FMEA技术手册(PPT 45张)
《MFMEA培训教材》课件
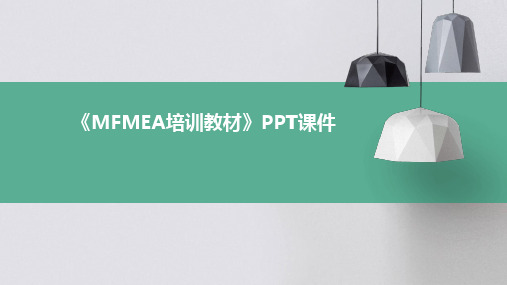
$number {01}
目录
• MFMEA基本概念 • MFMEA实施流程 • MFMEA分析方法 • MFMEA应用案例 • MFMEA总结与展望
01
MFMEA基本概念
MFMEA定义
MFMEA定义:MFMEA(失效模式与影响分析)是一种系统 化的方法,用于识别、评估和解决产品或过程中潜在的失效 模式及其对系统性能的影响。
MFMEA通过分析产品或过程中可能出现的失效模式,评估 其对整个系统性能的影响,并确定预防和减轻这些影响的措 施,从而提升产品和过程的可靠性和安全性。
MFMEA目的和意义
MFMEA目的
MFMEA的主要目的是识别、评 估和降低产品或过程中潜在的失 效风险,提高产品和过程的可靠 性和安全性。
意义
通过MFMEA,企业可以提前发 现和解决潜在问题,减少产品或 过程中的故障和缺陷,提高客户 满意度和产品竞争力。
未来,MFMEA将更加注重数据 分析和人工智能技术的应用,提 高故障模式识别的准确性和效率 。
针对复杂系统和产品的多层次、 多维度分析需求,MFMEA将进 一步发展其分层和集成分析能力 。
THANKS
在问题,提高产品质量和可靠性。
04
MFMEA的流程包括明确分析对象、确定分析层次 、列出故障模式、分析故障原因和影响、评估风险
优先级、制定改进措施等步骤。
MFMEA未来发展方向
随着技术的不断进步和应用领域 的拓展,MFMEA将进一步发展 并应用于更广泛的领域。
针对快速迭代开发和上市的需求 ,MFMEA将发展更高效的分析 方法和工具,缩短分析周期和降 低成本。
详细描述
故障影响评估应考虑产品或过程的功能要求、使用环境以及相关法律法规等因素,以确定故障对产品 或过程的影响程度。
《MFMEA培训教材》PPT课件
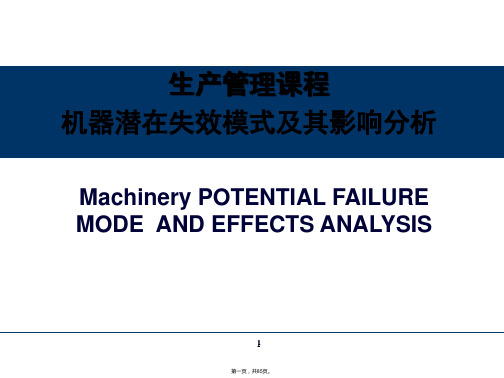
第十二页,共85页。
一个团队,应该是有思考性、自主性、合作性的组织。团队 的成员拥有共同的目标,是在一条船上共患难的水手!
对于团队,有个很新颖的解释:TEAM--Together Everybody can Achieve More! (只有在一起,每个人才能做到
更多!)
113
第十三页,共85页。
同角色的组合达至完美!
适合FMEA的小组成员:
-装配、制造人员(带来现场的经验) -设计人员(包括其它部件、子系统、系统和总成) -工艺人员(包括其它部件、子系统、系统和总成)
-可靠性分析/试验人员(带来失效的经验) -材料工程师(带来材料的要求) -质量工程师(带来质量控制的要求及相关的解决方案) -服务人员(带来客户处抱怨)
第三十一页,共85页。
8.核心小组
•列出所有被授权识别和执行任务的负责人姓名及所在部门(建议包含所有成 员的姓名,部门,电话号码,地址等)。
9a.子系统名称
输入对被分析的子系统名称的描述。
自动装货设备,锭子,水力的,电子的,工作站-5-左边。
设备等级术语
举例
•设备
转移生产线
•系统
设备工作站
•子系统
所有的MFMEA都关注设计。
MFMEA 作为专门的技术应用以识别并帮助最大程度地
减少潜在的隐患一直是非常重要的 !
