电镀均匀性改善
年度电镀质量异常总结(3篇)

第1篇一、前言随着我国电子产业的快速发展,电镀工艺在电子产品制造中的应用越来越广泛。
然而,在电镀过程中,由于各种原因,质量异常问题时有发生,给企业带来了巨大的经济损失和信誉风险。
为了提高电镀质量,降低质量异常发生率,本文对2021年度电镀质量异常情况进行总结,分析原因,并提出改进措施。
二、2021年度电镀质量异常情况概述1. 异常类型2021年度电镀质量异常主要包括以下几种类型:(1)外观缺陷:如氧化、腐蚀、起泡、脱皮、露底等。
(2)电镀层厚度不足:导致防护性能降低,易受腐蚀。
(3)电镀层结合力差:导致涂层脱落,影响产品使用寿命。
(4)电镀液稳定性差:导致电镀层质量不稳定,影响产品一致性。
2. 异常原因(1)原辅材料质量:原辅材料质量不合格是导致电镀质量异常的主要原因之一。
如:电镀液成分不稳定、添加剂含量不足等。
(2)设备故障:设备老化、维护不当或操作失误等原因导致设备故障,进而影响电镀质量。
(3)工艺参数控制:工艺参数设置不合理、温度、电流、时间等参数控制不准确,导致电镀层质量不稳定。
(4)环境因素:温度、湿度、灰尘等环境因素对电镀质量有较大影响。
三、2021年度电镀质量异常原因分析及改进措施1. 原辅材料质量(1)原因分析:原辅材料质量不稳定,如电镀液成分波动、添加剂含量不足等。
(2)改进措施:加强原辅材料供应商的管理,严格检验标准,确保原辅材料质量。
2. 设备故障(1)原因分析:设备老化、维护不当或操作失误等原因导致设备故障。
(2)改进措施:加强设备维护保养,定期进行设备检查,提高操作人员技能水平。
3. 工艺参数控制(1)原因分析:工艺参数设置不合理、温度、电流、时间等参数控制不准确。
(2)改进措施:优化工艺参数,制定详细的操作规程,加强工艺参数的监控。
4. 环境因素(1)原因分析:温度、湿度、灰尘等环境因素对电镀质量有较大影响。
(2)改进措施:加强车间环境管理,保持车间温度、湿度稳定,控制灰尘等污染源。
电镀均匀性说明

电镀均匀性及深镀能力测试规范一、目的:对我司完成安装调试的电镀线进行规范的均匀性测试评估。
二、使用范围:所有安装了我司电镀线的客户。
三、职责:工程部负责规范的制定和修改,客户负责前期的均匀性测试,工程部COV 跟进人员负责和客户一起对电镀均匀性和深镀能力评估、调试、测试或做进一步改善。
四、操作规范细则:1. 电镀线安装完成后,客户处技术部门人员需要对电镀COV 测试的准备工作做出相关的安排:1.1 电镀COV 、深镀能力测试板若干片,根据电镀线飞巴长度决定。
1.2 安排确定在哪个铜缸做COV 和深镀能力的测试评估。
1.3 出相关联络单,知会到相关部门协助、配合。
第1 页共20 页1.4 对要做测试的铜缸的硬件设施检查确认,如喷嘴无堵塞、歪斜、断裂,电流正负偏差在5%,摇摆幅度在控制范围内,浮架无偏差、夹具无掉落等。
2. 测试程序及条件:2.1 客户处技术部门人员可以先安排对电镀线的COV 进行测试,评估我司电镀线的COV 分布情况,后续再对电镀铜缸的深镀能力评估测试,测试时同时需要考虑药水的控制范围。
如在合同要求范围内,可以正常验收,如不在合同范围内,即未达到客户的要求范围,我司安排技术服务人员到现场跟进调整解决。
2.2 测试板规格:FR-4 1.624 mm 18〃*24 〃H/H 整板基铜偏差< 1um2.3 测试工具Oxford CMI700 铜厚测试仪、钳流表、卷尺2 . 4测试流程cov:开料一一标识一一磨板一一面铜测试一一电镀一一水洗烘干——面铜测试——数据分析——得出结论。
第2页共20页深镀能力:开料——标识——钻孔——沉铜——电镀——水洗烘干——孔铜测试——数据分析——得出结论。
上板时请按下列方式挂板:(注:面对上板方向从左往右编号。
)15ASF*100min (可根据实际生产情况调整)2.6测试选点COV测试:测量铜厚时,每块板的每面短方向(水平方向)每隔1.6i nch,长方向(竖直方向)每隔2.2 in ch,取一测试点,每面平均分布11*11=121个点,对此121点铜厚进行测试,续点记录相应测试点的铜厚数据。
