船舶双层底分段装配
浅析船体结构分段装配工艺研究
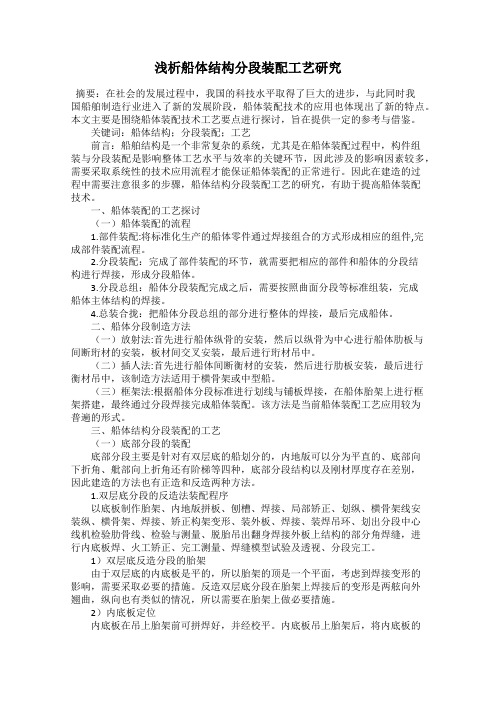
浅析船体结构分段装配工艺研究摘要:在社会的发展过程中,我国的科技水平取得了巨大的进步,与此同时我国船舶制造行业进入了新的发展阶段,船体装配技术的应用也体现出了新的特点。
本文主要是围绕船体装配技术工艺要点进行探讨,旨在提供一定的参考与借鉴。
关键词:船体结构;分段装配;工艺前言:船舶结构是一个非常复杂的系统,尤其是在船体装配过程中,构件组装与分段装配是影响整体工艺水平与效率的关键环节,因此涉及的影响因素较多,需要采取系统性的技术应用流程才能保证船体装配的正常进行。
因此在建造的过程中需要注意很多的步骤,船体结构分段装配工艺的研究,有助于提高船体装配技术。
一、船体装配的工艺探讨(一)船体装配的流程1.部件装配:将标准化生产的船体零件通过焊接组合的方式形成相应的组件,完成部件装配流程。
2.分段装配:完成了部件装配的环节,就需要把相应的部件和船体的分段结构进行焊接,形成分段船体。
3.分段总组:船体分段装配完成之后,需要按照曲面分段等标准组装,完成船体主体结构的焊接。
4.总装合拢:把船体分段总组的部分进行整体的焊接,最后完成船体。
二、船体分段制造方法(一)放射法:首先进行船体纵骨的安装,然后以纵骨为中心进行船体肋板与间断珩材的安装,板材间交叉安装,最后进行珩材吊中。
(二)插人法:首先进行船体间断衡材的安装,然后进行肋板安装,最后进行衡材吊中,该制造方法适用于横骨架或中型船。
(三)框架法:根据船体分段标准进行划线与铺板焊接,在船体胎架上进行框架搭建,最终通过分段焊接完成船体装配。
该方法是当前船体装配工艺应用较为普遍的形式。
三、船体结构分段装配的工艺(一)底部分段的装配底部分段主要是针对有双层底的船划分的,内地版可以分为平直的、底部向下折角、舭部向上折角还有阶梯等四种,底部分段结构以及刚材厚度存在差别,因此建造的方法也有正造和反造两种方法。
1.双层底分段的反造法装配程序以底板制作胎架、内地版拼板、刨槽、焊接、局部矫正、划纵、横骨架线安装纵、横骨架、焊接、矫正构架变形、装外板、焊接、装焊吊环、划出分段中心线机检验肋骨线、检验与测量、脱胎吊出翻身焊接外板上结构的部分角焊缝,进行内底板焊、火工矫正、完工测量、焊缝模型试验及透视、分段完工。
船舶双层底分段装配
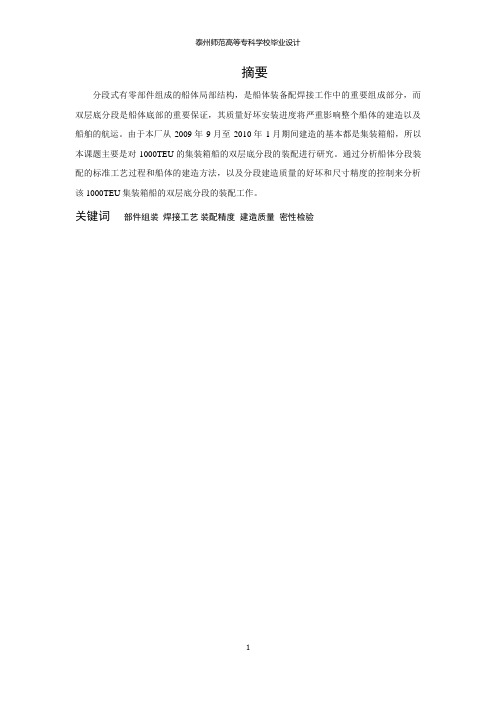
摘要分段式有零部件组成的船体局部结构,是船体装备配焊接工作中的重要组成部分,而双层底分段是船体底部的重要保证,其质量好坏安装进度将严重影响整个船体的建造以及船舶的航运。
由于本厂从2009年9月至2010年1月期间建造的基本都是集装箱船,所以本课题主要是对1000TEU的集装箱船的双层底分段的装配进行研究。
通过分析船体分段装配的标准工艺过程和船体的建造方法,以及分段建造质量的好坏和尺寸精度的控制来分析该1000TEU集装箱船的双层底分段的装配工作。
关键词部件组装焊接工艺装配精度建造质量密性检验AbstractSegmented composed of hull parts, is equipped with local structure with hull welding work is an important part of the double bottom block, and is an important guarantee of hull bottom, its quality installation schedule will seriously affect the ship hull building and shipping. Since the factory from 2009 September January 2010 were built during the basic container ship, so