现场改善经典培训讲义共44页文档
合集下载
现场管理及改善实用培训(ppt 45页)

第二部分:现场应完成的任务
一、现场的任务
1.生产的完成
完成生产任务意味着即要确保安全,又要全数保证下一道工序所提出的质量要求, 还要只在必要的时候加工必要的东西 .也就是说采用标准化的Q、D、C方法,完 成按企业盈利要求所制定的工作计划,就是现场所承担的最重要的任务 每个工序都“不制造不合格品,不向下一道工序流送不合格品”。为了实现这一 目的,就必须以标准为中心进行全方位管理,抑制人、物、设备、方法的散乱现 象,并且在发生不合格品的各个工序中,形成一种从发现到采取对策为止的最为 合适的良性循环状态。
发生不合适情况 寻找原因
防止再发生
P
防患于未然
* 发生率
探讨是否加入故障报警 * 再发生性
* 重要程度
探讨故障报警的种类
* 发生条件 * 发生率 * 顺序
D
故障报警的设置
* 实施部门 * 任务的分担
C
确认
* 验证 * 评价
A
维护管理
* 检修 * 方法
* 水平展开
应有的模式:全数保证后序工序所需的质量 原则Ⅰ…不制造不合格品 原则Ⅱ 标准操作的贯彻
(2) 标准化为何有必要
一、管理的基础
(3) 标准化的操作方法
工作的标准化一般按以下顺序进行 制定生产活动基本的标准 使制定的标准得到完全遵守的维护管理活动 问题的表面化及反馈活动 为进行更加高效地生产所做的改革活动
一、管理的基础
2. PDCA 周期的运转方式 (1) 管理周期的四个步骤 (2) 掌握事实的要点
* 通过对人、物、设备、方法的要素系列的倾向管理,来维护管理工序的能力, 使PDCA处于良性循环状态。
应有的模式:全数保证后序工序所需的质量 原则Ⅰ…不制造不合格品 原则Ⅱ 增加故障报警
生产车间现场管理培训课件(PPT 44页)
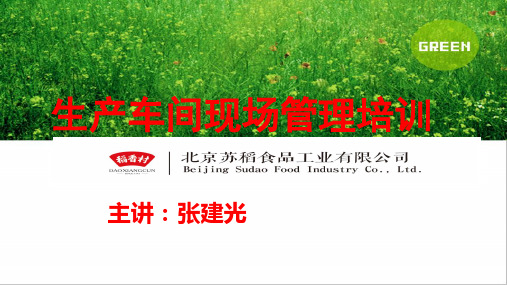
● PDCA循环法 (戴明环)
A
P
C
D
P(Plan) ——计划阶段 D(Do) ——执行阶段 C(Check)——检查阶段 A(Action)——处理阶段
三、生产现场的质量控制
1、在全面质量管理中使用PDCA循环法
阶段
步
骤
P 1、分析现状,找出问题 2、找出产生问题的原因或影响因素 3、找出原因中的主要原因 4、针对主要原因,制定解决问题的方案
一、优秀现场管理的标准和要求
一、优秀现场管理的标准和要求
3、现场管理六要素(5M1E分析法)
现场管理的六个要素即:人、机、料、法、环、测。 ----也称为5M1E分析法。
1) 人(Man):操作者对质量的认识、技术、身体状况等; 2) 机器(Machine):设备、测量仪器的精度和维护保养状况等; 3) 材料(Material):材料能否达到要求的性能等; 4) 方法(Method):生产工艺、设备选择、操作规程等; 5) 测量(Measurement):测量时采取的方法是否标准、正确; 6) 环境(Environment):工作现场的技术要求和清洁条件等; 由于这五个因素的英文名称的第一个字母是M和E,简称为5M1E。
D 5、按制定的计划认真执行 C 6、检查措施执行的效果 A 7、巩固提高,总结成功经验
8、把未解决或新出现的问题转入下一循环
主要方法和内容
调查表、分层法、排列图 因果图 排列图、相关图等 预期达到的目的(What) 在哪里执行措施(Where) 由谁来执行(Who) 何时开始和完成(When) 如何执行(How)
高企业经济效益。
