QC_7_tools品管七大手法合集
QC 7 Tools七大手法工具

20
40%
D 8 16 90
其它 5 10 100 合计 50 100 100
图表→自定义类型→线-柱图
10
20%
0 次数 A
B
C
D 其它
不良项目柏拉图
QC 7大手法-柏拉图 4
◆结果的数据 (现况分析)
问题
甲乙丙
◆要因的数据 (原因分析)
要因
1234
A B C
BA 甲
EDC
A BC
QC 7大手法-柏拉图 5
TOPIC
1. QC-STORY
1-1.QC Story VS. QC 7 Tools 1-2.脑力激荡法
2. QC 7大手法介绍与应用说明
2-1.查检表
2-2.鱼骨图 - 特性要因图/石川图 2-3.柏拉图 2-4.直方图 2-5.层别法 2-6.散布图 2-7.管制图
3. Q&A
QC Story-1
• 使用时机:
–掌握问题点、发现原因、效果确认
QC 7大手法-柏拉图 2
柏拉图制作步骤
1.决定不良的分类项目:
•藉由结果别分类(现况分析) •藉由原因别分类(要因分析) ※项目最好在4~8项
3.记入图表纸并且依据大小排列画 出柱状
2.决定数据收集期间,并且按照 分类项目搜集数据
•决定一天、一周、一个月 、一季 或一年为期间
1234 A B C
QC-Story vs QC-7 Tools
主题选定
现况分析及 目标设定
.
. .
.
..
.
. .
..
要因分析
1234
真因验证
AB
.
. .
.
QC7Tools品管七大手法

安全 -意外事件数、意外发生率....
士气 -出席率、提案改善率...
『要因』(Factor)
-影响『结果』的原因
-一般以5M1E(Man, Machine, Method, Material, Measurement , Environment)等6方向最为大要因
25
造成上下偏光片脏污的原因
〈问题点〉 特性
41
范例:甘特图 活动计划表
42
QC 7 Tools Summary-何时使用?
• 根据事实、数据发言:
图表 (Graph)、查检表 (Check Sheet)
• 整理原因与结果之关系,以寻找出可能的潜在性问 题:
特性要因图 (Characteristic Diagram)
• 并非对所有原因采取处置,而是先从影响较大的2~3 项采取措施:
20
柏拉图之应用
B.确认改善效果
改善前不良项目 柏拉图
单位:dppm
改善后不良项目 柏拉图
单位:dppm
DPPM降低17332
改善前、后之比较时,前后比较基准应一致!
21
22
范例:柏拉图
23
特性要因图 (Characteristic Diagram)
何谓特性要因图(因果图)
– 借着多人共同讨论,整理问题特性与要因间的关 系 ,成为有条理的图形,此图形称为特性要因图 – 亦称鱼骨图(Fish Bone Diagram),因果图 (Cause and Effect Diagram)或石川图(Ishikawa Diagram)
特性要因图制作顺序
Step 1:
1.1 确定问题及品质的特性 1.2 『特性』置于最右端,将『鱼脊』(spine)由左至 右对准『特性』画出
qc七大手法-QCtools 精品
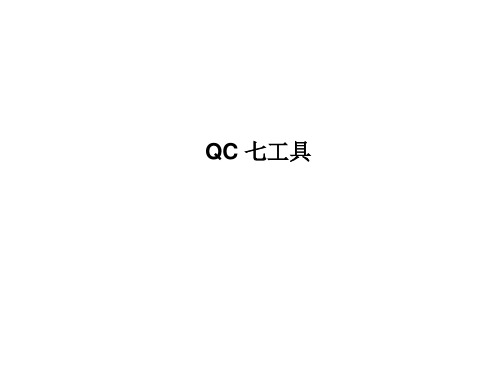
作出质量的结果,作出 成品或半成品.产品要 是良品.
制造工程结构的分析
8. 活用QC技法时的心理状态
(1)QC技法是为达成目的的有效手段. (2)问题的95%都是活用QC技法来解决的. (3) QC技法的价值根据使用的人或使用的目的而不同.
(4)为了使其成为活的QC技法有必要全员参加去活用它.
8. 活用QC技法时的心理状态
7. 应用QC技法的目的
1) 应用QC技法是一种手段,目的是管理现场. 2)在QC应用技法之前,先研讨以下一些现场的事情.
投入
供应作成一定质量时 需要的部品,材料. 制造适当良品的部品 和材料
规格,基准 ⊙ 什么样的质量 ⊙ 靠什么方法作出来?
作业
产出
人,设备,工具通过作业 方法作出更可靠的品质, 更低廉的,更安全的, 轻松的作业出来.
