第五章 主生产计划
第五章 主生产计划制定 (2)教材

产品
X Y
1周
30 20
2周
30 20
3周
30 20
4周
40 15
5周
40 15
第三节 粗生产能力计划
产品X、Y的物料清单
父件 子件 所需数量
产品X、Y能力需求
最终产品 单位能力需求 1.05 X Y 1.85
X
X Y Y C
A
A B C D
1
2 1 2 2
第一节
主生产计划
二、主生产计划制造环境 其计划对象是基于独立需求的最终物料,可能是最
终产品,也可能是一般的零件或部件。 关于制造环境,在第三章成品库存类型介绍过,4种 情况生产模式:备货生产,订货组装,订货制造,订货工 程方式。 MPS对象是基于最终产品,对不同制造环境其概念 不同。 1、备货生产: 先生产产品,依靠库存来满足要求,它是根据随市 场需求预测和安全库存,期初库存来制定MPS。备货生 产对象是生产流通领域内直接销售的产品。MPS和FAS 的计划对象是一致的,是产品结构中的顶层。
如图,一个最终产品由4个次组件和1个零件组成,每个
次组件有不同型式,如SA1有4种型式,SA2有2种,SA3 有3种,SA4有3种。 最终产品:
第一节
主生产计划
SA1 SA1
1
SA2 SA2
1
SA3 SA3
1
SA4 SA4
11
C C1 C2 C3 C4 C5
东北林业大学工程技术学院
第五章 主生产计划制定
第五章 主生产计划制定
1 3
2 3
第一节
主生产计划
第二节 主生产计划制定步骤 第三节 粗生产能力计划
第5章 主生产计划三大

主生产计划的计算过程: 首先根据预测量和合同量确定毛需求, 再根据毛需求和现有库存量及计划接受量来计算净需求,
从而确定何时投入?何时产出?投入多少?产出多少?
二、计算毛需求(Gross Requirements,GR)
毛需求不是预测信息,而是生产信息。 毛需求具有时段性,在需求时界内,毛需求=实际顾客合同量;在计划 时界内,毛需求取与测量和合同量中的最大值。在计划时界以外,毛需求 取预测值。
二、MPS的维护与修改(next lesson)
1、MPS的维护: 主生产计划是一个不断更新的滚动计划。 计划的变动、产品结构的变化、工艺的变动、采购件拖 期、加工件报废等都要修改MPS或MRP。更新的频率与需 求预测周期、客户订单的变更情况等因素有关。
2、MPS的修改:
一旦时间栏设定,一般不希望改动它们。部分原因是时间栏表明了修 改计划的困难程度和代价。不过,确有一些情况需做修改: 某用户变更或取消定单 可利用的生产能力发生变化(设备故障等) 无法提供原计划的材料,不得不停止生产 供方失约 出现过多的废品
时区:
MPS将计划展望期分为需求时区、计划时区和预测时区,不同时区的分 割点称作时界,有需求时界和计划时界。
总提前期 或 计划跨度 累计提前期(采购+加工+总装) 总装提前期
时区3
时区2
时区1
某时刻
计划时界 计划确认时界
需求时界
计划完工
时间顺序
时段: 1
2
3
4
5
6
7
8
9
10 11 12 13 14
MPS报表:
MPS的常见报表格式有:横式报表、竖式报表、综合报表。 横式报表:横式报表主要说明需求和供给以及库存量的计算过程。表 头部分信息来自物料主文件,除了现有库存量随时间变动外,其余信息属 于静态信息。
主生产计划内容及原理
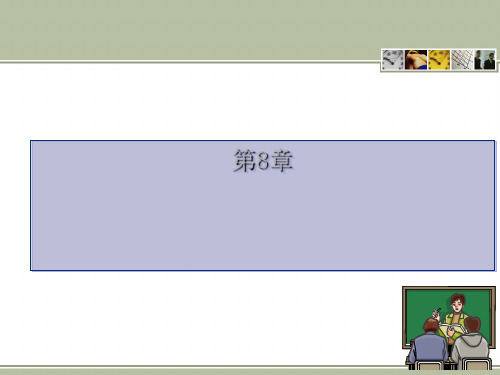
量和期初库存量,计算各时区的主生产计划产出量和预计可用 库存量。 (4) 计算可供销售量供销售部门决策选用。 (5) 用粗能力计划评价主生产计划备选方案的可行性。 (6) 评估主生产计划。 (7) 批准和下达主生产计划。
实际需求:已经接到客户订单,并做出了发货承诺,但 尚未发货。预测的客户订单;增加的客户订单
未消耗的预测:尚未被实际的客户订单消耗的预测,它 指出还可以期望得到多少客户订单
未消耗的预测=某时区的预测值减去同一时区的客户订 单
早于需求时界的累计未消耗的预测:移到需求时界之后 的第一个时区或忽略不计
