PCBA摆放拿取作业指导书
【最新推荐】pcb生产作业指导书word版本 (12页)

本文部分内容来自网络整理,本司不为其真实性负责,如有异议或侵权请及时联系,本司将立即删除!== 本文为word格式,下载后可方便编辑和修改! ==pcb生产作业指导书篇一:PCB生产能力作业指导书德信诚培训网PCB生产能力作业指导书1.0目的:提供本厂单双面生产技术能力的检查方法和标准,从而保证生产工具和不品之品质. 2.0应用范围:适用于目前的生产技术能力范围. 3.0责任:通过各种数据反映本厂生产能力范围. 4.0定义:CNC——电脑钻孔 PTH——化学沉铜 SLOT——槽孔 5.0参考文件:无6.0生产能力范围内容:6.1板料6.1.1本公司常备物料 A、玻璃纤维板(FR4)备注说明:1)、以上板料厚度含基铜厚度。
2)、以上板料厚度及公差为IPC-4101ClassB/L等级,如因设计需要其他规格及等级的板料首先查询仓库最新库存有无材料,如没有则通知业务部相关人员。
3)、以上几种板料供应商为KB(建滔)和国际,本厂常用板料尺寸规格为:41″*49″、43″*49″。
篇二:PCB生产能力作业指导书篇三:PCB设计作业指导书D1、目的规范产品的 PCB 工艺设计,规定 PCB 工艺设计的相关参数,使得 PCB 的设计满足电气性能、可生产性、可测试性等要求,在产品设计过程中构建产品的工艺、技术、质量、成本优势。
2、范围本规范适用于所有公司产品的 PCB 设计和修改。
3、定义(无)4、职责4.1 R&D 硬件工程师负责所设计原理图能导入PCB网络表,原理上符合产品设计要求。
4.2 R&D 结构工程师负责所设计PCB结构图符合产品设计要求。
4.3 R&D PCB Layout工程师负责所设计PCB符合产品设计要求。
5、作业办法/流程图(附后)5.1 PCB 板材要求5.1.1 确定 PCB 所选用的板材、板厚等,例如PCB板材:FR-1、FR-4、CEM-1、CEM-3、纸板等,PCB板厚:单面板常用1.6mm ,双面板、多层板常用1.2mm或1.6mm,PCB的板材和厚度由结构和电子工程师共同确定。
2018年pcba维修作业指导书-范文模板 (4页)

本文部分内容来自网络整理,本司不为其真实性负责,如有异议或侵权请及时联系,本司将立即删除!== 本文为word格式,下载后可方便编辑和修改! ==pcba维修作业指导书篇一:维修作业指导书1 目的本作业规范针对维修人员修复不良品过程中焊接及元器件更换的操作指导,有效保证维修质量。
2 适用范围适用于公司生产不良品的整个维修流程。
3.设备和材料电烙铁,热风枪,锡丝,洗板水,防静电刷,离子风机等。
4.作业步骤4.1 维修设备4.1.1 上班前维修员需记录《烙铁头点检表》、《腕带点检表》,确保焊接温度及ESD 防护符合质量要求。
4.1.2 电烙铁焊接温度范围为330℃~390℃,焊接持续时间在3 秒以下。
4.1.3 热风枪的最高温度范围为390℃±30℃,风速控制在6 档(旋钮刻度型)或45 以内(数控显示型)。
4.1.4 离子风机使用请按规范作业。
4.1.5 维修过程中需佩戴静电手环,离位接触产品应佩戴静电手套。
4.2 维修操作规范4.2.1 维修员对不良品进行维修前, 可将产品按测试工位的原则整理/分类后存放于指定区域。
维修时需保持台面整洁,良品及不良品物料应区分标识,维修不良品及维修良品按指定区域放置。
4.2.2 维修员依据最新产品原理图、BOM表,维修WI等对PCBA进行分析/维修,单板功能维修OK后须彻底清洗维修区域及附近组件,测试OK后录入维修模块,跳转首站开始生产。
对于需要更换元器件或焊接的单板,请遵照以下操作规范:4.2.2.1 单板维修OK后生产再次出现的不良品作为返修板修复,同时在维修模块体现维修历史记录,对于第三次产生的返修板(单板第四次不良)须协同技术部分析并记录三次返修板数据,修复后不可投入生产,按照《PCBA报废不良品流程处理》,每一单板允修次数≤3次。
