车身工艺介绍
汽车制造四大工艺介绍

汽车制造四大工艺介绍
汽车制造通常采用四大工艺,即冲压、焊接、涂装和总装。
1. 冲压工艺:冲压是将钢板等材料通过冲压机进行加工,形成汽车车身的各个部分,如车门、引擎盖、车顶等。
冲压工艺需要使用高精度的冲压机和模具,以保证车身的精度和质量。
2. 焊接工艺:焊接是将冲压成形的车身各个部分进行连接,形成完整的车身。
焊接工艺通常采用点焊、弧焊、激光焊接等技术,以保证车身的强度和密封性能。
3. 涂装工艺:涂装是将车身进行涂装,以保护车身并提高其外观和质感。
涂装工艺通常包括底漆、面漆和清漆的涂装,以及喷涂、烘烤等多个步骤。
4. 总装工艺:总装是将车身的各个部分进行组装,形成完整的汽车。
总装工艺通常包括发动机、变速器、悬挂系统、内饰等各个部分的组装,以及整车的调试和检测。
这四大工艺是汽车制造的核心环节,需要高度的技术和精密的设备来保证汽车的质量和性能。
随着科技的不断进步,汽车制造工艺也在不断发展和改进,以适应市场和消费者的需求。
车身工艺流程
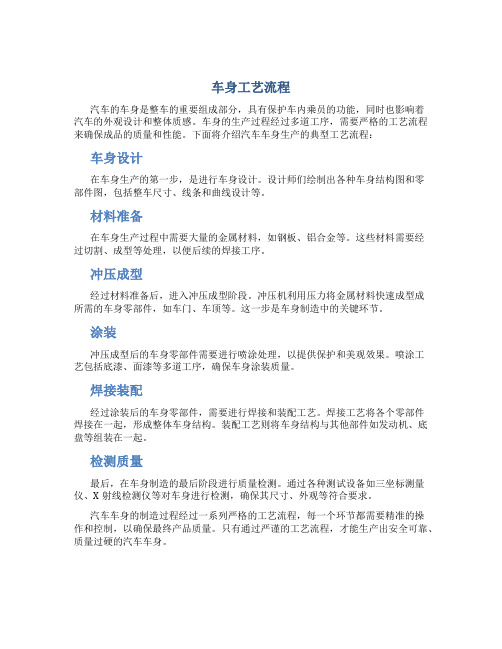
车身工艺流程
汽车的车身是整车的重要组成部分,具有保护车内乘员的功能,同时也影响着
汽车的外观设计和整体质感。
车身的生产过程经过多道工序,需要严格的工艺流程来确保成品的质量和性能。
下面将介绍汽车车身生产的典型工艺流程:
车身设计
在车身生产的第一步,是进行车身设计。
设计师们绘制出各种车身结构图和零
部件图,包括整车尺寸、线条和曲线设计等。
材料准备
在车身生产过程中需要大量的金属材料,如钢板、铝合金等。
这些材料需要经
过切割、成型等处理,以便后续的焊接工序。
冲压成型
经过材料准备后,进入冲压成型阶段。
冲压机利用压力将金属材料快速成型成
所需的车身零部件,如车门、车顶等。
这一步是车身制造中的关键环节。
涂装
冲压成型后的车身零部件需要进行喷涂处理,以提供保护和美观效果。
喷涂工
艺包括底漆、面漆等多道工序,确保车身涂装质量。
焊接装配
经过涂装后的车身零部件,需要进行焊接和装配工艺。
焊接工艺将各个零部件
焊接在一起,形成整体车身结构。
装配工艺则将车身结构与其他部件如发动机、底盘等组装在一起。
检测质量
最后,在车身制造的最后阶段进行质量检测。
通过各种测试设备如三坐标测量仪、X射线检测仪等对车身进行检测,确保其尺寸、外观等符合要求。
汽车车身的制造过程经过一系列严格的工艺流程,每一个环节都需要精准的操
作和控制,以确保最终产品质量。
只有通过严谨的工艺流程,才能生产出安全可靠、质量过硬的汽车车身。
车身制造四大工艺定义及特点

车身制造四大工艺定义及特点:§在汽车制造业中,冲压、焊装、涂装、总装合为四大核心技术即四大工艺;从结构上看,轿车属于无骨架车身,它的生产工艺流程大致为:焊装工艺:冲压好的车身板件局部加热或同时加热、加压而接合在一起形成车身总成;在汽车车身制造中应用最广的是点焊,焊接的好坏直接影响了车身的强度;汽车车身是由薄板构成的结构件,冲压成形后的板料通过装配和焊接形成车身壳体白车身,所以装焊是车身成形的关键;装焊工艺是车身制造工艺的主要部分;汽车车身壳体是一个复杂的结构件,它是由百余种、甚至数百种例如轿车薄板冲压件经焊接、铆接、机械联结及粘接等方法联结而成的;由于车身冲压件的材料大都是具有良好焊接性能的低碳钢,所以焊接是现代车身制造中应用最广泛的联结方式;焊装工艺点焊:通过导电,电阻加热,金属熔合;点焊的过程:预压-焊接-保压-休止;点焊相关工艺参数:电流/电压/电极压力/焊接时间/电极直径等;点焊设备:固定式点焊机,移动式点焊机,包括:供电系统变压器和二次回路、焊具部分机臂、电极夹持器、电极、加压机构气压、液压等、冷却系统、机体等;CO2气体保护焊接:一种熔化极气体保护电弧焊接法,利用焊丝与工件间产生的电弧来熔化金属,由CO2作为气体保护气,并采用光焊丝填充;焊接工艺参数:电源极性/焊丝直径/电弧电压/焊接电流/气体流量/焊接速度/焊丝伸出长度/直流回路电感等;§车身主体:主要由车前钣金、前围零件、地板总成、左/右侧围总成、后围总成、行李舱搁板总成和顶盖总成等零部件焊装而成§汽车车身部件焊接系列夹具§定位与夹紧,装配焊接三过程,一定位,二夹紧,三点固§定位是通过定位基准与夹具上的定位元件相接触而实现,定位元件有:挡铁,定位销,支承板,样板§夹紧:有力,稳定,避免焊接运动干涉涂装工艺§涂装有两个重要作用,第一车防腐蚀,第二增加美观;涂装工艺过程比较复杂,技术要求比较高;主要有以下工序:漆前预处理和底漆、喷漆工艺、烘干工艺等,整个过程需要大量的化学试剂处理和精细的工艺参数控制,对油漆材料以及各项加工设备的要求都很高,因此涂装工艺一般都是各公司的技术秘密;概述汽车车身的涂装质量要求最高,要长期在各种气候条件下使用而不发生漆膜劣化和锈蚀,还要能维持其光泽、色彩和美观;典型的轿车车身涂装工艺是电泳底漆、中涂、面漆3C3B3Coat3Bake体系;在电泳底漆与中涂之间有焊缝密封和底板防护涂层的喷涂,以保证车身的密封、降噪声和防锈,面漆后涂内腔防锈蜡;§表面涂层属于一级装饰精度,具有美丽的外观,光亮如镜或光滑的表面,无细微的杂质、擦伤、裂纹、起皱、起泡及肉眼可见的缺陷,并应有足够的机械强度;底面涂层属于优良保护层,应有优良的防锈性和防腐蚀性,很强的附着力;局部或全部刮涂附着力好、机械强度高的腻子,使用数年也不会出现锈蚀或脱落等现象;§总装工艺总装就是将车身发动机变速器仪表板车灯车门等构成整辆车的各零件装配起来生产出整车的过程;一、冲压车间的设备:单点单动机械压力机、闭式双点单动机械压力机、闭式四点单动