锡炉焊锡问题点的分析
焊锡次品分析报告
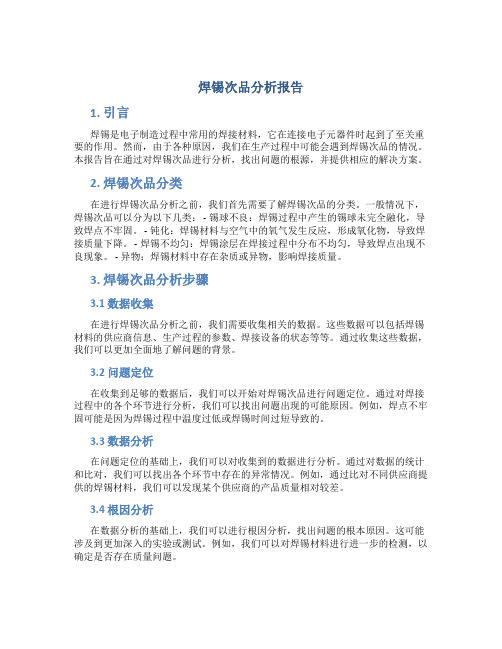
焊锡次品分析报告1. 引言焊锡是电子制造过程中常用的焊接材料,它在连接电子元器件时起到了至关重要的作用。
然而,由于各种原因,我们在生产过程中可能会遇到焊锡次品的情况。
本报告旨在通过对焊锡次品进行分析,找出问题的根源,并提供相应的解决方案。
2. 焊锡次品分类在进行焊锡次品分析之前,我们首先需要了解焊锡次品的分类。
一般情况下,焊锡次品可以分为以下几类: - 锡球不良:焊锡过程中产生的锡球未完全融化,导致焊点不牢固。
- 钝化:焊锡材料与空气中的氧气发生反应,形成氧化物,导致焊接质量下降。
- 焊锡不均匀:焊锡涂层在焊接过程中分布不均匀,导致焊点出现不良现象。
- 异物:焊锡材料中存在杂质或异物,影响焊接质量。
3. 焊锡次品分析步骤3.1 数据收集在进行焊锡次品分析之前,我们需要收集相关的数据。
这些数据可以包括焊锡材料的供应商信息、生产过程的参数、焊接设备的状态等等。
通过收集这些数据,我们可以更加全面地了解问题的背景。
3.2 问题定位在收集到足够的数据后,我们可以开始对焊锡次品进行问题定位。
通过对焊接过程中的各个环节进行分析,我们可以找出问题出现的可能原因。
例如,焊点不牢固可能是因为焊锡过程中温度过低或焊锡时间过短导致的。
3.3 数据分析在问题定位的基础上,我们可以对收集到的数据进行分析。
通过对数据的统计和比对,我们可以找出各个环节中存在的异常情况。
例如,通过比对不同供应商提供的焊锡材料,我们可以发现某个供应商的产品质量相对较差。
3.4 根因分析在数据分析的基础上,我们可以进行根因分析,找出问题的根本原因。
这可能涉及到更加深入的实验或测试。
例如,我们可以对焊锡材料进行进一步的检测,以确定是否存在质量问题。
3.5 解决方案在找到问题的根本原因后,我们可以提出相应的解决方案。
这些解决方案可能包括改变生产过程参数、更换供应商、进行设备维护等。
通过实施这些解决方案,我们可以有效地降低焊锡次品的发生率,提高焊接质量。
焊锡不良分析报告
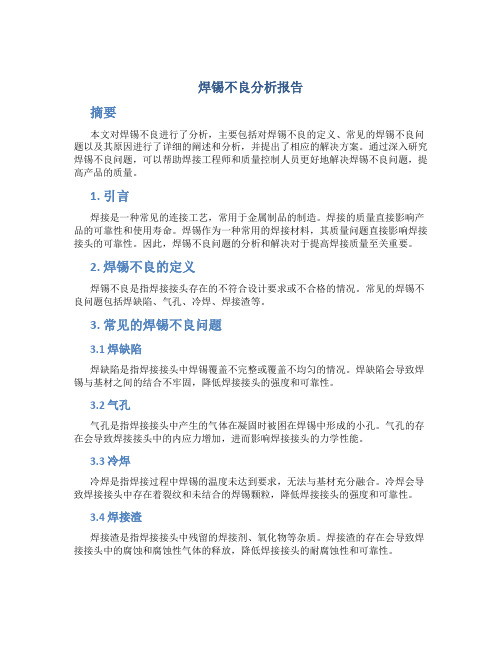
焊锡不良分析报告摘要本文对焊锡不良进行了分析,主要包括对焊锡不良的定义、常见的焊锡不良问题以及其原因进行了详细的阐述和分析,并提出了相应的解决方案。
通过深入研究焊锡不良问题,可以帮助焊接工程师和质量控制人员更好地解决焊锡不良问题,提高产品的质量。
1. 引言焊接是一种常见的连接工艺,常用于金属制品的制造。
焊接的质量直接影响产品的可靠性和使用寿命。
焊锡作为一种常用的焊接材料,其质量问题直接影响焊接接头的可靠性。
因此,焊锡不良问题的分析和解决对于提高焊接质量至关重要。
2. 焊锡不良的定义焊锡不良是指焊接接头存在的不符合设计要求或不合格的情况。
常见的焊锡不良问题包括焊缺陷、气孔、冷焊、焊接渣等。
3. 常见的焊锡不良问题3.1 焊缺陷焊缺陷是指焊接接头中焊锡覆盖不完整或覆盖不均匀的情况。
焊缺陷会导致焊锡与基材之间的结合不牢固,降低焊接接头的强度和可靠性。
3.2 气孔气孔是指焊接接头中产生的气体在凝固时被困在焊锡中形成的小孔。
气孔的存在会导致焊接接头中的内应力增加,进而影响焊接接头的力学性能。
3.3 冷焊冷焊是指焊接过程中焊锡的温度未达到要求,无法与基材充分融合。
冷焊会导致焊接接头中存在着裂纹和未结合的焊锡颗粒,降低焊接接头的强度和可靠性。
3.4 焊接渣焊接渣是指焊接接头中残留的焊接剂、氧化物等杂质。
焊接渣的存在会导致焊接接头中的腐蚀和腐蚀性气体的释放,降低焊接接头的耐腐蚀性和可靠性。
4. 焊锡不良问题的原因分析4.1 工艺参数不恰当焊接工艺参数的不恰当是导致焊锡不良的主要原因之一。
例如,焊接温度、焊接速度等工艺参数的调整不当会导致焊锡过热或过冷,从而产生焊缺陷、气孔等问题。
4.2 材料质量不合格焊锡材料质量的不合格也是导致焊锡不良的一个重要原因。
例如,焊锡材料的成分控制不严格、杂质含量过高等都会影响焊锡的焊接性能。
4.3 操作不规范焊接操作的不规范也是产生焊锡不良的原因之一。
例如,焊锡的存放和使用不当、焊接操作中的温度控制不严格等都会导致焊锡不良问题的发生。
?全自动焊锡机焊接常见问题原因及应对对策
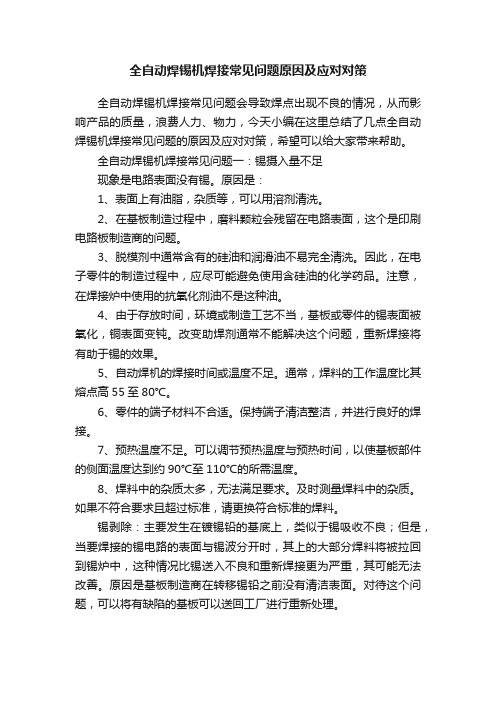
全自动焊锡机焊接常见问题原因及应对对策全自动焊锡机焊接常见问题会导致焊点出现不良的情况,从而影响产品的质量,浪费人力、物力,今天小编在这里总结了几点全自动焊锡机焊接常见问题的原因及应对对策,希望可以给大家带来帮助。
全自动焊锡机焊接常见问题一:锡摄入量不足现象是电路表面没有锡。
原因是:1、表面上有油脂,杂质等,可以用溶剂清洗。
2、在基板制造过程中,磨料颗粒会残留在电路表面,这个是印刷电路板制造商的问题。
