产品标识管理程序
产品标识与追溯管理程序

产品标识与追溯管理程序1目的规定产品追溯性的具体操作方法,确保能追溯到产品的材料接收、生产过程、交货情况,以便查找不合格产品的原因并采取相应的纠正预防措施。
2适用范围本程序适用于公司生产、科研过程中主要原材料的接收、贮存、使用过程中的产品标识及追溯。
3权责3.1 管理部确定产品标识的范围和方法及放置场所并予以实施。
3.2 管理部负责购入原材料的数量、名称、规格、明细,仓库负责保管。
3.3 生产部负责生产过程中原材料、制品、残材、废品贴上标识,并放在规定的置场。
4工作程序4.1 本公司为便于管理,以产品名称、颜色、标签等方式分别对不同形式、规格产品进行标识。
4.2 根据需要,生产部规定所有标识的方法,由质量部对其有效性进行监控。
4.3 当产品出现重大质量问题、客户有追溯要求、法律/法规和公司本身需要时,由质量部组织对产品进行追溯。
4.4 管理部或生产部负责各区域的材料的标识,负责将不同状态的材料分区置放,并负责对所有标识进行维护。
4.5 在有追溯性要求时,对产品予以标识,以便于追溯。
产品标识原则上采用所采购材料的原来本身的标识进行标识。
若原来的标识不清楚,管理部或生产部及时补上新的标识。
4.6 原材料状态标识4.6.1 进货原材料标识原材料进货时,根据到货资料,确认实际货物入库后根据不同品种、批号,分开堆放。
4.6.2 过程产品标识4.6.2.1 原材料由仓库发至生产现场后,定点放置好,并按批号、原材料种类分开堆放。
4.6.2.2 定点放置好后,交由车间人员核对(品种、数量、规格、批号等),生产配料单留存。
4.6.2.3 核对无误后,车间工作人员可以进行投料,在生产记录中记录投料数量、批号。
4.6.3 产品标识不同产品分别在标签上注明品名、批号、重量、生产日期等进行标识。
4.6.4 包装标识按照客户合同或出货通知对包装产品贴上标签进行标识。
4.6.5 各标识对应材料编码见材料编码原则4.7 产品追溯4.7. 1 生产部依据客户订单或合同开出出货通知,此客户订单或合同作追溯依据。
产品标签标识管理程序
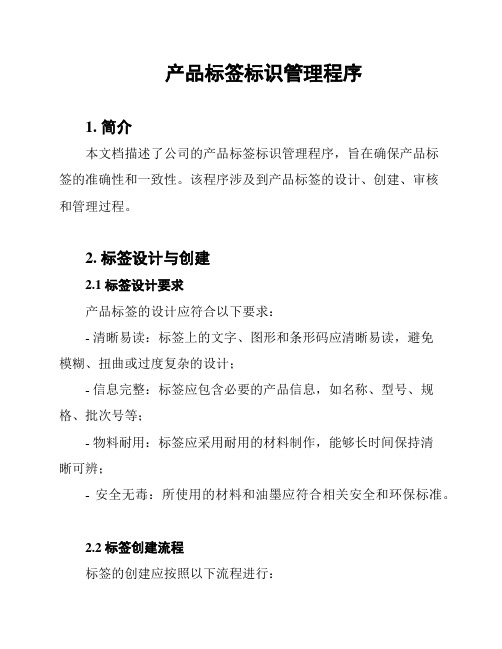
产品标签标识管理程序1. 简介本文档描述了公司的产品标签标识管理程序,旨在确保产品标签的准确性和一致性。
该程序涉及到产品标签的设计、创建、审核和管理过程。
2. 标签设计与创建2.1 标签设计要求产品标签的设计应符合以下要求:- 清晰易读:标签上的文字、图形和条形码应清晰易读,避免模糊、扭曲或过度复杂的设计;- 信息完整:标签应包含必要的产品信息,如名称、型号、规格、批次号等;- 物料耐用:标签应采用耐用的材料制作,能够长时间保持清晰可辨;- 安全无毒:所使用的材料和油墨应符合相关安全和环保标准。
2.2 标签创建流程标签的创建应按照以下流程进行:1. 收集产品信息:收集产品的名称、型号、规格、批次号等必要信息;2. 制定标签设计:根据标签设计要求,制定标签的尺寸、布局和样式;3. 开发标签模板:使用专业设计软件创建标签模板,包括文字、图形和条形码等元素;4. 审核与验证:由负责标签管理的人员进行审核和验证,确保标签的准确性和合规性;5. 打印与制作:使用标签打印机将标签模板打印出来,并将标签粘贴到相应的产品上。
3. 标签审核与管理3.1 标签审核要求为确保标签的准确性和一致性,应设立标签审核机制。
标签审核应满足以下要求:- 审核人员应具备相关产品知识和标签设计要求的理解;- 审核人员应对标签内容进行仔细检查,确保信息的准确性和合规性;- 审核人员应记录审核结果和意见,并及时与标签创建人员进行沟通和反馈。
3.2 标签管理流程标签的管理应按照以下流程进行:1. 标签申请:产品相关部门提出标签需求,包括产品名称、型号等信息;2. 标签创建:按照标签创建流程进行标签设计和制作;3. 标签审核:由审核人员对标签进行审核,确保标签的准确性和合规性;4. 标签发布:审核通过的标签发布给相关部门使用,并进行记录和更新;5. 标签更新:当产品信息有变更时,相关部门应及时提出更新申请,经审核后进行标签更新。
4. 总结以上便是公司产品标签标识管理程序的文档内容。
产品标识和可追溯性控制程序

