041.2毛坯件通用技术条件 铸钢件
毛坯铸钢件检验规范

液体渗透检验试验方法
JB/T 6440
阀门受压铸钢件射线照相检测
ISO 15156 石油天然气工业—油气开采中含硫化氢环境中使用的材料
4 订货须知
4.1 本规范是本公司签发的采购订单、零件图相配套的文件,供方提供的零件必须同时也 满足本规范的要求;
4.2 采购订单或零件图上的要求与本规范不一致时,应优先满足采购订单及零件图的要 求;
摆锤(V 形缺口)冲击试验。
b) 一项冲击试验至少以 3 个试样为一组,应以最终热处理条件下,每批炉号材料的代
表性试棒进行试验。试样的尺寸设计和加工按 A703/A703M 图 11 规定。
注:设计标准或地方要求,允许在高于-29℃(-20ºF)的最低设计温度时做冲击试验。
c) 冲击试验应按管道设计标准在最低温度下进行。
棒取法应遵守 1/4T 的原则,试棒加工按 A703/A703M 图 4 规定。
5.3.2 拉伸和弯曲试验的力学性能应符合本规范表 1(另附)要求; 5.3.3 冲击韧性试验是在客户有需要时做,但注意下列事项:
a) 用于规定设计温度低于-29℃(-20ºF)的碳钢承压件应按 ISO148-1 或 ASTM A370 进行
5.2.化学成份应符合本规范表 1(另附)要求;其偏差应符合表 2 要求,该偏差可取得买方
同意。
表 2 铸钢件化学成份分析允许偏差
元素 C Mn Si P
范围 5%
≤0.65 ≥0.65 ≤1.00 ≥1.00 ≤0.60 ≥0.60
全部
允许偏差 %
0.03×C+0.02 0.04
0.08×Mn+0.01 0.09
检验,并满 足标准要求 8.2 铸件交货时应提供的质量文件 a)材料标准和牌号; b) 炉号; c) 化学分析结果; d) 机械性能试验和硬度测试结果; e) 热处理方法及温度记录曲线图; f) 采购合同要求的其他补充试验结果,如冲击试验、金相分析、宏观浸蚀试验、硬度和
铸件通用技术要求

铸件通用技术要求
铸件表面上不允许有冷隔、裂纹、缩孔和穿透性缺陷及严重的残缺类缺陷(如欠铸、机械损伤等)。
铸件应清理干净,不得有毛刺、飞边,非加工表明上的浇冒口应清理与铸件表面齐平。
铸件非加工表面上的铸字和标志应清晰可辨,位置和字体应符合图样要求。
铸件非加工表面的粗糙度,砂型铸造R,不大于50μm。
铸件应清除浇冒口、飞刺等。
非加工表面上的浇冒口残留量要铲平、磨光,达到表面质量要求。
铸件上的型砂、芯砂和芯骨应清除干净。
铸件有倾斜的部位、其尺寸公差带应沿倾斜面对称配置。
铸件上的型砂、芯砂、芯骨、多肉、粘沙等应铲磨平整,清理干净。
对错型、凸台铸偏等应予以修正,达到圆滑过渡,一保证外观质量。
铸件非加工表面的皱褶,深度小于2mm,间距应大于100mm。
机器产品铸件的非加工表面均需喷丸处理或滚筒处理,达到清洁度Sa2 1/2级的要求。
铸件必须进行水韧处理。
铸件表面应平整,浇口、毛刺、粘砂等应清除干净。
1、铸件必须符合通用技术条件JB/T5000.6-1998的规定进行,尺寸公差C级,行为公差G 级
2、铸件不得有影响强度及外观的缺陷,要求进行探伤处理,安装受力处重点探伤,探伤按JB/T5000.14中Ⅲ级质量等级验收
3、铸件应进行正火处理消除内应力,然后进行机加工,铸件正火处理硬度169-217HB
4、调质处理241-286HB
5、所有油路必须仔细清洗
6、未注圆角R10-R15
7、棱角倒钝,未注倒角C2
8、各加工孔对称位置的偏差不大于0.2m。
铸造件等的通用技术要求

附表1拖拉机铸造件通用技术要求一、铸造件的通用技术要求1.1铸件内外表面不得有浮沙,不得有影响加工定位、装配的浇冒口残余、多肉、毛刺、飞边等缺陷;对于处于供气、供油、冷却、润滑、储油系统等的铸件内表面,应清理干净,不得有粘沙、毛刺、油漆堆积物、铁丸等存在。
1.2加工面上允许存在经机械加工可以消除的缺陷,铸件浇冒口残余、多肉高度,在非加工面上不大于1mm,加工面上不大于2mm。
1.3铸件上不允许有裂纹、冷隔等缺陷。
1.4铸件允许和不允许的缺陷,除按本标准规定外,特殊要求应在图样中另行规定。
1.5铸件工艺孔内及减轻铸件重量孔。
凹槽、筋等的拐角处,允许存在难以消除的毛刺和凸瘤,若影响加工定位和装配应在铸件图中注明。
1.6表面粗糙度应符合GB/T6060.1的规定,并按GB/T15056方法评定熔模铸造(精铸件)表面粗糙度不高于Ra12.5;其他铸造表面应达到Ra25的规定。
1.7未提及的要求按国家标准执行:球墨铸铁件验收技术条件;灰铸铁件验收技术条件;熔模铸件验收技术条件;铸造碳钢件验收技术条件。
