镀镍溶液净化方法
化学镀镍老液中镍磷的处理与回收

化学镀镍老液中镍、磷的处理与回收化学镀是指用化学还原剂使金属离子在具有催化活性的镀件表面上形成金属镀层的一种化学处理方法。
化学镀镍(又称无电镀镍)是一种有效提高工件耐蚀性和耐磨性的表面处理技术。
常用的以次亚磷酸盐为还原剂的化学镀镍新镀液的主要成分为镍盐、次亚磷酸盐,此外还含有PH调节剂、稳定剂、润滑剂和光亮剂等有机成分。
化学沉淀法是常用的处理含重金属废水的方法,采用苛性钠、石灰纯碱调节老化液的PH大于8,则可以生成NI(OH)2,通过静止后分离出沉渣、达到老化液中去除镍的目的,另外,硫化亚铁、硫化氨基甲酸二甲酯(DTC)、不溶性淀粉黄源酸酯(ISX)等也可以作为沉淀剂用于含镍废水的处理,通常是处理镍浓度小于500/mgL-1的含镍废水。
化学镀镍老化液中的磷可以采用化学氧化沉淀法处理,即利用高猛酸钾、过氧化氢等氧化剂将化学镀盐,然后再用沉淀剂使磷酸盐沉淀,从而减少废液中总磷的排放量。
化学沉淀法处理含镍、磷废水会产生大量沉渣,如处置不当会产生二次污染,目前对沉渣的处理除填埋外没有更好的方法。
2 试验部分2.1 主要试剂Ca(OH)2、H2SO4、CA(CLO)2等均为国产分析纯试剂。
2.2 主要仪器PHS-2酸度计,721-分光光度计,磁力温控搅拌器。
2.3 镍的去除与回收方法取老化液,边搅边定量加入15%的Ca(OH)2根据需要的应一定时间(如1h,2h)后停止搅拌,过滤,分析滤过液中的镍含量,计算镍的去率,溶液有待进一步处理;所得沉淀经120摄氏度下烘干、称重后用H2SO4溶出其中的镍,再次过滤,保留得到的含硫酸镍溶液,沉淀则成为最终废弃物。
2.4 磷的去除与回收方法取一定体积去除镍后的化学镀镍老化液,边搅拌边加入Ca(CLO)2粉末,反应一段时间后,停止搅拦,过滤后液内总P浓度;测定沉淀中Ni、p含量。
2.5 Ni总P的分析方法Ni、总P的分析方法参照《水与废水监测分析方法》。
3结果与讨论在室温及PH-12时,延长反应时间对化学镀镍老化液中镍的去除率有明显影响,试验中可以看出,反应1h后溶液中残余镍浓度为10.9mgL。
电镀镍溶液 除杂剂

电镀镍溶液除杂剂
电镀镍溶液除杂剂:
电镀镍溶液中的杂质会影响电镀质量和工艺效果,因此使用除杂剂是非常重要的。
以下是几种常用的电镀镍溶液除杂剂:
1. 酸洗剂:酸洗剂可以用来去除镍溶液中的氧化物和有机杂质。
常用的酸洗剂有硝酸、硫酸、盐酸等,可以根据不同情况选择合适的酸洗剂。
2. 氧化剂:氧化剂可以用来去除镍溶液中的金属杂质。
常用的氧化剂有过氧化氢、高锰酸钾等,可以在一定温度和时间条件下进行氧化反应,使金属杂质转化为不溶性沉淀,从而实现除杂的目的。
3. 螯合剂:螯合剂可以与镍溶液中的金属杂质形成配合物,使其变得稳定并易于去除。
常用的螯合剂有乙二胺四乙酸(EDTA)、乙二胺四乙二酸(EDDHA)等,可以有效去除溶液中的金属离子。
4. 还原剂:还原剂可以将镍溶液中的氧化性杂质还原为可溶性或可
挥发性物质,从而去除杂质。
常用的还原剂有亚硝酸钠、二硫化氢等。
5. 过滤器:在电镀镍溶液中使用过滤器可以去除悬浮颗粒和杂质,提高溶液的纯度。
常用的过滤器有滤纸、滤网、活性炭等,根据杂质的大小和性质选择适当的过滤器。
在使用除杂剂时,需要根据具体情况选择合适的剂量和处理时间,并注意操作安全。
同时,定期检测电镀镍溶液的杂质含量,以保持溶液的质量和稳定性。
镀镍溶液净化方法

镀镍溶液净化方法1.油脂和有机物去除油脂和有机物是常见的溶液污染物,可以使用油脂分解剂或表面活性剂将其分离出来,然后使用沉淀剂将其沉淀下来。
此外,也可以使用活性炭吸附的方法去除溶液中的有机物。
2.悬浮物去除镀液中的悬浮物会影响镀液的均匀性和镀层的质量。
可以通过使用过滤设备,如压滤机、离心机或砂滤器,将悬浮物分离出来。
另外,也可以使用沉降剂或絮凝剂将悬浮物聚集起来,然后进行沉淀或过滤处理。
3.无机盐去除溶液中的无机盐会随着镀液的循环和水分的挥发而逐渐积累,影响镀层的质量和沉积速度。
常用的无机盐去除方法包括电析、电渗析和逆渗析。
电析是利用电解技术,将无机盐通过膜层隔离和转移,从而实现去除的目的。
电渗析则是利用电场作用,通过离子的迁移,将无机盐从溶液中分离出来。
逆渗析则是利用半透膜,将溶液和纯水通过膜的选择性透过性,实现无机盐的去除。
4.酸碱中和和中性化处理镀液常常需要进行酸碱中和和中性化处理,以调节pH值和稳定镀液。
当镀液过酸或过碱时,不仅会影响镀液的稳定性,还会影响镀层的质量。
因此,可以使用酸碱中和剂或中性化剂进行处理,使镀液的pH值处于合适的范围内。
5.电解沉淀和电解氧化一些难以处理的溶液污染物或杂质可以通过电解沉淀和电解氧化的方法去除。
电解沉淀是将杂质通过电解反应的沉积作用,沉淀到电极上,然后将沉积物分离出来。
电解氧化则是利用电极的氧化作用,将有机物或杂质氧化分解为无害的物质,从而去除溶液中的污染物。
在实际操作中,可以根据镀液的具体情况和不同的污染物选择合适的净化方法。
此外,定期检测镀液的组成和性能,以及对镀液进行适时的补充和更新,也是保持镀液稳定性和提高镀液净化效果的重要措施。
镀镍溶液循环过滤的原理

镀镍溶液循环过滤的原理镀镍溶液循环过滤的原理是通过机械设备将溶液循环引流,经过过滤器进行过滤,去除其中的杂质和污染物,然后将干净的溶液重新循环使用。
镀镍溶液是通过电解镍的方法将镍金属沉积在工件表面上,来进行镀镍的过程。
在镀镍溶液中,通常会添加一些镀液添加剂,如有机添加剂、胶体添加剂等,用于提高镀层的质量和光泽。
然而,在镀镍溶液中存在着一些杂质和污染物,如金属离子、机械杂质等,这些杂质会对镀层质量产生不良影响。
为了保证镀层质量和延长溶液的使用寿命,需要对镀镍溶液进行循环过滤。
镀镍溶液循环过滤的设备主要包括过滤器、循环泵和管道系统。
过滤器是镀镍溶液循环过滤的核心设备,其作用是将溶液中的杂质和污染物过滤掉。
过滤器一般采用精密过滤器或滤芯,通过滤纸、滤网或滤布等材料,将溶液中的固体颗粒和悬浮物拦截下来,使干净的溶液通过。
循环泵是将溶液引流和循环的机械设备,其作用是通过机械能将溶液流动起来,并将溶液从源头输送到目标地点。
循环泵在循环过程中产生流动的动力,使溶液通过管道系统流动,经过过滤器进行过滤。
管道系统是将溶液从源头引流到目标地点的系统,包括进水管道、回水管道和过滤器的连接管道等。
管道系统要保持良好的密封性和流动性,以保证溶液能够顺畅地循环流动,并经过过滤器进行过滤。
镀镍溶液循环过滤的工作原理是通过循环泵将镀镍溶液从源头引流到过滤器,然后经过过滤器进行过滤。
在过滤器中,溶液经过滤材料的作用,将杂质和污染物拦截下来,使干净的溶液通过。
经过过滤的溶液再经过管道系统,回流到镀镍槽中,循环使用。
循环过滤可以有效地去除镀镍溶液中的杂质和污染物,提高镀层质量和光泽。