4. PDCA CYCLE
PDCA循环(PDCA Cycle) 戴明循环(Deming Cycle)
PDCA循环的概念最早是由美国质量管理专家戴明提出来的,所以又称为“戴明环”。 它是全面质量管理所应遵循的科学程序。全面质量管理活动的全部过程,就是质量计划 的制订和组织实现的过程。
PDCA循环是有效进行任何一项工作的合乎逻辑的工作程序。在质量管理中,PDCA循 环得到了广泛的应用,并取得了很好的效果,因此有人称PDCA循环是质量管理的基本 方法。之所以将其称之为PDCA循环,是因为这四个过程不是运行一次就完结,而是要 周而复始地进行。一个循环完了,解决了一部分的问题,可能还有其它问题尚未解决, 或者又出现了新的问题,再进行下一次循环。
QC 七工具
概述
1.什么是质量(Quality)? 2.什么是管理(Control)? 3.TQM与现场品质管理 4.PDCA CYCLE 5.质量管理的时代性变迁? 6.质量管理的观念的变化 7.应用QC技法的目的
QC7tools-品检员适用
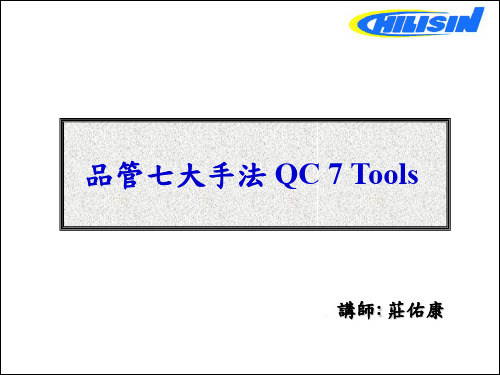
品管七大手法:
柏拉圖 (Pareto Diagram)
-- 用圖表用紙記入縱軸及橫軸 縱軸左側直線代表不良數,不良率或損失金額, 右側直線代表 累計影響度,橫軸代表項目。
32 30
25
不
良
20
率
15
%
10
5
100%
81.3% 累 75% 計
影 50% 響
度
25%
點上累計影響度,並以折 線連結則得柏拉圖
品管七大手法:
散佈圖 (Scatter Diagram)
四、散佈圖的判讀
Y
Y
Y
X 完全的正相關 Y
X 有正相關 Y
X 似有正相關
Y
X 有負相關
Y
X 完全的負相關
Y
X 似有負相關
Y
X 無相關
X 無相關
X 曲線相關
品管七大手法: 直方圖 (Histogram)
一、何謂直方圖
-- 一眼可看出變異狀況的方法 -- 又稱柱狀圖
(3)決定組數 (K)
組數 = 數據個數
(整數值)
組數 = 100 = 10
(4)決定組距 最大值 最小值 組距 = 組數
組距
Байду номын сангаас
=
82.8 77.5 10
= 0.53
測定器刻度讀數最小為 0.1,便於計算平均數或標準差, 組距常取5或 2的倍數 ,所以這裡組距可計算為 0.5
品管七大手法:直方圖 (Histogram)
(5) 決定組間的界值 (組界) -- 組間的界值以最小測定單位值之1/2 來決定 。 第一組下限 = 最小值 - 最小測定單位 2 第一組上限 = 第一 組下限 + 組距 第二組下限 = 第一組上限 第二組上限 = 第二組下限 + 組距
新QC七大工具(手法)完整版!

新QC七大工具(手法)完整版!品管七大手法,是常用的统计管理方法,又称为初级统计管理方法或者新旧QC七大工具(手法),都是由日本总结出来的。
日本人在提出旧七种工具推行并获得成功之后,1979年又提出新七种工具。
旧QC七大手法偏重于统计分析,针对问题发生后的改善,新QC 七大手法偏重于思考分析过程,主要是强调在问题发生前进行预防。
之所以称之为“七种工具”,是因为日本古代武士在出阵作战时,经常携带有七种武器,所谓七种工具就是沿用了七种武器。
旧七大工具:检查表、数据分层法、排列图、直方图、因果分析图、散布图、控制图。
新七大工具包括:1 . KJ法(亲和图法)(Affinity Diagram)2 . 关联图法(Rolation Diagram)3 . 系统图法(Systematization Diagram)4 . 矩阵图法(Matrix Diagram)5 . 过程决策计划图法(Process Dicesion program Chart)6 . 箭条图法(Arrow Diagram)7 . 矩阵数据分析法(Factor Analysis)01 . KJ法(亲和图法)┃新QC七大手法的使用情形,可归纳如下:亲和图 - 从杂乱的语言数据中汲取信息;关联图 - 理清复杂因素间的关系;系统图 - 系统地寻求实现目标的手段;矩阵图 - 多角度考察存在的问题,变量关系;PDPC法 - 预测设计中可能出现的障碍和结果;箭条图 - 合理制定进度计划;矩阵数据解析法 - 多变量转化少变量数据分析;┃新QC七大手法概述:┃新QC七大手法的特点:1 . 整理语言资料的工具2 . 将语言情报用图形表示的方法3 . 引发思考,有效解决凌乱问题;4 . 充实计划;5 . 防止遗漏、疏忽;6 . 使有关人员了解;7 . 促使有关人员的协助;8 . 确实表达过程。