二、现场管理的基本方法
(二)、作业标准化
3、标准的制定要求: 1)、目标指向:即遵循标准总是能保持生产出相同品
A
P
C
D
P(Plan) ——计划阶段 D(Do) ——执行阶段 C(Check)——检查阶段 A(Action)——处理阶段
三、生产现场的质量控制
1、在全面质量管理中使用PDCA循环法
阶段
步
骤
P 1、分析现状,找出问题 2、找出产生问题的原因或影响因素 3、找出原因中的主要原因 4、针对主要原因,制定解决问题的方案
一、优秀现场管理的标准和要求
一、优秀现场管理的标准和要求
3、现场管理六要素(5M1E分析法)
现场管理的六个要素即:人、机、料、法、环、测。 ----也称为5M1E分析法。
1) 人(Man):操作者对质量的认识、技术、身体状况等; 2) 机器(Machine):设备、测量仪器的精度和维护保养状况等; 3) 材料(Material):材料能否达到要求的性能等; 4) 方法(Method):生产工艺、设备选择、操作规程等; 5) 测量(Measurement):测量时采取的方法是否标准、正确; 6) 环境(Environment):工作现场的技术要求和清洁条件等; 由于这五个因素的英文名称的第一个字母是M和E,简称为5M1E。
D 5、按制定的计划认真执行 C 6、检查措施执行的效果 A 7、巩固提高,总结成功经验
8、把未解决或新出现的问题转入下一循环
主要方法和内容
调查表、分层法、排列图 因果图 排列图、相关图等 预期达到的目的(What) 在哪里执行措施(Where) 由谁来执行(Who) 何时开始和完成(When) 如何执行(How)
高企业经济效益。
二、现场管理的基本方法
(二)、作业标准化
3、标准的制定要求: 1)、目标指向:即遵循标准总是能保持生产出相同品
现场工作改善培训讲义精品文档40页

发现偏差
管理标准
训
AP
CD
控制记录
作业实施
OK
改善的意识
一。 现场,现物,现实的意识 现场意识,就是把现场看作问题发生的根
源,管理水平提升的基石。 现物意识,就是认为现场的问题往往有行
有据,哪里发生了问题,对什 麽造成了影响,都应加以明确。 现实意识,就是摈弃完全凭经验和感觉, 工作中注重数据和事实。
2。 管理与改善的理念 管理与改善的理念是指对发生的变异,
可以采取发现并纠正异常,使之稳定于 规格范围的管理,也可以采取缩小变异, 消除异常原因的改善。
工业工程的改善理念
工业工程(IE)的改善理念中, 最重要 的概念是“浪费”。 这里的浪费是广义 的,根据能力的利用程度,浪费可分为:
勉强:超过能力界限的超负荷状态。 浪费:负荷不足的不饱和状态。 不均:在超负荷不饱和之间波动的状态。
每次花很长时间调机, 转换浪费,不良浪费 材料也用了不少。
工厂生产中的“七大浪费”
A. 等待的浪费; B. 搬运的浪费; C. 不良品的浪费; D. 动作的浪费; E. 加工的浪费; F. 库存的浪费; G. 制造过多(早)的浪费;
等待的浪费
观察机器 等待材料 机器故障 质量检验 生产不均衡
搬运的浪费
B。设备 ( Machine ) 1)设备能力足够吗? 3)是否正确润滑了? 5)是否经常出故障? 7)设备布置正确吗? 9)设备数量够吗?
2)工作效率如何? 4)责任心怎样? 6)有足够经验吗? 8)有改进意识吗? 10)身体健康吗?
2)能按工艺要求加工吗? 4)保养情况如何? 6)工作准确度如何? 8)噪音如何? 10)运转是否正常?