机械压力机、闭式单点双动拉伸压力机、闭式双点双动拉伸压力机、闭式四点双动拉伸压力机、三座标闭式多工位压力机、大公称力的数控液压机、各种冷挤压机及多工位冷挤压机等锻压设备;钢板清洗涂油机、垛料翻转机、数控液压转塔冲床;二、焊装车间:单面双点点焊机、点焊机、点熔接机、二氧化碳保护焊机、硅整流弧焊机、硅镇流电焊机、气动X形悬挂焊机、直流弧焊机、压装机、自动校直点定机、机械手、传送线、CO2焊机、液压站、龙门框架合装设备、电热涨拉设备、等离子切割机、微电脑焊接控制焊机、进口数字式水平仪;发动机装配线专用设备:清洗机、打号机、总成装配输送线、单层自由辊道、双层柔性机动滚道托盘、缸体缸盖输送车、升降机、翻转机、涂胶机、组合式螺栓拧紧机、轴承外环振动压装机、油封压装机、间隙测量机、导向拧紧装置、发动机密封性能检验机、活塞加热机、总成综合性能试验台、扭矩校准仪、气动扳手、装配线计算机控制系统、吊装式LED大屏幕显示装置、单轴气动定扭矩扳手;变速箱装配线专用设备:变速器箱体打号机、总成装配输送线、涂胶机、组合式螺栓拧紧机、变速器轴承外环振动压装机、左油封压装机、变速器间隙测量机、导向拧紧装置、变速器密封性能检验机、变速器润滑油循环系统、总成综合性能试验台、变速器右箱体六头组合压装机、差速器间隙测量机、差速器轴承压装机双压头、变速器中间轴轴承压装机、变速器中间轴轴承压装机、变速器输入轴压装机、变速器主轴压装机、变速器输入轴油封及排气塞压装机双压头、变速器油封压装机、变速器离合器拨叉轴气动压装机、变速器换挡拨叉轴气动压销机、叉轴气动压销机、清洗机、变速器换挡轴气动压销机、扭矩校准仪、气动扳手、装配线计算机控制系统、辊道输送线、翻转机、单轴气动定扭矩扳手、电动单梁悬挂起重机;三、涂装车间:前处理设备、烘干固化设备、电泳设备、静电设备、喷枪、喷涂机、纯水设备、喷漆室、烘箱、阀门、防静电、燃烧器、抛丸机、高粘度喷涂机、高压清洗机、鼓风干燥箱;四、总装车间:带剪式升降机的地面平台式输送系统、旋转台、地面穿梭机、下行升降机、悬挂电气单轨系统、底盘结合系统、链式输送系统、地面平台交叉传递输送系统、铭牌制作机、底盘打号机、涂胶机、防冻液加注机、四轮定位仪、前照灯检测仪、转毂试验台、怠速排放分析仪、四柱液压整车举升机及空调加注机;。
车身四大工艺

汽车生产制造四大工艺
在现代化汽车生产制造业中,作为生产中的四大核心工艺技术,冲压、焊装、涂装、总装是必不可少的,我公司具有较完备、高智能化的生产装备,规范的工艺生产流程和科学有效的质量管理体系,以保证产品质量、性能达到技术设计要求。
冲压工艺
冲压技术在汽车制造业占有重要地位,汽车上有60%~70%的零件是用冲压工艺生产出来的。
因此,冲压技术对汽车的产品质量、生产效率和生产成本都有重要的影响。
冲压工序可分为四个基本工序:1、冲裁;2、弯曲;3、拉伸;4、局部成形。
焊装工艺
汽车车身壳体是一个复杂的结构件,它是由百余种、甚至数百种薄板冲压件经焊接、铆接、机械联结及粘结而成的。
由于车身冲压件的材料大都是具有良好焊接性能的低碳钢,所以焊接是现代车身制造中应用最广泛的联结方式。
涂装工艺
涂装对汽车制造来讲有两个重要作用,第一是给汽车增加防腐性,第二是给汽车增加美观。
涂装工艺过程比较复杂,技术要求比较高。
主要有以下工序:漆前预处理和底漆、喷漆工艺、烘干工等整个过程需要大量的化学试剂处理和精细的工艺参数控制,对油漆材料以及各项加工设备的要求都很高,因此涂装工艺是汽车制造的关键技术。
总装工艺
汽车总装是汽车全部制造工艺过程的最终环节,是把经检验合格的数以千计的各类零件,按规定的精度标准和技术要求组合成分总成、总成、整车,并经严格的检测顺序,确认其是否合格的整个工艺过程。
汽车产品要求有好的动力性、经济性和耐久性,以实现在各种复杂环境中的运载功能,现代汽车产品更要求安全可靠、造型美观、乘坐舒适并满足环保要求,这些要求,最终都是通过装配工艺来保证的。
新版汽车车身制造工艺

=4~10t,D=40~50mm
表10-9 工艺补充部分各部分旳作用及尺寸
表10-9 工艺补充部分各部分旳作用及尺寸
(四)压料面
(1)压料面旳作用与对拉深成形旳影响 压料面是指凹模上表面与压料圈下表面起压料作用旳那一部
分表面,其位置在凹模圆角部分以外。 (2)压料面设计原则
如上所述,压料面有两种情况:一种是压料面旳一部分就是 拉深件旳法兰面;另一种情况是压料面全部属于工艺补充部分。
汽车覆盖件冲模旳设计与制造是一项技术密集型 旳系统工程(6)覆盖件模具旳成套性
表10-8 模具旳成套性
三、覆盖件旳冲压工序
汽车覆盖件旳形状复杂、尺寸大、深度不均匀,所以一般不 可能在一道冲压工序中直接取得,有旳需要十几道工序才干取 得,至少旳也要三道基本工序:落料、拉深、修边。其他还有 翻边和冲孔等工序。也可根据需要将修边和冲孔合并、修边和 翻边合并。
第十章 汽车车身制造工艺
第一节 第二节 第三节 第四节
汽车车身冲压材料 汽车车身覆盖件冲压工艺 汽车车身装焊工艺 汽车车身涂装工艺
第一节 汽车车身冲压材料
一、汽车冲压用钢板旳特点 (1)质量要求高
1)汽车覆盖件旳轮廓尺寸、孔位尺寸、局部形状旳多种尺寸必须有很好旳尺 寸精度,确保装焊旳精确性、互换性,实现车身装焊旳自动化。 2)确保覆盖件具有足够旳刚性。 3)覆盖件在成形过程中,材料应能进行足够旳塑性变形,具有良好旳工艺性。 4)外覆盖件(尤其是乘用车)表面不允许有任何缺陷,曲线应圆滑,过渡应均匀, 具有极好旳表面质量。 5)对外覆盖件要求与车身造型设计一致,必须具有很高旳形状精度,与主模 型吻合。
车身涂装工艺基础介绍

前处理
做什么的呢?