磁钢电镀质量改进措施

磁钢电镀质量改进措施引言电镀是一种常用的表面处理技术,通过在金属制品表面形成一层金属薄膜,可以提高其外观、耐腐蚀性和导电性。
磁钢电镀是一种特殊的电镀工艺,常用于生产磁铁和磁性元件。
然而,磁钢电镀质量通常受到一些问题的影响,例如镀层厚度不均匀、氢脆、环境污染等。
本文将介绍一些常见的磁钢电镀质量改进措施,旨在提高磁钢电镀的质量和可靠性。
1. 前处理工艺优化在磁钢电镀之前,前处理工艺对于镀层的质量至关重要。
以下是一些前处理工艺优化的措施:•表面清洁:使用合适的清洗剂和设备,彻底清洁工件表面,去除油污、氧化物和其它杂质,以确保镀层的附着力和均匀性。
•光亮处理:在清洁之后,进行光亮处理可以进一步改善工件表面的光洁度,有利于后续电镀的质量。
•激活处理:通过激活处理,如酸洗或化学激活,可以增加表面的粗糙度并提高工件与镀液之间的相互作用,有助于形成均匀的镀层。
2. 电镀工艺优化电镀过程中的参数和条件对于镀层的质量起到至关重要的作用。
以下是一些电镀工艺优化的措施:•电镀液配方优化:选择合适的电镀液配方,控制金属盐的浓度、添加剂的种类和浓度,以及pH值等参数,以实现均匀且具有良好外观和性能的镀层。
•电流密度控制:根据工件的尺寸和形状,合理调整电流密度,以确保镀层在整个工件表面均匀沉积,避免区域性镀层厚度过薄或过厚的问题。
•温度控制:控制电镀液的温度,可以影响镀层的致密性和结晶度。
过高的温度可能会导致镀层结构松散,而过低的温度则可能影响镀层的附着力。
•搅拌和过滤:为了保持电镀液中的盐和添加剂的均匀分布,需要定期搅拌和过滤电镀液,以去除悬浮颗粒和杂质,保持电镀液的清洁度。
3. 后处理工艺优化电镀完成后,后处理工艺对于镀层的质量和性能同样重要。
以下是一些常见的后处理工艺优化措施:•清洗和中和:在电镀完成后,通过清洗工艺去除残留的电镀液和杂质,并用合适的中和剂中和表面的碱性洗涤剂,以防止残留的化学物质对镀层的影响。
•干燥和烘烤:将镀层的工件通过适当的干燥和烘烤工艺,去除残留的水分和挥发性物质,以防止镀层与环境中的湿气反应,导致质量下降或出现氢脆现象。
电镀镍厚控制以及金成本改善.
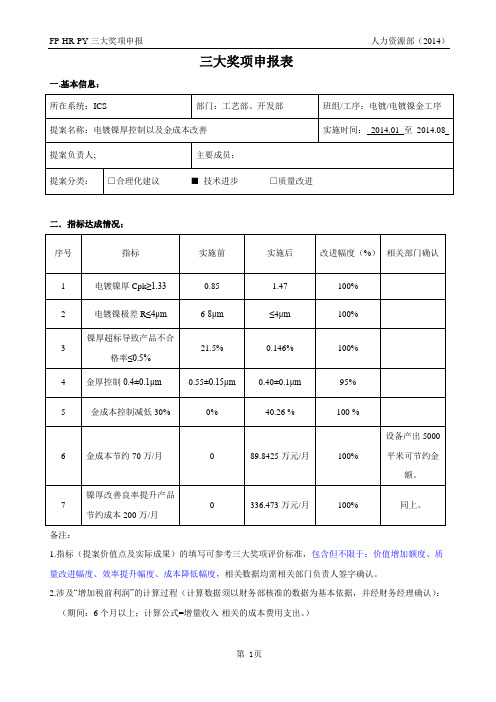
三大奖项申报表一.基本信息:二.指标达成情况:备注:1.指标(提案价值点及实际成果)的填写可参考三大奖项评价标准,包含但不限于:价值增加额度、质量改进幅度、效率提升幅度、成本降低幅度,相关数据均需相关部门负责人签字确认。
2.涉及“增加税前利润”的计算过程(计算数据须以财务部核准的数据为基本依据,并经财务经理确认):(期间:6个月以上;计算公式=增量收入-相关的成本费用支出。
)三.周边评价备注:周边评价部门为该提案实施以及应用中相关关联部门。
四.审核意见(详细内容请参阅总结报告):电镀镍厚控制以及金成本改善总结报告1.背景ICS封装基板电镀镍-金产品中,95%以上的客户对电镀镍金厚度以及手指宽度、间距提出明确的品质管控要求。
如手指宽度控制因客户工程文件要求存在一定制作难度以及前工序(蚀刻)制成能力偏差,这对电镀镍金工序的电镀镍厚控制提出更高要求。
ICS电镀镍金线设备初期电镀镍厚极差为6-8μm,这很难满足客户对电镀镍金产品的品质要求,使得前期电镀镍金产品因镍厚不合格产生大量报废,特殊产品报废率可达60%,制程能力低下。
因此改善电镀镍厚控制,提高镀镍制程能力具有积极的意义。
在封装基板生产过程中,金厚控制范围为0.3-1.0μm,金成本在整个ICS物料消耗中占据很大的组成部分。
因此通过提高镀金均匀性、优化板边设计、控制金厚以及减少金盐带出等手段对金成本控制具有非常显著以及积极的效果。
2.目标通过优化改善电镀镍厚控制,提高产品合格率,使得电镀镍极差R≤4μm,电镀镍镍金产品因电镀镍厚超标的报废率由最高50-60%降低至0.25%。
金成本减低30%左右。
实现电镀参数导入程序化、自动化,减少人为导入的错误,提高生产效率。
3.过程实施3.1电镀镍厚控制对电镀镍厚控制过程需结合电镀镍均匀性调整、飞巴与挂具间电镀镍厚偏差以及参数优化等过程。