1.8铸件涂层外观质量要求:采用环氧防锈底漆喷涂,漆膜平整均匀、颜色一致,不允许出现流挂、局部积漆、露底、磕碰划伤等漆膜弊病。
1.9以双方认定的产品图纸为依据,进行生产验收。
附表2拖拉机铸造件配套产品明细表序号产品名称产品图号标识材质重量(kg) 包装要求123456789101112131415备注:铸造件要符合铸造件通用技术要求。
(见铸造件通用技术要求)附表1拖拉机机械加工件通用技术要求一、机械加工件的通用技术要求1.1产品加工应符合图样及有关技术文件的规定,图样及有关技术文件未注明的按本标准要求规定执行。
1.2毛坯须经检验合格后,可投于加工,加工件不得有铸造的砂眼、缩松、裂纹等铸造缺陷。
1.3零件热处理后表面处理加工件光泽应均匀一致,零件表面不应有退火、烧伤、裂纹等热处理缺陷1.4零件加工表面不应有磕、碰、拉伤、锈蚀、和变形等降价零件使用性能与寿命的缺陷,其外露部分不得有影响外观的上述缺陷。
机车车辆用球墨铸铁件通用技术条件
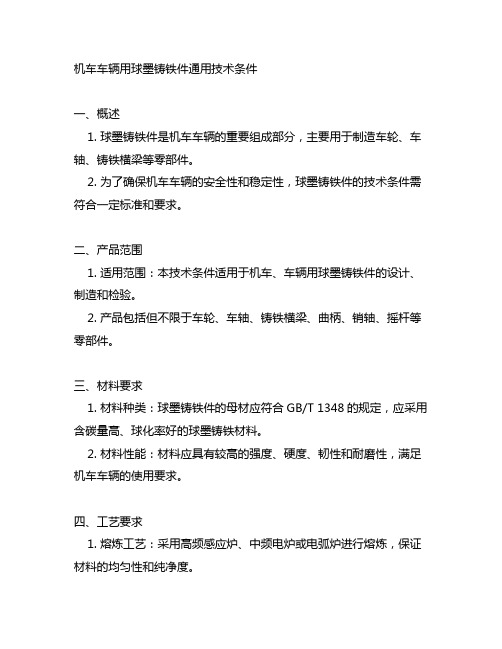
机车车辆用球墨铸铁件通用技术条件一、概述1. 球墨铸铁件是机车车辆的重要组成部分,主要用于制造车轮、车轴、铸铁横梁等零部件。
2. 为了确保机车车辆的安全性和稳定性,球墨铸铁件的技术条件需符合一定标准和要求。
二、产品范围1. 适用范围:本技术条件适用于机车、车辆用球墨铸铁件的设计、制造和检验。
2. 产品包括但不限于车轮、车轴、铸铁横梁、曲柄、销轴、摇杆等零部件。
三、材料要求1. 材料种类:球墨铸铁件的母材应符合GB/T 1348的规定,应采用含碳量高、球化率好的球墨铸铁材料。
2. 材料性能:材料应具有较高的强度、硬度、韧性和耐磨性,满足机车车辆的使用要求。
四、工艺要求1. 熔炼工艺:采用高频感应炉、中频电炉或电弧炉进行熔炼,保证材料的均匀性和纯净度。
2. 浇注工艺:采用自动化、精密化的浇注设备进行铸造,保证铸件的密度和无气孔、夹渣等缺陷。
五、外观要求1. 表面平整度:表面不得有明显的凹凸、裂纹等缺陷,保证外观质量。
2. 表面清洁度:表面不得沾有铁屑、油污等杂质,保证铸件的清洁度。
六、尺寸要求1. 全尺寸精度:按照设计要求进行尺寸检验,保证球墨铸铁件的准确性和稳定性。
2. 重量要求:球墨铸铁件的重量应符合设计要求,不得超过或低于标准重量。
七、机械性能要求1. 强度:球墨铸铁件的抗拉强度、屈服强度、延伸率等机械性能指标应符合相关标准。
2. 硬度:表面硬度和心部硬度应符合设计要求,保证零部件的使用寿命和稳定性。
八、表面质量检验1. 表面检验:采用目视、手感和放大镜等工具对球墨铸铁件的表面质量进行检验。
2. 探伤检验:采用超声波、X射线或磁粉探伤等技术对铸件进行内部缺陷检测。
九、检验方法1. 检验设备:应配备齐全的检测设备,包括硬度计、三坐标测量仪、金相显微镜等。
2. 检验程序:按照相关标准和规定执行检验程序,确保球墨铸铁件的质量可控。
十、贮存和包装要求1. 贮存条件:球墨铸铁件应存放在干燥、通风、无腐蚀性气体的仓库中。
知识篇——铸钢件的铸造技术要求及常见问题解析

知识篇——铸钢件的铸造技术要求及常见问题解析对于强度、塑性和韧性要求更高的机器零件,需要采用铸钢件。
铸钢件的产量仅次于铸铁,约占铸件总产量的15%。
一、化学成分分类按照化学成分铸钢可分为碳素铸钢和合金铸钢两大类。
其中以碳素铸钢应用最广,占铸钢总产量的80%以上。
1、碳素铸钢一般的,低碳钢ZG15的熔点较高、铸造性能差,仅用于制造电机零件或渗碳零件;中碳钢ZG25~ZG45,具有高于各类铸铁的综合性能,即强度高、有优良的塑性和韧性,因此适于制造形状复杂、强度和韧性要求高的零件,如火车车轮、锻锤机架和砧座、轧辊和高压阀门等,是碳素铸钢中应用最多的一类;高碳钢ZG55的熔点低,其铸造性能较中碳钢的好,但其塑性和韧性较差,仅用于制造少数的耐磨件。
2、合金铸钢根据合金元素总量的多少,合金铸钢可分为两低合金钢和高合金钢大类。
①低合金铸钢,我国主要应用锰系、锰硅系及铬系等。
如ZG40Mn、ZG30MnSi1、ZG30Cr1MnSi1等。
用来制造齿轮、水压机工作缸和水轮机转子等零件,而ZG40Cr1常用来制造高强度齿轮和高强度轴等重要受力零件。
②高合金铸钢,具有耐磨、耐热或耐腐蚀等特殊性能。
如高锰钢ZGMn13,是一种抗磨钢,主要用于制造在干磨擦工作条件下使用的零件,如挖掘机的抓斗前壁和抓斗齿、拖拉机和坦克的履带等;铬镍不锈钢ZG1Cr18Ni9和铬不锈钢ZG1Cr13和ZGCr28等,对硝酸的耐腐蚀性很高,主要用于制造化工、石油、化纤和食品等设备上的零件。
二、铸钢的铸造工艺特点铸钢的机械性能比铸铁高,但其铸造性能却比铸铁差。
