10万吨苯加氢项目催化剂装填、硫化和再生方案
10万吨年粗苯加氢精制工艺设计
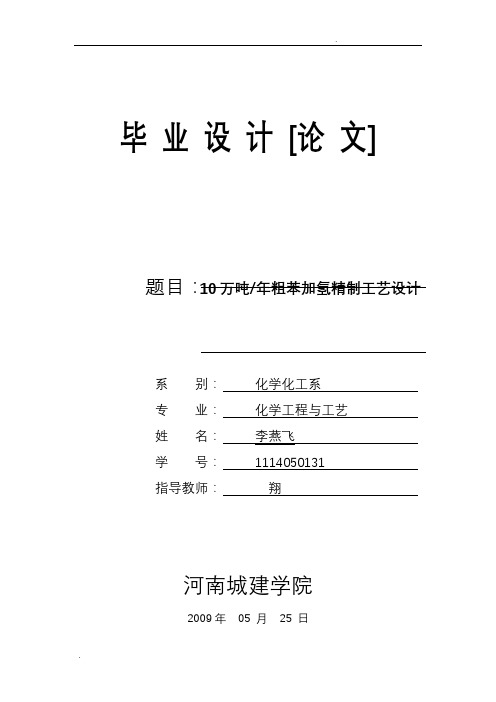
.毕业设计[论文] 题目:10万吨/年粗苯加氢精制工艺设计系别:化学化工系专业:化学工程与工艺姓名:李燕飞学号:1114050131指导教师:翔河南城建学院2009年05 月25 日河南城建学院毕业设计(论文)任务书题目10万吨/年粗苯加氢精制工艺设计系别化学化工系专业化学工程与工艺班级11140501 学号1114050131 学生姓名李燕飞指导教师李翔发放日期2009年03月16号河南城建学院本科毕业设计(论文)任务书注:任务书必须由指导教师和学生互相交流后,由指导老师下达并交教研室主任审核后发给学生,最后同学生毕业论文等其它材料一起存档。
毕业设计(论文)成绩评定答辩小组评定意见一、评语(根据学生答辩情况及其论文质量综合评定)。
二、评分(按下表要求评定)答辩小组成员签字年月日毕业答辩说明1、答辩前,答辩小组成员应详细审阅每个答辩学生的毕业设计(论文),为答辩做好准备,并根据毕业设计(论文)质量标准给出实际得分。
2、严肃认真组织答辩,公平、公正地给出答辩成绩。
3、指导教师应参加所指导学生的答辩,但在评定其成绩时宜回避。
4、答辩中要有专人作好答辩记录。
指导教师评定意见一、对毕业设计(论文)的学术评语(应具体、准确、实事求是):签字:年月日二、对毕业设计(论文)评分[按下表要求综合评定]。
(1)理工科评分表(2)文科评分表指导教师签字:年月日毕业论文(设计)正文及装祯基本要求:1、论文装祯顺序及要求(1)封面(2)封二(3)封三(封面、封二、封三利用前面已设计版面)(4)目录(5)内容摘要(其中英语摘要单词数量不少于500个)(6)正文(7)参考文献(8)封底(9)全部内容采取软包装形式进行装祯2、论文打印要求(1)统一A4纸打印(2)论文主标题3#字黑体,居中(3)副标题4#字黑体,居中(4)论文内各标题4#黑体(5)正文宋体小4#字(6)参考文献楷体4#字(7)注释一律采用脚注,宋体5#目录目录 (14)10万吨/年粗苯加氢精制工艺设计 (16)一、总论 (18)1.1 、设计指导思想和原则 (18)1.2、设计的意义 (18)1.2.1、纯苯 (19)1.2.2、甲苯 (19)1.2.3、二甲苯 (19)1.3、国内外发展状况 (19)1.4、设计依据 (21)二、生产方法和工艺流程的确定 (22)2.1、工艺技术的比较与选择 (22)2.1.1、主要生产工艺技术简介 (22)2.1.2、工艺技术的比较 (24)2.1.3、本设计采用的方法 (25)2.2、工艺加氢催化剂及萃取剂的选择 (25)三、生产流程叙述 (27)3.1、技术路线 (27)3.2、流程叙述 (27)四、工艺计算与设备选型 (29)4.1、系统物料衡算 (29)4.1.1、操作条件 (29)4.1.2、原料粗苯处理量 (29)4.1.3、两苯塔进出料 (30)4.1.4、预精馏塔进出料 (30)4.2、纯苯塔的设计计算 (30)4.2.1、纯苯塔的作用 (30)4.2.2、操作条件 (31)4.2.3、物料衡算 (31)4.2.4、塔径 (35)4.2.5、理论塔板数计算 (38)4.2.6、塔内件设计 (39)4.2.7、塔板流体力学验算 (43)4.2.8、塔板负荷性能图 (46)4.2.9、纯苯塔热量衡算 (51)4.2.10、常压塔主要尺寸确定 (52)4.3、辅助设备设计和选型 (55)4.3.1、再沸器 (55)4.3.3、储罐的选择 (55)五、设备一览表及公用工程 (56)5.1、设备一览表(附图) (56)5.2、公用工程规格 (56)六、原料及动力消耗量 (58)6.1、设计原料消耗量 (58)七、存在的问题及建议 (58)7.1、萃取溶剂的选择 (58)7.2、三废治理和综合利用 (59)7.2.1、废气的处理技术 (59)7.2.2、废水 (59)7.2.3、固体废弃物 (60)7.3、粗苯中的氯含量 (61)7.4、总结 (61)八、设计的体会和收获 (62)8.1、结论 (62)8.2、谢辞 (63)九、附图及附表 (64)9.1、工艺图纸 (64)9.2、附表 (64)参考资料 (65)10万吨/年粗苯加氢精制工艺设计(河南城建学院化学化工系河南平顶山李燕飞)指导老师:李翔【摘要】粗苯为中间体产品,本身用途极为有限,仅作为溶剂使用,但是精制后的焦化苯、焦化甲苯、焦化二甲苯等产品,是有机化工、医药和农药等的重要原料,在国内、国际上都有很好的市场,目前精苯产品价格持续上涨,市场潜力巨大。
年产10万吨苯加氢工艺设计毕业设计

毕业设计题目:年产10万吨苯加氢工艺设计摘要:本毕业设计以年产10万吨苯加氢工艺设计为目标,通过对苯加氢工艺的深入研究和分析,探讨了苯加氢反应的原理、条件以及催化剂的选择,并设计了一个适用于年产10万吨苯加氢的工艺流程。
同时,对该工艺的经济性与环境影响进行了评估,以实现可持续发展的目标。
关键词:苯加氢、工艺设计、催化剂、经济性、环境影响第一章引言近年来,苯加氢工艺在化工行业中得到了广泛应用。
苯加氢是一种将苯转化为环己烷的重要反应,可以用于制备燃料和溶剂。
本设计旨在通过详细研究苯加氢反应的原理和条件,设计一个适用于年产10万吨苯加氢的工艺流程。
第二章苯加氢反应原理和条件苯加氢是一种加氢反应,利用催化剂将苯经过反应转化为环己烷。
本章节主要阐述了苯加氢反应的原理和条件,包括反应机理、反应条件以及催化剂的选择。
第三章工艺设计根据年产10万吨苯加氢的总产量目标,设计了一个适用的工艺流程。
该工艺流程包括苯的净化、反应器的设计、分离塔的选择以及废水处理等。
同时对工艺流程进行了优化,以达到最佳经济效益和产能。
第四章经济性评估对设计的工艺流程进行经济性评估,涉及到成本估算、投资回收期、财务评估等方面。
通过分析经济性指标,评估该工艺流程的可行性和经济效益。
第五章环境影响评估对设计的工艺流程进行环境影响评估,包括废水处理、废气排放、能耗等方面。
通过综合分析,评估该工艺流程对环境的影响程度,并提出相应的环保措施,以确保工艺的可持续发展。
第六章结论通过对苯加氢工艺的深入研究和设计,本毕业设计完成了年产10万吨苯加氢的工艺设计,并对其经济性和环境影响进行了评估。
