轴套类零件加工工艺分析设计
毕业设计轴套--轴套零件的工艺分析
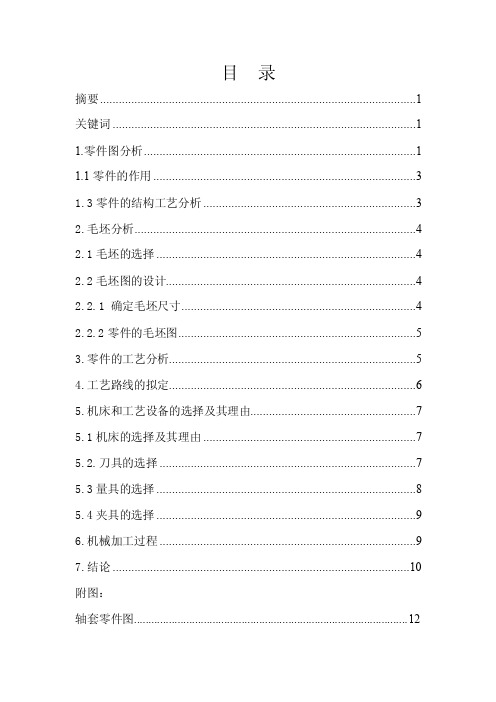
目录摘要 (1)关键词 (1)1.零件图分析 (1)1.1零件的作用 (3)1.3零件的结构工艺分析 (3)2.毛坯分析 (4)2.1毛坯的选择 (4)2.2毛坯图的设计 (4)2.2.1 确定毛坯尺寸 (4)2.2.2零件的毛坯图 (5)3.零件的工艺分析 (5)4.工艺路线的拟定 (6)5.机床和工艺设备的选择及其理由 (7)5.1机床的选择及其理由 (7)5.2.刀具的选择 (7)5.3量具的选择 (8)5.4夹具的选择 (9)6.机械加工过程 (9)7.结论 (10)附图:轴套零件图 (12)轴套毛坯图 (13)机械加工工艺过程卡1 (14)机械加工工艺过程卡2 (15)机械加工工序卡2 (16)机械加工工序卡3 (17)机械加工工序卡4 (18)机械加工工序卡5 (19)机械加工工序卡6 (20)机械加工工序卡7 (21)机械加工工序卡8 (22)机械加工工序卡9 (23)机械加工工序卡10 (24)机械加工工序卡11 (25)机械加工工序卡12 (26)机械加工工序卡13 (27)机械加工工序卡14 (28)机械加工工序卡15 (29)参考文献 (30)轴套零件的工艺分析摘要:轴套零件在机械中的作用主要是导正、限位、止转及定位作用。
本次毕业设计通过对轴套零件图的分析,确定了该零件的毛坯材料及尺寸规格,通过对零件的加工工艺分析,确定了该零件的加工工艺路线,编写了机械加工工艺过程卡片和工序卡片。
零件在加工中必须保证重要的尺寸精度和表面粗糙度,以及根据现有生产设备选择合理的机械加工路线。
关键词:轴套尺寸设备精度1.零件图分析轴套一般起滑动轴承作用,是在机械传动过程中起固定和减小载荷摩擦系数的部件。
图1轴套零件图该零件(图1)为轴套类零件。
表面由外圆柱面、轴肩退刀槽表面组成,其中2.0132±φmm ,60030.00φ+mm, 950022.0φ-mm 这三个直径尺寸有较高的尺寸精度和表面粗糙度要求,表面粗糙度要求为0.8,为了保证同轴度通常减小切削力和切削热的影响,粗精加工分开,使粗加工中的变形在精加工中得到纠正,要求尺寸较高为60030.00φ+mm 、950022.0φ-mm 、2.0132±φmm ,其表面粗糙度为Ra1.6µm、Ra0.8µm 零件的左端和有端有M6螺纹孔,深8mm 。
轴套零件的数控工艺分析与编程

轴套零件的数控工艺分析与编程轴套是一种常见的机械零件,广泛应用于各种机械设备中。
数控工艺分析与编程是指通过数控编程的方式对轴套的加工工艺进行分析,并编写相应的数控程序,以实现对轴套的高效、精确加工。
下面将详细介绍轴套零件的数控工艺分析与编程过程。
一、数控工艺分析数控工艺分析是指分析轴套零件的加工特点和要求,并确定相应的加工工艺路线和具体的加工参数。
具体分析如下:1.轴套的加工特点和要求:轴套通常由高强度的金属材料制成,具有高精度、高强度和耐磨损的特点。
在进行数控加工时,需要注意减小误差、提高加工精度和表面质量。
2.加工工艺路线:根据轴套的结构、尺寸和加工要求,确定加工工艺路线。
一般来说,轴套的加工工艺路线包括粗加工、精加工和表面处理等步骤。
-粗加工:主要包括车削、铣削、钻削等工艺,用于将原材料加工成近似形状的轴套毛坯。
-精加工:主要包括车削、钻削、拉削等工艺,用于将毛坯进一步加工成精确形状和尺寸的轴套。