3、脱模剂中通常含有的硅油和润滑油不易完全清洗。
因此,在电子零件的制造过程中,应尽可能避免使用含硅油的化学药品。
注意,在焊接炉中使用的抗氧化剂油不是这种油。
4、由于存放时间,环境或制造工艺不当,基板或零件的锡表面被氧化,铜表面变钝。
改变助焊剂通常不能解决这个问题,重新焊接将有助于锡的效果。
5、自动焊机的焊接时间或温度不足。
通常,焊料的工作温度比其熔点高55至80℃。
6、零件的端子材料不合适。
保持端子清洁整洁,并进行良好的焊接。
7、预热温度不足。
可以调节预热温度与预热时间,以使基板部件的侧面温度达到约90℃至110℃的所需温度。
8、焊料中的杂质太多,无法满足要求。
及时测量焊料中的杂质。
如果不符合要求且超过标准,请更换符合标准的焊料。
锡剥除:主要发生在镀锡铅的基底上,类似于锡吸收不良;但是,当要焊接的锡电路的表面与锡波分开时,其上的大部分焊料将被拉回到锡炉中,这种情况比锡送入不良和重新焊接更为严重,其可能无法改善。
原因是基板制造商在转移锡铅之前没有清洁表面。
对待这个问题,可以将有缺陷的基板可以送回工厂进行重新处理。
全自动焊锡机焊接常见问题二:冷焊或焊点不光滑这种情况可归为焊点不均匀的一种,这种情况发生在基材与锡波分离并固化且零件受到以下因素影响时外力移动并形成焊点。
焊接后要保持基板传送稳定,例如加强零件的固定,注意零件的销钉的方向等;简而言之,在移动之前,必须充分冷却待焊接的基板,以避免出现此问题。
解决的办法是再次通过锡波。
焊锡出现的问题和解决方法
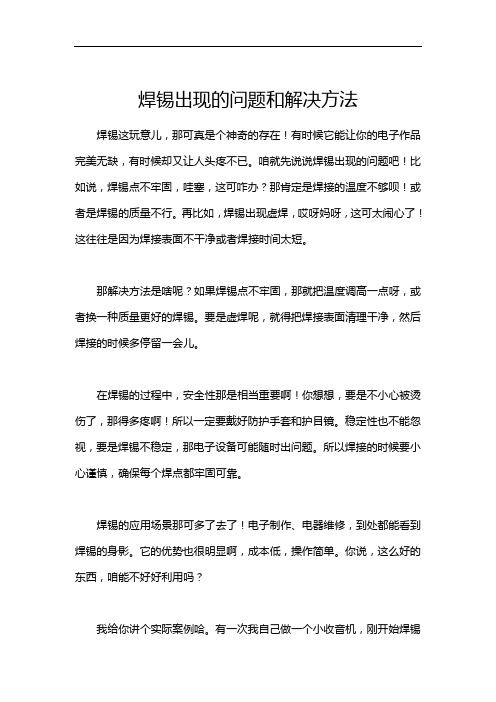
焊锡出现的问题和解决方法
焊锡这玩意儿,那可真是个神奇的存在!有时候它能让你的电子作品完美无缺,有时候却又让人头疼不已。
咱就先说说焊锡出现的问题吧!比如说,焊锡点不牢固,哇塞,这可咋办?那肯定是焊接的温度不够呗!或者是焊锡的质量不行。
再比如,焊锡出现虚焊,哎呀妈呀,这可太闹心了!这往往是因为焊接表面不干净或者焊接时间太短。
那解决方法是啥呢?如果焊锡点不牢固,那就把温度调高一点呀,或者换一种质量更好的焊锡。
要是虚焊呢,就得把焊接表面清理干净,然后焊接的时候多停留一会儿。
在焊锡的过程中,安全性那是相当重要啊!你想想,要是不小心被烫伤了,那得多疼啊!所以一定要戴好防护手套和护目镜。
稳定性也不能忽视,要是焊锡不稳定,那电子设备可能随时出问题。
所以焊接的时候要小心谨慎,确保每个焊点都牢固可靠。
焊锡的应用场景那可多了去了!电子制作、电器维修,到处都能看到焊锡的身影。
它的优势也很明显啊,成本低,操作简单。
你说,这么好的东西,咱能不好好利用吗?
我给你讲个实际案例哈。
有一次我自己做一个小收音机,刚开始焊锡
的时候总是出问题,不是虚焊就是焊锡点不牢固。
后来我按照上面说的方法,把焊接表面清理干净,调高了温度,换了好一点的焊锡,嘿,一下子就成功了!那个小收音机现在还能用呢。
焊锡虽然有时候会出现问题,但是只要我们掌握了正确的方法,就一定能让它发挥出最大的作用。
所以啊,大家别怕焊锡出现问题,勇敢地去尝试,相信你一定能成功。
锡焊过程中遇到的问题及解决方法
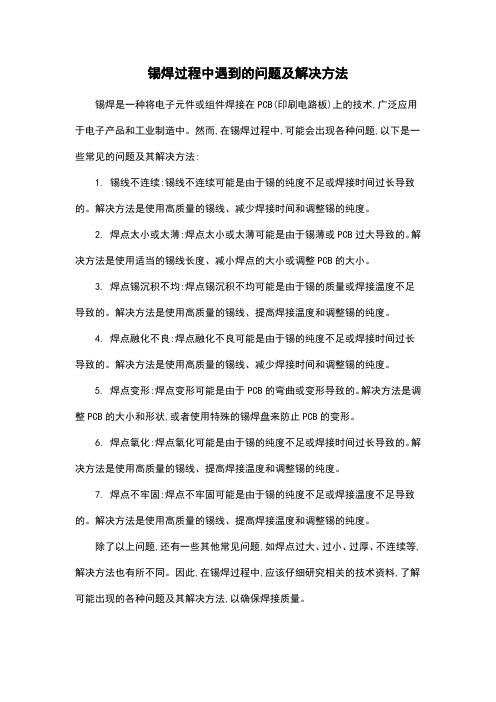
锡焊过程中遇到的问题及解决方法
锡焊是一种将电子元件或组件焊接在PCB(印刷电路板)上的技术,广泛应用于电子产品和工业制造中。
然而,在锡焊过程中,可能会出现各种问题,以下是一些常见的问题及其解决方法:
1. 锡线不连续:锡线不连续可能是由于锡的纯度不足或焊接时间过长导致的。
解决方法是使用高质量的锡线、减少焊接时间和调整锡的纯度。
2. 焊点太小或太薄:焊点太小或太薄可能是由于锡薄或PCB过大导致的。
解决方法是使用适当的锡线长度、减小焊点的大小或调整PCB的大小。
3. 焊点锡沉积不均:焊点锡沉积不均可能是由于锡的质量或焊接温度不足导致的。
解决方法是使用高质量的锡线、提高焊接温度和调整锡的纯度。
4. 焊点融化不良:焊点融化不良可能是由于锡的纯度不足或焊接时间过长导致的。
解决方法是使用高质量的锡线、减少焊接时间和调整锡的纯度。
5. 焊点变形:焊点变形可能是由于PCB的弯曲或变形导致的。
解决方法是调整PCB的大小和形状,或者使用特殊的锡焊盘来防止PCB的变形。
6. 焊点氧化:焊点氧化可能是由于锡的纯度不足或焊接时间过长导致的。
解决方法是使用高质量的锡线、提高焊接温度和调整锡的纯度。
7. 焊点不牢固:焊点不牢固可能是由于锡的纯度不足或焊接温度不足导致的。
解决方法是使用高质量的锡线、提高焊接温度和调整锡的纯度。
除了以上问题,还有一些其他常见问题,如焊点过大、过小、过厚、不连续等,解决方法也有所不同。
因此,在锡焊过程中,应该仔细研究相关的技术资料,了解可能出现的各种问题及其解决方法,以确保焊接质量。
焊锡不良分析及对策

焊锡条焊接出现的各种问题

焊锡条焊接出现的各种问题?