this topic is mainly to the container ships of 1000TEU assembly of double bottom block. Through the analysis of the standard of block assembly process and hull building method, and the construction quality of subsection and precision analysis to the control of 1000TEU this container ship assembly work double bottom block.Keywords: Assembly Welding process Fabrication accuracyConstruction quality tightness test目录摘要 (2)英文摘要 (3)目录 (4)一论双层底分段的装配 (5)(一)双层底分段介绍 (5)(二)双层底分段流程 (6)(三)双层底建造工艺 (7)(四)双层底分段装焊 (10)二分段矫正及检验 (12)(一)分段装配完工后的矫正 (12)(二)焊接过程中的检验 (13)(三)分段完工后的检验 (14)三分段建造工艺结论 (15)致谢 (17)参考文献 (18)论船舶双层底分段的装配一论双层底分段装配(一)双层底分段介绍双层底分段一般是指货舱的底部分段,其内底板又可分为平直的,舭部向下折角,舭部向上折角,以及阶梯状等四种,由于双层底分段的结构形式,通常建造方法有正身建造及反身建造,而大多数船厂都采用反身建造,此方法简单,翻身次数少,危险性小,同时也增加了产品效益,分段图如下所示:1-1双层底分段(二)双层底分段流程以内底板为基准,制作胎架→内底板拼板→刨槽→焊接、局部矫正→划纵、横骨架线→安装纵、横骨架→(可采用分离装配法或混合装配法)→焊接→矫正构架变形→(修顺构架底部型线)→装外板→焊接→装焊吊环→划出分段中心线及检验肋位线→检验与测量→脱离胎架吊出翻身→焊接外板上构件的部分角焊缝,同时进行内底板封底焊→火工矫正→完工测量→焊缝密性试验及透视→分段完工分段流程基本图片如下:1-2 内地板拼装与划线 1-3安装纵横骨架1-4分段预舾装 1-5分段拼装好后盖1-6分段翻身 1-7吊离胎架(三)双层底建造工艺1双层底分段反身建造的胎架:因双层底的内底板是平面,一般在设计时要根据分段平面图而做,1-8分段平面图建造分段胎架则还要考虑甲板梁拱,通常胎架的基准面是平面或带梁拱,若考虑焊接变形的影响,要作相应的反变形措施:双层底分段反身建造,在胎架上焊接后的横向变形往往是两舷向外翘曲,纵向亦有两头向上翘曲的变形,故需在胎架上作出相应的反变形措施。
船舶分段建造
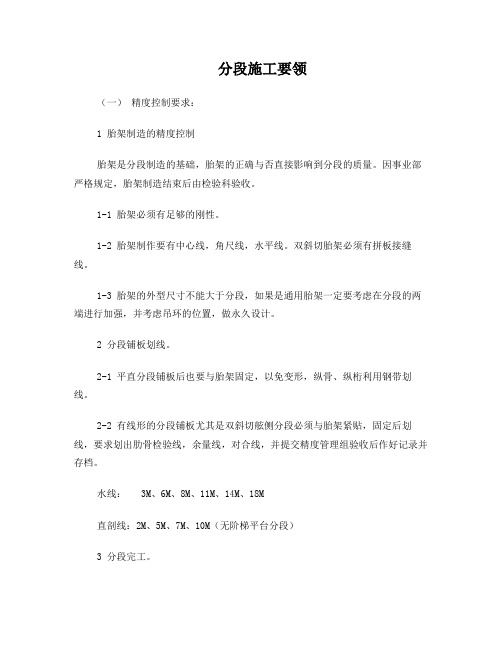
分段施工要领(一)精度控制要求:1 胎架制造的精度控制胎架是分段制造的基础,胎架的正确与否直接影响到分段的质量。
因事业部严格规定,胎架制造结束后由检验科验收。
1-1 胎架必须有足够的刚性。
1-2 胎架制作要有中心线,角尺线,水平线。
双斜切胎架必须有拼板接缝线。
1-3 胎架的外型尺寸不能大于分段,如果是通用胎架一定要考虑在分段的两端进行加强,并考虑吊环的位置,做永久设计。
2 分段铺板划线。
2-1 平直分段铺板后也要与胎架固定,以免变形,纵骨、纵桁利用钢带划线。
2-2 有线形的分段铺板尤其是双斜切舷侧分段必须与胎架紧贴,固定后划线,要求划出肋骨检验线,余量线,对合线,并提交精度管理组验收后作好记录并存档。
水线: 3M、6M、8M、11M、14M、18M直剖线:2M、5M、7M、10M(无阶梯平台分段)3 分段完工。
3-1 分段完工后必须按图纸要求划出肋骨检验线,水线,中心线,直剖线以及分段对合线。