结果显示,该工艺流程具有较好的经济性和较小的环境影响,可望在实际生产中得到应用。
2.王五,赵六.苯加氢工艺的设计与优化[J].化工进展,2024,52(3):45-50.。
年产10万吨年苯加氢制环己烷项目

山东菏泽玉皇化工有限公司10万吨/年苯加氢制环己烷项目可行性研究报告常州化工设计院有限公司二零一零年四月目录第一章总论 01.1概述 01.2编制项目可行性研究报告的依据和原则 01.3项目背景、经营意义、投资意义 (1)1.4项目的范围 (3)1.5研究结果 (3)第二章市场分析和价格预测 (7)2.1产品市场分析和价格预测 (7)2.2原料供求及价格预测 (9)2.3辅助材料、燃料的供应 (13)第三章生产规模、总工艺流程及产品方案 (14)3.1生产规模 (14)3.2总工艺流程 (14)3.3产品方案 (15)3.4全厂自控水平 (16)第四章工艺装置 (17)4.1工艺原理 (17)4.2工艺技术选择 (21)4.3环己烷装置工艺流程 (26)4.4自控水平 (31)4.5主要设备的选择 (35)4.10消耗指标 (36)4.7装置界区内的公用工程设施 (37)4.8装置“三废”排放 (37)第五章建厂地区条件和厂址选择 (39)5.1建厂条件 (39)5.2厂址选择 (42)第六章总图运输、储运、土建、厂内外管网 (43)10.1总图运输 (43)10.2储运 (45)10.3土建 (46)10.4厂区外管 (47)第七章公用工程 (50)7.1给排水 (50)7.2供电、电信 (51)7.3供热、供风 (56)7.4脱盐水站 (57)7.5采暖通风及空气调节 (57)第八章辅助生产设施 (59)8.1消防设施 (59)8.2维修设施 (61)8.3仓库 (62)8.5火炬 (62)第九章能耗分析及节能措施 (63)9.1概述 (63)9.2能耗构成分析 (63)9.3工艺装置节能措施 (65)第十章环境保护 (66)10.1编制依据 (66)10.2设计采用的环境质量标准和排放标准 (66)10.3建设地区环境现状 (66)10.4建设项目主要污染物状况及治理 (68)10.5环境保护工程所需投资和定员 (71)10.10环境影响评价分析 (71)第十一章劳动保护与安全卫生 (72)11.1设计依据 (72)11.2工程概述 (73)11.3建筑和场地布置 (75)11.4生产过程中职业危险、危害因素的分析 (75)11.5设计中采用的主要安全和劳动保护措施 (77)11.10预期效果评价 (78)11.7劳动安全卫生机构设置及人员配备情况 (79)第十二章企业组织及定员 (80)12.1企业经营体制 (80)12.2企业管理体制 (80)12.3装置定员 (80)12.4人员来源和培训 (81)第十三章企业管理设施和生活福利设施 (82)13.1企业管理设施 (82)13.2生活福利设施 (82)第十四章项目实施规划 (83)14.1建设周期的规划 (83)14.2实施进度规划 (83)第十五章投资估算和资金筹措 (85)15.1投资估算 (85)15.2资金筹措 (86)15.3资金运筹计划 (87)第十六章生产成本费用估算 (88)110.1成本费用估算依据 (88)110.2成本费用估算及分析 (89)第十七章财务评价 (90)17.1财务评价的依据和说明 (90)17.2效益及财务评价指标计算 (91)第十八章不确定性分析 (92)18.2敏感性分析 (92)第十九章综合评价 (93)19.1综合评价 (93)19.2研究报告结论 (93)第一章总论1.1概述1.1.1项目名称:10万吨/年苯加氢制环己烷项目1.1.2主办单位:山东菏泽玉皇化工有限公司1.1.3法定地址:山东菏泽市经济技术开发区1.1.4企业性质:民营企业1.1.5 法人代表:王金书1.1.10注册资金:35000万元1.1.7项目建设投资(估算):21089.10 万元1.2 编制项目可行性研究报告的依据和原则1.2.1 编制可行性研究报告的依据(1) 山东菏泽玉皇化工有限公司提供的10万吨/年环己烷工程可行性研究报告设计委托书。
粗苯加氢催化剂的装填及预硫化技术

n a t io n ;
c a
t a ly s t
:
d in g
:
pre
—
su
l fu
r a
t io
n
唐 山 中润 煤 化 工 有 限 公 司 拥有 两 套 10 万 讹 粗 苯 加 氢精 制 装 置 生 产 工 艺采 用 低 温 气 相 加氢 及 环 丁 砜 萃 取 蒸馏 技 术 生 产 的 纯 苯 能 达 到 石 油苯 要 求 粗 苯加氢催 化 剂 由德 国 B A S F 公 司 生 产 主 要 金 属 成 分 为 镍 和 钴 催 化 剂 主 要 性 能指 标 见 表 l 加 氢 装 置 稳 定 运 行 主 要 取 决 于 催化剂 的 寿 命 其 寿 命 又 主 要取 决 于 催 化 剂 的装 填 预 硫 化 原 料 组 成 和 操 作 温 度 后 两 项 在 生 产 中可 以 控 制 但 装 填 和 预 硫 化 是 次性 的 如 果 操作 不 当极 易 造 成 催 化 剂 粉 碎 和 操 作 时 的 飞 温 使 催化 剂 表 面产 生 结 焦 当结焦 达 到 定 程 度 后 就 必 须 进 行 催 化 剂 再 生 造 成 长 时 间 停 工 因 此 粗 苯 加氢 催 化 剂 的装 填 和 预 硫 化 技 术在 装 置 开 车 时就 显 得十 分 重 要
, 、
一
。
‘
,
,
。
—
—
-
Th
e
Te
c
h
n o
lo gy
o
f Hydr
o
ge
n
n a
t io
a
n
Wa
C
n m
a
t a ly s t
万吨苯加氢项目催化剂装填硫化和再生方案

100kt/a苯精制项目催化剂旳装填、硫化和再生方案本方案编写人:方案编写日期:本方案审核人:本方案同意人:方案同意日期:20**年*月*日100kt/a苯精制项目催化剂旳装填、硫化和再生方案1. 总则1.1 方案制定旳原则为保证催化剂旳对旳装填,为提高催化剂活性,对旳掌握催化剂旳硫化和再生旳措施,特制定本方案。
1.2 装填、硫化和再生组织机构和职责1.2.1 组织机构安装企业:建设单位:企业各专业及各部门:工艺专业、工程部门、安全专业、仪表专业、化验专业和各有关车间主任。
