装配线布置(一)
重卡装配线工艺布局
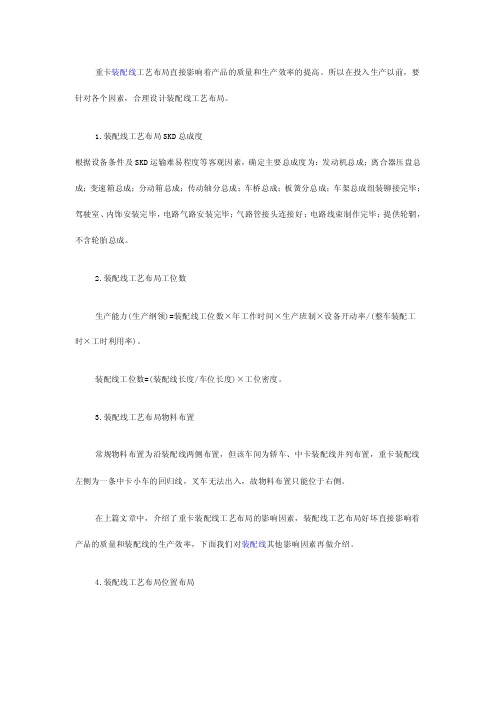
重卡装配线工艺布局直接影响着产品的质量和生产效率的提高。
所以在投入生产以前,要针对各个因素,合理设计装配线工艺布局。
1.装配线工艺布局SKD总成度根据设备条件及SKD运输难易程度等客观因素,确定主要总成度为:发动机总成;离合器压盘总成;变速箱总成;分动箱总成;传动轴分总成;车桥总成;板簧分总成;车架总成组装铆接完毕;驾驶室、内饰安装完毕,电路气路安装完毕;气路管接头连接好;电路线束制作完毕;提供轮辋,不含轮胎总成。
2.装配线工艺布局工位数生产能力(生产纲领)=装配线工位数×年工作时间×生产班制×设备开动率/(整车装配工时×工时利用率)。
装配线工位数=(装配线长度/车位长度)×工位密度。
3.装配线工艺布局物料布置常规物料布置为沿装配线两侧布置,但该车间为轿车、中卡装配线并列布置,重卡装配线左侧为一条中卡小车的回归线,叉车无法出入,故物料布置只能位于右侧。
在上篇文章中,介绍了重卡装配线工艺布局的影响因素,装配线工艺布局好坏直接影响着产品的质量和装配线的生产效率,下面我们对装配线其他影响因素再做介绍。
4.装配线工艺布局位置布局一工位:平衡轴、前后悬装配、车架翻身;二工位:车桥、传动轴、转向机装配;三工位:蓄电池装配;四工位:线束、管路装配;五工位:发离变装配;六工位:冷却系、排气系装配;七工位:油箱、驾驶室悬置装配;八工位:驾驶室、备胎架装配;九工位:轮胎装配,整车加油;十工位:装配保险杠、调整及整车下线。
为保证装配车辆的整体流水操作,装配线工艺布局与检测线布置于同一条直线上,车辆从装配线行驶下线直接进入检测线。
5.装配线工艺布局较重零件跨线方案由于物料布置只能位于装配线右侧,故对左侧装配的较重零件必须有合理的跨线方案。
(1) 左侧轮胎。
轮胎位于装配线末端,用手推小车从轮胎分装区送至装配地点的左右侧。
(2) 蓄电池箱体。
布局于三工位,借用天车从空中将蓄电池箱体从右侧运输到左侧。
驱动桥装配线设计与实施

驱动桥装配线设计与实施龚学全、金红卫、王宜前、刘奎波、梁兴华、洪旗、李明晟(广西柳工机械股份有限公司驱动桥厂)一、概述随着装载机市场的日趋成熟和增长,原有的驱动桥装配工艺已经不能满足要求。
通过“十一五”技术改造,改进驱动桥部件及总成的装配工艺、提高生产效率和装配质量,改善装配车间物流和工作环境,保证驱动桥装配水平在国内同行业适度领先,以适应公司发展战略需要。
二、工艺方案(一)工艺布局的改进1、改进前(如图1)(1)、生产线采用钢架结构,总长20m,高度0.8m。
分上下两层。
总成横向放置在小车上随车在轨道上层装配,由人力推动。
总成下线后小车由下层返回。
工人劳动强度较大,跨线操作困难;(2)、整条线可同时放置总成15根,两根桥间距不足0.5m。
装配过程采用批次装配(5-6根/批),各零部件(如轮架组件、轮壳组件、内齿轮以及主传动组件等)的供应也按照批次供应,因此主线存放较多的零部件;(3)由于主线一侧靠近墙壁,宽度不足3m,无足够的物料摆放区,造成现场摆放混乱。
定置管理困难。
工位不明确;(4)零部件的预装区位于主线一侧,另侧的物料用行车吊运进行装配,效率不高。
严重影响产能,无法满足公司发展需要;2、改进后(如图2)(1)、装配线长37.6m,有效工位18个,相邻两根桥间距1.2m,员工可自由通过装配线,极大方便了装配;(2)、装配台车采用地下返回,由电机拖动连续运转,大大降低了员工的劳动强度,并能够根据生产需要调整运行速度来调整生产节拍,实现精益生产;(3)、台车与牵引链之间为销联接,操作牵引销可调整装配线的工位间距,达到调整装配线工位数的目的。
台车上的支撑为活动式,可根据不同品种的桥的尺寸进行调节,实现不同车桥的混线生产,使生产组织柔性化;(4)、装配主线在原来的位置向外移动2m,与墙壁距离达到了5.6m。
两侧分别划分配送通道、物料区和操作区,彻底改变了装配现场的混乱局面。