客观环境是不断变化的,生产计划应当适应客观变化。但是,如果一味追随变化,朝 令夕改,势必造成生产上的混乱。因此,控制计划变动是保证计划可执行程度的重要 内容。当需要变动时,要分析变动计划的限制条件、难易程度、需要付出的代价并确 定审批权限,从而谋求一个比较稳定的主生产计划。ERP系统提出了时区与时界的概 念,向主生产计划员提供一个控制计划的手段。时界表明了修改计划的困难程度。修 改的时间越接近当前时间,则修改的困难越大。但有些情况,也不得不进行修改。例 如: ● 用户变更或取消订单。 ● 生产能力发生显著变化(例如,机床故障) ● 无法提供原计划所需材料(比如由于供方失约、原材料短缺等原因),不得不停止或 减少生产。 ● 出现过多废次品。 在修改MPS时,应着重考虑以下因素: ● 是否影响对用户的服务水平? ● 成本增加了没有? ● 所用物料是否增加? ● MPS的可信度是否严重下降? 确认订单和下达订单系统都不能自动修改,以保持计划的稳定性。如果要改,只能人 工修改,或把订单状态改回到计划状态,由系统修订。
第五章 主生产计划
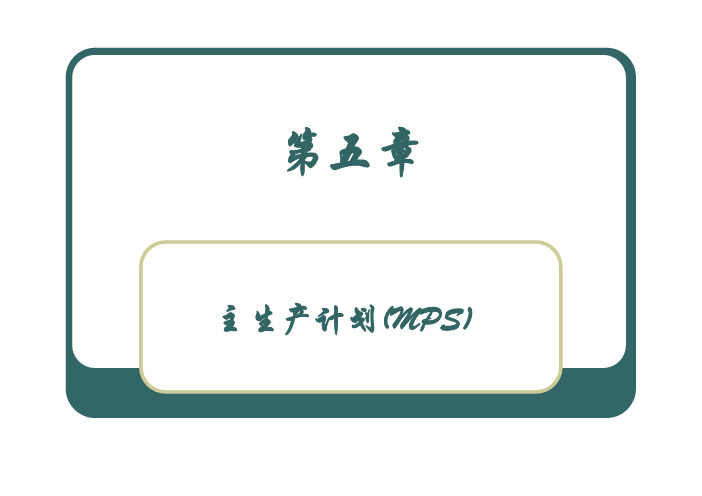
毛需求量的确定
毛需求量是生产信息,是分时段给出的。 将订单与预测结合起来,不同时段的毛需求确定有 如下方法:
⎧ Di (t ) ⎪ ⎪ GRi (t ) = ⎨max[ Di (t ), Fi (t )] ⎪ ⎪ Fi (t ) ⎩
t ≤ td td < t ≤ t p tp < t
毛需求量的确定
如何制定1-10周的主生产计划!
主生产计划的制定
表 5.2 预测和合同量
1 预测量 合同量 20 25 2 20 18 3 20 23 4 20 16 5 20 28 6 20 15 7 20 24 8 20 18 9 20 20 10 20 18
需求时界
计划时界
毛需求量的确定
表 3 毛需求计算结果 1 20 25 25 2 20 18 18 3 20 23 23 4 20 16 20 期间(周) 5 6 20 20 28 15 28 20 7 20 24 24 8 20 18 20 9 20 20 20 10 20 18 20
不同生产模式下的毛需求量确定 将订单与预测结合起来,有如下方法: (1)毛需求量=预测量------ 适合于备货生产 (2)毛需求量=订单量 ----- 适合于定货生产 (3)毛需求量=Max(预测量,订单量) ------适合于既有订单又有市场需求
在途量及预计在库量的确定
在途量(Scheduled Receipt, SR) 已经订购或者生产,预计在期间t到货的物料量SR(t)。 预计在库量(Projected On-Hand, POH) 假定某期间没有计划订单产出,则期末预计库存量 称为预计在库量。 POHi(1)= OH+SRi(1)-GRi(1) POHi(t)=PABi(t-1)+SRi(t)-GRi(t) 其中PABi(t-1)为预计可用库存量。
erp知识点总结
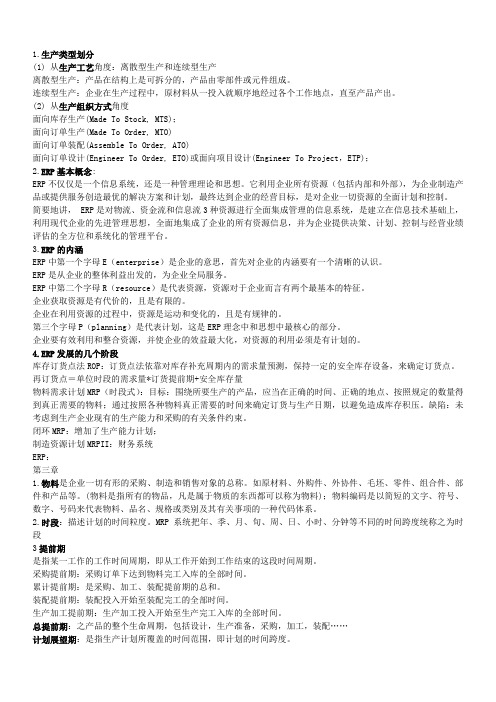
1.生产类型划分(1) 从生产工艺角度:离散型生产和连续型生产离散型生产:产品在结构上是可拆分的,产品由零部件或元件组成。
连续型生产:企业在生产过程中,原材料从一投入就顺序地经过各个工作地点,直至产品产出。
(2) 从生产组织方式角度面向库存生产(Made To Stock, MTS);面向订单生产(Made To Order, MTO)面向订单装配(Assemble To Order, ATO)面向订单设计(Engineer To Order, ETO)或面向项目设计(Engineer To Project,ETP);2.ERP基本概念:ERP不仅仅是一个信息系统,还是一种管理理论和思想。
它利用企业所有资源(包括内部和外部),为企业制造产品或提供服务创造最优的解决方案和计划,最终达到企业的经营目标,是对企业一切资源的全面计划和控制。
简要地讲, ERP是对物流、资金流和信息流3种资源进行全面集成管理的信息系统,是建立在信息技术基础上,利用现代企业的先进管理思想,全面地集成了企业的所有资源信息,并为企业提供决策、计划、控制与经营业绩评估的全方位和系统化的管理平台。