3-2 精度管理组在完工测量时必须认真检查分段的外形尺寸(以立体图作为测量草图)、焊接变形数据,型值必须控制在允许误差范围内,超差一律返工修正,不给后道工序造成隐患,并将数据存档,必要情况下应传达给船台或船坞。
3-3 检验工具必须经常校对,修正。
3-4 严格执行自由边火工工艺。
4 分段制造过程中焊接变形控制。
分段制造过程中的焊接变形一般可以分为两个过程。
4-1 在胎架上的变形,分段在胎架上制造时,由于构件间的焊接而产生变形。
此时,由于受胎架的刚性强制固定而显得不很突出,一旦脱离胎架,处于自由状态时就发现了明显的变形。
这种变形是很难控制的。
它是受装配构件时自强与强制情况及间隙大小而影响。
但是,这种变形是局部的,不是大面积的。
4-2 分段在胎架上随制造进度而产生变形。
例如,带有转圆的底部分段,(反造)在转圆外板焊接时就产生变形,这种变形是大面积的,而且造成的影响较大,在胎架制造时加放变形是防范措施之一。
4-3 分段脱离胎架后的焊接变形。
典型双层底分段制造
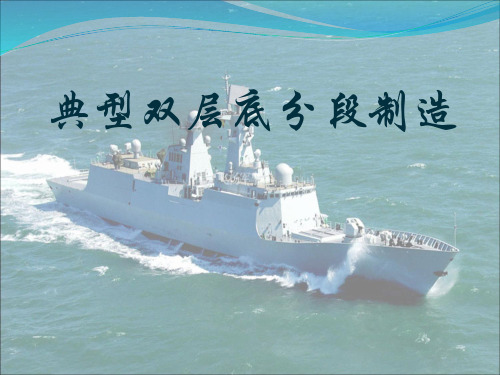
双层底分段(反造法)基本流程
划胎架格线
竖胎架支柱
胎架划线、 切割
内底板定位
焊接内底板
焊接外底板
安装外底板
焊接纵横构 架
安装纵横构 架
划纵横构架 线
安装吊环、 加强
划分段基准 线
吊离胎架
内底板接缝 清根、焊接
火工矫正、 完工报验
划胎架格线
根据胎架制造 图,在胎架平台上 划出胎架中心线、 角尺线(即肋骨检 验线)。
安装内底纵向构架
内底纵骨按零 件号,按在底板相 应的纵骨位置上, 并确定纵骨端部与 外板端缝的相对位 置。定位焊后,须 用角尺或水平尺检 查其垂直度,并用 钢板条加强。将侧 桁材吊上分段,对 准位置线后进行定 位。
安装横向构架
吊上肋板按相 应的肋位线插入侧 桁材之间。肋板在 船宽方向的位置一 定要对准内低板边 线,以确保舭部外 板线型。定位时, 肋板与底板先进行 定位,而后进行连 续侧桁材与肋板的 定位。侧桁材在定 位时应检查侧桁材 的垂直度。
典型双层底分段制造双层底分段制造底部分段位于船体的最下部它可分为单底和双层底两大类都包括船底板和船底骨架两部分双层底还多一层内底板即相关结构
典型双层底分分为单底和双层底两大 类,都包括船底板和船底骨架两部分,双层底还多一层内底 板,即相关结构。
双层底分段反造一般是以内底板为基准面,在胎架上制造。
安装外底纵骨
在纵骨吊装前, 应用粉线检查肋板 上的纵骨切口是否 正确,不正确要修 割正确,纵骨吊上 后,放对前后位置, 即可进行定位。定 位过程中应注意检 查和保持肋位之间 的距离及其与底板 (基面)的垂直度。
盖外板
线型平坦的外 板可预先拼焊好, 再吊上分段。曲型 较大的外板,则一 行一行吊装。先吊K 行板,使K行板中心 线对准分段中线, 并拉对外板前后位 置。再由中间向两 边依次吊装其余各 行板。
0106船体分装配造工艺
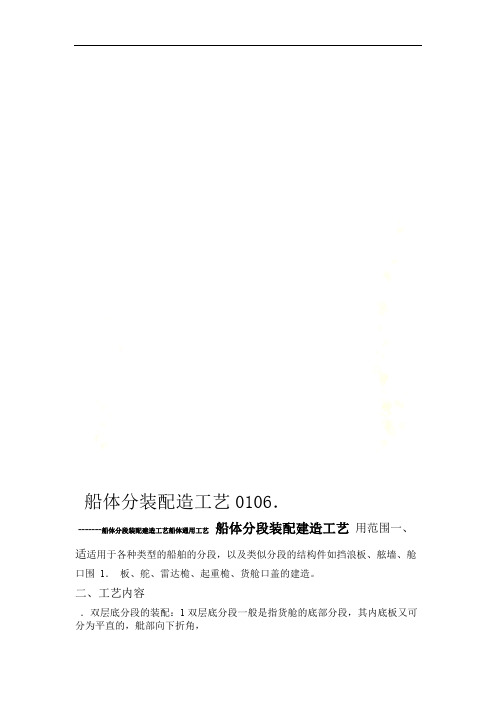
船体分装配造工艺0106.-------船体分段装配建造工艺船体通用工艺船体分段装配建造工艺用范围一、适适用于各种类型的船舶的分段,以及类似分段的结构件如挡浪板、舷墙、舱口围1.板、舵、雷达桅、起重桅、货舱口盖的建造。
二、工艺内容.双层底分段的装配:1双层底分段一般是指货舱的底部分段,其内底板又可分为平直的,舭部向下折角,舭部向上折角,以及阶梯等四种,由于双层底分段的结构形式,通常建造方法有正身建造及反身建造。
1双层底分段的反身建造1. 装配程序:2.以内底板为基准,制作胎架→内底板拼板→刨槽→焊接、局部矫正→划纵、横骨架线→安装纵、横骨架→(可采用分离装配法或混合装配法)→焊接→矫正构架变形→(修顺构架底部型线)→装外板→焊接→装焊吊环→划出分段中心线及检验肋位线→检验与测量→脱胎吊出翻身→焊接外板上结构的部分角焊缝,同时进行内底板封底焊→火工矫正→完工测量→焊缝密性试验及透视→分段完工双层底分段反身建造的胎架:因双层底的内底板是平面,但在制造上建分段胎架则 1.1.1 要考虑甲板梁拱。