焊锡条在焊接时多多少少会出现各种各样的焊接不良的情况出现,比如焊点问题、拉尖问题、侨联问题等。
下面兴鸿泰锡业工程师将针对焊锡条出现的各种不良现象进行一一的解答:
★焊锡条的焊点出现不完整的现象;
主要原因是因为焊锡条的助焊剂受热过多,还有一种情况就是PCB板或元器件本身质量有问题。
★焊锡条的润滑出现不良;
主要原因是由于PCB板的表面出现氧化,有比较严重的氧化膜,还有就是焊锡条中离子杂质太多也会导致以上问题的出现。
同时焊锡条的生产车间也要保持时刻清洁无污染,当然密封无尘车间最好,这样对于焊锡条的上锡润滑性是非常有帮助的。
★焊锡条焊接时出现包锡的现象,即我们说的吃锡不良。
这个原因有好几个,一是焊锡条的预热温度不够或者本身锡炉的温度就过于低;二是焊锡条使用的助焊剂活性不够,起不到辅助焊接的作用;三是焊锡条的过锡深度不精确;四是焊锡条在焊接流程中被严重污染了。
★焊锡条的焊点出现拉尖,即冰柱。
这主要是焊锡条溶锡时温度传导不是很均匀,还有就是PCB的设计不是很合理,当然电子元器件的质量好坏也是有关系的。
还有一个容易忽略的就是焊锡条的焊接设备的是否会老化,所以对于设备我们要经常检修和保养。
★焊锡条的润滑出现不均匀;
原因是PCB板的焊接表面受污染比较严重,出现很严重的氧化现象,使得焊锡条的锡液不能够均匀的覆盖,使得焊锡条的焊点不圆滑、不均匀。
★焊锡条焊接经常有锡球出现;
原因是焊锡条使用的助焊剂含水量过多,焊接环境过于潮湿也会出现以上的现象。
还有焊锡条焊接的PCB板预热温度要够,使板上的助焊剂风干,这样可以减少锡球的出现;。
锡焊过程中遇到的问题及解决方法
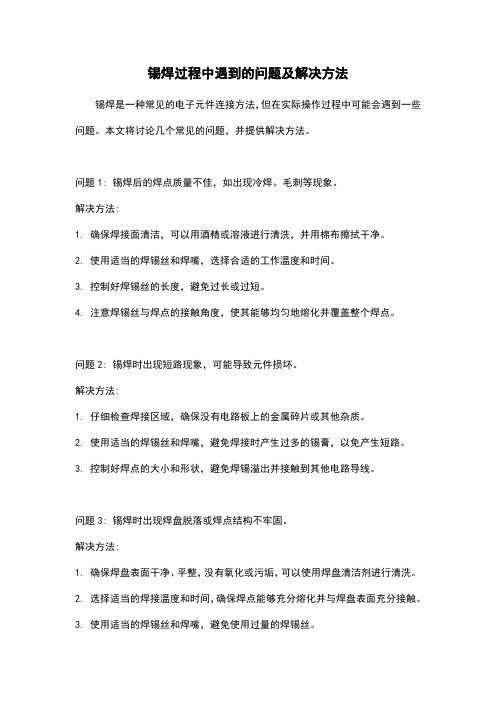
锡焊过程中遇到的问题及解决方法锡焊是一种常见的电子元件连接方法,但在实际操作过程中可能会遇到一些问题。
本文将讨论几个常见的问题,并提供解决方法。
问题1: 锡焊后的焊点质量不佳,如出现冷焊、毛刺等现象。
解决方法:1. 确保焊接面清洁,可以用酒精或溶液进行清洗,并用棉布擦拭干净。
2. 使用适当的焊锡丝和焊嘴,选择合适的工作温度和时间。
3. 控制好焊锡丝的长度,避免过长或过短。
4. 注意焊锡丝与焊点的接触角度,使其能够均匀地熔化并覆盖整个焊点。
问题2: 锡焊时出现短路现象,可能导致元件损坏。
解决方法:1. 仔细检查焊接区域,确保没有电路板上的金属碎片或其他杂质。
2. 使用适当的焊锡丝和焊嘴,避免焊接时产生过多的锡膏,以免产生短路。
3. 控制好焊点的大小和形状,避免焊锡溢出并接触到其他电路导线。
问题3: 锡焊时出现焊盘脱落或焊点结构不牢固。
解决方法:1. 确保焊盘表面干净、平整,没有氧化或污垢,可以使用焊盘清洁剂进行清洗。
2. 选择适当的焊接温度和时间,确保焊点能够充分熔化并与焊盘表面充分接触。
3. 使用适当的焊锡丝和焊嘴,避免使用过量的焊锡丝。
4. 控制好焊接压力和速度,确保焊点能够均匀地涂覆在焊盘上。
问题4: 锡焊时出现焊接位置不准确或焊点位置偏移。
解决方法:1. 在焊接前进行焊点位置的标记,可以使用标尺或模板等工具。
2. 确保焊点周围没有杂物或障碍物,以免影响焊接的准确性。
3. 控制好焊锡丝的长度和形状,避免过长或过短。
4. 在焊接过程中保持手的稳定性,使用辅助工具如放大镜或显微镜等,以确保焊点的准确性。
总结起来,锡焊过程中遇到的问题主要包括焊点质量不佳、短路现象、焊盘脱落和焊点位置偏移等。
通过保持焊接面的清洁、选择适当的焊锡丝和焊嘴、控制好焊接温度和时间、调整焊点大小和形状等方法,可以解决这些问题,提高焊接质量。
焊锡线在使用过程中常见问题分析及解决办法

焊锡线在使用过程中常见问题分析及解决办法凡是问题,都不会是单单一个原因造成的。
锡线的焊接也如此,一个问题的产生,总会有几种原因造成,下面来分析下在焊按过程中常遇到的问题,及造成的原因、解决办法。
一、锡线焊出来的焊点光亮度有偏差时,是否含锡量不稳定?答:这个问题要从影响焊点光亮度的几个因素入手分析:1.锡线含锡量有偏差时,光亮度有影响,但在一般情况下,5℃以内的含锡量可以分出来的,含锡量越低,焊点的光亮度越暗淡,当杂质的含量偏差较大时,焊点的光亮度也有比较明显的影响,如铜、银、铋等等。
2.温度对焊点的光亮度也有影响的,要使焊点表现出最佳的光泽,一定要使温度达到。
温度不足会使表面的光泽度下降且不光滑。
实验证明,用一支20w的烙铁和60w的烙铁焊同一种锡线其光亮度不同。
3.同样度数的锡线所用的助焊剂类型不同时其光亮度也有所不同,因活性剂中的某种物质对焊点的光亮度有影响。
如本厂用的活性剂有光亮和哑光两种,针对客户的要求生产。
结合以上几点,当出现焊点光亮度有变化时,应从多方面出发、去考虑仔细观察,找出原因。
二、锡线焊接时,上锡速度慢,锡珠沾在烙铁上,焊接时烟大、味嗅,此问题该如何处理?答: 大家必须明白锡线上锡是靠中间的助焊剂起作用的,再进一步仔细一点的说就是助焊剂中的活性剂起作用,松香只不过是活性剂的载体,松香与活性剂两种混合叫“助焊剂”,在焊接过程中起到三个作用: 1.清除焊接位的氧化物。
2.使焊料铺展开来,增强流动性。
3.焊料牢固的与焊接位粘合在一起。
(一) 如果遇到上锡速度慢,锡珠沾在烙铁上时,必须从以下几种方法入手:1.看焊接位的材料是什么?选择合适类型的助焊剂是焊接成功的一大因素。
2.同一类型的助焊剂,起火性也有强弱之分,这样会影响起上锡的速度和能否上锡。
3.最重要的一点,影响上锡的效果主要同助焊剂的含量有关系。
同一度数、同一直径的锡线,助焊剂含量越大上锡越容易,速度越快,但同样会带来烟雾越大。
焊锡点应 , , 表面 现象
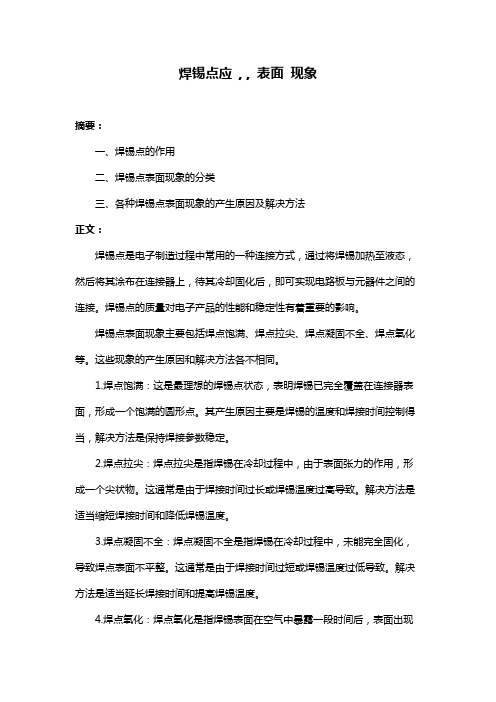
焊锡点应, , 表面现象
摘要:
一、焊锡点的作用
二、焊锡点表面现象的分类
三、各种焊锡点表面现象的产生原因及解决方法
正文:
焊锡点是电子制造过程中常用的一种连接方式,通过将焊锡加热至液态,然后将其涂布在连接器上,待其冷却固化后,即可实现电路板与元器件之间的连接。
焊锡点的质量对电子产品的性能和稳定性有着重要的影响。
焊锡点表面现象主要包括焊点饱满、焊点拉尖、焊点凝固不全、焊点氧化等。
这些现象的产生原因和解决方法各不相同。
1.焊点饱满:这是最理想的焊锡点状态,表明焊锡已完全覆盖在连接器表面,形成一个饱满的圆形点。
其产生原因主要是焊锡的温度和焊接时间控制得当,解决方法是保持焊接参数稳定。
2.焊点拉尖:焊点拉尖是指焊锡在冷却过程中,由于表面张力的作用,形成一个尖状物。
这通常是由于焊接时间过长或焊锡温度过高导致。
解决方法是适当缩短焊接时间和降低焊锡温度。
3.焊点凝固不全:焊点凝固不全是指焊锡在冷却过程中,未能完全固化,导致焊点表面不平整。
这通常是由于焊接时间过短或焊锡温度过低导致。
解决方法是适当延长焊接时间和提高焊锡温度。
4.焊点氧化:焊点氧化是指焊锡表面在空气中暴露一段时间后,表面出现
氧化层。
这会降低焊点的导电性和可靠性。
解决方法是在焊接完成后,立即进行清洗和防护处理,如使用助焊剂或进行电镀。
焊锡不良项目、产生原因、改善对策(7副件)

一、极性反:正负极焊反。
产生原因:1,脱皮、焊锡人员作业前没有分清极性。
2,查锡点人员不认真未能将不良查出改善对策:1,脱皮、焊锡人员作业前先分清极性再作业。
2,查锡点人员分两步,先查极性,再对其它不良进行检查。