其镍厚控制改善思路如下:3.1.1 电镀镍均匀性改善电镀镍均匀性提升主要通过改善设备几何尺寸、设计阴极挡板、阴极排布以及阴阳极相关位置。
电镀均匀性原因分析与改善

frequently used process.In this paper,the factors which effect the uniform ity are concluded and som e tests were
made to analyze the influence of the factors.The affecting factors cam e from operator,m achine,m aterial,m ethod
电镀均 匀性的因素,并结合实际测试数据进行分析说 明,以期 对实际生产提供一定的借
鉴 ~主 要 通过 人 、机 、料 、法和环 等 影 响 电镀 均 匀性 的 因素 .分 别 对挡 板 、浮 架 、 夹具 、
钛 篮 、添 加 铜球 前后 期 、上 扳 方 式和 电流 密度 等方 面进 行 对 比测 试 .
精 细线 路制 作时 , 由于线 宽要求越 来越 小 ,导致 在 相 同 控 制 公 差 要 求 下 ,线 宽 的控 制 范 围 越 来 越 小 , 其 控 制 难 度 更 大 , 因 此 需 要 从 垂 亢 电 镀 线 的 设 汁 上 就 提 出 l0 lum以 内 的 电镀 的均 匀性 , 降低 _而 铜 厚 度 之 间 的 极 差 ,减 小 精 细 线 路 的 线 宽 之 n=『j差 异 。
铜 厚之间的筹异△H作为指 标考察 电镀铜层 的均 匀
性 。 者 f/,3i-[‘ 方法 公 式 (1)~式 (4)所 示 。
l “
aVC= ∑ X ,
n I I
… … … … … … … … (1)
industry.
Key words PCB;Uniformity of Electroplating;Afecting Factor
浅谈电镀厚金均匀性研究改善

1 5 1 0D47 2 2 O 3 0 4 7 0 40 O 3 8 O 44 0 4 3 0 4 2 0 47 O. 3 8 8 9. 9 %
1 6 1 0D47 2 2 0 3 O 3 6 O 5 2 0 4 8 0 4 3 0 3 3 0 4 2 O 5 2 0 3 3 7 7 7 %
2 1 1 OD47 2 2 0 3 0 5 7 0 48 0 4 4 O 3 3 O 4 0 4 5 0 . 57 0 33 7 4 0 %
2 0 0 元 钱 ,产 品 无 法 获 利 。
22 1 OD47 2 2 0 3 O 3 9 O 38 0 3 7 0 4 2 0 40 O 3 9 0 42 O 37 94 0 %
1 7 1 0D4 72 2 O 3 0 4 0 O 5 8 0 5 7 0 4 4 0 3 5 0 4 7 O 5 8 O 3 5 7 5 3%
1 8 1 O D4 72 2 0 3 0 31 O 4 0 33 O 31 0 3 4 0 3 4 O 41 O 31 8 6 9%
数据 测量 统计 , 每 片板 的测量5 点 , 左 上 为A 点, 右 上为B 点, 右
下为C 点, 左下为D 点, 中 央 为E 点 分别 如下:
要 求 实 际测 最值 平 均 最 大 最小 N O 生产型号 金厚 均匀性 ( u m) A点 B点 C 点 D点 E点 值 值 值
难 因 为 镀 厚 金 不 同 于 镀 铜 、 镀 锡 、 D4 7 22 O 3 O 5 O 0 4 2 O 37 0 4 0 0. 4 0 0 42 O 5 0 O 3 7 8 5 7%
6 1 OD2 4 57 O 3 0 4 9 0 39 O 3 5 0 36 0 4 0 0 40 0 49 0 3 5 8 : j 6% 7 1 OD2 4 57 O 3 0 4 4 0 46 0 4 0 0 48 0 3 8 0 43 0 48 O 3 8 8 8 9%
铝件盲孔电镀的改善方法