通常胎架的基准面是平面或带梁拱,若考虑焊接变形的影响,要作相应的反变形措施:双层底分段反身建造,在胎架上焊接后的横向变形往往是两舷向外翘曲,纵向亦有两头向上翘曲的变形,故需在胎架上作出相应的反变形措施。
a、横向反变形Y计算:①当双层底半宽B≤7500mm,双层底高度H≤950mm时:Y=(2/1000~3/1000)×Bx式中:Bx为至中心线任意距离X=(2/1000~3/1000)×H②当双层底半宽B>7500mm,双层底高度>950mm,则X、Y值可取上式计算所得数值0.8倍。
-- 1 --船体通用工艺-------船体分段装配建造工艺b、纵向反变形计算:6m可不放反变形。
①当分段长度L≤Lx)×时,则Y=(2/100012m ②当分段长度L=6~为分段胎架放反变形值1/2L处的任意距离,YLx 式中:为至Lx(1.5/1000)×时,则③当分段长度L>12mY=把内底的周如果胎架上不作反变形措施,则要求在分段制造中采用加强固定措施,围和中部搭焊牢固。
船舶双层底装焊 工艺流程
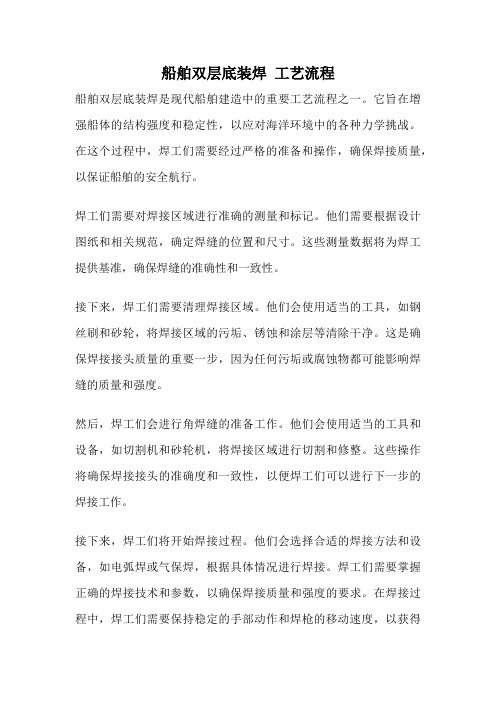
船舶双层底装焊工艺流程船舶双层底装焊是现代船舶建造中的重要工艺流程之一。
它旨在增强船体的结构强度和稳定性,以应对海洋环境中的各种力学挑战。
在这个过程中,焊工们需要经过严格的准备和操作,确保焊接质量,以保证船舶的安全航行。
焊工们需要对焊接区域进行准确的测量和标记。
他们需要根据设计图纸和相关规范,确定焊缝的位置和尺寸。
这些测量数据将为焊工提供基准,确保焊缝的准确性和一致性。
接下来,焊工们需要清理焊接区域。
他们会使用适当的工具,如钢丝刷和砂轮,将焊接区域的污垢、锈蚀和涂层等清除干净。
这是确保焊接接头质量的重要一步,因为任何污垢或腐蚀物都可能影响焊缝的质量和强度。
然后,焊工们会进行角焊缝的准备工作。
他们会使用适当的工具和设备,如切割机和砂轮机,将焊接区域进行切割和修整。
这些操作将确保焊接接头的准确度和一致性,以便焊工们可以进行下一步的焊接工作。
接下来,焊工们将开始焊接过程。
他们会选择合适的焊接方法和设备,如电弧焊或气保焊,根据具体情况进行焊接。
焊工们需要掌握正确的焊接技术和参数,以确保焊接质量和强度的要求。
在焊接过程中,焊工们需要保持稳定的手部动作和焊枪的移动速度,以获得均匀的焊缝和良好的焊接表面。
完成焊接后,焊工们会对焊缝进行质量检查。
他们会使用适当的工具和设备,如放大镜和超声波检测仪,对焊接接头进行检测和评估。
这些检查将确保焊接质量符合相关规范和标准,以保证船舶的结构强度和稳定性。
焊工们会对焊接区域进行喷涂保护。
他们会选择适当的防腐涂料,如船舶专用防锈漆,对焊接接头进行喷涂。
这将保护焊接接头免受腐蚀和氧化的影响,延长船舶的使用寿命。
船舶双层底装焊是一项关键的工艺流程,它需要焊工们具备专业的知识和技能。
只有通过严格的准备和操作,才能确保焊接质量和船舶的安全性。
焊工们的努力和专业精神将为船舶建造贡献巨大,为海洋事业的发展做出重要贡献。
关于双层底分段建造的工艺规定
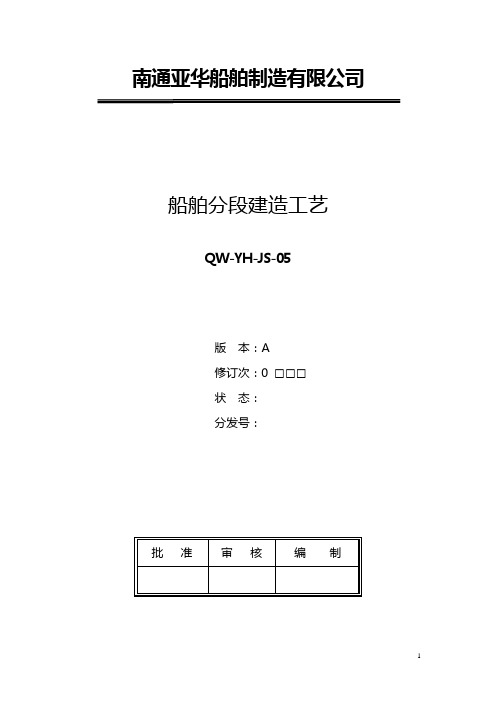
南通亚华船舶制造有限公司船舶分段建造工艺QW-YH-JS-05版本:A修订次:0 □□□状态:分发号:2006年6月28日发布 2006年7月1日实施关于分段建造的工艺规定现将分段建造的有关工艺要求通知如下,请相关小组在施工中施行。
一、双层底分段的建造方式:以内底为基面,设平面胎架反造。
二、胎架预制:1、胎架高≥1m,便于底部施工。
2、胎架长、宽按分段四周界缩100-150mm。
3、胎架反变形和焊接补偿量的放置:横向不放反变形,纵中两端下放0.5‰,舷边两端下放1‰,横向放焊接补偿量:1mm/纵骨间距。
4、胎架四周用板条围固,纵横强结构处装模板,空档处用角铁,槽钢栽成梅花桩,间距800。
