c=0抽样计划介绍
C=0抽样计划表

“C=0抽样计划”资料AQL 0.010 0.015 0。
025 0。
040 0。
065 0。
10 0.15 0.25 0.40 0。
65 1。
0 1.5 2。
5 4。
0 6。
5 10。
0 批量样本2—8 **** *** ***** 5 3 2 2 9-15 * *** * ** * ** 13 8 5 3 2 2 16—25 ******* **20 13 8 5 3 2 2 26-50 * **** ** * 32 20 13 8 5 5 5 3 51—90 **** **80 50 32 20 13 8 7 6 5 4 91-150 *** * *125 80 50 32 20 13 12 11 7 6 5 151—280 * ***200 125 80 50 32 20 20 19 13 10 7 6 281-500 ** *315 200 125 80 50 48 47 29 21 16 11 9 7 501—1200 *800 500 315 200 125 80 75 73 47 34 27 19 15 11 8 1201-3200 1250 800 500 315 200 125 120 116 73 53 42 35 23 18 13 9 3201—10000 1250 800 500 315 200 192 189 116 86 68 50 38 29 22 15 9 10001—35000 1250 800 500 315 300 294 189 135 108 77 60 46 35 29 15 9 35001-150000 1250 800 500 490 476 294 218 170 123 96 74 56 40 29 15 9 150001—500000 1250 800 750 715 476 345 270 200 156 119 90 64 40 29 15 9 500000and over 1250 1200 1112 715 556 435 303 244 189 143 102 64 40 29 15 9零缺陷抽样(C=0)使用的理解(C=0抽样计划不是国标、国际标准)国际标准, 国标, 缺陷零缺陷抽样(C=0)使用的理解(C=0抽样计划不是国标、国际标准)1)是以105E为基础,把抽样数减少,只是缺点数为“0",AQL值同样有从0。
C=0抽样方案

和抽样有关的几个分布
• 二项分布:二项分布是n个独立的是/非试验中成功的次数 的概率分布,其中每次试验的成功概率一样。(二项分布 的计算方式如何推导?)
• 超几何分布:由有限个物件中抽出n个物件,成功抽出指 定种类的物件的次数(不归还)。前述案例中已给出超几 何分布计算的案例。
• 泊松分布:当二项分布的n很大而p很小时,泊松分布可作
为二项分布的近似。事实上,泊松分布是由二项分布导出
的。
– 概率密度 – 累积概率
f
(
x
)
(
np
)
x
e
np
x!
r
F (x) f (x)
x0
OC曲线
• 案例:有N=10000个产品, 不良率为P,我们抽取n=100 个,1收2退。分别计算 P=1%,2%,3%时的接收概率 Pa
– 根据泊松分布,Pa分别为:
13
3201-10000 1250 800 500 315 200 192 189 116 86 68 50 38 29 22 15
10001-35000 1250 800 500 315 300 294 189 135 108 77 60 46 35 29 15
35001-150000 1250 800 500 490 476 294 218 170 123 96 74 56 40 29 15
*
*
* 315 200 125 80 50 48 47 29 21 16 11
9
501-1200
* 800 500 315 200 125 80 75 73 47 34 27 19 15 11
1201-3200
1250 800 500 315 200 125 120 116 73
C=0抽样方案
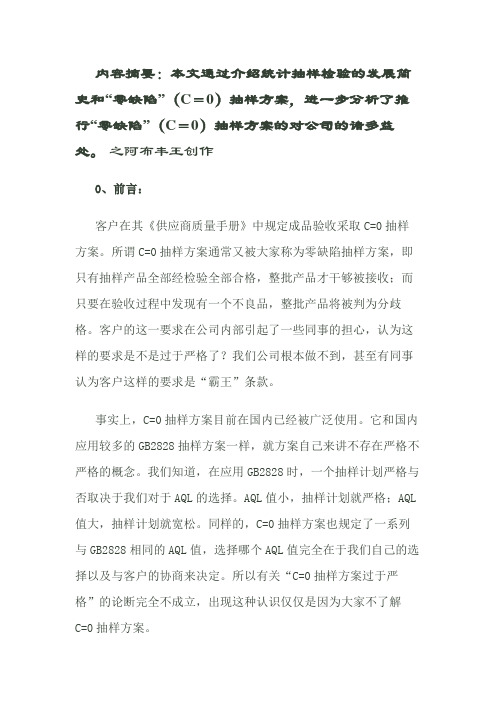
内容摘要:本文通过介绍统计抽样检验的发展简史和“零缺陷”(C=0)抽样方案,进一步分析了推行“零缺陷”(C=0)抽样方案的对公司的诸多益处。
