环式焙烧炉技术进展
环式焙烧炉

环式焙烧炉 (ring type baking furnace)国内外碳素焙烧炉发展状况环视焙烧炉是生产碳素制品最关键的大型热工炉窑设备,对一个预焙阳极生产厂而言,环式焙烧炉的基建投资占整个碳素厂总投资的50%~60%,而且焙烧炉设计及技术的先进性对产品的质量单位投资的产能、能耗及能源综合利用、炉子寿命、产品生产成本都有很大的影响,焙烧炉火道墙结构的设计,材质的选择和施工工艺是设计焙烧炉最关键的技术。
碳素生产企业环式焙烧炉火道墙采用砖砌结构,由轻质耐火砖、粘土耐火砖、异型耐火砖砌筑而成。
根据焙烧炉火道墙尺寸的不同,每条火道墙重约7~9吨,砖层多打40层。
在生产过程中,依照工艺要求反复地升降温(1250℃~1300℃),降温(20℃~30℃),每次装、出炉时,天车夹具、碳素产品都不可避免地会碰撞到火道墙上,这样火道墙就会发生变形,变形达到一定程度,就必须拆除重砌。
火道墙主要损坏形式:传统工艺采用耐火砖加耐火泥浆砌筑,采用了卧缝打灰、立缝不打灰的砌筑工艺,这样会出现砖缝泥浆脱落,影响了火道墙的整体结构强度。
由于砌砖更多的注重了火道墙的牢固性,但忽视了火焰的流向,不可避免地出现温度死角,对产品的均匀性造成影响。
在生产过程中由于产生不均匀热膨胀以及频繁升降温和装出焙烧品的撞击,造成火道墙变形,继而火焰不走正道→温度死角→温差变大→炉箱变形等恶性循环,能耗增大,降低炉体寿命,出现频繁中小修。
目前国内碳素焙烧炉的设计是50年代从国外引进的技术,火道墙采用砖砌筑结构,经历了半个世纪,并为大多数碳素厂所采用。
随着生产实践的进一步深入,该技术的一些技术问题也逐渐暴露出来。
(1)边火道墙向外突出或整体倾斜,使料箱变窄,装出炉困难;(2)中间火道向内外凹陷,使火道变窄,影响热流气体的流动和燃烧效果;(3)火道墙裂缝严重,导致漏风漏料,影响产品质量,增大热能损耗,破损比较严重的火道墙必须进行中修、大修,由于火道墙是由小块耐火砖砌筑而成,拆除一条火道墙大约需要7~8小时,重新砌筑需24小时左右,拆除并重砌一条火道墙就必须搬运近17吨的材料,这不仅给修炉工作带来困难,而且给车间的正常生产增加难度。
环式焙烧炉讲解

furnace) baking (ring type 环式焙烧炉国内外碳素焙烧炉发展状况环视焙烧炉是生产碳素制品最关键的大型热工炉窑设备,对一个预焙阳极生产厂而言,环式焙烧炉的基建投资占整个碳素厂总投资的50%~60%,而且焙烧炉设计及技术的先进性对产品的质量单位投资的产能、能耗及能源综合利用、炉子寿命、产品生产成本都有很大的影响,焙烧炉火道墙结构的设计,材质的选择和施工工艺是设计焙烧炉最关键的技术。
碳素生产企业环式焙烧炉火道墙采用砖砌结构,由轻质耐火砖、粘土耐火砖、异型耐火砖砌筑而成。
根据焙烧炉火道墙尺寸的不同,每条火道墙重约7~9吨,砖层多打40层。