同时,循环过滤还可以延长镀液的使用寿命,减少资源的浪费。
通过循环过滤,镀镍溶液可以保持一定的清洁度和稳定性,提高镀镍的效率和质量。
需要注意的是,在镀镍溶液循环过滤过程中,还需要定期对过滤器进行清洗和更换滤芯等维护工作,以保证过滤效果和设备的正常运行。
此外,还需要合理控制镀液的工作温度和pH值等条件,以提高镀液的稳定性和镀层的质量。
镀镍溶液中杂质的影响和处理方法

镀镍溶液中杂质的影响和处理方法1.镀镍溶液对杂质的敏感性较强,少量的杂质就会影响镀镍溶液的稳定性和镍镀层。
:工重镀,造成直接经济{损失。
下面我佗们将镀镍溶液中较常见的杂质和处理方法简介如下,以供读者参考。
2.1)铜在镀镍溶液中,铜是最为常见的杂质。
铜主要是由阴阳极导电铜棒、镍板的铜挂勾上产生。
,.—的铜绿和铜或黄铜镀件掉落到镀槽中、又未及时打捞起来造成腐蚀等原因而带人的。
(2)锌镀镍溶液中的锌杂质主要是从镀件那里带入而来的,例如电镀黄铜件,特别是电镀锌合所以,金压铸件。
由于镀件掉落到镀槽中,未及时打捞出 ek来,这样在酸性镀镍溶液中锌压铸件很快被腐蚀,会有大量的锌离子进入镀液中。
含锌量在20- 影响,权60mg/L范围内,能对镍镀层起光亮作用。
但这种光亮镀层的力学性能篛碱作用3增加而增大深圳电镀设备的。
锌离子超过这一范畴,镀乓值,而黑,且会产生针孔麻点,:液pH值较高时,刚’Il差更容易出现这一现象。
《淀法,总形式吸附在阴极表面,雪度较大时,形成氢薑氧化锌的几率会更多,所以在阴极上的吸附也随着 y。
,Jb增多,因而我们在镀件上可以看的区域,针孔现象出现得更多。
(3)铁铁是镀镍溶液中最常见的杂质之—,这是因为需镀镍的大多数零件是铁制品。
铁零件在酸洗后进镀槽前尽管表面锈已去除,但氧化膜在很短时间内就能形成,这肉眼不易看出的是氢氧化亚铁[Fe(OH)2],这层薄的氧化膜,在入槽时接触到酸性镀镍溶液和挂上阴极棒通电的极短时间内,就会发生溶解而使铁离子珪人到镀液中,其中管状零件尤甚。
另外,铁零件在电镀过程中难免会掉落到镀槽中,也会发生腐蚀,这样就会有铁离子进入。
所以,镀镍溶液中的铁杂质是不可避免的(o在一般镀镍溶液中,铁离子的允许浓度在o.05 No.08夕l,、严格来说,其实达到o.03夕L就会对镀层带:来不好严格来说,其实达到0. 03 g/L彭会对镀。
(4)六价铬镀镍溶液中有时也会碰到六价铬的污染。
在镀镍液中六价铬杂质污染及其排除方法

Cr 2 3 8 C 3 7 2 3 + H O + H =2 r+ H 0+ 02 O7 f
表j
待双氧水分解完毕后 ,然后  ̄ 5 a J %N OH,提高镀 D 液的p 值 ,于 是三价 铬 形成 氢氧化 物胶 体 ,再加 入 H
面;
工
程j
资
讯 ห้องสมุดไป่ตู้
置
( 6)用赫尔槽试验调整光亮剂并补加。 ( 7)继续小 电流 电解05h ,即可试镀。 . 后
4 12 保 险 粉 还 原 法 ._
用保险粉把 六价铬 还原成三价铬 ,然后 提高镀液 炭含有活性羧基A C=C=O,在 酸性至中性的条件会 的p 值 ,使 三价铬 生成 氢氧化铬沉淀 而除去 。 H
3 ,间隔 为 1 n 次 0mi,加 入2~3gL /活性 炭 ),趁热 过滤。 ( 5)分析调 整镀 液成分及p 值 后 ,小 电流 电解 H
4 h。
( 3) 入 1~3gL 性 炭 ( 3 加 入 , 间 隔 加 /活 分 次
一交 经流 验
1 n),吸 附氢 氧化铬胶体 ,静置后过滤 。 0mi 也可 以待双 氧水分解 完毕后 ,加入镀镍 综合除杂 剂 1 / ,充分搅 拌 。待数 十分 钟后 。调 整镀 液 ~2ml L 的p 值 至工 艺范 围的最 下 限 ,使 三价铬 离子 与镍 离 H 子共沉积而除去。这时无需加入活性炭 过滤 。 值得一提 的是 ,用活性炭 处理镀镍液后 。因活性
6 0—7 ℃ 。 0
一浇 经 验 交
( 加 入 1 / 或 更 多 )F S 。搅 拌3 6 2) gL( e O4 0 0 an ri 注 :添 加 01 /硫 酸 亚铁 可 处理 5mgL 六 。 . gL 6 /的
从镍电镀污泥回收的硫酸镍溶液的深度净化
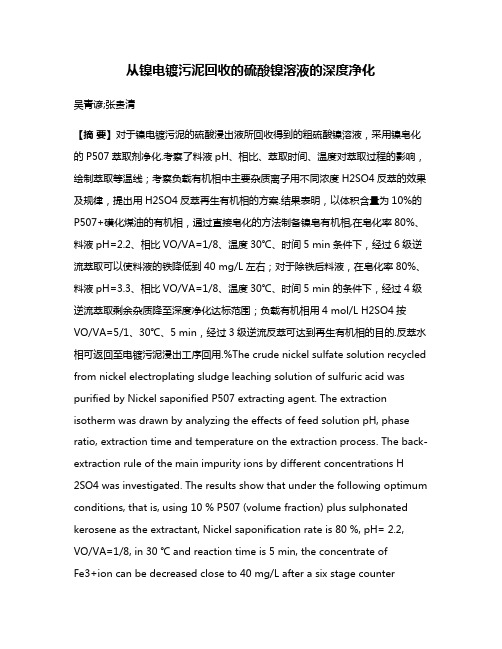
从镍电镀污泥回收的硫酸镍溶液的深度净化吴青谚;张贵清【摘要】对于镍电镀污泥的硫酸浸出液所回收得到的粗硫酸镍溶液,采用镍皂化的P507萃取剂净化.考察了料液pH、相比、萃取时间、温度对萃取过程的影响,绘制萃取等温线;考察负载有机相中主要杂质离子用不同浓度H2SO4反萃的效果及规律,提出用H2SO4反萃再生有机相的方案.结果表明,以体积含量为10%的P507+磺化煤油的有机相,通过直接皂化的方法制备镍皂有机相,在皂化率80%、料液pH=2.2、相比VO/VA=1/8、温度30℃、时间5 min条件下,经过6级逆流萃取可以使料液的铁降低到40 mg/L左右;对于除铁后料液,在皂化率80%、料液pH=3.3、相比VO/VA=1/8、温度30℃、时间5 min的条件下,经过4级逆流萃取剩余杂质降至深度净化达标范围;负载有机相用4 mol/L H2SO4按VO/VA=5/1、30℃、5 min,经过3级逆流反萃可达到再生有机相的目的.反萃水相可返回至电镀污泥浸出工序回用.%The crude nickel sulfate solution recycled from nickel electroplating sludge leaching solution of sulfuric acid was purified by Nickel saponified P507 extracting agent. The extraction isotherm was drawn by analyzing the effects of feed solution pH, phase ratio, extraction time and temperature on the extraction process. The back-extraction rule of the main impurity ions by different concentrations H2SO4 was investigated. The results show that under the following optimum conditions, that is, using 10 % P507 (volume fraction) plus sulphonated kerosene as the extractant, Nickel saponification rate is 80 %, pH= 2.2,VO/VA=1/8, in 30 ℃ and reaction time is 5 