电泳 电泳打磨
车身焊接后,铁会生锈,要防止生锈,就得打防锈油、有油污、杂质,怎 么喷漆,怎么电泳呢?前处理的作用就是除油、清洗干净车身、生成一层 磷化膜,给电泳做准备.涂装前处理会遇到以下问题:1、油污,包括冲 压拉延油、焊接防锈油等;2、焊接胶(黑色)有焊接焊缝胶、焊接膨胀 胶;3、杂质、赃物等;4、铁屑。
打磨要求:一找、二打、三摸准、四求经验。 一找:找缺陷,顺着光线、斜着看 二打:肯定是打磨:电泳打磨现场采用的干打磨,用打磨机进行打磨,尽量不打穿,电泳层防 锈,其厚度不如铁皮(0.7mm),只有18-27um (1000um等于1mm;1根头发丝约为 0.1mm,约为100um)。中涂打磨采用的是湿点打磨。 三摸准:流挂等缺陷是否打磨彻底要用手磨;车身不能残留有触手/刮手的颗粒缺陷。 四求经验:向人求教打磨方法,打磨机要端平打磨、手磨球也要端平;环形打磨不能直 线磨;砂纸的型号? 电泳吹灰/中涂吹灰:对车身打磨后的灰尘进行擦拭、吹净.要求车身内外板都需要干净、 无残留灰尘.
乙 涂
醇
汽车涂装工艺流程及相关岗位工艺质量要求
四区岗位分布:安装阻尼板、打磨、抛光、终检
抛光工艺:先进行点打磨,用3M的3125点打磨机进行点打磨缺陷;然后上抛光液,采用3M的 7125抛光机进行抛光。 抛光作用:消除车身漆膜清漆层上的缺陷,上抛光液,进行装饰上光,恢复光泽,可处理以下缺陷: 清漆层上的细小颗粒、小纤维、轻微桔皮等。 终检:对车身漆膜缺陷按<车身漆膜外观质量验收标准>进行检查,对不合格的缺陷进行标识,将不 合格车发往点被或大返修区域。
打胶就是对车身焊缝挤涂密封胶,主要起防止漏水、漏风和防腐蚀生锈作用。也是采用高压无气手工喷涂。 胶烘烤:130~145 ℃,约15分钟,把湿胶烘干固化,达到规定硬度。
汽车整车全装四大工艺流程
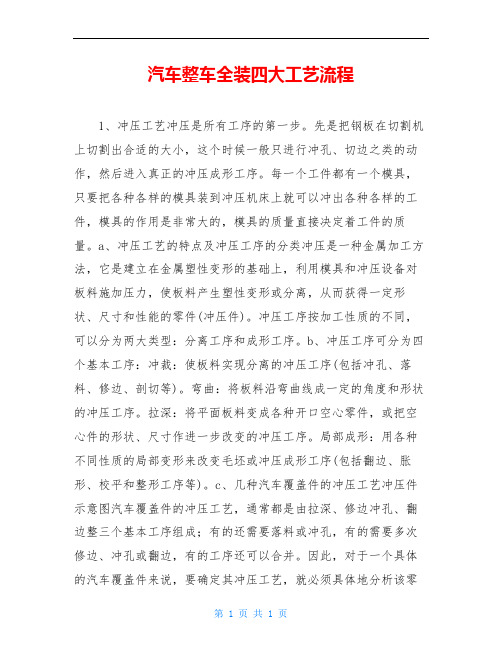
汽车整车全装四大工艺流程1、冲压工艺冲压是所有工序的第一步。
先是把钢板在切割机上切割出合适的大小,这个时候一般只进行冲孔、切边之类的动作,然后进入真正的冲压成形工序。
每一个工件都有一个模具,只要把各种各样的模具装到冲压机床上就可以冲出各种各样的工件,模具的作用是非常大的,模具的质量直接决定着工件的质量。
a、冲压工艺的特点及冲压工序的分类冲压是一种金属加工方法,它是建立在金属塑性变形的基础上,利用模具和冲压设备对板料施加压力,使板料产生塑性变形或分离,从而获得一定形状、尺寸和性能的零件(冲压件)。
冲压工序按加工性质的不同,可以分为两大类型:分离工序和成形工序。
b、冲压工序可分为四个基本工序:冲裁:使板料实现分离的冲压工序(包括冲孔、落料、修边、剖切等)。
弯曲:将板料沿弯曲线成一定的角度和形状的冲压工序。
拉深:将平面板料变成各种开口空心零件,或把空心件的形状、尺寸作进一步改变的冲压工序。
局部成形:用各种不同性质的局部变形来改变毛坯或冲压成形工序(包括翻边、胀形、校平和整形工序等)。
c、几种汽车覆盖件的冲压工艺冲压件示意图汽车覆盖件的冲压工艺,通常都是由拉深、修边冲孔、翻边整三个基本工序组成;有的还需要落料或冲孔,有的需要多次修边、冲孔或翻边,有的工序还可以合并。
因此,对于一个具体的汽车覆盖件来说,要确定其冲压工艺,就必须具体地分析该零件的形状、结构、材料和技术要求,结合生产批量(纲领)和生产设备条件,才能最后确定。
2、焊装工艺冲压好的车身板件局部加热或同时加热、加压而接合在一起形成车身总成。
在汽车车身制造中应用最广的是点焊,焊接的好坏直接影响了车身的强度。
汽车车身是由薄板构成的结构件,冲压成形后的板料通过装配和焊接形成车身壳体(白车身),所以装焊是车身成形的关键。
装焊工艺是车身制造工艺的主要部分。
汽车车身壳体是一个复杂的结构件,它是由百余种、甚至数百种(例如轿车)薄板冲压件经焊接、铆接、机械联结及粘接等方法联结而成的。
汽车车身制造工艺基本知识

3.4汽车制造过程中其它工艺基本知 识
•退火是将工件加热到适当温度,根据材料和工件尺寸采 用 不同的保温吋间,然后进行缓慢冷却,目的是使金厲 内 部组织达到或接近平衡状态,获得良好的工艺性能和 使 用性能,或者为进一步淬火作组织准备。
•正火是将工件加热到适宜的温度后在空气中冷却,正火 的 效果同退火相似,只是得到的组织更细,常用于改善 材 料的切削性能,也有时用于对一些要求不高的零件作 为 桌终热处理。
汽
转向鼷關職汽车向力是否适
(5) 平顺性试验:平顺性主要是根据乘坐者的舒适程度来评价的,所以又叫
其评价方法通常根据人体对震动的生理感受和保持货物
(6) 通过性试验:二般在汽车试验场和专用路段上进行该试验。
(7) 安全性试验:安全性试验项目很多,而且耗资巨大,特别是碰撞安全试
验,除正面撞车试验外,近来还
进入装配线、
3.4汽车制造过程中其它工艺基本知 识
3.43汽车试验
汽车的设计、制造过程始终离不幵试验,无论 是 设计思想和理论计算、初步设计、技术设计、汽 车定型 还是在生产过程,都要进行大量的试验。
汽车试验分为:
1汽车零部件试验 2汽车整车性能试验。
3.4汽车制造过程中其它工艺基本知 识
汽车整车性能试验