图1 图2表格1改进前后对比表项目改进前改进后线长(m)20 37.6工位数15 18动力人力电机劳动强度大小效率低高物流状况混乱拥挤整齐顺畅(二)装配工艺的改进1、改进前(1)工艺路线:总成装配→试验→清洗→存放→喷漆→成品存放(露天);(2)总成装配过程中,内齿轮由人工装配。
7种精益生产线布局
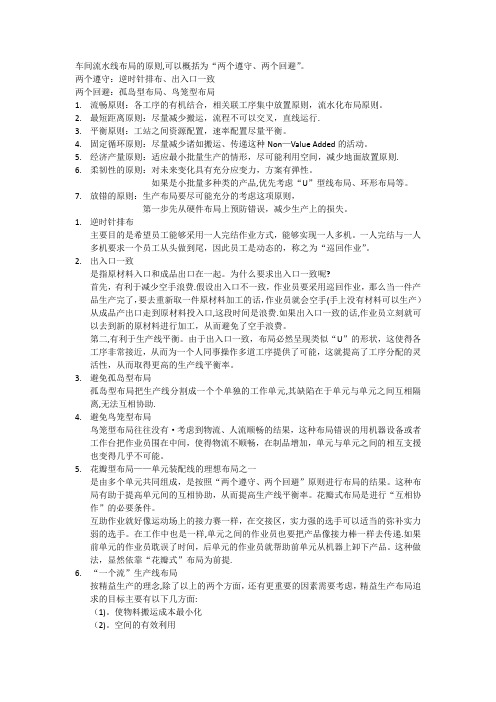
车间流水线布局的原则,可以概括为“两个遵守、两个回避”。
两个遵守:逆时针排布、出入口一致两个回避:孤岛型布局、鸟笼型布局1.流畅原则:各工序的有机结合,相关联工序集中放置原则,流水化布局原则。
2.最短距离原则:尽量减少搬运,流程不可以交叉,直线运行.3.平衡原则:工站之间资源配置,速率配置尽量平衡。
4.固定循环原则:尽量减少诸如搬运、传递这种Non—Value Added的活动。
5.经济产量原则:适应最小批量生产的情形,尽可能利用空间,减少地面放置原则.6.柔韧性的原则:对未来变化具有充分应变力,方案有弹性。
如果是小批量多种类的产品,优先考虑“U”型线布局、环形布局等。
7.放错的原则:生产布局要尽可能充分的考虑这项原则,第一步先从硬件布局上预防错误,减少生产上的损失。
1.逆时针排布主要目的是希望员工能够采用一人完结作业方式,能够实现一人多机。
一人完结与一人多机要求一个员工从头做到尾,因此员工是动态的,称之为“巡回作业”。
2.出入口一致是指原材料入口和成品出口在一起。
为什么要求出入口一致呢?首先,有利于减少空手浪费.假设出入口不一致,作业员要采用巡回作业,那么当一件产品生产完了,要去重新取一件原材料加工的话,作业员就会空手(手上没有材料可以生产)从成品产出口走到原材料投入口,这段时间是浪费.如果出入口一致的话,作业员立刻就可以去到新的原材料进行加工,从而避免了空手浪费。
第二,有利于生产线平衡。
由于出入口一致,布局必然呈现类似“U”的形状,这使得各工序非常接近,从而为一个人同事操作多道工序提供了可能,这就提高了工序分配的灵活性,从而取得更高的生产线平衡率。
3.避免孤岛型布局孤岛型布局把生产线分割成一个个单独的工作单元,其缺陷在于单元与单元之间互相隔离,无法互相协助.4.避免鸟笼型布局鸟笼型布局往往没有·考虑到物流、人流顺畅的结果,这种布局错误的用机器设备或者工作台把作业员围在中间,使得物流不顺畅,在制品增加,单元与单元之间的相互支援也变得几乎不可能。
线束装配及密封作业指导

力。线束的外护套不能出现波纹管断裂现象,否则必须进行包扎处理,包波
纹管后用胶带或扎带扎紧。
–
主线束与底盘线束的对接、顶架线束与主线束的对接、底盘线束与发动机线
束的对接、顶架线束与后尾线束的对接、电控线束的诊断插口等必须要放在
容易检修的地方。同时各种线束的插接头在线束捆扎固定时要放到维修人员
方便操作的检修口附近。
• 1.底盘线束和主线束在进入此舱体过封板时必须 有保护措施:圆孔用过线胶圈,同时要打胶密封; 边棱锐角要用波纹管或黑色胶皮地板革等,。
• 2. 各种电器控制单元要按照安装位置竖向摆放整 齐,固定牢固,按照线号、线色正确接线,要求 线束从下往上插接,避免水雾等顺线束进入电器 元件。
• 3.舱体内布线时用车身线卡打孔固定或用扎带捆 扎牢固。
–
线束经过孔洞时,必须用穿线护套保护(若无合适的穿线护套可用波纹管或
黑色橡胶替代,但要固定牢固不可使其脱落),穿过车身的孔洞,应加密封
胶填满孔洞缝隙,以免灰尘进入车厢内部。线束过拐角边棱时应包橡胶皮或
地板革保护,用地板革保护时,在外漏或打开舱门等容易看到的地方要用与
其周围的颜色相同或相近的颜色。
–
车辆批量生产时,有作业指导书的,首先应严格遵循作业指导书的要求执行。
质量要求
• 空调接地线应加平垫圈和弹簧垫圈固定牢 固。
2仪表主线束 工艺内容
a. 一般情况下用塑料扎带将主线束固定在前 仪表横梁上。扎带无法固定时必须使用仪 表线卡或车身线卡固定(使用手电钻在前 仪表横梁上打孔,将车身线卡或仪表线卡 固定在横梁上,从而固定线束)。
主要工艺参数
• 固定点间距不得大于200mm