改善的意识
问题,方法,协调意识 问题意识,就是以挑剔的眼光来看待现场
管理标准
训
AP
CD
控制记录
作业实施
OK
改善的意识
一。 现场,现物,现实的意识 现场意识,就是把现场看作问题发生的根
源,管理水平提升的基石。 现物意识,就是认为现场的问题往往有行
有据,哪里发生了问题,对什 麽造成了影响,都应加以明确。 现实意识,就是摈弃完全凭经验和感觉, 工作中注重数据和事实。
2。 管理与改善的理念 管理与改善的理念是指对发生的变异,
可以采取发现并纠正异常,使之稳定于 规格范围的管理,也可以采取缩小变异, 消除异常原因的改善。
工业工程的改善理念
工业工程(IE)的改善理念中, 最重要 的概念是“浪费”。 这里的浪费是广义 的,根据能力的利用程度,浪费可分为:
勉强:超过能力界限的超负荷状态。 浪费:负荷不足的不饱和状态。 不均:在超负荷不饱和之间波动的状态。
每次花很长时间调机, 转换浪费,不良浪费 材料也用了不少。
工厂生产中的“七大浪费”
A. 等待的浪费; B. 搬运的浪费; C. 不良品的浪费; D. 动作的浪费; E. 加工的浪费; F. 库存的浪费; G. 制造过多(早)的浪费;
等待的浪费
观察机器 等待材料 机器故障 质量检验 生产不均衡
搬运的浪费
B。设备 ( Machine ) 1)设备能力足够吗? 3)是否正确润滑了? 5)是否经常出故障? 7)设备布置正确吗? 9)设备数量够吗?
2)工作效率如何? 4)责任心怎样? 6)有足够经验吗? 8)有改进意识吗? 10)身体健康吗?
2)能按工艺要求加工吗? 4)保养情况如何? 6)工作准确度如何? 8)噪音如何? 10)运转是否正常?
改善的意识
问题,方法,协调意识 问题意识,就是以挑剔的眼光来看待现场
现场改善经典培训讲义
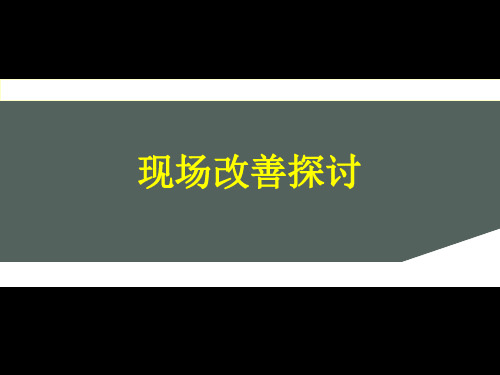
17
现场问题的发掘
机器的因素
机器的维护保养是否到位? 机器的维护保养是否到位? 机器参数是否设定正确? 机器参数是否设定正确? 机器是否有安全防护? 机器是否有安全防护? 模具是否有定期维护及生产前验证? 模具是否有定期维护及生产前验证? 夹具工装是否可以改进? 夹具工装是否可以改进? 有没有考虑防呆工装? 有没有考虑防呆工装?
19
现场问题的发掘
方法的因素
加工方法是否依照工艺书? 加工方法是否依照工艺书? 生产工序是否有改进空间? 生产工序是否有改进空间? 是否制定了明确的检验标准? 是否制定了明确的检验标准? 运输及包装是否存在问题? 运输及包装是否存在问题? 工人的加工动作是否可以简化? 工人的加工动作是否可以简化? 存储方式是否正确? 存储方式是否正确?
5
现场改善的定义
“改”与“善”:
“改”是指在现有的基础之上以最低的成本投入, 是指在现有的基础之上以最低的成本投入, 对现状进行的改进。 对现状进行的改进。 “善”是指不断地完善工作,包括了“没有最好 是指不断地完善工作,包括了“ 只有更好”的持续创新的作业意识。 只有更好”的持续创新的作业意识。
“鸡冠法” 又名“醍醐灌顶法” 鸡冠法” 又名“醍醐灌顶法”
不能再简化点吗? 不能再简化点吗?