8
第八页,共85页。
成功实施MFMEA项目的最重要因素之一是时间性。其含义是指 “事件发生前”的措施,而不是“事实出现后”的演练。为实现最大价 值,MFMEA必须在设备的失效模式被纳入到设备设计之前进行。事先 花时间很好地完成MFMEA分析,能够最容易、低成本地对设备进行更 改,从而最大程度地降低后期更改的危机。MFMEA能够减少或消除实 施可能会带来更大隐患的预防/纠正性更改的机会。
FMEA培训教材-PPT精选全文

客户要求 方便调整
舒适 移动顺畅
ቤተ መጻሕፍቲ ባይዱ
产品规格 调节高度 坐垫厚度 旋转角度 椅轮松紧
9
1
3
9
3
1
9
9
重要性 60% 30% 10%
分值
640
330
180
90
FMEA 得原理
客户要求 方便调整
舒适 移动顺畅
分值
产品规格 调节高度 坐垫厚度 旋转角度 椅轮松紧
9
1
3
9
3
1
9
9
640
330
180
90
参数
上升50CM
FMEA 得原理
一、FMEA基本知识
练习:
公司产品:车门 客户要求:
•方便开关 •噪音小 •安全
FMEA 得原理
FMEA 得原理
FMEA 得原理
客户质量要求 Input
客户质量目标
FMEA Output
CTQ 清单 CP 控制计划
FMEA
FMEA 得原理
Output
CTQ 清单
CTQ产出原则:
压 合 状 态
方法
特
样本Sample
殊 特 性 分
产品特 性/过程 参数规 格/公差
评价/ 测量技
术
容 量
频率
类
《
首检
MODULE 检验标
准》
5-20倍 显微镜
6P CS
:6PCS/ 抽检 : 每10PCS
抽1PCS
反应计
控制方法/ 统计技术
责任人
划
《CD-HFM0419701 LCM 镜检 不良明细
措施?
FMEA培训资料ppt
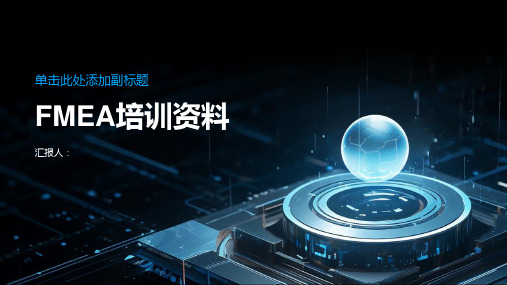
风险评估:对故障进行风 险评估,确定其危害程度 和发生概率
改进措施:提出针对该故 障的改进措施,包括设计、 工艺等方面的改进
实施效果:对改进措施的 实施效果进行评估和验证, 以确保改进的有效性。
如何整理和撰写FMEA报告
确定报告的目的 和范围
收集相关数据和 信息
整理和分析数据
撰写报告并完善 内容
FMEA报告的实例分享及解析
评估流程:按照规定的流程进行 风险评估,包括风险识别、分析、 评价等环节
添加标题
添加标题
添加标题
添加标题
评估标准:制定评估标准,包括 风险等级、严重程度等
数据采集:采集相关的数据和信 息,包括历史数据、行业数据等
FMEA中风险评估的步骤和要点
添加标题
确定评估对象:明确评估的对象,包括产品、过程、 系统等,并确定评估的范围和重点。
问题:FMEA分析缺乏系统性,未形成完整的分析流程 解决方法:建立完善的FMEA分 析流程,确保分析的全面性和系统性 解决方法:建立完善的FMEA分析流程,确保分析的全面性和系统性
问题:FMEA分析结果未得到有效应用,未发挥应有的作用 解决方法:加强 FMEA分析结果的应用,将分析结果应用于设计和生产中,提高产品质量和安全性。 解决方法:加强FMEA分析结果的应用,将分析结果应用于设计和生产中,提高产品质量和 安全性。
等。
案例分析:通过 具体的案例分析,
展示如何运用 FMEA解决实际 问题,并分享从 中获得的经验和
教训。
添加标题
结论:总结 FMEA实践经验 的重要性,并强 调其在提高产品 质量和降低风险 方面的贡献。
FMEA在实践中的应用案例
案例1:汽车行业中的FMEA应用 案例2:医疗器械中的FMEA应用 案例3:航空航天中的FMEA应用 案例4:化工行业中的FMEA应用
FMEA分析PPT演示文稿

PFMEA的原理