3.ERP的内涵ERP中第一个字母E(enterprise)是企业的意思,首先对企业的内涵要有一个清晰的认识。
ERP是从企业的整体利益出发的,为企业全局服务。
ERP中第二个字母R(resource)是代表资源,资源对于企业而言有两个最基本的特征。
企业获取资源是有代价的,且是有限的。
企业在利用资源的过程中,资源是运动和变化的,且是有规律的。
第三个字母P(planning)是代表计划,这是ERP理念中和思想中最核心的部分。
企业要有效利用和整合资源,并使企业的效益最大化,对资源的利用必须是有计划的。
4.ERP发展的几个阶段库存订货点法ROP:订货点法依靠对库存补充周期内的需求量预测,保持一定的安全库存设备,来确定订货点。
再订货点=单位时段的需求量*订货提前期+安全库存量物料需求计划MRP(时段式):目标:围绕所要生产的产品,应当在正确的时间、正确的地点、按照规定的数量得到真正需要的物料;通过按照各种物料真正需要的时间来确定订货与生产日期,以避免造成库存积压。
主生产计划
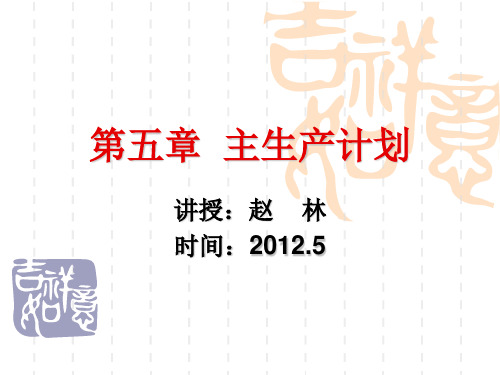
5-17
5.2.2 主生产计划的制订及计算逻辑
1、相关原始参数的确定
制订主生产计划时,应以时间分段记 录来说明主生产计划量、销售预测、预计 可用库存量和可供销售量之间的关系。
主生产计划的常用原始参数如表5.1所 示:
Copyright @ 济南大学机械工程学院,赵林, All Right Reserved
3、订货生产或订货工程
计划对象相当于产品结构的低层。 最终组装计划对象——产品结构的顶层产品。
Copyright @ 济南大学机械工程学院,赵林, All Right Reserved
5-7
5.1.3 主生产计划的制造环境
最终产品 MPS/FAS FAS 最终产品 FAS 最终产品
MPS
主生产计划是安时间分段计划企业应生产的最终产品
的数量和交货期。
主生产计划是一个滚动的计划。
Copyright @ 济南大学机械工程学Байду номын сангаас,赵林, All Right Reserved
5-4
5.1.2 计划对象
Month 1 2
Mattress production
900
950
Aggregate production plan for mattress
Rough-cut capacity Planning
Material Requirement Planning (MRP)
Capacity Req. Planning
仓库容量,技术人员和资金 需求的依据。
Short range
Operations Scheduling (Shop floor Scheduling & Control)
第五章主生产计划MPS

经济批量法
指某种物料的订货费用和保管费用之和为最低时的物料最佳批量法。 该方法适用于需求连续、库存消耗稳定的物料。这时需要增加描述经济 批量的属性。
7.计划产出量 8.计划投入量 9.可供销售量
➢ 未交付的订货及客户订单 ➢ 最终项目的预测 ➢ 工厂内部的需求 ➢ 备件 ➢ 客户可选件和附件
5.3 编制MPS初步计划
5.3.1 编制MPS计划的相关术语
计划展望期 时界
时段 时区
各时区、时界的关系如图6.2表示:
计划展望期或总提前期 累计提前期(采购+加工) 总装提前期
需求时区
计划时区
预测时区
当前
需求
计划
时期
时界
时界
计划
1 2 3 4 5 6 7 8 9 10 11 12 13 14 15 16 17 18 19 20 21
周期
5.3.2 编制MPS计划的基本步骤
1.编制MPS的基本思路
(1)根据生产规划和计划清单确定对每个最终项目的生产预测。 (2)根据生产预测、已收到的客户订单、配件预测以及该最终
5.2 MPS基本原理
5.2.1 MPS编制原则
❖ 最少项目原则 ❖ 独立具体原则 ❖ 关键项目原则 ❖ 全面代表原则 ❖ 适当裕量原则 ❖ 适当稳定原则
5.2.2 主生产计划的对象