在生产过程中,依照工艺要求反复地升降温(1250℃~1300℃),降温(20℃~30℃),每次装、出炉时,天车夹具、碳素产品都不可避免地会碰撞到火道墙上,这样火道墙就会发生变形,变形达到一定程度,就必须拆除重砌。
火道墙主要损坏形式:传统工艺采用耐火砖加耐火泥浆砌筑,采用了卧缝打灰、立缝不打灰的砌筑工艺,这样会出现砖缝泥浆脱落,影响了火道墙的整体结构强度。
由于砌砖更多的注重了火道墙的牢固性,但忽视了火焰的流向,不可避免地出现温度死角,对产品的均匀性造成影响。
在生产过程中由于产生不均匀热膨胀以及频繁升降温和装出焙烧品的撞击,造成火道墙变形,继而火焰不走正道→温度死角→温差变大→炉箱变形等恶性循环,能耗增大,降低炉体寿命,出现频繁中小修。
目前国内碳素焙烧炉的设计是50年代从国外引进的技术,火道墙采用砖砌筑结构,经历了半个世纪,并为大多数碳素厂所采用。
随着生产实践的进一步深入,该技术的一些技术问题也逐渐暴露出来。
(1)边火道墙向外突出或整体倾斜,使料箱变窄,装出炉困难;(2)中间火道向内外凹陷,使火道变窄,影响热流气体的流动和燃烧效果;(3)火道墙裂缝严重,导致漏风漏料,影响产品质量,增大热能损耗,破损比较严重的火道墙必须进行中修、大修,由于火道墙是由小块耐火砖砌筑而成,拆除一条火道墙大约需要7~8小时,重新砌筑需24小时左右,拆除并重砌一条火道墙就必须搬运近17吨的材料,这不仅给修炉工作带来困难,而且给车间的正常生产增加难度。
(word完整版)环式焙烧炉

环式焙烧炉 (ring type baking furnace)国内外碳素焙烧炉发展状况环视焙烧炉是生产碳素制品最关键的大型热工炉窑设备,对一个预焙阳极生产厂而言,环式焙烧炉的基建投资占整个碳素厂总投资的50%~60%,而且焙烧炉设计及技术的先进性对产品的质量单位投资的产能、能耗及能源综合利用、炉子寿命、产品生产成本都有很大的影响,焙烧炉火道墙结构的设计,材质的选择和施工工艺是设计焙烧炉最关键的技术。
碳素生产企业环式焙烧炉火道墙采用砖砌结构,由轻质耐火砖、粘土耐火砖、异型耐火砖砌筑而成.根据焙烧炉火道墙尺寸的不同,每条火道墙重约7~9吨,砖层多打40层。
在生产过程中,依照工艺要求反复地升降温(1250℃~1300℃),降温(20℃~30℃),每次装、出炉时,天车夹具、碳素产品都不可避免地会碰撞到火道墙上,这样火道墙就会发生变形,变形达到一定程度,就必须拆除重砌。
火道墙主要损坏形式:传统工艺采用耐火砖加耐火泥浆砌筑,采用了卧缝打灰、立缝不打灰的砌筑工艺,这样会出现砖缝泥浆脱落,影响了火道墙的整体结构强度。
由于砌砖更多的注重了火道墙的牢固性,但忽视了火焰的流向,不可避免地出现温度死角,对产品的均匀性造成影响。
在生产过程中由于产生不均匀热膨胀以及频繁升降温和装出焙烧品的撞击,造成火道墙变形,继而火焰不走正道→温度死角→温差变大→炉箱变形等恶性循环,能耗增大,降低炉体寿命,出现频繁中小修。
目前国内碳素焙烧炉的设计是50年代从国外引进的技术,火道墙采用砖砌筑结构,经历了半个世纪,并为大多数碳素厂所采用。