•把压力加工形变与热处理有效而紧密地结合起来进行, 使工 件获得很好的强度、韧性配合的方法称为形变热处 理;在 负压气氛或真空屮进行的热处理称为真空热处理, 它不仅 能使工件不氧化,不脱碳,保持处理后工件表而 光洁,提 高工件的性能,还可以通入渗剂进行化学知 识
3.3汽车车身制造工艺的基本知
识
•在车身冲压方面,实现了大型覆盖件的冲压生产机械化 或自 动化、坯料准备即卷料的开卷、校平、剪切和落料 等的自 动化以及冲压废料处理的自动化。现在正向着 CAD/CAM(车身设计、冲模设计、冲模制造和车身制造) 一体化系统的方向发展。 _ •在车身装焊方面,从现在大量
车身制造的其它工艺

手摸检查
灯光检查
油石Байду номын сангаас查
车身质量部
车身质量关键工艺
表面质量(返修): 通过检查发现的表面缺陷不符合质量标准的要求,需要进行返修。
返修时候根据缺陷情况大致是如下步骤: S1:如果变 形比较大,根 据是凸起或者 凹陷,使用平 头榔头或者撬 杠进行预调整。
车身质量关键工艺
车身质量部
表面质量(返修): 通过检查发现的表面缺陷不符合质量标准的要求,需要进行返修。
车身质量关键工艺
车身质量部
扭矩: 车身制造过程的扭矩要求主要体现在门、盖和翼子板及其它散件的装配扭矩。 一般采用的是定扭矩的气动枪打进,和表盘式扭力扳手抽样检查的方式进行控 制扭矩,气动枪定期进行标定。
控 制 体 系
合 格 员 工
车身质量关键工艺
车身质量部
表面质量(检查): 车身表面是指车身的外露面,主要包括四门两盖、前翼子板、加油小门、车顶、侧 框等外表面和前盖、后盖、四门、门框等未被内饰遮盖的内表面。
车身质量关键工艺
车身质量部
表面质量(返修): 通过检查发现的表面缺陷不符合质量标准的要求,需要进行返修。
特殊的时 候会用到部分 特制工具,如 折边处的较深 凹坑。
对于密封型车身 面板的凹陷,无 法利用现成的孔 洞使用撬棒撬起 时,可采用拉铆 枪进行修理。
车身质量部
车身质量部
涂胶 涂胶是使用气缸驱动的压力泵,把容器中的介质(胶)通过管道输送出通过涂胶枪等 将胶形成需要的尺寸规格,按照预定的轨迹涂抹在产品上。涂胶机的主要动力是压缩空 气。 压缩空气主要提供三个作用:涂胶泵的驱动、产生下降压力、取出空胶桶。
车身质量部
涂胶工艺分析包括涂胶位置及断面形状的 确定、涂胶所需的间隙尺寸分析、涂胶枪嘴 选型分析(√)
白车身的工艺方法有哪些
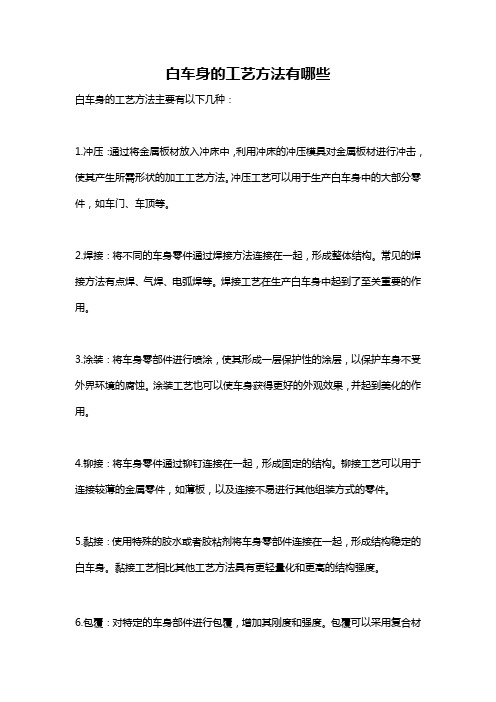
白车身的工艺方法有哪些
白车身的工艺方法主要有以下几种:
1.冲压:通过将金属板材放入冲床中,利用冲床的冲压模具对金属板材进行冲击,使其产生所需形状的加工工艺方法。
冲压工艺可以用于生产白车身中的大部分零件,如车门、车顶等。
2.焊接:将不同的车身零件通过焊接方法连接在一起,形成整体结构。
常见的焊接方法有点焊、气焊、电弧焊等。
焊接工艺在生产白车身中起到了至关重要的作用。
3.涂装:将车身零部件进行喷涂,使其形成一层保护性的涂层,以保护车身不受外界环境的腐蚀。
涂装工艺也可以使车身获得更好的外观效果,并起到美化的作用。
4.铆接:将车身零件通过铆钉连接在一起,形成固定的结构。
铆接工艺可以用于连接较薄的金属零件,如薄板,以及连接不易进行其他组装方式的零件。
5.黏接:使用特殊的胶水或者胶粘剂将车身零部件连接在一起,形成结构稳定的白车身。
黏接工艺相比其他工艺方法具有更轻量化和更高的结构强度。
6.包覆:对特定的车身部件进行包覆,增加其刚度和强度。
包覆可以采用复合材
料、纤维增强塑料等材料进行,以提高车身的轻量化和安全性。
汽车车身涂装工艺
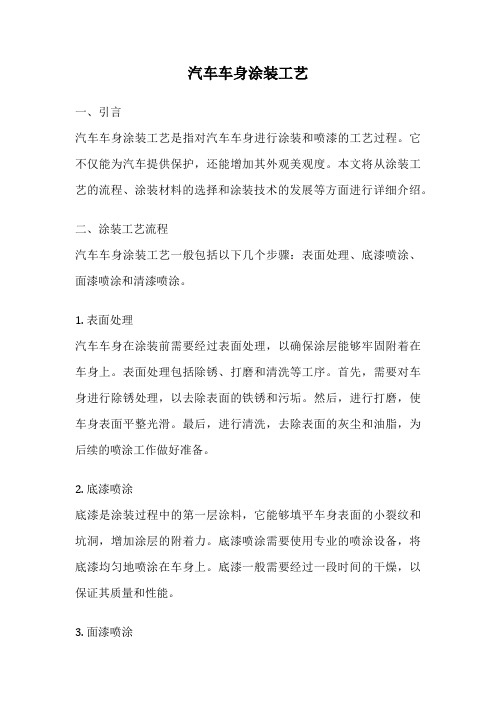
汽车车身涂装工艺一、引言汽车车身涂装工艺是指对汽车车身进行涂装和喷漆的工艺过程。
它不仅能为汽车提供保护,还能增加其外观美观度。
本文将从涂装工艺的流程、涂装材料的选择和涂装技术的发展等方面进行详细介绍。
二、涂装工艺流程汽车车身涂装工艺一般包括以下几个步骤:表面处理、底漆喷涂、面漆喷涂和清漆喷涂。
1. 表面处理汽车车身在涂装前需要经过表面处理,以确保涂层能够牢固附着在车身上。
表面处理包括除锈、打磨和清洗等工序。
首先,需要对车身进行除锈处理,以去除表面的铁锈和污垢。
然后,进行打磨,使车身表面平整光滑。
最后,进行清洗,去除表面的灰尘和油脂,为后续的喷涂工作做好准备。
2. 底漆喷涂底漆是涂装过程中的第一层涂料,它能够填平车身表面的小裂纹和坑洞,增加涂层的附着力。
底漆喷涂需要使用专业的喷涂设备,将底漆均匀地喷涂在车身上。
底漆一般需要经过一段时间的干燥,以保证其质量和性能。
3. 面漆喷涂面漆是涂装过程中的第二层涂料,它是汽车外观的主要颜色层。
面漆喷涂需要根据设计要求选择合适的颜色和效果。
喷涂面漆时需要注意喷涂的均匀性和厚度的控制,以保证涂层的质量和外观效果。
4. 清漆喷涂清漆是涂装过程中的最后一层涂料,它能够增加涂层的光泽和硬度,同时起到保护面漆的作用。
清漆喷涂时需要注意喷涂的均匀性和厚度的控制,以保证涂层的质量和外观效果。
三、涂装材料选择汽车车身涂装工艺中使用的涂料主要包括底漆、面漆和清漆。