产品标识和可追溯性控制程序1目的公司对产品的标识进行控制,以防止产品混淆,误用。
确保在需要时对产品质量的形成过程可追溯。
2范围本程序适用于本公司采购产品及生产过程中的半成品、成品。
3职责3.1品质部负责产品标识和可追溯性的控制与管理。
负责产品的检验和试验状态标识,并对其有效性进行监控。
检验人员负责对采购产品的标识及标识移植。
3.2仓库、生产车间负责所属区域内产品标识和维护管理,负责产品的分区摆放。
4程序4.1产品标识的内容与方法4.1.1产品标识的内容可包括产品名称、型号、研制阶段、关键件、重要件、例外(紧急)放行、产品状态、检验和试验状态、所处工序、质量状况、生产批次或编号、生产单位、生产者、检验者、制造日期、检验日期、保管期、产品处置、使用和防护、安全警示等。
4.1.2产品标识的方法可根据具体需要采用标签、铭牌、单据、记录、印章或其他标记等。
标识应清晰、牢固、耐久,并符合规范要求。
4.2采购产品的标识4.2.1采购产品包括原材料、外协件、外购件等。
采购产品进入公司后由采购人员负责将其放置于待检区,向品质部提出报检并提供相关质量证明,经检验员检验合格后方可办理入库手续。
仓库管理员按不同类型的采购产品分别进行标识库存。
4.2.2采购人员在购回物资时,对要求具有质量证明文件的产品,应保持物资原有标识(如生产单位、规格型号、生产批次编号和日期、执行的标准、储存条件、保管期、合格证等)。
4.2.3顾客提供的物资由接收人员标明名称、规格、数量、合同号以及用其本身铭牌等来标识。
4.2.4检验员在进货检验中应确认和保持产品标识,对具有追溯性的原始记录,应归档保存或按规定进行标识移植和替代。
4.2.5检验合格入库后的产品,库管人员应按规定要求保持或实施产品标识。
4.2.6检验不合格的外协外购件由检验员放置于不合格区域,做好不合格标识,按《不合格输出的控制控制程序》执行。
4.3生产过程的产品标识4.3.1对生产过程的产品(在制品、半成品),生产车间使用《工序流转卡》进行标识,填写生产部门、生产批次和日期、生产者、检验者、不合格处理结果等内容。
产品标识管理办法

产品标识管理办法一、目的:确保对原材料、半成品和成品进行标识,确保产品的用途得到保证。
同时在必要的时候进行追溯。
二、适用范围:适用于生产底座和绞车加工过程中的原材料、半成品和成品的标识。
三、职责:1、质检部和生产部负责办法的归口管理,并负责原材料、半成品和成品的现场标识。
2、供销部负责销售底座和绞车的可追溯记录。
四、工作程序:1、标识的分类标识的类别主要有标牌、铭牌、区域、书面文件或记录以及颜色。
2、标识的对象标识的对象包括主要原材料和外协件/外包产品(无法存放到库房内),库房内各类材料以及半成品和成品。
3、检验状态分类按检验状态分类有合格、不合格、待检、待处理、报废五项。
4、标识及具体的编号方法①对各类原材料的标识供销部负责通知生产部做好材料入库准备,并将其放在指定的待检区域内,质量部配合对材料进行验收,生产部负责标识—主要原材料(底座和绞车的A类材料)以区域划分合格或不合格,并在主要原材料上用红色油漆进行标识。
②对外协外包产品的标识外协、外包产品经检验合格后应在其表面醒目位置用红色油漆进行标注,并与合格的外包产品隔离开,防止混用;其他库存物资用标牌进行表示和可追溯。
标牌内容包括:名称、型号、规格、材质、批号等;无法存放到库房的原材料和外协/外包产品应按规定进行存放,《原材料检验单》和《入库单》上应记录供方名称、产品、材质、规格、数量、批号、日期等内容作为标识的可追溯。
③对半成品的标识生产现场应按规定设置合格区、不合格区和待检区以及成品区和半成品区,并在各工序相应的位置粘贴不合格标识和待检表示,合格的半成品可不作标识,各类记录需进行标识时,应在相应的《焊接操作记录》、《工序流转卡》上填写材质、生产编号、加工日期、操作者等作为标识和可追溯;报废的产品用红色油漆在其醒目位置打“×”标识并放置到不合格区,避免混用;生产现场各设备、工装夹具、检验状态区域应按《定置管理图》的规定进行设置并标识。
工程产品标识管理制度

工程产品标识管理制度一、总则为规范工程产品的标识管理,确保产品标识的准确性、一致性和有效性,提高产品质量和品牌形象,保障消费者权益,本制度制定。
二、适用范围本制度适用于公司内生产的所有工程产品的标识管理工作。
三、标识管理责任1. 公司领导层负责全面领导和监督标识管理工作,并承担最终责任。
2. 质量部门负责指导和监督标识管理工作的具体实施。
3. 各生产车间、部门负责本部门产品标识的设计、制作和管理。
4. 市场部门负责产品标识宣传和推广工作。
四、标识管理流程1. 标识设计a. 标识设计应符合相关标准和法规要求,准确表达产品特性和品牌形象。
b. 标识设计应提交质量部门审核,经审核通过后方可制作使用。
2. 标识制作a. 标识制作应选择优质材料和工艺,确保标识的质量和持久性。
b. 标识制作应按照设计稿样制作,不得有任何偏差或错误。
3. 标识管理a. 生产车间、部门应按照标识管理制度的要求,正确安装和使用产品标识。
b. 标识管理人员应定期检查标识的完好性和准确性,及时更换损坏或褪色的标识。
4. 标识宣传a. 市场部门应合理利用产品标识进行宣传和推广,提高品牌知名度和美誉度。
b. 不得擅自更改或篡改产品标识,不得使用侵权标识进行宣传。
五、标识管理措施1. 规范制定标识管理手册,明确标识管理的责任分工和流程要求。
2. 加强标识管理培训,确保标识管理人员熟悉相关制度和要求。
3. 定期对产品标识进行质量抽查,发现问题及时整改和处罚。
4. 建立标识管理档案,记录标识设计、制作、更换等过程,确保标识管理工作的可追溯性。
5. 定期评估标识管理工作,不断完善和提升管理水平。
六、违规处理对于违反标识管理制度的行为,将按照公司相关规定和程序进行处理,包括但不限于责令整改、警告、罚款、停工整顿、解雇等处罚。
七、附则本制度自公布之日起正式实施,如有需要修改,应经公司领导层审批后方可生效。
以上为工程产品标识管理制度的内容,希望各部门和员工认真遵守,共同维护公司产品标识的形象和品质。
产品标识和可追溯性管理程序