5、胎架上应标明中心线、肋位号、板缝定位线、舭部起弧点,首尾起翘点,并画上水平线、检验线等。
6、自检要点:检查胎架的长、宽、中心线、对角线、四角水平的精度,模板的直线度、垂直度、间距;模板与型线样板的吻合度等,并修正超差。
7、报检点:自检合格后,施焊前填单报检。
8、精度标准:长、宽度±4,对角线偏差4,四角水平差±4,模板直线度3,型线吻合度1.5,模板间距差2.0,高度差2。
(单位:mm)三、分段装配:1、装配程序:铺内底板、贴胎→划线→切割余量→以本分段中心为中,向四周发散式吊装结构及箱脚加强→调整光顺外观线形→安装企口(锁口)板、K行板→结构安装报检→施内结构焊→矫正构架变形→调整构架平整度、垂直度及其间距,焊缝修整,自由边打磨,预密试等→装外板和吊耳等→施外板缝,离胎、翻身→分段预修整施焊→清(补)焊→清仓,分段报检合格。
2、进平台拼装前应先检查拼板地坪是否符合拼装要求,如地坪不平整,用100×100大角铁垫在拼板下面,坡口切割按图上要求,切割完毕开始拼装,搭焊用φ3.2 507焊条,装配完工开始打磨,做好清洁工作提交QC报验,然后报验船东代表或船检NK验收合格,电焊班组安排CO2焊工打底至坡口平,打底过程中,每层次药渣要清除干净,在大拼板焊接过程中,要注意大拼板焊缝头尾两端300~400㎜,先打底2至3层,头尾两端头一定要先打底,这样可防止两端头产生裂缝,这点切记,大拼板CO2打底结束打磨干净,然后安排自动焊接,自动焊接时注意不要用错焊丝和药剂,正确选用焊接材料,A级钢用08A,焊剂用431,合金钢用10Mn2G焊剂用331,正面自动焊好以后,大拼板翻身气刨,气刨深度视板厚,22㎜板气刨6㎜深度,气刨结束打磨干净,然后继续自动焊。
船体分段装配流程

具体来说,船体分段装配包括以下几个步骤:
1. 设计分段方案。
根据船体结构特点,合理确定分段位置和尺寸,以便后续分段加工和装配。
2. 分段加工制造。
将分段图纸下发到相关工厂,按照要求分别加工制造各个分段。
3. 分段运输。
完成分段加工后,将各个分段通过运输工具运送到装配现场。
4. 分段就位。
在装配车间,根据顺序将分段吊装就位,并进行临时固定。
5. 分段焊接。
采用自动焊机或人工焊接的方式,将相邻分段焊接连通,形成整体船体。
6. 最终装配。
在分段装配的基础上,再进行甲板、舱室等上层结构的安装,完成整体船体的最终装配。
船体双层底分段及底边舱分段建造原则工艺探讨
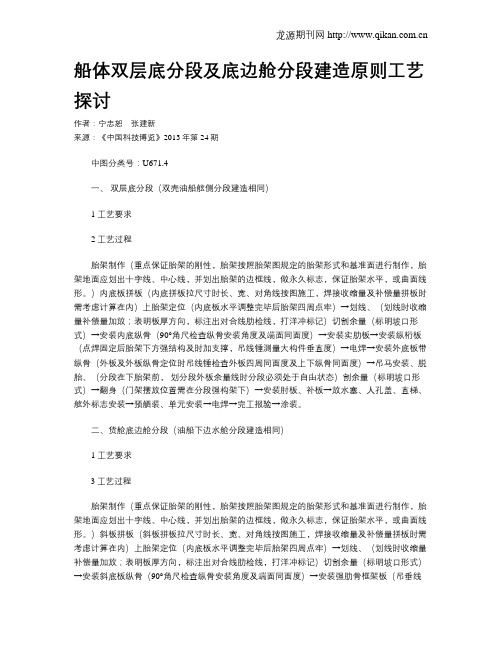
船体双层底分段及底边舱分段建造原则工艺探讨作者:宁忠恕张建新来源:《中国科技博览》2013年第24期中图分类号:U671.4一、双层底分段(双壳油船舷侧分段建造相同)1 工艺要求2 工艺过程胎架制作(重点保证胎架的刚性,胎架按照胎架图规定的胎架形式和基准面进行制作,胎架地面应划出十字线、中心线,并划出胎架的边框线,做永久标志,保证胎架水平,或曲面线形。
)内底板拼板(内底拼板拉尺寸时长、宽、对角线按图施工,焊接收缩量及补偿量拼板时需考虑计算在内)上胎架定位(内底板水平调整完毕后胎架四周点牢)→划线、(划线时收缩量补偿量加放;表明板厚方向,标注出对合线肋检线,打洋冲标记)切割余量(标明坡口形式)→安装内底纵骨(90°角尺检查纵骨安装角度及端面同面度)→安装实肋板→安装纵桁板(点焊固定后胎架下方强结构及时加支撑,吊线锤测量大构件垂直度)→电焊→安装外底板带纵骨(外板及外板纵骨定位时吊线锤检查外板四周同面度及上下纵骨同面度)→吊马安装、脱胎、(分段在下胎架前,划分段外板余量线时分段必须处于自由状态)割余量(标明坡口形式)→翻身(门架摆放位置需在分段强构架下)→安装肘板、补板→放水塞、人孔盖、直梯、舷外标志安装→预舾装、单元安装→电焊→完工报验→涂装。
二、货舱底边舱分段(油船下边水舱分段建造相同)1 工艺要求3工艺过程胎架制作(重点保证胎架的刚性,胎架按照胎架图规定的胎架形式和基准面进行制作,胎架地面应划出十字线、中心线,并划出胎架的边框线,做永久标志,保证胎架水平,或曲面线形。