之阿布丰王创作0、前言:客户在其《供应商质量手册》中规定成品验收采取C=0抽样方案。
所谓C=0抽样方案通常又被大家称为零缺陷抽样方案,即只有抽样产品全部经检验全部合格,整批产品才干够被接收;而只要在验收过程中发现有一个不良品,整批产品将被判为分歧格。
客户的这一要求在公司内部引起了一些同事的担心,认为这样的要求是不是过于严格了?我们公司根本做不到,甚至有同事认为客户这样的要求是“霸王”条款。
事实上,C=0抽样方案目前在国内已经被广泛使用。
它和国内应用较多的GB2828抽样方案一样,就方案自己来讲不存在严格不严格的概念。
我们知道,在应用GB2828时,一个抽样计划严格与否取决于我们对于AQL的选择。
AQL值小,抽样计划就严格;AQL 值大,抽样计划就宽松。
同样的,C=0抽样方案也规定了一系列与GB2828相同的AQL值,选择哪个AQL值完全在于我们自己的选择以及与客户的协商来决定。
所以有关“C=0抽样方案过于严格”的论断完全不成立,出现这种认识仅仅是因为大家不了解C=0抽样方案。
需要说明的是,该客户的《供应商质量手册》是根据ISO/TS16949(即GB/T18305)建立的,而ISO/TS16949在7.1.2 条款中明确要求接收水平必须是零缺陷。
(ISO/TS16949 7.1.2接收准则:组织应规定接收准则,要求时,由顾客批准。
对于计数型数据抽样,接收水平应是零缺陷。
)所以,客户的要求是根据的,不存在任何“霸王”要求。
1、抽样检验简介抽样检验又称为统计抽检检验,是指从交验的一批产品中,随机抽取若干单位产品组成样本进行检验,通过对样本的检验结果对整批产品做出质量判定的过程。
我们知道,检验是不发生价值的工作,因此如何更经济、快捷的进行检验就直接关系到生产的成本和效率。
零缺陷(C=0)抽样方案

零缺陷概念的产生:被誉为“全球质量管理大师”、“零缺陷之父”和“伟大的管理思想家”的菲利浦·克劳士比(Philip B. Crosby)在20世纪60年代初提出“零缺陷”思想,并在美国推行零缺陷运动。
后来,零缺陷的思想传至日本,在日本制造业中得到了全面推广,使日本制造业的产品质量得到迅速提高,并且领先于世界水平,继而进一步扩大到工商业所有领域。
零缺陷理论核心是:“第一次就把事情做对”。
所谓"零缺陷"抽样方案,简单的说,就是不管你的批量和样本大小如何,其抽样检验的接收数Ac=0,即"0收1退"。
举例:某客户在其《供应商质量手册》中规定成品验收采用 C=0 抽样方案。
所谓 C=0 抽样方案通常又被大家称为零缺陷抽样方案,即只有抽样产品全部经检验全部合格,整批产品才能够被接收;而只要在验收过程中发现有一个不良品,整批产品将被判为不合格。
客户的这一要求在公司内部引起了一些同事的担心,认为这样的要求是不是过于严格了?公司根本做不到,甚至有同事认为客户这样的要求是“霸王”条款。
事实上,C=0 抽样方案目前在国内已经被广泛使用。
它和我们中国应用较多的GB/T2828.1-2012抽样方案一样,就方案本身来讲不存在严格不严格的概念。
在应用GB/T2828.1-2012时,一个抽样计划严格与否取决于我们对于 AQL 的选择。
AQL 值小,抽样计划就严格;AQL 值大,抽样计划就宽松。
同样的,C=0 抽样方案也规定了一系列与GB/T2828.1-2012 相同的 AQL值,选择哪个AQL 值完全在于我们自己的选择以及与客户的协商来决定。
所以有关“C=0 抽样方案过于严格”的论断完全不成立,出现这种认识仅仅是因为大家不了解C=0 抽样方案。
需要说明的是,该客户的《供应商质量手册》是根据IATF16949:2016 建立的,而IATF16949 :2016标准条款8.6.6中明确要求接收水平必须是零缺陷。
C=0抽样计划表Word版