5.2.3 MPS的策略
➢ 主生产计划的基本原则 ➢ 预测 ➢ 展望期和计划时区 ➢ 交流
5.2.4 确定MPS需求数据
思考题:
1.什么是主生产计划? 2.请说明主生产计划的作用。 3.说明主生产计划编制对象的选择原则。 4.净需求量是如何产生的 ? 求净需求量有何意义? 5.说明制订主生产计划的步骤。 6.如何确定毛需求量?
主生产计划详解

主生产计划作用与意义主生产计划在MRPⅡ系统中的位置是一个上下内外交叉的枢纽,地位十分重要。
在运行主生产计划时要相伴运行粗能力计划,只有经过按时段平衡了供应与需求后的主生产计划,才能作为下一个计划层次——物料需求计划的输入信息,主生产计划必须是现实可行的,需求量和需求时间都是符实的。
主生产计划编制和控制是否得当,在相当大的程度上关系到MRPⅡ系统的成败。
这也是它称为“主”生产计划的根本含义,就是因为它在MRPⅡ系统中起着“主控”的作用。
1.1 MPS编制原则●最少项目原则:用最少的项目数进行主生产计划的安排。
如果MPS中的项目数过多,就会使预测和管理都变得困难.因此,要根据不同的制造环境,选取产品结构不同的级,进行主生产计划的编制。
使得在产品结构这一级的制造和装配过程中,产品(或部件)选型的数目最少,以改进管理评审与控制。
●独立具体原则:只列出实际的、具体的可构造项目,而不是一些项目组或计划清单项目。
这些产品可分解成可识别的零件或组件。
●关键项目原则:列出对生产能力、财务指标或关键材料有重大影响的项目.对生产能力有重大影响的项目,是指那些对生产和装配过程起重大影响的项目。
如一些大批量项目,造成生产能力的瓶颈环节的项目或通过关键工作中心的项目。
对财务指标而言,指的是与公司的利润效益最为关键的项目。
如制造费用高,含有贵重部件,昂贵原材料,高费用的生产工艺或有特殊要求的部件项目。
也包括那些作为公司主要利润来源的,相对不贵的项目.而对于关键材料而言,是指那些提前期很长或供应厂商有限的项目。
● 全面代表原则:计划的项目应尽可能全面代表企业的生产产品。
MPS 应覆盖被该MPS 驱动的MRP 程序中尽可能多数组件,反映关于制造设施,特别是瓶颈资源或关键工作中心尽可能多的信息。
● 适当裕量原则:留有适当余地,并考虑预防性维修设备的时间.可把预防性维修作为一个项目安排在MPS 中,也可以按预防性维修的时间,减少工作中心的能力。
第五章主生产计划(学生课件)

⑦ 计划产出量:系统计算得到的供应数量; 当净需求 > 0,计划产出量=N * 批量
⑧ 计划投入量:根据计划产出量、物品的提前期及物品的合 格率等计算出的投入量;
⑨ 可供销售量:某时段内,物料的产出数量若大于订单的数 量,这个差值就可以用于销售。 =某期间的计划产出量+包括计划接收量)-下一次出 现计划产出量之前各时段合同量之和
净需求量 3
32
计划产出量4
200
计划投入量5 200
200
预计库存量 88
160
2
可供销售量 88
188 96 8
4 200
200
216 136 24
-16
76
36
200
200
200
144 64 184
112
-10
76 200
200
104 24 144
140
可供销售量 80 0
0
102
0
140
(调整后)
周 预测 实际需求 毛需求量 净需求量
计划产出量
计划投入量 预计库存量 可供销售量
需求时区 12 3 90 85 80 72 100 92
计划时区 4567 80 80 80 80 40 64 112 40
预测时区 8 9 10 11 12 80 80 80 80 80 48 75 65 70 60
2019/11/14
8
5.1.2 各种BOM简介
A
① 单层BOM
10(3)
B
C
20
D(2)
30(2)
40
50
项目A 项目 数量 B1
10 3
C1
10
主生产计划ppt课件
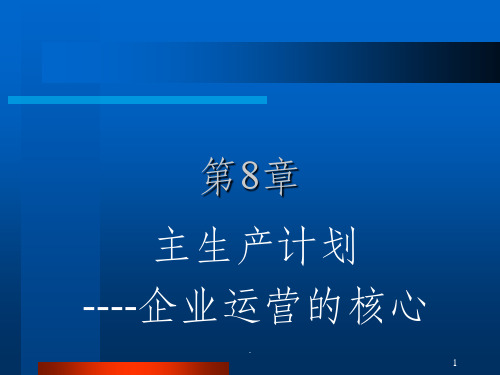
主生产计划(MPS)
• 主生产计划是制造部门的计划。它反应市场需求 和制造部门的能力,形成一个优先计划让制造部 门遵循。