规定上述各专业、各部门及承建单位共同参与本方案制定旳吹扫工作。
1.2.2 职责工艺专业:统筹管理催化剂旳装填、硫化和再生旳指挥工作,协调并督促本方案旳贯彻状况;负责编制催化剂旳装填、硫化和再生方案;负责监督本方案旳执行状况。
十二化建:负责对催化剂旳装填提供人力资源,需要加装临时性盲板旳要及时安装,提前备好;负责组织装填人员并及时到位;负责提供对催化剂旳筛选、瓷球过磅等所需人力。
工程部门:负责联络对应旳安装企业进行消除缺陷工作。
安全专业:负责贯彻本方案所波及到旳安全工作;负责登高作业票、安全作业票、进塔入罐作业票及其他与安全有关事项旳审批及检查等工作;负责监督安全措施贯彻状况;负责准备呼吸面具或自给式空气呼吸器等安全防护用品。
各车间主任:负责准备催化剂装填工具;负责所需临时性旳阀门、法兰、盲板等备品备件及其他多种应急物资旳准备工作;负责组织催化剂装填过程中所需人力物力调配事项;负责组织人员对催化剂进行检查、分析,检查催化剂内与否有杂质、油污和催化剂受潮湿浸蚀状况、机械强度与否符合规定等事项;负责组织人员填写催化剂旳装填记录,对检查出旳缺陷做出标识;负责催化剂硫化和再生全过程中各有关阀门旳启动和关闭等指挥工作;负责协调取样化验分析等详细事宜。
仪表专业:负责组织调校DCS系统,使压力、流量、温度、液位等指示精确、操作可靠;负责对DCS系统出现旳紧急故障进行维护工作。
苯加氢工艺流程

xxxx化工有限公司10 万吨/年粗苯加氢精制装置工艺流程2008 年10 月份第一章工艺流程说明1.加氢100单元1.1概述加氢100单元包括蒸发部分,反应部分,和稳定塔。
蒸发部分主要包括预蒸发器E-101A/E和带有多段蒸发器重沸器E-102A/B的多段蒸发器T-101。
预反应器R-101和带有主反应器加热炉H-101的主反应器R-102构成反应部分的关键设备。
原料(焦化轻油=COLO )在反应部分进行处理,像硫、氧和氮化合物杂质,在升温和加压下经过催化剂加氢处理掉。
另外,导致形成聚合物和结焦的不饱和碳氢物,石蜡和二烯烃变成饱和。
芳香烃几乎完全保存下来。
所需要的新鲜氢气由制氢单元提供。
通过换热器的特殊结构来回收热量,用反应后的出料作为一个热源。
1.2工艺描述焦化轻油(COLO )由罐区粗苯罐V-6101A/B/C/D,经粗苯泵送到主装置区。
首先经原料过滤器F-101A/B (过滤器的作用是除掉可能在焦化轻油中存在的固体颗粒和聚合体) 进入原料缓冲槽V-101,然后流到原料泵P-101A/B。
经过这个泵,原料被升压到大约 3.35Mpa (g)操作压力,与从循环气压缩机C-102A/B来的循环气体混合,通过预蒸发器的混合喷嘴J-101A进入预蒸发器E-101A中,在预蒸发器E-101A-E中原料与主反应物流逆向预热和部分蒸发,然后通过多段蒸发器重沸器的混合喷嘴J-102送到多段蒸发器的底部。
多段蒸发器底部操作压力大约是 2.77/3.05 Mpa( g)(SOR,CaseB/EOR,CaseC)和操作温度大约是209C (CaseA)到213C (CaseC)。
蒸发所需总热量是由被反应物料加热的多段蒸发器重沸器E-102A/B 来提供。
最底塔盘下的液体在多段蒸发器混合喷嘴J-103与从隔阻器来的蒸气混合,喷回塔内。
少量的焦化轻油(大约是总原料量的10%)作为回流送入多段蒸发器的顶部。
为了避免物料进一步处理的任何困难,从底部将一定量的高沸点化合物作为残油排出。
苯加氢催化剂预硫化技术探讨

Ke r s: Hy r r fn n Caa y t P e uf r t n y wo d d oe ig i t ls r —s lu ai o
催 化剂 预硫 化是 指原 料 进人 催化 剂 床层 之前 。 在氢气存 在下 ,用硫化氢 与催化 剂 中活性 金属氧 化 物反应 .使其 成 为活性金属硫 化物 。催化剂 预硫化
燃 料 与 化 工
Fe u l& Ch mia r c s e e c IP o e s s
J12 l u. 00
Vo . . 1 No4 41
・
煤气 净化 与 化 学产 品 加 工 ・
苯 加 氢 催化 剂预 硫化 技术 探讨
薛 占强 臧 旭 ( 鞍钢股份 有 限公 司化 工总厂 ,鞍 山 14 2 ) 10 1
素 .提 出 了操 作 时 的注 意 事项 。 关键 词 :苯 加 氢 催 化 剂 预 硫 化
中图 分 类号 :T 5 2 2 Q 2. 6
文献 标 识码 :A
文 章 编 号 :10 - 7 9 (0 0 4 04 - 3 0 1 30 2 1 )0 — 0 4 0
Te hn c l s u so npr -s lu a i n f rhy o e n n a a y t c ia c s in o e u f r to o dr r fi gc t l s di i
通 常催化 剂硫化在 氢气和 硫化氢存 在条件下 发
生硫化反应 :
Mo + H2+ . Mo 23 0 O32 s H2+ S+ H2 9 o + H2+ — C 989 0 C 0 8 s H2+ os+ H2 3 O+ H2+ — N 323 0 Ni 2 s H2+ i + H2 ¥
苯加氢催化剂使用说明书
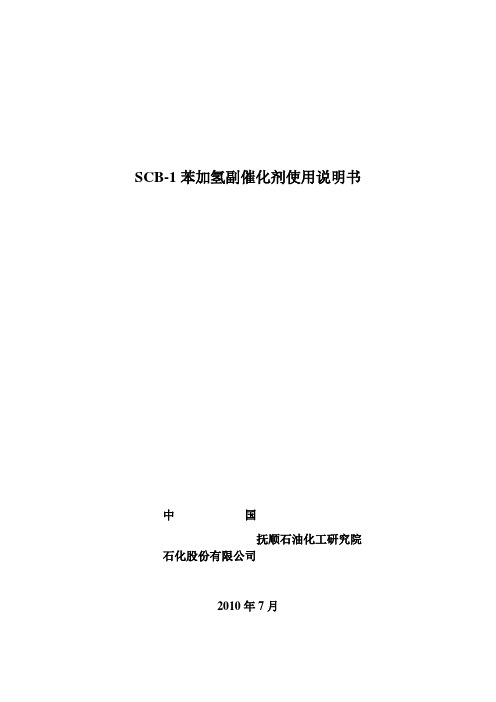
SCB-1苯加氢副催化剂使用说明书中国抚顺石油化工研究院石化股份有限公司2010年7月目录1.前言2.SCB-1苯加氢副催化剂3.产品质量要求4.催化剂对原料油和开工介质的要求5.催化剂装填6.催化剂开工7.正常操作及使用条件8.装置停车1. 前言SCB-1苯加氢副催化剂是由抚顺石油化工研究院和北京三聚环保共同开发生产的一种新型加氢催化剂。
该催化剂和主剂配套应用于苯加氢制环己烷的工艺过程。
该催化剂强度高、活性好,加氢精制后能使产品残余苯降到ppm级。
2.SCB-1苯加氢副催化剂SCB-1催化剂,以氧化铝为主要载体,以镍为加氢活性组分,其主要的物理化学性状列于表-1。
表-1 催化剂组成和物化性质3. 产品质量要求催化剂物化性质和催化性能达到指标要求。
在单管200ml加氢试验装置上,在压力2.0MPa、温度190℃、空速3.0h-1、氢油比80:1的操作条件下,以含苯5%的环己烷进行催化剂的评价,加氢后产品苯含量≤500μg/g。