随着生产实践的进一步深入,该技术的一些技术问题也逐渐暴露出来。
(1)边火道墙向外突出或整体倾斜,使料箱变窄,装出炉困难;(2)中间火道向内外凹陷,使火道变窄,影响热流气体的流动和燃烧效果;(3)火道墙裂缝严重,导致漏风漏料,影响产品质量,增大热能损耗,破损比较严重的火道墙必须进行中修、大修,由于火道墙是由小块耐火砖砌筑而成,拆除一条火道墙大约需要7~8小时,重新砌筑需24小时左右,拆除并重砌一条火道墙就必须搬运近17吨的材料,这不仅给修炉工作带来困难,而且给车间的正常生产增加难度。
多孔环式炭素焙烧炉砌筑施工工法

多孔环式炭素焙烧炉砌筑施工工法多孔环式炭素焙烧炉砌筑施工工法一、前言多孔环式炭素焙烧炉砌筑施工工法是指在建造炭素焙烧炉时所采用的一种施工方法。
这种施工工法具有许多特点,适用范围广泛,能够确保施工质量,同时也需要注意安全措施。
本文将详细介绍多孔环式炭素焙烧炉砌筑施工工法的工艺原理、施工工艺、劳动组织、机具设备、质量控制、安全措施、经济技术分析等内容,并附上一个工程实例。
二、工法特点多孔环式炭素焙烧炉砌筑施工工法的特点如下:1. 炭素焙烧炉采用多孔环式结构,能够提高炉内物料的利用率和烧结效果。
2. 工法施工简单,操作方便,能够提高施工效率和质量。
3. 多孔环式炭素焙烧炉砌筑具有较好的耐火性能和导热性能,能够保证炉体使用寿命和热效率。
4. 炭素焙烧炉采用多孔环式结构,能够方便进行炉内物料的装卸和烧结过程的控制。
5. 工法具有良好的环保效果,能够减少对环境的污染和资源的浪费。
三、适应范围多孔环式炭素焙烧炉砌筑施工工法适用于以下范围:1. 钢铁工业:可用于炼铁、钢铁冶炼等工艺中的焙烧炉建造。
2. 碳素工业:可用于炭素制品生产中的炼焦、煅烧等过程中的炭素焙烧炉建设。
3. 化工工业:可用于化工生产中的石油焙烧等工艺过程中的焙烧炉建造。
4. 粉末冶金工业:可用于粉末冶金中的烧结炉建设。
四、工艺原理:多孔环式炭素焙烧炉砌筑施工工法的核心在于利用多孔环式结构提高炉内物料的利用率和烧结效果。
其工艺原理主要有以下几点:1. 通过设定合理的炉体结构和烟道布置,保证炉内物料在焙烧过程中得到充分的接触和反应。
2. 通过选择适当的耐火材料和炉体材料,提高炉内物料的热传导性和耐高温性能。
3. 通过控制炉内温度、气氛和气流,实现物料的热解、烧结和冶炼等过程。
五、施工工艺多孔环式炭素焙烧炉砌筑施工工法的施工工艺包括以下几个阶段:1. 基础施工:包括基础开挖、基础搅拌、基础浇筑等工序。
2. 砌筑施工:包括炉壁砌筑、炉顶砌筑、烟道砌筑等工序。
一种环式焙烧炉的烘炉方法

多孔环式焙烧炉施工工艺

表2 回填 陆域边坡抗滑稳定计算成果表
量的测点作为永久监测点 。 [ 4 ] 王 强. 塑料排 水预压 法加 固软基机 理及 沉降计 算方 法研
4 . 2
水 平 位 移 监 测
究[ D] . 南京 : 河海大学硕 士论 文, 2 0 0 1 .