因为铸钢的熔点较高,钢液易氧化、钢水的流动性差、收缩大,其体收缩率为10~14%,线收缩为1.8~2.5%。
为防止铸钢件产生浇不足、冷隔、缩孔和缩松、裂纹及粘砂等缺陷,必须采取比铸铁复杂的工艺措施:1、由于钢液的流动性差,为防止铸钢件产生冷隔和浇不足,铸钢件的壁厚不能小于8mm;浇注系统的结构力求简单、且截面尺寸比铸铁的大;采用干铸型或热铸型;适当提高浇注温度,一般为1520°~1600℃,因为浇注温度高,钢水的过热度大、保持液态的时间长,流动性可得到改善。
压铸件毛坯质量检验标准 (规范)
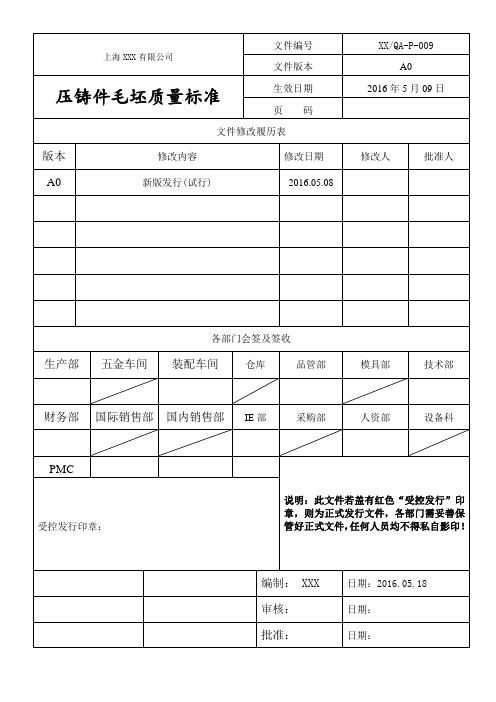
缺陷名称
缺陷范围
数值
备注
擦伤
深度(mm)
≤0.10
面积不超过总面积的百分数
5
凹陷
凹入深度(mm)
≤0.30
缺肉
深度(mm)
≤0.50
长度不大于(mm)
2
所在面上不允许超过的数量
2
离压铸件边缘距离(mm)
≥4
间距(mm)
≥10
网状毛刺
高度(mm)
≤0.2
2.1.2.4压铸件的浇口、飞边、溢流口、隔皮、顶杆痕迹等应清理干净。但允许留有痕迹。
2.1.6.2压铸件内部不允许有冷隔缺陷。
2.1.6.3压铸件内部允许有气孔、疏孔、夹杂等缺陷,但孔穴缺陷最大直径不超过壁厚的1/8,孔穴数量在任何剖面上不超过2个/cm2。
3.4.6.4重要压铸件的受力部位须进行解剖检查,符合表6中的规定。
表6压铸件指定解剖部位内部质量规定
孔穴平均直径mm
最多个数/cm2
2.技术要求
2.1压铸件质量要求
2.1.1压铸件应符合零件图样的规定。
2.1.2表面质量
2.1.2.1压铸件表面粗糙度应符合GB/T6060.1的规定。
2.1.2.2压铸件表面不允许有裂纹、欠铸、疏松、气泡和任何穿透性缺陷。
2.1.2.3压铸件表面允许有擦伤、凹陷、缺肉和网状毛刺等缺陷。但缺陷必须符合表1规定。
上海XXX有限公司
文件编号
XX/QA-P-009
文件版本
A0
压铸件毛坯质量标准
生效日期
2016年5月09日
页码
文件修改履历表
版本
修改内容
修改日期
修改人
铸件技术条件

铸件技术条件1、主题内容与适用范围1.1 本技术条件规定了电机铸件的类别加牌号、技术要求、验收项目和试验方法。
1.2 本技术条件适用于成批大量生产的中小型及分马力电机湿型铸造的灰铸铁和铝合金铸件,采用特种铸造工艺生产的铝合金铸件可参照本技术条件。
2、铸件的类别和牌号2.1 电机铸件分灰铁铸件和铝合金铸件两大类。
2.2 灰铁铸件按GB9439-88标准,采用牌号为HT150和HT200,其中HT150牌号为一般用途电机使用,HT200牌号为特殊环境条件电机使用。
2.3 铝合金铸件按GB1173-86标准,采用牌号为ZAlSi12,其代号为ZL102。
3、技术要求3.1 灰铁铸件的机械性能和硬度应符合表1的规定。
表1牌号铸件壁厚抗拉强度σb≥MPa硬度HB ≥≤HT150 2.5 10 175170~220 10 20 14520 30 13030 50 120HT200 2.5 10 220190~240 10 20 19520 30 17030 50 1603.2 铝合金铸件的机械性能和硬度应符合表2的规定。
表2牌号代号合金状态抗拉强度σb≥MPa延伸率σs≥%硬度ZAlSi2 ZL102F(铸态)143 4 50153 2T2(退火)133 4143 33.3 铸件的几何形状、基本尺寸应符合产品图样的要求。
3.4 铸件的精度等级、机械加工余量、尺寸偏差、重量偏差、铸型的拔模斜度以及铸件的圆角半径值应符合“铸件加工余量与毛坯公差”的规定。
3.5 铸件的表面质量应符合“电机铸件表面质量技术条件”的规定。
3.6 灰铸铁的机械性能以φ30mm单铸试棒的抗拉强度为合格依据,并符合表1的规定。
3.7 合格的灰铁铸件经清理后涂C06-1的醇酸铁红底漆,铝合金铸铁涂H06-2锌黄环氧底漆。
防锈底漆的粘度在20℃时用4#粘度计测定应不小于20秒。
4、验收规则和试验方法4.1 铸件的验收项目有:a)内在质量:机械性能、化学成份和金相组织;b)表面质量:表面粗糙度、表面缺陷和底漆质量;c)尺寸精度:加工余量、铸造斜度和重量上偏差。
铸件通用技术要求
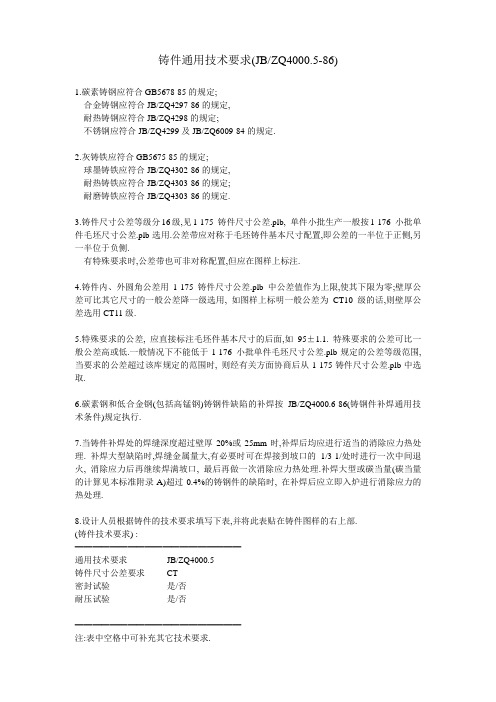