4.催化剂对原料油和开工介质的要求4.1原料中的硫硫是使催化剂中毒,缩短运转周期的主要因素,因此严格要求原料中的硫含量必须小于1.5μg/g。
4.2原料中的苯为防止反应器温升过大,进料空速≤2.0h-1时,原料中的苯含量不能超过5%;进料空速为3.0h-1时,原料中的苯含量不能超过3%。
4.3氢气的质量要求氢气中CO和CO2的总含量应小于20 μL/L(CO应小于10μL/L),氢气纯度≥99.9%,氢气中氧含量≤10μL/L,氢气露点≤-60℃,甲烷≤5μL/L,硫≤1μL/L。
4.4氮气的质量要求氮气纯度≥99.99%,氮气中氧含量≤10μL/L,氮气露点≤-65℃。
5.催化剂装填5.1 装填前的准备5.1.1 对惰性瓷球的要求装填所用瓷球最好为新瓷球,如用旧瓷球则必须洗净、风干,不能混有泥土和杂物。
铁污染的旧瓷球要先用酸洗、水洗、风干后才能使用。
5.1.2 反应系统的干燥与净化催化剂装入反应器前,加氢系统必须是干燥的、无硫的、洁净的。
年产10万吨苯加氢工艺设计

第一章工艺设计说明书1.1 概述苯加氢项目包括生产设施和生产辅助设施,主要为:制氢、加氢、预蒸馏、萃取、油库、装卸台等。
生产高纯苯、硝化级甲苯、二甲苯、非芳烃、溶剂油等。
苯、甲苯、二甲苯(简称BTX )等同属于芳香烃,是重要的基本有机化工原料,由芳烃衍生的下游产品,广泛用于三大合成材料(合成塑料、合成纤维和合成橡胶)和有机原料及各种中间体的制造。
纯苯是重要的化工原料,大量用于生产精细化工中间体和有机原料,如合成树脂、合成纤维、合成橡胶、染料、医药、农药。
它还是重要的有机溶剂。
我国纯苯的消费领域主要在化学工业,以苯为原料的化工产品主要有苯乙烯、苯酚、己内酰胺、尼龙66 盐、氯化苯、硝基苯、烷基苯和顺酐等。
在炼油行业中也会用作提高汽油辛烷值的掺和剂。
甲苯是一种无色有芳香味的液体,除用于歧化生产苯和二甲苯外,其化工利用主要是生产甲苯二异氰酸脂、有机原料和少量中间体,此外作为溶剂还用于涂料、粘合剂、油墨和农药与大众息息相关的行业等方面。
国际上其主要用途是提高汽油辛烷值或用于生产苯以及二甲苯,而在我国其主要用途是化工合成和溶剂,其下游主要产品是硝基甲苯、苯甲酸、间甲酚、甲苯二异氰酸酯等,还可生产很多农药和医药中间体。
另外,甲苯具有优异的有机物溶解性能,是一种有广泛用途的有机溶剂。
二甲苯在化工方面的应用主要是生产对苯二甲酸和苯酐,作为溶剂的消费量也很大。
间二甲苯主要用于生产对苯二甲酸和间苯二腈。
焦化粗苯主要含苯、甲苯、二甲苯等芳香烃,另外还有一些不饱和化合物、含硫化合物、含氧化合物及氮化合物等杂质。
粗苯精制就是以粗苯为原料,经化学和物理等方法将上述杂质去除,以便得到可作原料使用的高纯度苯。
近年来,国内许多钢铁企业的焦化项目纷纷上马,焦化粗苯的产量迅速增加,为粗苯加氢精制提供了丰富的原料。
1.1.1 项目的来源随着我国化工行业的快速发展,近年来苯下游产品产能增长较快,尤其是苯乙烯、苯酚、苯胺、环己酮等生产装置的大量建设,对苯、甲苯、二甲苯等重要的有机化工原料需求大增,而国内苯系列产品生产能力增长缓慢,不能满足市场需求,有一定的市场空间。
关于催化剂的预硫化

关于催化剂的预硫化1.苯加氢装置所用催化剂为两种:预反应催化剂(M8-21,NiMo 4.90吨;NiO:4%, MoO3:14%)和主反应催化剂(M8-12,CoMo 11.9吨; CoO:3.3%, MoO3:14%),预计催化剂运转周期为3年,总寿命约为6年。
2.催化剂的作用●在预反应器内进行如下反应:⑴炔烃等不饱和物的加成转化反应:CnH2n-2+H2NiMo CnH2nC6H5C2H3+H2NiMo C6H5C2H5⑵含硫化合物的加氢脱硫反应:CS2+4H2NiMo CH4+2H2S●在主反应器进行如下反应:⑴烯烃的加成反应C n H2n+H2CoMo C n H2N+2⑵加氢脱硫反应C4H4S(噻吩)+4H2CoMo C4H10+H2S⑶加氢脱氮反应C6H7N+H2CoMo C6H14+NH3⑷加氢脱氧反应C6H6O+H2CoMo C6H6+H2O⑸副反应、芳香烃氢化反应C6H6+3H2CoMo C6H123.催化剂预硫化的目的本装置所用原始催化剂的主要成分为金属钴、镍、钼的氧化物,对粗苯中杂质的加氢并不具备催化作用,需将其变为硫化态,方具有活性。
4.催化剂硫化的反应机理催化剂硫化所用硫化剂为DMDS(二甲基二硫),其在标准条件下为液体,恶臭,剧毒。
在催化剂硫化条件下,其被气化,并与氢气反应:CH3-S-S-CH3+ 3H2= 2 H2S + 2CH4反应生成的硫化氢再与金属钴、镍、钼的氧化物进行反应:H2S + CoO =Co S + H2OH2S + NiO =NiS + H2O2H2S + H2 + MoO3=MoS2 + 3H2O5.催化剂预硫化的过程⑴加氢系统的冷循环和升温加氢系统气密试验合格后,通过点燃H6101提高R6102的温度,通过循环,提到整个加氢系统的温度并应达到以下条件:V-6103 PIC-6171 2.4MPaR6101 TI-6151 159℃TI-6153 149℃H6101 TI-6161 145℃TI-6162A 244℃PICA-6167 开度16%R6102 TICA-6164 242℃TI-6167A 235℃E6104A TI-6145 65℃E TI-6144 63℃⑵B.T(总硫<1.0ppm)加入以上条件以达到主反应器预硫化的条件,但预反的温度比较低,不利于所需加入的DMDS的气化,为此必须提高与反应器的温度。
苯加氢说明
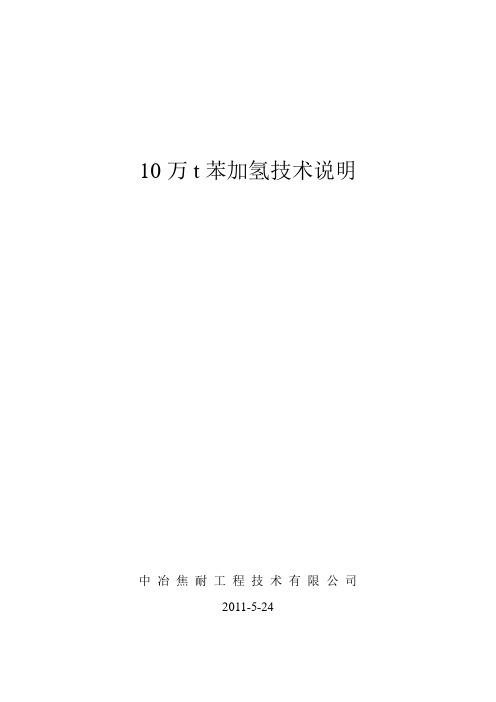
10万t苯加氢技术说明中冶焦耐工程技术有限公司2011-5-241原料、辅助原料及产品1.1原料规格1.1.1粗苯装置设计能力为年处理粗苯100,000t,原料可处理粗苯或轻苯。
原料的质量应符合YB/T5022-93国家标准,其标准如下:1.1.2氢气本装置年消耗氢气量约3680×103 Nm3,以焦炉煤气为制氢原料,由PSA变压吸附装置制得,氢气质量指标要求如下:纯度≥99.9%(V/V)含甲烷量≤0.1%(V/V)含氮量<10PPM总硫≤2.0ppm(wt.)CO+CO2≤10.0 ppm(wt.)H2O ≤30.0 ppm(wt.)含氧量≤10.0 ppm(wt.)操作压力: 1.6 MPa (g)操作温度:常温焦炉煤气中约含58%的氢气,其质量大致如下:温度:常温提取氢气后,排放的的弛放气送煤气净化系统。