5 ] 邓礼久 , 金 亮星 , 罗嘉金 . 塑料排 水堆栽预 压 法处理软基 的 在 回填土过程 中设置水平位移 观测 点进行监 测 , 回填至高程 [ 固结效果[ J ] . 铁道科 学与工程 学报 , 2 0 1 3 , l O ( 3 ) : 6 9 - 7 3 . 1 2 . 0 m 可按 2 4 h水平位移大 于 1 0 mm作为停止加载控制标准 ; 后 6 ] 黎 玉, 王齐福 . 塑料排 水板堆栽预 压法软基加 固监测分析 期 回填时以 2 4 h的水平位 移大于 5 m m作为 停止加 载控制标 准。 [ 填筑速率应 以水平位移控制为主 , 如超过此限应立即停止填筑。
实, 并 向湖 区方 向设 置 0 . 5 %的排水坡 面 。回填 速度 根据要 求进
工程 区场地起伏较 大 , 土层分 布变化 也 比较大 , 软 基分 布不 行控制 , 在 回填 过程 中对 侧 向变形进 行观 测 , 一 旦发 现侧 向变形 均匀 , 为节省工程投 资并确保 工程 的安全 性 , 首 先要 确定 软基 的 过大 , 则要减小加载 速度 或停 止加载 , 休止一段时间后再回填。 分布范围 , 有针对性 的采用 不同 的地基处 理方法 , 并 在施 工期及
多孔环式炭素焙烧炉砌筑
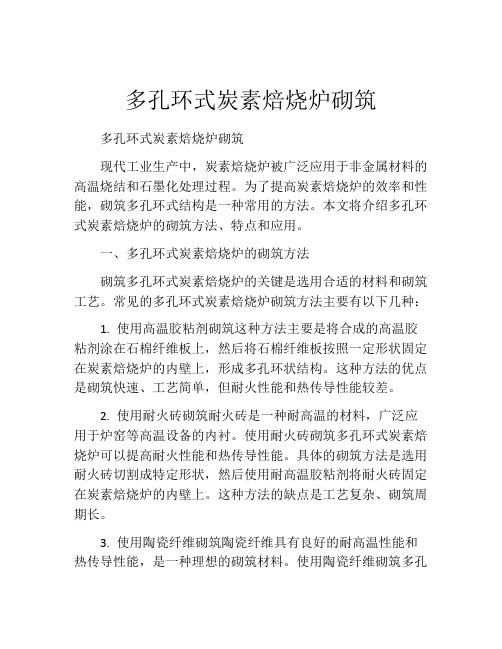
多孔环式炭素焙烧炉砌筑多孔环式炭素焙烧炉砌筑现代工业生产中,炭素焙烧炉被广泛应用于非金属材料的高温烧结和石墨化处理过程。
为了提高炭素焙烧炉的效率和性能,砌筑多孔环式结构是一种常用的方法。
本文将介绍多孔环式炭素焙烧炉的砌筑方法、特点和应用。
一、多孔环式炭素焙烧炉的砌筑方法砌筑多孔环式炭素焙烧炉的关键是选用合适的材料和砌筑工艺。
常见的多孔环式炭素焙烧炉砌筑方法主要有以下几种:1. 使用高温胶粘剂砌筑这种方法主要是将合成的高温胶粘剂涂在石棉纤维板上,然后将石棉纤维板按照一定形状固定在炭素焙烧炉的内壁上,形成多孔环状结构。
这种方法的优点是砌筑快速、工艺简单,但耐火性能和热传导性能较差。
2. 使用耐火砖砌筑耐火砖是一种耐高温的材料,广泛应用于炉窑等高温设备的内衬。
使用耐火砖砌筑多孔环式炭素焙烧炉可以提高耐火性能和热传导性能。
具体的砌筑方法是选用耐火砖切割成特定形状,然后使用耐高温胶粘剂将耐火砖固定在炭素焙烧炉的内壁上。
这种方法的缺点是工艺复杂、砌筑周期长。
3. 使用陶瓷纤维砌筑陶瓷纤维具有良好的耐高温性能和热传导性能,是一种理想的砌筑材料。
使用陶瓷纤维砌筑多孔环式炭素焙烧炉的方法是将陶瓷纤维按照一定形状固定在炭素焙烧炉的内壁上,然后使用高温胶粘剂进行固定。
这种方法的优点是砌筑周期短、砌筑简单,但陶瓷纤维的耐火性能稍逊于耐火砖。
二、多孔环式炭素焙烧炉的特点多孔环式炭素焙烧炉相比传统的炭素焙烧炉具有以下几个特点:1. 高温均匀多孔环式炭素焙烧炉砌筑多孔结构,可以提供更好的热传导性能,从而使燃烧更加均匀,提高炭素焙烧炉的高温效率。
2. 耐火性能优异多孔环式炭素焙烧炉使用耐火材料进行砌筑,耐高温性能优异,能够承受高温环境下的烧结和石墨化过程,延长炭素焙烧炉的使用寿命。
3. 操作方便多孔环式炭素焙烧炉具有砌筑周期短、操作方便的特点,降低了生产成本,提高了生产效率。
三、多孔环式炭素焙烧炉的应用多孔环式炭素焙烧炉广泛应用于非金属材料的高温烧结和石墨化处理过程。