铝件盲孔电镀的改善方法1.引言1.1 概述铝件盲孔电镀是一种常见的表面处理方法,它可以提高铝件的耐腐蚀性、强度和美观度。
然而,由于盲孔的封闭性和形状特殊性,导致在电镀过程中存在一些问题。
这些问题包括镀膜不均匀、盲孔内无法镀膜、镀膜质量不达标等。
为了解决这些问题,需要采取一些改善方法。
本文将介绍铝件盲孔电镀的改善方法,主要包括两种方法。
第一种方法是通过改变电镀工艺参数来优化镀膜质量,如控制电镀液的温度、酸度和电流密度等。
第二种方法是在盲孔内采取特殊手段,如使用导电涂料填充盲孔、改变盲孔的形状等,从而实现盲孔内的镀膜。
通过研究和实践,这些改善方法已经取得了一定的效果。
改善方法一可以提高铝件盲孔电镀的均匀性和质量稳定性,使得镀膜更加均匀、平滑。
改善方法二则可以解决盲孔内无法镀膜的问题,使得铝件的表面处理效果更加完美。
在未来,随着科学技术的发展,铝件盲孔电镀的改善方法将会更加多样化和精确化。
同时,我们也需要更加深入地研究盲孔电镀的机理和影响因素,以提高铝件表面处理的效率和质量。
综上所述,本文将详细介绍铝件盲孔电镀存在的问题及其改善方法。
通过对这些改善方法的应用,相信可以提高铝件盲孔电镀的效果,进一步拓宽铝件的应用范围。
同时,也为相关领域的研究和应用提供了有价值的参考和指导。
1.2 文章结构文章结构的主要目的是为了引导读者更好地理解和阅读文章内容。
通过清晰的结构,读者可以更好地掌握文章的主要论点和论证过程,同时也方便读者在需要的时候快速定位到所需信息。
本文的结构主要包括以下几个部分:2.正文:本部分将深入探讨盲孔电镀存在的问题以及两种改善方法。
2.1 盲孔电镀存在的问题:本节将详细介绍铝件盲孔电镀过程中常见的问题,如电镀效果不均匀、盲孔电镀不到位等,并分析造成这些问题的原因。
2.2 改善方法一:本节将介绍第一种改善方法,包括具体的操作步骤和技巧。
同时,还将详细解释这种方法是如何解决盲孔电镀存在的问题的。
2.3 改善方法二:本节将介绍第二种改善方法,同样包括具体的操作步骤和技巧。
电镀均匀性改善研究

电镀均匀性改善研究2008-8-15 17:02:04 源自: 作者:摘要:本文针对图形电镀线电镀均匀性不佳的状况,通过一系列细致的试验分析,完成了在缸体上部增加特定尺寸的阳极挡板,以及在浮槽侧面进行大小、间距适宜的开孔等改造措施,改善了该线的电镀均匀性,使其均匀程度由改善前的20.8%,提高到改善后10.3 %。
关键词:电镀均匀性;阳极挡板;浮槽1. 前言随着PCB 不断向轻、薄、短小高密度方向发展,给很多设备和生产工艺带来了更高要求。
其中线路板图形间距越来越小,而孔铜厚要求却越来越高,给图形电镀均匀性就提出了新的挑战。
我司旧图形电镀线在加工整板细密线路(最小间距3.5mil)的板子时,板边细密线路容易夹膜,导致报废。
且发现板上有规律的铜厚分布不均匀,导致半成品切片判断孔铜失误,不能有效对半成品的铜厚作出准确判断。
故决定对此线电镀均匀性进行专门测试分析,组织进行改善。
2. 测试说明:1)整个图形电镀线的电镀窗口为52×24(Inch2),深方向为24Inch;2)采用生益FR-4 板材,尺寸:24X24Inch2,2 块此尺寸板并排放置于电镀缸中进行测试;3)测试板距溶液表面0-1Inch,悬挂于溶液中间,不加分流条,22ASF,电镀60 分钟;4)深方向是指板子从镀液表面到溶液底部的方向;水平方向是指与阴极杆平行的方向;5)测量仪器采用的是德国Fischer 公司感应式表面铜厚测试仪,测量误差<0.5um;6)测试时每2×2Inch2 取一个测量点,用电镀后的铜厚减去电镀前的铜厚进行统计分析;7)因每进行一次测试,2 块板两面共有576 个数据,限于篇幅,文中只展示每次正面测量所作出示意图。
7 次测试的数据,作为附件,另附一个文档。
3. 改善目标:1)总体COV(标准偏差与总体平均值的比值百分数)<11%(业界参考标准为<=8-12%);2)深方向镀铜厚度平均差异(深方向极差)<3um。
影响镀层厚度分布均匀性的因素

一、影响镀层厚度分布均匀性的因素:使镀层厚度分布均匀的重要性电沉积时总希望镀层厚度在工件上的分布越均匀越好。