• 主生产计划也是市场销售部门的计划,因为它在 市场销售部门和生产部门之间建立以下重要联系:
– 主生产计划是企业对客户订单承诺成为可能,它计 划生产什么及何时生产。因此,它告知销售和制造 部门,产品在什么时候可以交付客户使用。
3个产品构成的产品族的生产规划
周
123456
预测
160 160 160 160 215 250
生产规划量 205 205 205 205 205 205
总库存量 545 590 635 680 670 625
产品族中个产品 的期初库存量: 产品A: 350 产品B: 100 产品C: 50 总计: 500
周 产品A 产品B 产品C 总预测量
一份主生产计划草案 123456
205 205 205 205
205 205 205 205 205 205 205 205
满意之处: ▪告诉工厂何时开始 及停止生产。 ▪能力与生产规划相 符
不满意之处: ▪与总库存相比, 其库存量平衡性差 ▪导致在第2和第3 周产品C缺货。
– 主生产计划是市场部和生产部门之间的契约,它是 一个双方认可的计划。
.
主生产计划(MPS)
• 制定主生产计划所需要的信息来源:
– 生产规划; – 单个终端产品的预测; – 收到的客户实际订单及库存补充; – 单个中断产品的库存量; – 能力限制。
.
主生产计划(MPS)
• 主生产计划和生产规划关系
• 生产规划控制住生产计划,主生产计划中的产品生产总量 应该等于生产规划中的产品生产总量。例如:如果生产规划
ERP原理:主生产计划——第五章

• RCCP:粗略产能规划 (Rough Cut Capacity Planning) 产能管理技术,通常分为四类:资源需求计划(RR P)、粗略产能规划(RCCP)、产能需求规划(CRP)以 及输入/输出控制(I/O)。在MRP系统中,典型的顺 序是建立主排程,使用RCCP来确认MPS是否可行, 把展开后的MRP表现出来,并且把以规划订单的 数据送到CRP中。
主生产计划报表
• 主生产计划一般按每种产品分别显示生产计划报 表。
• 报表的生成主要根据预测和合同信息,显示该产 品在未来各时段的需求量、库存量和计划生产量。
• 报表格式有横式和竖式两种。
例5.1 假定某叉车厂期初库存为160台,安全库存量为20台,生产批量为 200台,需求时界2,计划时界6,则MPS计划如表5-6所示。
• MM物料管理是SAP R/3系统的一个模块。
• SD(Sales and Distribution)模块,中文名称为销售与 分销模块。SD模块处理有关销售、装运、单据开 具的任务。
资源需求计划(RRP,Resource Requirements Planning)
预计可用库存 Projected Available
● 适当稳定原则:在有效的期限内应保持适当稳定。 主生产计划制订后在有效的期限内应保持适当稳定, 那种只按照主观愿望随意改动的做法,将会引起系 统原有合理的正常的优先级计划的破坏,削弱系统 的计划能力。
5.4 主生产计划的对象
• 主生产计划的计划对象主要是把生产规划中的产 品系列具体化以后的出厂产品,通称最终项目(En d Item),所谓“最终项目”通常是独立需求件。
5.1 MPS概念及内容 5.2 MPS作用与意义 5.3 MPS编制原则 5.4 主生产计划的对象 5.5 MPS基本方法 5.6 主生产计划的编制 5.7 MPS的实施与控制 5.8 本章小结
第五章 主生产计划

自行车分为24型和28型 自行车分为24型和28型 24型和28
时间跨度: 时间跨度:年、几年 计划时间单位: 双月、 计划时间单位:月、双月、季 人员:分组, 人员:分组,加班以及聘用等
2、主生产计划(MPS)
确定每一具体的最终产品在每一具体的时 间段内的生产数量
最终产品:本企业最终完成、 最终产品:本企业最终完成、要出 厂的完成品 计划时间单位:周(旬、日、月) 计划时间单位:
5.1 粗能力计划的计算