铸件通用技术要求(JB/ZQ4000.5-86)1.碳素铸钢应符合GB5678-85的规定;合金铸钢应符合JB/ZQ4297-86的规定,耐热铸钢应符合JB/ZQ4298的规定;不锈钢应符合JB/ZQ4299及JB/ZQ6009-84的规定.2.灰铸铁应符合GB5675-85的规定;球墨铸铁应符合JB/ZQ4302-86的规定,耐热铸铁应符合JB/ZQ4303-86的规定;耐磨铸铁应符合JB/ZQ4303-86的规定.3.铸件尺寸公差等级分16级,见1-175 铸件尺寸公差.plb, 单件小批生产一般按1-176 小批单件毛坯尺寸公差.plb选用.公差带应对称于毛坯铸件基本尺寸配置,即公差的一半位于正侧,另一半位于负侧.有特殊要求时,公差带也可非对称配置,但应在图样上标注.4.铸件内、外圆角公差用1-175铸件尺寸公差.plb 中公差值作为上限,使其下限为零;壁厚公差可比其它尺寸的一般公差降一级选用, 如图样上标明一般公差为CT10 级的话,则壁厚公差选用CT11级.5.特殊要求的公差, 应直接标注毛坯件基本尺寸的后面,如95±1.1. 特殊要求的公差可比一般公差高或低.一般情况下不能低于1-176 小批单件毛坯尺寸公差.plb规定的公差等级范围,当要求的公差超过该库规定的范围时, 则经有关方面协商后从1-175铸件尺寸公差.plb中选取.6.碳素钢和低合金钢(包括高锰钢)铸钢件缺陷的补焊按JB/ZQ4000.6-86(铸钢件补焊通用技术条件)规定执行.7.当铸件补焊处的焊缝深度超过壁厚20%或25mm时,补焊后均应进行适当的消除应力热处理. 补焊大型缺陷时,焊缝金属量大,有必要时可在焊接到坡口的1/3-1/处时进行一次中间退火, 消除应力后再继续焊满坡口, 最后再做一次消除应力热处理.补焊大型或碳当量(碳当量的计算见本标准附录A)超过0.4%的铸钢件的缺陷时, 在补焊后应立即入炉进行消除应力的热处理.8.设计人员根据铸件的技术要求填写下表,并将此表贴在铸件图样的右上部.(铸件技术要求) :━━━━━━━━━━━━━━━━━━━通用技术要求JB/ZQ4000.5铸件尺寸公差要求CT密封试验是/否耐压试验是/否━━━━━━━━━━━━━━━━━━━注:表中空格中可补充其它技术要求.。
灰铸铁、球墨铸铁件通用技术条件

灰铸铁、球墨铸铁件通用技术条件之阿布丰王创作1适应范围1.2铸件毛坯应符合图纸及有关技术文件的规定,图纸及技术文件未注明的按本技术条件的有关规定执行.2.概况质量2.1铸件概况不允许有冷隔、裂纹、铁豆、缩孔及影响外观的残缺类缺陷(如欠铸、机械损伤)2.2铸件的型砂、芯沙、芯骨、浇冒口和飞边应清除干净,非加工面的浇冒口残留、多肉、粘沙应铲磨平整2.3非加工面均需喷丸或滚筒处置.3.铸件毛坯公差按下表(单元mm)基本尺寸公差基本尺寸公差基本尺寸公差≤10±>63~100 ±3 >630~1000 ±>10~16 ±>100~160 ±>1000~1600 ±>16~25 ±>160~250 ±4 >1600~2500 ±>25~40 ±>250~400 ±>2500~4000 ±>40~63 ±>400~630 ±54、拔模斜度4.1起模斜度在铸件的加工面上时以增加铸件尺寸的形式,即基本尺寸定在起模斜度的小端4.2起模斜度在铸件的非加工概况上时以减少铸件尺寸的形式,即基本尺寸定在起模斜度的年夜端起模面高度≤10>10~40 >40~100 >100~160 >160~250 >25起模斜度≤2°55′1°25′40′30′25′25′正切值起模面高度>400~630 >630~1000 >1000~1600 >1600~2500 >2500起模斜度≤20′20′20′15′15′正切值mm,且不得与上表的公差值相加.6、加工余量6.1 确定回转体的加工余量时,基本尺寸可取其直径或高度中的较年夜值.6.3 直径小于50mm的孔可以不铸出.6.4 加工余量值见下表,表中每栏两个加工余量值,上面的数值以一侧为基准进行单侧加工的加工余量值;下面是双侧加工每侧的加工余量值..基本尺寸加工余量基本尺寸加工余量基本尺寸加工余量≤100 5 >250~400 >1000~1600 1512>100~1605 >400~630 11 >1600~2500 1713>160~250 86 >630~1000 1310>2500~4000 19157.内在质量要求7.1 铸件毛坯的机械性能应符合GB/T9439《灰铸铁件》和GB/T1348 《球墨铸铁件》的相应要求.7.2 铸件经加工的相对运动配合概况不得有缩松、气孔、沙眼和裂纹等缺陷存在.7.3铸件非外露的其它加工面上允许有轻微的缩松和非聚集的缺陷孔眼,其最年夜尺寸不年夜于4mm,深度不年夜于3mm 且不年夜于壁厚的1/4,在100mm×100mm范围内不很多于2个,相互间距或距边缘不小于10mm,且一个概况未几于10个.。
铸件铸造技术要求规范

铸件铸造技术要求规范(ISO9001-2015/IATF16949)1.0目的:规定本公司生产产品的原辅材料——铸件的技术要求、试验方法及规则。