4.2.2.2 维修过程中,同一单板相同器件焊接次数≤4次,每一单板焊接受热次数≤3次,并确保焊接质量。
AOI测试作业指导书

名称
AOI作业指导书
编号
一、目的:
规范AOI测试作业,提升产品品质
二、适用范围:
适用于SMT工序内回流后PCBA自动光学检测。
三、使用工具及辅料:
AOI(自动光学检测设备)、防静电周转架、防静电托盘、红色标识纸。
四、作业顺序:
1.拿起过炉的PCBA板2.目检AOI检测能力较弱元件焊接情况
3.将PCBA板放入测试轨道4.设备自动扫描测试
4..对检测后的图片进行确认,将AOI检查后的良品PCBA放入托盘或转运架,如误报不良很多的情况下通知技术人员进行确认并调试。
5.对PCBA重点检查确认IC、元件错料,对AOI检查出的不良点位或是AOI误判的不良目检人员需进行二次确认。
6.拿放PCBA时必须轻拿轻放,一次只准拿一片,且只能拿板板边,PCBA插入托盘时必须注意板边元件不能与托盘接触,避免撞件;
11.如实将不良项目记录在《SMD焊点自检记录表》中。
12.机器在运行时请勿将头或手伸进机器内,以免人员受损伤。
13.每日下班前都要清洁设备,保持机台清洁,班与班的交接一定把当班存在的问题交接清楚,便于下一班人员跟踪。
旧底图总号
底图总号
设计
1
审核
等级
标记
日期Biblioteka 签名第1页共1页更改标记
数量
更改单号
签名
日期
5.测试完后自动显示测试结果6.良品和不良品区分并做标示
五、作业标准及注意事项:
1.着装要求:穿静电服、鞋,戴静电帽、静电手环。
2.调用相应的程序,并且调整好轨道,进入AOI测试。
3.对HDMI接口,SD卡槽,贴片排针、母座等AOI设备检测能力较弱器件需全部目检是否存在虚焊、连焊、偏移等不良,并需对所有BGA器件目检是否存在底部垫元件问题。
PCBA运输作业规范
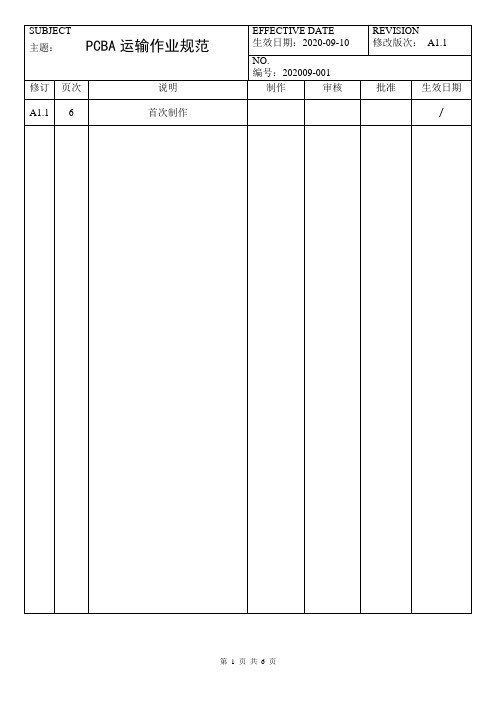
防静电泡棉
编号:202009-001
4.2.1不同层车间运输使用栈板,栈板限高1.4米,每个栈板最多摆放四层,每层摆放四个胶框。
栈板最多摆
放16个胶框
4.2.2同层车间运输使用滑板,滑板限高1.4米,每个滑板最多摆放四层,每层摆放一个胶框。
滑板最多摆
放4个胶框
4.3上、下栈板的注意事项:
4.3.1胶框的装载、存放请按要求作业:重不压轻,大不压小。
4.3.2搬运、装载、存放时请轻拿轻放,不允许野蛮操作,不允许有扔、砸产品的行为。
4.3.3如需接触PCBA时,必须佩带静电手套,禁止直接接触PCBA。
4.3.4如产品较重,装载、存放时需请人协助,由2人作业。
4.3.5存放时,所有胶框上的产品标识卡要朝外。
4.3.6各工序段,胶框要摆放整齐不能斜放,所有摆放好的胶框的边缘,要成水平垂直直角。
4.3.7搬运过程中,如出现产品掉落在地上或受外力碰撞时,必须退回上一工序,由上一工序所
在线别的QA确认,不允许直接放回胶框内,流入下一工序。
4.4拉货时的注意事项:
4.4.1不同层车间使用栈板运输时,要先做好货品防护--缠绕薄膜,薄膜缠绕在最上面的两层胶
不同厂房之间运输时,顶层的所有胶框,需盖上胶框盖子以防尘、防雨。
顶层胶框需加胶盖
5.参考文件: 无。
PCBA作业指导书(各工序)
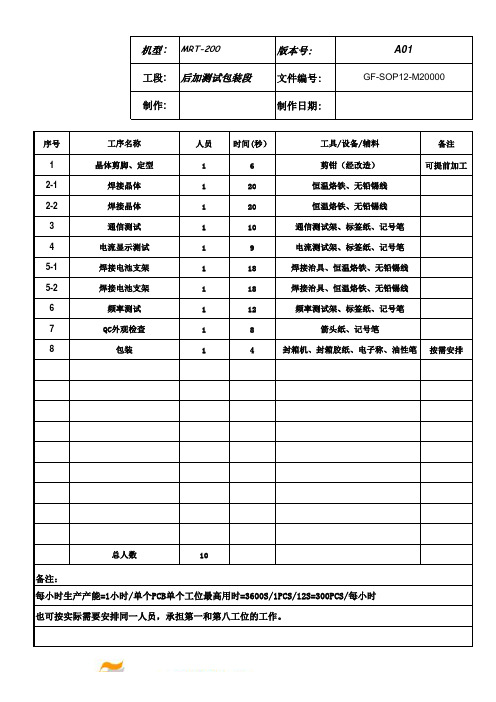
机型:
版本号:工段:文件编号:制作:
制作日期:
序号人员时间(秒)
备注116可提前加工
2-11202-212031104195-11185-211861127188
1
4
按需安排
10
备注:
每小时生产产能=1小时/单个PCB单个工位最高用时=3600S/1PCS/12S=300PCS/每小时也可按实际需要安排同一人员,承担第一和第八工位的工作。
总人数QC外观检查
箭头纸、记号笔
包装