(1) “过程功能/要求”:是指被分 析的过程或工艺。该过程或工艺可以是技 术过程,如焊接、产品设计、软件代码编 写等,也可以是管理过程,如计划编制、 设计评审等。尽可能简单地说明该工艺过 程或工序的目的,如果工艺过程包括许多 具有不同失效模式的工序,那么可以把这 些工序或要求作为独立过程列出。
PFMEA 分析
PFMEA以其最严密的形式总结了人们在生 产制造过程中防范于未然、追求卓越的思 想。
它通过对工艺和制造过程要求和功能的系 统分析,凭借已往的经验,在最大范围, 充分考虑到那些潜在的失效模式及其相关 的起因与后果。
PFMEA的原理
几个关键步骤: ● 确定工艺或制造过程潜在失效模式与起因; ● 评价失效对产品质量和顾客的潜在影响; ● 找出减少失效发生条件的过程控制变量,并制 定预防措施; ● 编制潜在失效模式严重程度分级表,确保严重 的失效模式得到优先控制; ● 跟踪控制措施的实施情况,更新失效模式分级 表。
PFMEA的原理
(9) “措施结果”:是对上述“建议采取 的措施”计划方案之实施状况的跟踪和确 认。在明确了纠正措施后,重新估计并记 录采取纠正措施后的严重性、可能性和不 易探测性数值,计算并记录纠正后的新的 风险级值,该数值应当比措施结果之前的 风险级值低得多,从而表明采取措施后能 够充分降低失效带来的风险。
这项技术出现于上世纪60年代中期,最早 应用在美国航空航天领域,如阿波罗登月 计划。
1974年被美国海军采用。 再后来被通用汽车、福特和克莱斯勒三大
汽车公司用来减少产品制造及工艺过程中 出现的失效模式,从而达到控制和提升质 量的目的。
PFMEA 分析
2003年2月1日,美国东部时间上午9时(北 京时间1日22时),返航的哥伦比亚号航天 飞机在大约63 km高空处与地面控制中心失 去联系,在得克萨斯州地区上空爆炸解体, 机上7名航天员全部遇难。
FMEA培训教材(ppt)(2024)

后果分析
针对每种失效模式,分析 其可能对产品功能、安全 性、可靠性等方面造成的 影响和后果。
风险评估
对每种失效模式及其后果 进行风险评估,确定其严 重度、发生度和检测度等 级。
14
评估风险等级并采取预防措施
风险等级评估
综合考虑严重度、发生度 和检测度等级,对每种失 效模式进行风险等级评估 。
2024/1/30
4
FMEA发展历程
起源
FMEA起源于20世纪40年代的军事领域,当 时主要用于评估武器系统的可靠性。
发展
随着工业技术的进步,FMEA逐渐应用于民 用领域,如汽车、航空航天、电子、医疗等 。
标准化
为了规范FMEA的实施,国际标准化组织( ISO)和美国汽车工程师学会(SAE)等制定 了相应的标准和指南。
。
2024/1/30
可靠性增长
在产品设计阶段,通过不断测试和 验证,提高产品的可靠性和稳定性 ,降低失效模式的发生概率。
持续改进
在产品设计和生产过程中,持续关 注失效模式的变化和趋势,及时采 取改进措施,确保产品质量的持续 改进和提升。
16
04
FMEA在生产过程控制中应用
2024/1/30
17
识别生产过程中潜在失效模式及后果
通过引入先进设备、优化工艺流程、提高员工技能等手段 ,提升生产过程的能力和效率,降低潜在失效模式的发生 概率。
风险管理机制完善
建立完善的风险管理机制,包括风险识别、评估、预防、 监控和应对等环节,形成闭环管理,确保生产过程风险的 有效控制和持续改进。
20
05
FMEA在设备维护保养中应用
2024/1/30
21
FMEA培训教材PPT完整版(2024)

产品设计阶段FMEA案例分析
案例一
某型号汽车发动机设计FMEA分 析。针对发动机系统可能出现的 故障模式进行分析,如气缸磨损 、活塞环断裂等,制定相应的改
进措施。
案例二
某型号手机电池设计FMEA分析 。针对电池可能出现的过热、短 路等故障模式进行分析,优化电 池结构和电路设计,提高电池安
全性。
26
过程控制阶段FMEA流程
定义过程范围和功能
01
识别潜在的故障模式
02
评估故障影响的严重度、发生