1.2原料、辅助原料及产品量表辅助原材料是指苯加氢装置在开工和正常生产时所需要的各种催化剂和化学试剂等。
1.3产品质量指标主要产品质量指标如下:a) 纯苯b)甲苯c)二甲苯d)非芳烃2建设规模及装置组成2.1确定原则本工程依据下列原则确定:a) 自产或外购的原料总量;b) 满足国内外一致公认的最小经济规模;c) 达到高起点、高水准、高附加值、深加工所必需的规模;d) 综合利用、降低能耗、提高环保水平所需的规模装配水平。
2.2生产规模及单元组成2.2.1生产规模本项目苯精制装置的建设规模为年处理粗苯10万t。
年操作时间:8000小时。
操作制度:四班三运转。
装置的操作弹性为设计处理能力的50~110 wt%。
2.2.2装置组成本工程由以下装置组成:a) 制氢装置:通过PSA变压吸附,由焦炉煤气制备氢气。
b) 加氢蒸馏装置:包括预分馏、蒸发汽化、加氢反应、加氢油稳定、萃取蒸馏及苯类产品蒸馏分离等生产装置。
包含导热油循环供热系统。
c) 生产油库装置:包括原料粗苯贮槽和各种产品贮槽的槽区及汽车装卸台。
10万吨粗苯加氢装置资料

1.工艺流程说明1.1工艺概述粗苯经脱重组分塔脱除C9及以上重组分,再经多级蒸发后,进行两级加氢处理(预加氢和加氢净化),反应所需的补充氢由PSA制氢装置提供。
粗苯加氢所产生的含H2S气体经稳定塔分离出来,送至装置界区外。
经加氢处理后的产品三苯馏份(BTXS)送往预分馏单元,经预分馏塔分离成含有苯和甲苯的BT 馏份和含有二甲苯的XS馏份,BT馏份送入萃取蒸馏单元,而XS馏份送入二甲苯蒸馏单元。
BT馏份中的非芳烃在萃取蒸馏塔中从BT馏份中分离出来,随后作为非芳烃产品送往罐区,精制的BT馏份经白土罐脱除痕量的杂质后进苯塔蒸馏,分离出产品苯、甲苯产品送往罐区。
XS馏份经二甲苯蒸馏,塔顶轻组分(C8-)、塔底重组分(C8+)从XS馏份中分离出来,侧线采出混合二甲苯,轻组分、重组分和混合二甲苯被送往罐区。
加氢单元所需高纯度氢气由焦炉煤气PSA制氢装置提供。
焦炉煤气经过压缩、预处理、PSA变压吸附和净化,最终得到高纯度氢气供主装置加氢使用。
1.2加氢精制工艺流程简述加氢精制包括粗苯原料预分离部分、反应部分、稳定部分。
主要包括脱重组分塔、蒸发器、反应器、压缩机、稳定塔和加热炉等设备。
(1)原料预分离不合格粗苯或粗苯原料经过滤器后进入脱重组分塔进行轻、重组分分离,塔顶轻苯进入加氢进料缓冲罐,经加氢进料泵升压后进入蒸发器,塔底重苯经冷却器冷却后送出装置。
脱重组分塔底重沸器热源采用240℃导热油加热。
(2)反应部分轻苯在蒸发器中与主反应产物进行换热后部分汽化,并在混合器与循环气混合后进入蒸发塔,闪蒸后的重物由塔底排出,闪蒸气体进入主反应产物/预反应进料换热器,与主反应产物换热后进入加氢预反应器底部,逆流向上通过催化剂床层,烯烃和苯乙烯等不饱和物在催化剂的作用下进行加氢饱和,该反应为放热反应。
在预反应器内进行如下反应:二烯烃等不饱和物的加成转化反应:CnH2n-2+H2NiMo CnH2nC6H5C2H3+H2NiMo C6H5C2H5含硫化合物的加氢脱硫反应:CS2+4H2NiMo CH4+2H2S预反应产物经主反应产物/预反应产物换热器、主反应器进料加热炉换热,加热后进入主反应器顶部。
苯加氢工艺流程

xxxx化工有限公司10万吨/年粗苯加氢精制装置工艺流程2008年10月份第一章工艺流程说明1.加氢100单元1.1概述加氢100单元包括蒸发部分,反应部分,和稳定塔。
蒸发部分主要包括预蒸发器E-101A/E和带有多段蒸发器重沸器E-102A/B的多段蒸发器T-101。
预反应器R-101和带有主反应器加热炉H-101的主反应器R-102构成反应部分的关键设备。
原料(焦化轻油=COLO )在反应部分进行处理,像硫、氧和氮化合物杂质,在升温和加压下经过催化剂加氢处理掉。
另外,导致形成聚合物和结焦的不饱和碳氢物,石蜡和二烯烃变成饱和。
芳香烃几乎完全保存下来。
所需要的新鲜氢气由制氢单元提供。
通过换热器的特殊结构来回收热量,用反应后的出料作为一个热源。
1.2工艺描述焦化轻油(COLO )由罐区粗苯罐V-6101A/B/C/D,经粗苯泵送到主装置区。
首先经原料过滤器F-101A/B (过滤器的作用是除掉可能在焦化轻油中存在的固体颗粒和聚合体) 进入原料缓冲槽V-101,然后流到原料泵P-101A/B。
经过这个泵,原料被升压到大约 3.35Mpa (g)操作压力,与从循环气压缩机C-102A/B来的循环气体混合,通过预蒸发器的混合喷嘴J-101A进入预蒸发器E-101A中,在预蒸发器E-101A-E中原料与主反应物流逆向预热和部分蒸发,然后通过多段蒸发器重沸器的混合喷嘴J-102送到多段蒸发器的底部。
多段蒸发器底部操作压力大约是 2.77/3.05 Mpa( g)(SOR,CaseB/EOR,CaseC)和操作温度大约是209C( CaseA)到213 C( CaseC)。
蒸发所需总热量是由被反应物料加热的多段蒸发器重沸器E-102A/B 来提供。
最底塔盘下的液体在多段蒸发器混合喷嘴J-103与从隔阻器来的蒸气混合,喷回塔内。
少量的焦化轻油(大约是总原料量的10%)作为回流送入多段蒸发器的顶部。
为了避免物料进一步处理的任何困难,从底部将一定量的高沸点化合物作为残油排出。
焦化粗苯加氢精制项目催化剂的硫化过程

-
3确认 加氢系统 建立B 循环 。 . T 4炉子出口流量为l5 N / 。 . 3O m3 h
0. 0 。 3
|。 R u NE 。 RLD 0 = T w 2ui
9 I 9 I
置才能顺利生产。 两套 粗苯 加氢 精 制 装置在 建 设 和运 行 过