产生不良;极性反。
二、PVC破皮或烫伤PVC:焊锡处外被有露铜或PVC处有变大现象。
产生原因:1,焊锡时温度过高、次数过多、时间过长。
2,焊锡人员指甲过长,焊锡时掐伤PVC有破皮。
改善对策:1,焊锡时温度调致作业指导书规定范围内,由IPQC确认后方可作业,焊锡次数 不可超过两次焊锡时间控制在1-1.5S。
2,焊锡人员指甲不可超过2MM,焊锡时指甲不可掐着PVC。
产生不良;短路、耐压不良。
三、短路:正负极两者间有金属(锡渣)或铜丝相连。
产生原因:正负极间有锡渣、锡尖、游离丝。
(原材料)四、焊点高 /大:根据该机种模具大小而定,但需保证不可有烫伤PVC、爆锡、露锡现象。
产生原因:1,焊锡时温度过底不易上锡,多次焊锡锡点大。
2,铜钉本身不易上锡,多次焊锡锡点大。
3,焊锡时烙铁头上余锡太多,多次焊锡锡点大。
改善对策:1,焊锡时温度调致作业指导书规定范围内,由IPQC确认后方可作业,焊锡次数 不可超过两次2,将铜钉正负极进行打磨后再焊锡。
3,要及时对烙铁头上余锡用湿海棉进行擦拭,做到焊锡20个锡点进行擦拭一次 产生不良:爆锡、露锡、耐压不良、短路。
五、游离丝:焊锡时铜丝没有用锡包住所产生的多余铜丝。
产生原因:1,焊锡时铜丝太散产生游离丝。
2,焊锡时上锡太少有单铜丝没有用锡将其包住产生游离丝。
改善对策:1,焊锡时对铜丝散要先理铜丝再进行焊锡,并做好自主检查。
2,焊锡时所上锡需将铜丝完全包住。
产生不良:耐压不良、短路、露铜丝。
六、锡尖:锡点表面所形成的角。
产生原因:1,焊锡时烙铁头余锡太多,焊锡时形成锡尖。
2,焊锡机烙铁头温度太低,焊锡时形成锡尖。
改善对策:1,焊锡时要及时对烙铁头上余锡用湿海棉进行擦拭,做到焊锡20个锡点进行擦 拭一次。
焊锡问题点解决方案

锡焊工程的不良原因分析及改善对策(一)1.短路(SHORT)焊接设计不当,可由圆型焊垫改为椭圆形。
加大点与点之间的距离。
零件方向设计不当,如S0IC的脚如与锡波平行,便易短路,修改零件方向,使其与锡波垂直.自动插件弯脚所致,由于PCB规定线脚的长度在2mm以下(无短路危险时)及担心弯脚角度太大时零件会掉,故因此造成短路,需将焊点离开线路2mm以上.基板孔太大.钖与孔中穿透至基板的上侧而造成短路,故需缩小孔径至下影响零件装插的程度。
自动插件时,残留的零件脚太长,需限制在2mm以下.锡炉温度太低。
钖无法迅速滴回锡槽,需调高锅炉温度.轴送带速度太慢,锡无法快速滴回,需调快轴送带速度.板面的可焊性不佳,将板面清洁。
基板中玻璃材料溢出,在焊接前检查板面是否有玻璃物突出.阻焊膜失效,检查适当的阻焊膜和使用方式.板面污染,将板面清洁。
2.针孔及气孔(PINHOLES AND BLOwHOLES)外表上,针孔及气孔的不同在于针孔的直径较小,现于表面.可看到底部。
针孔及气孔都表现为焊点中有气泡.只是尚未变大王表层,大部分都发生在基板底郎,当底部的气泡完全扩散爆开前已冷凝时,即形成了针孔或气孔。
形成的原因如下:基板或零件的线脚上沾有有机污染物.此类污染材料来自自动插件面,零件存放及贮存不良因素。
用普通的溶剂即可轻易的去除此类污染物,但遇sILICOK0II类似含有SILICON的产品则较困难。
如发现问题的造成是因为SILICON OIL,则须考虑改变润滑油或脱膜剂的来源。
基板含有电铍溶液和,类似材料所产生之水气,如果基板使用较廉价的材料,则有可能吸入此类水气,焊锡时产生足够的热,将溶液气化而造成气孔装配前将基板在烤箱中烘烤,可以改善此间题。
基板储存太多或包装不当,吸收附近环境的水氟,故装配前需先烘烤。
助焊剂活性不够,助焊剂润湿不良.也会造成针孔及氧孔.助焊剂槽中含有水份,需定期更换助焊剂。
助焊剂水份过多,也是造成针孔及气孔的原因,应更换助焊剂.发泡及空压机压缩中含有过多的水份,需加装滤水器,并定期排水.预热温度过低,无法蒸发水氟或溶剂,基板一旦进入锡炉,瞬间与高温接解,而产生爆裂,故需调高预热温度.3.吃锡不良(POOR WETTING)现象为线路板的表面有部分未沾到锡,原因为:表面附有油脂、杂质氧化等,可以溶解洗净。
波峰焊锡作业中问题点与改善方法

A、发生了连焊但未检出。
B、锡液未达到正常工作温度,焊点间有“锡丝”搭桥。
C、焊点间有细微锡珠搭桥。
D、发生了连焊即架桥。
7.2FLUX的问题
A、FLUX的活性低,润湿性差,造成焊点间连锡。
B、FLUX的绝阻抗不够,造成焊点间通短。
7.3PCB的问题
同意楼上意见,一般焊锡厂家都有含铜的和不含铜的的焊锡,含铜的焊锡一般是在新炉子第一次使用是加入,以后PCB上的焊盘会溶解一部分铜进入焊锡中,铜含量上升,就要加不含铜的的焊锡了。如果铜含量太高(超过0.85%),就应该从炉中取出一部分焊锡后再加不含铜的焊锡。
波峰焊锡作业中问题点与改善方法
1.沾锡不良 POOR WETTING:
? 走板速度和预热配合不好。
? 手浸锡时操作方法不当。
? 链条倾角不合理。
? 波峰不平。
6焊点太亮或焊点不亮
? FLUX的问题:A .可通过改变其中添加剂改变(FLUX选型问题)
B. FLUX微腐蚀。
? 锡不好(如:锡含量太低等)。
7短 路
E、热风整平时过锡次数太多
2) FLUX中的一些添加剂能够破坏阻焊膜
3) 锡液温度或预热温度过高
4) 焊接时次数过多
5) 手浸锡操作时,PCB在锡液表面停留时间过长
15高频下电信号改变
1) FLUX的绝缘电阻低,绝缘性不好
2) 残留不均匀,绝缘电阻分布不均匀,在电路上能够形成电容或电阻。
3) 发泡槽的发泡区域过大
4) 气泵气压太低
5) 发泡管有管孔漏气或堵塞气孔的状况,造成发泡不均匀
6) 稀释剂添加过多
锡炉焊锡问题点的分析

锡炉焊锡问题点的分析1.沾锡不良:这种情况是不可接受的缺点,在焊点上只有部分沾此类污染物锡.分析其原因及改善方式如下:1.1外界的污染物如油,脂,腊,灰尘等,此类污染物通常可用溶剂清洗,此类污染物有时是在印刷防焊剂时沾上。
1.2SILICON OIL通常用于脱模及润滑之用,通常会在基板及零件脚上发现,并SILICON OIL不易清理,因此使用它要非常小心尤其当它做抗氧化油常会发生问题,因它会蒸发沾在基板上造成沾锡不良。
1.3因储存不良或基板制程上的问题发生氧化,助焊剂无法除去时沾锡不良,过两次锡焊或可解决此问题。
1.4喷助焊剂不良,造成原因为气压不稳定或不足,喷头坏或喷雾控制系统不良,致使喷助焊剂不稳或不均及时喷时不喷,使基板部分没有沾到助焊剂。
1.5PCB板吃锡时间不足或锡温不够会造成锡焊不良,因为熔锡需要足够的温度及时间WETTING,通常焊锡温度应高于熔点温度50℃--80℃之间,沾锡总时间为3秒。
2.局部沾锡不良:此一情形与沾锡不良相似,不同的是局部锡不良不会露出铜箔面.只有薄薄的一层锡无法形成饱满的焊点,波峰不平。
3.冷焊或焊点不亮焊点看似碎裂,不平,大部分原因是零件在焊锡正要冷却形成焊点时振动造成,注意锡炉运输是或优异常振动。
4.焊点破裂此一情形通常是焊锡,基板,导通孔及元件脚之间膨胀系数未配合造成,应在基板材质,元件材料及设计上去改善。
5.焊点锡量太大通常在评定一个焊点,希望能又大又圆又胖的焊点,但事实上过大的焊点对导电性及抗拉强度未必有所帮助。
5.1锡炉输送角度不正确会造成焊点过大,倾斜角度由1-7度依PCB板的设计方式调整,角度越大沾锡越薄,角度越小沾锡越厚。