度和检测度
03
计算风险优先数(RPN)并排 序
04
制定并实施控制措施
2024/1/29
05
跟踪验证控制措施的有效性并
更新FMEA
06
27
过程控制阶段FMEA案例分析
案例一
某汽车制造厂涂装车间过程FMEA分 析
为生产过程FMEA提供支持
产品设计阶段FMEA的输出可以为生产过程 FMEA提供重要的输入和支持。
20
产品设计阶段FMEA流程
组建FMEA团队
由多部门、多学科的专业 人员组成,包括设计、制 造、质量、采购等。
2024/1/29
定义系统和子系统
明确产品的结构和功能, 划分系统和子系统。
识别故障模式
针对每个子系统或部件, 识别所有可能的故障模式 。
9
组建FMEA团队并分配任务
02
01
03
2024/1/29
组建多学科团队
包括设计、制造、质量、采购等相关领域专家。
分配角色与责任
明确团队成员的角色和责任,确保任务有效执行。
提供培训与支持
为团队成员提供FMEA培训,确保掌握相关知识和技 能。
FMEA培训教材演示文稿幻灯片

对组织和管理层的影响
• FMEA是企业内的一项重要活动,涉及整个产品实 现过程;
• FMEA很费时,而且需要有足够的资源; • 明确FMEA的职责以及高层管理者的承诺至关重要; • 要实施FMEA全面的培训,包括:管理层、使用者、
供方、推动者。
基本架构 Basic Structure
本手册所描述的建议FMEA格式的目的是为了组织收集和展 示相关FMEA信息,具体的格式可以根据组织的需要和顾客 的要求变化。
它工具之间的联系。
5. 对严重度、频度、探测度的打分表进行了改进,以便对实际的分析和 利用更有意义。
6. 引进了当前行业中正在被运用的可供选择的几种方法:增加了包含样 表和在特殊情况下运用的FMEA的附录;从以前关注“标准格式”改 变为几种代表当前行业中使用的FMEA的选择。
7. RPN不再被建议作为评价风险的首要方式,修订了改进的需求,包含 了一个附加的方法,而且明确说明了不建议使用RPN限值的方法。
什么是FMEA
在产品设计阶段和过程设计阶段,对构成产 品的子系统、零件,对构成过程的各个工序 逐一进行分析,找出所有潜在的失效模式, 并分析其可能的后果,从而预先采取必要的 措施,以提高产品的质量和可靠性的一种系 统化的活动。
FMEA的类型
SFMEA —— 对产品开发、过程策划综合评估,通过系统、 子系统不同层次展开,自上而下逐级分析,更注重整体性、 逻辑性。
• 20世纪70年代后期FMEA被美国汽车工业界所引用,作为设计评审的一 种工具。
• 1993年2月美国三大汽车公司联合编写了FMEA手册,并正式出版作为 QS-9000质量体系要求文件的参考手册之一,1995年2月出版了第二版, 2001年7月出版了第三版。
FMEA培训教材ppt完整版

FMEA培训教材ppt完整版•FMEA概述与基本原理•失效模式识别与评估方法•故障原因分析技巧与工具应用•风险等级划分标准与应对措施制定目录•FMEA在产品设计阶段应用实践•FMEA在生产过程监控和持续改进中作用•总结回顾与展望未来发展趋势01FMEA概述与基本原理FMEA定义及发展历程FMEA定义故障模式与影响分析(FailureModes and Effects Analysis)发展历程起源于军事领域,后广泛应用于航空、汽车、电子等各个行业FMEA核心思想与目标核心思想预防性分析,识别潜在故障模式及其对系统的影响,提前采取措施降低风险目标提高产品可靠性、减少维修成本、增强客户满意度032. 功能分析识别系统或部件的功能及潜在故障模式01适用范围产品设计、生产过程、服务流程等各个环节021. 定义范围明确分析对象及目标评估故障模式对系统性能、安全、经济等方面的影响3. 故障影响分析综合考虑故障发生概率、严重度及可检测性,对故障模式进行风险等级排序4. 风险等级评估针对高风险故障模式,制定预防措施和应急计划5. 制定措施定期回顾FMEA 结果,更新措施并持续改进6. 跟踪与持续改进02失效模式识别与评估方法产品无法实现设计功能或性能不达标,如电子设备无法开机、机械部件卡滞等。