2.0适用范围适用于公司产品用铸件。
3.0引用标准API 6A 井口装置和采油树设备规范GB/T 3077 合金结构钢4.0职责4.1技术部负责制定产品零件的铸件技术要求。
4.2质保部负责产品铸件的检验。
5.0程序5.1铸件分承压铸件和非承压铸件。
5.2铸造用钢应符合GB/T9439《灰铸铁件》、GB/T1348《球磨铸铁件》、JB/T4403《儒墨铸铁件》等的规定。
5.3用一般熔铸方法制造的铸件,其最高工作压力额定值应不大于70Mpa。
5.4铸造5.4.1 对承压铸件(如阀体、阀盖、四通、三通、法兰等)铸造厂必须制定熔炼铸造和热处理的作业文件,全部文件应保证承压铸件的质量,在成批生产前必须对首件进行严格的全面质量检查。
5.4.2 铸件的加工余量、尺寸公差及重量公差按GB/T 11350《铸件机械加工余量》、GB/T 11351《铸件重量公差》、GB 6414《铸件尺寸公差》执行。
特殊要求应在合同或图样上标出。
5.5焊补5.5.1 制造厂可对有缺陷的铸件,在热处理前进行焊补,选用焊条的强度应不低于被件补母材强度规定的最低值。
5.5.2 焊补抗硫化物应力开裂铸件的焊条,含镍量不得超过1%。
5.5.3 焊补应满足《焊接(补)工艺规范》的要求。
5.6热处理5.6.1 铸件必须进行时效处理,消除内应力。
5.6.2 铸件的热处理设备及工艺应符合《热处理检验规范》、《特殊过程控制程序》、《热处理工艺规范》要求。
5.7机械性能5.7.1 非承压铸件一般不作机械性能测试要求。
5.7.2 API 6A产品用铸件的机械性能应满足《金属材料机械性能试验规范》。
5.7.3 承压件需要进行机械性能测试时按5.7.2条执行。
5.8化学成份5.8.1 材料的化学成份应满足《铸钢件材料规范》要求。
铸件通用技术条件
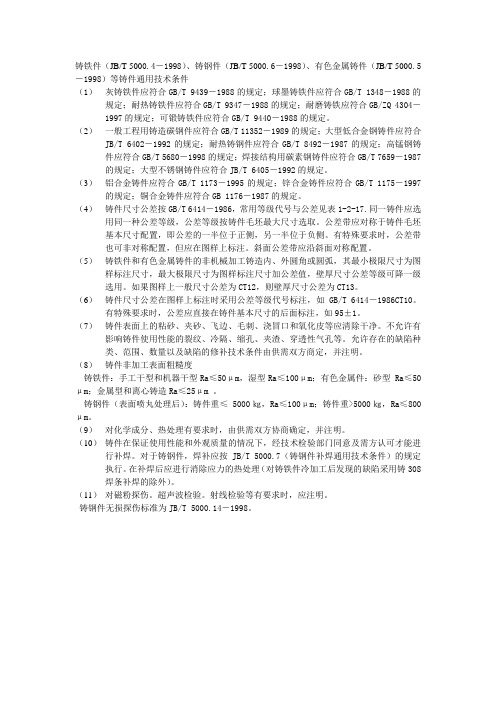
铸铁件(JB/T 5000.4-1998)、铸钢件(JB/T 5000.6-1998)、有色金属铸件(JB/T 5000.5-1998)等铸件通用技术条件(1)灰铸铁件应符合GB/T 9439-1988的规定;球墨铸铁件应符合GB/T 1348-1988的规定;耐热铸铁件应符合GB/T 9347-1988的规定;耐磨铸铁应符合GB/ZQ 4304-1997的规定;可锻铸铁件应符合GB/T 9440-1988的规定。
(2)一般工程用铸造碳钢件应符合GB/T 11352-1989的规定;大型低合金钢铸件应符合JB/T 6402-1992的规定;耐热铸钢件应符合GB/T 8492-1987的规定;高锰钢铸件应符合GB/T 5680-1998的规定;焊接结构用碳素钢铸件应符合GB/T 7659-1987的规定;大型不锈钢铸件应符合JB/T 6405-1992的规定。
(3)铝合金铸件应符合GB/T 1173-1995的规定;锌合金铸件应符合GB/T 1175-1997的规定;铜合金铸件应符合GB 1176-1987的规定。
(4)铸件尺寸公差按GB/T 6414-1986,常用等级代号与公差见表1-2-17.同一铸件应选用同一种公差等级,公差等级按铸件毛坯最大尺寸选取。
公差带应对称于铸件毛坯基本尺寸配置,即公差的一半位于正侧,另一半位于负侧。
有特殊要求时,公差带也可非对称配置,但应在图样上标注。
斜面公差带应沿斜面对称配置。
(5)铸铁件和有色金属铸件的非机械加工铸造内、外圆角或圆弧,其最小极限尺寸为图样标注尺寸,最大极限尺寸为图样标注尺寸加公差值,壁厚尺寸公差等级可降一级选用。
如果图样上一般尺寸公差为CT12,则壁厚尺寸公差为CT13。
(6)铸件尺寸公差在图样上标注时采用公差等级代号标注,如GB/T 6414-1986CT10。
有特殊要求时,公差应直接在铸件基本尺寸的后面标注,如95±1。
(7)铸件表面上的粘砂、夹砂、飞边、毛刺、浇冒口和氧化皮等应清除干净。
铸钢件综合技术条件

铸钢件综合技术条件1 主题内容与适用范围本标准根据GB 11352和GB/T 6967的相关内容,规定了一般工程用铸造碳钢件、一般工程与结构用低合金铸钢件的牌号及铸件技术条件。
以下所涉及的铸钢件均指此两类铸造碳钢件。
本标准适用于砂型或导热性与砂型相当的铸型铸造的碳钢件。
对用其他铸型铸造的铸钢件亦可参照使用。
2 牌号2.1 一般工程用铸造碳钢件按GB 5613的规定分为:ZG200-400;ZG230-450;ZG270-500;ZG310-570;ZG340-640五种铸钢牌号。
2.2 一般工程与结构用低合金铸钢件共包含八种牌号:ZGD270-480;ZGD290-510;ZGD345-570;ZGD410-620;ZGD535-720;ZGD650-830;ZGD730-910;ZGD840-1030。