min, the concentrate ofFe3+ion can be decreased close to 40 mg/L after a six stage countercurrent extraction. After iron removal process the Nickel sulfate solution can be deep purified under the following optimum conditions, that is, 80 % saponification rate, pH = 3.3, VO/VA=1/8, in 30 ℃ and reaction time is 5 min, after a four stage counter current extraction the concentrate of the rest impurity ions can be decreased to reach the range of deep purification standard. The purification loaded organic can be stripped using 4 mol/LH2SO4 solution under the following condition: VO/VA =5/1, in 30 ℃ and reaction time is 5 min, after a four stage counter current stripping the organic phase can be reused. The tripping liquor can be reused by the stage of electroplating sludge leaching.【期刊名称】《有色金属科学与工程》【年(卷),期】2016(007)005【总页数】7页(P26-32)【关键词】P507;硫酸镍;深度净化;镍电镀污泥;镍皂化【作者】吴青谚;张贵清【作者单位】中南大学冶金与环境学院,长沙410083;中南大学冶金与环境学院,长沙 410083【正文语种】中文【中图分类】X781.1;TF111.3电镀工艺在现代工业中扮演着非常重要的角色,它能对金属、非金属材料表面进行修饰、保护并使其获得新的性能,被广泛应用到工业生产中.但是电镀工序会产生含有大量复杂金属元素的废液需要处理.电镀污泥含有多种金属离子,需要经过无害化处理才能排放,否则会对环境造成严重污染.根据电镀污泥组分不同可采用稳定/固化法,火法处理,湿法处理这3种方法处理[1-3].对于含有大量的镍等有价金属的镍电镀污泥,用湿法处理的方式回收有价金属可以使其得以再利用并达到无害化的目的.湿法处理先采用酸浸或氨浸的方法将金属离子带入水相,再通过化学沉淀或者溶剂萃取等方式提取回收需要的有价金属.由于溶剂萃取技术具备良好的选择性适用于组分复杂的溶液,所以相比沉淀法更适于提取镍电镀污泥浸出液中的有价金属[4].研究中的料液来自宁波双能固废处理厂,是经过HBL110萃取镍电镀污泥硫酸浸出液后反萃产出的粗硫酸镍溶液,料液pH值在1.25左右,阴离子为SO42-,溶液中主要的杂质元素为Fe、Zn、Cu、Cr.由于镍电镀污泥浸出液中杂质含量较高,经过HBL110直接萃镍技术处理的后产出的硫酸镍溶液依然含有一定量的杂质,所以无法直接用于硫酸镍的生产,需要对硫酸镍溶液进行深度净化[5-6].早期对于硫酸镍的净化采用的是化学沉淀法,但是由于沉淀法会导致一定量镍的损失,并且对微量杂质分离效果不理想,所以化学沉淀法不适于处理复杂组分的硫酸镍溶液.据文献报道20世纪70年代就有人开始采用溶剂萃取的方法处理粗硫酸镍溶液.常用的萃取剂有P204、P507、M5640.上海冶炼厂的杨钟林等[7]提出采用镍皂化P204处理粗硫酸镍溶液,萃取除Cu2+,Fe3+,Zn2+,达到了良好的效果.20世纪90年代初骆有钔等[8]提出采用镍皂P507净化镍阳极泥水浸溶液制取硫酸镍,证明此方法可达到良好的镍钴分离效果,产品质量达到国家标准.李学鹏等[9]提出采用M5640+P204+P507三步净化硫酸镍溶液生产镍电解液,先用M5640除铜,再用P204除铁等杂质,最后用P507深度净化除Co,得到的硫酸镍溶液可用于生产5N镍电解液.金川公司针对含铁高的硫酸镍料液,采用黄钠铁矾法除铁再用25%的P507萃取除Cu2+,Co2+,Zn2+,Mn2+等杂质得到纯净的硫酸镍溶液[10].广东银亿的肖万林等[11]的专利中采用镍皂化P204萃取除杂,然后再用镍皂P507除Co2+,Mg2+得到硫酸镍溶液可直接返回电解工序.由前人的研究成果可见,对于相似组成的粗硫酸镍溶液,通常采取两步净化的方式:先采用化学沉淀法或萃取法对铁等易分离杂质进行初步除杂分离,再根据料液组成采用选择性良好的P507深度净化除杂.实验料液无大量的铁杂质,所以实验中直接采用分离效果优异的P507用作硫酸镍料液的净化,其萃取和反萃原理为[12]:P507的萃取通过阳离子交换实现,需通过皂化将部分H+离子替换成其他阳离子来稳定萃取过程中的溶液pH.由于硫酸镍的产品标准对Na+离子含量有严格的要求,不能采用常见的Na皂化方式处理有机相,借鉴前人研究成果,实验中决定采用Ni皂化的方式制备有机相.镍皂化后的P507萃取反应为[12]:根据料液组成,为了防止铁离子随pH的升高发生水解影响萃取效率,实验中采用先除铁,再深度净化除杂的方式制备高纯度硫酸镍.1.1 实验原料与试剂P507(江西省奉新申新化工有限公司,含量大于95%),稀释剂为磺化煤油;NaOH(西陇化工股份有限公司),分析纯;六水合硫酸镍(西陇化工股份有限公司),分析纯;浓硫酸(衡阳市凯信化工试剂有限公司),分析纯;碱式碳酸镍(天津科密欧化学试剂有限公司),分析纯;粗硫酸镍溶液(宁波双能固废处理厂),成分如表1所列.1.2 实验工艺流程实验工艺流程如图1所示.1.3 实验设备125 mL梨型分液漏斗,SHZ-82恒温水浴冷冻振荡器(江苏金坛亿通电子有限公司),iCAP 7000型电感耦合等离子发射光谱仪,722S紫外可见分光光度计(上海棱技术有限公司),S312电子恒速搅拌器(上海申生科技有限公司).1.4 净化目标参考HG/T 2824-2009工业硫酸镍标准中的硫酸镍I类一等品标准[13],按料液中Ni浓度确定溶液深度净化目标如表2所列.1.5 实验方法1.5.1 P507的配制与镍皂化萃取剂按10%的体积比,量取后与作为稀释剂的磺化煤油在烧杯中混合,充分搅拌后用于皂化.将配好的萃取剂与1 mol/L的硫酸镍溶液按VO/VA=1/1的相比在烧杯中混合,用搅拌器剧烈搅拌,为了中和皂化过程中产生的H+离子,根据80%的镍皂化率条件下会产生的H+的量换算所需加入的NaOH溶液体积,在搅拌过程中缓慢滴加相应体积的NaOH溶液,继续搅拌直到沉淀消失.