产品标识和可追溯性管理程序1 目的通过对工程设备、原材料及施工过程的产品和工序状态在接收入库、发放、安装各阶段加以标识控制,防止设备和材料混用、错用或产品状态的混淆,并有可追溯性要求时进行追溯、查寻。
2 范围程序适用于工程设备、材料、半成品、成品的标识管理与控制。
3 职责3.1 物资管理部门负责工程设备、材料出库前的标识管理与控制;3.2 领用部门负责设备、材料出库后的标识和标识维护;3。
3 质量管理部门、检测部门负责半成品和成品的标识管理;3。
4 质量管理部门负责标识的检查.4 材料和设备的标识4.1 设备、材料接收后,仓库管理员对未经验证的采购设备和材料,保持其原标识,并加以应醒目标识,如划分区域、挂待检标识牌等。
4。
2 设备、材料接收后,经验收合格,由仓库管理员填写入库手续,放入合格库存区,上架和分区存放,并进行标识,标识遵守如下规定:a)对有原标识的设备、材料(设备铭牌、材料编号或货号等),仓库管理员要保持原标识。
b) 对无原标识,而有国家规定标识的材料、设备,按国家规定进行标识。
c)对无原标识,又无国家规定标识的设备、材料,采用挂牌、涂色等方式进行标识。
d)入库产品采用“四定位"标识,做到清楚、易懂、不易消失。
4。
3 仓库管理员对验证不合格的设备、材料,隔离存放,醒目标识,如挂不合格标识牌等。
经处置合格后放入合格库存区.4.4 仓库管理员还应根据检验和试验报告或证明通过登记台帐的方式进行状态管理,表明此材料经检验和试验合格与否。
4.5 对有可追溯性要求的设备和材料应加以唯一的标识,并对标识进行记录。
4。
6 设备、材料出库时,物资管理部门仓库管理员应做好库存物资的标识移植工作。
4.7物资管理部门仓库管理员对库存设备、材料的标识予以维护.当标识损坏或丢失时,由检验人员或仓库管理员确认后追补标识,对需重新标识的设备及材料,重新标识前严禁发放。
4。
8 施工人员领用工程材料后,对有原标识的设备、材料维持原标识,也可根据需要对设备、材料重新标识,并维护标识。
HSF产品标识与追溯管理程序

5.2.1.HSF材料生产过程中所有相关质量记录(检验标准、追溯记录、转工序标签等)均应加盖“ROHS”印章以示区分环保与非环保,若已导入全环保则无需区分。
5.2.2.考虑到生产机台加工后会有残留物附着在机台表面及缝隙内,故每次生产前都应对机台进行清理。
5.2.3.生产过程中,应按生产订单量领料,每批物料的投入状况应记录于各制程的生产日报表中,每班在投入物料时,应在“生产日报表”上注明所投之物料批号.并使其可与生产制令单对应,以方便管控。客户对此有特殊需求时依需求作业。
5.4.3.成品仓划分环保产品合格品与不合格品放置区域,且环保产品加贴绿色RoHS标签;以防止环保产品与非环保产品的相互混入;
5.5.HSF管制标签:
客户有要求的环保物料均要有“ROHS”标签,其它标签均参阅ISO9001:20XX质量管理体系之《标识与可追溯控制程序》作业相关内容规定。
5.6产品追溯:
5.3.HSF出货产品标识:
5.3.1成品入库时在成品外箱标签上加贴“ROHS”标签以示区分,客户有要求使用特定的环保标签时,应按照各客户之要求,加贴客户指定标签。
5.3.2.经最终检验之成品其外包装须贴上成品检验合格标签,标签内容须显示产品的品名数量,包装日期,作业员姓名,以便日后追溯。
5.3.3.HSF物料出现异常时,应立即将该物料移至HSF不良品区上锁,并加贴红色不良品标签,.
5.3.4.对于质量上有异议的原材料,半成品或成品,由品质部贴不合格标识,放置于待判区等待裁决。
5.4.区域划分:
5.4.1.原材料仓划分环保材料良品与不良品的摆放区域,以防止HSF异常品与合格品的相互混入;
5.4.2.生产现场划分良品与不良品的摆放区域,且只允许放置HSF合格半成品.成品材料,并加以标识.
程序文件八产品标识及防护管理程序(二)2024

程序文件八产品标识及防护管理程序(二)引言概述:程序文件八产品标识及防护管理程序(二)是为了进一步加强和规范公司在产品标识及防护方面的管理,确保产品的质量和安全性。
本文将从五个大点入手,详细阐述程序文件八的内容和要求。
一、产品标识要求1. 标识位置:明确产品标识应放置在产品的何处,确保易于辨识和识别。
2. 标识内容:要求标识内容准确、清晰、易懂,包括产品名称、规格型号、生产批次等信息。
3. 标识材质:选择合适的标识材质,确保在产品使用寿命内不易损坏或褪色。
二、产品包装标识管理1. 包装标识设计:设计合理、美观的包装标识,包括产品名称、厂名厂址、生产日期等信息。
2. 包装标识打印:采用高质量的打印设备,确保打印效果清晰、不模糊。
3. 包装标识验证:在包装过程中进行严格的标识验证,确保每个产品都有正确的标识。
三、产品防护要求1. 原材料防护:制定严格的原材料保管措施,确保原材料的防潮、防尘等。
2. 生产环境控制:建立适当的生产环境控制措施,包括温湿度控制、防尘措施等。
3. 环境污染防护:采取必要的措施,防止产品在生产、贮存和运输过程中受到环境污染。
四、产品售后服务1. 售后服务承诺:明确公司对产品售后服务的承诺和责任,如无条件退换、免费维修等。
2. 售后服务流程:建立完善的售后服务流程,包括用户投诉受理、服务请求处理等。
3. 售后服务评价:定期对售后服务进行评估和改进,提高服务质量和用户满意度。
五、产品质量保障1. 质量监控:建立完善的质量监控体系,包括原材料检验、生产过程检测等。
2. 质量记录保存:规定质量记录的保存时间和方式,确保质量问题可追溯。
3. 质量改进措施:针对质量问题,及时采取纠正措施和预防措施,确保产品质量稳定提升。
总结:程序文件八产品标识及防护管理程序(二)是对公司产品标识和防护方面的要求和管理措施进行规范和强化。
通过明确产品标识要求、加强产品包装标识管理、落实产品防护要求、提高售后服务质量和加强产品质量保障,能够保证产品的质量和安全性,提升公司形象和用户满意度。
产品标识和可追溯性管理程序( ISO13485程序 )