9 . 管理工具,可以应用于QC以外的领域┃新QC七大手法的五项益处:1 . 迅速掌握重点 - 实时掌握问题重心,不似无头苍蝇般地找不到重点。
(品管工具QC七大手法)品管七大手法讲解
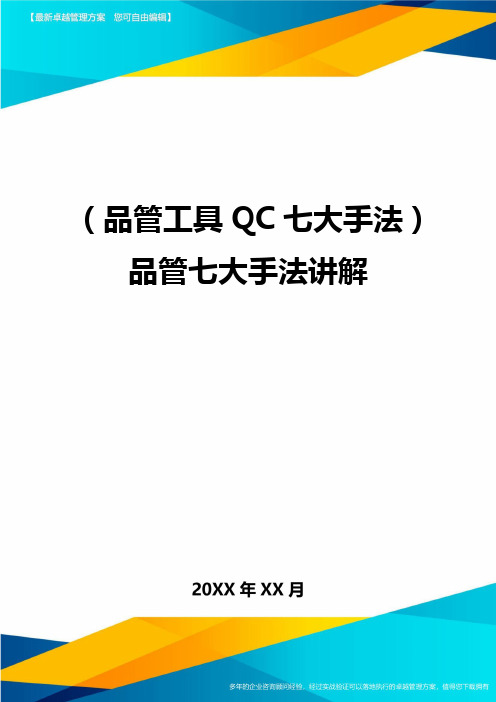
(品管工具QC七大手法)品管七大手法讲解品管七大手法講解壹.七大手法簡介:⏹ A.特性要因圖:尋找因果關係. ⏹ B.柏拉圖:找出“重要的少數”. ⏹ C.直方圖:了解數據分布與制程能力. ⏹ D.層別法:按層分類,分別統計分析. ⏹ E.查檢表:調查記錄數據用以分析. ⏹ F.散布圖:找出兩者的關係. ⏹G.管制圖:了解制程變異.二.品管七大手法所體現的精神:⏹ 1.用事實與數據說話. ⏹ 2.全面預防.⏹ 3.全因素、全過程的控制.⏹ 4.依據PDCA 循環突破現狀予以改善. ⏹5.層層分解、重點管理.三.特性要因圖:⏹對於結果與原因間或所期望之效果與對策間的關係,以箭頭連結,詳細分析原因或對策的壹種圖形稱為特性要因圖,工程魚骨圖或因果圖.⏹它為1952年日本品管權威學者石川馨博士所發明,又稱“石川圖”.作法:⏹ 1.4M1E 法:(人、機、料、法、環境)⏹ 2.5W1H 法:(What 、Where 、When 、Who 、Why 、HOW) ⏹ 3.創造性思考法:希望點例舉法、缺點列舉法、特性列案法. ⏹4.腦力激蕩法:“BrainStorming”嚴禁批評、自由奔放.兩類特性要因圖:⏹ 1.追求原因型:⏹2.追求對策型:柏拉圖的用途:⏹ 1.作為降低不良的依據.⏹ 2.決定改善的攻擊目標.⏹ 3.確認改善效果.4.用於發掘現場的重要問題點.⏹ 5.用於整理報告或記錄.⏹ 6.可作不同條件的評價.柏拉圖應用範圍:⏹ 1.時間管理.⏹ 2.安全.⏹ 3.士气.⏹ 4.不良率.⏹ 5.成本.⏹ 6.營業額. ⏹7.醫療.ABC 法應用:⏹ A.時間管理. ⏹ B.倉務管理. ⏹C.其他.柏拉圖實例:五.層別法:定義:為區別各種不同原因對結果之影響,而以個別原因為主體,分別作統計分析的方法,稱為層別法.分類:⏹ 1.時間的層別. ⏹ 2.作業員的層別. ⏹ 3.機械、設備層別. ⏹ 4.作業條件的層別. ⏹ 5.原材料的層別. ⏹6.地區的層別等.0%10%20%30%40%50%60%70%80%90%100%實例壹:結果顯示,周師傅的方法配美國材料良品率最高,為98%.實例二:法拉利笼动压成型品质情况日报表日期:班别:□白班□夜班模号:第壹套□第二套□第三套□實例三:某電子廠有批精密零件于下工程裝配時發生困難,經直方圖分析,超出規格甚多,再將此100個數據,按A,B,C三種機種別加以層別,發現A機種的產品低於規格下限的很多,而C機種的產品超出規格上限的很多,B機種的產品完全于規格內.因此,只要針對A,C兩機種著手改善即可.六.查檢表:為了便於收集數據,使用簡單記錄填記並予統計整理,以作進壹步分析或作為核對,檢查之用而設計的壹種表格或圖表.作法:⏹ 1.明確目的. ⏹ 2.決定查檢項目.⏹ 3.決定檢查方式(抽檢、全檢).⏹ 4.決定查驗基準、數量、時間、對象等. ⏹5.設計表格實施查驗.查檢表的種類:⏹1.記錄用查檢表:主要功用于於根據收集之數據以調查不良項目、不良主因、工程分布、缺點位置等情形.必要時,對收集的數據要予以層別.規 格規 格A BC規 格規 格2.點檢用查檢表:要功用是為要確認作業實施、機械設備的實施情形,或為預防發生不良或事故,確保安全時使用.這種點檢表能够防止遺漏或疏忽造成缺失的產生.把非作不可、非檢查不可的工作或項目,按點檢順序列出,逐壹點檢並記錄之. 實例:设备每日检查表收集數據應注意的事項:⏹ 1.收集的數據必須真實,不可作假或修正.⏹ 2.收集的數據應能獲得層別的情報.⏹ 3.查檢項目基準需壹致.⏹ 4.樣本數需有代表性.⏹ 5.明確測定、檢查的方法.⏹ 6.明確查驗樣本的收集方法、記錄方式、符號代表意義.⏹7.慎用他人提供的數據.七.散布圖:為研究兩個變量間的相關性,而搜集成對二組數據(如溫度與濕度或海拔高度與濕度等),于方格紙上以點來表示出二個特性值之間相關情形的圖形,稱之為“散布圖”.關係的分類:⏹ A.要因與特性的關係.⏹ B.特性與特性的關係.⏹ C.特性的兩個要因間的關係.