圈保护,且过线胶圈不松脱,打密封胶密封。 • 继电器盒和其它电器控制单元要摆放整齐,固定牢固,按照线号、
汽车制造工艺装配工艺
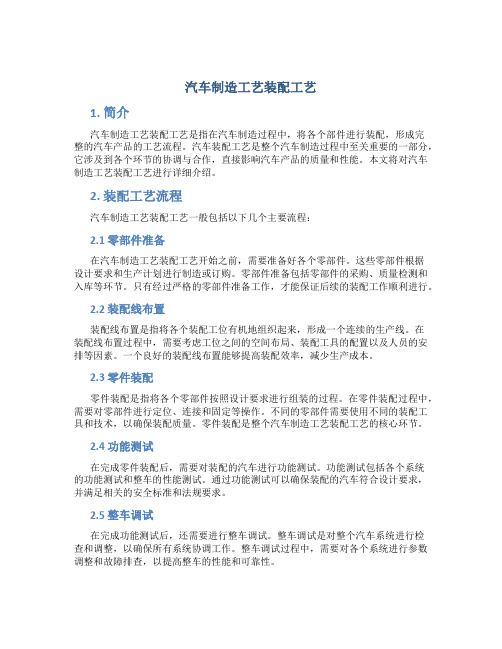
汽车制造工艺装配工艺1. 简介汽车制造工艺装配工艺是指在汽车制造过程中,将各个部件进行装配,形成完整的汽车产品的工艺流程。
汽车装配工艺是整个汽车制造过程中至关重要的一部分,它涉及到各个环节的协调与合作,直接影响汽车产品的质量和性能。
本文将对汽车制造工艺装配工艺进行详细介绍。
2. 装配工艺流程汽车制造工艺装配工艺一般包括以下几个主要流程:2.1 零部件准备在汽车制造工艺装配工艺开始之前,需要准备好各个零部件。
这些零部件根据设计要求和生产计划进行制造或订购。
零部件准备包括零部件的采购、质量检测和入库等环节。
只有经过严格的零部件准备工作,才能保证后续的装配工作顺利进行。
2.2 装配线布置装配线布置是指将各个装配工位有机地组织起来,形成一个连续的生产线。
在装配线布置过程中,需要考虑工位之间的空间布局、装配工具的配置以及人员的安排等因素。
一个良好的装配线布置能够提高装配效率,减少生产成本。
2.3 零件装配零件装配是指将各个零部件按照设计要求进行组装的过程。
在零件装配过程中,需要对零部件进行定位、连接和固定等操作。
不同的零部件需要使用不同的装配工具和技术,以确保装配质量。
零件装配是整个汽车制造工艺装配工艺的核心环节。
2.4 功能测试在完成零件装配后,需要对装配的汽车进行功能测试。
功能测试包括各个系统的功能测试和整车的性能测试。
通过功能测试可以确保装配的汽车符合设计要求,并满足相关的安全标准和法规要求。
2.5 整车调试在完成功能测试后,还需要进行整车调试。
整车调试是对整个汽车系统进行检查和调整,以确保所有系统协调工作。
整车调试过程中,需要对各个系统进行参数调整和故障排查,以提高整车的性能和可靠性。
2.6 质量检测在整车调试完成后,需要进行质量检测。
质量检测包括外观检查、性能检测和耐久性测试等。
质量检测能够发现装配过程中存在的问题和缺陷,并及时进行调整和修复,以确保装配的汽车质量达到标准。
2.7 最终装配和交付经过质量检测的汽车将进行最终装配和交付。
装配线计划
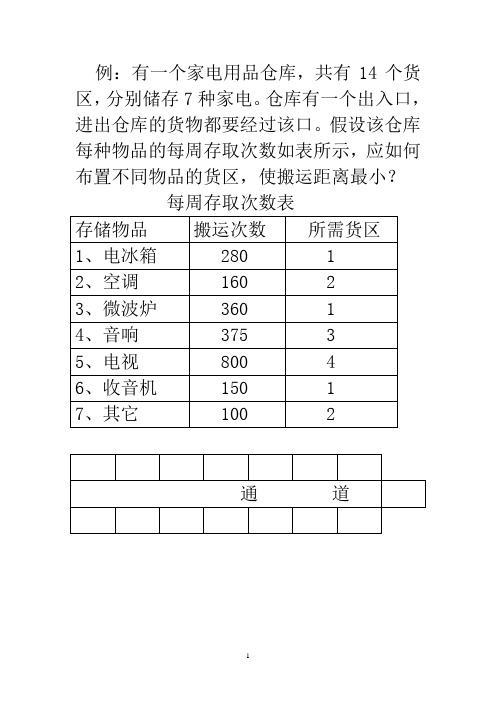
例:有一个家电用品仓库,共有14个货区,分别储存7种家电。
仓库有一个出入口,进出仓库的货物都要经过该口。
假设该仓库每种物品的每周存取次数如表所示,应如何布置不同物品的货区,使搬运距离最小?每周存取次数表4、生产线平衡步骤(1)用一个流程图表示作业先后关系(2)求出生产节拍 r = 计划期有效工作时间/计划期间计划产量 = Fe/N(3)计算满足节拍要求的最少工作地数S = 完成单件产品所需的总时间/节拍= ∑ti/r(4)将作业分配到各工作地(启发式分配规则)①从工作地1开始,从左向右给工作地分配作业。
②该工作地单件时间不超过工作地的剩余时间剩余时间 = 节拍—该工作地已分配作业单件时间之和③若干作业满足条件2a.分配后续作业数最多的作业b.分配加工时间最长的作业例1、一玩具要在一个传送带上组装,每天需生产500辆。
每天的生产时间为420分钟,下表中列出了玩具的组装步骤及其时间。
请(1)画出组装作业先后顺序图;(2)该组装线的节拍是多大;(3)求工作地最小数目。
玩具的组装步骤及其时间作业时间(秒) 紧前作业A 45 -B 11 AC 9 BD 50 -E 15 DF 12 CG 12 CH 12 EI 12 EJ 8 G,F,H,I K 6 J解:(1)画出流程图,表示作业先后关系FA BGD E H J KI(2)计算节拍节拍=每天的工作时间/每天的产量=420*60/500=50.4(秒/辆)(3)最小工作数目= 完成单件作业所需的总时间/节拍 =192/50.4=3.81最小工作地数目4个工作作作业剩余可安排的后续作业最时间最长地业时间时间紧后作业多的作业的作业1 A 45 5.4 无2 D 50 0.4 无3 B 11 39.4 C.E C .E EE 15 24.4 C.H. I CC 9 15.4 F.G.H.I F.G.H .I F.G.H.IF 12 3.4 无4 G 12 38.4 H .I H .I H.IH 12 26.4 II 12 14.4 JJ 8 6.4 KK 6 0.4 无例2. 一装配线计划每小时装配200件产品,每小时用于生产的时间是50分钟。