封箱机、封箱胶纸、电子称、油性笔
焊接电池支架焊接治具、恒温烙铁、无铅锡线频率测试频率测试架、标签纸、记号笔
电流显示测试电流测试架、标签纸、记号笔焊接电池支架焊接治具、恒温烙铁、无铅锡线焊接晶体恒温烙铁、无铅锡线通信测试通信测试架、标签纸、记号笔焊接晶体恒温烙铁、无铅锡线工序名称工具/设备/辅料MRT-200
A01
后加测试包装段
GF-SOP12-M20000
晶体剪脚、定型
剪钳(经改造)。
分板工艺作业指导书

1、分板时掰的方向是朝没有元件的PCB面;
2、合成板的板边需要使用剪钳剪断,而不能直接将产品放在平面上压断;
3、注意静电防护;
4、左手和右手拿起合成板,然后同时的用力将合成的板折断,分开合成板;
5、合成板分开成单板后,需要将单板上的板边再去除;
6、使用剪钳沿着PCB沿边的位置朝没有元件的板面用力将单板的板边去除,如果是单板的板边长度是和PCB的长度一样,则使用分板治具以第2步骤的方法分板。
7、分好的PCB板再传给下一道工序作业。
工位编号
工序名称
分工序
适用机型
通用
作业内容:
1、将分板治具摆放在工作台面上,拿出一片需要分板的产品。
2、首先将产品最外面的板边放入分板治具的板槽上,然后将板往没有元件的一面掰来分开PCBA的核心板和板边,重复该动作完成PCBA的四面板边的分板动作;
3、如果是合板的PCBA,还需要将合成的PCBA再分成单片的PCB板。
电子物料防护作业指导书2 (2)
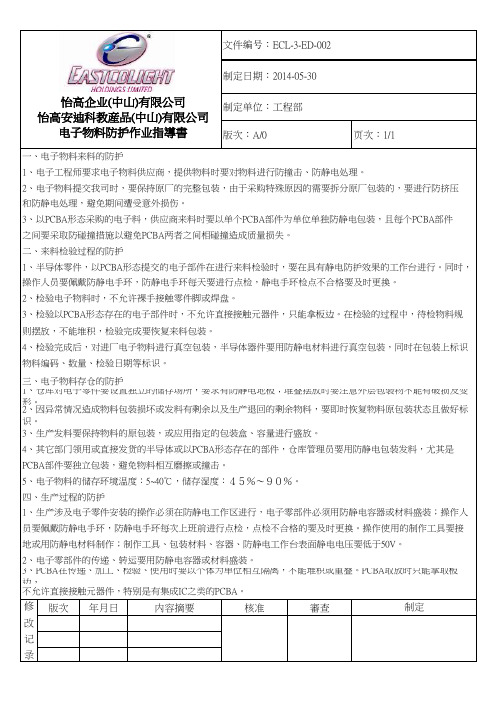
版次年月日内容摘要核准審查版次:A/0页次:1/1制定5、电子物料的储存环境温度:5~40℃,储存湿度:45%~90%。
3、PCBA在传递、加工、检验、使用时要以个体为单位相互隔离,不能堆积或重叠。
PCBA取放时只能拿取板边,不允许直接接触元器件,特别是有集成IC之类的PCBA。
修改记录2、电子零部件的传递、转运要用防静电容器或材料盛装。
文件编号:ECL-3-ED-002制定日期:2014-05-30制定单位:工程部一、电子物料来料的防护1、电子工程师要求电子物料供应商,提供物料时要对物料进行防撞击、防静电处理。
2、电子物料提交我司时,要保持原厂的完整包装,由于采购特殊原因的需要拆分原厂包装的,要进行防挤压四、生产过程的防护1、生产涉及电子零件安装的操作必须在防静电工作区进行,电子零部件必须用防静电容器或材料盛装;操作人和防静电处理,避免期间遭受意外损伤。
3、以PCBA形态采购的电子料,供应商来料时要以单个PCBA部件为单位单独防静电包装,且每个PCBA部件之间要采取防碰撞措施以避免PCBA两者之间相碰撞造成质量损失。
二、来料检验过程的防护员要佩戴防静电手环,防静电手环每次上班前进行点检,点检不合格的要及时更换。
操作使用的制作工具要接地或用防静电材料制作;制作工具、包装材料、容器、防静电工作台表面静电电压要低于50V。
2、因异常情况造成物料包装损坏或发料有剩余以及生产退回的剩余物料,要即时恢复物料原包装状态且做好标识。
3、生产发料要保持物料的原包装,或应用指定的包装盒、容量进行盛放。
4、其它部门领用或直接发货的半导体或以PCBA形态存在的部件,仓库管理员要用防静电包装发料,尤其是PCBA部件要独立包装,避免物料相互磨擦或撞击。
1、仓库对电子零件要设置独立的储存场所,要求有防静电地板;堆叠摆放时要注意外层包装物不能有破损及变形则摆放,不能堆积,检验完成要恢复来料包装。
4、检验完成后,对进厂电子物料进行真空包装,半导体器件要用防静电材料进行真空包装,同时在包装上标识物料编码、数量、检验日期等标识。
514-SMTPCB拿取放作业指导书

文件编号日期工序
机种版本
【目的】
为了使作业员更好的了解如何对PCB拿,取,放的标准操作,并给初学者以指导.【范围】
适用于SMT 车间的所有人员.【职责】
1.生产:执行对PCB拿取放的标准.
2.技术:培训所有人员对PCB的拿取放达成共识.