程序文件编号:NK/QSP-753-01版号:A/0发布日期:2018年02月01日实施:2018年02月01日拟制:审核:批准:受控编号:受控印章:1.目的防止不同类别、不同检验状态的产品混用和误用,当有规定时,实现产品的可追溯性。
2.适用范围适用于物料、半成品和成品的产品标识及检验状态标识。
3.职责3.1.生产部组织实施生产过程中产品标识和可追溯性工作。
3.2. 质量部负责确定生产过程各阶段产品可追溯性的唯一性标识以及标识的位置和方法。
3.3. 质量部负责所有产品标识的监督检查工作及检验状态或印章使用。
3.4. 仓库管理员负责对入库原辅材料、外购外协件和不同品种、规格、批次、货源单位进行明确标识和记录,防止混用。
4.5.仓库、车间负责所属区域产品的标识,负责不同检验状态产品的分区摆放,及所有标识的维护。
4.工作程序4.1.进货物料4.1.1.物料进厂,仓管员负责将其放置于待检区,对于本身未做产品标识或标识不清的物料,需贴物料标识卡,注明物料名称、数量、进货日期等内容。
4.1.2.经质量部检验合格的物料,由检验员签字后方可办理入库手续。
4.1.3.检验不合格的物料保持原有产品标识,放置于不合格品区。
4.1.4.对于紧急放行的物料用“紧急放行”标签或印章对其进行标识,便于追溯(本公司不执行紧急放行)。
4.2.生产过程中的标识4.2.1.对于生产过程中所使用的物料,如未能保持其原有产品标识,车间可在盛装的容器上直接标明其名称、型号(规格),进行标识。
4.2.2.对于待检品,需放置于待检盒,对于合格品,需放置于合格品区,对于不合格品(包括物料),需放置于不合格品区。
4.3.成品标识4.3.1.加工完成或各种原因退回的成品,如包装上已有注明,可不再做产品标识,放置于待检区(检验后,可保持其原有产品标识)。
4.3.2.检验合格的成品,由检验员签字后方可办理入仓手续。
4.3.3.检验不合格的成品,直接将其放置于不合格品区。
标识和可追溯性控制程序(含流程图)

标识和可追溯性控制程序1目的为明确自生产至交付所有阶段中产品的标识以表明生产过程产品的实际状态和达到可追溯性的目的和有效控制,制定本程序。
2范围本程序仅适用于自生产至产品交付所有阶段对产品进行标识。
3职责3.1生产车间、仓管员对所属区域内的产品进行标识和检验状态标识。
3.2质检部门负责对各自检验的产品进行标识。
4程序4.1标识4.1.1产品流转/存放标识4.1.1.1物料进厂,原料仓库仓管员应检查物料的外包装标记。
对于未有标记或标记不清的物品应挂以标识或贴上标签,对于物料本身的外包装标记已明确,可利用其标记进行识别,也可予以标识。
原物料应分类堆放。
4.1.1.2生产过程中的半成品或暂歇期间的在制品,生产车间应对每堆物资放置标签,并注明其目前的工作状态并分类堆放,产品加工过程采用《自制件随工流转卡》进行标识。
4.1.1.3加工完成的成品可根据客户要求在其外包装上按客户要求进行标记。
客户没有要求的,在存放期间应放置相应的识别标识。
4.1.1.4对加工过程中的关键件除采用《自制件随工流转卡》进行标识外,还要有《关键件检验记录》记录检验结果,做到质量可追溯性,对焊接、总装、涂装有《焊接检验指导书及记录》《总装配检验指导书及记录》《涂装检验指导书及记录》进行可追溯记录。
4.1.1.5所有流转/存放的标识除类别标牌外,应清楚说明标识的内容。
4.1.2检验/试验状态标识4.1.2.1检验/试验状态标识分待检及不良品字样的牌子/标签,并分区堆放。
正常合格品使用产品流转单/标识牌/标签,并在上签名/盖章,不另作检验/试验合格状态标识。
4.1.2.2物料进厂,仓管员应通知检验部门进行检验并负责放置“待检”牌,经检验部门检验/验证合格,检验人员在进仓单据上签名并取摘“待检”牌,仓库方可入库。
4.1.2.3生产过程中的不合格应放置在标有红色不良警示字样的容器内。
4.1.2.4无论是材料还是半成品、成品,对于检验不合格,需放置红色不合格字样的标签/标牌或不合格标记或存放在标有红色不良警示字样的区域内。
产品标识与可追溯性管理程序(含表格)

产品标识与可追溯性管理程序(IATF16949-2016/ISO9001-2015)1.0目的建立和实行产品标识和记录制度,根据标识或记录对产品进行追溯,为分析产品质量和采取纠正措施提供依据。
2.0适用范围本程序适用于所有在公司范围内的原材料、半成品和成品的标识。
3.0职责3.1.生产部负责在线产品的标识方法,负责生产过程中原材料、半成品、成品状态的标识。
3.2.品质部负责检验和试验状态的标识。
3.3.仓管部负责库存品的标识4.0程序内容4.1.产品标识4.1.1.来料标识:由供方在外包装上用标签进行标识。
4.1.2.原材料存贮时标识。
4.1.2.1.原材料来料时,由IQC标明检验状态,原材料检验完成后在包装箱贴上检验标识,并注明该原材料的品名、数量、供应商及检验结果,参照《进料检验管理程序》。
4.1.2.2.原材料入库时由仓管员根据品质部检验结果标识状态办理,且在《物料标识卡》记录原材料的入库时间、品名、数量。
4.1.3.成品标识4.1.3.1.单一产品标识:在成品的指定位置贴上该成品的成品条码、QC Passed 标签,成品条码按照《产品条码编码规范》执行。
4.1.3.2.外箱标识:在外箱的指定位置贴上标签,注明产品的型号、生产日期、客户名、检验结果、检验日期、生产批号等。
4.1.4.执行状态标识。
4.1.4.1.生产状态标识为:待处理品、完成品和不良品等,生产中根据各工序的不同情况进行标识。
4.1.4.2.检验状态标识参见《成品检验管理程序》将检验情况进行标识。
4.1.4.3.具有相对独立性的各作业段半成品用“产品流程卡”作为标识,从流程卡上可追溯到生产线别,机型等特性。
4.1.4.3.1.产品流程卡标识4.1.4.3.2.作业员每天将其所用流程卡流水号记录于《条码记录表》上。
4.1.5.不良品标识:用红色的标签标识和带红色标识的防静电周转箱进行隔离,具体参照《不合格品管理程序》。
4.1.6.区域标识:现场区域采用挂牌、斑马线等方法进行标识。
IATF16949:2016产品标识和可追溯性管理程序