将皂化后的两相倒入大分液漏斗中静置,待两相澄清后放出水相.再按相比VO/VA=1/1向漏斗中加入纯水将有机相中夹带的钠离子洗脱,分相后获得镍皂P507.1.5.2 萃取实验先量取所需体积的料液加入125 m L的分液漏斗中,按照所需体积相比量取相应体积的皂化好的有机相加入有水相的分液漏斗中,将分液漏斗置于恒温水浴振荡器,根据实验要求的条件控制振荡过程,震荡结束后取出分液漏斗静置等待分相.分析萃余液中目标元素浓度并计算萃取率E1:式(1)中:Ca2是萃余液中金属浓度,g/L;Ca1是料液中金属浓度,g/L;Va2是萃余液体积,mL;Va1是料液体积,mL.1.5.3 反萃实验先量取所需体积的反萃剂溶液加入125 mL的分液漏斗中,按所需相比量取相应体积的负载有机相加入已有水相的分液漏斗,将分液漏斗置于恒温水浴振荡器中根据实验要求的条件控制振荡过程,震荡结束后取出分液漏斗静置等待分相.分析反萃液中目标元素的浓度,计算反萃率E2:式(2)中Co2是反萃后有机相负载的金属浓度,g/L;Co1是负载有机相中金属浓度,g/L;Vo2是反萃后负载有机相体积,m L;Vo1是加入的负载有机相体积,mL.1.5.4 分析方法水相中金属离子浓度采用iCAP 7000型电感耦合等离子发射光谱仪检测,负载有机相中金属离子浓度主要根据相应水相中对应离子浓度用差减法得到.负载有机相中金属离子浓度检测是先取一定量有机相滴于纸上置于烧杯中,在电炉上将其烧成灰烬,用一定量王水充分煮沸溶出,收集水相稀释定容,经过自然过滤后用检测水相中金属离子浓度的方式检测溶出的水相中的金属浓度,换算出有机相中的金属浓度.2.1 萃取除铁结果2.1.1 平衡pH对萃取的影响实验中,pH是主要控制因素.为了不增加料液中的Na+,对于料液采用在快速搅拌的条件下加入碱式碳酸镍的方式调节pH;萃取条件:VO/VA=1/1、萃取时间5 min、萃取温度30℃.平衡pH对主要杂质Fe、Cu、Cr、Zn萃取的影响如图2所示.由图2可见,金属杂质的萃取率随pH提高而提高,Fe3+在pH高于2以后萃取率高于50%,而其他金属萃取率较低.继续提高pH铁的萃取效果会继续提升,但pH继续提高到2.5以上时,铁会发生水解,此时铁的萃取率上升缓慢的同时铁的水解导致萃取效率下降,所以除铁实验采用的料液最佳pH值为2.2.2.1.2 相比对萃取的影响料液不变,用碱式碳酸镍调节料液pH至2.2;萃取条件:萃取时间10 min,萃取温度30℃,改变萃取相比VO/VA分别为1/2、1/2.5、1/5、1/10、1/20、1/40.相比对主要杂质的萃取影响如图3所示.由图3可见,随着VO/VA的降低,铁的萃取率逐渐下降,相比VO/VA高于1/10时萃取率高于50%,当VO/VA=1/2.5时能保证较高的萃取率,从单级萃取的角度考虑应该选择VO/VA=1/2.5为最佳相比,但是在实际生产中,不仅要考虑单级萃取分离效果,同时应考虑尽可能提高萃取剂的利用率以及元素的富集,故最佳相比在1/2.5到1/10的区间内选择,然后结合串级实验来确定具体相比.2.1.3 接触时间对萃取的影响料液:料液使用碱式碳酸镍将pH调到2.2;萃取条件:VO/VA=1/1、萃取温度30℃,考查的萃取时间分别为0.5、1、2、5、10 min,研究萃取时间对铁萃取率的影响,实验结果如图4所示.由图4可见,Fe3+的萃取率随时间升高而升高.从图4中可见2 min之后萃取率波动趋于平缓,为方便操作取5 min为最佳反应时间.2.1.4 萃取等温线由于Fe是本环节除杂的目标元素,所以以Fe为目标绘制操作线.料液采用宁波双能提供的料液.按照最佳条件,料液使用碱式碳酸镍将pH调到2.2;萃取条件:VO/VA=1/1、萃取时间5 min,萃取温度30℃.采用多次接触法绘制萃取等温线,如图5所示,图5中6个点从左到右分别是第1到第6次的水相和有机相中的Fe3+离子浓度.由图5可知,有机相饱和萃铁量为2.2 g/L左右.从相比实验结果可使本料液在相比大于VO/VA=1/10时铁萃取率高于50%,考虑有机相实际利用率,选择VO/VA=1/8,依照逆流萃取原理,绘制马克凯勒-齐利图,设萃余液中铁浓度为6.6 mg/L,按照相比VO/VA= 1/8绘制铁萃取的操作线,从图5可以看出,通过6级逆流萃取铁的理论萃取率可接近100%.不会在深度除杂的pH升高过程中发生水解.2.1.5 串级模拟实验实验采用7个分液漏斗模拟6级逆流萃取实验.料液采用宁波双能提供的料液.按照最佳条件,料液使用碱式碳酸镍将pH调到2.2;萃取条件:VO/VA=1/8、萃取时间5 min,萃取温度30℃.共模拟13排.取后4排萃余液分析铁浓度,计算萃取率.结果如表3所列.由表3可知,经过6级逆流萃取,萃余液铁浓度在40 mg/L左右,铁萃取率接近80%,萃余液pH= 2.4.铁的萃取率虽然未达到预期效果,但其浓度不会对后续深度除杂过程的pH调节构成影响,所以认为6级为串级萃取除铁阶段的最佳级数.2.2 深度净化结果深度净化实验采用的是除铁实验后收集的料液,料液的pH=2.5,成分如表4所列.2.2.1 平衡pH对萃取影响料液使用碱式碳酸镍调节至不同pH.萃取条件:VO/VA=1/1、萃取时间5 min、萃取温度30℃.萃取结束后测量萃余液平衡pH值,分析萃余液中含量较高的Fe3+、Cu2+、总Cr、Zn2+的浓度,计算萃取率,结果如图6所示.由图6可见当pH高于3.6时Cr、Zn2+、Fe3+的萃取率都基本达到最佳,由于料液中Cu2+含量较低,采用多级逆流萃取的工艺即可达到净化目标,所以料液的最佳萃取pH确定为3.6.2.2.2 萃取等温线由pH调节实验结果可见,主要杂质中Cu2+是最难除的杂质,故以Cu2+为目标做萃取等温线确定理论萃取级数.料液采用除铁实验中收集的萃余液,由于pH= 2.5的料液对碱式碳酸镍的利用率低下,故采用本实验使用的镍皂有机相,在VO/VA=1/10的条件下通过萃取的方式将料液pH调节到3.6左右;P507体积浓度10%,皂化率80%;萃取条件:VO/VA=1/8、萃取时间5 min,萃取温度30℃.采用多次接触法绘制萃取等温线,如图7所示,图7中3个点从左到右分别是第1到第3次的水相和有机相中的Cu2+离子浓度.由图7可见,与除铁段相同选择VO/VA=1/8,依照逆流萃取原理,绘制马克凯勒-齐利图,设萃余液中铜浓度为36 mg/L,按照相比VO/VA=1/8绘制铜萃取的操作线,通过3级逆流萃取水相中铜萃取率接近100%,萃余液中的铜含量达到除铜目标,由于料液中Zn2+含量高于Cu2+含量,为了保证萃取的效果,决定增加1级采用4级逆流萃取除杂.2.2.3 串级模拟实验实验用5个分液漏斗模拟4级逆流萃取实验.料液采用除铁后的料液.按照最佳条件,现将料液在VO/VA=1/10的条件下用萃取剂将pH调到3.3;萃取条件:VO/VA=1/8、萃取时间5 min,萃取温度30℃.