3.IPQC人员:检查所有人员是否正确的拿取放PCB.【操作内容】
1,PCB板的拿板方式如右图所示:双手捧住PCB的两边(图片1)。
2,PCB板的取板方式:如下图注意两手的动作(图2)。
3,PCB板的放板方式:如右边图所示双手紧抓PCB 两边(图3)。
4,使用正确的PCB拿取放方法作业可以减少人为的抺板,撞件。
注意事项:接触PCB必须带防静电手套.防静电手环。
在印刷工位前装板时要认真检查板面是否有异物.静电手套 ,静电手环 批准:
审核
制作: 李强
工程名
PCB拿取放方法
5,印刷、QC 、维修以及SMT 所有工位在防静电框内装PCB 或PCBA 时,每层只能装 1片拼扳PCB 或PCBA.(一层内严禁多片排放和叠放)
WI-SMT-4-W12514
2018.6.11PCB拿取放作业所有机种
C1
作业顺序及方法
使用工具深 圳 特 发 东 智 科 技 有 限 公 司
PCB拿取放作业指导书
文件名称
图1
图2
图3。
PCBA测试步骤
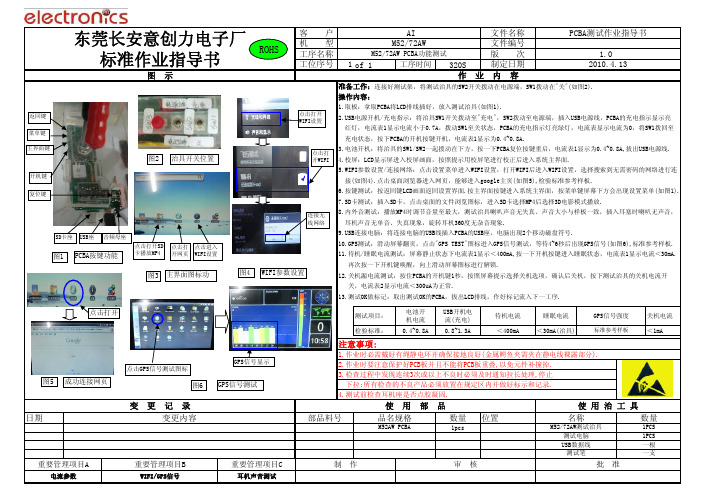
图2
开机键 复位键
治具开关位置
√
连接无 线网络 SD卡座 USB座 音频母座 点击打开SD 卡播放MP4 点击打 开网页 点击进入 WIFI设置
图1
PCBA按键功能
图3
主界面图标功
图4
WIFI参数设置
12.关机漏电流测试:按住PCBA的开机键1秒,按照屏幕提示选择关机选项,确认后关机,按下测试治具的关机电流开 关,电流表2显示电流<300uA为正常. 13.测试OK做标记:取出测试OK的PCBA,拔出LCD排线,作好标记流入下一工序.
东莞长安意创力电子厂 标准作业指导书
图 示
ROHS
客 户 机 型 工序名称 工位序号
AI M52/72AW
M52/72AW PCBA功能测试
1 of 1
工序时间
320S 作
文件名称 文件编号 版 次 制定日期 业 内 容
PCBA测试作业指导书 1.0 2010.4.13
准备工作:连接好测试架,将测试治具的SW2开关拨动在电源端,SW1拨动在"关"(如图2). 操作內容:
点击打开
测试项目: 检验标准:
电池开 机电流 0.4~0.8A
USB开机电 流(充电) 0.8~1.3A
待机电流 <400mA
睡眠电流 <30mA(治具)
GPS信号强度
标准参考样板
关机电流 <1mA
注意事项:
GPS信号显示 点击GPS信号测试图标
图5
成功业时必需戴好有绳静电环并确保接地良好(金属鳄鱼夹需夹在静电线裸露部分). 2.作业时要注意保护好PCB板并且不能将PCB板重叠,以免元件补撞掉. 3.检查过程中发现连续3次或以上不良时必须及时通知拉长处理,停止 下拉;所有检查的不良产品必须放置在规定区内并做好标示和记录. 4.测试前检查耳机座是否点胶凝固.
PCBA通用标准作业指导书
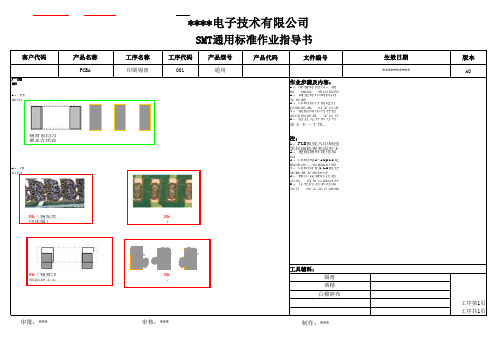
产品代码
文件编号
生效日期 ****-**-**
版本 A0
14)反白 (翻
文字面
R757
翻 面
文字面(翻白)
NG不允许有翻面现象。(即元件表面印丝帖于
PCB一面,无法识别其品名、规格。) 16)孔
塞:
锡尖
孔塞不良
19)多件:依据BOM和ECN或样板等,不应帖装部品的位置 或PCB上有多余的部品均为多件;
1)焊点的机械强度要足够; 2)焊接可靠,保证导电性能; 3)焊点表面要光滑、清洁;
2、焊接检验工艺: 1)各焊接点焊接时焊点用锡不能过多,否则会出现焊点 过太,焊点雍肿; 2)各焊点焊接要圆滑不能有梭角,倒角及缺口; 3)各焊点焊接必须牢固,不能有裂锡等不良现象; 4)PCB板不能有氧化,脱焊,虚焊,焊盘松脱,铜皮翘起,断路, 短路等不良现象; 5)焊点表面必须有金属光泽,爬锡高度应超过焊点端头的1/2,焊 锡覆面率为80%以上,并且焊点无指纹, 无松香,无冷焊等不良现象;
4、元器件插装的方式: 1)元器件插装后,其标志应向着易于认读的方向,并尽可能从左到右的顺序读出; 2)有极性的元器件极性应严格按照图纸上的要求安装,不能错装; 3) 元器件在PCB板上的插装应分布均匀,排列整齐美观,不允许斜排、立体交叉和重叠排列;不允许一边 高,一边低;也不允许引脚一边长,一边短; 4)PCB板上是卧式的元器件都必须贴平PCB板插上, 立式元件必须垂直贴平插在PCB板,不能有元件插的东 倒西歪及元件没插平等不良现象; 5)三极管及特殊元件可以不用贴平PCB板插上,但必须要有1/2 以上插到PCB板上不能离PCB板很高;