2(3)再确定各时段的负荷由哪些物品引起 ( ) 的,各占用的资源情况如何,然后平衡工 各占用的资源情况如何, 作中心的能力,同时要总体平衡 作中心的能力,同时要总体平衡MPS的最 的最 终产品的各子件的进度(可初步平衡, 终产品的各子件的进度(可初步平衡,详 细的平衡在物料需求计划与能力需求计划 时制订进行)。 时制订进行)。
3、物料需求计划
主生产计划确定以后,生产管理部门下一 主生产计划确定以后,生产管理部门下一 步要做的事是 的事是, 步要做的事是,保证生产主生产计划所规 定的最终产品所需的全部物料(原材料、 定的最终产品所需的全部物料(原材料、零 部件等) 件、部件等)以及其他资源能在需要的时候 供应上。 供应上。 所谓的物料需求计划 物料需求计划, 所谓的物料需求计划,就是要制定这样的 原材料、零件和部件的生产采购计划: 原材料、零件和部件的生产采购计划:外 购什么、生产什么、 购什么、生产什么、什么物料必须在什么 时候订货或开始生产,每次订多少, 时候订货或开始生产,每次订多少,生产 多少等等。 多少等等。
5.2 粗能力计划(RCCP) 粗能力计划的制定
1. 建立关键工作中心的资源清单 2. 寻找超负荷时段 3. 确定各时段负荷的起因
主生产计划模板ppt课件

25. .主1生主产计生划时产段计的划划分的基本概念 某产品单次生产计划在时间上的时区分布关系
时区3
总提前期 或 计划跨度
累计提前期(采购+加工) 总装提前期
时区2
时区1
某时刻
计划时界
需求时界
计划完工
时间顺序
计划确认时界
时段:1 2 3 4 5 6 7 8 9 10 11 12 13 14 15 16 17 18 19 20 21
5.2 主生产计划的计算逻辑
15+20-25= 10
10+0-18= - 8
5.2 主生产计划的计算逻辑
5.2.5 计算净需求(Net Requirement) 净需求实质就是实际生产需求。因为毛需求是根据客户订单
和预测得到的一个需求值,并没有考虑现有库存量。净需求 不一定等于毛需求。
不考虑安全库存:
5.1 主生产计划的基本概念
5.1.4 MPS的时段概念
1. MPS的变与不变 可实行性的最大挑战是如何适应持续不断的变化。
变的因素包括: 内部:设备故障、质量事故、缺料待料等。 外部:市场需求变化、顾客取消定单。 导致:主生产计划的增加、减少、提前、推后
(最终产品)。 时段性解决了这个问题。在MRPⅡ应用计算机轻
时区是说明某一计划的产品(物品)在某时刻处于该产 品(物品)的计划跨度内的时间位置 时区1:是产品的总装提前期的时间跨度,即指从产品投 入加工开始到产品装配完工的时间跨度 时区2:在产品的累计提前期的时间跨度内,超过时区1 以外的时间跨度 时区3:超过时区2以外的时间跨度 需求时界(Demand Time Fence):时区1与时区2的分界 点 计划时界(Planning Time Fence):时区2与时区3的分界点
- 1、下载文档前请自行甄别文档内容的完整性,平台不提供额外的编辑、内容补充、找答案等附加服务。
- 2、"仅部分预览"的文档,不可在线预览部分如存在完整性等问题,可反馈申请退款(可完整预览的文档不适用该条件!)。
- 3、如文档侵犯您的权益,请联系客服反馈,我们会尽快为您处理(人工客服工作时间:9:00-18:30)。
时段 1 2 3 4 5 6 7 8 9 10 11 12 13 14 15 16 17
长度 月周 月周 月周 月 周 月周 月周 月周 月周季 月周季 月周季 月周— —月周 季月— 季月— 月—季 —季 —
第一 月第前:一3周年月计:划月周,计后划三,月:月计划,后九第后月二三:年月季:计季月划计划
❖ 在生产任务管理中检查生产任务的处理情况;
❖ 在委外加工任务管理中检查委外加工任务的处理情 况;
❖ 在主生产计划中设置 MPS 向导方案; ❖ 在主生产计划中根据 MPS 向导,进行 MPS 计算:
❖ 预测单处理: 企业计划人员根据销售部门的 信息,做出产品的预测,经过内部讨论后, 做为正式的产品预测录入系统。
时区(Time Zone)与时界(Time Fence)
某产品单次生产计划在时间上的时区分布关系
时区3
总提前期 或 计划跨度
累计提前期(采购+加工) 总装提前期