共模拟12排.稳定后取后6排萃余液分析铁浓度,计算萃取率.结果如表5所列.由表5可见,通过4级逆流萃取可以将有机相中的主要杂质基本除尽,深度净化后料液成分如表6所列.由表6可见,由于深度净化时料液pH较高,镍离子部分被萃取,料液中Na+离子浓度无明显变化,其他金属杂质都被萃取完,硫酸镍溶液基本达到深度净化的要求.2.3 反萃结果实验中反萃所用负载有机相来自所有萃取实验收集汇总的负载有机相.其主要成分如表7所列.2.3.1 反萃剂的选择根据P507的萃取机理,增加H+浓度会使萃取平衡向左移动从而达到反萃的效果,为了保证体系中不含SO42-以外的阴离子,所以借鉴其他论文报道的相似硫酸体系的P507负载有机相的反萃方法,选用H2SO4溶液作为反萃剂[14].2.3.2 反萃剂H2SO4对反萃的影响.有机相采用萃取实验收集的有机相;水相:H2SO4溶液;反萃条件:温度30℃,相比VO/VA=5/1,两相接触时间5 min.反萃结果如表8所列.由表8可见,Ni2+、Cu2+、Zn2+这3种高含量的杂质都能被完全反萃,根据Fe3+的反萃率变化趋势最终选用4 mol/L的硫酸溶液作为反萃剂用于再生负载有机相.2.3.3 串级反萃实验根据酸度实验得出的结论,尝试采用4 mol/L硫酸进行4级逆流反萃的方式进行反萃实验,考察反萃效果.实验采用5个分液漏斗模拟4级逆流反萃实验.有机相采用萃取实验收集的有机相;水相:4 mol/L H2SO4溶液;实验条件:温度30℃,相比VO/VA=5/1,两相接触时间5 min.共模拟8排,取最后两排有机相分析金属浓度,结果如表9所列.由表9可见,经过4级反萃,负载有机相中的Cu2+、Ni2+、Zn2+已被反萃完全,Fe3+的含量降低至0.03 g/L,达到反萃目的.通过测量发现反萃液的pH<1,阴离子为SO42-,元素的构成与镍电镀污泥硫酸浸出液相似,所以可以考虑返回到电镀污泥酸浸工序回用.1)H2SO4体系中,P507体积浓度10%,皂化率80%;萃取条件:VO/VA=1/8、萃取时间5 min,萃取温度30℃,料液pH=2.2的条件下,经过6级逆流萃取,Fe3+的萃取率可达到80%.料液中所残留的铁离子不会在后续的深度净化工序中发生水解.2)H2SO4体系中,P507体积浓度10%,皂化率80%;萃取条件:VO/VA=1/8、萃取时间5 min,萃取温度30℃,料液pH=3.3的条件下,经过4级逆流萃取,萃余液中所有杂质的含量都已满足深度净化要求.3)用 4 mol/L硫酸溶液,在温度30℃,相比VO/VA=5/1,两相接触时间5 min的条件下,经过4级逆流反萃可达到有机相反萃再生目的,反萃后的高酸度水相可以在电镀污泥酸性浸出工序回用.【相关文献】[1]张殿彬,陈为亮,王迎爽,等.从电镀污泥中回收有价金属的研究进展[J].湿法冶金,2012(5):281-283.[2]李彩丽.含镍电镀污泥中镍的回收和综合应用[D].太原:太原理工大学,2010.[3]季文佳,黄启飞,王琪,等.电镀污泥资源化与处置方法的研究[J].电镀与环保,2010(1):42-45.[4]傅江,程洁红,周全法.电镀污泥的重金属湿法回收资源化技术及展望[J].资源再生,2009(6):47-49.[5]莫兴德,肖连生,张贵清,等.HBL110从红土镍矿加压浸出液中萃取镍的研究[J].有色金属(冶炼部分),2014(6):30-33.[6]莫兴德.红土镍矿加压浸出—直接萃取镍的研究[D].长沙:中南大学,2014.[7]杨钟林,蒋祖惠.P204镍盐萃取法净化硫酸镍溶液[J].上海有色金属,1980(3):5-10. [8]骆有钔.P507萃取法生产硫酸镍[J].有色金属(冶炼部分),1994(2): 45-46.[9]李学鹏.M5640+P204+P507萃取净化镍电解液[J].有色金属(冶炼部分),2011(12):15-17.[10]文力,徐文兵.一种硫酸镍溶液去除杂质的方法:中国,CN101126127A[P].2008-02-20.[11]肖万林,王多冬,和润秀,等.红土镍矿湿法提镍工艺中保持钠、镁、水体系平衡的方法:中国,CN102181665A[P].2011-09-14.[12]张启修,张贵清,唐瑞仁,等.萃取冶金原理与实践[M].长沙:中南大学出版社,2014. [13]HG/T2824-2009,工业硫酸镍标准[S].[14]张魁芳,曹佐英,肖连生,等.P507从硫酸体系中萃取镓的研究[J].矿冶工程,2014(6):90-93.。
光亮镍溶液高锰酸钾-活性炭净化处理

光亮镍溶液双氧水-活性炭净化处理(2008-7-11 8:34:55)光亮镍溶液双氧水-活性炭净化处理采用双氧水一活性炭净化处理光亮镀镍溶液是行之有效的大处理方法之一,但当处理工序安排不当,操作方法不严,有可能事倍功半,达不到预期效果,甚至有可能出现故障。
下面就此法作简要叙述。
(1)用5%浓度的稀硫酸将镀镍溶液的pH值调至3~3.5,此pH值条件有利于提高双氧水的氧化能力。
(2)在搅拌下缓慢地加入双氧水2~4mL/L(加入前先稀释5~10倍,以利于发挥其作用,减少损耗),继续搅拌1h,使溶液中的Fe2+氧化成Fe抖,有机杂质存在时也易被氧化,容易被活性炭吸附。
(3)加温至40℃左右,继续搅拌lh,使双氧水充分发挥氧化作用,促使Fe2+充分氧化成Fe3+2FeS04+H202+H2S04→Fe2(S04)3+2H20并促使有机杂质还原成碳。
(4)加温至70℃,在此温度条件下,使残余的双氧水充分分解,以免光亮剂遭到破坏。
△2H202→2H20+02↑(5)在搅拌下加入氢氧化镍或碳酸镍,提高pH至5.5~6,使Fe3+形成氢氧化铁沉淀Fe2(S04)3+3Ni(0H)2→2Fe(OH)2+3NiS04注意:氢氧化镍必须配制新鲜溶液,商品氢氧化镍溶解性差NiS04+2Na0H→Ni(0H)2↓+Na2S04配成后弃去上层清液,将沉淀用水清洗几遍后即可使用。
(6)加入FJ—N5去铜剂1~3mL/L,搅拌15~30min,使铜杂质沉淀。
(7)将3~5g/L化学纯粉末状活性炭用水调成糊状后加入,继续搅拌2h,使有机杂质充分被吸附除去,静止3~4h后过滤(沉淀时间不宜过长,否则有可能因脱附而影响处理效果)。
(8)调整pH值至工艺规范后试镀,如色泽正常即可补充光亮剂,并以0.1~0.2A/dm2的低电流处理,以除去残存的重金属杂质,经一定时间处理之后称取按工艺配制量的l/2的糖精,并将略高于此值的初级光亮剂溶于少量水中,在搅拌下加入槽中即可试镀。
化学镀镍废水镍离子去除方法
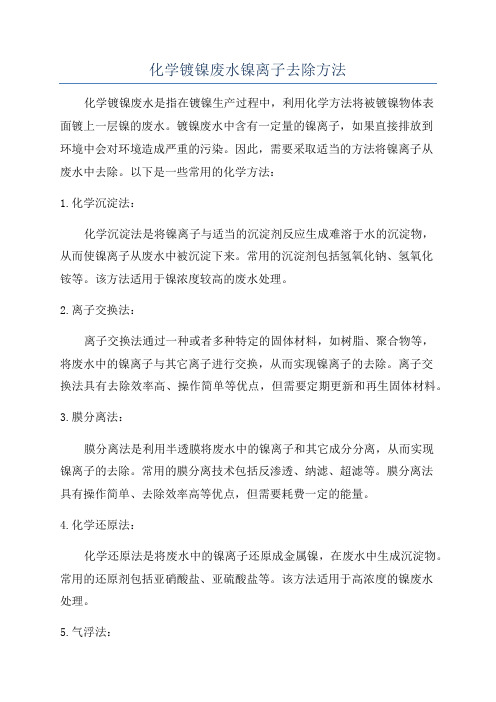
化学镀镍废水镍离子去除方法化学镀镍废水是指在镀镍生产过程中,利用化学方法将被镀镍物体表面镀上一层镍的废水。
镀镍废水中含有一定量的镍离子,如果直接排放到环境中会对环境造成严重的污染。