文件名称:产品标识和可追溯性管理程序文件编号:DF-G∕B(02)15-2017总页数:版本版次: AOL目的防止不同类别、不同检验状态的产品混用和误用。
当有规定时,实现产品的可追溯性。
2.范围适用于物料、半成品和成品的产品标识及检验状态标识。
3、定义3.1所有生产物料/在制品、半成品、成品,在此都被定为【产品】。
3.2于公司内各个场所放置之产品,依其本身品质状况、产出日期等,加上适当标识称之为“状态标识”,状态标识可分为:3.2.1进料检验/过程检验/成品检验/出货检验产品合格时,使用绿色、灰色或印有‘检'字的白色塑料箱。
3.2.2进料检验/过程检验/成品检验/出货检验时产品不合格时,使用红色塑料箱。
3.2.3进料检验/过程检验/成品检验/出货检验产品待检时,使用印有‘生’字的白色塑料箱。
3.3于公司内各个场所放置之产品,依其本身品质、类别、规格,放置于适当地线区域内的称之“区域标识”,区域标识可分为:3.3.1合格品区一划线圈定区域,将合格产品放于内,产品包装物上摆放合格品标识。
3.3.2不合格品区一划线圈定区域,将不合格品放于内,产品包装物上摆放不合格品标识。
3.3.3待检区一划线圈定区域,当设备发生故障时,将待检产品或可疑产品放于内,产品包装物摆放品名标识。
3.4品名标识:即将产品的名称/数量/批次/生产单位等信息写在标识卡上,摆放在产品的包装物上。
4.职责3.1生产部负责执行本程序(所有标识的编制、修订和有效性监督等)。
3.2检验人员负责检验状态标签或印章的使用,负责产品或半成品、成品检验状态的标识。
当产品出现质量问题时组织对其进行追溯。
操作者负责自己生产的产品名称、规格、生产者的标识。
5.95.10货物料标识5.10.1料进厂,库管员负责将其放置于检验员指定区域,并填写《物资入厂检验申请单》。
5.10.2检验合格的物料,由检验员填写《入厂检验报告单》,库管员根据物料名称、规格、数量等内容办理入库手续,并将该批物料置于相应合格品区域。
产品标识和可追溯性管理程序
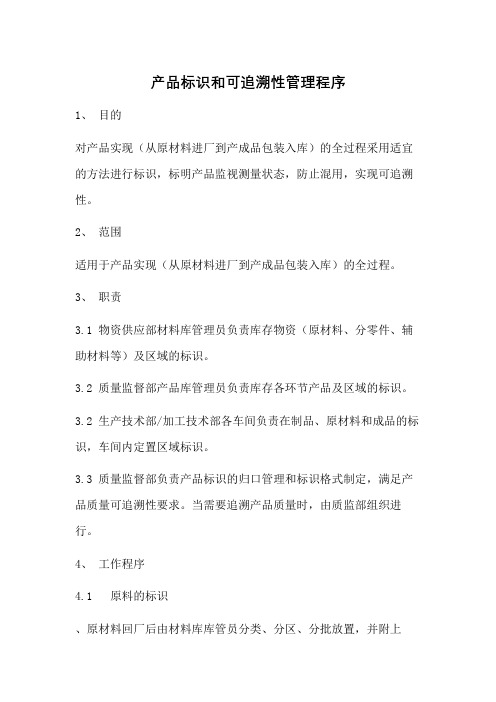
产品标识和可追溯性管理程序1、目的对产品实现(从原材料进厂到产成品包装入库)的全过程采用适宜的方法进行标识,标明产品监视测量状态,防止混用,实现可追溯性。
2、范围适用于产品实现(从原材料进厂到产成品包装入库)的全过程。
3、职责3.1 物资供应部材料库管理员负责库存物资(原材料、分零件、辅助材料等)及区域的标识。
3.2 质量监督部产品库管理员负责库存各环节产品及区域的标识。
3.2 生产技术部/加工技术部各车间负责在制品、原材料和成品的标识,车间内定置区域标识。
3.3 质量监督部负责产品标识的归口管理和标识格式制定,满足产品质量可追溯性要求。
当需要追溯产品质量时,由质监部组织进行。
4、工作程序4.1 原料的标识、原材料回厂后由材料库库管员分类、分区、分批放置,并附上《原料检验(验证)标识卡》,、按标识卡上内容(材料名称、批次、厂家、进货重量、进货日期、库管员)填写完整,并签字确认。
标识位置:由库管员装入塑料袋内后固定在该批料的外包装或盛装的容器外表面上,无包装的原材料标识要悬挂在该批料存放的醒目位置,严禁将标识卡放在物料里面。
每批原料用完后,应对原有可回收使用的容器(如周转桶)悬挂的原标识卡清除干净,以防混料,造成无法进行产品追溯。
原料批次为生产厂家的批号。
4.2 配料室所存原料及配好的成料的标识4.2.1 配料室所存原料由配料员分类、分区、分批放置,并附各自的《原料标识卡》。
标识内容包括材料名称、批次、厂家或产地、重量。
标识位置:装入塑料袋内后固定在该批料的外包装或盛装的容器外表面上,无包装的原材料标识要悬挂在该批料存放地的醒目位置。
每批原料用完后,应对原有可回收使用的容器(如周转桶)悬挂的原标识卡清除干净,以防混料,造成无法进行产品追溯。
4.2.2所配好的成料用《钢锭(甩片)流通卡》进行标识。
由配料人员按标识卡上要求的各项内容填写完整,经复核后根据复核结果由复核人员签字确认后下转下一工序。
对于要分装的成料也用《钢锭(甩片)流通卡》进行标识,为防止混料,每个分装桶内再各附一张《成料标识卡》(填写内容:成料批号、分装号、操作人员)进行标识。
产品标识与可追溯性控制程序