时区2
时区1
某时刻
计划时界
需求时界
计划完工
时间顺序
计划确认时界
时段: 1 2 3 4 5 6 7 8 9 10 11 12 13 14 15 16 17 18 19 20 21
时段 天数
11 3-70 12 3-71 13 93-0 14 93-10 15 93-20 16 9-2 17 - 18 - 19 - 20 -
时段 天数
21 - 22 - 23 - 24 - 25 - 26 - 27 - 28 - 29 - 30 -
时段 天数
31 - 32 - 33 - 34 - 35 - 36 - 37 - 38 - 39 - 40 -
主生产计划(MPS)
主生产计划(Master Production Schedule,简 称为MPS)是确定每一个具体的产品在每一 个具体的时间段的生产计划。计划的对象一般 是最终产品,即企业的销售产品,但有时也可 能是组件的MPS计划,然后再下达最终装配 计划。主生产计划是一个重要的计划层次。
❖ 主生产计划的确定过程伴随着粗能力计划的运 行,即要对关键资源进行平衡。
5.1生产规划和主生产计划
❖ 在ERP的计划层次中,销售与运作规划是一个对 产品族的高层的计划过程。
❖ 销售规划:对产品族总需求的预测。 ❖ 生产规划:为每个产品族建立适当的生产率是制
定销售与运作过程的第二项基本任务,这个生产 率称为生产规划。 ❖ 通常生产规划按产品族以每月的生产率进行描述。 ❖ 生产规划是为了体现企业经营规划而制定的产品 系列大纲,它用以协调满足经营规划的产量与可 用资源之间的差距。 ❖ 生产计划大纲是生产规划的表现形式。
经营规划
需求管理
销售与运作规划 主生产计划
粗能力计划
物料需求计划 能力需求计划
车间作业计划 采购作业计划
执行
ERP的五个计划层次
❖ 经营规划 ❖ 销售与运作规划
具有宏观的性质,是 粗略的和概括的
❖ 主生产计划——宏观向微观的过渡计划
❖ 物料需求计划——主生产计划的具体化
❖ 能力需求计划——把物料需求转化为能力需 求
其意义为产品累计提前期内的计划一般都已经确 认,如果没有确认,可用的生产时间很可能小于 产品的累计提前期,即使马上确认,也可能造成 计划拖期。
ERP 内部集成应用
MRP II 计划的时间三要素
1. 计划期 (跨度)
• 时间是连续、无限延绵的 • 看多远?—≈总提前期 • 预见性
2. 时段
• 分多细?—计划的精度 (分、时、日、周、旬、月、季、年) • 区别优先级
❖ 销售订单处理:企业销售人员根据客户的实际需求, 录入销售订单,并进行相应的处理。
❖ MPS 计算 ❖ 在系统设置-公共资料中设置的物料、仓库的属性; ❖ 在生产数据管理中设置的 BOM、工厂日历; ❖ 在主生产计划中设置展望期、设置计划方案;
❖ 在销售管理中检查销售订单的处理情况;
❖ 在采购管理中检查采购订单的处理情况;
厂长 临时需求小于 可供销售量
下达及确认 系统不能自动更改
人工干预 改动代价大
主生产计划员
临时需求小于可供销售量 通过主生产计划员
计划 系统自动更改
计划员 无限制
5.2.2主生产计划的对象
❖ 主生产计划的对象主要是具有独立需求的 物料和比较重要的物料。
❖ 比较重要的物料主要是指在瓶颈资源上加 工或市场上比较紧俏,或采购提前期较长, 很容易缺货的物料。
❖ 预测均化处理:企业计划人员根据不同的时 间,将预测数量按月、周、日进行均化处理, 均化后的结果做为MPS的来源。
❖ 预测冲销处理: 企业计划人员将销售人员录 入的客户实际销售订单与产品预测进行冲销 处理,避免产生多余的需求。
5.2主生产计划基本原理与计算
❖ 5.2.1MPS的时间基准 ❖ MPS按照时间基准进行计划编制。主生产计划的时间基准
❖ 相对与手工管理来说,MPS/MRP计划可以大大提 高计划下达的效率,并大大增加计划的准确性、及 时性,从根源既计划层面杜绝不必要的库存,减少 浪费。
MRP II 计划与控制层次
层次
决 策 1经营规划 层
2 销售与运作规划
能力
企业资源 资源计划
计划期 时段 复核期 计划对象 工作量