“C=0抽样计划”资料AQL 0.010 0.015 0.025 0.040 0.065 0.10 0.15 0.25 0.40 0.65 1.0 1.5 2.5 4.0 6.5 10.0 批量样本2-8 * * * * * * * * * * * * 5 3 2 2 9-15 * * * * * * * * * * 13 8 5 3 2 2 16-25 * * * * * * * * * 20 13 8 5 3 2 2 26-50 * * * * * * * * 32 20 13 8 5 5 5 3 51-90 * * * * * * 80 50 32 20 13 8 7 6 5 4 91-150 * * * * * 125 80 50 32 20 13 12 11 7 6 5 151-280 * * * * 200 125 80 50 32 20 20 19 13 10 7 6 281-500 * * * 315 200 125 80 50 48 47 29 21 16 11 9 7 501-1200 * 800 500 315 200 125 80 75 73 47 34 27 19 15 11 8 1201-3200 1250 800 500 315 200 125 120 116 73 53 42 35 23 18 13 9 3201-10000 1250 800 500 315 200 192 189 116 86 68 50 38 29 22 15 9 10001-35000 1250 800 500 315 300 294 189 135 108 77 60 46 35 29 15 9 35001-150000 1250 800 500 490 476 294 218 170 123 96 74 56 40 29 15 9 150001-500000 1250 800 750 715 476 345 270 200 156 119 90 64 40 29 15 9 500000and over 1250 1200 1112 715 556 435 303 244 189 143 102 64 40 29 15 9零缺陷抽样(C=0)使用的理解(C=0抽样计划不是国标、国际标准)国际标准, 国标, 缺陷零缺陷抽样(C=0)使用的理解(C=0抽样计划不是国标、国际标准)1)是以105E为基础,把抽样数减少,只是缺点数为“0”,AQL值同样有从0.01-10;2)不存在加严、多次抽样等;3)只能用于静态的抽样,如IQC\FQC\OQC等,IPQC不适用;4)对IQC来说,对供应商要求高,但IQC的作业量减少;5)对产品检验过程中,只要有一个缺点在,即可判定,基本上不用全检完,有利于客户方;6)对供应商的品质逐渐提高和改善是不利的,往往一锤子打死;7)定义A\B\C(严重缺点(注意:C=0)、主要缺点、次要缺定)的定义要慎重,否则实际现场作业面复杂性提高,操作尴尬;8)用C=0抽样表,一般用起来不考虑它是从哪里来的,实际上与105E是“亲属”关系;9)有的公司为了避免说不清楚,干脆将C=0与105E合为一张比较表,谁问一看有出处;此表如同105E抽样计划表一样留在手边随查;10)C=0抽样计划用以来较为简单,网站有些帖子讨论的C=0复杂了,我的经验是一定要读懂105E的抽样的基本概念和其抽样技术,否则对C=0理解会偏掉;11)参考资料:《品质管理实战指南》张智勇编著,《国内企业外常用抽样技术和测量技术》陈晋美主编。
C=0-抽样方案介绍

C=0-抽样方案介绍1965年,零缺陷抽样检验方案(c=0)首次发表在国际刊物上,虽然零缺陷抽样检验方案目前还是不是国际和国家标准。
但由于“零缺陷”的品质理念已经深入人心,在加上ISO/TS16949:2002中有明确的条文要求。
所以欧美很多的企业,特别是汽车供应链相关企业普遍采用的都是零缺陷抽样检验方案。
零缺陷抽样检验方案简单的说,就是不管你的批量和样本大小如何,其抽样检验的接收数Ac=0,即“0收1退”。
在抽样检验过程中,一旦发现一个缺陷或不合格,就要实施100%的全检或退货处置。
零缺陷抽样检验方案的优点就是不存在加严、放宽与正常检验之间的转移规定。
在ISO/TS16949:2002里面的7.1.2条款里面有明确规定“7.1.2接收准则必须由组织定义,要求时,必须由顾客批准。
对于计数型数据抽样,接收水平必须是零缺陷”。
标准条文明确规定的,也就是我们要恪守的。
其实我们也一直在实用C=O的抽样检验方案。
但对其认识上可能存在一定的误区。
导致其真正的效率发挥的不够充分。
所以希望通过本文,能起抛砖引玉作用,为公司后续检验和试验活动更加顺畅的开展起到积极作用。
首先,零缺陷抽样检验方案的准则就是我们通常说的C=0,0收1退。
但其要和GB/T2828.1-2003按接收质量限(AQL)检索逐批检验抽样计划结合使用,要使用GB/T2828.1来确定其“零缺陷抽样检验方案”的样本大小。