Crest?
对现状能有所改变吗? 对现状能有所改变吗?
25
现场的改善
改善的出发点: 改善的出发点: 的出发点
进一步推动5S 进一步推动 进一步减少浪费 创建流水式生产模式 七种浪费
1.生产过剩的浪费 生产过剩的浪费 2.窝工浪费 窝工浪费 3.搬运浪费 搬运浪费 4.加工本身的浪费 加工本身的浪费 窝工:因安排不当 工作人员无事做 窝工:因安排不当,工作人员无事做 或不能发挥作用. 本来3天的工作 天的工作,5天 或不能发挥作用 本来 天的工作 天 就是窝工2天 才完成 就是窝工 天. 5.库存浪费 库存浪费 6.动作浪费 动作浪费 7.生产次品的浪费 生产次品的浪费
现场改善的培训

踢/换 培訓/推
不知
引导/沟通
利用不同的方法/手段,达到目的
思想篇
改善
改善的经历
3)合作
1)怀疑
2)了解
負面對抗
正面對抗
改善 改善
----是须要有勇气否定現狀
思想篇
改善须要我们----1)勇气
2)吸收 3)抛弃 4)创新
思想篇
放大问题
思想篇
不可能,不可能……
改 变
第一步,第二步……
持续改善
思想篇
技能篇
5Why
1) 1Why~4Why是原因 2) 第5个Why才是真因
解决问题的根本方法
技能篇 7种方法
开发创意。大但提出你的任何方案
老板 满意
演讲完毕,谢谢观看!
思想篇 目标
5 4 3 2 1
現狀
1)主动 完成的
過程
转变----1)主动
2)被动
2)被逼 达成的
時間
思想篇
• 什么是转变?------- 转变就是改变现状
• 最坏的转变,不是不变,而是变得更坏
– 不进则退 – 进退两难 – 往后的一成不变
• 所以我们须要的是
正面改善
负面改善
思想篇
不愿意 不能
现场改善系列培训 ---基层管理
课程内容
1) 前言 2) 现场改善理念 3) 认识浪费 4) 改善的基本原则 5) 改善的基本方法
思想篇
?
改喜 改善
放大
5Why
动手
成就感
1)---动手 2)---变化
思想篇
变化
1)等变化 2)创造变化
思想篇
思维
是什么?
态度
精益生产现场改善PPT培训讲义

步步为营
供应链
价值流
制程分析
5S
改善不是一步登天
三 现场改善的实施步骤
实施 步骤
现场改善的实施步骤
1观测 2分析,BF&AF表单填写 3改善 4改善效果追踪 5标准工时与作业指导书的修订
到现场去
◆现场观测 ◆数据分析(收集相关基础数据,工时, 不良率) ◆问题汇总 ◆方案分析,制定计划 ◆方案执行 ◆ 效果验证,标准化
加工
检验
搬运
成
品
搬运
销售
去掉时间浪费,缩短生产周期
维修
均时,就需要对这些工序进行调整和合并。
提高流程的效率,改善平面布置图
重排(Rearrange):重组也称为替换。
十适合工大序步订分单析骤,的大一一批般量顺,生序产展。 开预备调查,使问题明确化。
研-同究一牵步工涉序到骤有几多个二人不作同,业工时作分,站分或解别地测点工取之作流程业动时关。间系。,藉将以找工出改程善的内地方容. 按要素项目进行分解。
,从而有效地消除重复现象。当工序之间的生产能力不平衡,出现人浮于事和忙闲不 均时,就需要对这些工序进行调整和合并。
重排(Rearrange):重组也称为替换。就是通过改变工作程序,使工作的先
后顺序重新组合,以达到改善工作的目的。例如,前后工序的对换、手的动作改换为 脚的动作、生产现场机器设备位置的调整等。