3-7年 年 1-3 年 月
❖ MPS 计算: ❖ .在系统设置-公共资料中设置的物料、仓库的属性; ❖ .在生产数据管理中设置 BOM、工厂日历; ❖ .在主生产计划中设置展望期、设置计划方案; ❖ .在销售管理中检查销售订单的处理情况; ❖ .在采购管理中检查采购订单的处理情况; ❖ .在生产任务管理中检查生产任务的处理情况; ❖ .在委外加工任务管理中检查委外加工任务的处理情况; ❖ .在主生产计划中设置 MPS 向导方案; ❖ .在主生产计划中根据 MPS 向导,进行 MPS 计算:
❖ 2.订单量
❖ 由客户下达订单确定的需求量,是总的订单 数减去已出库的数量。销售订单的需求日期 以销售订单上建议的交货日期为准。
❖ 3.毛需求量
❖ 指未扣除现有库存及预计入库量时的需求, 包括销售订单、产品预测单对物料的独立 需求和上层物料对下层物料的相关需求。
❖ 预测时区:毛需求=预测量 ❖ 计划时区:毛需求=取预测量和订单量的最
3. 时界
• 控制计划的稳定性 • 预测量/合同量的取舍 • 需求时界—≈总装提前期 • 计划时界—≈累计提前期
ERP 内部集成应用
时段划分与需求量显示
原始 数据
01/09 01/14 01/25 02/10 02/28 03/04 05/15 06/30 07/11 07/17 09/30 10/31 11/30 12/29 500 500 1000 750 750 2000 1000 1500 1000 1000 1000 1000 1000 1000
❖ 时区1:也称需求时区,是产品的总装提前期的时 间跨度,即从产品投入加工开始到产品完工的时 间跨度。
❖ 时区2:也称计划时区,在产品的累计提前期的时 间跨度。
❖ 时区3:也称预测时区,超过时区2以外的时间跨 度为时区3.
❖ 需求时界:时区1和时区2的分界点为需求时界。 ❖ 计划时界:时区2与时区3的分界点为计划时界。 ❖ 计划确认时界:计划时界也称为计划确认时界,
❖ 企业的物料需求计划、车间作业计划、采购计 划等均来源于主生产计划,即先由主生产计划 生成物料需求计划,再由物料需求计划生成车 间作业计划与采购计划。
❖ 预测单处理:企业计划人员根据销售部门的信息,做出产品 的预测,经过内部讨论后,做为正式的产品预测录入系统。
❖ 预测均化处理:企业计划人员根据不同的时间,将预测数量 按月、周、日进行均化处理,均化后的结果做为MPS的来源。
年
¥
小
月 产品系列
计 3 主生产计划( MPS ) 粗能力计划
划
层
4 物料需求计划
能力需求计划
( MRP )
( CRP )
3-18 周 周-季 周-季 最终成品
3-18 周 日-周 日-周
组装件 加工件 采购件
执 行 5 生产作业控制 层 ( SFC/PAC )
投入/产出 控制
日
日 ቤተ መጻሕፍቲ ባይዱ-日 工 序
大
季度 计划
月度 计划
1 5500
2 2500
3 3000
4 3000
1 2 34 2000 1500 2000 0
5 6 7 8 9 10 11 12 1000 1500 2000 0 1000 1000 1000 1000
周/月 1 2 3 4 5 6 7 8 9 10 11 12 13 14 15 16 17 18 滚动计划 0 1000 0 1000 0 750 0 0 2750 0 0 0 0 1000 1500 2000 0 1000
1.1
1.8
1.15
1.22
某产品多个订单计划在时间上的时区分布关系
总提前期 或 计划跨度
累计提前期(采购+加工) 总装提前期
时区1
时区2
时区3
某时刻
需求时界
计划时界
时间顺序
时段:1 2 3 4 5 6 7 8 9 10 11 12 13 14 15 16 17 18 19 20 21
50台
60台
表5.3 主生产计划的对象与方法
销售环境 现货生产
订货生产
计划依据 MPS计划对象 计划方法
主要根据市场 预测安排生产
根据客户订货 合同组织生产
独立需求类型 物料
独立需求类型 物料
单层MPS 制造BOM 计划BOM
单层MPS 制造BOM
举例 大批生产的定 型产品