重型车装配生产线规划设计与实践装配生产线

重型车装配生产线规划设计与实践装配生产线公司根据汽车规模化生产需要,提出了对车辆装配采取上自动生产线装配模式的规划,这对原来一直采用地摊式手工做和的装配模式无疑是一种新的技术创新。
在结合公司重型车辆特点、产品品种多、近期产量规模不大、线体需具备兼容性、扩展性等特点,设计了使用多车型柔性装备的混流自动流水线的。
主要适用于三轴、四轴重型车,车型宽包括2.5mm及3mm。
1 总装车间生产线布置规划设计在总装车间生产线规划过程中,根据已有厂房的构造及210m×24m的作业面积,设计了三套生产线布置规划方案,即地面输送生产线、空中输送生产线、半自动输送生产线。
在对生产纲领、车型特点、装配工艺流程、生产线体经济性以及线体的运行形式等方面进行了综合考虑后,采纳了第一套方案并对工位设置及物流输送等方面进行了优化。
形成了由地面输送设备、工艺装备、部件分装区、物料输送线、照明、动力管网等构成的有机整体,完成了生产线布置规划设计。
设计了有效长度165mm的地拖链形势的自动生产线,生产线设置15个工位。
在分装区的布置规划上,为达到最短的物流配送路线,以保障物料配送及物料上线输送简短、便捷、顺畅。
将部件分装区布置自动生产线体相邻一侧,与生产线各工位装配内容一一对应。
在物料输送线的规划上,我们在综合考虑厂房空间的利用率、物料配送距离、人员移动的损耗和以后产能扩展的便利性等因素,将部件分装区一侧设置以主物流通道,通道宽度为4m,可允许火车或叉车配送物料。
生产线体另一侧色绘制一副物流通道,通道宽度为2.5m,只允许通过叉车配送物料。
2 装配生产线线体设计2.1 产品装配工艺流程设计根据产品特点,我们对装配线体工艺流程安排如下。
工位1:车架上线。
工位2:前桥安装,后板簧安装。
工位3:平衡悬架安装。
工位4:中、后桥安装,传动轴安装。
工位5:车架翻转、台车支点转换。
工位6:排气系消声器及管路安装,水箱、中冷器安装,发动机部位管路安装、分动器安装。
装配线如何合理布局_

装配线如何合理布局_装配线的布置受设备、产品、人员、物流运输与生产方式等多种因素的影响。
合理的装配线应尽量减少迂回、停整与搬运,保持装配生产的灵活性,并有效利用人力与面积,这不仅能使物流更加畅通,而且能有效提高生产效率。
企业或者工厂不论大小,最终目的是要以高质量的产品、低成本、最短的交货期与最佳的投产时间去开拓市场,因此企业需从经营的角度论证与确定装配线的设计原则。
首先应确定设计思想,具体设计从大而全向专业化、柔性化方向进展,不断改善装配线的布置,从而习惯新的生产经营要求。
确定基本指导思想如何的装配线布置才称之为合理呢。
我认为它应该达到下列几个目标:尽量减少迂回、停整与搬运;保持装配生产的灵活性;有效利用人力与面积;提高士气;为车间管理提供方便。
我们不仅需要一个理想的装配线布置,而且需要一个经济的装配线设计,尽量做到少投入、多产出。
装配线的设计要精心,否则,设计好的产品、昂贵的设备与良好的销售都会断送于拙劣的装配线设计。
同时,装配线的布置要与现代化管理相结合,要考虑如何进行管理,先进的管理方式有的直接与装配线布置有关,如全面质量管理、均衡生产管理、生产现场计算机管理、一个流生产方式、定置管理及物料管理等。
将这些管理纳入装配线的设计能提高管理的有效性。
影响装配线布置的因素:1.产品产品结构与装配过程设计是装配线设计中首要考虑的重点。
对产品结构进行分析、研究,提出改进产品结构的意见,能够大大简化装配生产过程。
2.设备装配工艺设备的选择是根据产品技术要求与装配工艺方法确定的。
正确选择工艺设备与工装,不仅能提高生产效率、降低制造成本,还可使装配线布置合理化。