当工件上沉积的总金属量相同时,若厚度分布不均匀,则会带来很多坏处:(1)对于阳极性镀层,镀层薄处经不起牺牲腐蚀会先使基体产生锈蚀。
而一个制件部分锈蚀后则已不合格,造成了镀层过厚处金属的浪费。
若为保证最薄处不生锈,只能加大平均厚度,导致电镀成本增大。
(2)对于阴极性镀层,薄处镀层孔隙率高,很易产生点状锈蚀,继而锈点加大,形成连片锈蚀。
与阳极性镀层相比,阴极性镀层薄处锈蚀更快。
对于局部防渗氮、渗碳镀层,薄处易形成孔眼,失去保护作用。
若厚度均匀则各部分孔隙率差别不大,总体防蚀性提高。
例如,对电池钢壳滚镀亮镍,壳内(特别是靠底部的地方)镀层很薄,甚至在清洗烘干时即已起小锈点、泛黄,为此要“出白”处理,迅速用水溶性封闭剂封闭后干燥。
(3)对于光亮性电镀,镀层薄处因阴极电流密度小,故光亮整平性差,影响整体外观。
(4)合金电沉积时,不同厚度处的合金组分不相同,或外观不均(如仿金镀),又或抗蚀性不一致(如锌镍合金)。
(5)不同厚度处镀层的物理、机械性能(如脆性、内应力等)不一样。
若镀后还要作冲压成型等机加工处理,镀层过厚处往往机加工性能不良(起皮、开裂、粉状脱落等)。
无论从防蚀性,还是外观、机加工性能等方面讲,都希望提高镀层厚度的均匀性。
对于尺寸镀硬铬,若用户要求镀后不作磨削处理,则很难办到;有时为了保证最薄处达到最终尺寸要求,厚度均匀性差时,不得不大大加大平均厚度,这在生产中并不少见。
为使制件上镀层各部分厚度尽量接近,必须了解影响厚度分布均匀性的因素。
二、影响镀层厚度分布均匀性的因素:镀液性能因素-镀液的分散能力与深镀能力这是镀液的两项重要技术指标,一般为新工艺研究的必测指标。
镀液的分散能力是指镀液使镀层厚度分布均匀的能力,又称均镀能力,通常用T·P表示。
在其他条件相同时,分散能力越好,则镀层厚度分布越均匀。
板面电镀均匀性研究

板面电镀均匀性研究1. 前言电镀均匀性直接影响着图形转移时蚀刻的均匀程度。
3/3 线的制作已经成为一种瓶颈,如果电镀铜厚不均匀,会对蚀刻的均匀性产生很大的影响,从而造成线幼或间距过小。
印制电路板的高可靠性也对线路的质量和线路的均匀性提出了很高的要求,因此对电镀均匀性的研究显得非常重要[1]。
目前很多PCB生产厂采用传统的单点夹具,上板时板和板之间存在或大或小的间距,每块板上夹具的数量也不相同,分配到每块板上的电流大小也不尽相同,从而导致电镀铜厚的差别很大。
针对该问题,本实验从改变上板方式、夹具间链接方式等问题入手,对影响电镀均匀性的因素进行了研究,并根据实验结果对夹具进行更新设计,通过实验证明新夹具在改善电镀均匀性的合理性。
2. 实验部分本实验所用板材为双面板,板厚为1mm 左右,板面铜箔厚度为HOZ,裁成尺寸为16″×20″的样板。
2.1 上板:本实验根据板间距离分成两组,一组为板与板之间留有或大或小的空隙,另一组为板和板之间不留空隙,两块板紧靠。
在每组板中,又设计了四种不同的板间互连方式。
一种为板间不互连,作为对照;一种用铜箔包住板的上端,实现板与板间互连,夹具加在铜箔上;一种是在板下角钻孔后用铜丝将板连在一起;最后一种是将夹具用铜丝连在一起。
实验方案列于表1,各不同实验的上板方式和互连方式如图1 所示。
2.2 电镀:利用槽式垂直电镀线对上述8 组试板分别电镀,电镀参数为20ASF×48min,电镀过程中用钳表测各夹具上通过的电流。
2.3 数据采集及切片分析:每Panel 取9 个切片,切片位置如图2 所示。
每个切片X、Y 方向各读取5 个数据,这10 个数据的平均值作为该点的铜厚。
不同位置的铜厚进行板内偏差分析(X、Y 分别分析),9 个切片的平均值作为整板铜厚,整个飞靶上的板作板间偏差分析。
按纵向和横向将9 个位置的板厚分成3 组,分别统计各板板边和中心部位铜厚的差别。
电镀均匀性改善 徐正

板的尺寸(英寸) 24
改善前R均值 0.7775 改善后R均值 0.32
22
0.735
0.46
20
0.865 0.48
18
1.04
0.50
分布 下端厚 下端厚
改善前R均值
改善后R均值
1.2
1
0.8
0.6
0.4 0.2
方案二成功了!