产品在量产前由检验员进行检验,发现不合格品时,由检验员对不合格品进行“不合格品”标识,并监督生产部将不合格品移至不合格品区进行隔离,未得到不合格品处理通知之前,任何人不得将其转入下道工序。
5.3 产品质量追溯
5.3.1 产品追溯流程:
5.3.1.1 根据《生产指令单(工单)》、检验记录、入库有关记录等相关资料可以追溯到生产历史。
5.2.1.3 仓管员根据IQC检验合格物料进行入库处理,入库后物料按《仓库储存管理规定》执行及以物料类别、型号进行区分标识管理。
5.2.2 生产过程标识及记录
5.2.2.1 生产车间所用的物料时须核对《生产指令单(工单)》中物料,核对无误后将物料放置在“待生产”货架或“待生产区”内。
5.2.2.2 半成品流入下一道工序前,在轴标或周转车内放置物料跟踪卡以识别半成品,防止过程混料/错料。
5.4.2 批次号作为产品可追溯性的依据,应记录在生产过程中所有表格、记录、装箱单、出货标签。批次号填写要做到统一、准确与实际相一致,以便对产品可追溯性进行控制。
6、相关文件
《IQC来料检验规范 》
《制程检验规范》
《成品检验规范》
《不合格品控制程序》
《仓库储存管理规定》
7、表单记录
《进料检验报告》
《生产指令工单》
5.2 产品标识
5.2.1 进料物料标识及记录
5.2.1.1 采购物料到公司后,仓库根据供应商的《送货单》进行清点收货,并将物料放置待检区作待检标识,并通知质检部进行质量检验。
5.2.1.2 品质部IQC按《IQC进料检验规范》检验作业,并记录于《IQC进料检验报告》,经检验合格的作“已检OK”标识、不合格物料将其放置在“不合格品区”并按《不合格品控制程序》执行。
产品标识及防护管理程序

产品标识及防护管理程序1、目的:对物料、半成品、成品的搬运、贮存、防护及交付过程进行管理,确保产品质量。
对产品进行必要的标识,防止在产品实现过程中的混用。
2、范围:适用于公司采购的所有物料、半成品及成品。
3、职责:3.1生产部负责生产中半成品、成品的包装、保管、搬运,负责对本部门存贮的物料和产品的标识管理。
3.2仓库负责物料、成品的入库、出库手续及在库物品的标识、保管。
4.、作业内容4.1物料入库4.1.1供应商物料送到后,仓管员核对《送货单》,确认物料的品名、规格、数量无误,包装无损后,签收送货单,填写《来料送检单》送质量部检验。
4.1.2质量检验合格后,仓库清点数量无误后开具《收料单》入库,登记入帐,并标明日期。
4.1.3质量检验不合格时应及时通知采购部。
4.2物料分类:4.2.1对仓库划分区域,分为成品库、材料库,各区域应隔离并分类存放予以标识。
4.2.2物料的标识与摆放4.2.2.1所有物料应按照类别分别按区域放置,应摆放整齐、平稳。
4.2.2.2物料名称、型号、数量等应标识清楚。
4.2.2.3当整箱物料开箱后小包装上,如无标识则需另加标识,散料用容器或纸箱盛装,并应加标识。
4.2.2.4 具有化学性质的危险品应隔离管制,并指定专人负责。
4.3物料发放4.3.1仓库管理员以研发部的《物料清单》和《生产任务单》预备生产所用的材料并放置备料区。
4.3.2生产部领料人依《物料清单》数量填写《领料单》到仓库领料,仓管员核对物品的名称、型号、数量等然后发料。
4.3.3仓库发料时应遵循先进先出的原则,物料按入库的日期,先入库的物料先出库使用。
若物料上有标识生产日期,按先生产日期先出库使用。
4.3.4生产部补料时需填写《生产补料单》,由部门负责人审核后,仓库开出《领料单》,方能给予补料。
4.4退料作业4.4.1生产多余的良品退库时,应填写《内部退料单》,物料经质量管理部确认合格后,仓管员接收存放于原物料区内,并登记入帐。
产品标识和可追溯性管理程序