涂料的选择应根据汽车的用途、环境条件和设计要求等因素来确定。
1. 底漆底漆应具有良好的附着力、填充性和耐腐蚀性,能够有效地填平车身表面的小裂纹和坑洞,增强涂层的附着力。
常见的底漆有环氧底漆、丙烯酸酯底漆和聚氨酯底漆等。
2. 面漆面漆应具有良好的光泽、颜色稳定性和耐候性,能够满足汽车外观的设计要求。
常见的面漆有溶剂型面漆、水性面漆和粉末面漆等。
3. 清漆清漆应具有良好的光泽、硬度和耐候性,能够保护面漆不受外界环境的影响。
常见的清漆有溶剂型清漆和水性清漆等。
车身工艺介绍2016

—Page20
汽车车身工艺介绍-焊接工装
内部材料 注意保密
每个工装都是由这些单 元组合而成的。这些单 元又由更小的单元组成。
—Page21
汽车车身工艺介绍-焊接工装
内部材料 注意保密
—Page22
汽车车身工艺介绍-焊接工装
L-block
内部材料 注意保密
pin
Rough locator
Tighten bolt
—Page12
车身工艺介绍-螺柱焊
内部材料 注意保密
提弧螺柱焊接是把金属螺柱结合到车身零件上的工艺。 螺柱焊接所需的热量是通过螺柱末端和车身钢板之间提弧形成的。 当接触面由电弧加热后,螺柱被压合至板材。 由于不同的螺柱需要不同的螺柱焊枪,产品设计的时候,应该尽量减少螺柱的 种类。
—Page13
Mounting bracket riser
Anti-rotator pin retainer
shim
datum
—Page23
汽车车身工艺介绍-GATE总拼台
内部材料 注意保密
总拼台从功能上来讲,都是为了实现对整车拼焊的定位,这是整个车身焊接工 装中最重要的一个工位,其机械、控制的复杂程度也最高。 目前有固定式总拼台,开放式总拼台等技术,开放式的柔性相对最高,占地最 少 对modular build和layer build来讲,其总拼台的设计理念完全相同 layer build对总拼工位的定位焊点数量要少于modular build的总拼台
2018/10/21
—Page28
内部材料
Layer build双总拼结构
注意保密
SV71项目采用了乘用车的Layer build (双总拼)设计结构;这在国内商用车 行业是首次运用
汽车车身涂装工艺及其质量控制(全文)
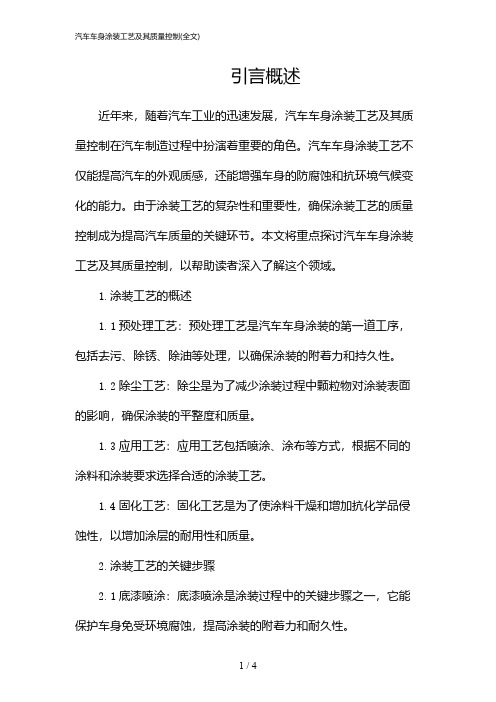
引言概述近年来,随着汽车工业的迅速发展,汽车车身涂装工艺及其质量控制在汽车制造过程中扮演着重要的角色。
汽车车身涂装工艺不仅能提高汽车的外观质感,还能增强车身的防腐蚀和抗环境气候变化的能力。
由于涂装工艺的复杂性和重要性,确保涂装工艺的质量控制成为提高汽车质量的关键环节。
本文将重点探讨汽车车身涂装工艺及其质量控制,以帮助读者深入了解这个领域。
1.涂装工艺的概述1.1预处理工艺:预处理工艺是汽车车身涂装的第一道工序,包括去污、除锈、除油等处理,以确保涂装的附着力和持久性。
1.2除尘工艺:除尘是为了减少涂装过程中颗粒物对涂装表面的影响,确保涂装的平整度和质量。
1.3应用工艺:应用工艺包括喷涂、涂布等方式,根据不同的涂料和涂装要求选择合适的涂装工艺。
1.4固化工艺:固化工艺是为了使涂料干燥和增加抗化学品侵蚀性,以增加涂层的耐用性和质量。
2.涂装工艺的关键步骤2.1底漆喷涂:底漆喷涂是涂装过程中的关键步骤之一,它能保护车身免受环境腐蚀,提高涂装的附着力和耐久性。
2.2静电喷涂:静电喷涂是一种高效的涂装工艺,通过静电作用使涂料均匀附着在车身表面,提高涂装的质量和效率。
2.3清洗和除尘:清洗和除尘是涂装过程中不可忽视的步骤,它能够确保涂装表面的洁净度和平整度,提高涂装的质量。
2.4高温固化:高温固化是为了加速涂料的固化过程,提高涂装的耐久性和表面硬度。
2.5涂层涂装:涂层涂装是最后一道工序,它通过涂布或喷涂方式,使车身涂装具有优良的表面质感和外观效果。
3.汽车车身涂装质量控制的方法3.1人工检验:人工检验是质量控制过程中最基本的方法之一,通过人工目视检查涂装的质量、颜色和涂装缺陷等,确保涂装质量达到要求。
3.2无损检测:无损检测是一种通过磁粉、超声波、射线等非破坏性检测方法,检测涂装中是否存在隐藏的缺陷和质量问题。
3.3自动化检验:自动化检验利用先进的机器视觉和图像处理技术,精确地测量涂装的厚度、粗糙度等参数,提高涂装质量的一致性和准确性。
车身制造工艺(3篇)

第1篇随着汽车工业的快速发展,车身制造工艺作为汽车制造过程中的重要环节,其技术水平和质量直接影响到汽车的整体性能和安全性。
本文将从车身制造工艺的概述、主要工艺流程、关键技术和质量控制等方面进行详细阐述。
一、车身制造工艺概述车身制造工艺是指将车身零件按照一定的顺序和方法,通过各种加工设备和工艺手段,将其组装成完整车身的过程。
车身制造工艺主要包括车身焊接、车身涂装、车身装配等环节。
车身制造工艺的发展经历了从手工制作到自动化生产的过程,其技术水平和自动化程度不断提高。
二、车身制造工艺流程1. 车身焊接车身焊接是车身制造工艺的核心环节,主要包括车身结构焊接、车身覆盖件焊接和车身骨架焊接。
车身结构焊接是指将车身骨架的各个零件通过焊接连接成整体;车身覆盖件焊接是指将车身覆盖件与车身骨架焊接在一起;车身骨架焊接是指将车身骨架的各个零件焊接成一体。