0
24
22
20
18
結論:通過與修改前數據對比,均16勻/25性有很大改善,
鈦 籃
*電力線就是鍍銅過程中正負離子的運動線路, 在電力線密集區域,銅離子析出過多,會導 致該區域鍍銅過厚。 這種鍍銅過厚的現象通常發生在底部,我們 稱之為尖端效應。
電力線
目前產品一般比鈦藍短,尖端效應強,底部易 鍍厚
為了減弱這種效應,故于板底部設定浮架來遮避多餘的電力線
7/25
改善歷程
這是廠家提供的原浮架設計結構。
呈遞減趨勢
18/25
成果驗證
正因為電鍍課改善層出不窮,故電鍍課不僅完成了產能 任務,更出色的保証了品質.
電鍍5-8月份電鍍總報廢率
0.4% 0.3% 0.2% 0.1% 0.0%
0.38% 0.10%
5月份
0.38%
0.35%
0.09%
0.16%
6月份
7月份
19/25
0.35% 0.12%
8月份
績效匯總
23/25
改善心得
用不滿意的眼光看事物 理性分析問題 改善永無止境
24/25
歡迎咨詢交流
聯係人:徐正 單 位:HA01電鍍課 分 機:23105
25/25
感谢下 载
镀铜均匀性报告2
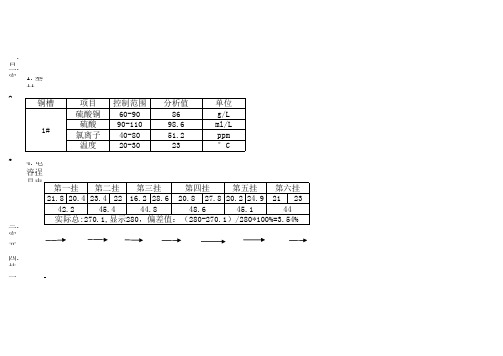
电镀镀铜均匀性报告
一.目的:通过对镀铜线现有生产条件进行整改,重新测试镀铜均匀性,评估镀铜产线制程能力
二.实验条件:
1.基材:250mm*250mm*12PNL,1oz/1oz,基材厚0.1mm.
3.电镀参数:1.8ASD*18分钟,设定总电流280A,实际钳表测定总电流为267.5A.
4.电流误差为(280-267.5)*100%/280=4.5%,即总电流误差〈5%,在允许误差范围内。
三.实验流程:
开料 挂板 酸洗 镀铜 水洗 收板 烘干 收集数据
四.挂板方式:
一飞巴挂六挂,每挂上板2pnl.挂具之间紧密排列.如下图
五.数据收集:(每PNL取9个点切片分析,切片取样点位置图如下)
六.结论
镀铜铜槽经整改后整靶均匀性12.24%,COV<10%,COV差异超过10%部分均为挂板2边;为持续提升镀铜线均匀性,下步改善动作如下《七》项内容.
七.后续仍须改进项目,以增强阴阳极导电效果和分流作用,从而提高镀铜均匀性。
电镀表面叻架不均匀处理方法

电镀表面叻架不均匀处理方法
电镀表面不均匀的处理方法可以参考以下几种:
1.手工修整:对于表面不平整的电镀件,可以采用手工修整的方法。
使用打磨机器将电镀件表面磨平,然后再进行电镀处理。
这种方法适合小批量的产品,但是需要耗费大量的时间和人力。
2.高温退火:对于电镀液流动性差的情况,可以在电镀之前进行高温退火,使电镀件表面变得更加平整。
这种方法可以提高电镀的均匀性,但是需要注意温度和时间的控制,以免影响电镀件的的整体性能。
3.控制镀液成分:如果电镀液中含有杂质或气泡,可以通过控制镀液的成分来改善电镀的均匀性。
镀液中添加防泡剂和去杂质剂可以有效提高电镀效果。
4.重做挡板:如果其他方法都无法改善电镀不均匀的情况,最终的解决办法就是重做挡板。
这虽然会增加成本和时间,但是可以确保产品的质量和美观度。
5.外观检测:为电镀检测的基本功能,从外观上可以看出电镀工艺条件的适合性及电镀药水可能产生的变化。
6.使用色差仪:为了确保电镀件的颜色品质,厂商在批量生产前,首先就需要和客户确认电镀件标准色样及色差参考样,从而帮助电镀厂参考打板。
而由于以上多种因素,不同电镀厂生产工艺不一样,难免出现打样板颜色差异的问题,因此,就可以通过色差仪来进行测量,评定打样板与标准色样之间的色差程度,处理电镀色差问题。
以上就是处理电镀表面不均匀的一些常见方法,但具体操作可能会因实际情况而有所不同,建议咨询专业人士获取更多信息。
提高镀银件厚度均匀性工艺研究

提高镀银件厚度均匀性工艺研究针对压气缸类件镀银厚度不均匀情况,设计制作360°无动力自旋阴极装置,使工件各部位的厚度偏差控制在±10%以内,解决厚度不均带来的工件质量问题,有效提高了工件的合格率,降低了产品的成本。
标签:阴板装置;转速;金属沉积;镀层均匀0 引言镀银技术是高压开关设备核心技术之一,镀银层质量的优劣直接影响到高压开关产品性能和使用寿命。
在高压电器产品中核心导电部位均采用镀银工艺,以减少连接部位接触电阻。
