标的原则如下:1摩擦性能:μ=F/pA (1) 其中,F是制动衬片和摩擦盘之间的摩擦力,单位牛顿;p是特定的制动压力,单位兆帕;A是名义上的制动衬片的表面积,单位平方毫米;在每一次测试中,摩擦盘的转数都设置为5000轮,测试并注意不断变化的摩擦力,然后按照公式(1)计算并显示瞬时摩擦有效系数。
例如,当压力是1.0Mpa 时,速度为15m/s,表面温度自然上升,摩擦系数的曲线随时间变化如图3所示:由于表面形态和温度影响摩擦力,这在前2500轮不是稳定的,所以,每个工作条件下的摩擦系数是在后2500轮中计算出来的。
2摩擦系数的稳定性:а=μ/μmax*100% (2) 分别是每个制动过程中制动衬片摩擦力的平均值和最大值。
其中,μ和μmax2.3实验方案在超过30m/s的条件下,为了研究制动压力p,滑动速度V和表面温度t对摩擦系数μ和稳定性a的影响,进行了大量实验,实验方案设计如下:在研究制动压力和滑动速度对摩擦性能的影响时,发热的测试仪器被关闭电源,随着实验的进行,温度自然上升。
测试的制动压力值分别设置为1,1.4,1.8,2.2,2.6和3兆帕。
同时,滑动速度实验值分别设置为5,10,15,20,25和30米/秒,在每个制动压力和滑动速度组合条件下,重复试验三次。
而且,摩擦系数的平均值和它的每个制动条件下的稳定系数被选为最终结果。
在调查表面温度对摩擦性能的影响时,摩擦盘表面温度通过加热管加热和保持热量,通过温度控制系统常数。
表面温度的测试值分别设置为100,150,200,250,300和350摄氏度,在每一个温度下,制动压力和滑动速度都设置为一定值,实验重复三次,摩擦系数的平均值和它的每个制动条件下的稳定系数被选为最终结果。
3结果与讨论3.1制动压力对摩擦的影响当摩擦盘的表面温度自然增加,摩擦系数的变化极其稳定性与制动压力系数关系如图4所示(a),(b),从图4(a)中发现,当滑动速度是确定的,摩擦系数随着制动压力的增加而降低。
制动压力对摩擦系数的影响在速度超过30m/s 时更显著,尤其是在高压下。
从图4(b)中发现,当滑动速度较低,摩擦系数稳定性随着制动压力的增加变化平稳。
稳定的系数值超过85%以上,这表明在低速期,制动压力对摩擦稳定性影响很小。
然而,当滑动速度超过30m/s时,摩擦系数的稳定性随着刹车压力的增大而降低。
稳定系数明显低于之前的值,例如,当制动压力上升到3.0Mpa时,稳定系数下降近70%。
正如摩擦学的理论所述,制动压力或负载的影响主要通过摩擦力表面的实际接触面积变化。
假设制动衬片与摩擦盘之间的实际接触面积为A0,剪切在制动衬片上的压力为τ,然后摩擦力F可以表示如下:*τ (3) F=A把公式(1)、(3)联合,得到摩擦系数μ可计算如下:*τ/pA (4)μ= A由于剪切力是材料固有的,所以很容易从公式(4)中得出,摩擦系数μ与实际接触面积A0成正比,而与额定制动压力p成反比。
当制动压力p增加,公式(4)的分母也会增加,因此,摩擦系数会降低。
但从另一方面,随着制动衬片上的负载的增加,实际接触面积A0也将增加,因此使得摩擦系数上升。
事实上,如果制动压力的增加导致更大增量比例的实际接触面积,摩擦系数将会上升。
相反,如果增加接触面积比小于负载,然后,摩擦系数将会下降。
最初的半金属制动衬片在每个正常的实验之前,经过3000轮旋转后被磨损,所以制动衬片和摩擦盘之间的接触面积可能达到了一个稳定值。
因此,有制动压力的增加而引起的A0的增加量必须被限制。
故制动压力的增加主要导致公式(4)分母的上升。
然后如图(4)(a)所示,随着制动压力的增加,摩擦系数减小。
正如2.1节所说,半金属刹车片里有将近一半有利于热传导的的铜纤维粉。
当滑动速度不高,一方面,摩擦热量不是很高,另一方面,铜纤维粉和粉末也可以及时进行热传导。
所以,在低速时摩擦热对半金属制动片的摩擦性能有很小的影响。
在图(4)(a)中,摩擦系数随着制动压力的增加而变化较平稳,在途(4)(b)中摩擦系数的稳定性显示稳定。
然而,当速度超过30m/s时,摩擦热量迅速增加。
高温度会软化和表层融化材料,是材料摩擦性能变差。
因此,在图(4)高速时期,摩擦系数及其稳定性显著减少。
图4随着刹车压力的摩擦性能的变化基于实验结果和结论,得出的结论是,它不是只通过提高汽车的制动距离压力来缩短制动距离。
这是因为制动压力增加会导致摩擦系数降低,所以制动扭矩不一定上升。
特别是,当滑动速度非常高时,制动压力的增加明显降低摩擦系数和其稳定性系数,这是对汽车的制动安全和可靠性是非常危险的。
3.2表面温度对摩擦的影响当制动压力为1.8Mpa时,在不同滑动速度、摩擦系数及其稳定性对半金属刹车片的影响与表面温度关系如图5(a)和(b)所示。
如图5(a)所示,总的来说,制动衬片的摩擦系数随着温度的增加先上升后下降。
绝大部分的最大摩擦系数出现在2008摄氏度。
当温度超过2508摄氏度时,摩擦系数下降的速度明显比以前更快了。
在图5(b)中,当表面温度低于2008摄氏度时,摩擦系数稳定性变化平稳,但此后大大降低。
正如摩擦学理论表明,在滑动副滑动过程中,表面温度是表面层材料发生质的变化,其结果影响了摩擦性能(Huang等人)。
当表面温度不高于2008摄氏度,在半金属的耐热性限制下,制动衬片表层材料仍可以保持正常的结构和性能。
在此温度间,随着温度的上升,实际联系的微极点越容易黏在一起。
更多的坚持会使实际的接触面积更大,因此,摩擦系数随着图5(a)中变化而上升。
其稳定性系数变化随着图5(b)中变化而稳定。
然而,当表面温度超过2008摄氏度时,实际温度对接触点的影响远高于摩擦热的影响。
如果实际接触区的温度超过了铜的熔点,那么铜纤维和铜粉会融化形成润滑膜。
更甚的是,高温使粘结材料热解出一些气体,如氢气和一氧化碳,然后释放到空气中film的表面上。
如上所分析,高温使一些面层材料发生定性的变化。
结果,从干摩擦到有一半液体和气体润滑的摩擦形态变化,因此,摩擦系数及其稳定性在如图5(a)(b)中的高温期都明显减少。