3 技术要求3.1 生产方法除另有规定外,生产方法和铸造工艺可由供方自行决定。
3.2 化学成分各牌号的化学成分应符合表1的规定:表1 铸钢牌号及化学成分牌号元素最高含量(%)C Si Mn S P残余元素Ni Cr Cu Mo V 总和ZG200-400 0.2 0.5 0.80.04 0.04 0.30 0.35 0.30 0.20 0.05 1.00ZG230-450 0.3 0.5 0.9ZG270-500 0.4 0.5 0.9ZG310-570 0.5 0.6 0.9ZG340-640 0.6 0.6 0.9ZGD270-480 / / / / / / / / / ZGD290-510 / / / / / / / / / ZGD345-570 / / / / / / / / / ZGD410-620 / / / / / / / / / ZGD535-720 / / / / / / / / / ZGD650-830 / / / / / / / / /ZGD730-910 / / /0.35 0.35 / / / / / /ZGD840-1030 / / / / / / / / / 注:1)一般工程用铸造碳钢件对上限减少0.01%的碳,允许增加0.04%的锰;对ZG200-400的锰最高至1.00%,其余四个牌号锰最高至1.20%。
铸件毛坯外观技术要求
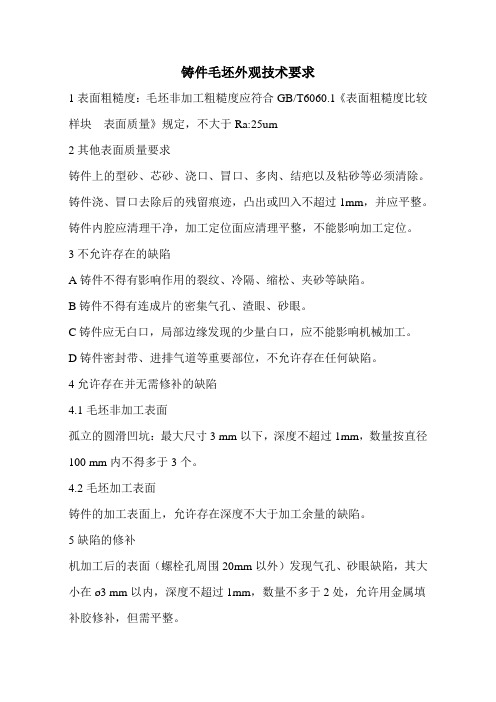
铸件毛坯外观技术要求
1表面粗糙度:毛坯非加工粗糙度应符合GB/T6060.1《表面粗糙度比较样块表面质量》规定,不大于Ra:25um
2其他表面质量要求
铸件上的型砂、芯砂、浇口、冒口、多肉、结疤以及粘砂等必须清除。
铸件浇、冒口去除后的残留痕迹,凸出或凹入不超过1mm,并应平整。
铸件内腔应清理干净,加工定位面应清理平整,不能影响加工定位。
3不允许存在的缺陷
A铸件不得有影响作用的裂纹、冷隔、缩松、夹砂等缺陷。
B铸件不得有连成片的密集气孔、渣眼、砂眼。
C铸件应无白口,局部边缘发现的少量白口,应不能影响机械加工。
D铸件密封带、进排气道等重要部位,不允许存在任何缺陷。
4允许存在并无需修补的缺陷
4.1毛坯非加工表面
孤立的圆滑凹坑:最大尺寸3 mm以下,深度不超过1mm,数量按直径100 mm内不得多于3个。
4.2毛坯加工表面
铸件的加工表面上,允许存在深度不大于加工余量的缺陷。
5缺陷的修补
机加工后的表面(螺栓孔周围20mm以外)发现气孔、砂眼缺陷,其大小在ø3 mm以内,深度不超过1mm,数量不多于2处,允许用金属填补胶修补,但需平整。
铸造毛坯件检验规范

1、目的为了规范公司对铸造件质量的检验。
2、适用范围适用于公司内所有球墨铸铁材质的产品。
3、引用标准GB /T5612-2008 铸铁牌号表示法GB/T1348-1988 球墨铸铁件GB 231-84 金属布氏硬度试验法GB/T9441-2009 球墨铸铁金相检验GB/T6414-1999 铸件尺寸公差与机械加工余量GB 6060.1-85 表面粗糙度比较样块铸造表面4、验收标准4.1 铸件材质检验标准:4.1.1 球墨铸件材质验收标准应符合GB1348-1988 球墨铸铁的标准,以机械性能(抗拉强度、延伸率)、金相组织为验收依据,硬度及化学成分做为参考。
牌号化学成份重量百分比(%)C Si Mn P S Mg Re CuQT450-10 3.4~3.92.6~3.1≤0.3 ≤0.07 ≤0.030.025~0.060.02~0.04---QT500-7 3.4~3.92.6~3.0≤0.45 ≤0.07 ≤0.030.025~0.060.02~0.04---QT600-3 3.2~3.72.4~2.80.4~0.5≤0.07 ≤0.030.025~0.060.02~0.040.2~0.4牌号机械性能抗拉强度σb(MPa)屈服强度σ0.2(MPa)延伸率δ(%)硬度(HB)QT450-10 ≥450 ≥310 ≥10 160~210 QT500-7 ≥500 ≥320 ≥7 170~270 QT600-3 ≥600 ≥370 ≥3 190~270 4.1.1.3 壳体毛坯件的球墨铸铁材质正火后其珠光体(正火索氏体)组织等级在3级以上。
4.1.2 材质检验取样规范4.1.2.1机械性能检查:机械性能测试的试块,每班次每种牌号至少浇注三根,若铸件进行热处理,必须连同试块一同进行热处理。
二根用于生产厂测试性能(第一根合格则该批次合格,余下试块(留有生产日期、包次标识)留存。