5.2提高锡槽温度,加长焊锡时间,使多馀的锡再回流到锡槽,来改善。
5.3提高预热温度,可减少PCB板沾锡所需热量,曾加助焊效果。
5.4改变助焊剂比重,降低助焊剂比重,通常比重越高吃锡越厚越易短路,比重越低吃锡越薄越易造成锡桥,锡尖。
焊接不良的原因分析
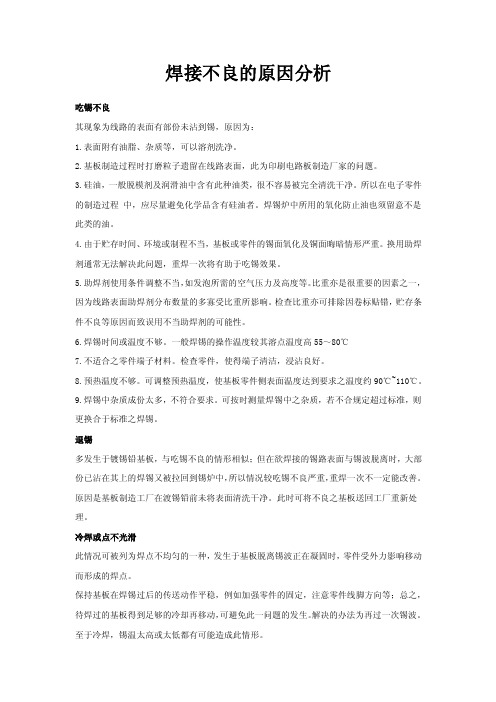
焊接不良的原因分析吃锡不良其现象为线路的表面有部份未沾到锡,原因为:1.表面附有油脂、杂质等,可以溶剂洗净。
2.基板制造过程时打磨粒子遗留在线路表面,此为印刷电路板制造厂家的问题。
3.硅油,一般脱模剂及润滑油中含有此种油类,很不容易被完全清洗干净。
所以在电子零件的制造过程中,应尽量避免化学品含有硅油者。
焊锡炉中所用的氧化防止油也须留意不是此类的油。
4.由于贮存时间、环境或制程不当,基板或零件的锡面氧化及铜面晦暗情形严重。
换用助焊剂通常无法解决此问题,重焊一次将有助于吃锡效果。
5.助焊剂使用条件调整不当,如发泡所需的空气压力及高度等。
比重亦是很重要的因素之一,因为线路表面助焊剂分布数量的多寡受比重所影响。
检查比重亦可排除因卷标贴错,贮存条件不良等原因而致误用不当助焊剂的可能性。
6.焊锡时间或温度不够。
一般焊锡的操作温度较其溶点温度高55~80℃7.不适合之零件端子材料。
检查零件,使得端子清洁,浸沾良好。
8.预热温度不够。
可调整预热温度,使基板零件侧表面温度达到要求之温度约90℃~110℃。
9.焊锡中杂质成份太多,不符合要求。
可按时测量焊锡中之杂质,若不合规定超过标准,则更换合于标准之焊锡。
退锡多发生于镀锡铅基板,与吃锡不良的情形相似;但在欲焊接的锡路表面与锡波脱离时,大部份已沾在其上的焊锡又被拉回到锡炉中,所以情况较吃锡不良严重,重焊一次不一定能改善。
原因是基板制造工厂在渡锡铅前未将表面清洗干净。
此时可将不良之基板送回工厂重新处理。
冷焊或点不光滑此情况可被列为焊点不均匀的一种,发生于基板脱离锡波正在凝固时,零件受外力影响移动而形成的焊点。
保持基板在焊锡过后的传送动作平稳,例如加强零件的固定,注意零件线脚方向等;总之,待焊过的基板得到足够的冷却再移动,可避免此一问题的发生。
解决的办法为再过一次锡波。
至于冷焊,锡温太高或太低都有可能造成此情形。
焊点裂痕造成的原因为基板、贯穿孔及焊点中零件脚等热膨胀收缩系数方面配合不当,可以说实际上不算是焊锡的问题,而是牵涉到线路及零件设计时,材料及尺寸在热方面的配合..另,基板装配品的碰撞、得叠也是主因之一。
上锡不良类型及原因分析
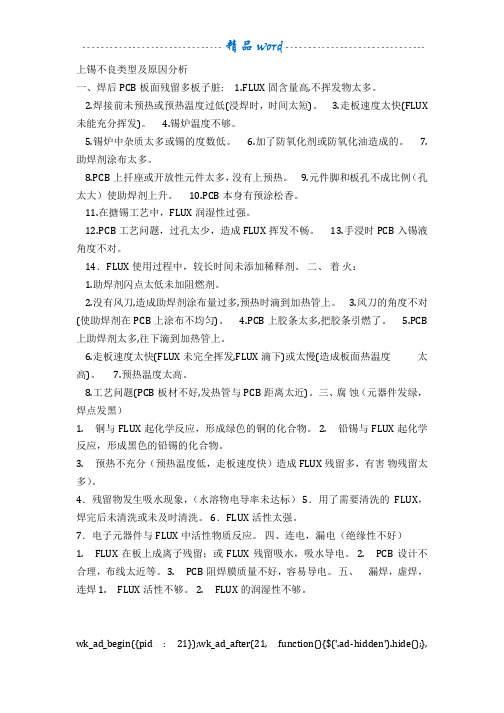
上锡不良类型及原因分析一、焊后PCB板面残留多板子脏: 1.FLUX固含量高,不挥发物太多。
2.焊接前未预热或预热温度过低(浸焊时,时间太短)。
3.走板速度太快(FLUX 未能充分挥发)。
4.锡炉温度不够。
5.锡炉中杂质太多或锡的度数低。
6.加了防氧化剂或防氧化油造成的。
7.助焊剂涂布太多。
8.PCB上扦座或开放性元件太多,没有上预热。
9.元件脚和板孔不成比例(孔太大)使助焊剂上升。
10.PCB本身有预涂松香。
11.在搪锡工艺中,FLUX润湿性过强。
12.PCB工艺问题,过孔太少,造成FLUX挥发不畅。
13.手浸时PCB入锡液角度不对。
14.FLUX使用过程中,较长时间未添加稀释剂。
二、着火:1.助焊剂闪点太低未加阻燃剂。
2.没有风刀,造成助焊剂涂布量过多,预热时滴到加热管上。
3.风刀的角度不对(使助焊剂在PCB上涂布不均匀)。
4.PCB上胶条太多,把胶条引燃了。
5.PCB 上助焊剂太多,往下滴到加热管上。
6.走板速度太快(FLUX未完全挥发,FLUX滴下)或太慢(造成板面热温度太高)。
7.预热温度太高。
8.工艺问题(PCB板材不好,发热管与PCB距离太近)。
三、腐蚀(元器件发绿,焊点发黑)1. 铜与FLUX起化学反应,形成绿色的铜的化合物。
2. 铅锡与FLUX起化学反应,形成黑色的铅锡的化合物。
3. 预热不充分(预热温度低,走板速度快)造成FLUX残留多,有害物残留太多)。
4.残留物发生吸水现象,(水溶物电导率未达标) 5.用了需要清洗的FLUX,焊完后未清洗或未及时清洗。
6.FLUX活性太强。
7.电子元器件与FLUX中活性物质反应。
四、连电,漏电(绝缘性不好)1. FLUX在板上成离子残留;或FLUX残留吸水,吸水导电。
2. PCB设计不合理,布线太近等。
3. PCB阻焊膜质量不好,容易导电。
五、漏焊,虚焊,连焊 1. FLUX活性不够。
2. FLUX的润湿性不够。
wk_ad_begin({pid : 21});wk_ad_after(21, function(){$('.ad-hidden').hide();},function(){$('.ad-hidden').show();});3. FLUX涂布的量太少。
焊锡不良的原因及对策

焊锡不良的原因及对策
焊锡不良是指在焊接过程中,焊锡未能完全覆盖被焊接的金属表面,或者焊锡与被焊接的金属表面粘合不良,导致焊点强度不足、易脱落、易出现短路等问题。
以下是焊锡不良的原因及对策:
1. 焊锡材料质量不良:焊锡材料中含有杂质或氧化物等不良物质,会影响其润湿性和流动性,导致焊锡不良。
对策是选择质量好的焊锡材料,并对其进行充分的清洗和干燥处理。
2. 焊接温度不当:焊接温度过高或过低都会导致焊锡不良。
过高的温度会使焊锡材料过度蒸发,导致焊接点强度下降;过低的温度则会使焊锡材料无法充分润湿被焊接的金属表面,导致焊锡不良。
对策是根据具体情况选择合适的焊接温度。
3. 焊接时间过短或过长:焊接时间过短会导致焊锡材料无法充分渗透到被焊接的金属表面,导致焊锡不良;焊接时间过长则会使焊锡材料过度熔化,导致焊点强度下降。
对策是根据具体情况选择合适的焊接时间。
4. 助焊剂不足或使用不当:助焊剂能够提高焊锡材料的润湿性和流动性,从而减少焊锡不良的发生。
如果助焊剂不足或使用不当,就会
导致焊锡不良。
对策是选择质量好的助焊剂,并按照说明书使用。
5. 焊接工艺不当:如果焊接工艺不当,例如焊接顺序不合理、焊接顺序不连贯等,也会导致焊锡不良。
对策是根据具体情况选择合适的焊接工艺。
总之,焊锡不良的原因可能有很多,需要根据实际情况进行综合分析和判断,采取相应的对策来解决问题。
常见的焊锡炉不良的原因

常见的焊锡炉不良的原因焊锡炉是一种重要的电子元件焊接设备,其主要功能是熔化焊锡条提供熔融焊锡。
然而,由于长时间使用或其他原因,焊锡炉可能会出现一些不良情况。
以下是常见的焊锡炉不良的原因:1. 加热系统故障:焊锡炉的加热系统是保证焊锡炉正常运行的重要组成部分。
加热系统故障可能导致焊锡炉无法达到预设的温度。
这可能是由于加热元件损坏或温控器故障引起的。
如果温度控制不准确,焊锡炉温度可能过高或过低,影响焊接质量。
2. 焊头损坏:焊头是将热量传递到焊锡条的部件。
如果焊头损坏或磨损,可能无法提供足够的热量来熔化焊锡条。
这可能导致焊接不良,如焊接点不均匀,焊锡块等。
3. 温度控制不准确:焊锡炉的温度控制系统起着关键作用,确保焊接过程中的恒定温度。
如果温控器故障或校准不准确,焊锡炉可能无法保持所需的温度。
这可能导致焊接缺陷,如焊锡温度过高或过低,焊锡不易流动或过度流动等。
4. 焊锡条质量问题:焊锡炉使用焊锡条作为焊接材料,而焊锡条质量可能会影响焊接结果。