2. 车身涂装车身涂装是车身制造工艺的另一个重要环节,主要包括底漆、中涂漆和面漆的涂装。
底漆起到防锈、防腐的作用;中涂漆起到增强车身涂层附着力、提高车身涂层耐候性的作用;面漆起到美化车身外观、提高车身涂层耐久性的作用。
3. 车身装配车身装配是指将车身焊接、涂装后的各个零件按照一定的顺序和方法组装成完整车身的过程。
车身装配主要包括车身内饰装配、车身外饰装配、车身电气系统装配等。
三、车身制造关键技术1. 自动化焊接技术自动化焊接技术是车身制造工艺的核心技术之一,主要包括激光焊接、电阻点焊、气体保护焊等。
自动化焊接技术可以提高焊接质量,提高生产效率,降低生产成本。
2. 高精度冲压技术高精度冲压技术是车身制造工艺的基础,主要包括冷冲压、热冲压等。
高精度冲压技术可以提高车身覆盖件的尺寸精度和形状精度,为后续的焊接、涂装等环节提供保障。
3. 车身涂装技术车身涂装技术是车身制造工艺的关键技术之一,主要包括电泳涂装、喷涂涂装等。
车身涂装技术可以提高车身涂层的附着力、耐候性、耐腐蚀性等性能。
汽车车身 新制造工艺讲解

排样时需要考虑因素: (1)尽量减少废料,提高材料利用率; (2) 保证制作质量,单向弯曲应按弯曲线与板材轧制方向垂直剪裁;
双向弯曲件曲线应按板材轧制方向45度剪裁。 (3) 尽量做到剪切连续,操作安全,劳动强度低。
3、 剪切下料
按排样图将钢板剪切成各种各样形式的冲压件毛坯。
全自动化冲压生产线是在自动化单机的基础上,配置工序间零件输送装置、 翻转(或转位)装置、废料排除装置等由控制装置统一协调各单机和各种装置的 动作,使各工件按规定的程序自动地逐步进入各种冲压工位,全部冲压成型而被送出。
1、压力机单机机械化和自动化
特点—安装自动化上、下料装置
图1-25 接件机械手
图1-26 气动摇臂式机械手
图1-4几种典型的弯曲件
a-模具压弯;b-滚弯;c-折弯;d-拉弯
图1-5 弯曲件的加工形式
1. 弯曲变形过程及变形特点
1) 弯曲变形过程分为四个阶段
表1-5 板料弯曲变形工艺过程分析
2) 弯曲变形特点
变形区部位:主要在弯曲件的圆角部分,正方形网格 变成了扇形
变形特点:应变中性层纤维长度不变,外侧区伸长, 内侧区缩短
上:凸模不能进入凹模
拉深深度尽可能浅
下: 凸模能进入凹模
尽量采用垂直修边 工艺补充部分尽量小
图1-19 覆盖件的凹形 决定拉深方向
(3) 压边面
压边面指板料在凹模圆角以外的法兰部分,
由工件本体部分或工艺补充部分组成,其应是平
面或曲率较小的曲面,不允许有大的起伏或拐点。
在拉伸成形的过程中,压边面的材料被逐渐 (a) 拉入凹模腔内,转化为覆盖件形状。
图1-1 典型的冲压成形工序
车身的工艺流程
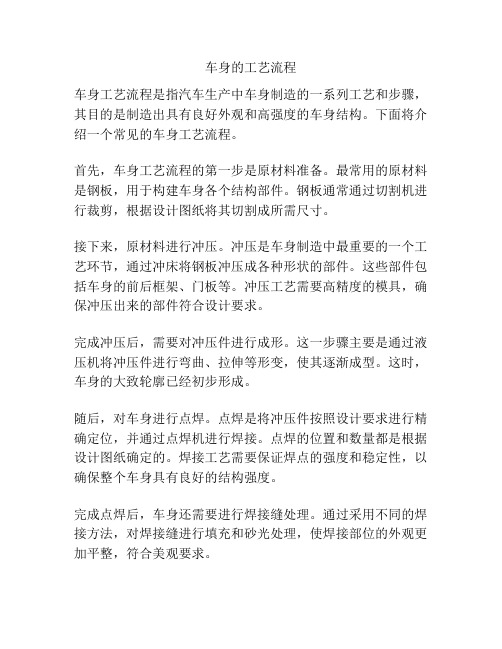
车身的工艺流程车身工艺流程是指汽车生产中车身制造的一系列工艺和步骤,其目的是制造出具有良好外观和高强度的车身结构。
下面将介绍一个常见的车身工艺流程。
首先,车身工艺流程的第一步是原材料准备。
最常用的原材料是钢板,用于构建车身各个结构部件。
钢板通常通过切割机进行裁剪,根据设计图纸将其切割成所需尺寸。
接下来,原材料进行冲压。
冲压是车身制造中最重要的一个工艺环节,通过冲床将钢板冲压成各种形状的部件。
这些部件包括车身的前后框架、门板等。
冲压工艺需要高精度的模具,确保冲压出来的部件符合设计要求。
完成冲压后,需要对冲压件进行成形。
这一步骤主要是通过液压机将冲压件进行弯曲、拉伸等形变,使其逐渐成型。
这时,车身的大致轮廓已经初步形成。
随后,对车身进行点焊。
点焊是将冲压件按照设计要求进行精确定位,并通过点焊机进行焊接。
点焊的位置和数量都是根据设计图纸确定的。
焊接工艺需要保证焊点的强度和稳定性,以确保整个车身具有良好的结构强度。
完成点焊后,车身还需要进行焊接缝处理。
通过采用不同的焊接方法,对焊接缝进行填充和砂光处理,使焊接部位的外观更加平整,符合美观要求。
接下来,对车身进行防腐处理。
防腐处理是为了保护车身免受腐蚀,延长其使用寿命。
可以采用喷涂、电泳等方式,将特殊的防腐漆涂覆在车身上,并通过烤炉进行固化。
最后一步是车身的涂装。
涂装是车身制造中最关键的环节之一,决定了整车的外观质量和色彩效果。
涂装工艺采用喷涂机对车身进行上色,先进行底漆喷涂,然后进行面漆喷涂,最后进行清漆涂覆。
以上是一个常见的车身工艺流程,每个环节都需要高度精确的操作和控制,以保证车身的质量和性能。
随着技术的进步,车身工艺流程也在不断改进和完善,以适应市场需求和提高生产效率。
车身的工艺流程

车身的工艺流程
《车身的工艺流程》
车身作为汽车的重要组成部分,其制作工艺流程十分复杂,需要经过多道工序和精密加工。
下面将从钣金加工、焊接、喷涂和总装等几个方面简要介绍车身的制作工艺流程。
首先,钣金加工是车身制作的第一步。
在这一过程中,车身的轮廓和零部件会根据设计图纸进行切割、冲压和折弯。
这些加工过程需要高精度的设备和严格的工艺要求,以确保车身的尺寸和质量达到设计标准。
其次,焊接是车身制作的关键环节。