因此,需要采取适当的方法将镍离子从废水中去除。
以下是一些常用的化学方法:1.化学沉淀法:化学沉淀法是将镍离子与适当的沉淀剂反应生成难溶于水的沉淀物,从而使镍离子从废水中被沉淀下来。
常用的沉淀剂包括氢氧化钠、氢氧化铵等。
该方法适用于镍浓度较高的废水处理。
2.离子交换法:离子交换法通过一种或者多种特定的固体材料,如树脂、聚合物等,将废水中的镍离子与其它离子进行交换,从而实现镍离子的去除。
离子交换法具有去除效率高、操作简单等优点,但需要定期更新和再生固体材料。
3.膜分离法:膜分离法是利用半透膜将废水中的镍离子和其它成分分离,从而实现镍离子的去除。
常用的膜分离技术包括反渗透、纳滤、超滤等。
膜分离法具有操作简单、去除效率高等优点,但需要耗费一定的能量。
4.化学还原法:化学还原法是将废水中的镍离子还原成金属镍,在废水中生成沉淀物。
常用的还原剂包括亚硝酸盐、亚硫酸盐等。
该方法适用于高浓度的镍废水处理。
5.气浮法:气浮法是利用气泡将废水中的镍离子吸附到气泡上,然后将气泡带出废水,从而实现镍离子的去除。
气浮法具有操作简单、效率高等优点,但需要耗费一定的能量。
除了以上的化学方法,还可以结合生物方法和物理方法进行废水处理,以提高去除镍离子的效率和降低处理成本。
例如,可以利用微生物将镍离子转化为难溶于水的沉淀物,然后再通过沉淀或者膜分离等物理方法进行去除。
总结起来,化学镀镍废水镍离子的去除方法多种多样,可以根据实际情况选择合适的技术进行处理。
不同的方法具有不同的优缺点,需要综合考虑处理效率、成本和可操作性等方面进行选择。
化学镀镍废水处理方法汇总

化学镀镍废水处理方法汇总
化学镀镍废水处理
(一)化学镀镍废液中,若不存在络合剂或络合剂的量较少时,可直接采用氢氧化钠调节pH值,根据废液中镍离子的浓度,加入适量的NaOH,把pH调节至11以上,使镍离子沉淀为Ni(OH)2除去。
(二)对于化学镀镍废水,废水中含有柠檬酸、酒石酸、苹果酸、乳酸等络合剂,络合剂会与镍离子结合生成小分子,络合小分子在废水中很稳定,使用氢氧化钠、石灰、硫化钠、一般的液体重捕剂或者固体重捕剂均不能破坏络合剂与镍离子的结合键,镍离子难以去除。
可以加入重金属捕捉剂进行反应,使废液中的大部分镍离子和重金属捕捉剂发生螯合反应,再加入适量的高分子絮凝剂,加速不溶物的沉降,除去镍离子。
(三)而对于比较难处理的EDTA镍,有时需要在前端进行次氯酸钠氧化处理,次氯酸钠在进行简单破络以后,络合健的结合力会变弱,有利于重捕剂进行螯合反应。
(四)使用重金属捕捉剂进行处理的办法,重金属捕捉剂中含有大量的除镍基团,除镍基团在微观条件下会化变形,表面形成负电荷场,从而吸附镍离子生成沉淀。
镀镍液净化新工艺

镀镍液净化新工艺2011-10-14摘要:本文在总结前人研究的基础上,结合四年的实践经验,提出了一种镀镍液净化新工艺。
赫尔槽试验和微量元素分析试验结果表明:该工艺净化效果好,适用于解决镀镍层出现毛刺、针孔等缺陷。
关键词:镀镍液;净化中国分类号:TQ153.12 文献标识码:BA new process for purification of nickel electrolyteWU Hui( Crangzhou Zhaohe Vibration Damper Co. , Ltd. ,)Abstract: A new process for purification of nickel electrolyte was advanced based on previous studies and the author' s 4 years experience in nickel electroplating . Hull cell test and analysis of trace element show that this process has good purification result which is applicable to solve deposit defects such as burrs and pinholes in nickel plating.Keywords : nickel electrolyte ; purification1 前言19世纪末,镀镍技术已获得广泛应用。
据统计,每年镀镍消耗的镍量约占世界镍总产量的1/10。
这与镀镍层优良的物理、化学性质是分不开的。
镀镍在汽车、自行车、钟表、医疗器械和日用五金等方面应用广泛。
在镀镍生产中,由于种种原因,镍液中的各种杂质会不断积累,而杂质对镀液的影响非常敏感,因此,对镍液的定期净化显得尤其重要。
当镀镍液中含有铁、锌、铜等杂质,和加工残留的切削液、防锈油、抛光油脂、灰尘、电镀添加剂的分解物时,镀层出现针孔、麻点、粗糙、发黑、条纹,甚至脱皮等疵病(亮镍镀液对杂质尤为敏感)。
拿走,收藏好!以后别再问我镀镍液怎么大处理了
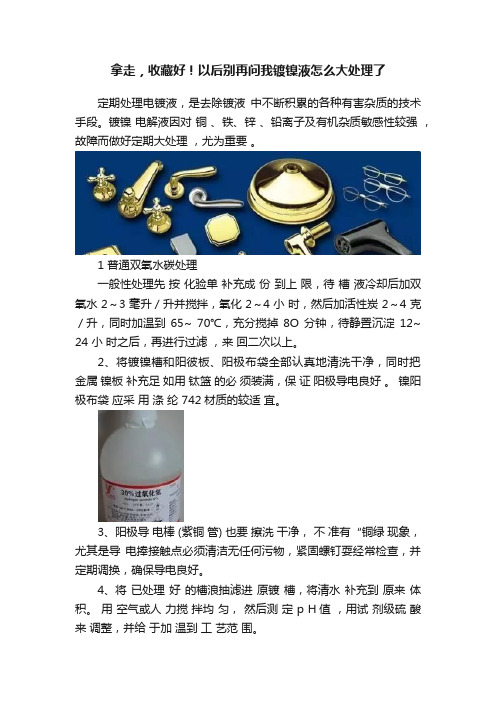
拿走,收藏好!以后别再问我镀镍液怎么大处理了定期处理电镀液,是去除镀液中不断积累的各种有害杂质的技术手段。
镀镍电解液因对铜、铁、锌、铅离子及有机杂质敏感性较强,故障而做好定期大处理,尤为重要。
1 普通双氧水碳处理一般性处理先按化验单补充成份到上限,待槽液冷却后加双氧水 2~3 毫升/升并搅拌,氧化 2~4 小时,然后加活性炭 2~4 克/升,同时加温到65~ 70℃,充分搅掉8O 分钟,待静置沉淀12~ 24 小时之后,再进行过滤,来回二次以上。
2、将镀镍槽和阳彼板、阳极布袋全部认真地清洗干净,同时把金属镍板补充足如用钛篮的必须装满,保证阳极导电良好。
镍阳极布袋应采用涤纶 742材质的较适宜。
3、阳极导电棒 (紫铜管) 也要擦洗干净,不准有“铜绿现象,尤其是导电捧接触点必须清洁无任何污物,紧固螺钉耍经常检查,并定期调换,确保导电良好。
4、将已处理好的槽浪抽滤进原镀槽,将清水补充到原来体积。
用空气或人力搅拌均匀,然后测定 p H值,用试剂级硫酸来调整,并给于加温到工艺范围。
5、在已全部处理调整好的镀镍槽里,挂上产品镀件或者铁板少量 (比平时正常生产的阴极面积少五分之一)用小电流进行电解 2~4 小时,视镀层色泽,如光亮镀镍可加入光亮剂,待正常后,再挂上正品镀件进行电镀。
二、镀镍槽液处理金属杂质的方法(1)、如镀液里有铁杂质的话,那束先将镀液用试剂硫酸把pH 值降低至 3左右,然后加入 80%的双氧水 1~2 毫升/升,将镀液充分搅拌均匀,待氧化分解2~4 小时,加温至65~ 70℃,用 20%的氢氧化钠稀溶液提高 p H 值至 6 左右,并连续搅拌 2~8 小时。
此时由于氢氧化钠的沉淀 pH 值也随着降低,故要多次测量 pH 值的变化,要保持 pH 值 6 左右,静置 8~12小时后过滤。