散布圖的判讀:⏹1.強正相關:X 增大,Y 也隨之增大,稱為強正相關. Y⏹ 3.強負相關:X 增大時,Y 反而減小,⏹ 5.曲線相關: X 開始增大時,Y 也隨之增大,但達到某壹值后,當X 增大時,Y 卻減小.散布圖判讀注意事項⏹ 1.注意有無異常點. ⏹ 2.见是否有層別必要⏹3.是否為假相關.⏹ 4.⏹5.數據太少,SPC---StatisticalProcessControl.統計制程管制.☆由制程調查來改進制程能力,不斷降低產品品質變異性,而提升產品品質的壹種方法.☆七十年代風行於日本,以至於仍有不少日本人至今仍深信其功效,而抵觸ISO9000的導入. ☆它的主要工具為管制圖.質量有兩大特性:⏹ 11.規律性⏹ 22.波動性:正常波動、異常波動管制圖的功效:⏹ aA.及時掌握異常波動,克服影響因素,維持制程穩定.Y X⏹2.弱正相關:X 增大,Y 也隨之增大,但增大的幅度不顯著. 4.弱負相關:X 增大時,Y 反而減小,但幅度並不顯著.YYX⏹bB.了解制程能力.(Cpk、Ca、Cp)⏹cC.應客戶的要求,提供給客戶作為質量控制的依據.管制圖與直方圖的區別:⏹1.管制圖控制時間段,直方圖控制時間點.⏹2.管制圖反映的Cpk是動態的Cpk,直方圖反映的Cpk是靜態的Cpk.⏹3.“直方圖是管制圖的基礎,管制圖是直方圖的升華.”八.直方圖:⏹直方圖是將所收集的測定值或數據之全距分為幾個相等的區間作為橫軸,並將各區間內之測定值所出現次數累積而成的面積,用柱子排起來的圖形.製作步驟:⏹ 1.製作次數分配表:A.由全體數據中找到最大值與最小值.如:200個數據中之170和124.B.求出全距(最大值與最小值之差).全距=170-124=46C.決定組數,壹般為10組左右,不宜太少或太多.參照下表進行分組:附表:D.決定組距:組距=全距/組數E.決定各組之上下組界.1.最小壹組的下組界=最小值-測定值之最小位數/22.最小壹組的上組界=下組界+組距=123.5+4=127.5依此類推. F.作次數分配表.(如附表)附表:⏹2.製作直方圖:畫出短形方塊及規格的上限及下限.(如附表)⏹ 1.⏹⏹ 4.⏹A.⏹B.: :⏹5.⏹6.⏹7.⏹1.測知制程能力,作為制程改善依據. 標準差S 愈小愈好,平均值越接近規格中限越好.標準值S=規格中心(u)規格上下限Cp==⏹C.精確度Cpk(制程能力指數):Cpk=(1-Ca)*Cp=或之最小值制程能力指數判定表:⏹ 3.調查是否混入兩個之上不同群體: 兩個不同操作者,兩台不同機器,兩種不同材料,兩條不同生產線者. ⏹ 4.測知有無假數據:有無因測定誤差或檢查錯誤導致之假數據(絕壁型). ⏹ 5.測知分配型態,了解制程有無異常.6.藉以訂定規格界限:如為常態分布,壹般來說,X+45為規格上限,X-45為規格下限.⏹ 7.與規格或標準值比較: A.合乎規格: a.理態型:(附圖) b.壹側無余裕:(附圖)c.d.余裕太多B.a.b.c.⏹8.T 規格容許差 6r6倍標準偏差3a應採取緊急措施,改善品質並追究原因,必要時規格再作檢討.非常不足Sl Su0.67>Cp 5 產品有不良品產生,需作全數遷別,制程有妥善管理及改善之必要.不足 Sl Su 1.00>Cp ≧0.67 4 使制程保持於管制狀態否則產品隨時有發生不良品的危險,需注意. 警告 Sl Su 1.33>Cp ≧1.00 3 理想狀態,繼續維持 合格 Sl Su 1.67>Cp ≧1.33 2 制程能力太好,可酌情縮小規格,或考慮化管理與降低成本.太佳 Sl SuCp ≧1.67 1 處制程能力判斷 分布與規格之關係 Cp NO. ssss s317400 45500 2700 63 0.57 0.00268.26 95.45 99.73 99.9937 99.999943 99.9999998 ±1r ±2r ±3r ±4r ±5r ±6r 百萬分缺點數 百分比(%) ±Kr-6r -5r -4r -3r-2r +6+1r +2r +3r +4r +5r 規格下限 規格上限常態分配(規格中心不偏移) 697700 308700 66810 6210 233 3.4 30.23 69.13 93.32 99.3790 99.97670 99.999660 ±1r ±2r ±3r ±4r ±5r ±6r百萬分缺點數百分比(%)±Kr 下限6r-PPM 制程介紹: ⏹ 1.何謂6r 制程:(零缺陷的質量管理).