按我们以前的经验,采用GB/T2828.1的时候,首先是确定批量大小、确定检验水平、那么它的样本大小就确定,再定义我们的接收质量限(AQL)就可以得出我们的接收准则,而现在采用零缺陷抽样检验方案的接收准则是已知的,意味着AQL值在零缺陷抽样检验方案中就失去了作用。
这就是我们认识上的一个明显误区。
试想,如果采用零缺陷抽样检验方案与AQL值无关的话,那么假设采用GB/T2828.1里面的正常检验一次抽样方案II级检验水平的话,意味着样本量是统一的。
C=0抽样方案

抽样检的缺点
抽样检验也有如下一些固有缺点: 1、存在接受“劣质”批和拒收“优质”批
的风险。 2、增加了计划工作和文件编集工作。 3、样组所提供的产品情报一般而言较之于
全检要少。
抽样方案所规定的假定
抽样方案通常都被假定为
(实践中,这些假定并不完全靠得住) 1、检验员是按照指定的抽样方案进行工作的。 2、所做的检验是没有误差的,即在测量或鉴定产品
强的预防性 寻因性检验:在产品的设计阶段,通过充分的预测,寻找
潜在不合格的原因
2、统计抽样检验基本概念
检验分类(按检验目的):
生产检验 验收检验 监督检验 验证检验 仲裁检验
检验分类(按检验后样品状况):
非破坏性检验 破坏性检验
2、统计抽样检验基本概念
检验分类(按质量特性数据性质):
C=0零缺陷抽样计划 培训教材
制作:周亮 日期:2016-4-22
目录
一、抽样检验基础知识 二、C=0 Sampling Plan 三、MIL-STD-105E抽样与C=0抽样比 四、C=0抽样表 五、C=0抽样案例
1、统计抽样的由来与发展
1965年,美国的一位大学教授尼古拉斯•斯托格力亚发表 C=0抽样方案,几经改版,目前最新的版本为第四版。 C=0抽样方案是根据MIL-STD105 修改而成,接收准则限 定为“0收1退”,因而又被人们称为“零缺陷”抽样方案。
2、统计抽样检验基本概念
检验分类(按检验数量):
全数检验:对每个产品进行评判,接收的全是合格品, 拒绝的是少量不合格品。
抽样检验:根据对部分产品的检验结果,对一批产品做 出判断,接收的产品中可能有不合格品,拒绝的是整批 产品 (统计抽样检验、非统计抽样检验)
c=0抽样计划表优点

c=0抽样计划表优点
c=0抽样计划是一种统计抽样方法,其优点包括:
1. 明确确定了样本数量,简单易懂,易于实施和理解。
2. 具有一定的可靠性和精度,样本的代表性较高。
3. 可以有效地控制抽样误差,减小统计结果的误差。
4. 对于样本错误或不合格的数据可以很快地做出判断和处理。
5. 节约了人力、物力和时间资源,降低了统计成本,提高了效率。
6. 适用于从大样本中抽取中小样本的情况,且不需要考虑每个样本的特征或属性,适用于大多数普查、统计调查等。
总之,c=0抽样计划是一种常用的、简单有效的抽样方法,具有一定的优点和适用性。
C=0抽样方案

C=0抽样方案-CAL-FENGHAI-(2020YEAR-YICAI)_JINGBIAN内容摘要:本文通过介绍统计抽样检验的发展简史和“零缺陷”(C=0)抽样方案,进一步分析了推行“零缺陷”(C=0)抽样方案的对公司的诸多益处。
0、前言:客户在其《供应商质量手册》中规定成品验收采用C=0抽样方案。
所谓C=0抽样方案通常又被大家称为零缺陷抽样方案,即只有抽样产品全部经检验全部合格,整批产品才能够被接收;而只要在验收过程中发现有一个不良品,整批产品将被判为不合格。
客户的这一要求在公司内部引起了一些同事的担心,认为这样的要求是不是过于严格了我们公司根本做不到,甚至有同事认为客户这样的要求是“霸王”条款。
事实上,C=0抽样方案目前在国内已经被广泛使用。
它和国内应用较多的GB2828抽样方案一样,就方案本身来讲不存在严格不严格的概念。
我们知道,在应用GB2828时,一个抽样计划严格与否取决于我们对于AQL的选择。
AQL值小,抽样计划就严格;AQL值大,抽样计划就宽松。
同样的,C=0抽样方案也规定了一系列与GB2828相同的AQL值,选择哪个AQL值完全在于我们自己的选择以及与客户的协商来决定。
所以有关“C=0抽样方案过于严格”的论断完全不成立,出现这种认识仅仅是因为大家不了解C=0抽样方案。
需要说明的是,该客户的《供应商质量手册》是根据ISO/TS16949(即GB/T18305)建立的,而ISO/TS16949在条款中明确要求接收水平必须是零缺陷。