因其对电气性能要求高,又与绝缘材料直接接触,所以必须采用局部镀银工艺才能满足这一性能要求。
本文针对电镀过程中出现厚度不均匀的瓶颈问题,展开一系列工艺技术研究。
通过对360°无动力自旋阴极技术的攻克,提高镀层沉积速度及分散性,以确保镀层厚度的均匀性,从而提高工件的镀层质量,降低了产品生产成本。
1 技术研究方案360°无动力自旋阴极装置(简称阴极装置)研制。
压气缸类件是公司产品核心导电工件,在镀银加工过程中,采用常规遮蔽技术和传统的静止挂镀的方式进行局部镀银,由于工件外圆尺寸一般为150~180范围,要求镀银50μm,受限于槽体结构和静置挂镀的工艺方法,溶液流动不畅通,工件不同部位镀层厚度差异率大,偏差约为50%~300%,为了满足最小部位镀层厚度,只有延长电镀时间,这样不但生产效率低,银料消耗大,而且镀层质量也得不到保证。
(1)阴极装置设计思路。
根据压气缸类工件结构特点,设计制作360°无动力自动旋转阴极装置,依靠槽体内溶液的流动力带动工装下端扇页的旋转,使得工装的主体旋转。
为了能使旋转连续,并尽最大可能地减少转动阻力,在挂具上端引进轴承结构。
从而达到不借助外力情况下溶液能够带动工部件旋转,金属离子在工件表面沉积机会均衡,镀银层表外溶液环境流动活跃,增大电流密度范围,节约电镀时间并得到厚度均匀的镀层。
(2)阴极装置结构设计。
该阴极装置设计包括:轴套挂具头、上挂主杆、旋转扇页三部分。
基于电镀均匀性改善的一些创新与改进

基于电镀均匀性改善的一些创新与改进陈世金【摘要】针对电镀过程中电镀槽、阳极遮板、喷管、挡电边条、阴极浮架等影响电镀均匀性的硬件部分,对其合理布局和设计等提出了具体要求,为提升电镀均匀性提出改善依据及思路.【期刊名称】《印制电路信息》【年(卷),期】2016(024)003【总页数】4页(P38-41)【关键词】电镀均匀性;电镀槽;阳极遮板;喷管;挡电边条;阴极浮架【作者】陈世金【作者单位】博敏电子股份有限公司,广东梅州514768【正文语种】中文【中图分类】TN41自20世纪60年代后期起,电镀行业在第三次产业革命的推动下得到了长足的进步,给包括印制电路板行业在内的各行各业带来了技术的突飞猛进和飞速发展.到目前为止,人们对电镀技术的应用已日趋成熟,并促进电镀工艺不断向低能耗、低物耗、低污染、高质量、高效率方向迅速发展.电镀均匀性一直是伴随电镀技术的发展而发展的,不同的应用领域对电镀均匀性有不同的要求,电镀均匀性的提升已成为电镀技术的"永恒主题".电镀技术在印制电路板行业的应用也有好几十年的历史了,随着电子技术的飞速发展,对印制电路板的电镀要求将会越来越高.印制板行业的电镀设备不断创新和改进,由最早的手动电镀设备,逐步发展到垂直龙门电镀线、垂直连续电镀线、脉冲电镀线、水平电镀线等,其整体均匀性水平也得到了极大的提升.但是以上这些电镀设备,不是说已经做到尽善尽美、无可挑剔了,仍然是有一定的改进空间,尤其是涉及到一些硬件部分的构造、布局和设计等,如电镀槽体、阳极遮板、阳极钛篮设计,电镀喷管、喷嘴的构造,以及挡电边条、阴极浮架的正确使用等.这些都将直接影响到电镀均匀性,性能优异的电镀线必然会有合理的设计与布局,传统的电镀线只要在以上提到的硬件部分做好设计与布局的规划,也可以满足各类中高难度电路板的电镀制作要求。
1.1 电镀槽电镀槽的设计十分讲究,槽体的尺寸(包括长度、宽度和深度)要根据所电镀产品的类型来确定,阴阳极距离、钛篮位置及排放数量等需要核算和测试才能确定.喷射和打气都可以实现药水的交换,但有其各自特点,也需要精确计算喷管、喷嘴、打气孔的方向、数量、距离等,随心所欲的设计肯定是无法达到理想的效果.基于对产品追求电镀的侧重点不同,也会对以上设计会有所不同,如侧重深镀能力的提升与侧重均匀性的提升是需要对其进行差异化设计的.生产75 μm/75 μm等级线路需要控制最大面铜厚度和铜厚极差,电镀均匀性是一个重要的追求指标,如采用传统垂直电镀线制作,则必须对其阳极钛篮的长短、形状、数量、排放位置和排列,喷管的数量、喷嘴的形状、数量、排列及流量大小,以及阳极遮板、阴极浮架的高度、形状等进行周密的计算[1]。
- 1、下载文档前请自行甄别文档内容的完整性,平台不提供额外的编辑、内容补充、找答案等附加服务。