功能性失效安全性失效可靠性失效产品存在安全隐患,可能导致人身伤害或财产损失,如汽车刹车失灵、电器短路引发火灾等。
产品在规定条件下和规定时间内无法完成规定功能,如电池寿命短、设备频繁故障等。
030201常见失效模式类型介绍失效模式识别技巧与工具技巧了解产品工作原理及结构特点分析历史故障数据及维修记录•运用头脑风暴等方法集思广益工具故障树分析(FTA)事件树分析(ETA)因果图(Cause-Effect Diagram)01020304•方法选择:根据失效模式的性质和影响程度选择合适的评估方法,如风险矩阵、风险指数等。
实施流程1. 明确评估目标和范围2. 收集相关数据和信息3.选择合适的评估方法并建立评估模型4.对失效模式进行定量或定性评估5.根据评估结果制定相应的改进措施并跟踪验证03故障原因分析技巧与工具应用故障树分析法概述故障树的建立故障树的定性分析故障树的定量分析故障树分析法(FTA )原理及应用01020304介绍FTA 的基本概念、原理、作用及适用范围。
FMEA制作教程PPT(共155页)
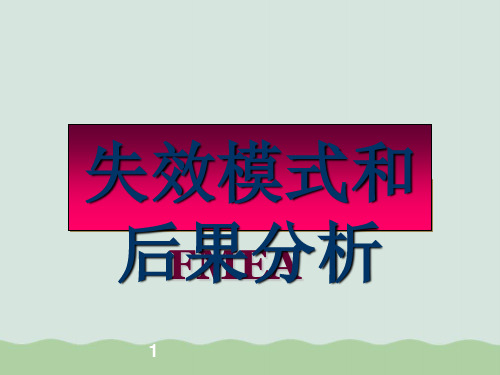
1
没有预兆
中国古代名言
还没有成为事实
计 能规于 未 , 虑 能防于 未 .
兆
然
计谋和策 略
思考和谋划
2
课程大
●FMEA的基本概念
○定义和特点
纲●产品设计/过程设计/过程控制
的责任
○FMEA的发展历史 ○FMEA在产品实现中的作用
●可靠性基础知识
○FMEA基本概念
●DFMEA的分析方法 ●PFMEA的分析方法 ●设备维护FMEA简介
11
FMEA在产品实现中的作
FMEA是开发经验的用记载和积累,将 为其他类似产品的设计和开发提供经 验。
ISO/TS16949要求: 产品设计输入——信息的利用:组织应有一个过
程,将从以往设计项目、竞争对手分析、供方反馈、内部 输入、外部数据及其他相关来源获取的信息推广应用于当 前和未来有相似性质的项目。
13
FMEA在产品实现中的作 用
FMEA是提高员工质量意识、培训员 工操作技能的教材。
ISO/TS16949要求: 对影响产品质量的岗位,组织应对新上岗或调整工作
的人员提供岗位培训。包括合同制人员和代理工作人员。 应将不符合质量要求给顾客带来的后果告知对质量有影响 的工作人员。
作业指导书从正面描述了过程的要求,而FMEA从顾 客的立场反面向作业者预警了不合格产品及其原因。
该 项能性力能: 指标的临界值就是“故障判据”或“失效判据”。
由于产品发生故障带有偶然性,所以可靠性定义中的“能
力”具有统计学上1的7意义,表示能力的指标有可靠度、平均寿
命、失效率等。
产品质量和可靠 性 产品质量: 一组固有特性满足顾客和其他相关方要求的能力其
FMEA培训教材PPT课件

20
APQP手册的目的是将由克来斯勒、福特和通用汽车公司联合制定的一 般产品质量策划指南提供给供方或分承包方。 APQP手册为制定产品质量计划提供指南,使用该指南具有如下预期的 收益: -将资源致力于顾客满意; -促进对所需更改的早期识别; -避免晚期更改; -以最低的成本及时提供优质产品。
21
7
FMA-失效模式分析
– 什么是FMA? –Failure Mode Analysis
• 关键词: 失效-已实际发生 • 100%既成事实 • 集中于: 诊断-处理已知问题 • FMA在生产范围内实施 • FMEA的输入
8
Fault Tree Analysis (FTA) 失效树分析
灯泡烧了
房间变暗
实践,但并不推荐使用。
13
第二章 FMEA实施的目的和流程
※ 为什么需要进行FMEA? ※ FMEA会给我们带来什么?