-表面处理:主要包括抛光、热处理等工艺,用于提高轴套的表面质量和硬度。
3.加工参数确定:根据轴套的材料和加工要求,确定各工艺步骤对应的切削速度、进给速度、切削深度和切削用液等加工参数。
二、数控编程数控编程是指根据数控设备的编程语言和指令集,编写相应的数控程序,实现对轴套的自动化加工。
具体编程步骤如下:1.绘制零件图纸:根据轴套的几何形状和尺寸要求,绘制轴套的详细图纸。
图纸应包括轴套的三维模型、尺寸和加工要求等信息。
2.分析加工特点:根据轴套的加工特点和要求,对加工工艺进行分析,并确定加工工艺路线和加工参数。
3.编写数控程序:根据加工工艺路线和加工参数,编写数控程序。
数控程序是指通过一系列的数控指令,控制数控机床进行轴套的加工。
4.调试和优化:将编写好的数控程序输入数控机床,并进行调试和优化,确保加工过程的准确性和稳定性。
5.加工监控和质量检验:在整个加工过程中,需要进行对加工状态的监控和质量检验,确保轴套的加工质量符合要求。
轴套类零件加工工艺及方案
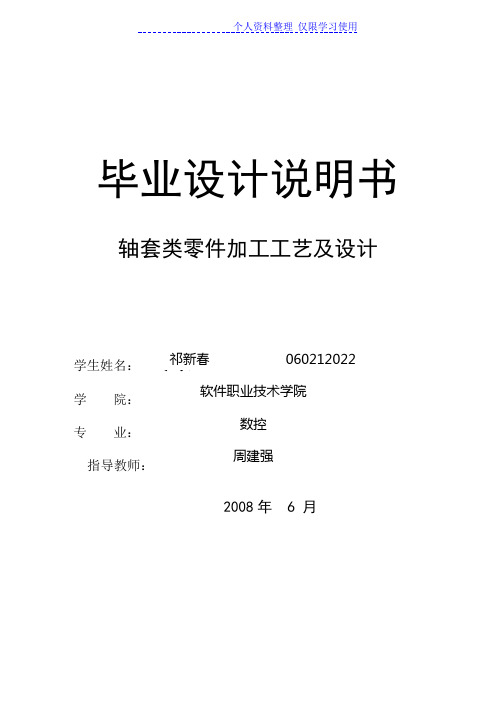
个人资料整理 仅限学习使用毕业设计说明书轴套类零件加工工艺及设计学生姓名: 学号: 学 院:专 业: 指导教师:2008年 6 月祁新春 0602120225 软件职业技术学院 数控 周建强目录1引言12数控机床的概述22.1数控及自动编程的发展简介22.1.1数控机床的发展过程:22.1.2自动编程软件的发展、联系及优越性22.2数控机床的基本组成及工作原理32.2.1数控机床的基本组成32.2.2数控机床的工作原理32.3数控机床的分类32.3.1按控制刀具与工件相对运动轨迹分类32.3.2按加工方式分类32.3.3按控制坐标轴数分类42.3.4按驱动系统的控制方式分类42.4数控机床的应用范围42.5数控机床的特点4第三章轴类零件的加工工艺5第四章轴类零件实例加工<一)64.1实体零件的生成64.2加工工艺分析74.2.1分析零件图纸和工艺分析74.2.2确定装夹方案94.2.3确定加工路线及进给路线94.2.4刀具的选择104.3选择切削用量124.3.1主轴转速的确定124.3.2进给速度的确定124.3.3背吃刀量确定124.4编程134.4.1编程技巧134.4.2编程特点154.4.3编程方法154.4.4编程步骤164.4.5实例分析165典型实例分析<二)176设计总结21附录A 加工程序 (23)参考文献30致谢311引言科学技术和社会生产的不断发展,对机械产品的性能、质量、生产率和成本提出了越来越高的要求。
机械加工工艺过程自动化是实现上述要求的重要技术措施之一。
他不仅能够提高品质质量和生产率,降低生产成本,还能改善工人的劳动条件,但是采用这种自动和高效率的设备需要很大的初期投资,以及较长的生产周期,只有在大批量的生产条件下,才会有显著的经济效益。
随着消费向个性化发展,单件小批量多品种产品占到70%--80%,这类产品的零件一般采用通用机床来加工。
而通用机床的自动化程度不高,基本上由人工操作,难于进一步提高生产率和保证质量。
毕业论文-轴套零件的加工工艺规程及夹具设计
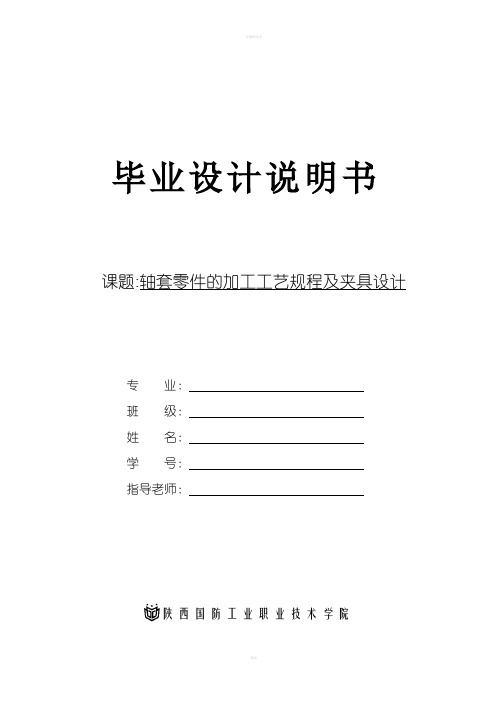
毕业设计说明书课题:轴套零件的加工工艺规程及夹具设计专业:班级:姓名:学号:指导老师:陕西国防工业职业技术学院二O一一届毕业设计(论文)任务书专业:数控技术班级:数控姓名:学号:一、设计题目(附图):轴套零件机械加工工艺规程制订及第25 工序工艺装备设计。