精益生产现场改善
二 现场改善的基本原则
LR
1.抛弃固有的传统观念 2.思考如何做,而不是为何不能做 3.不找借口,从否定现有的做法开始 4.不求完美,马上去做 5.立即改正错误 6.从不花钱的项目开始改善 7.遇难而进,凡事总有办法 8.问5次”为什么?”,找出根本原因 9.众人拾柴火焰高
现场改善手法培训共53页文档

☆ 动作单元力最少 ☆ 动作距离最短 ☆ 动作轻松、容易
22
(3)三角形原理
作业点
手持工具
小零件
作业过程中,作业点、
工具和零部件三个位置构
成三角形关系。此三角形
越小,作业效率越高。
23
7、IE之线平衡分析与瓶颈改善
线平衡
线平衡是对生产线的全部工序进行负荷分析,通过调 整工序间的负荷分配使之达到能力平衡,最终提高生产线的 整体效率。这种改善工序间能力平衡的方法又称为瓶颈改善。
标准 化
变化
事故
NG OK 改善
确认
问题 发现
原因 分析
设计 实验
确定 对策
4
实验设计
有目的、计划地在某种条件下进行实 验,从而获得能预测某种现象的统计资料, 并通过分析实验结果,从该现象中归纳出 普遍性及再现性规律的改善方法。
例如:在设计治具之前,很多想法不知道是否能实现, 这时候就要进行实验来预测。而试验是通过试作进行检验 要注意“实验”和“试验”区分
常见的加工浪费:
☆ 加工余量
☆ 过高的精度
☆ 不必要的加工
过剩加工造成的浪费:
☆ 设备折旧
☆ 人工损失
☆ 辅助材料损失
☆ 能源消耗
18
库存 库存造成额外成本 浪费
库存的危害:
常见的库存:
☆ 额外的搬运储存成本
☆ 原材料、零部件
☆ 造成空间浪费
☆ 半成品
☆ 资金占用(利息及回报损失)
☆ 成品
☆ 物料价值衰减
线平衡分析及瓶颈改善的主要目的是: ☆ 提高人员及设备的生产效率
☆ 减少产品的工时消耗,降低成本 ☆ 减少在制品,降低在库 ☆ 实现单元化生产,提高生产系统的弹性
22
(3)三角形原理
作业点
手持工具
小零件
作业过程中,作业点、
工具和零部件三个位置构
成三角形关系。此三角形
越小,作业效率越高。
23
7、IE之线平衡分析与瓶颈改善
线平衡
线平衡是对生产线的全部工序进行负荷分析,通过调 整工序间的负荷分配使之达到能力平衡,最终提高生产线的 整体效率。这种改善工序间能力平衡的方法又称为瓶颈改善。
标准 化
变化
事故
NG OK 改善
确认
问题 发现
原因 分析
设计 实验
确定 对策
4
实验设计
有目的、计划地在某种条件下进行实 验,从而获得能预测某种现象的统计资料, 并通过分析实验结果,从该现象中归纳出 普遍性及再现性规律的改善方法。
例如:在设计治具之前,很多想法不知道是否能实现, 这时候就要进行实验来预测。而试验是通过试作进行检验 要注意“实验”和“试验”区分
常见的加工浪费:
☆ 加工余量
☆ 过高的精度
☆ 不必要的加工
过剩加工造成的浪费:
☆ 设备折旧
☆ 人工损失
☆ 辅助材料损失
☆ 能源消耗
18
库存 库存造成额外成本 浪费
库存的危害:
常见的库存:
☆ 额外的搬运储存成本
☆ 原材料、零部件
☆ 造成空间浪费
☆ 半成品
☆ 资金占用(利息及回报损失)
☆ 成品
☆ 物料价值衰减
线平衡分析及瓶颈改善的主要目的是: ☆ 提高人员及设备的生产效率
☆ 减少产品的工时消耗,降低成本 ☆ 减少在制品,降低在库 ☆ 实现单元化生产,提高生产系统的弹性
相关主题