3)短路:
短路/ 连锡/
1、不同位置两焊点或两导脚间连锡、碰脚为不良NG; 2、在不影响外观的前提下,同一线路两焊点可短路。
PCBA搬运和暂存通用规范2016.5.23

PCBA搬运和暂存通用规范一、适用范围1、PCBA的搬运是指工序工位之间的运输、班组之间的运输。
2、PCBA的存储是指在周转区的存放、工序工位上的存放。
二、规范内容(一)作业过程1、做好PCBA的防静电措施,使用合适的容器、工具等。
2、运输应选择合适的工具。
工具应确保良好,如轮子、框架等;异常应及时报修,禁止“带伤”使用,以免运输中半成品的跌落、挤压等情况发生。
3、运输工具、存储工具、工位上存储等作业前要做好清扫工作,不允许出现杂物、锡渣等。
避免互相摩擦中造成PCBA的损伤。
提前检查运输工具、存储工具,检查的内容包括把手、梁的位置、台面有无突起、台面之间的距离等,在放置半成品过程前应注意做好相应措施,以免发生碰撞PCBA损伤。
4、运输、存储的PCBA容器、工具车上应该做好明确的标识,记录产品相关的信息,以免错放、混放等。
暂存区域应做好标识、划线,原则上同一状态的同一产品才能放置在同一区域,避免错放、混放。
5、在运输工具上、周转区存储、工序工位存储时,禁止PCBA 之间直接叠放,尤其是在运输中,直接的重叠放置,摩擦会导致元器件之间的损坏。
在PCBA之间,即使进行了隔板的必要的防护措施,也要严格注意叠放层数,层数限定在4层及以内,避免最下面一层受到挤压或者整体倒塌。
(注:CPU控制在10层及以内)6、运输装卸过程中,要稳妥有序,禁止野蛮装卸。
7、在运输工具上、周转区存储PCBA时,码放后要做好四周的防护,避免掉落。
PCBA的易损面应避免和工具直接接触,应注意码放稳固,不倾斜。
8、运输过程中,注意路面状况是否良好,有无障碍物、坑洼突起等,避免车辆颠簸造成半成品的损伤。
运输工具的速度,要均衡合理。
在运输工具开始和停止时,运输工具会和半成品产生摩擦,此时应注意缓慢加速和减速,避免太大的摩擦造成元器件损伤。
9、工位之间的板卡传递,通过传送带或者“手递手”进行等方式,都必须避免出现PCBA的重叠放置、挤压。
严禁在转运和传递中,抛掷等动作。
【参考文档】pcb板作业指导书-word范文模板 (6页)

本文部分内容来自网络整理,本司不为其真实性负责,如有异议或侵权请及时联系,本司将立即删除!== 本文为word格式,下载后可方便编辑和修改! ==pcb板作业指导书篇一:电路板设计作业指导书1、目的规范产品的 PCB 工艺设计,规定 PCB 工艺设计的相关参数,使得 PCB 的设计满足电气性能、可生产性、可测试性等要求,在产品设计过程中构建产品的工艺、技术、质量、成本优势。
2、范围本规范适用于所有公司产品的 PCB 设计和修改。
3、定义(无)4、职责4.1 R&D 硬件工程师负责所设计原理图能导入PCB网络表,原理上符合产品设计要求。
4.2 R&D 结构工程师负责所设计PCB结构图符合产品设计要求。
4.3 R&D PCB Layout工程师负责所设计PCB符合产品设计要求。
5、作业办法/流程图(附后)5.1 PCB 板材要求5.1.1 确定 PCB 所选用的板材、板厚等,例如PCB板材:FR-1、FR-4、CEM-1、CEM-3、纸板等,PCB板厚:单面板常用1.6mm ,双面板、多层板常用1.2mm或1.6mm,PCB的板材和厚度由结构和电子工程师共同确定。
5.1.2 确定 PCB 铜箔的表面处理方式,例如镀金、OSP、喷锡、有无环保要求等。
注:目前应环保要求,单面、双面、多层PCB板均需采用OSP表面处理工艺,即无铅工艺。
(特殊工艺要求除外,如:轻触按键弹片板表面需镀金处理)5.1.3 确定PCB有关于防燃材料和等级要求,例如普通单面板要求:非阻燃板材XPC或FR-194HB和94V-0; TV产品单面板要求:FR-1 94V-0;TV电源板要求:CEM1 94V-0;双面板及多层板要求:FR-4 94V-0。
(特殊情况除外,如工作频率超过1G 的,PCB不能用FR-4的板材)5.2 散热要求5.2.1 PCB 在布局中考虑将高热器件放于出风口或利于空气对流的位置。
PCBA加工操作通用规范2016.5.23
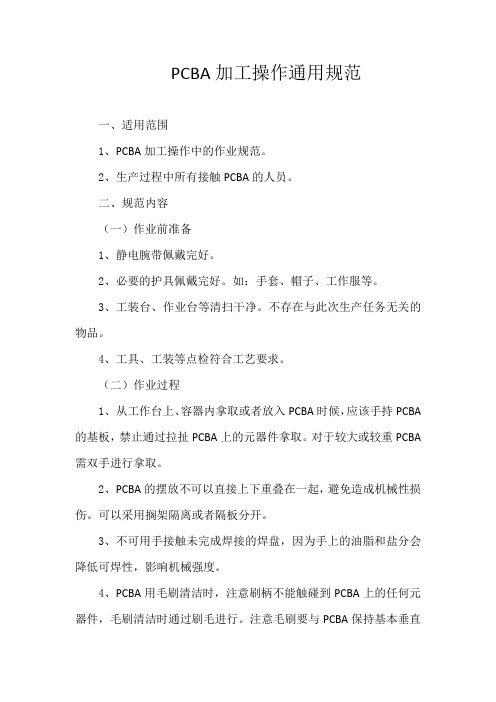
PCBA加工操作通用规范一、适用范围1、PCBA加工操作中的作业规范。
2、生产过程中所有接触PCBA的人员。