二、设计条件:l、零件图;2、生产批量:中批量生产。
三、设计内容:1、零件图分析:l)、零件图工艺性分析(结构工艺性及技术条件分析);2)、绘制零件图;2、毛坯选择:1)、毛坯类型;2)、余量确定;3)、毛坯图。
3、机械加工工艺路线确定:1)、加工方案分析及确定;2)、基准的选择;3)、绘制加工工艺流程图(确定定位夹紧方案)。
4、工艺尺寸及其公差确定:1)、基准重合时(工序尺寸关系图绘制);2)、利用尺寸关系图计算工序尺寸;3)、基准不重合时(绘制尺寸链图)并计算工序尺寸。
5、设备及其工艺装备确定:6、切削用量及工时定额确定:确定每道工序切削用量及工时定额。
7、工艺文件制订:1)、编写工艺设计说明书;2)、填写工艺规程;(工艺过程卡片和工序卡片)8、指定工序机床夹具设计:1)、工序图分析;2)、定位方案确定;3)、定位误差计算;4)、夹具总装图绘制。
9、刀具、量具没计。
(绘制刀具量具工作图)10、某工序数控编程程序设计。
四、上交资料(除资料2使用标准A3手写外,其余电子文稿指导教师审核后,打印上交)1、零件机械加工工艺规程制订设计说明书一份;(按统一格式撰写)2、工艺文件一套(含工艺过程卡片、每一道工序的工序卡片,工序附图);3、机床夹具设计说明书一份;(按统一格式撰写)4、夹具总装图一张(打印图纸);零件图两张以上(A4图纸);5、刀量具设计说明书一份;(按统一格式撰写)6、刀具工作图一张(A4图纸);量具工作图一张(A4图纸)。
7、数控编程程序说明书五、起止日期:2010年月日一2010年月日(共8周)六、指导教师:七、审核批准:教研室主任:系主任:年月日八、设计评语:九、设计成绩:年月日本文主要介绍轴套零件的机械加工工艺过程,首先通过对该其零件图纸进行分析,再确定其加工工艺,选择合理的设备及工艺装备,并制定出合理的工艺路线,选择合理的刀具、切削用量等,其次设计钻两斜孔的钻孔夹具、专用刀具、专用量具等,最终制定并填写机械加工工艺卡片和机械加工工序卡片。
轴套类零件的加工工艺及设计
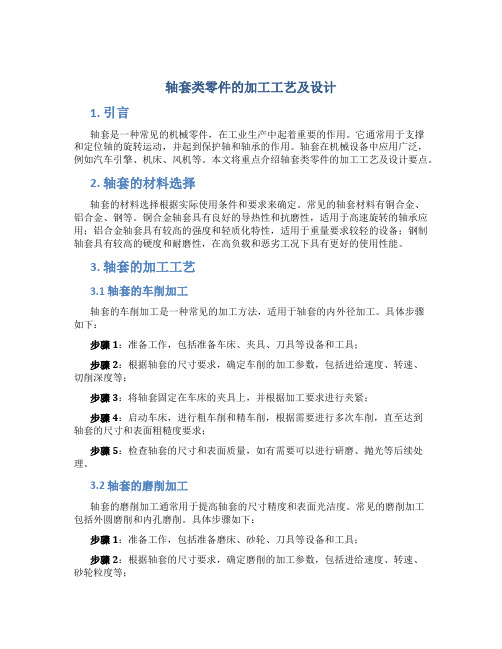
轴套类零件的加工工艺及设计1. 引言轴套是一种常见的机械零件,在工业生产中起着重要的作用。
它通常用于支撑和定位轴的旋转运动,并起到保护轴和轴承的作用。
轴套在机械设备中应用广泛,例如汽车引擎、机床、风机等。
本文将重点介绍轴套类零件的加工工艺及设计要点。
2. 轴套的材料选择轴套的材料选择根据实际使用条件和要求来确定。
常见的轴套材料有铜合金、铝合金、钢等。
铜合金轴套具有良好的导热性和抗磨性,适用于高速旋转的轴承应用;铝合金轴套具有较高的强度和轻质化特性,适用于重量要求较轻的设备;钢制轴套具有较高的硬度和耐磨性,在高负载和恶劣工况下具有更好的使用性能。
3. 轴套的加工工艺3.1 轴套的车削加工轴套的车削加工是一种常见的加工方法,适用于轴套的内外径加工。
具体步骤如下:步骤1:准备工作,包括准备车床、夹具、刀具等设备和工具;步骤2:根据轴套的尺寸要求,确定车削的加工参数,包括进给速度、转速、切削深度等;步骤3:将轴套固定在车床的夹具上,并根据加工要求进行夹紧;步骤4:启动车床,进行粗车削和精车削,根据需要进行多次车削,直至达到轴套的尺寸和表面粗糙度要求;步骤5:检查轴套的尺寸和表面质量,如有需要可以进行研磨、抛光等后续处理。
3.2 轴套的磨削加工轴套的磨削加工通常用于提高轴套的尺寸精度和表面光洁度。