14
ISO/TS16949 技术规范结构
顾客关于以下内容的支持 参考手册:
产品质量先期策划和控制 计划APQP&CP MSA FMEA SPC 其他工具和技能等
国际标准 ISO9001:2000
15
ISOTS16949:2009 7.1 产品实现的策划
组织必须策划和开发产品实现所需的过程。产品实现的策划必须与质量管理体系 其他过程的要求相一致(见4.1)。 在对产品实现进行策划时,组织必须确定以下方面的适当内容: a) 产品的质量目标和要求, b) 针对产品确定过程、文件和资源的需求, c) 产品所要求的验证、确认、监视、检验和试验活动,以及产品接收
23
输入(源于第二章的输入)
设计失效模式和后果分析 (DFMEA) 可制造性和装配设计 设计验证 设计评审 制造样件-控制计划 工程图样(包括数学数据) 工程规范 材料规范 图样和规范更改 新设备、工装和设施要求 特殊产品和过程特性 量具/有关试验装备要求 小组有关可行性承诺和管理 者支持
FMEA培训教材ppt
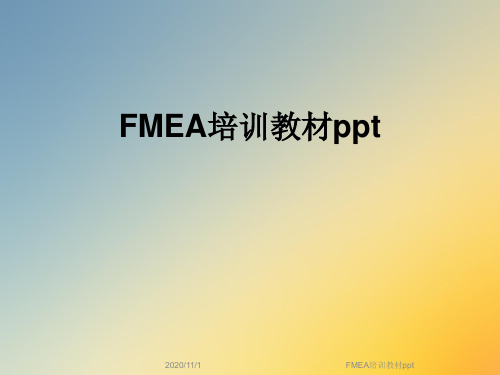
FMEA培训教材ppt
制程失效定义: 产品在经过一制造程序时,因制程而造成 其特性无法满足产品规格或甚至损坏者,即为制程失效.
失效效应的严重等级分为四級:
(A).I级:致命失效
此类失效模式发生可能会导致整个系統
FMEA培训教材ppt
2020/11/1
FMEA培训教材ppt
目录
•什么叫FMEA •FMEA分类和特点 •FMEA技术的发展与应用 •RPN评价 •FMEA的应用(以PFMEA为 例)
FMEA培训教材ppt
FMEA由来
AIAG 全称Automotive Industry Action Group,即汽车工业行动小组。该组织 成立于1982年,由美国三大汽车公司通用、福特和克莱斯勒共同创建,是全 球公认的著名的非盈利组织。
3
- 第二章﹕過程FMEA (Process Failure Mode & Effect Analysis )
PFMEA分析方法的流程 先期规划 主流程 结果应用
FMEA培训教材ppt
组成FMEA团队 资料收集
制定执行方案
先期规划
产品设计 制造工艺 使用维修 环境
表格格式 分析层次 失效定义 成果整合
注意
不要混淆 DFMEA与PFMEA的起因和失效
过程潜在的失效模式及后果分析
过程FMEA(PFMEA)
PFMEA简介
1.确定与产品相关的过程潜在失效模式 2.评价失效对顾客的潜在影响 3.确定潜在或装配过程失效的起因﹐确 定减少失效发生或找出失效条件的过程 控制变量 4.编制潜在失效模式分级表﹐然后建立 考虑纠正措施的优选体系 5.将制造或装配过程的结果编制成文件
FMEA培训资料新版 ppt课件

资料
2.1 可靠性与可靠度
新版
2.1.1 可靠性
产品在规定的条件下和规定的时间内完成规 定功能的能力。
规定条件:使用条件、环境条件、贮存条件 规定时间:小时、频次、里程 规定功能:故障判据
产品质量特性随时间变化的内在规律
SS
FMEA培训资料新版
FMEA
可靠性的形成
} 设计过程形成:分析、评估、优化 固有 可靠性 生产过程形成:控制计划
评价产品或过程中潜在的失效模式,查明其对 系统的影响程度,以便采取措施进行预防。
并联系统可靠性模型
A1 A2
—— 系统与系统结构图
An
n
RS(t)= 1 - 〔 1 - Ri(t)〕
i=1
SS
—— 系统与系统结构图
混联系统可靠性模型
B1