二、规范内容(一)作业前准备1、静电腕带佩戴完好。
2、必要的护具佩戴完好。
如:手套、帽子、工作服等。
3、工装台、作业台等清扫干净。
不存在与此次生产任务无关的物品。
4、工具、工装等点检符合工艺要求。
(二)作业过程1、从工作台上、容器内拿取或者放入PCBA时候,应该手持PCBA 的基板,禁止通过拉扯PCBA上的元器件拿取。
对于较大或较重PCBA 需双手进行拿取。
2、PCBA的摆放不可以直接上下重叠在一起,避免造成机械性损伤。
可以采用搁架隔离或者隔板分开。
3、不可用手接触未完成焊接的焊盘,因为手上的油脂和盐分会降低可焊性,影响机械强度。
4、PCBA用毛刷清洁时,注意刷柄不能触碰到PCBA上的任何元器件,毛刷清洁时通过刷毛进行。
注意毛刷要与PCBA保持基本垂直方向,避免毛刷清洁过程中,刷柄触碰到较高元器件造成损坏。
5、用镊子、偏口钳等工具时,注意动作平稳,不要触碰到元器件。
6、拼板的分板作业中,手工作业需要手持基板进行,不能在元器件上着力。
使用分板工装,加持工艺边时,避免触碰板卡上元器件。
7、工位上PCBA码放禁止出现直接叠放,较多PCBA应及时转移到下一工位或者存放在容器等工装工具中。
8、在选择性波峰焊、功能测试等使用工装过程中,注意查看PCBA上元器件有无倾斜,是否和工装的孔位对齐,避免元器件受力。
9、作业员焊接完成,转到下一工序,不管是放置在流水线或者手工传递过程中,禁止抛掷、台面横推等作业方式。
应注意节奏、轻放轻取。
10、工位台面上要及时清扫杂物,如锡渣等。
避免由于杂物和PCBA之间的摩擦造成损伤。
11、PCBA手工焊接元器件、焊线等过程中,应注意焊接时对其他元器件的影响,避免焊接过程中,板卡边缘位置、板卡背面位置和板卡较高元器件受力损坏。
12、手工剪脚工位注意避免剪脚时剪到周边元器件管脚。
SMT通用作业指导书

SMT通用作业指导书2、检查PCBA表面元件是否完好无损,无漏焊、虚焊、短路、反向等缺陷;检查PCBA表面无异物、无划痕、无变形等现象。
图2回流焊出口注意事项:1、操作前请戴好防静电手环,并接好地。
2、操作中要轻拿轻放,避免PCBA表面受损。
3、如发现不良品,请及时记录并报告相关人员。
物资编码拟制:XXX规格数量位置审核:设备/工具/辅料防静电手环数量1批准:注意事项1、请勿在操作过程中用力碰撞PCBA表面。
2、操作中请注意防静电措施,避免静电损坏元件。
3、如发现不良品,请及时记录并报告相关人员。
在检查PCBA之前,需要先检查锡是否呈粉末状(未融化),同时也要检查PCBA是否有损坏、变形、烤黄等问题。
如果发现问题,需要立即向拉长或技术员反映,以便及时解决。
对于检查合格的PCBA,需要将其侧放入“L”型防静盒中,不同机型或种类需要分区放置,放置间隔以板与板不相互摩擦、碰撞为原则。
同时,需要注意数量的控制。
在进行PCBA检查时,需要将检视板覆盖在PCBA上,检查贴片元件是否有多件、少件及IC反向等问题。
合格后,在板边用颜色笔作标记放置于合格品区待下一FQC目检,不良品则需要用红色箭头标签贴在不良位置,并在FQC报表记录不良状况。
对于PCBA的焊锡状况检查,需要将PCBA放在放大镜前,检查元件是否有短路、虚焊、移位浮起、锡尖及锡珠等不良。
如发现不良,需要做好标识区分,并记录在《焊点面FQC检验日报表》中。
不良现象参照图样,OK代表良品,NG代表不良品。
在进行检查时,需要注意以下两个情况,如果发生,应立即反应IPQC:连续3块PCBA板出现同样不良时,以及同一不良项每小时超过5块PCBA时。
Standard XXX。
Ltd.XXX:Product Name:n Name:Process Name:Standard Working Hours:Controlled Status:n: A2XXX:Page Number:ns:1.In Figure 1.if the component shift is greater than 2/3W。
湿敏元器件及PCB、PCBA存储作业指导书
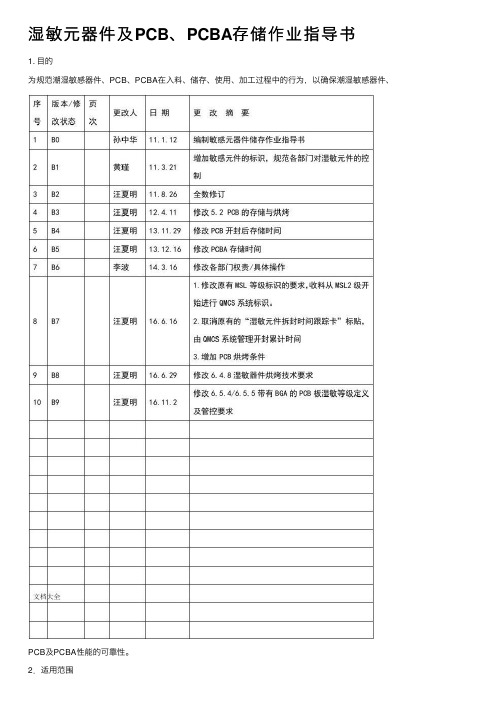
湿敏元器件及PCB、PCBA存储作业指导书1. ⽬的为规范潮湿敏感器件、PCB、PCBA在⼊料、储存、使⽤、加⼯过程中的⾏为,以确保潮湿敏感器件、PCB及PCBA性能的可靠性。
2.适⽤范围2.1适⽤于本公司所有湿敏元器件、PCB、PCBA以及各接触到湿敏元器件、PCB、PCBA的部门。