常见的磨削加工包括外圆磨削和内孔磨削。
具体步骤如下:步骤1:准备工作,包括准备磨床、砂轮、刀具等设备和工具;步骤2:根据轴套的尺寸要求,确定磨削的加工参数,包括进给速度、转速、砂轮粒度等;步骤3:将轴套固定在磨床上,并调整好夹具,保证轴套的稳定性;步骤4:启动磨床,进行粗磨削和精磨削,根据需要进行多次磨削,直至达到轴套的尺寸和表面粗糙度要求;步骤5:检查轴套的尺寸和表面质量,如有需要可以进行抛光等后续处理。
3.3 轴套的冷镦加工轴套的冷镦加工主要用于加工内孔上的花纹或沟槽。
冷镦加工与车削和磨削不同,它通过冷镦机将金属材料挤压成型。
轴套类零件加工工艺分析
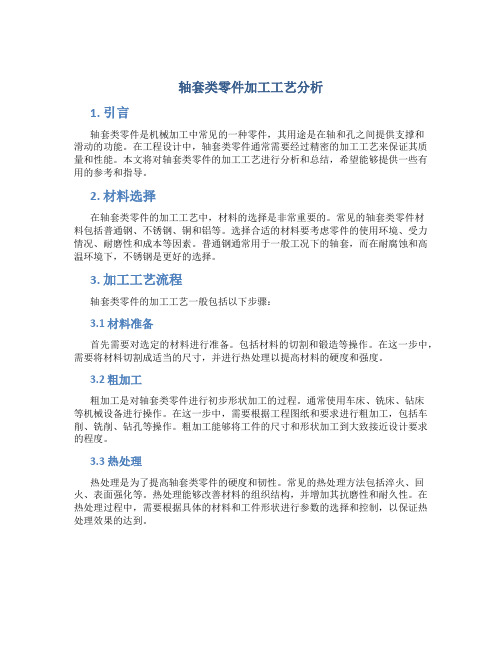
轴套类零件加工工艺分析1. 引言轴套类零件是机械加工中常见的一种零件,其用途是在轴和孔之间提供支撑和滑动的功能。
在工程设计中,轴套类零件通常需要经过精密的加工工艺来保证其质量和性能。
本文将对轴套类零件的加工工艺进行分析和总结,希望能够提供一些有用的参考和指导。
2. 材料选择在轴套类零件的加工工艺中,材料的选择是非常重要的。
常见的轴套类零件材料包括普通钢、不锈钢、铜和铝等。
选择合适的材料要考虑零件的使用环境、受力情况、耐磨性和成本等因素。
普通钢通常用于一般工况下的轴套,而在耐腐蚀和高温环境下,不锈钢是更好的选择。
3. 加工工艺流程轴套类零件的加工工艺一般包括以下步骤:3.1 材料准备首先需要对选定的材料进行准备。
包括材料的切割和锻造等操作。
在这一步中,需要将材料切割成适当的尺寸,并进行热处理以提高材料的硬度和强度。
3.2 粗加工粗加工是对轴套类零件进行初步形状加工的过程。
通常使用车床、铣床、钻床等机械设备进行操作。
在这一步中,需要根据工程图纸和要求进行粗加工,包括车削、铣削、钻孔等操作。
粗加工能够将工件的尺寸和形状加工到大致接近设计要求的程度。
3.3 热处理热处理是为了提高轴套类零件的硬度和韧性。
常见的热处理方法包括淬火、回火、表面强化等。
热处理能够改善材料的组织结构,并增加其抗磨性和耐久性。
在热处理过程中,需要根据具体的材料和工件形状进行参数的选择和控制,以保证热处理效果的达到。
3.4 精密加工精密加工是将轴套类零件的尺寸和形状加工到精确的设计要求的过程。
精密加工通常包括数控加工、磨削、线切割等操作。
数控加工能够实现高精度的加工,磨削能够提高零件的表面质量和几何精度,线切割能够加工出复杂的内部结构。
3.5 表面处理表面处理是为了提高轴套类零件的表面质量和耐腐蚀性。
常见的表面处理方法包括电镀、喷涂、氮化等。
表面处理能够在一定程度上提高轴套类零件的耐磨性和使用寿命。
4. 加工工艺优化为了提高轴套类零件的加工效率和质量,可以对加工工艺进行优化。
毕业设计——轴套的加工工艺分析

毕业设计——轴套的加工工艺分析一、选题背景随着机械零件加工工艺的不断发展,对于高精度零件加工的需求也越来越高。
轴套作为机械中非常重要的零件,它的质量也直接影响到整个机械设备的性能和寿命。
因此,对于轴套的加工工艺的分析和研究具有非常重要的意义。
本篇论文将对轴套的加工工艺进行详细的分析研究,以期能够提高轴套的加工质量和效率。
二、轴套的定义和作用轴套是一种机械零件,也叫做衬套,是用来安装在机械零件的轴上,起到支撑、固定和减少磨损等作用。
在机械设备中,轴承是最基本的传动部件之一,直接影响到设备性能和使用寿命。