最后用试剂硫酸调整 p H 值在正常工艺范围,即可试镀。
在光亮镀镍槽中用双氧水处理铁杂质的同时,也可以对有机杂质进行综合处理,只要在加入双氧水氧化后,再加入 2~4克/升的活性炭边加边搅拌,加温至65~ 70℃,静置 8~ l2 小时然后过滤,既除铁又除有机杂质一举二得.用此法处理周期在 3~4个月一次.(2)、如镀液里有铬杂质的话,那要将镀液用试剂硫酸将 p H 值降低至 3以下,在搅拌的同时加入保险粉 0 4~0.8 克/升进行还原 (要看六价铬含量来定 ) 然后将镀液用 20%氢氧化钠稀溶液 (试剂级 )提高 pH 值至 5~6 加温至65~ 70℃,连续搅拌井多次测量调整 p H 值。
如何防止镀液中积累杂质并净化镀液(中)
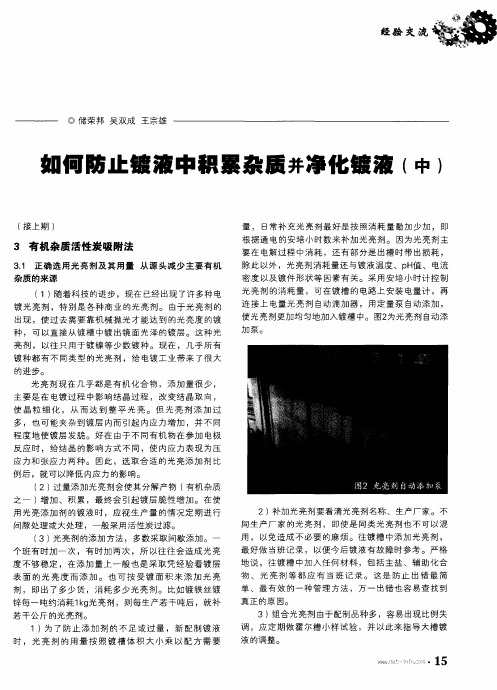
用 光亮添 加剂 的镀液 时 ,应视 生产 量 的情 况定 期进行 间隙处理 或大处理 ,一般 采用活性炭过滤。 ( 3) 光亮剂 的添加 方法 ,多数采取 间歇添 加。一
个班 有 时加一 次 ,有 时加两 次 ,所 以往往 会造成 光亮
2) 补 加光亮剂要看清光亮剂名称 、生产 厂家。不 同生产 厂 家的光亮 剂 ,即使 是同类 光亮剂 也不可 以混
边搅 拌边 缓 慢 加入 1 ~3 ml / L 双 氧 水( 3 0 %) ,搅拌 2 h
( 双氧水 反应后 的产 物是水 ,过 量的双氧 水易加 热除
有机添加 剂加入镀 液 中 ,除 了能够 改善镀层 的质 量 外 ,其本 身也会在 电镀 生产过程 中在 阳极 上氧化而
分解成 为有机 杂质。在 品质不高 的有机添加 剂中 ,往 往 除 了有效 的成 分之外还 含有相 当数量 的无效成 分 , 积 累 到一 定 的程 度 也成 为有 害于 镀 液 性 能 的有 机杂 质 。基于有机 物均含碳 的特点 ,因此 ,电镀 工作者 习 惯 以镀 液 中 的 有 机碳 总含 量 T O C( T o t a l Or g a n i c C a r d o n) 表示镀 液中有机 物的总量 ,其 中既有有机添 加 剂所含 的碳 ,也 有无机杂质所 含 的碳 。 由于镀液 中 的有 机添 加 剂 的含 碳 量 是 一定 的 ,因此 当镀 液 中的 T O C 越来 越高 时 ,就表 明镀液 中的有机杂质 含量也在 不 断地增加 。减 少 有机 杂质对镀 液性能和 镀层质量 危 害 的积极措 施 ,是使 用优 质 中间体 配制 的、用量 小、
可以 ,则 不必加氧化剂 氧化 ,若 发现直接 吸附不行 , 可以按照下面大处理 方法处理 之。
从镍电镀污泥回收的硫酸镍溶液的深度净化

时间 5 mi n 的条件 下 .经过 4级 逆 流 萃取 剩余 杂 质 降至 深度 净 化达 标 范围 ; 负载有 机相 用 4 mo l / L
H 2 S O 4 按 0 , A = 5 / 1 、 3 O℃ 、 5 ai r n , 经过 3级逆 流反 萃 可达到 再 生有机 相的 目的 . 反 萃水相 可返 回至 电
Ab s t r a c t :T h e c r u d e n i c k e l s u l f a t e s o l u t i o n r e c y c l e d f r o m n i c k e l e l e c t r o p l a t i n g s l u d g e l e a c h i n g s o l u t i o n o f
镀 污 泥 浸 出 工 序 回 用.
关 键词 : P 5 0 7; 硫 中图分 类号 : X7 8 1 . 1 ; T F 1 l 1 . 3 文献标 志码 : A
De e p p ur i f i c a t i o n o f n i c k e l s u l f a t e s o l u t i o n p r o d u c e d b y Ni - - e l e c t r o p l a t i n g s l u d g e r e c y c l i n g p r o c e s s
T h e r e s u l t s s h o w t h a t u n d e r t h e ̄l l o w i n g o p t i mu m c o n d i t i o n s , t h a t i s , u s i n g 1 0% P 5 0 7( v o l u m e f r a c t i o n ) p l u s
如何防止镶液中积累杂质并净化镀液(下)

安美特 ( A t o t e c h )公司推 出的用于 吸附光 亮镀镍
溶液 中 有机杂质 的 《 Nl K O T E C T 吸收 系统 》是 目前较
为先进 的镀液 有机杂质 吸附处理 系统。该 吸附剂 不再 是传统 的活性 炭 ,而是 一种新 型的聚合 物树脂。 它吸 附的有机物质 可 以被 洗脱 ,吸附剂则可 以重复使 用。
4 镀液杂质处理的封闭循环 系统
如 果将镀 液 的连续 循环过 滤处理 、小 电流 电解 处 理 、有 机杂质 的活性炭 ( 或聚合 物树脂 )吸附处理 等 清除镀 液 中杂质 的方法 ,在槽外 串联 起来 ,就形成 一 个封闭的循环 ,如图3 所示 。由此而产生 的效果 ,绝 非 是三者 各 自处理 效果 的简 单叠加 ,而是 为电镀 生产提 图3 镀液杂质处理 的封 闭循环 系统
当该 装置与连 续循环过 滤装置 串联 起来 ,形成镀 液杂 质 处理 的封 闭循环 系统 时 ,就 可 以保证 镀镍溶 液中有 机碳 总含量 ( T O C) 始终 不超过警 戒 的限度 。使 用该 装置之后 ,不再需要 使用活性 炭 、双氧 水 、高锰酸 钾 等方法来清 除镀液 中的有机杂质 ,操作更为方便。
( 5) 镀液杂质的处理 已不再是排除镀液故障 的一 种技术措 施 ,而 是 电镀生产 过程 中一项具 有预 防性质
的质 量 控 制 手段 ,为落 实和 贯彻 清 洁 生产 创 造 了条
件。
表面工程 团・ 经验交流
I N FOR 矗 ATl ON OF SI 】 懿 CE E N I N 氍琏 1 N
◎ 储荣邦 吴双成 王宗雄
如何 防 止镶 液 中积 累杂 质 并净化 镶液 ( 下)
Hale Waihona Puke ( 接上期 ) 3 . 3 . 4 新型聚合物树脂吸附有机杂质 的优越性
镀镍液净化新途径

镀镍液净化新途径
沈品华;刘唯明
【期刊名称】《电镀与环保》
【年(卷),期】1996(016)002
【摘要】镀镍液净化新途径沈品华,刘唯明(上海市永生助剂厂,200333)1传统净化处理浪费惊人镀镍液在电镀过程中杂质会逐渐积累,到达一定的量,镀液性能变劣,影响镀镍层质量,因此不得不停产进行净化处理。
镀镍液中杂质有无机物和有机物两种。
无机杂质常有铜、铁、锌等...