硫 闭。 压力控制 在24 a . MP l 化 反应 开始 。 9观察预反应器温度上升情况。 . 9紧急泄放 阀前后 阀打开 , . 任何情况不能关 l. 反应器进 口温度接近2 0 控制器 O当预 1 ̄ C, 闭。 投 自 调节预 反应器进E温度至20 。 动, l 2 ̄ C l. 0预蒸发 器注 水点 阀门加 盲板, 反前换 预 l. 1 主反应器升温 期间 , 保持 预反应器进 口 热器前注水 阀门手阈打开。 j 温魔 匾定, 监测预反应器出口温度。 23 . 触煤硫化 1. 2 当主 反应器进 口温 度升 至3 0 2 ℃时 。 停 2 31 .. 硫化前 的确 认 DMDS 人 。 注 1 . 加热炉进 出口温差高报警 由152 加氢 3  ̄提 1. 3 主反应 器进 口温度升至3 0 时保持3 , 2 ̄ C 4 至30 0 ̄ C。 时, 观察高压 分离器集液罐 内水位。 2 确 认 加 氢 系 统循 环 升 温 , 反应 器进 . 预 l. 4主反应器进 口温度3 0C 2  ̄保持期 间, 间歇 口温 度为 l 0 2 0 9 0 ℃。、 反 应器进 口温 度 为 主 注入D MD , S 维持循环气中12 体积含量不低于 tS 可通过 加人少量D MD 判断催化剂 S 硫化是否结束。 如果加入少量D S MD 后循环气中 H2含量瞬 间升高, s 可判断催化剂硫化结束。 程 中, 总结和 积累了不少经验, 有一定的 参考 具 主反应器进 口 度2 0 时进行硫化 温 2 ̄ C 1. 6催化剂硫化结束 后, 0 / 的速率降 以3 h C 和借鉴价值 。 在公司发展的同时, 宝源 公司还丰 l 】 主 反应 器进 I温 度恒 定后 , L l 开始往加 氢 系 温: 用这 些经验协 助国内其他的 同类装 置企业 开车 统 中注入DMDS 。 主反应器温 度从3 O 2 ℃降至2 0 8 ̄ C 成功 , 并随时欢迎 同行前 来学 习和交流 经验 , 在 催化 剂硫化 期 间, 要频 繁分析H2 含量 需 S 预反应器温度从2 O 2 ℃降至102 9 ̄ 这 里仅对催化剂 的硫 化操作过 程进行讨论 和分 及循环气组分H , H 需根据现场 情况 列出分 2 C 4( 保持循环气中H S 2 体积含量高于03 . % 析, 希望对国内催化剂硫化的发展有所帮助。 析 频次) 。 I 调 节 高 压 分离 器的压 力至 正常 操 作 压 力 1 硫化技术 。 1 . 观察高压分离器集 液罐水位, 根据 液位进 2 6 r 2.ba 新催化剂 ( 或再生后的催化剂)的活性 物质 行排放。 注: 硫化时涉及到的化学反应 钴、 、 等是 氧化态 , 钼 镍 而加氢催化 剂只有在硫 2循环气间歇排放 , . 保持循环气中氢气体积 Cl 3 S i S CH3 + 3 2 — 2 H4 + 2 S H C 1 q2 化态才有较高的活性 、 定性 和选择性 , 稳 而且抗 浓度维持在5% 0 以上 。 Ni 十 H2 O S + N S + H2 i 0 毒 性强、 寿命长 , 才能满足加 氢反应的需 要。 因 3调节DM s 料泵冲程 , . D 给 首先加入5 L 0/ Co + 2 — Co + H2 O H S S 0 此催化剂在接触油之前必须进行硫化, 使其与硫 h 然后将速率提升至10 / 。 , 0 L h Mo 03 + H 2 + 2 S — M o 2 + 3 2 H2 S H 0 化物接触并反应转为硫化态 。 4观察每台反应器床层上 的放热 反应 。 . 3 重要注 意事项 、 两 套 装 置的 催化 剂 硫化 都是 采 用湿 法 硫 5主反应器进出1温差不得超过3 — O . 2 1 0 4 ℃, 1反应器温 升不能超过 3 -4  ̄, . 0 0 否则降低 化 : 氢气存 在下, 高含硫的油 品在液相状态 否则降低或停D S I 在 用 MD  ̄ 料。 J D DS 人量 。 M 加 下进行 的催化 剂液相 硫化 。 就是在 硫化 油中 也 6主 反应器催化剂 床层最高温 度不能超 过 . 2调节DM OSJ入量 , .  ̄ n 使主反应器进 口H2 S 加 入硫化卉 D s 《 MD 进行催化剂硫 化, 这样 既可缩 3 0 。 7℃ 体积含量保持 在05 1 % . . 。 - O 短催化剂硫化所需要的时间, 又可提高催化剂的 7 . 催化剂硫 化期间, 如压缩机 跳闸, 应立即 3及时 排放 高压分离器集液罐 中溶有H2 . S 加氢活性。 fJD S  ̄ E MD 注入 , T 防止反应器内出现 热点。 的水。 2 硫化过程 . 主 反应 器进 出 口没 有 温 差 时 , 以 提 高 可 4保 持循环 氢中氢气体积 含量在5 % . 0 以上 硫化步骤包括原料 的准备、 系统加 压、 系统 D S MD 注入量。 预计注入D S 2 l,时到达 (0 7 % MD  ̄1一 6 、 J 5 — 0 之内) 同时保持循环气中甲 体积含 。 烷 加 热和 催化剂 干燥 、 系统 引入纯 苯和 甲苯 混 合 H S 2 突破1, 2 这时循环气中H S 1 2 体积含量一O % 量低于 l%。 . 。 2 O 如果循环气中氢气或 甲烷含量超 出 物B 、 加入D S T MD 硫化催化剂等。 预计注AD S 小时可能检测到微量H S( .MD  ̄8 2 体 范围, 需要排放 , 加入补充氢气。 21 . 硫化作业前的准备工作 积含量小于00% 。 . ) 硫化结束也可以通过主反应 5 5每隔一小时用钢瓶取循环气, . 分析循环气 1 . 硫化剂D S MD 已准备就绪。 器出E温度下降来判断。 作工每 小时记录DC 中的H s 1 操 S 2 含量 。 正常情况下加入DMDS z时 后8 , J 2 注硫化剂泵完好可用状态 。 . 各参数值, MD  ̄ 入量及分析结果 。 D Sn J 开始出现微量H2 。 S 3记录用 表格及H2 检知 器和检知 管准 备 . S 主 反 应 器升温 过 程 中 ( 口温 度2 02 进 2  ̄— 4 结论 . 就绪。 30 ) 2  ̄ 硫化 C 影 响 加 氢催化 剂 硫化 的 操作 参 数 因素较 22硫化作业前阀门设 置 . 当H2  ̄ 达 突破 I , sl J : 降低DM DS 1 后 注入 量 多: 载体性 质、 金属 、 硫化方法、 硫化度、 硫化压 1 . 关闭进V的手动 阀门 1 至 10 / , 0 L h 同时 调节主 反应器加热 器 负荷 , 以 力、 硫化 油、 氢气浓度、 硫化时 间、 空速、 硫化氢 2加 氢进 料缓 冲罐 顶压 力前后 阀打开 , . 