而轴套作为轴承的辅助零件,可以起到保护和增强轴承的作用,减少轴承的磨损和损坏,从而提高机械设备的使用寿命和稳定性。
三、轴套的加工工艺1.工艺流程轴套的加工工艺流程一般包括下面几个步骤:(1)材料准备。
轴套的材料一般选用高强度和高耐磨的合金钢或不锈钢。
在材料选择上要严格控制质量。
(2)车削加工,用车床进行轴套的粗加工和精加工,通过车削去除外层的毛刺和表面粗糙度,从而保证加工精度和表面质量。
(3)磨削加工,通过磨床对轴套进行光洁度和尺寸精度的进一步加工和修整,使轴套表面光滑细腻,尺寸精度达到要求。
(4)抛光加工,进行抛光和光澈处理,使轴套表面光洁度更高,达到无暇无瑕的表面效果。
(5)质量检测,对轴套进行各项质量指标的检测和测试,确保达到技术标准和质量要求。
2.切削工艺车削是轴套加工中最为基础的工艺,由于轴套的制造精度要求较高,因此,车削是制造轴套最重要的环节之一。
轴套车削加工流程一般分为粗车和精车两个阶段。
粗车的主要目的是将加工余量切除,使轴套的形状和尺寸基本符合设计要求;精车的主要目的是对粗车后的轴套进行加工,达到所要求的纵向、横向和径向精度,同时提高轴套表面的光洁度和平整度。
3.磨削工艺磨削是轴套加工的另一个基础工艺,它的主要目的是提高轴套的加工精度和表面光洁度。
磨削加工中,砂轮选择和磨削参数的设置是比较关键的。
轴套类零件的加工工艺及设计
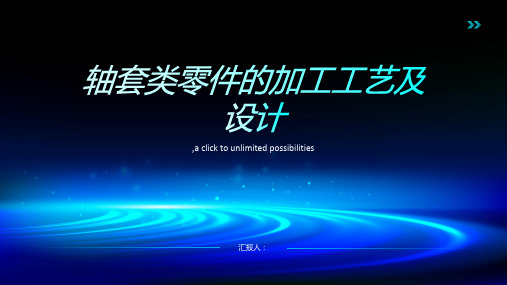
智能化设计:利用先进的人工智能 技术,实现轴套类零件的智能化设 计,提高设计效率和准确性。
定制化设计:根据客户需求和个性化 需求,实现轴套类零件的定制化设计, 提高产品的附加值和市场竞争力。
添加标题
添加标题
添加标题
添加标题
绿色环保设计:注重环保和可持续发 展,采用环保材料和制造工艺,降低 能耗和排放,提高产品的环保性能。
加工方法:半精加工常用的方法有车削、铣削、磨削等,根据不同的加工要求和材料 选择合适的加工方法。
加工精度:半精加工的精度要求比粗加工高,需要保证零件的尺寸、形状和位置精 度,以及表面粗糙度等质量要求。
精加工的定义和目的 精加工的方法和设备 精加工的工艺流程和操作要点 精加工的质量控制和检测方法
定义:超精加工是一种精密加工方法, 通过高精度机床和特殊磨料对零件表 面进行超精细加工,以达到极高的表 面质量和精度
设计的优化考虑加 工工艺:在设计过 程中,需要考虑加 工工艺的限制和要 求,通过优化设计 来提高加工效率和 产品质量。
协调与优化的实践 经验:通过实际生 产中的经验积累, 不断协调和优化加 工工艺与设计的关 系,提高生产效率 和产品质量。
智能化加工:采用先进的数控技术,提高加工精度和效率 绿色环保:减少能源消耗和环境污染,采用环保材料和工艺 高效化加工:提高加工速度和效率,缩短生产周期 柔性化加工:适应多品种、小批量的生产需求,提高加工灵活性
加工设备:粗加工设备包括铣床、车床、钻床等。
注意事项:在粗加工过程中,应选择合适的刀具和切削参数,保证加工质量和效率。同时,应 注意保护机床和刀具,避免损坏。
定义:半精加工是指在粗加工的基础上进行进一步的加工,以达到规定的质量要求。
加工内容:半精加工包括对轴套类零件的外圆、内孔、端面等表面的加工,以及螺 纹、键槽等结构的加工。
- 1、下载文档前请自行甄别文档内容的完整性,平台不提供额外的编辑、内容补充、找答案等附加服务。
- 2、"仅部分预览"的文档,不可在线预览部分如存在完整性等问题,可反馈申请退款(可完整预览的文档不适用该条件!)。