(ISO/TS16949 接收准则:组织应规定接收准则,要求时,由顾客批准。
对于计数型数据抽样,接收水平应是零缺陷。
)所以,客户的要求是根据的,不存在任何“霸王”要求。
1、抽样检验简介抽样检验又称为统计抽检检验,是指从交验的一批产品中,随机抽取若干单位产品组成样本进行检验,通过对样本的检验结果对整批产品做出质量判定的过程。
我们知道,检验是不产生价值的工作,因此如何更经济、快捷的进行检验就直接关系到生产的成本和效率。
C=0抽样方案

– 对象:产品、过程、服务 – 符合性:“合格”、“不合格”;或“满足”、“不满足” – 活动:测、比、判的过程
品质决定命运,创新引领未来
2、统计抽样检验基本概念
• 单位产品:构成产品总体的基本单位(产品、材料、 服务)
• 检验批:同样生产条件下生产的单位产品汇集 • 样本:取自一个批并且提供有关该批的信息的一个或
• 检验分类(按检验方式):
– 理化检验:依靠仪器、仪表、测量装置或化学方法 进行检验
– 感官检验:利用手、眼、耳的感觉进行判断 – 试验性使用
品质决定命运,创新引领未来
2、统计抽样检验基本概念
• 检验分类(按检验系统):
– 逐批检验 – 周期检验
• 检验分类(按检验效果):
– 判定性检验:依据标准的符合性判断,是把关的职 能
国家标准ANSI/ASQC Z1.4-1993代替之。但一些公司 仍在使用MIL-STD-105E。
➢ 后来美国军方就开始使用C=0抽样标准。
➢ 2008年,美国国家标准ANSI/ASQ Z1.4-2008发布。
品质决定命运,创新引领未来
2﹑C=0的发展历史
• 零缺陷计划是由Nicholas L. Squeglia所开发的。 • 它和MIL-STD-105E相比可以以较少检验数而
一组产品 • 样本与总体之间是一种推断关系,抽样检验就是用统
计的方法控制总体质量水平
品质决定命运,创新引领未来
2、统计抽样检验基本概念
• 检验分类:
– 按检验数量 – 按检验人员 – 按检验地点 – 按生产过程 – 按检验方式
按检验系统 按检验效果 按检验目的 按供需关系 按质量特性的数据性质 按检验后样品的状况
C=0抽样计划
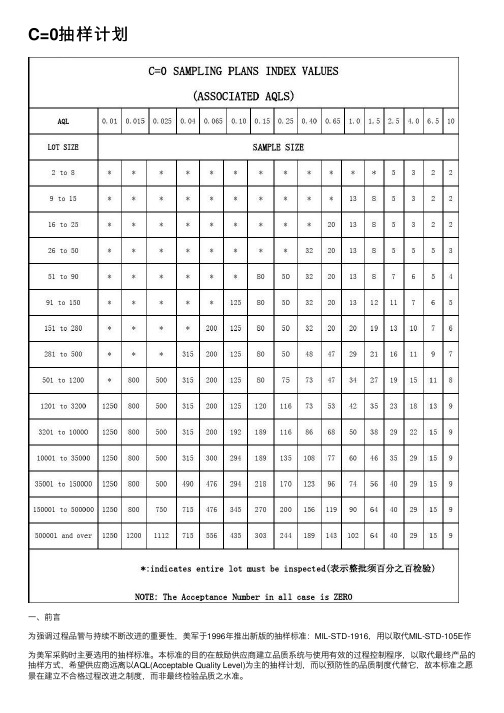
C=0抽样计划⼀、前⾔为强调过程品管与持续不断改进的重要性,美军于1996年推出新版的抽样标准:MIL-STD-1916,⽤以取代MIL-STD-105E作为美军采购时主要选⽤的抽样标准。
本标准的⽬的在⿎励供应商建⽴品质系统与使⽤有效的过程控制程序,以取代最终产品的抽样⽅式,希望供应商远离以AQL(Acceptable Quality Level)为主的抽样计划,⽽以预防性的品质制度代替它,故本标准之愿景在建⽴不合格过程改进之制度,⽽⾮最终检验品质之⽔准。
MTL-STD-1916与MIL-STD-105E 抽样标准不同之处,主要有以下⼏点:1、抽样计划以单次抽样(含加严、正常及减量)为主,删除双次与多次抽样,抽样以“0收1退”(ZBA Zero Based Acceptance )当做判定标准,强调不允许不良品之存在。
2、建⽴持续不断改善之品质系统制度与善⽤多项品质改善⼯具。
j#y3、以预防代替检验,在过程中执⾏统计过程品管(SPC )。
V5s c)[bbs.6sq4、对计数、计量及连续性抽样作业均可适⽤(分别有三种抽样表),不再像以往MIL-STD-105E 仅限于计数值抽样,MIL-STD-414仅限于计量值抽样与MIL-STD-1235仅限于连续性抽样(以上标准美军均已废⽌)。
5、把抽样视为⼀种浪费的⾏为,如供应商可提出不同产品的接收计划,如获顾客同意后,则可按约定的接收⽅式办理验收。
6、MIL-STD-1916强调供应商品质系统的建⽴,以预防为主,⽽MIL-STD-105E 强调顾客的抽样技术,避免接收不合格件。
b;此外,以往最常⽤的MIL-STD-105E 抽样标准,使⽤的查检表上就有加严、正常及减量等对应查检表数⼗个,在运⽤上并不是很⽅便,⽽MIL-STD-1916所使⽤的表格(含计数、计量及连续性抽样),就只有4个,在使⽤的简便性上,已有⼤⼤的改善。
-n l*d1P5m⼆、适⽤范围$^H1、本标准所提供的品质计划与程序,不能减轻供应商满⾜顾客需求的责任,供应商必须建⽴品质系统,包括制造程序,品管监控等作业,⽤以⽣产符合顾客品质要求的产品。