- 2、"仅部分预览"的文档,不可在线预览部分如存在完整性等问题,可反馈申请退款(可完整预览的文档不适用该条件!)。
- 3、如文档侵犯您的权益,请联系客服反馈,我们会尽快为您处理(人工客服工作时间:9:00-18:30)。
线镀层均匀性改善
2009-8-27 15:26:43资料来源:PCBcity作者: 刘良军
摘要:以公司新引进的VCP 电镀线为研究对象,通过试验对比及生产数据搜集,发现在优化液位高度、挂架间距、夹板深度后,合适的底屏、边屏位置,可有效改善垂直方向板边的电力线分布,减少“边缘效应”影响,从而提高镀层均匀性。
试验结果表明:底屏及边屏分别移动2mm 和20mm,对板底部铜厚与均值差均会有约4%的影响;同时优化底屏、边屏后,可将整板CoV 由平均7.0%提至5.1%。
关键词:VCP 底屏边屏镀层均匀性CoV
一、前言
VCP 即Vertical Continuous Plating 的缩写,意为垂直连续电镀,与传统的垂直电镀相比,阴极受镀物采取步进的方式工作是其最大的特点,该工作方式有效提高了电镀品质,同时占地面积大大缩小,且在批量化生产方面也拥有优势,所以近来受到电镀业者的亲睐。
图1 是VCP 线大致工作示意图,该图为操作界面的正面视图。
操作者在上板区进行挂具上板后,板依次进入除油、水洗、预浸段,然后进入镀铜段,完成电镀后,板经过水洗、风干至出板;而挂具进入褪镀段,褪镀完毕至上板区待用。
图1 VCP 线工作示意图
传统的垂直电镀线,阴极相对固定位置,阳极钛篮排布、夹板方式及夹板间距对板件水平方向均匀性有着显著影响,如图2 中所示,一飞巴中,板件夹板间距、Dummy 板使用、端板位置均会影响电力线的分布,从而影响镀铜均匀性。
而以我司的一条VCP 线为例,单边约300 个阳极钛篮,这些钛篮对铜厚共同起着平均的作用,所以单个钛篮的偏位或者缺失对镀铜均匀性的影响几乎可忽略不计。
同时,VCP 采用单个挂具夹一块板的做法,夹板方式固定、单一,夹板深度机械控制,基本不存在变数。
所以VCP 线镀铜均匀性的关键影响因素还需重新验证。
二、试验部分
2.1 试验条件
采用24(L)*18(W)inch 、20(L)*16(W)inch 、16(L)*20(W)inch 三种常用尺寸的试验板;厚度0.3;底铜HOZ ;镀铜液温度25±1℃;电流密度18-20ASF ;镀铜时间54-60min ;目标铜厚;假设电镀效率90-100% 。
2.2 评估方法
测量方法采用通用85 点测试方法,具体测试点分布如图4 所示;镀层均匀性统计方法采用CoV(Coefficient of variance) 评估,CoV 定义如下:,其中:
图4 铜厚85 点测量法
2.3 试验因素
VCP 线与传统垂直电镀线在溶液交换的处理上不同,传统垂直电镀线多采用打气,而VCP 线多采用喷流,两相对比,喷流在保证溶液交换充分的同时,液面相对平稳,对于板垂直的摆动影响更小,这点对于薄板加工更为有利。
VCP 线顶部未设阳极挡板,槽内液位相对平稳,因此对于板顶部的镀铜均匀性而言,液位高度是一个值得考量的因素。
对于底部铜厚,关键影响因素为底屏及边屏设置,这两者可有效改善板底部电力线分布,从而改善铜厚分布。
VCP 的底屏、边屏设置示意图参考图5。
底屏即bottom shield ,通过调整H 型的底屏顶部与板底部的间距,优化板底约50mm 的电力线分布;而边屏即side shield ,通过调整边屏顶部与板底部的间距,优化板底从50mm-200mm 间的电力线分布。
电力线优化示意图参照图3。
至于水平方向的镀铜均匀性,基于VCP 线设计原理,夹具间距的设定,决定了前后板间距,该间距对水平方向镀铜均匀性起着决定性作用。
三、结果与讨论
3.1 板间距对铜厚水平分布的影响
板间距同时影响着相邻两块板板边的铜厚分布。
理想情况,板间距越小越好,那么铜缸中所有的板可被视作一整块板,板件的水平均匀性能达到最佳。
但实际状况是,0 间距会导致板前进过程中发生碰撞。
从试验结果可以得出:为批量稳定生产考虑,不大于10mm 的板间距可有效保证水平铜厚分布。
从图6 可以看出,当我们将板间距从25mm 降低至10mm 时,CoV 由7.04% 下降至3.85% ,降低了45.3% 。