- 3、如文档侵犯您的权益,请联系客服反馈,我们会尽快为您处理(人工客服工作时间:9:00-18:30)。
轴套类零件加工工艺分析设计轴套类零件加工工艺分析设计目录第一章前言 (3)第二章摘要 (5)第三章零件结构及毛坯分析 (6)3.1零件完整性与正确性分析 (6)3.2材料分析 (6)3.3毛坯分析 (6)第四章零件结构工艺 (8)第五章选择加工设备与刀、夹、量具 (10)5.1机床的选择 (10)5.2刀具的选择 (11)5.3夹具的选择 (12)第六章加工工艺分析 (14)6.1 夹紧方式 (14)6.2定位基准的选择 (14)6.3加工顺序的安排 (15)6.4切削用量的确定及功率的效核 (16)6.5切削液的选择 (18)第七章数控加工刀具卡 (20)第八章数控加工工艺卡 (21)第九章数控加工工序卡 (23)第十章程序的编制 (26)第十一章加工步骤 (29)第十二章参考文献 (31)总结 (32)后记 (34)前言毕业设计是我们结束大学学习生活走向社会的一个中介和桥梁。
毕业设计是我们大学生才华的第一次显露,是向祖国和人民所交的一份有分量的答卷,是投身社会主义现代化建设事业的报道书。
撰写毕业设计是我们在校最后一次知识的全面检验,是对基本知识,基本理论和基本技能掌握程度的一次总测试。
撰写毕业设计中需要将理论运用于实际操作中,并通过自己对知识的掌握和学习将零件的结构分析清楚。
并进一步对其进行工艺分析。
精密主轴的加工涉及到我们数控知识的很多方面。
首先必须能够作到:1:合理选用材料和规定的相应热处理。
2:掌握基本指令的综合使用能力。
3:掌握综合轴类的加工工艺分析。
4:能设计简单的夹具并选择相应的机床。
5:能确定各工序有关的切削因素,能对加工质量进行分析处理。
6:能熟练掌握基准的选择,掌握保证尺寸精度的技能技巧。
此次设计的磨床主轴加工方案的技能点主要在于锥面的加工,带凹槽零件的编程,深孔的加工,内螺纹的加工,外圆的铣扁,高精度磨削。
这些都是我们学习三年数控必须掌握的基础知识,也是考验我们是否能学以至用的时候。
通过对需要加工的零件,进行结构与技术要求的分析和加工工艺的分析及刀具及机床的选择,使得自己对所学的知识做一次全面的总结。
在这个过程中也了解到关于数控技能方面的一些操作规程。
零件的结构关系着整个设计方案的设计思路和逻辑思维顺序,而技术要求则是在零件加工过程中要求零件的完整性与正确性,对材料的选择也是需要及其用心分析的。
结构工艺则包括精度分析,粗糙度分析,尺寸标注应符号数控加工特点。
而工艺规程设计则包括1:基准的选择。
2:加工方法的选择。
3:划分加工程序。
4:热处理。
5:辅助工序。
6:工艺路线制定分析。
而在此过程中选择加工设备与刀,夹,量具是个十分重要的选择环节,加工为成品的零件若要达到预期的尺寸与精度,必须选择与其相应的精确的机床与刀具。
而加工之前必须将工件所需要的夹具选定好,并且装夹好。
而加工工艺设计则包括工序尺寸及公差计算,切削参数的计算,切削用量的计算,走刀路线的计算和时间定额计算。
这些知识得到了充分的利用,也锻炼了我们三年来的运用数控的能力,当然还包括了对我们综合素质的考验,语言组织能力,逻辑思维能力等等。
通过这次设计明白了还有很多知识都需要自己去努力学习,所以诚心希望老师多多指导,忠心感谢!摘要通过轴类零件加工工艺分析设计,使我们在拟定工工艺分析方案过程中,得到方案分析、结构工艺性、机械制图、零件设计、编写技术文件和查阅技术资料的等方面的综合训练,树立正确的设计思想,掌握基本的设计方法,并培养学生具有初步的结构分析、结构设计与计算能力,并阐述了在学校机械加工实习课中如何对轴类零件进行工艺分析,从而提高工件质量。