通过气体保护焊、焊丝焊接和激光焊接等方式,将钣金加工好的零部件进行组装,形成车身的骨架结构。
焊接过程需要保证焊接点的强度和密封性,以确保整个车身结构的稳固和安全。
然后,喷涂是车身制作的另一个重要环节。
通过喷涂工艺,对车身进行底漆、面漆和清漆的涂装,以确保车身的外观和防腐蚀性能。
喷涂工艺需要在无尘车间进行,利用高压空气将漆料均匀喷涂在车身表面,并通过烘干和抛光等环节,使车身的表面光滑平整,色彩明亮。
最后,总装环节将各个部件组装到车身骨架上,形成完整的汽车车身。
在这一过程中,需要对各个部件进行精确的安装和调试,确保车身的各项功能正常、耐久性好。
总之,车身的制作工艺流程需要经历多道复杂的工序和严格的质量要求,以确保车身的质量和性能符合设计标准。
只有这样,才能生产出安全、美观、耐用的汽车车身。
车身工艺介绍

车身工艺介绍嘿,朋友们!今天咱们来聊聊车身工艺这档子事儿。
您知道吗,每次在路上看到那些飞驰而过的汽车,我就忍不住琢磨它们那漂亮的车身是咋弄出来的。
就像上次我去一家汽车工厂参观,那场面,真叫一个震撼!咱先来说说车身材料吧。
现在的车身可不简单,用的材料那是五花八门。
有高强度钢,这玩意儿结实得很,能在关键时刻保护咱们的安全;还有铝合金,轻得很,能让车子跑起来更轻快,还省油呢!比如说一辆普通的家用轿车,它的车架可能用的就是高强度钢,这样在发生碰撞时,就像给咱们装了个坚固的保护罩。
而像发动机盖这类地方,可能就会用上铝合金,减轻车头重量,操控起来更灵活。
再讲讲冲压工艺。
这就好比做糕点,把一块大面团压成各种形状。
汽车厂里面的冲压机器那可厉害啦,巨大的冲头“哐哐哐”几下,就能把一大块钢板变成车门、引擎盖这些零部件的形状。
我在工厂里看到那巨大的冲压机工作时,震得地面都有点微微颤抖,那声音,“轰轰”作响,感觉特别带劲!然后是焊接工艺。
您想想,把一个个冲压好的零部件拼接在一起,这得需要多精细的活儿啊!现在的焊接技术那是越来越先进,有激光焊接、点焊等等。
激光焊接就像是给车身缝了一道看不见的线,特别美观而且牢固。
记得那次在工厂,我看到工人师傅们戴着护目镜,专注地操作着焊接设备,火花四溅,就像过年放的烟花,可漂亮啦!还有涂装工艺。
这就像是给车身化妆,让它变得漂漂亮亮的。
先要经过预处理,把车身表面清理得干干净净,不能有一点灰尘和杂质。
然后就是喷漆,一层又一层,要保证颜色均匀、光滑。
有一次我在路上看到一辆刚喷完漆的新车,在阳光下闪闪发光,那颜色,简直太迷人了!最后是总装工艺。
这可是把所有的零部件都装到车身上,让车子成为一个完整的整体。
从内饰到发动机,从座椅到轮胎,每一个步骤都要精准无误。
我在工厂看到工人们熟练地操作着工具,有条不紊地进行着装配工作,那认真的劲儿,让人不得不佩服。
总的来说,车身工艺就像是一场精心编排的舞蹈,每个环节都要配合得天衣无缝,才能打造出一辆性能优越、外观漂亮的汽车。
- 1、下载文档前请自行甄别文档内容的完整性,平台不提供额外的编辑、内容补充、找答案等附加服务。
- 2、"仅部分预览"的文档,不可在线预览部分如存在完整性等问题,可反馈申请退款(可完整预览的文档不适用该条件!)。
- 3、如文档侵犯您的权益,请联系客服反馈,我们会尽快为您处理(人工客服工作时间:9:00-18:30)。
sub assembly
Closure Parts Closure Parts
门盖分总成
Deck Lid
Rear Door RH
Front Door RH Fender RH To Next Process Front Door LH Hood Fender LH
Rear Door LH
Vehicle Manufacturing Engineering
M/C SUB ASM
Vehicle Manufacturing Engineering
Body Assembly Process
Under body sub assembly UB(地板) UR(地板补焊)
Under body
Under Body ASM Rear Floor Front Floor Motor Compartment
Framing (Modui)
Roof
Shelf
Rear End Body Side RH
To Next Process Framing (Marriage)
Under Body ASM Body Side LH
Vehicle Manufacturing Engineering
Body Assembly Process
Vehicle Manufacturing Engineering
车间B+U的输入
• 管路排设要求
车间的能源主要包括水、气、电;所有这些主管路的排设均在车间地面高度7米 以上;7米以下的部分由M+E供应商负责
• 焊接冷却水的要求
输入压力:0.4 MPa 输出压力:0.25 MPa 输入温度:< 24° 焊接水为闭环系统;每15米,车间提供1个焊接冷却水接口
Vehicle Manufacturing Engineering
典型生产工艺
Welding Clinch
Sealing
Hemming
Torque
• 压机(die hemming)
零件
- 前盖, 门, 后盖, 后举门等.