3.责任⼈此作业指导书的维护责任⼈为供应商品质经理,同时任何部门⼈员提出对此作业指导书的维护建议,供应商品质经理必须给与回复,并研究讨论是否更新此作业指导书。
4.定义4.1 SMD:表⾯贴装器件,主要指通过SMT⽣产的PSMD(Plastic Surface Mount Devices),也即塑封表⾯贴(封装)器件;如下表描述的器件;4.2湿敏元器件是指易于吸收湿⽓,受热(回流焊或波峰焊)后湿⽓膨胀,导致内部损坏或分层的器件,基本上都是SMD器件;4.3 ⼀般器件:指除潮湿敏感器件以外,组装时需要焊接的所有元器件;4.4 存储条件:是指与所有元器件封装体和引脚直接接触的外部环境;4.5 存储期限:是指元器件从⽣产⽇期到使⽤⽇期间的允许最长保存时间;4.6 PCB:印制电路板,printed circuit board的简称。
在绝缘基材上,按预定设计形成印制元件或印制线路以及两者结合的导电图形的印制板。
4.7 MSL:标准等级使⽤期即不同湿敏级别的物料在⼯⼚温湿度条件下的存储条件。
5.权责5.1 仓库----仓库区域环境温湿度的管制,和防潮箱的环境温湿度管制,负责湿敏元器件的⼊库,存储,发放。
5.2 IQC----验货区域的环境温湿度的管制,负责湿敏元器件的等级确认,标签贴付和来料检验。
5.3 ⽣产部----⽣产区域、物料暂存区域温湿度敏感组件的管制,负责湿敏元器件的领取以及在产线的存储、使⽤。
5.4 其它部门----维修及有涉及到湿敏元器件的部门要做好湿敏元件的管制。
5.5 IPQC----参与对仓库及各车间的温湿度、敏感元器件的储存、使⽤进⾏定期的点检并监控,及时将稽核问题进⾏通报。
PCBA摆放拿取作业指导书

版本号A03 PCBA摆放拿取作业指导书生效日期2016-5-28页码 1 of 7修订履历序号原内容修订后旧版修订人修订日期1 无装箱图片等描述增加装箱内容及图片A01 2014-5-212 原作业内容及图片信息较少增加及完善作业内容及图片信息.A02 2015-11-193 无PCBA拿取信息描述增加2.10及拿取作业内容及图片信息.A03 2016-5-2841.目的:规范本公司生产部生产的PCBA半成品摆放与拿取(包含SMT、AI、波峰焊后周转工序),防止物理损坏,提高产品品质。
2.作业步骤:2.1根据PCBA的尺寸大小确定板架摆放数量,板架上的PCBA不得相互碰撞,如图一、图二、图三所示:同一个板架只可放置一个产品每个板架上的数量需一致。
图一图二图三板架单排摆放板架双排摆放周转架摆放(正确) (正确) (正确)2.2 板架上的PCBA摆放好后单层放置到周转架上,如图四;图四图五单层平整摆放双层叠放(正确) (错误)版本号A03 PCBA摆放拿取作业指导书生效日期2016-5-28页码 2 of 72.3根据PCBA横/纵方向板边元器件分布情况,确定PCBA上板架的摆放方向;并根据摆板方向上/下板边元器件分布情况,确定PCBA摆放方式;确保PCBA在板架的卡槽边缘3MM内不得有元器件,避免碰损.如图六、图七所示:图六图七图八图九横向摆放纵向摆放对称摆放不对称摆放(正确)(错误)2.4台面堆积摆放的产品最多3-5PCS,如图十。
产品堆积过多造成叠板有撞件隐患,如图十一:如多出5PCS的产品需使用防静电的平垫或吸塑盒整齐有序的摆放,如图十二。
图十图十一图十二图十三台面最多摆放3-5PCS 台面产品堆积过多装盘整齐摆放装盘后PCBA相互碰撞(正确)(错误) (正确) (错误) (正确)(错误)(正确) (错误)图十四图十五整齐摆放,不碰撞摆放太多,相互碰撞(正确) (错误)版本号A03 PCBA摆放拿取作业指导书生效日期2016-5-28页码 3 of 7图十六图十七整齐摆放,不碰撞摆放太多,相互碰撞(正确) (错误)图十八图十九图二十整齐摆放,不碰撞摆放太多,相互碰撞半成品板不可摆板架(正确) (错误) (错误)图二十一图二十二整齐摆放,不碰撞整齐摆放,板边对齐,不碰零件(正确) (允许)版本号A03 PCBA摆放拿取作业指导书生效日期2016-5-28页码 4 of 7 图二十三图二十四图二十五图二十六吸塑盒一格一个摆放凌乱整齐摆放,不碰撞吸塑盒一格一个(正确) (错误) (正确) (正确)2.5生产带线材的小板出现堆积超过5PCS时需用防静电平垫整齐有序的放置。
回流焊后捡板作业指导书

客户:
通用
编号:版本:
机型
通用
工段
SMT
工位
炉后捡板制定日期:图解:
图示1
图示2
图示3
工具数目单位静电手环1只静电手套1双标示卡
1