科技成果——炭素环式焙烧炉燃烧系统优化技术

科技成果——炭素环式焙烧炉燃烧系统优化技术适用范围钢铁行业炭素环式焙烧炉燃烧系统及炉盖节能改造行业现状目前我国大部分炭素企业采用环式炉进行生制品的一次焙烧。
由于燃料由火井上部的煤气入口水平喷入,煤气和炉内产生的沥青烟燃烧不充分,沥青烟产生量大,炉盖漏风,保温性差,能耗高,废气净化难度大。
据统计,目前国内炭素企业的平均焙烧能耗约340kgce/t。
目前该技术可实现节能量7万tce/a,减排约18万tCO2/a。
成果简介1、技术原理该技术采用新型的燃烧器,煤气自上而下进入火井,与自下而上的烟气及助燃空气混合,使燃烧更加充分,提高了燃烧效率;根据炉室温度和升温曲线自动调节煤气流量,使炉子温控更精确,减少燃料浪费;通过使更多的沥青烟参与燃烧,最大限度地节省燃料,减少沥青烟的产生和排放量;通过新型联通罩的自动调节,降低炉室负压,减少烟气量,降低烟气流速,提高传热效率,减少热损失;通过提高炉盖的密闭性和保温效果,减少热损失。
2、关键技术(1)采用先进的煤气燃烧器、可移动式燃烧架和烟气联通罩,通过采集炉室温度和系统压力参数,自动调节煤气用量和烟气量,实现对炉室温度的精确控制,提高煤气及沥青烟的燃烧效率,提高产品(2)通过改变炉盖的部分结构及耐火材料,减轻了炉盖重量、提高保温和密封效果,延长使用寿命。
3、工艺流程炭素环式焙烧炉燃烧系统优化工艺流程图主要技术指标焙烧品单位能耗(包括新增的蒸气及电力消耗)可降低约39%。
技术水平该技术于2010年通过中国炭素行业协会组织的科技成果鉴定,目前已在国内30多台炭素环式焙烧炉上使用,能耗平均下降30%以上,节能效果显著。
典型案例典型用户:中钢集团吉林炭素股份有限公司、河北联冠电极股份典型案例1建设规模:年产1.32万t石墨电极焙烧品的新型炭素焙烧炉,建设条件为煤气热值大于1200kcal/Nm3,煤气中粉尘、焦油含量小于800mg/m3(粉尘、焦油含量为合测值),需蒸汽1t/h。
循环流态化焙烧技术在复杂难处理金矿生态环保中的应用探讨

循环流态化焙烧技术在复杂难处理金矿生态环保中的应用探讨随着人们对环境保护意识的增强和对资源的日益消耗,复杂难处理金矿的生态环保问题备受关注。
循环流态化焙烧技术作为一种环保型的金矿处理技术,具有高效、低污染、节能等优点,在复杂难处理金矿生态环保中正发挥着重要的作用。
本文将就循环流态化焙烧技术在复杂难处理金矿生态环保中的应用进行探讨。
首先,循环流态化焙烧技术可以有效降低废气排放。
在复杂金矿的焙烧过程中,会产生大量的尾气,其中包括二氧化硫等对环境有害的气体。
传统的焙烧技术在处理这些废气时存在着一定的难题,而循环流态化焙烧技术通过合理设计和优化,能够将废气中的有害成分去除,减少对环境的污染。
其次,循环流态化焙烧技术还能实现资源的有效利用。
复杂难处理金矿中含有一些有价值的金属元素,如铜、铅等。
传统的焙烧技术无法很好地进行资源的回收利用,而循环流态化焙烧技术可以通过精细控制操作参数,使金属元素在焙烧过程中得以回收利用,从而减少资源浪费,对环境起到积极的保护作用。
此外,循环流态化焙烧技术还可以降低固体废弃物的排放。
复杂难处理金矿的焙烧过程中会产生大量固体废弃物,包括焦炭、尾矿渣等。
传统的焙烧技术无法对这些固体废弃物进行有效处理,容易导致土壤和水源的污染。