C=0抽样方案

• 除了经济优点外,它还易于使用及管理。
• 起初是用在军方产品,后来更广泛应用于许多 任务业上计数型的抽样,特别强调在零缺陷的 输出。
• 目前根据105E来做修改,目前已是第四版。
抽样概念的说明
母体
管 理
结论
抽样 分析
“不满足” – 活动:测、比、判的过程
2、统计抽样检验基本概念
• 单位产品:构成产品总体的基本单位(产品、材料、 服务)
• 检验批:同样生产条件下生产的单位产品汇集 • 样本:取自一个批并且提供有关该批的信息的一个或
一组产品 • 样本与总体之间是一种推断关系,抽样检验就是用统
计的方法控制总体质量水平
2、统计抽样检验基本概念
• 检验分类(按生产过程):
– 进货检验(首批样品检验和成批检验) – 过程检验(首件检验、巡回检验、工序段检验) – 最终检验
• 检验分类(按检验方式):
– 理化检验:依靠仪器、仪表、测量装置或化学方法 进行检验
– 感官检验:利用手、眼、耳的感觉进行判断 – 试验性使用
2、统计抽样检验基本概念
1、统计抽样的由来与发展
2﹑C=0的发展历史
➢ 1950年﹐美国国防部发布了军用标准MIL-STD-105A。 ➢ 1958年修订为MIL-STD-105B。 ➢ 1961年修订为MIL-STD-105C。 ➢ 1963年修订为MIL-STD-105D。 ➢ 1989年修订为MIL-STD-105E。 ➢ 1995年美国军方就宣布取消MIL-STD-105E﹐用美国
– 生产检验 – 验收检验 – 监督检验 – 验证检验 – 仲裁检验
C=0抽样计划

C=0抽样计划
一﹑目的
明确品保部各单位的抽样标准,并提供文件支持。
二﹑范围
适用于本公司所生产的汽车工业链上的相关产品。
适用于进料、制程、成品检验时,计数型数值允收水准的确定。
三﹑权责
3.1品保经理:确定各阶段的AQL值。
3.2品检人员:C=0 抽样标准的实施。
四﹑定义
4.1 C=0抽样计划:零缺陷抽样计划,即收0退1,Acc=0,Rej=1。
五﹑作业内容
5.1使用方法
5.1.1确定检验项目、判定标准
根据客户要求及产品特性确定。
5.1.2确定允收水准AQL值
外观:AQL0.65
尺寸:AQL 10
5.1.3根据实际批量及规定的AQL值从“附件一”中查出应抽取的样本数量。
5.1.4从批量中随机抽取规定的样本数。
5.1.5检验
根据Acc=0 Rej=1判定。
5.2如遇特殊情况,品保部可根据客户要求更改允收品质水准AQL,只需书面通知相关部门,
而无需更改本规定及相关检验标准。
六﹑参考文件
无
七﹑使用表单
无
八﹑附件
8.1C=0抽样计划表
C=0抽样计划表
注:* 表示整批须百分之百检验。
c=0抽样计划介绍
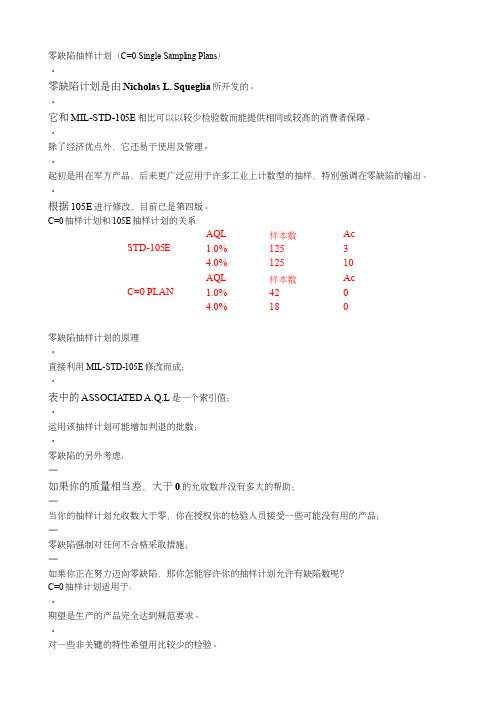
期望是生产的产品完全达到规范要求。
•
对一些非关键的特性希望用比较少的检验。
• 对所有零件的所有特性的 100%检验无法实施时。 •
问题纠正前的临时检验。
•
不同原因的审核:
库存产品的确认审核 对潜在的搬运损坏项目的审核 供应商业绩验证。
•
正常的外观检验。 零缺陷使用注意事项:
•
没有检验水平的设定;
零缺陷抽样计划(C=0 Single Sampling Plans)
•
零缺陷计划是由 Nicholas L. Squeglia 所开发的。
•
它和 MIL-STD-105E 相比可以以较少检验数而能提供相同或较高的消费者保障。
•
除了经济优点外,它还易于使用及管理。
•
起初是用在军方产品,后来更广泛应用于许多工业上计数型的抽样,特別强调在零缺陷的输出。
•
没有正常、加严、放宽的区分;
•
只有正常的表格使用;
•
对消费者的保证比较大;
• 对生产者的风险比较高。
•
根据 105E 进行修改,目前已是第四版。
C=0 抽样计划和 105E 抽样计划的关系
AQL
样本数
Ac
STD-105E
1.0%
125
3
4.0%
125
10
AQL
样本数AcFra bibliotekC=0 PLAN
1.0%
42
0
4.0%
18
0
零缺陷抽样计划的原理
•
直接利用 MIL-STD-105E 修改而成;
• 表中的 ASSOCIATED A.Q.L 是一个索引值; •
运用该抽样计划可能增加判退的批数;