产品标识和可追溯性管理程序1 目的为防止生产过程中从原材料到半成品、成品及不合格品的混用或误用,确保产品符合顾客要求,并可追溯产品及过程的质量问题,特制定本程序。
2 适用范围本公司所有原材料、半成品、成品及不合格品的标识与追溯均适用。
3 定义3.1产品标识:指用适当的方法在生产、服务运作全过程中对采购产品/材料、半成品、成品或包装物上做出适当的标记或标签。
3.2可追溯性:指根据或利用记载标识的记录,追溯一个项目或产品的生产加工过程、应用情况、用途或所处场所的能力。
3.3检验与试验状态:指材料或产品有无进行检验/试验,以及经检验/试验之后合格与否的状态。
4 职责4.1产品追溯性及追溯性标识由技术中心设计人员负责将标准(国标、铁标、国外标准)、法律法规和客户对产品标识的要求转化为产品标识和可追溯性标识要求;4.2需要模具上体现标识和追溯性的技术中心负责将规定的标识转化在相应的模具上,并定期更新模具标识;负责采购定额输出,明确标识工艺路线;特殊工艺标识要求在设计评审阶段就进行论证;负责在包装方案中明确产品发出时包装箱上的标识要求;负责公司内工艺布局区域划分标识的制定。
4.3质保部负责产品状态标识中检验状态标识的制定和监督实施情况;负责检验状态标识印刷申请的提出。
4.4物资管理部、库房负责对购入的仓储产品进行标识;物资管理部负责按照产品定额进行标识的采购;4.5生产车间负责按设计、工艺和质量管理的要求对车间存放的原材料、在制品、半成品、成品的标识,负责产品状态标识中生产状态标识在生产过程中产品的识别性标识方式、方法和标识的维护,负责保护标识在流转过程中的有效性;负责生产状态标识的打印或印刷申请的提出;车间主任负责建立所管辖人员工位号的建立与时时更新。
6、工作内容7、附加说明7.1 仓库、车间以待检品、合格品、不合格品等标识牌进行区域标示,使之一目了然,并按《库房管理程序》实施管理,置于合格品区的成品、物料才允许出库。
产品检验状态标识管理制度
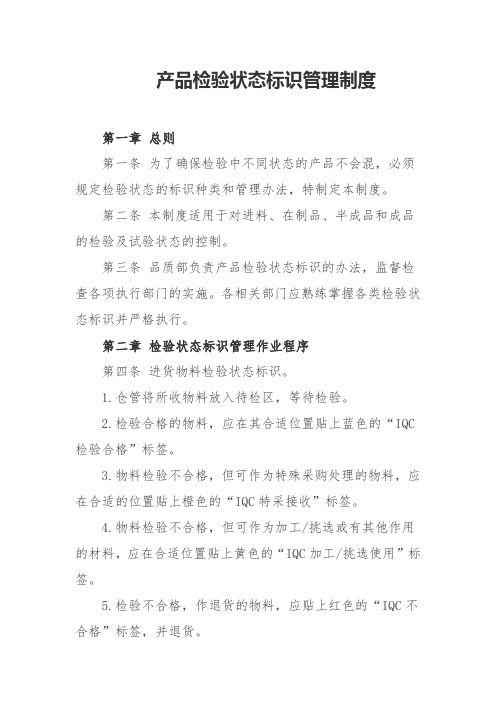
产品检验状态标识管理制度第一章总则第一条为了确保检验中不同状态的产品不会混,必须规定检验状态的标识种类和管理办法,特制定本制度。
第二条本制度适用于对进料、在制品、半成品和成品的检验及试验状态的控制。
第三条品质部负责产品检验状态标识的办法,监督检查各项执行部门的实施。
各相关部门应熟练掌握各类检验状态标识并严格执行。
第二章检验状态标识管理作业程序第四条进货物料检验状态标识。
1.仓管将所收物料放入待检区,等待检验。
2.检验合格的物料,应在其合适位置贴上蓝色的“IQC 检验合格”标签。
3.物料检验不合格,但可作为特殊采购处理的物料,应在合适的位置贴上橙色的“IQC特采接收”标签。
4.物料检验不合格,但可作为加工/挑选或有其他作用的材料,应在合适位置贴上黄色的“IQC加工/挑选使用”标签。
5.检验不合格,作退货的物料,应贴上红色的“IQC不合格”标签,并退货。
第五条单个不合格品标识:生产过程中检查或自检发现单个不合格品时,在其相应部位贴上红色箭头纸或者放在有“不合格品”红色标签区域内。
第六条五金、塑胶车间QC巡检状态标识。
1.做好的产品应该放在待检区域或生产机器旁待检。
2.巡检员巡检合格后,在半成品或成品批次标识卡上盖蓝色的“QC巡检合格”章,或者放在“合格”产品区域内。
3.虽然不合格,但可以接受的产品批次,可以在产品上贴橙色的“QC巡检让步接收”标签。
4.不合格产品,如需返工处理,应贴上黄色的“QC巡检返工”标签。
5.如只能作为报废处理的产品,应该贴上“QC巡检报废”标签。
第七条五金、塑胶车间QA半成品入仓检验状态标识。
1.未被检验的产品,放在待检区域内,贴上“QA正在检查中”标牌。
2.入仓检验合格,在半成品标识卡上盖蓝色的“QA检查合格”章。
3.检验不合格但可以接受的,贴上橙色“QA让步接收”标签。
4.不合格需返工的半成品,贴上黄色的“QA放工”标签。
5.不合格须作为报废处理的,贴上红色“QA报废”标签。
产品标识及可追溯性管理程序

产品标识及可追溯性管理程序1. 简介在现代的供应链中,产品标识和可追溯性管理程序是非常重要的环节。
通过有效的产品标识和可追溯性管理,企业可以更好地控制产品的生命周期,提高产品的质量和安全性,并满足各种监管要求。
本文将介绍产品标识及可追溯性管理程序的基本概念、重要性和实施步骤。
2. 产品标识的定义和作用产品标识是指在产品上或产品的包装上使用的各种标记、标签或编码,用于区分和识别不同的产品。
产品标识通常包括产品的名称、型号、规格、批次号、生产日期等信息。
产品标识的作用主要有以下几个方面:•产品识别:通过产品标识,可以快速准确地识别不同的产品,避免混淆和错误。
•产品追溯:产品标识可以提供产品的详细信息和历史记录,便于追溯产品的来源、加工过程和流向。
•产品验证:通过产品标识,可以验证产品的合法性、真实性和可靠性,防止假冒伪劣产品的流入。
3. 可追溯性管理的定义和意义可追溯性管理是指通过有效的记录和追踪系统,将产品或原材料的信息与其生产、加工和供应环节相连接,实现对产品的全过程控制和追踪。
可追溯性管理的意义主要体现在以下几个方面:•提高生产效率:通过可追溯性管理,可以更好地控制生产过程和生产资源,提高生产效率和运营效益。
•管理风险:可追溯性管理能够及时发现并追踪产品的问题,帮助企业及时采取措施,减少不良事件的发生,降低风险。
•满足监管要求:许多行业都有严格的监管要求,要求企业对产品的来源和流向进行详细记录和报告,可追溯性管理可以帮助企业满足这些要求。
•提高品牌价值:通过可追溯性管理,产品的品质和安全性得到有效保障,有助于提升品牌的信誉和价值。
4. 产品标识及可追溯性管理程序的实施步骤4.1 确定标识要素和标识方式在开始产品标识及可追溯性管理程序之前,首先需要确定产品的标识要素和标识方式。
标识要素包括产品的名称、型号、规格、批次号、生产日期等信息。
标识方式可以采用条形码、二维码、RFID等技术,也可以使用印刷、贴纸等传统方式。
产品标识管理程序