制程精密度Cp=2.0、制程能力指數Cpk ≧1.5、即:規格範圍為數據分布範圍的2倍. ⏹ 2.以6r 訂為品質缺點的基準理由:于無制程變異情況下(Cp=Cpk=2.0),產生之缺點n 率為0.002PPM(10億分之2).于制程無法消除變異情況下,Cp=2.0,Cpk=1.5產生之缺點n 率為3.4PPM(百万分之3.4).附圖:九.管制圖:⏹“品質管制始於管制圖,終於管制圖”.管制圖,是壹種以實際產品品質特性與根據過去經驗所判明的制程能力的管制界限比較,而以時間順序用圖形表示者.E.最大值與最小值管制圖(L-SChart).⏹2.計數據管制圖:管制圖所依據的數據均屬於以單位計數者.(如缺點數、不良數5月10日2520 15 105 0 77.2 78.2 79.2 80.2 81.2 82.2 83.2 84.2 次數規格下限規格上限xn=100x=80.16(ms)S=1.01(ms)改善前動作時間(ms)-3r -2r -1r +1r +2r +3r等).A.不良率管制圖(PChart).B.不良數管制圖(PnChart).C.缺點數管制圖(CChart).D.單位缺點數管制圖(UChart).管制圖依用途分:⏹ 1.管制用管制圖:用於控制制程之品質,如有點子跑出界限時,立即采取如下措施.A.追查不正常原因.B.迅速消除此原因.C.研究采取防止此項原因重復發生的措施.⏹2.解析用管制圖:A.決定方針用.B.制程解析用.C.制程能力研究用.D.制程管制之準備用.1.管制用管制圖先有管制界限,后有數據. (Processcontrolchart)2.解析用管制圖先有數據,后才有管制界限.(Set-upchart)于計量值管制圖中,X-R管制圖系最常用的壹種,所謂平均值與全距管制圖,系平均值管制圖(XChart)與全距管制圖(RChart)二者合並使用.平均值管制系管制平均值的變化,即分配的集中趨勢變化;全距管制圖則管制變異的程度,即分配的離散程度的狀況.RXX4X3 X2X1 S A M P L ETIME 4/244/21 4/20 4/18 4/17 4/14 4/13 4/124/114/10 4/7 4/6 DATE SAMPLING FREQUENCY:LCLS/S:DIE#:INSPECTOR:CL SPEC: REV: M/C#: UCL PRODUCT UNIT: P/N: PERIOD: R CHARTX CHARTQUALITY CHARACTERISTIC:DESCRIPTION:TYPE: □ SET UP CHART □ PROCESS CONTROL CHARTCHART23.9523.9323.91RCHART 0.050.020.00.‧ ‧ ‧ ‧ ‧ ‧ ‧ ‧ ‧ ‧ ‧ ‧ ‧ ‧ ‧‧ ‧ ‧ ‧ ‧‧ ‧‧ ‧ ‧ ‧ ‧ ‧ ‧ ‧ ‧ ‧ ‧ ‧ ‧ ‧ ‧ ‧ ‧‧‧ ‧ ‧ ‧ ‧ ‧ ‧x-RControlChart 繪制步驟:⏹ 11.Setupchart (解析用管制圖).a.選定管制項目(工標作出規格).b.收集數據(x 1、x 2、x 3、x 4).c.計算各組平均值:x=d.計算極差:R=Xmax-Xmine.計算總平均值:x=f.計算极差平均值:R=g.計算管制界限及繪出x 管制圖:中線CLx=x 上線UCLx=x+A 2R 下線LCLx=x-A 2R R 管制圖 中線CLR=R 上線UCLR=D 4R下線LCLR=D 3R☆A 2、D 4、D 3由系統表查得. h.點圖:將數據點繪管制圖上,相鄰兩點用直線連接. i.管制界限確定.j.將計算出之管制界限確定為“processcontrolchart”(管制用管制圖)之管制界限.⏹ 2.ProcessControlChart:a.繪入Setupchart 之管制界限.b.其余作法與Setupchart 相同.c.管制狀態判讀.d.有異常狀態時,采取措施. f.采取措施后,管制界限重新計算.____ _管制圖界限的計算⏹1.“Setupchart”階段:如繪制管制界限后,發現有點子超界,則視為正常,無須改善.⏹2.“ProcessControlChart”階段:如Cpk壹直于1.5之上,有必要提出建議制工更改管制規格,取消原管制,因Cpk=1.5時,不良率為3.4DPPM.⏹3.不可將規格的上下限直接作為管制界限,將規格的中心值作為管制圖的中心線.管制圖的判讀:滿足下列條件,即可認為制程是于管制狀態:⏹1.