选择工艺设备时要考虑的问题包含:产品生产纲领;产品质量要求;设备的先进性;设备的可靠性;设备的价格;设备的利用率;设备的安全性;设备维修的方便性。
3.人员人是生产要素之一,又是活的因素,且流淌性大,需通过培训使之习惯岗位工作的要求。
装配线布置时要考虑具备良好安全的劳动条件,制造一个较好的劳动环境,有助于提高劳动积极性。
一汽轿车总装简介(车间图片1)
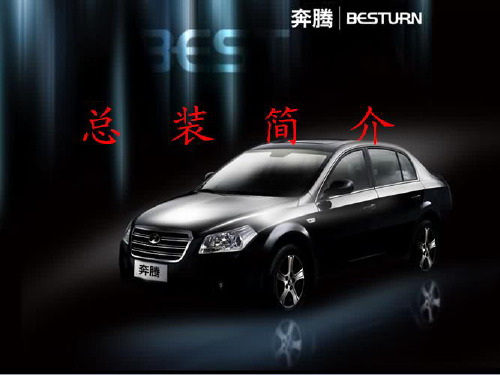
线165米,线宽10 米
装配工位21个
二 次 内 饰 装 配 线
装配工位 32个
线长297米, 宽10米
主要装配及检查内容: 装配轮胎、备胎、前后风窗玻璃、仪表板后段、 电瓶、前后座椅、车门模块等;加注燃油、动力 转向油、风窗清洗液、R134a防冻液等;调整车 门;检查电器功能和整车完整性。 机械化输送设备: 采用6″积放链输送机、5轨轨道输送和双板式 带输送机输送。 主要工艺设备: 轮胎、备胎、电瓶、座椅装配机械手、轮胎电 动定值拧紧机、燃油泄漏检查仪、燃油加注机、 四合一加注机、二合一加注机、车门装配机械手、 EOL写入设备、灯光隧道等。
冷却液
检测仪
发动机尾气排放检测
转鼓试验台
防撞气囊
驾驶员防撞气囊装配
四轮定位及前灯调整
前刹车器总成装配
前刹车器装配
动力总成装配线
动力总成装配线
付车架及发动机总成连接
前减震叉装配
后刹车器装配
后刹车器推力杆装配
后桥总成装配
后桥卷簧压装装配
底盘线设备
下臂定值拧紧机
AGV磁导航车
【总装生产线】
路试跑道 入库 9个工位 淋雨线 10个工位 10个工位 终检线 涂装车间送来的 车身
完整性检查
二次内饰
一次内饰(40工位)
检测线
仪表框分装
前桥分装 二 次 内 饰 ( 个 工 位 ) 底 盘 线 ( 24 个 工 位 ) 动力总成分装线 8个工位 后桥分装 20个工位 发动机与变速器分装线
生产车型:
1、M6及M6的系列变型车 2、基于M6底盘的自主开发车 3、MPV及其变型车 奔腾(C301)
M6轿车
4、B130车等
厂房建筑面积: 54463 m2 (主厂房占地47514 m2, 生产使用面积24300 m2,物流使用面积:23214 m2 ) 生产节拍:101秒 工位数:94个装配工位及36个检测、检查车位。 主要先进设备: 1、检测线:由美国宝克公司制造,具有国际最先进水 平。包括四轮定位仪、 转毂试验台、大灯检 测仪、侧滑实验台等。 2、加注机:由德国申克公司制造,具有国际最先进水 平。包括四合一加注机(加注介质:R134a、动力转 向油、防冻液、风窗清洗液)、二合一加注机(加 注刹车液、进行空调初抽真空)。 3、机械化输送系统:包含11条输送线,如:摩擦滑橇、 积放链、双板式带、积放轨道、自行葫芦输送机等。 4、室外配置1920米综合试验跑道。
装配流水线的设置和注意事项
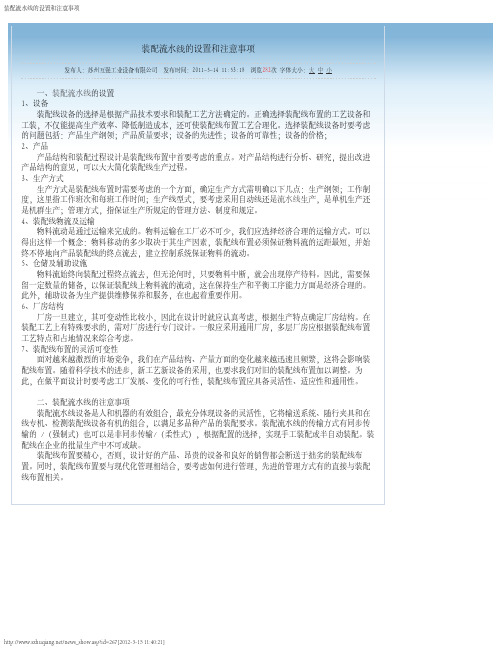
装配流水线的设置和注意事项
发布人:苏州互强工业设备有限公司 发布时间:2011-5-14 11:53:18 浏览282次 字体大小:大 中 小
一、装配流水线的设置 1、设备 装配线设备的选择是根据产品技术要求和装配工艺方法确定的。正确选择装配线布置的工艺设备和 工装,不仅能提高生产效率、降低制造成本,还可使装配线布置工艺合理化。选择装配线设备时要考虑 的问题包括:产品生产纲领;产品质量要求;设备的先进性;设备的可靠性;设备的价格; 2、产品 产品结构和装配过程设计是装配线布置中首要考虑的重点。对产品结构进行分析、研究,提出改进 产品结构的意见,可以大大简化装配线生产过程。 3、生产方式 生产方式是装配线布置时需要考虑的一个方面,确定生产方式需明确以下几点:生产纲领;工作制 度,这里指工作班次和每班工作时间;生产线型式,要考虑采用自动线还是流水线生产,是单机生产还 是机群生产;管理方式,指保证生产所规定的管理方法、制度和规定。 4、装配线物流及运输 物料流动是通过运输来完成的。物料运输在工厂必不可少,我们应选择经济合理的运输方式。