而循环流态化焙烧技术采用闭路循环运行方式,能够对废弃物进行高效处理和回收利用,从而减少固体废弃物的排放量,保护生态环境。
循环流态化焙烧技术的应用还需要克服一些挑战。
首先,技术本身仍存在一定的不足之处,如操作的复杂性、设备的投资成本高等。
因此,在实际应用中需要加强对技术的研发和改进,以提高其运行稳定性和经济性。
其次,金矿的矿石在化学成分和物理性质上差异较大,因此需要针对不同的金矿类型进行技术调整和优化。
此外,还需要加强对焙烧过程中产生的废气、废水等有害物质的处理与排放控制,确保生态环境的安全。
为了更好地推广和应用循环流态化焙烧技术,政府、企业和科研机构需要加强合作,制定相关的技术标准与规范,推动技术的进一步发展。
循环流态化焙烧技术在复杂难处理金矿浸出反应中的应用研究

循环流态化焙烧技术在复杂难处理金矿浸出反应中的应用研究随着人们对金矿资源的开采需求的不断增加,传统的金矿浸出反应面临着一系列的问题,例如浸出效率低、金矿资源回收率低、对环境的污染问题等。
因此,提高金矿浸出反应的效率和资源回收率成为了金矿开采和加工领域的研究热点之一。
在这背景下,循环流态化焙烧技术应运而生,并在复杂难处理金矿浸出反应中取得了令人瞩目的应用研究成果。
循环流态化焙烧技术是一种通过高温氧化还原反应,将金矿中的金属硫化物转化为可溶性的金属氧化物的技术。
该技术基于反应炉内的循环流态化特性,通过恰当的气体氧化还原条件,将金矿中的金属硫化物在短时间内快速氧化,使其转化为溶于浸出溶液中的金属氧化物。
相比传统的金矿浸出反应,循环流态化焙烧技术具有以下优点:首先,循环流态化焙烧技术具有较高的浸出效率。
该技术能够将金属硫化物有效转化为金属氧化物,使得金矿中的金属物质更容易被浸出液所溶解。
与传统浸出反应相比,循环流态化焙烧技术能够显著提高金矿中金属的溶解率,从而实现更高的金属回收率。
其次,循环流态化焙烧技术对环境的影响较小。
该技术的反应过程在密封的环境中进行,使得烟气中的有害污染物减少到最低限度。
此外,通过合理的气体循环设计,可以有效地回收焙烧过程中产生的热量和有用的矿物质,减少资源的浪费。
再次,循环流态化焙烧技术具有较短的反应时间。
该技术能够在短时间内完成金属硫化物的转化,并将金属氧化物溶解入浸出液中。
相比较传统的金矿浸出反应,使用循环流态化焙烧技术可以显著缩短处理时间,提高生产效率。
然而,在复杂难处理金矿浸出反应中应用循环流态化焙烧技术时,仍然面临一些挑战。
首先,金矿样品的复杂性和多样性使得技术的适应性和稳定性成为了一个关键问题。
根据金矿样品的不同特点,需要对循环流态化焙烧技术进行优化和改进,以提高处理效果。
其次,金矿浸出反应中的物质平衡和能量平衡也需要被充分考虑。
通过调整反应条件和提高热能的利用效率,可以实现金属硫化物的高效转化和能量回收。
循环流态化焙烧技术在复杂难处理金矿废弃物综合利用中的应用研究

循环流态化焙烧技术在复杂难处理金矿废弃物综合利用中的应用研究随着中国经济的快速发展和城市化进程的加速,金矿废弃物作为一种重要的固体废弃物已经成为严重的环境问题。
金矿废弃物中含有大量的金属元素,如金、银、铜等,也包含着一定量的有害元素,如重金属、挥发性有机物等。
因此,合理利用金矿废弃物成为了当今金矿开采行业所面临的一项严峻挑战。
循环流态化焙烧技术作为一种高效、低污染的垃圾焚烧技术,在金矿废弃物综合利用中具有广阔的应用前景。