)斜板拼板(斜板拼板拉尺寸时长、宽、对角线按图施工,焊接收缩量及补偿量拼板时需考虑计算在内)上胎架定位(内底板水平调整完毕后胎架四周点牢)→划线、(划线时收缩量补偿量加放;表明板厚方向,标注出对合线肋检线,打洋冲标记)切割余量(标明坡口形式)→安装斜底板纵骨(90°角尺检查纵骨安装角度及端面同面度)→安装强肋骨框架板(吊垂线检查垂直度做好临时支撑)→安装纵桁板(控制斜板与内底板角度(角度样板测量)及节点)→安装外板纵骨(端头向斜板吊线锤检查同面度)→安装外板(吊线锤或是用马板卡住一端保证同面度;舭龙骨安装位置及角度(角度样板测量))→安装吊马翻身→安装外板上肘板或T 型材(测量肘板安装位置保证合拢口T型材长度、端口同面度)→电焊(焊接结束,外板不平整及时火攻处理)→割余量(标明斜板的坡口形式)→脱胎(门架摆放位置需在分段强构架下)→人孔盖、直梯、舷外标志安装→预舾装、单元安装→电焊→完工报验→涂装。
- 1、下载文档前请自行甄别文档内容的完整性,平台不提供额外的编辑、内容补充、找答案等附加服务。
- 2、"仅部分预览"的文档,不可在线预览部分如存在完整性等问题,可反馈申请退款(可完整预览的文档不适用该条件!)。
- 3、如文档侵犯您的权益,请联系客服反馈,我们会尽快为您处理(人工客服工作时间:9:00-18:30)。
摘要分段式有零部件组成的船体局部结构,是船体装备配焊接工作中的重要组成部分,而双层底分段是船体底部的重要保证,其质量好坏安装进度将严重影响整个船体的建造以及船舶的航运。
由于本厂从2009年9月至2010年1月期间建造的基本都是集装箱船,所以本课题主要是对1000TEU的集装箱船的双层底分段的装配进行研究。
通过分析船体分段装配的标准工艺过程和船体的建造方法,以及分段建造质量的好坏和尺寸精度的控制来分析该1000TEU集装箱船的双层底分段的装配工作。
关键词部件组装焊接工艺装配精度建造质量密性检验AbstractSegmented composed of hull parts, is equipped with local structure with hull welding work is an important part of the double bottom block, and is an important guarantee of hull bottom, its quality installation schedule will seriously affect the ship hull building and shipping. Since the factory from 2009 September January 2010 were built during the basic container ship, so this topic is mainly to the container ships of 1000TEU assembly of double bottom block. Through the analysis of the standard of block assembly process and hull building method, and the construction quality of subsection and precision analysis to the control of 1000TEU this container ship assembly work double bottom block.Keywords: Assembly Welding process Fabrication accuracyConstruction quality tightness test目录摘要 (2)英文摘要 (3)目录 (4)一论双层底分段的装配 (5)(一)双层底分段介绍 (5)(二)双层底分段流程 (6)(三)双层底建造工艺 (7)(四)双层底分段装焊 (10)二分段矫正及检验 (12)(一)分段装配完工后的矫正 (12)(二)焊接过程中的检验 (13)(三)分段完工后的检验 (14)三分段建造工艺结论 (15)致谢 (17)参考文献 (18)论船舶双层底分段的装配一论双层底分段装配(一)双层底分段介绍双层底分段一般是指货舱的底部分段,其内底板又可分为平直的,舭部向下折角,舭部向上折角,以及阶梯状等四种,由于双层底分段的结构形式,通常建造方法有正身建造及反身建造,而大多数船厂都采用反身建造,此方法简单,翻身次数少,危险性小,同时也增加了产品效益,分段图如下所示:1-1双层底分段(二)双层底分段流程以内底板为基准,制作胎架→内底板拼板→刨槽→焊接、局部矫正→划纵、横骨架线→安装纵、横骨架→(可采用分离装配法或混合装配法)→焊接→矫正构架变形→(修顺构架底部型线)→装外板→焊接→装焊吊环→划出分段中心线及检验肋位线→检验与测量→脱离胎架吊出翻身→焊接外板上构件的部分角焊缝,同时进行内底板封底焊→火工矫正→完工测量→焊缝密性试验及透视→分段完工分段流程基本图片如下:1-2 内地板拼装与划线 1-3安装纵横骨架1-4分段预舾装 1-5分段拼装好后盖1-6分段翻身 1-7吊离胎架(三)双层底建造工艺1双层底分段反身建造的胎架:因双层底的内底板是平面,一般在设计时要根据分段平面图而做,1-8分段平面图建造分段胎架则还要考虑甲板梁拱,通常胎架的基准面是平面或带梁拱,若考虑焊接变形的影响,要作相应的反变形措施:双层底分段反身建造,在胎架上焊接后的横向变形往往是两舷向外翘曲,纵向亦有两头向上翘曲的变形,故需在胎架上作出相应的反变形措施。
(1)横向反变形Y计算:①当双层底半宽B≤7500mm,双层底高度H≤950mm时:Y=(2/1000~3/1000)×Bx式中:Bx为至中心线任意距离X=(2/1000~3/1000)×H②当双层底半宽B>7500mm,双层底高度>950mm,则X、Y值可取上式计算所得数值0.8倍。
(2)纵向反变形计算:①当分段长度L≤6m可不放反变形。
②当分段长度L=6~12m时,则Y=(2/1000)×Lx式中:Lx为至1/2L处的任意距离,Y为分段胎架放反变形值③当分段长度L>12m时,则Y=(1.5/1000)×Lx如果胎架上不作反变形措施,则要求在分段制造中采用加强固定措施,把内底的周围和中部搭焊牢固。
焊工要严格遵守工艺规程采用合理的焊接程序选择正确的焊接顺序内底板进行定位:内底板在吊上胎架前可拼焊好,并经校平。
内底板吊上胎架后,将内底板的中线与胎架中线对准,并摆准首端或尾端肋位后,则内底板可与胎架电焊固定,搭焊固定时,不仅四周要搭焊,且在中间部位的中线和内部构架位置均作75-150或75-225间断焊固定,以免造成分段严重变形。
2 画纵横骨架线1-9划纵横骨架线先把胎架的中心线和检验肋位线,引到内底板上划出中心线和检验肋位线,再根据图纸或草图划出纵骨、肋板中、旁桁材肘板等纵横构架线,并标上肋骨零件及构件理论线厚度方向,由于分段是反装划线,须对调骨架的左右方向,即原来的左变右、右变左,这点要特别注意。
3安装纵横骨架1-10安装纵横骨架一般采用分离装配法,其装配程序:内底纵骨安装→旁桁材→肋板→插入中桁材→肘板或内底纵骨、中桁材安装→肋板与旁桁材交错装→肘板内部骨架,在安装时,均需要用角尺或水平尺检查其垂直度,特别是中桁材和肋板,都应确保其垂直,必要时可以用临时支撑加固,以防变形。
安装和如要插入构件(或中桁材插入肋板间)的话,则其空间的间隔为插入构件板厚加1~2mm,其间隙不得随意扩大造成焊接收缩变形量增大,一定要确保装配的质量,因为返工比较麻烦。
4内底边板安装(根据具体船只结构,有的船没有,则不要安装)。
5外板装配:外板装配时,一般先做好脚手架,便于工作,曲度平坦的外板,视平坦程序,可将整体外板或中间三行外板先拼缝好再吊上分段装配,外板曲度大的,可一行板一行板对称吊装。