Inner Panel Adhesive (折边胶) Pre-punch Mastic Sealer
To Next Process
Skid (搬送用)
Vehicle Manufacturing Engineering
Body Assembly Process
Body side sub assembly (Modular Build )
BS (侧围) BSI (侧围内板) BSO (侧围外板)
Outer
framing ( Layer Build )
FO(外板总拼)
Outer framing
Body Side outer RH
Rear end
Body Side outer LH To Next Process
Vehicle Manufacturing Engineering
Body Assembly Process
Parts Loading Pre-hemming
典型生产工艺
Welding Clinch
Sealing
Hemming
Torque
• die hemming
Closure Parts
- Hood, Doors, Deck Lid, Tailgate etc.
Lower Die
Main-hemming
Pin Locator
Fix Locator
Vehicle Manufacturing Engineering
定位工装
Vehicle Manufacturing Engineering
定位工装
Vehicle Manufacturing Engineering
开放式总拼Open Gate
Gate:用来安装定 位元件
Body Assembly Process
前围 分总成
侧围内板 分总成
侧围外板 分总成
四门两盖 分总成
底板分总成
内总拼
外总拼
B-LINE
Vehicle Manufacturing Engineering
Body Assembly Process
Motor compartment MC(发动机舱)
•
气体保护焊 (MAG Welding)
保护气体 焊枪 焊机
自动送丝系统
Vehicle Manufacturing Engineering
典型生产工艺
Welding
Clinch Sealing Hemming Torque
•
激光焊 (Laser Welding)
Laserbeam
Pressure Roller Device
Vehicle Manufacturing Engineering
输送方式
SHUTTLE输送线
EMS小车
Vehicle Manufacturing Engineering
雪橇输送系统
车身 概况
车身 焊装 过程
车身 主要 设备
典型 加工 工艺
车身 新技 术
Vehicle Manufacturing Engineering
• 气源的要求
•输入压力:0.6 MPa
•气源为开环系统;每15米,车间提供1个气源接口
Vehicle Manufacturing Engineering
车间B+U的输入
• 电源的要求
• 车间使用的电压分380V和220V • 电源的分配采用母线+插接箱的结构;
• 母线分为焊接母线和清洁母线;焊接母线的作用是为焊接设备提供电源供应;清 洁母线的作用是为照明和控制元器件提供电源供应;1台焊机需要1个插接箱;1 个控制箱需要1个插接箱
D06\16 BSI
SGM308 U/B
Hood
D06 D16 BSO SGM 308 BSO
D06\D16 U/B Material Storage
Phase I only
Material Storage Phase I only
Deck lid
Material Storage
T/G
Material Storage
Center station: 用来定位地板
Gate support: 用来移动Gate
Transfer System:用 来纵向移动Gate
Vehicle Manufacturing Engineering
Y approach device: 用来横向移动gate, 并将Gate锁定
开放式总拼Open Gate
典型加工工艺
Welding
Hemming
Sealer
Torque
Clinch
Vehicle Manufacturing Engineering
典型生产工艺
Welding Clinch Sealing Hemming Torque
电源
• 电阻焊 (spot weld) 电阻焊是车身车间的主要焊接工
焊接控制箱 C型焊枪
悬挂平衡系统
艺,我们选用了带自馈系统的梅
达焊接控制器,保证我们的焊接 质量,目前所有车型焊点合格率 在99.3%以上。
焊接电缆 焊接变 压器
冷却水系统
气路系统
X型焊枪
手工焊枪
Vehicle Manufacturing Engineering
典型生产工艺
Welding Clinch Sealing Hemming Torque
Pressure Pad Sealer Gun Main Punch
Sealing Inner Loading
Bending:45° Hemming Machine
Outer Panel
Lower Die
Parts Loading Guide Vehicle Manufacturing Engineering
Roof
Side panel outer
95°
4
Vehicle Manufacturing Engineering
典型生产工艺
Welding
Clinch
Sealing
Hemming
Torque
•
铆接(Clinch)
– Clinch是采用自铆接的方式,来实现板材和板材之间的连接。
– 与点焊相比,clinch的费用可以节省30%~60% – 与点焊相比,clinch的强度只有焊点的50%~70%;但是其抗疲劳强度远远高于焊点。因此, clinch工艺比较多的应用在对强度要求不高的门盖区域。 – 铝材,多采用clinch的工艺
Body Assembly Process
Body in White (Fitting) FITTING(调整线 调整门盖安装 的间隙等)Door RH Front Door RH Fender RH to Paint Shop Hood Rear Door LH
Roof
and brace loading ( Layer Build )
Roof
RSP或RL(补焊线)
Roof
brace
To Next Process (Respot)
brace
Vehicle Manufacturing Engineering
Body Assembly Process
Closure
电阻点焊 (spot weld) 的概念
加压 : 180 ~ 300 Kg・n
Weld Gun
加 压
通 电 1 Spot Weld Time Manual = 2.0 ~ 4.0 Sec. Robot = 1.5 ~ 3.0 Sec.