【总页数】3页(P8-10)
【作者】沈品华;刘唯明
【作者单位】上海市永生助剂厂;上海市永生助剂厂
【正文语种】中文
【中图分类】TQ153.12
【相关文献】
1.镀镍液净化新工艺 [J], 巫辉
2.镀镍液净化新工艺 [J], 巫辉
3.国内外化学镀镍老化液净化再生技术研究现状 [J], 王海燕;于秀娟;周定;马焕明
4.废化学镀镍液的净化和再生 [J],
5.电渗析法净化再生、化学镀镍老化液的研究 [J], 于秀娟;周定;王海燕;李朝林
因版权原因,仅展示原文概要,查看原文内容请购买。
- 1、下载文档前请自行甄别文档内容的完整性,平台不提供额外的编辑、内容补充、找答案等附加服务。
- 2、"仅部分预览"的文档,不可在线预览部分如存在完整性等问题,可反馈申请退款(可完整预览的文档不适用该条件!)。
- 3、如文档侵犯您的权益,请联系客服反馈,我们会尽快为您处理(人工客服工作时间:9:00-18:30)。
镀镍溶液净化工艺
0 摘要
本文在总结前人研究的基础上,结合四年的实践经验,提出了一种镀镍液净化新工艺。
赫尔槽试验和微量元素分析试验结果表明:该工艺净化效果好,适用于解决镀镍层出现毛刺、针孔等缺陷。
关键词:镀镍液;净化
1 前言
19世纪末,镀镍技术已获得广泛应用。
据统计,每年镀镍消耗的镍量约占世界镍总产量的1/10。
这与镀镍层优良的物理、化学性质是分不开的。
镀镍在汽车、自行车、钟表、医疗器械和日用五金等方面应用广泛。
在镀镍生产中,由于种种原因,镍液中的各种杂质会不断积累,而杂质对镀液的影响非常敏感,因此,对镍液的定期净化显得尤其重要。
当镀镍液中含有铁、锌、铜等杂质,和加工残留的切削液、防锈油、抛光油脂、灰尘、电镀添加剂的分解物时,镀层出现针孔、麻点、粗糙、发黑、条纹,甚至脱皮等疵病(亮镍镀液对杂质尤为敏感)。
此时,应对镀液进行净化。
传统镍液的净化是用稀释的氢氧化钠调节镀液pH值到6左右,使氢氧化钠与三价铁反应生成氢氧化铁胶体沉淀,以除去铁杂质。
此方法会使镀镍液引入Na+,当Na+的含量积累到一定数值时,会对镀层的物理、化学性能带来不良影响,如镀层内应力增加,脆性增大,发雾等。
由于目前还没有除去镀液中的Na+离子的方法,而且此方法不能有效去除添加剂的分解物、油脂和锌、铜等杂质,因此对镍液不能起到全面彻底的净化作用。
本文介绍了一种全面净化镍液的工艺。
2 电镀镍工艺介绍
本文所介绍的全面净化镍液的工艺可操作性强。
现仅介绍笔者所在镍—镍—装饰铬自动生产线的电镀镍工艺。
镀镍液配方及工艺条件:
a.半光亮镍镀液配方和工艺条件
硫酸镍 260~300g/L
氯化镍 38~45g/L
硼酸 40~50g/L
电流密度 2~5A/dm2
pH值 3.7~4.0
温度 50~55℃
光亮剂 SB—M 1.5mL/L
b.光亮镍镀液配方和工艺条件
硫酸镍 260~300g/L
氯化镍 38~45g/L
硼酸 40~50g/L
电流密度 2~5A/dm2
pH值 3.8~4.0
温度 50~55
光亮剂 N—11 20mL/L
N-22 2mL/L
3 镀镍液的净化
3.1 镀镍液净化装置
镍液净化的频度可根据待镀工件的表面状态以及生产的实际情况来确定。
本文是按产量来确定镍液净化的额度。
当生产量达到20~30dm2/L时净化一次。
为使本槽能够得到清理,每个镀镍槽都必须配备一个预备槽。
预备槽与本槽之间通过三进式过滤机连接。
如图1所示。
另外预备槽必须配备搅拌装置(如空气搅拌),最好还能配备恒温加热装置。
半光亮镍本槽 过滤机 半光亮镍预备槽 光亮镍本槽 过滤机 光亮镍预备槽
3.2 镍液净化的步骤
镍液净化的具体步骤为:
①用三进式过滤机将本槽液体移送到预备槽,打开空气搅拌。
②用精制H2SO4调节槽液pH值对到3左右(有利于氧化还原反应);加入0.5~1.5mL/L 35%(质量分数)的精制H2O2,充分搅拌,使Fe2+(主要金属杂质)氧化成Fe3+,有机杂质氧化成易于被活性炭吸附的物质。
H2O2十2FeSO4十H2SO4→Fe2(SO4)3十2H2O
从上述反应式可以看出,在硫酸存在下,氧化还原反应容易进行。
③将槽液升温至60~70℃,并保温1h,使之充分氧化,同时使残余的双氧水分解、挥发。
边搅拌,边加入碳酸镍的悬浊液,调整槽液的pH值≥5.5,使Fe3+形成氢氧化铁沉淀。
Fe3+十3OH-→Fe(OH)3↓
以上过程同时也可去除Cu2+、Zn2+。
采用碳酸镍调整pH值,应注意以下几点:
a用线外的容器(如桶)溶解碳酸镍,不能将碳酸镍直接投加到槽液中。
b按2~4g/L的添加量,用热的槽液将碳酸镍溶解在容器中,搅拌成悬浮液。
c在搅拌条件下,将碳酸镍悬浊液缓慢加入预备槽。
d保温1h,测定pH值。
如果pH值低于5.5,仍应继续添加碳酸镍悬浮液至所需pH值。
NiCO3十H2O→Ni2+十HCO3-十OH—
④将2~4g/L精制粉末活性炭加入预备槽中,搅拌5h以上,使有机杂质充分吸附。
关闭空气搅拌,将槽液静置8h以上,使氢氧化铁及活性炭充分沉淀。
⑤将本槽充分刷洗,阳极袋,阳极钛蓝和阳极镍块用稀盐酸浸泡刷洗后再回用,以除去吸附在上面的红褐色铁锈。
⑥用过滤机将槽液抽回本槽(过滤机必须添加助滤剂)。
抽完液后必须更换、清洗滤布。
如有多台过滤机,则每台过滤机及其滤布都应定期清洗。
预备槽使用6~8次后应清理一次。
⑦用烧杯采样观察或用过滤的方法确认抽回本槽的液体是否混有活性碳,如有,必须重复以上步骤。
⑧用精制H2SO4在本槽槽液加热、搅拌的状态下调整pH至正常工艺范围,用瓦楞形电解板(大阴极)以小电流(0.25~1A/dm2)模拟电解3~5h,除去剩余的铜、锌等金属杂质,以电解板瓦楞波峰和波谷不见灰色沉淀物为止。
为了在电解时使镍的损失最低而杂质去除效率最高,模拟电解条件如下:低pH值、低电流密度、搅拌、加温等;另外还要定时清除电解板表面海绵状的疏松镀层。
⑨补充光亮剂,进入电镀作业。
光亮剂的添加量应严格按照工程品质的要求添加,如上述工艺就是按:
SB—M:0.5mL/L N-11:5mL/L N-22:0.2mL/L进行补充。
4 槽液净化后的检验
4.1 赫尔槽试验
取250mL净化后的镍液于250mL的赫尔槽中,用I=1A和I=3A的试验样板记录如下:
所得试片表面光亮,无毛刺,针眼等缺陷。
4.2 微量元素分析
净化后的镍液各类杂质(有机杂质,金属杂质)的去除率都相当高,一般情况,净化后Fe2+含量可以控制在3ppmg/L,以下,Cu2+可以控制在0.1ppmg/L 以下。
4.3 生产实践检验
经过三年的实践检验,上述生产线的不良率一直控制在0.01%以下。
由于有优良的镍层,工件的耐蚀性维持在9级(GB6461—86)(CASS试验)以上。
5 结论
镀镍液的定期净化是维持电镀正常生产所必需的,净化的方法五花八门,而许多方法往往只能片面地去除金属杂质或者有机杂质,有的甚至会给镍液带来新的杂质。
如何比较全面地净化镍液,是许多电镀工作者一直在研究的课题,本文所介绍的镍液净化新工艺,由于碳酸镍的使用,不会给镍液带入杂质,使用效果良好,适用于解决镀镍生产线出现毛刺、针眼等缺陷。