旁 1 ̄ h 0 / 的速率 ( l ̄ h 稳定l C 提O/, C 小时) 提高主 反 浓度、 升温 速度, 注硫速度等, 为了提高催化剂的 通阀关闭 , 设定值i 0 0 KP 投 自 , a 动 下限 报警5 应器进口温度。 O 活性、 稳定性 、 选择 性和 使用寿命, 避免事故 的 K a 上限报警10 K a P, 5 p 。 1分析循环 气O H2 含量 及循环气 中各组 发生, . O S 必须根据实际条件选择合适的操作条件 , 1胜 达因泵进 1阀门打开, ) . 3 出口关闭。 小 最 进而达到延长 装置运转周期, 提高经济效 益。 流量阀打开。 f 2 观察两台反应器的出口温度, . 根据反应 器 2. 氢进 料调节 阀关 闭, )口 力 前后阀打开, 关闭 进出1温差调节D S 入量 。 2 1 MD 注 旁路阀。 3如果 其中一台反应 器的进 出口温 差超 过 . 3把 蒸发塔液位计上下阀打开, . 保证蒸发塔 3 - 0C, 0 4  ̄ 降低D MDS 注入量 。 至加氢进 料缓 冲罐管线畅通。 J 4当两台反应器的进出1温差低于2 ̄以下 . 7 1 0 C 4预 反进 口温度调节阀开 10 . 0 %预反应器进
- 1、下载文档前请自行甄别文档内容的完整性,平台不提供额外的编辑、内容补充、找答案等附加服务。
- 2、"仅部分预览"的文档,不可在线预览部分如存在完整性等问题,可反馈申请退款(可完整预览的文档不适用该条件!)。
- 3、如文档侵犯您的权益,请联系客服反馈,我们会尽快为您处理(人工客服工作时间:9:00-18:30)。
100kt/a苯精制项目催化剂的装填、硫化和再生方案本方案编写人:方案编写日期:本方案审核人:本方案批准人:方案批准日期:20**年*月*日100kt/a苯精制项目催化剂的装填、硫化和再生方案1. 总则1.1 方案制定的原则为保证催化剂的正确装填,为提高催化剂活性,正确掌握催化剂的硫化和再生的方法,特制定本方案。
1.2 装填、硫化和再生组织机构和职责1.2.1 组织机构安装公司:建设单位:公司各专业及各部门:工艺专业、工程部门、安全专业、仪表专业、化验专业和各相关车间主任。
要求上述各专业、各部门及承建单位共同参与本方案制定的吹扫工作。
1.2.2 职责工艺专业:统筹管理催化剂的装填、硫化和再生的指挥工作,协调并督促本方案的落实情况;负责编制催化剂的装填、硫化和再生方案;负责监督本方案的执行情况。
十二化建:负责对催化剂的装填提供人力资源,需要加装临时性盲板的要及时安装,提前备好;负责组织装填人员并及时到位;负责提供对催化剂的筛选、瓷球过磅等所需人力。
工程部门:负责联系相应的安装公司进行消除缺陷工作。
安全专业:负责落实本方案所涉及到的安全工作;负责登高作业票、安全作业票、进塔入罐作业票及其他与安全有关事项的审批及检查等工作;负责监督安全措施落实情况;负责准备呼吸面具或自给式空气呼吸器等安全防护用品。
各车间主任:负责准备催化剂装填工具;负责所需临时性的阀门、法兰、盲板等备品备件及其他各种应急物资的准备工作;负责组织催化剂装填过程中所需人力物力调配事项;负责组织人员对催化剂进行检查、分析,检查催化剂内是否有杂质、油污和催化剂受潮湿浸蚀情况、机械强度是否符合要求等事项;负责组织人员填写催化剂的装填记录,对检查出的缺陷做出标记;负责催化剂硫化和再生全过程中各相关阀门的开启和关闭等指挥工作;负责协调取样化验分析等具体事宜。
仪表专业:负责组织调校DCS系统,使压力、流量、温度、液位等指示准确、操作可靠;负责对DCS系统出现的紧急故障进行维护工作。
化验专业:负责对催化剂硫化、再生时取样分析工作,提供的分析数据要求准确无误;负责准备取样分析所需各种化验器具。
2.催化剂及填料装填2.1 催化剂装填2.1.1装填催化剂注意事项2.1.1.1 在装填催化剂之前,应对催化剂进行检查、分析,检查催化剂内是否有杂质、油污,是否受到潮湿浸蚀,机械强度是否符合要求。
2.1.1.2 必要时要对催化剂进行筛选,筛除催化剂粉和小颗粒的碎催化剂等杂质,以减小催化剂床层阻力。
2.1.1.3 将实际要装填的催化剂及瓷球过磅称出毛重,装填时再称空桶和剩下的催化剂及瓷球,得出装填净重。
2.1.1.4 反应器(转化炉)要彻底隔离。
2.1.1.5 催化剂在装填过程中应避免受潮,因此催化剂暴露于大气的时间必须限定到最短(要用时才开桶),应在天气干燥、湿度较低的时候进行。
2.1.1.6 当催化剂装填工作由于下雨需中断时,反应器(转化炉)入口及装填设备必须用帆布袋(块)盖紧,反应器(转化炉)内用干燥气(仪表风)密封,若因别的原因需要中止时,亦须采用同样措施。
2.1.1.7 由于催化剂易碎,禁止从1米以上高度掉落,也不能用脚踩压,必要时用550×550mm木板垫脚。
2.1.1.8 进入反应器(转化炉)前必须测定内部的氧浓度,当氧浓度大于20%或带有空气面罩方可进入。
2.1.1.9 装填人员必须按规定穿戴劳动保护用品,工作完毕必须充分淋浴。
2.1.2 加氢单元预反应器、主反应器催化剂填装2.1.2.1 准备工作(1)检查瓷球并标明球的外部尺寸(1/4″、1/2″、1″)。
(2)预反应器、主反应器用催化剂分开。
预反应器:M8-21 主反应器:M8-12(3)塔内清洁干燥(无锈及其它污物),内件应按规格进行核查。
(4)塔内瓷球层及催化剂填充高度须标明。
(5)准备好吊车、大吊装漏斗、软管、防爆灯、测氧仪等工器具。
2.1.2.2 主反应器装填步骤(1)装填1″瓷球至高度按设备图纸,保持水平;装填1/2″瓷球至高度按设备图纸,保持水平;装填1/4″瓷球至高度按设备图纸,保持水平。
(2)装填M8-12催化剂约11.3m3高度按设备图纸,当装至热电偶所在的催化剂高度时,重新安装热电偶。
(3)安装下边的中间筛网。
(4)装填约1″瓷球至按设备图纸,保持水平。
(5)装中部配管,H2管。
(6)安装格栅;(7)安装上边的中间筛网。
(8)装填1″瓷球至高度按设备图纸,保持水平;装填1/2″瓷球至高度按设备图纸,保持水平;装填1/4″瓷球至高度按设备图纸,保持水平。
(9)装填M8-12催化剂约11.3m3高度按设备图纸,当装至热电偶所在的催化剂高度时,重新安装热电偶。