【关键词】:轴类零件、零件图的工艺分析、数控加工工序卡第三章零件结构及毛坯分析3.1 零件完整性与正确性分析3.11 零件的完整性分析机床主轴一般为精密主轴,它的功用为支承传动件(如齿轮、带轮、凸轮等)、传递转距,除承受交变弯曲应力和扭转应力外,还受冲击载荷作用,因此,对其要求有较高的综合力学性能,以保证装在主轴上的工件或切削工具(如刀具、钻头、砂轮等)具有一定的回转精度。
3.12 零件的正确性分析零件加工为成品时其用途是要达到预期效果的,而往往因为各方面的原因,零件的精确度总会受到一定的影响,所以零件的正确性需要在各个因素约束下才能达到。
通过加工工艺的调整使零件在加工过程中达到要求的精度,是设计内容中的一个重要部分。
3.2 材料分析.3.21材料分析:毛坯材料为20Cr380x55mm,工件较长属细长轴的加工有一定的难度。
需选择合理的机床并采用相应的加工方案,选择合理的切削参数及刀具获得表面粗糙度Ra0.4.零件切削所选择的材料是20Cr,经过正火可以:①改善组织结构和切削加工性能。
②消除内应力。
该零件在毛坯锻造后正火可以消除其锻造时产生的内应力,细化晶粒,降低硬度,改善了加工性能。
由于粗加工后已切除大部分的余量,工件直径减小,容易淬透,经高温回火使中心层能得到韧性好耐冲击的回火索氏体组织。
调质处理又能消除一部分粗加工后引起的内应力,代替了时效处理,且调质后工件产生的变形可以在后道工序中消除。
精车后进行高频淬火以提高主轴的强度硬度和耐磨性,起淬火变形可以通过后续工序的磨削加工来消除,故该零件的选材及热处理要求合理。
3.22毛坯的制造方法轴套类零件毛坯的形式有棒料,锻件和铸件三种。
光轴和直径相差不大的阶梯轴,毛坯一般以棒料为主外圆直径相差较大的轴或重要的(如主轴)宜选用锻件毛坯,既节省材料,减少切削加工的劳动量,又改善其力学性能。
结构复杂的大型轴类零件(如曲轴)可以采用铸件毛坯。
该零件为外圆直径相差较大的主轴,所以应该选用铸件毛坯。
第四章零件结构工艺.1、零件图如图所示:(1)、未注倒角1×45o,锐角倒钝0.2×45°。
(2)、未注公差尺寸按 GB1804-M。
(3)、端面允许打中心孔。
(4)、毛坯尺寸:(φ55×150)。
其余(5)、材料:45#,调质处理HRC 26~364.2.零件零件结构工艺该零件表面由圆柱面、圆锥面、顺圆弧面、逆圆弧面、螺纹面、沟槽面及内孔面等表面组成.图示零件各几何元素之间关系表达清楚完整,其中多个直径尺寸有较严的尺寸精度和表面粗糙度要求.¢520-0.03的外圆面、锥面、¢350-0.03的外圆表面粗糙度为Ra1.6um, ¢520-0.03的外圆面轴线对¢28+0.04的内孔面轴线的同轴度公差为¢0.025.零件材料为45钢,调质处理26-36HRC,材料的切削加工性能好。
根据上述零件几何结构分析及技术分析,选择棒料,毛坯尺寸为¢55×150。
在数控车床上按粗加工阶段、半精加工阶段和精加工阶段进行加工。
粗加工时,为保证高的表面质量,留余量0.25mm待精加工。
依据基准统一原则与重合的原则,精加工时,以外圆为基准,加工轮廓的外形,按“先基准后其他”的加工顺序原则,先加工¢28+0.04的内孔面。
由于工件有硬度要求,粗加工后、精加工之前进行调质处理,加工过程中,应穿插安排检验的辅助工序。