多數之點子集中于中心線附近.⏹2.少數之點子落于管制界限附近.⏹3.點之分布呈隨機狀態,無任何規則可循.⏹4.沒有點子超出管制界限之外.非管制狀態:⏹1.點于管制界限的線外(誤判率為0.27%)⏹2.點雖于管制界限內,但呈特殊排列.(見附圖)3.管制圖上的點雖未超出管制界限,但點的出現有下列法時,就判斷有異常原因發生.(a)點于中心線的單側連續出現7點之上時(b)出現的點連續11點中有10點,14點中有12點,17點中14點,20點中16點出現于中心線的單側時(d)出現的點,連續3點中有2點,7點中有3點,10點中有4點出現于管制界限近旁(2δ線外)時(e)出現的點,有周期性變動時(f)3點中有2點于A 區或A 區以外者 (g)5點中有4點于B 區或B 區以外者(h)有8點于中心線之兩側,但C 區並無點子者 (i)連續14點交互著壹升壹降者(j)連續15點于中心線上下兩側之C 區者(k) 有1點在A 區以外者 ⏹ 1.品管開具制程異常聯絡單. ⏹ 2.會簽品工、制工、模修相關人員分析原因及給出對策. ⏹ 3.品管人員將詳細資料寫入<<改善行動記錄>>表中. ⏹ 4.QE 依會簽結論作改善跟蹤. ⏹5.品管重新量測,描點在管制狀態才可繼續生產 FORMULARESULTVERIFICATIONROOTCAUSEDATEX= £ Xi/nR= £ Ri/n UCL x= X+A2RLCL x=X-A2R UCL r=D4RLCLr=D3Rr=R/d2CPK=MIN{(UCL-X)/3r,(X-LCL)/3r}_ =__ _。
品质7大手法-QC7大手法

02
品质7大手法详解
层别法
总结词
将数据按照不同的特性进行分类,并分别统计各类别下的数 据量。
详细描述
层别法是一种将数据按照不同的特性进行分类的方法,通过 对各类别下的数据进行统计和分析,可以更好地了解数据的 分布和特点,从而找出问题的根源和解决方法。
检查表法
总结词
列出所有可能的问题点,并逐一检查 每个问题点是否存在。
详细描述
在品质检测中,检查表法主要用于对产品进 行全面的检测和评估,以确保产品质量符合 要求。通过制定详细的检查表,可以确保检 测过程中不遗漏任何重要环节,并且对产品 进行全面的评估。这种方法有助于发现潜在 的质量问题,并及时采取措施进行纠正和改
进。
柏拉图法在问题解决中的应用
要点一
总结词
要点二
详细描述
详细描述
检查表法是一种通过列出所有可能的 问题点,并逐一检查每个问题点是否 存在的方法。这种方法可以帮助我们 全面地了解问题的情况,并对问题进 行有效的控制和管理。
柏拉图法
总结词
将影响品质的问题按照影响程度进行排序,并找出影响最大的问题。
详细描述
柏拉图法是一种通过将影响品质的问题按照影响程度进行排序,并找出影响最 大的问题的方法。这种方法可以帮助我们优先解决最重要的问题,提高解决问 题的效率。
04
层别法只适用于定量的数据,对于定性数 据可能不太适用。
检查表法的优势与局限性
01
检查表法的优势
02
可以对大量数据进行快速、简单的整理和分析。
可以记录和追溯数据的来源和变化过程。
03
检查表法的优势与局限性
可以对数据进行分类和筛选,便于发现问题和异 常值。
品管七大手法QC7 Tool

24
直方圖-8
❖ 型態、形成原因與對策:
型號 型 別
特徵
作業系 統狀況
1
常態型 中間高、兩 規格、重量
邊低,有集 等計量值的
中的趨勢, 相關特性都
左右幾乎對 處於安定狀
稱
態,製品工
程狀況良
好。
型態
型號 2
型別 雙峰型
特徵 有兩個峰
作業系 統狀況
當抽樣檢查 的樣本是來 自不同機器 或材料時, 便會產生不 同的測量 值。
❖用途說明:
1.檢定兩變數間的相關性。 2.從特性要求尋找最適要因。 3.從要因預估特性水準。
32
散佈圖-2
❖ 成對數據的對應關係
種類 特性/特性 特性/要因 要因/要因
因果關係 結果/結果 結果/原因 原因/原因
例如 身高/體重 水果產量/施肥量 父親身高/母親身高
33
散佈圖-3
❖ 目的:
1.知道兩組數據(或原因與結果)之間是否有相關及相關程度. 2.依據各種可能影響原因層別繪製散佈圖,可找出最適的要因. 3.檢視是否為不相關.
❖ 製作步驟:
1.蒐集相對應數據,至少30組以上,並且整理寫到數據表上. 2.找出數據之中的最大值和最小值. 3.畫出縱軸與橫軸刻度,計算組距. 4.將各組對數據標示在座標上. 5.記錄必要事項.