若第一根试块不合格,测试剩余二根,若第二根不合格则该批次产品全部报废,若第二根合格,应加试第三根,合格则判定该炉产品合格,若第三根不合格则该批次产品全部报废)。
铸钢件国标

铸钢件国标
【实用版】
目录
1.铸钢件的概述
2.铸钢件国标的意义和作用
3.铸钢件国标的主要内容
4.铸钢件国标对行业的影响
正文
铸钢件是一种以铁为主要元素,以铁为主要成份,含碳量一般在之间,并含有少量的锰、硅、硫、磷等元素的铸造材料。
铸钢件在机械、汽车、船舶、铁路、石油化工等领域有着广泛的应用。
我国的铸钢件国标,即《铸钢件》国家标准,对于规范铸钢件的生产、检验和贸易,提高铸钢件的质量和可靠性,保证设备安全运行,推动铸钢件行业的发展具有重要的意义和作用。
铸钢件国标的主要内容包括铸钢件的分类、牌号和化学成分、力学性能、热处理、检验方法等。
其中,牌号和化学成分是铸钢件的重要指标,直接影响铸钢件的性能和用途。
力学性能是铸钢件使用性能的重要指标,包括抗拉强度、屈服强度、伸长率等。
热处理是为了改善铸钢件的组织结构和性能,提高其使用性能。
铸钢件国标对行业的影响主要体现在以下几个方面:一是提高了铸钢件的质量和可靠性,保证了设备安全运行;二是推动了铸钢件行业的技术进步,提高了行业的整体水平;三是促进了铸钢件的国际贸易,提高了我国铸钢件的国际竞争力。
第1页共1页。
- 1、下载文档前请自行甄别文档内容的完整性,平台不提供额外的编辑、内容补充、找答案等附加服务。
- 2、"仅部分预览"的文档,不可在线预览部分如存在完整性等问题,可反馈申请退款(可完整预览的文档不适用该条件!)。
- 3、如文档侵犯您的权益,请联系客服反馈,我们会尽快为您处理(人工客服工作时间:9:00-18:30)。
重量公差值 %
>0.4
- 5 6 8 10 12 14 16 18 20 24 - - - - -
>0.4~1
- 4 5 6 8 10 12 14 16 18 20 24 - - - -
>1~4
- 3 4 5 6 8 10 12 14 16 18 20 24 - - -
>4~10
- 2 3 4 5 6 8 10 12 14 16 18 20 24 - -
制备(加工和热处理),及进行试验。
4
附录A
Q/DZQ 041.2-2006
(规范性附录)
铸钢件尺寸公差、加工余量、重量偏差
A.1 铸钢件尺寸公差数值见表A.1。
表 A.1 铸件尺寸公差
单位为毫米
毛坯铸件
铸件尺寸公差等级CT
基本尺寸
7
8
9
10
11
12
13
14
15
16
大于 至
尺寸公差值
-
10 0.74 1
6
9
11
14
18
100 160 1.2 1.8 2.5 3.6
5
7
10
12
16
20
160 250 1.4
2
2.8
4
5.6
8
11
14
18
22
250 400 1.6 2.2 3.2 4.4 6.2
9
12
16
20
25
400 630 1.8 2.6 3.6
5
7
10
14
18
22
28
630 1000 2
2.8
4
2
Q/DZQ 041.2-2006
4.2.4 铸钢件的特殊热处理如高锰钢(ZGMn13)铸件的水韧处理,按公司相关规定确定
实施单位,并在订货协议中注明。
4.3 焊补
4.3.1 供方可在表 1 规定的铸钢件允许焊补范围内焊补,在清除缺陷且见到良好金属后
进行。
表1 铸件铲除缺陷后允许焊补范围
壁 厚,mm
≤15
16~30
31~50
51~100 101~300
>300
缺陷深度
穿透
≤70%
≤60%
≤50%
≤40%
≤30%
注:缺陷深度系指铲除缺陷后坡口深度与该处壁厚的百分比。
4.3.2 焊补工艺由供方制定,并符合 Q/DZQ 148-2005 标准规定。 4.3.3 焊补后进行热处理,焊补处与本体金属硬度差不得高于或低于本体金属硬度的 15% 。 4.3.4 重大焊补必须事先经过需方书面确认,焊补的范围及部位应记录在交于需方的检 验文件中。 4.4 标识与合格证 4.4.1 铸钢件应做出可追溯标识,若设计图样或合同无规定,铸件需在特定位置或非加 工面做出炉号标识,且与试块相对应。 4.4.2 供方交货时必须提供由供方检验部门执行并由该部门代表签字的符合订货协议的 检验合格证和检验报告。检验合格证应注明下列各项:
>1000~4000
- - - - - - 2 3 4 5 6 8 10 12 14 16
>4000~10000
- - - - - - - 2 3 4 5 6 8 10 12 14
>10000~4000
- - - - - - - - 2 3 4 5 6 8 10 12
注1:本表摘自GB/T 11351-1989。
机械加工余量等级