A1
A1
B2
B3
C1 A3
C2
SS
2.4 可靠性工程
FMEA
目的 : 减少失效率和寿命周期费用;
费用
总费用 研制费用
最佳区域
使用费用
SS
2.3 系统与可靠性模型 系统:
FMEA 培训资 料新版
广义概念: 由若干个单元有机组成的一个可完成某一 功能的综合体。
狭义概念: 为完成某项任务或实现某种功能的设备、 人员、技术及环境的集合。
系统的可靠性R系=R设·R软件·R人员·R接口
SS
——系统与系统结构图
一般系统的功能结构图
SE1.1
格” 建议不要把RPN作为风险评估的首要方法。
FMEA培训资料新版
第一章:提供了FMEA通用指南,提出管理者支持的需求 和定义一个开发并维持FMEA的过程的需求,以及持续改 进需求;
- 1、下载文档前请自行甄别文档内容的完整性,平台不提供额外的编辑、内容补充、找答案等附加服务。
- 2、"仅部分预览"的文档,不可在线预览部分如存在完整性等问题,可反馈申请退款(可完整预览的文档不适用该条件!)。
- 3、如文档侵犯您的权益,请联系客服反馈,我们会尽快为您处理(人工客服工作时间:9:00-18:30)。
4.1972年美國福特汽車公司所屬北美汽車業務部 訂定之“可靠性方案”中設置一個專案小組負 責研議FMEA,其後列於該公司Q-101品質管理 規範中。 5.1974年美軍出版MIL-STD-1629 FMECA作業程 序,並於1980年修訂為MIL-STD-1629 A,延 用至今。 6.1985年國際電工委員會(IEC)出版之FMECA 國際標準(IEC 812),即係參考MIL-STD1629 A加以修改而成
7.1993年,美國品質管制學會(ASQC)和汽車 工業行動集團(AIAG)整合三大汽車廠(Ford, Chrysler,GM)的FMEA指南,發行了FMEA參 考手冊(第一版)。 8.1995年2月QS 9000 FMEA參考手冊發行第二版, 再於2001年7月發行第三版。
FMEA特点
DFMEA的理解对象
1) 2) 3) 4) 系統功能 任務輪廓 環境輪廓及 操作模式
DFMEA 可靠度方块图
1) 产品的分解 2) 系统的interface
可靠性方块图(1)
系統 車身
事件发生前”的措施,而不是“事实出 现 后”的演练。 是一种系统活动 动态的及时反映最新的工艺 团队的参与 永不停止的持续改进
实施FMEA的目的及意义
一般而言,FMEA的具體目的有下列數項:
1.發現、評價產品 / 製程中潛在的失效及其效 應。 2.找到能夠避免或減少這些潛在失效發生的措 施。
3.總結上述的過程並予以文件化。
DFMEA
对于D-FMEA,“顾客”为:
国家法律、法规 (如,安全、排放、噪 音) 最终使用者, 车型设计工程师/小组, 总成、部件、零件制造和装配过程设计 工程师/小组 总成、部件、零件制造和装配过程
DFMEA的流程
依據國際電工委員會(IEC)所制定的FMEA規範,設計 FMEA的實施程序如下圖示:
FMEA的产生
1.1950年格魯曼(Grumman)公司因飛機的推動方式由 螺旋槳進步到噴射引擎;操控系統也由鋼索改為油壓 或電器裝置,為防範飛機飛行時,該等裝置故障而開 發了FMEA。 2.波音與馬丁公司在1957年正式編訂FMEA的作業程序, 列在其工程手冊中。 3.1960年代初期,美國航空暨太空總署(NASA)實施阿 波羅(Apollo)計劃時,將可靠性及安全管理列為合約 中的重要條款,並要求合約對象實施FMEA。
【實施程序】