如果焊锡条含有过多的杂质或不均匀的成分,可能会导致焊接不良,如焊接点虚焊、焊缝不牢固等。
5. 使用不当:焊锡炉的使用者在操作时需要严格按照使用说明进行操作。
如果操作不当,可能导致焊锡炉故障。
例如,长时间超负荷使用焊锡炉,未按照规定进行维护保养等。
6. 电源问题:焊锡炉的电源是焊锡炉正常运行的基础。
如果供电电压不稳定或电源线路存在问题,可能导致焊锡炉无法正常工作。
这可能会影响焊接质量,如焊接点不牢固、焊锡不易流动等。
7. 设备老化:焊锡炉作为一种机械设备,随着使用时间的增加,可能会出现老化问题。
例如,电子元件老化、接触不良等,可能导致焊锡炉性能下降,影响焊接质量。
总结起来,常见的焊锡炉不良原因包括加热系统故障、焊头损坏、温度控制不准确、焊锡条质量问题、使用不当、电源问题和设备老化等。
为了确保焊接质量,需要及时发现并处理这些问题,修复或更换有问题的部件,并进行定期的维护保养工作。
- 1、下载文档前请自行甄别文档内容的完整性,平台不提供额外的编辑、内容补充、找答案等附加服务。
- 2、"仅部分预览"的文档,不可在线预览部分如存在完整性等问题,可反馈申请退款(可完整预览的文档不适用该条件!)。
- 3、如文档侵犯您的权益,请联系客服反馈,我们会尽快为您处理(人工客服工作时间:9:00-18:30)。
锡炉焊锡问题点的分析1.沾锡不良:这种情况是不可接受的缺点,在焊点上只有部分沾此类污染物锡. 分析其原因及改善方式如下:1.1 外界的污染物如油,脂,腊,灰尘等,此类污染物通常可用溶剂清洗, 此类污染物有时是在印刷防焊剂时沾上.1.2 SILICON OIL通常用於脱模及润滑之用,通常会在基板及零件脚上发现, 并SILICON OIL不易清理,因此使用它要非常小心尤其当它做抗氧化油常会发生问题,因它会蒸发沾在基板上造成沾锡不良.1.3 因储存不良或基板制程上的问题发生氧化,助焊剂无法除去时沾锡不良,过两次锡焊或可解决此问题. 1.4 喷助焊剂不良,造成原因为气压不稳定或不足,喷头坏或喷雾控制系统不良,致使喷助焊剂不稳或不均及时喷时不喷,使基板部分没有沾到助焊剂.1.5 PCB板吃锡时间不足或锡温不够会造成锡焊不良,因为熔锡需要足够的温度及时间WETTING,通常焊锡温度应高於熔点温度50 ℃--80 ℃之间,沾锡总时间为3秒.2.局部沾锡不良:此一情形与沾锡不良相似,不同的是局部锡不良不会露出铜箔面.只有薄薄的一层锡无法形成饱满的焊点,波峰不平.3.冷焊或焊点不亮焊点看似碎裂,不平,大部分原因是零件在焊锡正要冷却形成焊点时振动造成,注意锡炉运输是或优异常振动.4.焊点破裂此一情形通常是焊锡, 基板,导通孔及元件脚之间膨胀系数未配合造成,应在基板材质, 元件材料及设计上去改善.5.焊点锡量太大通常在评定一个焊点,希望能又大又圆又胖的焊点,但事实上过大的焊点对导电性及抗拉强度未必有所帮助.5.1 锡炉输送角度不正确会造成焊点过大,倾斜角度由1—7度依PCB板的设计方式调整,角度越大沾锡越薄, 角度越小沾锡越厚.5.2 提高锡槽温度,加长焊锡时间,使多馀的锡再回流到锡槽.来改善5.3 提高预热温度,可减少PCB板沾锡所需热量,曾加助焊效果.5.4 改变助焊剂比重,降低助焊剂比重,通常比重越高吃锡越厚越易短路, 比重越低吃锡越薄越易造成锡桥,锡尖.6.锡尖(冰柱)此一问题通常发生在DIP或WIVE的焊接制程上,在电子元件脚顶端或焊点上发现有冰尖般的锡.6.1 PCB板的可焊性差, 此一问题通常伴随著沾锡不良,应从PCB板的可焊性去探讨,可试由提升助焊剂比重来改善6.2 PCB板上金道(PAD)面积过大,可用绝缘(防焊)漆线将金道分隔来改善, 绝缘(防焊)漆线在大金道面分隔成5mm乘10mm区块.6.3 锡槽温度不足吃锡时间太短,可用提高锡槽温度,加长焊锡时间,使多馀的锡再回流到锡槽来改善.6.4 PCB板出波峰後之冷却风流角度不对,不可朝锡槽方向吹,会造成锡点急速冷却,多馀焊锡无法受重力於内聚力拉回锡槽.6.5 手焊时产生锡尖,通常为烙铁温度太低,致锡温度不足无法立即因内聚力回缩形成焊点. 可用提高烙铁温度,加长焊锡时间.7.防焊绝缘漆留有残锡7.1 PCB板制作时残留物与助焊剂不相容的物质,在预热之後熔化产生粘性粘著焊锡形成,可用丙酮(已被蒙特娄公约禁用之化学溶剂)氯化烯类等溶剂来清洗,若清洗後还是无法改善,则PCB板的层材CURING不正确的可能,本项事故应即使回馈PCB板供应商.7.2 不正确的PCB板CURING会造成此一现象,可在插件前先进行烘烤120℃两小时, 本项事故应即使回馈PCB板供应商.7.3 锡渣被PUMP打入锡槽内再喷流出来, 造成PCB板面沾上锡渣,此一问题较为单纯良好的锡炉维护,锡槽正确的锡面高度.8.白色残留物在焊接或溶剂清洗过后发现有白色残留物在基板上,通常是松香的残留物,这类物质不会影响表面电阴质,但客户不接受.8.1 助焊剂通常是此问题主要原因,有时改用另一种助焊剂即可改善,松香类助焊剂常在洗时产生白班,此事最好的方式是寻求助焊剂供应的协助,产品是他们供应他们较专业.8.2 基板制作过程中残留杂质,在长期储存下亦会产生白斑,可用助焊剂或溶剂清洗即可.8.3 不正确的CURING亦会造成白班,通常是某一批量单独产生,应及时回馈基板供应商并使用助焊剂或溶剂清洗即可.8.4 厂内使用之助焊剂与基板氧化保护层不相容,均发生在新的基板供应商,或更改助焊剂厂牌时发生,应请供应商协助.8.5 因基板制程中所使用之溶剂使基板材质变化,尤其是在镀镍过程中的溶液常会造成此问题,建义储存时间越短越好.8.6 助焊剂使用过久老化,暴露在空气中吸收水氧劣化,建义更新助焊剂(通常发泡式助焊应每周更新,浸泡式助焊剂每两周更新,喷雾式每月更新即可).8.7 使用松香型助焊剂,过完焊锡炉候停放时间太久才清洗,导致引起白班尽量缩短焊锡与清洗的时间即可改善.8.8 清洗基板的溶剂水分含量过高,降低清洗能力并产生白班应更新溶剂.9.深色残馀物及浸蚀痕迹:通常黑色残馀物均发生在焊点产底部或顶端,此问题通常是不正确的使用焊剂或清洗造成.9.1 香型助焊剂焊接后未立即清洗,留下黑褐色残留物,尽量提前清洗即可.9.2 性助焊剂留在焊点上造成黑色腐蚀颜色,且无法清洗,此现象在手焊中常发现,改用较弱之助焊剂并尽快清洗.9.3 剂在较高温度下烧焦而产生黑班,确认锡槽温度,改用较可而高温的助焊助即可.10.绿色残留物:绿色残留物是腐蚀造成,特别是电子产品并非完全如此,因为很难分辨到底是绿銹或是其他化学产品,但通常来说发现绿色物质应为警讯,必须立刻查明原因,尤其是此种绿色物质越来越大,应非常注意,通常可用清洗来改善.10.1 腐蚀的问题通常发生在裸铜面或含铜合金上,使用非松香性助焊剂,这种腐蚀物质内含有离子因此呈绿色,当发现绿色腐蚀物,即可证明是在使用非松香助焊剂後未正确清洗.10.2 COPPER ABIETAES是氧化铜与ABIETIC ACID(松香主要成分)的化合物,此一物质是绿色但绝不是腐蚀物且具有高绝缘性,不影响品质但客户不会同意应清洗.10.3 PRESULFATE的残馀物或PCB板制作上类似残馀物,在焊锡後会产生绿色残馀物,应要求PCB板制作厂商在PCB板制作清洗後再做清洁度测试,以确保PCB板清洁度的品质.11.白色腐蚀物:第八项谈的是白色残留物是指PCB板上白色残留物,本项目谈的是零件脚及金属上的白色腐蚀物,尤其是含铅成分较多的金属上较易生成此残馀物,主要是因为氯离子易与铅形成氯化铅,再与二氧化碳形成碳酸铅(白色腐蚀物).