可以 得出这样一个概念:物料移动的多少取决于其生产因素,装配线布置必须保证物料流的运距最短,并始 终不停地向产品装配线的终点流去,建立控制系统保证物料的流动。 5、仓储及辅助设施 物料流始终向装配过程终点流去,但无论何时,只要物料中断,就会出现停产待料。因此,需要保 留一定数量的储备,以保证装配线上物料流的流动,这在保持生产和平衡工序能力方面是经济合理的。 此外,辅助设备为生产提供维修保养和服务,在也起着重要作用。 6、厂房结构 厂房一旦建立,其可变动性比较小,因此在设计时就应认真考虑,根据生产特点确定厂房结构。在 装配工艺上有特殊要求的,需对厂房进行专门设计。一般应采用通用厂房,多层厂房应根据装配线布置 工艺特点和占地情况来综合考虑。 7、装配线布置的灵活可变性 面对越来越激烈的市场竞争,我们在产品结构、产量方面的变化越来越迅速且频繁,这将会影响装 配线布置。随着科学技术的进步,新工艺新设备的采用,也要求我们对旧的装配线布置加以调整。为 此,在做平面设计时要考虑工厂发展、变化的可行性,装配线布置应具备灵活性、适应性和通用性。 二、装配流水线的注意事项 装配流水线设备是人和机器的有效组合,最充分体现设备的灵活性,它将输送系统、随行夹具和在 线专机、检测装配线设备有机的组合,以满足多品种产品的装配要求。装配流水线的传输方式有同步传 输的 /(强制式)也可以是非同步传输/(柔性式),根据配置的选择,实现手工装配或半自动装配。装 配线在企业的批量生产中不可或缺。 装配线布置要精心,否则,设计好的产品、昂贵的设备和良好的销售都会断送于拙劣的装配线布 置。同时,装配线布置要与现代化管理相结合,要考虑如何进行管理,先进的管理方式有的直接与装配 线布置相关。
某产品装配线优化设计
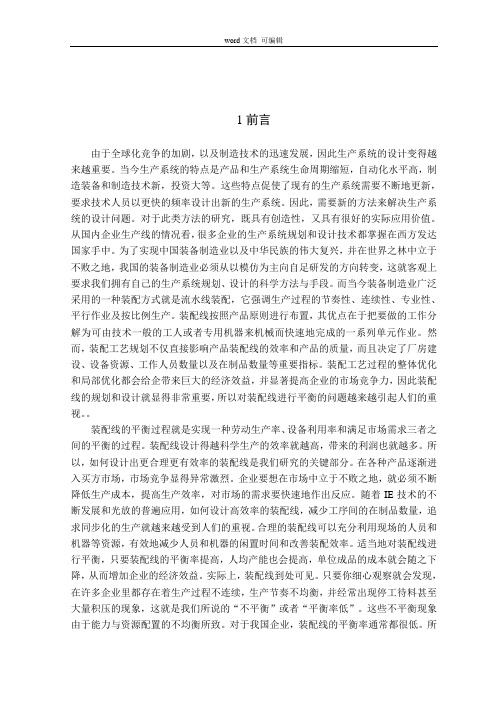
1前言由于全球化竞争的加剧,以及制造技术的迅速发展,因此生产系统的设计变得越来越重要。
当今生产系统的特点是产品和生产系统生命周期缩短,自动化水平高,制造装备和制造技术新,投资大等。
这些特点促使了现有的生产系统需要不断地更新,要求技术人员以更快的频率设计出新的生产系统。
因此,需要新的方法来解决生产系统的设计问题。
对于此类方法的研究,既具有创造性,又具有很好的实际应用价值。
从国内企业生产线的情况看,很多企业的生产系统规划和设计技术都掌握在西方发达国家手中。
为了实现中国装备制造业以及中华民族的伟大复兴,并在世界之林中立于不败之地,我国的装备制造业必须从以模仿为主向自足研发的方向转变,这就客观上要求我们拥有自己的生产系统规划、设计的科学方法与手段。
而当今装备制造业广泛采用的一种装配方式就是流水线装配,它强调生产过程的节奏性、连续性、专业性、平行作业及按比例生产。
装配线按照产品原则进行布置,其优点在于把要做的工作分解为可由技术一般的工人或者专用机器来机械而快速地完成的一系列单元作业。
然而,装配工艺规划不仅直接影响产品装配线的效率和产品的质量,而且决定了厂房建设、设备资源、工作人员数量以及在制品数量等重要指标。
装配工艺过程的整体优化和局部优化都会给企带来巨大的经济效益,并显著提高企业的市场竞争力,因此装配线的规划和设计就显得非常重要,所以对装配线进行平衡的问题越来越引起人们的重视。
装配线的平衡过程就是实现一种劳动生产率、设备利用率和满足市场需求三者之间的平衡的过程。
装配线设计得越科学生产的效率就越高,带来的利润也就越多。
所以,如何设计出更合理更有效率的装配线是我们研究的关键部分。
在各种产品逐渐进入买方市场,市场竞争显得异常激烈。
企业要想在市场中立于不败之地,就必须不断降低生产成本,提高生产效率,对市场的需求要快速地作出反应。
随着IE技术的不断发展和光放的普遍应用,如何设计高效率的装配线,减少工序间的在制品数量,追求同步化的生产就越来越受到人们的重视。
装配线使用说明书