c=0抽样计划

5. C=0抽样计划5.1﹑发行历史1965年,C=0抽样计划首次发表于国际刊物而于1969年首版出书1981年再版,1983年三版ه目前还不是国际或国家标准,但由于“零缺ه陷”的质量观念已通行全球,因此欧美许多企业者广泛采用零缺陷数C=0抽样计划ه5.2﹑零缺点的品质零缺点的质量要求已成为产品市场的趋势,从抽样观点来看,C=0抽样计划可以符合这精神هA) 若你的产品质量非常差,则允许数大于0的抽样计划(如MIL-STD-105中可见)并没有太大帮助ه)若你的抽样计划中允许数大于0,实际上你已同意你的检验员接受无法使用的零件或产品هC) 若你为零缺点的质量而一直奋斗,你又怎么能忍受你的抽样计划中允许不良品的存在呢?D)QS9000标准中的4.10检验和试验要素中明确规定:对计数型抽样计划的接受准则应为零缺陷,MIL-STD- 105E 中说明:规定AQL数值,并不意味着供货立有仅提供任何已知的不合格产品单元ه5.3﹑节省成本从使用者报告中显示,当公司的抽样计划由MIL-STD-105表改换成C=0抽样计划时可节省8%-30%ه理论上节省的多寡主要和批量及AQL指标有关批量及AQL指标值愈大,节省成本愈多ه5.4﹑应用范围广任何以批量检验的产品,C=0抽样计划均可应用ه5.5﹑一些概念的更新术语“暂扣批”(withhold the lot)是一个特别的概念,它并不意味着“拒收”,在“零缺陷抽样计划”中,只有抽检样本数“不合格” (non conformances)为零时才接收(即Ac=0)ه当发现一个和几个“不符合”时,该批就是“暂扣批”,一般需要工程/管理部门根据“不符合” 的严重程度和数量进行评审﹑复检﹑以决定接收或拒收ه缺陷(defect)是描述产品的某一“不合格” 特征项缺陷品(defective)是具有一个或多个缺陷的产品5.6﹑其它特点c=0 抽样计划更适合独立批检验,c=0抽样计划无加严﹑放宽转移的规定5.7﹑C=0抽样计划与MIL-STD-105 抽样计划比较***MIL-STD-105 抽样计划比较当应用MIL-STD-105 计划时,针对不同的AQL,我们将会得到较高的允收概率一般来说允收概率为0.9-0.98ه也就是说被拒收的概率(风险)为0.1-0.02 ه此被拒收的概率(风险)被为生产者冒险率αه通常使用AQL观念时, 消费者和生产者间已达成协议一当送验批质量达到此AQL水平时消费者愿意尽量允收该批, 亦即有保护生产者的功能ه***C=0抽样计划相对于AQL的另一观念为L TPDهL TPD是从消费者对于质量不良忍受程度的极限(拒收水平)来探讨一当送验批不良率达到此L TPD限度时,消费者希望能尽量拒收该批,亦即允收该批的机率愈低愈好(一般定为0.1) ه此被允许的机率(即发生错误的机率)称为消费者冒险率βه亦即以保护消费者为出发点هC=0 计划即基于L TPD的观点而设计(消费者冒险率为0.1), 因此以保护消费者来说可相等或更大于MIL-STD-105抽样计划هA)从下表中可知, C=0 计划比MIL-STD-105 将会更经济ه (愈大的批量及AQL愈经济) هB)由附图中可知, 在消费者冒险率0.1下, C=0 计划提供相等或更L TPD 保护ه。
C=0-抽样方案介绍

C=0-抽样方案介绍
C=0-抽样方案介绍
C=0-抽样方案介绍
1965年,零缺陷抽样检验方案(c=0)首次发表在国际刊物上,虽然零缺陷抽样检验方案目前还是不是国际和国家标准。
但由于“零缺陷”的品质理念已经深入人心,在加上ISO/TS16949:2002中有明确的条文要求。
所以欧美很多的企业,特别是汽车供应链相关企业普遍采用的都是零缺陷抽样检验方案。
零缺陷抽样检验方案简单的说,就是不管你的批量和样本大小如何,其抽样检验的接收数Ac=0,即“0收1退”。
在抽样检验过程中,一旦发现一个缺陷或不合格,就要实施100%的全检或退货处置。
零缺陷抽样检验方案的优点就是不存在加严、放宽与正常检验之间的转移规定。
在ISO/TS16949:2002里面的7.1.2条款里面有明确规定“7.1.2接收准则必须由组织定义,要求时,必须由顾客批准。
对于计数型数据抽样,接收水平必须是零缺陷”。
标准条文明确规定的,也就是我们要恪守的。
其实我们也一直在实用C=O的抽样检验方案。
但对其认识上可能存在一定的误区。
导致其真正的效率发挥的不够充分。