34
散佈圖-4
❖範例:身高與體重散佈圖
23 43 21 41
39 37
35
33
班 級:208班
人數:30人
導光板外觀不良柏拉圖
不良個數
累積不良率
200
100%
160
不 120 良 數 80
QC_七大手法讲解-品管

專業多媒體音箱制造廠第一章﹕柏拉圖講解何謂柏拉圖﹕1﹑是意大利經濟學家Pareto把國民所得大小分配以圖表表示所制作出來的﹐由Juran引用到品質管理。
2﹑把一堆構成同一結果的東西﹐或把一些構成問題的各個數據﹐按照大小的順序進行排列﹐用棒形圖與累積曲線表示的圖﹐以80﹕20的原理進行重點分析之圖表。
專業多媒體音箱制造廠第一章﹕柏拉圖講解柏拉圖的目的﹕以垂直性的長條表現數據資料中各種問題的發生頻率﹐幫助我們辯認關鍵問題為何。
它能夠以圖表方示提醒你﹐這個圖表讓你找出關鍵的少數問題。
淇譽電子(深圳)有限公司專業多媒體音箱制造廠柏拉圖使用時機﹕1﹑當你要將數據分類統計分析時2﹑當你要排定改進事項的優先順序﹐並設定目標時(不合格優先減少計划)3﹑當你要呈現問題之間的相對重要性時4﹑當你要改善作業品質時第一章﹕柏拉圖講解淇譽電子(深圳)有限公司專業多媒體音箱制造廠柏拉圖的制作步驟﹕1﹑決定數據的分類項目﹐可先從結果著手﹐以找出問題所在﹐然後進行原因分類﹐注意A 類因素不能超過三個﹐否則失去了重點﹐應重新分類。
2﹑選定適當的數據單位。
3﹑決定收集數據的時間范圍。
4﹑在紙上畫出橫軸和縱軸﹐縱軸注明數據單位﹐橫軸標明所收集到的問題。
第一章﹕柏拉圖講解淇譽電子(深圳)有限公司專業多媒體音箱制造廠柏拉圖的制作步驟(續)﹕5﹑畫出每一條塊﹐其寬度是相同的﹐而其高度則決定於它在縱軸上的對數值6﹑在橫軸上標明每一條塊所代表的問題﹐其高度代表發行的次數7﹑將條塊依從高到低遞減排列8﹑在坐標圖的右端另畫出一條縱軸﹐作為累計各項問題所占百分比之用9﹑從左到右依序累計每一塊與其前面條塊合計後所占百分比﹐並在座標圖內標出對應點﹐再將這些點連成一條曲線第一章﹕柏拉圖講解專業多媒體音箱制造廠第二章﹕特性要因圖講解何謂特性要因圖﹕也叫因果圖或叫石川圖﹐是由日本品質管理專家石川將所有影響某一特性的因素或问题原因列出,形成有相互关系的系统图形,并找出最大影响因素。
品管七大手法(QC 7 Tools)

效果 確認
再發 防止
(1)以屬別推移圖等確認效果 (2)在柏拉圖來比較效果 (3)以直方圖確認或比較效果
以推移圖來看標準化從效果是否
能維持
QA Cheng Lin
2
簡介
查檢表 柏拉圖 特性要因圖 散佈圖 管制圖 直方圖 層別法
QC 七大手法為:
用途:
查檢表:易於找到重要要因 柏拉圖:掌握重大問題點 特性要因圖:集思廣義找出問題之要因 散佈圖:找出因果關係 管制圖:從圖表中深入探討製程 直方圖:了解製程之中心與變異 層別法:迅速了解情報內容
QA Cheng Lin
22
7.製作次數分配表
8.製作直方圖
以橫軸表示測量值的變化,縱軸表示次數,兩軸各取出適當長度標 示上記號,然後將各組組界標示在橫軸上,各組次數的多寡用柱形 畫在格各組距上,柱與柱之間不要有間隔。
QA Cheng Lin
23
四、直方圖判定:
常態分配型:製程良好穩定 缺齒型:製作方式或數據蒐集不對 左右偏:規格值無法取得某數值以下 絕壁型:數據被全檢過或製程被全檢過 雙峰型:樣品來自不同機器或材料 高原型:不同平均值的分配混合在一起 離島型:異常原因混入
三、圖表的種類:
1.解析用圖表 2.計劃用圖表 3.計算用圖表 4.說明用圖表 5.其他用途圖表
QA Cheng Lin
18
四、圖表製作的步驟:
1.要明確製作的目的 2.蒐集數據並加以整理 3.選擇適用的圖表 4.記入相關事項
五、管制圖:
從每日生產的產品線中所測得的零亂數據中,找出經常發生和偶然 發生事故的數據,以便幫助找出問題原因,這就非依靠管制圖不可。
16
QA Cheng Lin
17
- 1、下载文档前请自行甄别文档内容的完整性,平台不提供额外的编辑、内容补充、找答案等附加服务。
- 2、"仅部分预览"的文档,不可在线预览部分如存在完整性等问题,可反馈申请退款(可完整预览的文档不适用该条件!)。
- 3、如文档侵犯您的权益,请联系客服反馈,我们会尽快为您处理(人工客服工作时间:9:00-18:30)。
150-
-80
66.7%
不 100-
-60
17.9%
良
50-
-40
5.1%
6.2%
4.1
产品
D
其它
-20
三、 因果图
因果图:将造成某种结果的众多原因,以系统的方式图解之, 以图的方式表达结构(特性)与原因(要因)之间的关系。
某种结果的形成,必有其原因,应设法利用图解的方法找出原 因来。也称石川图或鱼骨图。
5
5.3
5.6
2
4.1
4.6
5
5.3
5.7
3
4.2
4.6
5
5.3
5.8
4
4.2
4.6
5
5.3
5.9
5
4.2
4.7
5
5.4
5.9
6
4.3
4.7
5
5.4
5.9
7
4.3
4.8
5.1
5.4
5.9
8
4.4
4.8
5.1
5.4
6
9
4.5
4.9
5.2
5.5
6.1
10
4.6
5
5.3
5.5
6.5
计算过程:
1 定出组数 7 组 2 最大值 : 6. 5
1 建立柏拉图须先以层别法建立要求目的之统计表 2 建立柏拉图之目的在于掌握影响全局较大的少数项目 3 要利用因果图针对这些项目形成的原因逐一探讨,