在使用松香类助焊剂时,因松香不溶於水会将含氯活性剂包灼不致腐蚀,但如使用不当溶剂,只能清洗松香无法去出含氯离子,如此一来反加速腐蚀.12.针孔及气孔:针孔与气孔之区别, 针孔是在焊点上发现一小孔,气孔则是焊点上较大孔可看到内部,针孔内部针孔通常是空的,气孔则是内部空气完全喷出造成大孔,其形成原因是焊锡在未完全排除即已凝固,形成此问题.12.1 有机污染物CB板与元件脚都可能产生气体造成针孔或气孔,其污染源可能自自动插件机或储存状况不佳造成,此问题较为简单只要用溶剂即可,但如发现污染物为SILICONIL因其不容易被溶剂清洗,故在制程中应考庐其他代用品.12.2 PCB板有湿气:如使用较便宜的PCB板材质,或使用较粗的钻孔方式,在贯孔处容易吸收湿气,焊锡过程中受到高热蒸发出来造成,解决方法是放在烤箱中120℃烤二小时.12.3 电镀溶液中的光亮剂:使用大量光亮剂电镀时,光亮剂常与金同时沉积,遇到高温则挥发造成,特别是镀金时,改用含光亮剂较少的电镀液,党然这要回馈到供应商.13.残留油污氧化防止油被打入锡槽内经喷流涌出污染PCB板,此问题应为锡槽焊锡液面过低,锡槽内加焊锡即可改善.14.焊点灰暗:此现象分为二种:1. 焊锡过後一段时,(约半载至一年)焊点颜色转暗.2. 经制造出来的成品焊点即使灰暗的.14.1 焊锡内杂质:必须每三个月定期检验焊锡内的金属成分.14.2 助焊剂在热的表面上亦会产生某种程度的灰暗色,如RA及有机酸类助焊剂留在焊点上过久也会造成轻微腐蚀而呈灰暗色,在焊接後立刻清洗应可改善.14.3 在焊锡合金中,锡含量低者(如40/60焊锡)焊点亦较灰暗.15.焊点表面粗糙:焊点表面呈砂状突出表面,而焊点整体形状不改变.15.1 金属杂质的1 金属杂质的结晶:必须每三个定期检验焊锡内的金属成分.15.2 锡渣:锡渣被PUMP打入锡槽内经喷流涌出,因锡内有锡渣而使焊点表面有砂状突出,应为锡槽焊锡液面过低,锡槽内追加焊锡,并清理锡槽及PUMP即可改善.15.3 外来物质:如毛边,绝缘材质等藏在零件脚上,亦会产生粗糙表面.16.黄色焊点:焊锡温度过高造成,立即查看锡温及温控器是否故障.17.短路:过大的焊点造成两点以上焊点相连接.后的防焊油墨很难去除,当它沾到到焊接面时,只能以磨擦或工具除去,这种机械清洁法,普通被使用,但也较容易埋藏一些极小的粒子於PCB表面.以下将作进一步产说明.2.埋藏的粒子外来物质埋藏於焊接物表面也会影响润焊性,在软质的金属表面,使用磨石或研磨机,很容易将硬物嵌金属表面.这些非金属物质,顾然不能与锡铅合金焊接,也无法用助焊剂除掉.某此合成材料做的刷子,也会造成类似问题这种情况最好的处理方法,是用化学药品进行整面的蚀刻(ETCHING),除去非金属的杂质.这些蚀刻药都是很强的化学物质,必须妥善管制,最好能询问PCB供应厂详细的使用技术.3.矽利康油矽利康油虽然如上述第一点所提到,是种外界的污染,但因安独特的性质,所以另外讨论.矽合成物由於其附著力强,被用来当作润滑剂或粘著剂,一旦被合成物污染,即使薄薄的一层,没有任何溶剂可以有效的清除.因引矽的合成物被认为是焊锡润焊的最大障碍.造成矽污染的原因很多,包装塑胶袋由於使用矽来作为生产脱模剂,而被认为是一大污染.近来有很多的安全塑胶包装已经改善此一问题,但还是要注意选择.另一来源则是过锡前所涂的散热剂.厂内矽合成物的使用,虽然达离焊锡流程,但由於人员手接触的“传染”,很快会布满焊锡流程,所以要特别注意.目前为止还没有清除矽油的办法,唯一的办法就是尽量保持干净和严格的控制.4.严重氧化膜PCB焊锡表面的氧化膜不能被助焊剂彻底清除,也是造成润焊不良的来源之一, 金属表面只要接触空气,氧化膜就会形成,但是轻微的氧化膜可以轻易的被助焊剂清除,但PCB储存不当或制造流程不良,都会造成相当严重的氧化,让助焊剂也无可奈何.以下列举一些简单的解决方法供参考:通常活性较强的助焊剂有较强的清洁能力,可以帮助去严重的氧化膜,但活性强的助焊剂只能针对某些特殊的使用,并不能适合全部的PCB,使用这类“超规格”的助焊剂接后,尤其要注意其残留物对PCB品质的影响,必须列表追踪.PCB可用较强的助焊剂先过行喷锡或滚锡(PRETIN)作业,然后再以水或溶剂清洗,即先藉由强活性助焊剂去除严重氧化膜后,再以锡后覆,防止氧化.可能化学溶剂进行蚀刻,即用强酸类的溶液,适当稀释后擦拭氧化线路,然后马上插件过锡.使用这类溶液於PCB表面,若不马上过锡,会造成PCB更严重的氧化,过锡后的PCB也要列表追踪.助焊剂本身污染,活性不够或操作方式不对,也不能有效的去除氧化膜,所以也要列入评估.过锡时间不够或预热温度不够,会使助焊剂不够时间清除氧化膜,若能延长进锡时间及加强预热效果,绝对有助於氧人膜的除去.锡球和锡桥(SOLDER WEBBING)形成的地点不同,锡球大多数发生在PCB的零件面,而锡桥则发生在焊锡面(SOLDER SIDE)因这些油墨过锡时有一段软化过程,也容易沾锡球.把锡球推挤出PCB表面的“反应机构”与吹气孔(BLOW HOLES)的形成非常类似.只是两者气体形成的时间不一样.以锡球的形成而言,焊孔内大量的气体快速形成而急於挥发,此时焊孔顶端的熔锡还未凝固,所以锡球较容易从顶端冲出,而不易从底端形成吹气孔(BLOW HOLES)或锡洞(EMPITIES).相反的以吹气孔而言,孔内气体生较慢且较少,当要往上挥发时,焊孔顶端的锡已凝固,所以只能从底部未干的熔锡冲出,而形成锡洞.大部分锡球的生都是PCB过锡时,未干的助焊剂挥发(稀释剂)或助焊剂含水量过高.当瞬间接触高温的熔锡时,气体体积大量膨胀,造成锡爆发.爆发的同时,锡就补喷出,而形成锡球.1.锡球发生之原因很多的助焊剂配方中,多少都参入微量的水,但这微量的不还不致与引起锡球,当锡球突然发生时,可能是以下原因所造成的:* PCB预热不够,导致表面的助焊剂未干.* 助焊剂的配方中含水量过高.* 压缩气体中有水.* 不良的贯穿孔.* 工厂环境温度过高.2.焊接过程中湿气或水气过多,可能来自以下几项原因:* 满装助焊剂的桶(200E 或20E ,暴露在雨中时,水气会聚集在桶口周围,当温度变化时,会把水气从松动的开口处吸入桶内.所以要随时检查助焊剂桶的开口是否紧开,对助焊剂的储存是很重要的.* 在发泡过程中,空气压缩机会夹带大量的水气及油污进入发泡槽内,所以加装水筛检程式,定时放水,放油检查是必要的工作.* 制造流程中要注意是否有湿的零件或工具参与其中,要尽量避免.* 使用气刀作业,除了帮忙预热之不足外,更可预防夹具(FINGER) 夹带水分回来,而污染发泡横.锡球发生时,修补的程式和锡桥相同,只是零件面有很多零件阻档,更难以用刷子的方式除去.检查时必须小零件下面锡球,因他们常隐藏起来不易发现.锡球是焊锡过程中任何时间都可能发生的缺点,了避免它预防是唯一可靠的措施.冷焊的定义是焊点表面不平滑,焊点表面呈沙状及裂纹,冷焊是焊点凝固过程中,零件与PCB相互移动所形成这种相互移动的过程,影响锡铅合金的结晶过程,降低了整个合金的强度,当冷焊严重时,焊点表面会放生裂逢或断裂.1.造成冷焊的原因,有一列几种来源:* 输送轨道的皮带振动.* 机械轴承或马达转动不平衡.* 抽风设备或电扇风力过大.PCB过锡后,保持输送轨道的平稳,让锡铅合金固化的过程中,达到完美的结晶,当冷焊发生时可用补焊的方式整修,若冷焊严重时,则可考虑重新过一次锡.