所以希望通过本文,能起抛砖引玉作用,为公司后续检验和试验活动更加顺畅的开展起到积极作用。
【干货】零缺陷(C=0)抽样方案
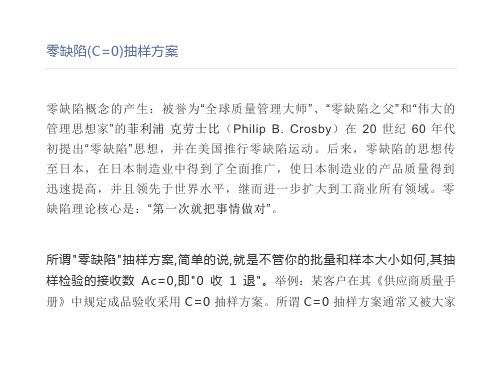
零缺陷(C=0)抽样方案零缺陷概念的产生:被誉为“全球质量管理大师”、“零缺陷之父”和“伟大的管理思想家”的菲利浦·克劳士比(Philip B. Crosby)在20世纪60年代初提出“零缺陷”思想,并在美国推行零缺陷运动。
后来,零缺陷的思想传至日本,在日本制造业中得到了全面推广,使日本制造业的产品质量得到迅速提高,并且领先于世界水平,继而进一步扩大到工商业所有领域。
零缺陷理论核心是:“第一次就把事情做对”。
所谓"零缺陷"抽样方案,简单的说,就是不管你的批量和样本大小如何,其抽样检验的接收数Ac=0,即"0收1退"。
举例:某客户在其《供应商质量手册》中规定成品验收采用C=0抽样方案。
所谓C=0抽样方案通常又被大家称为零缺陷抽样方案,即只有抽样产品全部经检验全部合格,整批产品才能够被接收;而只要在验收过程中发现有一个不良品,整批产品将被判为不合格。
客户的这一要求在公司内部引起了一些同事的担心,认为这样的要求是不是过于严格了?公司根本做不到,甚至有同事认为客户这样的要求是“霸王”条款。
事实上,C=0 抽样方案目前在国内已经被广泛使用。
它和我们中国应用较多的 GB/T2828.1-2012抽样方案一样,就方案本身来讲不存在严格不严格的概念。
在应用 GB/T2828.1-2012时,一个抽样计划严格与否取决于我们对于 AQL 的选择。
AQL 值小,抽样计划就严格;AQL 值大,抽样计划就宽松。
同样的,C=0 抽样方案也规定了一系列与GB/T2828.1-2012相同的AQL值,选择哪个AQL值完全在于我们自己的选择以及与客户的协商来决定。
所以有关“C=0抽样方案过于严格”的论断完全不成立,出现这种认识仅仅是因为大家不了解C=0 抽样方案。
需要说明的是,该客户的《供应商质量手册》是根据 IATF16949:2016建立的,而IATF16949:2016标准条款8.6.6中明确要求接收水平必须是零缺陷。
- 1、下载文档前请自行甄别文档内容的完整性,平台不提供额外的编辑、内容补充、找答案等附加服务。
- 2、"仅部分预览"的文档,不可在线预览部分如存在完整性等问题,可反馈申请退款(可完整预览的文档不适用该条件!)。
- 3、如文档侵犯您的权益,请联系客服反馈,我们会尽快为您处理(人工客服工作时间:9:00-18:30)。
期望是生产的产品完全达到规范要求。
•
对一些非关键的特性希望用比较少的检验。
• 对所有零件的所有特性的 100%检验无法实施时。 •
问题纠正前的临时检验。
•
不同原因的审核:
库存产品的确认审核 对潜在的搬运损坏项目的审核 供应商业绩验证。
•
正常的外观检验。 零缺陷使用注意事项:
•
没有检验水平的设定;
•
没有正常、加严、放宽的区分;
•
只有正常的表格使用;
•
对消费者的保证比较大;
• 对生产者的风险比较高。
•
根据 105E 进行修改,目前已是第四版。
C=0 抽样计划和 105E 抽样计划的关系
AQL
样本数
Ac
STD-105E
1.0%
125
3
4.0%
125
10
AQL
样本数
Ac
C=0 PLAN
1.0%
42
0
4.0%
18
0
零缺陷抽样计划的原理
•
直接利用 MIL-STD-105E 修改而成;
• 表中的 ASSOCIATED A.Q.L 是一个索引值; •
运用该抽样计划可能增加判退的批数;
•
零缺陷的另外考虑:
– 如果你的质量相当差,大于 0 的允收数并没有多大的帮助; –
当你的抽样计划允收数大于零,你在授权你的检验人员接受一些可能没有用的产品;
–
零缺陷强制对任何不合格采取措施;
–
如果你正在努力迈向零缺陷,那你怎能容许你的抽样计划允许有缺陷数呢? C=0 抽样计划适用于:
零缺陷抽样计划(C=0 Single Sampling Plans)
•
零缺陷计划是由 Nicholas L. Squeglia 所开发的。
•
它和 MIL-STD-105E 相比可以以较少检验数而能提供相同或较高的消费者保障。
•
除了经济优点外,它还易于使用及管理。
•
起初是用在军方产品,后来更广泛应用于许多工业上计数型的抽样,特別强调在零缺陷的输出。