理解解析对象 作可靠性方块图
列举失效模式
影响度解析
严重度评估
扩展到各种对策
DFMEA的理解对象
(1)規格:產品的使用目的、機能、性能、壽命、限制條件等。 (2) 環境條件-使用時、停止時、保管時的溫度、溼度、噪音、 放射線量、震動、壓力等。 (3)使用條件-啟動和停止次數、啟動時間、連續運轉時間、操 作步驟、操作者的水準等。
(4)可靠性、維護性特性:稼動率、可靠性、維護性、保養支 援的目標值、運轉和保養人員、操作或保養人員之技術水 準等。
DFMEA的理解对象
(4)維護性計畫:定期保養、故障診斷、維護性實施計劃、 維護性作業之期間。
(5)法律上的要求事項:產品之使用或製造、建築所產生法 律上的限制等。 (6)圖書類:系統之系統圖、機器構造圖、動作順序、各種 設定值、操作步驟書、操作說明書、故障事例等 (7)類似系統的調查:機能、性能、特性、任務、使用條 件等方面類似的系統,調查其主要特徵、問題點和對策 製作特性比較表、故障事例,以及其他公司產品的比較IΒιβλιοθήκη O/TS16949 系列培训教程之
FMEA技术手册
课程目的
为了使您:
1. 理解实施FMEA的目的及意义
2. 掌握实施FMEA方法及要点
3. 熟悉实施FMEA的操作流程 4. 知晓DFMEA及PFMEA制作方法
课程内容
FMEA的定义及特点 实施FMEA目的及效益 FMEA的工作模式 FMEA的工作流程
FMEA在产品策划中的运用
DFMEA运用
PFMEA运用
FMEA定义
FMEA是“Failure Mode Effects Analysis”的縮 寫,一般稱為「失效模式與效應分析」。 FMEA係一種預防技術,它是一項系統化的 活動;工程人員自概念設計階段開始,就透過 嚴密的分析作業;列出及評估系統內潛在的失 效模式和可能造成的效應並及時採取矯正措施, 使設計、生產、製造、組裝等作業得以注意改 善,並使產品逐漸朝向最佳化設計的目標。
实施FMEA的目的及意义
實施FMEA有下列益處: 1.累積經驗,早期發現失效原因及採取因應之道 2.促進設計改良。 3.改善作業方法。 4.幫助作業人員訓練,使其能學到正確找出失效 原因的方法及採取有效的措施。 5.公司對經驗的累積及技術能制度化的保存。
FMEA实施手法
FMEA过程顺序
子系 统 功能 要求 潜在 失效 模式 潜在 失效 后果 严 重 度 S 级 别 潜在 失效 起因/ 机理 频 度 O 现行控制 预 防 探 测 探 测 度 D R P N 建议 措施 责任及 目标完 成日期 措施结果 采取 的措 施 S O D R P N
FMEA在产品策划中的运用
DMEA
跨功能小组在开展设计FMEA时,应参考以下文件和资料:
保修信息。 顾客抱怨、退货资料。 纠正和预防措施。 类似产品的设计FMEA APQP第一阶段输出,即第二阶段输入和 任何其它相应输入。
DFMEA输出
设计FMEA的输出
潜在设计失效模式。 潜在关键设计要求。 设计问题:曾经受到制造和装配作业挑 战的设计问题。 新设计要求:尚无制造或组装作业的经 验。 设计验证计划和报告(DVP&R) 改进设计,或更改原有设计。
后果是 什么? 功能、特 性或要求 是什么? 会是什么问题? -无功能 -部分功能/功能 过强/功能降级 -功能间歇 -非预期功能
有多 糟糕 ? 起因是 什么? 发生的频 率如何?
能做些什么? -设计更改 -过程更改 -特殊控制 -标准、程序或 指南的更改
怎样能得到 预防和探测? 该方法在 探测时 有多好?