产品标识管理程序1.⽬的在接收、⽣产和交付的各阶段为防⽌混⽤,以适当⽅式标识产品。
当合同、法律规定或管理需要有可追溯性要求时,对每个或每批产品进⾏唯⼀性标识。
2.范围本程序适⽤于公司在接收、⽣产和交付的各阶段需要标识的产品。
3.职责3.1各部门负责接收、⽣产和交付各阶段产品的标识、维护。
3.2品质部负责对各单位执⾏情况的指导、考核品质部对原材料、⼊库成品、产品的检验状态进⾏标识及防护监管。
4.定义4.1产品标识:指⽤适当的⽅法在⽣产、服务运作全过程的采购产品/材料、在制品、成品或包装物上做出适当的标记或标签。
4.2可追溯性:指根据或利⽤所记载标识的记录,追溯⼀个项⽬或实体的历史、应⽤情况或⽤途或所处场所的能⼒。
4.3检验与试验状态:指材料或产品有⽆进⾏检验和/或试验,以及经检验和/或试验之后合格与否的状态。
4.4RoHS标识:法律法规禁限⽤物质标识。
5.程序5.1标识策划5.1.1产品标识⽅法:各检验、⽣产过程、仓库贮存阶段的所有产品、原材料/辅助材料、在制品、成品、ROHS等,各部门均需根据产品实际所需的标识状况和本部门实际的⽣产状况对其以适当的标识⽅法进⾏标识;产品标识的⽅法可⽤标签、批次号、颜⾊、符号、装载容器、堆置区域等形式进⾏划分,标识应清晰和易于识别。
5.1.2检验、试验状态分类与分区:1) 检验、试验状态由检验和/或试验⼈员确定;2) 不同状态的产品分区域存放:a. 未经检验、试验------------未检验/试验区b. 已经检验、试验合格--------合格区c. 已经检验、试验待定--------待定区d. 已经检验、试验不合格------不合格品区分别⽤:未检/试品、待定品、合格品、不合格品(⼜可分废品)⽂字或标牌进⾏标识。
5.1.3状态标识⽅法:凡公司从原材料、辅料进⼚到⽣产过程中和各仓库储存、存放的在制品(半成品)和成品均须按以下规定进⾏明确的状态标识:1)对于采购产品a.等待检验和/或试验的以黄⾊“物料标签”或将其移⼊待检区进⾏标识;b. 经检验和/或试验合格的以绿⾊“物料标签”或将其放合格区进⾏标识;c. 经检验和/或试验不合格以红⾊“物料标签”或将其放不合格区进⾏标识;d. 未检验和/或试验结论未经评审被确认为紧急放⾏的应在⽣产报表上注明“紧急放⾏”字样。
- 1、下载文档前请自行甄别文档内容的完整性,平台不提供额外的编辑、内容补充、找答案等附加服务。
- 2、"仅部分预览"的文档,不可在线预览部分如存在完整性等问题,可反馈申请退款(可完整预览的文档不适用该条件!)。
- 3、如文档侵犯您的权益,请联系客服反馈,我们会尽快为您处理(人工客服工作时间:9:00-18:30)。
一目的:
确保所有产品由原物料到成品出货的各阶段均加以鉴别与标示,以便发生异常时,能对产品进行追溯,以便了解真正的不良起因.
二范围:
自原物料进厂到成品出货各阶段之产品标识和追溯作业皆属之。
三定义:
3.1追溯:是指追溯所考虑对象的历史、应用情况或所处位置的能力。
注1:当考虑产品时,可追溯性可涉及到:
——原材料和零部件的来源;
——加工的历史;
——产品交付后的发送和所处位置。
四权责:
4.1 原物料标识:资材、品保;
4.2 制程中原物料与产品标识:生产、品保;
4.3 成品标识:生产、资材、品保;
4.4 标签由品保部进行设计制定。
五程序内容:
5.1 原物料标识:
5.1.1 技术部在进行零件承认时,根据物料编码原则对每一种物料给出一种唯一对应之编号,协力厂商在送货时需在材料包装上贴上标签,以标示材料之编号、数量、日期、批量等。
5.1.2 协力厂商送料时,收货员应将物料放置于待检区,无法放入待检区的应及时在堆放处挂“待检验”标识。
并开出【送检单】给进料检验员.
5.1.3 进料检验员根据【送检单】、《进料检验规范》、《零件图》、样品等对原物料进行品质判定后贴上相对应之标签如,合格为绿色“合格”标签,特采为黄色“特采”标签,不合格为红色“不合格”标签和紫色“返修/配修”标签。
免检为蓝色“免检标签”。
5.1.4 仓库根据进料检验员对材料的合格标识和特采标识入库、登记、入帐、上架、上卡,且标示名称;
5.1.5 仓库应分区管理,每区应张挂“区域标示图”,货架应贴上产品标签,每一种产品挂上“物料卡”;
5.1.6 适用时,物料应设置摆放高度限高要求及用红色警戒线标示;退协力厂商产品、客退品放置在不良品区(红色线规定的区域内),等待处理;
5.2 制程标识:
5.2.1产品上线生产前,由生产部根据【制造命令单】对相应的主机进行钢印编号及【产品追踪卡】,生产过程中每一个工序都须使用【产品追踪卡】进行工序控制,【产品追踪卡】必须如实记录订单编号、制令单号、相应的班别、工序、生产时间、操作人员及数量。
5.2.2 各生产线之物料暂存处之标示应注明机型、名称、编号、数量、日期、品质状态。
生产线各工序上之材料依相应作业指导书之编号标示识别;且在放材料之胶框上加以注明材料名称,编号、状态。
生产出之半成品应放上标示牌,写明
机型名称.
5.2.3 制造过程中发现的和生产出的不良品应放置于红色不良品盒子内(或红色线区域内),待确认或待检验之产品应放置于黄色“待验区域”内,标示清楚,利于下工序作业;
5.2.4 制程中整机组装合格需入库时,应通知成机检验员进行检验,检验合格则贴上“合格证”,若不合格则贴红色“不合格”标签。
退生产进行重工处理。
5.3 成品标识:
5.3.1 仓库收到入库之合格成品应妥善放于相应区域内,并挂牌加以标示:成品编号,数量等。
并做好相应的账目工作。
5.3.2 待出货之机器应放置在“出货区”内,等待装车出货;
5.3.3 成品出货检验时应明确检验各产品标识是否齐全,若不齐全应以不合格品处理。
5.4 各部门应保持产品状态标识,若有未标识明确之产品,应主动进行隔离或知会相关责任人立即处理。
5.3 相关记录依《记录控制管理程序》执行。
相关文件:六
6.1《进料检验规范》
6.2《零件图》
6.3《物料印记管理办法》
6.4《纠正预防管理程序》
6.5《记录控制管理程序》
七相关记录:
7.1【送检单】
7.2【产品追踪卡】
八产品标签(附件一)
合格标签
图号供应商/工序不良数量检验单号
检验日期检验员
□合格产品状况
不合格标签
供应商/工序图号
不良数量不合格单号检验日期检验员
不良状况□外观不良□性能不良□尺寸不良处理方式□机加返工□装配修配□退供应商
特采标签
供应商/工序图号
不合格单号不良数量
检验日期检验员
□尺寸不良□性能不良□外观不良不良状
况.处理方式□机加返工□装配修配□其它。