大于
至
C
D
E
F
G
H
-
40
0.2
0.3
0.4
0.5
0.5
0.7
40
63
0.3
0.3
0.4
0.5
0.7
1
63
100
0.4
0.5
0.7
1
1.4
2
100
160
0.5
0.8
1.1
1.5
2.2
3
160
250
0.7
1
1.4
2
2.8
4
250
400
0.9
1.3
1.4
2.5
3.5
5
400
630
1.1
1.5
注2:最大尺寸为最终机械加工后铸件的最大轮廓尺寸。
单位为毫米
J
K
1
1.4
1.4
2
2.8
4
4
6
5.5
8
7
10
9
12
10
14
11
16
14
18
14
20
16
22
17
24
6
A.4 铸件重量公差见表A.4。
Q/DZQ 041.2-2006
表A.4 铸件重量公差
重量公差等级MT
公称重量,kg
1 2 3 4 5 6 7 8 9 10 11 12 13 14 15 16
6
8
11
16
20
25
32
1000 1600 2.2 3.2 4.6
7
9
13
18
23
29
37
1600 2500 2.6 3.8 5.4
8
10
15
21
26
33
42
2500 4000 -
4.4 6.2
9
12
17
24
30
38
49
4000 6300 -
-
7
10
14
20
28
35
44
56
6300 10000 -
-
12
车轮、托辊 金属型
底面 顶面
外径 轴孔
H
12
12
12
J
12
12
12
齿条、其他 砂型
底、侧面 顶面
轴孔
J
13
13
13
K
14
14
14
注 1: MA:加工余量等级;CT:尺寸公差等级;MT:重量偏差等级。
注2: 壁厚尺寸公差降级选用。
A.3 铸件机械加工余量见表A.3。
表 A.3 铸件机械加工余量
最大尺寸
1.5
2
2.8 4.2
-
-
-
-
10
16 0.78 1.1 1.6 2.2 3.0 4.4
-
-
-
-
16
25 0.82 1.2 1.7 2.4 3.2 4.6
6
8
10
12
25
40 0.9 1.3 1.8 2.6 3.6
5
7
9
11
14
40
63
1
1.4
2
2.8
4
5.6
8
10
12
16
63 100 1.1 1.6 2.2 3.2 4.4
5
Q/DZQ 041.2-2006 A.2 常用铸钢件尺寸公差等级、加工余量等级、重量偏差等级见表A.2。
表 A.2 常用铸钢件尺寸公差等级、加工余量等级、重量偏差等级
相对浇注
零件名称 铸造方法
位置
铸件部位
MA
加工面 非加工面
CT
CT
MT
齿轮、齿圈 金属型
底面 顶面
外径 轴孔
H
12
12
12
J
12
12
其随后所有的修改单(不包括勘误的内容)或修订版均不适用于本部分,然而,鼓励根据 本部分达成协议的各方研究是否可使用这些文件的最新版本。凡是不注日期的引用文件, 其最新版本适用于本部分。
GB/T 222-2006 钢的成品化学成分允许偏差 GB/T 223 钢铁及合金化学分析方法 GB/T 5680-1998 高锰钢铸件 GB/T 6060.1-1997 表面粗糙度比较样块 铸造表面 GB/T 6414-1999 铸件 尺寸公差与机械加工余量 GB/T 7233-1987 钢铸件超声探伤与质量评级标准 GB/T 11351-1989 铸件重量公差 GB/T 11352-1989 一般工程用铸造碳钢件 JB/T 6402-1992 大型低合金钢铸件 Q/DZQ 148-2005 铸钢件补焊工艺守则 3 术语和定义 重大焊补 铸钢件铲除缺陷后产生的坡口,其深度超过该处壁厚的20%或超过25mm时,或缺陷面积 超过65cm2时为重大焊补。 4 通用技术条件 4.1 基本要求 4.1.1 铸钢件的牌号、化学成分、力学性能应符合需方所提供的图样要求及 GB/T 11352-1989、 JB/T 6402-1992、GB/T 5680-1998 的规定。
I
Q/DZQ 041.2-2006
毛坯件通用技术条件 铸钢件
1 范围 Q/DZQ 041的本部分规定了铸钢件通用技术要求。 本部分适用于集团公司铸钢毛坯件的外协采购。 当有特殊要求时,由供需双方按有关规定协商解决。
2 规范性引用文件 下列文件中的条款通过本部分的引用而成为本部分的条款。凡是注日期的引用文件,
2.2
3
4
6
630
1000
1.2
1.8
2.5
3.5
5
7
1000 1600
1.4
2
2.8
4
5.5
8
1600 2500
1.6
2.2
3.2
4.5
6
9
2500 4000
1.8
2.5
3.5
5
7
10
4000 6300