先吊装K行板(K行板两边接缝匀为正确边口可预先开好坡口),将K行板的中心线对准分段中心,并摆准前后位置,与肋板和中桁材搭焊定位,定位时应从中间向两端定位,或从一端顺向定位。
其余外板均由中间向两边,按照外口对准板路线装配,其余量放在靠船中一边板口,当外板吊上分段时迭在前一列板上,因此在前一列板上接缝板口50~100mm (根据余量多少而定),外划一根线作为基准线,供下列板划余量,当该行板位置放对后,即可根据该线划出余量,割掉拼合最后吊装转圆板(R板),吊装前在转圆板上先焊好靠板,防止下滑,装配好后即完毕报验。
6分段组装完毕在分段吊出胎架前应将中心线及肋位检验线复到外板上,以作大合拢的依据,在划线同时可安装吊耳,为了防止分段吊运时将外板与骨架间的焊缝拉裂,在吊耳安装区骨架与外板的焊接加强、加大,须较吊攀焊缝长一倍以上。
然后将分段吊离胎架翻身,摆平垫实后,进行外板内缝与外底纵横骨架的焊接以及内底板接缝进行碳刨封底焊,焊接工作结束后,火工矫正。
然后做外板焊缝密性试验及透视双层底分段在装配过程中尚应注意下述二点:(1)凡安装放水塞的分段,应在分段外板安装时,按图纸要求装焊放水塞。
(2)转圆板(即R板)与底板靠外面的角焊缝不应焊接,因焊接后外板易朝里凹,在船台上装配时与相邻底部及舷部参数以减少分段的变形。
(四)双层底分段装焊(1)平台准备:水平度控制在5mm之内。
(2)铺设内底板进行装配划线:内底板铺在平台上,不平处用重物压平,用马板固定。
划出中心线和中间肋骨线、内底纵骨、肋板、纵桁位置线和内底板轮廓线,画出厚度和型钢符号,将构件处焊缝批平。
(3)装内底纵骨:误差控制在2毫米之内。
(4)装纵桁和肋板。
一定要校正好后再进行焊接,且要焊接牢靠。
(5)装外底纵骨:分段两端200毫米范围不焊接,以便于船台合拢。
(6)焊构架焊缝:控制焊接变形,一般由8至12位焊工同步焊接。
(7)分段舾装:在未装外板前将一些零部件,组件进行组装,即预舾装,如图1-11纵横构架-部件拼装1-12纵横构架拼装(8)装外板:首先装龙骨底板,其余依次安装。
(9)分段划线和余量切割:装配结束,用激光仪画出分段中心线和肋骨检验线,画出分段两端轮廓线,按要求留补偿切割余量。
(10)分段翻身、焊接:完成外板和骨架间的平角焊和内底板上面的衬底焊。
同时进行完工测量和结构性验收。
(11)分段二次除锈和涂装。
二分段矫正及检验(一)分段装配完工后的矫正船体分段在装配过程中由于施焊电弧高温引起的焊接变形,包括缩短、角度改变、弯曲变形等。
焊接变形对结构安装精度有很大影响,过大的变形将显著降低结构的承载能力;所以通常采用以下几种措施:(1)采用反变形措施(2)采用小锤锤击中间焊(3)采用合理的焊接顺序和焊接工艺(4)利用工卡具刚性固定(5)分析回弹常数(6)火工矫正在船厂通常采用火工矫正的方法,例如以下图片2-1 工人们正在对一些零部件进行火工矫正(二)焊接检验焊接检验内容包括从图纸设计到产品制出整个生产过程中所使用的材料、工具、设备、工艺过程和成品质量的检验,分为三个阶段:焊前检验、焊接过程中的检验、焊后成品的检验。
检验方法根据对产品是否造成损伤可分为破坏性检验和无损探伤两类。
(1)焊前检验焊前检验包括原材料(如母材、焊条、焊剂等)的检验、焊接结构设计的检查等。
(2)焊接过程中的检验包括焊接工艺规范的检验、焊缝尺寸的检查、夹具情况和结构装配质量的检查等。
(3)焊后成品的检验焊后成品检验的方法很多,常用的有以下几种:①外观检验焊接接头的外观检验是一种手续简便而又应用广泛的检验方法,是成品检验的一个重要内容,主要是发现焊缝表面的缺陷和尺寸上的偏差。
一般通过肉眼观察,借助标准样板、量规和放大镜等工具进行检验。
若焊缝表面出现缺陷,焊缝内部便有存在缺陷的可能。
②致密性检验对于船体外板以及内底板,其焊缝的不致密缺陷,如贯穿性的裂纹、气孔、夹渣、未焊透和疏松组织等,可用致密性试验来发现。