循环流态化焙烧技术是将金矿废弃物投入到焙烧炉中,通过高温反应和氧化还原等过程,实现金属和非金属的分离回收,最大限度地减少废弃物对环境的污染。
首先,循环流态化焙烧技术可以实现金矿废弃物中金属元素的有效回收。
金矿废弃物中的金、银等贵金属元素分布在矿石中,并以粒状物的形式存在。
循环流态化焙烧技术利用高温气体的热传导和物理力学作用,将金属矿石中的金属元素与矿石剥离和分离。
经过焙烧后,金属元素可以通过冷凝和沉积的方式回收,实现了金矿废弃物中有价值的金属元素的资源化利用。
其次,循环流态化焙烧技术能够有效降低金矿废弃物对环境的污染程度。
金矿废弃物中存在着一定量的有害元素,如重金属和挥发性有机物。
这些有害元素一旦进入到环境中,会对土壤、水体和大气造成严重的污染。
循环流态化焙烧技术通过高温处理的方式,将金矿废弃物中的有害元素转化为无害的气体和固体产物。
焙烧后的气体经过处理可以达到排放标准,固体产物可以通过后续的处理措施进行无害化处置。
此外,循环流态化焙烧技术还可以实现金矿废弃物的资源化利用。
金矿废弃物中除了金属元素外,还存在着一定量的非金属矿石和矿渣。
这些非金属矿石和矿渣可以通过焙烧后转化为新材料,例如建筑材料、环保材料等。
通过适当的加工处理,这些新材料可以广泛应用于各个领域,实现金矿废弃物的资源化利用。
综上所述,循环流态化焙烧技术在复杂难处理金矿废弃物综合利用中具有广泛的应用前景。
该技术通过有效回收金属元素、降低环境污染和实现废弃物资源化利用,解决了金矿废弃物带来的环境问题,同时也为金矿开采行业带来了可持续发展的机遇。
循环流态化焙烧技术在复杂难处理金矿环境修复中的应用研究

循环流态化焙烧技术在复杂难处理金矿环境修复中的应用研究随着工业化的快速发展,金矿环境中的污染问题日益凸显,特别是复杂难处理金矿环境中的修复难题更加突出。
为了解决这一问题,循环流态化焙烧技术被广泛应用于金矿环境修复。
本文将对循环流态化焙烧技术在复杂难处理金矿环境修复中的应用进行深入研究,探讨其原理、方法、优势和挑战。
循环流态化焙烧技术是一种通过加热、氧化等化学反应将污染物固化和转化为无害物质的方法。
它基于炉内固体床的循环流动,在高温下通过氧化反应,将有毒有害物质转化为稳定、无害的化合物。
这种焙烧技术具有高效、低成本、无二次污染等优点,因此在复杂难处理金矿环境中得到了广泛应用。
首先,循环流态化焙烧技术可以有效处理金矿环境中的难降解有机污染物。
循环流态化焙烧技术可以在高温下将有机污染物氧化为无毒无害的气体和固体产物,彻底消除了有机污染物对环境的危害。
同时,该技术还可以实现有机废物的资源化利用,降低了环境污染的综合风险。
其次,循环流态化焙烧技术还可以处理金矿环境中的重金属污染。
重金属污染是金矿环境中常见的污染问题,具有较高的毒性和难降解性。
通过循环流态化焙烧技术,可以将重金属化合物转化为稳定的化合物或固体,并在炉内完成固化过程。
这种方法不仅可以减少重金属的迁移和释放风险,还可以实现重金属资源的回收再利用。
此外,循环流态化焙烧技术在处理金矿环境中的气体污染方面也具有显著的优势。
复杂难处理金矿环境中的气体污染主要包括硫化物、氮氧化物等,这些污染物对环境和人体健康都带来了严重的影响。
通过循环流态化焙烧技术,可以将这些气体污染物转化为无害的气体或固体产物,达到净化环境的目的。
然而,循环流态化焙烧技术在复杂难处理金矿环境修复中也面临一些挑战。