本
合格且要正确佩带
正确佩带状态标示
使用工具及操作要求
要求
免过高倒塌。
6、捡完之后,应将其装箱且做好标识,存放在半成品存放处。
7、如是锡膏板,则等待处理锡珠,执锡后再生产第二面。
注意事项:
1、不同机种的PCBA不可摆在一起,并做好状态标示
2、PCBA取放须轻拿轻放不可叠放相碰
3、待PCBA 到达炉口时,由于炉子温度较高.(红胶温度最高为180℃\锡膏温度为230℃)摆放所用的珍珠棉材质不能承受如此高温,故首先要将PCBA 放在特定的卡板上(如图示一)待冷却后再放在珍珠棉上。
4、PCBA 冷却后,将其整齐且保持至少1CM 的间距,防止PCBA 在运输
过程中摩擦掉件.而且PCBA 不能背对背摆放,只能单层摆放(如图示二)。
5、如机型批量较大,摆放层数不能超过15层(如图示三)或高度不能超过50cm.以回流焊后捡板作业指导书
操作步骤:
1、首先把炉后台面整理干净,保证充足的摆放空间。
2、准备好防静电珍珠棉,戴好防静电手环、手套。
- 1、下载文档前请自行甄别文档内容的完整性,平台不提供额外的编辑、内容补充、找答案等附加服务。
- 2、"仅部分预览"的文档,不可在线预览部分如存在完整性等问题,可反馈申请退款(可完整预览的文档不适用该条件!)。
- 3、如文档侵犯您的权益,请联系客服反馈,我们会尽快为您处理(人工客服工作时间:9:00-18:30)。
版本号A03 PCBA摆放拿取作业指导书生效日期2016-5-28
页码 1 of 7
修订履历
序号原内容修订后旧版修订人修订日期1 无装箱图片等描述增加装箱内容及图片A01 2014-5-21
2 原作业内容及图片信息较少增加及完善作业内容及图片
信息.
A02 2015-11-19
3 无PCBA拿取信息描述增加2.10及拿取作业内容
及图片信息.
A03 2016-5-28
4
1.目的:
规范本公司生产部生产的PCBA半成品摆放与拿取(包含SMT、AI、波峰焊后周转工序),防止物理损坏,提高产品品质。
2.作业步骤:
2.1根据PCBA的尺寸大小确定板架摆放数量,板架上的PCBA不得相互碰撞,如图一、图二、图三所示:
同一个板架只可放置一个产品每个板架上的数量需一致。
图一图二图三板架单排摆放板架双排摆放周转架摆放
(正确) (正确) (正确)
2.2 板架上的PCBA摆放好后单层放置到周转架上,如图四;
图四图五
单层平整摆放双层叠放
(正确) (错误)
版本号A03 PCBA摆放拿取作业指导书生效日期2016-5-28
页码 2 of 7
2.3根据PCBA横/纵方向板边元器件分布情况,确定PCBA上板架的摆放方向;并根据摆板方向上/下板边元器件分布
情况,确定PCBA摆放方式;确保PCBA在板架的卡槽边缘3MM内不得有元器件,避免碰损.如图六、图七所示:
图六图七图八图九横向摆放纵向摆放对称摆放不对称摆放
(正确)
(错误)
2.4台面堆积摆放的产品最多3-5PCS,如图十。
产品堆积过多造成叠板有撞件隐患,如图十一:如多出5PCS的
产品需使用防静电的平垫或吸塑盒整齐有序的摆放,如图十二。
图十图十一图十二图十三
台面最多摆放3-5PCS 台面产品堆积过多装盘整齐摆放装盘后PCBA相互碰撞
(正确)(错误) (正确) (错误) (正确)(错误)(正确) (错误)
图十四图十五
整齐摆放,不碰撞摆放太多,相互碰撞
(正确) (错误)
版本号A03 PCBA摆放拿取作业指导书生效日期2016-5-28
页码 3 of 7
图十六图十七
整齐摆放,不碰撞摆放太多,相互碰撞
(正确) (错误)
图十八图十九图二十整齐摆放,不碰撞摆放太多,相互碰撞半成品板不可摆板架
(正确) (错误) (错误)
图二十一图二十二
整齐摆放,不碰撞整齐摆放,板边对齐,不碰零件
(正确) (允许)
版本号A03 PCBA摆放拿取作业指导书生效日期2016-5-28
页码 4 of 7 图二十三图二十四图二十五图二十六吸塑盒一格一个摆放凌乱整齐摆放,不碰撞吸塑盒一格一个
(正确) (错误) (正确) (正确)
2.5生产带线材的小板出现堆积超过5PCS时需用防静电平垫整齐有序的放置。
图二十七图二十八图二十九
装盘整齐摆放装盘后相互堆叠在台面相互堆叠
(正确) (错误) (错误)
图三十图三十一图三十二每格摆放2PCS 每格摆放2PCS 摆放太多,显凌乱
(正确)(正确) (错误)
图三十三图三十四图三十五每格摆放4PCS 平整摆放,PCBA不碰撞摆放太多, 相互叠压、碰撞
(正确) (正确) (错误)。