有关於零件的振动而影响焊点的固化,使焊点表面不平整或外形不完全的情况.各公司工程部可以设立焊点的外观标准,让参与焊锡作业人员有判断的依据.焊点不完整,在电子界流传使用的名称很多,如吹氮孔、针孔、锡落或空洞.在往后的说明中,我们将分别地讨论这些缺点,并依其不同的特性来解释我们的观点,所以焊点不完整可以分焊孔锡不足或贯穿孔壁润焊不良二类来加以定义.1.焊孔锡不足(UNFILLES HOLES)在单层板、双层板、多层板、焊点四周360度都没有被锡包裹.2.贯穿孔润焊不良(POOL SOLDER RISR)锡没有完全润焊到孔壁顶端.此情发生在双面或多层板(PTH),当新的PCB设计完成,第一次过锡时,此问题的追踪更加复杂.若是设计完善生已经很稳定的PCB及焊锡流程,发现这些问题可循以下的专案,琢一检查,改善.但讨论以下的专案以前,必须先完成机器及材.例如:温度、速度、助焊剂、焊锡等.确定问题不是来自机器及材料时,则是循下列专案再做检查.A 锡不足, 发生原因可归类如下:1.零件及PCB本身焊锡性不良.2.贯穿孔里面不干净.3.防焊油墨流入贯穿孔内或沾到铜线路表面(单层板).4.零件孔及零件脚的比率不正确(零件孔太大或零件脚太细)5.锡波不稳定或输送带振动.B 贯穿孔壁有断裂或有杂物残留1.零件及PCB本身的焊锡性不良.2.贯穿孔壁有断裂或有毁物残留.3.贯穿孔受到污染.4.助焊剂因过度受热而没有活性.当以上这些问题发生在某几批零件或PCB时,可以查看并比较其他批次的零件或PCB,找出其差异性,或其上游厂商有制造流程是束有更动.当问题重复发生在某此特定的零件时,可能是当初的设计没有考虑平衡问题.即PCB焊点温度分布不衡所导致.从此观点中可以暸解多层板更须要特别的预温度处理.热量尤其要传达到贯穿孔顶端,因若有焊点不完整的情况时,以多层板而言,必将不能接受至於贯穿孔的锡位商度各厂视品的要求应该要有自已标准.以双层板而言.IPC规定贯穿孔顶点有锡位高度可以允许25%的下落(以PCB的厚度标准),但虽然下落25%其贯穿孔壁四周必须完全润焊才算通过,若以多层板而言,很多厂商则规定,贯穿孔必须完全补满才可.包锡的定义是焊点的四周被过多的包覆而不断定其是否标准焊点过多锡隐藏了焊点和PCB间润焊(WETTING)的曲度,它也可能覆盖零件脚该露出的部分,使肉眼看不到.而且多馀的锡并不能加强焊接物的牢固度或导电度,只是浪费锡能了.第间电子公司必须有一套适合自已的品或焊锡流程的作业指南,其中必须规定每一颗焊点最大的吃锡量.总之焊点的表面,顶端及底部必须润焊良好,成弧度标准的锥状.A 造成包锡的原因:1.过锡的深度不正确.2.预热或锡温不正确.3.助焊剂活性与比重的选择不当.4.PCB及零件焊锡性不良.5.不适合的油脂物脂夹混在焊锡流程里.6.锡的成份不标准或已经严重污染.(有害的微量金属元素,如铜、铝等).当发现包锡时,必须把它排除,最有效率的方法是再这一次锡,但必须让PCB静置4-6小时,让PCB树脂结构能恢复强度.若太快过两次锡,则会造成热破坏(HEAT DAGAME).包锡的发生会最严重地影响品的敏感度.它会掩盖焊锡缺点,不论是机械强度,电器特性,或标准外观都会造成令人头疼的问题,所以没有任何焊锡标准能允许严重的包锡发生.冰柱这名词可以非常贴切地形容焊点形状.其发生的原因是当溶锡接触被焊物时,因温度大量浪失急速冷却,来不及达成润焊(WETTING)的任务,而拉成尖锐如冰柱之形状,它们常发生在锡波焊接(WAVE SOLDER).浸锡焊接(DIP SOLDER),手浸焊接(TOUCHUP)的流程,其造成原因右归类如下:1.手焊: 当用烙铁手焊时,焊点及烙铁尖端有小旗状发生,这是国为温度传导不均造成锡急剧冷却所致也就是烙铁热供应更大的烙铁热含量较高,温度稳定的富,铁或改用接触面较大的烙铁头,烙铁尖端保持干净,适当的焊锡线,正确的手焊技术,也有助於解决冰柱的问题.2.波峰焊接及浸锡焊接以自动锡所造成的冰柱,其原因相当复杂,除了温度传导问题外,其他如焊锡性;设计及机劋设备也会有影响.以下让我们琢一讨论:A 温度传导:a)机器设备或使用工具温度输出不均衡.b)PCB表面太大的焊接面设计,或密集的焊接物,过锡时会局部吸热造成热传导不均匀.c)太重的金属零件吸热.B 焊锡性:a)PCB或零件本身的焊锡性不良.b)助焊剂的活性不够,不足以润焊.C 设计:a)零件脚与零件孔的比率不正确.b)没插零件的贯穿孔(PTH)太大.c)PCB表面焊接区域太大时,造成表面熔锡凝固慢,流动性大.D 机器设备:a)PCB过锡太深.b)锡波流动不稳定.c)手动或自动锡的锡渣或浮悬物.d)解决冰柱的方法道先须判断其来源.温度传导及机器设备的问题可以用检测的方法调整;设计的问题则必须改善原始设计,或以手焊业克服.至於焊锡性不良,则必须用其他方法解决.锡桥发生时会造成PCB短路,其原因可能来自吃锡过剩(EXCESS SOLDER).但造成短路的原因不单纯是架桥而已,问题可能发生在PCB防焊油墨包覆下的金属线路.或零件本身(第十节将会提到).当短路因PCB表面焊点与焊的相连才定度架桥.架乔主要起因於PCB线路设计、焊锡材料或机器设备.1.PCB的设计?PCB焊接面没有考虑锡流的排放(没有按照PCB设计标则),所以当锡流经时,易造成堆积而形成架桥.?PCB过锡后,焊点或其他焊接线未干生熔锡流动,沾到邻近的焊点或线路而形成.?PCB线路设计太接近.零件弯脚不规或零件脚彼此太接近.2. 焊锡材料?PCB或零件脚有锡或铜等金属之杂物残留.?PCB或零件脚焊锡性不良.?助焊剂活性不够.?锡铅合金受到污染.3. 机器设备?过热不够.?锡波表面冒出浮渣.?PCB浸锡太深.?当发现架桥时,可用用焊分离.短路(SHORT CIRUIT)通常简称SHORT,有此短路是发生在PCB防焊油里面的线路.当发生在零件与零件相互接触,这些现角形成的短路不能与架桥(BRIDGING)混一谈,发生短路时PCB本身的动能得不到政党发挥,此时可以由各种自动测试信劋检测,并加以校正,但PCB若是因温度的变化、振动或冲击而有间歇性的短路发生时,就很难正确的检测其位置,当碰到这类间歇性短路的情况时可以根据以下不同的情况来过行分析与检查.1.短路发生在防焊油墨包覆下的线路此原因的发生主要是PCB底层线路作镀锡或喷锡加工时,镀锡遇厚因镀锡时,有此镀锡会再次被250℃的溶锡所熔化,而四处流动(REFLOW),大部分是流到底部,当镀锡被熔化的肯瞬间,PCB本身的材质及防焊油发生很大的张力,导致溶融状态的锡生移动,这瞬间的张力失扒挤常会把锡挤到邻近金属线路上,而造成短路,这种情况经常发生在线路设计很近的妇层板或SMT板.a)PCB镀锡或喷锡作业时,尽量减不锡的厚度,这种方法右以降低焊油墨包覆下锡的含量.b)PCB线路设计时,尽量拉开线路.c)新包覆防焊油墨,这是标准的处理方法.2.短路发生在零件与零件之间这是设计问题或加工程式不良所致A. 设计问题1.露出的线路太靠近焊点顶端.2.金属零件或脚线(LEAD WIRE)太靠近露出的线路.零件或脚线本身互相接触.B 加工程式1.锡波振动太严重.2.焊锡时生锡的气爆(OUT GASSING).3.锡膏作业(IR REFLOW)或锡波作业(SOLDER WAVE)生锡球.短路若发生在零件本身时,非常不容易找出原因,目前只有X光技术可以解决,但是速度慢且昂贵,不符经济效益,发生时只有把零件更换或修理才能解决.。