首先,焙烧过程中废气处理是一个关键问题,需要选择合适的废气处理方法,以确保排放的废气达到环保标准。
其次,固体床中的矿石成分复杂,需要进行合理设计和控制,以确保焙烧过程的稳定性和高效性。
循环流态化焙烧技术在复杂难处理金矿废弃物处理中的应用

循环流态化焙烧技术在复杂难处理金矿废弃物处理中的应用随着全球金矿的开采数量逐渐增加,对于金矿废弃物处理的需求也越来越迫切。
金矿废弃物通常包含了多种有害物质,如氰化物、重金属等,对环境造成较大威胁。
为了高效、安全地处理金矿废弃物,循环流态化焙烧技术被广泛应用。
该技术通过将金矿废弃物与氧化剂进行高温反应,使有害物质得以分解并转化为相对无害的物质,达到废弃物处理和资源回收的目的。
循环流态化焙烧技术的基本原理是将金矿废弃物与适量的氧化剂(如空气或氧气)在高温环境下进行反应。
在循环流态化设备内,氧化剂和金矿废弃物以气固两相形式进入,并在设备内进行充分的混合与反应。
通过调节温度、气体流速、氧化剂与金矿废弃物的比例等参数,可以实现金矿废弃物的高效处理。
循环流态化焙烧技术在复杂难处理金矿废弃物处理中的应用具有以下几个优势:1. 高效处理能力:循环流态化焙烧技术能够在较短时间内将金矿废弃物中的有害物质进行分解和转化,大大提高了处理效率。
同时,循环流态化设备内的气固两相反应也增加了废弃物与氧化剂的接触面积,从而提高了反应效果。
2. 资源回收:在循环流态化焙烧过程中,金矿废弃物中的有害物质经过反应后,部分可以得到转化为相对无害的物质,而另一部分可以回收利用。
例如,焙烧过程中产生的尾气可以通过适当的处理和净化后续利用,从而实现资源的回收再利用。
3. 低能耗和环境友好性:与传统处理金矿废弃物的方法相比,循环流态化焙烧技术能够以较低的温度和较少的能量消耗实现废弃物的处理。
与此同时,由于循环流态化设备内的反应是在密闭的环境中进行,因此减少了有害物质的释放,对环境造成的污染也较小。
然而,值得注意的是,在应用循环流态化焙烧技术处理复杂难处理金矿废弃物时,仍然存在一些挑战和问题需要解决。
首先,金矿废弃物的成分复杂多样,包含有多种有害物质,使得废弃物的处理和转化难度较大。
针对不同的金矿废弃物,需要进行充分的分析和测试,以确定最合适的处理方案和参数。
环式焙烧炉技术进展

环式焙烧炉技术进展
冯乃祥;姜东涛
【期刊名称】《炭素技术》
【年(卷),期】1994()1
【摘要】环式焙烧炉技术进展冯乃祥,姜东涛(东北大学)1.前言当今世界的冶金炭素工业普遍采用环式焙烧炉生产电极和炭块制品或半制品。
这类焙烧炉一般可分为两种类型:一种是敞开环式焙烧炉(图1);一种是带盖环式焙烧炉(图2)。
采用环式焙烧炉的优点是可以连续性作业,容...
【总页数】7页(P20-26)
【关键词】碳素制品;环式;焙烧炉
【作者】冯乃祥;姜东涛
【作者单位】东北大学
【正文语种】中文
【中图分类】TQ127.11
【相关文献】
1.带盖环式焙烧炉节能技术分析 [J], 高占英
2.论环式炉和车底炉焙烧技术的差异 [J], 谢志群
3.带盖环式焙烧炉与敞开环式焙烧炉应用之比较 [J], 赵杰三;潘三红
4.36室带盖有火井环式焙烧炉最高焙烧温度探讨 [J], 栗兵
5.敞盖环式焙烧炉焙烧铝用阴极炭块的工艺技术探讨 [J], 潘三红;张涛;周朋;米寿杰
因版权原因,仅展示原文概要,查看原文内容请购买。