并采取改善对策 4 因果图可以单独使用,也可以连接柏拉图使用。
练习 1
四、 散布图
散布图:是用来表示一组成对的数据之间是否有关联性。这种成对的 数据或许是《特性---要因》,《特性--特性》《要因--要因》的关系。
范例:
某部门将上个月生产的产品作出统计,总不良数414个,其中不 良项目可见以下的层别图
顺序 1 2 3 4 5
合计
产品
A
B C D 其它
占不良总数 累积比率
不良件数
比率 %
%
195
47.1
90
21.7
68.8
65
15.8
84.6
45
10.9
95.5
19
4.5
100
414
100
200-
-100
84.65%
2 记录用查核表用来收集计量和计数资料,通常使用划记法。 其格式如下:
修整项目
尺寸不良
表面斑点
装配不良
电镀不良
其
它
次数
六、直方图
直方图又称柱状图,可将杂乱无章之资料,解析出其规则性。 借者直方图,对于资料中得心值或分布状况可一目了然。
直方图可达到下列目的: 1 评估或查验制程 2 指出采取行动的必要 3 测量矫正行动的效应 4 比较机械绩效 5 比较物料 6 比较供应商
QC 7 工具
培训教材
制作:培训部
目的: 1 掌握 QC 7种工具的应用方法
2 懂得利用QC 7种工具解决生产中的问题
3 树立 “ Q C ” 意识
内容: 一 “ Q C ” 认识
二 “ Q C ” 7 工具
层别法 柏拉图 散点法 查验表 控制图 练习 3
因果图 直方图
练习 1 练习 2
三 “ Q C ” 新7 工具简介
●●
●
●●
生
●●
●
●
● ●
存 ●●
力
品质
度 温 的 油
• •
• •
•••
•
•
• •
•••
油的黏度
负相关
•
•
重 体
•
••
• •
•
• •
•
•
身高
弱正相关
•
度
• • ••
温
•• •
• •
•
•
•
气压
毫不相关
•• •
••
伐 步
•
•
•
•••
• •
温度
弱负相关
散布图的绘制程序如下:
1 收集资料 (至少30组以上) 2 找出数据中的最大值与最小值 3 准备坐标纸,划出纵轴,横轴的刻度,计算组距
“QC”认 识 篇
Q C :质量管理 (Quality Control ), 围绕企业方针目标和现场存
在的问题,以改进质量,降低消耗,提高经济效益和人的 素质为目的,运用的各种理论和方法。
宗旨:调动人的积极性,充分发挥人的无限能力创造尊重人,
充满生气和活力的工作环境改善和提高企业素质。
“QC”7工具篇
通常纵轴表示结果, 横轴表示原因 组距的计算应以数据中的最大值减最小值再除以所设定的组数 4 将各组对应数标示在坐标上 5 须填上资料的收集时间,地点,测定方法,制作者等项目。
五、查核表
简单得查核表,就是背忘录,将要进行查看得工作项目一项一 项地整理出来,然后定期或定时检查。 1、点检用得查核表 此类表在记录时只做 < 有,没有> ,< 好,不好>的记录。 制 作程序如下: a 制作表格,决定记录形式 b 将点检项目列出 c 查核 d 异常事故处理
直方图制作之步骤
1 收集资料,并记录在统计表格内 2 定组数,最大值,最小值并计算全距,组距 3 定组界,决定组的中心点 4 制作直方图 5 填上次数,规格,平均值,数据来源,日期
例题
某型号线路板线宽公差 W = 5 +/- 1mil , 先从生产线上抽取50块
样板,测量数据如下:
1
3.8
4.6
使用要以层别法的项目别(现象别)为前提,依照顺序调整过后的统 计表才能画制成柏拉图。
柏拉图分析步骤
1 将要处理的事,以状况(现象)或原因加以层别 2 纵轴可以表示件数或百分比,但最好以金额表示
比较强烈 3 决定收集资料的期间,自何时至何时,作为柏拉
图资料的依据,期间尽可能定期 4 各项目依照合计之大小顺序由左至右排列在横轴上 5 绘制柱状图 6 连接累积曲线
人员
方法
环境
精神不佳 参数偏差 程序问题
含尘量大
上钻不当
资料有误
主轴故障
铝片不平
孔损
异常停机 钻咀崩尖 钻咀质量问题
机器
物料
因果图使用步骤
1 集合有关人员 2 就影响问题,采用脑筋激荡法收集原因。 3 就收集到的原因,判定影响大小。 4 按照影响大小,给原因排出顺序。 5 列出优先处理的原因。
因果图与柏拉图之使用关系
最小值 : 3. 8 全距 : 6. 5 + 3. 8 = 12. 3 组距 : 12. 3 / 7 = 1. 70 3 最小一组的下组界 4 分组 5 作直方图
一、层别法
将多种多样的资料,根据目的的需要,分成不同的类 别,使之方便以后的分析。
A组
B组
C组
员 人
器 机
料 材
法 方
它 其
实例
在某一工序,统计出集中报废坏点所占的百分比如下 :破损 47.1%, 变形 21.7%,刮花 样的5.8%,尺寸不良 10.9%, 其 它4.5%, 加以分类如下:
占不良总数 累积比率
顺序 不良项目 不良件数
比率 %
%
1
破损
195
47.1
2
变形
90
21.7
68.8
3
刮花
65
15.8
84.6
4
尺寸不良
45
10.9
95.5
5
其它
19
4.5
100
总计
414
100
二、柏拉图
在工厂或办公室里,把低效率,缺点,制品不良等损失按 其原因别或现象别换算成损失金额来表示,把金额大小按 顺序排列,对占总金额80%以上的项目加以追究处理,这 就是所谓的柏拉图 ( Pareto ).