(10)装上部筛网。
(11)装填1″瓷球至高度按设备图纸,保持水平。
2.1.2.3预反应器装填步骤(1)安装格栅,底部安装筛网。
(2)装填约1″瓷球至高度按设备图纸,保持水平;装填约1/2″瓷球至高度按设备图纸,保持水平;装填约1/4″瓷球至高度按设备图纸,保持水平。
(3)装填M8-21催化剂9.2m3高度5.2mm;当装至热电偶所在的催化剂高度时,重新安装热电偶。
(4)安装顶部筛网。
(5)装填约1/2″瓷球至高度按设备图纸,保持水平。
2.1.3 转化炉催化剂填装2.1.3.1 准备工作(1)对催化剂开桶进行质量检查,用6-10目的钢网筛将催化剂中的碎粉筛除备用。
(2)准备好吊车、大吊装漏斗、软管、防爆灯、测氧仪等工器具。
(3)将转化炉上、下封头拆下,先检查转化炉质量是否符合要求,再将转化炉内上下封头、列管内、管板和花板上的铁锈杂物全部清除干净,必要时可进行酸洗、水洗,再擦净、吹干备用,要求无铁锈、无杂物。
(4)下封头花板上按要求规格放2层12目丝网,往花板上堆满已经衰洗干净的φ10-12mm的氧化铝瓷球,将瓷球上表面推平,要求瓷球上表面与转化炉下花板面保持有10-15mm高的空间。
(5)重新装好上、下封头,通气对转化炉再次进行试漏,当确认下封头大法兰不漏气后,方可泄压排气,准备装填催化剂。
2.1.3.2 装填步骤(1)卸下转化炉上盖,再次检查转化炉内是否干净,如不符合要求,要重新清扫干净。
逐根检查反应管,看有无堵塞等异常现象。
(2)逐根定体积装填催化剂,并做记号,以免漏装或重装。
(3)装填时不能急于求成,以防出现架桥现象,当出现架桥时应做好标记,及时处理。
(4)定量装填完后,再逐根检查有无漏装,确认无漏装并已处理了架桥现象。
如需要,再补充加装一遍,保证每根管内催化剂量基本相等。
(5)当全部装填完毕后,用仪表空气吹净上管板,装好转化炉上封头及管线。
(6)卸下转化炉下部过滤器,将丝网上杂物清扫干净,装好过滤器。
2.1.4 当催化剂装填结束后,检查有无异物留在反应器(转化炉)内,按要求对反应器(转化炉)进行气密性试验,确保封头、法兰无泄漏。
2.2 填料填装3. 催化剂的硫化、再生、钝化3.1 催化剂的硫化加氢系统装填的催化剂在初次使用或再生后均是氧化状态的,为提高其活性,在第一次运转及再生之后,催化剂必须进行衰减和硫化。
最好的硫化方法是向加氢苯、纯芳烃及循环气体中混入二甲基二硫化物(DMDS)。
75kg硫相当于110kgDMDS,硫化所需时间24h到36h之间(不含系统置换和充压、升温时间)。
R302填装M8-12共22.61m3约15.15吨,需DMDS约1667Kg。
R301填装M8-21共9.19m3约6.06吨,需DMDS约667Kg。
3.1.1 硫化前的准备工作3.1.1.1 系统检查(1)系统设备、管道已吹扫,气密实验已结束,R301、R302内催化剂已按要求填装完毕。
(2)检查系统内所有阀门的开、关位置,应符合开车要求。
(3)公用设施电、压缩空气、仪表风、氮气、蒸汽、循环水等满足开工要求。
(4)与中控室联系各控制仪表是否良好并处于开车位置。
3.1.1.2 惰性化(1)关新鲜氢总阀,关V302进口阀(设盲板), 切断V304至E401管线(设置盲板)、切断V304放空阀等与系统相连工序的阀门,使得200#和300#成为独立系统。
同时打开系统内的各直通阀、旁路阀。
特别注意氢气管线的置换。
(2)由C202A/B进口处引N2入系统。
参照岗位操作中开车前准备部分的用氮气吹扫200#和300#独立系统。
(3)注意死角,如分析、放空等多处取样,分析O2含量<0.5%,分析合格后,打开放空管连通阀,氮气冲压至0.1MPag。
3.1.1.3 引入H2开新鲜氢总阀、C201AB旁通阀FV2101,引新氢进入高压系统,用氢气置换氮气,参照高压系统开车中氢气置换氮气部分。
3.1.1.4 系统升压升压速度<0.3Mpa/h,当系统压力升至1.1MPag时,关C201A/B旁路阀,启动氢气压缩机C201升压。
当系统压力升至2.0MPag时,启动循环气压缩机C202打循环,循环量控制在10000Nm3/h左右(1.0t纯芳烃需800Nm3循环气),系统压力最后控制在2.8MPag。
升压过程中分别在1.1MPag、2.0MPag、2.8MPag时,对系统进行气密实验。
3.1.1.5 升温系统压力2.8MPag无泄漏,压缩机运行正常,开始升温。
为保护催化剂、设备,首次升温速度<20℃/h,后升温速度<30℃/h。
热源来自E303中压蒸汽,开工加热器E306和电热器F301。
参照高压系统开车中升温部分。
温度升至120℃时,恒温4h,升至200℃时,恒温4小时,此时进行热紧工作,热紧完成后继续升温,当预反应器R301升至190-200℃,主反应器R302升至280℃时,恒温,并做气密实验。
升温时,反应器进出口温差<30℃。
3.1.1.6 建立物料循环:用于硫化的载体必须绝对不含乙烯,否则在催化剂表面将形成像沉淀物的结焦物等,这将导致一个较短的再生循环。
基于这个原因,不允许用粗苯作为硫化载体。
较好的方法就是用80%的纯苯加上20%的甲苯(全硫<2ppm,作为硫化载体,于V302混合。
硫化载体打入T301,跟据T301液位(蒸发情况)逐步加大进料量FRC3101至14000L/h,由E303中压蒸汽、F301电热器控制反应器的温度,系统压力由PV3402控制,当V304液位达60%时,开FV3403的前后截止阀,出料回至V302,再次循环。
以上过程完成后,在保证反应器温度的前提下,逐渐降低系统压力到2.0MPag,以保证硫化剂能够完全蒸发。
3.1.2 硫化3.1.2.1 按以下条件调整预硫化条件系统压力(PICA3402)2000kPag主反应器R302入口温度(TR3304-1-2)230℃主反应器R302出口温度(TR3309-1-2)230℃(不低于220℃)F301出口温度(TRCA3303)240℃预反应器R301入口温度(TRA3209-1-2)200℃(不低于190℃)预反应器R301出口温度(TRA3212-1-2)200℃(不低于190℃)混合原料流量(FRC3101)14.8M3/h硫化过程见上图,其温升、DMDS芳烃混合物加入量可根据化验分析结果作出相应调整。