一.概述 (2)二.系统操作 (2)1. 一般说明 (2)1. 主操作站 (3)2. A段180°翻转机操作分站 (7)3. A段90°翻转机操作分站 (8)3. 升降机1、3操作分站 (9)4. 型号选择按钮分站和机械手启动分站 (10)5. 主辅升降机/机械手操作分站 (10)6. C段线体滚道1操作分站 (13)7. 线体急停操作分站 (14)8. 注意事项: ..................................................... 错误!未定义书签。
三.触摸屏操作 . (15)三.系统维护 (22)1. 系统的故障查找方法 (22)2. 系统的故障排除 (23)一.概述杭州汽车发动机厂柴油机装配线(以下简称装配线)电气系统采用日本三菱公司Q2AS PLC、975GOT(触摸屏)及CC-LINK现场总线构成。
1.使用电源:主电源:交流380V、50Hz(工厂供电)电机电源:交流380V、50Hz交流控制回路:交流220V、50Hz直流控制回路:DC:DC24V按钮开关:DC24V接近开关、光电开关、电磁阀:DC24V注意:电气柜内粉色线为一次线,即在主电源开关断电时仍然有电,主要为电气柜散热器、电气柜照明供电。
电气柜门上设电源通断按钮开关,控制电气柜内主断路器的电动手柄,实现总电源的通断。
1.声光报警:柜顶安装塔灯及喇叭。
塔灯为三色,红色为系统故障报警,黄色表示设备正在调整,绿色表示系统正在正常运行。
喇叭在系统工作准备及自动启动按钮按下时响起,对线体上工作人员起警示作用。
柜门上设有小型蜂鸣器,故障时响起,按“蜂鸣器停止”或“报警复位按钮”停止。
电气柜内设散热风扇及照明灯,均由柜门联锁行程开关控制:柜门关闭时散热风扇工作,为电气柜散热;柜门打开时照明灯亮。
二.系统操作1. 一般说明1.操作控制分手动和自动方式,一切动作从操作站面板或触摸屏下指令,由按钮或切换按钮来控制。
汽车生产线施工方案装配工艺与流水线布置

汽车生产线施工方案装配工艺与流水线布置一、引言汽车生产线施工方案装配工艺与流水线布置是汽车制造过程中至关重要的一环。
为了保证汽车生产的质量、效率和安全性,需要制定合理、科学的施工方案与装配工艺,并对流水线进行适当的布置。
二、施工方案的制定1. 施工前期准备在制定施工方案之前,需要对整个生产线进行充分的调研和评估。
这包括对工厂场地、设备条件、人员配备等的全面了解。
同时,根据产品的特点和需求,制定出满足生产要求的施工方案。
2. 施工流程规划在制定施工方案时,需要明确整个生产线的流程和工序,并确定每个工序所需的所需时间、人员和设备。
合理的流程规划可以最大限度地提高生产效率和降低生产成本。
3. 设备布置根据产品的特点和生产要求,对设备进行合理的布置。
需要考虑设备之间的空间关系、设备与人员之间的距离以及设备的通风、安全等要求。
4. 人员培训和安全在施工方案中,还要考虑到人员的培训和安全。
对于高风险的工序,需要进行相关的培训,并落实安全措施,确保员工的身体健康和安全。
三、装配工艺的设计1. 零部件的选材和加工在汽车生产线的装配过程中,零部件的选材和加工至关重要。
需要根据产品的设计要求和性能需求,选择合适的材料,并对零部件进行精确的加工和检验。
2. 装配工序的安排根据产品的结构和装配顺序,合理安排装配工序。
需要确保每个工序都能顺利进行,并避免因为装配上的错误导致产品的损坏或质量问题。
3. 装配工具和设备的选择为了提高装配的效率和质量,需要选择合适的装配工具和设备。
这包括使用专业的工具和设备,如紧固工具、喷涂设备等,以及采用自动化装配设备来提高生产效率。
四、流水线布置1. 流程分析和优化在进行流水线布置之前,需要进行流程分析和优化。
根据产品的特点和生产要求,合理划分流水线的工序和工作站,以达到最佳的生产效率和质量。
2. 空间布局和平衡在流水线布置过程中,需要合理进行空间布局和平衡。
这包括确定每个工作站的位置和间距,确保操作人员能够顺畅进行工作,并且设备之间的空间能够满足操作和维护的需求。
总装车间布置经验

第 14 页
三、一汽-大众汽车总装车间简介
3.2 总装车间主要数据
Jetta轿车:
年设计纲领15万辆,采用二班工作制生产,生产节拍1.5分钟,整车单台装配总工时为15小