第五章选择加工设备与刀,夹,量具5.1 加工设备的选择Φ500×1500mmZ2——42高频淬火机床技术参数:机床重量2097KG机床外形尺寸3168×100×11905.2 刀具刀具切削部分的材料,直接影响刀具的切削性能。
刀具的刀杆可以采用45钢或40Cr钢等结构钢材制造,调制后硬度为30——40HRC。
而刀具的切削部分不仅要承担切削过程中的高温高压及冲击载荷,而且还要受到切屑及工件的强烈摩擦,因此作为刀具的切削部分的材料,必须具备下列性能:1)硬度必须高于工件材料的硬度。
2)足够的硬度及韧性。
3)较高的耐热性能。
4)较高的耐磨性。
5)良好的工艺性。
其中高速钢及硬质合金是目前使用最广的两类刀具材料。
1)高速钢广泛用于各种刀具,特别是切削刃形状较复杂的刀具。
2)目前车刀大都采用硬质合金,其他如钻头.铣刀.丝锥.齿轮刀具等也可以采用镶片或整体结构形式使用。
钨钛钴类合金适用于加工钢材,钨钴类适用于加工铸铁及有色金属材料。
考虑到以上几个方面,联系到我们所加工的零件,我们选用硬质合金材料的车刀刀片,钻头.丝锥等可以采用高速钢材料。
(详细见(图一)注:加工零件右端外圆柱表面;(图二)注:加工零件右端3MM直槽(图三)注:精车外圆车刀:刀尖角为35°,螺钉压紧式刀尖圆弧半径为0.4mm.(图四)注:精车内孔: 93°内孔车刀5.3 夹具1.车床夹具的主要功能,就是在车削加工工件的过程中,按照正确的位置和方向,稳定可靠的装夹工件。
即使工件在加工过程中受到切削力和其它外力影响,仍然始终保持工件被装夹在正确的位置和方向。
同时,车床夹具应该保持工件不因受夹紧力影响而造成尺寸精度或形状位置精度超过允许范围。
2.在设计机床使用夹具时,其结构应保证在一次定位后实现多面的加工,使工件加工部位都可以得以加工。
应力求使夹具结构简单,标准化,通用化和自动化。
以提高加工效率和降低成本.加工费用。
尽可能使用通用元件的拼装的组合可调夹具,以缩短生产准备周期。
通用元件重复使用,经济效益好。
3.夹具设计时,应保证工件装卸方便迅速,以减少工件的夹紧松开时间,机床所使用的夹具应具有足够的精度,并具有良好的精度保持性和足够的刚度,以防止受力变形而失去原有的精度。
考虑以上几点,我们的夹紧方案如下:1粗车时:采用一夹一顶装夹方式,其夹具前三爪卡盘和后顶尖。
2半精车时:采用两顶尖间装夹方式。
5.4量具检验是测量和监控主轴加工质量的一个重要环节。
除了工序间检验以外,在全部工序完成之后,应对主轴的尺寸精度.形状精度.位置精度和表面粗糙度进行全面的检查。
以便确定主轴是否达到各项技术要求,还可以从检验是否达到各项技术要求,而且还可从检验的结果及时发现各道工序中存在的问题,以便及时纠正,监督工艺过程正常进行。
检验的依据是主轴工作图。
检验工作按一定顺序进行,先检验各级外圆的尺寸精度,素线平行度和圆度,用外观比较法检验各表面的粗糙度及表面缺陷,然后在专用夹具上测量位置偏差。
在成批生产时,若工艺过程比较稳定,且机床精度较好,有些项目常常采用抽检的办法,并不逐项检验。
主要配合表面的硬度应在热处理车间检验。
量具我们选用:(1)游标卡尺(2)主轴检测棒(3)内径千分尺第六章加工工艺分析6. 1装夹方式零件没有较高的同轴度要求。
因此采用三爪自定心卡盘装卡。
零件右端为圆弧面不易装夹,所以应先加工右端,Φ36表面可以作为掉头装夹表面。
掉头加工接刀点位于10.25圆弧最高点Φ52处。
1 )装卡零件毛坯外露120mm,车工艺卡口Φ53*25mm。