时,年设计纲领总劳动量225万小时。达产时设计工作人员总数为1580人。总装车间工艺投 资总数为2409万马克及6754万人民币。设备总台数221台(条),其中国外引进设备48台套。 Jetta轿车总装、分装、调试、返修所占面积37200m2。 所需非标准专用工装、夹具、吊具及工位器具68种2248台(套),所需专用工具98种670把 (件)。均为国内设计制造。 所需国内标准工具100种6687件,投产前一次性引进国外工具约30种386件。
空调、加速制动踏板等重要的零部件。一般情况下,这些部件都由不同的供应商提供。
第4页
一、总装车间的布置
1.2 动力总成工段
发动机是汽车的心脏,而动力总成则囊括了发动机、离合器、变速箱、前后桥以及悬架等 汽车底部重要的零部件。由于动力总成的组成零部件比较多,一般整车厂会将其设置为独 立的一条“副线”,工人们在副线上完成动力总成的装配,再由推车把此模块送到总装
3.2 总装车间主要数据
厂房及公用工程: 设在厂房屋顶上南北各一排的通风机房共装有40台送风机组,其送风管路系统沿厂房屋架 上的最上层敷设,并沿厂房柱子向下延伸到3.5m高度均匀分布,共设有360个送风口,上述 系统的采用使车间内的总送风量达2.4×l06m3/h,夏季每小时换气次数3次,冬季新鲜空气 补充量9.2×l06m3/h,每小时换气次数一次。厂房内冬季设计采暖温度为16℃。该系统的实
总装车间布1、认识和了解整车总装生产线布置方式 2、探讨总装车间布置优缺点。
第1页
生产线布局(超详细)全解

2019/3/31
6
产生更严重的成本连锁反应……
“一人错误百人忙” 的成本暴增曲线
更多的 防火成本
更多的 救火成本 更多的 返工成本
救火、防火、多余监 督、过度控制、多余 检验、投诉处理、退 货维修、商誉损失、 顾客流失等效应连锁 扩大成本! 重工、返修、报废成本
日常管销/制造成本
7
正常成本
2019/3/31
2019/3/31
精益生产方式
1. 采用了看板管理,拉动生产方式 2. 车间布局U型布局; 3. 不同类型的机器摆放在一块; 4. 实现了单件流的生产; 5. 机器小型化 ; 6. 工序中间很少甚至没有库存; 7. 实现了作业标准化; 8. 对工人实行了多技能培训; 9. 具有完善的作业改善活动制度
= 0.007 分钟/产品
换句话说,每分钟生产140单位的产品。
2019/3/31 40
产品原则布局
4.进行作业活动分配(作业活动分配到各工作站) 5.向工作站分配作业(作业活动在工作站内分配) 6.评估装配线平衡后的效率 E=T/(Na × Ct)
E——装配线平衡效率 T——完成作业所需的时间总量 Na——实际工作站数 Ct——生产节拍
• 将原材料和设备按照使用次序和移动的难易程度 在产品的四周进行生产
起源
• 19世纪初亨利福特的汽车装配线
2019/3/31
17
定位原则布局
使用范围:
• 批量小 • 体积大
布局特点
• 以产品为中心 • 不考虑物流成本和复杂程度
2019/3/31
18
工艺原则布局
定义:
• 将相似的设备或功能集中放在一起的布局方式 • 也称车间布局,如车床车间
- 1、下载文档前请自行甄别文档内容的完整性,平台不提供额外的编辑、内容补充、找答案等附加服务。
- 2、"仅部分预览"的文档,不可在线预览部分如存在完整性等问题,可反馈申请退款(可完整预览的文档不适用该条件!)。
- 3、如文档侵犯您的权益,请联系客服反馈,我们会尽快为您处理(人工客服工作时间:9:00-18:30)。
装配线布置(一)
设备
装配线设备的选择是根据产品技术要求和装配工艺方法确定的。
正确选择装配线布置的工艺设备和工装,不仅能提高生产效率、降低制造成本,还可使装配线布置工艺合理化。
选择装配线设备时要考虑的问题包括:产品生产纲领;产品质量要求;设备的先进性;设备的可靠性;设备的价格;
产品
产品结构和装配过程设计是装配线布置中首要考虑的重点。
对产品结构进行分析、研究,提出改进产品结构的意见,可以大大简化装配线生产过程。